提高延迟焦化装置负荷率研究报告2
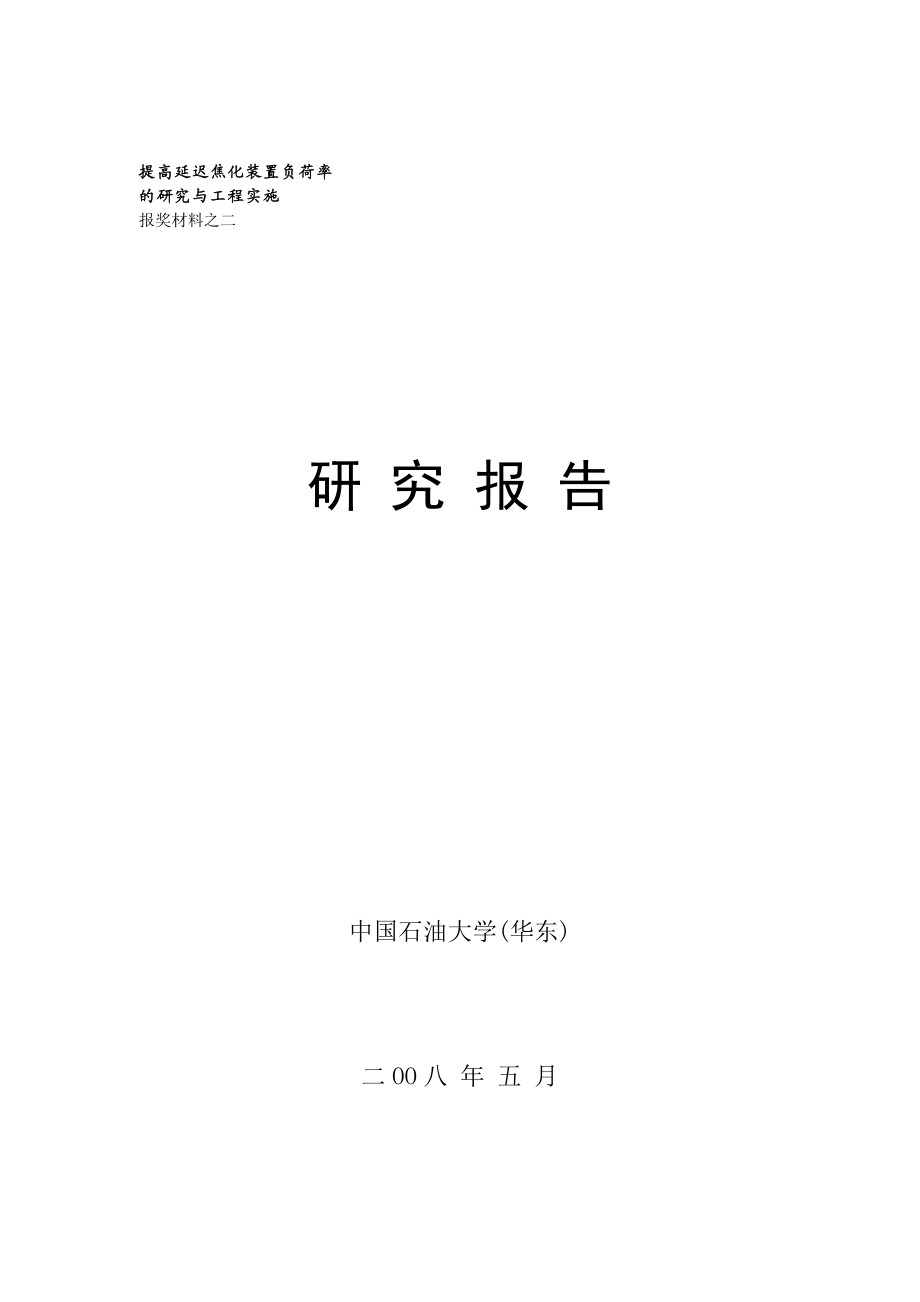


《提高延迟焦化装置负荷率研究报告2》由会员分享,可在线阅读,更多相关《提高延迟焦化装置负荷率研究报告2(23页珍藏版)》请在装配图网上搜索。
1、提高延迟焦化装置负荷率的研究与工程实施. 研究报告 第 -22- 页提高延迟焦化装置负荷率的研究与工程实施报奖材料之二研 究 报 告中国石油大学(华东) 二OO八 年 五 月1. 研 究 背 景沧州炼厂延迟焦化装置是1999年投产的、采用上个世纪八十年代设计理念建造的设计产能为50万吨/年、一炉两塔结构的延迟焦化装置。改造前,装置加工能力为50万吨,焦化炉与焦炭塔为装置提高处理装置能力的瓶颈所在,焦炭产率系数(装置焦炭产率/原料康式残炭)在1.61.7之间、操作周期大约为8个月左右。延迟焦化工艺特点具有半间歇半连续操作特性,原料在焦化加热炉管内获得重油轻质化所需要的能量,然后在焦炭塔内完成生焦
2、反应。焦化炉需要在控制炉管结焦速率的同时,尽量提高焦化炉对生焦反应的给热量,以确保生焦反应完全彻底,降低装置的焦炭产率。本项研究的目的有二:一是消除焦化炉与焦炭塔对提量操作的瓶颈制约,二是在生焦周期缩短原料劣质化的同时,尽量提供较多的生焦反应给热量以降低装置焦炭产率。由于理论上减少炉管结焦与降低焦炭产率目标相互矛盾,缩短生焦周期与减少炉管结焦有利的操作方案,可能导致焦炭塔内生焦反应不完全,焦炭中低挥发分增多进而影响液体产物收率,因而提高延迟焦化装置负荷率的研究与工程实施必须以控制炉管结焦为基础。本项研究焦炭塔采用20小时生焦周期以减少焦粉携带;在满足装置长周期运行的生产要求前提下,对焦化炉进行
3、局部改造与优化操作,在消除焦化炉的瓶颈制约的同时提高生焦反应给热,利用现有装置每年加工处理65万吨的减压渣油,避免减压渣油直接出厂而导致经济损失,科研组所作的工作,可分为基础研究、配套设备动改措施论证、优化操作方案制定三大部分,本报告将分类加以总结。2. 主要研究工作2.1 相关基础研究为了便于掌握提高延迟焦化装置负荷率研究的实质,本节将与项目有关的基础工作做一简要介绍。图-1 炉管结焦关联式对特例焦化炉结焦厚度的预测(8000小时,初开工、中期及结束状态)2.1.1炉管结焦机理 1炉管结焦机理研究是从事提高延迟焦化装置负荷率研究的基础。炉管结焦速率与装置操作、加热炉结构及原料物性都有关系,焦
4、化炉炉管结焦速率等于结焦前体物生成速率与脱落速率之差:炉管结焦速率焦炭生成速率焦炭脱落速率 (1)由特定动态实验得到结焦速率关联常数后,对特例焦化炉典型工况下结焦厚度沿炉管的变化进行理论推算,结果1参见图1。该项内容获得了中石化1999年度科技进步二等奖。2.1.2“最大可裂化度”与“正常延迟状态” 概念利用高压射流清洗机高压水的冲击力将粘附在管壁上的焦层剥离,用特制金图-2 特例炉实测焦厚分布属编织袋将冲击出来的焦炭截流,用溶剂油和甲苯除掉粘附在焦炭上的油分,用水标定出焦炭的密度,假定同一根炉管上焦层均匀分布,将焦层重量值转换成炉焦厚度,利用变形蜡块得到炉管管焦的周向分布,3个特例炉管管焦沿
5、炉管分布工业数据2参见图2,工业数据炉管结焦厚度变化趋势与理论推算结果吻合,证明了结焦前体物附壁之前存在脱落;但由于炉管管焦层系操作周期内累积形成,操作周期内很难保证操作平稳,非正常及误操作状态限制了结焦速率关联式的实际应用。在裂解深度较低时,实验中检测不到结焦前体物的生成,结焦前体物产率为零;但当裂解深度增加到结焦前体物出现后,结焦母体产率随裂解深度增加而急速增加,裂解深度与结焦母体产率曲线明显存在一个加速拐点的现象;造成这种现象的原因可能是:重油的裂化反应为自由基反应历程,反应开始裂解深度较低时,反应过程产生的自由基被重油胶质所“笼蔽”,阻碍了自由基之间的进一步叠合,这时自由基如同漂浮在空
6、中的云里水汽,并不能相互凝结成雨滴;一旦裂解深度增加,进而导致自由基浓度增加后,重油胶质的“笼蔽”效应被破坏,自由基之间的叠合就无障碍,结焦母体产率随裂解深度增加激增。定义导致“笼蔽”效应被破坏的最小裂解深度为介质的“最大可裂化度”。焦化炉老的设计规范源于1965年埃索研究工程公司制定的设计准则(五),工艺上只对炉管表面热强度和冷油流速进行校核,设计时要求炉管表面热强度在3238kW/m2之间;冷油流速的范围为12001800kg/m2s。尽管利用这种方法完成了多套焦化炉的常规设计与操作,但这种方法由于没有体现炉管结焦速率与结构、操作及物性之间的相互关系,不能用于提高延迟焦化装置负荷率研究3,
7、为确保焦化炉管不发生严重结焦,我们在提高延迟焦化装置负荷率研究时用:最高油膜温度; 管内两相流流型;焦化炉炉出口裂解深度。三参数,作为判断焦化炉管内介质流动及反应过程是否处于“正常延迟状态”的依据,尤其要将关键炉管管内两相流流型控制为喷雾流、炉出口实际裂解转化深度控制在介质的最大可裂化度之内4。2.1.3生焦反应焦化炉给热概念及提高生焦反应给热量的方法图-3反应温度对重油热转化产品的影响 重油在焦炭塔内的生焦反应是一个裂解(吸热)与缩合(放热)反应同时进行的综合过程,总体表现为吸热,反应所需要的热量全部来自于焦化炉,焦化炉给热量越大,反应越彻底,装置焦炭产率越低。图3是反应时间为1小时,不同反
8、应温度下特例重油热转化反应主要产品收率的实验数据,表明将焦炭塔内泡沫层温度控制在460上下是必要的。加热炉内燃料燃烧放出的热量与管内介质吸热量之间的关系可用下式表示: (2)式中: QF 燃料燃烧放出的热量,kWQ1 燃料及空气带进的显热,kWQ2 烟气带走的热量,kWQL 炉体散热损失,kWQ 管内介质的吸热量,kW介质吸收的热量,一部分用于升温和汽化,另一部分用于焦化炉管内的热裂解反应: (3)式中: QT 介质升温所需要的热量,kWQE 介质汽化所需要的热量,kWQR 介质反应所需要的热量,kW图-4 不同装置焦炭产率系数及生焦反应给热比图-5缩合与裂解反应速率之比与反应温度之间的关系过
9、去炉管内介质反应所需要的热量往往被忽略。实际上,尽管介质在管内停留时间不长,热转化深度不高,但反应所需要的热量在总吸热量中占有相当的分量。生焦反应焦化炉给热量详细计算方法参见文献5,不同装置生焦反应给热与装置焦炭产率系数(装置焦炭产率与原料康式残炭之比)参见图4,表明提高生焦反应焦化炉给热量是必要的。不同重油缩合与裂解反应速率之比与反应温度的对应关系参见图5,由于缩合反应活化能比裂解大,当反应温度增加后,缩合反应速率激增,因而仅靠提高炉出口温度而提高生焦反应给热量不仅会使最高油膜温度增加,也加深了焦化原料的二次反应,进而导致装置干气产率上升液收下降。详细内容参见文献6:基于“生焦反应给热”及“
10、正常延迟状态”概念,在出口温度不变时延长停留时间,可以提高炉出口重油热转化深度及焦化炉生焦反应给热量。2.1.4焦化炉方案制定系统软件开发与完善生焦反应给热及炉出口裂解深度不能直接检测,如何通过炉出口温度及注汽量得到生焦反应给热及控制炉管结焦的关键工艺参数,必须通过焦化炉管内外过程模拟才能得到;焦化炉管内外工艺过程极为复杂包括燃料燃烧、高温烟气湍流流动及辐射传热、重油热转化反应及结焦、两相流流动等过程,操作方案制定必须借助专门的计算工具。2.1.4.1简明理论基础实验表明,大多数重油当温度超过430即会发生剧烈的裂解与缩合反应,焦化炉出口温度一般在500,重油在管内发生裂解与缩合反应是不可避免
11、的。定义炉出口裂解气及轻油产率为操作裂化度,显然,操作裂化度是介质在管内每个截面反应的累计结果,可以用下式表达: (4)式中, Xo 炉出口重油的操作裂化度Xi 每个小微元段介质的热转化率炉管内各个截面的温度、压力、组成都不相同,计算停留时间时同样需要将炉管分段,假定每段内油品的流速不变。介质在管内的停留时间为各微元段停留时间i之和: (5)式中 ,Li 为第I段炉管的长度,m;Ui 为第I段炉管内的流速,m/s; 可用下式计算: (6)式中, H2Okgs 管内注汽量,kg/s; Wkgs 管内介质流量,kg/s;H2O 注水的汽相密度,kg/m3 eW 管内介质的平衡气化率 ,m%;L 管
12、内介质的液相密度 ,kg/m3;V 管内介质的汽相密度 , kg/m3。微元段重油的eW、L、V均与微元段的温度T、压力P及组成Zi有关: (7)任意截面组成Zi与入口处Z0i之间的关系可用下式表示: (8)式中Xi为I组分的热转化率,与重油的反应过程有关,由必须开发相应的产物分布模型来确定。2.1.4.2 技术支撑及软件功能完善图-6 修正后的加热炉管式反应模型 重油热裂解产物分布模型详细内容参见文献7,结合国外大陆油公司发表的管式反应模型与国内实际情况,中国石油大学重质油加工国家重点实验室开发的模型参见图6;详细细节参见文献8 ,中国石油大学重质油加工国家重点实验室开发模型的实验考察主要结
13、果参见表1;利用特定装置对不同产地重油进行模拟实验【9】,得到的12集总重油热裂解产物分布模型模型常数数据参见表2。表1热烈解产物分布模型模拟值与动态实验结果之间的对比项 目实 验 1实 验 2实 验 3实验值模拟值实验值模拟值实验值模拟值裂解气样重(g)12.3/9.6/5.3/裂解油样重(g)7272.5/6446.6/3113.4/产气率(m%,下同)0.16880.1780.14890.1300.16990.112总热转化率4.28 2.862.73802.0832.0001.808出口210馏分收率0.1600.250.2650.1830.1250.158出口210-330馏分收率2
14、.380.8280.4820.6030.1190.518出口330-510馏分收率14.3413.9814.5913.6114.3313.47表-2 11种原料混合后关联结果项目活化能与气体常数之比E/R相关系数RF检验实验值R95%R99%R实验F值99%F总裂解28517.150.940.150.211144.836.80缩合34744.090.65121.46瓦斯气23295.500.90697.67汽油35134.750.68141.54柴油26734.610.951484.55蜡油26949.060.941139.5521035134.750.68141.5424026704.470
15、.92910.5427026960.920.941256.1430027591.710.93997.3133027813.830.92834.1936027867.580.89610.3139027906.460.88548.6642028459.770.87511.5845028113.070.84380.5848026448.320.78245.8951024746.570.72178.49焦化炉炉管结焦是导致操作后期炉管管壁温度上升的根本原因。炉管管焦导热系数是焦化炉设计及焦化炉管内外过程模拟所必须的重要基础数据,由于炉管结焦是一个缓慢的过程,得到现场管焦试件十分困难,公开文献上无法找到
16、炉管管焦的导热系数及随温度变化数据。详细细节参见文献9,我们利用直接测量法,完成了炉管管焦导热系数的测定,实验表明,当温度为100550范围时,随着温度的升高,管焦导热系数降低的速度逐渐减缓并最终稳定在3.8 W/m,实验误差不超过10%。所得到的管焦导热系数随温度变化回归方程,最大相对误差不超过4%。为了考察不同管外传热模型对关键工艺参数的影响,工作中10扩充了原开发的模拟软件管外部分,包括了罗伯伊万斯、别洛康半经验半理论传热模型及Monte Carlo方法三个模块,考察了不同管外传热模型对管内停留时间、炉出口热转化率和油膜温度等工艺参数的影响,提出了对操作工况关键工艺参数的极限变化区间进行
17、判断的思路。由于双面辐射加热流程与原单面辐射不同,辐射进料直接进对流室,工作中我们采用三级定位技术11,开发了一个使用方便、界面友好的可用于多股物流、不同炉管形式及排列方式的对流室通用传热校核软件,软件可自动完成节点和计算段的划分,提供各计算段管内外介质出口温度、热负荷、压降、抽力及最低管壁温度等关键数据,主要计算结果与TDChTH 计算结果接近。由于对流室底部几根炉管既有对流又有辐射传热,提出同时考虑烟气辐射与对流计算遮蔽段总传热系数的方法(c-k法),利用现场收集到的4套不同加热炉结构及操作数据,由传热速率方程和热平衡方程联立求解得出遮蔽段总传热系数K值,并与c-k法及传统计算方法进行了对
18、比,结果表明c-k法计算误差小于传统计算方法,进行遮蔽段传热计算时错流温差校正系数可近似按1处理。基于以校核管内停留时间、炉出口热转化率和油膜温度三参数影响炉管结焦速率为核心的计算方法,用Visual Basic编辑了一个复杂的计算软件,出口热转化率模拟结果通过了动态实验考核,炉膛温度、入口压力等模拟结果同现场标定及操作统计进行了对比,并在中华人民共和国国家版权局进行了计算机软件著作权登记(软件名称:焦化炉管内外过程模拟软件V1.0,著作权人:石油大学(华东),中国石油化工股份有限公司,登记号为2004SR00414);软件在焦化炉大型化设计、现场操作诊断分析方面都发挥了重要作用。2.1.5结
19、焦因子概念图-7 不同油样不同条件下修正结焦因子在从事提高延迟焦化装置负荷率研究时,搞清焦化原料的结焦倾向是必要的。过去对重油结焦倾向的评价主要基于渣油四组成、20密度、粘度、残炭值、分子量、硫含量、氮含量、H/C原子比以及渣油的特征参数KH等综合物性参数的分析,参照重油的成焦机理我们提出在相同反应条件下,在实验室内快速得到不同油样结焦因子(结焦前体物生成量)的变化,作为评价原料结焦倾向的方法,与传统方法相比一方面理论上最为直接,另一方面考虑了胶质、金属含量等对结焦倾向的贡献,不同油样不同条件下结焦因子,参见图-7,该项内容获得了中石化2006年度科技进步二等奖。2.2 设备动改部分减少炉管结
20、焦与降低焦炭产率目标是相互矛盾的:从减少炉管结焦的角度,应采取低炉出口温度与大注汽量操作,但这种方式会降低生焦反应焦化炉给热量,进而导致焦炭塔内生焦反应不完全,焦炭中低挥发分增多,严重影响液体产物收率;从降低焦炭产率的角度,应采取高炉出口温度与小注汽量操作,但这种方式会导致炉出口热转化深度、炉管表面热强度及油膜峰值温度增加,可能造成炉管严重结焦。为达到提高延迟焦化装置负荷率的同时确保装置轻油收率、延长操作周期并节约燃料消耗,对装置进行了必要的设备改造。由于焦化炉是装置的核心单元设备,对每一项设备动改措施进行了详细的技术论证。2.2.1 底部增设辐射炉管12图-9 增加两个炉管炉管布置示意 参见
21、图9,为了降低焦化炉炉管表面热强度、增加介质行程长度、充分利用单面辐射炉辐射室有效空间、消除装置消除瓶颈制约,对底部空间排布炉管进行了论证,在特例焦化炉增设了22根辐射炉管:针对底部布管可能引起倒传热及热强度过大的疑虑,利用自编软件和CFX对辐射室内温度场及流场进行了详细模拟分析;现场测定了特例焦化炉底部烟气温度;利用现场管内介质实测温升数据,对底部布管的传热效果了进行标定。2.2.2特殊结构的中间桥墙13图-10 一般单面辐射焦化炉炉型及中间桥墙示意为了提高低温段炉管表面热强度、减少两排火嘴之间的相互干扰、降低不正常操作时火焰舔管,参见示意图10,利用自编软件对不同桥墙高度和桥墙形式对热强度
22、分布的影响进行了模拟计算,提出了特殊结构的中间桥墙,操作中发现,增设桥墙后,炉膛温度明显下降,解决了特例焦化炉多年炉管氧化曝皮的问题。2.2.3 辐射增敷注水炉管14注水量虽然不大,仅占原料量的12%,但由于水的汽化潜热比较大,当注水以液态注入油管汽化后,可使350以上油温下降1015,进而使焦化炉有效负荷增大,增加了炉管表面热强度,不利于提高装置负荷。为了降低烟气入空气预热器温度、提高加热炉热效率,参见图-11,对辐射室进行了改造,在靠近火焰附近增敷了62,有效的降低炉膛温度。图-11 靠近火焰附近增敷了62 降低炉膛温度2.2.4下进上出加热方式15 参见示意图12,辐射进料过去一般从辐射
23、室顶部进入辐射室,由于热强度大极易舔管部位刚好是结焦速率最大的地方,往往造成炉管氧化曝皮,严重时经常导致生产事故,因而国内不少厂家采用一种“下进中出”的加热方式,利用图12焦化炉辐射进料的三种不同的加热方式CFX得到的不同加热方式下辐射室热强度分布,为了降低焦化炉出口压力、减少装置停电对结焦的影响,我们提出了下进上出的加热方式,1999年我们完成了下进上出加热方式的专利申请,2001年美国人以同样内容申请了专利。2.2.5 两点注汽方式图13对流布管方式我国延迟焦化操作的明显特点是注汽量大,使介质在管内停留时间偏短、炉出口介质实际裂解深度偏低进而导致生焦反应焦化炉给热量少、焦炭塔内生焦反应未能
24、彻底完成:注汽量虽然只占焦化进料量的百分之几,但由于水的分子量小及水在辐射管内密度低,注汽量的细微变化对重油在管内的停留时间及热转化深度影响甚大,根据结焦机理,炉出口实际裂解深度低于最大可裂化度时,增加注汽只是降低了流动边界层的厚度;理论上,只要介质在管内的停留时间不是太长,炉出口热转化深度不超过最大可裂化度,边界底层中形成的结焦母体能扩散到流动主体之中,炉管中的结焦速率就不至于过快,因而合理的注汽应使炉出口热转化深度不高于最大可裂化度,但也不能太低使炉出口介质热转化深度太低导致焦炭塔内温降过大。参见图13,将辐射室注水管作为第1点注汽汽源,第2点注汽汽源热量从对流室顶部烟气中获得。2.2.6
25、 换热网络优化沧州炼化焦化装置原料渣油150进装置,经换热器换热后终温为233。为了提高渣油换后终温,参见图14添加一台蜡油渣油换热器,引入中段油热量,可使渣油换后终温可达到260。191210259227256渣油15075 t/h12 t/h32537525t/h50 t/h296柴油换热器中段油换热器蜡油换热器图14 改造后的原料换热流程图 上述设备改造措施除换热网络优化未落实外,其他全部现场实施,炉出口反应深度、生焦反应给热量、反应行程长度等关键工艺参数的都发生了变化,详细细节参见下文装置优化操作部分。2.3 优化操作部分由于控制炉管结焦的关键工艺参数与生焦反应给热量现场都不能直接检测
26、,现场难以检测到产品分布的变化,必须对操作方案结果进行理论剖析,对理论推论进行现场标定验证。2.3.1注汽对焦化炉出口温度影响的工业实验16图15 注汽降量前后生焦反应焦化炉给热模拟结果为了搞清注汽量及出口温度变化对生焦反应给热及装置产品分布的影响,在某装置停工前我们进行了半个月的工业装置实验,在燃料量不变的条件下,考察了注汽量减少后对原料进出口温度、炉膛温度、管内压降、焦化炉热效率、富气组成、装置产品分布的影响,并用过程模拟软件对操作结果进行了详细的剖析。注汽量降低后,生焦反应焦化炉给热参见图15,装置产品分布变化参见表3。表3 介质在管内停留时间对产品分布影响工业实验结果焦 化 装 置 生
27、 产 日 报焦化车间2005年8月19日单位:吨序号项目名称当日产量 当日收率累计产量累计收率1焦化原料116402384102回炼油53098403焦化脱后干气524.4710494.44焦化脱后液化气211.83751.575焦化汽油14412.37299012.546焦化柴油43937.71856435.927焦化蜡油22319.16425817.868焦 炭19416.67【注】436218.39焦化甩油151.296712.8110焦化循环油655.5813505.6611焦化轻污油000012燃料油000013酸性气40.34770.3214损 失70.61450.6115轻质油5
28、8350.091155448.4616总液收88676.121783374.817焦炭出库1844579备注调整注汽焦炭产率下降1.63制表: 都梅芳2.3.2多点注汽对生焦反应给热影响的过程模拟17我国延迟焦化装置普遍存在焦炭产率过高的问题,焦炭产率系数大约为1.61.8,工作中对我国主要焦化装置进行了现场调研,对不同装置焦化炉原料处理量、辐射与对流油的进出口温度与压力、焦炭塔塔顶温度、注汽量与注汽温度等 80余万个关键工艺参数操作记录进行了统计分析18。基于典型操作与操作统计数据,利用前期开发的过程模拟软件,对两焦化炉的操作进行了剖析,结论是:通过同时控制炉出口温度及注汽量可以改变生焦给热
29、:采用多点注汽时,增加第二点注汽比例,将第二点注汽位置后移均有利于提高生焦反应焦化炉给热。 2.3.3 研究对象改造前后的关键工艺参数变化 19焦化炉改造后处理能力可达67万吨/年(状态值),辐射进料管内停留时间为108.5114.3s,焦化炉改造前辐射进料管内停留时间为71. 5s;改造后430以上停留时间为52.954.7s,焦化炉改造前430以上停留时间为33.96,与同类装置的对比情况参见图16;改造后管内裂化转化率为11.53612.132%,焦化炉改造前管内裂化转化率为8.069%,与同类装置的对比情况参见图17:改造后430以上停留时间高于所收集装置,为确保一炉两塔装置操作操作安
30、全,通过采用多点注汽与出口温度优化,出口裂解深度控制在在役炉上限附近但不超过上限。图16 改造后焦化炉430以上停留时间 图17 改造后焦化炉管内裂化转化率改造后炉膛温度为740800,焦化炉改造前炉膛温度为740790;改造后炉管平均热强度为30.87831.499kW/m2,焦化炉改造前炉管平均热强度为23.076kW/m2,与同类装置的对比情况参见图18,改造后接近旧的操作规范上限,高于收集到在役单面辐射炉管表面热强度。劣质渣油在高热强度下仍能保证长周期运行:管外特殊结构的中间桥墙避免了火嘴间的相互干扰,限制了火焰舔管;改造后最大表观流速为40.60742.288m/s,焦化炉改造前最大
31、表观流速为39.394 m/s;改造后出口汽化分率为49.62549.755%,焦化炉改造前出口汽化分率为48.521,确保了管内关键炉管为喷雾流型;多点注汽作用不能忽略。图18改造后焦化炉平均热强度图19改造后生焦反应焦化炉给热图-20 标油消耗对比生焦反应焦化炉给热为385.71397.36 kJ/kg,与同类装置的对比情况参见图19,焦化炉改造前生焦反应焦化炉给热为343.52 kJ/kg;燃料消耗为30.1133.94kgEo/T渣油(理论值),与同类装置的对比情况参见图20,焦化炉改造前燃料消耗为28.81 kgEo/T渣油(理论值);标油消耗高但生焦反应给热低的原因是由于经费原因换
32、热网络优化设计提高换后终温的措施未有实施。改造后反应行程长度为414.06417.66m,焦化炉改造前反应行程长度为388.85m,与同类装置的对比情况参见图21。改造后介质总吸热为7806.847963.91 kW,焦化炉改造前介质总吸热为5569.13kW;改造后生焦反应总给热/介质总吸热为65.3165.88%,焦化炉改造前生焦反应总给热/介质总吸热为64.25%,与同类装置的对比情况参见图22;改造后炉内反应总吸热/介质总吸热为20.8321.01,焦化炉改造前炉内反应总吸热/介质总吸热为16.21%。提高生焦反应给热品质仍有空间。图21不同焦化炉反应行程长度图22 生焦反应总给热/介
33、质总吸热2.3.4 缩短生焦周期消除焦炭塔瓶颈20装置为一炉两塔型,操作弹性较小,为此制定了20小时生焦周期表,在规定时间内达到装置生产需要,各个环节相辅相成,联系紧密,确保装置平稳运行。 焦炭塔操作时间老塔处理:小吹汽:时间1.5hr,流量1-1.5T/h 大吹汽:时间2hr,流量10T/h,达到顶温365 小给水:时间1hr,流量20T/h ,根据焦炭塔顶压力随时调节。 大给水:时间4hr,流量20-245 T/h,根据焦炭塔顶压力随时调节。 放水:时间1.5hr。总共时间:10 hr,每步时间可在10 hr范围内稍做调节。除焦、试压、蒸汽预热时间5 hr。新塔准备:时间5 hr引油气:0
34、.5-1 hr 油气循环:4-4.5 hr(油气循环1小时内,循环量应700Nm3/h, 1小时后至最大量) 严格焦炭塔阻泡剂加注控制在延迟焦化反应过程中,随着焦床的升高,泡沫层极易发生携带使大量焦粉随着高温油气一道进入分馏塔,其中绝大部分将沉积于分馏塔底部,进而进入辐射炉管,只有很少一部分进入侧线产品中,根据结焦机理,聚集于塔底及炉管中的焦粉,作为结焦的晶核,在高温条件下将加剧分馏塔底及炉管结焦,严重威胁着装置的长周期平稳运行.为此需向焦炭塔顶加注消泡剂.消泡剂的物理性质:外观:无色或淡黄色液体,活性物质含量45%密度:25 0.83g/cm3粘度:2050mpa.s闪点(开口) 70加注流
35、程桶装消泡剂 加药剂泵 消泡剂罐 柱塞式计量泵焦炭塔顶 加注量:相对于焦炭塔内总进料量(即辐射进料量)本消泡剂的加注量为80ppm加注方法:将桶装破乳剂170公斤通过加药剂泵加入到消泡剂罐中,然后用4倍的柴油进行稀释,控制溶液加入量36kg/h消泡剂的作用效果:抑制泡沫层的增长,每塔加剂时间基本为6小时。3. 总 结本项目属于石油炼制领域,项目开发成功一种提高延迟焦化装置负荷率延长装置操作周期并降低装置焦炭产率的综合技术。主要内容包括:焦化炉采用下进上出流程;辐射室中间桥墙增设倒梯型中间桥墙;焦化加热炉炉底增加四根炉管;采用多点注汽;充分利用辐射室空间,在辐射室底部靠近火嘴增加注水加热炉管;
36、调整对流辐射取热比例;生焦周期缩短到20小时;实现常压与焦化装置热联合;加强辐射线和转油线的保温延迟焦化虽然是项老技术,但由于渣油组成及影响炉管结焦的因素复杂,过去仅将焦化炉作为加热设备而未考虑其管内的热转化与缩合反应以及对渣油在焦炭塔生焦反应的影响,现场仅以控制炉出口温度作为唯一参数,本项技术基于反应结果受反应温度及停留时间共同影响的原理,通过设备改造及现场优化操作,对升温过程及出口温度都进行了优化设计与控制,强化了低温段的炉管传热能力,增加了反应段行程长度与停留时间,降低了管内压降,汽化点前移强化了管内传热,在同样炉出口温度下达到了增加油品生焦反应焦化炉给热量的目的并降低了炉管结焦速率,进
37、而达到了生焦周期缩短与原料劣质化的同时,提高了装置负荷与降低装置焦炭产率的目的。在沧州炼化公司的应用结果表明,本项技术投资低,能消除焦化炉的瓶颈制约、减缓炉管结焦延长装置操作周期,并在生焦周期缩短与原料劣质化的同时,降低装置焦炭产率:2006年 完成改造后设计产能为50万吨/年的焦化炉消除瓶颈制约,产能达到65万吨/年,装置负荷率达到设计产能的130为国内装置负荷率之首;炉膛温度小于780,炉管壁温最高点小于650,烧焦周期到达1年以上,实现了装置长周期运行;装置焦炭产率系数为1.391.53(装置焦炭产率2526,原料残炭1718),焦炭产率系数比中石化系统平均水平低0.10.24,综合技术
38、经济指标达到国际先进水平。本项技术的应用为沧州炼化公司减压渣油的平衡加工利用发挥了重要作用,不计减少焦炭产率及延长操作周期带来的效益,加工1吨减压渣油获利按300元/吨计,仅减少渣油出厂一项,年创效益就达4500 万元。延迟焦化装置普遍面临提负荷增加加工量的需求,随着焦化原料越来越重与焦炭塔缩短生焦周期操作,本项技术具有重要社会效益,有广阔的推广应用前景。主要参考文献1 Xiao etc:STUDY ON CORRELATIVE METHODS FOR DESCRIBING COKING RATE IN FURNACE TUBESPETROLEUM SCIENCE AND TECHNOLOGY
39、18 (3&4),305-318(2000)2 石油大学延迟焦化科研组:“焦化炉炉管结焦量的采集与分析” ,技术报告,第1章 第1节3 肖家治等:“焦化炉工艺校核方法的研究” 炼油设计2001年第10 期4 石油大学延迟焦化科研组:“重油热转化反应规律的研究” ,技术报告,第1章 第2节5 楼艰炯等:“提高焦化炉生焦反应给热方法的研究”,石油大学学报 vol.27 No.6(2003)6 张承甲等:“双面辐射炉注汽量及炉出口温度的优化设计”,齐鲁石油化工,Vol.31,No.1(2003)7 肖家治等:“12集总重油热解反应产物分布模型的开发”,石油大学学报(自),2001年第 5 期8 王兰
40、娟等:“用动态实验考核重油热裂解产物分布模型”, 石油大学报(自),2002年第 1 期9 肖家治等:“焦化炉炉管管焦导热系数的测定”,石油大学学报(自),2001年第 4 期10 王兰娟等:“传热模型对焦化炉关键校核参数影响的研究”,石油化工设备技术,2002年第 2 期11 肖家治等:“遮蔽段总传热系数的计算”, 石油大学报(自),2004年第 1 期12 石油大学延迟焦化科研组:“辐射室底部敷设炉管的研究” ,技术报告,第2章 第1节13 石油大学延迟焦化科研组:“辐射室桥墙的优化设计与单一条件模拟” ,技术报告,第2章 第2节14 石油大学延迟焦化科研组:“注水状态对焦化炉操作的影响” ,技术报告,第2章 第3节15 石油大学延迟焦化科研组:“焦化炉管外热强度分布与加热流程安排的研究” ,技术报告,第2章 第4节16 石油大学延迟焦化科研组:“注汽对焦化炉出口温度的影响”,技术报告,第3章,第1节17 石油大学延迟焦化科研组:“多点注汽对生焦反应给热的影响”,技术报告,第3章,第2节18 石油大学延迟焦化科研组:“典型装置焦化炉操作状况剖析”,技术报告,第3章,第3节19 石油大学延迟焦化科研组:“焦化炉改造前后关键工艺参数变化”,技术报告,第3章,第4节20 沧州炼油三部:“20小时生焦周期工作方案制定”,技术报告,第3章,第5节
- 温馨提示:
1: 本站所有资源如无特殊说明,都需要本地电脑安装OFFICE2007和PDF阅读器。图纸软件为CAD,CAXA,PROE,UG,SolidWorks等.压缩文件请下载最新的WinRAR软件解压。
2: 本站的文档不包含任何第三方提供的附件图纸等,如果需要附件,请联系上传者。文件的所有权益归上传用户所有。
3.本站RAR压缩包中若带图纸,网页内容里面会有图纸预览,若没有图纸预览就没有图纸。
4. 未经权益所有人同意不得将文件中的内容挪作商业或盈利用途。
5. 装配图网仅提供信息存储空间,仅对用户上传内容的表现方式做保护处理,对用户上传分享的文档内容本身不做任何修改或编辑,并不能对任何下载内容负责。
6. 下载文件中如有侵权或不适当内容,请与我们联系,我们立即纠正。
7. 本站不保证下载资源的准确性、安全性和完整性, 同时也不承担用户因使用这些下载资源对自己和他人造成任何形式的伤害或损失。