金属化孔常见缺陷及预防
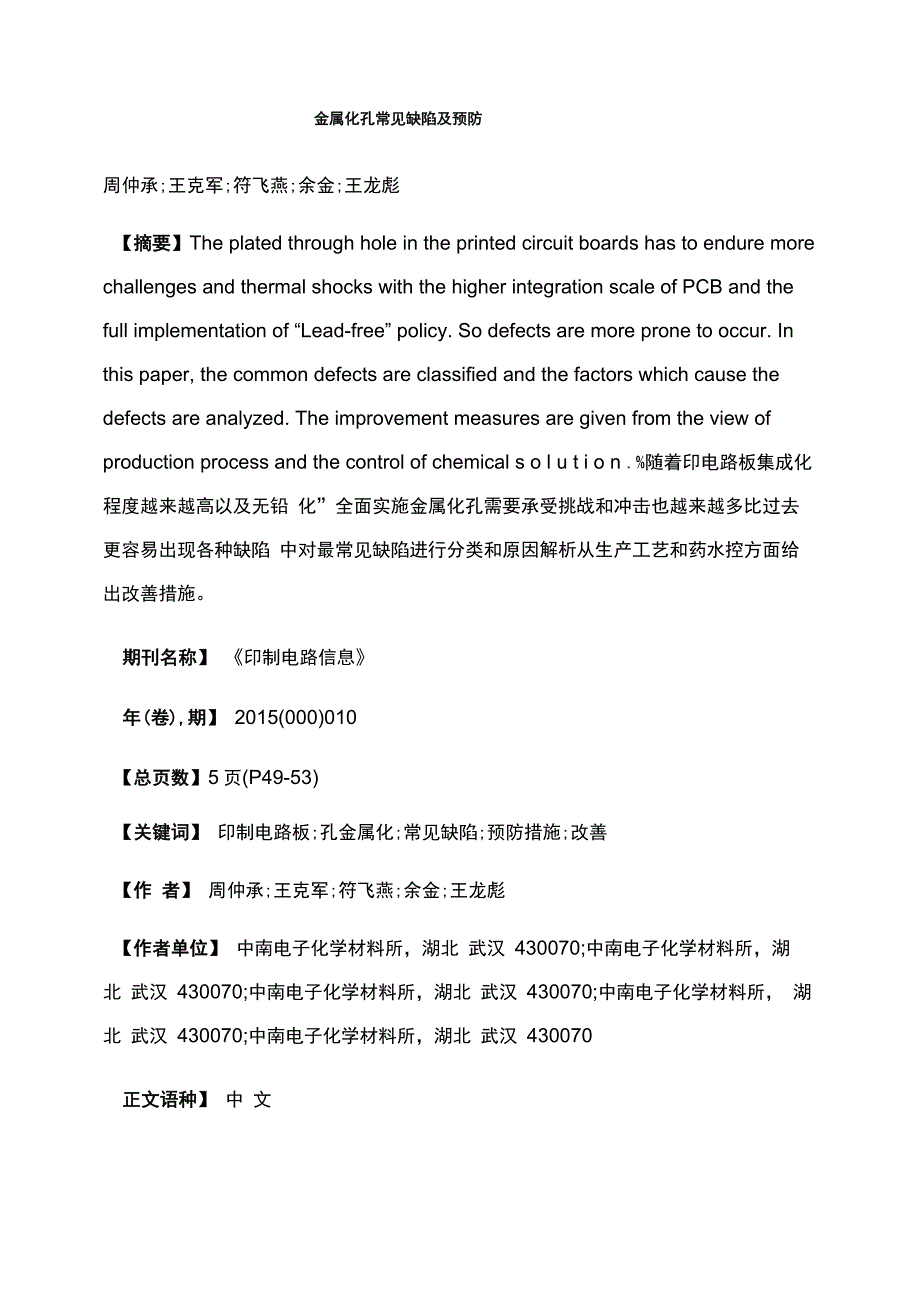


《金属化孔常见缺陷及预防》由会员分享,可在线阅读,更多相关《金属化孔常见缺陷及预防(11页珍藏版)》请在装配图网上搜索。
1、金属化孔常见缺陷及预防周仲承;王克军;符飞燕;余金;王龙彪【摘要】The plated through hole in the printed circuit boards has to endure more challenges and thermal shocks with the higher integration scale of PCB and the full implementation of “Lead-free” policy. So defects are more prone to occur. In this paper, the common defects ar
2、e classified and the factors which cause the defects are analyzed. The improvement measures are given from the view of production process and the control of chemical s o l u t i o n .%随着印电路板集成化程度越来越高以及无铅 化”全面实施金属化孔需要承受挑战和冲击也越来越多比过去更容易出现各种缺陷 中对最常见缺陷进行分类和原因解析从生产工艺和药水控方面给出改善措施。期刊名称】 印制电路信息年(卷),期】 2015(
3、000)010【总页数】5页(P49-53)【关键词】 印制电路板;孔金属化;常见缺陷;预防措施;改善【作 者】 周仲承;王克军;符飞燕;余金;王龙彪【作者单位】 中南电子化学材料所,湖北 武汉 430070;中南电子化学材料所,湖 北 武汉 430070;中南电子化学材料所,湖北 武汉 430070;中南电子化学材料所, 湖北 武汉 430070;中南电子化学材料所,湖北 武汉 430070正文语种】 中 文【中图分类】TN41印制电路板(PCB )上的各种连通孔起着连接不同层间电路的作用,其金属化(Plated Through Hole,PTH)是PCB制造中极为重要的一道工序。PTH效果
4、 的好坏直接影响到后续电镀镀层的质量以及镀层与PCB基材的结合力,进而影响 到整块PCB的性能和使用寿命,许多PCB的失效都是由通孔连接失效所引起的。 随着通讯电子设备向“轻、薄、短、小”、多功能化、便携化发展,PCB的集成 化程度也越来越高且向“密、薄、平”发展,PCB板面布线越来越密,通孔的孔 径越来越小、厚径比越来越大。最小孔径将达到0.3 mm 0.1 mm,多层板集 成的层数将在40层以上,通孔厚径比将在15以上1。此外,随着环保要求的愈加严格,PCB基材及阻燃剂类型也发生了变化,所用焊 料也由含铅更换为无铅体系,需承受的热处理温度更高、高温焊接时间更长。这一 切使得金属化孔的难度增
5、加很多,对PTH化学药水与生产工艺提出了更高要求 2,缺陷产生的概率也大为增加。高密度化和无铅化给PCB制造工艺和各工序带来了巨大挑战。1.1 高密度化带来挑战 高密度化是印制线路板发展的必然趋势,其具体表现是高多层化、孔微小化、高厚 径比化和盲孔化,使得PCB的孑L金属化与电镀更为复杂和困难。在高厚径比、高可靠性背板制造时,由于其典型的厚径比值接近或超过15:1 , 必须考虑在孔内的流体流动动力学、化学药水的活性组分必须能与孔壁发生相互作 用,此外,发生在化学溶液中的物料交换也须加修正3。1.2 无铅化多层板还面临着无铅化焊接的要求。无铅化要采用更高的热分解温度(Td )和玻 璃化温度(Tg
6、 )的覆铜板材料,会带来加工新问题;无铅化焊接工艺的焊接温度 更高、高温焊接时间更长和冷却速度更快,要求导通孔内的铜镀层不仅要有更好的 延展性,而且要与孔壁有较好的结合力;无铅化工艺所制造的成品板要经得起更多 次“热循环”、“热冲击”等考验。上述挑战使PCB孔金属化镀层更易发生“空洞”、“裂缝”、“剥离”等现象。 由于制造难度的挑战,PTH工艺过程“孔破”出现几率有了较大增加,成为最为 常见的缺陷,也是困扰业界的一个难题。“孔破”指在孔壁在金属化或后续工序中,孔壁镀层出现了局部破洞、环状孔破, 孔壁分离、整孔无铜的现象,最常出现的是镀层“空洞”和孔壁分离4。如果 在电性测试时经检测出来而报废,
7、会造成生产成本的浪费,而更为严重的则流失到 客户端产生PCBA报废。该缺陷涉及流程长,影响因素多,属于制程与管理结合的缺陷,加上属于信赖性缺 点,从外观目视无法做识别,需借助传统电性测试做关卡,但电性测试并不能 100%侦测到该缺点,故并不能完全依赖测试,需从源头进行预防和改善,孔壁分离是PCB在热处理(热风整平锡、热冲击、回流焊)过程中,通孔的孔壁 镀层与基材发生分离的一种缺陷。孔壁分离最直接的原因是在热处理时,孔壁镀层 与基材之间的结合力无法对抗基材与孔壁镀层的热膨胀系数存在差异而产生的拉扯 力以及基材内存在的湿气对孔壁铜的膨胀力,从而导致孔壁镀层与基材分离。随着 无铅化的到来,各种多功能
8、、高耐热性的无铅材料的出现,孔壁分离的出现越来越 频繁,在厚板,大通孔板上表现尤为突出。导通孔产生“空洞”是指孔内镀铜层与孔壁的界面之间、或者铜镀层中存在着无镀 层区的域。“空洞”产生的原因有:钻孔参数不合理,孔壁粗糙度未达到要求;去 钻污过度引起玻璃纤维突出孔壁;孔金属化效果不好,有不连续镀层;在热处理或 压合时未合理烘板等。可能引起孔壁分离和镀层“空洞”的因素很多,包括PCB设计、PCB加工、PCB 原材料性能等方面5,应分别针对各种因素进行改善和预防。2.1 PCB设计 随着孔径减小,孔壁曲度越来越大,这样对抗孔壁分离的孔壁铜自身的支撑力越大, 出现孔铜分离的几率将越来越小,因此,孔壁分
9、离大都出现在大孔的孔壁。对于多层板而言,孔壁与内层铜有连接时,相当于将孔壁铜用一个“钉子”铆住, 对孔壁分离有一定的对抗作用;而孔壁铜与内层铜无连接时,则出现孔壁分离的几 率较高。由此可见,PCB的设计对孔铜分离有一定影响。孔的大小因为设计的需要,不可 能改变,但是大通孔将是孔壁分离的易发区。而对于多层厚板,尽量在无需连接的 层设计无功用的孤立焊盘,可以将孔壁铜铆住,避免分离5。2.2 PCB基材为了应对无铅化、无卤化、以及低热膨胀系数(CTE)、低Dk/Df,anti-caf等要 求,板材供应商开发了许多特殊板材。大量试验和应用都证明,采用高Tg和低 CTE的基材,孑L壁镀层发生“分离”、“
10、空洞”等缺陷就少很多。但是,制造加 工过程中会带来新问题,应注意加工工艺的改进。用酚醛树脂类取代双氰胺为固化剂,可以将环氧树脂Dd提高到340 C左右,能 明显减少“空洞”和“分层”缺陷。但此类树脂脆性大,加工困难,且Tg低、 CTE大,仍可能会出现各种热缺陷。最好是采用多功能或改性的环氧树脂系,使 覆铜板在具有高Td的同时,还具有高Tg和低CTE。然而,与传统FR-4相比, 伴随着这些特殊功能的实现,也付出相应的代价,如成本提高、可加工性能(械加 工性能和化学处理加工性能)降低。这些板材在进行PTH操作时,有很多不同于 传统板材的地方:无铅材料的树脂大都具有更高交链密度和更复杂的化学结构,去
11、 钻污和得到比表面积大的粗糙表面更加困难。实验研究表明,普通材料通过加强去钻污能够有效增大孔壁的微观粗糙度,但是针 对某些高Tg材料,加强去钻污只是将钻孔留下的比较粗糙的孔壁表面“抛光”而 不能进一步咬蚀而变得更加光滑,反而不利于孔壁铜与基材的结合,埋下孔壁分离 的隐患。而对于刚挠结合板,印制板材料的热膨胀系数(尤其是 Z 轴热膨胀系数)对保证 金属化孔的可靠性十分重要6Z轴热膨胀系数越大的材料在经受热冲击时对 孔壁铜的冲击力就越大,就会更容易造成金属化孔铜镀层的断裂或孔壁开裂。由于 刚挠印制板所采用粘结材料是非支撑(无增强材料)不流动性的热塑性粘结材料, 如丙烯酸粘结材料等。丙烯酸胶的玻璃化
12、温度较低,其热膨胀系数是其它材料的数 倍。在现有的粘结材料中丙烯酸胶的玻璃化温度最低,热膨胀系数是环氧树脂的数 倍。因此,应尽量减少使用丙烯酸粘结片,即使使用也应控制其厚度不超过 0.05 mm,避免受到热冲击时孔壁镀层开裂。刚挠印制板所选用的材料中,无论是覆铜还是非覆铜的挠性材料,其吸水性均高于 FR-4 材料6。因此,在刚挠板加工过程和挠性材料的储存方面必须重视挠性 材料的这一特点,尤其是刚挠板压制前和热风整平前,一定要对在制板进行干燥处 理,避免在高温下板内潮气汽化加大金属化孔内层镀层与孔壁铜的应力,使刚挠板 出现金属化孔孔壁开裂等质量问题。所以,PCB厂家在设计和选择板材时,一定要认真
13、评估材料与厂家自身制程和药 水的匹配与兼容性问题,防止出现“南辕北辙”的效果。2.3 层压及相关工序层压工序使用的FR-4、聚四氟乙烯(PTFE )、聚酰亚胺(PI)、陶瓷基材料等, 都有其特定的加工参数和使用条件。传统的FR-4材料由于受到Tg温度和CTE的 影响,在无铅化的高温高压条件下,基材内部易形成分层或者微空隙,需要进行改 性处理,降低加工过程中残余应力。各种特殊填料的加入,在改变材料特性的同时 也增加了相应的加工难度,在真空条件下高温压合,如控制不好加工参数或者内层 芯板前处理不良,树脂与内层铜箔的结合不良会对后续的制造和应用埋下隐患。因 此,选择合适的PP型号、稳定工艺流程和调整
14、适宜的加工参数,在层压工序是改善镀层空洞的主要方法7。2.4 钻孔 钻孔质量的好坏对孔壁质量有着较大的影响,如果钻孔不好,一是容易造成“孔 粗”,形成连续性差的化学镀铜层,电镀铜层的连续性也差,这样在受到热冲击时, 很容易引起孔壁铜与基材分离;另一个方面是会对基材造成“内伤”,孔壁基材微 裂痕多,孔的晕圈大,使得湿气很容易渗入孔壁基材包覆其中,在热处理过程中, 湿气的剧烈膨胀破坏孔壁铜与基材的结合,产生镀层“空洞”缺陷。随着对钻孔质量要求的提高,对钻孔参数的要求如下8:(1)随孔径缩小, 钻孔速度要相应提高。当钻孔的直径减小时,为了保证孔壁质量和生产力,必须把 数控钻床的转速提高。同时,要适当
15、调整进钻速度,如果进钻速度与钻头转速不匹 配,在界面处易造成“撕裂”的缝隙等,埋下“空洞”、“楔形空洞”等缺陷隐患。(2)当钻孔直径不断地减小时,孔壁粗糙度要相应地减小。孔径越小,化学药水 经过越困难,大的粗糙度容易引起“驻液”或处理不到,形成“空洞”等缺陷。为 保证孔金属化的效果,不同孔径对孔壁粗糙度的要求如表 1 所示。钻孔的质量,受到钻头的结构和组成影响外,钻头的状态(特别是钻头刃部的锋利 和完整程度)也对钻孔质量有着很大的影响。如过刃部锋利度不足或磨损过大(钻 孔过多、刃磨次数太多)以及刃部有缺口等,在钻孔过程中容易造成“撕裂”、 “冲切”作用而带来孔壁缺陷,从而形成孔金属化“空洞”等
16、问题。此外,为改善 钻孔质量,还需要在工艺参数、刀具的选择及寿命、翻磨次数、盖板以及垫板等多 方面进行选择和优化。由于刚挠印制板中既含有刚性材料,又含有挠性材料,其机械加工性能完全不一样。 为了保证钻孔效果,除了注意上述几点外,还应该做好以下几项6:钻孔前烘 板、使用新钻头和调整钻孔数量上限、调整转速和进给等。首先要选用新钻头,在 钻孔数量大于1000个后,孔壁的腻污量增多了,钉头现象也出现了,甚至还出现 了介质层撕裂的现象。钻孔转速应适当降低,尽量控制钻头升温速度不要过快,以 免在钻低Tg材料时产生过多的钻污。如有条件可以考虑对钻头进行冷气降温,效 果会更好。降低进给对提高钻孔质量有好处,但
17、是过度地降低进给会延长钻头对孔 壁的摩擦时间,同样会增加腻污量。除了优化转速和进给参数外,还应该采用全新 铲形钻头、严格控制每支钻头的钻孔数量、选择合适的上下垫板。另外,在钻孔前 进行预烘(120 C左右,2 h 4 h)对钻孔质量有明显改善,尤其是在潮湿的夏 季。但是在烘板处理时需要注意,烘板的温度过高或时间过长会引起树脂老化。2.5 去钻污工艺 随着厚径比的提高和孔径的缩小,如果钻孔参数未调整好、真空吸力不足、清洗不 足或静电吸附等,很容易造成孔内“残渣”,孔壁余胶及粉屑,由于其“松散”的 状态,在孔化和电镀过程中,往往受到外界因素“松动”而脱落离去,从而形成镀 层空洞,并随着板件厚径比的
18、增加,这种影响更为明显。在生产时,要定期对刷板 机的刷辊、喷嘴的压力及工作状况进行点检和维护,对于厚径比大于10:1的板 件,还应增加线外超声波水洗来保证孔壁的润湿性并排出孔内的异物 7。此外, 还必须进行彻底的去钻污处理。去钻污处理一是除掉孔壁钻污或残留,显露内层 “铜环”;二是维持一定树脂咬蚀量,使处理后的孔壁表面有“比表面积”非常大 的蜂窝状粗糙结构。目前,绝大多数去钻污是采用碱性高锰酸盐溶液除去内层铜环 上的钻污并形成粗糙表面。程静9 运用Guldberg-Waage质量作用定理计算了高锰酸盐凹蚀液中高锰酸 根、锰酸根、氧化锰等组分的反应速率方程,并计算了去钻污速率与反应物浓度、 生成
19、物浓度和温度的关系。高锰酸根在酸性溶液中会缓慢歧化分解,析出棕色的二 氧化锰,并释放出氧气;在中性或碱性溶液中高锰酸根也会歧化分解,但分解速率 更为缓慢;温度和光照会加速高锰酸根的分解。随着除钻污的进行,副产物锰酸钾 和二氧化锰含量增大,除钻污速率会明显减慢。为了维持蚀刻速率的稳定,需要对 凹蚀液进行再生处理,最常用的是电解再生方法,操作电流为每平方米板件/每小 时乘以7.5安培;电压:6 V 9 V,电压偏高,说明再生槽内的氢氧化钠浓度可 能过高。不同树脂的性能是不一样的,因此,使用高锰酸盐溶液处理效果也不一样。对常规的FR-4有较好处理效果的凹蚀溶液和工作参数,在处理高性能(高Td和高Tg
20、 ) 树脂基材时,蚀刻速率只有普通基材的1/3 1/4,且处理后的树脂表面粗糙度难 以达到要求8。因此,对于高性能树脂基材的处理要改变处理液的组成和方法, 特别是改变“溶胀(sweller) ”处理液配方和处理时间8,或者在碱性高锰酸 盐凹蚀液中加入“敏化剂”,才能获得良好的树脂表面形态和粗糙度。对于高多层背板的去钻污工艺来说,由于背板基材多为高Tg树脂或环氧树脂与聚 氧苯撑(PPO)的共聚交连物,采用传统的去钻污药水,树脂的蚀刻量和表面形 貌均难以满足要求。而如果升高凹蚀液中高锰酸盐浓度、处理温度及延长处理时间, 树脂减重量可以达到要求,但表面形貌难以令人满意,解决方法是采用新型的溶胀 剂3
21、,增强了树脂的渗透能力,即便采用传统的凹蚀处理参数,也可得到满意 的蚀刻深度与表面形貌。PCB基材越来越多地采用无卤阻燃剂。无卤阻燃剂大多采用含磷化学物和无机填 料,其产生的钻污更难除去8。因此,在前处理和去钻污过程中,必须重新调 整操作参数,才能保证镀层与基材的结合力。刚挠印制板使用的材料有:环氧树脂、聚酰亚胺树脂、丙烯酸树脂、玻璃纤维和铜 箔。通常,聚酰亚胺产生的钻污量比较少,而环氧和丙烯酸胶易产生钻污6。由于挠性部分的聚酰亚胺树脂在浓硫酸中呈惰性,采用常规的浓硫酸洗孔的方法只 能去除环氧树脂钻污,而对于丙烯酸树脂和聚酰亚胺树脂则没有作用。无法用浓硫 酸法去除刚-挠结合板中的钻污10。另外
22、,聚酰亚胺树脂呈憎水性,且不耐强碱溶液,在传统的碱性高锰酸盐凹蚀液中 会溶胀甚至少部分溶解。丙烯酸树脂既不耐强碱溶液又不耐强酸溶液,也无法采用 传统方法进行去钻污处理。采用铬酸法和等离子处理可以获得较好的去钻污和凹蚀 效果。只是采用铬酸法仍需要进行去除玻璃纤维,且环境污染严重。等离子处理可 以同时与树脂和玻璃纤维反应,并增强孔壁的亲水性,是较为理想的去钻污和凹蚀 技术。SJ20604中规定的多层板凹蚀深度的允许值是5 pm 80 pm。根据目前 的刚挠印制板的布线密度和应用环境,刚挠印制板的最佳凹蚀深度约为13 pm 8 pm6。等离子处理难以除去刚性基材内的玻璃纤维,在等离子处理后,需 用化
23、学 溶液对伸出孔壁的玻璃纤维再进行处理。此外,为了去除刚挠印制板中的 潮气,在等离子体处理前应对刚挠板进行烘板。在生产过程中,应经常作质量损失试验,质量损失控制在(0.13 0.5 ) mg/cm2、凹蚀深度控制在815微米之间6。凹蚀速度不能太快太强,容易 引起溶液稳定性下降,沉淀增多,影响小孔的凹蚀效果。此外,凹蚀液的温度不能 低,否则,容易析出结晶,堵塞小孔径且去除胶渣不净。2.6 化学镀铜 为了改善化学铜与基材的结合,降低出现孔壁分离和“空洞”的几率,化学沉铜层 应该具备如下特质5:坚固致密的晶体结构、内部应力应该足够小、具有极好 的一致性。由于孔壁与化学镀铜层之间是通过作用力较弱的“
24、范得华力”结合,沉积结构也是 “疏松”的,延展性也不是很好,因此要求化学镀铜层的厚度在保证完整性和导电 性的前提下,要尽量薄一些,一般要求在0.3 pm 0.6 pm之间8。对于多 层板来说,化学沉厚铜(4 pm 10 pm)是越来越少采用了,特别是从2006年 实施无铅化焊接以来,化学沉厚铜是不宜使用的。为了得到高质量的化学镀铜层,除了槽液的配方组成必须经过科学合理的设计和筛 选外,槽液的操作与控制也是非常重要的,其中又以各组分浓度的补充、槽液温度 的控制、化学镀铜前的处理以及搅拌过滤等最为重要11。槽液当中的铜盐、 氢氧化钠以及甲醛的浓度,都需要达到特定的程度,并且应处于一种平衡状态。除
25、此之外,槽液的温度必须适当,而且还需要有一个清洁的镀槽。所以不论是在槽液 的配方组成、以及槽液的操作控制等方面,化学镀铜均比电镀铜槽的要求更为严格 而对于小孔径PCB,在化学镀铜时还需要注意几个方面12:溶液鼓泡不能太 大,否则,容易产生气泡进入孔内或微小气泡被铜覆盖现象,在成品板焊接时可能 出现“放炮孔”。反应速度不易过快,太快会使析氢强烈,气体容易吸附在孔壁上 面,而产生破孔现象,引发周期控制在1分钟左右为宜。铜离子浓度维持在上限 值,槽液负载控制0.8 dm2/L左右,比重控制在1.12 1.14之间,且必须要有振 动、摆动及过滤装置。保证各工序药水与孔壁的充分接触与交换、及时排出孔内气
26、泡和维持药水浓度的均 一与稳定是非常关键的。主要办法有8:(1)机械方法,如提高搅拌幅度与 频率、斜挂、振动、上下跳动等;(2)物理方法,射流技术喷射镀液、加速循环 过滤等;(3)化学方法,改进镀液组成(如增加湿润、降低表面张力、细化氢气 气泡等)。还可以把一次完成化学镀铜时间分为“两次”完成化学镀铜等。此外, 采用水平设备可以增强药水在孔壁内的流动和交换,比垂直线有更好的处理效果8。刚挠印制板的孔壁由环氧树脂、玻璃布、聚酰亚胺树脂、改性环氧树脂粘结片和铜 组成,其中聚酰亚胺树脂表面光滑且不耐强碱,与镀层的结合力较低;另外,改性 环氧树脂挠性粘结片的热膨胀系数高于其它材料数倍,这对镀层的延展性
27、提出了更 高的要求 6 。选择合适的工艺流程和确定适合刚挠印制板的孔金属化工艺参数, 才能保证金属化孔电镀铜的厚度和孔壁铜镀层的均匀性及延展性。由于大部分采用的是强碱性的清洗/调整剂、离子钯溶液及镀铜液,且处理时间都在5 min以上。如果按照正常工艺流程完成孔化沉铜、图形电镀以及后续加工工序后,在显微剖切时常会产生孔壁开裂缺陷,并且几乎每个试样都出现聚酰亚胺突 出孔壁的现象。这是因为聚酰亚胺不耐强碱,如果刚挠印制板在强碱性的溶液中停 留的时间过长,聚酰亚胺会在强碱性溶液中发生溶胀,溶胀后的聚酰亚胺首先破坏 了孔化前处理形成的孔壁凹蚀效果,还有可能污染相邻的内层铜端面,降低内层铜 与孔壁铜的结合
28、力。解决该问题的途径就是适当缩短在强碱性溶液中的处理时间, 其他工位因为都不是强碱性溶液,因此保持正常工艺参数和流程。为了消除金属化孔缺陷,除了选用性能更好的化学药水外,还必须从PCB设计、钻孔、去钻污、孔金属化等各个环节加强控制,从源头上减少缺陷发生的概率。【相关文献】1 王恒义.PCB产业发展对化学镀,镀的要求J. 2010中国电子制造技术论坛论文集,2010:1-16.2 遇世友等. 以石墨为导电基质的黑孔化新技术 J .印制电路信息, 2012(7):40-43.3 杨维生. 高厚径比,高可靠性背板孔处理及金属化 J . 电子电路与贴装,2003(5):1-8.4 杨耀果. 浅谈孔破成
29、因及解决之道 J . 印制电路信息, 2012(12):33-40.5 杨波等.PCB孑L壁分离的影响因素分析及改善措施J.印制电路信息,2011 ( 12 ): 50-51,62. 6 石磊,郭晓宇. 刚挠印制板镀覆孔孔壁开裂原因分析 J . 电子工艺技术, 2011,32(1):31-35.7 程骄等.PCB制程中金属化孔镀层空洞的成因及改善J.印制电路信息,2013 (8):21-23.8林金堵,吴梅珠. PCB 镀通孔发生空洞的根本原因和对策 J . 印制电路信息,2010(4):31-36. 9 程静,汪浩,杨琼等. 除钻污机理,缺陷类型及改良措施 J . 印制电路信息,2012(5):33-38.10 李小刚刚-挠印制板去钻污及凹蚀技术J.印制电路资讯,2006 (4): 62-64.11 刘君平. 化学镀铜槽液在生产中的操作控制与问题对策 J . 电子电路与贴装, 2004(3):7-10.12 冯裕彬. 小孔径印制电路板化学镀铜电镀铜的工艺控制 J . 电子电路与贴装, 2002(4):24-25.周仲承,工程师,长期从事PCB专用化学药水的研发和技术服务工作,研发的多项产品在PCB生 产厂家使用,在相关刊物发表论文多篇。
- 温馨提示:
1: 本站所有资源如无特殊说明,都需要本地电脑安装OFFICE2007和PDF阅读器。图纸软件为CAD,CAXA,PROE,UG,SolidWorks等.压缩文件请下载最新的WinRAR软件解压。
2: 本站的文档不包含任何第三方提供的附件图纸等,如果需要附件,请联系上传者。文件的所有权益归上传用户所有。
3.本站RAR压缩包中若带图纸,网页内容里面会有图纸预览,若没有图纸预览就没有图纸。
4. 未经权益所有人同意不得将文件中的内容挪作商业或盈利用途。
5. 装配图网仅提供信息存储空间,仅对用户上传内容的表现方式做保护处理,对用户上传分享的文档内容本身不做任何修改或编辑,并不能对任何下载内容负责。
6. 下载文件中如有侵权或不适当内容,请与我们联系,我们立即纠正。
7. 本站不保证下载资源的准确性、安全性和完整性, 同时也不承担用户因使用这些下载资源对自己和他人造成任何形式的伤害或损失。