汽车前围板拉延成形模面及工艺优化
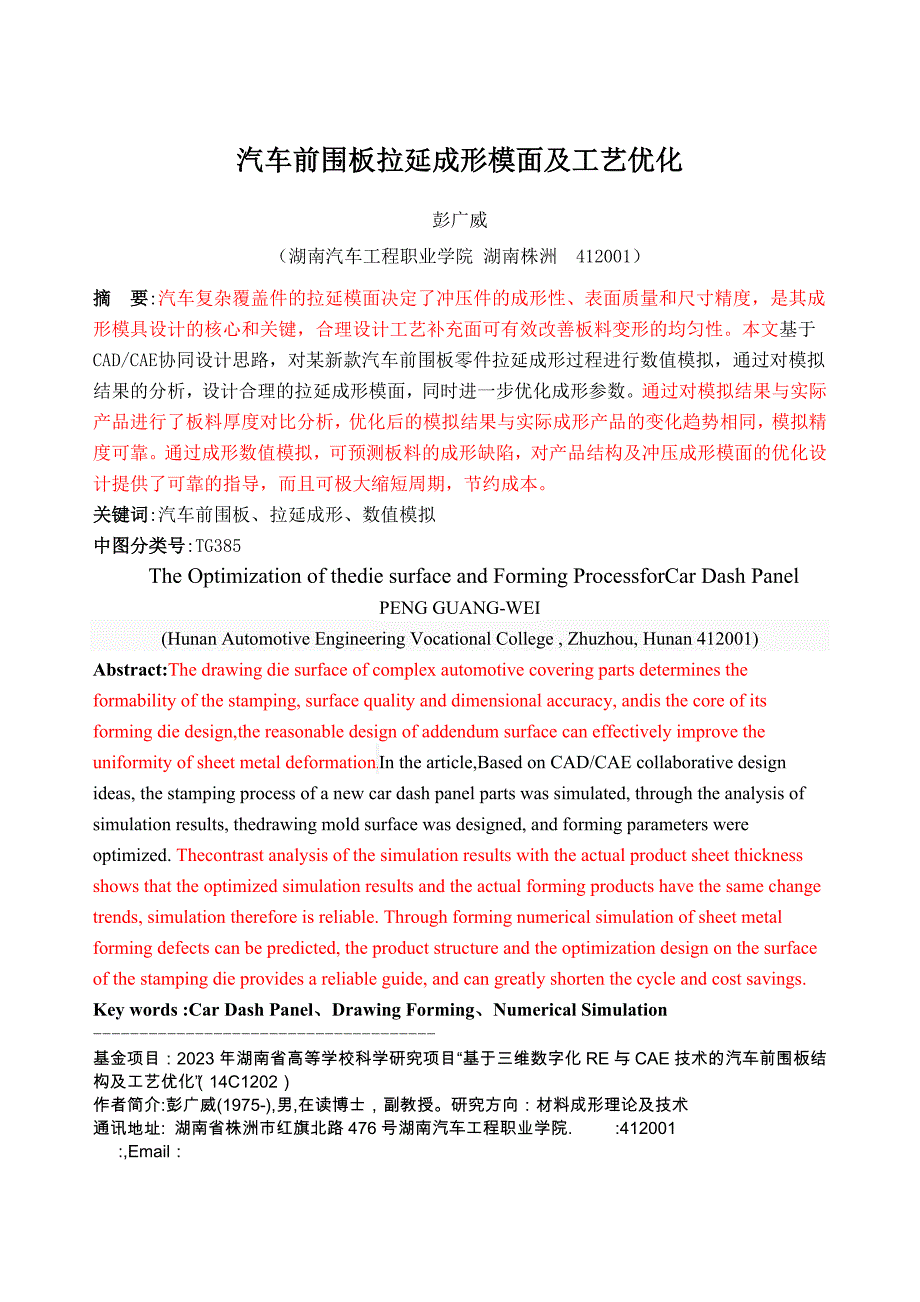


《汽车前围板拉延成形模面及工艺优化》由会员分享,可在线阅读,更多相关《汽车前围板拉延成形模面及工艺优化(7页珍藏版)》请在装配图网上搜索。
1、汽车前围板拉延成形模面及工艺优化彭广威(湖南汽车工程职业学院 湖南株洲412001)摘要:汽车复杂覆盖件的拉延模面决定了冲压件的成形性、表面质量和尺寸精度,是其成形模具设计的核心和关键,合理设计工艺补充面可有效改善板料变形的均匀性。本文基于CAD/CAE协同设计思路,对某新款汽车前围板零件拉延成形过程进行数值模拟,通过对模拟结果的分析,设计合理的拉延成形模面,同时进一步优化成形参数。通过对模拟结果与实际产品进行了板料厚度对比分析,优化后的模拟结果与实际成形产品的变化趋势相同,模拟精度可靠。通过成形数值模拟,可预测板料的成形缺陷,对产品结构及冲压成形模面的优化设计提供了可靠的指导,而且可极大缩短
2、周期,节约成本。关键词:汽车前围板、拉延成形、数值模拟中图分类号:TG385The Optimization of thedie surface and Forming ProcessforCar Dash Panel PENG GUANG-WEI(Hunan Automotive Engineering Vocational College , Zhuzhou, Hunan 412001)Abstract:The drawing die surface of complex automotive covering parts determines the formability of the
3、 stamping, surface quality and dimensional accuracy, andis the core of its forming die design,the reasonable design of addendum surface can effectively improve the uniformity of sheet metal deformation.In the article,Based on CAD/CAE collaborative design ideas, the stamping process of a new car dash
4、 panel parts was simulated, through the analysis of simulation results, thedrawing mold surface was designed, and forming parameters were optimized. Thecontrast analysis of the simulation results with the actual product sheet thickness shows that the optimized simulation results and the actual formi
5、ng products have the same change trends, simulation therefore is reliable. Through forming numerical simulation of sheet metal forming defects can be predicted, the product structure and the optimization design on the surface of the stamping die provides a reliable guide, and can greatly shorten the
6、 cycle and cost savings.Key words :Car Dash Panel、Drawing Forming、Numerical Simulation-基金项目:2023年湖南省高等学校科学研究项目“基于三维数字化RE与CAE技术的汽车前围板结构及工艺优化”(14C1202)作者简介:彭广威(1975-),男,在读博士,副教授。研究方向:材料成形理论及技术通讯地址: 湖南省株洲市红旗北路476号湖南汽车工程职业学院. :412001 :,Email:1、引言汽车前围板是汽车发动机舱与车厢之间的隔板,为典型的汽车覆盖件零件,与一般冲压件相比,具有材料薄、尺寸大、结构复杂、材
7、料强度高、表面质量要求高等特点。覆盖件成形的基本工序包括:拉延、修边及翻边等,其中拉延成形工序最为关键1。本文采用有限元分析软件Dynaform对某款新型车的前围板零件的拉延成形进行了模拟仿真,通过模拟分析,利用CAD软件对零件的成形模面进行了优化设计,并进一步调整成形工艺,合理设置拉延筋,从而避免了开裂和起皱等成形缺陷,保证了工件质量,CAD/CAE的协同设计能有效指导汽车覆盖件产品的开发与生产2。2、零件的工艺性分析及数模预处理汽车前围板零件如图1所示,材料为DC06。零件的长、宽、高的尺寸约为1400mm540mm210mm, 材料厚度为1.6mm。零件表面有20个大小各异的孔,而且在零
8、件的两端和中间存在明显的高度差,零件成形工艺较复杂,主要包括拉延、切边冲孔、翻边、冲孔整形等工序。本零件的冲压成形质量主要取决于第一道拉延工序,因其形状复杂,必须通过数值模拟分析其拉延成形工艺性,以设计合理的拉延模面及成形工艺参数3。图1 汽车前围板零件Fig.1 Car Dash Panel3、预成形模拟与结果分析在对零件进行结构与工艺优化之前,利用Dynaform软件进行冲压成形预模拟,分析零件的成形工艺性,分析板料的变形状态与规律,找出存在开裂及起皱等缺陷的地方,然后有针对性地对零件拉延模面结构及成形工艺进行改进和优化。3.1产品模型预处理产品的翻边、凸缘及孔洞一般都是通过后续工序成形出
9、来的,故拉延工序模拟时,需对原始零件数字模拟进行预处理。数模的预处理是将原始零件中的孔洞填充、翻边展平、边界面的延伸以及调整冲压成形方向,生成拉延工序成形的曲面数模。为减少在Dynaform中对模型进行设置与操作的工作量,零件曲面数模的预处理可先在三维CAD软件中进行,完成后的凹模曲面模型如图2所示。图2 零件数模的预处理Fig.2Preproccess of the digital model3.2 预模拟分析模型该零件材料为国产冷轧低碳钢DC06,模拟时采用材料库中的DC06#36材料模型,其相关参数定义如表1所示。表1 材料参数Table1 Material parameters材料牌号
10、板料厚度t/mm屈服强度/MPa抗拉强度/MPa泊松比弹性模量E/GPa强化系数K硬化指数N各向异性系数R00R45R90DC061.601803500.282076480.221.621.552.10在将模型调入到Dynaform中后,通过偏置凹模的方法生成凸模和压边圈,模型中凸模、凹模及压边圈均定义为刚性材料。分析中采用 Belytschko-Tsay薄壳元理论,坯料的网格采用自适应划分,等级为3可满足零件的成形要求4。凸、凹模单边间隙采用1.1t,即1.76mm,毛坯与模具部件间的摩擦系数为 0.125,压边力根据公式F=Aq初步计算取300KN,成形速度 3000mm/s,压边速度 2
11、000mm/s。3.3预模拟成形结果分析预模拟成形的FLD如图3所示。从图中可看到:(1)前中间内凹转角处(A、B处)有开裂危险外,板料多数地方有严重起皱或呈起皱趋势。通过分析冲压模拟过程得知:A、B处的开裂危险是因为直边面拉延过深,变形程度大而过渡圆角太小,同时C、D处的严重起皱,造成该处板料无法顺利流动补给;(2)板料四个角E、F、G、H等区域出现严重起皱,是由于两侧的凹面较平坦,变形程度过小,板料流入凹模后形成褶皱;(3)后侧I、J等区域出现严重起皱是由于后侧面过于平缓,板变形程度小而造成板料堆积所致;(4)顶部K、L等区域出现严重起皱,而其它部分区域板料未充分变形,是由于压料面不平顺,
12、进料不均匀,一部分区域材料流动阻力小,材料较多地流入凹模型腔形成褶皱,另一部分区域材料流动阻力大,造成零件后平面部位及两侧球凹面成形不充分,局部区域未达到预期的形状,模拟成形产品的质量不符合要求。图3预模拟成形FLD图Fig.3 FLD of PreparatoryBlank Forming4、凹模型面结构优化及工艺优化分析成形失效原因后,拟从以下三个方面进行改进:(1)根据模拟结果增加工艺补充面,在出现严重起皱区域增加拉延台,通过拉延台吸收变形时多余的材料,从而改善板料变形的均匀性;(2)进一步光顺轮廓边界,设计合理的压料,以保证材料的流动性;(3)根据模拟变形过程分段设置拉延筋,并优化其相
13、关参数。4.1拉延凹模型面优化拉延凹模面的型面优化主要包括压料面优化及拉延零件工艺补充面设计。压料面及工艺补充面设计如图4所示。主要包括:图4 优化后的凹模曲面模型Fig.4The Optimized Die Surface Model(1)根据前后两侧零件的拉延高度变化利用截面法设计平滑压模曲面5,模口圆角取810mm。(2)在前端A、B等可能出现应力集中而开裂的地方增设前后拉延变形过渡台阶,减小直边拉延高度,留下部分区域在后续的切边、翻边及整形工序中再进行成形。(3)在两侧凹面处增加拉延台,以改善零件各方向变形的均匀性,使两侧充分拉延,避免因材料流入凹模内堆积而造成E、F、G、H等区域起皱
14、的问题。这部分的拉延特征要在后续的切边工序中切除,然后再进行侧端翻边,所以要预留足够的切边尺寸。(4)将后侧的翻边面进行侧向延伸补充成拉延台,不仅可改善板料变形的均匀性,避免I、J处的起皱,同时可直接将后侧翻边成形,多余板料在后续工序中进行切除。4.2成形工艺优化将优后化的曲面模型重新导入Dynaform,为了调节板料流进模腔的进料阻力,需在压料面上适当位置设置拉延筋,在有限元仿真分析中,采用等效拉深阻力代替实际拉深筋,拉延筋为复杂的空间曲线,离模口的距离取30mm。经多次模拟优化,最终设置的拉延筋位置如5所示,设定其完全锁模力为500N。因顶部成形特征较复杂,为保证质量,将模具单边间隙调整为
15、5%,模面优化后的压边力取240KN。图5 拉延筋的设置 Fig.5The Draw-bead Setting4.3优化后的模拟结果经多次参数优化后的成形模拟FLD如图6所示。在成形零件的有效区域内,开裂危险区和严重起皱区基本消除,起皱趋势区大幅度减小,产品各成形区域达到预期的形状,表面较为光整平滑,质量符合要求。图6 优后化的成形FLD图 Fig.6 FLD of OptimizedBlank Forming4.4 成形产品的对比分析通过模面及工艺参数优化后的成形产品实物如图7所示。图7 成形产品实物Fig.7The Real Forming Product通过观察对比,产品补面区和压边区的
16、局部起皱区域与模拟结果能较好的吻合。为进一步验证数值模拟精度,选择了如图8模拟结果中所示几处关键部位与产品实物进行了厚度对比,其中A、B、C、D、E处为变薄较严重区,F、G、H、I、J处为变厚较严重区。对比结果如表2所示。图8 板料模拟成形的厚度变化Fig.8 The Thickness of The Sheet Forming Simulation表2 模拟结果与产品实物的厚度对比Table2 The simulation results compared with the thickness of the product部位模拟厚度值(mm)产品厚度值(mm)偏差值(mm)A1.151.2
17、1+0.06B1.281.27-0.01C1.301.32+0.02D1.161.23+0.07E1.181.29+0.11F1.781.77-0.01G1.841.80-0.04H1.761.78+0.02I1.731.78+0.06J1.741.82+0.08由对比数值可得:模拟结果与实物成形后的厚度变化基本趋势相同,整体模拟精度较高,但也存在一些厚度值的偏差。分析原因主要有:(1)数字模面的一些转角通过多次倒圆角而成,并不光顺,而实际模具的转角曲面是通过钳工多次修磨,在冲压润滑剂的作用下减轻了变薄趋势,如A、D处;(2)实际板料的各向异性与模拟时的板料参数有一定差别,同时因为压边力误差的
18、存在,从而使得部分区域的偏差值较大,如I、J处。4、结论(1) 通过CAE/CAD协同设计,根据模拟结果,反复对汽车前围板的成形模面及成形工艺进行了优化设计,优化后的模拟结果与实际成形产品的厚度变化趋势相同,模拟精度可靠。(2) 拉延模面决定了冲压件的成形性、表面质量和尺寸精度,是复杂覆盖件成形模具设计的核心和关键,合理设计工艺补充面可有效改善板料变形的均匀性。(3)通过成形数值模拟,可预测板料的成形缺陷,对产品结构及冲压成形模面的优化设计提供了可靠的指导,而且可极大缩短周期,节约成本6。参考文献:1 王秀凤,郎利辉.板料成形CAE设计及应用 M.北京:北京航空航天大学出版社,2023.1.1
19、05-119.Wang Xiufeng, Lang Lihui. Sheet Metal Forming CAE Design and ApplicationM. Beijing: Beijing University of Aeronautics and Astronautics Press, 2023.1.105-119.2 陈文琳, 李志杰, 王少阳. 汽车前围板冲压数值模拟及工艺参数优化J.精密成形工程,2023.3(3):15-19.Chen Wenlin, Li Zhijie, Wang Shaoyang. Numerical Simulation and Parameter Op
20、timizing of the Stamping Forming Process of Auto Front PanelJ. Journal of Net-Shape Forming Engineering, 011.3(3):15-19.3 陈泷,陈炜,单英,等. 复杂车身覆盖件拉深模具模面设计研究 J. 热加工工艺,2023,43(7):89-91.Chen Long, Chen Wei, Shan Ying,etc. Study on Die Face Design of Complex Automobile Panel Drawing DieJ. Hot Working Technol
21、ogy,2023,43(7):89-91.4 彭广威. 汽车仪表盘支架数值模拟与工艺优化J. 热加工工艺,2023,42(19):95-99.Peng Guangwei. Numerical Simulation and Technology Optimization on Forming ofInstrument Board Bracket for AutomobileJ. Hot Working Technology,2023,42(19):95-99.5 胡平. 汽车覆盖件模具设计M . 北京:机械工业出版社,2023.3. 102-118.Hu ping. automobilepane
22、ldiedesignM. Beijing:China MachinePress,2023.3. 102-118.6苏春建,于涛.金属板材成形CAE分析及应用M.北京:国防工业出版社,2023.5.198-213.SuChunjian, YuTao. Sheet Metal Forming CAE Analysis and ApplicationM.Beijing:NationalDefenceIndustryPress,2023.5.198-213.专家审稿意见:文章基于CAD/CAE协同设计思路,用DYNAFORM软件对汽车前围板零件的拉延成形过程进行了数值模拟,并与实物进行了比对,验证了模
23、拟的结果,通过模拟设计的合理拉延成形模面,及优化的成形工艺参数,得到了合格的成形产品。结论有一定的应用价值。但是对比结果存在明显的不足,只用一张实物图进行对比远远不够,应添加一些关键点处的厚度值的对比,才能更清楚地说明模拟的精度,请务必补充。您的修改稿(15216)存在如下问题:缺少修改说明。您需要对“专家审查意见”逐条做出书面修改说明或答复。也就是说,如果您同意专家的修改建议,就要详细地说明是怎样修改的,如果不同意专家的意见,就要说明不同意的理由。所有修改之处、以及文中参考文献标引号都应使用红色字。摘要过于笼统、空洞,缺乏结果、结论性内容,摘要部分未能概括全文核心内容和主要结果、结论,请务必
24、补充,如有量化的结果最好,可从结论部分选取比较重要的内容补充带摘要中。摘要字数为250字左右。原文为非英文(即中文、俄文、日文等)的参考文献,需要同时给出对应的英文。请登录本刊网站,查看“投稿指南” 栏目,按其中要求对贵稿的参考文献进行修改。参考文献中作者的英文姓名应统一采用“Wang Xiaomei ”这种写法。修改说明:1. 针对专家提出的修改意见,做了如下补充:添加了“4.4 成形产品的对比分析”整节,详细对比分析了模拟结果与实际成形产品的多个关键部位的厚度变化情况,添加了“图8”和“表2”。2. 图“6”选用另一张成形FLD图更清晰。3. 进一步修改完善了中英文摘要至257字。4. 修改调整了部分参考文献,并对于非英文参考文献,添加了英文部分。5. 将基金项目及作者情况介绍移到首页末尾。6. 另小错误的修正见文中红字部分。谢谢!
- 温馨提示:
1: 本站所有资源如无特殊说明,都需要本地电脑安装OFFICE2007和PDF阅读器。图纸软件为CAD,CAXA,PROE,UG,SolidWorks等.压缩文件请下载最新的WinRAR软件解压。
2: 本站的文档不包含任何第三方提供的附件图纸等,如果需要附件,请联系上传者。文件的所有权益归上传用户所有。
3.本站RAR压缩包中若带图纸,网页内容里面会有图纸预览,若没有图纸预览就没有图纸。
4. 未经权益所有人同意不得将文件中的内容挪作商业或盈利用途。
5. 装配图网仅提供信息存储空间,仅对用户上传内容的表现方式做保护处理,对用户上传分享的文档内容本身不做任何修改或编辑,并不能对任何下载内容负责。
6. 下载文件中如有侵权或不适当内容,请与我们联系,我们立即纠正。
7. 本站不保证下载资源的准确性、安全性和完整性, 同时也不承担用户因使用这些下载资源对自己和他人造成任何形式的伤害或损失。