混凝土液压泵车毕业设计
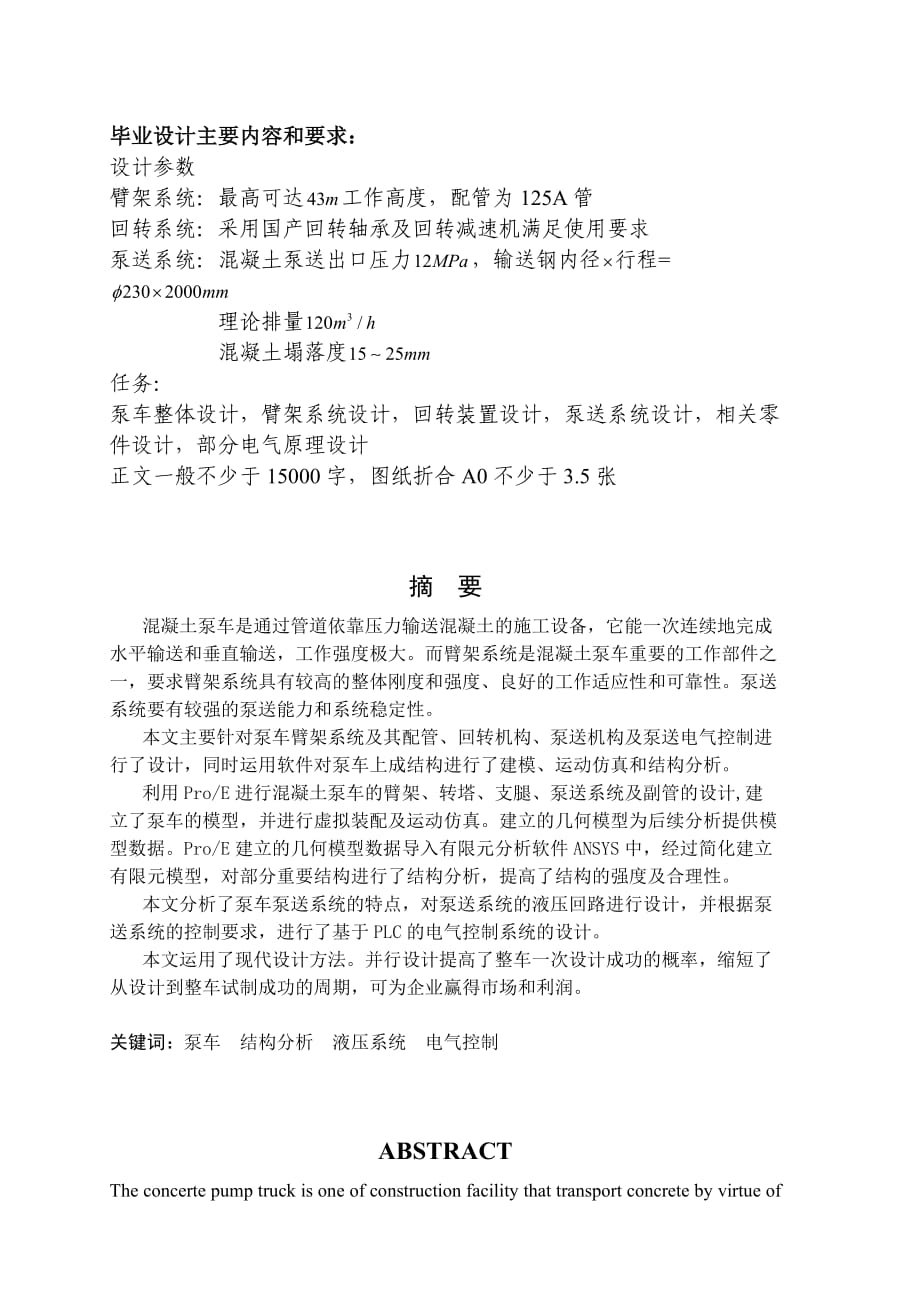


《混凝土液压泵车毕业设计》由会员分享,可在线阅读,更多相关《混凝土液压泵车毕业设计(78页珍藏版)》请在装配图网上搜索。
1、毕业设计主要内容和要求:设计参数臂架系统:最高可达工作高度,配管为125A管回转系统:采用国产回转轴承及回转减速机满足使用要求泵送系统:混凝土泵送出口压力,输送钢内径行程= 理论排量 混凝土塌落度任务:泵车整体设计,臂架系统设计,回转装置设计,泵送系统设计,相关零件设计,部分电气原理设计正文一般不少于15000字,图纸折合A0不少于3.5张摘 要混凝土泵车是通过管道依靠压力输送混凝土的施工设备,它能一次连续地完成水平输送和垂直输送,工作强度极大。而臂架系统是混凝土泵车重要的工作部件之一,要求臂架系统具有较高的整体刚度和强度、良好的工作适应性和可靠性。泵送系统要有较强的泵送能力和系统稳定性。本文
2、主要针对泵车臂架系统及其配管、回转机构、泵送机构及泵送电气控制进行了设计,同时运用软件对泵车上成结构进行了建模、运动仿真和结构分析。利用Pro/E进行混凝土泵车的臂架、转塔、支腿、泵送系统及副管的设计,建立了泵车的模型,并进行虚拟装配及运动仿真。建立的几何模型为后续分析提供模型数据。Pro/E建立的几何模型数据导入有限元分析软件ANSYS中,经过简化建立有限元模型,对部分重要结构进行了结构分析,提高了结构的强度及合理性。本文分析了泵车泵送系统的特点,对泵送系统的液压回路进行设计,并根据泵送系统的控制要求,进行了基于PLC的电气控制系统的设计。本文运用了现代设计方法。并行设计提高了整车一次设计成
3、功的概率,缩短了从设计到整车试制成功的周期,可为企业赢得市场和利润。关键词:泵车结构分析 液压系统 电气控制ABSTRACTThe concerte pump truck is one of construction facility that transport concrete by virtue of press throuth the pipe and it can transport the concrete with horizontal and vertical continuously.Its work strength is very high.The arm system
4、is one of the very important equipment in concrete pump.It must have high strength and stiffness, good working adaptability and reliability. Pump system need have strong pump ability and stability .This paper designed the arm system、turret、leg、pump system and electrical control.It make the concrete
5、pump truck model by Pro/E and designd the arm system,pump system and so on.The virtual assembly and movement simulation is successful and it served for the later design.The simplified date provided by Pro/E is used by ANSYS during the structure analysis.This can improve the important structers stren
6、gth and rationality.This paper analysised the concrete pump trucks characteristics and design the hydraulic system. Base on the pumps control ,it also designd the electrical system. This paper use the modern design method. Parallel designed can decrease the design period and inhance the design effic
7、iency. It can help the company win the market and make profit.Keywords:Concrete pump Structure analysis Hydraulic system Electrical system目 录1 绪论11.1 混凝土泵车的设计背景11.2国内外泵车研究现状及发展趋势21.2.1臂架系统方面21.2.2泵送系统方面21.2.3节能技术方面21.2.4自动化、智能化方面21.3课题研究思路和主要内容32 混凝土泵车的总体设计42.1泵车臂架系统设计52.1.1臂架折叠方式62.1.2臂架结构特点特点72.1.
8、3连杆的结构82.1.4臂架油缸结构型式82.2泵车转塔结构92.2.1转台结构92.2.2回转机构92.2.3 固定转塔结构92.2.4支承结构102.3泵送机构的基本构造112.3.1泵送系统组成122.3.2料斗和S阀总成132.3.3摆摇机构152.3.4搅拌机构152.3.5配管163 臂架系统详细设计183.1臂架箱型结构分析183.2臂架钢板及焊接性能183.2.1钢板性能183.2.2焊接性能183.3臂架系统结构设计193.3.1第五臂架设计203.3.2第四臂架设计223.3.3第三臂架设计233.3.4第二臂架设计253.3.5第一臂架设计263.4臂架系统的计算机辅助设
9、计273.4.1臂架五的仿真过程283.4.2臂架二的仿真过程293.5连杆的受力313.5.1直连杆二设计及应力校核313.5.2弯连杆二设计323.6臂架1号液压缸的详细设计333.6.1液压缸的结构选型333.6.2活塞杆内径及缸径计算333.6.3活塞及其密封的设计353.6.4活塞杆的设计383.6.5安装连接元件393.6.6连接油口设计403.6.7内卡环的设计414 转塔设计414.1回转支承设计414.1.1回转支承的结构414.1.2回转支承选型424.1.3外载荷的确定424.1.4安装螺栓的选择434.2回转减速机设计434.2.1回转阻力计算444.2.2输出齿轮轴的
10、设计454.3回转减速机轮系设计474.3.1 齿数及行星轮数的确定474.3.2马达的选取及轮系输出转矩计算484.3.3齿轮材料、热处理工艺及制造工艺的选定494.3.4第一级轮系计算494.3.5第二级行星轮系计算514.3.6减速机轴承设计544.4摩擦片式离合器584.4.1离合器总体结构584.4.2摩擦片的设计584.4.3摩擦式离合器的发热计算594.4.4活塞及弹簧的设计604.4.5其它辅件的设计614.5臂架与转塔铰接设计及应力分析624.6支腿设计要求635 泵送机构设计635.1管路长度及泵送阻力计算635.2 泵送压力计算645.3活塞杆设计655.4限位油缸的设计
11、655.5摆摇机构的设计656泵送PLC自动控制676.1 泵送系统液压回路676.2泵送系统电气自动控制716.2.1泵送系统的PLC控制回路的设计726.2.2硬件选型图726.2.3PLC流程图737 结论74参考文献75翻译部分77英文原文77中文译文82致 谢881 绪论1.1 混凝土泵车的设计背景混凝土泵车是利用压力将混凝土沿管道连续输送的机械。由泵体和输送管组成。按结构形式分为活塞式、挤压式、水压隔膜式。泵体装在汽车底盘上,再装备可伸缩或屈折的布料杆,就组成泵车。混凝土泵车是在载重汽车底盘上进行改造而成的,它是在底盘上安装有运动和动力传动装置、泵送和搅拌装置、布料装置以及其它一些
12、辅助装置。混凝土泵车通过动力分动箱将发动机的动力传送给液压泵组或者后桥,液压泵推动活塞带动混凝土泵工作。然后利用泵车上的布料杆和输送管,将混凝土输送到一定的高度和距离。自从水泥发明后,混凝土的输送与浇注就一直是人们研究的对象,传统的建筑施工方式是采用吊斗,效率低,不能满足现代工业化的发展要求,二十世纪初欧洲就一直在研究混凝土输送泵,但效果不佳,未能起到推广应用,直到二十世纪五十年代德国施维英公司(SCHWING)才生产了世界上第一台液压驱动的拖式混凝土输送泵,使拖式混凝土泵得到了迅猛发展,结构不断完善,泵送能力也不断增强。到目前为止,混凝土泵送高度最高已达532米,泵送最长水平距离达2015m
13、,最大理论泵送量达,极大的提高了生产效率,尤其是在高层建筑施工中,已成为必备的设备,但是使用过程中,人们逐渐的发现了拖泵的一些局限性:拖泵使用时必须在建筑物上铺设管道,准备工作量大;随着浇灌位置变化,必须人工将管道出口不断移动个,很不方便;拖泵总在固定的地点工作之道工程完成,这种工作方式使用设备利用率很低。针对拖泵的这些不足,在二十世纪七十年代,研制出了集行驶,泵送,布料功能于一体的混凝土泵车混凝土泵车是将用于泵送混凝土的泵送机构和用于布料的臂架集成在汽车底盘上的专用车辆,工作时,利用汽车底盘柴油机发动机的动力,通过分动箱将动力传给液压泵,然后带动混凝土泵送机构和臂架系统,泵送系统将料斗内的混
14、凝土加压送入管道内,管道附在臂架上,臂架可移动,从而将泵送机构泵出的混凝土直接送到浇注点。与拖泵相比,泵车有以下优越性:1、臂架上附着管道,开到工作地点后,很快就能打开臂架进行工作,通常在半小时内就能准备就绪,准备时间短; 2、配备液压卷折式臂架,在工作范围内能灵活转动,布料方便快捷,而且泵送速度快,一般在90/h 至150/h,工作效率高 ;3、自动化程度高,整台泵车从泵送到布料均能由一人操作,一般配备无线遥控系统,操作方便;4、机动性能好,在一个工程作业完成后能迅速转移到另一个工程继续作业,能同时负责几个工程的混凝土泵送,设备利用率高。我国泵车最早使用于1979年,当时从日本引进泵车在上海
15、宝钢施工,1982年湖北建设机械厂从日本“石川岛”引进臂架生产技术开始生产泵车成为国内第一家混凝土泵车生产厂。随着建筑业的发展,泵车生产厂家逐渐增多,但臂架部分开始大都是进口,现在逐步改为自制为主和进口为辅生产配套模式。1999年三一重工开始自行研制37米长混凝土泵车,成为国内最早自行研制长臂架混凝土泵车的企业。目前我国混凝土泵车生产制造企业有十余家,生产能力主要集中在三一重工、徐工科技、辽宁海诺、上海普茨麦斯特等几个企业,其中三一重工约占国内市场的50%以上。1.2国内外泵车研究现状及发展趋势1.2.1臂架系统方面泵车的作业范围受到臂架长度的制约,臂架长度越长其作业范围越大,适用范围也越广。
16、但臂架越长,车辆行驶尺寸也越长,泵车在行驶及施工时往往受到限制。目前主要规格有:24,28,32,37,40,42,45,48,50,52,56,60,62,66,72米等。但总的来说,随着科技的发展,混凝土泵车朝着臂架更长的方向发展。目前,我国的臂架系统已基本实现自制,并在某些方面达到原装进口臂架的性能。但我国国产的钢材尚不能应用在臂架上,任然需要全部依靠进口,在制造过程中,焊条和焊接工艺要求非常严格。臂架系统在世界范围内尚是一个需要攻克的难题,如臂架应力裂缝,臂架断裂等。臂架应力断裂一般在应力较集中的焊接部位。目前,国外许多泵车的臂架制造都是采用不同厚度的高强度钢板拼焊焊接而成,采用这种方
17、法制造臂架时,需要知道可能出现的最大载荷。通过仿真计算臂架结构实际受力的大小。此外,臂架还存在振动较大的问题。涉及到设计、制造、元件和匹配问题。1.2.2泵送系统方面由于一些大型工程的施工需要,为满足在短时间内浇注大量混凝土的需要,泵车的泵送排量不断增大,上世纪九十年代,混凝土泵车的理论排量都在至左右,国外最大理论排量达到,泵送系统配置大直径的输送缸(直径为、),具有吸料性能好,泵送性能好的优点,不仅减少了磨损,而且降低了运营成本。分配阀形式主要采用S管阀。在易损件耐磨性方面,采用新耐磨材料、新工艺、新技术,较好地解决了易损件磨损快、更换频繁、影响设备正常施工等问题,使其寿命大大提高。1.2.
18、3节能技术方面由计算机自动判断负荷,并自动设定油耗模式,节约能源和保护设备过早磨损。而目前一般的泵车在任何工作强度下都是同一种耗油模式,造成了能源的浪费。1.2.4自动化、智能化方面 自动化、智能化是所有设备追求的目标,对于环境恶劣、劳动强度大的混凝土泵送设备尤其重要。目前混凝土泵车自动化技术已取得了一定成就,如全自动高低压切换、泵送排量无极调节、砼活塞自动退回、发动机转速闭环控制、防堵管控制、智能臂架、防倾翻保护和故障自动诊断等。对于泵车的堵管,本身堵管是混凝土泵送经常遇到的事,堵管若能早发现并采取正确的措施,一般都能排除,但发现太晚或没有采取正确的措施,管道就可能堵死,引起长时间的施工中断
19、,甚至影响建筑质量。防堵管控制采用压力传感器时时监测管道,当堵塞发生时,管道内压力会发生异常,压力传感器会将这一讯号传到PLC,PLC将立即发出警示,同时自动采取疏通措施。智能臂架方面,目前泵车臂架只能由操作者直接控制每一节臂架的动作,使臂架运动到理想的位置,而智能臂架的每一节臂都装有位置传感器,通过计算机可实现闭环控制和运动协调控制。操作时,只需要一个开关命令,控制计算机就能按规定程序控制臂架实现初始时的自动展开和用毕后的自动收拢;只需要给出泵车臂架末端出料口位置,就能实现多节臂的协调动作,使臂架能自动以最佳形态平稳移动到目标位置,简化了臂架操纵过程,提高了控制精度,也提高了施工效率。也可预
20、先设定臂架末端出口移动路线,使泵车臂架按程序设定的方式连续布料。泵车的防倾翻保护功能:首先混凝土泵车的支腿展开后能自动进行地面、支腿位置及整机水平等一系列监测,发现问题将会报警并锁住臂架不能展开。臂架在运行的时候,PLC仍会时刻监控整车的稳定性,发现四条支腿出现不稳定情况时,臂架会自动停止向危险的方向运动,同时发出警示,最大限度的保障安全。对于故障诊断,由于数字控制技术、智能传感等技术的发展,最终将会出现故障自动诊断技术,混凝土泵车将会有一个良好的人机界面。计算机会对整机进行监控,出现问题时,计算机能自动识别并通过人机界面进行交流,明确显示故障的部位及类型,比如活塞磨损到一定程度,系统自动提示
21、更换活塞;或者是转速不对、功率不足等等,系统都能自动向操作者提示。1.3课题研究思路和主要内容对泵车的整体结构、臂架系统、转塔系统、泵送系统及部分电气功能进行设计。设计过程中,泵送系统的泵送能力和混凝土塌落度决定了臂架系统配管的管径,臂架系统围绕此负载和要实现的泵送距离而进行设计。臂架系统的设计结果如果合理,将依照此来进行回转支承的选型和空间结构安排。通过计算臂架惯性力、风载、回转阻力等载荷后将数据用于回转减速机的设计。最后在根据泵车的浇注范围和浇注时臂架中心的移动范围设计支腿的机构和支承跨距。臂架系统的设计中运用虚拟设计。设计结果与传统设计进行比较。以查找泵车中存在的不足。转塔系统的受力仿真
22、计算,求出的受力情况真实的反映了泵车的工况。设计还包括泵送系统的泵送能力和总体设计。通过S管的承压、润滑和摆缸及料斗结构的联合设计,避免了空间上的干涉,满足运动要求和强度要求。回转减速机的设计采用了常用的二级行星齿轮减速机的结构。为力士乐的GFB系列回转减速机。对其内部齿轮进行标准更换,重新对齿轮轴强度分析,对回转支承的驱动采用了双惰轮驱动,满足了轮齿强度。对减速机制动离合器进行了设计。对泵送系统的工作情况进行分析,设计液压回路并实现电气控制自动化。专题为对臂架系统Pro/E中的三维实现,运动学仿真和动力学仿真。也对重要构件用ANSYS进行了结构分析。2 混凝土泵车的总体设计混凝土泵车的种类很
23、多,但其基本组成部件是相同的,混凝土泵车主要由底盘、臂架系统、转塔、泵送机构、液压系统和电气系统六大系统组成,如图2.1所示。1-底盘;2-臂架系统;3-转塔;4-液压系统;5-电气系统;6-泵送机构图2.1混凝土泵车总图其中底盘由汽车底盘、分动箱和副梁等部分组成;臂架系统由多节臂架、连杆、油缸和连接件等部分组成;转塔由转台、回转机构、固定转塔(连接架)和支撑结构等部分组成;泵送机构由主油缸、水箱、输送缸、砼活塞、料斗、S阀总成、摇摆机构、搅拌机构、出料口、配管等部分组成;电气系统主要由控制柜、遥控器及其它电气元件等部分组成。混凝土泵车的表示方法如图2.2所示。图2.2混凝土泵车表示方法291
24、混凝土泵装在底盘的尾部,以便混凝土搅拌运输车向泵的料斗卸料。如图2.3所示:混凝土搅拌车卸料到泵车料斗后,由其泵送机构压送到输送管,经末端软管(件15)排出。各节臂架的展开和收拢靠各节臂架油缸来完成。其中臂架中的1#臂架(件7)的仰角可在范围内摆动。2#臂架(件10)和3#臂架(件12)可摆动。四节臂架依次展开,其中4#臂架(件14)的动作最为频繁,它可以摆动左右,其末端软管在工作时应尽可能靠近工作部位,同时臂架可以通过回转马达及其减速机驱动回转轴承绕固定转塔旋转。1-泵送机构;2-支腿;3-配管总成;4-固定转塔;5-转台;6-1#臂架油缸;7-1#臂架;8-臂架输送管;9-2#臂架油缸;1
25、0-2#臂架;11-3#臂架油缸;12-3#臂架;13-4#臂架油缸;14-4#臂架;15-软管图2.3 37m泵车工作示意图2.1泵车臂架系统设计臂架系统用于混凝土的输送和布料。通过臂架油缸伸缩,转台转动,将混凝土经由附在臂架上的输送管,直接送达臂架末端所指位置即浇注点。以混凝土泵车臂架参考,其在一个固定点的某一平面的工作范围图如图2.4所示。图2.4混凝土泵车臂架工作范围2.1.1臂架折叠方式臂架系统主要由多节臂架、连杆、油缸、连接件铰接而成的可折叠和展开的平面四连杆机构组成,根据各节臂架间转动方向和顺序的不同,臂架有多种折叠型式,如:R型、Z型(或M型)、综合型等。各种折叠方式都有其独到
26、之处。R型结构紧凑;Z型臂架在打开和折叠时动作迅速;综合型则兼有前两者的优点而逐渐被广泛采用。具体的结构型式如图2.5所示。图2.5臂架折叠型式本设计采用的折叠方式如图2.6所示,为RZ混合型,接合了结构紧凑和折叠迅速的特点。图2.6综合型臂架折叠2.1.2臂架结构特点特点臂架可简化为一个细长的悬臂梁,其主要载荷为自重。它要求臂架强度大、刚性好、重量轻、因此,臂架的结构一般设计成四块钢板围焊而成的箱型梁,材料选用高强度细晶粒合金结构钢。为充分利用高强度钢优良的力学性能,按梁上各处应力趋于一致的原则,将梁设计成渐变梁。具体型式如图2.7所示。图2.7臂架的典型型式 2.1.3连杆的结构连杆一般为
27、直杆或弓形的二力杆,也有三角结构的连杆,如图2.8所示。图2.8连杆的几种典型形式2.1.4臂架油缸结构型式各节臂之间用液压油缸支撑,油缸为臂架运动提供动力,它有压力有推动活塞前后运动,从而驱动平面四连杆机构中的臂架绕铰接轴转动。缸体的进油口应设有液压锁,以防治液压软破裂时发生臂架坠落事故。具体结构如图2.9所示。1端盖,2阀安装板;3缸筒;4支撑环;5密封圈;6活塞;7活塞杆;8端盖;9压板;10耳环图2.9油缸的结构简图臂架油缸的行程控制由PLC控制单元智能控制,综合考虑,不再为臂架油缸设置缓冲装置。2.2泵车转塔结构转塔主要由转台、回转机构、固定转塔(连接架)和支撑结构等几部分组成。转塔
28、安装在汽车底盘中部,行驶时其载荷压在汽车底盘上;而泵送时,底盘轮胎离开地面,底盘和泵送机构也挂在转塔上。整个泵车(包括底盘、泵送机构、臂架系统和转塔自身)的载荷由转塔的四条支腿传给地面。臂架系统安装在转塔上,转塔为臂架提高一个稳固的底座,整个臂架可以在这个底座上旋转,每节臂架还能绕各自的轴旋转,转塔的四个支腿直接支承在地面上。2.2.1转台结构转台是由高强度钢板焊接而成的结构件,作为臂架的基座,它上部用臂架连接套与臂架铰接,下部用高强度螺栓与回转支承相连,主要承受臂架载荷,同时可随臂架一起在水平面内旋转。结构如图2.10所示。图2.10 转塔结构简图2.2.2回转机构回转机构集支承、旋转和连接
29、功能于一体,它由高强度螺栓、回转支承、回转减速机、主动齿轮和过渡齿轮(按强度取舍)组成。结构如图2.11所示。图2.11 回转机构结构简图回转减速机带动主动齿轮,经过渡齿轮驱动回转支承外圈,实现回转支承内外圈之间的慢速旋转。回转支承的外圈与上部转台、内圈与下部固定转塔用高强度螺栓相连,内外圈之间由交叉滚子(或钢球)连接。因此,它上部连接的臂架、转台与固定转塔之间即可实现低速旋转,而臂架、转台的工作载荷通过回转支承传给固定转塔。2.2.3 固定转塔结构固定转塔是由高强度钢板焊接而成的箱型受力结构件,是臂架、转台、回转机构的底座。混凝土泵车行驶时主要承受上部的重力,而混凝土泵车泵送时主要承受整车的
30、重力和臂架的倾翻力矩。同时高强度钢板围焊的空间,又可做液压油箱或水箱。因此,它既要有足够的强度和刚性,又要有良好的密封性。如图2.12所示。图2.12 固定转塔结构简图2.2.4支承结构支承结构的作用是将整车稳定地支承在地面上,直接承受整车的负载力矩和重量。1-支撑油缸;2-右前支腿;3-前支腿伸缩油缸;4-前支腿展开油缸;5-右后支腿;6-后支腿展开油缸;7-左后支腿;8-左前支腿图2.13 支撑结构简图图2.13为经常使用的后摆伸缩型支腿的支撑结构,由四条支腿,多个油缸组成。其中四条支腿、前后支腿展开油缸、前支腿伸缩油缸和支撑油缸构成大型框架,将臂架的倾翻力矩,泵送机构的反作用力和整车的自
31、重安全的由支腿传入地面。支腿收拢时与底盘同宽,展开支撑时能保证足够的支撑跨距。工作状态下,泵车在工地上的占地空间和整车的支撑稳定性由负载力矩、结构重量、支撑宽度、结构力学性能、支撑地面状况等因素决定。因此,它应具有合理的结构形式、足够的力学性能和有效的支撑范围,保证其承载能力和整车的抗倾翻能力,确保泵车工作时的安全稳定性。同时,应将支腿支撑在有足够刚度的或用其它材料按一定要求垫好的地面上,且整车各个方向倾斜度不超过,为此,在混凝土泵车左右两侧各装有一个水平仪来辨别倾斜度。2.3泵送机构的基本构造泵送机构是混凝土泵车的执行机构,用于将混凝土沿输送管道连接输送到浇注现场。泵送机构由主油缸、水箱、输
32、送缸、砼活塞、料斗、S阀总成、摆摇机构、出料口、配管等部分总成。工作原理:泵送机构如图2.14所示:泵送机构由两个主油缸1、2,水箱3,两个混凝土输送缸4、5,两个砼活塞6、7,摆摇机构8,分配阀9(S型阀),搅拌机构10,料斗11和出料口12组成。1、2-主油缸;3-水箱;4、5-输送缸;6、7-砼活塞;8-摆摇机构;9-分配阀(S阀总成);10-搅拌机构;11-料斗;12-出料口图2.14 泵送机构简图双列液压活塞式混凝土泵的两个主油缸交替工作,使混凝土的输送工作比较平稳、连续而且排量也大为增加,充分利用了原动机的功率。S管阀混凝土泵,其砼活塞(6、7)分别与主油缸(1、2)活塞杆连接,在
33、主油缸的作用下,作往复运动,一缸前进,另一刚后退;输送缸出口与料斗和S阀连通,S阀出料端接出料口,另一端通过花键轴与摆摇机构的摆臂连接,在摆摇机构的摆动油缸作用下,可以左右摆动。泵送混凝土料时,在主油缸的作用下,砼活塞7前进,砼活塞6后退,同时在摆动油缸作用下,S阀9与输送缸4连通,输送缸5与料斗连通。这样砼活塞6后退,便将料斗内的混凝土吸入输送缸,砼活塞7前进,将输送缸内混凝土料送入分配阀泵出。当砼活塞6后退至行程终端时,控制系统发出信号,主油缸1、2换向,同时摆动油缸换向,使S阀9与输送缸5连通,这时砼活塞7后退,砼活塞6前进。依次循环,从而实现连续泵送。反泵时,通过反泵操作,使处在吸入行
34、程的输送缸与S阀连通,处在推送行程的输送缸与料斗连通,从而将管路中的混凝土抽回料斗,如图2.15所示。图2.15 泵送机构工作状态简图2.3.1泵送系统组成泵送系统是泵送机构的核心部件,它是把液压能转换为机械能,通过油缸的推拉交替动作,使混凝土克服管道阻力输送到浇注部位。它主要是由主油缸、输送缸、水箱、砼活塞和拉杆等几部分组成。(一)主油缸主油缸由油缸体、油缸活塞、活塞杆、活塞头及缓冲装置组成。由于活塞杆不仅与油液接触,而且还与水等其它物质接触,为了改善活塞杆的耐磨和耐腐蚀性,在其表面要镀一层硬铬。(二)输送缸输送缸后端与水箱连接,前端与料斗连接,并通过料斗座与付梁固定,通过拉杆固定在料斗和水
35、箱之间。主油缸活塞杆伸入到输送缸内,前端与砼活塞连接。 输送缸一般用无缝钢管制造,由于输送缸内壁与混凝土、水长期接触,承受着剧烈的摩擦和化学腐蚀,因此,在输送缸内壁镀有硬铬层,或经过特殊处理以提高其耐磨性和抗腐蚀性。(三)砼活塞砼活塞由活塞体、导向环、密封体、活塞头芯和定位盘等组成。活塞密封体一般用耐磨的聚氨酯制成,其起导向、密封和输送混凝土的作用。如图2.16所示。图2.16 砼活塞(四)限位油缸限位油缸的作用是:当需要更换或者检查砼活塞时,限位油缸2的压力油从油口1卸载,从而式主油缸中的活塞能够一直退回到水箱中。如图2.17所示。1限位油缸油口;2限位油缸;3限位活塞:4主油缸油口:5主油
36、缸图2.17 限位油缸结构简图(五)水箱水箱用钢板焊制而成,既是储水容器,又是主油缸与输送缸的支持连接件。其上面有盖板,打开盖板可以清洗水箱内部,而且可以观测水位,如图2.18,在推送机构工作时,水在输送缸活塞后部随着输送缸活塞来回流动,起所起的作用主要是:1、清洗作用:清洗输送缸壁上每次推送后的残余物,以减少输送缸体与砼活塞的磨损2、密封作用:增加活塞杆的密封性,提套泵送吸入效率;3、冷却润滑作用:冷却润滑砼活塞、活塞杆及活塞杆密封部位。图2.18 水箱结构简图2.3.2料斗和S阀总成料斗料斗主要用于储存一定量的混凝土,保证泵送系统吸料时不会吸空和连续泵送。料斗主要由料斗体、上斗体、筛网、后
37、墙板和料门等几部分组成。料斗体用钢板焊接而成。左右带圆孔的侧板用来安装搅拌装置,其后墙板与两个输送缸连通,前墙板与输送管道相连。筛网用圆钢或钢板条焊接而成,用两个焦点同料斗连接。筛网可以防止混凝土中大于规定尺寸的骨料或其它杂物进入料斗,减少泵送故障,同时保护操作人员的安全。在停止泵送时,打开料门,可以排出余料和清洗料斗。具体结构如图2.19所示。1、后墙板;2、止动勾;3、筛网;4、上斗体;5、料斗体;6、料门图2.19 料斗结构简图S阀S阀是混凝土泵的关键部件,它位于料斗内连接输送缸和输送管,协调各部件动作的机构,因而直接影响混凝土泵的使用性能,而且也直接影响混凝土泵的整体设计。S管阀的管体
38、有变径和不变径两种型式。其特点是可以靠混凝土的压力推动切割环自动密封管口,密封性能好,使混凝土泵具有较强的输送能力,而且流道通畅,不易阻塞。具体结构如图2.20所示。1-出料口;2-大端轴承座;3-S管体;4-切割环;5-小端轴承座;6-螺母图2.20 S阀结构简图硬质合金机构眼镜板如图2.21所示,眼镜板由硬质合金环和眼镜板本体两部分组成,硬质合金材质为SD15,具有超强的硬度和耐磨性,提高了高压泵送易损件寿命。图2.21 眼镜板结构简图对分配阀设计有以下基本要求:1.良好的集、排料性能欲使混凝土泵具有良好的集、排料性能,能平滑地通过分配阀,分配阀的流道就必须短且流畅,截面和形状变化小;且对
39、混凝土的适应性强,能泵送不同塌落度的混凝土。2.良好的密封性阀门和阀体的相对运动,要有良好的密封性,以减少漏浆现象,影响混凝土的使用性能和泵送性能。3.良好的耐磨性分配阀的工作条件相当恶劣,工作过程中始终与混凝土进行强烈的摩擦,如果耐磨性不好,将极易损坏,而且破坏分配阀的密封性,影响混凝土泵的泵送性能指数。本设计采用材料为抗冲击、耐磨损的高锰钢ZGMn13Cr2铸成。4.换向动作灵活、可靠分配阀的换向动作,即吸入和排除动作应当协调、及时、迅速。一般换向动作应在0.1-05秒(最好0.2秒内完成),以防止砂浆倒流。S阀是混凝土泵的关键部件,它位于料斗内谅解输送缸和输送管,协调各部件动作的机构,因
40、而直接影响混凝土泵的使用性能,而且也直接影响混凝土泵的整体设计。S管阀的管体有变径和不变径两种形式。其特点是可以考混凝土的压力推动切割环自动密封管口,密封性能好,使混凝土泵油较强的输送能力,而其流道通畅,不易阻塞。S阀之所以被广泛应用,在于S阀最大的优点:切割环的浮动、自密封及橡胶弹簧自动补偿间隙。浮动指切割环在S阀上没有轴向固定,可以自由窜动;自密封指高压混凝土会作用在切割环的环面上,将切割环与眼镜板贴紧。2.3.3摆摇机构S阀的摆摇机构如图2.22所示,主要由摆缸固定座、左右摆阀油缸、摇臂和摆缸卡板等部分组成,处于料斗的后方。在液压油的作用下推动左右两个摆阀油缸的活塞杆,活塞杆驱动摇臂,摇
41、臂带动S阀左右摆动,从而实现S阀的换向。要求换向迅速,动作有力。摆缸固定座上有旋盖油杯,以供定期润滑,使球形摩擦面处于良好的润滑状态。图2.22 摇摆机构示意图2.3.4搅拌机构搅拌机构包括搅拌轴部件、搅拌轴承及其密封件。如图2.23所示:搅拌轴部件由搅拌轴叶片、轴套组成。搅拌轴是靠两端的轴承、轴承座(马达座)支撑的,搅拌轴承采用调心轴承,轴承座外部还装有黄油嘴的螺孔,其孔道通到轴承座的内腔,工作时可对轴承进行润滑。为了防止料斗内的混凝土浆进入搅拌轴承,搅拌轴左右两端装有多重密封圈和防尘圈。搅拌轴一端通过花键套和液压马达连接,工作时由液压马达直接驱动搅拌轴带动搅拌叶片搅拌。搅拌机构的主要作用是
42、对料斗里的混凝土进行二次搅拌,防止其离析。1-端盖;2-轴承座;3-左搅拌叶片;4-搅拌轴;5-右搅拌叶片;6-J型防尘圈;7-密封圈;8-轴承;9-马达座;10-液压马达图2.23 搅拌机构示意图2.3.5配管配管由一系列弯管、直管、卡管和输送管支撑组成,如图2.24所示。配管总的要求是在输送阻力尽量小的情况下,管道布置美观大方,与整车协调一致。图2.24 配管示意图臂架输送管附在臂架的臂侧,长度与臂长相配,各臂中部为一节节直管,二各臂两端头各为一个弯管。两管之间可相互旋转,两节相连臂架端头的弯管绕两臂架铰接轴轴线旋转,即可实现输送管随臂架转动而转动。输送管路的布置方式有两种,一种布管中有相
43、对转动的弯管均不横穿臂节相联结处的铰接销孔,另一种布管则是部分具有相对转动的弯管横穿臂节间的铰接销孔。第一种布管虽然支撑件的设计比较麻烦,但可以有效减小第三节弯臂对一二臂中性面的偏心扭矩,改善臂架整体受力状况。后者虽然布管方便许多,但臂架整体受力状况欠佳。本设计采用了图2.25所示的方案。图2.25臂架系统配管俯视图两输送管与管夹间连接的结构如图2.26所示。图2.26 输送管连接示意图由于各管安装位置不同,各输送管受到的冲击和磨损也不同,一般弯管比直管磨损大,越往臂末端走输送管磨损越小。但倒数第二个弯管的模数最大,它除受到一般的磨损外,还受到混凝土下落的重力冲击。因此,各输送管应采用不同的耐
44、磨措施,尽量使整套输送管寿命趋于一致。输送管支撑在臂架上,其重量、冲击和偏心力矩都由臂架承受,原则上臂架左右交替布管,并应尽量靠近臂架,以减小偏心力矩,在保证一定输送通径、强度 磨损余量的基础上应尽量轻。由于输送管的重量是臂架载荷的一部分,输送管不允许增加壁厚和外径,否则会降低臂架的使用寿命,也影响泵车的稳定性。输送管必须在臂架不受张力的状态下安装,如每节臂都自由地平置(各节臂架都被支撑好)、或每节臂被支撑时未折叠、或臂架完全收回并放到支承上时,臂架即不受张力。否则输送管上可能出现应力,造成管支架和臂架损坏,在泵送作业时,末端软管甚至可能剧烈晃动、脱出。3 臂架系统详细设计3.1臂架箱型结构分
45、析为减轻臂架重量,提高臂架强度,刚度和稳定性是改善臂架性能的主要途径。可采用高强度材料,合理选择截面形状,使臂架自重减小,充分利用材料,正确的设计计算方法往往带来事半功倍的效果。臂架有多种截面形式,如图3.1所示,其中矩形截面是由翼缘板和和腹板焊接而成的10。于其它截面相比,矩形截面的制造工艺简单,具有较好的抗弯能力和抗扭强度。图(a)的截面型式较好,整个臂架应力流畅,无明显力流阻滞和应力集中,而且重量较轻,至于抗扭曲和截面的稳定性可以通过焊接横穿臂架两侧板的输送管支撑件来解决。图3.1 臂架箱型结构3.2臂架钢板及焊接性能3.2.1钢板性能泵车臂架钢板采用瑞典SSAB公司的WELDOX960
46、钢板WELDOX系列钢板是瑞典SSAB钢铁公司开发生产的超高强度钢,集高强度与可焊性、长寿命于一身,WELDOX960作为新一代低合金高强钢,具有细晶粒超洁净度、高均匀性、高强度、高韧性和良好综合性能的新材料。在国内得到了较快的发展应用,主要应用范围:压力钢管、采矿设备矿用自卸车体和汽车起重机、桥梁、铁路、帆船龙骨、大的拱梁、斗铲的顶边的框架和主要的高韧性部件等领域。重量的减轻,减少了产品的总重量。3.2.2焊接性能焊接选取瑞典生产的ED-FK 1000高强焊丝,设计了WELDOX960高强钢的混合气体保护焊工艺,在预热、焊接线能量、层间温度的条件下进行多道焊接。WELDOX高强度结构钢板的合
47、金含量低,碳当量低,从而可用任何普通的电弧焊方法,就可将其焊在普通结构钢板上。在焊接WELDOX板时,其目标是:在焊接接头处获得适当的强度和良好的韧性。国际焊接学会推荐的碳当量公式为:随着碳当量的增加,钢材的焊接性能会变差,当值大于时,冷裂纹的敏感性将增大,焊接时需采取预热、后热等系列工艺措施。当焊接结构钢时,尽量减少冷裂纹的出现(氢裂或延期裂纹)至关重要。产生裂纹出现的主要原因是在有应力出现的焊口有氢气存在。工程机械的工作工况大多需要承受动载荷及重载荷,对焊缝的要求除强度指标外,还要求有较高的韧性。对于焊缝强度的选择问题,长期以来其高强钢的焊接大多采用“等强度匹配”,但对于诸如WELDOX系
48、列钢板,高强钢,除考虑强度外,还必须考虑焊接区的韧性和裂纹敏感性。就焊缝金属而言,强度越高,可达到的韧性水平往往越低,甚至低于木材的韧性水平。因此,在特殊情况下,对焊缝金属强度要求可低于母材,或刚度很大的焊接结构,为了减少焊接冷裂纹倾向,可选择比母材强度低一些的焊接材料。预热预热对平头焊缝和根部焊道最为重要。焊接过程中和焊接后的温度越高,则氢气越容易溢出;钢板越厚,预热的必要性越大,以补偿厚板更快的冷却速度,而且厚板的碳当量值更高;对被刚性固定的工件焊接时,预热也是必要的;对于不同钢种的钢焊接在一起时或焊接材料的碳当量比母材高,预热温度由碳当量最高的母材或焊接材料决定。当板厚大于时,必须分多层
49、焊接,第一层用ER49-1进行打底焊,第二层焊满,焊接层间温度控制在之间,焊接速度,电流,电压,送丝速度为。预处理所有焊缝焊前必须保证焊道干燥、清洁,除掉其中表面的油、水、锈和防锈漆,预热后必须用钢刷清理焊缝区域以清除积碳。焊丝,坡口及坡口周围范围内必须清理干净,不得有影响焊接质量的铁锈、油污、水和涂料等异物。对于重要的焊缝,在焊缝两端应设置尺寸合适的引弧板和引出板时,应注意防止在引弧和收弧处产生焊接缺陷。焊后热处理WELDOX只有在设计规则有特殊要求时方进行焊后热处理。避免裂纹出现的方法有:焊前预热母体材料:确保焊接面的清洁与干燥;选择含氢量小的焊料;通过良好的焊接顺序与工作的合理匹配减少收
50、缩内应力。(1) 确保焊接面的清洁和干燥。产生冷裂纹的主要原因时有应力存在的焊缝金属中有氢的存在。焊件在组装前应彻底清除坡口表面及附近母材上的氧化皮、铁锈、油污、水分等,直至露出金属光泽并保证清理范围内无裂纹与夹层等缺陷。(2) 减少构件内应力。采用合理的焊接顺序进行装焊,避免强力组对以减少构件的残余应力:焊接组装时应将工件压紧或垫置牢固,以防止因焊接受热而产生附加的应力和变形。(3) 焊后消氢处理。在焊接完成后,立即将焊件后热到,并按每毫米板厚不少于进行恒温处理后缓冷(且总的恒温时间不得小于),确保焊接接头中的残余氢能扩散溢出,减少延迟冷裂纹的产生。(4) 焊后热处理。进行焊后热处理是为了减
51、少焊接残余应力,高强钢焊后壁板不进行焊后热处理,热处理会使接头的某些力学性能下降,如:冲击韧度等。只有在设计规则有特殊说明时,方进行焊后热处理。3.3臂架系统结构设计臂架的设计高度约为,设计应该从第五节臂架依次向前,其载荷有管路的自重、混凝土重量、风载、惯性力其外加载荷如人力对末端软管的拽引等。输送管路所用钢管密度输送管路的单位长度重量:普通混凝土表观密度。输送管路中单位长度混凝土重量:取末端软管的长度为,重量为3.3.1第五臂架设计设计流程图如3.2所示。图3.2 臂架五设计流程图人对末端软管的拽引力折合为初步取臂架五的钢板厚度为,由于其为薄壁箱型结构,为悬臂梁。如图3.3所示。图3.3 薄
52、壁箱型由于臂架五的纵向截面非规则形状。故估取,可估算臂架五的单位长度重量:按臂架五长度为计算,臂架五的总重量为:臂架五的受力分析如图3.4可知,各臂架铰接处受力最大时,即是该臂架水平时。此时臂架的重心离铰接点最远,油缸的支撑力也是最大。臂架五铰接点附近的箱型结构强度计算:铰接点附近的箱型:; 臂架的抗弯强度初步计算:臂架五的铰接端最大拉应力计算:采用钢板的抗拉强度为 满足图3.4 臂架五受力图其中,;由Pro/E建模,测算得由此可得,动载系数即臂架油缸五的最大推力负载为实际设计时,考虑油缸的负荷裕量,取第五臂架油缸的为的型号。按工程车辆液压缸的标准选型即可。不再详细设计。臂架铰接处用柱销,尺寸
53、按以下材料性能计算:取材料为SiMn钢,抗拉强度,屈服点,断后伸长率,钢材退火或高温回火供应状态布氏硬度,安全系数取。横向力F作用时,若柱销的直径太小,对臂架的撕裂性显著增加,因此,可以将此销的尺寸加大,并作为空心销,柱销外径尺寸定为。3.3.2第四臂架设计臂架四的受力如图3.5所示:图3.5 臂架四受力图设计计算方法如同臂架五的设计。初定;臂架四的箱型截面,钢板厚度为单位长度重量由三维软件测算得:;;由动载荷及油缸裕量,选取臂架四油缸为的型号臂架间铰接处用柱销柱销尺寸按以下材料性能计算:取材料为SiMn钢,抗拉强度b885MPa屈服点s 735 MPa,断后伸长率5 15%,钢材退火或高温回
54、火供应状态布氏硬度HBS 229安全系数取横向力F作用时,因此,柱销尺寸定为臂架的抗弯强度初步计算:铰接点附近的箱型:; 臂架五的铰接端最大拉应力计算:满足钢板抗拉强度要求。3.3.3第三臂架设计第三臂架为折弯臂架,如图3.6所示。图3.6 臂架三由臂架折叠时空间上避免干涉,故第三节臂架设计为折弯式。折弯距离为相应管路也应该满足空间上不干涉的基本要求。初定臂架三长度为,钢板厚度为臂架三的箱型截面,受力情况如图3.7所示。图3.7 臂架三受力图;;由裕量和动载,所以取液压缸型号为臂架间铰接处用柱销柱销尺寸按以下材料性能计算:取材料为SiMn钢,安全系数取横向力F作用时,因此,柱销尺寸定为臂架的抗
55、弯强度初步计算:;臂架三的铰接端最大拉应力计算:采用钢板的抗拉强度为 满足抗弯强度,抗扭强度的计算如下:抗扭截面系数计算公式如下:满足抗扭强度要求。3.3.4第二臂架设计初定臂架长度为,钢板厚度为臂架二的箱型截面,受力如图3.8所示。图3.8 臂架二受力图;;所以臂架二的油缸二推力必须大于臂架的抗弯强度初步计算:;臂架五的铰接端最大拉应力计算:采用钢板的抗拉强度为 满足抗弯强度。由于臂架三的抗扭合格,因此臂架二的抗扭不用再加以校核。臂架铰接用柱销柱销尺寸按以下材料性能计算:取材料为SiMn钢,安全系数取横向力F作用时,因此,柱销尺寸定为3.3.5第一臂架设计初定臂架一长度为 钢板厚度为10mm
56、臂架一的箱型截面,受力如图3.9所示。臂架的抗弯强度初步计算:;臂架一的铰接端最大拉应力计算:采用钢板的抗拉强度为 满足抗弯强度。臂架三的抗扭合格,因此臂架一的抗扭不再加以校核。图3.9 臂架一受力图油缸推力因此,油缸的额定推力应该大于3.4臂架系统的计算机辅助设计运用Pro/E对设计的臂架系统的各臂架及相关辅件进行精确的设计,然后在MECAMISM中仿真,得出准确的结论,然后重新校核臂架油缸的推力及各臂架的最大拉应力及扭转应力是否满足要求。3.4.1臂架五的仿真过程在Pro/E Mechanica(M)中仿真必须注意到,臂架系统建模不应该过于复杂,尤其是其中的装配辅件不应过多,否则会出现计算
57、量过大,不能快速而准确的计算出仿真结果。将主要的结构件进行正确的装配,其余臂架上的附属构件、臂架附管、附管中的混凝土等的质量先进行初步计算,同时计算的还有附加载荷,如风载、人对末端软管的拉力等。然后以等质量钢板的形式平均地加在各段臂架上,如图3.10所示。管路为标准125A管,其中混凝土的体积为定值。混凝土的表观密度取。图3.10 臂架负载的等效代替对于臂架五的运动过程局部分析。取油缸五型号为,其额定推力约为,取仿真的初始位置为臂架处于水平时的位置。运动中测量位置如图3.11所示。运动终点和运动相关结果如图3.12所示。我们可以得出。臂架五的末端运动速度在终点时上升至约为,加速度保持在,总体惯
58、性力满足正常的工作要求。图3.11 仿真参量图图3.12 臂架五仿真曲线图3.4.2臂架二的仿真过程仿真初始位置如图3.13所示。图3.13 臂架二油缸受力仿真初始位置图对于臂架二的运动过程及油缸二受力分析。取油缸五型号为,取仿真的初始位置为臂架二、三、四处于水平时的位置。运动终点为臂架全部伸直时。运动中测量位置如图3.13所示。运动相关结果如图3.14所示。我们可以得出。臂架五的末端运动速度在终点时上升至约为,加速度保持在,总体惯性力满足正常的工作要求。图3.14 臂架二的运动仿真图由各臂架的单位长度估算各臂架重量如表3.1。表3.1 各臂架重量臂架重量/kg臂架一臂架二臂架三臂架四臂架五计
59、算过程估取值(按中部截面)1520688588439127Pro/E三维模型测量值1702835604426154其误差率分别为:;表3.2为各臂架油缸额定推力的详细计算值和仿真值的统计,分析其误差率,进行数据修订。表3.2 各臂架油缸载荷油缸型号/t油缸一油缸二油缸三油缸四油缸五详细计算11510871317.6Pro/E仿真12811772348.8其误差率分别为:;选取臂架油缸按仿真值选取。由于误差值并没有超出,故不用再修改臂架的钢板厚度或者箱型结构。3.5连杆的受力连杆编号与油缸编号相对应,连杆受力表3.3。表3.3 连杆受力连杆受力/KN连杆二连杆三连杆四连杆五直连杆11707203
60、4088弯连杆129093540363连杆材料的选取,四个直连杆和四个弯连杆均为高强抗拉钢板焊接而成。钢板材料为瑞典SSAB公司的WELDOX960钢板,屈服极限3.5.1直连杆二设计及应力校核连杆柱销尺寸按以下材料性能计算:取材料为SiMn钢,安全系数取横向力F作用时,因此,柱销尺寸定为。连杆的铜基无油轴承如图3.15所示。图3.15铜基无油轴承无油轴承直径,长度,承压面积:最大承载能力为:而臂架二在臂架一铰接点处的最大负荷为,小于轴承能承受的最大承压能力。其安全系数,满足使用要求。由于连杆为受压状态,为了保证连杆不被压溃,在连杆之间设计了两道加强筋作为支撑。如图3.16所示。图3.16 连杆结构简图在ANSYS中分析连杆的受力如图3.17所示。图3.17 直连杆二受力云图3.5.2弯连杆二设计及应力校核图3.18 弯连杆结构简图从图3.18可以看出,与直连杆铰接的孔的承压面积较小,其尺寸由直连杆宽度和臂架二的内侧宽度共同决定。承压面积:最大承载能力为:而直连杆二在直连杆一铰接点处的最大负荷为,小于轴承能承受的最大承压能力。其安全系数,满足使用要求。为了防止弯连杆与油缸二的活塞杆、直连杆二在臂架二运动时发生干涉,将弯连杆二的加强筋设计为如图所示的型式,最大限度的保证了其结构的
- 温馨提示:
1: 本站所有资源如无特殊说明,都需要本地电脑安装OFFICE2007和PDF阅读器。图纸软件为CAD,CAXA,PROE,UG,SolidWorks等.压缩文件请下载最新的WinRAR软件解压。
2: 本站的文档不包含任何第三方提供的附件图纸等,如果需要附件,请联系上传者。文件的所有权益归上传用户所有。
3.本站RAR压缩包中若带图纸,网页内容里面会有图纸预览,若没有图纸预览就没有图纸。
4. 未经权益所有人同意不得将文件中的内容挪作商业或盈利用途。
5. 装配图网仅提供信息存储空间,仅对用户上传内容的表现方式做保护处理,对用户上传分享的文档内容本身不做任何修改或编辑,并不能对任何下载内容负责。
6. 下载文件中如有侵权或不适当内容,请与我们联系,我们立即纠正。
7. 本站不保证下载资源的准确性、安全性和完整性, 同时也不承担用户因使用这些下载资源对自己和他人造成任何形式的伤害或损失。