硅溶胶型壳常见缺陷及防止措施
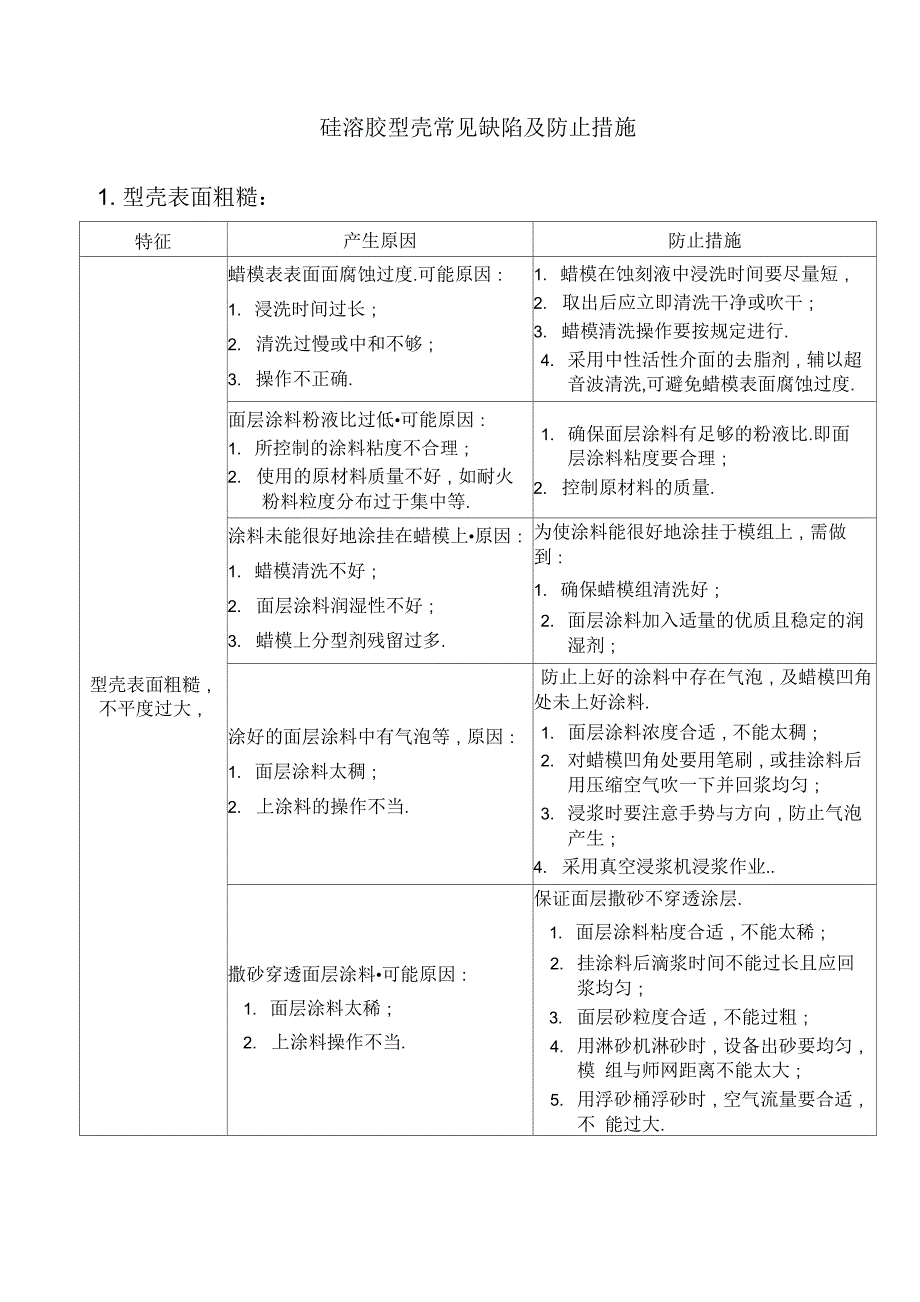


《硅溶胶型壳常见缺陷及防止措施》由会员分享,可在线阅读,更多相关《硅溶胶型壳常见缺陷及防止措施(7页珍藏版)》请在装配图网上搜索。
1、硅溶胶型壳常见缺陷及防止措施1. 型壳表面粗糙:特征产生原因防止措施型壳表面粗糙, 不平度过大,蜡模表表面面腐蚀过度.可能原因:1. 浸洗时间过长;2. 清洗过慢或中和不够;3. 操作不正确.1. 蜡模在蚀刻液中浸洗时间要尽量短,2. 取出后应立即清洗干净或吹干;3. 蜡模清洗操作要按规定进行.4. 采用中性活性介面的去脂剂,辅以超 音波清洗,可避免蜡模表面腐蚀过度.面层涂料粉液比过低可能原因:1. 所控制的涂料粘度不合理;2. 使用的原材料质量不好,如耐火 粉料粒度分布过于集中等.1. 确保面层涂料有足够的粉液比.即面 层涂料粘度要合理;2. 控制原材料的质量.涂料未能很好地涂挂在蜡模上原因
2、:1. 蜡模清洗不好;2. 面层涂料润湿性不好;3. 蜡模上分型剂残留过多.为使涂料能很好地涂挂于模组上,需做到:1. 确保蜡模组清洗好;2. 面层涂料加入适量的优质且稳定的润 湿剂;3. 射蜡模应合理使用分型剂用量.涂好的面层涂料中有气泡等,原因:1. 面层涂料太稠;2. 上涂料的操作不当.防止上好的涂料中存在气泡,及蜡模凹角 处未上好涂料.1. 面层涂料浓度合适,不能太稠;2. 对蜡模凹角处要用笔刷,或挂涂料后 用压缩空气吹一下并回浆均匀;3. 浸浆时要注意手势与方向,防止气泡 产生;4. 采用真空浸浆机浸浆作业.撒砂穿透面层涂料可能原因:1. 面层涂料太稀;2. 上涂料操作不当.保证面层
3、撒砂不穿透涂层.1. 面层涂料粘度合适,不能太稀;2. 挂涂料后滴浆时间不能过长且应回 浆均匀;3. 面层砂粒度合适,不能过粗;4. 用淋砂机淋砂时,设备出砂要均匀,模 组与师网距离不能太大;5. 用浮砂桶浮砂时,空气流量要合适,不 能过大.2. 型壳面层裂纹:特征产生原因防止措施型壳表面层出现不规 则的裂纹,或出现极 细小的龟状裂纹这些裂纹是型壳干燥时产生的,主 要是由于面层干燥过快,或涂料干 燥收缩过大引起的,或由于蜡模热 膨胀使面层型壳被胀裂.及型模焙 烧不当引起具体产生原因:1. 环境相对湿度太低2. 面层干燥时间过长3. 空气流动不均匀而且过大4. 环境温度变化过大5. 壳模焙烧不当
4、.1.2.3.4.5.面层干燥区相对湿度宜在RH60 70%之间.面层干燥时间以46h为宜,特殊 产品不要超过10h.风不要正对模组吹,应降低直接吹 到模组上的气流量.制壳间温度应严格控制,保持在 2225C之间.脱蜡后壳模应在至少4h后装炉焙 烧.尽量避免高温-低温-高温焙烧 及二次焙烧.3. 型壳面层鼓裂:特征型壳面层局部与蜡模分开 向外鼓起(图a),或鼓起后 破裂导致背层涂料流到蜡 模和面层之间,但未将空 隙填满(图b、图c).产生原因防止措施1.面层型壳与蜡模间附着力太 差1确保蜡模清洗好.2面层涂料润湿剂加入量合适.2.面层型壳外表面干燥过度、内 表面干燥不足.1.控制好环境相对湿度
5、、面层干燥时 间和风速,确保面层型壳外、内表面 干燥合适.2应使面层涂料厚合适,不要过厚.3.面层型壳湿强度不足,特别是 在蜡模锐角处其强度低1. 保证面层型壳湿强度.为此,要保证 硅溶胶和耐火材料的质量,按工艺规 范保持涂料正确配方,配制方法及确 保涂料性能合格.2. 要保证蜡模锐角处有一定厚度的 涂料,且涂料不要滴得过干.4.制壳间温度不均匀保持制壳间温湿度均匀.4. 型壳内孔搭桥:特征产生原因防止措施内孔、凹槽处的型壳不致 密,局部有未上好涂料,未撒 上砂使该处型壳存在孔隙 搭桥.I-SS 2哩世1. 第一层或背层涂料太稠.2. 孔洞或狭缝处浸浆不足.3. 撒砂过粗,以致孔洞或狭缝 处很
6、快就被塞住.4. 孔洞或狭缝处松散砂粒在 浸下层浆时未被清除掉.5. 内孔或凹槽处型壳干燥不 足.1. 控制好第二层和背层涂料粘度.2. 细致地上孔洞或狭缝处的涂料.3. 撒砂使用较细的砂,防止孔洞或 狭缝处过早被塞住.4注意将孔洞或狭缝处松散的浮 砂吹除,再上下层涂料.5注意内孔或凹槽处型壳干燥情 况,不干时不能制作下层模壳.5. 型壳面层剥落:特征产生原因防止措施型壳型腔尺寸变 大,表面不光洁.面浆与蜡型的附着力太差1. 改善蜡模蚀刻清洗,利用溶剂轻微腐 蚀蜡模表面以增强其与浆层的吸附 力.2. 破坏宽大之平面,在宽广平面上加上 若干凸出物或筋,减少平面宽广程度, 以利浆附着.3. 在型蜡
7、中添加一些亲水性物质,改善 蜡的亲水性,也可有效增强面浆与蜡 型的吸附力.面层在制下层型壳过程中剥落,这是 由于面层还没有干燥就制第二层型 壳,硅溶胶发生回溶现象,使面层型壳 剥落.控制好环境相对湿度、温度、风速和干燥 时间,确保面层干燥后再做第二层.面层干燥过快或过度增加面层干燥区的的湿度,一般为 RH6070%,但在特殊有深穴如盒状铸件 内部不易干燥的状况,甚至相对湿度设定 为7080%减少空气的流速,避免内外 速率相差太大,外部本就较易干燥,若再 加风吹,则外部已干燥过度,而内部尚未 干燥,因此减少空气流动,对拉动内外干 燥一致有较大助益.相对湿度愈高,风速愈小,则室内的干湿 球温差愈小
8、,如此,可避免壳型在干燥初 期,因为快速干燥蒸发水汽,温度急降而 使蜡型收缩,待干燥后,蜡型又因吸收室 内温度而而升温膨胀,如此缩胀,轻则龟 裂,重则剥落.温度变化不均确保除湿间的绝热性与温度的均衡性.型壳脱蜡时面层剥落.原因是面层和 第二层型壳间结合力太差而赞成的.1. 面层太太厚.2. 第二层涂料粘度太大,难于渗入 面层.3. 面层撒砂太细,一二层很难形成 牢固的镶嵌结构.4. 撒砂中粉尘量及含水量过大,造 成分层.5. 面层撒砂过慢等引起撒砂未能嵌 入涂层内部.而是浮贴在涂层上, 或根本未撒上砂子形成涂料与涂 料接触,产生分层.6. 上第二层涂料前未去除面层型壳 上松散的浮砂.7. 未使
9、用预湿剂,导致个别地方涂 挂不良.焙烧时型壳面层剥落,则是由于两涂 层间热胀系数不同而造成的.1. 面层太厚的原因导之于面浆过浓,粘 砂时,耐火材料仅在浆的表面而无法 深入浆层,失去键销阻绝大面收缩的 效果,使浆层干燥后产生微裂,因此,可 适当降低浆液的浓度.2. 第二层涂料粘度不能太大.3. 砂粒不应太细,以形成粗糙的背面,使 一二层镶嵌紧密.4. 控制砂的质量,将粉尘含量列入管制 标准.撒砂中粉尘含量与水的含量均 应低于0.5%.5. 滴回浆不可过干,撒砂不应过慢.6. 在制第二层型壳前以柔和风吹去表面 松散砂粒.7. 制第二层型壳前,把模组浸入硅溶胶 预湿剂中(不超过2S),取出甩干或滴
10、干 (表面无明显滴落胶液),再上第二层涂 料.尽量使面层和二层的材料热膨胀系数相 近.6. 型壳强度低:特征产生原因防止措施型壳强度不足1.硅溶胶质量差,如胶体粒径过大,胶体 结构不不致密,杂质多等.1.选用质量好而稳定的硅溶胶,同时强化 进料检验.2.硅溶胶中SiO2含量低.2.确保硅溶中SiO2质量分数.3.耐火材料质量差,如耐火材料矿物组 成不符合要求,杂质量含咼等.3.保证耐火材料质量好而稳定.4.涂料质量不好,如涂料配比不合理,配 料时未按照规范进彳丁.4严格控制涂料配比和配制工艺,保证涂 料质量.5制服壳同操作不当,发涂料上得不匀, 涂层过薄;撒砂粒度不合适等等.5.严格按照制壳工
11、艺规范进行制壳作业.6.型壳干燥不透,这常是硅溶胶型壳强 度不咼.的主要原因.6控制好制壳间的温度、湿度、风速和干 燥时间,确保型壳干透.7未上预湿剂,或上预湿剂不当.预湿剂 起强化型壳的作用,是防止型壳分层的 重要措施.7.按型壳大小等正确规定上预湿剂的规 范.8型壳层数不够.8应根据铸件大小等,正确选择型壳层数.7. 型壳裂纹:特征产生原因防止措施型壳开裂,浇出 的铸件有一规 则的毛刺、飞边.1.脱蜡时蜡模膨 胀大于型壳膨胀, 而型壳湿强度又 低,使型壳开裂.1. 脱蜡前型壳应存放在恒温的制壳间,脱蜡时运到脱蜡处.立刻 装车入脱蜡釜脱蜡,不允许型壳过长时间放在脱蜡间中.2. 脱蜡蒸汽压力上
12、升要快,14S内必须升到0.6kg.3. 组树方案正确,以保证蜡易流出.4. 型壳应有足够的透气性,对有的铸件应设透气孔.5采取各种措施保证型壳强度(见本表型壳强度低缺陷的防止 措施).6防止组树时蜡模间距离太近,使型壳不易干燥,造成型壳强度 低.7.铸件上平面大时,应设法增加型壳强度.8. 气泡、毛刺:特征产生原因防止措施壳模制作不紧 实,浇铸后因钢 水穿透而形成 毛刺.浆的浓度太高浆的浓度太咼时,流动性自然较差,浆液无法进入蜡型的死角位 置仍被空气占据,为一气泡形态,解决方法:先用含有湿润剂预 浸液(硅溶胶溶液或较稀的浆液)预浸蜡树,使死角处的空气被 预浸液挤排除去,浸浆时,浆液将顺着预浸
13、液进入死角而避免了 气泡的产生.不正确的浸浆作 业当浸浆时,预湿液已经干燥或流失,则死角地区仍被空气占据, 失去预浸功能,因此,应训练作业人员的回浆作业手法,在浸浆 之前,应用回浆手法使预湿液能均匀的占据蜡型(或壳型)的每 一个角落挤除空气并预湿表面.浆内气泡太多配制浆料后,必须要经过4h以上的浸润浆料及排除气泡,湿润 剂在过度的搅拌下也会产生气泡,故需对搅拌速度进行适当设 定虽然一切均无问题,浆液中仍会因混入空气而有小气泡,故 在浆液中要加入少量的消泡剂辅助去除气泡.浆的浓度太低当浆的浓度太低时,面层浆自然会太薄,且粉料太少会使面层有 许多的小孔隙,而且因面层太薄,后面耐火砂堆集的孔隙,对浆
14、 层无支撑力,当铸造时,金属会穿入这些孔隙中形成痱子状的尖 刺(毛刺),此时,应在沾浆作业时多沾一次浓度较咼的浆液,并回 浆均匀后再沾耐火砂.耐火砂粒度太粗面层用的耐火砂过粗时,粒间空隙太大,对面层而言无支撑力, 会使金属液穿刺而形成痱子,故可选用较细的耐火砂做面浆的 支撑.9. 未润湿:特征产生原因防止措施蜡模组表面挂 浆性不佳,个别 位置出现露出 蜡面或涂挂层 太薄,可见蜡色过多的离型剂(脱模剂)训练射蜡作业员正确的离型剂喷涂方法.清洗不确实用溶剂清洗时,可能溶剂效能已降低,浸洗时间没有相应延长, 致清洗不完全.若用中性介面活性剂的去脂剂清洗时,冋样亦会 因使用一段时间后,效能降低.故在此
15、状况下,均以延长浸洗时 间来解决,倘仍不能解决,则只能更换清洗剂.面浆内的湿润剂 不够不同厂牌的湿润剂,效果不同,其用量亦不相同,应各自试用恰 当的用量,不可过多,否则会产生过多的气泡.另外醇基湿润剂 会挥发,故隔一段时间后应继续追加.10. 壳模破裂:特征形成原因防止措施壳模局部位置 表面出现一定 深度的裂痕,严 重者则为自内 而外穿透性裂缝.脱蜡前陶壳破裂浸浆室及干燥区的温度不稳定,造成蜡型热胀,使陶壳胀裂。 需改善空调温控系统与除湿间的保温绝热性能。脱蜡时热能不足 胀裂高压蒸汽脱蜡,是利用每克水蒸汽冷凝为不时,所释放出的539 卡潜热来达到瞬间熔脱蜡的目的,所以脱蜡釜中水蒸汽的量就 代表
16、热能的多少,压力越高代表蒸汽量越多,热能越大,附带 的蒸汽贯穿陶壳直接接触蜡型熔脱蜡的能力也越大。脱蜡釜后的温控泄压阀无法泄压时,舱内升压虽快,但因有大 量热空气占据空间,而非热蒸汽,其脱蜡热能仍有不足。此时应更换温控泄压阀或减少单次脱蜡量。若升压太慢时,应加大锅炉发气量或减少单次脱蜡量。当蜡树的体积及表面积很大时,若次脱蜡数量太多,其所需 的热能就多,但因舱内空间减少,使汽量减少,相对亦会热能 不足,此时,应减少 次脱蜡量来解决。陶壳湿态强度不 够因陶壳的强度与厚度成正比,因此增加陶壳厚度为最简单有效 的方法。若是干燥不足时,则应延长封浆后的干燥时间。蜡液自模中排出 不易浇道蜡的熔点太高时,
17、当蜡型蜡已熔而浇道却未熔,致蜡无法 顺浇道排出,而会胀裂陶壳,此时应更换浇道蜡为低熔点蜡。11. 壳模层间剥落:特征形成原因防止措施壳模在层与层 之间剥离分开蒸汽脱蜡时,泄 压降得过快陶壳虽然是多孔性可透气,但毕竟是有阻抗透气,在维持高压 脱蜡时,陶壳内外均维持高压状态下的均压。当泄压时,外部 压力降低,陶壳内的蒸汽自会向低压区扩散,若压差太大扩散 力量便成为陶壳分层的推挤力。一般泄压时间约为lmin。面层耐火砂堆积 太厚面层耐火砂一般均用100目左右的细砂,在面层沾浆作业时, 常会产生堆集层,在浸第二层浆前,预浸时未将堆集的耐火砂 支队,则经二层浆所接触的是面层的浮砂而非面层壳,形成脆 弱的
18、浆一砂一砂一浆结构,而不是正常的浆一砂一浆一砂结 构。解决办法为在制作下层型壳前抖落或吹除浮砂。背层浆料料浓度 太高背层浆的浓度太高时,浆的流动性本就不够好,再加上前层干 陶壳的吸水作用,使浆的流动性更差无法渗入砂层建立坚强的 陶壳,仅能沾在前层陶壳砂的外端,自然很容易形成浆一砂一 砂一浆的不良陶壳。在脱蜡泄压太快或陶壳在脱蜡后放置干燥 时间不够,在烧结陶壳时的快速升温,都会因蒸汽压而使陶壳 分层剥裂。12. 壳模鼓胀变形、强度不足:特征形成原因防止措施宽广平面背层干 燥时,将面层拉离 蜡型制造宽广平面陶壳时,面层虽然完全干燥,但因为避免太厚造成 微龟裂,故不可能很厚,强度自然不咼,浸第二层陶
19、壳时,因陶壳 的干燥收缩,将面层陶壳拉离蜡型,在未脱蜡时,剖开陶壳便会 发现陶壳鼓胀,解决方法:是在宽广平面上加香菇状的凸出物 或微小筋,缩小平面面积,增加面层陶壳对蜡型表面的附着力. 二是利用陶瓷砂芯沾附于面层陶壳之后,以增加面层陶壳的强 度,再浸二层时,便无法将面层拉离而形成鼓胀.烘模温度过高陶壳所使用的粘结剂为硅溶胶,其成分为SiO2,而SiO2的软化 点为1200C,倘为铸造超薄的铸件时,不求增加水口缩短充填 距离,而一味的升咼烘模温度,超过1200C时则陶壳软化形成 鼓胀,导致铸件厚度大于蜡型,解决方法为增加陶壳厚度,使变 软的陶壳仍有足够的强度支撑金属静压而不致产生鼓胀,或者 增加水口将烧结温度降至1200C以下.另外便是不用硅溶胶 作粘结剂,而改用铝胶液.耐火材料耐火度 不够更换相态稳定耐火度咼的ai2o3系列熟料.金属静压太高降低金属静压或增加陶壳强度.陶壳强度不够增加陶壳层数及厚度.浇注温度太咼降低浇注温度或增加陶壳强度.
- 温馨提示:
1: 本站所有资源如无特殊说明,都需要本地电脑安装OFFICE2007和PDF阅读器。图纸软件为CAD,CAXA,PROE,UG,SolidWorks等.压缩文件请下载最新的WinRAR软件解压。
2: 本站的文档不包含任何第三方提供的附件图纸等,如果需要附件,请联系上传者。文件的所有权益归上传用户所有。
3.本站RAR压缩包中若带图纸,网页内容里面会有图纸预览,若没有图纸预览就没有图纸。
4. 未经权益所有人同意不得将文件中的内容挪作商业或盈利用途。
5. 装配图网仅提供信息存储空间,仅对用户上传内容的表现方式做保护处理,对用户上传分享的文档内容本身不做任何修改或编辑,并不能对任何下载内容负责。
6. 下载文件中如有侵权或不适当内容,请与我们联系,我们立即纠正。
7. 本站不保证下载资源的准确性、安全性和完整性, 同时也不承担用户因使用这些下载资源对自己和他人造成任何形式的伤害或损失。