催化裂化装置滑阀设计技术规定
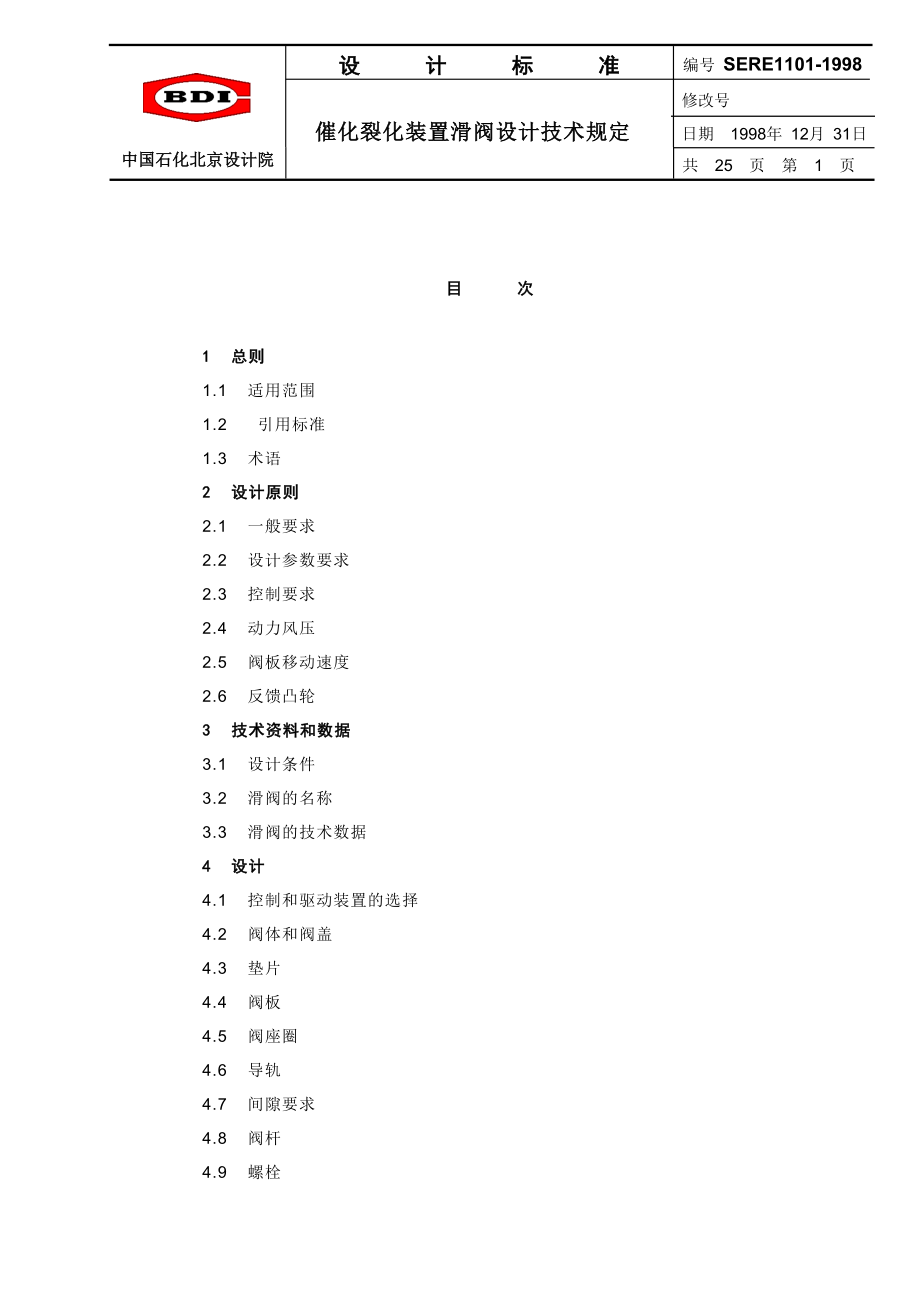


《催化裂化装置滑阀设计技术规定》由会员分享,可在线阅读,更多相关《催化裂化装置滑阀设计技术规定(25页珍藏版)》请在装配图网上搜索。
1、设计标准催化裂化装置滑阀设计技术规定 编号 SERE1101-1998 修改号 日期 1998年 12月 31日中国石化北京设计院 共 25 页 第 25 页目次1 总则1.1 适用范围1.2 引用标准1.3 术语2 设计原则2.1 一般要求2.2 设计参数要求2.3 控制要求2.4 动力风压2.5 阀板移动速度2.6 反馈凸轮3 技术资料和数据3.1 设计条件3.2 滑阀的名称3.3 滑阀的技术数据4 设计4.1 控制和驱动装置的选择4.2 阀体和阀盖4.3 垫片4.4 阀板4.5 阀座圈4.6 导轨4.7 间隙要求4.8 阀杆4.9 螺栓4.10 平衡吊挂5 材料5.1 阀体部分所用的主要
2、材料及用途5.2 材料的化学成分和机械性能应符合有关标准的规定5.3 奥氏体不锈钢材料的含碳量不低于0.04%6 制造技术要求6.1 焊接6.2 喷焊或堆焊6.3 衬里6.4 水压试验6.5 操作性能试验7 附图附录A编制说明1 总则1.1 适用范围 本规定适用于提升管流化催化裂化装置及催化裂解装置的催化剂再生单动滑阀、待生单动滑阀、循环单动滑阀、切断单动滑阀和烟气双动滑阀的结构设计。1.2 引用标准 GB150-1998钢制压力容器 GB699-88优质碳素结构钢技术条件 GB/T983-1995不锈钢焊条 GB984-85堆焊焊条 GB1220-92不锈钢棒 GB1221-92耐热钢棒 G
3、B2100-80不锈耐酸钢铸件技术条件 GB3077-88合金结构钢技术条件 GB4238-92耐热钢板 GB/T5117-1995碳钢焊条 GB/T5118-1995低合金钢焊条 GB6654-1996压力容器用钢板 GB7659-87焊接结构用碳素钢铸件 JB2536-80压力容器油漆、包装和运输 JB4703-92长颈对焊法兰 JB/T4709-92钢制压力容器焊接规程 JB4708-92钢制压力容器焊接工艺评定 JB4730-94压力容器无损检测 SH3074-95石油化工钢制压力容器 SH3075-95石油化工钢制压力容器材料选用标准 BA10-11-3-96滑阀外部保温施工技术条件
4、 BA10-11-5-95滑阀、蝶阀隔热耐磨衬里施工技术条件1.3 术语1.3.1 输入信号 来自变送器的控制信号(气动信号-压力范围0.020.1MPa或电动信号电流范围420mA),根据工艺参数的变化,控制滑阀的动作。1.3.2 输出信号 来自变送器的反馈信号(气动的或电动的),用于指示滑阀的阀位开度。1.3.3 气开式(正比) 当输入信号达到最大值时(气信号为0.1Mpa,电信号为20mA),滑阀处于全开位置,最小值(气信号为0.02MPa,电信号为4mA)时处于关闭位置。1.3.4 气关式(反比) 当输入信号达到最大值时,滑阀处于关闭位置,最小值时处于全开位置。1.3.5 灵敏度 阀杆
5、在任意位置开始动作所需最小的输入信号变动量,以输入信号全量程的百分比表示。1.3.6 准确度 阀杆在任意位置只要输入信号有变化,阀杆都要移动到与新的输入信号相对应的位置上,实际的位置与对应的位置之差称滑阀的准确度或非线性偏差,用全行程的百分比表示。1.3.7 稳定性 输入信号经反馈达到平衡后,阀杆应保持不动,以单程振荡次数表示之。1.3.8 最高操作压力 滑阀在正常工作过程中可能产生的最高压力。1.3.9 设计压力 在相应设计温度下,用以确定阀体计算壁厚的压力。1.3.10 设计压差 滑阀上游与下游设计的压力差,用于确定内部元件的尺寸。1.3.11 最高操作温度 滑阀在正常工作过程中可能产生的
6、最高温度,由不正常操作引起滑阀短时超温不属本范畴之内。1.3.12 设计温度 滑阀在正常操作过程中,在相应的设计压力下,规定阀体壁和内部元件可能达到的最高温度。2 设计原则2.1 一般要求2.1.1 滑阀的设计必须符合工艺操作的要求。2.1.2 阀体内部的结构设计必须保证其内部元件拆卸方便。2.1.3 阀体内部元件的设计必须最大限度地抗催化剂的冲刷与磨损,以提高其使用寿命。2.1.4 阀体的零部件设计必须考虑工作状态时的热膨胀变形。2.1.5 阀座圈、阀板和导轨等内部零件应布置在阀口的下游,以避免催化剂的直接冲刷。2.1.6 驱动装置必须备有手动操纵机构。2.1.7 滑阀必须设有机械限位装置。
7、2.1.8 在阀体、阀盖和驱动装置上应设置吊耳、供吊装用。2.2 设计参数要求2.2.1 设计压力 滑阀的设计压力通常取1.1倍的最高操作压力,但不低于0.5MPa。2.2.2 操作压差和设计压差 a) 滑阀的操作压差包括催化剂的料柱,按工艺要求定,但不宜过大,否则会加剧滑阀内部零件的磨损。一般按操作压差的1.21.5倍选取。 b) 对调节用单动滑阀,滑阀的设计压差最大不应超过0.2MPa;双动滑阀最大不应超过0.12MPa;对切断单动滑阀最大不应超过滑阀的操作压力。2.2.3 设计温度 滑阀的设计温度按最高操作温度加50选取,对冷壁滑阀阀体壁设计温度取3502.3 控制要求2.3.1 控制方
8、式 a) 单动滑阀的控制方式根据工艺的要求决定,一般气动采用气开式,电液采用正比式。 b) 双动滑阀的控制方式气动采用气关式;电液采用反比式。2.3.2 灵敏度 a) 气动单动滑阀的灵敏度要求达到1/200,电液的要求达到1/1000。 b) 气动双动滑阀的灵敏度要求达到1/400,电液的要求达到1/1000。2.3.3 准确度 气动滑阀的准确度要求达到1/100;电液的要求达到1/600。2.3.4 稳定性 单程振荡次数气动的不大于3次,电液的不大于1次。2.4 动力风压 对于风动马达驱动的滑阀来说,进入滑阀的动力风压力为0.4-0.6MPa。2.5 阀板移动速度2.5.1 气动调节风动驱动
9、的滑阀,动力风为0.5MPa时,一般不小于15mm/s。2.5.2 电液控制和驱动的滑阀不小于25mm/s。2.6 反馈凸轮 气动调节的定位器和阀位变送器用反馈凸轮的设计转角应不大于254。3 技术资料和数据3.1 设计条件 滑阀的设计条件由工艺专业提供,其中应包括:3.1.1 滑阀的接管直径(衬里内的和衬里外的直径);3.1.2 开口面积和余隙(双动滑阀);3.1.3 最高操作压力和操作温度;3.1.4 滑阀的操作压差;3.1.5 滑阀的安装方位及介质流向;3.1.6 滑阀的控制方式;3.1.7 滑阀的名称(再生、待生和循环等)及其作用(调节的或切断的)。3.2 滑阀的名称在图中表示的滑阀名
10、称应简单明了,即要反映驱动与控制方式,又要反映滑阀的规格和结构特点,举例如下:3.2.1 GO2.0-585/660单动滑阀(用于待生斜管) 安装位置 衬里(上游/下游)内直径 风动马达功率(KW) 滚珠丝杠传动箱3.2.2 FQ7.5-800切断单向滑阀(用于外取热上斜管) 安装位置 衬里内直径 风动马达功率(KW) 型梯形螺纹传动箱3.2.3 BDY9A-700冷壁式单动滑阀(用于再生斜管) 安装位置 衬里内直径 改型序号 液压系统压力(Mpa) 分离式电液传动控制装置 隔爆型 注:制造图不注安装位置,凡是没有标出冷壁式的滑阀都是热壁式结构。3.3 滑阀的技术数据 滑阀的说明书和图纸中应表
11、示如下内容的技术数据。3.3.1 气动调节风动滑阀 a) 阀体部分 1) 设计压力 Mpa 2) 设计温度 3) 设计压差 Mpa 4) 全开口径 mm 5) 全开面积 cm2 6) 关闭余隙面积 cm2 7) 阀杆行程 mm 8) 通过介质 9) 试验压力 Mpa b) 风动马达 1) 空气压力 Mpa 2) 空气耗量 Nm3/min 3) 出轴转速 r/min 4) 相应主轴功率 KW c) 传动部分 1) 总减速比 2) 出轴转速 r/min d) 阀位变送及定位部分 1) 传动速比 2) 凸轮实际转角 度 e) 滑阀特性 1) 灵敏度 2) 准确度 3) 开或关时间 S 4) 稳定性
12、f) 控制方式 g) 设备衬里 1) 耐磨层 2) 厚度 mm 3) 隔热层 4) 厚度 mm3.3.2 电液控制和驱动滑阀 a) 阀体部分 1) 设计压力 Mpa 2) 设计温度 3) 设计压差 Mpa 4) 全开口径 mm 5) 全开面积 cm2 6) 关闭余隙面积 cm2 7) 阀杆行程 mm 8) 通过介质 9) 试验压力 Mpa b) 电液执行机构 1) 油缸 油缸内径 mm 活塞杆直径 mm 最大行程 mm 最大/运行推力 N 2) 轴向柱塞油泵 型号 额定流量 L/min 环境温度 额定压力 Mpa 3) 电动机 型号 功率 KW 转速 r/min 防爆等级 dBT4 4) 蓄能
13、器 容量 L 操作容量 L 5) 油箱容量 L 6) 系统压力 Mpa 7) 液压油牌号 8) 滑阀特性 灵敏度 1/1000 准确度 1/600 稳定性 1 开、关时间 S 9) 控制要求 输入信号 420mA 250 输出信号 420mA 250 仪表电源 220V/1/50 电磁阀电源 24VDC 控制方式 正比或反比 c) 设备衬里 1) 耐磨层 mm 2) 厚度 mm 3) 隔热层 4) 厚度 mm4 设计4.1 控制和驱动装置的选择 滑阀的控制和驱动装置根据用户的需要,选择可采用:4.1.1 气动调节风动驱动装置;4.1.2 电液控制和驱动装置。 电液执行机构推力大,精度高应优先采
14、用。4.2 阀体和阀盖4.2.1 阀体和阀盖的最小设计壁厚应考虑内部所承受的压力和驱动装置的推拉力以及管道所施加的外部载荷。4.2.2 从制造角度考虑,阀体与阀盖有铸造与焊接两种结构形式,应尽量采用焊接结构,以避免铸造易产生的缺陷。4.2.3 阀体与管道的连接,一般应采用焊接连接,对于口径在350mm以下的滑阀,为了便于检修阀体内部的零部件,可采用法兰与管道连接。4.2.4 阀体和阀盖的连接法兰有圆形和矩形两种,其大小必须保证阀体内部零件(阀板、阀座圈和导轨)从此法兰连接口中取出,并有足够的空间来除去导轨和阀座圈螺栓的焊点。4.2.5 法兰的设计 a) 法兰的计算应考虑内部的压力和驱动装置的推
15、拉力或管道所施加的外部载荷。 b) 对热壁阀体的圆形法兰采用PN6.4(6.4Mpa)级的JB4703-92长颈对焊法兰。 c) 对冷壁阀体的圆形法兰采用PN2.5(2.5Mpa)级的JB4703-92长颈对焊法兰。 d) 法兰密封面选用凹凸面型式。 e) 矩形法兰按特殊要求设计。4.2.6 阀体和阀盖的隔热型式。 a) 热壁式在阀体外(法兰除外)按BA10-11-3-96滑阀外部保温施工技术条件的要求铺设隔热层见“图4.2.6-1”,阀体壁温与内部零件的温度基本相同。 b) 冷壁式隔热衬里铺设在阀体内部,见“图4.2.6-2”阀体外壁的温度小于200。4.2.7 在阀体上不宜采用外部加强肋板
16、,以避免在操作过程中,肋板对阀板造成附加热应力。4.2.8 气动滑阀阀盖上应有二个直径为13mm的定位销,以保证阀盖在每次拆装后能正确对中。4.2.9 电液冷壁滑阀阀体上中法兰与阀盖法兰分别设两个导向销及孔,以保证阀盖折装方便。4.2.10 定位销或导向销应对称布置在垫片密封面之外。4.2.11 阀体中心与阀口中心应设计成偏心(见“图4.2.11”)使滑阀在正常操作条件下,阀的开口与阀体接管基本对中,以减少催化剂对阀体的冲刷,其偏心大小按阀口开度面积的5060%考虑。4.2.12 节流锥的设计采取焊接结构,如图4.2.12。4.2.13 当介质流向往上时,见“图4.2.6-1”,阀盖上应设置二
17、个DN20,配有PN2.5(2.5Mpa)管法兰的吹扫管。吹扫管的位置必须对准导轨的滑道面。吹扫介质允许采用压力为0.5MPa的压缩空气或1.0MPa的饱和蒸汽,每个孔需要的耗气量为1520Nm3/hr或12Kg/hr,蒸汽量由工艺安装专业在进气管路上设降压孔板限压。 当介质流向往下时,导轨采用V形槽结构见“图4.6.3”,阀盖上不设导轨吹扫管。见“图4.2.6-2”。4.2.14 填料函的设计 填料函必须采用两级密封结构形式见“图4.2.14”。这种结构在填料发生泄漏的情况下,可以采取加大填料函的吹扫气量,并在油环处注入塑料质的液体填料,更换压盖填料函的填料,从而实现不停工检修的目的。填料函
18、的配置见“图4.2.14”填料函结构。 a) 压盖填料函内至少应放置四圈方形截面的填料,第一圈及最后一圈为夹铜丝的编织的石墨石棉盘根,中间二圈为柔性石墨填料圈。 b) 在主填料函内放置十圈方形截面的填料,对称布置在油环的两侧。每侧前后圈为夹铜丝石墨石棉盘根;中间三圈为柔性石墨填料圈。 c) 在填料函的油环截面上,应设置一个DN15的注油管,管上应装有针形阀和注油嘴。 d) 在主填料函的底部放置一个衬套作为阀杆的支承。 e) 填料函的内侧应设置一个DN15,配有PN2.5(2.5Mpa)管法兰的吹扫管,用以吹扫并冷却阀杆,在吹扫管的下端要有一个ZG1/2的排放管塞。与导轨吹扫介质相同,允许采用压
19、力为0.5MPa的压缩空气或1.0MPa的饱和蒸汽,需要的耗气量为1520Nm3/hr或12Kg/hr,蒸汽量由工艺安装在进气管路上设降压孔板限压。4.2.15 内部衬里 a) 在阀体和阀盖内应尽可能多地铺设耐磨衬里,以抵御催化剂的冲刷。 b) 单层耐磨衬里的铺设按BA10-11-5-95的要求进行。 c) 双层衬里的铺设按BA10-11-5-95的要求进行 d) 衬里两端一般设6mm厚的挡板和端板。端板距阀体端面的距离一般不小于100mm。挡板高30mm。端板上要开膨胀缝。4.3 垫片4.3.1 园形法兰采用带内加强环缠绕式垫片。垫片用0Cr18Ni9的不锈钢带和柔性石墨带缠绕而成,垫片规格
20、按JB4705-92缠绕垫片选用。4.3.2 矩形法兰采用复合型垫片,用2.5mm厚的OCr18Ni9不锈钢板作基板;二侧复以0.4mm厚的柔性石墨带,垫片的宽度视法兰的大小不同,一般为812mm。4.4 阀板4.4.1 阀板按简支梁计算强度,最大允许挠度应不大于0.13mm。4.4.2 T型槽要设在阀板的背面,使阀杆头部免遭催化剂的冲刷见“图4.4.2”。4.4.3 阀板全关闭时,对于单动滑阀来说,阀板前端面A距阀口前端边缘的距离应为50mm,阀板后端面B及阀板两侧面C、D距阀口后端边缘和阀口两侧边缘均应等于或大于60mm。对于双动滑阀来说,阀板全关时中心余隙按工艺要求定,阀板两侧面C、D距
21、阀口两侧边缘距离以及阀板后端B距阀口后端边缘距离应等于或大于60mm。见图“4.4.2”。4.4.4 阀板的滑动面有两种设计:L形和形见“图4.4.2”。4.4.5 阀板的结构尺寸如“图4.4.2”所示。L1,L2由设计者根据阀口尺寸及本规定要求定;h根据设计压差计算。开口面积1250cm2 b40 C60 a26.5。4.4.6 阀板T型槽E面与阀杆头部的间隙根据计算节流锥热膨胀量(按设计温度减20的温度计算)+5mm的数值选取。4.4.7 如”图4.4.2”所示,在各滑动面的全长上须喷焊或堆焊司太立6号硬质合金材料,加工后的合金层厚度不得小于3mm。施焊前,各边应倒圆3mm,施焊后各边应磨
22、出1.5mm的圆角。4.4.8 阀板上安装龟甲网,其前端结构如“图4.4.2”所示焊有隔板,隔板之间的距离大约为25mm,上下隔板错开斜布置,隔板与龟甲网之间用档板隔开。4.4.9 阀板的磨损面应尽可能多地铺设耐磨衬里,衬里的铺设按BA10-11-5-95的要求进行。4.4.10 衬里烘干后阀板耐磨衬里面必须磨平,其粗糙度不低于。4.5 阀座圈4.5.1 调节式单动滑阀的阀口形状有正方形或前半部是圆形,后半部是矩形两种。切断式单动滑阀阀口形状为圆形。4.5.2 阀口棱角部应倒圆,圆角半径为50mm。4.5.3 阀座圈上催化剂冲刷的部位应铺设耐磨衬里见“图4.5.3”,铺设的方法按 BA10-1
23、1-5-95的要求进行。 隔板的安装和阀板相同。 密封面上的衬里宽度不小于60mm,并且应高于阀座圈的金属基体,使金属基体免受催化剂的冲刷。4.5.4 衬里烘干后,阀座密封面必须磨平,其粗糙度与阀板面相同。4.6 导轨4.6.1 与阀板的滑动面相对应,导轨有L形和形两种如“图4.6.1”4.6.2 “图4.6.1”所示,在导轨整个长度上喷焊或堆焊司太立6号硬质合金材料,加工后金属层厚度不得小于3mm;在导轨滑道的下侧面上再敷设一层司太立1号硬质合金材料,加工后司太立1号合金层厚度同样不应小于3mm。 焊接前,各边应倒圆3mm,施焊后各边应磨出1.5mm的圆角。4.6.3 为防止催化剂堆积,在导
24、轨滑道面开60通槽,其间距为80mm,见“图4.6.3”所示,L,h尺寸由设计计算定。4.6.4 导轨应用足够的长度和强度来支承阀板,当阀板在全开或全关位置上时,允许导轨比阀板的滑动面短50150mm,视计算而定。4.6.5 为便于阀板的安装与拆卸,导轨长度除满足上述要求外,导轨外端面距侧阀口端面的距离应等于或小于1/2阀板长度。见“图4.6.1”4.6.6 导轨内端面距阀口边缘的距离应大于60mm,以免受催化剂的直接冲刷,见“图4.6.1”。4.6.7 导轨滑道与阀板接触面宽度不小于20mm,见“图4.6.3”,开口面积1250cm2,C25mm。4.7 间隙要求 阀板与阀座圈、阀板与导轨之
25、间的各部间隙,如图“图4.2.6-1”和“图4.2.6-2”A-A所示,过大的间隙会导致内部零件磨损过快。4.8 阀杆4.8.1 阀杆应在设计温度下能承受驱动装置的最大推拉力而不发生弯曲变形。阀杆结构见“图4.8.1”。4.8.2 阀杆头部采用T形结构,为了避免应力集中,T形头与杆部采用圆角过渡,圆角半径取R3,见“图4.8.2(a)”。 a) T形头的大小应足以保证其台肩所承受的弯曲应力和挤压应力,不致超过材料的许用应力值。 b) 阀杆的头部与阀板T形槽之间,轴向要留有0.5mm的间隙供阀板自由滑动,避免阀杆弯曲。4.8.3 口径350mm以下的滑阀,其阀杆头部允许采用普通闸阀阀杆的结构形式
26、,见“图4.8.2(b)”。4.8.4 采用风动驱动装置的滑阀,阀杆上应设计有后座面,当滑阀在全开位置上时,后座面应靠在阀盖上,以限制阀板的开启位置。全关位置是依靠设置在传动丝杠端部的挡块来限位的。4.9 螺栓4.9.1 内部螺栓的直径应不小于20mm,拧入深度为1.25倍的直径,并应采用普通粗牙螺纹。内外螺纹公差选用6H/6e配合。4.9.2 内部螺栓装配时,螺栓的螺纹上应涂以二硫化钼润滑剂或氢氧化镁,防止螺纹在高温下咬合。4.9.3 内部螺栓装配并调整后,应将每个螺母点焊牢。4.10 平衡吊挂4.10.1 滑阀应设计有平衡吊挂,以吸收管道系统热膨胀加在滑阀上的载荷。4.10.2 平衡吊挂有
27、恒力弹簧吊挂和平衡重块两种,通常使用恒力弹簧吊挂。4.10.3 吊挂的负载以等于或略大于驱动装置的重量为宜,取1890N。吊挂的移动距离及方向由设备专业根据管道系统热膨胀的大小及方向提供。5 材料5.1 阀体部分所用的主要材料及用途如下:5.1.1 0Cr18Ni9(GB4238-92)板材 适用于780以下的节流锥、热壁筒体。5.1.2 ZGOCr18Ni9(GB2100-80)铸件 适用于780以下使用的节流锥、阀板、阀座圈。5.1.3 0Cr18Ni9锻钢和棒材 适用于780以下导轨、内部螺母。5.1.4 4Cr14Ni14W2Mo(GB1221-84)锻件 适用于780以下使用的阀杆。
28、5.1.5 ZG1Cr5Mo(GB1221-84)铸件 适用于550以下使用的热壁铸造阀体和阀盖。5.1.6 除了T形头和螺纹部分外,阀杆表面应喷焊一层Ni60或其它类似的硬质合金材料,喷焊层加工后的厚度不小于0.5mm。5.1.7 GH33棒材或锻件 适用于780使用的内部螺栓。5.1.8 GH180棒材或锻件 适用于900使用的导轨、阀杆、内部螺栓、螺母。5.1.9 GH180板材 适用于900的节流锥。5.1.10 GH180铸件 适用于900使用的阀板、阀座圈、节流锥。5.1.11 30CrMoA(GB3077-88)棒材 适用于500以下螺栓、螺母。5.1.12 15CrMo(GB3
29、077-88)板材 适用于550以下使用的热壁焊接阀体和龟甲网等零件。5.1.13 16MnR(GB700-88)板材 适用于冷壁焊接阀体和阀盖。5.2 材料的化学成分和机械性能应符合有关标准的规定。5.3 奥氏体不锈钢材料的含碳量不低于0.04%。6 制造技术要求6.1 焊接6.1.1 阀体和阀盖等受压部件的焊接应符合GB150-1998钢制压力容器的要求。6.1.2 阀体的纵向焊缝不宜与任何开口相交。6.1.3 所有对接焊缝均为双面焊。6.1.4 应选择与母体材料化学成分相同的焊条焊接,对于两种不同材料的母体焊接,应选择与合金元素含量高的母体成分相同的焊条焊接。6.1.5 受压焊缝(对接焊
30、缝和角焊缝)应进行射线或超声波探伤检查,探伤长度占焊缝总长度的50%,检查结果应符合JB4730-94第二篇“焊缝射线透照检测中的级为合格,或符合JB4730第三篇“超声检测”中的级为合格。6.2 喷焊或堆焊6.2.1 阀板、导轨和阀杆应根据上述有关部分的要求喷焊或堆焊硬质合金材料。6.2.2 硬质合金喷焊或堆焊层加工后应进行液体渗透检查。 液体渗透检查的方法可按JB7340“压力容器无损检测”,缺陷累积长度级为合格。6.2.3 阀杆表面的喷焊层不允许有任何裂纹和分层等影响填料密封的缺陷存在。6.2.4 允许在阀板和导轨的喷焊或堆焊层上存在一些缺陷,其中裂纹应该是不连贯的,且在长200mm内裂
31、纹的总数不超过45条,其中0.1mm宽度的裂纹不超过3条,裂纹深度不超过硬质合金层的厚度。 此外,硬质合金层不允许有片状脱落,但是允许在200mm长度内有23个直径小于10mm,深度不大于1mm的缺肉。6.3 衬里 衬里的铺设方法及质量要求按BA10-11-5-95的要求进行。6.4 水压试验6.4.1 阀体和阀盖在消除焊接应力的热处理,并经检查合格后,铺设衬里前应进行水压试验。6.4.2 水压试验的压力按下述公式确定: MPa (6.4.2) 式中: PT 内压容器的试验压力,Mpa P 设计压力,MPa 试验温度下材料的许用应力,MPa(20) t 设计温度下材料的许用应力MPa 之比值最
32、高不超过1.8,且PT值不得小于0.7MPa6.5 操作性能试验6.5.1 出厂前,滑阀必须作操作性能试验,各项指标符合图纸的要求。6.5.2 出厂前滑阀还应在全开、50%开度和全关三个位置上测定阀板和阀座圈、阀板和导轨之间的各部间隙,并应符合图纸的要求。6.6 油漆6.6.1 滑阀的油漆按JB2536-80和制造厂的规程进行。6.6.2 滑阀在油漆前进行喷丸除锈处理。6.6.3 除了不锈钢和加工的表面外,在滑阀的外表面刷油漆三遍;底漆一遍,面漆两遍。7 附图图4.2.6-2 冷壁式单动滑阀图4.2.11 阀开口偏心示意图4.2.12 节流锥焊接结构图4.5.3 阀座圈图4.2.14 填料函结构附录A 编制说明1 本标准代替BA10-11-1-95。2 本标准条文层次、条文编排等按照院标CT0304-1998标准编制规定进行。
- 温馨提示:
1: 本站所有资源如无特殊说明,都需要本地电脑安装OFFICE2007和PDF阅读器。图纸软件为CAD,CAXA,PROE,UG,SolidWorks等.压缩文件请下载最新的WinRAR软件解压。
2: 本站的文档不包含任何第三方提供的附件图纸等,如果需要附件,请联系上传者。文件的所有权益归上传用户所有。
3.本站RAR压缩包中若带图纸,网页内容里面会有图纸预览,若没有图纸预览就没有图纸。
4. 未经权益所有人同意不得将文件中的内容挪作商业或盈利用途。
5. 装配图网仅提供信息存储空间,仅对用户上传内容的表现方式做保护处理,对用户上传分享的文档内容本身不做任何修改或编辑,并不能对任何下载内容负责。
6. 下载文件中如有侵权或不适当内容,请与我们联系,我们立即纠正。
7. 本站不保证下载资源的准确性、安全性和完整性, 同时也不承担用户因使用这些下载资源对自己和他人造成任何形式的伤害或损失。