管道基础知识
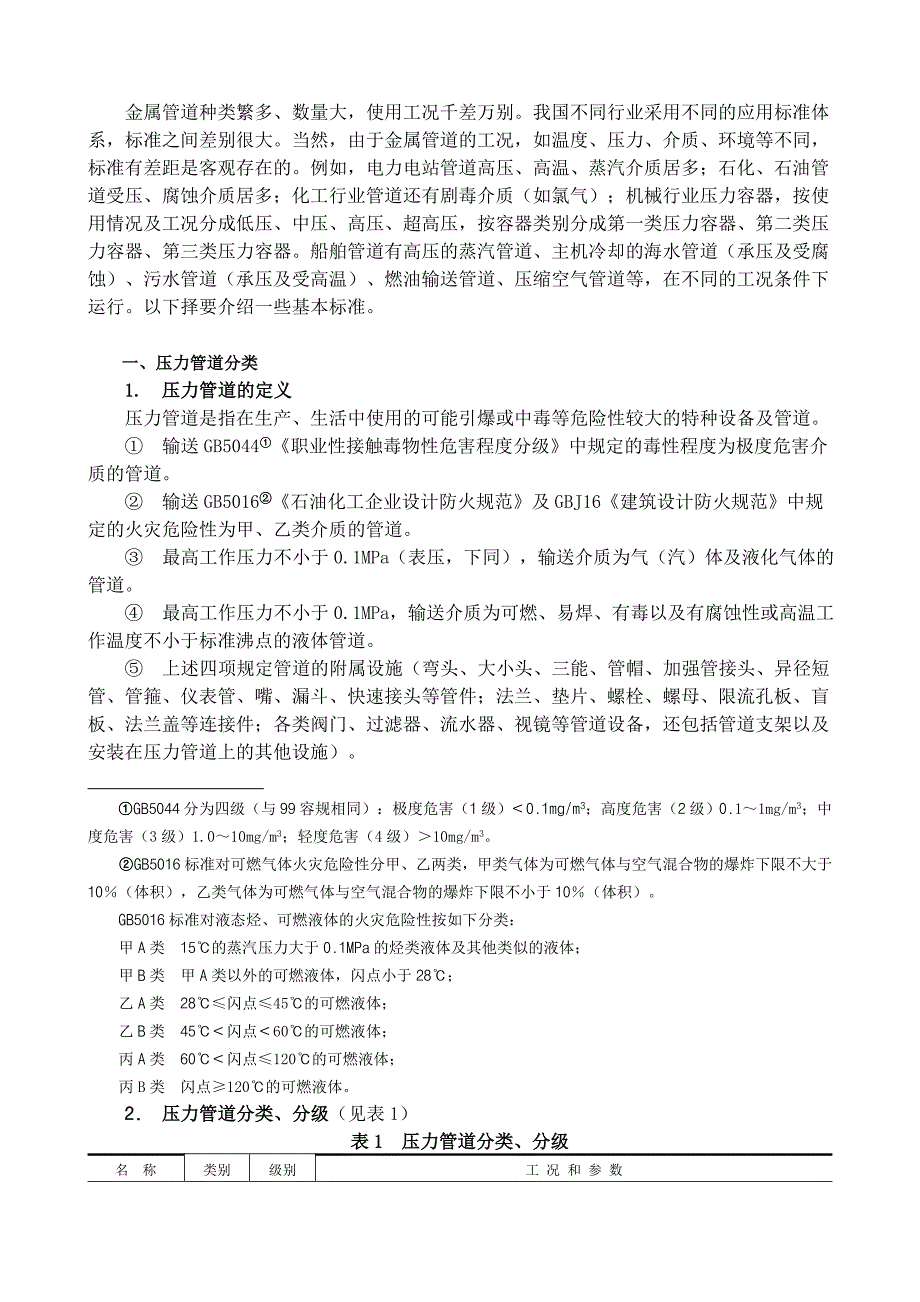


《管道基础知识》由会员分享,可在线阅读,更多相关《管道基础知识(20页珍藏版)》请在装配图网上搜索。
1、金属管道种类繁多、数量大,使用工况千差万别。我国不同行业采用不同的应用标准体系,标准之间差别很大。当然,由于金属管道的工况,如温度、压力、介质、环境等不同,标准有差距是客观存在的。例如,电力电站管道高压、高温、蒸汽介质居多;石化、石油管道受压、腐蚀介质居多;化工行业管道还有剧毒介质(如氯气);机械行业压力容器,按使用情况及工况分成低压、中压、高压、超高压,按容器类别分成第一类压力容器、第二类压力容器、第三类压力容器。船舶管道有高压的蒸汽管道、主机冷却的海水管道(承压及受腐蚀)、污水管道(承压及受高温)、燃油输送管道、压缩空气管道等,在不同的工况条件下运行。以下择要介绍一些基本标准。一、压力管道
2、分类1. 压力管道的定义压力管道是指在生产、生活中使用的可能引爆或中毒等危险性较大的特种设备及管道。 输送GB5044职业性接触毒物性危害程度分级中规定的毒性程度为极度危害介质的管道。 输送GB5016石油化工企业设计防火规范及GBJ16建筑设计防火规范中规定的火灾危险性为甲、乙类介质的管道。 最高工作压力不小于0.1MPa(表压,下同),输送介质为气(汽)体及液化气体的管道。 最高工作压力不小于0.1MPa,输送介质为可燃、易焊、有毒以及有腐蚀性或高温工作温度不小于标准沸点的液体管道。 上述四项规定管道的附属设施(弯头、大小头、三能、管帽、加强管接头、异径短管、管箍、仪表管、嘴、漏斗、快速接
3、头等管件;法兰、垫片、螺栓、螺母、限流孔板、盲板、法兰盖等连接件;各类阀门、过滤器、流水器、视镜等管道设备,还包括管道支架以及安装在压力管道上的其他设施)。 GB5044分为四级(与99容规相同):极度危害(1级)0.1mg/m3;高度危害(2级)0.11mg/m3;中度危害(3级)1.010mg/m3;轻度危害(4级)10mg/m3。 GB5016标准对可燃气体火灾危险性分甲、乙两类,甲类气体为可燃气体与空气混合物的爆炸下限不大于10(体积),乙类气体为可燃气体与空气混合物的爆炸下限不小于10(体积)。GB5016标准对液态烃、可燃液体的火灾危险性按如下分类:甲A类 15的蒸汽压力大于0.1
4、MPa的烃类液体及其他类似的液体;甲B类 甲A类以外的可燃液体,闪点小于28;乙A类 28闪点45的可燃液体;乙B类 45闪点60的可燃液体;丙A类 60闪点120的可燃液体;丙B类 闪点120的可燃液体。2. 压力管道分类、分级(见表1)表1 压力管道分类、分级名 称类别级别工 况 和 参 数长输管道GAGA1 介质:有毒、可燃易爆气体,P1.6MPa的管道 介质:有毒、可燃易爆气体,DN300mm,输送距离200km的管道 介质:浆体中,DN150mm,输送距离50km的管道GA2 介质:有毒、可燃易爆气体,P1.6MPa的管道 GA1(2)范围以外的长输管道 GA1(3)范围以外的长输管
5、道公用管道GBGB1 燃气管道GB2 热力管道工业管道GCGC1 GB5044标准中,毒性程度为极度危害介质的管道 GB50160、GBJ16标准中规定的火灾危险性为甲、乙类可燃气体或甲类可燃气体介质,且P4.0MPa的管道 输送流体介质,且P10.0MPa的管道GC2 输送GB50160、GBJ160标准中规定的火灾危险性为甲、乙类可燃气体或甲类可燃气体介质,且P0.4MPa的管道 流体介质:可燃、有毒,P4.0MPa,t400的管道 流体介质:不可燃、无毒,P10MPa,t400的管道 流体介质: P10.0MPa,t400的管道注:表中P为设计压力;t为工作温度;DN为公称直径。3. 中
6、石化集团公司压力管道分类(见表2)表2 中石化集团公司压力管道分类类别工 况 和 参 数第一类 输送毒性程度为极度、高度危害的介质所使用管道(苯除外) 35.0MPaP10.0MPa的管道第二类 P10.0MPa,输送甲、乙类可燃气体,甲A类、乙类可燃液体介质的管道 工作温度高于闪点的可燃液体介质管道 P4.0MPa,无毒、不可燃介质管道(不含输水管道)第三类 乙B类、丙类可燃液体管道 P1.6MPa,不可燃介质管道(不含水管) P0.1MPa,输送介质为汽(气)体,有毒、有腐蚀性或温度不低于标准沸点的液体管道第四类 P35.0MPa超高压管道第五类长输管道第六类公用管道,含公用燃气和热力管道
7、 4. 管子系列标准压力管道设计及施工,首先考虑压力管道及其元件标准系列的选用。世界各国应用的标准体系虽然多,大体可分成两大类。压力管道标准见表3。法兰标准见表4。表3 压力管道标准分 类大外径系列小外径系列规格DN-公称直径外径DN15-22mm,DN20-27mmDN25-34mm,DN32-42mm DN40-48mm,DN50-60mm DN65-76(73)mm,DN80-89mm DN100-114mm,DN125-140mm DN150-168mm,DN200-219mm DN250-273mm,DN300-324mmDN350-360mm,DN400-406mm DN450-4
8、57mm,DN500-508mm DN600-610mm,DN15-18mm,DN20-25mmDN25-32mm,DN32-38mm DN40-45mm,DN50-57mm DN65-73mm,DN80-89mm DN100-108mm,DN125-133mm DN150-159mm,DN200-219mm DN250-273mm,DN300-325mmDN350-377mm,DN400-426mm DN450-480mm,DN500-530mm DN600-630mm,表4 法兰标准分 类欧式法兰(以200为计算基准温度)美式法兰(以430为计算基准温度)规格PN压力等级压力等级:PN0.
9、1,PN0.25,PN0.6,PN1.0,PN1.6,PN2.5,PN4.0,PN6.3,PN10.0,N16.0,PN25.0,PN40.0压力等级:PN2.0(CL150),PN5.0(CL300),PN6.8(CL400),PN10(CL600),PN15.0(CL600),PN25(CL1500),PN42.0(CL2500)注:对于CL150(150lb级)是以300作计算基准温度。从表3、表4可知,无论是管子还是法兰,两个系列均不能混合使用。二、管道焊接常用标准1. 管道焊接常用标准关于压力管道的施工规范,综合性的有GB 50235、GB 50236和SH 3501石油化工剧毒、可
10、燃介质管道施工验收规范、HC 20225化工金属管道施工及验收规范、J28城市供热管网工程及验收规范、CJJ23城市燃气输配工程施工及验收规范等。GB 50235和SH 3501这两个综合性施工规范是目前石油化工生产建设中最常用的标准。输油、输气长输管道建设发展很快,这方面的标有行业标准SY 04011998输油输气管道线路工程施工及验收规范。为了便于阅读,在表5中列出了压力管道焊接常用标准。表5 压力管道焊接常用标准编 号名 称 国家质量技术监督局 锅发(1999)154号 压力容器安全技术监察规程(99容器) DL 5031、(DL-5007) 电力建设施工及验收技术规范(管道篇)(焊接篇
11、) GB 50235 工业金属管道工程施工及验收规范 GB 50236 现场设备工业管道焊接工程施工及验收规范 GB50184 工业金属管道工程质量检验评定标准 GB 985 气焊、手工电弧焊气体保护焊焊缝坡口的基本形式与尺寸 GB986 埋弧焊焊缝坡口的基本形式和尺寸 JB 4708 钢制压力容器焊接工艺评定 JB/T 4709 钢制压力容器焊接规程 JB 4730 压力容器无损检测 SHJ 502 钛管道施工及验收规范 SHJ 509 石油化工工程焊接工艺评定SHJ 517 石油化工钢制管道工程施工工艺 SHJ 514 石油化工设备安装工程质量检验评定标准 SHJ 520 石油化工工程铬钼
12、耐热钢管道焊接技术规程 SH 3501 石油化工剧毒、可燃介质管道施工及验收规范 SH 3508 石油化工工程施工工程及验收统一标准 SH 3523 石油化工工程高温管道焊接规程 SH 2525 石油化工低温钢焊接规程 SH 3526 石油化工异种钢焊接规程 SH 3527 石油化工不锈钢复合钢焊接规程 HC 20225 化工金属管道施工及验收规范 CCJ 28 城市供热管网工程及验收规范 GB/T 9711.11998 螺旋焊管生产标准 中国船级社材料与焊接规范1998第九章压力管系焊接SY 04011998 输油输气管道线路工程施工及验收规范为了对国外通用的和先进的相关标准体系有所了解,现
13、将有关管道的国外部分常用标准体系列于表6。表6 国外部分常用标准体系国 别标 准 号标 准 名 称德国(DNI)DIN 2410.T.1管子及钢管标准概述DIN 2448无缝钢管 尺寸及单位长度质量DIN 2458焊接钢管 尺寸及单位长度质量DIN 2501.T.1法兰连接尺寸美国(ANSI)ANSI/ASME 836.10无缝及焊接钢管ANSI/ASME B36.19不锈钢无缝及焊接钢管ANSI/ASME E16.9工厂制造的钢对焊管件ANSI/ASME B16.28钢制对焊小半径弯头和回弯头ANSI/ASME B16.5管法兰和法兰管件ANSI/ASME B16.47大直径钢法兰日本(JI
14、S)JIS G3452普通用途碳钢管JIS G3454承压用碳钢管JIS G3455高压用碳钢管JIS G3456高温用碳钢管JIS G3457电弧焊碳钢管JIS G3458合金钢管JIS G3459不锈钢钢管JIS G3468电弧焊大直径不锈钢钢管JIS B2201铁素体材料管法兰压力等级JIS B2202管法兰尺寸JIS B2210铁素体材料管法兰基础尺寸JIS B2220钢制管法兰JIS B2311普通用途的钢制对焊管件JIS B2312钢制对焊管件JIS B2313钢板制对焊管件国际标准化组织(ISO)ISO 4200焊接和无缝平端钢管尺寸和单位长度ISO 1127不锈钢钢管尺寸公差和
15、单位长度质量ISO 3183石油和天然气工业用钢管ISO 6759热交换器用无缝钢管ISO 7005-1金属管法兰英国(BS)BS 1600石油工业用钢管尺寸BS 3600承压用焊接钢管和无缝钢管的尺寸及单位长度质量BS 3605.1承压焊接无缝不锈钢钢管BS 1965对焊承压管件BS 1640石油工业用对焊管件三、压力管道焊接规范规程标准摘录压力管道规范规程很多,焊接规范规程也不少,现摘录部分规范规程供读者在工作中参阅。1. 国家质量技术监督局压力容器安全技术监察规程1999154号(摘录)1) 压力容器分类 按设计压力(P)分为低压、中压、高压和超高压四个压力等级,见表7。表7 压力容器等
16、级压力等级代号压力P/MPa压力等级代号压力P/MPa低压L0.1P1.6高压H10P100中压M1.6P10超高压UP100 按压力容器在生产工艺过程中的作用原理分为五种,见表8。表8 按作用原理压力容器分类分 类代 号用 途反应压力容器R 主要用于完成介质的物理、化学反应的压力容器、反应器、反应釜、分解锅、硫化罐、分解塔、聚合釜、高压釜、超高压釜、合成塔、变换炉、蒸煮锅、蒸球、蒸压釜、煤气发生炉等换热压力容器E 主要用于完成介质热量交换的压力容器、管壳式余热锅炉、热交换器、冷却器、冷凝器、蒸发器、加热器、消毒锅、染色器、烘缸、蒸炒锅、预热锅、溶剂预热器、蒸锅、蒸脱机、电热蒸汽发生器、煤气发
17、生炉水夹套等分离压力容器S 主要用于完成介质的流体压力平衡缓冲和气体净化分离器的压力容器,如分离器、过滤器、集油器、缓冲器、吸收塔、铜洗塔、干燥塔、汽提塔、分汽缸、除氧器等储存压力容器C,其中球罐代号B 主要用于储存、盛装气体、液体、液化气体等介质的压力容器,如各种形式的储罐 介质毒性程度的分级和易燃介质的划分,参照GB 5044,分为四级;极度危害(级),最高允许浓度0.1mg/m3;极度危害(级),最高允许浓度0.11.0mg/m3;极度危害(级),最高允许浓度1.010mg/m3;极度危害(级),最高允许浓度10mg/m3。 压力容器按适用范围分类(一、二、三类压力容器)。按99容规第2
18、条适用范围内的压力容器分类,见表9。表9 压力容器分类容器类别容 器 范 围第一类压力容器 低压容器0.1MPaP1.6MPa(第二类、第三类中规定的压力容器除外)第二类压力容器 中压容器1.6MPaP10MPa低压容器(仅限毒性程度为极度和高度危害介质)低压反应容器和低压储存容器(仅限易燃介质或毒性程度为中度危害介质)低压管壳式余热锅炉低压搪玻璃压力容器第三类压力容器高压容器10MPaP100MPa中压容器(仅限毒性程度为极度和高度危害介质)中压储存容器(仅限易燃或毒性程度为中度危害介质,且PV乘积大于或等于10MPam3)中压反应容器(仅限易燃或毒性程度为中度危害介质,且PV乘积大于或等于
19、0.5MPam3)低压容器(仅限毒性程度为极度和高度危害介质,且PV乘积大于或等于0.2MPam3)高压、中压管壳式余热锅炉中压搪玻璃压力容器使用强度级别较高(指相应标准中抗拉强度规定值下限大于或等于540MPa的材料制造的压力容器)移动式压力容器,包括:铁路罐车,介质为液化气体、低温液体;罐式汽车液化气体运输(半挂)车、低温液体运输(半挂)车、永久气体运输(半挂)车和罐式集装箱(介质为液体气体、低温液体等)球形储罐(容积大于50m3)低温液体储存容器(容积大于5m3)2) 焊接工艺和焊工(1)压力容器焊接工定的要求 压力容器产品施焊前,对受压元件之间的对接焊接接头和要求全焊透的T形焊接接头,
20、受压元件与承载的非受压元件之间全焊透的T形或角接焊接接头,以及受压元件的耐腐蚀堆焊层都应进行焊接工艺评定。 钢制压力容器的焊接工艺评定符合JB 4708钢制压力容器焊接工艺评定标准的有关规定。有色金属制压力容器的焊接工艺评定应符合有关标准的要求。 焊接工艺评定所用焊接设备、仪器以及参数调节装置,应定期检定和校验。评定试件应由压力容器制造单位技术熟练的焊接人员(不允许聘用外单位焊工)焊接。 焊接工艺评定完成后,焊接工艺评定报告和焊接工艺指导书应经制造(组焊)单位焊接责任工程师审核,总工程师批准,并存入技术档案。焊接工艺指导书或焊接工艺卡应发给有关的部门和焊工,焊接工艺评定技术档案及焊接工艺评定试
21、样应保存至该工艺评定失效为止。(2)焊接压力容器的焊工必须按照锅炉压力容器焊工考试规则进行考试,取得焊工合格证后,才能在有效期间内担任合格项目范围内的焊接工作。焊工应按焊接工艺指导书或焊接工艺卡施焊。制造单位应建立焊工技术档案,制造单位检查员应对实际的焊接工艺参数进行检查,并做好记录。(3)压力容器的组焊要求 不宜采用十字焊缝。相邻的两筒节间的纵缝和封头拼接焊缝与相邻筒节的纵缝应错开,其焊缝中心线之间的外圆弧长一般应大于筒体厚度的3倍,且不小于100mm。 在压力容器上焊接的临时吊耳和拉筋的垫板等,应采用与压力容器壳体相同或在力学性能和焊接性能方面相似的材料,并用相适应的焊材及焊接工艺进行焊接
22、。临时吊耳和拉筋的垫板割除后留下的焊疤必须打磨平滑,并应按图样规定进行渗透检测或磁粉检测,确保表面无裂纹等缺陷。打磨后的厚度不应小于该部位的设计厚度。 不允许强力组装。 受压元件之间或受压元件与非受压元件组装时的定位焊,若保留成为焊缝金属的一部分,则应按受压元件的焊缝要求施焊。(4)压力容器打焊工钢印压力容器主要受压元件焊缝附近50mm处的指定部位,应打上焊工代号钢印。对无法打钢印的,应用简图记录焊工代号,并将简图列入产品质量证明书中提供给用户。(5)焊接接头返修的要求 应分析缺陷产生的原因,提出相应的返修方案。 返修应编制详细的返修工艺,经焊接责任工程师批准后才能实施。返修工艺至少应包括:缺
23、陷产生的原因;避免再次产生缺陷的技术措施;焊接工艺参数的确定;返修焊工的指定;焊材的牌号及规格;返修工艺编制人、批准人的签字。 同一部位(指焊补的填充金属重叠的部位)的返修次数不宜超过2次。超过2次以上的返修,应经制造单位技术总负责人批准,并应将返修的次数、部位、返修后的无损检测结果和技术总负责人批准字样记入压力容器证明书的产品制造变更报告中。 返修的现场记录应详尽,其内容至少包括坡口形式、尺寸、返修长度、焊接工艺参数(焊接电流、电弧电压、焊接速度、预热温度、层间温度、后热温度和保温时间、焊材牌号及规格、焊接位置等)和施焊者及其钢印等。 要求焊后热处理的压力容器,应在热处理前焊接返修,如在热处
24、理后进行焊接返修,返修后再进行热处理。 有抗晶间腐蚀要求的奥氏体不锈钢制压力容器,返修部位仍需保证原有的抗晶间腐蚀性能。 压力试验后需返修的,返修部位必须按原要求经无损检测合格。由于焊接接头或接管泄漏而进行返修的,或返修深度大1/2壁厚的压力容器,还应重新进行压力试验。钢制压力容器及其受压元件应按GB 150的有关规定进行焊后热处理。2. 钢制压力容器(GB 1501998)本标准规定了钢制压力容器的设计、制造、检验和验收要求,适用于设计压力不大于35MPa的容器;本标准内容有:范围、引用标准、总论、材料、内压圆筒和内压球壳、外压圆筒和外压球壳、封头、开孔和开孔补强、法兰、制造、检验和验收及附
25、录(内容有材料的补充规定、指导性规定、低温压力容器、非圆形截面容器、焊接结构等)。3. 电力建设施工及验收技术规范(管道篇)(DL 50311994)本规范是中华人民共和国电力行业标准,内容有总则、术语、管子、管件和管道附件及阀门的检验,管子、管件及管道附件的配制;管道安装,管道系统的试验和清洗以及工程验收。本标准介绍弯管、卷管、支架制作及管道安装技术工艺以及管道系统的试验和清洗,同时应参阅如下标准:弯管弯曲半径应符合设计要求,设计无规定时,弯管的最弯曲半径应符合行业标准DL/T 515电站弯管;管子的切割应符合现行的DL 5007电力建设施工及验收技术规范火力发电厂焊接篇的相应规范。现将总则
26、摘录如下,供参考。 本规范适用于火力发电厂和热力网的下列管道的配制、施工及验收。a. 600MW及以下亚临界参数火力发电机组的主蒸汽管道及相应的再热蒸汽管道和主给水管道;b. 火力发电厂范围内的一般性汽水管道、热力网管道和压缩空气管道;c. 施工用临时管道。 本规范不适用于:a. 铸铁管道;b. 钢筋混凝土管道;c. 有色金属管道(钛、铜等);d. 非金属管道(塑料等);e. 非金属衬里管道;f. 复合金属管道。 下列各类管道的特殊施工及验收,除遵守本规范技术要求外,还应按照电力建设施工及验收技术规范中有关专业篇的规定执行;a. 汽轮机和发电机本体范围内的各类管道;b. 锅炉本体范围内的各类管
27、道,以及烟、风、煤、燃油、燃气和除灰系统的管道;c. 油管道及水处理的各类管道;d. 制氢、供氢系统的各类管道;e. 热工仪表管道;f. 氧气及乙炔管道。 进口火力发电机组管道的施工及验收工作,除建造合同中另有具体规定的部分外,应按本规范的规定执行。 电厂管道安装工程,应由具备必要的技术力量、检测手段和管理水平的专业队伍承担施工。 电厂管道施工应按基本建设程序进行,具备下列条件方可施工;a. 设计及其技术资料齐全,施工图纸业经会审;b. 电厂管道工程的施工组织设计和施工方案已经编制和审批;c. 技术交底和必要的技术培训与考核已经完成;d. 劳动力、材料、机具和检测手段基本齐全;e. 施工环境符
28、合要求;f. 施工用水、电气等均可满足施工需要。 管子、管件及管道附件的制造质量及选用应符合现行国家或行业(或专业)技术标准。 各类管子、管件及管道附件的保管,应按照现行的SDJ 68电力基本建设火电设备维护保管规程及相应的补充规定进行。 各类管道应按照设计图纸施工,如需修改设计或采用代用材料时,必须提请设计单位按有关制度办理。 管道施工中的切割、焊接工作,除按照本规范中有关规定外,还应符合现行的DL 5007电力建设施工及验收技术规范(火力发电厂焊接篇)的相应规定。 管道的保温与涂漆应按照SDJ 245电力建设施工及验收技术规范(锅炉机组篇)的规定执行。管道的涂色应按照DL 5011电力施工
29、及验收技术规范(汽轮机机组篇)的规定执行。 电厂管道施工的安全、环境和防火应按照现行的DL 5009.1电力建设安全工作规程(火力发电厂部分)的有关规定执行。4. 船舶压力管系的焊接(中国船级社材料与焊接规范1998)1) 适用范围 本规定适用于采用手工、自动或半自动电弧焊以及经中国船级社认可的其他方法所焊接的管子对接接头、支管和法兰连接的接头。 氧乙炔气体焊仅限用于焊接直径不超过100mm或壁厚不超过9.5mm的管子对接接头。2) 管子接头的焊接(1)一般要求 焊缝应远离管子弯曲处和膨胀补偿部分,焊缝应布置在受弯矩和交变负荷作用最小的位置。 管系的焊接应尽可能安排在车间里进行。确定在船上进行
30、的焊接,应考虑有足够的空间以进行预热、焊接、热处理和检查焊接接头。(2)焊接 装配时,焊件应保证轴向对准,尽可能减少其表面错边。通常类和类管系的对准偏差应不大于以下要求。a. 对带固定垫环的管子:0.5mm。b. 对不带固定垫环的管子(t为管壁厚度):内径小于150mm,厚度不大于6mm时,为1mm或t/4,取较小值;内径小于300mm,厚度不大于9.5mm时,为1.5mm或t/4,取较小值;内径大于或等于300mm或厚度超过9.5mm时,为2.0mm或t/4,取较小值; 施焊前应清除焊缝边缘上的氧化物、潮湿和油污等,焊缝间隙和坡口应符合焊接工艺规程的要求。 管子接头的预热温度应根据其材料的化
31、学成分和管壁厚度确定。预热温度一般应符合表10的要求。表10 管接头的预热温度钢 材 种 类较厚部分的厚度/mm最小预热温度/碳钢及碳锰钢(C+Mn/60.40)2050碳钢及碳锰钢(C+Mn/60.40)201000.3Mo131001Cr0.5Mo13100131502.25CrMo及0.5Cr0.5Mo0.251315013200 对该类材料,如中国船级社对焊接工艺认可中的硬度试验结果认为可以接受,则可免除厚度为6mm及以下的材料的预热。 对环境温度低于0,不论厚度如何,均应按最小预热温度进行预热。特别情况中国船级社将特殊考虑。 表中数值为低氢的焊接方法。如采用非低氢焊接方法,则应考虑采
32、用较高的预热温度。 对接头的焊缝与母材的过渡应平缓且均匀。3) 焊接质量检查(1)一般要求 管子焊接后应进行外观检查、无损检测和液压试验。 液压试验应按中国船级社钢质海船入级与建造规范第3篇第2章第5节的规定进行。(2)外观检查焊缝表面不应有裂纹、焊瘤、气孔、咬边以及未填满的弧坑和凹陷存在。如有上述缺陷应进行修补。(3)无损检测 类受压管系的对接焊缝应按表11的规定进行射线检测;类受压管系的对接焊缝由中国船级社验船师指定位置进行射线检测。射线检测的灵敏度应符合材料与焊接规范7.5.4.5的规定。表11 类受压管系对接焊缝的射线检测范围管子外径/mm检测范围管子外径/mm检测范围76由中国船级社
33、验船师指定位置抽查76焊缝100进行检查 如用超声波检测代替射线检测,应经中国船级社同意。 类受压管系的填角焊缝应按表12的规定进行磁粉检测;类受压管系的填角焊缝由中国船级社验船师指定位置进行磁粉检测。表12 类受压管系填角焊缝的磁粉检测范围管子外径/mm检测范围管子外径/mm检测范围76由中国船级社验船师指定位置抽查76焊缝100进行检查4) 焊后热处理 碳钢和碳锰钢钢管及组合分支管。在下列情况下,应进行焊后消除应力的热处理:a. 钢管和组合分支管的含碳量超过0.23%;b. 钢管和组合分支管的含碳量未超过0.23%,但壁厚超过20mm的类受压管或壁厚超过30mm的类受压管。 所有合金钢钢管
34、和组合分支管。在下列情况下,均应进行适当的热处理:a. 用电弧焊连接;b. 经加热成形,或弯管加工的;c. 冷弯成形而弯心半径小于3倍管子外径的(弯心半径从弯管内侧边缘测量)。 凡采用氧乙炔气体焊连接的管子,焊后均应进行正火加回火处理,对材料为碳钢或碳锰钢时,亦可采用正火处理。 碳钢、碳锰钢的消除应力热处理温度为580620;保温时间按每25mm管壁厚度1h选取。合金钢消除应力热处理的温度应根据材料成分确定,并经中国船级社验船师同意。5. 工业金属管道工程施工及验收规范(管道加工、管道焊接)(GB 50231997)1) 总则 为了提高工业金属管道工程的施工水平,保证工程质量,制定本规范。 本
35、规范适用于设计压力不大于40MPa,设计温度不超过材料允许的使用温度的工业金属管道(以下简称“管道”)工程的施工及验收。 本规范不适用于核能装置的专用管道、矿井专用管道、长输管道。 管道的施工应按设计文件进行。当修改设计时,应经原设计单位确认,并经建设单位同意。 现场组装的机器或设备所属管道,应按制造厂的技术文件施行,但质量标准不得低于本规范的规定。 管道的施工除应执行本规范的规定外,尚应执行国家现行有关标准、规范的规定。2) 管道加工(1)管子切割 管子切割前应移植原有标记。低温钢管及钛管,严禁使用钢印。 碳素钢管、合金钢管宜采用机械方法切割。当采用氧乙炔焰切割时,必须保证尺寸正确和表面平整
36、。 不锈钢管、有色金属管应采用机械或等离子方法切割。不锈钢管及钛管用砂轮切割或修磨时,应使用专用砂轮片。 镀锌钢管宜用钢锯或机械方法切割。 管子切口质量应符合下列规定。a. 切口表面应平整,无裂纹、重皮、毛剌、凸凹、缩口、熔渣、氧化物、铁屑等。b. 切口端面倾斜偏差(见图1)不应大于管子外径的1%,且不得超过3mm。(2)弯管制作 弯管宜采用壁厚为正公差的管子制作。当采用负公差的管子制作弯管时,管子弯曲半径与弯管前管子壁厚的关系宜符合表13的规定。表13 弯曲半径与管子壁厚的关系弯曲半径R弯管前管子壁厚弯曲半径R弯管前管子壁厚R6DN1.06Tm5DNR4R1.14Tm6DNR5R1.08Tm
37、4DNR3DN1.25Tm注:DN公称直径;Tm设计壁厚。 高压钢管的弯曲半径宜大于管子外径的5倍,其他管子的弯曲半径宜大于管子外径的3.5倍。 有缝管制作弯管时,焊缝应避开受拉(压)区。 钢管应在其材料特性允许范围内冷弯或热弯。 有色金属管加热制作弯管时,其温度范围应符合表14的规定。表14 有色金属管加热温度范围管 道 材 质加热温度范围/管 道 材 质加热温度范围/铜500600铝锰合金450铜合金600700钛350铝1117150260铅100130铝合金LF2、LF3200310 采用高合金钢管或有色金属管制作弯管,宜采用机械方法,当充砂制作弯管时,不得用铁锤敲击,铅管加热制作弯管
38、时,不得充砂。 钢管热弯或冷弯后的热处理,应符合下列规定。a. 除制作弯管温度自始至终保持在900以上的情况外,壁厚大于19mm的碳素钢管制作弯管后,应按表15的规定进行热处理。表15 常用管材热处理条件管材类别名义成分管材牌号热处理温度/加热速率恒温时间冷却速率碳素钢C10、15、20、25600650 当加热温度升至400时,加热速率不应大于20525/T/h 恒温时间应为每25mm壁厚1h,且不得小于15min,在恒温期间内最高与最低温差应低于65 恒温后的冷却速率不应超过26025/T/h,且不得大于260/h,400以下可自然冷却中、低合金钢C-Mn16Mn、16MnR600650C
39、-Mn-V09MnV60070015MnV600700C-Mo16Mo600650C-Cr-Mo12CrMo60065015CrMo700700C-Cr-Mo12Cr2Mo7007605Cr1Mo7007609Cr1Mo700760C-Cr-Mo-V12Cr1MoV700760C-Ni2.25Ni6006503.5Ni600630b. 当表15所列的中、低合金钢管进行热弯时,对公称直径大于或等于100mm,或壁厚大于或等于13mm的,应按设计文件的要求进行完全退火、正火加回火或回火处理。c. 当表15所列的中、低合金钢进行冷弯时,对公称直径大于或等于100mm,或壁厚大于或等于13mm的,应按
40、表15的要求热处理。d. 奥氏体不锈钢制作的弯管,可不进行热处理;当设计文件要求热处理时,应按设计文件规定进行。 弯管质量应符合下列规定。a. 不得有裂纹(目测或依据设计文件规定)。b. 不得存在过烧、分层等缺陷。c. 不宜有皱纹。d. 测量弯管任一截面上的最大外径与最小外径差,当承受内压时其值不得超过表16的规定。表16 弯管最大外径与最小外径之差管 子 类 别最大外径与最小外径之差管 子 类 别最大外径与最小外径之差 输送剧毒流体的钢管或设计压力P大于或等于10MPa的钢管为制作弯管前管子外径的5% 钛管为制作弯管前管子外径的5% 铜/铝管为制作弯管前管子外径的5% 输送剧毒流体以外或设计
41、压力P小于10MPa的钢管为制作弯管前管子外径的8% 铜合金/铝合金管为制作弯管前管子外径的5% 铅管为制作弯管前管子外径的5% e. 输送剧毒流体或设计压力P大于或等于10MPa的弯管,制作弯管前、后的壁厚之差,不得超过制作弯管前管子壁厚的10%;其他弯管,制作弯管前、后的管子壁厚之差,不得超过制作弯管前管子壁厚的15%,且均不得小于管子的设计壁厚。f. 输送剧毒流体或设计压力P大于或等于10MPa的弯管,管端中心偏差值不得超过1.5mm/m,当直管长度L大于3m时,其偏差不得超过5mm。其他类别的弯管,管端中心偏差值(见图2)不得超过3mm/m,当直管长度L大于3m时,其偏差不得超过10m
42、m。 形弯管的平面度允许偏差(见图3)应符合表17的规定。表17 形弯管的平面度允许偏差长度L/mm5005001000100015001500平面度/mm34610 高压钢管制作弯管后,应进行表面无损探伤,需要热处理的应在热处理后进行;当有缺陷时,可进行修磨。修磨后的弯管壁厚不得小于管子公称壁厚的90%,且不得小于设计壁厚。高压钢管弯管加工合格后,应按规定的格式填写“高压管件加工记录”。(3)管道焊接 管道焊接应按5和现行国家标准现场设备、工业管道焊接工程施工及验收规范的有关规定进行。 管道焊缝位置应符合下列规定。a. 直管段上两对接焊口中心面间的距离,当公称直径大于或等于150mm时不应小
43、于150mm;当公称直径小于150mm时,不应小于管子外径。b. 焊缝距离弯管(不包括压制、热推或中频弯管)起弯点不得小于100mm,且不得小于管子外径。c. 卷管的纵向焊缝应置于易检修的位置,且不宜在底部。d. 环焊缝距支、吊架净距不应小于50mm;需热处理的焊缝距支、吊架不得小于焊缝宽度的5倍,且不得小于100mm。e. 不宜在管道焊缝及其边缘上开孔。f. 有加固环的卷管,加固环的对接焊缝应与管子纵向焊缝错开,其间距不小于100mm。加大环距管子的环焊缝不应小于50mm。 管子、管件的坡口形式和尺寸应符合设计文件规定,当设计文件无规定时,可参照表20的规定确定。 管道坡口加工宜采用机械方法
44、,也可采用等离子弧、氧乙炔焰等热加工方法。采用热加工方法加工坡口后,应除去坡口表面的氧化皮、熔渣及影响接头质量的表面层,并应将凹凸不平外打磨平整。 管道组成件组对时,对坡口及其内外表面进行的清理应符合表18的规定;清理合格后应及时焊接。表18 坡口及其内外表面的清理管道材质清理范围/mm清 理 物清 理 方 法碳素钢不锈钢合金钢10油、漆、锈、毛剌等污物手工或机械等铝及铝合金50油污、氧化膜等 有机溶剂除净油污,倾泻或机械法除净氧化膜铜及铜合金20钛50 除设计文件规定的管道冷拉伸或冷压缩焊口外,不得强行组对。 管道对接焊口的组对应做到内壁齐平,内壁错边量应符合表19的规定。表19 管道组对内
45、壁错边量管 道 材 质内 壁 错 边 量钢不宜超过壁厚的10,且不大于2mm铝及铝合金壁厚5mm不大于0.5mm壁厚5mm不宜超过壁厚的10%,且不大于2mm铜及铜合金、钛不宜超过壁厚的10%,且不大于1mm 不等厚管道组成件组对时,当内壁错边量超过表19的规定或外壁错边量大于3mm时,应进行修整(见图4)。 在焊接和热处理过程中,应将焊件垫置牢固。 当对螺纹接头采用密封焊时,外露螺纹应全部密封。 对管内清洁要求较高且焊接后不易清理的管道,其焊缝底层应采用氩弧焊施。机组的循环油、控制油、密封油管道,当采用承插焊时,承口与插口的轴不宜留间隙。6. 现场设备、工业管道焊接工程施工及验收规范(管道焊
46、接)(GB 50236)1) 一般规定 本章适用于含碳量小于或等于0.30%的碳素钢、低合金结构、低温钢、耐热钢、不锈钢、耐热耐蚀高合金钢现场焊接设备和管道的手工电弧焊、氩弧焊、二氧化碳气体保护焊、埋弧焊及氧乙炔焊。 焊缝的设置应避开应力集中区,便于焊接和热处理,并应符合下列规定。a. 钢板卷管或设备、容器的筒节与筒节、筒节与封头组对时,相邻两纵向焊缝间的距离应大于壁厚的3倍,且不应小于100mm;同一筒节上两相邻纵缝间的距离不应小于200mm。b. 加热炉受热面管子的焊缝中心与管子弯曲起点、联箱外壁及支、吊架边缘的距离不应小于70mm;同一直管段上两个对接焊缝间的距离不应小于150mm。c.
47、 除焊接及成形管件外的其他管子对接焊缝的中心到管子弯曲起点的距离不应小于管子外径,且不应小于100mm;管子对接焊缝与支、吊架边缘之间的距离不应小于50mm。同一直管两对接焊缝中心面间的距离:当公称直径大于或等于150mm时不应小于150mm;公称直径小于150mm时不应小于管子外径。d. 不宜在焊缝及其边缘上开孔。 焊缝的坡口形式和尺寸应符合设计文件和焊接作业指导书的规定。当无规定时,埋弧焊焊缝坡口形式及尺寸应符合现行国家标准埋弧焊焊缝坡口的基本形式与尺寸GB 986的规定,其他焊缝坡口形式和尺寸应符合表20的规定。2) 焊前准备 焊件的切割和坡口加工宜采用机械方法,也可采用等离子弧、氧乙炔
48、焰等热加工方法,在采用热加工方法加工坡口后,必须除去坡口表面的氧化皮、熔渣及影响接头质量的表面层,并应将凹凸不平处打磨平整。 焊件组对前应将坡口及其内外侧表面不小于10mm范围内的油、漆、垢、锈、毛剌及镀锌层等清除干净,且不得有裂纹、夹层等缺陷。 除设计规定需进行冷拉伸或冷压缩的管道外,焊件不得进行强行组对。 管子或管件对接焊缝组对时,内壁应齐平,内壁错边量不宜超过管壁厚度的10,且不应大于2mm。 设备、容器对接焊缝组对的错边量应符合表21及下列规定:表21 设备、容器对接焊缝组对时的错边量母材厚度/mm错边量/mm纵向焊缝环向焊缝12/4/412203/420403540503/850不小
49、于/16,且不大于10不小于/8,且不大于20 a. 只能从单面焊接的纵向和环向焊缝,其内壁最大错边量不应超过2mm;b. 复合钢板组对时,应以复层表面为基准,错边量不应超过钢板复层厚度的50%,且不应大于1mm。 不等厚对接焊件组对时,薄件端面应位于厚件端面之内。当内壁错边量超过本规范焊前准备、条规定或外壁错边量大于3mm时,应对焊件进行加工。 焊件组对时应垫置牢固,并应采取措施防止焊接和热处理过程中产生附加应力和变形。 当焊件采用半自动或自动焊接时,纵焊缝两端宜装上与母材相同材质的引弧板和熄弧板。 不锈钢焊件坡口两侧各100mm范围内,在施焊前应采取防止飞溅物沾污焊件表面的措施。 焊条、焊
50、剂在使用前应按规定进行烘干,并应在使用过程中保持干燥。焊丝使用前应清除其表面的油污、锈蚀等。3) 焊接工艺要求 焊条、焊丝的选用,应按照母材的化学成分、力学性能、焊接接头的抗裂性、焊前预热、焊后热处理、使用条件及施工条件等因素综合确定,且应符合下列规定。a. 焊接工艺性能应良好。b. 同种钢材焊接时,焊缝金属的性能和化学成分应与母材相当。低温钢应选用与母材的使用温度相适应的焊材;耐热耐蚀高合金钢,可选用镍基焊材。c. 异种钢材焊接时的焊条选用。当两侧母材均为非奥氏体钢或均为奥氏体钢时,可根据合金含量较低一侧母材或介于两者之间的选用焊材;当两侧母材之一为奥氏体钢时,应选用25Cr-13Ni型或含
51、镍量更高的焊材。d. 复合钢板焊接时,基层和复层应分别选用相应焊材,基层与复层过渡处的焊接,应选用过渡层焊材。e. 碳素钢及合金钢焊接材料的选用,宜符合设计技术文件、焊件作业指导书及工艺文件的规定。 埋弧自动焊时,选用的焊剂应与母材和焊丝相互匹配。 定位焊缝应符合下列规定。a. 焊接定位焊缝时,应采用与根部焊道相同的焊接材料和焊接工艺,并应由合格焊工施焊。b. 定位焊缝的长度、厚度和间距,应能保证焊缝在正式焊接过程中不致开裂。c. 在焊接根部焊道前,应对定位焊缝进行检查,当发现缺陷时,应处理后方可施焊。d. 与母材焊接的工、卡具其材质宜与母材相同或同一类别号。拆除工、卡具时不应损伤母材,拆除后
52、应将残留焊疤打磨修整至与母材表面齐平。 严禁在坡口之外的母材表面引弧和试验电流,并应防止电弧擦伤母材。 对含铬量大于或等于3%或合金元素总含量大于5%的焊件,氩弧焊打底焊接时,焊缝内侧应充氩气或其他保护气体,或采取其防止内侧焊缝金属被氧化的措施。 焊接时应采取合理的施焊方法和施焊顺序。 施焊过程中应保证起弧和收弧处的质量,收弧时应将弧坑填满。多层焊的层间接头错开。 管子焊接时,管内应防止穿堂风。 除工艺或检验要求需分次焊接外,每条焊缝宜一次连续焊完,当因故中断焊接时,应根据工艺要求采取保温缓冷或后热等防止产生裂纹的措施,再次焊接前应检查焊层表面,确认无裂纹后,方可按原工艺要求继续施焊。 需预拉
53、伸或预压缩的管道焊缝,组对时所使用的工、卡具应在整个焊缝焊接及热处理完毕并经检验合格后方可拆除。 低温钢、奥氏体不锈钢、耐热耐蚀高合金钢以及奥氏体与非奥氏体异种钢接头焊接时应符合下列规定:a. 应在焊接作业指导书规定的范围内,在保证焊透和熔合良好的条件下,采用小电流、短电弧、快焊速和多层多道焊工艺,并应控制层间温度;b. 对抗腐蚀性能要求高的双面焊缝与腐蚀介质接触的焊层应最后施焊,宜对低温钢焊缝表面焊道进行退火处理。 复合钢焊接应符合下列规定:a. 严禁使用基层和过渡层焊条焊接复层;b. 焊接过渡层时,宜选用小的焊接线能量。 应根据设计规定对奥氏体不锈钢焊缝及其附近表面进行酸洗、钝化处理。4)
54、 焊前预热及焊后热处理 进行焊前预热及焊后热处理应根据钢材的淬硬性、焊件厚度、结构刚性、焊接方法及使用条件等因素综合确定。 要求焊前预热的焊件,其层间温度应在规定的预热温度范围内。 当焊件温度低于0时,所有钢材的焊缝应在始焊处100mm范围内预热到15以上。 对有应力腐蚀的焊缝,应进行焊后热处理。 非奥氏体异种钢焊接时按焊接性较差的一侧钢材选定焊前预热和焊后热处理温度,但焊后热处理温度不应超过另一侧钢材的临界点Ac1。 调质钢焊缝的焊后热处理温度,应低于其回火温度。 焊前预热的加热范围,应以焊缝中心为基准,每侧不应小于焊件厚度的3倍;焊后热处理的加热范围,每侧不应小于焊缝宽度的3倍,加热带以外
55、部分应进行保温。 焊前预热及焊后热处理过程中,焊件内外壁温度应均匀。 焊前预热及焊后热处理时,应测量和记录其温度,测温点的部位和数量应合理,测温仪表应经计量检定合格。 对容易产生焊接延迟裂纹的钢材,焊后应及时进行焊后热处理,当不能及时进行焊后热处理时,应在焊后立即均匀加热至200300,并进行保温缓冷,其加热范围应与焊后热处理要求相同。 焊前预热及焊后热处理温度应符合设计或焊接作业指导书的规定,当无规定时,常用管材焊接的焊前预热及焊后热处理温度宜符合表22的规定;设备、容器焊接的焊前预热及焊后热处理温度应符合现行国家标准钢制压力容器GB150的有关规定。 当采用钨极氩弧焊打底时,焊前预热温度可
56、按表22规定的下限 温度降低50。表22 常用管材焊前预热及焊后热处理工艺条件钢 种焊前预热焊后热处理壁厚/mm温度/壁厚/mm温度/ C2610020030600650 C-Mn1515020020 Mn-V560590 C-0.5Mo600650 0.5Cr-0.5Mo650700 1Cr-0.5Mo1015025010 1Cr-0.5Mo-V62003006700750 1.5Cr-1Mo-V2.25Cr-1Mo 5Cr-1Mo250350任意壁厚 9Cr-1Mo750780 2Cr-0.5Mo-WV 3Cr-1Mo-VTi 12Cr-1Mo-V 焊后处理的加热速率、热处理温度下的恒温时
57、间及冷却速率应符合下列规定。a. 当温度升至400以上时,加热速率不应大于(20525/)/h,且不得大于330/h。b. 焊后热处理的恒温时间应为每25mm壁厚恒温1h,且不得小于15min,在恒温期间内最高与最低温差应低于65。c. 恒温后的冷却速率不应大于(6025/)/h,且不得大于260/h,400以下可自然冷却。 热处理后进行返修或硬度检查超过规定要求的焊缝应重新进行热处理。5) 焊件的坡口形式和尺寸钢焊件坡口形式和尺寸应符合表20的规定。7. 输油输气管道线路工程施工及验收规范(SY04011998)1) 总则 为提高输油、输气管道线路工程施工水平,确保管道工程质量,降低工程成本
58、,制定本规范。 本规范适用于新建或改、扩建的陆地输送原油、天然气的管道线路工程的施工及验收。本规范不适用于输油、输气场站内部的工艺管道,油气田集输管道,城市燃气输配管网及工业企业内部的油、气管道,以及投入运行的油、气管道改造、大修工程。 管道线路工程施工主要分为:测量放线,施工作业带清理和修筑施工便道,管沟开挖材料、设备检验、材料存放和钢管运输,管道防腐绝缘,组装焊接,管道下沟、回填、试压、清管及输气管道干燥,线路截断阀安装,管道穿跨越工程线路以及附属工程。 施工前,应进行施工图会审、设计交底和现场交底,并做好记录。应编写施工组织设计,根据工程量、工期、沿线自然条件等情况合理地安排施工。 施工单位应建立质量保证体系,编制合理的质量计划和检验计划,确保工程质量。 承担输油、输气管道线路工程施工的企业,必须取得国家或行业主管部门颁发的石油施工企业资质证,并在资质证规定的施工范围内承担工程。
- 温馨提示:
1: 本站所有资源如无特殊说明,都需要本地电脑安装OFFICE2007和PDF阅读器。图纸软件为CAD,CAXA,PROE,UG,SolidWorks等.压缩文件请下载最新的WinRAR软件解压。
2: 本站的文档不包含任何第三方提供的附件图纸等,如果需要附件,请联系上传者。文件的所有权益归上传用户所有。
3.本站RAR压缩包中若带图纸,网页内容里面会有图纸预览,若没有图纸预览就没有图纸。
4. 未经权益所有人同意不得将文件中的内容挪作商业或盈利用途。
5. 装配图网仅提供信息存储空间,仅对用户上传内容的表现方式做保护处理,对用户上传分享的文档内容本身不做任何修改或编辑,并不能对任何下载内容负责。
6. 下载文件中如有侵权或不适当内容,请与我们联系,我们立即纠正。
7. 本站不保证下载资源的准确性、安全性和完整性, 同时也不承担用户因使用这些下载资源对自己和他人造成任何形式的伤害或损失。