顺序阀单阀控制原理区别操作注意事项
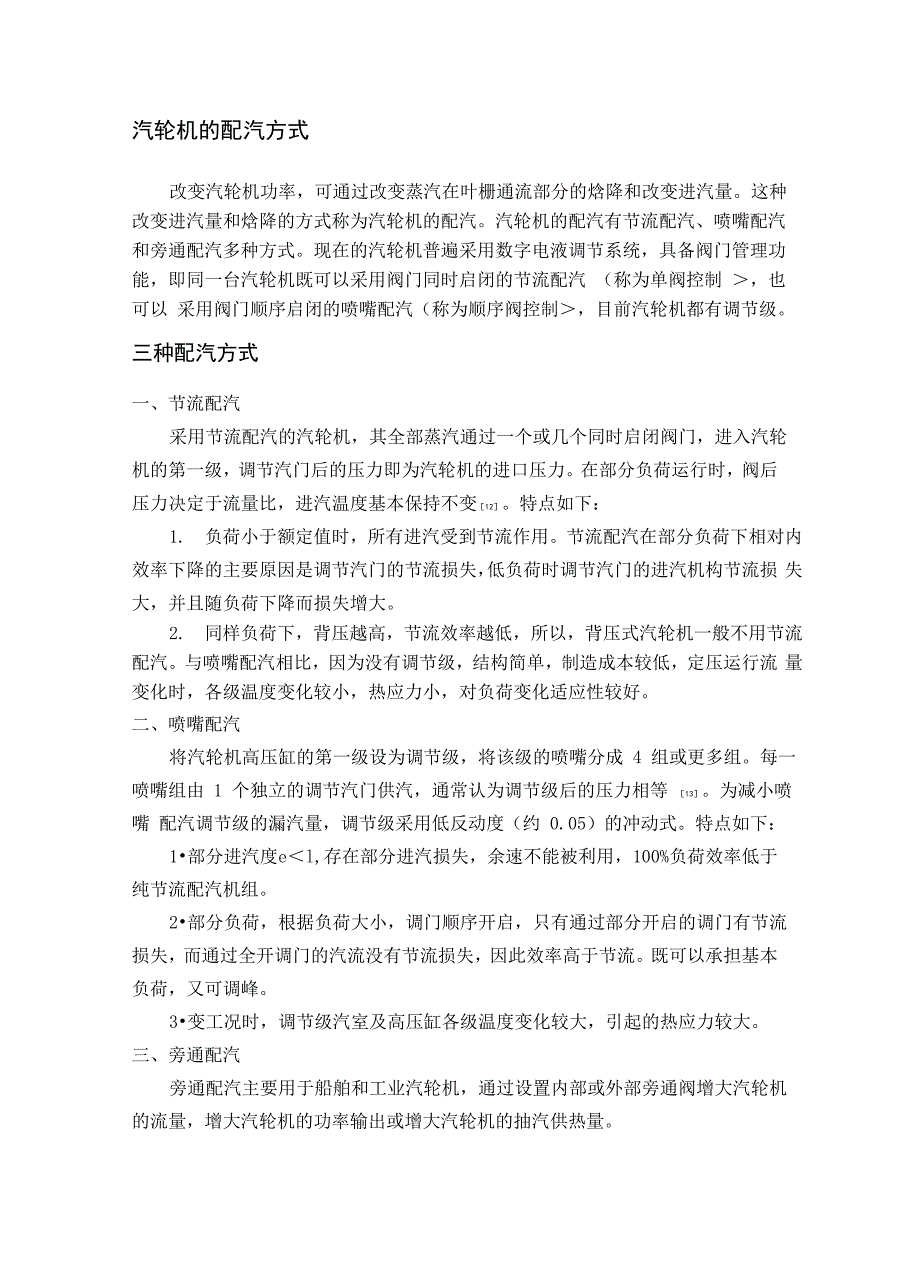


《顺序阀单阀控制原理区别操作注意事项》由会员分享,可在线阅读,更多相关《顺序阀单阀控制原理区别操作注意事项(16页珍藏版)》请在装配图网上搜索。
1、汽轮机的配汽方式改变汽轮机功率,可通过改变蒸汽在叶栅通流部分的焓降和改变进汽量。这种 改变进汽量和焓降的方式称为汽轮机的配汽。汽轮机的配汽有节流配汽、喷嘴配汽 和旁通配汽多种方式。现在的汽轮机普遍采用数字电液调节系统,具备阀门管理功 能,即同一台汽轮机既可以采用阀门同时启闭的节流配汽 (称为单阀控制 ,也可以 采用阀门顺序启闭的喷嘴配汽(称为顺序阀控制,目前汽轮机都有调节级。三种配汽方式一、节流配汽采用节流配汽的汽轮机,其全部蒸汽通过一个或几个同时启闭阀门,进入汽轮 机的第一级,调节汽门后的压力即为汽轮机的进口压力。在部分负荷运行时,阀后 压力决定于流量比,进汽温度基本保持不变12。特点如下:
2、1. 负荷小于额定值时,所有进汽受到节流作用。节流配汽在部分负荷下相对内 效率下降的主要原因是调节汽门的节流损失,低负荷时调节汽门的进汽机构节流损 失大,并且随负荷下降而损失增大。2. 同样负荷下,背压越高,节流效率越低,所以,背压式汽轮机一般不用节流 配汽。与喷嘴配汽相比,因为没有调节级,结构简单,制造成本较低,定压运行流 量变化时,各级温度变化较小,热应力小,对负荷变化适应性较好。二、喷嘴配汽将汽轮机高压缸的第一级设为调节级,将该级的喷嘴分成 4 组或更多组。每一 喷嘴组由 1 个独立的调节汽门供汽,通常认为调节级后的压力相等 13。为减小喷嘴 配汽调节级的漏汽量,调节级采用低反动度(约
3、0.05)的冲动式。特点如下:1部分进汽度el,存在部分进汽损失,余速不能被利用,100%负荷效率低于 纯节流配汽机组。2部分负荷,根据负荷大小,调门顺序开启,只有通过部分开启的调门有节流 损失,而通过全开调门的汽流没有节流损失,因此效率高于节流。既可以承担基本 负荷,又可调峰。3变工况时,调节级汽室及高压缸各级温度变化较大,引起的热应力较大。三、旁通配汽旁通配汽主要用于船舶和工业汽轮机,通过设置内部或外部旁通阀增大汽轮机 的流量,增大汽轮机的功率输出或增大汽轮机的抽汽供热量。喷嘴调节与节流调节的比较一、调节级压力与流量的关系调节级的最危险工况是当第一调节汽门全开而其他调节汽门都关闭时,调节级
4、 动叶受力最大,为最危险工况14。1. 当只有第一调节汽门全开而其他调节汽门关闭时,第一级理想比焓降最大;2. 此时流过第一喷嘴组的流量是第一喷嘴组的最大流量;3. 这股流量集中在第一喷嘴组后少数动叶上,每片动叶分摊的蒸汽流量最大;4. 动叶的蒸汽作用力正比于流量和比焓降之积。二、喷嘴调节与节流调节的比较1.汽缸沿圆周上温度的均匀性节流调节原多应用于小型机组,目的是使调节系统及汽缸的结构简单,但是, 现在大型机组亦有采用节流调节,其理由是:节流调节可以做到全周进汽,使汽缸 在进汽段高温段)温度均匀,汽缸结构简单,减小汽缸体内的热应力和因温度不匀 引起的翘曲。对于大型机组采用节流调节时,为着避免
5、节流调节阀尺寸过大,开启 阀门所需要的提升力过大,将节流调节阀设计成为相同的若干个,外观上与喷嘴调 节相同,但各阀同步开启和关闭。当用数个调节阀时,可以在机内内部联通成为全 周进汽,亦可以分为几个弧段进汽降低汽缸承受的最大压差),这时进汽度稍小于 1。喷嘴调节是几个调节阀分别向几个对应的喷嘴弧段供汽,随着负荷的增加,各 阀依次开启15。为使汽缸结构简化,调节阀可设计安置在机旁,用导汽管与汽缸内 喷嘴弧段蒸汽室)相联。因考虑热膨胀,导汽管甚长,使调节阀后有一不小的中间 容积。当调节阀的数目较多、阀的尺寸较小时,亦有直接布置在上汽缸和下汽缸 上,与汽缸直接相连。因为喷嘴调节的喷嘴弧段是依次投入工作
6、的,所以有一些弧 段内为新汽,有一部分是节流后的新汽,当调节阀尚未开启时,该喷嘴弧段中的压 力和温度和调节级后相等,使喷嘴弧段间的温差甚大,同时与其相邻及相接的汽缸 亦有较大的温差;加上在调节级只有调节阀开启的弧段有强烈蒸汽流动,对应于未 开启调节阀的弧段没有蒸汽流动。这些都将导致调节级处汽缸沿周向温度不均匀, 除在汽缸体内会引起热应力外,还会使汽缸产生热翘曲。为了保证安全运行,使得 汽轮机的前轴封和第一非调节级的喷嘴板汽封的径向间隙不能调得过小,否则会引 起动、静之间碰磨,使机组发生事故。但较大的汽封间隙将增大漏汽量,降低效 率。有一些机组采用了喷嘴调节,又不希望在调节级汽缸处有过大的热应力
7、和热变 形,故设计成在开机及低负荷时各调节阀都开一些,各喷嘴弧段都有一些蒸汽通 过,使汽缸圆周间温度较均匀。随着负荷增加,进入汽轮机的流量随之增大,除正 常工作的喷嘴弧段外,其它调节阀及相应的喷嘴弧段又停止进汽,只有到大负荷时 方重新开启。纯滑压运行常是调节阀全开,新汽温度维持不变,故汽缸在进汽段沿 圆周间温度是均匀的。另外,有些机组滑压运行时不是让各调节阀都全开,这时汽 缸沿圆周温度将不均匀。2.调节级叶片的负载 对于节流调节或滑压调节,因为调节级工作喷嘴数不变,工作时通流面积不 变,调节级前温度近似不变或不变;则认为在不同进汽流量下,调节级前后压力比 近似认为不变,即焓降不变,叶片上所受到
8、的蒸汽作用力只是随着流量的增大而增 大,故在最大流量时,叶片受力为最大。对于喷嘴调节,当第一个调节阀刚全开 时,喷嘴前的压力近于新汽压力,调节级后压力因为流量较小而较低,故这时级的 焓降为最大。同时级前后压差亦为最大,这时虽然全机流量并不大,但通过每一个 工作喷嘴的流量却为最大常为临界流量),故这时作用到与工作喷嘴相对应的叶片 上所受的蒸汽作用力要比额定工况时大得多 16。 加上工作叶片有时有工作蒸汽流 过,有时又没有,使叶片所受到的扰动力很大,动应力大。调节叶片强度即按此工 况设计,所以对调节级叶片强度要求很高,常把叶根设计成双 T 型,或者橄树型。 叶片的宽度亦随机组的容量增大而增大,叶宽
9、由高压机组的 50mm 左右逐步增大到 75mm、100mm,甚至大到120mm左右,而相同参数及容量的节流调节机组,第一级叶 片的宽度只有7080mm。喷嘴调节的调节级叶片在叶顶还需要较厚的包箍或双包 箍,有时调节级就采用分流,而第一压力级并不分流,目的之一也是为了降低调节 级叶片应力。为了减小喷嘴调节机组低负荷时的应力,应当增大第一个调节阀全开 时的流量,提高调节级后压力,减小这时调节级的理想焓降。若采用较大尺寸的第 一个调节阀,又会引起阀门设计和制造上的麻烦,并使开启阀门的提升力过大,调 节阀零件不能互换等缺点,故常用的方法是让第一、二个调节阀结构相同并同时开 启,要比只一个调节阀全开时
10、全机流量大一倍,调节级后压力亦高一倍,使焓降变 小,有时还会使通过每个叶片的流量变小 变为不超临界),使调节级叶片应力变 小。3. 负荷变化时汽缸及转子温度的变化对于喷嘴调节的机组,在负荷变小时,调节级级后压力变低,调节级的焓降增 大,使调节级后的汽温随负荷升降而变动,这就使转子和汽缸受到冷却或加热,它 们的内外温差增大,引起较大的交变热应力,因而限制了机组的负荷变化速度,以 保证机组一定的使用寿命。对于节流调节,汽轮机在低负荷运行时,用调节阀节流 降低新汽压力,汽温亦有些降低,但在流量由 100%下降到 25时 以 CLN600- 24.2/566/566型600MW汽轮机为例)汽温只下降3
11、8C,只是喷嘴调节的三分之一多 些,故负荷适应性能较好17。 对于滑压调节,在负荷降低新汽压力降低时,但新汽 温度不变,则转子及汽缸最高温度在负荷变动时基本不变,这样就允许机组的负荷 有较快的变动,即机组的适应性为最好。4. 高压缸排汽温度 在负荷变动时,高压缸排汽温度亦将发生变化,当流量由 100减小到 25时,对喷嘴调节的机组,高压缸排汽温度下降108C,节流调节只下降21C,而滑 压调节还升高8C。由上可以看出,对于节流调节的机组,在流量由100%下降到 25%时,高压缸内的蒸汽温度平均下降2040C,滑压调节时高压缸内蒸汽、汽缸 温度近似于不变。故从整个高压转子和汽缸的温度变化大小来看
12、,喷嘴调节不适于 负荷快速变化,滑压调节的负荷适应性最好。应当注意,上述的数据都是对稳态而言,对于动态过程,因为中间再热机组有 一甚大的中间再热容积,容积时间常大到1015s,这使得在汽轮机负荷变动时, 例如负荷降低时,高压缸的排汽压力、中间再热压力较缓慢的下降,对于调节级或 者节流调节的第一级来讲,距中间再热容积较远,受中间再热容积的压力影响较 小,随着负荷下降,流量下降,压力较快下降,但不是阶跃式下降;对于距中间容 积最近的一些级,例如高压缸最后一个级组,因级组前的压力因流量减小而降低, 但级组后压力受中间容积中压力惯性的影响下降得很少,使得这一级组的焓降变 小,效率变低,使高压缸的排汽温
13、度不但不随负荷的降低而降低,反而有所升高, 然后高压缸排汽温度再随着中间再热容积压力降低而降低。5. 汽轮机的效率 对于节流调节和滑压调节来讲,高压缸的理想焓降在负荷变动时,基本上不变,当流量由 100%下降到 25%时,节流调节高压缸理想焓降基本上不变,只稍有 增加,约4.2kJ/kg,对滑压调节亦是稍有增加,增加23kJ/kg,即理想焓降分别增 大 3%及5%,故高压缸的相对内效率可以近似地认为不变。对于喷嘴调节而言,全开调节阀后压力近似于不变,而高压缸的排汽压力因流 量减小而降低,使蒸汽在高压缸内的理想焓降增大361.7kJ/kg,非调节级的理想焓 降因喷嘴前温度变低, 还会变少一些,
14、调节级的理想焓降比此值还大一些 393kJ/kg,使调节级的理想焓降增大了几倍3.13倍),亦即使级的速度比变 小,离开设计点较多,使调节级的效率显著下降,高压缸的相对内效率下降。根据对调节方案的分析,从热效率来看,节流调节及滑压调节都因初压变低, 使每公斤蒸汽的作功能力变小,而喷嘴调节的每公斤蒸汽作功能力为最大。虽然喷 嘴调节因高压缸排汽温度下降,使蒸汽在再热器中吸热量增大,仍可能是喷嘴调节 的热效率高些。对具体机组要具体分析,进行比较最后方能决定 18。一般地说,对 于超高压机组,在负荷变低时,还是喷嘴调节的热效率稍高些、稍经济些,或者说 与滑压调节的热效率相近。对于额定负荷来讲,喷嘴调节
15、时仍是部分进汽,所以调 节级有鼓风损失和斥汽损失,使调节级效率稍低,而节流调节和滑压调节,可以设 计成全周进汽,或者部分进汽度较大,斥汽损失、鼓风损失较小,故在额定负荷时 调节级的效率稍高,较喷嘴调节的调节级的效率高出0.4%0.6%,此数值虽小,对 于经常在满负荷下运行的大机组,亦是一个不可忽视的因素19。顺序阀改造方案汽轮机原有阀门控制函数托电汽轮机原有高压调门控制函数与纯单阀稍有不同,采取的是滑压复合配汽 方式运行,如图3-1所示20 212223。 图中可以看出,先后两种控制方式对应两种不同 的进汽方式,低流量时单阀方式可以实现机组的节流调节运行,高流量时部分实现 机组的喷嘴调节运行。
16、为减小启动过程中的热冲击,以单阀方式启动即采用节流配 汽全周进汽方式),避免汽缸及转子应力过大,保证机组顺利启动,在达到目标负 荷且温度场趋于稳定后可以切换到部分喷嘴配汽,提高一定的经济性。在大部分运 行时间内,四个调门均参与调节,节流损失大。因为是采用中压缸启动,在流量0- 20%期间,高压调门并不开启,而是由中调门进行控制,中调门全开后,高调门开始 开启。再热蒸汽通过2个中压联合汽阀进入中压部分,中压部分为全周进汽,因此中 压调节阀仅采用节流调节方式运行。流量在20以下时起调节作用,以维持再热器 内必要的最低压力,流量大于20时,调节阀一直保持全开,仅由高压调节阀调节 负荷 2425262
17、7。单阀函類(I20d0師801001Z0-SO L 涼量指令图 3-1 原有汽轮机高压调门函数曲线Fig 3-1 The original function curves of turbine governing valves汽轮机高压阀门位置及原有顺序图托电汽轮机原有高压阀门位置及顺序见图3-2。Fig 3-2 The originalposition and opening sequence of turbine governing valves 启动过程无论是采用中压缸启动还是高中压缸联合启动,在汽轮机冲转、升 速、并网、带低负荷阶段一般选用节流调节方式。因该方式为汽流全周进入中压缸
18、或高压调节级,使汽缸和转子能均匀地加热膨胀,故能有效降低启动过程中的热应力和调节级动叶的机械应力。图 3-3 所示为托电汽轮机的阀门升程曲线及调节级后 温度变化曲线。图 3-4 所示为托电汽轮机的调门升程曲线。自话切换(I部分进汽ATG2贞荷究变吋的温廈班化全剧进汽 调节列AAT;I金属温度朮荷先寅100 Lt Hid图 3-3 汽轮机调门升程及调节级后温度变化曲线Fig 3-3 The curved line of governing valvelift and temperature change behind velocity stage of tFig 3-4 The curved l
19、ine of governing valvelift of turbine汽轮机调节级配汽数据托电汽轮机调节级配汽数据见表3-1,调节级喷嘴组数据见表3-2。表 3-1 汽轮机调节级配汽数据Table 3-lThe steam distributing data of turbine velocity stage名称型线Kp(Kd出口角节距叶片数叶高叶宽出口面积面积比符号NoSina/1g(B.a/ ig(BtZLp/LdBFp(FdFd/Fp单位/2g/2g0mm只mmmmcm2/喷嘴JZ.640.250914.5317.09184/19255.954.86440.92/动叶DZ.370.3
20、8722.7774.634458.976.2717.261.627备注 & =1时,Z=156只,静叶平均直径971mm,动叶平均直径973mm。表 3-2 汽轮机调节级喷嘴组数据Table 3-2 The nozzle group data of turbine velocity stage喷嘴组号进汽率喷嘴出口面积喷嘴数符号Fp工FpZp工Zp单位/cm2cm2只只I0.29690.2969136.60136.605757II0.18230.479283.88220.483592III0.18230.661583.88304.3535127W0.29690.9583136.60440.92
21、57184确定顺序阀改造方案喷嘴调节机组在部分负荷运行时,调节级喷嘴部分进汽。不同的阀门开启顺 序,进汽的部位不同,对机组产生不同的影响。主要影响有两个。一是启动时,进 汽的部位不同,汽缸被加热的部位不同,产生的热应力有大有小。但是, 600MW 机 组用单阀启动,全周进汽,没有这个问题。二是部分进汽时,进汽的动叶受到一个 汽流产生的切向力和前后压差产生的轴向力,不进汽的动叶就没有这些力。所以, 调节级叶轮受到不均衡的切向力和轴向力 28。这些力通过转子作用到轴承上,对 1 号和 2 号轴承的载荷产生较大的影响,不同的开启顺序产生不同的影响,而且调节 级功率越大,产生的影响越大,不容忽视。托电
22、汽轮机顺序阀改造提出三种方案,如图 3-5 所示。图 3-5 汽轮机高压阀门开启顺序三种改造方案Fig 3-5 Three transforming schemes of opening sequence of turbine governing valves经过比较,B方案是比较安全的,最终确定了 “1号、4号调门同时先开,然后 依次开 2 号和 3 号调门”的方案,如图 3-6。顺序阀切换时间的选择顺序阀不容易实现的原因之一就是单阀与顺阀切换过程中机组跳闸,使人产生 害怕心理。盘山电厂在切换过程中机组多次跳闸,平圩电厂机组也因此跳闸过。经 过分析认为是切换时间短,蒸汽的扰动力大,使转子失稳
23、,轴瓦温度和振动快速上 升。经验表明切换时间大于10分钟,蒸汽的扰动力减少很多,转子稳定,轴瓦温度 和振动变化缓慢。初步确定托电汽轮机单阀、顺序阀切换时间为15分钟。单阀、顺序阀切换实验单阀、顺序阀方式切换方法两套函数单阀控制函数为原控制函数,顺阀控制函数为新设计函数),根据要 求由运行人员手动进行阀门控制方式切换。在机组主画面“ DEH CV MODE ”按钮,进 入“CV CONTROL MODE”画面(即单阀、顺序阀切换操作画面。该画面与“DEH AUTO CTL” (DEH自动控制画面类似,除画面中新增的两个按钮 “CV CTRL MODE”和 “MODE HOLD ”外,其余按钮及对
24、话框所具备的功能与“ DEH AUTO CTL ”画面中的相应的按钮及对话框一致,画面如图3-8。1. 在单阀控制方式下,“CV CONTROL MODE ”画面显示相关描述为:显示字体“ SINGLE VLV MODE”。 “TRANSFORM PROCESS”为“100%”。“ TIME ”所对应的时间为完成整个转换过程所需要的时间。2在顺序阀控制方式下,“CV CONTROL MODE ”画面显示相关描述为:显示字体“ SEQUENCE VLV MODE”。 “TRANSFORM PROCESS”为“100%”。“ TIME ”所指示的时间为完成整个转换过程所需要的时间。2 339CV
25、CONTROL MODEBREAKER 1-1M5V STEAM PREIP1STGINLEFPRELCCS DEMANDv .L15 t3MPa.2 . bMPa32-1%COLD START-二一、W5Y TNLETPREIP1STGINLEFPRE2l:;丨、= =. =15.5MPb2.6UFh.-=HP LEI匚 DUTLET 5TM PREIP1 STi-INLETPRES12.3MPb2,6UPiTf. I-1 T . II 宀卜CV MODEH:L:Id i- -H i.:Il 1 l C VLV MODETIME 300. SECTRANSFORM PROCESSIDO .K
26、LLD7Z%r /n1nMPn /n SnLI Vr.-I: I .J 窪 I3ZT1J .MW/nln图 3-8 单阀、顺序阀切换操作画面Fig 3-8 The operation frame of switching from single-valve to sequence-valve mode3. 由单阀控制方式向顺序阀控制方式转换点击“CV CTRL MODE ”按钮,弹出对话框,“SINGLE ”为红色字体,“SEQ” 为黑色字体,“CONFIRM”为灰色字体;点击“SEQ”按钮,在“CONFIRM”变为黑色 字体时迅速点击其按钮,则转换过程开始,然后“ SEQ ”变为红色字体,“
27、SINGLE” 变为黑色字体,“CONFIRM ”恢复为灰色字体。转换过程中画面文字主要显示:“SINGLE TO SEQUENCE” 闪烁;“TRANSFORM PROCESS”从 0%向 100% 变化;字体“ SINGLE VLV MODE ” 消失。转换完成后画面显示顺序阀控制状态下的正常显示。4. 顺序阀控制方式向单阀控制方式转换点击“CV CTRL MODE”按钮,弹出对话框,“SEQ”为红色字体,“SINGLE” 为黑色字体,“CONFIRM”为灰色字体;点击“ SINGLE”按钮,在“ CONFIRM”变为 黑色字体时迅速点击其按钮,则转换过程开始,然后“ SINGLE ”变为
28、红色字体,“SEQ ”变为黑色字体,“CONFIRM ”恢复为灰色字体。转换过程中画面文字主要显示:uSEQUENCE TO SINGLE” 闪烁;“TRANSFORM PROCESS” 从 0%向 100%变化;字 体“ SEQUENCE VLV MODE ” 消失。转换完成后画面显示单阀控制状态下的正常显示。5. MODE HOLD”按钮的使用在 CV 调门控制方式转换过程中,系统一但出现异常情况,运行人员可点击“MODE HOLD”按钮,在弹出的对话框中点击“HOLD”按钮,使转换过程停止并保持 在当前状态,画面显示红色闪烁字体“ HOLD”。当系统稳定后,再点击“ MODE HOLD”
29、按钮对话框中的“RESET”键,使转换过程继续进行。此按钮只有在CV控制 模式转换过程中起作用,与“ DEH AUTO CTL ”画面中的“ GOHOLD”按钮无任何关 系。单阀、顺序阀方式切换注意事项1汽轮机冲车前确认CV控制方式在“ SINGLE VLV MODE”;2. 机组首次进行CV控制方式转换时使用DEH LOAD CONTROL;3. 当实际负荷与负荷指令偏差大于20MW时或DEH在手动控制方式都会导致转换 过程自动停止相当于手动点击“ MODE HOLD ”按钮);4从“ HOLD ”状态恢复到模式转换过程只能通过运行人员手动按“ HOLD MODE” 中的“ RESET ”键
30、。5.在转换过程中,可随时进行反切换。例如在由单阀控制方式向顺序阀控制方 式转换过程中,若想停止转换过程并重新恢复到单阀控制模式,可参照前面所述的“由顺序阀控制方式向单阀控制方式转换”的相关内容进行操作即可;反之亦然。顺序阀运行及切换安全措施根据实验过程,制定了顺序阀运行及切换安全措施:1顺阀运行时 顺序阀运行期间,负荷出现大幅度异常波动,立即将汽机自动切至手 动,机组参数稳定后,再重新投入。顺序阀运行期间,加强对#1、2瓦温度及振动的监视。顺序阀运行期间,每班对照两次阀门函数表,观察阀门位置是否正常,发现 异常及时汇报专业,并通知热控人员。2切换注意事项单阀、顺阀互切时,将机组负荷维持300
31、MW以上(尽量低一些,各参数稳定 后再进行切换。首先解除机、炉主控自动,退出 CCS CTL(协调顺序系统,投入 LOAD CTL(DEH负荷控制,然后开始进行切换。切换过程中,出现负荷或阀位摆动大,立即按“ HOLD ”按钮进行保持(切换时 负荷与初始负荷偏差达到20MW后,切换自动保持,解除汽机DEH自动,手动调整 总阀位指令,维持切换前负荷参数稳定后,投入DEH自动及LOAD CTL,按 “RESET”复位,继续进行切换。3特殊方式下注意事项冲转前必须确认汽机调门控制方式在“单阀”方式,否则切换至单阀方式。 正常停机,机组负荷300MW时将汽机调门控制方式切换至“单阀”方式。汽机总阀位指
32、令顺阀与单阀时不同,机组发生RB、灭火等紧急降负荷的情况 时,注意观察机组负荷及各调门开度,防止逆功率保护动作。改造效果及其评价托电公司汽轮机顺序阀改造后,降低了轴承金属温度,轴承振动没有大的变 化,提高机组了运行的安全性和可靠性;顺序阀有明显节能效益,汽轮机热耗下降 从而使煤耗降低,提高了机组的经济性。节能效果显著托电公司目前装机容量为8X600MW,因为线路送出受阻八台,机组运行最大负 荷将近4000MW,最大负荷率将近90%,正常负荷率75%,即机组平均负荷为450MW。 根据实验及实际运行情况看,汽轮机顺序阀改造后的机组发电煤耗下降在1.5克/千 瓦时以上。托电2007年八台机组发电量
33、约244亿kWh,消耗原煤约1290万吨,折合标煤 约 782 万吨。按煤耗降低 1.5 克/千瓦时(实际发电煤耗 311.19 克/千瓦时,节约原 煤约 62180 吨,折合标煤约 37694 吨,按照标煤单价 246.8 元/吨计算,燃料成本将 降低约 930.29 万元。从上面数据可以看出,电厂汽轮机顺序阀改造大大地提高了机组运行的经济 性,有非常显著节能效果。延长设备寿命,提高设备可靠性汽轮机采用顺序阀配汽可使 1、2 号轴承金属温度显著下降,轴承工作状况得到 了明显改善,从而降低汽轮机轴承损坏的故障率,提高了汽轮机运行的可靠性。顺序阀不能实现的首要原因就是单阀与顺阀切换过程中机跳闸,
34、托电在改造过 程中,延长了切换时间到 15 分钟,没有出现在切换过程中机组跳闸的现象,说明此 时间选择比较合理,提高了顺序阀切换的可靠性。减少环境污染汽轮机采用顺序阀配汽后,机组煤耗降低,相当于少燃烧煤碳,减少了氮氧化 物、二氧化硫、粉尘和大量二氧化碳等污染物的排放,降低对大气污染,保护了环 境。如果按照燃煤含硫量 0.764%计算,则减少二氧化硫排放量约 760 吨(燃烧产物 80%计算;燃煤燃烧后按照 28.3%灰渣量计算,则减少灰渣排放量约 17597 吨,环 保效果明显。门杆断裂问题托电 3 号机组曾发生过高压调门门杆断裂的问题。经过分析,汽轮机高压调门 伺服阀在0100%之间调节过程
35、是双向调节,同时控制油动机的进口和出口,将油 动机固定在相应的位置。而改为顺序阀调节后,在 50%以上负荷时有两个阀门基本 是常开的,油动机只提供单向动力,阀杆长期受油动机牵引力极易导致连接部分断 裂。解决问题的措施:1. 油动机100%开度要比阀门的全行程小57mm,限制油动机全开。2. 加大连接部分的几何尺寸。3. 更换阀门的材质。托电通过更改油动机开度,最大只开 95%,阀杆双向受力,门杆断裂的问题再未发生。负荷振荡托电 3 号汽轮机在投入顺阀后,机组在 AGC 运行方式下,曾发生负荷振荡,原 因为原协调参数在顺阀方式下不适应一次调频动作后引起的机组负荷扰动,重新调 整协调 PID 参数后此问题已解决。并对其他机组按 3 号机组参数进行优化,同类事 件的没有再次发生。低负荷状态2 号机组于 2007 年 6 月 15 日发生一次灭火不停机事故,灭火前机组处于 600MW 满负荷顺阀方式,灭火后机组在顺阀方式快速减负荷至30MW,随后锅炉点火成功, 机组重新升负荷至500MW。此过程机组一直保持在顺阀方式,汽机转速及负荷控制 很稳定,未发生转速飞升和负荷振荡现象,这从另一个角度说明了托电的顺阀函数 可以在任意负荷状态下能够安全稳定运行。综上所述,若该方法在全国电力系统 600 兆瓦级同型汽轮机全面推广,既提高 机组运行的经济性,又降低污染物的排放,经济效益和环保效益相当可观。
- 温馨提示:
1: 本站所有资源如无特殊说明,都需要本地电脑安装OFFICE2007和PDF阅读器。图纸软件为CAD,CAXA,PROE,UG,SolidWorks等.压缩文件请下载最新的WinRAR软件解压。
2: 本站的文档不包含任何第三方提供的附件图纸等,如果需要附件,请联系上传者。文件的所有权益归上传用户所有。
3.本站RAR压缩包中若带图纸,网页内容里面会有图纸预览,若没有图纸预览就没有图纸。
4. 未经权益所有人同意不得将文件中的内容挪作商业或盈利用途。
5. 装配图网仅提供信息存储空间,仅对用户上传内容的表现方式做保护处理,对用户上传分享的文档内容本身不做任何修改或编辑,并不能对任何下载内容负责。
6. 下载文件中如有侵权或不适当内容,请与我们联系,我们立即纠正。
7. 本站不保证下载资源的准确性、安全性和完整性, 同时也不承担用户因使用这些下载资源对自己和他人造成任何形式的伤害或损失。