机械制造工艺学课程设计设计左支座零件的机械加工工艺规程及工艺装备(全套CAD图纸)
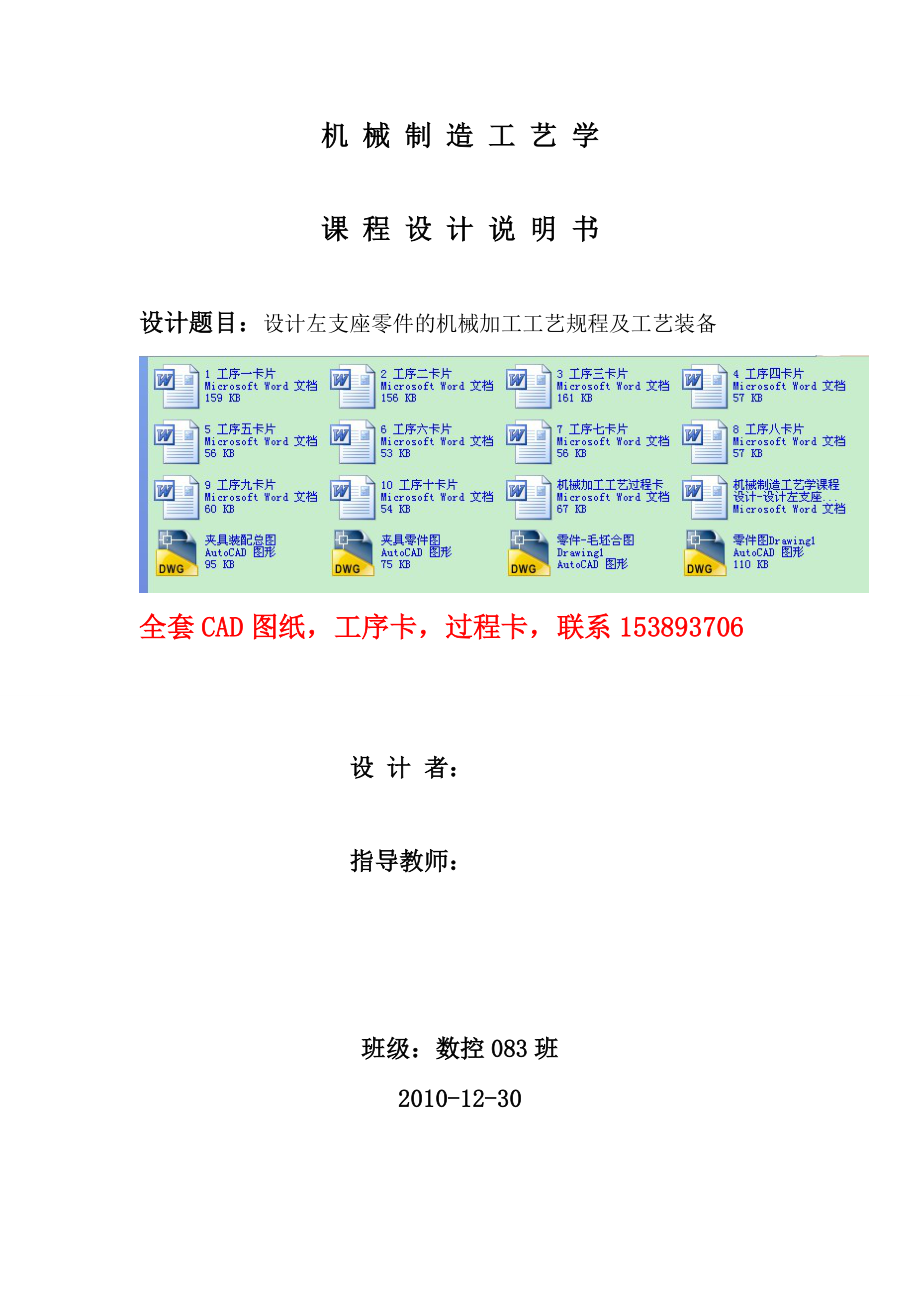


《机械制造工艺学课程设计设计左支座零件的机械加工工艺规程及工艺装备(全套CAD图纸)》由会员分享,可在线阅读,更多相关《机械制造工艺学课程设计设计左支座零件的机械加工工艺规程及工艺装备(全套CAD图纸)(18页珍藏版)》请在装配图网上搜索。
1、机 械 制 造 工 艺 学课 程 设 计 说 明 书设计题目:设计左支座零件的机械加工工艺规程及工艺装备全套CAD图纸,工序卡,过程卡,联系153893706设 计 者: 指导教师:班级:数控083班2010-12-30机械制造工艺学课程设计任务书题目:设计左支座零件的机械加工工艺规程及专用夹具内容:(1)零件一毛坯合图 1张(2)机械加工工艺规程卡片 10张(3)夹具装配总图 1张(4)夹具零件图 1张(5)课程设计说明书 1份原始资料:该零件图样一张;生产类型为中批生产。班 级:数控083学 生: 指导老师: 时 间: 2010年 12月 30日目 录 序言:设计目的 1 一、零件的分析
2、1 1、零件的作用 2、零件的工艺分析 二、确定毛坯,画毛坯零件合图 5 1、选择毛坯 2、确定机械加工余量,毛坯尺寸和公差 3、零件的毛坯图(如附图二所示) 三、工艺规程设计 6 1、定位基准的选择 2、零件表面加工方法的选择 3、制定工艺路线 四、加工工序设计 9 1、选择加工设备及工艺装备 2、确定工序尺寸 五、确定切削用量及基本时间 11 1、切削用量 2、时间定额计算 六、夹具设计 14 1、确定设计方案 2、计算夹紧力并确定螺杆直径 3、定位精度分析设计目的:机械制造工艺学课程设计是在学完了机械制造工艺学(含机床夹具设计)和大部分专业课,并进行了生产实习的基础上进行的一个教学环节。
3、这次设计使我们能综合运用机械制造工艺学中的基本理论,并结合生产实习中学到的实践知识,独立地分析和解决工艺问题。初步具备了设计一个中等复杂程度零件(左支座)的工艺规程的能力和运用夹具设计的基本原理和方法,拟订夹具设计方案,完成夹具结构设计的能力,也是熟悉和运用有关手册,图表等技术资料及编写技术文件技能的一次实践机会,为今后的毕业设计及未来从事的工作打下良好的基础。一、零件的分析1、零件的作用左支座零件,是机床上的一个支座。支座孔中安装轴,侧面的耳孔中安装螺栓可将轴夹紧,使轴固定。松开螺栓后轴可转动或滑动,也可以利用夹紧程度的不同来调节孔与轴之间的间隙,零件下底座有两个定位销孔,用两个定位销将其定
4、位。2、 零件的工艺分析 由零件图可知,其材料为HT200,该材料为灰铸铁,具有较高强度,耐磨性,耐热性及减振性,适用于承受较大应力和要求耐磨零件。(零件图见附图一)由零件图可知,该零件的主要加工面分为:底座大端面A面,粗糙度为3.2;80H9内孔表面,粗糙度为1.6;底座的四个13的通孔和四个20的沉孔,内孔表面的粗糙度为12.5,过渡表面的粗糙度为6.3;底座10销孔的内孔表面粗糙度为1.6;侧面耳孔43孔、21孔、25H7孔、38孔的内孔表面粗糙分别为12.5、12.5、3.2、12.5;其过渡面的粗糙度分别为6.3、12.5;M8-7H、M10-7H深18的螺纹孔的表面粗糙度为6.3;
5、宽度为5mm槽的粗糙度为12.5。 由于10销孔的表面粗糙度为1.6,要求较高,而且直径也较小,所以应采用钻-铰的加工方法,而80H9内孔表面的表面粗糙度为1.6,且与A面有垂直度要求,应分为粗镗精镗的加工方法。2、 确定毛坯,画毛坯零件合图(附图二)1、 选择毛坯根据零件材料确定毛坯为灰铸铁HT200,由于零件在机床工作过程中起支撑作用,所以受的动载荷和交变载荷也较小。由于是中批量生产,而且零件的轮廓尺寸不大,故毛坯的铸造方法选用砂型机器造型,又由于零件的80mm孔需铸出,故还应安放型芯。此外,为消除残余应力,铸造后应安排人工时效。参考文献1表2-1,该种铸件的尺寸公差等级CT为812级,加
6、工余量等级MA为G级。故取CT为9级,MA为G级。铸件的分型面选择通过竖直槽的对称轴线,且与A面垂直的面。浇口位置分别位于耳座两侧。2、 确定机械加工余量,毛坯尺寸和公差参考文献1:查表2-3、表2-4确定RMA、CT当外表面作机械加工时:RMA=1.4,CT=2.2;有公式:R=F+2RMA+CT/2=100+2*1.4+2.2/2=103.9mm当内腔作机械加工时:RMA=2,CT=2.2;有公式:R=F-2RMA-CT/2=80-2*2-2.2/2=74.9mm 其余尺寸由铸造获得 估计质量为2.0kg通过计算法确定各表面的总加工余量如表2-1所示。表2-1 各加工表面总余量加工表面基本
7、尺寸(mm)加工余量等级加工余量数值(mm)说 明底面A面140G4mm单侧加工80孔80H2.5mm孔降一级,双侧加工 参考文献1表2.3,用查表法可得铸件主要尺寸的公差,如表2-2所示。表2-2 主要毛坯尺寸及公差(mm)主要面尺寸零件尺寸总余量毛坯尺寸公差CT底座轮廓尺寸1401402.580孔802.5+2.5752.2A面距上端面10041042.5圆柱R55R552.5耳座80802.23、 零件的毛坯图(如附图二所示)3、 工艺规程设计1、 定位基准的选择精基准的选择:左支座底面为边长140 mm的正方形、中间80的孔、10的销孔及四个4-13的孔既是装配基准,又是设计基准,用它
8、们作精基准,能使加工遵循“基准重合”的原则,实现左支座零件“一面二孔”的典型定位方式。此外底面的面积较大,定位比较稳定,夹紧方案也比较简单可靠,操作方便。粗基准的选择:按照有关粗基准的选择原则,当零件有不加工表面的时候,应该选取这些不加工的表面为粗基准;若零件有若干个不加工表面时,则应该选择与加工表面相对位置精度要求较高的不加工表面作为粗基准.现取R55的外圆柱表面作为定位基准,以消除X,Y的转动和X,Y的移动四个自由度,再用80H9的小端端面可以消除Z周的移动。2、 零件表面加工方法的选择该零件毛坯包括底座下端平面、一个大孔、六个阶梯孔、两个销孔、两个螺纹孔、两个缝槽、一个内孔倒角,材料为H
9、T200。根据各表面加工要求和各种加工方法能达到的经济精度,以公差等级和表面粗糙度要求,参考机械制造技术基础课程设计指导教程有关资料,其加工方法选择如表3-1所示。表3-1左支座零件各表面加工方案加工表面尺寸精度表面粗糙度Ra/um加工方案备注底面A面IT93.2粗铣精铣表1-880H9孔IT91.6粗镗精镗表1-74-13孔IT1212.5钻扩表1-72-10销孔IT91.6钻铰表1-74-20孔IT1212.5粗铣表1-8内螺纹M8-7HIT76.3钻扩攻螺纹表1-7内螺纹M10-7HIT76.3钻扩攻螺纹表1-738孔IT1212.5粗铣表1-825H7IT73.2粗铣精铣表1-821I
10、T1212.5粗铣表1-843IT1212.5粗铣表1-8垂直缝槽IT1212.5粗铣表1-8水平缝槽IT1212.5粗铣表1-8倒角IT12粗铣表1-83、制定工艺路线遵循“先基准后其他”原则,首先加工底面A面、80的孔、10的销孔及四个4-13的孔;遵循“先粗后精”原则,先安排粗加工,后安排精加工;遵循“先主后次”原则,先主要表面后次要表面;遵循“先面后孔”原则,确定如下表3-2所示加工工艺路线:表3-2左支座加工工艺路线序 号工 序 内 容简 要 说 明铸造时效消除内应力涂底漆防止生锈10粗铣削A面先加工基准面20粗镗80H9孔留精镗余量30钻4-13孔、钻10的孔留扩铰加工余量40粗铣
11、20孔用立铣刀50粗铣削43、21孔用立铣刀60粗铣削38、25孔留25孔精铣削余量70粗铣削垂直槽用锯片铣刀80粗铣削水平槽用锯片铣刀90粗铣80H9内孔边缘倒角粗加工结束100精铣削A面精加工开始110铰削10销孔用自动铰削120扩4-13孔保证表面精度要求130精铣25H7孔用立铣刀140精镗80H9孔精加工结束150钻、扩、攻螺纹孔M10-7H、M8-7H工序分散,平衡节拍160加工倒角R15、R10、R3钳工工作台170检验180入库四、工艺设计1、 选择加工设备及工艺装备由于生产类型为中批量生产,故加工设备宜以通用机床为主,辅以少量专用机床。其生产方式为以通用机床加专用夹具为主,辅
12、以少量专用机床的流水生产线。工件在各机床上的装卸及各机床间的传送均有人工完成。 工序一:粗铣、精铣A面, 考虑到工件的定位夹紧方案及夹具结构设计等问题,应选立式铣床,故选常用的X52K型铣床。选直径D为200镶齿套式面铣刀(参考文献1表3-23)、专用夹具和三用游标卡尺。 工序二:粗镗、精镗80H9孔,宜选用卧式镗床,故选常用的T6025镗床。选功率为1.5KW的1TA20镗削头(参考文献2表3.2-44),选用镗通孔的镗刀、专用夹具、三用游标卡尺。 工序三:钻削4-13孔、10销孔,选用在立式钻床上加工,故选用Z3025型立式钻床。选用莫氏锥柄麻花钻(参考文献1表3-4),专用夹具、三用游标
13、卡尺。 工序四:粗铣38、25H7、43、21孔,精铣25H7孔选用的机床应使用范围较广为宜,故选常用的802D立式铣床,选用D=16mm高速钢直柄立铣刀(参考文献1表3-15),专用夹具、三用游标卡尺。 工序五:粗铣20孔,选用的机床应使用范围较广为宜,故选常用的802D立式铣床,选用D=16mm高速钢直柄立铣刀(参考文献1表3-15),专用夹具、三用游标卡尺。 工序六:粗铣缝槽,应选用卧式铣床,故选常用的X61型铣床即能满足加工要求。选用切口铣刀(参考文献1表3-14),专用夹具、三用游标卡尺。 工序七:钻削M10-7H、M8-7H螺纹底孔,可在钻床上加工,故选Z3025型立式钻床,选用莫
14、氏锥柄麻花钻(参考文献1表3-4),专用夹具,三用游标卡尺、塞规检查孔径。工序八:攻M10-7H、M8-7H螺纹孔,可在车床上加工,故选CA6140车床,选用直柄机用丝锥(参考文献1表3-32),专用夹具、塞规检查孔径、丝锥夹头、螺纹塞规。工序九:扩13的孔、铰10销孔,可在钻床上加工,故选Z3025型立式钻床,选用直柄机用铰刀(参考文献1表3-33),专用夹具、塞规检查孔径。工序十:粗铣80H9内孔倒角,选用802D立式铣床,选用D=20mm高速钢直柄倒角刀(参考文献1表3-17)。(11)工序十一:在钳工工作台上,加工倒角R15、R10、R3。2、确定工序尺寸由P42表2-29得:80H9
15、毛坯孔直径为75,第一次粗镗到 77.5,第二次粗镗到 79.5,精镗到80 。由P41表2-28得:2-10第一次钻到9.8第一次铰到9.96第二次铰到铰10。由P46表2-39得:M10-7H第一次钻到8.5,攻丝得M10。由P46表2-39得:M8-7H第一次钻为6.7,攻丝得M8由P45表2-36得:粗铣下表面铣削加工余量为1.5,公差为+0.5,直接精铣到所剩的加工余量。由P41表2-26得垂直缝槽5 粗铣宽度余量0.3,公差为+0.1。由P41表2-26得水平缝槽5 粗铣宽度余量0.3,公差为+0.1。由P45表2-36得:粗铣25H7孔加工余量为1.5,公差为+0.5,直接精铣到
16、所剩的加工余量。五、确定切削用量及基本时间(工序四)1、切削用量该工序分五个工步,工步一:以下端A面和孔80H9以及两13孔定位(一面两孔定位),粗铣21孔;工步二:同“工步一”定位,粗铣43孔;工步三:同“工步一”定位,工件旋转180度,粗铣孔25H7();工步四:同“工步三”定位,精铣孔25H7();工步五:同“工步三”定位,粗铣38孔。(1)工步一:粗铣21孔背吃刀量的确定 工步一的背吃刀量ap取为0.7mm进给量的确定 由表5-10,工件-夹具系统刚度为中等条件选取,该工序的每齿进给量fz取为0.04mm/z铣削速度的计算 由表5-15,按d/z=16/3的条件选取38m/min。有公
17、式(5-1)n=1000v/d可得该工序的铣刀转速,n=1000*38/*16=756.37r/mm。参照4-15所列750r/mm。再将此转速代入公式(5-1),可求出该工序的实际铣削速度v=nd/1000=750*16/1000=37.68m/min。(2)工步二:粗铣43孔 同“工步一”的计算。(3)工步三:粗铣孔25H7() 背吃刀量的确定 取背吃刀量ap取为0.7mm进给量的确定 由表5-10,工件-夹具系统刚度为中等条件选取,该工序的每齿进给量fz取为0.03mm/z铣削速度的计算 由表5-15,按d/z=16/3的条件选取44m/min。有公式(5-1)n=1000v/d可得该工
18、序的铣刀转速,n=1000*44/*16=875.80r/mm。参照4-15所列950r/mm。再将此转速代入公式(5-1),可求出该工序的实际铣削速度v=nd/1000=950*16/1000=47.73m/min。(4)工步四:精铣孔25H7()背吃刀量的确定 取背吃刀量ap取为0.4mm进给量的确定 由表5-10,工件-夹具系统刚度为中等条件选取,该工序的每齿进给量fz取为0.02mm/z铣削速度的计算 由表5-15,按d/z=16/5的条件选取53m/min。有公式(5-1)n=1000v/d可得该工序的铣刀转速,n=1000*53/*16=1054.94r/min。参照4-15所列1
19、180r/mm。再将此转速代入公式(5-1),可求出该工序的实际铣削速度v=nd/1000=1180*16/1000=59.28m/min。(5)工步五:粗铣38孔 同“工步一”的计算。2、时间定额计算工序四的基本时间如下计算:根据表5-43中铣削基本时间计算公式Tj(L+L1+L2)/Fmz,可求出该工序的基本时间。由于该工序包括五个工步。工步一:粗铣21孔,直接铣为通孔,所以L=80mm,L2=13mm,取L2=3mm;L1=0.5*d+(12)=0.5*16+2=10mm,Fmz=f*n=fz*Z*n=0.04*3*750=90mm/min。将上述结果代入公式Tj(L+L1+L2)/Fm
20、z,则该工步的基本时间:Tj(80+10+3)/90=1.03min=62s工步二:粗铣43孔,深度为1mm,所以L=1mm,L2=13mm,取L2=3mm;L1=0.5*d+(12)=0.5*16+2=10mm,Fmz=f*n=fz*Z*n=0.04*3*750=90mm/min。将上述结果代入公式Tj(L+L1+L2)/Fmz,则该工步的基本时间:Tj(1+10+3)/90=0.16min=9.6s工步三:粗铣孔25H7() ,深度为46mm,所以L=46mm,L2=13mm,取L2=3mm;L1=0.5*d+(12)=0.5*16+2=10mm,Fmz=f*n=fz*Z*n=0.03*3
21、*950=85.5mm/min。将上述结果代入公式Tj(L+L1+L2)/Fmz,则该工步的基本时间:Tj(46+10+3)/85.5=0.70min=42s工步四:精铣孔25H7(),直接下到指定深度,所以取L=4mm,L2=13mm,取L2=1mm;L1=0.5*d+(12)=0.5*16+1=9mm,Fmz=f*n=fz*Z*n=0.02*3*1180=70.8mm/min。将上述结果代入公式Tj(L+L1+L2)/Fmz,则该工步的基本时间:Tj(4+9+1)/70.8=0.20min=12s工步五:粗铣38孔,深度为6mm,所以L=6mm,L2=13mm,取L2=3mm;L1=0.5
22、*d+(12)=0.5*16+2=10mm,Fmz=f*n=fz*Z*n=0.04*3*750=90mm/min。将上述结果代入公式Tj(L+L1+L2)/Fmz,则该工步的基本时间:Tj(6+10+3)/90=0.21min=12.6s工序四的辅助时间Ta的计算: 根据第五章第二节所述,辅助时间Tf与基本时间Tj之间的关系为Tf=(0.150.2)Tj,本工序取Tf=0.15Tj,则本工序的辅助时间为:Tf=0.15*Tj=0.15*(62+9.6+42+12+12.6)=20.73sTj=62+9.6+42+12+12.6=138.2s工序四其他时间的计算:除了作业时间(基本时间与辅助时间
23、之和)以外,每道工序的单件时间还包括布置工作地点、休息与生理需要时间和准备与终结时间。由于该零件是中批量生产,分摊到每个工件上的准备与终结时间甚微,可以忽略不计;布置工作地时间Tb是作业时间的2%7%,休息与生理需要时间Tx是作业时间的2%4%,该零件取3%,则工序四的其他时间(Tb+Tx)可按关系式(3%+3%)*(Tj+Tf)计算,如下所示:工序四其他时间:Tb+Tx=6%*(138.2+20.73)=9.54s单件时间Tdj的计算:Tdj=138.2+20.73+9.54=168.47s6、 夹具设计 本次设计的夹具为第四道工序粗铣孔43、孔21粗铣,粗铣孔38,粗铣及精铣孔25H7()
24、1、 确定设计方案这道工序所加工的孔在耳座两侧,按照基准重合原则,应以下端A面和孔80H9以及孔13定位(一面两孔定位),以穿过80H9孔的圆柱螺钉用快换螺母进行夹紧,对耳座的一侧进行加工,待耳座加工完成后有人工翻转180度,按同样的定位、夹紧方式加工耳座的另一侧。夹具以夹具体安装面和定位孔、定位销,使用T型槽螺栓连接。工件以A面在夹具上定位,限制了三个自由度,其余三个自由度应以两13孔限制(两个孔应选对角的两个)。在其中的一个13的孔中插入一个圆柱销以限制两个自由度,另一个13的孔中插入削边销以限制一个自由度。用一个两端带螺纹的螺栓插入80H9的孔中,并以快换螺母夹紧下端面,另一端安装在夹具
25、体上。本道工序的夹具需要翻转,若采用气动或液压夹紧,则气管或油管会防碍操作,所以应采用手动夹紧,夹具结构简单,操作方便。2、 计算夹紧力并确定螺杆直径 因为夹具的夹紧力与切削力的方向垂直,实际所需夹紧力F夹与切削力F之间的关系为:F夹=KFL/(f1H+L)。式中的K为安全系数。参考文献表10-1,当夹紧力与切削力的方向垂直时,取K=2.5。有参考文献表9-5,得F=9.81*42.7d*(N)=9.81*42.7*16*1=3220N参考文献1表10-1,因夹具的夹紧力与切削力方向垂直,实际所需夹紧力F夹与切削力F之间的关系为:F夹=KFL/(f1H+L)=2.5*3220*72.5/(0.
26、3*100+72.5)=5693N参考文献1表9-10,从强度考虑,因一个M16的螺栓能承受125334N的许用夹紧力,所以用M16的螺栓完全满足要求。但从夹具的刚度及整体对称性考虑,这里选用M20的螺栓。并确定螺杆为170mm。3、 定位精度分析基准A面是在一次装夹下完成粗加工的,它们之间的位置精度由上顶面和工作台面保证,与其有关的专用夹具尺寸如193mm、180mm、185mm的尺寸公差参考文献1表12-1,取工件公差的1/4,即夹具尺寸公差为0.125mm。由螺杆与80H9的孔有配合要求,根据参考文献1表12-8,确定配合公差等级为H9/g7,查公差表得出最大配合间隙为(+0.074mm
27、)-(+0.005mm)=0.069mm,底面A面的13孔的配合公差等级为H7/n6。有参考文献1表11-2夹具体由T形螺钉固定在机床工作台上螺栓直径为d=10mm,D=12mm,D1=24mm,R=6mm,R1=12mm,L=18mm,H=32mm,b=4mm。参 考 文 献 【1】 邹青主编 机械制造技术基础课程设计指导教程机械工业出版社【2】 李华主编 机械制造技术高等教育出版社出【3】 刘登平主编机械制造工艺及机床夹具设计北京理工大学出版社【4】 刘友才,肖继德主编 .机床夹具设计.机械工业版社【5】 马霄主编互换性与测量技术基础北京理工大学出版社【6】孟少农主编机械加工工艺手册.机械工业出版社【7】李益民主编机械制造工艺设计简明手册机械工业出版社【8】薛源顺主编机床夹具设计机械工业出版社
- 温馨提示:
1: 本站所有资源如无特殊说明,都需要本地电脑安装OFFICE2007和PDF阅读器。图纸软件为CAD,CAXA,PROE,UG,SolidWorks等.压缩文件请下载最新的WinRAR软件解压。
2: 本站的文档不包含任何第三方提供的附件图纸等,如果需要附件,请联系上传者。文件的所有权益归上传用户所有。
3.本站RAR压缩包中若带图纸,网页内容里面会有图纸预览,若没有图纸预览就没有图纸。
4. 未经权益所有人同意不得将文件中的内容挪作商业或盈利用途。
5. 装配图网仅提供信息存储空间,仅对用户上传内容的表现方式做保护处理,对用户上传分享的文档内容本身不做任何修改或编辑,并不能对任何下载内容负责。
6. 下载文件中如有侵权或不适当内容,请与我们联系,我们立即纠正。
7. 本站不保证下载资源的准确性、安全性和完整性, 同时也不承担用户因使用这些下载资源对自己和他人造成任何形式的伤害或损失。