现代切削加工技术试卷
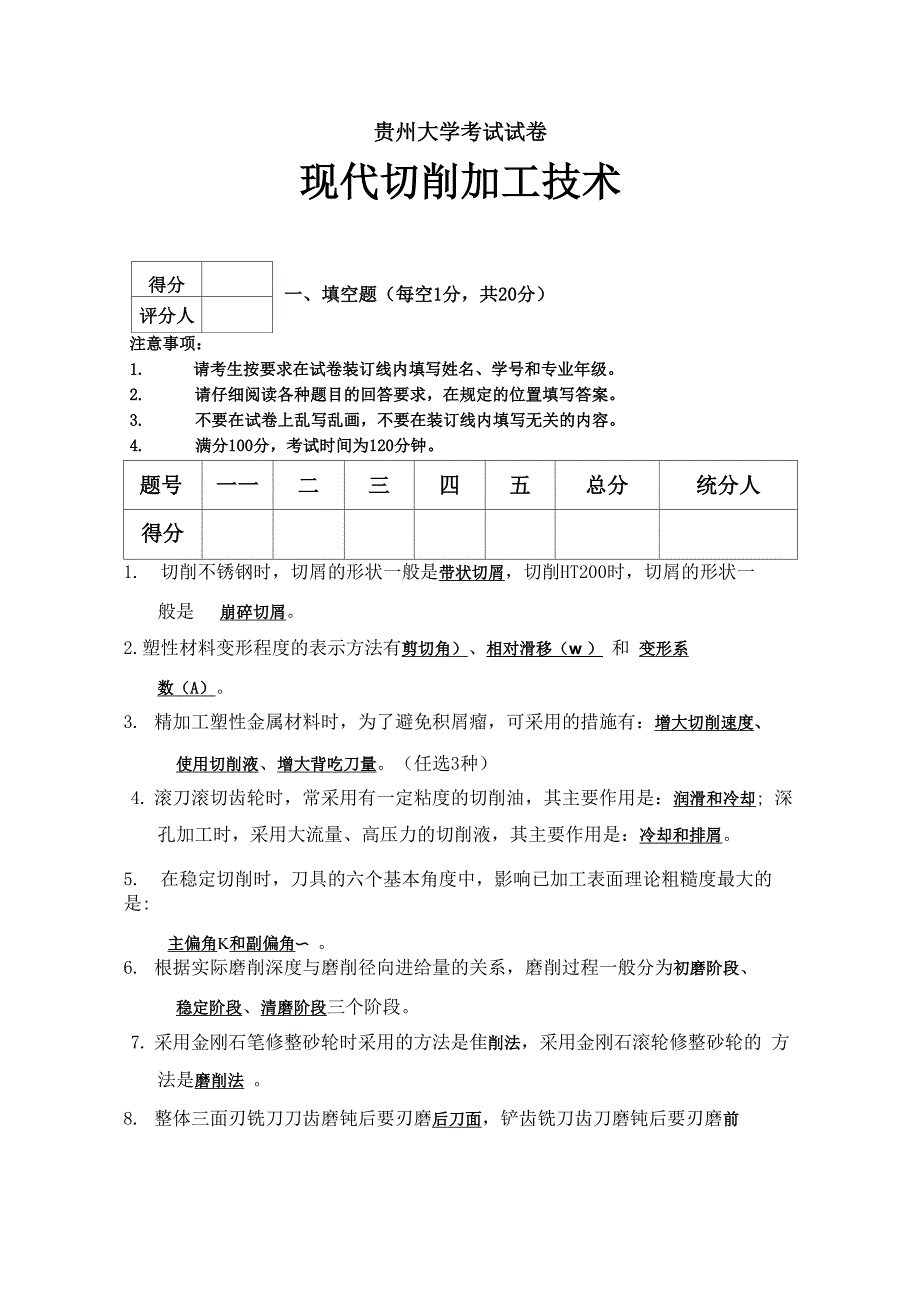


《现代切削加工技术试卷》由会员分享,可在线阅读,更多相关《现代切削加工技术试卷(13页珍藏版)》请在装配图网上搜索。
1、贵州大学考试试卷现代切削加工技术得分评分人一、填空题(每空1分,共20分)注意事项:1. 请考生按要求在试卷装订线内填写姓名、学号和专业年级。2. 请仔细阅读各种题目的回答要求,在规定的位置填写答案。3. 不要在试卷上乱写乱画,不要在装订线内填写无关的内容。4. 满分100分,考试时间为120分钟。题号一一二三四五总分统分人得分1. 切削不锈钢时,切屑的形状一般是带状切屑,切削HT200时,切屑的形状一般是崩碎切屑。2.塑性材料变形程度的表示方法有剪切角)、相对滑移(w ) 和 变形系数(A)。3. 精加工塑性金属材料时,为了避免积屑瘤,可采用的措施有:增大切削速度、使用切削液、增大背吃刀量。
2、(任选3种)4. 滚刀滚切齿轮时,常采用有一定粘度的切削油,其主要作用是:润滑和冷却; 深孔加工时,采用大流量、高压力的切削液,其主要作用是:冷却和排屑。5. 在稳定切削时,刀具的六个基本角度中,影响已加工表面理论粗糙度最大的是:主偏角K和副偏角 。6. 根据实际磨削深度与磨削径向进给量的关系,磨削过程一般分为初磨阶段、稳定阶段、清磨阶段三个阶段。7. 采用金刚石笔修整砂轮时采用的方法是隹削法,采用金刚石滚轮修整砂轮的 方法是磨削法 。8. 整体三面刃铣刀刀齿磨钝后要刃磨后刀面,铲齿铣刀齿刀磨钝后要刃磨前刀面,才能保持其原来要求的廓形精度。(前刀面 后刀面前、后刀面)9. 端铳有对称铳、不对称
3、逆铳和不对称顺铳三种方式,铳削不锈钢和耐热合金时, 为了减少硬质合金刀具的脱落,提高切削速度,宜采用不对称顺铳。10. 28AS0JT5080-70表示TMG28工具系统的 主柄 模块,符合ISO标 准,规格为50号锥柄7: 24。得分评分人二、单项选择题(每小题2分,共20分)1. 关于金属的切削变形,下列说法正确的是(A )A. 金属切削过程是金属切削层在刀具前刀面的推挤作用下,发生以剪切滑移为 主的塑性变形而形成切屑的过程;B. 金属切削过程是金属切削层在刀具后刀面的推挤作用下,发生以剪切滑移为 主的塑性变形而形成切屑的过程;C. 车削45号钢棒时,作用在车刀前刀面上的摩擦主要以外摩擦为
4、主,该外摩擦 系数随工件的硬度、切削厚度、切削速度以及刀具的前角变化而变化;D. 根据切削第一定律(Lee and Shaffer公式),前角增大时,剪切角减小,切 屑变形增大。2. 关于切削力,下列说法正确的是( B )A. 随着切削速度的增大,切削力增大;B. 随着进给量和背吃刀量的增大,切削力增大;C. 随着刀具前角的增大,切削力先减小,后增大;D. 随着主偏角的增大,主切削力F增大。c3. 关于切削温度,下列说法不正确的是(C )A. 切削温度的测量有自然热电偶、人工热电偶等方法;B. 在常规的切削速度范围内,切削速度越大,切削温度越高;C. 加工过程中,产生的切削热越多,切削温度越高
5、;D. 工件材料或刀具材料的导热性能越好,切削温度越低。4. 关于工件材料的切削加工性,下列说法正确的是(D )A. 断屑性能越好,工件材料的切削加工性越差。B. 相对切削加工性Kv越大,工件材料的切削加工性越差;C. 工件材料的切削加工性只取决于材料本身,与其他因素无关;D. 铸铁的化学成分中,凡是能促进石墨化的元素,均能提高切削加工性;5. 在砂轮直径、径向进给量:工件直径dw相同的前提下,外圆磨削、平面磨srw削、内圆磨削三者接触时间的关系是(A)A. 内圆磨削t 平面磨削t 外圆磨削tc内C平C外B. 外圆磨削t 平面磨削t 内圆磨削tC外C平c内C. 外圆磨削t =平面磨削t =外圆
6、磨削tC外C平c内D. 内圆磨削t 外圆磨削t =平面磨削tC内C外C平6. 关于镗刀的特点及应用,下列说法正确的是(C )A. 双刃定装镗刀不能消除由径向切削力对镗杆的作用而造成的加工误差;B. 加工直径小的孔可以选用机夹可转位镗刀;C. 双刃浮动镗刀不能校正孔的直线度误差和位置偏差;D. 双刃浮动镗刀能校正孔的直线度误差和位置偏差。7. 关于麻花钻的的修磨措施,下列说法不合理的是(B )A. 麻花钻的主副切削刃交界处处磨损严重,可将该处修磨出双重顶角,直径较 大时可修磨出三重顶角;B. 钻削强度和硬度很高的塑性材料或脆性材料时,为了减小切削变形,可在前 刀面上磨出卷屑槽,以增大前角;C.
7、钻削塑性材料时为了便于排屑,可以在主后刀面或前刀面上磨出分屑槽。D. 为了有利于钻头的定心和减小轴向力,可将横刃修短。8. 关于可转位机夹车刀,下列说法正确的是(C )A. 刀片磨损后,需要重磨;B. 刀片厚度的选择取决于切削温度的高低。C. 同样大小的刀片,切削刃数越多,刀片的寿命越长;D. 刀片在刀槽中的定位精度取决于刀片的精度,与刀槽精度无关。9. 关于圆柱铣刀和面铣刀,下列说法正确的是(B )A. 圆柱铳刀的螺旋角小于刃倾角;B. 圆柱铳刀主偏角等于90。C. 粗加工时选择细齿面铳刀;D. 面铳刀的每齿的基面均相同。10下列哪种刀具材料不适合高速切削( C )A.聚晶金刚石B.立方氮化
8、硼C.高速钢 D.金属陶瓷得分评分人三、简答题(共4题,共25分)1. 什么是准干式切削技术?实施MQL技术的关键技术是什么?(6分)准干式切削的概念:准干式切削是一个介于纯干式切削和湿式切削之间的最小润滑技术(MQL),原理是将压缩空气与少量的切削液混合气化后,再喷射到工件的加工部位,使刀一一 屑接触区得到冷却和润滑。(4分) 实施MQL的关键技术是:(1)如何保证切削液可靠进入切削区进行充分冷却和润滑,解决办法 是采用外喷法和内喷法;(2)如何确定所需的切削液用量。1,刃-0 Kz2. 为什么采用阿基米德螺线作为成形铳刀的齿背曲线? (6分)在成形铳刀的铲齿过程中,阿基米德螺线上任一点的后
9、角为:tan a加=灵Kz磨后新齿顶后的后角:tan a =,随着成形铳刀的刃磨,0增大,则a加随之增大。fM 2 兀RfM但是计算表明,变化很小,可忽略不计。所以阿基米德螺线可以保证重磨后,后角基本不变。3. 超声波振动切削的特点有哪些? (6分)(1) 周期性地改变了实际切削速度的大小和方向。(2分)振动切削时实际切削速度的大小和方向随时间变化而变化,在一个振动周期里,前半周期,实际切削速度大于工件速度,二者方向相同;后半周期,实际切削速度小于工件速度,二者方 向相反。(2) 周期性地改变刀具工作角度(2分) 根据切削用量对刀具工作角度的影响可知,当切削用量发生变化时,刀具的工作角度也随之
10、变化。振动切削过程中,实际切削速度成周期性变化,因此,刀具的工作角度也随之周期性 的变化。(3)切削力的波形影响切削过程,改变已加工表面的形成过程,提高表面质量和加工精度(2分)由于脉冲切削时间极短,切削热也以脉冲的形式出现,切削温度低,提高了刀具寿命,减 少了加工硬化和残余应力的产生;脉冲切削力使切削利用了刀具和工件的振动过渡过过程,由 于脉冲时间小于刀具与工件振动的过渡时间,刀具切削工件时强迫工件振动,而工件还未来得 及振动,刀具就离开了工件,这就是振动切削能减小振动,提高加工精度和减小表面粗糙度的 原因。4. 图为镗刀压电晶体补偿装置,简述其工作原理。(7分)1-圆柱弹簧;2-楔块;3-
11、压电晶体管;4-绝缘套;5-弹性胀套;6-压板;2.7镗 刀;8-套筒;9-碟形弹簧;10、11-螺钉;12-插头;13-绝缘螺塞;14-弹簧触片; 15-镗杆。图中镗刀7用螺钉10固定在套筒8上面,螺钉11用于调整镗刀位置。通交流电或脉冲 直流电时,压电晶体管3在每个交流电的正半波(脉冲直流电的每一个脉冲)时伸长,克服弹 性胀套5与压板6之间的碟形弹簧9的弹力,将固定镗刀的套筒8顶出,使镗刀获得径向微量 位移。在每个交流电的负半波或直流电的脉冲之间,3缩短,2在1的作用下顶紧3,故镗刀不 会退回,完成补偿。得分评分人四、论述题(本题15分)缓进给磨削技术在历史上曾经停滞不前,最主要的原因是缓
12、进给磨削的磨削 温度不高,但却容易发生难以控制的严重烧伤的矛盾现象。英国Bristol大学利用 沸腾换热的理论,提出了控制缓进给磨削烧伤的措施。试根据沸腾换热曲线解释上述矛盾现象,并指出控制缓进给磨削烧伤的措施。1. 如图,根据沸腾换热理论,随热流密度的增加镍丝表面可以依次出现三种不同的换热 状态:(1) 0 q W q,对流换热阶段,相当于曲线0a段。a(2) q q q ,泡核沸腾阶段,相当于曲线ab段。alim(3) q三q,成膜沸腾阶段,相当于曲线的bed段。lim在ae段,温度虽然不高(不超过120C),但是在这个阶段,缓进给磨削时弧区磨削液 因发生成膜沸腾,热流密度急剧上升导致工件
13、突发烧伤,而且很严重。(6分)2. 根据上述分析,要控制缓进给磨削时发生的突发性烧伤,关键在于控制热流密度,而 控制热流密度的主要手段,是要能使砂轮在缓进给磨削过程中始终保持相同的锋利状态。(3分)3. 控制缓进给磨削烧伤的措施有:(1) 连续修整所谓连续修整系指边磨削边将砂轮再成形和修锐的方法。采用连续修整方法时,金刚石修 整滚轮始终与砂轮接触。连续修整具有磨削效率提高;最长磨削长度不再取决于砂轮的磨损, 而取决于磨床可利用的磨削长度;比磨削能低,磨削力及磨削热低,磨削过程是稳定的特点。(2) 强化换热为减少表面烧伤,在进行缓进给磨削时应采用强化换热,这包括两方面的内容:1) 冷却液以一定压
14、力和流量送入磨削区起到强冷却作用,将砂轮磨削长度上所产生的热 能迅速带走而不传入工件,同时冲掉附着在砂轮表面上的一部分丝状磨屑。2) 冷却液还用来冲洗砂轮表面,磨削后的砂轮表面上附着的切屑在磨削区被冷却液带走 一部分。(3) 采用大气孔砂轮在缓进给磨削中常采用大气孔砂轮,由于砂轮中有许多大气孔的存在,大气孔周边有效磨 刃容屑槽的扩大,致使它的有效磨刃比普通砂轮的有效磨刃更为锋锐,在磨削工件时,能切下 较厚的磨屑。在同等试验条件下,大气孔砂轮磨削和普通砂轮在磨削区接触弧长相等,在横向 断续进给相同情况下,大气孔砂轮与工件的接触面积比普通砂轮小,导致砂轮与工件总摩擦力较小,由于上述两个原因,大气孔
15、砂轮磨削比普通砂轮磨削力小,消耗功率也小,磨削效率较高。得分评分人五、综合应用题(本题20分)用车刀车削一长度为300mm,直径为30mm的轴类零件,零件毛坯的直径为Q 41mm,要求加工到35 +0.05,分为粗、精两次加工。已知:-0.05工件材料:刀具材料:刀具角度:45 钢调质(b 二 0.637GPa)b(a) YT30; (b)陶瓷;(c) YT5; (d) PCD 王偏角:(a) k 30 ; (b) k 90rr 前角:(a) y 10 ; (b) y 20oo 刃倾角:(a)九0。; (b)九5。ss切削用量:(a) a = 2.4mm, f = 0.5 mm/r, v 二
16、60 m/minp(b) a = 0.6mm, f = 0.1 mm/r, v 二 100m/minp回答以下问题:1. 粗车和精车时刀具材料应选(2. 粗车和精车时切削用量应选(3. 粗车和精车时车刀合理前角应选(和( ),合理主偏角应选(4. 上述主偏角选择的依据是什么。)和()。(填序号)(2分)和()。(填序号)(2分)和( ),合理刃倾角应选()和()。(填序号)(6分)(2分)5-查表计算粗加工时的切削力Fc、Ff。(8分)回答以下问题:1. 粗车和精车时刀具材料应选(c )和(a )。(填序号)(2分)2. 粗车和精车时切削用量应选(a )和(b )。(填序号)3. 粗车和精车时
17、车刀合理前角应选(a )和(b ),合理刃倾角应选(a )和 合理主偏角应选(b )和(b )(填序号)4. 上述主偏角选择的依据是什么。答:零件是细长件,刚度比较差,径向不能受力,所以选择较大的主偏角。5. 查表计算粗加工时的切削力F、Ff解:切削力经验公式的选择:F =9.81C - a Xf - fyc (60v )fc K cF p ccFC acF =9.81C a xFf fyf 60v )f KfFf fcFf査表得:n = - 0.15,FcC =270, x =1O y =0.75,FFFcccK =K K K KFcmFK rFJ入SFc=(b )作 x 0.89 x 1.
18、0 x 1.0 =(0.637亦捫 X O.89 X 1.0 X 1.0 = O.89C =294, x =1.0, y =0.5, n = 0.4,FfFfFfFfK =K K K KFfmFK rFU九SF=(丄i)Ff x 1.17 x 1.0 x 1.0 = (0)1.0 x 1.17 x 1.0 x 1.0 = 1.17 0.637 f0.637将上述系数及指数代入切削力经验公式得:F =9.81C a XfcF =981C=9.81 x 270 xFf2165(N)f60(2分)(b ),(6分)(2分)(1分)(1分)(2分)(2分)(1分)=1113(N)=9.81 X294X2-410 Xom X(60X6?-0.4 X 1.17
- 温馨提示:
1: 本站所有资源如无特殊说明,都需要本地电脑安装OFFICE2007和PDF阅读器。图纸软件为CAD,CAXA,PROE,UG,SolidWorks等.压缩文件请下载最新的WinRAR软件解压。
2: 本站的文档不包含任何第三方提供的附件图纸等,如果需要附件,请联系上传者。文件的所有权益归上传用户所有。
3.本站RAR压缩包中若带图纸,网页内容里面会有图纸预览,若没有图纸预览就没有图纸。
4. 未经权益所有人同意不得将文件中的内容挪作商业或盈利用途。
5. 装配图网仅提供信息存储空间,仅对用户上传内容的表现方式做保护处理,对用户上传分享的文档内容本身不做任何修改或编辑,并不能对任何下载内容负责。
6. 下载文件中如有侵权或不适当内容,请与我们联系,我们立即纠正。
7. 本站不保证下载资源的准确性、安全性和完整性, 同时也不承担用户因使用这些下载资源对自己和他人造成任何形式的伤害或损失。