宝钢碱性氧气转炉炼钢生产及洁净钢控制外文翻译、中英对照、英汉互译
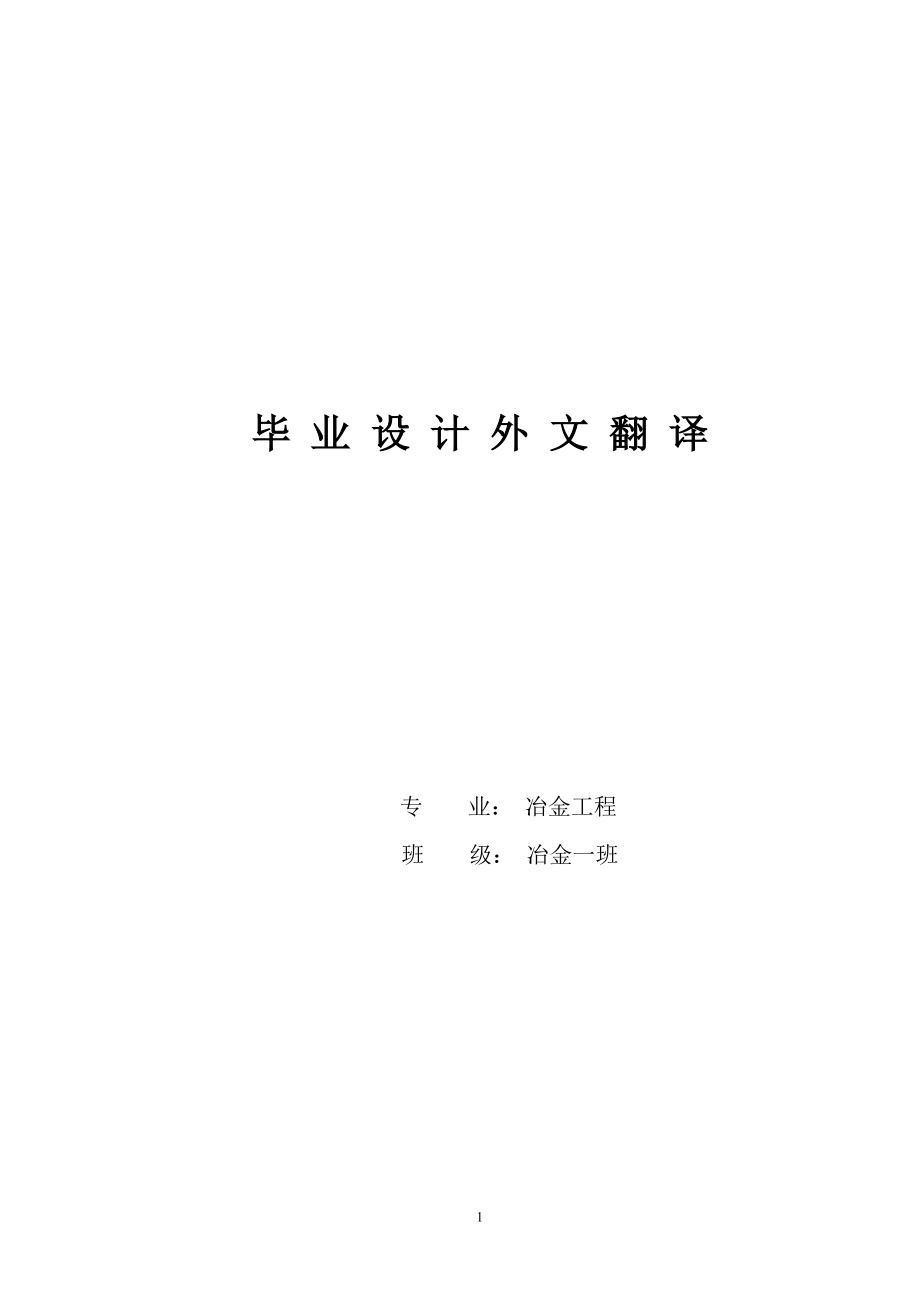


《宝钢碱性氧气转炉炼钢生产及洁净钢控制外文翻译、中英对照、英汉互译》由会员分享,可在线阅读,更多相关《宝钢碱性氧气转炉炼钢生产及洁净钢控制外文翻译、中英对照、英汉互译(19页珍藏版)》请在装配图网上搜索。
1、毕 业 设 计 外 文 翻 译 专 业: 冶金工程 班 级: 冶金一班 Basic oxygen furnace based steel-making processes and cleanliness control at BaosteelL. Zhang*1, J. Zhi2, F. Mei2, L. Zhu2, X. Jiang2, J. Shen2, J. Cui2, K. Cai3 and B. G. Thomas4Optical microscopy, total oxygen measurements and slime tests have been conducted to
2、quantify the size distribution and amount of inclusions at various processing steps during basic oxygen furnace (BOF) based steel production at Baosteel. The effects on steel cleanliness of specific operational improvements during steel refining and continuous casting have been investigated. Such im
3、provements to these processes and the resulting level of steel cleanliness at Baosteel are summarised in the present paper. Ladle slag reduction lowers FeO + MnO in the slag to below 5%, decreasing steel reoxidation by the slag. Calcium treatment by CaSi wire injection during ladle furnace (LF) refi
4、ning is used to modify inclusions . Slag detection is employed at the ladle bottom during continuous casting. Flow control devices, CaO containing filters and high CaO based basic powder with CaO/Si024 are used in the tundish to remove more inclusions. With this BOF based steelmaking process, impuri
5、ty levels can be controlled to achieve-total oxygen (TO)16 ppm, S5 ppm, P35 ppm, N29 ppm, H1 ppm in line pipe steels, and C16 ppm, TO19 ppm, N15 ppm in interstitial free (IF) steels.Keywords: Clean steel, Inclusions, Impurity elements, Interstitial free steel, Line pipe steelIntroductionThe importan
6、ce of clean steel in terras of product quality is increasingly being recognised. Clean steel requires control of the size distribution, morphology and composition of non-metallic oxide inclusions in addition to the amount. Furthermore, sulphur, phosphorus, hydrogen, nitrogen and even carbon1,2 shoul
7、d also be controlled to improve the steel properties. For example, ,formability, ductility and fatigue strength worsen with increasing sulphide and oxide inclusion contents. Lowering the carbon and nitrogen enhances strain aging and increases ductility and toughness. Hardenability and resistance to
8、temper embrittlement can be enhanced by reducing phosphorus. The definition of clean steel varies with the steel grade and its end use. For example, interstitial free (IF) steel requires both carbon and nitrogen to be 30 ppm; line pipe steel requires sulphur, phosphorus and total oxygen (TO) all to
9、be 30 ppm,low hydrogen, low nitrogen and suitable Ca/S and bearing steel requires the total oxygen to be less than 10 ppm.3 In addition, many applications restrict the maximum size of inclusions 3,4 , so the size distribution of inclusions is also important. Baoshan Iron & Steel Co., Ltd (Baosteel)
10、is currently the largest steel company in China. Its annual steel production was 115 million tonnes in 2003, 119 million tonnes in 2004 and 14.0 million tonnes in 2005. With regard to the basic oxygen furnace (BOF) based steelmaking route, there are three 300 t and two 250 t BOFs; several steel refi
11、ning units, including one CAS-OB unit (controlled argon stirring-oxygen blow), two RH (Ruhrstahl-Heraeus) degassers and one ladle furnace (LF). Since 1990, efforts to improve steel cleanliness have focused on developing steelmaking practices to lower TO, N, S, P, H and C levels to achieve low carbon
12、 aluminium killed (LCAK) steel. For LCAK steel and IF steel, the production process is BOFRHcontinuous casting (CC), and for line pipe steel, the process is BOFRHLFCC.Experimental method and examination of inclusions in steelExperimental methodsLadle steel samples were taken 500-600 mm below the top
13、 slag in the ladle, tundish steel samples from 300 mm above its outlet and mould steel samples from 150 mm below the meniscus and 300 mm away from the submerged entry nozzle (SEN) outports. The sampler was a cylindrical steel cup with a cone shaped copper cover to protect it from slag entrainment du
14、ring immersion. Attached to a long bar, the sampler was immersed deep into the molten steel, where the copper melted and the cup was filled. Small steel samples , 80mm in length and 30mm in diameter, were machined into 5 (dia.) x 5 mm cylinders for TO and nitrogen analysis, and 20 (dia.) 15 mm cylin
15、ders for microscope examination. The steel powders resulting from machining were used for analysis of the carbon, phosphorus and sulphur contents. Large Steel samples from the ladle and tundish, 200 mm in length and 80 mm in diameter, were machined into 60 (dia.) 150 mm cylinders; as shown in Fig. 1
16、. TO and nitrogen measurement. Analysis included the chemical composition of slag and steel samples, microscope examination of microinclusions, slime extraction of macroinclusions and SEM analysis of the morphology and composition of inclusions. Fig.1 Sampling locations for continuously cast slab: T
17、O total oxygenIn the present work, macroinclusions were those greater than 50 um in diameter. Most of these were detected in the residues extracted by electrolytic isolation (slime test) from the larger steel samples. The microinclusions data derive from microscopic assessments carried out on planar
18、 sections, most of which were smaller than 50 mMorphology and composition of typical inclusions The morphology ,composition and likely sources of typical inclusions found in LCAK steel samples form the ladle ,tundish and mound are shown in Figs.2 and 3 respectively.The morphologies included: (a) ang
19、ular aluminate(Fig.2 d and f and Fig.3b);(b)alumina cluster (Fig.2b and c);and (c) spherical silicate (Fig. 2a and c and Fig. 3a). a. ladle; b. tundish; c,d. mound; e,f. slab Fig.2 Typical inclusions from given samples examined by microscope (a) tundish (b) slabFig. 3 Typical inclusions from given s
20、amples extracted using slime method The possible sources were deoxidation products, reoxidation products or broken refractory lining bricks. In line pipe steel, besides these common inclusions, many nanoscale TiN inclusions were found along grain boundaries. These nano TiN changed from square to ell
21、ipsoid if combined with Ti2O3 , as shown in Fig. 4 5 a . compound inclusions with composition Ti2O3+MnS ; b. TiN inclusion Fig.4 Nanoprecipitates in line pipe steelTotal oxygen measurement is an indirect method of evaluating oxide inclusions in a steel.3 The total oxygen (TO) in the steel is the sum
22、 of the free oxygen (dissolved oxygen) and the oxygen combined as non-metallic inclusions. Free oxygen, or active oxygen, can be measured relatively readily using oxygen sensors. It is controlled mainly by equilibrium thermodynamics with deoxidation elements, such as aluminium. If %A1 =0.03-0-06, th
23、e free oxygen is 3-5 ppm at 1600C. Because the free oxygen does not vary much, the total oxygen is a reasonable indirect measure of the total amount of oxide inclusions in the steel. Owing to the small population of large inclusions in a steel and the small sample size for TO measurement (normally 2
24、0 g), it is rare to find a large inclusion in a sample. Even if a sample contains a large inclusion, it is probably discounted because of the anomalous high reading.Thus, the TO content actually represents the level of 50 um small oxide inclusions only. The current TO in IF and line pipe steel slabs
25、 at Baosteel is 16 ppm. The TO in the ladle, tundish, mould and slab in two typical sequences of LCAK steel is shown in Fig.5 , indicating that the TO decreased from the ladle to the tundish, to the mould and to the continuously cast slab. Fig.5 Total oxygen in steel from ladle to slab Ladle operati
26、ons to remove more inclusionsLadle slag reduction treatmentReoxidation to form alumina in the ladle during steel refining is mainly caused by Si02 in the slag and lining refractory, and MnO and FeO in the ladle slag, by the following reactions:3/2(Si02) + 2Al=(Al203) + 3/2Si 3(MnO) + 2Als = (Al203)
27、+ 3Mn 3(FeO) + 2Als = (A1203) +3FeSlag reduction treatment is carried out by adding aluminium and lime onto the top of the ladle slag to reduce its FeO and MnO content. The effect of ladle slag reduction treatment on the TO content in the steel is shown in Fig. 6. A larger FeO + MnO content in the l
28、adle slag corresponds to higher total oxygen. With the slag reduction treatment, MnO and FeO in the ladle slag were reduced to 5%, corresponding to 25 ppm in order to prevent solid alumina based inclusion clogs . Too much calcium can also generate CaS with a high melting point (2450C). Too much sulp
29、hur in the steel and too low a temperature also enables CaS generation. Baosteel practice indicates that 0.09 favours prevention of nozzle clogging (Fig. 17). Hence, Ca needs to be controlled within the range 25-50 ppm, and Ca/Al0-09, to avoid nozzle clogging problems.Control of nitrogen, carbon, su
30、lphur and phosphorus in steelNitrogenNormally, a large nitrogen content at tapping tends to result in a large nitrogen content in the slab. Thus, the control of nitrogen should mainly focus on lowering the nitrogen content during BOF blowing and preventing nitrogen pickup during tapping, steel refin
31、ing and continuous casting. Currently, at Baosteel, nitrogen during BOF steelmaking fluctuates from 11 to 43 ppm. Plant experiments indicate that when N is less than 30 ppm before RH treatment, N cannot be lowered further by RH treatment. Oxygen pickup is always many times greater than the measured
32、nitrogen pickup, owing to its faster absorption kinetics at the air/steel interface.7 In addition, nitrogen pickup is faster when the oxygen and sulphur contents are low.8 Thus, to reduce nitrogen pickup, deoxidation is best carried out after tapping, which is the current practice for clean steel gr
33、ades at Baosteel. The current nitrogen content of IF steel and line pipe steel slabs is 15-30 ppm, and nitrogen pickup from ladle to tundish can be controlled below 1.5 ppm by optimised shrouding, argon gas injection and fibre sealing at the tundish and SEN.CarbonThe greatest decarburisation is for
34、IF steel by converter treatment which can reach to higher than 90% and further decarburization for IF is by RH. Techniques to improve this operation include:(1) optimising initial C and O before degassinginto the ranges of 500-650 ppm and 300-450 ppm, respectively.(2) enlarging the snorkel diameter
35、from 500 to 750 mm and increasing the argon flowrate from 1000 to 3000 NL minT-1. After this treatment, C can be lowered to10ppm.The C pickup occurring during continuous casting is controlled below 6 ppm by the following techniques: (4)using low carbon, high viscosity mould flux, decreasing carbon p
36、ickup at the continuous casting mould from 5.5 to 1.8 ppm. (5) using carbon free ladle refractory lining(6)using high basic, low carbon tundish flux (CaO/SiO24)SulphurThe initial sulphur content of the molten iron at Baosteel is 200 ppm. After hot metal desulphurisation by injection of CaC2 powder o
37、r magnesium based powder, the sulphur decreases to 10-30 ppm. It is important to remove the top slag quickly after desulphurisation in order to decrease sulphur pickup. During the BOF steelmaking process, there is 10-30 ppm sulphur pickup, mainly from lime and scrap. To achieve an ultralow sulphur c
38、ontent, especially for line pipe steels, three desulphurisation methods during the steel refining process have been developed:(1) CaO-CaF2 flux is added to the vacuum chamber through the alloy addition hoppers; slag carryover from the BOF is controlled carefully for these heats, and ladle slag reduc
39、tion treatment is carried out to decrease the FeO content in the slag before steel desulphurisation; S is lowered from 28.4 to 16.2 ppm (2) After strong deoxidation, CaO-CaF2 powder is injected into the molten steel in the ladle by a lance below the up snorkel; S can be lowered from 61.9 to 35.8 ppm
40、 (3) A suitable emulsification condition, improving the reaction between slag and molten steel; S can be lowered from 67.0 to 8.7 ppm. This method can lower the sulphur below 10 ppm, so is currently used for the production of ultraclean line pipe steel. It should be noted that the MgO-CaO refractory
41、 lining and tundish flux may also remove some sulphur by the following reaction:(CaO)+2/3Al+S=(CaS)+1/3Al2O3PhosphorusFive different processing routes are used to achieve low phosphorus steel at Baosteel: (1) de-Si, de-P and de-S at hot metal treatment,followed by BOF steelmaking with a small slagco
42、ntent, lowering P to 120 ppm .(2) de-S at hot metal treatment, then the BOFprocess with a large slag content, lowering P to100 ppm.(3) de-Si, de-P and de-S at hot metal treatment,followed by BOF steelmaking with a large slagcontent, lowering P to66 ppm .(4) de-P at hot metal treatment, followed by B
43、OFsteelmaking with a large slag content, lowering P to 58 ppm .(5) double BOF steelmaking process, achieving 20 ppm P in the steel. The control of impurity elements at Baosteel has improved considerably during the past 15 years, as indicated in Table 1. Baosteel steel can now achieve TO16ppm, S5 ppm
44、, P35 ppm, N29 ppm, H1 ppm in line pipe steel, and C16 ppm, TO19ppm, N15ppm in IF steel. Currently, S + P + TO + N + H in line pipe steel can be maintained below 85-5 ppm, and C + TO + N in IF steel can be kept below 50 ppm.Table 1 Impurity content of line pipe steel and interstitial free (IF)steel
45、achieved at Baosteel,ppm Line pipe steel IF steel S P TO N H C N TO1996 32 134 35 47 2 50 24 501999 16 89 24 30 2 23 16 282003 9 54 16 30 1.5 16 15 192004 4.8 35.0 15.8 29.0 1.0 . . .Conclusions1. Techniques to improve steel cleanliness at Baosteel include ladle slag reduction treatment to lower FeO
46、 and MnO in the ladle slag to below 5% before steel refining, suitable CaSi wire injection in the ladle, ladle slag detection during pouring, development of a CaO based basic tundish flux, optimisation of flow control devices in the tundish and optimisation of mould flow to avoid mould slag entrainm
47、ent.2. Inclusions concentrate mostly within 20 mm of the slab surface. Some slabs experience occasional accumulation at one-quarter to one-half slab thickness from the inner radius.3. Castability has been improved by an improvement of steel cleanliness, the use of optimal calcium treatment to preven
48、t nozzle clogging and application of a breakout prediction system at the caster.Currently, the impurity elements in steel can be controlled to TO16 ppm, S5 ppm, P35 ppm, N29 ppm, H1 ppm for line pipe steels, and C16 ppm, TO19 ppm, N4的高含量等技术来进一步去除杂质。随着碱性氧气转炉炼钢过程的发展,管线钢杂质含量可控制在总氧 (TO)16ppm, S5ppm, P19
49、ppm, N15ppm H1ppm。 IF 钢可达到C16ppm, TO19ppm, N15ppm。关键词:洁净钢 夹杂 杂质元素 超冲深无间隙原子钢 管线钢 引言: 洁净钢质量的重要性正逐步得到人们的认可。洁净钢除了对杂质总量的要求外还要求对非金属氧化物夹杂的形状分布,形态和组成进行控制。另外,还对 S, P, H, N甚至 C 进行控制来进一步提高钢的性能1,2。例如,硫化物和氧化物夹杂会使钢的可锻性、塑性和疲劳强度恶化,降低碳、氮含量会提高钢的应变时效以及塑性和韧性,磷含量的降低对淬透性和抗回火脆性均有所改善。“洁净钢”根据钢号的不同可以有多种要求。例如:IF 钢要求 C 和 N 总量
50、30ppm;管线钢要求S, P, 和 TO 30ppm,低 H 低 N 和适当的 Ca/S;轴承钢要求总氧量 10ppm3。另外,许多用途都要限制夹杂物的最大形状3,4,因此对杂质的形状分布也有重要要求。宝钢是中国最大的钢铁企业,2003年产钢量为 1150 万吨,2004年 1190 万吨,2005年达到 1400 万吨。炼钢系统现有3座300吨,2座250吨碱性氧气转炉。精炼设施包括1座 CAS-OB,2座RH精炼炉和1座LF精炼炉。1990年以来,洁净钢的研究主要集中在炼钢过程中对TO, N, S , P, H 和C的含量控制来生产铝脱氧低碳镇静钢(LCAK)。LCAK钢和IF 钢工艺流
51、程为 BOFRHCC ;管线钢流程为 BOFRHLFCC。实验方法和钢中杂质元素检测:实验方法: 钢包钢样从钢渣液面以下500600mm处取样,中间包钢样自出口300mm以上处取样,结晶器钢样由液面150mm以下,离浸入式水口300mm处取样。试样做成带圆锥形铜罩的圆柱形钢杯,以防进入时被钢渣冲掉。试样绑在一个长杆上深入熔池,待铜罩融化后钢液便进入钢杯。小金属试样长80mm,直径30mm,加工成5(直径)5mm圆柱试样,分析总氧和氮含量,20(直径)15mm圆柱试样进行显微镜微观分析,加工所产生的钢屑用于C, P, S 含量分析。钢包和中间包的大试样长200 mm,直径50 mm,加工成60(
52、直径)150mm圆柱。如图1所示总氧和氢含量测定。这个分析包括渣样和钢样的化学组成,细微夹杂物的显微观测,渣泥中提取的宏观夹杂物以及夹杂物的表面形态和组成的扫描电子显微镜分析。图 1 板坯试样:总氧量现阶段,所谓宏观夹杂是指直径大于50m的夹杂,大部分从钢样残泥中电解析出(泥浆测试法);大部分小于50m的微观夹杂的数据是由显微镜观测到的平面部分。典型夹杂的表面形态和组成LCAK钢样中典型夹杂的表面形态,组成和来源如图2,图3所示。这些表面形态包括 :(a) 呈角状的铝酸盐(图2 d和f,图3 b);(b) 氧化铝簇(图2 b和e)和(c)球状硅酸盐(图2 a和c,图3 a)。 图2 a 钢包;
53、 b 中间包; c d 结晶器; e f 板坯(a)中间包 (b)板坯图 3 泥浆法提取的试样中的典型夹杂这些物质可能为脱氧产物,二次氧化产物或残余的耐火砖的成分。在管线钢中,除这些普通的夹杂外,在晶界处还发现许多极细的TiN颗粒。这些细的TiN杂质如果和Ti2O3化合则他们的形状将由方形转变为椭圆形, 图 4如图4所示5 a. 由Ti2O3+MnS组成的复合夹杂; b. TiN夹杂钢中总氧量的测量是通过估测钢中氧化物夹杂而间接测量的3。总氧量TO是钢中自由氧(未溶解的氧)和与金属夹杂结合的氧的总和。“自由氧”又称为活氧,可由氧传感器方便的测出。它主要受脱氧元素如铝的热力学平衡所控制。 160
54、0C时,如果%Al=0.030.06,则自由氧含量为35 ppm。由于自由氧含量比较稳定,这样可以间接测量钢中氧化物夹杂总量。实验中由于测量总氧的试样比较小并且杂质中氧化物含量不高,因此试样中很少能找到大的氧化物夹杂,即使试样中包含了大的夹杂也会由于读数偏大而无法测量。这样一来,总氧含量实际上仅仅代表了小于50m的小氧化物夹杂的含氧量。宝钢现在的IF 钢和管线钢中的总氧含量已小于16 ppm。两套系统中钢包,中间包,结晶器和板坯中的的总氧含量如图5所示,表明总氧量从钢包到中间包,结晶器,连铸坯依次减少。 图 5 从钢包到板坯的总氧量钢包操作进一步去杂:钢包还原渣处理:钢包中由炉渣和耐火材料内衬
55、产生的SiO2以及钢包渣中MnO和FeO和Al反应生成Al2O3,反应如下:3/2(Si02) + 2Al=(Al203) + 3/2Si 3(MnO) + 2Als = (Al203) + 3Mn 3(FeO) + 2Als = (A1203) +3Fe通过向钢包渣中加入铝和石灰来降低渣中FeO和MnO含量的方法来造还原渣,这个还原反应对钢渣中的总氧含量的影响如图6所示。钢渣中随FeO和MnO含量升高则总氧量也升高。在所造的还原渣中,渣中的MnO和FeO减少到小于5%,对应中间包中的总氧量小于20 ppm。 图 6 钢渣中FeO和MnO的含量对总氧的的影响钙处理铝脱氧镇静钢中如果水口堵塞会引
56、发一系列问题,如降低拉速,产生不对称液流,结晶器钢液面波动等导致夹渣,有时还会发生漏岗。防止水口堵塞最好的方法是连铸前去除尽量多的杂质,并且这是对于严格要求钢的韧性的可行性的唯一手段6。 宝钢精炼时向钢液中喂入CaSi线,氧化铝和氧化钙生成铝酸钙,如果生成的铝酸钙熔点低则可以使水口堵塞问题得到改善。该处理可能生成的化合物包括CA6,CA2,CA,C12A7和C3A,C和A分别代表CaO和Al2O3。由于前两个熔点高于1700C所以应该避免。宝钢研究表明为防止固体Al2O3堵塞应使Ca大于25ppm。但太高的Ca会产生高熔点的CaS(2450C),太高的S或太低的温度也会产生 CaS。实践证明钢中Ca 0.09时也会防止堵塞。因此钙应在2550 ppm范围内,并且Ca/Al0.09。钢中氮,碳,磷,硫的控制氮通常情况下由于出钢时钢水含氮量高而导致板坯中含氮量高,因此应注重在转炉吹炼过程中降氮,防止出钢过程中增氮以及在精炼和连铸过程中对氮进行控制。宝钢碱性氧气转炉炼钢条件下可使氮含量波动在1143 ppm之间,实验证明在精
- 温馨提示:
1: 本站所有资源如无特殊说明,都需要本地电脑安装OFFICE2007和PDF阅读器。图纸软件为CAD,CAXA,PROE,UG,SolidWorks等.压缩文件请下载最新的WinRAR软件解压。
2: 本站的文档不包含任何第三方提供的附件图纸等,如果需要附件,请联系上传者。文件的所有权益归上传用户所有。
3.本站RAR压缩包中若带图纸,网页内容里面会有图纸预览,若没有图纸预览就没有图纸。
4. 未经权益所有人同意不得将文件中的内容挪作商业或盈利用途。
5. 装配图网仅提供信息存储空间,仅对用户上传内容的表现方式做保护处理,对用户上传分享的文档内容本身不做任何修改或编辑,并不能对任何下载内容负责。
6. 下载文件中如有侵权或不适当内容,请与我们联系,我们立即纠正。
7. 本站不保证下载资源的准确性、安全性和完整性, 同时也不承担用户因使用这些下载资源对自己和他人造成任何形式的伤害或损失。