毕业设计(论文)年产100th 的推钢式加热炉设计
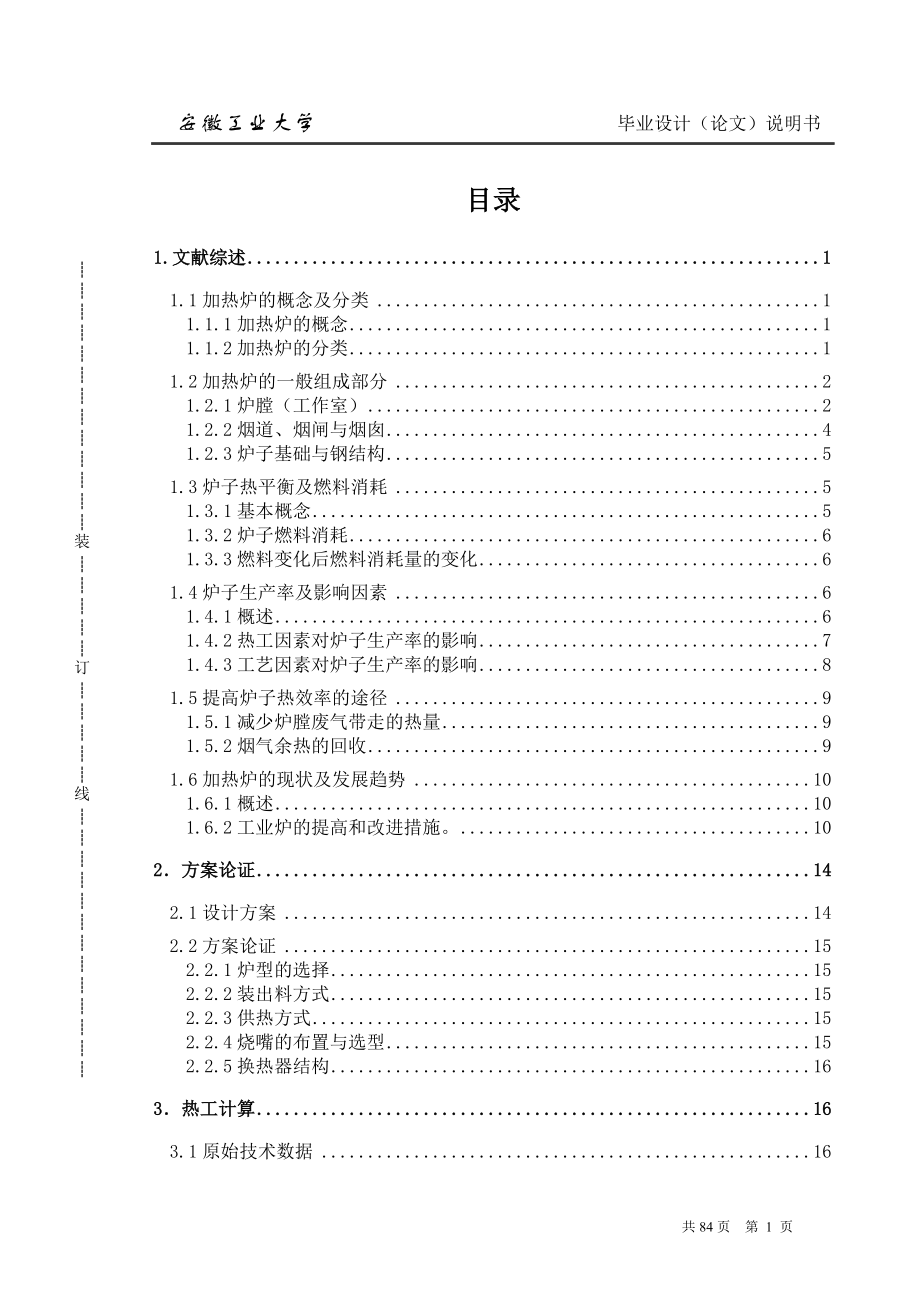


《毕业设计(论文)年产100th 的推钢式加热炉设计》由会员分享,可在线阅读,更多相关《毕业设计(论文)年产100th 的推钢式加热炉设计(89页珍藏版)》请在装配图网上搜索。
1、装订线安徽工业大学 毕业设计(论文)说明书目录1.文献综述11.1加热炉的概念及分类11.1.1加热炉的概念11.1.2加热炉的分类11.2加热炉的一般组成部分21.2.1炉膛(工作室)21.2.2烟道、烟闸与烟囱41.2.3炉子基础与钢结构51.3炉子热平衡及燃料消耗51.3.1基本概念51.3.2炉子燃料消耗61.3.3燃料变化后燃料消耗量的变化61.4炉子生产率及影响因素61.4.1概述61.4.2热工因素对炉子生产率的影响71.4.3工艺因素对炉子生产率的影响81.5提高炉子热效率的途径91.5.1减少炉膛废气带走的热量91.5.2烟气余热的回收91.6加热炉的现状及发展趋势101.6
2、.1概述101.6.2工业炉的提高和改进措施。102方案论证142.1设计方案142.2方案论证152.2.1炉型的选择152.2.2装出料方式152.2.3供热方式152.2.4烧嘴的布置与选型152.2.5换热器结构163热工计算163.1原始技术数据163.2热工计算163.2.1燃料燃烧计算163.2.2炉膛热交换计算193.2.3金属加热时间计算223.2.4炉子主要尺寸的计算293.2.5炉膛热平衡与燃料消耗计算313.2.6煤气烧嘴的选用373.2.7空气换热器设计计算383.2.8空气管路阻力损失及鼓风机的选择453.2.9烟道阻力损失及烟囱计算50结论55致谢56参考文献57
3、英文原文58英文翻译75共84页 第 87 页装订线安徽工业大学 毕业设计(论文)说明书1.文献综述1.1加热炉的概念及分类1.1.1加热炉的概念 加热炉是将物料或工件加热的设备。在冶金工业中,加热炉习惯上是指把金属加热到轧制成锻造温度的工业炉。1.1.2加热炉的分类在冶金行业中,一般可把加热炉分为室式加热炉和连续加热炉。(1)室式加热炉室式加热炉 用于金属坯或锭锻压前的加热。物料加热时不移动;炉内不分段,要求各处炉温均匀,对于大钢锭加热采用周期性的温度制度(即炉温按时间分为预热期、加热期、均热期等)。室式加热炉有两种:固定炉底室式炉和车底式炉。(2)连续加热炉广义来说,包括推钢式炉、步进式炉
4、、转底式炉、分室式炉等连续加热炉。连续加热炉多数用于轧制前加热金属料坯,少数用于锻造和热处理。主要特点是:料坯在炉内依轧制的节奏连续运动,炉气在炉内也连续流动;一般情况,在炉料的断面尺寸、品种和产量不变的情况下,炉子各部分的温度和炉中金属料的温度基本上不随时间变化而仅沿炉子长度变化。本设计主要研究推钢式连续加热炉。1)推钢式连续加热炉简介推钢式连续加热炉靠推钢机完成炉内运料任务的连续加热炉。料坯在炉底或在用水冷管支撑的滑轨上滑动,在后一种情况下可对料坯实行上下两面加热。炉底水管通常用隔热材料包覆,以减少热损失。为减小水冷滑轨造成的料坯下部的“黑印”,近年来采用了使料坯与水管之间具有隔热作用的“
5、热滑轨”。有的小型连续加热炉采用了由特殊陶质材料制成的无水冷滑轨,支撑在由耐火材料砌筑的基墙上,这种炉子叫“无水冷炉”。2)推钢式连续加热炉的发展一段式:是最古老的形式简单的的连续炉。现在几乎不用,钢坯沿着炉子单面加热,因此钢坯的上下面的温差很大。因炉温一段控制,操作不灵活。二段式:为了弥补上述一段式的缺点,使用水冷滑轨。钢坯上下两面加热,提高了单位炉底面积的的产量,炉温上下两段控制,均热炉的炉温不单独控制,因此也和一段式操作不灵活。三段式:加热段和均热段明显分开。在加热段把钢坯加热到轧钢温度,在均热段消除黑印,使钢坯温度达到均匀。炉子分三段。改变各段的炉温可以改变加热速度,操作灵活。这种炉子
6、对连续式炉的合理化、现代化做出了贡献。五段式:式三段式加热炉的发展。在三段式加热炉的装料端又增加了两个加热段。五段式加热炉炉尾温度比三段式加热炉的高。其目的是为了提高加热能力。因此单位炉底面积的产量比三段式加热炉有大幅度提高。但是,炉尾的温度高废气热损失大,燃料单耗相当高。这种炉子为了减少钢坯加热黑印,提高加热的均匀性,减少钢坯背面划伤,设置热滑轨,在均热段设有炉顶烧嘴和用出料机出钢等,但都未得到十分满意的效果。1.2加热炉的一般组成部分加热炉一般由炉子热工工艺系统、装出料系统、热工检测及自动控制系统等三部分组成。三个系统互相配合,使炉子正常运转。炉子的热工工艺系统是火焰炉最基本的组成部分,包
7、括炉子的工作室(炉膛)供热系统(风机、油泵、管道、燃烧装置等),排烟系统(烟道、烟闸、换热器、余热锅炉、烟囱、排烟机等)以及冷却系统等。工作室是炉子的核心。主要的热工及工艺过程都在工作室内完成。炉子其他各部分的任务是为工作室内所进行的热工工艺过程提供有利条件。装出料系统和热工检测及自动控制系统是现代化火焰炉不可缺少的两个工作系统。它们可以实现炉子的自动化操作,从而提高炉子的生产指标。下面仅对热工工艺系统中的主要组成部分加以介绍。1.2.1炉膛(工作室)炉膛一般包括炉顶、炉墙、炉底组成一个近乎六面体的空间。炉膛的大小对钢料加热、燃料燃烧和炉膛本身寿命都有很大的影响。从炉内气体流动来讲,火焰的高速
8、喷出使得喷出口周围造成一个低压区。炉膛过大将使火焰末尾以后的低温气流返流到这个低压区,低温气流和火焰混合使火焰温度降低,不利于钢料加热。炉膛过大还易使火焰偏向某一边,使火焰贴着炉顶或钢坯流动。相反,炉膛过小会产生火焰冲刷炉衬和钢料表面,形成局部高温,与加热质量和炉衬寿命都不利。大多数炉膛是在高温下工作,经受炉气,炉尘,炉渣的侵蚀和冲刷。因此,要求构成炉顶 、炉墙和炉底等所用的材料,结构形式和尺寸等都必须适应这一特点,以保证炉子的正常工作。(1)炉墙炉子四周的围墙称为炉墙,分为侧墙和端墙。沿炉子长度方向的炉墙称为侧墙,炉子两端的炉墙称为端墙。为保证炉墙结构的稳定性,炉墙必须有一定厚度,并应随炉子
9、尺寸的增大和炉膛温度的升高而增厚。为了减少散热和蓄热损失,炉墙应设有绝热层。各种炉墙结构中,以提高绝热性能,增加隔热层厚度,减少耐火材料厚度最为经济,不应采取增加耐火材料厚度来使隔热材料温度降到许用值以下。而应采用耐热性能较好的隔热材料作为缓冲带。为了提高炉子的强度和气密性,炉墙外包以410mm厚的钢板。此外,炉墙上应设有炉门、窥视孔、烧嘴孔以及热工参数检测孔等孔洞。为了防止砌体破坏,炉墙应尽量避免直接承受附加负荷。炉门、冷却水管等构件应设置在钢结构上。(2)炉顶炉顶使炉膛组成中薄弱环节。炉顶是否牢固可靠,对炉子工作有重大影响。炉顶按其结构型式可分为拱顶和吊顶两种。拱顶可用楔形砖砌筑或不定形耐
10、火材料捣制而成。结构简单,砌筑方便,不需要复杂的金属结构。拱顶的拱角为 60180之间。通常采用的有60、90、120和180。60拱顶的半径等于跨度 b, 拱角矢高h=0.134b 称为标准拱顶。180拱顶称为半圆拱顶,其特点是不产生水平分力,不需要钢结构加固,造价低。但炉顶下面的矢高h太大,不利于炉内气体的合理流动和实现均匀加热,且有较大的上推力。多用于埋在地下的烟道上。拱顶的厚度和材质与炉子跨度和炉内温度条件有关。一般随炉子跨度增大,拱顶厚度也应适当的增厚。吊顶由一些特制的异形砖组成。异形砖用金属吊杆单独地或成组地吊在炉子钢结构上。槽砖吊挂结构,这种结构和砌筑比较简单,更换方便。为了避免
11、挂砖的工字钢温度过高,砖的上表面不允许敷设绝热层。因此炉顶散热量较大。颈吊式吊挂结构,这种结构的每一块吊砖都有一个夹钩和一个吊杆。由于金属夹钩在砌体外面,故可以在部分表面敷设绝热层,炉顶散热量较小。但这种结构只适用于吊挂水平的及倾斜度不大的炉顶,较大倾斜度及转弯处须做特殊处理。齿槽式吊挂结构,砖与砖之间相互咬合,整体性和气密性好。个别砖即使断裂也不致掉落。缺点是砖形复杂,公差要求较严格,砌筑难度大,炉顶也不宜敷设绝热层。可塑料吊挂炉顶结构,这种结构通过吊挂埋在可塑料里面的铆固转将炉顶吊挂在钢结构上,这种吊顶可以敷设大面积隔热层,密封性能也很好,但施工时需要模板支撑。吊顶砖的材质高温部分通常采用
12、一级粘土砖或高铝砖。低温部分可用普通粘土砖。加热炉炉膛宽小于3.54米的一般用拱顶。大于此宽度时用吊顶。(3)炉底炉底是炉膛底部的砌砖部分,炉底的工作条件是非常恶劣的。它不仅要承受被处理物料的机械负荷、碰撞与摩擦等作用,有时还要受到被处理物料的化学侵蚀及熔体的渗透等。炉底结构型式和所用材料决定于工艺过程和炉内的工作温度及化学反应的性质。加热炉的炉底结构型式基本有两种:固定式炉底和移动式炉底。固定底的炉子,坯料在炉底的滑轨上移动,除加热圆坯料的斜底炉外,其他加热炉的固定炉底一般都是水平的。活动炉底的坯料是靠炉底机械的运动而移动。加热炉炉底砌体厚度与材质取决于炉子尺寸与温度。厚度一般变化在2007
13、00mm;材质一般是粘土砖须注意的是在与料坯接触的炉底部分散热损失“价值”大,故应加强绝热。炉子的砌体尺寸,在设计时的习惯做法是:炉子的水平耐火砌体的砌砖尺寸取116mm的倍数;垂直的砌砖尺寸取68mm的倍数。这样所产生的误差不会给施工带来困难。1.2.2烟道、烟闸与烟囱(1)烟道与烟闸烟道是连接炉膛和烟囱的烟气通道。设计烟道时,必须充分考虑其断面尺寸和密封绝热问题,因为前者的大小影响烟气流动阻力损失和造价,后者的好坏影响排烟系统的吸力和余热回收率。烟道断面尺寸通常是根据选取的烟气流速进行计算来初步确定的。而烟道最小断面还必须考虑清扫和检修的可能性,所以烟道断面形状和具体尺寸常根据初步计算结果
14、按标准系列选用。烟道布置要尽量缩短长度和减少烟气流动阻力距离,要与厂房柱基,设备基础和电缆保持一定的距离。以免它们受烟道温度的影响。当烟道内设有余热回收装置时,一般要设置分烟道和相应的烟道闸板。 为了控制排烟量以及调节炉膛压力,烟道上必须设置烟道闸板。烟道闸板的型式从结构特征上来分,有蝶式、升降式和百叶窗式等。从冷却方式上分,有水冷式、风冷式和无冷却式等。从材质上分,有金属型和金属与非金属结合型两种。从操作上有手动和电动之分,等等。当烟气温度低于400600C时,闸板可用灰口铸铁件或铸钢件制作;当温度高于600700C时,应采用水冷闸板、空冷闸板、衬砖闸板或耐热合金钢制造的闸板。(2)烟囱烟囱
15、时最常用的一种排烟装置。烟囱结构有砖烟囱、钢筋混凝土烟囱(内衬砖)和金属烟囱(有的衬砖有的不衬砖)。烟囱高度低于6070m时,砖烟囱比钢筋混凝土烟囱造价低,但砖烟囱砌筑比较困难,而且寿命也不如钢筋混凝土烟囱。所以小烟囱常采用砖烟囱,45m高以上的烟囱一般采用钢筋混凝土烟囱。烟囱必须有独立的基础,不能与烟道基础相连,以免烟囱下沉时烟道基础断裂。烟囱底部应设人孔,以备烘烤烟囱、扒灰和修理内衬之用。金属烟囱一般用510mm厚钢板焊成,其寿命低,但修建快,造价低,在小炉子上常采用。当温度较高时,内部须衬以耐火材料。1.2.3炉子基础与钢结构(1)炉子基础修建炉子时必须打好炉子的基础。炉子的基础一方面要
16、承受整个炉子的质量不致下沉或倒塌;一方面还要防止炉底受潮或遭受地下水的侵袭,保证炉子的正常工作。根据炉子的大小和土质的好坏,炉子基础可采用不同材料和结构来砌筑。小炉子可用红砖或块石砌筑;绝大多数大中型都采用混凝土或钢筋混凝土修建,因为它既结实又抗压。炉子基础设计和修筑炉子基础时应注意以下几点: 1) 混凝土任何部分的温度都不允许超过300,否则混凝土就会变质而压坏。因此,当炉底直接建筑在混凝土上时,要在炉底与混凝土之间用绝热材料隔开;对于温度较高的炉子,要把炉底架空起来,靠空气冷却基础。 2) 炉子基础必须是整块的,不允许有断裂现象。炉子基础要与其他基础(如辅助设备、厂房、烟囱等基础)分开,以
17、避免由于基础受力不同而引起不均匀下沉,使炉子基础开裂或设备倾斜。 3) 基础的底部应在地基的冻土线以下,以免因天气寒冷使基础遭到破坏。 4) 炉子基础因尽可能地建于地下水平面以上,以免由于地下水的侵入而损坏基础的强度。炉子个别部分(如烟道、换热器等)必须建在地下水以下时,一定要有防水沟或防水层等严密的防水措施。(2)炉子钢结构炉子钢结构一般由钢柱、横梁、拉杆、拱角梁等组成的钢架。为了使钢架形成整体而把炉子夹固起来。各个独立的钢件之间必须相互连接起来。除有特殊要求采用活动连接外,一般采用焊接结构。钢柱下端固定在炉子基础上,各部分砌体均需要留有膨胀缝,以免受热后钢架变形。为了使钢结构工作可靠,又能
18、节约钢材,各种钢件的尺寸和规格的选用都应通过计算,并参照实际使用资料来确定。1.3炉子热平衡及燃料消耗1.3.1基本概念根据能量守恒定律,任何一座炉窑或其他热工设备的热量收支是平衡的,即炉子热收入诸项目的总和等于热支出诸项的总和,这就是炉子热平衡。热平衡是评价炉子工作和设计、研究炉子时不可缺少的,特别是在分析炉子燃料消耗,寻求节能途径时更是需要的。(1)编制热平衡的意义在现场生产的炉子上,通过实测编制热平衡是为了分析研究和评价炉子的热工作,了解热量利用和损失的程度,找出燃料浪费的缘由,寻求技术对策,以改进炉子的热工指标。在设计新炉子的时候,通过计算编制热平衡是为了由平衡关系中求出炉子的燃料消耗
19、量,同时为设计炉子的供热、排烟系统和余热回收装置等提供设计依据。此外,也可把热量收支各项所占的百分比与现有炉子进行比较,从而帮助设计者判断炉子设计方案的优缺点。另外,建立炉子或其中某个局部的热平衡方程式和传热方程式及其二者之间的关系,从中找出各热工参数之间的相互关系,是进行炉子热工理论研究和分析解决各种工程实际问题最基本的研究方法和手段。1.3.2炉子燃料消耗(1)炉子燃料消耗量炉子燃料消耗量是炉子一个重要操作参数,它是指单位时间内炉子的燃料消耗量。在设计炉子的时,确定燃料消耗量有两种方法:一是计算法,一是经验法。前一种方法时从热平衡的关系中求得炉子的燃料消耗量;而后一种方法时参照同类炉子的数
20、据,选定炉子的燃料的消耗量。(2)炉子单位燃料消耗量炉子单位燃料消耗量是炉子的一个重要生产指标。单位燃耗愈低,燃料用的愈节省。单位燃耗的表示方法有:单位燃耗、单位标准燃耗、单位热耗。1.3.3燃料变化后燃料消耗量的变化炉子使用什么燃料,不仅取决于工艺和热工上的要求,而且在很大程度上取决于一个国家的能源资源和生产情况,以及一个工厂和一个地区乃至国家的燃料平衡。因此使用燃料的种类以及燃料的成分和发热量的变动,在生产上都是常见的事。对于各种炉子,明确的提出一种燃料与另一种燃料之间的合理置换比,是件十分重要的工作。当前,尤其重要的是指出重油与各种煤和煤气之间的合理置换比,这不仅可以作为生产者日常规定炉
21、子燃料消耗量的参考,而且也可以作为国家领导机关分配燃料的参考依据。1.4炉子生产率及影响因素1.4.1概述炉子的生产率是炉子的一个重要生产指标,用符号 P 表示,它是指单位时间内炉子的生产量。为了寻求提高炉子生产率的途径,必须了解影响炉子生产率的各种因素及其作用。然而这是一个比较复杂的问题,因为影响炉子生产率的因素是多方面的,其中包括工艺要求、热工过程、炉子寿命、机械化自动化程度以及生产管理等。但就炉子本身而言,主要是工艺因素和炉子结构、操作因素。对各种不同的炉子来说,工艺过程是千差万别的,所以不可能对每一种情况都进行具体分析;炉子结构和操作随炉子的用途和工艺的不同,尽管也有较大的差异,但它们
22、都是通过热工过程间接的影响着炉子生产率,而热工过程却具有一些共同的基本特征。1.4.2热工因素对炉子生产率的影响 热工过程包括炉内燃烧、气体流动和传热三过程。其中传热过程是基本的,而炉内燃烧和气体流动是通过传热过程来影响炉子生产率的。在工艺过程一定的情况下,炉料(金属)在炉内所须获得的热量是一定的。因此,炉子的生产率就取决于单位时间传给炉料的热量。所以,改善炉内热交换,增加对炉料(金属)的传热,就能提高炉子的生产率。单位时间传给炉料的热量Q 为:式中炉气、炉壁对炉料的导来辐射系数,KJ/(hK); 炉壁和炉料表面的温度K; 炉料受热面积,; a炉气对炉料的对流给热系数,KJ/(h); 炉气对炉
23、料的对流传热热流,KJ/(h)。 由上式可见影响炉子生产率的热工因素主要有下列四点: 1)炉气和炉料间的辐射温压; 2)炉气、炉壁对炉料的导来辐射系数; 3)炉料受热面积; 4)炉气对炉料的对流传热热流q。 下面从这方面着手来讨论提高炉子生产率的方法:在工艺一定的条件下,决定平均辐射温压,并构成影响炉子生产率的部分热工因素主要有:1)燃料入炉时的燃烧温度()。根据经验公式愈高,炉内平均辐射温压愈大,炉子生产率愈高。2)出炉膛废气温度(T ),T 愈高平均辐射温压愈大,炉内热交换愈强烈,炉子生产率愈高。3)炉内析热场(炉气温度曲线的形状)。为了提高平均辐射温压,炉子应该采用端头集中供热,并实现快
24、速燃烧,但实际生产条件下,往往受到一些条件的限制。 对推钢式连续加热炉,就受到下列加热工艺等方面的严格限制: 1)如果炉子出料端炉温过高,则必将造成钢坯出炉时具有较大的断面温差,产生“硬心”或“阴阳面”,达不到所要求的透烧程度,影响加热质量。 2)如果高温端炉温过高,就难于控制加热钢坯的表面温度,特别是当轧机停轧、待轧时,容易使钢温过高,造成“烧化”现象和粘钢事故,较严重时甚至使钢坯被烧毁而造成废品。 此外,全部采用端头供热的炉子,往往因为火焰长度难于调整,与多点传热,端侧供热的炉子比,炉子的温度制度缺乏必要的灵活性和适应性。因而对钢种、规格、产量的变化和轧机停轧、待轧和事故的适应性小,同时也
25、会导致燃料消耗的增加等。综上所述,单纯从提高平均辐射温压,提高炉子生产率的角度出发,应尽可能地提高理论燃烧温度,提高出炉废气温度,端头供热快速燃烧,但这些措施可能受到热效率和加热质量的限制。生产率、热效率和加热质量之间是互相矛盾统一的,在实际设计和操作中必须把这三者连同其他一些因素团结起来,统一地加以考虑。由式(1)可见,在其他条件一定的情况下,导来辐射系数C()愈大,传给炉料的热量愈多,炉子生产率愈高,除在特定条件下,例如要在炉内实现定向传热或分层燃烧等外,在炉子设计时,应尽量避免在炉内有低温气层存在。特别应避免火焰下部低温气层的存在,否则将阻碍向炉料的传热,影响炉子生产率的提高。近年来,国
26、内在轧钢加热炉炉型结构改造中,采取了适当低压低炉膛高度,缩小炉膛容量的措施,以减小和消除炉内存在的低温气层(循环气流)。在强化炉内辐射传热,提高炉子产量和降低燃料消耗等方面均收到较好的效果。在其它条件一定时,传给炉料的热量与炉料受热面积成正比,所以增加炉料受热面积,是提高炉子生产率的一个重要途径。为了增加炉料的受热面积,往往牵涉到炉子结构的变动,一般采用双面加热采增大受热面。对流传热量主要大于气流速度及温度,在炉型结构设计方面,对诸如炉膛高度,绕嘴布置以及排烟方式和位置等的设计应为能在炉内形成气流的高速冲击和强烈循环创造良好条件。1.4.3工艺因素对炉子生产率的影响炉子结构、热工操作和炉内所进
27、行的热工过程,都必须符合工艺的要求,而工艺的要求。而工艺要求与炉子结构、热工操作及热工过程之间又存在相互影响、相互制约的关系,但必须明确炉子热工是为工艺服务的,因此,工艺因素对炉子生产率及其它生产指标的影响不可忽视。 对轧钢加热炉来说,加热炉工艺的主要要求是钢锭(坯)加热温度和断面温度均匀性;对某些合金钢加热还要考虑装钢温度、加热速度、保温时间以及氧化、脱碳等。这些加热工艺参数的变化必将要求炉子温热制度与之相适应,进而影响炉子生产率。因此,在满足轧钢工艺要求下,降低钢坯出炉温度,提高加热速度,缩短加热时间等,必能提高炉子生产率。1.5提高炉子热效率的途径1.5.1减少炉膛废气带走的热量炉膛废气
28、带走的热量,通常包括废气物理显热和燃料不完全燃烧的化学热两部分。废气热损失的大小主要决定于废气量、废气温度以及废气中含有的可燃成分等。因此,改善炉子的燃烧条件和传热条件是减少炉膛废气带走热量的主要途径。(1)正确控制空气消耗系数对加热炉的正确的燃烧控制,应在保证燃料完全燃烧的条件下,尽可能的降低空气消耗系数。其最佳值的大小,将随炉子不同而不同。(2)正确控制炉膛压力加热炉是一个不严密的热工设备。当炉子或某个局部为负压时,就会从炉门或不严密处往炉内吸入冷空气,降低炉温,增加废气量,减少向炉料的传热,增大废气热损失;若为正压时,高温炉气外溢,造成溢气热损失。为了减少这种损失,在设计炉子时,对炉型结
29、构、烧嘴配置、烟囱高度、烟道、烟闸以及炉压检测和调节装置等的选择,都应考虑到炉压分布及其调节问题。使炉子在正常的生产条件下,零压面保持在炉门坎水平面上,并使炉内压力分布均匀。(3)改善炉内传热条件当向炉内供入的热量一定时,在炉内传给炉料的热量愈多,出炉废气温度就愈低。因此,凡是能改善炉内传热条件的措施,都可以减少,出炉废气热损失,提高炉子热效率。 1.5.2烟气余热的回收1)降低单位面积炉底产量,即适当延长不供热的预热段,将烟气余热用于预热入炉钢坯;2)采用高温抽烟机将预热器后的烟气抽到炉子的预热段来喷吹预热钢坯;3)利用余热预热助燃空气; 4)采用余热锅炉产气或发电。钢铁厂的节能投资应优先用
30、于回收烟温高于700C和烟量大的加热炉上,其次才考虑回收低温余热。采用预热器或喷流预热段都可能把排入大气的烟温降到350C以下。总之,回收余热时首先考虑空气(煤气)预热器,因为它可以降低炉子的一次消耗,提高炉子本身的热效率,以节约燃料油和高发热量燃料,其次才考虑供给余热锅炉去产气。1.6加热炉的现状及发展趋势 1.6.1概述我国工业炉是耗能大户,约占全国总能耗的25,仅次于热力发电和锅炉的能耗量。加热炉的能耗占工业炉总能耗的90以上,可见加热炉在我国制造领域中占据着举足轻重的地位。在机械行业中,目前先进的炉型所占比倒不超过20,绝大多数为20世纪6080年代建设或改造的结构形式,数以万计的锻件
31、、铸件加热炉在不同程度上存在加热质量差、热效率低和机械化程度低的缺陷。虽然一些较大的台车式护,环形炉和步进炉,基本实现了流量、压力,温度的自动检测与过程控制,但据统计,其中有近 l/3的炉子,由于执行元件和控制仪表性能不稳定、维护不及时、操作人员培训不到位而不能坚持使用。对于大量小型加热炉而言,只配备温度指示仪表外,一般为人工凭经验操作。我国的工业炉能源利用率较低,其热效率平均约为 25 其中锻造加热炉为520,热处理炉为8 25,连续加热炉的热减率稍高一些,也只有30 40。而世界上发达国家燃料炉的热效率平均为50左右。我国工业炉节能还存在很大潜力。对工业炉加热技术和装备水平的评价,主要从满
32、足工艺要求 提高产品质量、降低生产成本、合理利用能源、保护环境以及改善劳动条件等几个方面进行。工业炉首先应满足工艺要求,提高工件加热或热处理的质量,减少工件加热过程中的氧化和税碳损失,提高最终产品质量。保证加热工件的质量是根本,只有保证工件质量的前提下。其他指标才有意义。其次通过节约能源,降低产品能耗,实现降低产品成本的目标。能耗的高低直接反映在产品的成本和价值上,直接影响到产品的竞争力,甚至影响到企业的生存和发展。再次提高炉子自动化控制水平和机械化水平,改善劳动环境,降低工人劳动强度。工业炉装备水平的提高是工业化生产文明进步的标志。1.6.2工业炉的提高和改进措施。(1)改善燃料燃烧状况燃料
33、作为能源使用,具有如下的特殊性: 1)资源的有限性 燃料是有限的使用而不是用不完的,总会有一天使用殆尽。 2)使用的纯消耗性 燃料的使用是典型的不可逆过程,只能一次性使用而不可重复使用。 3)使用的低效性 在使用过程中必然伴有部分能量损失,其损失程度依被使用的方式、过程情况和控制水平等不同而异。 4)对环境的影响性 在燃料使用过程中,必然伴有废弃物的产生和扩散,影响环境清洁。燃料燃烧是通过安装在工业炉上的燃烧器完成,其性能的好坏,直接影响炉子燃料的消耗量。一个性能良好的燃烧器应达到:保证提供工艺所需的供热能力;保持较低的和稳定不变的空气过剩系数;燃烧效率高和燃烧完全;可适应温度较高的助燃空气;
34、火焰的形状根据需要可调节;操作和维修方便。正确的使用高效燃烧器可以节能5以上。目前,我国工业炉上普遍采用的是 20世纪7080年代以前的高压喷射烧嘴和低压涡流式烧嘴。新型燃烧器的使用不超过 10。近年来,我国成功地自行开发研制了多种适合国情的优质燃烧装置。例如,平焰烧嘴、高速调温烧嘴和蓄热式烧嘴等。平焰烧嘴的火焰呈圆盘型,加强了炉墙对工件的辐射传热作用,最适合在高温锻造加热炉上使用,冷炉升温速度可提高 40,加热速度的加快可以改善工件加热质量,减少金属氧化脱碳烧损,同时达到节约能源的目的。平焰烧嘴的安装是很重要的,如果安装不好会造成烧嘴不好使用,如火焰形状变形、燃烧不稳定、点不着火等等,甚至无
35、法生产。高速调温烧嘴的高温燃烧产物以高速 (lOOms)喷出,强化了炉内气体循环,改善了炉温均匀性。它适用于各类中低温热处理炉。蓄热式燃烧是最近两年从冶金行业的加热炉移植到机械行业的燃烧技术,燃烧器由一支燃料喷枪 (配燃烧器喷头)、两个蓄热室和一个四通换向阀组成蓄热式燃烧单元,采用 “燃料不换向技术”和 “高温低氧燃烧技术”组织燃料燃烧向炉膛供热。蓄热式燃烧器空气预热温度最高可以达到 1000左右,通过蓄热室的烟气排出温度 200,炉子热效率达到 30以上。蓄热式燃烧器在使用热值较低的燃料时,由于烟气量大干空气量,仍有一部分烟气不经蓄热室被直接排放,这些高温烟气中的热量可以通过换热器对煤气进行
36、预热,以更能有效地提高余热利用率。(2)优化炉衬结构 工业炉炉衬材料分为砖砌炉衬、浇注料炉衬和纤维炉衬。目前国内的加热炉绝大多数采用传统的耐火砖砌筑形式,炉衬的散热和蓄热占炉子总能耗的 2040。筑炉材料的发展趋向是 “两高一轻”,即高温、高强、轻质。合理选择炉衬材料和优化复合炉衬结构,可以减少炉体散热、蓄热损失,取得很好的节能效果。 1) 浇注料炉衬的导热系数比砖体炉衬小,炉体气密性好,使用寿命长,从而提高了炉子的作业率,因此可以全面改善炉子的技术经济指标。近年来浇注料在品种、质量上均有长足进步,在很大程度上满足了炉子耐高温、耐急冷急热、耐冲腐等要求。使用浇注料炉衬比砖砌炉子可节能 24左右
37、。 2) 耐火纤维是一种超轻质耐火材料,它的基本性质是相对密度小、导热系数小、比热容低。所以用这种材料筑炉,在节能、省材、提高炉子生产能力和改善炉子热工性能等方面都具有明显的效果。使用耐火纤维炉衬比砖砌炉子可节能 58。随着耐高温耐火纤维制品的研制成功,耐火纤维长期在炉温 1200l300下使用已不再是难事,这促进了耐火纤维的推广使用。耐火纤维施工方法直接影响其使用效果和使用寿命,传统的锚固法在使用中经常发生一些问题,如纤维脱落和纤维烧后缝隙加大等。一种新的施工方法是将散装纤维棉经高压风送出喷枪,结合剂与纤维棉外混,一起喷到工作表面。这种施工方法既保留了纤维的固有特性,又消除了炉衬的接缝,从而
38、提高了节能效果,延长了炉子寿命。 3) 红外节能涂料有很好的节能效果。红外节能涂料能使用于炉温 300-1800的各种燃料炉。将其喷涂于炉衬内表面,形成0-305mm的涂层,利用涂层的红外辐射性能,达到增加热效、减少能耗、延长炉衬寿命的作用。 (3)采取余热回收措施据近期对冶金、建材、轻工、机械四行业的调查,现有燃料炉总台数近 6万台,能耗为9694万t标煤 a,可回收的余热资源量为 1210万t标煤a,实际的余热回收率只有24,就是说还有76的余热资源有待回收,因此燃料炉必须配制余热回收装置,而且预热助燃风温度应在350以上。降低烟气排放温度,利用烟气的余热来预热炉料或预热助燃空气节约能源。
39、一般来说,助燃空气预热温度每提高 100T,即可减少燃料消耗5以上,提高燃烧温度约50。助燃空气预热对炉子热工产生极好的影响,甚至可以在一般的炉子上使用发热值较低的煤气。利用烟气预热炉料和燃料受诸多因素制约,对燃料炉而言最有效和应用最广的是预热助燃空气。下面介绍几种常见的空气预热器。 1) 金属换热器,气密性好,体积小,设备紧凑。对于普碳钢及其表面渗铝材质,其预热风温控制在 350以下,用不锈钢材质预热风温可达450,耐热钢材质预热风温达500C以上。主要结构形式有加筋辐射式、喷流辐射式、喷流管式、板 (管)式,在实际应用中如何选择要依据炉子排烟方式决定。 2) 蓄热式换热器预热风温可高达 8
40、O0 以上,但换热器体积庞大,限制了其推广使用。这种换热器的关键是开发高效、长寿的蓄热元件和处理好换向技术。目前国内外有发展蓄热式换热器技术的趋势,尤其是蓄热式换热器与烧嘴一体化并配以自动控制技术,近几年在国内有一些企业已经在尝试使用。(4)提高控制水平工业炉计算机过程控制是提高加热质量、减少环境污染、节约能源、提高生产管理的有效措施之一。目前国内有数以百计的工业炉采用计算机控制和管理。 1) 燃料燃烧控制 工业炉进行计算机控制的第一步是实现燃料燃烧控制,即实现炉温、供燃料量、燃料量与空气量的配比以及炉压的控制,其中核心是配比燃烧控制。最简单的办法是按流量测量值控制配比。实际生产中由于换热器漏
41、风、燃料热值和压力波动以及计量不准等问题存在,使燃烧配比失真。用测量烟气中含氧量来控制配比,即残氧分析法,不受漏风、热值与压力波动以及计量不准的影响,是个好办法。但氧化锆探头寿命短、价格贵 ,限制了其推广应用。为此又出现一些控制软件技术予以弥补,如 自寻优控制,多目标专家寻优控制等方法控制配比。脉冲式燃烧供热技术近几年被广泛采用。脉冲式燃烧控制器是以高速调温烧嘴为控制对象,改量控为时控,以小火作为长明火,用控制大火输出时间来控制升温速度。该种控制方式是在开炉调试时将小火、大火燃烧的空,燃比值设定合适即可,加热过程中不需要动态控制空,燃比,只需控制燃料和助燃空气压力的稳定,这大大地简化了控制系统
42、构成,降低了炉子建造成本。但脉冲控制高速燃烧系统的实际炉膛温度与设定控制温度偏差较大,缩短脉冲时间,炉膛温度与设定控温偏差将显著减小。上述燃料燃烧控制方法在生产过程中已被广泛采用。通过实践验证,上述燃烧控制方法能够有效改善燃料燃烧状况,为炉子其他热工参数的自动控制提供有利条件,同时节约了燃料,提高了炉子的热效率。燃料燃烧控制的节能效果约为510。 2) 数学模型优化控制 在实现燃料燃烧控制的基础上,进一步提高控制水平就要用数学模型进行优化控制,主要内容是优化炉子的热制度。炉子热制度的核心是炉温制度和供热制度,因此可以是控制炉温曲线为最佳,也可以是控制供热曲线为最佳。数学模型的确定方法主要根据实
43、验数据或生产数据经过数学处理得出。数学模型优化控制在燃烧控制的基础上可以进一步取得节能 5的效果。控制炉膛压力能保证炉子工况稳定,提高工件加热质量,减少热量损失,提高炉子热效率。炉压控制是在炉膛内的合适位置设置取压元件,通过信号的转换,使控制阀门的执行机构动作,改变烟道阀门的开度,使炉膛内压力调整到设定值。炉压恒定在最佳值范围工作,从而消除冷空气吸入炉内造成炉子温度降低或炉子冒火现象。这样提高了热能利用率,改善了炉子周围环境条件,延长了炉子使用寿命。炉门、炉车和炉体的密封是燃料炉密封的难点,硅酸铝纤维的应用为解决炉子的密封提供了有利条件。利用硅酸铝纤维的柔软和富有弹性的特点,制成了钢性对柔性的
44、密封面,采用弹簧或汽缸压紧,使炉膛成为一个密封体。炉膛密闭是控制炉压稳定的前提和条件。 (3)生产管理优化控制 工业炉是工厂或车间中的一个局部,其工作应放到整体中加以衡量,炉子 自身的燃烧控制、数学模型控制可能是最佳效果,但放在工厂或车间整体衡量则不一定是最优,这当中涉及各设备间的协调、调度和管理等问题,因此再提高一个层次就要进行管理优化控制。管理优化控制的效果在数学模型优化控制的基础上可再节能约 5。进行计算机控制的炉子要具备一些基础条件,必须是有关炉子的一些成熟技术已被采用,如燃烧装置先进、余热进行回收、炉体结构和筑炉材料合理等,否则即使采用了计算机控制也不会得到满意的结果。 (5)结语
45、目前,全球经济、资源和环境逐渐趋于一体化,我国能源、环保都面临很大的压力。工业炉的加热技术进步和装备水平的提高,是一个全局性的系统工程,要想取得有效进展,逐步缩小在能源效率、产值能耗等方面与国际先进水平的差距,必须把政府规范行为与企业发展意识有机地结合起来,通过广大工业炉领域的工作者积极研究、推广先进的技术和装备,使工业炉的发展走科技含量高、经济效益好、能源消耗低、环境污染少的可持续发展道路。2方案论证2.1设计方案1设计题目:100t/h推钢式加热炉设计2炉子工作时间:一年炉子按照正常工作330天,检修30天3燃料的选择: 选用混合煤气混合煤气干成分表 (%) 成分种类COCHOH CHCO
46、N合计焦炉煤气3.12.90.457.925.49.01.3100高炉煤气13.9_0.33.00.626.256.01004生产产品的规格1) 种类:优质碳素钢(20钢)2) 尺寸:150mm150mm3000mm3) 料坯入炉温度:t=204) 金属加热终了温度:5) 金属断面温差:5) 废气出炉温度:t=8006) 加热方式:采用三段式(预热、加热、均热)炉型,上下端侧结合加热7) 排烟方式:下排烟8) 换热器的选型:平滑直管金属换热器(带“一”字形纽带插入件)9) 进出料方式:端进侧出10)炉顶结构:吊顶结构2.2方案论证2.2.1炉型的选择采用三段式连续加热炉优点:(1)允许加热段有
47、更高的炉温,因而可提高炉子的单位生产率。(2) 因具有均热段,料坯出炉时可获得较均匀的加热。(3) 在必要时三段炉型可按两段制度操作,而二段炉型难于按三段制度操作。(4) 三段连续加热炉的实炉底(如果有炉底地的话)在均热段内,在一定程度上与高温的加热段分开,因而由于熔渣所造成的炉底上涨现象没有二段式炉型那样严重。(5) 三段式炉型均热段末端火压较低,可减少出料门吸风。因此,在设计时应尽可能采用三一般采段式炉型。2.2.2装出料方式进料方式现在一般采用端进料,而出料方式两种方式均有使用。基于本设计中料坯断面尺寸小,且要求金属加热终了时断面温差小,也就是加热质量要求高,综上所述采用侧出料较好。2.
48、2.3供热方式 本设计中加热分配为:上加热占40%,下加热占60%;同时炉子长度上分配为:加热段占80%,均热段占20%。这样分配完全根据工艺要求及产品要求而制定的,能使料坯良好的经过加热,加热终了是断面温差很小。2.2.4烧嘴的布置与选型 烧嘴完全根据加热量的分配而进行布置的。连续加热炉加热段炉温较高,且我们要求炉温均匀性较好,因此烧嘴燃烧火焰要有一定长度和铺展面。根据各种煤气烧嘴的特性,查有关手册决定选用低压涡流式烧嘴,即DW型煤气烧嘴。2.2.5换热器结构 选用平滑直管金属换热器,并带“一”字型纽带插入件,这样可以提高对流热系数,从而提高换热效率。其他许多设计方案在此不一一加以说明,将在
49、热工计算中详细说明。3热工计算3.1原始技术数据1炉子生产率:P=100t/h。2加热金属规格:1)种类:优质碳素钢(20钢);2)尺寸:150mm150mm3000mm;3)料坯入炉温度:t=20;4)金属加热终了温度:1250;5)金属断面温差:30。3燃料:1)种类:混合煤气;2)焦炉煤气成分(干成分):参见表31;表31 混合煤气干成分(%) 成分种类COCHOH CHCON合计焦炉煤气3.12.90.457.925.49.01.3100高炉煤气13.9_0.33.00.626.256.01003)出炉膛烟气温度:t=800;4)煤气不预热:=20;5)空气预热温度:t=350。3.2
50、热工计算3.2.1燃料燃烧计算1混合煤气干、湿成分的换算: 计算结果如表32。表32 混合煤气湿成分(%) 成分种类COCHOH CHCONW合计焦炉煤气2.992.790.3955.7524.458.661.253.72100高炉煤气13.38_0.292.890.5825.2253.923.721002计算混合煤气的低发热值1)计算焦炉煤气低发热值把表32中焦炉煤气的湿成分代入公式得:Q=126.48.66+10855.75+35824.45+5912.79=17518kJ/标m2) 计算高炉煤气低发热值Q=126.425.22+1082.89+3580.59=3711kJ/标m3)焦高比
51、为3:7的混合煤气的低发热值Q=0.317518+0.73711=7853 kJ/标m3.按焦高比3:7,计算混合煤气湿成分见表3-3表3-3混合煤气成分(%) 成分种类COCOCHCHHONHO混合煤气20.2510.267.740.8418.750.3238.123.724计算理论空气需要量L把表33中混合煤气湿成分代入公式得:L=1.77标m/标m5计算实际空气需要量L,取n=1.1代入公式: L=nL L =(1+0.00124)L可得:L=1.771.1=1.948标m/标m L=(1+0.0012418.9)1.948=1.994标m/标m6.计算燃烧产物生成量及成分 把表33中混
52、合煤气湿成分代入公式(118)可得: =0.3993标m/标m 其他见表3-4表34混合煤气燃烧产物生成量及成分 成分名称CONOHO合计生成量(标m)0.39931.95650.04700.44302.8458体积含量(%)14.0368.751.6515.571007 .计算混合煤气燃烧产物重度 把表34中燃烧产物体积百分含量代入式(121)可得: =1 .284kg/标m8计算燃料理论燃烧温度 由t=350,查资料可得c=1 .296 kJ/标m,空气带入的物理热QQ=Lct =1.9941.296350 =904.478 kJ/标m 燃料带入的物理热= Q=(20.251.3021+1
53、0.261.640+1.57547.74+0.841.8347+18.751.2801+0.321.3099+38.121.3264+3.721.4935) 20 =27.49 kJ/标m设t=18002100,可查资料得c=1.672 0.3+1.714 0.7 kJ/标m. 设Q=0,按式= =1814.4 1800因此可以满足连续加热炉的加热工艺要求。3.2.2炉膛热交换计算计算的目的是确定炉气经过炉壁对金属的导来辐射系数计算方法和步骤如下:预确定炉膛主要尺寸炉膛宽度 查工业炉设计手册,对于中型加热炉,加热炉炉底强度H可取550kg/(mh),取推钢比E=220,代入公式: 其中 P炉子
54、生产率,kg/h H炉子有效炉底强度,kg/(mh) L料坯长度,m E推钢比,可取200250得n=1.84 可取n=2则采用双排料;将n=2代入公式B=nl+(n+1)a式中:L料坯长度,mm a料坯端头与炉墙内表面的距离,一般取200250mm(取200mm)则:B=23 +(2+1)0.2=6.6m对砌砖炉体结构,为了砌筑施工方便,炉体宽度应为耐火砖宽度(0 .116m)的整数倍.经计算:6.6不是0.116整数倍,可以取B=570.116=6.612m,满足了为耐火砖宽度的整数倍的要求.所以取: B=6.612m=6612mm炉膛高度:查资料,对于燃气的中型加热炉,取H1600mm,
55、H1750mm,H900mm,H1000mm,H1200mm3) 炉膛长度:设均热段长度为L,加热段长度L,预热段长度L。4)炉顶结构:吊顶结构。5)出料方式:侧出料。2计算炉膛相关尺寸1)各段炉底面积 F= F F2)各段炉墙(侧墙)和炉顶(吊顶结构)面积 =9.323 同理可得 各段包围炉气内表面积 各段充满炉气的空腔体积 3计算各段平均有效射程 按聂夫斯基近似公式计算得: 4计算炉气中二氧化碳和水汽分压由燃料计算得:14.03/100=0.1403大气压; 15.57/100=0 .1557大气压5 .计算各段炉气温度1)设均热段炉温比加热终了时金属表面温度高75,即:751250751
56、3252)设加热段温度比加热终了时金属表面温度高100,即:1001250100=13503)预热段炉气温度变化规律近似围线性,则:(+)/2=(1350+800)/2=10756计算各段炉气黑度 由=+而:=可得:7 .计算炉壁对金属的角度系数对于吊顶同理可得:8计算各段导来辐射系数,其中:炉气黑度 炉壁对金属的角度系数 炉料黑度 查表2-1,取炉料黑度=0 .8预热段: 加热段: 均热段:计算各段炉气热工系数列入表3-5表3-5 各段炉气热工系数系数各段预热段0.2580.68799.195加热段0.2820.592710.160均热段0.2550.64409.2983.2.3金属加热时间
57、计算金属加热计算是加热炉热工计算的核心,其主要目的是确定金属在炉内的加热时间,这个时间是指金属从入炉开始加热到工艺要求的温度出炉时所经过的总时间,金属加热时间受钢种、尺寸、形状以及其在炉内的摆放、炉型结构、燃料种类以及温热制度等一系列因素的影响。详细计算过程如下:首先将三段式加热炉用4个界面分成三个区段,即金属入炉处为0界面;预热段终了加热段开始为1界面;加热段向均热段过渡处为2界面;均热终了出炉处为3界面.则01为预热段;12为加热段;23为均热段.计算顺序为界面3、2、1、0.如下:1 2 3 4 预热段加热段(双面加热)均热段(双面加热)计算4界面处金属加热有关参数1) 已知金属表面温度
58、和金属断面温差,求算均热段钢坯的均热时间及温度参数.本设计均热段采用架空式,用公式 式中:均热度,可以在设计手册上查图3-10可得,一般取0 .6,即相当于取0 .242) 加热时间 其中 S金属透热深度 金属导温系数查表3-7得,1250时,20#钢的导温系数=0.021 m/h则由金属加热工艺可知,出炉时钢坯断面温差为30,则加热终了是钢坯平均温度3)加热终了时钢坯表面的热流查表3-1得,1230时钢的导温系数=112.0 KJ/()KJ/(m)4)均热段炉气温度: t计算结果与假设均热段炉气温度相差很小,所以不需要重新计算.计算3界面处金属有关参数前面已经计算得F=0.6由式(3-26)
59、 KJ/() 根据F 查表3-13得 =1240按式(8-5)得: =172551 2)加热段炉气温度 =1358与假设相差的不大,不需要重新计算。计算金属断面温差 设=1200 查表(3-1)得=107.3 KJ/() =60计算金属中心温度和平均温度 =1240-60=1180 =1198与设定值相差很小,所以不必重新计算。计算金属热焓值 根据 查表(3-3)得=0.6866 KJ/(kg) =823 KJ/kg计算2界面处金属的有关参数计算炉膛燃料利用系数由公式(4-31)知: ,本设计只预热助燃空气,所以可改写为:,查表1-5,350时=1 .296;=800 时, 1 .534;7853;1.948;。则:2)计算加热段燃料利用系数,由公式
- 温馨提示:
1: 本站所有资源如无特殊说明,都需要本地电脑安装OFFICE2007和PDF阅读器。图纸软件为CAD,CAXA,PROE,UG,SolidWorks等.压缩文件请下载最新的WinRAR软件解压。
2: 本站的文档不包含任何第三方提供的附件图纸等,如果需要附件,请联系上传者。文件的所有权益归上传用户所有。
3.本站RAR压缩包中若带图纸,网页内容里面会有图纸预览,若没有图纸预览就没有图纸。
4. 未经权益所有人同意不得将文件中的内容挪作商业或盈利用途。
5. 装配图网仅提供信息存储空间,仅对用户上传内容的表现方式做保护处理,对用户上传分享的文档内容本身不做任何修改或编辑,并不能对任何下载内容负责。
6. 下载文件中如有侵权或不适当内容,请与我们联系,我们立即纠正。
7. 本站不保证下载资源的准确性、安全性和完整性, 同时也不承担用户因使用这些下载资源对自己和他人造成任何形式的伤害或损失。