0404086庄茂团汽车覆盖件前纵梁冲压工艺及模具设计
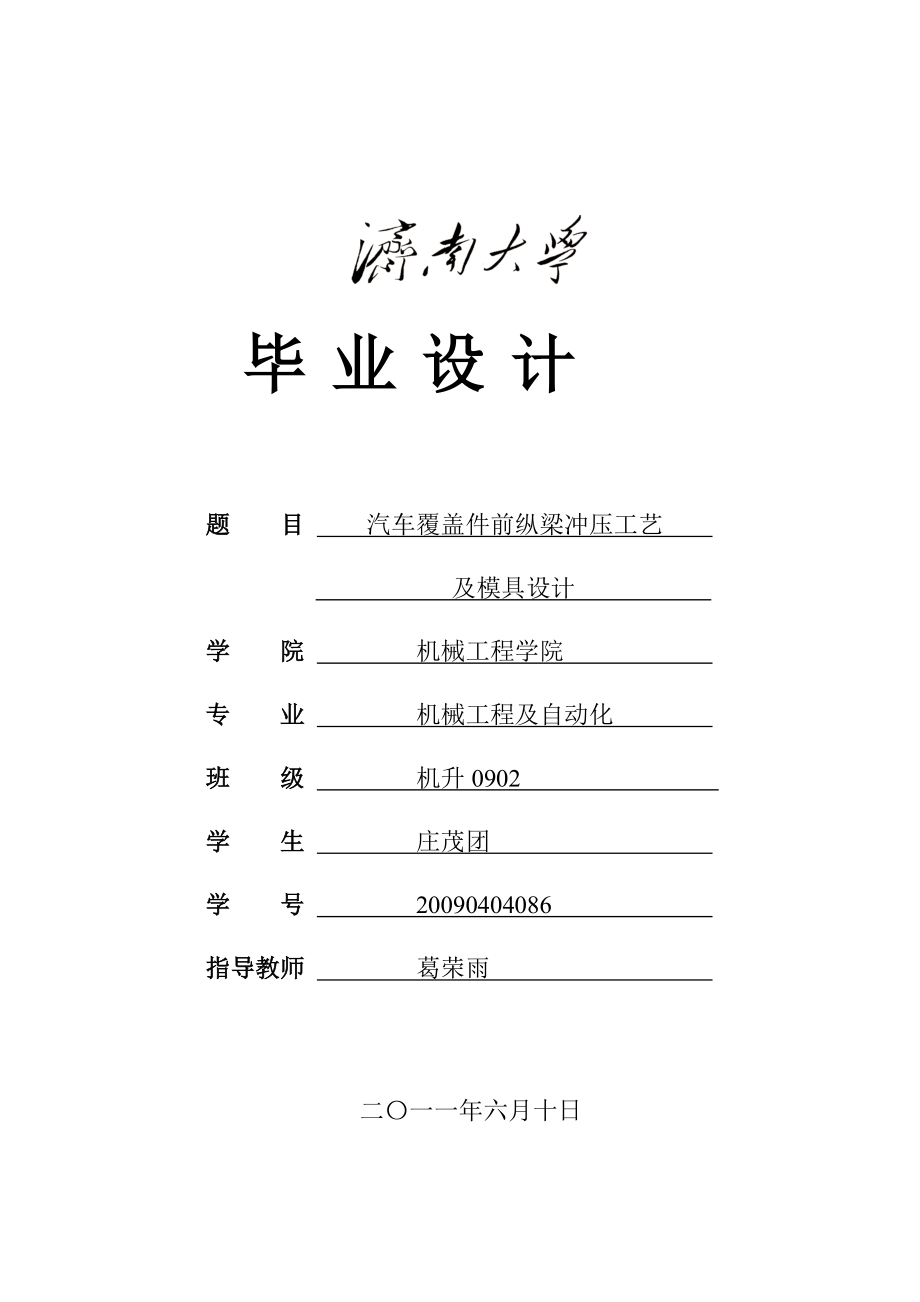


《0404086庄茂团汽车覆盖件前纵梁冲压工艺及模具设计》由会员分享,可在线阅读,更多相关《0404086庄茂团汽车覆盖件前纵梁冲压工艺及模具设计(38页珍藏版)》请在装配图网上搜索。
1、济南大学毕业设计毕业设计题 目 汽车覆盖件前纵梁冲压工艺 及模具设计 学 院 机械工程学院 专 业 机械工程及自动化 班 级 机升0902 学 生 庄茂团 学 号 20090404086 指导教师 葛荣雨 二一一年六月十日- 1 -济南大学毕业设计前言本课题主要研究汽车覆盖件前纵梁冲压工艺及模具设计,课题来源于韩国现代汽车集团子公司威亚汽车模具(山东)有限公司。课题要求通过对零件结构的分析、制定出合理的冲压工艺方案,通过分析比较几种可能的方案,选择合理的方案设计出相应的模具,并进行相关的工艺设计计算,使之具有实用性、经济性和自动化方面的要求。 课题内容主要包括:冲压工艺规程的制定,装配图和零件
2、图的绘制,以及确定合理的冲压工艺。1 概论1.1 课题内容、来源及意义本课题是关于汽车覆盖件前纵梁的冲压工艺及模具设计(工件图如图1.1),课题来自于威亚汽车模具(山东)有限公司。所用材料为SPRC440,厚度为1.6mm。课题要求通过对零件结构的分析、制定出合理的冲压工艺方案,通过分析比较几种可能的方案,选择合理的方案设计出相应的模具,并进行相关的工艺设计计算,使之具有实用性、经济性和自动化方面的要求。此次汽车覆盖件前纵梁冲压工艺及模具设计有助我们进一步学习和研究这方面的技术,使我们了解现代化工业的发展理念,用技术、经济统一的观点来分析解决实际问题的能力,培养我们创新精神和实践能力,更重要的
3、是通过对该零件的成形模设计,综合的运用在大学和公司所学的知识和方法,培养善于运用工程图纸、实验研究、计算机技能、以及书面和口头表达工程技术的能力同时也训练我们查阅应用中外科技文献,检验我们的工程素质,提高我们的综合能力,为踏入工作岗位打下一定的基础。图1.1 现代汽车覆盖件 前纵梁1.2 国内外模具技术现状随着与国际接轨的脚步不断加快,市场竞争的日益加剧,模具制造技术现已成为衡量一个国家制造业水平高低的重要标志,并在很大程度上决定企业的生存空间。近年许多模具企业加大了用于技术进步的投资力度,将技术进步视为企业发展的重要动力。一些国内模具企业已普及了二维CAD,并陆续开始使用UG、Pro/Eng
4、ineer、I-DEAS、Euclid-IS等国际通用软件,个别厂家还引进了Moldflow、C-Flow、DYNAFORM、Optris和MAGMASOFT等CAE软件,并成功应用于冲压模的设计中。以汽车覆盖件模具为代表的大型冲压模具的制造技术已取得很大进步。我国已能生产部分轿车覆盖件模具。如东风汽车模具有限公司,已设计制造了富康轿车部分内覆盖件模具。一汽模具中心生产了捷达王轿车外覆盖件模具。轿车覆盖件模具,具有设计和制造难度大,质量和精度要求高的特点。可代表覆盖件模具的水平。在设计制造方法,手段上面已基本达到了国际水平,模具结构功能方面也接近国际水平,在轿车模具国产化进程中前进了一大步。但
5、在制造质量、精度、制造周期和成本方面,与国外相比还存在一定的差距。标志冲模技术先进水平的多工位级进模和多功能模具,是我国重点发展的精密模具品种。有代表性的是集机电一体化的铁芯精密自动叠片多功能模具,已达到国际水平。如南京长江机器制造厂的电机铁芯自动叠铆硬质合金多工位级进模具有自动冲切、叠压、铆合、计数、分组,转子铁芯扭斜,安全保护等功能,凹模采用拼块式,零备件可互换。常州宝马集团公司的步进电机定转子带双回叠片硬质合金级进模。具有转子冲片落料、旋转72再叠片,定子冲片落料、回转90再叠片、(以消除料厚误差)等功能。这两项模具精度达2m, 步距精度2-3m,双回转精度1,寿命达到1亿次以上,制造周
6、期5-6个月,而价格仅为同类进口模具的1/2-1/3,已达到国际先进水平,完全可以替代进口。其他如48、54、68条腿集成电路框架多工位级进模、电子枪硬质合金多工进级进模、别克轿车安全带座式工位级进模、空调器散热片多工位级进模,均达到国外同类产品水平。但总体上和国外多工位级进模相比,在制造精度、使用寿命、模具结构和功能上,仍存在一定差距。在一般冲模方面,浙江慈溪鸿达电面模具制造中心的铁芯片复合冲模 ,实现系列化、 标准化、专业化生产,质量稳定,模具费用较一般低30%-50%,交货周期7-20天,并备有现货供应。在适应市场经济方面迈出了可喜的一步。此外,许多研究机构和大专院校开展模具技术的研究和
7、开发。经过多年的努力,在模具CAD/CAE/CAM技术方面取得了显著进步;在提高模具质量和缩短模具设计制造周期等方面做出了贡献。例如,吉林大学汽车覆盖件成型技术所独立研制的汽车覆盖件冲压成型分析KMAS软件,华中理工大学模具技术国家重点实验室开发的注塑模、汽车覆盖件模具和级进模CAD/CAE/CAM软件,上海交通大学模具CAD国家工程研究中心开发的冷冲模和精冲研究中心开发的冷冲模和精冲模CAD软件等在国内模具行业拥有不少的用户。总之,模具加工技术明显的发展方向如下: 高速铣削技术的进一步发展及其推广应用;电火花加工技术的不断发展;快速原型制造和快速制模(RPM/RMT)技术将得到更快更好的发展
8、;超精加工、微细加工和复合加工;先进表面处理技术将进一步受到重视;模具研磨抛光将向复合化、自动化、 智能化方向发展;模具自动加工系统的研制和发展;模具CAM/DNC技术及软件的发展和推广应用;切削加工刀具的正确选用。虽然中国模具工业在过去十多年中取得了令人瞩目的发展,但许多方面与工业发达国家相比仍有较大的差距。例如,精密加工设备在模具加工设备中的比重比较低;CAD/CAE/CAM技术的普及率不高;许多先进的模具技术应用不够广泛等等,致使相当一部分大型、精密、复杂和长寿命模具依赖进口。1.3 现代模具工业发展趋势 随着汽车工业的迅速发展,新车型更新换代的速度不但加快,传统的覆盖件模具设计制造方法
9、已不能适应产品开发的要求。汽车覆盖件模具作为汽车车身生产的重要工艺装备,直接制约着汽车产品的质量和新车型的开发。覆盖件模具因其设计制造难度大、周期长而常常成为制约汽车生产的主要因素。通用的二维CAD系统无法满足模具设计的一些特殊要求。为了提高模具设计的技术水平、缩短模具设计周期,应用针对汽车覆盖件模具结构设计的CAD系统进行设计是十分必要的。1.4 汽车覆盖件简介 汽车覆盖件(以下简称覆盖件)是指构成汽车车身或驾驶室、覆盖发动机和底盘的薄金属板料制成的异形体表面和内部零件。轿车的车前板和车身、载重车的车前板和驾驶室等都是由覆盖件和一般冲压件构成的。覆盖件组装后构成了车身或驾驶室的全部外部和内部
10、形状,它既是外观装饰性的零件,又是封闭薄壳状的受力零件。覆盖件的制造是汽车车身制造的关键环节。1.4.1覆盖件的分类按功能和部位分类,可分为外部覆盖件、内部覆盖件和骨架类覆盖件三类。外部覆盖件和骨架类覆盖件的外观质量有特殊要求,内部覆盖件的形状往往更复杂。按工艺特征分类如下:(1)对称于一个平面的覆盖件。诸如发动机罩、前围板、后围板、散热器罩和水箱罩等。这类覆盖件又可分为深度浅呈凹形弯曲形状的、深度均匀形状比较复杂的、深度相差大形状复杂的和深度深的几种。(2)不对称的覆盖件。诸如车门的内、外板,翼子板,侧围板等。这类覆盖件又可分为深度浅度比较平坦的、深度均匀形状较复杂的和深度深的几种。(3)可
11、以成双冲压的覆盖件。所谓成双冲压既指左右件组成一个便于成型的封闭件,也指切开后变成两件的半封闭型的覆盖件。 (4)具有凸缘平面的覆盖件。如车门内板,其凸缘面可直接选作压料面。 (5)压弯成型的覆盖件。以上各类覆盖件的工艺方案各有不同,模具设计结构亦有很大差别。1.4.2 覆盖件的特点和要求同一般冲压件相比,覆盖件具有材料薄、形状复杂、结构尺寸大和表面质量要求高等特点。覆盖件的工艺设计、冲模结构设计和冲模制造工艺都具有特殊性。因此,在实践中常把覆盖件从一般冲压件中分离出来,作为一各特殊的类别加以研究和分析。 覆盖件的特点决定了它的特殊要求:(1)表面质量覆盖件表面上任何微小的缺陷都会在涂漆后引起
12、光线的漫反射而损坏外形的美观,因此覆盖件表面不允许有波纹、皱折、凹痕、擦伤、边缘拉痕和其他破坏表面美感的缺陷。覆盖件上的装饰棱线和筋条要求清晰、平滑、左右对称和过渡均匀,覆盖件之间的棱线衔接应吻合流畅,不允许参差不齐。总之覆盖件不仅要满足结构上的功能要求,更要满足表面装饰的美观要求。(2)尺寸形状覆盖件的形状多为空间立体曲面,其形状很难在覆盖件图上完整准确地表达出来,因此覆盖件的尺寸形状常常借助主模型来描述。主模型是覆盖件的主要制造依据,覆盖件图上标注出来的尺寸形状,其中包括立体曲面形状、各种孔的位置尺寸、形状过渡尺寸等,都应和主模型一致,图面上无法标注的尺寸要依赖主模型量取,从这个意义上看,
13、主模型是覆盖件图必要的补充。(3)刚性覆盖件拉延成型时,由于其塑性变形的不均匀性,往往会使某些部位刚性较差。刚性差的覆盖件受至振动后会产生空洞声,用这样零件装车,汽车在高速行驶时就会发生振动,造成覆盖件早期破坏,因此覆盖件的刚性要求不可忽视。检查覆盖件刚性的方法,一是敲打零件以分辨其不同部位声音的异同,另一是用手按看其是否发生松驰和鼓动现象。(4)工艺性覆盖件的结构形状和尺寸决定该件的工艺性。覆盖件的工艺性关键是拉延工艺性。覆盖件一般都采用一次成型法,为了创造一个良好的拉延条件,通常将翻边展开,窗口补满,再加添上工艺补充部分,构成一个拉延件。工艺补充是拉延件不可缺少的组成部分,它既是实现拉延的
14、条件,又是增加变形程度获得刚性零件 的必要补充。工艺补充的多少取决于覆盖件的形状和尺寸,也和材料的的性能有关,形状复杂的深拉延件,要使用08ZF钢板。工艺补充的多余料需要在以后工序中去除。拉延工序以后的工艺性,仅仅是确定工序次数和安排工序顺序的问题。工艺性好可以减少工序次数,进行必要的工序合并。审查后续工序的工艺性要注意定位基准的一致性或定位基准的转换,前道工序为后续工序创造必要的条件,后道工序要注意和前道工序衔接好。1.5 课题的重点和难点重点:冲压工艺规程的制定,装配图和零件图的绘制,以及确定合理的冲压工艺,尽量使工件在各个工序之间不翻转或少翻转。难点:此冲压件属汽车覆盖件,其具有空间自由
15、曲面的特点,曲面形状复杂,确定其落料展开图和确定冲压中心和冲压方向为其首要难点;其次,工艺补充部分的设计和拉延筋的布置及形状;再者,在拉延工序中的工件缺陷的防止,如拉裂和起皱的防止,以及防止缺陷的方法。2冲压工艺方案2.1 零件的工艺性分析2.1.1 零件结构分析产品零件为前纵梁冲压件。材料SPRC440冷轧钢板,厚度1.6mm,大批量生产。具体尺寸见产品零件图,工件图见图1.1。从拉延件的零件图可以看出,地板加强板基本上属于是一种矩形拉延件。该零件选用SPRC440冷轧钢板进行拉延是合宜的,因为SPRC440冷轧钢板具有很好强度,可以满足加强作用。由覆盖件拉延特点知,为了避免拉延缺陷(褶皱)
16、,应给毛坯设计工艺补充面。该零件的基本特点是工件尺寸较大(长866mm、宽432mm)、尺寸精度一般、材料强度较高。零件外形呈左右对称结构,有凹凸和其他形状突变,系典型的板料冲压件,可拉延成型。从零件的形状对其分析,虽然此拉延件整体形状复杂,但是拉延部分基本上规则,由于拉深深度很大,不可一次拉伸成型,需要后序整形工序。工件的主要变形属于不变薄拉深,材料流动量很大。2.1.2零件冲压工艺性分析(1)成形件的形状复杂但对称,其模具较易加工,工艺易实现。(2)拉延成形的变形程度大(最大拉伸高度为163mm),但是变形部分分布较均匀。(3)工件为汽车结构加强部件,外廓尺寸精度要求不是很高。 (4)工件
17、上的孔位较多(12个),主要用于汽车总装固定,所以孔位的位置精度要求较高。相应的模具设计与加工要保证其位置精度。(5)在冲压工艺中少不了拉延和成型等工艺,考虑到材料的各向异性,材料在各变型工序中难免会出现回弹、翘曲、起皱、变薄、划痕等问题,这就需要设计出合理的冲压工艺和正确的模具结构来控制其的发生,从而生产出合格的产品。2.2 工序方案的确定本零件可供选择的工艺方案有:(1) 落料拉延修边冲孔侧冲孔整形;(2) 落料拉延、冲孔修边整形;(3) 落料拉延修边冲孔整形。考虑到该零件的修边复杂性和冲孔的复杂性,修改后选定的工艺方案为:落料拉延修边冲孔整形冲孔侧修边翻孔冲孔。材料SPRC其, 最大延伸
18、率为32%,流动性能、塑性较差,基于这些特点分析上述方案的可行性。采用此工艺方案理由:(1)零件为梁类零件。在汽车覆盖件中属于成形难度大。(2)材料属于高强度钢板,是目前车身轻量化高强度化的发展前沿。属于新材料类型。突出特点:成型性差、反弹严重。需采取整形措施。(3)零件拉延成形深度深,局部产品R圆角过小,需要在拉延工程对产品进行修改,后工程采取整形手段进行修正。(4)后工程的冲压方向与第一工程冲压方向不能保持一致,需要旋转。(5)两端正常的垂直修边满足不了要求,需要采用侧修边。(6)产品中央有翻孔工序内容,需要翻孔工程完成。局部R值 过小翻孔一工序冲压方向修边工序此冲压方向不能满足要求图2.
19、1 冲压方向分析图2.2 第一工序拉延图2.3 第二工序修边冲孔图2.4 第三工序整形冲孔图2.5 第四工序侧修边翻孔2.3冲裁精度的确定冲裁件的尺寸精度,是指冲裁实际的尺寸与基本尺寸的差值,差值越小,则冲裁件的精度越高。引起零件尺寸产生误差的因素主要为凸、凹模的制造精度 ,冲裁后材料的弹性回复,以及操作的偶然因素(如定位不准、材料性能不稳等)。由于零件尺寸未注公差值,按国家标准非配合尺寸的IT14级处理,而模具的设计精度可以取IT12或IT13,此零件为支撑件,因此我们可以取精度为IT13。2.4拉延件的设计2.4.1拉延件的冲压方向拉深方向的确定原则是:覆盖件本身有对称面的,其拉深方向是以
20、垂直于对称面的轴进行旋转来确定的;不对称的覆盖件是绕汽车位置相互垂直的两个坐标面进行旋转来确定拉深方向的;拉深工序的冲压方向尽量和以后工序的冲压方向一致。此外,确定拉深方向必须考虑以下几方面的问题。(1)拉深凸模能否进入凹模拉深凸模在拉深终了时,应能进入拉深件成形所要求的每一个角落,不应出现凸模接触不到的死角和死区,这样才能够使拉深件成形。即拉深件的侧壁与拉深方向无负角现象(图2.6中的角)。按图2.6(a)的冲压方向,凸模无法进入凹模,拉深成为不可能。按图2.6(b)的冲压方向,凸模能顺利进入凹模,且进入拉深件的所有角落,所以是可行的拉深方向。图2.6 拉深凸模必须能够顺利进入凹模(2)拉深
21、深度应均匀拉深效果的好坏,进料阻力各向相等是重要因素。若想进料阻力相等,拉深深度均匀又是必要条件。在确认拉深凸模能顺利进入凹模之后,首先要考虑的是拉深深度应均匀。图2.7所示的是两种拉深方向产生的拉深深度。(a)不均匀 (b) 均匀图2.7 拉深深度程度的比较(3)拉入角相等拉深进行过程中,应尽量做到凸模相对两侧的拉入角相等。使材料进入凹模速度趋于相等,达到理想的变形条件。(4)凸模开始与毛坯接触状态要平稳应尽量做到接触的部位在中间,接触面积要大,接触点要多。只有这样才能保证拉深时毛坯不窜动,拉深过程稳定(如图2.8)。图2.8 凸模开始拉深时与拉深毛坯的接触状态示意图(5)工艺补充部分少工艺
22、补充是拉深件不可缺少的部分,好的拉深工序设计,应当是在最少的材料消耗下,拉深出合格的拉深件。基于以上条件和零件的形状结构,选择冲压方向图2.1所示的冲压方向。2.4.2压料面的确定压料面各部位的进料阻力不一样,在拉深过程中毛坯有可能经凸模顶部窜动影响表面质量,严重的会产生拉裂和起皱。应使压料面两端一样高,则进料阻力均匀,凸模开始拉深时与拉深毛坯的接触部位接近中心,拉深成形好。要使压料面各部位的进料阻力均匀,除了通过设计合理的压料面形状和拉深筋等措施外,拉延深度要均匀是主要条件。还要使凸模对应两侧的材料的拉入角尽量相等。此外,确定压料面形状必须考虑以下几点:(1)降低拉深深度降低拉延深度,有利于
23、防皱防裂。如果压料面就是覆盖件本身的一部分时,不存在降低拉延深度的问题。如果压料面是由工艺补充部分补充而成,必要时就要考虑降低拉延深度的问题。(2)凸模对毛坯一定要有拉伸作用这是确定压料面形状必须充分考虑的一个重要因素。只有使毛坯各部分在拉深过程中处于拉伸状态,并能均匀地紧贴凸模,才能避免起皱。2.4.3工艺补充部分设计为了实现覆盖件的拉深,需要将覆盖件的孔、开口、压料面等结构根据拉深工序的要求进行工艺处理,这样的处理称为工艺补充。 工艺补充是拉深件不可缺少的部分,工艺补充部分在拉深完成后要将其修切掉,过多的工艺补充将增加材料的消耗。因此,应在满足拉深条件下,尽量减少工艺补充部分,以提高材料的
24、利用率。由零件结构分析,此零件工艺补充后属于带凸缘的盒形件拉深,因此修边线的选择应该在盒形件拉深的底部、垂直修边,且修边线距拉深筋的距离应有一定数值。综上所叙压料面尺寸沿周边80mm,拉延筋沿周边12mm;工艺补充部分在深拉伸处各工艺补充60mm,浅拉伸处补充30mm。2.4.4拉延筋的设置 拉延筋设置在压料面上,通过不同数量、不同位置、不同的结构尺寸以及拉深筋与槽之间松紧的改变,以调节压料面上各部位的阻力,控制材料流入,减慢进料速度,削弱压应力,提高制件的刚度,防止拉深时起皱和开裂。 敷设拉延筋的原则是:(1)拉深深度浅的应敷设为增加刚性的拉深筋或拉深槛;(2)为使进料阻力均衡,在直线部分敷
25、设拉深筋或拉深槛;(3)为克服起皱,应在凸曲线敷设较宽的拉深筋;(4)拉深筋或拉深槛尽量靠近凹模圆角,但不能影响修边模的强度;(5)在同一位置应尽量布置一条拉深筋,必要时才增至两条或三条。综上分析零件的成型结构和工艺补充后的形状,拉延部分变形较大,所以必须设置拉延筋。同时考虑到工件材料(SPRC440)拉延性能较差,拉延形状类似盒形,故压料筋在直边处设有,在圆角边不设有。在零件的四个直边处各设有一条拉延筋。压料筋距离凸模外轮廓尺寸沿凸模外轮廓形状不变,尺寸大小决定于凹模圆角大小和压料圈强度,一般取3035mm(考虑到零件的结构,本例中取20mm)。压料筋相互之间的尺寸沿压料筋形状不变,一般取2
26、830mm(本套模具取只取一条拉延筋)。如果压料面就是覆盖件本身的凸缘面时,则压料筋距凸模外轮廓尺寸等于压料筋距修边线尺寸和修边线距凸模外轮廓尺寸之和。压料筋之间的尺寸同样取2830mm。压料筋突出高度在图样上为4mm,实际上第一根压料筋往外的压料筋高度是依次递减的。压料筋的宽度A有12mm,16mm两种,根据拉延件的大小决定,一般取宽度为16mm (本套模具采用的是12mm)。3 应用CAD/CAE提高冲压工艺水平3.1 CAD应用3.1.1 CAD设计介绍自20世纪80年代以来,计算机辅助设计技术(CAD)已得到了广泛的应用,并且得到了快速的发展,在模具设计、制造中也显示了巨大的优越性。
27、CAD设计的优势在于:能够直观反映设计的真实状态,通过运动模拟、干涉检查等数字化分析手段,在设计阶段就能避免以往在生产制造中才能发现的问题。标准件库可为模具结构设计提供可以直接装配的参数化、系列化的零件;冲压设备库、典型结构库为结构设计提供了可参考的模型;而基础结构库使模具设计更加灵活、智能。资源库与知识工程的有机结合,形成了模具结构设计的知识库,成为三维实体设计的基础。与3D-DL图技术、实体泡沫加工技术的结合,达到真正意义上的三维实体设计。并以此为契机,带动整个模具生命周期的技术提升。实现模具制造的CAE/CAD/CAM一体化,使模具生产越来越依赖于高科技手段,最大限度地降低人工劳动的强度
28、,提高模具的制造精度,缩短模具生产周期。3.1.2 CAD软件介绍AutoCAD(Auto Computer Aided Design)是美国Autodesk公司首次于1982年生产的自动计算机辅助设计软件,用于二维绘图、详细绘制、设计文档和基本三维设计。现已经成为国际上广为流行的绘图工具。.dwg文件格式成为二维绘图的事实标准格式。Pro/Engineer 是美国PTC公司的产品,于1988年问世。10多年来,经历20余次的改版,已成为全世界及中国地区最普及的3D CAD/CAM系统的标准软件,广泛应用于电子、机械、模具、工业设计、汽车、航天、家电、玩具等行业。 Pro/E是全方位的3D产品
29、开发软件包,和相关软件Pro/DESINGER(造型设计)、Pro/MECHANICA(功能仿真),集合了零件设计、产品装配、模具开发、加工制造、钣金件设计、铸造件设计、工业设计、逆向工程、自动测量、机构分析、有限元分析、产品数据库管理等功能,从而使用户缩短了产品开发的时间并简化了开发的流程;国际上有27000多企业采用了PRO/ENGINEER软件系统,作为企业的标准软件进行产品设计。Pro/E独树一帜的软件功能直接影响了我们工作中的设计、制造方法。与其他同类三维软件(MDT、UG、CATIA等)相比,Proe/ENGINEER的不同之处在于以下几点:(1)基于特征的(Feature-Bas
30、ed)Pro/ENGINEER是一个基于特征的(Feature-Based)实体模型建模工具,利用每次个别建构区块的方式构建模型。设计者根据每个加工过程,在模型上构建一个单独特征。特征是最小的建构区块,若以简单的特征建构模型,在修改模型时,更有弹性。(2)关联的(Associative)通过创建零件、装配、绘图等方式,可利用Proe/ENGINEER验证模型。由于各功能模块之间是相互关联的,如果改变装配中的某一零件,系统将会自动地在该装配中的其他零件与绘图上反映该变化。(3)参数化(Parametric)Pro/ENGINEER为一参数化系统,即特征之间存在相互关系,使得某一特征的修改会同时牵
31、动其他特征的变更,以满足设计者的要求。如果 某一特征参考到其他特征时,特征之间即产生父/子(parent/child)关系。(4)构造曲面(surface)复杂曲面的生成主要有三种方法:1)由外部的点集,生成三维曲线,再利用Pro/E下surface的功能生成曲面。2)直接输入由Pro/desinger(造型设计)产生的曲面。3)利用import(输入)功能,以IGES、 SET、VDA、Neutral等格式,输入由其他软件或三维测量仪产生的曲面(5)在装配图中构建实体根据已建好的实体模型,在装配(component)中,利用其特征(平面,曲面或轴线)为基准,直接构建(Create)新的实体模
32、型。这样建立的模型便于装配,在系统默认(default)状态下,完成装配。3.1.3 CAD在本设计中的应用基于CAD软件的优势,本设计采用Auto CAD绘制二维图。图3.1 凹模平面图图3.2 压边圈平面图三维实体图的绘制采用Pro/Engineer。另外冲压分析时应用了 Catia V5,在实体图的演示方面采用了Product View。图3.3 凸模立体图3.2 CAE应用3.2.1 CAE分析介绍成型CAE在模具设计中的应用,实际上是对模具设计方案进行评估优化的过程。在板料设计中合理应用CAE技术,可以避免和减少传统模具设计方法产生的浪费、失误甚至报废,有效提高模具开发的效率,降低开
33、发成本。CAE在汽车钣金零件设计中的应用由于汽车覆盖件形状及其成形过程的多样性和复杂性,多数情况下成形工序与工艺参数要通过多次试验才能确定。加工过程的控制、模具的设计和制造都直接影响产品的质量和价格。加工过程不当或模具形状不合适很容易出现成形件破裂、起皱或其他成形缺陷。为了避免这类情况的发生,通常需要修改成形工序和工艺参数或修改模具形状。随着工业化的日益发展,产品更新换代周期越来越短,传统的设计方法已经明显不适应现代工业的发展要求。汽车企业为了缩短开发周期,提高新产品开发的综合效益,大量采用计算机辅助技术来设计和模拟分析车身覆盖件,从而大大缩短了车身覆盖件的开发周期。3.2.2 CAE软件介绍
34、本文运用的AutoForm是一款由瑞士开发的专业薄板成形快速模拟软件,可以用于薄板、拼焊板的冲压成形、液压胀形等过程的模拟,配合不同的功能模块,还可以进行冲压件单步法成形模拟以及拉深工序工艺补充面的设计。3.2.3 CAE应用介绍1冲压方向的确定传统冲压方向的确定有很大的局限性,对一些复杂冲压件冲压方向的确定显得束手无策(传统工艺确定冲压方向可操作性不强),往往有些形状复杂的冲压件因为冲压方向确定的不合理出现调试不出合格件的情况。传统工艺确定;中压方向的方法如下。(1)保证凸模能够顺利进入凹模。(2)使凸模接触毛坯的面积大。(3)压料面各部分进料阻力要均匀可靠。而运用CAE分析可以根据冲压件的
35、几何形状快速确定最佳冲压方向、有无冲压负角以及最浅拉深深度。如图3.4,可以根据冲压件的工艺编排情况来确定最佳的冲压方向。Average normal:平均法向 Min draw depth:最小拉深深度Min backdraft:最小负角 Screen axes:目视方向图 3.4 冲压方向分析确定对于一些复杂冲压件的冲压方向确定亦可以根据经验手动调整冲压方向,便于材料流动同时车身坐标系与冲压坐标系的转换亦能轻松实现。2 毛坯尺寸的估算 优化以及排样的优化(1)毛坯尺寸的估算对于一些冲压件可根据成形方式(拉深、压弯等)来反求毛坯尺寸,使用不同的约束条件将得到不同的毛坯尺寸(Onestep)。
36、(2)迭代法优化坯料尺寸反求出的毛坯尺寸可能不够精确使用A u t o fo r m优化(Optimization)模块,反复求解得出最接近结果的真值(迭代的次数越多,其结果越接近真值,但所需计算时间越长)。(3)优化排样提高材料利用率,传统排样方式,材料利用率为80 ,而优化排样(如图3.5)为经过CAE软件优化过的排样利用率有所高。图3.5 优化排样(4)CAE分析结果对模具设计的优化 拉延筋的布置及宽度使用优化模块可以对拉延筋的布置、宽度进行优化选择合理的拉延筋形状对材料流动的约束,达到材料充分拉伸的目的。(排版)图3.6 优化前后的拉延结果由图3.6看出,更改拉延筋后(增大拉延筋的约束
37、力)的拉深情况远好于更改前的。这样,模具调试周期被大大缩短,调试成本也相应减少。CAE分析结果可以为工艺准备前期提供有力的保证传统工艺方法对压床的选用局限于简单压弯件(可计算压弯力、冲裁力),对于复杂冲压件的压床的选用只能根据经验采取类比的方法,而根据CAE软件可迅速反求的凸凹模及压料圈在成型过程中所需要的力然后根据所需压力选用合适的压力机,避免出现设备浪费或者压力不足的情况。3 总结(1)要以现实冲压条件为基础,掌握实际冲压条件的数学描述方法。否则,CAE分析只能成为理论分析,不能应用于实际生产。要准确描述实际冲压条件,需要进行大量的调查分析。(2)CAE分析与经验学习积累同等重要。如在欧美
38、多数采用仿真设计,但在日本模具设计师通常更多依靠经验来设计模具。经验的重要性体现在:在板料成形CAE分析的预处理过程中,好的工艺辅助面及拉延筋可以快速达到预期的目的;在后处理分析发现成形缺陷时无论通过什么方法来改善,都需要有丰富的经验。(3)CAE分析必须与零件及模具的CAD,CAM并行交互。CAE分析是为零件及模具的设计和工艺参数优化等服务的,不能将CAE分析孤立,而应该更多地渗入零件及模具的设计、工艺设计,及早地改善模具设计,优化工艺参数,甚至改进零件设计,才能缩短开发周期,降低开发成本。图3.7 Auto form 分析结果显示说明3.2.4 应用CAE分析制件的成形问题及提出解决方法
39、FLC曲线外侧应变失效点主要为产品尖角撕裂区图3.8 成形限制极限图图3.9 产品成形性评估分析结果该区域产品形状有过渡变薄及撕裂趋势可以通过调整模具R圆角和板材大小压边力大小来改变 该区域产品延伸不足可以通过调整模具圆角和压边力大小改变图3.10 产品最终分析结果局部详细示图3.2.5 分析报告该产品在冲压工艺分析过程中,考虑到工艺补充部分圆角小,在调试中更改此区圆角;另外板料尺寸需按实际情况调整。其中,上图图示红色区域为过渡变薄区域,调试时应注意控制板料变薄率,变化范围应在20%以内。4 工艺计算及主要参数确定4.1 毛坯尺寸的确定 依据工艺数模得该件最大拉深距离为170mm。毛坯尺寸可以
40、根据制件展平后的轮廓尺寸和压料尺寸来确定。其毛坯尺寸确定计算为:第一部分:工件轮廓尺寸 最大长度1160mm,最大宽度256mm;第二部分:压料尺寸 压料面沿周边80mm 拉延筋沿周边12mm; 第三部分:工艺补充部分 深拉伸处各工艺补充60mm,浅拉伸处补充30mm;其总面积为:1300396=5148000mm2 。 在实在实际生产中为了便于取料,将毛坯尺寸确定为1300mm400mm材料的利用率:=制件面积/毛坯面积100%=296960mm2/520000mm2=57.1%4.2 计算拉深工序的力压边力必须适当,如果压边力过大,会增加拉入凹模的拉力,使危险断面拉裂;如果压边力不足,则不
41、能防止凸缘起皱。压边力为压边面积乘单位压边力即=Ap (4.2.1) 式中 压边力 ,N;A在压边圈下毛坯的投影面积 ,mm;p单位压边力,MPa。在材料为SPRC440的情况下,其单位压边力在2.53.0取3.0,在压边圈下的投影面积为A=302744mm2 故压边力由式(4.2.1)得PQ=3027443.0=908232N对于横截面为矩形的拉深件拉深力(4.2.2) 式中 拉深力,N ;L危险断面周长,mm;利用软件分析L=2860mm; t工件坯料厚度,mm ;t=1.6mm; p危险断面上的单位拉深力,MPa ;SPRC440的抗拉强度为280390Mpa,取300Mpa. =286
42、01.6300=1287000N。总的拉深力P为拉深所需要的力和压料所需要的力,即=908232+128700=2195232 N2.2 KN4.3 修边力、卸料力、推件力及顶件力的计算 计算冲裁力的目的是为了合理选用压力设备和模具设计,压力机的吨位必须大于冲裁力,才适应冲裁要求。(1)冲裁力 (4.3.1)式中 冲裁力(N);L 冲裁件的周长(mm) ;t 材料的厚度(mm) ; 材料的抗剪强度(MPa),SPRC440的抗剪强度为220310 MPa,取310 MPa。但考虑到凸凹模刃口的磨损,模具间隙的波动,材料的力学性能的变化和材料厚度偏差等因素,实际需要的冲裁力还需增加30%,即F=
43、1.3 F0 (4.3.2)=31031.5310=1442895 NF=1.31442895=18757631.88 KN(2)切刃侧压力 (4.3.3) =0.63 KN(3)卸料力 (4.3.4) 其中,K卸料力系数,查表4.1取0.05; =0.051.88=0.094 KN(4)推件力 (4.3.5) 其中 n=h/t,n同时卡在凹模内的零件或废料数; h圆柱形凹模的腔口高度(mm); t料厚(mm); K卸料力系数,查表4.1,K=0.055。 由设计知,h=6mm,则n=4, =40.0551.88 =0.42 KN(5)顶件力 (4.3.6) 其中,K顶件力系数,查表4.1,K
44、取0.06; 修边的冲裁力(N); =0.061.23 =0.074 KN(6)冲裁总的冲压力 (4.3.7) =(1.88+0.63+0.094+0.42+0.074) KN =3.098 KN3.1KN表4.1 卸料力、推件力及顶件力系数料厚(mm)K推K顶K卸052.50.0550.060.040.054.4 冲压设备的选择 4.4.1 拉延工序冲压设备的选择压力机的选择应根据工作台面尺(左右前后)1810mm1320mm,闭合高度850mm, 总的拉深力F=2.2 KN来选择。实际生产中,可按下式估算压力机的公称压力F0,浅拉深:F0(1.61.8)F总 (4.4.1) F0=2.21
45、.6=3.52KN经过计算压力机的公称压力要大于352吨,则选择J36800B闭式双点单动压力机。 则必须满足最大装模高度模具的最大高度即 990850满足要求。表4.2 J36800B闭式双点单动压力机技术参数序号名称数值单位1公称压力800吨2最大装模高度990毫米3滑块行程500毫米4最小装模高度450毫米6滑块速度空程下行80毫米7滑块行程次数10次/分8工作台板尺寸(前后左右)18004000毫米9电机总功率90千瓦4.4.2 修边冲孔工序冲压设备的选择压力机的选择应根据工作台面尺(左右前后)1500mm1130mm,闭合高度950mm, 总的冲压力F=3.1KN来选择。实际生产中,
46、可按下式估算压力机的公称压力F0,F0(1.61.8)F总 F0=3.11.6=4.96KN经过计算压力机的公称压力要大于500吨,则选择YA32630液压四柱压力机。 则必须满足最大开口高度与模具闭合高度之差小于液压机的滑块行程 即 1700-950 F; 拉深所需要的总的冲压力为F=2.2KN,J36800B闭式双点单动压力机的公称压力为Fg=8.0KN,故Fg F,满足要求。(2) 压力机的装模高度必须符合模具闭合高度的要求,即: Hmax - 5mm Hm Hmin + 10mm ; 式中 Hmax、Hmin分别为压力机的最大、最小装模高度(mm);Hm模具闭合高度(mm);所选压力机
47、的最大装模高度990mm,最小装模高度450mm,模具闭合高度850mm,所以:990-5850450+10,满足要求。(3) 压力机的滑块行程必须满足冲压件的成形要求。对于拉深工艺,为了便于放料和取料,其行程必须大于拉深件高度的22.5倍;压力机的滑块行程为500mm,拉延件的最大高度为140mm,所以500140(2-2.5),满足要求。(4) 为了便于安装模具,压力机的工作台面尺寸应大于模具尺寸,一般每边大5070mm,台面上的孔应保证冲压件或废料能漏下。压力机台面尺寸,前后为1800m,左右为4000mm,拉延模的最大宽度1350mm,最大长度1810mm,符合要求。综上所述,J368
48、00B闭式双点单动压力机的选择符合冲压要求。5 模具结构设计5.1 拉延模结构5.1.1 拉延模结构种类拉深模结构可分为:按使用的压力机不同,可分为单动压力机上使用的拉深模与双动压力机上使用的拉深模;按工序的组合程度不同,可分为单工序拉深模、复合工序拉深模与级进工序拉深模;按结构形式与使用要求的不同,可分为首次拉深模与以后各次拉深模、有压料装置拉深模与无压料装置拉深模、顺装式拉深模与倒装式拉深模、下出件拉深模与上出件拉深模。5.1.2 拉延模结构的确定形状简单、深度浅的覆盖件一般采用单动压力机来成型;形状复杂、深度深的覆盖件必须采用双动压力机成型。这是因为单动压力机的压料力是靠机床下面的油缸的
49、压力和行程都比双动压力机小得多,其不能提供较大压料力和复杂深拉延件所需的成形力。其次,单动压力机所用拉延模的压边圈比较薄,刚性相对弱,亦不能适应复杂深拉延件的成型。分析后地板加强板的形状结构,可知该拉延件属于浅拉延,拉延件形状相对简单,因此确定该拉延模采用单动压力机上使用的拉延模。单动拉延模结构比较简单,主要由三大件(凸模、凹模和压料圈)组成。这种拉延模呈倒装形式,凸模与压料圈、凹模与凸模之间分别装有倒向装置,模具外轮廓尺寸和闭合高度必须严格适应压力机参数要求。根据所采用的模具形式,此拉延模的凸模、凹模、压料圈都采用实型铸造而成,为方便安装,节约材料在不影响刚度和强度的条件下对非重要部分进行挖
50、空。并且在影响强度和刚度的部位设计加强筋。模具铸件的壁厚与模具的尺寸大小、零件生产批量、以及受力情况都有很大的关系,该制件是批量生产,该模具是中型模具。参照汽车模具标准设计凸模、凹模结构尺寸。其它小零件尽量选用标准件。确定凸模和凹模工作部分尺寸时,应考虑模具的磨损和拉延件的弹复。依据拉延件三维数模尺寸来确定凸模和凹模工作部分尺寸。其相关尺寸见凸模和凹模零件图。综上所述,拉延模设计如图5.2。表5.1 大批量生产时拉延模铸件壁厚(单位:mm)模具大小ABCDEFG中小型40503545354535453545455530大型7095608050654565506540503040435211.凹
51、模 2.压边圈 3.凸模 4.顶杆 5.导滑板 图4.2 拉延模结构图5.1.3 凸、凹模结构 (1)凸、凹模圆角凸、凹模的结构设计得是否合理,直接影响拉延时坯料金属流动性。凹模圆角半径R凹越大,材料越易进入凹模;但R凹过大,材料易起皱。因此,在材料不起皱的前提下,R凹=(68)t 式中 t板料厚度(mm);但当凹模圆角处于工艺补充部分上,根据常用板料厚度,取中间值(68)t。当压料面是制件本身凸缘的一部分时,则凹模圆角半径就是拉延件要求的圆角半径。如果拉延件要求圆角半径过小,影响拉延变形时,则适当加大到合适数值,用后续的工序整形圆角也能达到要求数值。根据所给数模标准,测量R凹=5mm。凸模圆
52、角半径R凸过小,会使坯料在此受到过大的弯曲变形,导致危险断面材料严重变薄甚至拉裂;R凸过大,会使坯料悬空部分增大,容易产生“内起皱”现象。一般R凸R凹,取R凸=(0.71.0)R凹,但根据所给数模,R凸=8mm。拉延凸模的圆角半径即拉延件的内轮廓圆角半径,尺寸和拉延件圆角半径要求的尺寸相同。(2)凸、凹模间隙拉延凸、凹模间隙的大小,对拉延力、制件质量和模具寿命都有影响。间隙过大,容易起皱;过小,则拉延件壁变薄加重,甚至拉断。在此拉延过程中,凸模与凹模之间的间隙,直边部分取z=t=1.5mm,在圆角部分由于材料复原,故其间隙应比直边部分间隙大0.1t,即z=t+0.1t=1.65mm。(t为零件
53、厚度)凸模和凹模工作部分尺寸应该根据拉延件的尺寸来确定,在确定凸模和凹模工作部分尺寸时,应考虑模具的磨损和拉延件的弹复。5.1.4压边圈设计压边圈的质量决定拉延过程中的压料效果,它既要有一定的压料力,还要使压料区的材料在不起皱的情况下,顺利的流入凹模口内。本次设计的压料面上有8个上导挡料板定位毛坯方便送料,上导挡料板选用汽模标准QM31152002。8个小凸台安装平衡块其作用是调整进料阻力,通过调整压料圈与凹模之间的间隙来实现。平衡块选用标准件,查标准QM16232002。该模具是中型模具,选用直径为60mm,高度为20mm的平衡块。5.1.5导向装置根据工艺方法的不同,模具对导向精度和导向刚
54、度的要求也不同,模具的导向形式也不同。常用的导向方式有导柱导套导向、导板导向、导块导向及背靠块导向等四种基本形式。由于此件属于中型件的拉延采用导滑板导向,此结构相对简单、造价低。需要导向的有上模板(凹模)和下模板(凸模)的导向及压边圈的导向。以上模板上的导滑平台为基准,在下模板和压料圈上安装导滑板。根据模具的实际结构和拉延深度,查标准QM1301-2002,上模板和下模板选用C100100的导板8个,下模板与压边圈选用C100125的导板8个。5.1.6 卸料装置由相对拉延毛坯外形均匀分布的8根顶杆在液压缸的驱动下推动压边圈,使压边圈向上运动,完成凸模的卸料,在凹模座内,分布2个卸料顶销,完成
55、凹模的卸料。这样就可以提高自动化生产程度,模具运行也较稳定从而延长了设备的寿命,保证了工件质量也有利于减小噪音。 6 模具制造、操作及维护要点由于模具的制造成本比较高,所以在模具制造、操作及维护中都要求用科学的方法去选择制造模具的材料和制造模具的合理科学的工艺过程。这样可以使得模具的寿命延长,减少零件的制造成本。对模具材料的要求是必须要有足够的硬度和耐磨性,模具工作部分材料的硬度,经过热处理后必须高于材料的2倍以上。因此,冲压模具工作部分的硬度一般要求达到HRC54以上。凸、凹模在使用一段时间以后,有时可以明显的看出其磨损现象,例如:冲裁凸模和凹模刃口变钝、棱角变圆、在刃口附近的平面或规则曲面
56、因磨损变成凹面或凸面和不规则曲面;在拉深凹模或冲裁凸、凹模的工作表面上出现粘接瘤和剥落坑等。这些现象的大多数是因黏着磨损造成,少数为磨粒磨损,表面疲劳磨损和腐蚀磨损较少。所以在选择材料时,应当重点从降低粘着磨损的角度去考虑。模具在使用中因磨损而使工作部分尺寸发生变化,影响冲压件质量,所以要求模具材料有良好的耐磨性,以保证模具的寿命。模具的耐磨性和模具材料的硬度及炭化物的种类、数量、形状、分布等有关。对模具材料的要求必须满足一定的强度和韧性,模具在工作的时候,往往受到很大的冲击,所以要求模具材料有足够的强度和韧性。此外,还要求模具要有良好的加工工艺性能。6.1 提高模具使用寿命的途径(1) 合理
57、的设计模具,在设计模具时,主要应考虑选取合适的间隙值,保证足够的刚度,注意凸模的外形设计,采用导向装置,降低模具表面粗糙度,适当选取模具硬度等。(2) 正确选用模具材料和采用新材料,传统的选用Cr12。(3) 保证热处理的质量。(4) 保证加工质量和采用新的加工方法。6.2 模具在制造过程中的要求(1) 所有的、安装在模具上的圆柱销必须易于拆卸,为了达到这样的要求,可以在模具中提供拆卸孔或者使用带螺纹孔的圆柱销。(2) 在不易装拆的零件上,打出两个螺纹孔。这样在装拆零件的时候可以避免许多麻烦。(3) 对大型机加工零件提供起重孔和加工用的固定孔。(4) 对模具零部件打印出件号、材料的牌号。(5)
58、 对模具零部件或铸件的尖角进行倒角处理。这样可消除尖角出的铸造应力。(6) 对模具敞开的压料板、退料板弹簧和气路装置的周围,提供保护装置。(7) 冲孔用的冲头使用后拔除,将孔堵上并修整到不影响制件质量。6.3 模具安装使用维护说明(1) 检查压床是否工作正常(2) 开出压床工作台,将托杆按模具铭牌上注明的位置放入工作台托杆孔内。(3) 将快速定位销按照模具上铭牌注明的位置放入工作台托杆孔内。(4) 将模具按照定位销或键槽位置吊放在工作台面上。(5) 工作台开入压床到位,滑块用点动和微调方式逐渐接触上底板。(6) 将上底板用压床螺钉紧固,下底板压板螺钉先不拧紧。(7) 开动滑块,取出存放限制器放好,滑块上下导正三次后,将下底板压板螺钉紧固。(8) 闭合高度调到距限制器1mm处。模具气路系统接通气源。(9) 按铭牌要求调整压床气垫压力。(10) 将板料放入模具内连续冲压三件,检查合格后批量生产。(11) 保证废料滑出畅通无阻并定时清理废料盒中废料。(12) 一个批次生产完之后检查模具状态并清理杂物,表面涂防锈油,放好存放限制器入库保存。(13) 所有易损件、导柱或滑块表面应定期涂润滑油或润滑脂。7 结 论本课题对汽车前纵梁冲压工艺作了全面
- 温馨提示:
1: 本站所有资源如无特殊说明,都需要本地电脑安装OFFICE2007和PDF阅读器。图纸软件为CAD,CAXA,PROE,UG,SolidWorks等.压缩文件请下载最新的WinRAR软件解压。
2: 本站的文档不包含任何第三方提供的附件图纸等,如果需要附件,请联系上传者。文件的所有权益归上传用户所有。
3.本站RAR压缩包中若带图纸,网页内容里面会有图纸预览,若没有图纸预览就没有图纸。
4. 未经权益所有人同意不得将文件中的内容挪作商业或盈利用途。
5. 装配图网仅提供信息存储空间,仅对用户上传内容的表现方式做保护处理,对用户上传分享的文档内容本身不做任何修改或编辑,并不能对任何下载内容负责。
6. 下载文件中如有侵权或不适当内容,请与我们联系,我们立即纠正。
7. 本站不保证下载资源的准确性、安全性和完整性, 同时也不承担用户因使用这些下载资源对自己和他人造成任何形式的伤害或损失。