生产现场管理与改善
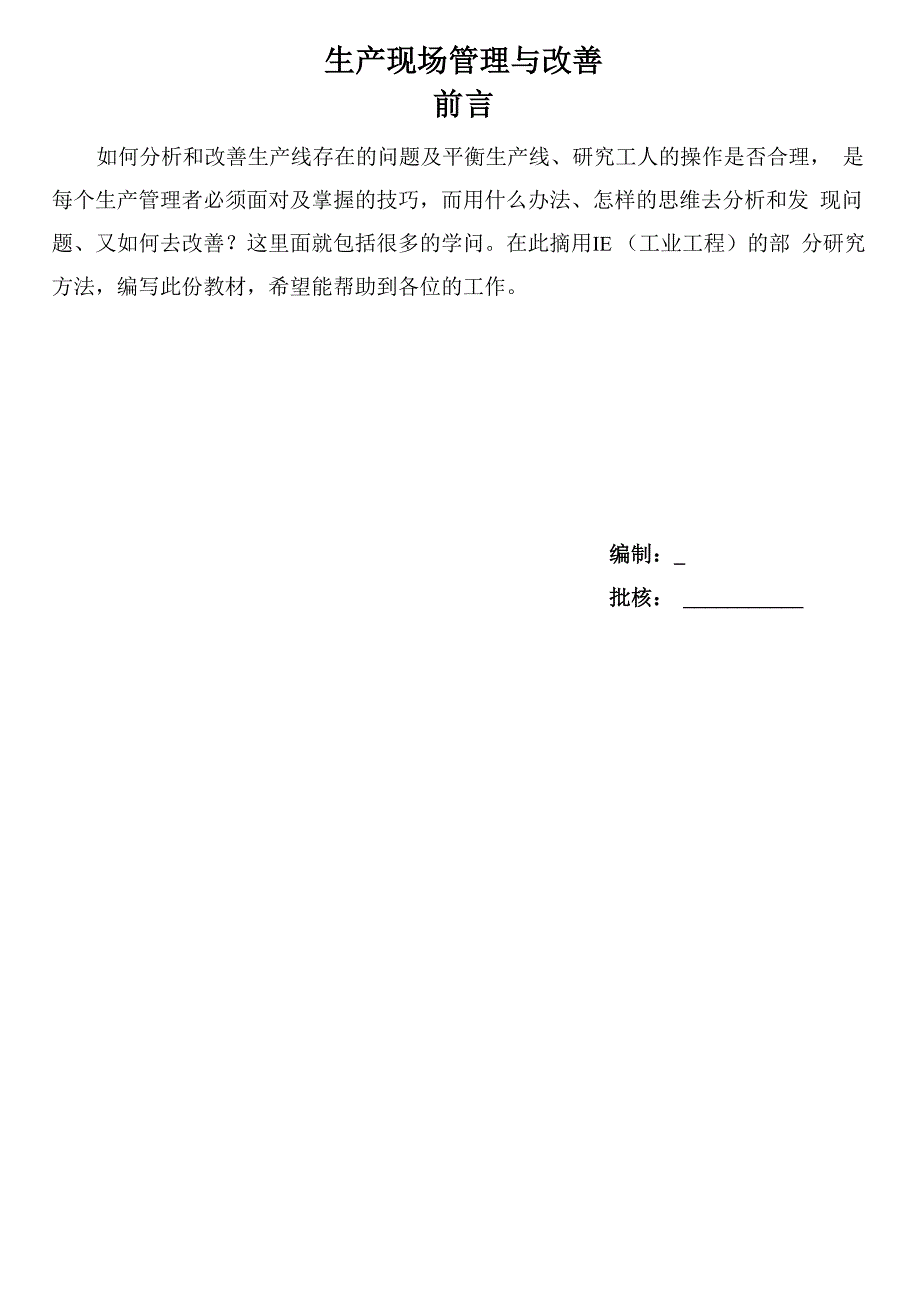


《生产现场管理与改善》由会员分享,可在线阅读,更多相关《生产现场管理与改善(8页珍藏版)》请在装配图网上搜索。
1、生产现场管理与改善前言如何分析和改善生产线存在的问题及平衡生产线、研究工人的操作是否合理, 是每个生产管理者必须面对及掌握的技巧,而用什么办法、怎样的思维去分析和发 现问题、又如何去改善?这里面就包括很多的学问。在此摘用IE (工业工程)的部 分研究方法,编写此份教材,希望能帮助到各位的工作。编制:_批核:一、如何排拉1. 流水线的作用就让互不关联工序形成一个流的生产,从而减少搬运及等待的时间,而 提高生产效率,所以合理排拉就是如何实现高效的一个流生产.2. 要排出一条顺畅的生产线,首先必须了解所生产产品的每道工序及其操作法和技巧, 然后编制出工序流程即排拉表.3. 在编制流程表时,必须遵循以
2、下原则:流程原贝说明产 品 工 艺 线 路般1. 路线最短原则2. 禁止孤岛加工3. 禁止局域路线分离4. 减少停滞的原则5. 禁止重复的停滞6. 禁止交叉7. 禁止逆行路线长度,范围越小越好减少工序的分离减少(去除)很难流水线化的大型设备 减少中间停滞禁止重复的停滞禁止交叉流动禁止逆行流动生产线8. 减少物流前后摇摆9. 减少无谓移动10. 去除工序间隔11.I/O 致原则12.物料上下移动减少减少物料流动的左右摇摆 减少无实际作业内容的移动 去除加工设备间的间隔 投入(IN)与取出(OUT) 致 减少去除生产过程中物料的上下移动作 业 流 程般 生 产 线1. 线路最短原则2. 去除间隔的
3、原则3. 与产品工艺致原则4.I/O 致的原则5. 禁止逆行的原则6. 零等待的原则路线长度、范围越小越好去除加工设备的间隔作业内容全部集中产品流程内完成 投入(IN)与取出(OUT) 致禁止逆行流动消除机械自动状态下的等待二、如何分析生产线存在的问题1流程分析法:1.1 流程分析法的主要目的是希望在制造过程中 ,利用人/机/物/法/环分析原则来发现下列问题,并将其剔除后设法改善的一种方法,利用人/机/物/法/环具体问题及项目 见下表:项次目的调查或计测项目1发觉工程或作业的配置、顺序、分割、合并是否适当工作能力,作业站工时单位产量2发觉是否有不必要的迟延迟延工时3发现搬运的路线、方法或次数、
4、负荷是否适当路径、长度、次数、负荷、恬性系数4发现搬运的距离是否可缩短距离、时间5发现是否有等待时间,可否缩短等待时间、次数6发现是否可同时加工或检验加工数、工序、检验次数、效率7发现品质变异及品质状况品质统计数据8发现报废或返工品质不良数据9发现变动品质成本品质成本分析10发现工作现场之抱怨工作难易度、满意度、安全性1.2 流程分析法的一般分析步骤1.2.1 分析前之准备1.2.1.1 先确定分析的目的.1.2.1.2 先了解现有的资料,如(产品图、材料表、作业标准书、检验标准书).1.2.1.3 将产品所需的配件,找齐从头到尾自己组装一次.1.2.1.4 依据自己组装的顺序编制流程表.1.
5、2.2 做调查及分析1.2.2.1 针对各工程详细加以调查,发现及分析存在的不良.1.2.2.2 分析作业顺序及作业方法是否合理正确,(如工序的前后顺序、工作时间、工人 的动作、作业距离、瓶颈工序、出现的问题).1.2.3 抓出不合理项目将不合理的不妥当的项目抓出来,并加以整理成表.1.2.4 进行改善对改善的方法应先做评估,是否有价值.1.2.5 制作新的流程图将改善获得实效的新流程绘制成流程图,并付于实施.1.2.6 流程分析法在实施过程中,还应用的手法有:工作简化法、动作研究法、时间研究、 动作分析、动作经济等方法的配合.三、如何判断工人的动作是否合理及布置生产线1.动作经济原则:1.1
6、 所谓的动作经济原则,即人在操作时,能以最少的劳力达到最大的工作效果的经济 原则,动作经济原则的基本原则如下:1.1.1 动作能量活动原则在人的身体各部位,凡是能具有进行动作能力的部份 ,都希望全部活用,具体总结 如下:1.1.1.1 脚部或左手能操作的事,不使用右手.1.1.1.2 尽量使两手同时作业,也同时结束动作.1.1.1.3 双手不要使其同时静止,手空闲时,可用脑想另一个动作.1.1.2 动作量节约原则 多余的运动量,不但浪费时间及空间,更会消耗体力,所以应采用以下原则节约动作量.1.1.2.1 尽量使用小运动来操作工作,小单元的动作次数,应尽量减少.1.1.2.2 材料及器具应放置
7、于伸手能及的范围内,并使用易拿取的容器,工作物长、重或 体积大时应利用保持的工具,且工具应简单,易用.1.1.3 动作法改善原则1.1.3.1 动作应该规律化,不可随意更改.1.1.3.2 利用惯性、重力、自然力或动力装置来节约人体能量。1.1.3.3 作业椅及作业台的高度应适当,以减少工人疲劳度.1.1.4 人体动作方面,人体动作方面含以下原则:1.1.4.1 双手并用原则:即双手最好同时开始,同时完成工作,除了规定的休息时间外,双 手不应同时空闲.1.1.4.2 对称反向原则:即双臂或双手之动作,应反向对称为之.1.1.4.3 排除合并原则:除去不必要的动作.1.1.4.4 节奏轻松原则:
8、动作安排尽量轻松,并有自然节奏,避免使用限住性动作.1.1.4.5 手脚并用及姿势原则:减少手的工作负荷,或用脚代替控制性的工作 ,适当的坐 姿可避免疲劳.1.1.5 工具设备方面,工具设备方面含以下原则:1.1.5.1 利用工具原则:就是能够利用工具的,应尽量利用工具.1.1.5.2 万能工具原则:就是用一次可完成两个动作或功能的工具.1.1.5.3 易于操作原则:就是工具的把手或按键易操作和控制 ,工具摆放位置适当,不改 变姿势即可操作.1.1.6 场所布置方面,含以下原则:1.1.6.1 定点放置原则:就是任何物品、工具、设备应定点放置,易寻找或拿用,且依工作 顺序做最佳摆放.1.1.6
9、.2 使用原则:就是物品,零件应尽量使用容器或装具,并尽量关到使用点.1.1.6.3 避免担心原则:就是场所布置、设施、环境、作业方法应尽量减少使人担心会 有伤害.1.1.6.4 照明通风原则:就是工场工作场所之光线应适度,通风应良好,温度应适度.四、如何平衡生产线及合理安排人员:1.工序平衡法1.1 工序平衡法主要研究的是工序间流动的差距 ,减少因工序的不平衡所造成之等待 或滞留,从而确保生产顺畅.1.2 工序平衡的目的:1.2.1 物流快速合理,减少生产周期.1.2.2 减少或消除物料或半成品周转场所.1.2.3 消除工程瓶颈,提高作业效率.1.2.4 稳定品质.1.2.5 提升工作士气,
10、改善作业秩序.1.3工序平衡表示法:1.3.1 生产线的平衡:一般采用坐标的技术来表示,纵轴表示时间,横向则依工程顺序表 示并画出其标准时间,画法可使用曲线图或直条图.例:生产流动平衡表(直条图)40DM | 35| 30 标25 准20 间15105不平衡损失时间TC流 毛动/ 、速度-工程名0尔合计工程序号123456789101112配置人员11231221131119标准 时间1518172014132116171516171991人1518346014264216174516173201.3.2 对生产线进行分析时,依下列步骤进行:1.3.2.1.对生产线的各工程顺序予订定,测各工序
11、的实质时间单位(秒),并填入生产流动 平衡表内.1.322清点各工序作业人数,1人实质作业时间三人数二分配时间,记入时间栏.1.3.2.3 按时间分配画出柱状图或曲线图, 在分配的实际时间的最高这一工序顶点横向 画一条线.1.3.2.4 计算不平衡损失:即为不平衡部份损失的总合 ,其计算方法为:不平衡损失=(最 高的DMX合计人数)-(各工序时间的合计)如上图=(21X 19)-320=791.3.2.5 生产线平衡计算公式:生产线平稳率=各工序实质量时间(人)合计=320= 80.2%最高的DMX合计人数21X19生产线不平衡损失率=1-生产线平稳率=1-80.2%-19.8%.1.3.2.
12、6如使用输送带之动力传送,应计算输送带的流动速度(M/时间单位)称为节损时 间,符号TC通常:TC-实际工作时间三生产量,在TC计算出来后,再横向画线,比较 生产线是否平衡.1.4不平衡的检讨与改善:1.4.1 将生产线流动平衡图画出,计算好平衡损失率及节拍时间后,一条生产线的面貌 基本就出来了,根据这个情况再作进一步的实际改善,改善一般依以下几种方向来 进行.1.4.1.1 减少耗时最长工序(第一瓶颈)的作业时间,改善办法常为:将此工序分割给其它 工序,改良工夹具,提高作业技能,调换或增加作业者.1.4.1.2 用(工作简化法)进行作业方法改善,即(剔除)不必要的动作,(合并)微小动作,(重
13、 排)作业工序或动作,(简化)复杂动作.1.4.2 除上述的改善办法外,也可以对材料、零件包括设计方法来检讨,对新手在配置上 尤其注意,如生产不平衡时,只习惯加人来弥补,是一个不动脑筋的做法,不足为取.1.5工序平衡与人力配置的技巧:1.5.1 工序的平衡主要取决于人力的配置技巧.因为人力配置不当,将增加平均损失率, 即降低效率,现用一实例来论证说明它们的关系 :某一生产线,依工程分析设计 10 个作业工序每人工序时间为下表:工序12345678910合计备注标准时间DM18121514251241202812197DM1DM=0.01 分=0.6 秒人数111111111110人从上表可看到
14、,如果上述工序均配置 1 人,那么会导致严重不平衡,工序 2,3,4,6,10 则接近可配1人,工序5,9大约为tact(基准时间)时间2倍,则需配2人,第“7工序为 tact(基准时间)3倍可配3人,工序“8”接近tact时间1.5倍,如改善的时间没那么大, 则还是配置2 人,剩下的工序“1”配2 人可看出浪费太大,只有配1 人的状态下想法 来分割或缩短时间到15DM以下,则可使产能达到最高,平衡损失率可降至最低,现用 公式计算如下:a每个工序配1人时:平衡损失率=1-(197三41 X 10) X 100%=52%,即损失52%,如 产能以480分计,即8小时每人只产=(480X 10人)
15、三(0.41 X 10人)=1170PCSF 10 人=117PCS.b如工序依人力平衡技巧配置则将工序“5, 8, 9”各加1人,工序“7”加2人,总 人数至15人时,计算如下:平衡损失率=1-(197三225) X100%=12.4%,即从原来 的52%降低到12.4%,如产能仍以480分计即8小时每人可产=(480X15人)三 (0.15X15 人)=3200PCSF15 人=213PCS.1.5.1.3 现将人力配置 1 和 2 的方法做比较得出下表结果:项目配置序号人数平均损失率产量(480分计)人均产量(480分计)方法110人52%1170pcs117pcs方法215人12.4%3200pcs213pcs比较差值+5人-39.6%+2030pcs+82%从上表可以看出,通过人力的有效配置,可将平衡损失率大大降低,从而有效的提 升产能,得出的结果是工序的平衡主要取于人力的均衡配置 ,他们的相互关系也是如 此.
- 温馨提示:
1: 本站所有资源如无特殊说明,都需要本地电脑安装OFFICE2007和PDF阅读器。图纸软件为CAD,CAXA,PROE,UG,SolidWorks等.压缩文件请下载最新的WinRAR软件解压。
2: 本站的文档不包含任何第三方提供的附件图纸等,如果需要附件,请联系上传者。文件的所有权益归上传用户所有。
3.本站RAR压缩包中若带图纸,网页内容里面会有图纸预览,若没有图纸预览就没有图纸。
4. 未经权益所有人同意不得将文件中的内容挪作商业或盈利用途。
5. 装配图网仅提供信息存储空间,仅对用户上传内容的表现方式做保护处理,对用户上传分享的文档内容本身不做任何修改或编辑,并不能对任何下载内容负责。
6. 下载文件中如有侵权或不适当内容,请与我们联系,我们立即纠正。
7. 本站不保证下载资源的准确性、安全性和完整性, 同时也不承担用户因使用这些下载资源对自己和他人造成任何形式的伤害或损失。