元素对钢的性能的影响及裂纹的形成和影响范文
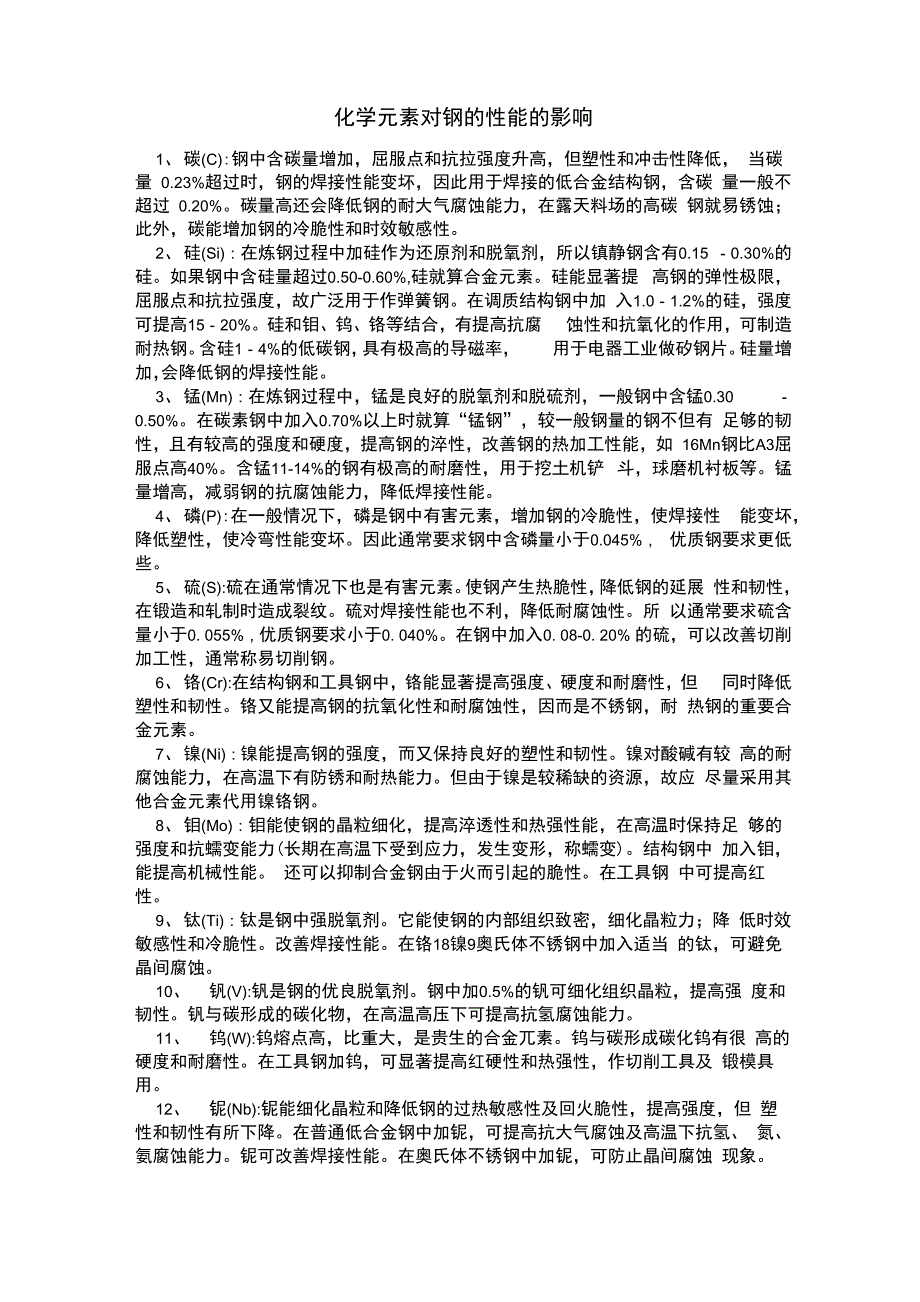


《元素对钢的性能的影响及裂纹的形成和影响范文》由会员分享,可在线阅读,更多相关《元素对钢的性能的影响及裂纹的形成和影响范文(7页珍藏版)》请在装配图网上搜索。
1、化学元素对钢的性能的影响1、碳(C):钢中含碳量增加,屈服点和抗拉强度升高,但塑性和冲击性降低, 当碳量 0.23%超过时,钢的焊接性能变坏,因此用于焊接的低合金结构钢,含碳 量一般不超过 0.20%。碳量高还会降低钢的耐大气腐蚀能力,在露天料场的高碳 钢就易锈蚀;此外,碳能增加钢的冷脆性和时效敏感性。2、硅(Si):在炼钢过程中加硅作为还原剂和脱氧剂,所以镇静钢含有0.15 0.30%的硅。如果钢中含硅量超过0.50-0.60%,硅就算合金元素。硅能显著提 高钢的弹性极限,屈服点和抗拉强度,故广泛用于作弹簧钢。在调质结构钢中加 入1.01.2%的硅,强度可提高1520%。硅和钼、钨、铬等结合
2、,有提高抗腐 蚀性和抗氧化的作用,可制造耐热钢。含硅14%的低碳钢,具有极高的导磁率, 用于电器工业做矽钢片。硅量增加,会降低钢的焊接性能。3、锰(Mn):在炼钢过程中,锰是良好的脱氧剂和脱硫剂,一般钢中含锰0.30 0.50%。在碳素钢中加入0.70%以上时就算“锰钢”,较一般钢量的钢不但有 足够的韧性,且有较高的强度和硬度,提高钢的淬性,改善钢的热加工性能,如 16Mn钢比A3屈服点高40%。含锰11-14%的钢有极高的耐磨性,用于挖土机铲 斗,球磨机衬板等。锰量增高,减弱钢的抗腐蚀能力,降低焊接性能。4、磷(P):在一般情况下,磷是钢中有害元素,增加钢的冷脆性,使焊接性 能变坏,降低塑性
3、,使冷弯性能变坏。因此通常要求钢中含磷量小于0.045%, 优质钢要求更低些。5、硫(S):硫在通常情况下也是有害元素。使钢产生热脆性,降低钢的延展 性和韧性,在锻造和轧制时造成裂纹。硫对焊接性能也不利,降低耐腐蚀性。所 以通常要求硫含量小于0. 055%,优质钢要求小于0. 040%。在钢中加入0. 08-0. 20% 的硫,可以改善切削加工性,通常称易切削钢。6、铬(Cr):在结构钢和工具钢中,铬能显著提高强度、硬度和耐磨性,但 同时降低塑性和韧性。铬又能提高钢的抗氧化性和耐腐蚀性,因而是不锈钢,耐 热钢的重要合金元素。7、镍(Ni):镍能提高钢的强度,而又保持良好的塑性和韧性。镍对酸碱有
4、较 高的耐腐蚀能力,在高温下有防锈和耐热能力。但由于镍是较稀缺的资源,故应 尽量采用其他合金元素代用镍铬钢。8、钼(Mo):钼能使钢的晶粒细化,提高淬透性和热强性能,在高温时保持足 够的强度和抗蠕变能力(长期在高温下受到应力,发生变形,称蠕变)。结构钢中 加入钼,能提高机械性能。 还可以抑制合金钢由于火而引起的脆性。在工具钢 中可提高红性。9、钛(Ti):钛是钢中强脱氧剂。它能使钢的内部组织致密,细化晶粒力;降 低时效敏感性和冷脆性。改善焊接性能。在铬18镍9奥氏体不锈钢中加入适当 的钛,可避免晶间腐蚀。10、钒(V):钒是钢的优良脱氧剂。钢中加0.5%的钒可细化组织晶粒,提高强 度和韧性。钒
5、与碳形成的碳化物,在高温高压下可提高抗氢腐蚀能力。11、钨(W):钨熔点高,比重大,是贵生的合金兀素。钨与碳形成碳化钨有很 高的硬度和耐磨性。在工具钢加钨,可显著提高红硬性和热强性,作切削工具及 锻模具用。12、铌(Nb):铌能细化晶粒和降低钢的过热敏感性及回火脆性,提高强度,但 塑性和韧性有所下降。在普通低合金钢中加铌,可提高抗大气腐蚀及高温下抗氢、 氮、氨腐蚀能力。铌可改善焊接性能。在奥氏体不锈钢中加铌,可防止晶间腐蚀 现象。13、钴(Co):钴是稀有的贵重金属,多用于特殊钢和合金中,如热强钢和磁性 材料。14、铜(Cu):武钢用大冶矿石所炼的钢,往往含有铜。铜能提高强度和韧性, 特别是大
6、气腐蚀性能。缺点是在热加工时容易产生热脆,铜含量超过 0.5%塑性 显著降低。当铜含量小于 0.50%对焊接性无影响。15、铝(Al):铝是钢中常用的脱氧剂。钢中加入少量的铝,可细化晶粒,提高 冲击韧性,如作深冲薄板的 08Al 钢。铝还具有抗氧化性和抗腐蚀性能,铝与铬、 硅合用,可显著提高钢的高温不起皮性能和耐高温腐蚀的能力。铝的缺点是影响 钢的热加工性能、焊接性能和切削加工性能。16、硼(B):钢中加入微量的硼就可改善钢的致密性和热轧性能,提高强度。17、氮(N):氮能提高钢的强度,低温韧性和焊接性,增加时效敏感性。18、稀土 (Xt):稀土元素是指元素周期表中原子序数为57-71的15个
7、镧系元 素。这些元素都是金属,但他们的氧化物很象“土”,所以习惯上称稀土。钢中 加入稀土,可以改变钢中夹杂物的组成、形态、分布和性质,从而改善了钢的各 种性能,如韧性、焊接性,冷加工性能。在犁铧钢中加入稀土,可提高耐磨性。见淬火裂纹有以下 10 种类型模具钢热处理中,淬火是常见工序。然而,因种种原因,有时难免会产生淬火 裂纹,致使前功尽弃。分析裂纹产生原因,进而采取相应预防措施,具有显著的 技术经济效益。常见淬火裂纹有以下 10种类型。1 纵向裂纹裂纹呈轴向,形状细而长。当模具完全淬透即无心淬火时,心部转变为比容最 大的淬火马氏体,产生切向拉应力,模具钢的含碳量愈高,产生的切向拉应力愈 大,当
8、拉应力大于该钢强度极限时导致纵向裂纹形成。以下因素又加剧了纵向裂 纹的产生:钢中含有较多S、P、Sb、Bi、Pb、Sn、As等低熔点有害杂质,钢 锭轧制时沿轧制方向呈纵向严重偏析分布,易产生应力集中形成纵向淬火裂纹或 原材料轧制后快冷形成的纵向裂纹未加工掉保留在产品中导致最终淬火裂纹扩 大形成纵向裂纹;(2)模具尺寸在钢的淬裂敏感尺寸范围内(碳工具钢淬裂危险尺 寸为8-15mm,中低合金钢危险尺寸25-40mm)或选择的淬火冷却介质大大超过该 钢的临界淬火冷却速度时均易形成纵向裂纹。预防措施:(1)严格原材料入库检查,对有害杂质含量超标钢材不投产;(2) 尽量选用真空冶炼、炉外精炼或电渣重熔模
9、具钢材;(3)改进热处理工艺,采用 真空加工热、保护气氛加热和充分脱氧盐浴炉加热及分析淬火、等温淬火;(4) 变无心淬火为有心淬火即不完全淬透,获得强韧性高的下贝氏体组织等措施,大幅度降低拉应力,能有效避免模具纵向开裂和淬火畸变。2 横向裂纹裂纹特征是垂直于轴向。未淬透模具,在淬硬区与未淬硬区过渡部分存在大 的拉应力峰值,大型模具快速冷却时易形成大的拉应力峰值,因形成的轴向应力 大于切向应力,导致产生横向裂纹。锻造模块中s、P、Sb、Bi、Pb、Sn、As等 低熔点有害杂质的横向偏析或模块存在横向显微裂纹,淬火后经扩展形成横向裂 纹。预防措施:(1)模块应合理锻造,原材料长度与直径之比即锻造比
10、最好选在 2-3之间,锻造之间双十字形变向锻造,经五镦五拔多火锻造,使钢中碳化物和 杂质呈细、小、匀分布于钢基体,锻造纤维组织围绕型腔无定向分布,大幅度提 高模块横向力学性能,减少和消除应力源;(2)选择理想的冷却速度和冷却介质: 在钢的Ms点以上快冷,大于该钢临界淬火冷却速度,钢中过冷奥氏体产生的应 力为热应力,表层为压应力,内层为张应力,相互抵消,有效防止热应力裂纹形 成,在钢的 Ms-Mf 之间缓冷,大幅度降低形成淬火马氏体时的组织应力。当钢中 热应力与相应应力总和为正(张应力)时,则易淬裂,为负时,则不易淬裂。充分 利用热应力,降低相变应力,控制应力总和为负,能有效避免横向淬火裂纹发生
11、。 CL-1 有机淬火介质是较理想淬火剂,同时可减少和避免淬火模具畸变,还可控 制硬化层合理分布。调正 CL-1 淬火剂不同浓度配比,可得到不同冷却速度,获 得所需硬化层分布,满足不同模具钢需求。3 弧状裂纹常发生在模具棱角、凸台、刀纹、尖角、直角、缺口、孔穴、凹模接线飞边等 形状突变处。这是因为,淬火时棱角处产生的应力是平滑表面平均应力的 10 倍。 另外,(1)钢中含碳(C)量和合金兀素含量愈高,钢Ms点愈低,Ms点降低2U, 则淬裂纹倾向增加12倍,Ms点降低8,淬裂倾向则增加8倍;钢中不同 组织转变和相同组织转变不同时性,由于不同组织比容差,造成巨大组织应力, 导致组织交界处形成弧状裂
12、纹;(3)淬火后未及时回火,或回火不充分,钢中残 余奥氏体未充分转变,保留在使用状态中,促使应力重新分布,或模具服役时残 余奥氏体发生马氏体相变产生新的内应力,当综合应力大于该钢强度极限时便形 成弧状裂纹;(4)具有第二类回火脆性钢,淬火后高温回火缓冷,导致钢中 P、S 等有害杂质化合物沿晶界析出,大大降低晶界结合力和强韧性,增加脆性,服役 时在外力作用下形成弧状裂纹。预防措施:(1)改进设计,尽量使形状对称,减少形状突变,增加工艺孔与加 强筋,或采用组合装配;(2)圆角代直角及尖角锐边,贯穿孔代盲孔,提高加工 精度和表面光洁度,减少应力集中源,对于无法避免直角、尖角锐边、盲孔等处 一般硬度要
13、求不高,可用铁丝、石棉绳、耐火泥等进行包扎或填塞,人为造成冷 却屏障,使之缓慢冷却淬火,避免应力集中,防止淬火时弧状裂纹形成;(3)淬 火钢应及时回火,消除部分淬火内应力,防止淬火应力扩展;(4)较长时间回火, 提高模具抗断裂韧性值:(5)充分回火,得到稳定组织性能;(6)多次回火使残余 奥氏体转变充分和消除新的应力;(7)合理回火,提高钢件疲劳抗力和综合机械 力学性能;(8)对于有第二类回火脆性模具钢高温回火后应快冷(水冷或油冷), 可消除二类回火脆性,防止和避免淬火时弧状裂纹形状。4 剥离裂纹模具服役时在应力作用下,淬火硬化层一块块从钢基体中剥离。因模具表层组 织和心部组织比容不同,淬火时
14、表层形成轴向、切向淬火应力,径向产生拉应力, 并向内部突变,在应力急剧变化范围较窄处产生剥离裂纹,常发生于经表层化学 热处理模具冷却过程中,因表层化学改性与钢基体相变不同时性引起内外层淬火 马氏体膨胀不同时进行,产生大的相变应力,导致化学处理渗层从基体组织中剥 离。如火焰表面淬硬层、高频表面淬硬层、渗碳层、碳氮共渗层、渗氮层、渗硼 层、渗金属层等。化学渗层淬火后不宜快速回火,尤其是300C以下低温回火快 速加热,会促使表层形成拉应力,而钢基体心部及过渡层形成压缩应力,当拉应 力大于压缩应力时,导致化学渗层被拉裂剥离。预防措施:(1)应使模具钢化学渗层浓度与硬度由表至内平缓降低,增强渗 层与基体
15、结合力,渗后进行扩散处理能使化学渗层与基体过渡均匀;(2)模具钢 化学处理之前进行扩散退火、球化退火、调质处理,充分细化原始组织,能有效 防止和避免剥离裂纹产生,确保产品质量。5 网状裂纹裂纹深度较浅,一般深约001一15mm,呈辐射状,别名龟裂。原因主要有:(1)原材料有较深脱碳层,冷却削加工未去除,或成品模具在氧化气氛炉中加热 造成氧化脱碳;(2)模具脱碳表层金属组织与钢基体马氏体含碳量不同,比容不 同,钢脱碳表层淬火时产生大的拉应力,因此,表层金属往往沿晶界被拉裂成网 状;(3)原材料是粗晶粒钢,原始组织粗大,存在大块状铁素体,常规淬火无法 消除,保留在淬火组织中,或控温不准,仪表失灵,
16、发生组织过热,甚至过烧, 晶粒粗化,失去晶界结合力,模具淬火冷却时钢的碳化物沿奥氏体晶界析出,晶 界强度大大降低,韧性差,脆性大,在拉应力作用下沿晶界呈网状裂开。预防措施:(1)严格原材料化学成分、金相组织和探伤检查,不合格原材料 和粗晶粒钢不宜作模具材料;(2)选用细晶粒钢、真空电炉钢,投产前复查原材 料脱碳层深度,冷切削加工余量必须大于脱碳层深度;(3)制订先进合理热处理 工艺,选用微机控温仪表,控制精度达到土 1.5C,定时现场校验仪表;(4)模具 产品最终处理选用真空电炉、保护气氛炉和经充分脱氧盐浴炉加热模具产品等措 施,有效防止和避免网状裂纹形成。6 冷处理裂纹模具钢多为中、高碳合金
17、钢,淬火后还有部分过冷奥氏体未转变成马氏体,保 留在使用状态中成为残余奥氏体,影响使用性能。若置于零度以下继续冷却,能 促使残余奥氏体发生马氏体转变,因此,冷处理的实质是淬火继续。室温下淬火 应力和零度下淬火应力叠加,当叠加应力超过该材料强度极限时便形成冷处理裂 纹。预防措施:(1)淬火后冷处理之前将模具置于沸水中煮30-60min,可消除 15%-25%淬火内应力并使残余奥氏体稳定化,再进行-60C常规冷处理,或进行 -120C深冷处理,温度煎低,残余奥氏体转变成马氏体量煎多,但不可能全部转 变完,实验表明,约有2-5残余奥氏体保留下来,按需要保留少量残余奥氏 体可松驰应力,起缓冲作用,因残
18、余奥氏体又软又韧,能部分吸收马氏体化急剧 膨胀能量,缓和相变应力;(2)冷处理完毕后取出模具投入热水中升温,可消除 40-60冷处理应力,升温至室温后应及时回火,冷处理应力进一步消除,避 免冷处理裂纹形成,获得稳定性组织性能,确保模具产品存放和使用中不发生畸7 磨削裂纹常发生在模具成品淬火、回火后磨削冷加工过程中,多数形成的微细裂纹与磨 削方向垂直,深约0.05-1.0mm( 1)原材料预处理不当,未能充分消除原材料块 状、网状、带状碳化物和发生严重脱碳;(2)最终淬火加热温度过高,发生过热, 晶粒粗大,生成较多残余奥氏体;(3)在磨削时发生应力诱发相变,使残余奥氏 体转变为马氏体,组织应力大
19、,加上因回火不充分,留有较多残余拉应力,与磨 削组织应力叠加,或因磨削速度、进刀量大及冷却不当,导致金属表层磨削热急 剧升温至淬火加热温度,随之磨削液冷却,造成磨削表层二次淬火,多种应力综 合,超过该材料强度极限,便引起表层金属磨削裂纹。预防措施:(1)对原材料进行改锻,多次双十字形变向镦拔锻造,经四镦四 拔,使锻造纤维组织围绕型腔或轴线呈波浪形对称分布,并利用最后一火高温余 热进行淬火,接着高温回火,能充分消除块状、网状、带状和链状碳化物,使碳 化物细化至2-3级;(2)制订先进的热处理工艺,控制最终淬火残余奥氏体含量 不超标;(3)淬火后及时进行回火,消除淬火应力;(4)适当降低磨削速度、
20、磨削 量、磨削冷却速度,能有效防止和避免磨削裂纹形成。8 线切割裂纹该裂纹出现在经过淬火、回火的模块在线切割加工过程中,此过程改变了金属 表层、中间层和心部应力场分布状态,淬火残余内应力失去平衡变形,某一区域 出现大的拉应力,此拉应力大于该模具材料强度极限时导致炸裂,裂纹是弧尾状 刚劲变质层裂纹。实验表明,线切割过程是局部高温放电和迅速冷却过程,使金 属表层形成树枝铸态组织凝固层,产生600-900MPa拉应力和厚约003mm的高应 力二次淬火白亮层。裂纹产生原因:(1)原材料存在严重的碳化物偏析;(2)仪表 失灵,淬火加热温度过高,晶粒粗大,降低材料强韧性,增加脆性;(3)淬火工 件未及时回
21、火和回火不充分,存在过大的残余内应力和线切割过程中形成的新内 应力叠加导致线切割裂纹。预防措施:(1)严格原材料入库前检查,确保原材料组织成分合格,对不合 格原材料必须改进锻,击碎碳化物,使化学成分、金相组织等达到技术条件后方 可投产、模块热处理前加工成品需留足一定磨量后淬火、回火、线切割;(2)入 炉前校验仪表,选用微机控温,控温精度15,真空炉、保护气氛炉加热, 严防过热和氧化脱碳;(3)采用分级淬火、等温淬火和淬火后及时回火,多次回 火,充分消除内应力,为线切割创造条件;(4)制订科学合理线切割工艺。模具服役时在交变应力反复作用下形成的显微疲劳裂纹缓慢扩展,导致突 然疲劳断裂。(1)原材
22、料存在发纹、白点、孔隙、疏松、非金属夹杂、碳化物严(下 接 2、3 版中缝)重偏析、带状组织、块状游离铁素体冶金组织缺陷,破坏了基体组织连续性,形成不均匀应力集中。钢锭中H2未排除,导致轧制时形成白点。钢中存在Sb、 Bi、Pb、Sn、As和S、P等有害杂质,钢中的P易引起冷脆,而S易引起热脆, S、P有害杂质超标均易形成疲劳源;(2)化学渗层过厚、浓度过大、渗层过徒、 硬化层过浅、过渡区硬度低等都可导致材料疲劳强度急剧降低;(3)当模面加工 粗糙、精度低、光洁度差,以及刀纹、刻字、划痕、碰伤、腐蚀麻面等也易引起 应力集中导致疲劳断裂。 预防措施:(1)严格选材,确保材质,控制Pb、As、 S
23、n等低熔点杂质与S、P非金属杂质含量不超标;(2)投产前进行材质检查,不 合格原材料不投产;(3)选用具有纯洁度高、杂质少、化学成分均匀、晶粒细、 碳化物小、等向性能好,疲劳强度高等特点的电渣重熔精炼钢,对模具型面表面 喷丸强化和表面化学渗层改性强化处理,使金属表层为预压应力,抵消模具服役 时产生的拉应力,提高模具型面疲劳强度;(4)提高模具型面加工精度和光洁度; (5)改善化学渗层和硬化层组织性能;(6)采用微机控制化学渗层厚度、浓度和硬 化层厚度。9. 疲劳断裂模具服役时在交变应力反复作用下形成的显微疲劳裂纹缓慢扩展,导致突然疲 劳断裂。 (1)原材料存在发纹、自点、孔隙、疏松、非金属夹杂
24、、碳化物严重偏 析、带状组织、块状游离铁素体冶金组织缺陷,破坏了基体组织连续性,形成不 均匀应力集中。钢锭中112未排除,导致轧制时形成白点。钢中存在*、Bi、Pb、 Sn、As和S、P等有害杂质,钢中的P易引起冷脆,而s易引起热脆,S,P有害 杂质超标均易形成疲劳源; (2)化学渗层过厚、浓度过大、渗层过度、硬化层过 浅、过渡区硬度低等都可导致材料疲劳强度急剧降低; (3)当模面加工粗糙、精 度低、光洁度差,以及刀纹,刻字、划痕、碰伤、腐蚀麻面等也易引起应力集中 导致疲劳断裂。预防措施:(1)严格选材,确保材质,控制Pb、As、Sn等低熔点杂质与S、P 非金属杂质含量不超标; (2)投产前进
25、行材质检查,不合格原材料不投产; (3) 选用具有纯洁度高、杂质少、化学成分均匀、晶粒细碳化物小、等向性能好, 疲劳强度高等特点的电渣重熔精炼钢,对模具型面表面喷丸强化和表面化学渗层 改性强化处理,使金属表层为预压应力,抵消模具服役时产生的拉应力,提高模 具型面疲劳强度; (4)提高模具型面加工精度和光洁度; (5)改善化学渗层和硬 化层组织性能; 采用微机控制化学渗层厚度、浓度和硬化层厚度。10应力腐蚀裂纹该裂纹常发生在使用过程中。金属模具因化学反应或电化学反应过程,引起从 表至内组织结构损坏腐蚀作用而产生开裂,这就是应力腐蚀裂纹。模具钢因热处 理后组织不同,抗蚀性能也不同。最耐蚀组织为奥氏
26、体(A),最易腐蚀组织为屈 氏体(T),依次为铁素体(F)马氏体(M)珠光体(P)索氏体(S)。因此,模具钢热处 理不宜得到T组织。淬火钢虽经回火,但因回火不充分,淬火内应力或多或少依 然存在,模具服役时在外力作用下也会产生新的应力,凡有应力存在于金属模具 中就会有应力腐蚀裂纹发生。预防措施:(1)模具钢淬火后应及时回火,充分回火,多次回火,以消除淬 火内应力;(2)模具钢淬火后一般不宜在350-400回火,因T组织常在此温度 出现,发生有 T 组织模具应重新处理,模具应进行防锈处理,提高抗蚀性能;(3) 热作模具服役前进行低温预热,冷作模具服役一个阶段后进行一次低温回火消除 应力,不仅能防止和避免应力腐蚀裂纹发生,还可大幅度提高模具使用寿命,一 举两得,有显著技术经济效益。
- 温馨提示:
1: 本站所有资源如无特殊说明,都需要本地电脑安装OFFICE2007和PDF阅读器。图纸软件为CAD,CAXA,PROE,UG,SolidWorks等.压缩文件请下载最新的WinRAR软件解压。
2: 本站的文档不包含任何第三方提供的附件图纸等,如果需要附件,请联系上传者。文件的所有权益归上传用户所有。
3.本站RAR压缩包中若带图纸,网页内容里面会有图纸预览,若没有图纸预览就没有图纸。
4. 未经权益所有人同意不得将文件中的内容挪作商业或盈利用途。
5. 装配图网仅提供信息存储空间,仅对用户上传内容的表现方式做保护处理,对用户上传分享的文档内容本身不做任何修改或编辑,并不能对任何下载内容负责。
6. 下载文件中如有侵权或不适当内容,请与我们联系,我们立即纠正。
7. 本站不保证下载资源的准确性、安全性和完整性, 同时也不承担用户因使用这些下载资源对自己和他人造成任何形式的伤害或损失。
最新文档
- 《认识角》ppt教学讲解课件
- 《从数据谈节水》数据的收集、整理与描述优秀教学ppt课件
- 人员配置-公司组织架构与人员配置计划课件
- 《认识分式》ppt课件
- 《从百草园到三味书屋》第一课时ppt课件
- 公路工程概预算三课件
- 中考物理专题突破-综合能力题教学课件
- 《创新设计》高考英语二轮复习(江苏专用)ppt课件:第二部分-基础语法巧学巧练-专题八-非谓语动词
- 中考物理专题复习课件:滑轮及滑轮组
- CIM安全标识统一规划课件
- 中考物理专题复习教学课件-质量和密度
- 《处理民族关系的原则平等团结共同繁荣》ppt课件
- 中考物理专题复习之物理实验和探究题复习指导教学课件
- 《十二人人都会有挫折》初中心理健康教育闽教版《中学生心理健康》七级课件
- Cisco无线网络-安全-Brief课件