挡盖模具设计说明书大学毕设论文
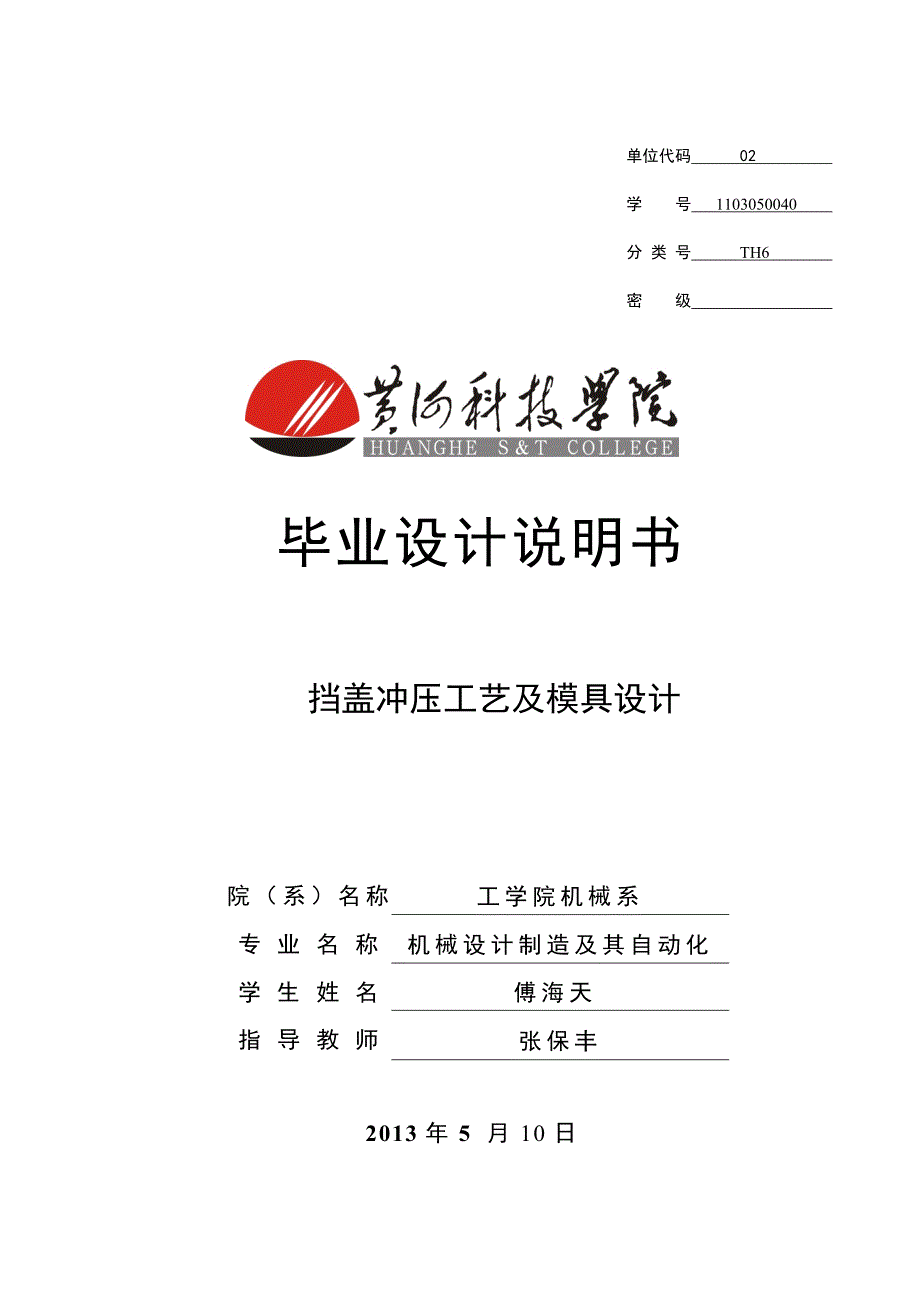


《挡盖模具设计说明书大学毕设论文》由会员分享,可在线阅读,更多相关《挡盖模具设计说明书大学毕设论文(35页珍藏版)》请在装配图网上搜索。
1、单位代码 02 学 号 1103050040 分 类 号 TH6 密 级 毕业设计说明书挡盖冲压工艺及模具设计 院(系)名称工学院机械系 专业名称机械设计制造及其自动化 学生姓名 傅海天 指导教师张保丰 2013年5 月10日黄河科技学院本科毕业设计(论文)任务书 工 学院 机械 系 机械设计制造及其自动化 专业 2011 级 专升本 班学号 1103050040 学生 傅海天 指导教师 张保丰 毕业设计(论文)题目 挡盖冲压工艺及模具设计 毕业设计(论文)工作内容与基本要求(目标、任务、途径、方法,应掌握的原始资料(数据)、参考资料(文献)以及设计技术要求、注意事项等)(纸张不够可加页)工作
2、内容:通过对挡盖零件进行冷冲压工艺分析,设计出相应的冲压模具。 设计要求: 1)查阅相关资料,完成文献综述; 2)结合设计内容,完成外文文献翻译; 3)对于支撑板零件,进行冲压成形工艺分析,编制出三种以上的成形工艺路线,进行冲压工艺方案论证。对其中部分关键工序设计出相应的成形模具,包括总装配图、主要的零件图。 4)按照毕业设计要求撰写设计说明书; 5)设计过程中,强化综合能力的培养,包括:通过各种途径查找相关参考资料的能力;熟练运用设计手册、参考文献等的能力;运用外文资料的能力;分析问题、解决问题的能力;熟练运用计算机进行辅助设计和编辑电子文档的能力,等等。 主要参考资料: 1李奇涵主编. 冲
3、压成形工艺与模具设计. 科学技术出版社,2007. 2汤酞则主编. 冷冲模课程设计与毕业设计指导.湖南大学出版社,2008. 3肖祥芷等.中国模具设计大典第3卷.江西科学技术出版社,2003. 4罗益旋主编.最新冲压新工艺新技术机模具设计实用手册.银声音像出版社,2004. 时间进度安排: 第1周:对课题进行调研、完成开题报告; 第2-3周:完成文献综述与专业相关的文献翻译; 第4-10周:完成工艺和结构分析、工艺和结构设计计算、装配图、零件图; 第11周:完成设计说明书的编制; 第12周:修改论文与图纸,准备答辩; 第13周:答辩。 毕业设计(论文)时间: 2013 年 2 月 25日至 2
4、013 年 5月 24 日计 划 答 辩 时 间: 2013 年 5 月 25日工作任务与工作量要求:原则上查阅文献资料不少于12篇,其中外文资料不少于2篇;文献综述不少于3000字;文献翻译不少于3000字;设计说明书不少于8000字(同时提交有关图纸和附件),毕业设计(论文)撰写规范及有关要求,请查阅黄河科技学院本科毕业设计(论文)指导手册。 挡盖零件图零件材料:45,退火态;料厚2mm;精度:IT13;大批量生产,未注圆角R2mm;专业(教研室)审批意见:审批人(签字):IV 黄河科技学院毕业设计说明书 第 页 挡盖冲压工艺及模具设计摘 要本次设计了一套落料、拉深、冲孔的模具。经过查阅资
5、料,首先要对零件进行工艺分析,经过工艺分析和对比,采用落料、拉深冲孔的工艺进行模具设计。通过冲裁力、顶件力、卸料力等计算,确定压力机的型号。再分析对冲压件加工的模具适用类型选择所需设计的模具。得出将设计的模具类型后将模具的各工作零部件设计过程表达出来。在文档中第一部分,主要叙述了冲压模具的发展状况,说明了冲压模具的重要性与本次设计的意义,接着是对冲压件的工艺分析,完成了工艺方案的确定。第二部分,对零件排样图的设计,完成了材料利用率的计算。再进行冲裁工艺力的计算和冲裁模工作部分的设计计算,对选择冲压设备提供依据。最后对主要零部件的设计和标准件的选择,为本次设计模具的绘制和模具的成形提供依据,以及
6、为装配图各尺寸提供依据。通过前面的设计方案画出模具各零件图和装配图。本次设计阐述了对冷冲压模具的结构设计及工作过程。本模具性能可靠,运行平稳,提高了产品质量和生产效率,降低劳动强度和生产成本。关键词:落料,冲孔,拉伸,模具间隙,模具设计The Retaining Rover Stamping Process and Die Design Author : Fu Haitian Tutor : Zhang BaofengAbstract The design of the die set of blanking, drawing, punching. Through access to info
7、rmation, the first part to process analysis, through process analysis and comparison, the mold design of blanking, drawing and punching process. Punching through, the top pieces, such as the discharge of calculation, determine the type of press. Further analysis of the stamping process of the mold u
8、sed to select the desired type design. The design of the mold type after the working parts mold design process expression.In the first part of the document, mainly describes the development of stamping die, stamping die illustrates the importance and significance of this design, then stamping proces
9、s is analyzed to determine the completion of the process plan. The second part, the part layout diagram design, complete the calculation of material utilization. Then the blanking force calculation and design calculation of blanking die working parts, provide the basis for the selection of stamping
10、equipment. Finally the design and standards on the main parts selection, provide the basis for the design of forming die drawing and mould, and provide the basis for the assembly of all sizes. The design drawing mold parts drawing and assembly drawing.The design describes the structure design and wo
11、rking process of the cold stamping die. The mold reliable, stable operation, improve the product quality and production efficiency, reduce labor intensity and production cost.Key words: Blanking, Punching, Stretching, Die clearance, Die design目 录1绪 论11.1模具工业在国民经济中的地位11.2模具的分类21.3我国模具工业的现状32 设计原始数据53
12、零件及冲压工艺性分析63.1 结构与尺寸63.2 精度63.3 材料63.4 批量64 确定冲压工艺方案74.1 落料工艺74.2 拉深工艺74.3 冲孔工艺74.4组合方案及比较75 主要工艺参数计算85.1毛坯展开尺寸计算85.2 确定排样方案和计算材料利用率85.3确定板料规格96 各工序工艺、冲压力及零部件的设计计算106.1 落料工艺、冲压力及零部件的设计计算106.1.1 落料工艺计算106.1.2 落料冲压力的计算116.1.3 落料模主要零部件设计计算116.2 拉深工艺计算及零部件设计176.2.1 拉深工艺计算176.2.2 拉深工艺方案的确定176.2.3 拉深力及工作部
13、分尺寸、零部件设计计算186.3冲孔工艺及零件的设计206.3.1冲裁力的计算206.3.3冲孔凸模、凹模尺寸计算216.3.4 凹模外形尺寸的确定216.4工作零件间隙的确定226.5模具压力中心的确定236.6定位零件237装 配 图24总 结27参 考 文 献2828 黄河科技学院毕业设计说明书 第 页 1绪 论模具是工业生产的重要工艺装备。由于用模具加工成形零部件,具有生产高效、质量好、节约原材料和能源、成本低等一系列优点,已成为当代工业生产的重要手段和工艺发展方向。模具制造是一个生产周期要求紧迫,技术手段要求较高的复杂生产过程。总之,模具具有结构复杂、型面复杂、精度要求高、使用的材料
14、硬度高、制造周期短等特点。应用数控加工进行模具的制造可以大幅提高加工精度,减少人工操作,提高加工效率,缩短模具制造周期。同时,模具的数控加工具有一定典型性,并比普通产品的数控加工有更高的要求。在模具的加工中,各种数控加工均有用到,应用最多的是数控铣及加工中心,数控线切割加工与数控电火花加工在模具数控加工中的应用也非常普遍,线切割主要应用在各种直壁的模具加工,如冲压加工中的凹凸模,注塑模中的镶块、滑块,电火花加 工用的电极等。对于硬度很高的模具零件,采用机加工办法无法加工,大多采用电火花加工,另外对于模具型腔的尖角、深腔部位、窄槽等也使用电火花加工。我国模具工业的现状及发展趋势:模具是制造业的重
15、要工艺基础,在我国,模具制造属于专用设备制造业。中国虽然很早就开始制造模具和使用模具,但长期未形成产业。直到20世纪80年代后期,中国模具工业才驶入发展的快车道。近年,不仅国有模具企业有了很大发展,三资企业、乡镇(个体)模具企业的发展也相当迅速 。 近年,模具行业结构调整和体制改革步伐加大,主要表现在,大型、精密、复杂、长寿命、中高档模具及模具标准件发展速度高于一般模具产品;塑料模和压铸模比例增大;专业模具厂数量及其生产能力增加;“三资”及私营企业发展迅速;股份制改造步伐加快等。从地区分布来看,以珠江三角洲长江三角洲为中心的东南沿海地区发展快于中西部地区,南方的发展快于北方。目前发展最快、模具
16、生产最为集中的省份是广东和浙江,江苏、上海、安徽和山东等地近几年也有较大发展。1.1模具工业在国民经济中的地位模具是制造业的一种基本工艺装备,它的作用是控制和限制材料(固态或液态)的流动,使之形成所需要的形体。用模具制造零件以其效率高,产品质量好,材料消耗低,生产成本低而广泛应用于制造业中。模具工业是国民经济的基础工业,是国际上公认的关键工业。模具生产技术水平的高低是衡量一个国家产品制造水平高低的重要标志,它在很大程度上决定着产品的质量,效益和新产品的开发能力。振兴和发展我国的模具工业,正日益受到人们的关注。早在1989年3月中国政府颁布的关于当前产业政策要点的决定中,将模具列为机械工业技术改
17、造序列的第一位。模具工业既是高新技术产业的一个组成部分,又是高新技术产业化的重要领域。模具在机械,电子,轻工,汽车,纺织,航空,航天等工业领域里,日益成为使用最广泛的主要工艺装备,它承担了这些工业领域中6090的产品的零件,组件和部件的生产加工。模具制造的重要性主要体现在市场的需求上,仅以汽车,摩托车行业的模具市场为例。汽车,摩托车行业是模具最大的市场,在工业发达的国家,这一市场占整个模具市场一半左右。汽车工业是我国国民经济五大支柱产业之一,汽车工业重点是发展零部件,经济型轿车和重型汽车,汽车模具作为发展重点,已在汽车工业产业政策中得到了明确。汽车基本车型不断增加,2005年将达到170种。一
18、个型号的汽车所需模具达几千副,价值上亿元。为了适应市场的需求,汽车将不断换型,汽车换型时约有80的模具需要更换。中国摩托车产量位居世界第一,据统计,中国摩托车共有14种排量80多个车型,1000多个型号。单辆摩托车约有零件2000种,共计5000多个,其中一半以上需要模具生产。一个型号的摩托车生产需1000副模具,总价值为1000多万元。其他行业,如电子及通讯,家电,建筑等,也存在巨大的模具市场。目前世界模具市场供不应求,模具的主要出口国是美国,日本,法国,瑞士等国家。中国模具出口数量极少,但中国模具钳工技术水平高,劳动成本低,只要配备一些先进的数控制模设备,提高模具加工质量,缩短生产周期,沟
19、通外贸渠道,模具出口将会有很大发展。研究和发展模具技术,提高模具技术水平,对于促进国民经济的发展有着特别重要的意义。1.2模具的分类模具主要类型有:冲模,锻摸,塑料模,压铸模,粉末冶金模,玻璃模,橡胶模,陶瓷模等。除部分冲模以外的的上述各种模具都属于腔型模,因为他们一般都是依靠三维的模具形腔是材料成型。(1) 冲模:冲模是对金属板材进行冲压加工获得合格产品的工具。冲模占模具总数的50以上。按工艺性质的不同,冲模可分为落料模,冲孔模,切口模,切边模,弯曲模,卷边模,拉深模,校平模,翻孔模,翻边模,缩口模,压印模,胀形模。按组合工序不同,冲模分为单工序模,复合模,连续模。(2) 锻模:锻模是金属在
20、热态或冷态下进行体积成型是所用模具的总称。按锻压设备不同,锻模分为锤用锻模,螺旋压力机锻模,热模锻压力锻模,平锻机用锻模,水压机用锻模,高速锤用锻模,摆动碾压机用锻模,辊锻机用锻模,楔横轧机用锻模等。按工艺用途不同,锻模可分为预锻模具,挤压模具,精锻模具,等温模具,超塑性模具等。(3) 塑料模:塑料模是塑料成型的工艺装备。塑料模约占模具总数的35,而且有继续上升的趋势。塑料模主要包括压塑模,挤塑模,注射模,此外还有挤出成型模,泡沫塑料的发泡成型模,低发泡注射成型模,吹塑模等。(4) 压铸模:压铸模是压力铸造工艺装备,压力铸造是使液态金属在高温和高速下充填铸型,在高压下成型和结晶的一种特殊制造方
21、法。压铸模约占模具总数的6。(5) 粉末冶金模:粉末冶金模用于粉末成型,按成型工艺分类粉末冶金模有:压模,精整模,复压模,热压模,粉浆浇注模,松装烧结模等。模具所涉及的工艺繁多,包括机械设计制造,塑料,橡胶加工,金属材料,铸造(凝固理论),塑性加工,玻璃等诸多学科和行业,是一个多学科的综合,其复杂程度显而易见。1.3我国模具工业的现状自20世纪80年代以来,我国的经济逐渐起飞,也为模具产业的发展提供了巨大的动力。20世纪90年代以后,大陆的工业发展十分迅速,模具工业的总产值在1990年仅60亿元人民币,1994年增长到130亿元人民币,1999年已达到245亿元人民币,2000年增至26027
22、0亿元人民币。今后预计每年仍会以1015的速度快速增长。目前,我国17000多个模具生产厂点,从业人数五十多万。除了国有的专业模具厂外,其他所有制形式的模具厂家,包括集体企业,合资企业,独资企业和私营企业等,都得到了快速发展。其中,集体和私营的模具企业在广东和浙江等省发展得最为迅速。例如,浙江宁波和黄岩地区,从事模具制造的集体企业和私营企业多达数千家,成为我国国内知名的“模具之乡”和最具发展活力的地区之一。在广东,一些大集团公司和迅速崛起的乡镇企业,为了提高其产品的市场竞争能力,纷纷加入了对模具制造的投入。例如,科龙,美的,康佳和威力等知名集团都建立了自己的模具制造中心。中外合资和外商独资的模
23、具企业则多集中于沿海工业发达地区,现已有几千家。 在模具工业的总产值中,企业自产自用的约占三分之二,作为商品销售的约占三分之一。其中,冲压模具约占50(中国台湾:40),塑料模具约占33(中国台湾:48),压铸模具约占6(中国台湾:5),其他各类模具约占11(中国台湾:7)。中国台湾模具产业的成长,分为萌芽期(19611981),成长期(19811991),成熟期(19912001)三个阶段。萌芽期,工业产品生产设备与技术的不断改进。由于纺织,电子,电气,电机和机械业等产品外销表现畅旺,连带使得模具制造,维修业者和周边厂商(如热处理产业等)逐年增加。在此阶段的模具包括:一般民生用品模具,铸造用
24、模具,锻造用模具,木模,玻璃,陶瓷用模具,以及橡胶模具等。1981年1991年是台湾模具产业发展最为迅速且高度成长的时期。有鉴于模具产业对工业发展的重要性日益彰显,自1982年起,台湾地区就将模具产业纳入“策略性工业适用范围”,大力推动模具工业的发展,以配合相关工业产品的外销策略,全力发展整体经济。随着民生工业,机械五金业,汽机车及家电业发展,冲压模具与塑料模具,逐渐形成台湾模具工业两大主流。从1985年起,模具产业已在推行计算机辅助模具设计和制造等CAD/CAM技术,所以台湾模具业接触CAD/CAM/CAE/CAT技术的时间相当早。2 设计原始数据 零件材料:45,退火态;料厚t=2mm;精
25、度:IT13;大批量生产;冲压件零件图见图1.1。图1.1 零件图3零件及冲压工艺性分析3.1 结构与尺寸该挡盖零件形状简单,结构对称,拉伸深度为10直径为60且在拉深的平面上中心冲一直径20的圆孔。最后在四周存在R2的圆角。3.2 精度该零件无尺寸精度要求,也无其他特殊尺寸要求,可采取IT13IT14加工精度,利用普通冲裁方式可以达到零件图样的设计要求。3.3 材料45钢淬透性好,它具有较高的硬度,韧性,较好的耐腐性,热强性和冷变形性能。退回状态下的抗剪强度为600Mpa,可以进行冲裁加工。根据以上分析,该零件工艺性较好,适合冲裁加工。3.4 批量该零件属于大批量生产,在冲压加工下操作简便,
26、劳动强度低,生产效率高,成本低,适合冲裁。结论:该零件的工艺性较好,可以冷冲压加工。4 确定冲压工艺方案首先根据零件形状确定冲压工序类型和选择工序顺序。冲压该零件需要的基本工序有落料、拉深和冲圆孔。其中拉深和冲孔决定了零件的总体形状和尺寸,因此选择合理的拉深和冲孔方法直接关系到零件的精度和使用要求。4.1 落料工艺 落料的形状为直径100的圆,其结构对称,形状简单,而且对毛坯料的精度要求不是很高,变形程度小,材料的塑性较好,这就给落料工艺提供了有利条件。4.2 拉深工艺该方法为一次拉深成形,其优点是用一副模具成形,可以提高生产率,减少所需设备和操作人员。缺点是毛坯的整个面积几乎都参与激烈的拉深
27、变形,零件表面擦伤严重,零件形状与尺寸都不精确,拉深处起皱严重,所以在设计拉深模具的过程中要特别注意。4.3 冲孔工艺 本次冲孔是在拉深工艺之后进行的,对冲孔的位置和精度要求比较高。4.4组合方案及比较 根据冲压该零件需要的基本工序和拉深方法的选择,可以作出下列各种组合方案: (1)落料-冲孔-拉深,用单工序模生产。(2)拉深落料-冲孔,采用单工序模生产。(3)落料拉深冲孔,用单工序模生产。方案(1) 模具结构简单,制造周期短,成本低,操作简单,但冲孔后拉伸不能保证孔的位置精度,且冲孔后拉深容易使孔周围产生应力集中,发生变形难以满足零件形状和位置要求。方案(2) 落料后冲孔,冲孔模复杂,且产生
28、的应力集中使拉深时发生零件变形尺寸和形状不精确,操作难度较大,生产效率低。方案(3) 拉深后冲孔,可以保证孔的位置精度,且减少了拉深时的应力集中,保证了拉深时零件的完整性,使得拉深时零件精度高。上所述,该零件使用时,应减少其应力集中,同时为了保证其精度,减少大批量生产时零件的修整时间,应采用方案(3)进行生产。5 主要工艺参数计算5.1毛坯展开尺寸计算毛坯零件的形状如图5.1 图5.1 零件毛坯图所有尺寸均视为中性层尺寸,根据拉深件计算表面积相等简化计算得坯料直径D= =111.35mm,取112mm。5.2 确定排样方案和计算材料利用率排样中相邻两制件之间的余料或制件与条料边缘间的余料称为搭
29、边。其作用是补偿定位误差和保持有一定的强度和刚度,防止由于条料的宽度误差、送进步距误差、送料歪斜等原因而冲裁出残缺的废品,保证冲出合格的工件,便于送料。搭边是废料,从节省材料出发,搭边越小越好。但过小的搭边值容易挤进凹模,增加刃口磨损,降低模具寿命,并且也影响冲裁件剪切表面质量。 查冲压模具设计与制造表确定搭边值 两工件间的搭边:a=3.0mm; 工件边缘搭边:a1=3.0mm; 步距为:h=115mm 条料宽度b=118mm确定后排样图如图5.2所示 图5.2落料排样图 一个步距内的材料利用率为:=19847/(118115)100%=72.6% 式中 A冲裁面积(包括内形结构废料); n
30、一个冲距内冲冲裁件数目; b条料宽度; h进距。确定排样方案,根据零件形状选用合理的排样方案,以提高材料的利用率。该零件毛坯形状为圆形状,直径尺寸较大,为便于送料和操作方便,采用单排方案。5.3确定板料规格根据条料的宽度尺寸选择合适的板料规格,使剩余的边料越小越好,该零件直径用料为112mm,以选择2mm(厚度)*118(宽度)的板料为宜。6 各工序工艺、冲压力及零部件的设计计算6.1 落料工艺、冲压力及零部件的设计计算6.1.1 落料工艺计算落料工艺计算主要为凸、凹模刃口尺寸计算,落料时凸、凹模刃口尺寸的设计原则是以凹模为设计基准,间隙取在凸模上,设计时采用最小合理间隙值Zmin。冲裁间隙的
31、大小主要与材料的性质及厚度有关,材料越硬,厚度越大,则间隙值应越大。选取间隙时应结合冲裁件的具体要求和世家的生产条件来考虑。其总的原则应该是在保证满足冲裁件剪断面质量和尺寸精度的前提下,是模具寿命最长。设计时一般采取查表法确定,在冲模制造时,也可按材料厚度的百分比估算。45钢,为硬刚,根据材料厚度2mm查表取Zmax=0.270mm,Zmin=0.210mm落料时落料凹模尺寸为: Dd=(Dmax-x)按IT12级去112mm的偏差为0.35 mm,即=0.35 mm,根据厚度及工件公差查的磨损系数x为0.5, Dmax=112+0.35=112.35mm该零件形状简单,刃口尺寸偏差按IT6取
32、值:=+0.033mm, =0.020mm。所以:Dd=(112.35-0.35*0.5)=112.16mm凸模尺寸D=( Dd- Zmin)=(112.16-0.21)=111.95,如图6.1所示 图 6.1 落料凸模 6.1.2 落料冲压力的计算(1) 计算冲裁力 冲裁力是设计模具、选择压力机的重要参数。计算冲压力的目的是为了合理地选择冲压设备和设计模具。选用冲压设备的标称压力必须大于所计算的冲裁力,所设计的模具必须能传递和承受所计算的冲裁力,已适应冲裁的要求。P=KLT=1.3*112*2*350=457184N320.02kN式中:P冲裁力,N L冲裁周边长度,mm L= D-(D:
33、圆的直径) 材料抗剪强度,MPa 查表为320380Mpa,取350Mpa K系数,通常取1.3(2) 计算卸料力、推件力 卸料力 P=KP=0.04*320.02KN=12.8kN 推件力P=nKP=5*0.055*320.02=88 kN式中:n卡在下模洞口内的工件数,n=h/t=10/2,取n=5 h凹模孔口高度 K卸料系数,查表得K=0.040.05 K推件系数,查表得K=0.055(3) 计算冲压力总和P总=P+P+P=320.02+12.8+88=420.82 kN(4) 压力机的选择选择压力为1500kN工作行程为30mm的压力机 经查文献可选用J11-50单台式压力机。6.1.
34、3 落料模主要零部件设计计算6.1.3.1 凹模的设计计算(1)凹模孔口形式为一般圆柱的形式其数据如下:凹模孔口高度 t5-10mm h=10-15mm该落料件厚t=2mm,取h=10 mm(2) 凹模外形尺寸的计算凹模厚度Ha=34.78mm, 取凹模厚度为35mm凹模周界尺寸,即凹模壁厚C=(1.52)Ha,所以C=2Ha=70mm,如图6.2所示 图 6.2 落料凹模6.1.3.2 固定板的设计计算(1)凹模固定板的设计凹模固定板的厚度与凹模一致,取70mm(2)凸模固定板的设计凸模固定板的外形尺寸与凹模固定板或卸料板尺寸相同,但本例采用的是橡胶直接卸料,故凸模固定板的外形尺寸可以小些。
35、凸模固定板的厚度H=(0.62-0.8)H=(0.6-0.8)*70, 取H=50mm6.1.3.3 卸料版的设计计算(1)卸料板类型选择 一般常用的卸料板有固定卸料板和弹性卸料板两种。固定卸料板装于下模,具有卸料力大、工作可靠、模具安装方便等优点;但是冲裁时卸料板压不住材料,冲出的工件平整度差。固定卸料板与凸模的间隙一般为0.2-0.6mm,冲裁厚度大于1.5mm。弹性卸料板除了在冲裁后卸料外,还可以在冲裁前压住材料,使冲制的工件平整度好,一般冲制厚度小于1.5mm或材料较软的工件。本例中的材料虽然大于1.5mm,但由于用单个毛坯,如果采用固定卸料板会给送料、定位增加难度,所以采用弹性卸料板
36、。弹性卸料板与凸模的双边间隙一般为0.1-0.2mm,或采用H9/f8等间隙配合。为了可靠卸料,弹性卸料板应高出凸模0.2-0.5 mm。(2)卸料板的尺寸 外形。弹性卸料板的外形一般与同方向上的固定板的外形一致;固定板卸料一般与凹模外形一致。 厚度。查冷冲模设计指导得H=40mm。 成形孔。基本与凹模刃口的形状相同。6.1.3.4 定位零件的设计计算本设计中定位零件采用模具设计大典里的定位销和定位螺钉定位,其尺寸大小根据模具大小选择合适的标准件。6.1.3.5 弹性元件设计计算此冲模中弹性元件主要为聚氨酯橡胶,橡胶的压缩量一般不能超过橡胶自由高度的30%,否则橡胶会过早失去弹性。根据工件材料
37、厚度为2mm,冲裁时凸模进入凹模深度取2mm,考虑模具维修时刃磨流量2mm,在考虑开启时卸料板高出凸模1mm,则总的工作行程h=2+2+2+1=7mm橡胶的自由高度H自=h/0.25-0.30=(23-28)mm, 取25mm橡胶预压量为h预=(0.10.15)*H自由=2.53.75mm 取h预=3mm橡胶安装高度H安=25-3=22mm橡胶直径P=A*p, p为与橡胶压缩量有关的单位压力,查冷冲模设计指导得p=1.52 Mpa。所以A= P/p橡胶直径:D=53mm, 取D=55mm。6.1.3.6 凸模的设计计算(1)凸模的结构设计 凸模的刃口形式。 圆形凸模,可以采用加工成台阶式结构或
38、直接不分段结构。 凸模的固定形式。 凸模根据冲制零件的形状、尺寸、加工方法的不同而有多种固定形式。该模具以台肩与固定板固定,凸模与凸模固定板的配合部分采用过渡配合(H7/m6或H7/n6)。(2)凸模长度计算L= H+H自+H歇-Y=122mm式中:L凸模的长度,mm H凸模固定板厚度 H自卸料橡胶自由高度 Y为了可靠卸料,在橡胶高度上所加的量,取2mm, H歇卸料版厚度6.1.3.7 其它零件的设计和计算(1)模架模架是整副模具的骨架,模具的全部零件都固定在它的上面,并且承受冲压过程中的全部负荷。模架的上模座通过模柄与压力机滑块相连,下模座螺钉压板固定在压力机工作台面上,上、下模之间靠模架的
39、导向装置来保持其精准位置,以引导凸模的运动,保证冲裁过程中间隙均匀。一般模架均已标准化,设计模具时,应加以正确选用。模架的要求:要有足够的强度与刚度:要有足够的精度(如上、下模座要平行,导柱、导套中心要与上下模座垂直,模柄要与上模座垂直等);上、下模之间的导向要精确(导向件之间的间隙要很小),上,下模之间的移动应平稳和无滞住现象。模架的形式 在标准模架中,应用最广泛的是用导柱和导套作为导向装置的模架。根据导柱和导套配置的不同由以下四种基本形式: 后测导柱模架 后侧导柱送料方便,可以纵向和横向送料。但是冲压时如果有偏心载荷,则导柱、导套会单边磨损。它不能用于模柄与上模浮动连接的模具。 中间导柱模
40、架 两侧导柱左右对称分布,应力平衡,所以导柱、导套磨损均匀。但是只有一个送料方向。 对角导柱模架 导柱的位置是对称的,而且纵横都能送料。对焦导柱模架的两导柱之间距离较远,在导柱、导套之间同样间隙的条件下,这种模架的导向及高度较高。 四导柱模架 其导向精度与刚度都较好,用于大型冲模。在本设计中采用后侧导柱模架。其选用如图6.3。后侧导柱模架(摘自GBT2851.3-1990)(mm)模架200160190235 GBT2851.5 模架技术要求:按JBT8050-1999的规定(2)导柱与导套导柱与导套的结构与尺寸都可直接由标准间中选取。在选用时应注意导柱的长度应保证冲模在最低工作位置时,下模座
41、底面与导柱底面的距离应为0.51mm。导柱与导套之间的配合根据冲裁模的间隙大小选用。当冲裁版厚载0.8mm以下的模具时,选用H6h5配合的I级精度模架。当冲裁板厚为0.84mm时,选用H7h6配合的II级精度模架。 导柱标准 B28 h6170 GBT2861.1图6.3 后侧导柱模架技术条件:按JBT8070-1995的规定材料:20钢数量:2个 导套的标准 B28 H710038 GBT2861.6技术条件:按JBT8070-1995的规定材料:20钢数量:2个(3)模座 后侧导柱上模座标准 上模座20016045 GBT2885.5 材料:HT200技术条件:按JBT8070-1995的
42、规定 后侧导柱下模座标准下模座20016055 GBT2855.6材料:HT200技术条件:按JBT8070-1995的规定(4) 模柄模柄由刚性和浮动两大类。所谓刚性模柄是指模柄与上模座是刚性连接,不能发生相对运动。所谓浮动模柄是指模柄相对上模座能做微小的摆动采用浮动模柄后,压力机滑块的运动误差不会影响上、下模的导向。常用的刚性模柄有四种型式:整体式、压入式、旋入式和凸缘式。模柄B50100 GB2862.3-81材料:Q235-A技术条件:按JBT7853-1994的规定模柄紧固螺钉:M1040 GB70-76材料:45钢技术条件:按GB2862.6-81的规定数量:4个(5)垫板设计该模
43、具在压力机安装时加垫板,垫板厚度取40mm。6.1.3.8 落料模闭合高度的计算模具闭合高度H模=Hs+Hx+Ha+Lt-h1=70+40+70+72-1=251mm 取250mm6.2 拉深工艺计算及零部件设计 6.2.1 拉深工艺计算(1)确定修边余量 由以上毛坯直径计算时确定得修边余量h=1.5mm(2)确定拉深次数确定毛坯相对高度 t/D=2/112=0.0179工件相对高度H/d=10/100=0.1查相关设计资料得n=1,故初步确定需1次拉深即可。(3)计算拉深直径查表得极限拉深系数为m=0.25,初步计算拉深直径为:d=ma=0.25*112 =28mm6.2.2 拉深工艺方案的
44、确定挡盖拉深后高度为10mm,板材的厚度为2mm,在拉深的过程中材料由简单的圆形状形成有凸台的挡盖形状。拉深零件图见6.4 图6.4 拉深制件图6.2.3 拉深力及工作部分尺寸、零部件设计计算6.2.3.1拉深拉深力及工作部分尺寸零部件设计计算(1)拉深力计算 拉深所需的压力:P=P拉+P压 P拉=dtk=3.14*60*2*400*0.8=120.576kN P压=Ap=/4*(112-100)*4=8kN 所以:P=P拉+P压=120.576+8=128.576 kN 式中: P拉拉深力,NP压压边力,Nt -材料厚度k修正系数,一般取0.50.8,t/D与m值小时,k取大值拉伸件材料的抗
45、拉强度,MPa,查得Q235350 MPa,取400 MPa A有效压面积,mm2 p单位压边力,查得取p=4 MPa(2)初选压力机压力机的公称压力P0(1.61.8)P取P0=1.8*128.576=231.44 kN故初选压力机的公称压力为250kN,选用J23-25压力机(3)凸、凹模间隙的计算拉伸间隙是指单边间隙,即Z=(da-dt)/2。间隙过小会增加摩擦力,是拉深件容易拉裂,且易擦伤制件表面,降低模具寿命。间隙过大则对坯料的校直作用小,影响制件的尺寸精度。因此,确定间隙的原则是,既要考虑板料厚度的公差,又要考虑圆筒形件的增厚现象,根据拉深时是否采用压边圈和制件的尺寸精度、表面粗糙
46、度要求合理确定。此件拉深采用压边装置,经工艺计算取间隙为Z=1.05t=2.1mm(4)凸、凹模圆角半径的计算经以上计算得,一次拉深时凹模圆角半径r1=10mm,凸模圆角半径r2=6mm(5)凸、凹模工作部分尺寸计算此工件要求的是外形尺寸,设计凸、凹模时应以凹模尺寸以基准进行计算,即:凹模尺寸Da=(0.75)=60.75mm式中,D拉深件的基本尺寸,mm 拉深件尺寸公差(6)其它零部件的设计计算 压边圈的设计 压边圈的外形尺寸与凹模外形尺寸相同,压边圈材料与凸、凹模一致,热处理强度略低于凸、凹模的硬度。取Hy =60mm 压边装置的设计该拉深模选在单动压力机上进行拉深加工,所以必须借助弹性元
47、件在受压时所产生的压力提供压边力。故选用具有通用性的弹性压边装置作为弹性元件,这样可避免每副模具都设计一套专用的弹性压边装置。模具只需配备压边圈和顶杆并采用倒装结构。(7)拉深模闭合高度的计算拉深模的闭合高度是指滑块在下止点位置时,上模座上平面与下模座下平面之间的距离,即:H=Hs+Hag+Ha+Hy+Htg+Hx+s+t =70+70+70+15+50+70+(20-25)+2 =367372mm, 取H=400mm式中, Hs上模座厚度,mm Hx下模座厚度,mm Hag凹模固定板厚度,mm Ha凹模厚度,mm Hy压边圈厚度,mm Htg凸模固定板厚度,mm S安全距离,mm, 一般取2
48、025mm t拉深件厚度, mm(8)确定凸模通气孔通气孔直径一般可在38mm之间选取,选取的原则一般视凸模尺寸而定。此工序通气孔直径选5mm。6.3冲孔工艺及零件的设计6.3.1冲裁力的计算1)冲孔模具冲裁力的计算冲裁力按下式计算:F=KLtb 式中F冲裁力; L冲裁周边长度;t材料厚度;b材料抗剪强度; K系数,系数是考虑到实际生产中,模具间隙值的波动和不均匀,刃口磨损、板料力学性能和厚度波动等原因的影响而给出修正系数,一般取=1.3。计算冲裁件轮廓周长冲孔件是规则的圆形所以L=3.14*20查文献取b=325Mpa所以F=KLtb =1.362.82325 =53066(N)6.3.2卸
49、料力、推料力的计算卸料力FX FX=KXF 推料力FT FT =KTF FX=KXF =0.0453066 =2122.64(N) (KX、KT为卸料力、推件力系数,)FT=KTF =0.05553066 =2918.63(N)所以总冲压力FZ=F+FX+FT=53066N+2122.64N+2918.63N =58107.27(N)根据冲压力计算结果拟选压力机规格为J236.3。6.3.3冲孔凸模、凹模尺寸计算该制件有冲孔,落料。其尺寸计算公式:dT=(dminx) 0-T dA=( dTZmin)A0 A=0.020mm T=0.020mm X=0.75校核:TA=0.040mmCmaxC
50、min,满足TACmaxCmin的条件。将已知和查表所得的数据代入公式,即得:Zmin=3%t=0.06凸模dT=(20+0.750.24)0-0.02=20.180-0.02mm 凹模dA=(20.18+0.06)0+0.20=20.240+0.20mm6.3.4 凹模外形尺寸的确定本设计凹模采用圆柱形孔口凹模。圆形凹模可按冷冲模国家标准或工厂标准选用,非标准尺寸的凹模的外形尺寸常用经验公式计算确定。凹模厚度的确定式: H=Kb凹模壁厚(指凹模刃口与外边缘的距离)的确定式见 C=(23)H(大型凹模)式中 b凹模孔的最大宽度,mm; 因数,见表2.5; H凹模厚度,mm; C凹模壁厚,mm。
51、按上式计算的非标准凹模外形尺寸,可以保证凹模有足够的强度和刚度,一般可不再进行强度校核。本设计支撑板零件,是非标准尺寸凹模,则按上述公式有: b=101mm H=Kb=0.22100mm=22mm C=2H=222mm=44mm L=b+2C=100224=188mm B=n2C=45244=133mm6.4工作零件间隙的确定1)间隙对冲裁件尺寸精度的影响冲裁件的尺寸精度是指冲裁件的实际尺寸与基本尺寸的差值,差值越小,则精度越高,这个差值包括两方面的偏差,一是冲裁件相对于凸模或凹模的偏差,二是模具本身的制造偏差。2)间隙对模具寿命的影响模具寿命受各种因素的综合影响,间隙是模具寿命诸因数中最主要
52、的因数之一,冲裁过程中,凸模与被冲的孔之间,凹模与落料件之间均有摩擦,而且间隙越小,模具作用的压应力越大,摩擦也越严重,所以过小的间隙对模具寿命极为不利。而较大的间隙可使凸模侧面及材料间的摩擦减小,并延缓间隙由于受到制造和装配精度的限制,出现间隙不均匀的不利影响,从而提高模具寿命。3)间隙对冲裁工艺力的影响随着间隙的增大,材料所受的拉应力增大,材料容易断裂分离,因此冲裁力减小。通常冲裁力的降低并不显著,当单边间隙在材料厚度的520%左右时,冲裁力的降低不超过510%。间隙对卸料力推料力的影响比较显著。间隙增大后,从凸模里卸料和从凹模里推料都省力当当单边间隙达到材料厚度的1525%左右时的卸料力
53、几乎为零。但间隙继续增大,因为毛刺增大,又将引起卸料力、顶件力迅速增大。4)间隙值的确定由以上分析可见,凸、凹模间隙对冲裁件质量、冲裁工艺力、模具寿命都有很大的影响。因此,设计模具时一定要选择合理的间隙,以保证冲裁件的断面质量、尺寸精度满足产品的要求,所需冲裁力小、模具寿命高,但分别从质量,冲裁力、模具寿命等方面的要求确定的合理间隙并不是同一个数值,只是彼此接近。考虑到模具制造中的偏差及使用中的磨损、生产中通常只选择一个适当的范围作为合理间隙,只要间隙在这个范围内,就可以冲出良好的制件,这个范围的最小值称为最小合理间隙Cmin,最大值称为最大合理间隙Cmax。考虑到模具在使用过程中的磨损使间隙
54、增大,故设计与制造新模具时要采用最小合理间隙值Cmin。 查文献1145钢: t1mm,C=(4%5%)t t=13mm,C=(6%8%)t t=38mm,C=(8%13%)t6.5模具压力中心的确定为了确保压力机和模具正常工作,应使模具的压力中心与压力机滑块的中心相重合,否则,会使冲模和力机滑块产生偏心载荷,使滑块和导轨之间产生过大的摩擦,模具导向零件加速磨损,降低模具和压力机的使用寿命。该挡盖零件为中心对称图形,经分析得到其几何中心即为压力中心。6.6定位零件 挡料销根据模具的结构采用固定挡料销装在凸模上选取直径,露出部分长度3mm,固定挡料销M47, 导料销M47,材料45钢,数量2个。7装 配 图装配图应用足够说明模具构造的投影图
- 温馨提示:
1: 本站所有资源如无特殊说明,都需要本地电脑安装OFFICE2007和PDF阅读器。图纸软件为CAD,CAXA,PROE,UG,SolidWorks等.压缩文件请下载最新的WinRAR软件解压。
2: 本站的文档不包含任何第三方提供的附件图纸等,如果需要附件,请联系上传者。文件的所有权益归上传用户所有。
3.本站RAR压缩包中若带图纸,网页内容里面会有图纸预览,若没有图纸预览就没有图纸。
4. 未经权益所有人同意不得将文件中的内容挪作商业或盈利用途。
5. 装配图网仅提供信息存储空间,仅对用户上传内容的表现方式做保护处理,对用户上传分享的文档内容本身不做任何修改或编辑,并不能对任何下载内容负责。
6. 下载文件中如有侵权或不适当内容,请与我们联系,我们立即纠正。
7. 本站不保证下载资源的准确性、安全性和完整性, 同时也不承担用户因使用这些下载资源对自己和他人造成任何形式的伤害或损失。