砂型铸造生产工艺参数选择
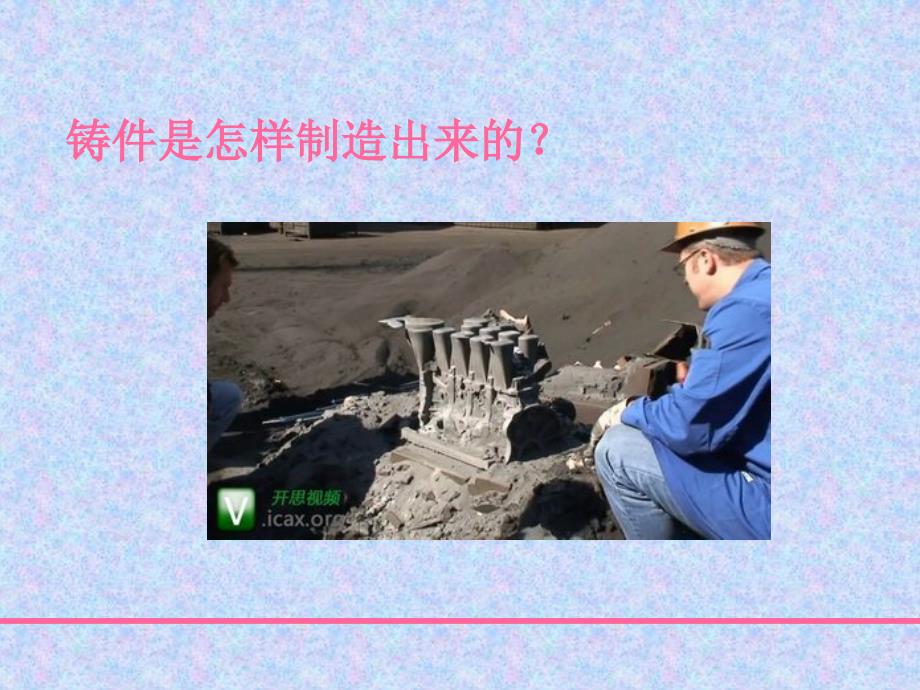


《砂型铸造生产工艺参数选择》由会员分享,可在线阅读,更多相关《砂型铸造生产工艺参数选择(79页珍藏版)》请在装配图网上搜索。
1、 铸件是怎样制造出来的?铸件是怎样制造出来的?第二节 浇注位置与分型面的选择v浇注位置的选择原则浇注位置的选择原则v分型面的选择原则分型面的选择原则 6.5.1浇注系统设计浇注系统设计浇注系统由浇注系统由浇口杯、浇口杯、直浇道、直浇道、横浇道横浇道内浇道内浇道四部分组成四部分组成图图6.19 浇注系统浇注系统1浇口杯浇口杯 2直浇道直浇道3横浇道横浇道 4内浇道内浇道 浇注位置浇注位置浇注时,铸件在铸浇注时,铸件在铸型中所处的位置型中所处的位置/铸件的某个铸件的某个表面位于铸型的上、下还是侧表面位于铸型的上、下还是侧面。面。浇口位置浇口位置内浇口与铸型型内浇口与铸型型腔连接处的位置腔连接处的位
2、置/液态金属流液态金属流入铸型型腔的位置。入铸型型腔的位置。上下浇注位置的选择 1、铸件的重要加工面或主要工作面应朝下。、铸件的重要加工面或主要工作面应朝下。2、铸件的大平面应朝下,以免夹砂。、铸件的大平面应朝下,以免夹砂。3、为防止铸件薄壁部分产生浇不足或冷隔现象,应将面、为防止铸件薄壁部分产生浇不足或冷隔现象,应将面积大的薄壁部分置于铸型下部或使其处于垂直、倾斜积大的薄壁部分置于铸型下部或使其处于垂直、倾斜位置。位置。4、容易形成缩孔缩松的铸件,厚大部位放在分型面附近、容易形成缩孔缩松的铸件,厚大部位放在分型面附近的上部或侧面,以便于安放冒口、冷铁。的上部或侧面,以便于安放冒口、冷铁。5、
3、应减少型芯的数量,便于型芯固定和排气。、应减少型芯的数量,便于型芯固定和排气。6、尽可能避免使用吊砂、吊芯或悬臂式砂芯。、尽可能避免使用吊砂、吊芯或悬臂式砂芯。7、应使合箱位置、浇注位置和铸件冷却位置一致,避免、应使合箱位置、浇注位置和铸件冷却位置一致,避免多次翻动砂箱。多次翻动砂箱。一、浇注位置的选择原则 浇注位置的选择原则车床床身上中下中铸件的重要加工面或主要工铸件的重要加工面或主要工作面应朝下作面应朝下因为在液体金属的浇注因为在液体金属的浇注过程中,其中的气过程中,其中的气体和熔渣往上浮;体和熔渣往上浮;而且由于静压力较而且由于静压力较小的原因也使铸件小的原因也使铸件上部组织不如下部上部
4、组织不如下部的致密。如图所示的致密。如图所示为车床床身的浇注为车床床身的浇注位置:床身的导轨位置:床身的导轨面是关键部分,要面是关键部分,要求组织致密且不允求组织致密且不允许有任何铸造缺陷,许有任何铸造缺陷,因此通常采用导轨因此通常采用导轨面朝下的浇注位置。面朝下的浇注位置。浇注位置的选择原则铸件的重要加工面或主要工铸件的重要加工面或主要工作面应朝下作面应朝下卷扬机筒 浇注位置的选择原则铸件的大平面应朝下,铸件的大平面应朝下,以免在此面上出现气孔和夹以免在此面上出现气孔和夹砂等缺陷。砂等缺陷。因为在金属液的充型过程中,灼热的金属液会对砂因为在金属液的充型过程中,灼热的金属液会对砂型上表面有强烈
5、的热辐射作用,使该表面的型砂拱型上表面有强烈的热辐射作用,使该表面的型砂拱起或开裂,导致金属液钻进裂缝处,这将使铸件的起或开裂,导致金属液钻进裂缝处,这将使铸件的该表面产生夹砂缺陷。该表面产生夹砂缺陷。浇注位置的选择原则为防止铸件薄壁部分产生浇不足或冷隔现象,应将面为防止铸件薄壁部分产生浇不足或冷隔现象,应将面积大的薄壁部分置于铸型下部或使其处于垂直、倾斜积大的薄壁部分置于铸型下部或使其处于垂直、倾斜位置位置。浇注位置的选择原则为防止铸件薄壁部分产生浇不足或冷隔现象,应将面积大为防止铸件薄壁部分产生浇不足或冷隔现象,应将面积大的薄壁部分置于铸型下部或使其处于垂直、倾斜位置的薄壁部分置于铸型下部
6、或使其处于垂直、倾斜位置。浇注位置的选择原则容易形成缩孔缩松的铸件,厚大部位放在分型面附近容易形成缩孔缩松的铸件,厚大部位放在分型面附近的上部或侧面,便于安置冒口。的上部或侧面,便于安置冒口。浇注位置的选择原则应减少型芯的数量,便于型芯固定和排气。应减少型芯的数量,便于型芯固定和排气。浇注位置的选择原则应减少型芯的数量,便于型芯固定和排气。应减少型芯的数量,便于型芯固定和排气。浇注位置的选择原则尽可能避免使用吊砂、吊芯或悬臂式砂芯。尽可能避免使用吊砂、吊芯或悬臂式砂芯。分型面分型面砂箱间的接触面砂箱间的接触面1、尽可能使用最少的分型面。、尽可能使用最少的分型面。2、应尽量使型芯、活块数量少。、
7、应尽量使型芯、活块数量少。3、尽量将铸件全部或大部放在同一砂箱以防止错型、飞翅、尽量将铸件全部或大部放在同一砂箱以防止错型、飞翅、毛刺等缺陷,保证铸件尺寸的精确。毛刺等缺陷,保证铸件尺寸的精确。4 4、应使铸件的加工面和加工基准面处于同一砂箱中。若铸件的、应使铸件的加工面和加工基准面处于同一砂箱中。若铸件的加工面很多,又不可能全部与基准面放在分型面的同一侧时,加工面很多,又不可能全部与基准面放在分型面的同一侧时,则应使加工基准面与大部分加工面处于分型面的同一侧。则应使加工基准面与大部分加工面处于分型面的同一侧。5、尽量选用平面、尽量选用平面避免曲面分型,并应尽量选在最大截面上,避免曲面分型,并
8、应尽量选在最大截面上,以简化模具制造和造型工艺。以简化模具制造和造型工艺。6、为便于造型、下芯、合箱、检验及检查,尽量将型腔置于、为便于造型、下芯、合箱、检验及检查,尽量将型腔置于下箱下箱二、分型面的选择原则 分型面的选择原则尽可能使用最少的分型面。尽可能使用最少的分型面。分型面的选择原则尽可能使用最少的分型面。尽可能使用最少的分型面。分型面的选择原则应尽量使型芯、活块数量少。应尽量使型芯、活块数量少。分型面的选择原则尽量将铸件全部或大部放在同一砂箱以防止错型、飞翅、尽量将铸件全部或大部放在同一砂箱以防止错型、飞翅、毛刺等缺陷,保证铸件尺寸的精确。毛刺等缺陷,保证铸件尺寸的精确。分型面的选择原
9、则尽量将铸件全部或大部放在同一砂箱以防止错型、飞翅、尽量将铸件全部或大部放在同一砂箱以防止错型、飞翅、毛刺等缺陷,保证铸件尺寸的精确。毛刺等缺陷,保证铸件尺寸的精确。分型面的选择原则尽量将铸件全部或大部放在同一砂箱以防止错型、飞翅、尽量将铸件全部或大部放在同一砂箱以防止错型、飞翅、毛刺等缺陷,保证铸件尺寸的精确。毛刺等缺陷,保证铸件尺寸的精确。分型面的选择原则应使铸件的加工面和加工基准面处于同一砂箱中。应使铸件的加工面和加工基准面处于同一砂箱中。螺栓塞头方头 分型面的选择原则 铸件的加工面很铸件的加工面很多,又不可能全部与多,又不可能全部与基准面放在分型面的基准面放在分型面的同一侧时,则应使加
10、同一侧时,则应使加工基准面与大部分加工基准面与大部分加工面处于分型面的同工面处于分型面的同一侧。一侧。轮毂的分型面加工基准 分型面的选择原则尽量选用平面,尽量选用平面,避免曲面分型,并应尽量选在最大截面上,避免曲面分型,并应尽量选在最大截面上,以简化模具制造和造型工艺。以简化模具制造和造型工艺。分型面的选择原则尽量选用平面。尽量选用平面。分型面的选择原则为便于造型、下芯、合箱、检验及检查,尽量将型腔置于为便于造型、下芯、合箱、检验及检查,尽量将型腔置于下箱下箱 第三节 铸造工艺参数的选择v机械加工余量机械加工余量v最小铸出孔、槽最小铸出孔、槽v拔模斜度拔模斜度v铸造圆角铸造圆角v收缩率收缩率v
11、型芯头型芯头v其它如分型负数、工艺补正量等其它如分型负数、工艺补正量等 1、机械加工余量铸件上为切削加工而加大的尺寸叫机械加工余量铸件上为切削加工而加大的尺寸叫机械加工余量铸造工艺参数的确定铸造工艺参数的确定12 1、机械加工余量零零件件上上需需要要加加工工的的表表面面,如如零零件件图图上上标标有有表表面面粗粗糙糙度度符符号号的的部部位位、注注有有尺尺寸寸公公差差的的部部位位、有有螺螺纹纹符符号号的的部部位位、注注有有表表面面形形位位尺尺寸寸公公差差代代号号的的部部位位等等应应需需有有适当的加工余量。适当的加工余量。加加工工余余量量过过大大,不不仅仅浪浪费费金金属属、增增加加机机加加工工工工时
12、时,而而且且还还会会因因截截面面增增加加、使使铸铸件件晶晶粒粒粗粗大大,力力学学性性能能降降低低;加加工工余余量量过过小小,可可能能会会因因错错型型等等原原因因造造成成切切削削余余量量不不够够、表表面面硬硬度度偏偏高高、甚甚至至留留有有黑黑皮皮达达不不到到尺尺寸寸精精度而报废。度而报废。铸造工艺参数的确定铸造工艺参数的确定 1、机械加工余量铸铸件件加加工工余余量量的的大大小小取取决决于于铸铸件件的的材材料料、铸铸造造方方法法、铸铸件件尺尺寸寸与与复复杂杂程程度度、生生产产批批量量、加加工工面面与与基基准准面面的的距距离离及及加加工工面面在在铸铸型型中中的的位位置置、加加工工精精度度要要求求等。
13、等。灰灰铸铸铁铁件件较较铸铸钢钢件件线线收收缩缩率率小小、熔熔点点低低,铸铸件件表表面面较较光光洁洁、平平整整,故故其其加加工工余余量量小小,铸铸钢钢件件加加工工余余量量应应比比铸铸铁铁件件大大:非非铁铁合合金金铸铸件件表表面面光光洁洁、且且材材料料昂昂贵贵、加加工工余余量量应应比比铸铸铁铁件件小小;铸铸件件的的尺尺寸寸愈愈大大或或加加工工面面与与基基准准面面的的距距离离愈愈大大,铸铸件件的的尺尺寸寸误误差差也也愈愈大大,故故余余量量也也应应随随之之加加大大;大大量量生生产产时时,因因采采用用机机器器造造型型,铸铸件件精精度度高高,故故余余量量可可减减小小,反反之之,手手工工造造型型余余量量应
14、应加加大大,此此外外,浇浇注注时时朝朝上上的的表表面面,因因产产生生缺缺陷陷的的机机率率大,其加工余量应比底面和侧面大。大,其加工余量应比底面和侧面大。铸造工艺参数的确定铸造工艺参数的确定 加工余量加工余量 铸造工艺参数的确定铸造工艺参数的确定 2、最小铸出孔、槽零零件件上上的的孔孔、槽槽、台台阶阶等等应应从从铸铸件件质质量量及及经经济济方方面面考考虑虑。较较大大的的孔孔、槽槽等等应应铸铸出出来来,以以便便节节约约金金属属和和机机械械加工工时,同时还避免铸件局部过厚所造成的热节,加工工时,同时还避免铸件局部过厚所造成的热节,提高铸件的质量;较小提高铸件的质量;较小的孔槽,则不宜铸出,的孔槽,则
15、不宜铸出,直接加工反而方便;有直接加工反而方便;有特殊要求,且无法实行特殊要求,且无法实行机加工的孔如弯曲孔,机加工的孔如弯曲孔,则一定要铸出。则一定要铸出。铸造工艺参数的确定铸造工艺参数的确定 3、拔模斜度为为使使模模样样容容易易从从铸铸型型中中取取出出或或型型芯芯自自芯芯盒盒中中脱脱出出,平行于起模方向在模样或芯盒壁上的斜度称为拔模斜度。平行于起模方向在模样或芯盒壁上的斜度称为拔模斜度。凡垂直于分型面(凡垂直于分型面(分盒面)的没有结分盒面)的没有结构斜度的壁均应设构斜度的壁均应设起模斜度。起模斜起模斜度。起模斜度的大小,应根据度的大小,应根据模壁测量面高度、模壁测量面高度、模样材料及造型
16、方模样材料及造型方法确定。法确定。铸造工艺参数的确定 3、拔模斜度外壁外壁0.253,内壁,内壁310铸造工艺参数的确定上下 4、铸造圆角R=(1/31/5)(a+b)/2铸造工艺参数的确定 5、收缩率收缩率指为了补偿铸件收缩,模样比铸件图样尺寸增指为了补偿铸件收缩,模样比铸件图样尺寸增大的数值。而用来度量模样尺寸的刻尺称为缩尺大的数值。而用来度量模样尺寸的刻尺称为缩尺(模模样工缩尺样工缩尺),其分度以普通尺的单位长度乘以,其分度以普通尺的单位长度乘以(1十铸十铸件线收缩率件线收缩率)。灰口铸铁:灰口铸铁:0.7%1.0%铸造碳钢:铸造碳钢:1.3%2.0%铝硅合金:铝硅合金:0.8%1.2%
17、有色合金:有色合金:1.0%1.5%铸造工艺参数的确定 6、型芯头型芯头指指模模样样上上的的突突出出部部分分,在在型型内内形形成成芯芯座座并并放放置置芯芯头头。或或指指型型芯芯的的外外伸伸部部分分,不不形形成成铸铸件件轮轮廓廓,只只是是落落入入芯芯座座内内,用用以以定定位位和和支支承型芯。承型芯。芯头可分为垂直芯头和水平芯头。单支芯头可分为垂直芯头和水平芯头。单支点的水平芯头又称为悬臂芯头。点的水平芯头又称为悬臂芯头。铸造工艺参数的确定 垂直芯头一般都有上下芯头,芯头高度垂直芯头一般都有上下芯头,芯头高度H主要取决于芯头直径主要取决于芯头直径d。为了提高芯头的稳。为了提高芯头的稳定性和可靠性,
18、下芯头定性和可靠性,下芯头斜度应小些斜度应小些(510),高度高度H应大些;为便于应大些;为便于合型、上芯头的斜度应合型、上芯头的斜度应大些大些(615),高度,高度H应小些。短而粗的芯头应小些。短而粗的芯头也可不留上芯头。也可不留上芯头。铸造工艺参数的确定 水平芯头其长度上主要取决于芯头直径水平芯头其长度上主要取决于芯头直径d和芯的长度。为便于下芯及合型,铸型上的芯和芯的长度。为便于下芯及合型,铸型上的芯座端部也应留有一定座端部也应留有一定的斜度、悬臂芯头必的斜度、悬臂芯头必须做得比较长而大,须做得比较长而大,并使用芯撑以防止芯并使用芯撑以防止芯下垂或被液体抬起。下垂或被液体抬起。芯头和芯座
19、之间应有芯头和芯座之间应有14mm的间隙的间隙S。铸造工艺参数的确定 7、分型负数分型负数 指为抵消铸件在分型部位的增厚,在模样指为抵消铸件在分型部位的增厚,在模样上相应减去的尺寸。砂型的分型面一般不可能上相应减去的尺寸。砂型的分型面一般不可能很平整,因此干型或表面烘干型合型后,上下很平整,因此干型或表面烘干型合型后,上下型不能密合,金属液就有可能从分型面处溢出,型不能密合,金属液就有可能从分型面处溢出,即即“跑火跑火”。为了防止跑火,就要在下型的分。为了防止跑火,就要在下型的分型面上铺设泥条、油泥条或石棉绳等,使上、型面上铺设泥条、油泥条或石棉绳等,使上、下型接触面密封,这样就使上箱抬高,增
20、加了下型接触面密封,这样就使上箱抬高,增加了铸件的高度或铸件顶面的厚度。制做模样时,铸件的高度或铸件顶面的厚度。制做模样时,为了使模样符合零件图上尺寸的要求,在模样为了使模样符合零件图上尺寸的要求,在模样上相应减去这个抬高的尺寸,即为分型负数。上相应减去这个抬高的尺寸,即为分型负数。铸造工艺参数的确定 7、工艺补正量工艺补正量由于工艺上的原因,在铸件相应部位非加由于工艺上的原因,在铸件相应部位非加工面上增加的金属层厚度称为工艺补正量。在工面上增加的金属层厚度称为工艺补正量。在单件、单件、小批量手工砂型铸造时,由于偏心,错小批量手工砂型铸造时,由于偏心,错型等原因可能造成铸造缺陷,采用工艺补正量
21、型等原因可能造成铸造缺陷,采用工艺补正量以减少废品率;对于成批大量生产的铸件,不以减少废品率;对于成批大量生产的铸件,不使用工艺补正量,而采用修改模具的方法。使用工艺补正量,而采用修改模具的方法。铸造工艺参数的确定 1、分型面分型面/浇注位置:用蓝线(或红线)和箭头表示,浇注位置:用蓝线(或红线)和箭头表示,加以汉字表示方向加以汉字表示方向2、机械加工余量:用红线画出轮廓,剖面处用红剖、机械加工余量:用红线画出轮廓,剖面处用红剖面线或全涂以红色表示。数值用红字标在加工符号面线或全涂以红色表示。数值用红字标在加工符号上。若加工余量带有斜度,可用分数表示。上。若加工余量带有斜度,可用分数表示。3、
22、非铸出孔、非铸出孔/槽:用红槽:用红“”表示。剖面处用红剖面线表示。剖面处用红剖面线或全涂红色。或全涂红色。4、芯头和型芯:用蓝线画出芯头,并注明尺寸。、芯头和型芯:用蓝线画出芯头,并注明尺寸。5、浇注系统:用红线画出,并标注尺寸。、浇注系统:用红线画出,并标注尺寸。6、活块:用红笔注明、活块:用红笔注明“活块活块”及其形式和编号。及其形式和编号。铸造工艺图的绘制 7、冷铁:用绿线或蓝线画出,并表明冷铁:用绿线或蓝线画出,并表明“冷铁冷铁”及其主要及其主要尺寸和编号尺寸和编号8、拔模斜度:用红线或文字表示。、拔模斜度:用红线或文字表示。9、铸造圆角:用文字表示。、铸造圆角:用文字表示。10、冒
23、口、冒口/出气口:用红线表示并表明主要尺寸及编号。出气口:用红线表示并表明主要尺寸及编号。11、其它参阅、其它参阅铸造手册铸造手册铸造工艺图的绘制 应用综合举例应用综合举例 铸造工艺图 铸造工艺图 【例2】要铸造图示支承台零件要铸造图示支承台零件40个,此件用于中等静个,此件用于中等静载荷,试选择铸造合金和绘出铸造工艺图。载荷,试选择铸造合金和绘出铸造工艺图。10 1.选材:选材:HT1502.铸型、造型方法:砂型,手工造型铸型、造型方法:砂型,手工造型3.浇注位置浇注位置/分型面:因支承台分型面:因支承台50mm的内孔及的内孔及外壁均无需加工,只有两端面有机械加工要外壁均无需加工,只有两端面
24、有机械加工要求。为使支承台两端面组织致密、满足加工求。为使支承台两端面组织致密、满足加工要求,所以将铸件水平放置、使两加工面在要求,所以将铸件水平放置、使两加工面在侧壁位置作为该件的浇注位置,这样还有利侧壁位置作为该件的浇注位置,这样还有利于型芯的固定、排气和检验。为便于起模、于型芯的固定、排气和检验。为便于起模、下芯和检验,选中间对称的最大截面为分型下芯和检验,选中间对称的最大截面为分型面。此时分型面与分模面一致。面。此时分型面与分模面一致。方案1 4.加工余量:最大尺寸加工余量:最大尺寸200查表得查表得4mm,考虑拔模斜度,下端取考虑拔模斜度,下端取3mm5.最小铸出孔:最小铸出孔:18
25、、21不予铸出不予铸出6.拔模斜度:垂直拔模斜度取拔模斜度:垂直拔模斜度取17.铸造圆角:铸造圆角:R358.型芯设计:型芯设计:9.浇注系统浇注系统10.铸造工艺图铸造工艺图 1.选材:选材:HT1502.铸型、造型方法:砂型,手工造型铸型、造型方法:砂型,手工造型3.浇注位置浇注位置/分型面:采用三箱造型分型面:采用三箱造型方案2 6.6铸件结构设计铸件结构设计6.6.1从合金的铸造性能考虑设计铸从合金的铸造性能考虑设计铸件结件结构构6.6.2从铸造工艺考虑设计铸件结构从铸造工艺考虑设计铸件结构 缺陷分析:缺陷分析:结论:结论:铸件壁厚介于临界壁厚和最小壁厚之间铸件壁厚介于临界壁厚和最小壁
26、厚之间1.铸件壁厚的设计铸件壁厚的设计原则原则1:合理设计铸件壁厚:合理设计铸件壁厚概念:概念:最小壁厚:在各种工艺条下,铸造合金能充满型腔的最小厚度。最小壁厚:在各种工艺条下,铸造合金能充满型腔的最小厚度。主要取决于合金的种类、铸件的大小及形状等因素。主要取决于合金的种类、铸件的大小及形状等因素。临界壁厚:各种铸造合金都存在一个临界壁厚,在砂型铸造条件下,临界壁厚:各种铸造合金都存在一个临界壁厚,在砂型铸造条件下,各种铸造合金临界壁厚约等于其最小壁厚的各种铸造合金临界壁厚约等于其最小壁厚的3倍。倍。如果所设计铸件的壁厚小于允许的如果所设计铸件的壁厚小于允许的“最小壁厚最小壁厚”,铸件就易产生
27、,铸件就易产生浇不足、冷隔等缺陷。浇不足、冷隔等缺陷。在铸造厚壁铸件时,容易产生缩孔、在铸造厚壁铸件时,容易产生缩孔、缩松、结晶组织粗大等缺陷,缩松、结晶组织粗大等缺陷,从而使铸件的力学性能下降。从而使铸件的力学性能下降。6.6.1从合金的铸造性能考虑设计铸件结构从合金的铸造性能考虑设计铸件结构 砂型铸造条件下铸件的最小壁厚值砂型铸造条件下铸件的最小壁厚值 原则原则2铸件壁后应均匀,铸件壁后应均匀,避免厚大截面避免厚大截面缺陷分析:缺陷分析:铸铸件如果壁厚过大会出现集中的缩孔铸铸件如果壁厚过大会出现集中的缩孔 原则原则3原则原则3:避免锐角连接:避免锐角连接缺陷分析:缺陷分析:锐角连接处易出现
28、热结合应力,并会导致应力集中,从锐角连接处易出现热结合应力,并会导致应力集中,从而产生裂纹、缩孔等缺陷。而产生裂纹、缩孔等缺陷。原则原则4原则原则4:减缓肋、辐收缩的阻碍减缓肋、辐收缩的阻碍缺陷分析:铸件各部分冷却速度不同而收缩不一致,形成较大的内应力。缺陷分析:铸件各部分冷却速度不同而收缩不一致,形成较大的内应力。当此应力超过合金的强度极限时,铸件会产生裂纹。当此应力超过合金的强度极限时,铸件会产生裂纹。实例分析实例分析1:a轮辐对称,收缩力相互抗衡,易出现裂纹,轮辐对称,收缩力相互抗衡,易出现裂纹,b、c较好较好 原则原则5原则原则5:避免出现过大的水平面避免出现过大的水平面缺陷分析:缺陷
29、分析:薄壁罩壳铸件,当其壳顶呈水平面时,因薄薄壁罩壳铸件,当其壳顶呈水平面时,因薄壁件金属液散热冷却快,渣、气易滞留在顶壁件金属液散热冷却快,渣、气易滞留在顶面,易产生浇不足、冷隔、气孔和夹渣缺陷。面,易产生浇不足、冷隔、气孔和夹渣缺陷。实例:实例:6.6.2从铸造工艺考虑设计铸件结构从铸造工艺考虑设计铸件结构1.铸件的外形设计铸件的外形设计应保证模样能顺利从铸型中取出:应保证模样能顺利从铸型中取出:b、d较好较好 应尽量减少分型面的数量应尽量减少分型面的数量 应尽量使分型面是一个平直的面应尽量使分型面是一个平直的面若分型面是一曲面,则必须用挖砂造型若分型面是一曲面,则必须用挖砂造型(a)(b
30、)图5.51摇臂铸件(a)不合理(b)合理 铸件的垂直壁上应考虑给出结构斜度铸件的垂直壁上应考虑给出结构斜度图5.54结构斜度的设计 2.铸件的内腔设计铸件的内腔设计原则:减少原则:减少型型芯数量,利于型芯的固定、排气和清理。芯数量,利于型芯的固定、排气和清理。作用:防止偏芯、气孔等缺陷的产生;作用:防止偏芯、气孔等缺陷的产生;简化造型工艺,降低成本。简化造型工艺,降低成本。铸件内腔设计铸件内腔设计减少型芯的数量,避免不必要的型芯;减少型芯的数量,避免不必要的型芯;便于型芯的稳定、排气和铸件的清理。便于型芯的稳定、排气和铸件的清理。减少型芯的数量,避免不必要的型芯减少型芯的数量,避免不必要的型
31、芯实例分析:实例分析:实例分析实例分析:便于型芯的稳定、排气和铸件的清理便于型芯的稳定、排气和铸件的清理实例分析:实例分析:6.7铸造常见缺陷及控制铸造常见缺陷及控制6.7.1铸造常见缺陷铸造常见缺陷6.7.2铸件的修补铸件的修补 6.7.1铸造常见缺陷铸造常见缺陷缩孔的形成:纯金属、共晶成分和凝固温度范围窄的合金纯金属、共晶成分和凝固温度范围窄的合金,浇注后在型浇注后在型腔内是由表及里的逐层凝固。在凝固过程中,如得不到腔内是由表及里的逐层凝固。在凝固过程中,如得不到合金液的补充,在铸件最后凝固的地方就会产生缩孔合金液的补充,在铸件最后凝固的地方就会产生缩孔.1缩孔与缩松缩孔与缩松 缩松的形成
32、原因缩松的形成原因:铸件最后凝固的收缩未能得到补足,或者结晶铸件最后凝固的收缩未能得到补足,或者结晶温度范围宽的合金呈糊状凝固,凝固区域较宽,温度范围宽的合金呈糊状凝固,凝固区域较宽,液、固两相共存,树枝晶发达,枝晶骨架将合液、固两相共存,树枝晶发达,枝晶骨架将合金液分割开的小液体区难以得到补缩所致。金液分割开的小液体区难以得到补缩所致。缩松图5.59缩松形成过程散热方向凝固层 消除缩孔和缩松的方法消除缩孔和缩松的方法定向凝固原则定向凝固原则铸件让远离冒口的地方先凝固,铸件让远离冒口的地方先凝固,靠近冒口的地方次凝固,最后靠近冒口的地方次凝固,最后才是冒口本身凝固。实现以厚才是冒口本身凝固。实
33、现以厚补薄,将缩孔转移到冒口中去。补薄,将缩孔转移到冒口中去。原理原理合理布置内浇道及确定浇铸工艺。合理布置内浇道及确定浇铸工艺。方法方法合理应用冒口、冷铁和补贴等工艺措施。合理应用冒口、冷铁和补贴等工艺措施。a)合理选择内浇道)合理选择内浇道在铸件上的引入在铸件上的引入位置和高度;位置和高度;b)开设冒口;)开设冒口;c)放置冷铁。冷)放置冷铁。冷铁是用来控制铸铁是用来控制铸件凝固顺序的激件凝固顺序的激冷物。冷物。解决缩孔的方法解决缩孔的方法 铸件收缩时受阻就产生铸造应力,铸造应力按铸件收缩时受阻就产生铸造应力,铸造应力按产生的原因不同,主要可分为热应力、收缩应力两产生的原因不同,主要可分为
34、热应力、收缩应力两种。种。(1)热应力:)热应力:铸件在凝固和冷却过程中,不同部铸件在凝固和冷却过程中,不同部位由于不均衡的收缩而引起的应力,称热应力。位由于不均衡的收缩而引起的应力,称热应力。(2)收缩应力:铸件在固态收缩时,因受铸型、)收缩应力:铸件在固态收缩时,因受铸型、型芯、浇冒口等外力的阻碍而产生的应力称收缩应型芯、浇冒口等外力的阻碍而产生的应力称收缩应力。力。2铸造应力铸造应力 铸件收缩时受阻就产生铸造应力,当应力超过材料的铸件收缩时受阻就产生铸造应力,当应力超过材料的屈服极限时,铸件产生变形。应力超过材料的抗拉强度屈服极限时,铸件产生变形。应力超过材料的抗拉强度时,铸件就产生裂纹
35、时,铸件就产生裂纹3变形和裂纹变形和裂纹4气孔气孔在铸件内部、表面或近于表面处,出现的大小不等的在铸件内部、表面或近于表面处,出现的大小不等的光滑孔眼。光滑孔眼。在铸件内部或表面形状不规则的孔眼。孔眼不光滑,里在铸件内部或表面形状不规则的孔眼。孔眼不光滑,里面全部或部分充塞着熔渣。面全部或部分充塞着熔渣。5渣气孔渣气孔6砂眼砂眼在铸件内部或表面充塞着型砂的孔眼在铸件内部或表面充塞着型砂的孔眼7粘砂粘砂在铸件表面上,全部或部分覆盖着一层金属(或金属氧化在铸件表面上,全部或部分覆盖着一层金属(或金属氧化物)与砂(或涂料)的混(化)合物或一层烧结的型砂物)与砂(或涂料)的混(化)合物或一层烧结的型砂 8夹砂夹砂在金属瘤片和铸件之间夹有一层型砂在金属瘤片和铸件之间夹有一层型砂9冷隔冷隔在铸件上有一种未完全融合的缝隙或洼坑在铸件上有一种未完全融合的缝隙或洼坑10浇不到浇不到金属液未完全充满型腔。金属液未完全充满型腔。6.7.2铸件的修补铸件的修补铸件的修补方法有:铸件的修补方法有:1 1气焊或电焊修补气焊或电焊修补 2 2金属喷镀金属喷镀 3 3浸渍法浸渍法 填腻修补填腻修补 5 5金属液熔补金属液熔补
- 温馨提示:
1: 本站所有资源如无特殊说明,都需要本地电脑安装OFFICE2007和PDF阅读器。图纸软件为CAD,CAXA,PROE,UG,SolidWorks等.压缩文件请下载最新的WinRAR软件解压。
2: 本站的文档不包含任何第三方提供的附件图纸等,如果需要附件,请联系上传者。文件的所有权益归上传用户所有。
3.本站RAR压缩包中若带图纸,网页内容里面会有图纸预览,若没有图纸预览就没有图纸。
4. 未经权益所有人同意不得将文件中的内容挪作商业或盈利用途。
5. 装配图网仅提供信息存储空间,仅对用户上传内容的表现方式做保护处理,对用户上传分享的文档内容本身不做任何修改或编辑,并不能对任何下载内容负责。
6. 下载文件中如有侵权或不适当内容,请与我们联系,我们立即纠正。
7. 本站不保证下载资源的准确性、安全性和完整性, 同时也不承担用户因使用这些下载资源对自己和他人造成任何形式的伤害或损失。