外文翻译--矿井提升机绳索的失效分析
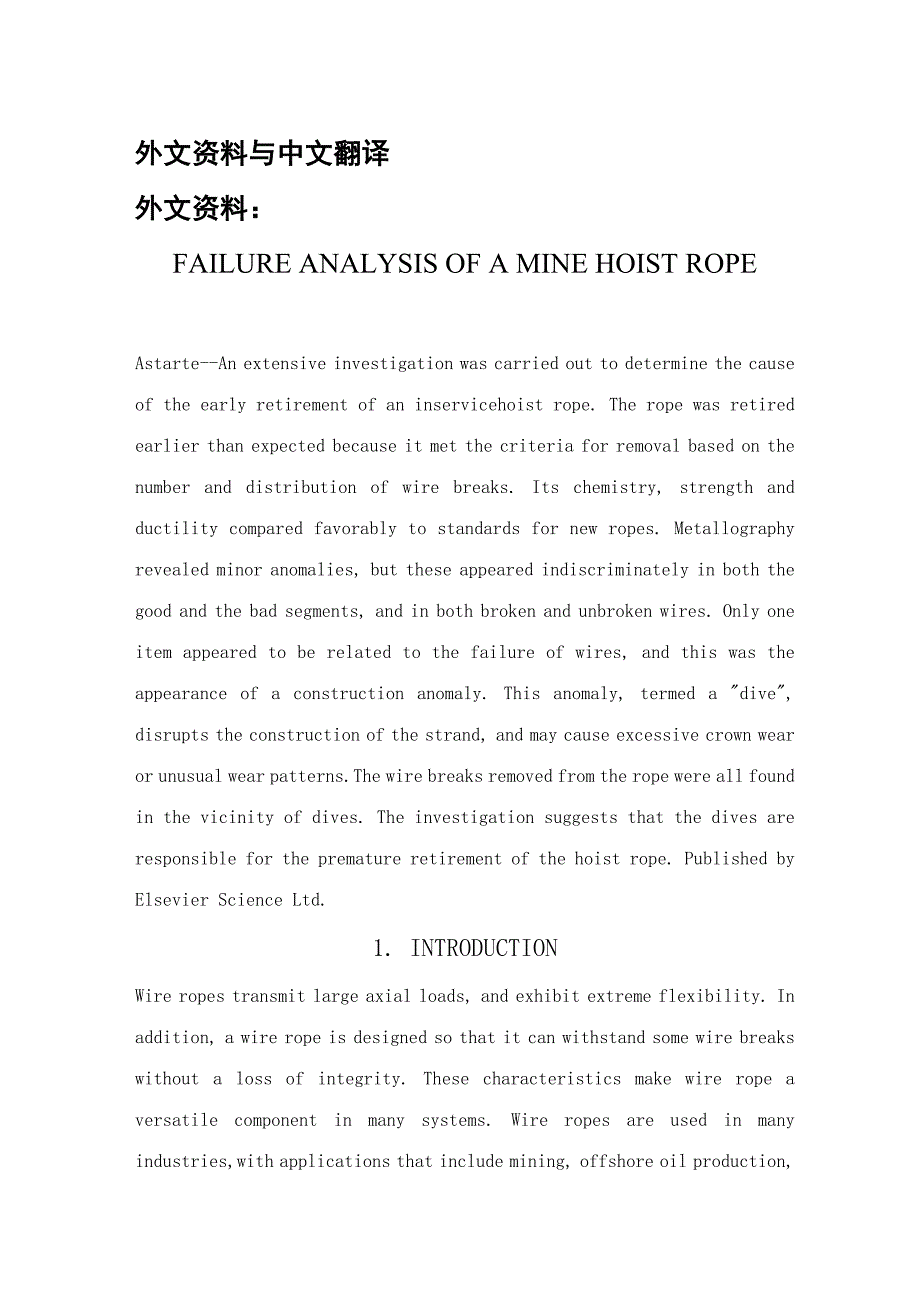


《外文翻译--矿井提升机绳索的失效分析》由会员分享,可在线阅读,更多相关《外文翻译--矿井提升机绳索的失效分析(48页珍藏版)》请在装配图网上搜索。
1、 外文资料与中文翻译 外文资料: FAILURE ANALYSIS OF A MINE HOIST ROPE Astarte--An extensive investigation was carried out to determine the cause of the early retirement of an inservicehoist rope. The rope was retired earlier than expected because it met the criteria for removal based on the number and distr
2、ibution of wire breaks. Its chemistry, strength and ductility compared favorably to standards for new ropes. Metallography revealed minor anomalies, but these appeared indiscriminately in both the good and the bad segments, and in both broken and unbroken wires. Only one item appeared to be related
3、to the failure of wires, and this was the appearance of a construction anomaly. This anomaly, termed a "dive", disrupts the construction of the strand, and may cause excessive crown wear or unusual wear patterns.The wire breaks removed from the rope were all found in the vicinity of dives. The inves
4、tigation suggests that the dives are responsible for the premature retirement of the hoist rope. Published by Elsevier Science Ltd. 1. INTRODUCTION Wire ropes transmit large axial loads, and exhibit extreme flexibility. In addition, a wire rope is designed so that it can withstand some wire breaks
5、 without a loss of integrity. These characteristics make wire rope a versatile component in many systems. Wire ropes are used in many industries,with applications that include mining, offshore oil production, and towing or mooring of ships. The Albany Research Center has been studying the degradatio
6、n mechanisms of wire ropes with the goal of more accurately predicting when the end of the useful life of a rope has been reached. In partnership with Henderson Mine, Albany Research Center personnel investigated a hoist rope that was retired after an unexpectedly short service life.After 9 months o
7、f service, the rope was retired because it exceeded the allowable number of broken wires per lay length [1]. Two rope segments were selected for investigation. One segment was at or near the location that required retirement because of broken wires (hereafter referred to as the bad segment), and the
8、 other segment came from the dead wrap on the drum (hereafter referred to as the good segment). The two segments were analyzed for differences in construction, steel composition and processing, and mechanical properties. Since it was felt that this rope was retired prematurely, the analysis was desi
9、gned to identify, and, if possible, quantify, any differences that might account for the wire breaks. Initial examination focussed on two broad questions: (1) what are the differences between the wires in the good and the bad rope segments, and (2) are there any physical or mechanical differences be
10、tween broken and unbroken wires in the bad segment? 2. BACKGROUND Wire ropes are composed of wires wound into bundles called "strands", which are then wound into the final rope (Fig. 1). The centermost wire of a strand, known as the king wire, provides support for the wires wrapped around it. One
11、or more layers may be wrapped around the king wire to form the strand. The last layer of wires forms the outside of the strand, and, hence, the wires are called outside wires. The number, size and arrangement of wires in a strand, and the number of strands in a rope, determine its construction. The
12、wires within the strand and the strand within the Fig. 1. The three basic components of a wire rope are the wire, the strand, and the core. The wire is a single, continuous length of metal that is drawn from a rod. The strand is a symmetrically arranged and helically wound assembly of wires. The
13、core is the central member of a wire rope, about which the strands are laid. It can be made of a fiber, a wire strand, or an independent wire rope. rope can be wound in either a right or a left helix. Wire rope terminology refers to a right regular lay or left lang lay. The terms right and left re
14、fer to the helix of the strand within the rope, while the lay refers to the relationship between the helix of the wires in the strand and the helix of the strand in the rope. A regular lay rope has the wires in the strand wound in the opposite direction to the strands in the rope, whereas a lang lay
15、 rope has the wires in the strand and the strands in the rope wound in the same direction. The rope core can be either another strand, a smaller rope [called the independent wire rope core (IWRC)], or a fiber. A non-rotating rope (also known as a rotationresistant rope) is a specialty rope that cons
16、ists of multiple layers of strands where different types of lays are alternated to reduce the natural rotation of the rope. The wear that occurs within ropes used in mine hoisting operations usually occurs as the result of one of three types of contact: (1) contact of the outer strands of the rope
17、with an external member, such as a sheave, drum, or layer of rope on the drum, a contact that is often called crown wear; (2) line contact between wires within a single strand or between strands; and (3) point contact between wires within a single strand or between strands. Actual wear of the wires
18、results from the combination of stresses that develop at these contact areas during tensioning of the rope, and during localized movement as the rope is bent, loaded and unloaded. Crown wear appears as a reduced cross section on the outside wires of the rope [Fig. 2(a)]. Wear between strands appears
19、 as nicks, which are easily visible as oblong wear scars [Fig. 2(b)]. A characteristic pattern, consisting of one or more nicks with a similar orientation and depth, forms on each wire at the multiple-wire contact site between strands. This characteristic pattern of nicks created by point and line c
20、ontacts between strands is known as "trellis" or interstrand nicking [Fig. 2(c)]. One evaluation of wear in a wire rope has revealed that crown wear results from abrasion [Fig. 3(a)], and interstrand nicking results from fretting [Fig. 3(b)], with differences in appearance due to the severity of the
21、 wear mechanism [2]. 3. EXPERIMENTAL PROCEDURE The two rope segments were approximately 10 ft in leng.The bad segment contained numerous breaks, and was in the vicinity of the location requiring retirement. The good segment contained no breaks, and came from the dead wrap on the drum (Fig. 4).
22、During service, the bad segment of the rope experienced cyclic bending stresses from both the head sheave and the drum, as well as varying tensile stress from the weight of the rope and the counterweight. The good segment of the rope experienced some tensile stress from the weight of the rope and th
23、e counterweight. All wires were disassembled and labeled by rope segment, layer (outside strands = layer 1 to core = layer 5), strand, and wire position, as shown in Fig. 5. Broken wires were only found in the bad rope segment. In this segment, all breaks were contained within two outside layer str
24、ands, and one strand from the third layer. These three strands also contained the construction anomaly referred to as a "dive". These were named dives because, while visually following outside wires around a strand, it was noticed that a wire would occasionally "dive" into the interior of the strand
25、,and could no longer be followed visually. A different wire would come out of the interior of the strand, and take the position of the outside wire that disappeared. It was later determined that, beyond the axial location of the dive, the king wire from before the dive functioned as an outside wire,
26、 and the outside wire from before the dive functioned as a king wire. One such dive is shown in Fig. 6. Additionally, one strand from the good rope segment contained a dive, but no associated wire break. Although only the strands that contained dives contained wire breaks, not all dives had a corres
27、ponding wire break, nor were all wire breaks found at a dive. During a dive, a king wire and an outside wire physically change position within the strand. This presented a difficulty in labeling the wires and performing statistical comparisons. For labeling purposes, king wires were initially iden
28、tified by strand position referenced to one end of the rope segment. However, many of the planned evaluations were based on groupings of nominally identical wires. Therefore, for analyses, both king and outside wires were determined solely by diameter. Implicit in these analyses is that the conclusi
29、ons pertain to a strand that does not contain dives. The chemistry of all groups of wires in the rope segments were examined. Since the alloying composition of a wire can have a large affect on the mechanical response, (1) the alloying composition of broken and unbroken wires in the bad segment we
30、re evaluated for significant differences, and (2)the overall alloying composition of each individual layer was evaluated. The alloying composition of the good segment was assumed to be identical to that of the bad segment: therefore, chemical analyses of the wires from the good segment were not perf
31、ormed. However, since king wires do not have the same diameter as the outside wires, there is no reason to expect that they are from the Fig. 3. (a) Abrasive wear is commonly seen as the principal mode of damage in wires that are exposed to external surfaces. (b) Fretting results from the relative
32、motion between wires, such as is seen at nicks. Fracture craters due to delamination are present. Some material has been extruded from the area of contact. same steel heat. Therefore, t,he chemistry of the king wires was evaluated separately from the outside wires. The following elements were deter
33、mined: carbon, sulfur, silicon, phosphorus, manganese, chromium and nickel. Carbon and sulfur were determined by gas analysis, and silicon, manganese, phosphorus and chromium by wet chemistry methods. In order to obtain a statistical representation of the alloying composition, multiple samples from
34、each layer were analyzed. The results are reported in Table 1. Torsion tests were performed according to the American Petroleum Institute (API) Specification for Wire Rope [3]. Table 2 lists the requirements for the minimum number of torsions (i.e. the number of twists to failure) to be attained by
35、 wires made out of electric furnace steel after fabrication into wire rope. In addition to the API requirements for minimum torsions, Table 2 also lists the average number of experimentally determined torsions for wires in the good segment and the bad segment, and for broken wires in the bad segment
36、 (XGOOD, XBAD, XBROKEN, respectively). A column labeled 0.3J(GOOD is included as a comparison to a practice by the Ontario Ministry of Labour. The Ontario Ministry of Labour tests ropes before they are put into service to determine initial reference values, and subsequently tests periodic cutoffs. T
37、hey recommend caution when the number of Fig. 4. Schematic of hoisting operation. The rope in question came from the counterweight of a double drumhoist. The segment requiring removal was at the location marked "bad" section. The comparison sample("good" segment) came from the dead wraps on the d
38、rum. torsions drops to 30% of the initial reference value, and recommend that ropes be retired when the number of torsions drops below 15% [4]. Tensile tests were performed according to the API Specification for Wire Rope [3]. Table 3 lists the requirements for the average minimum breaking strengt
39、h to be attained by wires made out of electric furnace steel after fabrication into wire rope. In addition to the API requirements for minimum tensile strength, Table 3 also lists the experimentally determined average breaking strength for wires in the good segment, the bad segment, and broken wires
40、 in the bad segment ()?GOOD, XBAD, "~BROKEN, respectively). Metallographic and fractographic investigations were carried out in order to identify the cause(s) of failure of individual wires. For the metallographic investigation, one outside and one king wire from each strand layer of both the good
41、and the bad segments were evaluated in the transverse direction at sites of general wear, crown wear, and nicks between adjacent strands. These samples Fig. 5. Construction ofretired hoist rope. Wires in the rope were examined as a function oflayer (outside=layer 1, core = layer 5) and strand pos
42、ition (wires 1~5 = outside wires, wire 7 = king wire). Strands in each layer were labeled in a clockwise relationship to strand 1, an arbitrarily chosen reference strand. For illustration purposes, the two strands from layer 1 that contained wire breaks (strands 2 and 13) are shown. Fig. 6. Appeara
43、nce of a dive. A dive is a location where an outside wire and a king wire switch positions in the strand structure. White arrows indicate positions where an outside wire moves into the interior of the strand to assume the function of a king wire. were evaluated for decarburization, cracks, ma
44、rtensite, and the appearance of the wear scar. In addition, wires involved with dives were also evaluated. 4. EXPERIMENTAL RESULTS AND DISCUSSION 4.1. Rope construction The construction anomalies were named dives, and are locations where an outside wire and a king wire switch position in the stra
45、nd structure. Along the strand axis, the interchange of the two wires will take place over a length of several centimeters, and results in a larger than normal strand diameter (Fig. 7). Unusual and unexpected wear and/or deformation will take place between the wires within the strand. In some cases,
46、 as also shown in Fig. 7, this is observed as deep nicks (gouges). In other cases, the result will be extensive flattening of the wire surface and/or excessive crown wear (Fig. 8), with the amount of crown wear increasing as the proximity to the dive increases. In addition to the wear and deformatio
47、n, the interchange of wires, especially of different diameters, will alter the load distribution in the strand. During disassembly, 12 dives were identified in three different strands in the bad segment. All wire breaks were found in these three different strands (Figs 9-11), and were often locate
48、d at or between dives. In contrast, only one dive was found in the good segment (Fig. 12), and there was no associated wire break. In wire rope design, king wires typically have a larger diameter than outside wires. Overall, the king wires (wire 7) had a diameter of approximately 2.95 mm, in compari
49、son with Fig. 7. Dive from layer 1, strand 2. The strand diameter at the location of the dive is larger than elsewhere, as is shown by the two white arrows. The gouge produced as a result of this expanded diameter is shown by the black arrow. Fig. 8. Dive from layer 1, strand 13. A total of f
50、our wire fractures are visible, and two are matching fractures. The location where the king wire switches position and becomes an outside wire is at the location marked "'dive." This wire shows extensive flattening and crown wear just prior to its fracture location. The two gray arrows point out dif
51、ferences in the severity of the crown wear. As the location of the dive is approached, the crown wear of the surrounding wires becomes more severe. Fig.9. Wire diameters and location of wire breaks for layer 1, strand 2, bad rope segment. The shaded portion of the wire has a significantly la
52、rger diameter. The bottom illustration shows the relationship of dives and wire breaks in the assembled strand. (Dimensions are in mm.) 2.82 mm for the outside wires. In attempting to group like wires/sizes, it was found that a continuous king wire could not be identified in strands 2 and 13 from l
53、ayer 1 as illustrated in Figs 9 and 10 . This, in addition to the difficulty unwinding strands containing dives, suggests that the anomaly was not created during service. Fig. 10. Wirc diameters and location of wire breaks for layer 1, strand 13, bad rope segment. The shaded portion of the wire h
54、as a significantly larger diameter. The bottom illustration shows the relationship of dives and wire breaks in the assembled strand. (Dimensions are in mm.) 4.2. Chemical analysis Wire ropes used in the United States are not required to meet alloying standards. However, the API does require that
55、 the wire be produced from: (1) acid or basic open-hearth, (2) basic oxygen, or (3) electric furnace steelmaking processes; and that the wire so produced meets certain mechanical property specifications, e.g. breaking strength and torsional requirements, dependent upon the steelmaking process used.
56、Breaking strength and torsional requirements are highly dependent on alloying composition, and API-acceptable results have been developed for each of the three different steelmaking processes. Therefore, the type of steelmaking process needs to be determined for later comparisons with API specificat
57、ions. The chemistries of the wires in Table 1 are typical of an electric furnace steel [5]. Residual alloying elements (manganese, chromium and nickel) and impurities (sulfur and phosphorus) are generally higher in electric furnace steel than in open-hearth or basic oxygen steel. In general, higher
58、 levels of alloying elements result in lower ductility and higher strength. This is reflected in the API specifications, where the electric furnace steel has the highest requirement for tensile strength and the lowest for torsion. The steel used in this rope was considered to be produced in an elect
59、ric furnace. This was later verified by the rope manufacturer. A multivariate analysis of the chemical analysis data was performed to determine if differences in chemical composition exist between the different layers of wires. The analysis revealed that there is a significant difference in the che
60、mistries between the first three layers and the two layers that comprise the independent wire rope core. The results can be summarized as follows: (1) Layers 1 3 contain wires with very similar composition, and are probably obtained from the same heat of steel. Furthermore, the outside wires from l
61、ayers I-3 were obtained from one heat of steel, and the king wires from the same layers were obtained from another heat. It should be noted that layer 2 appears to be produced from the same steel heats as layers 1 and 3, yet contains no wire breaks of either king or outside wires. (2) Layers 4 and
62、5 have significantly different composition from the first three layers, and are probably not obtained from the same heat as layers 1 3. (3) Layers 4 and 5 differ significantly from each other, and probably do not come from the same heat. Again, the king wires appear to be from a different heat than
63、 the outside wires. In all, it appears that there are six distinct heats of steel represented in this rope. Independent of the type of steelmaking process used, one of the primary questions to be addressed is whether the wire material itself is responsible for premature failure of the wires. As ca
64、n be seen in Table 1, the chemical analyses of broken and unbroken wires in the bad rope segment are very similar. A multivariate analysis of variance shows no significant difference between the chemistries,with the possible exception of the nickel content of the layer 1 king wires. Although the sta
65、tistical analysis identifies the nickel content as being significantly different, from a practical standpoint the difference is not great enough to affect the behavior of the material. It appears that the steel used for this wire rope came from six distinct heats from an electric furnace. All of th
66、e broken wires were found in layers 1 and 3, which would comprise only two of six distinct steelmaking heats identified. No significant difference was found between the broken and unbroken wires. It can, therefore, be concluded that it is highly unlikely that the overall chemistry of the wires was responsible for the wire breaks. 4.3. Torsion results For the rope segments examined, the number of torsions may reasonably be expected to be lower than those in the API specifications, due to fatigu
- 温馨提示:
1: 本站所有资源如无特殊说明,都需要本地电脑安装OFFICE2007和PDF阅读器。图纸软件为CAD,CAXA,PROE,UG,SolidWorks等.压缩文件请下载最新的WinRAR软件解压。
2: 本站的文档不包含任何第三方提供的附件图纸等,如果需要附件,请联系上传者。文件的所有权益归上传用户所有。
3.本站RAR压缩包中若带图纸,网页内容里面会有图纸预览,若没有图纸预览就没有图纸。
4. 未经权益所有人同意不得将文件中的内容挪作商业或盈利用途。
5. 装配图网仅提供信息存储空间,仅对用户上传内容的表现方式做保护处理,对用户上传分享的文档内容本身不做任何修改或编辑,并不能对任何下载内容负责。
6. 下载文件中如有侵权或不适当内容,请与我们联系,我们立即纠正。
7. 本站不保证下载资源的准确性、安全性和完整性, 同时也不承担用户因使用这些下载资源对自己和他人造成任何形式的伤害或损失。