hljit6h240变速器设计本科学位论文
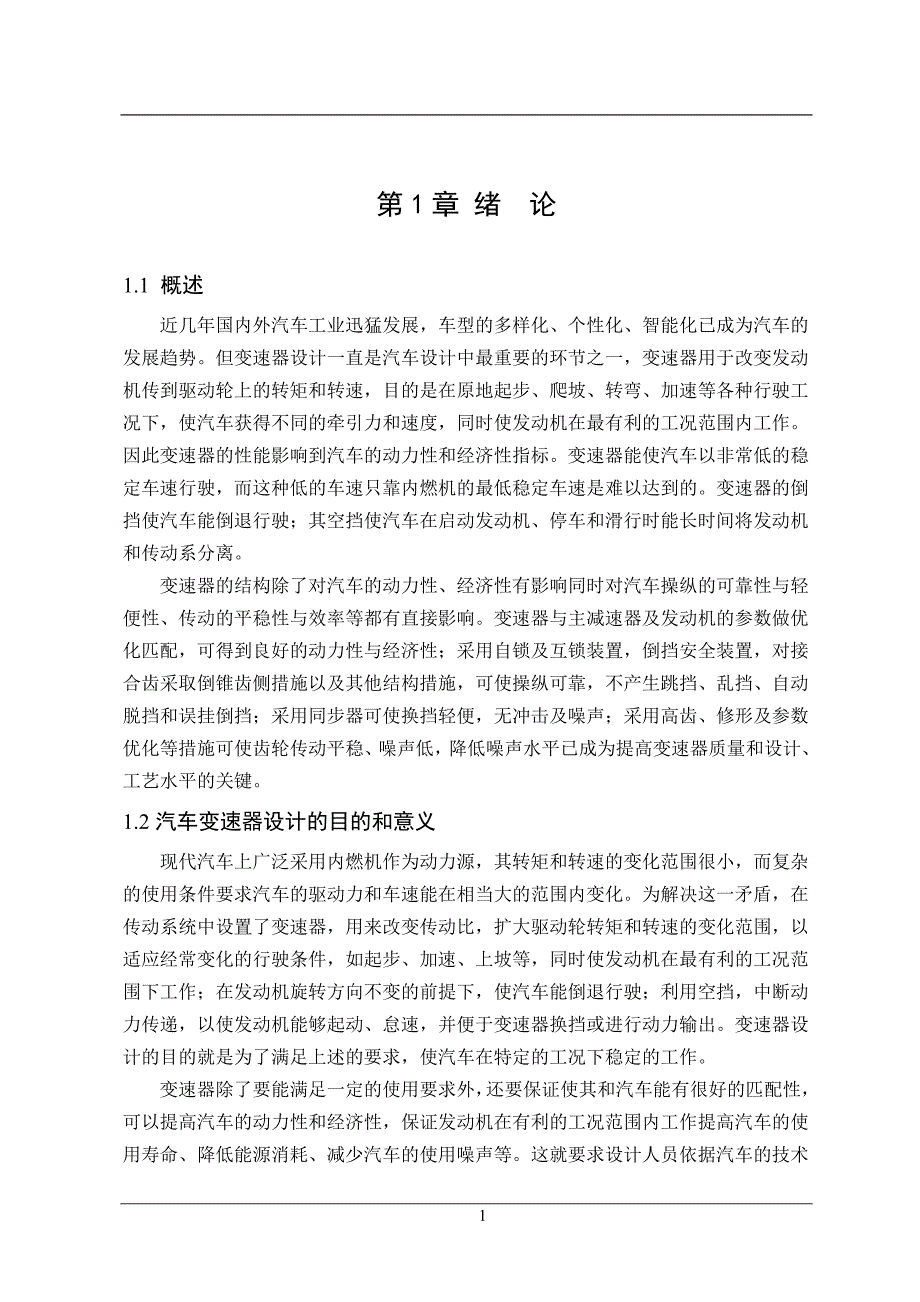


《hljit6h240变速器设计本科学位论文》由会员分享,可在线阅读,更多相关《hljit6h240变速器设计本科学位论文(65页珍藏版)》请在装配图网上搜索。
1、 第1章 绪 论1.1 概述近几年国内外汽车工业迅猛发展,车型的多样化、个性化、智能化已成为汽车的发展趋势。但变速器设计一直是汽车设计中最重要的环节之一,变速器用于改变发动机传到驱动轮上的转矩和转速,目的是在原地起步、爬坡、转弯、加速等各种行驶工况下,使汽车获得不同的牵引力和速度,同时使发动机在最有利的工况范围内工作。因此变速器的性能影响到汽车的动力性和经济性指标。变速器能使汽车以非常低的稳定车速行驶,而这种低的车速只靠内燃机的最低稳定车速是难以达到的。变速器的倒挡使汽车能倒退行驶;其空挡使汽车在启动发动机、停车和滑行时能长时间将发动机和传动系分离。变速器的结构除了对汽车的动力性、经济性有影响
2、同时对汽车操纵的可靠性与轻便性、传动的平稳性与效率等都有直接影响。变速器与主减速器及发动机的参数做优化匹配,可得到良好的动力性与经济性;采用自锁及互锁装置,倒挡安全装置,对接合齿采取倒锥齿侧措施以及其他结构措施,可使操纵可靠,不产生跳挡、乱挡、自动脱挡和误挂倒挡;采用同步器可使换挡轻便,无冲击及噪声;采用高齿、修形及参数优化等措施可使齿轮传动平稳、噪声低,降低噪声水平已成为提高变速器质量和设计、工艺水平的关键。1.2汽车变速器设计的目的和意义 现代汽车上广泛采用内燃机作为动力源,其转矩和转速的变化范围很小,而复杂的使用条件要求汽车的驱动力和车速能在相当大的范围内变化。为解决这一矛盾,在传动系统
3、中设置了变速器,用来改变传动比,扩大驱动轮转矩和转速的变化范围,以适应经常变化的行驶条件,如起步、加速、上坡等,同时使发动机在最有利的工况范围下工作;在发动机旋转方向不变的前提下,使汽车能倒退行驶;利用空挡,中断动力传递,以使发动机能够起动、怠速,并便于变速器换挡或进行动力输出。变速器设计的目的就是为了满足上述的要求,使汽车在特定的工况下稳定的工作。变速器除了要能满足一定的使用要求外,还要保证使其和汽车能有很好的匹配性,可以提高汽车的动力性和经济性,保证发动机在有利的工况范围内工作提高汽车的使用寿命、降低能源消耗、减少汽车的使用噪声等。这就要求设计人员依据汽车的技术参数,合理的选择变速器的参数
4、,使所设计的变速器能和整车具有很好的匹配性。1.3汽车变速器国内外现状和发展趋势1.3.1汽车变速器国内外现状早期的汽车传动系,从发动机到车轮之间的动力传动形式是很简单的。1892年法国制造出第一辆带有变速器的汽车。1921年英国人赫伯特福鲁特采用耐用的摩擦材料进一步完善了变速器的性能。现代汽车变速器是1894年由法国人路易斯雷纳本哈特和艾米尔拉瓦索尔推广使用的。目前为止,变速器经历了几个发展阶段,主要为:1、手动变速器手动变速器主要采用齿轮传动的降速原理。变速器内有多组传动比不同的齿轮副,而汽车行驶时的换挡工作,也就是通过操纵机构使变速器内的不同的齿轮副工作。手动变速器又称手动齿轮式变速器,
5、含有可以在轴向滑动的齿轮,通过不同齿轮的啮合达到变速变矩的目的。手动变速器的换挡操作可以完全遵从驾驶者的意志,且结构简单、故障率相对较低、价廉物美。2、自动变速器自动变速器是根据车速和负荷(油门踏板的行程)来进行双参数控制,挡位根据上面的两个参数来自动升降。自动变速器与手动变速器的共同点,就是二者都属于有级式变速器,只不过自动变速器可以根据车速的快慢来自动实现换挡,可以消除手动变速器“顿挫”的换挡感觉。自动变速器是由液力变矩器、行星齿轮和液压操纵机构组成,通过液力传递和齿轮组合的方式来达到变速变矩的目的。3、无级变速器无级变速器又称为连续变速式无级变速器。这种变速器与一般齿轮式自动变速器的最大
6、区别,是它省去了复杂而又笨重的齿轮组合变速传动,而只用了两组带轮进行变速传动。无级变速器结构比传统变速器简单,体积更小,它既没有手动变速器的众多齿轮副,也没有自动变速器复杂的行星齿轮组,主要靠主动轮、从动轮和传动带来实现速比的无级变化。4、无限变速式机械无级变速器(IVT)无限变速式机械无级变速器与其它自动变速器的差别之一是不使用变矩器。变矩器的作用是通过油液介质将发动机动力传递给变速器,它的传递效率通常只有80%。IVT由于不使用变矩器,与其它变矩器比较,IVT具有效率高、不易打滑、油耗低、不需要工艺复杂造价高昂的金属传送带、结构简单、成本低等一系列优点,加上传递扭矩大,长时间使用也不会过度
7、发热,不但使用于轿车,也使用于越野车,是一种新型变速器。1.3.2汽车变速器的发展趋势回顾汽车变速器的发展可以清楚的知道,变速器作为汽车传动系统的重要组成部分,其技术的发展,是衡量汽车技术水平的一个重要依据。现代汽车变速器的发展趋势,是向着可调自动变速器或无级变速器的方向发展。自动变速器多挡化虽能扩大自动变速的范围,但它并非安全迅速。理想的无级变速器是在整个传动范围内能连续的、无挡比的切换变速比,是变速器始终按最佳换挡规律自动变速。无级化是对自动变速器的理想追求。现代无级变速器传动效率提高,变速反应快、油耗低。随着电子技术的发展,变速器的自动控制进一步完善,在各种使用工况下能实现发动机与传动系
8、的最佳匹配,控制更加精确、有效,性能价格比大大提高。无级变速器装有自动控制装置,行车中可以根据车速自动调整挡位,无需人工操作,省去了换挡及踩踏离合器踏板的操作。其不足之处在于价格昂贵、维修费用很高,而且使用起来比手动挡车费油,尤其是低速行驶或堵车中走走停停时,更会增大油耗。当今世界各大汽车公司对无级变速器的研究都十分活跃。不久的将来,随着电子控制技术的进一步完善,电子控制式的无级变速器可望得到广泛的发展和应用。1.4手动变速器的特点和设计要求及内容1.4.1手动变速器的特点手动变速器的挡数通常在6挡以下,当挡数超过6挡时,可以在6挡以下的主变速器的基础上,再行配置副变速器,通过两者的组合获得多
9、挡变速器。近年来,为了降低油耗,变速器的挡数有增加的趋势。目前,乘用车一般采用4-5个挡位的变速器。发动机排量大的乘用车多用5个挡。商用车变速器采用4-5个挡或多挡。载质量在2.0-3.5t的货车采用五挡变速器,载质量在4.0-8.0t的货车采用六挡变速器。多挡变速器多用于总质量大些的货车和越野车上。某些汽车的变速器,设置有用在良好的路面上轻载或空车驾驶的场合的超速挡,超速挡的传动比小于1。采用超速挡,可以提高汽车的燃油经济性。但是如果发动机功率不高,则超速挡使用频率很低,节油效果不显著,甚至影响汽车的动力性。从传动机构布置上来说,目前,两轴式和三轴式变速器都得到了广泛的应用。其中,两轴式变速
10、器多用于发动机前置前轮驱动的汽车上。三轴式变速器的第一轴的常啮合齿轮与第二轴的各挡齿轮分别与中间轴的相应齿轮相啮合,且第一、第二轴同心。将第一、第二轴直接连接起来传递转矩则称为直接挡。此时,齿轮、轴承及中间轴均不承载,而第一、第二轴也仅传递转矩。因此,直接挡的传动效率高,磨损及噪声也最小,因为直接挡的利用率要高于其它挡位,因此提高了变速器的使用寿命;在其它前进挡位工作时,变速器传递的动力需要经过设置在第一轴、中间轴和第二轴上的两对齿轮传递,因此在变速器中间轴和第二轴之间的距离(中心距)不大的情况下,一挡仍有较大的传动比;挡位高的齿轮采用长啮合齿轮传动,挡位低的齿轮可以采用或不采用长啮合齿轮传动
11、;多数传动方案中除一挡以外的其它挡位的换挡机构,均采用同步器或啮合套换挡,少数结构的一挡也用同步器或啮合套换挡,还有各挡同步器或啮合套多数情况下装在第二轴上。手动变速器的发展趋势是增多常啮合齿轮副的数目,从而可采用斜齿圆柱齿轮。斜齿圆柱齿轮比直齿圆柱齿轮有更长的寿命、更低的噪声,虽然其制造稍微复杂且在工作时有轴向力。因此,在变速器中,除低挡及倒挡齿轮外,直齿圆柱齿轮已被斜齿圆柱齿轮所取代。当然,常啮合齿轮副的增多将导致旋转部分总惯性力矩的增大。1.4.2手动变速器的设计要求(1)、正确选择变速器的挡位数和传动比,使其和发动机参数优化匹配,以保证汽 车具有良好的动力性和经济性;(2)、设置空挡以
12、保证汽车在必要时能将发动机和传动系长时间分离,设置倒挡使汽车能倒退行驶;(3)、操纵简单、方便、迅速、省力;(4)、传动效率高,工作平稳、无噪声;(5)、体积小、质量轻、承载能力强,工作可靠;(6)、制造容易、成本低廉、维修方便、使用寿命长;(7)、贯彻零件标准化、部件通用化及总成系列化等设计要求,遵守有关标准规定;(8)、需要时应设置动力输出装置。1.4.3变速器设计的主要内容本设计主要是依据瑞麒G52010款梅西版2.0TCI手动舒适性汽车的有关参数,通过对变速器各部分参数的选择和计算,设计出一种基本符合要求的6档手动变速器,并绘制出变速器装配图及主要零件的零件图。本文主要完成下面一些主要
13、工作:1、对变速器传动机构的分析与选择通过比较两轴和中间轴式变速器各自的优缺点,以及所设计车辆的特点,确定传动机构的布置形式。2、变速器主要参数的选择变速器主要参数的选择:档数、传动比、中心距、齿轮参数等。3、变速器齿轮强度的校核变速器齿轮强度的校核主要对变速器的齿根弯曲疲劳强度和齿面接触疲劳强度进行校核。4、轴的基本尺寸的确定及强度计算。对于轴的强度计算则是对轴的刚度和强度分别进行校核。5、轴承的选择与寿命计算。对变速器轴的支撑部分选用圆锥磙子轴承,寿命计算是按汽车的大修里程来衡量,轿车的为30万公里。本次设计主要是查阅近几年来有关国内外变速器设计的文献资料,结合所学专业知识,在老师的正确指
14、导下进行设计。通过比较不同方案和方法选取最佳方案进行设计,计算变速器的齿轮的结构参数并对其进行校核计算;同时对同步器、换档操纵机构等结构件进行分析设计;另外,对现有传统变速器的结构进行改进、完善。 第2章 变速器传动机构与操纵机构的布置2.1变速器传动方案布置机构 机械式变速器具有结构简单、传动效率高、制造成本底和工作可靠等优点,故在不同形式的汽车上得到广泛应用。2.1.1变速器传动方案分析与选择机械式变速器传动机构布置方案主要有两种:两轴式变速器和中间轴式变速器。1.两轴式变速器的特点分析与中间轴式变速器相比较,两轴式变速器结构简单、紧凑且除最高挡外其他各挡的传动效率高、噪声低。轿车多采用前
15、置发动机前轮驱动的布置,因为这种布置使汽车的动力-传动系统紧凑、操纵性好且可使汽车质量减少6%10%。两轴式变速器则方便于这种布置且使传动系的结构简单。两轴式变速器没有直接挡,因此在高挡工作时,齿轮和轴承均承载,因而噪声较大,也增加了磨损,这是它的缺点。如图2.1ac所示为发动机前置前轮驱动轿车的两轴式变速器传动方案。其特点是:变速器输出轴与主减速器主动齿轮做成一体;多数方案的倒挡传动常用滑动齿轮,其它挡位均用常啮合齿轮传动。图2.1c中的倒挡齿轮为常啮合齿轮,并用同步器换挡;图2-1a所示方案的变速器有辅助支承,用来提高轴的刚度。图2.1 两轴式变速器传动方案2.中间轴式变速器特点分析中间轴
16、式变速器多用于发动机前置后轮驱动汽车和发动机后置后轮驱动的客车上。变速器第一轴的前端经轴承支承在发动机的飞轮上,第一轴上的花键用来装设离合器的从动盘,而第二轴的末端经花键与万向节连接。如图2.2ad所示为中间轴式变速器的传动方案,其中ab为中间轴式五挡变速器,cd为中间轴式六挡变速器的传动方案。中间轴式变速器的共同特点为:变速器第一轴后端与常啮合主动齿轮做成一体。绝大多数方案的第二轴前端经轴承支承在第一轴后端的孔内,且保证两轴轴线在同一直线上,经啮合套将它们连接后可得到直接挡。使用直接挡,变速器的齿轮和轴承及中间轴均不承载,发动机转矩经变速器第一轴和第二轴直接输出,此时变速器的传动效率高,可达
17、到90%以上,噪声低、齿轮和轴承的磨损减少。因为直接挡的利用率要高于其他挡位,因而提高了变速器的使用寿命;在其他前进挡位工作时,变速器传递的动 图2.2中间轴式变速器传动方案力需要经过设置在第一轴、中间轴和第二轴上的两对齿轮传递,因此在变速器中间轴与第二轴之间的距离(中心距)不大的条件下,一挡仍然有较大的传动比;挡位高的齿轮采用常啮合齿轮传动,挡位低的齿轮可以不采用常啮合齿轮传动;多数传动方案件中除一挡以外的其他挡位的换挡机构,均采用同步器或接合套换挡,少数结构的一挡也采用同步器或接合套换挡,各挡同步器或接合套多数情况下装在第二轴上。在除直接挡以外的其他挡位工作时,中间轴式变速器的传动效率略有
18、降低,这是它的缺点。以上各方案中,凡采用常啮合齿轮传动的挡位,其换挡形式可以用同步器或啮合套来实现。同一变速器中,有的挡位用同步器换挡,有的挡位用啮合套换挡,那么一定是挡位高的用同步器换挡,挡位低的用啮合套换挡。对不同类型的汽车,具有不同的传动系档位数,其原因在于它们的使用条件不同、对整车性能要求不同、汽车本身的比功率不同。而传动系的档位数与汽车的动力性、燃油经济性有着密切的联系。就动力性而言,档位数多,增加了发动机发挥最大功率附近高功率的机会,提高了汽车的加速和爬坡能力。就燃油经济性而言,档位数多,增加了发动机在低燃油消耗率区下作的能力,降低了油耗。从而能提高汽车生产率,降低运输成木。不过,
19、增加档数会使变速器机构复杂和质量增加,轴向尺寸增大、成本提高、操纵复杂。 综上所述,由于此次设计的变速器驱动形式属于发动机前置前轮驱动,且可布置变速器的空间较小,对变速器的要求较高,要求运行噪声小,设计车速高,故选用二轴式变速器作为传动方案。2.1.2倒档布置方案分析倒挡布置应注意以下几点:(1)倒挡齿轮在非工作位置时,不得与第二轴的齿轮有啮合现象;(2)换入倒挡时不得与其他齿轮发生干涉;(3)倒挡轴在变速器壳体上的支承不得与与中间轴的齿轮相碰。常见的倒档布置方案如图2.3所示。图2.3b方案的优点是倒档利用了一档齿轮,缩短了中间轴的长度。但换档时有两对齿轮同时进入啮合,使换档困难;图2.3c
20、方案能获得较大的倒档传动比,缺点是换档程序不合理;图2.3d方案对2.3c的缺点做了修改;图2.3e所示方案是将一、倒档齿轮做成一体,将其齿宽加长;图2.3f所示方案适用于全部齿轮副均为常啮合的齿轮,换档换更为轻便。 图2.3倒档布置方案变速器的一挡或倒挡因传动比大,工作时在齿轮上作用的力也增大,并导致变速器轴产生较大的挠度和转角,使工作齿轮啮合状态变坏,最终表现出轮齿磨损加快和工作噪声增加。为此,无论是两轴式变速器还是中间轴式变速器的一挡与倒挡,都应当布置在靠近轴的支撑处,以便改善上述不良情况,然后按照从低挡到高挡的顺序布置各挡齿轮,这样做既能使轴具有足够大的刚性,又能保证容易装配。倒挡的传
21、动比虽然与一挡的传动比接近,但因为使用倒挡的时间非常短,从这点出发有些方案将一挡布置在靠近轴的支承处,然后再布置倒挡。为防止意外挂入倒挡,一般在挂倒挡时设有一个挂倒挡时需克服弹簧所产生的力,用来提醒驾驶员注意。 综合考虑以上因素,为了换档轻便,减小噪声,倒档传动采用图2.3f所示方案。2.1.3零部件结构方案分析1.齿轮分析变速器用齿轮有直齿圆柱齿轮和斜齿圆柱齿轮两种。与直齿圆柱齿轮比较,斜齿圆柱齿轮有使用寿命长、运转平稳、工作噪声低等优点;缺点是制造时稍有复杂,工作时有轴向力,这对轴承不利。变速器中的常啮合齿轮均采用斜齿圆柱齿轮,尽管这样会使常啮合齿轮数增加,并导致变速器的质量和转动惯量增大
22、。所以本设计全部选用斜齿轮。变速器齿轮可以与轴设计为一体或与轴分开,然后用花键、过盈配合或者滑动支承等方式之一与轴连接。齿轮尺寸小又与轴分开,其内径直径到齿根圆处的厚度(图2.2)影响齿轮强度。要求尺寸应该大于或等于轮齿危险断面处的厚度。为了使齿轮装在轴上以后,保持足够大的稳定性,齿轮轮毂部分的宽度尺寸,在结构允许条件下应尽可能取大些,至少满足尺寸要求: (2.1)式中:花键内径。为了减小质量,轮辐处厚度应在满足强度条件下设计得薄些。图2.4中的尺寸可取为花键内径的1.251.40倍。 图2.4 变速器齿轮尺寸控制图齿轮表面粗糙度数值降低,则噪声减少,齿面磨损速度减慢,提高了齿轮寿命。变速器齿
23、轮齿面的表面粗糙度应在m范围内选用。要求齿轮制造精度不低于7级。2变速器轴变速器轴多数情况下经轴承安装在壳体的轴承孔内。当变速器中心距小,在壳体的同一端面布置两个滚动轴承有困难时,输出轴可以直接压入壳体孔中,并固定不动。用移动齿轮方式实现换档的齿轮与轴之间,应选用矩形花键连接,以保证良好的定心和滑动灵活,而且定心外径及矩形花键齿侧的磨削比渐开线花键要容易。两轴式变速器输入轴和中间轴式变速器中间轴上的高档齿轮,通过轴与齿轮内孔之间的过盈配合和键固定在轴上。两轴式变速器的输出轴和中间轴式变速器的第二轴上的常啮合齿轮副的齿轮与轴之间,常设置有滚针轴承、滑动轴承,少数情况下齿轮直接装在轴上。此时,轴的
24、表面粗糙度不应低与m,硬度不低于5863HRC。因渐开线花键定位性能良好,承载能力大且渐开线花键的齿短,小径相对增大能提高轴的刚度,所以轴与同步器上的轴套常用渐开线花键连接。倒档轴为压入壳体孔中并固定不动的光轴,并由螺栓固定。由上述可知,变速器的轴上装有轴承、齿轮、齿套等零件,有的轴上又有矩形或渐开线花键,所以设计时不仅要考虑装配上的可能,而且应当可以顺利拆装轴上各零件。此外,还要注意工艺上的有关问题。3.变速器轴承的选择变速器轴承常采用圆柱滚子轴承、球轴承、滚针轴承、圆锥滚子轴承、滑动轴套等。滚针轴承、滑动轴承套主要用在齿轮与轴不是固定连接,并要求两者有相对运动的地方。 变速器中采用圆锥滚子
25、轴承虽然有直径较小、宽度较大因而容量大、可承受高负荷等优点,但也有需要调整预紧、装配麻烦、磨损后轴易歪斜而影响齿轮正确啮合的缺点。 由于本设计的变速器为两轴变速器,具有较大的轴向力,所以设计中变速器输入轴、输出轴的前、后轴承按直径系列均选用圆锥滚子轴承。2.2变速器操纵机构布置方案2.2.1 概述根据汽车使用条件的需要,驾驶员利用操纵机构完成选档和实现换档或退到空档。变速器操纵机构应当满足如下主要要求:换档时只能挂入一个档位,换档后应使齿轮在全齿长上啮合,防止自动脱档或自动挂档,防止误挂倒档,换档轻便。变速器操纵机构通常装在顶盖或侧盖内,也有少数是分开的。变速器操纵机构操纵第二轴上的滑动齿轮、
26、啮合套或同步器得到所需不同档位。用于机械式变速器的操纵机构,常见的是由变速杆、拨块、拨叉、变速叉轴及互锁、自锁和倒档装置等主要零件组成,并依靠驾驶员手力完成选档、换档或推到空档工作,称为手动换档变速器。1、直接操纵式手动换档变速器当变速器布置在驾驶员座椅附近时,可将变速杆直接安装在变速器上,并依靠驾驶员手力和通过变速杆直接完成换档功能的手动换档变速器,称为直接操纵变速器。这种操纵方案结构最简单,已得到广泛应用。近年来 ,单轨式操纵机构应用较多,其优点是减少了变速叉轴,各档同用一组自锁装置,因而使操纵机构简化,但它要求各档换档行程相等。2、远距离操纵手动换档变速器平头式汽车或发动机后置后轮驱动汽
27、车的变速器,受总体布置限制,变速器距驾驶员座位较远,这时需要在变速杆与拨叉之间布置若干传动件,换档手力经过这些转换机构才能完成换档功能。这种手动换档变速器,称为远距离操纵手动换档变速器。3、电动自动换档变速器20世纪80年代以后,在固定轴式机械变速器基础上,通过应用计算机和电子控制技术,使之实现自动换档,并取消了变速杆和离合器踏板。驾驶员只需控制油门踏板,汽车在行驶过程中就能自动完成换档,这种变速器成为电动自动换档变速器。由于所设计的变速器为两轴变速器,采用发动机前置前轮驱动,变速器离驾驶员座椅较近,所以采用直接操纵式手动换档变速器。2.2.2 典型的操纵机构及其锁定装置 图2.5 为典型的操
28、纵机构图定位装置的作用是将被啮合件保持在一定位置上,并防止自动啮合和分离,一般采用弹簧和钢球式机构。1、换挡机构形式(a) 直齿滑动齿轮换挡 (b)啮合套换挡 (c)同步器换挡 图2.6换挡机构形式如图2.6变速器换挡机构有直齿滑动齿轮、啮合套和同步器换挡三种形式。直齿滑动齿轮换挡要求驾驶员有熟练的操作技术(如两脚离合器)才能使换挡时齿轮无冲击;换挡行程长,换挡瞬间驾驶员注意力被分散,又影响行驶安全。因此,尽管这种换挡方式结构简单,制造、拆装与维修工作皆容易,并能减小变速器旋转部分的惯性力矩,但除一挡、倒挡已很少使用。啮合套换挡不能消除换挡冲击,而且要求驾驶员有熟练的操作技术。此外,因增设了啮
29、合套和常啮合齿轮,使变速器旋转部分的总惯性力矩增大。因此,目前这种换挡方法只在某些要求不高的挡位及重型货车变速器上应用。使用同步器能保证迅速、无冲击、无噪声换挡,而与操作技术的熟练程度无关,从而提高了汽车的加速性、燃油经济性和行驶安全性。同上述两种换挡方法比较,虽然它有结构复杂、制造精度要求高、轴向尺寸大等缺点,但仍然得到广泛应用。通过比较,考虑汽车的操纵性能,本设计全部档位均选用同步器换档。2、防脱档设计互锁装置是保证移动某一变速叉轴时,其它变速叉轴互被锁住,该机构的作用是防止同时挂入两档,而使挂档出现重大故障。常见的互锁机构有: (1)互锁销式图2.7是汽车上用得最广泛的一种机构,互锁销和
30、顶销装在变速叉轴之间,用销子的长度和凹槽来保证互锁。图2.7,a为空档位置,此时任一叉轴可自由移动。图2.7,b、c、d为某一叉轴在工作位置,而其它叉轴被锁住。图2.7 互锁销式互锁机构(2)摆动锁块式图2.8为摆动锁块式互锁机构工作示意图,锁块用同心轴螺钉安装在壳体上,并可绕螺钉轴线自由转动,操纵杆的拨头置于锁块槽内,此时,锁块的一个或两个突起部分A档住其它两个变速叉轴槽,保证换档时不能同时挂入两档。(3)转动钳口式图2.9为与上述锁块机构原理相似的转动钳口式互锁装置。操纵杆拨头置于钳口中,钳形板可绕A轴转动。选档时操纵杆转动钳形板选入某一变速叉轴槽内,此时钳形板的一个或两个钳爪抓住其它两个
31、变速叉,保证互锁作用。 图2.8 摆动锁块式互锁机构 图2.9 转动钳口式互锁机构操纵机构还应设有保证不能误挂倒档的机构。通常是在倒档叉或叉头上装有弹簧机构,使司机在换档时因有弹簧力作用,产生明显的手感。锁止机构还包括自锁、倒档锁两个机构。自锁机构的作用是将滑杆锁定在一定位置,保证齿轮全齿长参加啮合,并防止自动脱档和挂档。自锁机构有球形锁定机构与杆形锁定机构两种类型。倒档锁的作用是使驾驶员必须对变速杆施加更大的力,方能挂入倒档,起到提醒注意的作用,以防误挂倒档,造成安全事故。本次设计属于前置前轮驱动的轿车,操纵机构采用直接操纵方式,锁定机构全部采用,即设置自锁、互锁、倒档锁装置。采用自锁钢球来
32、实现自锁,通过互锁销实现互锁。倒档锁采用限位弹簧来实现,使驾驶员有感觉,防止误挂倒档。2.3本章小结本章主要依据变速器几种常见的传动机构布置方案,对两轴式和中间轴式的变速器的结构特点作了简要说明,分析了各种方案的优缺点,同时介绍了几种常见的倒挡机构布置方案,并比较了各个方案的优缺点。在零部件的选择部分,对变速器齿轮、换挡机构的形式和变速器防止自动脱挡的结构进行了分析和说明。最后结合本次设计所依据车辆的主要技术参数,选择了本设计的传动机构布置方案和零、部件的结构形式,作为以后各章节设计的基础。 第3章 变速器主要参数的选择变速器主要参数的选择本设计是根据瑞麒G52010款梅西版2.0TCI手动舒
33、适性汽车的技术参数来设计的一种汽车变速器,其具体参数如表3.1 : 发动机最大功率125km车轮型号205/60 R16 发动机最大转矩235km最大功率时转速5500rpm最大转矩时转速1900rpm最高车速210km/h 整备质量1598kg变速器形式手动六档 表3.1 瑞麒G5的主要技术参数3.1档数的确定变速器的挡数可在320个挡位范围内变化,通常变速器的挡数在6挡以下,当挡数超过6挡以后,可在6挡以下的主变速器基础上,再行配置副变速器,通过两者的组合获得多挡变速器。增加变速器的挡数,能够改变汽车的动力性和燃油经济性以及平均车速。挡数越多,变速器的结构越复杂,并且使轮廓尺寸和质量加大,
34、同时操纵机构复杂,而且在使用时换挡频率增高并增加了换挡难度。在最低挡传动比不变的条件,增加变速器的挡数会使变速器相邻的低档与高档之间的传动比比值减小,使换挡工作容易进行。要求相邻挡位之间的传动比值在1.8以下,该值越小换挡工作越容易进行。因高挡使用频繁,所以又要求高档区相邻挡位之间的传动比比值,要比低档区相邻挡位之间的传动比比值小。近年来,为了进一步节省燃油,装用手动变速器的轿车普遍采用5挡变速器,也有采用6挡变速器的。本设计采用6挡。3.2 传动比范围变速器传动比范围是指变速器最高档与最低档传动比的比值。最高档通常是直接档,传动比为1.0;有的变速器最高档是超速档,传动比为0.70.8。影响
35、最低档传动比选取的因素有:发动机的最大转矩和最低稳定转速所要求的汽车最大爬坡能力、驱动轮与路面间的附着力、主减速比和驱动轮的滚动半径以及所要求达到的最低稳定行驶车速等。目前乘用车的传动比范围在3.04.5之间,总质量轻些的商用车在5.08.0之间,其它商用车则更大。由于本设计是二轴变速器,所以最高挡是超速档,传动比范围为0.7-0.8.取最高挡传动比为0.75,即ig=0.75。3.3变速器各挡传动比的确定 1、主减速器传动比的确定 发动比的确定动机转速与汽车行驶速度之间的关系式为: = 0.377 (3.1)式中:汽车行驶速度(km/h); 发动机转速(r/min); 车轮滚动半径(m);
36、变速器传动比; 主减速器传动比。已知:最高车速=200 km/h;最高档为超速档,传动比=0.75;车轮滚动半径由所选用的轮胎规格205/60R16.得到r=R=162.54102+2050.6=326.2mm=0.326m;发动机转速=5500(r/min);由公式(3.1)得到主减速器传动比计算公式: =0.377=2、确定最低挡传动比 确定最低挡传动比时,要考虑下列因素:汽车最大爬坡度、驱动轮与地面的附着力、汽车最低稳定车速及主传动比等。1)根据最大爬坡度确定一挡传动比 汽车在最大上坡路面上行驶时,最大驱动力应能克服轮胎与地面间滚动阻力及上坡阻力,由于汽车上坡行驶时,车速不高,忽略空气阻
37、力,这时 + (3.2)式中 最大驱动力,=; 滚动阻力,= fmgcos;最大上坡阻力,=mgsin。 将上述有关参数代入式(3.2)得mg(fmgcos+mgsin)=mg (3.3)式中发动机最大转矩,=240N.m;主减速比,=4.51;m汽车总质量,m=2000kg;道路最大阻力系数;f滚动阻力系数(良好的沥青或混凝土路面f=0.0100.018取f=0.015);变速器一挡传动比;汽车传动系效率,=0.9;g重力加速度,g=9.8;驱动轮滚动半径,=0.326m;道路最大上坡角(最大爬坡度为30%,即=16.7,则sinmax=0.287,cosmax=0.958;将上述有关参数代
38、入式(3.3)得=1.97671.982)根据驱动轮与路面的附着力确定一挡传动比汽车行驶时,为了使驱动轮不打滑,必须使驱动力等于或小于驱动轮与路面间的附着力,此条件可用下列不等式表示 (3.4) (3.5)式中 -路面附着系数,计算时取 =0.6 Fn-驱动轮的地面法向反力,;已知:kg;取0.6,把数据代入(3.5)式得: =3.94所以,一档转动比的选择范围是:故一挡传动比取=2.6 3) 确定其它各挡传动比一般汽车各挡传动比大致符合如下关系 = q (3.6)式中 q常数,也就是各挡之间的公比,q=1.28421.28因此,各挡传动比为=2.6=0.753.4中心距的选择对两轴式变速器,
39、将变速器输入轴与输出轴轴线之间的距离称为变速器中心距A,中心距对变速器的尺寸及质量有直接影响,所选的中心距应能保证齿轮的强度,初选中心距A时,可根据下述经验公式计算: A= (3.7) 式中 A变速器中心距(mm);中心距系数,商用车:8.99.6,多挡变速器:=9.511.0乘用车取=8.99.3, 发动机最大转矩(Nm);变速器一挡传动比;变速器传动效率,=0.96。将上述有关参数代入式(3.7)得A=(8.99.6)=75.02580.926取A=78mm3.5变速器的外形尺寸变速器的横向外形尺寸,可根据齿轮直径以及倒挡中间齿轮和换挡机构的布置初步确定。影响变速器壳体的轴向尺寸的因素有挡
40、数、换挡机构形式以及齿轮形式。乘用车四挡变速器壳体的轴向尺寸为(3.03.4)A。商用车四挡变速器壳体的轴向尺寸可参考下列数据选用:(1)四挡 (2.22.7)A (2)五挡 (2.73.0)A(3)六挡 (3.23.5)A 当变速器选用的挡数和同步器多时,上述中心距系数应取给出范围的上限。为了检测方便,中心距A最好取为整数。轴向尺寸为故初选L=2603.6齿轮参数的确定1.模数的选取齿轮模数是一个重要参数,影响它的选取因素有很多,如齿轮的强度、质量、噪音、工艺要求等。齿轮模数选取的一般原则:1)为了减少噪声应合理减小模数,同时增加齿宽;2)为使质量小些,应该增加模数,同时减少齿宽;3)从工艺
41、方面考虑,各挡齿轮应该选用一种模数;4)从强度方面考虑,各挡齿轮应有不同的模数。 对于轿车,减少工作噪声较为重要,因此模数应选得小些;对于货车,减小质量比减小噪声更重要,因此模数应选得大些。所选模数值应符合国家标准的规定。啮合套和同步器的接合齿多数采用渐近线。由于工艺上的原因同一变速器中的接合齿模数相同。其取值范围是:乘用车和总质量在1.8-14.0t的货车为2.03.5。表3.2 汽车变速器齿轮的法向模数车 型乘用车的发动机排量V/L货车的最大总质量/t1.0V1.61.6V2.56.014模数/mm2.252.752.753.003.504.504.506.00轿车模数的选取以发动机排量作
42、为依据,由表3.2选取各档模数为,由于轿车对降低噪声和振动的水平要求较高,所以各档均采用斜齿轮。2.压力角的选取齿轮压力角较小时,重合度较大并降低了轮齿刚度,为此能减少进入啮合和退出啮合时的动载荷,使传动平稳,有利于降低噪声;压力角较大时,可提高轮齿的抗弯强度和表面接触强度。实际上,因国家规定的标准压力角为20,所以变速器齿轮普遍采用的压力角为20。啮合套或同步器的接合齿压力角为20、25、30等,但普遍采用30压力角。本变速器为了加工方便,故全部选用标准压力角20。3.螺旋角的确定斜齿轮在变速器中得到广泛应用。选取斜齿轮的螺旋角,应注意它对齿轮工作噪声、轮齿的强度和轴向力有影响。在齿轮选用大
43、些的螺旋角时,使齿轮啮合的重合度增加,因而工作平稳、噪声降低。试验还证明:随着螺旋角的增大,齿的强度也相应提高。不过当螺旋角大于30时,其抗弯强度骤然下降,而接触强度仍继续上升。因此,从提高低档齿轮的抗弯强度出发,并不希望用过大的螺旋角,以1525为宜;而从提高高档齿轮的接触强度和增加重合度着眼,应选用较大的螺旋角。斜齿轮螺旋角可在下面提供的范围内选用:(1)乘用车变速器1)两轴式变速器为20252)中间轴式变速器为2234(2)货车变速器:1826所以初选斜齿轮螺旋角。4.齿宽b的确定齿轮宽度b的大小直接影响着齿轮的承载能力,b加大,齿的承载能力增高。但试验表明,在齿宽增大到一定数值后,由于
44、载荷分配不均匀,反而使齿轮的承载能力降低。所以,在保证齿轮的强度条件下,尽量选取较小的齿宽,以有利于减轻变速器的重量和缩短其轴向尺寸。通常根据齿轮模数m()的大小来选定齿宽:(1)直齿b=m, 为齿宽系数,取为4.58.0;(2)斜齿轮b=,取为6.08.5。所以本设计斜齿,取为6.08.5,取6.0mm5.齿轮变位系数的选择原则变位齿轮主要有两类:高度变位和角度变位。高度变位齿轮副的一对啮合齿轮的变位系数的和为零。高度变位可增加小齿轮的齿根强度,使它达到和大齿轮强度想接近的程度。高度变位齿轮副的缺点是不能同时增加一对齿轮的强度,也很难降低噪声。角度变位齿轮副的变位系数之和不等于零。角度变位可
45、获得良好的啮合性能及传动质量指标,故采用得较多。变位系数的选择原则 :1)对于高档齿轮,应按保证最大接触强度和抗胶合及耐磨损最有利的原则选择变位系数。2)对于低档齿轮,为提高小齿轮的齿根强度,应根据危险断面齿厚相等的条件来选择大、小齿轮的变位系数。 3)总变位系数越小,齿轮齿根抗弯强度越低。但易于吸收冲击振动,噪声要小一些。为了降低噪声,对于变速器中除去一、二档以外的其它各档齿轮的总变位系数要选用较小一些的数值。一般情况下,随着档位的降低,总变位系数应该逐档增大。一、二档和倒档齿轮,应该选用较大的值。 6.齿顶高系数的确定齿顶高系数对重合度、齿轮强度、工作噪音、轮齿相对滑动速度、轮齿根切和齿顶
46、厚度等有影响。规定齿顶高系数取1.00。7.齿轮材料的选择变速器齿轮可以与轴设计成一体或与轴分开,然后用花键、过盈配合或者滑动支撑等方式之一与轴连接。齿轮尺寸小又与轴分开,其内径直径到齿顶圆处的厚b影响齿轮强度。要求尺寸b应该大于或等于齿轮危险断面处的厚度。为了使齿轮装在轴上以后,保持足够大的稳定性,齿轮轮毂部分的宽度尺寸,在结构允许条件下应尽可能大一些,至少满足尺寸,为花键内径。为了减小质量,轮辐处厚度应满足强度条件下设计得薄些。齿轮表面粗糙度数值降低,则噪音减小,齿面磨损速度减慢,提高了齿轮寿命。变速器齿轮齿面的表面粗糙度应在范围内选用。要求齿轮制造精度不低于7级。国内汽车变速器齿轮材料主
47、要采用、。渗碳齿轮表面硬度为。心部硬度为。值得指出的是,采用喷丸处理、磨齿、加大齿根圆弧半径和压力角等措施能使齿轮得到强化。3.7 各档齿轮齿数的分配及传动比的计算本设计变速器采用斜齿圆柱轮。斜齿 = (3.8)1.确定一挡齿轮的齿数和传动比一挡传动比为=2.6 =53轿车可在1217之间选取, 为了使尽量大些,应将取得尽量小些,则取=15=38 对中心距A进行修正因为计算齿数和后,经过取整数使中心距有了变化,所以应根据取定的和齿轮变位系数重新计算中心距,再以修正后的中心距作为各挡齿轮齿数分配的依据。取整得mm,为标准中心矩。2.确定二挡齿轮的齿数和传动比 (3.9) (3.10)已知:=80
48、mm,=2.031,=2.75,;将数据代入(3.9)(3.10)两式,齿数取整得:,所以二档传动比为:3、确定三档齿轮的齿数和传动比 (3.11) (3.12)已知:=80mm,=1.587,=2.75,;将数据代入(3.11)(3.12)两式,齿数取整得:,所以三档传动比为:4、确定四档齿轮的齿数和传动比 (3.13) (3.14)已知:=80mm,=1.240,=2.75,;将数据代入(3.13)(3.14)两式,齿数取整得:,所以四档传动比为:5、确定五档齿轮的齿数和传动比 (3.14) (3.16)已知:=80mm,=0.969,=2.75,;将数据代入(3.15)(3.16)两式,
49、齿数取整得:,所以五档传动比为:6、确定六档齿轮的齿数和传动比 (3.17) (3.18)已知:=80mm,=0.75,=2.75,;将数据代入(3.17)(3.18)两式,齿数取整得:,所以六档传动比为:7、确定倒档齿轮的齿数和传动比 初选倒档轴上齿轮齿数为=22,输入轴齿轮齿数=15,为保证倒档齿轮的啮合不产生运动干涉齿轮11和齿轮13的齿顶圆之间应保持有0.5mm以上的间隙,即满足以下公式 (3.19)已知:,把数据代入(3.19)式,齿数取整,解得:,则倒档传动比为:输入轴与倒档轴之间的距离:mm输出轴与倒档轴之间的距离:mm 3.8变速器齿轮的变位及齿轮螺旋角的调整齿轮的变位是齿轮设
50、计中一个非常重要的环节。采用变位齿轮,除为了避免齿轮产生根切和配凑中心距以外,它还影响齿轮的强度,使用平稳性,耐磨损、抗胶合能力及齿轮的啮合噪声。变位齿轮主要有两类:高度变位和角度变位。高度变位齿轮副的一对啮合齿轮的变位系数之和等于零。高度变位可增加小齿轮的齿根强度,使它达到和大齿轮强度相接近的程度。高度变位齿轮副的缺点是不能同时增加一对齿轮的强度,也很难降低噪声。角度变位齿轮副的变位系数之和不等于零。角度变位既具有高度变位的优点,又避免了其缺点。由几对齿轮安装在中间轴和第二轴上组合并构成的变速器,会因保证各挡传动比的需要,使各相互啮合齿轮副的齿数和不同。为保证各对齿轮有相同的中心距,此时应对
51、齿轮进行变位。当齿数和多的齿数副采用标准齿轮传动或高度变位时,对齿数和少些的齿轮副应采用正角度变位。由于角度变位可获得良好的啮合性能及传动质量指标,故采用得较多。对斜齿轮传动,还可以通过选择合适的螺旋角来达到中心距相同的要求。变速器齿轮是在承受循环负荷的条件下工作,有时还承受冲击负荷。对于高挡齿轮,其主要损坏形式是齿面疲劳剥落,因此应按保证最大接触强度和抗胶合及耐磨损最有利的原则选择变位系数。为提高接触强度,应使总变位系数尽可能取大些,这样两齿轮的齿廓渐开线离基圆较远,以增大齿廓曲率半径,减小接触应力。对于低档齿轮,由于小齿轮的齿根强度较低,加之传递载荷较大,小齿轮可能出现齿根弯曲、断裂的现象
52、。为提高小齿轮的抗弯强度,应根据危险断面齿厚相等的条件来选择来选择大小齿轮的变位系数,此时小齿轮的变位系数,此时小齿轮的变位系数大雨零。由于工作需要,有时齿轮齿数取得少(如一挡主动齿轮)会造成轮齿根切。这不仅削弱了轮齿的抗弯强度,而且使重合度减少。此时应对齿轮进行正变位,以消除根切现象。总变位系数减少,一对齿轮齿根总的厚度越薄,齿根越弱,抗弯强度越低。但是由于轮齿的刚度减小,易于吸收冲击振动故噪声要小一些。另外,值越小,齿轮的齿形重合度越大,这不但对降噪有利,而且由于齿形重合度增大,单齿承受最大载荷时的着力点距齿根近,弯曲力矩减小,相当于齿根强度提高,对由于齿根减薄而产生的削弱强度的因素有所抵
53、消。采用变位齿轮的原因:配凑中心距;提高齿轮的强度和使用寿命;降低齿轮的啮合噪声。为了降低噪声,对于变速器中除去一、二档以外的其它各档齿轮的总变位系数要选用较小一些的数值。一般情况下,随着档位的降低,总变位系数应该逐档增大。一、二档和倒档齿轮,应该选用较大的值。变位系数如下图3.1: 图3.1变位系数图倒挡啮合角:计算得:=210查图得:0.42 -0.260.42其余各档啮合角: =21.80查图得:0.35同理计算得:,0.28, -0.22 , 3.9变速器齿轮尺寸的确定本次设计所有齿轮的几何尺寸如表3.5所示。 表3.3斜齿圆柱齿轮的几何尺寸 (mm)齿数153817362132242
54、927263023模数2.752.752.752.752.752.752.752.752.752.752.752.75变位系数0.37-0.020.280.070.220.130.13-0.220.13-0.220.220.13螺旋角212122222424242424242424压力角202020202020202020202020端面模数2.952.952.972.973.013.013.013.013.013.013.013.01端面压力角21.321.321.421.421.721.721.721.721.721.721.721.7分度圆直径38.3512368.1593.272.95
55、91.493.788.6578.682.7587.573.85齿顶高3.772.702.722.452.363.113.112.422.312.702.162.14齿根高2.423.492.672.942.812.063.082.442.422.032.112.13齿全高6.196.195.395.395.175.174.864.864.734.734.374.37齿顶圆直径43.16130.674.1996.0875.6793.6277.9291.9581.8285.0590.7876.22齿根圆直径33.51116.162.8187.3267.3387.2867.5483.7773.767
56、8.6983.2869.59中心距80基圆直径35.7411056.7488.9860.7487.9871.4874.2376.9868.7478.4863.243.10 本章小结本章主要介绍了变速器主要参数的选择,包括确定挡数、传动比范围,根据最大爬坡度和驱动轮与地面的附着力确定一挡传动比和六挡传动比,进而确定其它各挡传动比,选择中心距、外形尺寸以及齿轮参数,根据变速器的传动示意图确定各挡齿轮齿数,进行各挡齿轮变位系数的分配。最后列出了各挡齿轮的几何尺寸。这些为之后齿轮、轴的设计计算做好了准备。 第4章 变速器齿轮及轴强度校核4.1 变速器齿轮强度校核 4.1.1变速器齿轮弯曲强度校核 mmmmmmrad输出轴的挠度和转角的计算:输出轴上作用力与输入轴上作用力大小相等,方向相反。已知:a=25mm;b=236mm;L=261mm;d=45mm,把有关数据代入(4.11)、(4.12)、(4.13)得到:
- 温馨提示:
1: 本站所有资源如无特殊说明,都需要本地电脑安装OFFICE2007和PDF阅读器。图纸软件为CAD,CAXA,PROE,UG,SolidWorks等.压缩文件请下载最新的WinRAR软件解压。
2: 本站的文档不包含任何第三方提供的附件图纸等,如果需要附件,请联系上传者。文件的所有权益归上传用户所有。
3.本站RAR压缩包中若带图纸,网页内容里面会有图纸预览,若没有图纸预览就没有图纸。
4. 未经权益所有人同意不得将文件中的内容挪作商业或盈利用途。
5. 装配图网仅提供信息存储空间,仅对用户上传内容的表现方式做保护处理,对用户上传分享的文档内容本身不做任何修改或编辑,并不能对任何下载内容负责。
6. 下载文件中如有侵权或不适当内容,请与我们联系,我们立即纠正。
7. 本站不保证下载资源的准确性、安全性和完整性, 同时也不承担用户因使用这些下载资源对自己和他人造成任何形式的伤害或损失。