金属力学性能脚本——张学习.2.6
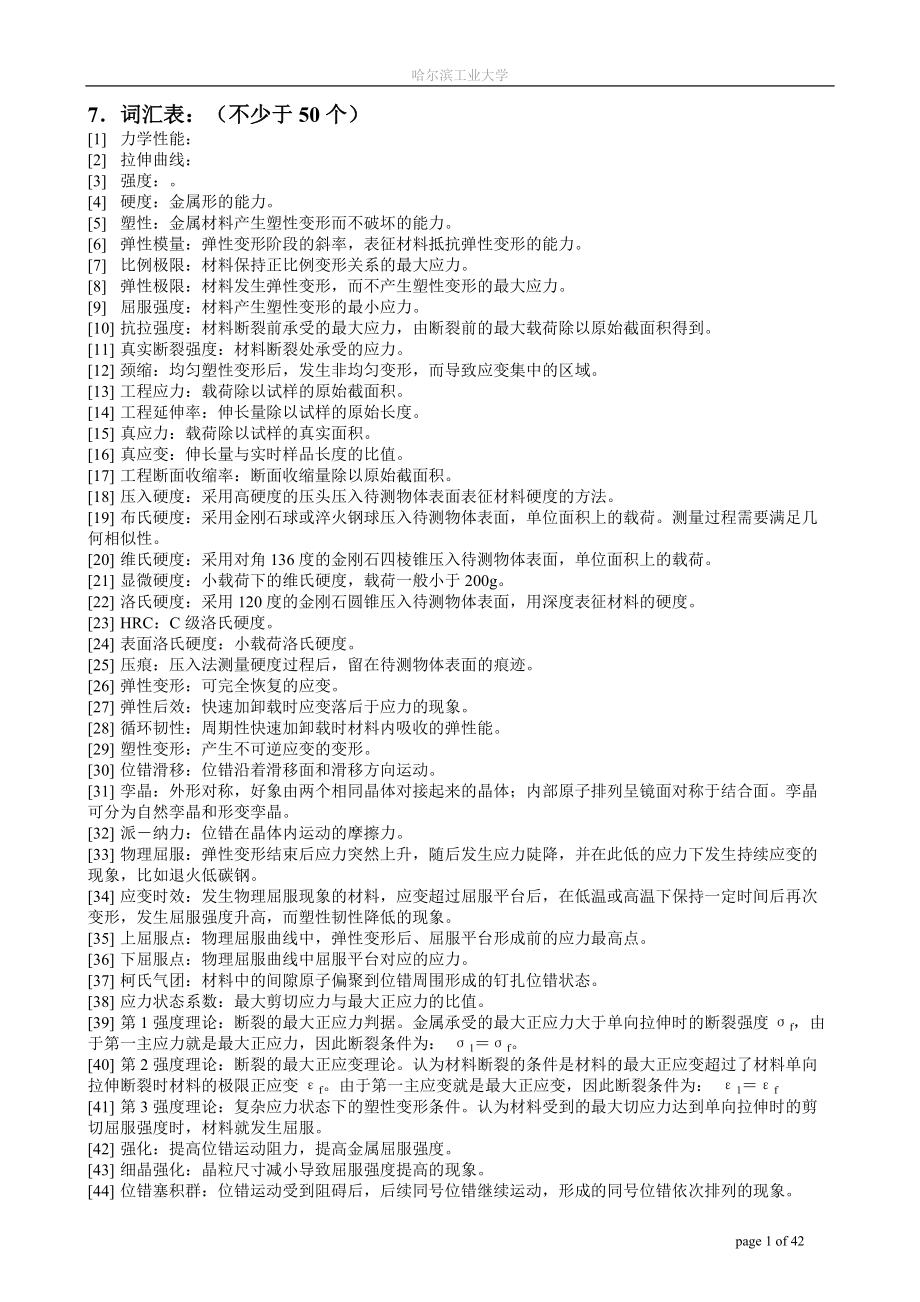


《金属力学性能脚本——张学习.2.6》由会员分享,可在线阅读,更多相关《金属力学性能脚本——张学习.2.6(42页珍藏版)》请在装配图网上搜索。
1、哈尔滨工业大学7词汇表:(不少于50个)1 力学性能:2 拉伸曲线:3 强度:。4 硬度:金属形的能力。5 塑性:金属材料产生塑性变形而不破坏的能力。6 弹性模量:弹性变形阶段的斜率,表征材料抵抗弹性变形的能力。7 比例极限:材料保持正比例变形关系的最大应力。8 弹性极限:材料发生弹性变形,而不产生塑性变形的最大应力。9 屈服强度:材料产生塑性变形的最小应力。10 抗拉强度:材料断裂前承受的最大应力,由断裂前的最大载荷除以原始截面积得到。11 真实断裂强度:材料断裂处承受的应力。12 颈缩:均匀塑性变形后,发生非均匀变形,而导致应变集中的区域。13 工程应力:载荷除以试样的原始截面积。14 工
2、程延伸率:伸长量除以试样的原始长度。15 真应力:载荷除以试样的真实面积。16 真应变:伸长量与实时样品长度的比值。17 工程断面收缩率:断面收缩量除以原始截面积。18 压入硬度:采用高硬度的压头压入待测物体表面表征材料硬度的方法。19 布氏硬度:采用金刚石球或淬火钢球压入待测物体表面,单位面积上的载荷。测量过程需要满足几何相似性。20 维氏硬度:采用对角136度的金刚石四棱锥压入待测物体表面,单位面积上的载荷。21 显微硬度:小载荷下的维氏硬度,载荷一般小于200g。22 洛氏硬度:采用120度的金刚石圆锥压入待测物体表面,用深度表征材料的硬度。23 HRC:C级洛氏硬度。24 表面洛氏硬度
3、:小载荷洛氏硬度。25 压痕:压入法测量硬度过程后,留在待测物体表面的痕迹。26 弹性变形:可完全恢复的应变。27 弹性后效:快速加卸载时应变落后于应力的现象。28 循环韧性:周期性快速加卸载时材料内吸收的弹性能。29 塑性变形:产生不可逆应变的变形。30 位错滑移:位错沿着滑移面和滑移方向运动。31 孪晶:外形对称,好象由两个相同晶体对接起来的晶体;内部原子排列呈镜面对称于结合面。孪晶可分为自然孪晶和形变孪晶。32 派纳力:位错在晶体内运动的摩擦力。33 物理屈服:弹性变形结束后应力突然上升,随后发生应力陡降,并在此低的应力下发生持续应变的现象,比如退火低碳钢。34 应变时效:发生物理屈服现
4、象的材料,应变超过屈服平台后,在低温或高温下保持一定时间后再次变形,发生屈服强度升高,而塑性韧性降低的现象。35 上屈服点:物理屈服曲线中,弹性变形后、屈服平台形成前的应力最高点。36 下屈服点:物理屈服曲线中屈服平台对应的应力。37 柯氏气团:材料中的间隙原子偏聚到位错周围形成的钉扎位错状态。38 应力状态系数:最大剪切应力与最大正应力的比值。39 第1强度理论:断裂的最大正应力判据。金属承受的最大正应力大于单向拉伸时的断裂强度f,由于第一主应力就是最大正应力,因此断裂条件为: 1f。40 第2强度理论:断裂的最大正应变理论。认为材料断裂的条件是材料的最大正应变超过了材料单向拉伸断裂时材料的
5、极限正应变f。由于第一主应变就是最大正应变,因此断裂条件为: 1f41 第3强度理论:复杂应力状态下的塑性变形条件。认为材料受到的最大切应力达到单向拉伸时的剪切屈服强度时,材料就发生屈服。42 强化:提高位错运动阻力,提高金属屈服强度。43 细晶强化:晶粒尺寸减小导致屈服强度提高的现象。44 位错塞积群:位错运动受到阻碍后,后续同号位错继续运动,形成的同号位错依次排列的现象。45 HallPetch公式:sikD-1/246 固溶强化:间隙或置换固溶原子与位错交互作用,导致材料屈服强度提高的现象。47 丛聚区:原子局部偏聚区。48 第二相强化:基体中第二相物质导致基体屈服强度提高现象。49 弥
6、散第二相:尺寸远小于基体晶粒尺寸的第二相。50 大块聚集型第二相:尺寸与基体晶粒尺寸可类比的第二相。51 加工硬化:通过应变使金属屈服强度提高的现象。52 变形协调位错:基体和第二相变形不协调,在第二相附近产生的位错。53 形变强化指数:真应力与真应变之间的关系:S=ken,n形变强化指数54 时效:固溶淬火后形成过饱和固溶态,在室温或高温下析出第二相的过程。55 欠时效:时效初期的状态,材料硬度逐渐升高(Al-Cu中形成铜的丛聚区,共格,容易变形)。56 峰时效:材料硬度最高的时效状态(Al-Cu 中CuAl2 弥散分布,细小,共格关系部分遭到破坏,部分可变形)。57 过时效:时效后期,析出
7、相尺寸长大,硬度逐渐降低(Al-Cu 中CuAl2 长大,共格关系破坏,难以变形,位错只能绕过)。58 韧性断裂:断裂前产生明显宏观塑性变形的断裂方式。59 脆性断裂:断裂前不产生明显宏观塑性变形的断裂方式。60 正断:断裂的表面垂直于最大正应力的断裂方式。61 切断:断裂的表面平行于最大切应力方向的断裂方式。62 穿晶断裂:裂纹沿晶粒内部扩展导致的断裂方向。63 沿晶断裂:裂纹沿晶界扩展导致的断裂。64 切离:断面收缩率达到100的断裂方式。65 微孔聚集型断裂:断裂过程经历微孔的形成、微孔经切离方式而连接的断裂方式。66 韧窝:微孔聚集型断裂方式中裂纹形成后经历外应力方向的伸长和垂直于外应
8、力方向的切离断裂而形成的、凹形形貌。67 撕裂棱:微孔聚聚型断裂方式中裂纹经切离过程而形成的尖锐线状形貌,构成韧窝的边界。68 解理断裂:裂纹沿特定晶面形成并扩展而导致的断裂,为脆性断裂的一种。69 河流花样:解理裂纹形成后沿不同高度的同一晶面族扩展、连接而形成的类似河流状的断口形貌。70 准解理断裂:发生在含有高密度弥散分布的碳化物质点的钢中,裂纹在第二相质点处形成、并向外放射状扩展,形成河流花样。71 应力集中:局部的应力升高现象。72 平面应力:只有二向主应力的应力状态,容易导致塑性变形。73 平面应变:只有两向主应变的应力状态。74 缺口强化:发生在能够发生全面屈服变形(或大部分区域发
9、生塑性变形)的缺口试样中,由于塑性变形区的应力高于材料的屈服强度,而导致缺口断裂强度提高的现象,属于几何强化,不能作为强化手段使用。75 冲击试验:采用机械载荷冲击试样,测试材料冲击韧性、缺口敏感性或低温脆性的试验方法。76 冲击韧性:表征材料在断裂过程中吸收冲击能力的能力,常用Ak值表示。77 AK值:冲击试样冲击过程单位面积吸收的能量。78 低温脆性:温度降低导致材料脆性断裂倾向提高的现象,一般发生在bcc和hcp结构的金属中。79 韧脆转变温度:材料韧性断裂和脆性断裂转变的温度。80 Griffith理论:Griffith采用能量方式得到的含裂纹试样的断裂应力理论。81 裂纹面:裂纹的延
10、长面。82 I型裂纹:裂纹面与应力方向垂直的裂纹。83 II型裂纹:裂纹面与应力方向平行,裂纹倾向于滑开的裂纹。84 III型裂纹:裂纹面与应力方向平行,裂纹倾向于撕开的裂纹。85 应力场强度因子:表征裂纹尖端应力场强弱的参量。86 平面应变断裂韧性:样品断裂时处于平面应变应力条件下测量的断裂韧性值。87 平面应力断裂韧性:样品断裂时处于平面应力条件下测量的断裂韧性值。88 疲劳:交变的载荷导致材料发生破坏的现象。89 应力比:疲劳载荷的最小值与最大值的比值。90 贝纹线:疲劳裂纹扩展过程中由于突然停机、开机或环境条件的变化,使疲劳断口上出现的条纹。91 疲劳条带:疲劳裂纹扩展过程中对应于一个
11、应力循环、或多个应力循环,疲劳裂纹扩展留下的条纹。92 疲劳源:疲劳裂纹萌生区。93 Paris公式:疲劳裂纹扩展稳态区中疲劳裂纹扩展速率与应力场强度因子幅的关系。94 疲劳极限:光滑试样不发生疲劳断裂的最大应力。95 疲劳曲线:疲劳断裂周次与疲劳应力的关系。96 疲劳裂纹扩展门槛值:含裂纹试样疲劳裂纹不扩展的最大应力场强度因子幅。97 近门槛区:疲劳裂纹扩展低速区。98 高周疲劳:应力低于金属屈服强度、疲劳断裂前发生107-108以上周次的疲劳形式。99 低周疲劳:应力大于金属屈服强度、疲劳断裂前发生小于102-105周次的疲劳形式。100 Paris区:疲劳裂纹扩展稳态区,可以用Paris
12、公式描述。101 驻留滑移带:相对于外加疲劳载荷,晶体取向较好的晶粒中优先发生位错滑移而形成的条带。102 循环硬化:交变载荷作用下,材料发生塑性变形后,相同应变量条件下应力增大的现象。103 循环软化:交变载荷作用下,材料发生塑性变形后,相同应变量条件下应力减小的现象。104 包申格效应:反向加载导致材料屈服强度降低的现象。105 热疲劳:温度变化导致的材料疲劳现象。106 振动疲劳:振动载荷作用导致的材料疲劳现象。107 挤出脊:交变载荷作用下形成的材料挤出样品表面的区域。108 摩擦:相对运动的物体表面间的相互阻碍作用现象。109 磨损:机器运转过程中,相对运动的摩擦表面的物质逐渐损耗,
13、使零件尺寸、形状和位置精度以及表面质量发生变化的现象。110 润滑:减轻摩擦和磨损所应采取的措施。111 滑动摩擦:物体表面间的运动形式是相对滑动而产生的作用。112 滚动摩擦:物体表面间的运动形式是相对滚动而产生的作用。113 干摩擦:两零件表面直接接触后,因为微观局部压力高而形成许多冷焊点,运动时被剪切的现象。114 粘着:两个摩擦表面接触时,在外载荷作用下只有表面上少数微凸起处接触,接触点上的应力很大,产生弹性变形,进而产生塑性变形使接触面积增大。接触点上的氧化膜被压碎,致使两个摩擦表面金属分子相互吸引和扩散而溶合,形成接触点处两种金属冷焊现象。115 边界摩擦:运动副表面有一层厚度b问
14、题84: 说明低温脆性的影响因素。解答:1)晶体学特性。 晶体结构:f.c.c不存在低温脆性。b.c.c和某些h.c.p的低温脆性严重。位错:位错宽度大,不显示低温脆性。层错能,韧性。形成柯氏气团,韧性。2)冶金因素(1)溶质元素 间隙原子,使韧性下降。 置换式溶质,对韧性影响不明显 杂质元素S、P、As、Sn 使韧性下降(2)显微组织 a)晶粒大小 b)金相组织 回火索氏体贝氏体珠光体,韧性下降 第二相(大小、形态、数量、分布)3)外部因素1、温度 钢的“蓝脆”525550(钢的氧化色为蓝色) C、N原子扩散形成柯氏气团。 2、加载速率 加载速率,脆性,韧脆转变温度Tk ; 3、试样尺寸和形
15、状 试样增厚,Tk(表面上的拉压应力最大); 带缺口/不带缺口时,脆性及Tk不同。问题85: 结合缺口试样冲击过程中裂纹形成和萌生过程,说明缺口载荷位移曲线与断口特征之间的对应关系.解答: PGY之前,弹性变形 PGY后,塑性变形;载荷增大到Pmax,塑性变形区逐渐扩展到整个缺口面(塑性区为图中红色虚线和缺口面之间面积); 在Pmax附近,应力最大点位于红色虚线上;因此在此处产生裂纹;随后裂纹向前和向后同时扩展;扩展机制是微孔聚集型,形成图中“脚跟形纤维状区”;此过程中材料承载面积减小,载荷逐渐下降到PF。 载荷达到PF后,裂纹迅速以解理断裂方式快速扩展,在材料中形成“放射形结晶状区”;这时材
16、料承载面积迅速减小,载荷也迅速降低到PD。 载荷达到PD后,裂纹扩展到样品边缘,产生平面应力状态,形成剪切唇区。问题86: 液氮罐为什么采用奥氏体钢制造,而不能采用低碳钢制造?解答:奥氏体在液氮温度下没有低温脆性转变。问题87: 为什么冲击韧性不具有可设计性?解答:断裂过程包括弹性变形、塑性变形和断裂。冲击过程吸收的能量为以上所有过程能量的总和。因此“Ak值不具有明确的物理意义”。问题88: 冲击韧性及其作用?解答:1、表征材料在冲击载荷作用下,吸收塑性变形功和断裂功的大小。 AkU/F,U为冲击过程吸收的能量,F为缺口面积。 Ak单位,J/cm2;或kgf/cm22、作用(1)揭示冶金缺陷的
17、影响;(2)对s大致相同的材料,评定缺口敏感性。(3)评定低温脆性倾向。问题89: 说明KIc的基本原理及对试样尺寸的要求解答:试样处于平面应变状态。问题90: 平面应变断裂韧性(KIc)的意义和测量方法解答:表征金属抵抗裂纹扩展的能力。采用三点弯曲或紧凑拉伸试样,保证样品应力状态主要处于平面应变状态,测量样品断裂对应的载荷,由裂纹长度和样品尺寸计算得到。计算结果需要进行验证。问题91: 有一大型板状构件,具有20mm长的I型穿透型裂纹,构件材料的屈服强度1200MPa,承受900 MPa的平均拉应力,计算其应力场强度因子KI及屈服区宽度R0。解答:168MPam1/2,2.2mm问题92:
18、有一车轴平均工作拉应力150MPa,在40下材料的屈服强度为300MPa,KIc62MPam1/2。问在这种情况下允许表面存在增多深的半椭圆裂纹?解答:45mm问题93: 影响断裂韧性的因素?解答: 1、材料因素(内在因素) 晶体特征 (晶体结构、位错) 化学成分 显微组织(晶粒大小,各相,第二相,夹杂) 处理工艺(热处理、强化处理)2、(外因)环境因素 温度、应变速度等。问题94: 叙述低应力脆断的原因及在强度设计方面防止低应力脆断的方法解答:采用断裂强度设计方法。问题95: 应力场强度因子与应力有什么区别?解答:同为状态参量,复合参量,有效描述裂纹尖端受力状态问题96: 叙述影响裂纹尖端塑
19、性区尺寸的因素解答:根据I型裂纹尖端塑性区尺寸的表达式,看出影响因素:1)所受应力的影响,应力越大,塑性区尺寸越大;2)试样几何形状,不同的几何形状有不同的y值3)裂纹长度的影响,长度越长,塑性区尺寸越大;4)应力状态的影响,分清平面应力状态和平面应变状态的区别。问题97: 分析断裂韧性与冲击韧性的异同点及其相互关系解答:概念差别;测试方法差别;物理意义差别。都描述了材料的韧性。问题98: 叙述Griffith强度理论分析断裂问题的思路解答:(1)出发点能量观点:材料中已存在裂纹;局部应力集中;裂纹扩展(增加新的表面),降低系统弹性(2)格雷菲斯模型a)单位厚度、无限宽薄板,仅施加一拉应力(平
20、面应力)。 在没有裂纹时,板内任何一点都受到拉应力作用,储存弹性能,单位面积材料储存的弹性能为:b)在板内引入一长度为2a,垂直于应力方向的裂纹。此时引入裂纹的区域,将释放弹性能(释放的能量,前面加负号)c)裂纹形成产生新表面所需要的能量 W=4a (有两个表面)总能量问题99: 通常纯铁的s2J/m2,E2105 MPa,a02.51010m,试求其理论断裂强度m。解答:4104MPa问题100: 有一材料E21011N/m2, s8 J/m2,计算在7107 N/m2的应力作用下,该材料中能扩展的裂纹最小长度。解答:0.4mm问题101: 典型疲劳断口的宏观特征是什么?如何从这些特征判断疲
21、劳源和裂纹萌生方向?解答:1、疲劳源 裂纹的萌生地;裂纹处在亚稳扩展过程中。由于应力交变,断面摩擦而光亮。随应力状态及其大小的不同,可有一个或几个疲劳源。 2、疲劳区(贝纹区) 断面比较光滑,并分布有贝纹线。循环应力低,材料韧性好,疲劳区大,贝纹线细、明显。有时在疲劳区的后部,还可看到沿扩展方向的疲劳台阶(高应力作用)。 3、瞬断区 一般在疲劳源的对侧。脆性材料为结晶状断口;韧性材料有放射状纹理;边缘为剪切唇。疲劳源区的断面一般因摩擦而光亮,可以根据这个特征判断疲劳源区。当疲劳断口可以观察到疲劳条纹时,可以根据疲劳条纹间距大小判断疲劳裂纹扩展方向,疲劳条纹间距增大的方向为疲劳裂纹扩展方向。问题
22、102: 某汽车发动机连杆螺栓在工作时承受交变拉应力,最大拉应力59640N,最小拉力56900N,螺栓螺纹处内径为11.29mm,试求应力半幅,平均应力解答:应力半幅:(5964056900)/21370 N平均应力:(5964056900)/(23.1411.2911.290.2510-6)=6.85 MPa问题103: 什么是包申格效应?形成的原因是什么?解答:反向加载引起屈服强度降低。一般初始应变量为14才产生。形成原因为林位错机制:第一次加载形成位错塞积群反向加载塞积群容易自身排斥问题104: 低碳钢的疲劳曲线中平台形成的原因是什么?为什么铝合金疲劳曲线中没有平台?解答:平台形成原因:1. 应变时效强化滑移区域,使该区域强度提高正面作用2. 塑性滑移和疲劳裂纹生成使滑移区域承载能力降低累积损伤作用负面作用两者平衡,裂纹停止生长,材料不断裂问题105: 什么是循环软化和循环硬化?形成的原因是什么?解答:恒定应变幅下实验,应力随循环的进行应力增大的为循环硬化,否则为循环软化。形成原因:取决于应力强化能力,加工硬化指数n0.1,循环硬化或循环稳定问题106: 疲劳裂纹形成的方式有哪些?解答:驻留滑移带晶界开
- 温馨提示:
1: 本站所有资源如无特殊说明,都需要本地电脑安装OFFICE2007和PDF阅读器。图纸软件为CAD,CAXA,PROE,UG,SolidWorks等.压缩文件请下载最新的WinRAR软件解压。
2: 本站的文档不包含任何第三方提供的附件图纸等,如果需要附件,请联系上传者。文件的所有权益归上传用户所有。
3.本站RAR压缩包中若带图纸,网页内容里面会有图纸预览,若没有图纸预览就没有图纸。
4. 未经权益所有人同意不得将文件中的内容挪作商业或盈利用途。
5. 装配图网仅提供信息存储空间,仅对用户上传内容的表现方式做保护处理,对用户上传分享的文档内容本身不做任何修改或编辑,并不能对任何下载内容负责。
6. 下载文件中如有侵权或不适当内容,请与我们联系,我们立即纠正。
7. 本站不保证下载资源的准确性、安全性和完整性, 同时也不承担用户因使用这些下载资源对自己和他人造成任何形式的伤害或损失。