换刀机械手毕业论文
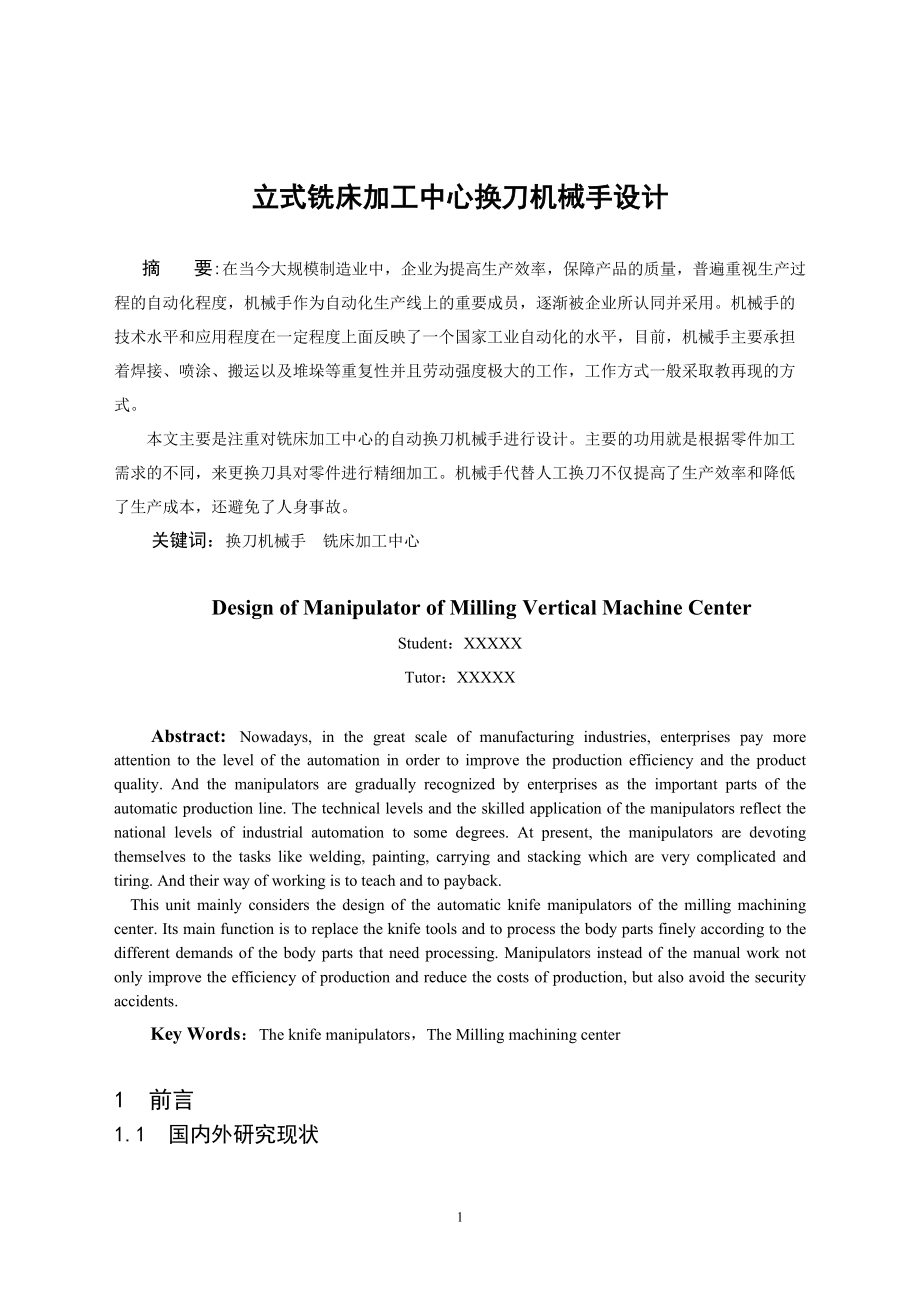


《换刀机械手毕业论文》由会员分享,可在线阅读,更多相关《换刀机械手毕业论文(29页珍藏版)》请在装配图网上搜索。
1、立式铣床加工中心换刀机械手设计 摘 要:在当今大规模制造业中,企业为提高生产效率,保障产品的质量,普遍重视生产过程的自动化程度,机械手作为自动化生产线上的重要成员,逐渐被企业所认同并采用。机械手的技术水平和应用程度在一定程度上面反映了一个国家工业自动化的水平,目前,机械手主要承担着焊接、喷涂、搬运以及堆垛等重复性并且劳动强度极大的工作,工作方式一般采取教再现的方式。本文主要是注重对铣床加工中心的自动换刀机械手进行设计。主要的功用就是根据零件加工需求的不同,来更换刀具对零件进行精细加工。机械手代替人工换刀不仅提高了生产效率和降低了生产成本,还避免了人身事故。关键词:换刀机械手 铣床加工中心 De
2、sign of Manipulator of Milling Vertical Machine CenterStudent:XXXXXTutor:XXXXXAbstract: Nowadays, in the great scale of manufacturing industries, enterprises pay more attention to the level of the automation in order to improve the production efficiency and the product quality. And the manipulators
3、are gradually recognized by enterprises as the important parts of the automatic production line. The technical levels and the skilled application of the manipulators reflect the national levels of industrial automation to some degrees. At present, the manipulators are devoting themselves to the task
4、s like welding, painting, carrying and stacking which are very complicated and tiring. And their way of working is to teach and to payback. This unit mainly considers the design of the automatic knife manipulators of the milling machining center. Its main function is to replace the knife tools and t
5、o process the body parts finely according to the different demands of the body parts that need processing. Manipulators instead of the manual work not only improve the efficiency of production and reduce the costs of production, but also avoid the security accidents.Key Words:The knife manipulators,
6、The Milling machining center 1 前言 1.1 国内外研究现状加工中心是在数控铣床的基础上发展起来的。1952 年,美国麻省理工学院首先实现了三坐标铣床的数控化,数控装置采用真空管电路。1955 年,第一次进行了数控机床的批量制造。数控机床是电子技术、自动控制技术、机械技术的综合应用,是机械加工领域划时代的重大技术突破。数控机床利用编程软件,将简单工序集中起来,从而大大提高零件的加工效率和加工质量。但在复杂零件工序高度集中时,必须频繁地更换刀具以满足不同工序的加工要求,从而限制了生产效率的提高。为了解决自动换刀问题,提高生产效率,最早出现了转塔头立式钻铣床。1956
7、 年日本富士通研究成功数控转塔式冲床。美国IBM 公司同期也研制成功了“APT”(刀具程序控制装置)。1958 年美国K&T 公司研制出带ATC(自动刀具交换装置)的加工中心。同年,美国UT 公司首次把铣钻等多种工序集中于一台数控铣床中,通过自动换刀方式实现连续加工,成为世界上第一台加工中心。1967年出现了FMS(柔性制造系统)。1978 年以后,加工中心迅速发展,带有ATC 装置可实现多种工序加工的机床,步入了机床发展的黄金时代。1983 年国际标准化组织制定了数控刀具锥柄的国际标准,自动换刀系统便形成了统一的结构模式。日本三井哲夫在上世纪八十年代中期将弧面凸轮用于ATC 的刀臂旋转控制,
8、取得极佳效果。20 年来此类机构长盛不衰,已成为ATC 机构的主流。目前发达国家数控加工中心的自动换刀机械手主要采用弧面凸轮式换刀机械手。1.2 选题研究意义在机械工业中,应用机械手的意义可以概括如下:1.以提高生产过程中的自动化程度应用机械手有利于实现材料的传送、工件的装卸、刀具的更换以及机器的装配等的自动化的程度,从而可以提高劳动生产率和降低生产成本。2.以改善劳动条件,避免人身事故在高温、高压、低温、低压、有灰尘、噪声、臭味、有放射性或有其他毒性污染以及工作空间狭窄的场合中,用人手直接操作是有危险或根本不可能的,而应用机械手即可部分或全部代替人安全的完成作业,使劳动条件得以改善。在一些简
9、单、重复,特别是较笨重的操作中,以机械手代替人进行工作,可以避免由于操作疲劳或疏忽而造成的人身事故。3可以减轻人力,并便于有节奏的生产应用机械手代替人进行工作,这是直接减少人力的一个侧面,同时由于应用机械手可以连续的工作,这是减少人力的另一个侧面。因此,在自动化机床的综合加工自动线上,目前几乎都没有机械手,以减少人力和更准确的控制生产的节拍,便于有节奏的进行工作生产。综上所述,有效的应用机械手,是发展机械工业的必然趋势。2 加工中心2.1 加工中心简介加工中心(Machining Center)是一种具有自动换刀功能的高效自动化机床,由机械部件与数控系统组成,适用于加工复杂零件1。这种机床能装
10、多把刀具,在一次装夹中完成铣、镗、钻、扩、铰、攻螺纹、切内槽等工序的加工。高精度加工中心可以代替精密坐标镗床,还可作为基础部件组成柔性制造系统和计算机集成制造系统。加工中心的工作过程为:根据零件图样制定工艺方案,采用手工编程或计算机自动编程方式编制零件的加工程序,将加工零件所需的机床各种动作及全部工艺参数变成机床数控装置所能接受的信息代码,并把这些信息代码存储在信息载体上,将信息载体送到输入装置读出信息,并送入数控装置11。进入数控装置的信息,经过一系列处理和运算变成脉冲信号,部分信号送到机床的伺服系统,通过伺服机构对其进行放大,再经过传动机构,驱动机床有关部件。使刀具和工件严格执行零件程序所
11、规定的相对运动。部分信号送到可编程序控制器中,用以控制机床的其它辅助动作,如冷却液的开关和自动更换刀具等。加工中心的基本结构由三部分组成:CNC 数控系统。加工中心一般都采用CNC 数控系统。伺服系统。伺服系统的作用是把来自数控装置的信号转换为机床移动部件的运动。机械部件13。加工中心和一般通用机床相比,其结构简单,精度高,结构刚性好,可靠性高;显著区别是具有对零件进行多工序加工的能力2。2.2 自动换刀装置的组成在实际生产中,大多数零件都要进行多道工序的加工。当用数控机床实现多工序加工时,真正用于切削工件的时间只占整个作业时间的30%左右,其余大部分时间都花在安装、调整刀具、装卸、搬运零件和
12、检查加工精度等辅助工作上。为充分发挥数控机床的作用,在机床中配备自动换刀装置而成为加工中心。自动换刀装置(Automatic Tool Changer,简称ATC)由刀库、机械手和驱动装置等部分组成3。刀库的功能是用于存储刀具,并把即将要用的刀具准确地送到换刀位置,供换刀机械手完成新旧刀具的交换。刀库配置在主轴附近,换刀机构在主轴和刀库之间执行换刀动作,完成此功能的机构称为机械手。机械手包括送刀臂、摆刀站和换刀臂等部分。机械手完成刀具装卸和在主轴头与刀库之间的传递。驱动装置是使刀库和机械手实现其功能的动力装置,一般由步进电机或液压(或气液机构)或凸轮机构组成。自动换刀装置的形式多种多样,其换刀
13、过程、选刀方式、刀库结构、机械手类型等各不相同,但都是在数控装置及可编程序控制器的控制下,由电机、液压或气动机构来驱动刀库和机械手来实现刀具的选择和交换。早期自动换刀装置采用转塔式机构来实现自动换刀,后来陆续出现了无换刀机械手式和带换刀机械手式的自动换刀装置。无换刀机械手式换刀主要有两种方式:一种是悬臂式刀库,水平安放在铣头旁边,刀库留有一个空缺的刀位,换刀时偏心轮带动刀库回转,然后拔刀、转位、换刀,最后插刀进入主轴。另一种是刀库固定,用机床主轴运动去配合刀库,完成插刀和拔刀动作。这种无机械手式ATC 换刀时必须先将用过的刀具送回刀库,然后再从刀库中取出新刀具。该两种动作不能同时进行,换刀时间
14、较长。虽然结构简单,但机床配置的刀具量较少。带换刀机械手式换刀类型比较多,按驱动装置的不同可以分凸轮式、液压式、齿轮式、连杆式以及多种机构复合式,其中以凸轮式应用最广,采用该换刀形式的加工中心可以配备较多的刀具3。2.3 换刀机械手换刀机械手是执行刀库和主轴之间换刀动作的装置5,分为以下几种类型:2.3.1 单臂机械手该换刀机械手仅有一个手臂。可细分为单手式和双手式两种: (1) 单手式:一个换刀臂仅有一个抓刀手。如图1。 特点:所有动作均由单手完成,执行动作多,换刀时间长,但结构简单,刀库与主轴轴线平行或垂直的情况均适用。图1 单手式Fig.1 Single hand type(2) 双手式
15、:一个换刀臂两端各有一个抓刀手。如图2。特点:机械手同时抓取主轴和刀库上的刀具,回转 180 度,同时放回和装入刀具,换刀时间短,较为常用,多用于刀座与主轴轴线平行的场合。图2 双手式Fig.2 Hands to type2.3.2 双臂机械手两个机械手臂,每个手臂端部都有一个抓刀手。如图c。 特点:其抓刀和换刀动作类似于人手动作,除执行换刀动作外有些还可以起运输刀具的作用。这种机械手换刀时间短,但结构较复杂。图3 双臂手Fig.3 Aims in hand2.3.3 带送刀臂、摆刀站和换刀臂的机械手送刀臂将刀具从刀库中取出送到摆刀站,由摆刀站将刀具送到换刀位置,最后由换刀臂进行换刀。如图4所
16、示,A 为送刀臂,B 为摆刀站,C 为换刀臂,D 为刀库,E 为主轴。特点:结构更复杂,各部分在空间巧妙配置和组合,更具变化性。换刀时间较短,适用于刀库距离主轴较远的场合。图4 带送刀臂、摆刀站和换刀臂的机械手Fig.4 Manipulator of deliver the tool arm,waggle the tool station and exchange the tool arm2.4 常用换刀机械手2.4.1 单臂双爪式机械手单臂双爪式机械手也叫扁担式机械手,它是目前加工中心上用得最多的一种。这种机械手的拔刀、插刀动作,大都由液压缸来完成4。 近年来凸轮式联动式单臂双爪机械手得到广
17、泛的应用,这是因为这种机械手由电动机驱动,不需要复杂的液压系统及其密封、缓冲机构,没有漏油现象,机构简单,工作可靠。同时,机械手手臂的回转和插刀、拔刀的分解动作是联动的,部分时间可重叠,大大缩短了换刀时间。2.4.2 双臂单爪交叉式机械手2.4.3 单臂双爪且手臂回转轴成45的机械手 这种机械手换刀动作可靠,换刀时间短,缺点是刀柄精度要求高,结构复杂,联机调整的相关精度要求高,机械手离加工区较近。2.5 刀库刀库是存储刀具的装置,刀库主要有以下几种形式:a.转塔式刀库包括水平转塔头和垂直转塔头两种。特点:所有刀具固定在同一转塔上,无换刀臂,储刀数量有限,通常为68把。一般仅用于轻便而简单的机型
18、。常见于车削中心和钻削中心。在钻削中心储刀位置即主轴,其外部结构紧凑但内部构造复杂,精度要求高b.盘式刀库该刀库呈盘状,刀具沿盘面垂直排列(包括径向取刀和轴向取刀)。沿盘面径向排列或成锐角排列的刀库,结构简单紧凑,应用较多,但刀具单环排列,空间利用率低。如果要增加刀库容量必须使刀库的外径增大,那么转动惯量也相应增大,选刀运动时间增长。此刀库所存贮的刀具数量一般不多于32 把。对于刀具呈多环排列的刀库,其空间利用率高,但取刀机构复杂,适用于机床空间受限制而刀库容量大的场合;双盘式结构是两个较小容量的刀库分置于主轴两侧,布局较紧凑,储刀数量也相应增大,适用于中小型加工中心。c.链式刀库链环形式有多
19、种形式,包括单环链和多环链。该刀库所占空间小,适用于刀具容量较大的场合,一般用于刀具数在30120把的机床。该刀库结构可通过增加链条长度增加刀具数,而不必增加圆周速度,其转动惯量小于盘式刀库。d.直线式刀库和组合刀库直线式刀库结构简单,刀具单行排列,刀库容量小,多用于数控车床和钻床上。组合刀库一般是转塔式刀库的组合,转塔式与盘式刀库的组合及链式刀库的组合。单个刀库的储刀量较小,换刀速度快。另外,还有一些密集型的鼓轮式、弹匣式和格子式刀库。这些密集型刀库虽占地面积小,但由于结构限制,基本上不用于单机加工中心,多用于FMS 的集中供刀系统。2.6 换刀机械手的组成加工中心换刀机械手由执行机构、驱动
20、机构、控制系统、检测机构组成6,各部分特点如下:2.6.1 执行机构执行机构是完成各种动作的部件总称,它由抓取部分(手部)、腕部、臂部和手架等运动部件所组成。手指部分:即直接与工件接触部分,一般是回转型或平移型,手爪多为两指,也有多指;根据需要分为内抓式或外抓式;也可用负压式或真空式的空气吸盘和电磁吸盘。本设计采用夹持式手部,即由手爪和传力机构组成,它的主要功能是在换刀过程中完成抓住工件、握持工件和释放工件的动作。手腕部分:用于连接手指部分和手臂部分的部件。手臂部分:手臂是支撑被抓物体以及手指部分的重要部件,起调整和改变工件方位的作用。本设计中手臂的主要作用是带动手指去抓取物件。手架部分:用于
21、承受手部以及手臂部分的总体重量,在本设计中它还用于通过旋转运动实现加工中心主轴刀具和刀库刀具的互换运动。2.6.2 驱动机构驱动机构是用来为各个部件的运动提供动力,是实现一切运动的动力源,有气动、液动、电动和机械式四种形式15。其中液压气驱动用的最多,占90%以上,电动、机械驱动用的较少。液压驱动主要是通过油缸、阀、油泵和邮箱等实现传动。它利用油缸、马达加上齿轮、齿条实现直线运动;利用摆动油缸、马达与减速器、油缸与齿条、齿轮或链条、链轮等实现回转运动。液压驱动的优点是压力高、体积小、出力大、运动平缓,可无级变速,自锁方便,并能在中间位置停止。缺点是需要配备压力源,系统复杂成本较高。气压驱动所采
22、用的元件为气压缸、气压马达、气阀等。一般采用4-6个大气压,个别的达到8-10个大气压。他的优点是气源方便,维护简单,成本低。缺点是出力小体积大。由于空气的可压缩性大,很难现实中间位置的停止,只能用于点位控制,而且润滑性较差,气压系统容易生锈。为了减少停机时产生的冲击,气压系统装有速度控制机构或缓冲机构。电气驱动采用的不多现在都用三相感应电动机作为动力,用大减速比减速器来驱动执行机构;直线涌动则用电动机带动丝杠螺母机构;有的采用直线电动机。通用机械手则考虑用步进电机、直流火交流的伺服电机、变速箱等。电气驱动的优点是驱动源简单,维护,使用方便。驱动机构和控制系统可以采用统一形式的动力,出力比较大
23、;缺点是控制响应速度比较慢。机械驱动只用于固定的场合。一般用凸轮连杆机构实现规定的动作。它的优点是动作确实可靠,速度高,成本低;缺点是不易调整。2.6.3 控制系统 此系统是用来控制驱动机构工作,从而实现按预定程序进行工作的机构。它通过位置检测的反馈来检测各部分机构工作的位置精度,从而保证能准确地实现加工中心换刀机械手的换刀动作。控制系统包括程序控制部分和行程反馈部分。2.6.4 检测机构检测是为了进行比较和判断提供依据,位置检测是通过将位置变化反馈给输入变量从而达到一定的定位精度和位置精度。本设计中伸缩和升降机构采用压力继电器进行位置控制。2.7 换刀方式换刀方式主要有随机任选换刀和固定任选
24、换刀。前一种方式刀库的刀套号和刀具号在换刀完成后,就不一致了。而后一种方式,刀套号和刀具号始终一致。1固定换刀方式A(无机械手,无刀具准备功能):无论换刀次数,刀套号与刀具号始终一一对应,如N号刀套中始终是N号刀。这种换刀方式换刀时间较长,适合用于刀具容量较少的小型加工中心。且无刀具准备,必须先归旧刀再找新刀加工(无机械手,用主轴运动进给),换刀时间较长,适用于小型刀库(BT40一下,20把刀以内,刀库速度快)。2固定换刀方式B(有机械手,可实现刀具准备)刀具号仍与刀套号一致,无刀具表,系统可记忆当前主轴刀具和下吧所选的刀具,机械手用油缸驱动,故易受油质、阀体质量、油压、油温等外界因素的影响,
25、需定期进行调整,并清洗阀体。此种适和用于换刀不很频繁、刀具数为40-60把、主轴锥孔为BT40以上的刀库。3随机换刀(有机械手,可实现刀具准备):刀具号与刀套号不一一对应,系统有相应的刀具表随时记忆刀具的使用情况,刀表中的刀套是固定的,而刀具号则随刀具的交换随时更新。例如在刀具表初始化后,N号刀套中是N号刀,但只要生产刀具交换,则刀具表随之进行数据交换(需在梯形图中处理并设定相应的数据表)。当所选刀具直径超过相邻刀套中心距时(产生刀具干涉时),需做大径到判断后采取不同的换刀方式:如为大径刀,使用固定刀套换刀方式:如为小径刀则采用随机换刀。大径刀的判别可用多种方式实现,如采用宏程序或在梯形图中处
26、理。综上所述,不同的换刀方式各有各的优缺点,使用时应根据具体情况选择使用。2.8 刀具的识别装置1 接触式刀具识别装置 接触是刀具识别装置应用广泛,特别适用于空间位置较小的刀具编码。这种识别装置结构简单,但可靠性较差,且难于快速换刀。2 非接触式刀具识别装置非接触式刀具识别装置无机械接触、无磨损、无噪声、寿命长、反应速度快,适用于高速且换刀频繁的场合。非接触式刀具识别方法主要有:磁性识别法、光学纤维识别法、图像识别法。夹爪的类型更具刀柄在换刀机构刀臂上的夹持方式可分为固定爪、活动爪、单夹爪、双夹爪、弹簧爪、动力爪等类型。固定爪是指刀臂夹持部能吻合刀柄V形槽的半圆部分,半圆形夹持部的一端或两端有
27、弹簧扣,即所谓单夹爪、双夹爪;由两个可张开的夹指所组成即活动爪,其加紧里由弹簧产生的即弹簧爪,通常以直进方式抓刀松刀;由液压缸等动力源控制其张合的为动力爪。3 换刀动作顺序和驱动方案的比较选择3.1 换刀顺序图5 换刀动作设计方案Fig.5 Design proposal of tool exchange movement如图5所示,其运动过程如下:换刀手由准备位置B移至位置A,当主轴退出刀杆后,换刀臂和联接体现实一起绕轴I转动180,主轴箱复位,刀杆插入主轴,卡爪松开后,换刀手回至位置B(此时,主轴已经开始工作,下述换刀动作为辅助运动,与工件加工同步进行),导轨以上的机构由B运动到C、D、E
28、而将刀具插入刀库中,然后运动到位置B。刀库转动,将所需刀具转至位置E,由位置B-E-D-C-B完成取刀过程,此时,换刀手夹持着新刀具在准备位置B待命。至此本轮换刀结束,待接到新的换刀命令后,重复上述过程。3.2 驱动方案的比较3.2.1 方案1 将45换刀机械手与移动式换刀机械手相结合如图6:图6 立式换刀机械手方案1Fig.6 Manipulator proposal of vertical tool change 1换刀手准备位置B至图示位置A,当主轴箱1退出刀杆后,在机构5的作用下,换刀臂2、4和连接体3前移至图示位置再一起绕轴I转动180,主轴箱1再换刀,卡爪松开后,纵向差动油缸8带动
29、换刀手至位置C(此时,主轴已经开始工作,下述换刀动作为辅助运动,与工件加工同步进行);横向油缸带动换刀手至位置D,油缸8使其移动至位置E而将刀具插入刀库中;横向油缸回位,使换刀手回到换刀准备位置B。刀库电机转动,将所需刀具转至位置E,换刀手在差动油缸8和横向油缸的共同作用下,完成由位置B-E-D-C-B的转换过程,此时,换刀手夹持着新刀具在换刀准备位置B待命。至此本轮换刀结束,待接到新的换刀命令后,重复上述过程。机构5,7选用液压驱动齿轮齿条机构,横向油缸固定在机架上。3.2.2 方案2原理图如图7,采用伺服电机作为动力源来实现换刀运动。实现两个直线于东、两个旋转运动的过程如下:换刀手由伺服电
30、动机驱动齿轮齿条传动装置3中的齿轮4传到齿轮5再传到齿轮11和齿条12,是轴II丹东机构1和换刀臂及联接体由准备位置B移至图示位置A;当主轴箱退出刀杆后,在伺服电动机的带动下,再由齿轮11带动齿条12使换刀手运动至位置B;此时由机构2带动机构3、机构1和换刀臂联接体及刀具实现从B到C再到D最后到E而将刀具插入刀库中,再由机构2使机构3、机构1和换刀臂连接体回到准备位置B。刀库转动,将所需的刀具转至位置E,换刀手在机构2使机构3、机构1和换刀臂联接体完成由位置B-E-D-C-B的取刀运动过程。此时换刀手夹持着新刀再准备位置B待命。至此本轮换刀结束,待接到新的换刀命令后,重复上述过程。图7 立式换
31、刀机械手方案2Fig.7 Manipulator proposal of vertical tool change 23.2.3 方案3原理如图8,液压缸4直接驱动换刀手。其运动过程如下:换刀手由气缸3推动在导轨上运动,由准备位置B移动至位置A,当主轴退出刀杆后,在液压缸4的驱动下,换刀臂和连接体实现一起绕轴I转动180主轴箱复位,刀杆插入主轴,卡爪松开后气缸3将换刀手拉回至位置B(此时,主轴已开始工作,下述换刀动作为辅助运动,与工件加工同步进行),由凸轮机构1带动导轨以上的机构由B运动到C、D、E而将刀具插入刀库中,然后凸轮机构1使他们运动到位置B。刀库转动,将所需刀具转至位置E,导轨以上的
32、机构再在凸轮机构1的作用下有位置B-E-D-C-B完成取刀过程,此时,换刀手夹持着新刀具在准备位置B待命。至此本轮换刀结束,带接到新的换刀命令后,初伏上述过程图8 立式换刀机械手方案3Fig.8 Manipulator proposal of vertical tool change 33.2.4 方案4本方案的设计思路是:在刀库和45换刀机械手之间加一个小型的送到机械手装置并固定在一合理的位置,再装配一个暂存刀位置。这样一来,就去掉凸轮机构,只需其它的机构就可以实现换刀。以方案3的图为例简述其换刀过程:换刀手由准备位置B移至位置A,主轴箱退出刀杆,轴I旋转180,主轴箱再换刀,卡爪松开后,运
33、动到位置B(此时,主轴已经开始工作),将刀具放入暂存刀位置,送刀机械手将刀取回刀库,再选取新刀放在暂存到位置,然后换刀机械手将刀从暂存刀位置取出在位置B待命。至此本轮换刀结束,待接到新的换刀命令后,重复上述过程。3.2.5 方案比较 方案1采用的液压作为动力源,由于液压驱动的机械手需要采用严格的密封,还需要较复杂的缓冲机构;控制机械手动作的电磁阀有一定的时间滞后,因而换刀速度慢且不易维护,不足取。方案2采用了伺服电动机作为动力源,虽然避免了使用液压时的一些问题,但同时也存在一些不足;采用齿轮齿条机构的传动,将使定位精度降低,同时降低了运动平衡性,在定位精度和运动平稳性要求较高的换刀过程中出现这
34、种现象是不可取的。另外,增加量齿轮齿条机构,加大了重量,使得整个换刀机械手显得笨大,不能满足结构简单的设计思想,因此也不可取。方案3是方案2的改进方案,由于换刀手及刀具的重量并不是很到,不必要再加一些中间装置直接由液压缸驱动换刀手进行绕轴I转动,这样联接结构简单,减少了零件的数目,减少了中间环节的影响,没有间隙,效率高;既增加了定位精度又减少了换刀时间。在实现从B-C-D-E-B的过程中,采用了凸轮结构,不需要复杂的液压系统及其密封、缓冲机构,结构简单,工作可靠,从而大大的缩短了换刀时间。对于方案4来说,动作比较多不容易协调,反而增加了换刀时间,不足取。综上所述,方案3比较合理。4 换刀机械手
35、的结构设计及尺寸确定4.1 手指夹紧力的计算手指加在工件上的加紧力,是设计手部的主要依据。必须对大小放心和作用点进行分析计算。一般来说需要克服工件重力所产生的静载荷以及工件运动状态变化的惯性力产生的载荷,以便工件保持可靠的加紧状态。手指对工件的夹紧力可按公式计算: (1)式中: ,本设计中取 ,本设计中取 。本设计中取 。本设计中刀具质量8kg,所以重力为 带入公式得:4.2 手部的驱动力计算如下图所示,P为油压力,G为刀具的重量,N为手指夹住刀具的夹紧力,则P=2bctgN其中 c为动力臂,b为阻力臂,c=b/2,去=15从而P=4Ntga15为了考虑刀具在传动时惯性力、振动及传动效率的影响
36、,其实际驱动力: (2)式子中: 在此分别取值: , , 。从而: = 图9 手部受力分析Fig.9 Hand force analysis机械手卡爪中销的选择机械手卡爪中销,都选用的是圆柱销M8,材料为45号钢,其许用切应力核算: (3)已算出:,根据上式算出 (4)所以该圆柱销符合要求4.3 机械手卡爪机构选用及工作原理如图10,油缸11、定位块8固定在换刀臂10上,活塞固定于定位块8上。换刀手由准备位置移动至换刀位置,键2卡进刀具定位槽中,此时,油缸11推动活塞组件9,在定位块8的导向下向前滑动,使得两卡爪1、3分别绕轴4、5转动,直至卡爪加紧刀具,此时,活塞组件9将卡爪锁上。卡爪的松开
37、是由油缸11内的弹簧带动活塞组件9后移,卡爪1、3分别在弹簧球6、7的作用下与活塞组件件9保持接触,卡爪松开后,换刀手退至准备位置。本卡爪加紧机构利用活塞组件9实现了卡紧、锁止的联动,在油压较小时也能有效的锁紧刀具。当锁止角=15时,也就是说作用于卡爪上的力比所提供的作用于活塞组件9上的油压大约大4倍,故可满足锁止要求。图10 机械手卡爪机构Fig.10 Manipulator claw mechanism4.4 滚动直线导轨机械手由准备位置到换刀位置的往返直线运动选用THKHRA型50166滚动直线导轨来实现。这样,不仅提高了机械手的定位精度,而且低速时无爬行现象。采用滚动直线导轨还可以施加
38、预紧力,以提高它的承载能力,是机械手的运动精度和稳定性有了保证。5 凸轮机构的设计5.1 结构方案在实际应用中,多数凸轮机构是一个凸轮驱动一个从动件,极少采用一个凸轮驱动多个从动件。在立式加工中心换刀机械手的研究设计中,为了满足使用要求,采用了两个凹槽式凸轮驱动分别带动2个从动件,是机械手完成一个正方形运动,从而实现插刀和拔刀。使得凸轮机构的结构设计简单化,成本也大大降低。根据立卧两用换刀机械手的设计方案,采用一个凸轮的轮廓曲线同时驱动两个从动件实现B-C-D-E形状的正方形运动,两个从动件的运动规律应该完全相同。所以两个凸轮带动2个从动件运动规律也与一个凸轮2个从动件相同,设计原理也相同。设
39、一个凸轮2个从动件原理图如图11所示,凸轮采用的方案为一个具体有两个互相垂直从动件的圆柱滚子凸轮机构,并且推程、回程角都为904。图11 凸轮原理Fig.11 Principle of CAM5.2 运动规律计算 凸轮的轮廓形状取决于从动件的运动规律,在确定从动件运动规律时,要考虑由于加速度突变所引起的冲击19。应尽量选择加速度曲线连续的运动规律。根据从动件所要求完成的运动,在从动件1相对凸轮运动时,从动件2必须静止,然后从动件2运动、从动件1静止。因此凸轮必须具有双停歇运动规律,即具有远近休止角。所以在行程两端的速度和加速度应为零。这样,在推程和回程衔接处,加速度过渡平滑,且可使最大速度和最
40、大加速度下降,对受力情况和减少振动都是有利的。凸轮的转速n应依据换刀辅助时间来确定,完成插刀及拔刀所需时间为2s,则凸轮的转速n=1r/s,即n=60r/min为低速运动。其次自机械手爪、连接体及所推动的箱体,初步估计为60kg-80kg,属中等载荷。根据规律为改进正弦加速度运动规律。插刀、拔刀整个过程的轨迹为正方形,正方形的尺寸主要由于刀具的尺寸所决定,及LCD(C、D两点间的距离)必须大于刀具刀柄的半径才能顺利取出刀具,而且LBC(B、C两点间的距离)尺寸必须大于刀柄的长度,才能实现插刀、拔刀。现依据这个条件,进行凸轮设计计算。刀柄半径为40mm,刀柄长度为70mm。根据这个条件,确定B-
41、C-D-E正方形的边长为80mm。由于凸轮需要现实插刀、拔刀的正方形轨迹是唯一不变的,即凸轮无论在正转、反转都能改变其走过的几何形状。因此,凸轮的形状轮廓相对某条轴线相对称,即推程与回程具有相对应的特征。取回程运动方程与推程运动方程相同,则从动件的运动方程如下所示。推程运动方程前段: (5) (6) (7)中段: (8) (9) (10)后段: (11) (12) (13)回程运动方程前段: (14) (15) (16)中段: (17) (18) (19)后段: (20) (21) (22)休止角运动规律及参数根据从动件所要完成的运动轨迹曲线B-C-D-E的尺寸,到达远休止角时,其升程为80m
42、m。元休止角的范围为。 处于远休止段时:s=80mm:近休止段时,从动件相对静止、位移最小,近休止角的范围为。 即:处于近休止段时:s=0,。位移曲线方程依据从动件的运动方程休止角运动规律及参数,得出从动件完整的位移曲线方程,即从动件运动规律为: 范围 位移曲线方程 (23) (24) (25) (26) (27) (28) 凸轮轮廓曲线的绘制 依据从动件的位移曲线方程,绘制凸轮的轮廓曲线如下图图12 凸轮轮廓Fig.12 The contour of cam5.3 凸轮结论立式加工中心换刀机械手采用凸轮式驱动方式克服了液压式驱动所存在的缺点,是机械手的换刀速度及可靠性等大为提升:采用双从动件
43、的结构形式,克服了由于两个凸轮分别驱动两个从动件带来的结构庞大和造价高等缺点9;凸轮曲线采用修正正弦曲线,容易加工且在使用过程中提高了运动的平稳性。6 零件的简单计算和选择6.1 弹簧的设计计算弹簧选用普通圆柱压缩弹簧,弹簧类型为II类,是硅锰弹簧钢,查取许用切应力为 选择旋绕比C=8,则 (29) 根据安装空间选择弹簧中径D=42mm,估算弹簧丝直径 试算弹簧丝直径 (30)根据变形情况确定弹簧圈的有效圈数: (31)选择标准为n=3,弹簧的总圈数圈最后确定D=42mm,d=7mm,6.2 机械手回转轴上的齿轮齿条设计回转轴上齿轮采用渐开线标准直齿圆柱齿轮形式计算齿轮几何尺寸设计的基本菜熟:
44、初取齿数z=45,模数m=3,压力角=20分度圆直径d: d=mz=齿顶高齿根高齿全高齿顶圆直径齿根圆直径齿距齿厚齿槽宽顶隙材料选择:齿轮材料为45号钢(调质处理)硬度为24HBS,查表得齿轮的接触疲劳强度极限 查表得齿轮的弯曲疲劳强度极限;弯曲疲劳寿命系数Kfn=0.88,计算弯曲疲劳许用应力取弯曲疲劳安全系数S=1.4得齿条的基本尺寸,按外齿轮几何尺寸的计算公式计算。6.3 电动机类型的选择13目前常用的加工中心换刀机械手,它的手架旋转运动是由两个液压缸实现的。一个液压缸用来实现手架到达工作位置,换刀运动过程准备开始。另一个液压缸则是在拔刀过程结束后,实现整个手臂转180的运动, 是主轴刀
45、具与刀库刀具互换位置。虽然这种结构工作原理很简单,但由于驱动机构较多,它们之间以及它们和手架伸缩液压缸的活塞杆之间的连接机构却比较复杂。在手架旋转轴上设计了一个很长的键槽,所以只需要用一个驱动机构带动齿轮机构或蜗轮蜗杆机构,就可实现手架在拔、插刀前后的多次旋转运动。对于这个驱动机构,它需要能实现手臂180旋转。若采用液压缸和行程开关进行控制,则一般只能实现一种角度的旋转。而如果采用电动机进行传动,则只需控制好电动机的起、停时间就可以实现各种预期的运动。TYV系列高精度微型特种减速电动机采用高新技术,具有齿轮减速、蜗轮减速、直线往复等多种结构,并可配有电子无级调速、阻尼制动、电磁刹车等功能,适用
46、于交流、直流多种电压,是一种高效、节能、低噪音的微特减速电动机,它还具有结构紧凑、安装方便、减速比大、体积小、输出转矩大及运行可靠等特点,因此,本设计中的手臂旋转机构选用TYV系列高精度微型特种减速电动机作为驱动机构。6.4 轴的计算选用45号钢,查资料取轴的传动效率取0.95查电机系列,取TYV4型齿轮减速电动机,其基本参数如下:允许负载为P=60w,输出转速为n=150r/min。轴的扭转强度条件为: (32)式中:扭转切应力,MPa; 轴的抗扭截面系数,;T轴所受的扭矩,Nmm; n轴的转速,r/min; P轴传递的功率,kw; d计算截面处轴的直径,mm; r动力系数,考虑稳定性本设计
47、取r=1 许用扭转切应力,查表得45号钢为2545MPa由上述式子可得轴的直径: (33) =57W 查表得45号钢为126103,取=120 初步计算得mm,取84mm。校核轴的强度9550000计算应力为: (34)式子中:轴的计算应力,MPa; 轴所受的弯矩,Nmm; 轴所收的扭矩,Nmm; 轴的抗弯截面系数,查机械设计教课书此处取计算公式; 对称循环变应力时轴的许用弯曲应力,查机械设计教课书此处取60 此处轴是受电动机进行旋转,所以没有受到弯曲应力,弯矩W=0 Nmm 原式=所以满足应力要求。轴的刚度校核计算:此处轴用于旋转不考虑弯曲刚度的计算,只考虑轴的扭转刚度的校核计算。公式: (
48、35) 式中:轴所受的扭矩,Nmm; 轴的材料的剪切弹性模量,MPa,对于钢材,; 轴截面的极惯性矩,对于圆轴,; 轴的扭转刚度条件为 (36)为轴每米长的允许扭转角,与轴的使用场合有关。对于一般传动轴,可取;对于精密传动轴,可取;对于精度要求不高的轴,可大于。本设计是一般传动轴取1原式=满足刚度要求。轴的结构如图13图13 轴Fig.13 Shaft6.5 键的选择和强度计算键的选择根据轴的轴径d=84mm,查机械设计表61普通平键,键宽b=22mm,键高h=14mm,键的长度L=180mm键的强度计算普通平键连接的强度条件为 (37)式子中:传递的转矩,Nm;键与轮毂键槽的接触高度,=0.
49、5h,此处h为键的高度mm; 键的工作长度,mm,圆头平键=Lb,平头键=L,这里L为键的公称长度,mm;b为键的宽度,mm; 轴的直径,mm; 键、轴、轮毂3者中最弱材料的许用挤压应力,差机械设计表62取80MPa 原式=68.5MPa 所以选用的普通平键适合7 结论自动换刀装置是数控加工中心在工件的一次装夹中实现多道工序加工不可缺少的装置,主要由刀库、机械手和驱动装置几部分组成。机械手和驱动装置是两个关键部分,根据驱动装置的不同,自动换刀装置可分为凸轮式、液压式、齿轮式、连杆式及各种机构复合式,其中以凸轮式用得较多。 发达国家数控加工中心的立式铣床换刀机械手主要采用凸轮式,我国加工中心技术
50、起步较晚,对自动换刀机械手研究较少。迄今为止,我国制造的加工中心配置的自动换刀机械手大多数是进口的。其主要原因:一是国内生产的换刀机械手质量较差,成本也不低;二是进口换刀机械手价格虽然较高,但在整个加工中心中所占份额不大。作为加工中心的配套技术,自动换刀机械手的研究和开发将直接影响到我国自动化生产水平的提高,从经济上、技术上考虑都是十分必要的。对于数控加工中心凸轮式立式换刀机械手,目前国内外同类产品较少,使设计难度增加。依据总体方案的设计,凸轮机构必须在刀库中完成插刀、拔刀的过程。机械手插刀、拔刀整个过程的运动轨迹为四边形,因此凸轮机构的设计计算难度大,主要是如何提高凸轮机构运动平稳性的问题。
51、通过一个凸轮的轮廓曲线,是从动件上的一点完成机械手插刀、拔刀的整个过程,采用双从动件来完成,而且两个从动件的运动规律应该相同,只能是存在一个时间差。凸轮的轮廓形状取决于从动件的运动规律,因此在设计凸轮轮廓线之前,应首先根据工作要求确定从动件的运动规律。在选择从动件运动规律时,要考虑由速度曲线的突变引起的刚性冲击和由于加速度曲线突变所引起的冲击。尽量使从动件运动规律不存在任何冲击,用以获得连续而光滑的位移、速度、加速度曲线,从而保证从动件运动的平稳性。参考文献1 成大先 机械设计手册(第三版、第一卷)M. 北京:化学工业出版社,19942 张柱银,陈思义,明兴祖.数控原理与数控机床M. 北京:化
52、学工业出版社,2003.3彭晋龄.加工中心应用与维修M.北京:机械工业出版社,19924 贺炜,夏粉玲,唐学飞.凸轮式立卧两用换刀机械手的研究J.咸阳:西北轻工业学院学报.2003 5贺炜,夏粉玲,李体仁等,关于立卧两用换刀机械手的设计J.咸阳:西北轻工业学院学报.6 李峻勤,费仁元.数控机床及其使用与维修M北京:国防工业出版社.20007 廉元国.加工中心新近技术动向.机床J. 1990.18 阎大忱.加工中心的实用技术M.北京:机械工业出版社.1990.109 杨玮.数控加工中心自动换刀机械手的研究D西北轻工硕士学位论文.2002.110林益耀.加工中心的发展动向J.组合机床与自动化技术.
53、 1990.311刘瑞已.加工中心快速自动换刀装置J.机械工程师.2004.1112贺炜. 蔚泽峰.加工中心弧面自动换刀装置(ATC)J.制造技术与机床.2000.813王科社杨庆东 孙志永.浅谈快速自动换刀装置J.新技术新工艺2002.1014王科社,朱骥北.对加工中心ATC 设计若干问题的探讨 J.机床与制造技术,1995.1115许石.数控加工中心双刀库自动换刀的控制方法与实现J.CAD/CAM 与制造业信息化.2003.616罗爱辉.数控加工中心凸轮式自动换刀机械手的研究D 西北轻工业学院硕士学位论文.200217熊光华.数控机床M.北京:机械工业出版社,2001.218 H S Ya
54、n,H H ChenGeometry Design of Roller Gear CamswithHyperboloidRollersJ.Mathematical and Computer Modeling.1995.22(8)19Tsay, D.M. and Lin, and Lin, B.J. Design and Machining of Globoidal Index Cams.ASME J.Journal of Manufacturing Science and Engineering ,1997.Vol.11920 D.M. Tsay and H C Ho. Considerati
55、on of manufacturing parameters in the designgrooved globidal cam indexing mechanisms J.Proc. Instn Mech .Engineeringscience.PartC Journal of Mechanical Engineering Science,2001. l:215-22321 Faydor L.Litvin,etc. Computerized design, simulation of meshing, and contactandstress analysis of face-milled formate generated spiral bevel gearsJ.Mechanism and MachineTheory,2001.37(5): 441459致 谢 通过几个月的探索和学习,终于把本次毕业设计完成了。从一开的对设计的不会做和对书本知识遗忘,慢慢的熟悉起来,但是自己还是有很多的东西不太懂,还需要老师的指
- 温馨提示:
1: 本站所有资源如无特殊说明,都需要本地电脑安装OFFICE2007和PDF阅读器。图纸软件为CAD,CAXA,PROE,UG,SolidWorks等.压缩文件请下载最新的WinRAR软件解压。
2: 本站的文档不包含任何第三方提供的附件图纸等,如果需要附件,请联系上传者。文件的所有权益归上传用户所有。
3.本站RAR压缩包中若带图纸,网页内容里面会有图纸预览,若没有图纸预览就没有图纸。
4. 未经权益所有人同意不得将文件中的内容挪作商业或盈利用途。
5. 装配图网仅提供信息存储空间,仅对用户上传内容的表现方式做保护处理,对用户上传分享的文档内容本身不做任何修改或编辑,并不能对任何下载内容负责。
6. 下载文件中如有侵权或不适当内容,请与我们联系,我们立即纠正。
7. 本站不保证下载资源的准确性、安全性和完整性, 同时也不承担用户因使用这些下载资源对自己和他人造成任何形式的伤害或损失。