合成氨工艺学
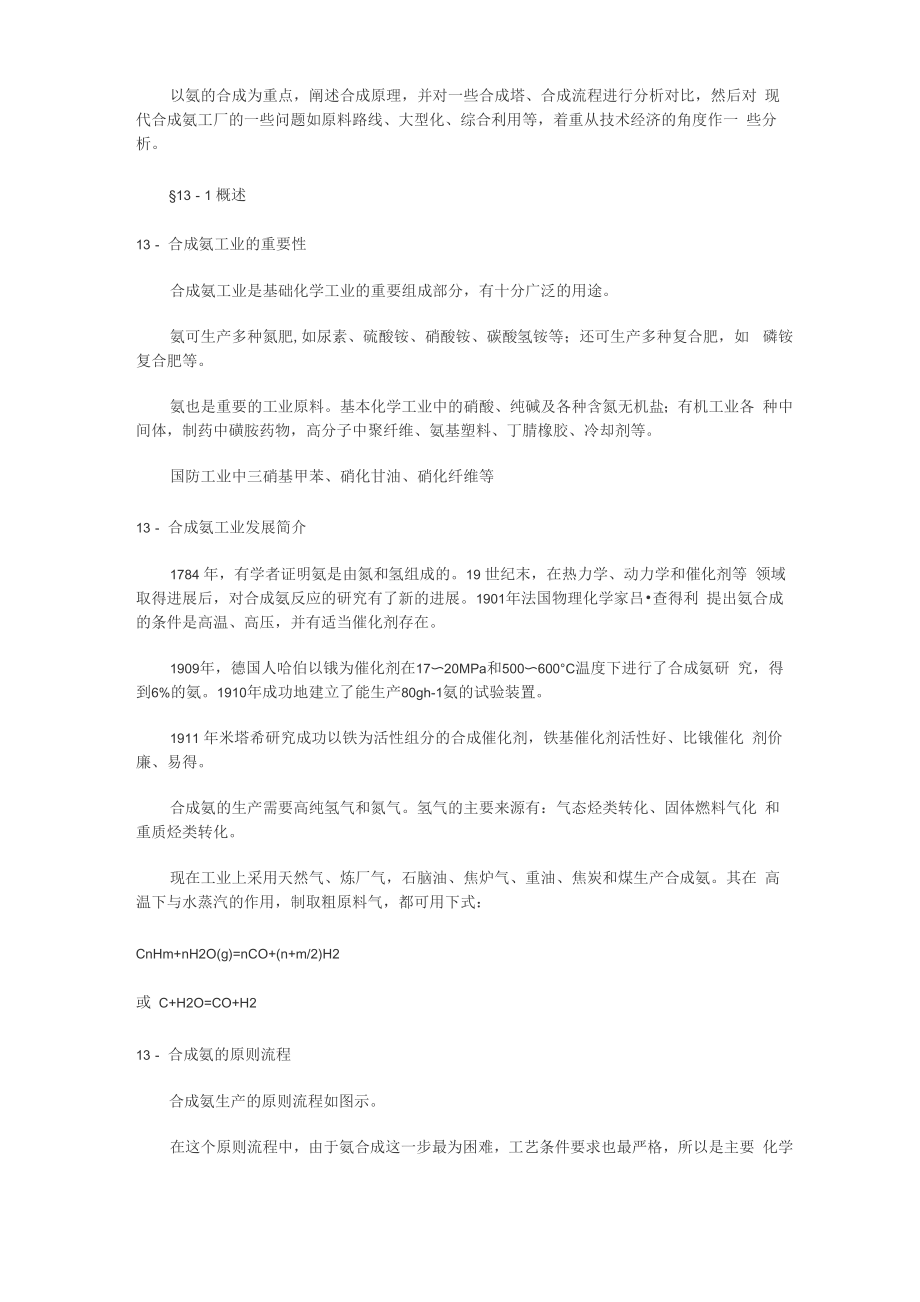


《合成氨工艺学》由会员分享,可在线阅读,更多相关《合成氨工艺学(17页珍藏版)》请在装配图网上搜索。
1、以氨的合成为重点,阐述合成原理,并对一些合成塔、合成流程进行分析对比,然后对 现代合成氨工厂的一些问题如原料路线、大型化、综合利用等,着重从技术经济的角度作一 些分析。131 概述13 合成氨工业的重要性合成氨工业是基础化学工业的重要组成部分,有十分广泛的用途。氨可生产多种氮肥,如尿素、硫酸铵、硝酸铵、碳酸氢铵等;还可生产多种复合肥,如 磷铵复合肥等。氨也是重要的工业原料。基本化学工业中的硝酸、纯碱及各种含氮无机盐;有机工业各 种中间体,制药中磺胺药物,高分子中聚纤维、氨基塑料、丁腈橡胶、冷却剂等。国防工业中三硝基甲苯、硝化甘油、硝化纤维等13 合成氨工业发展简介1784 年,有学者证明氨是由
2、氮和氢组成的。19 世纪末,在热力学、动力学和催化剂等 领域取得进展后,对合成氨反应的研究有了新的进展。1901年法国物理化学家吕查得利 提出氨合成的条件是高温、高压,并有适当催化剂存在。1909年,德国人哈伯以锇为催化剂在1720MPa和500600C温度下进行了合成氨研 究,得到6%的氨。1910年成功地建立了能生产80gh-1氨的试验装置。1911 年米塔希研究成功以铁为活性组分的合成催化剂,铁基催化剂活性好、比锇催化 剂价廉、易得。合成氨的生产需要高纯氢气和氮气。氢气的主要来源有:气态烃类转化、固体燃料气化 和重质烃类转化。现在工业上采用天然气、炼厂气,石脑油、焦炉气、重油、焦炭和煤生
3、产合成氨。其在 高温下与水蒸汽的作用,制取粗原料气,都可用下式:CnHm+nH2O(g)=nCO+(n+m/2)H2或 C+H2O=CO+H213 合成氨的原则流程合成氨生产的原则流程如图示。在这个原则流程中,由于氨合成这一步最为困难,工艺条件要求也最严格,所以是主要 化学反应过程,应该首先进行优化。原料气的生产和净化过程是氨合成的前置过程,它的优 化必须以满足氨合成的要求为前提;氨的分离和循环气返回合成塔既是氨合成的后继过程也 是氨合成的前置过程。因此氨的合成和分离必须结合在一起统筹考虑。132 氨合成的热力学基础 从化学工艺的角度看其核心是反应过程工艺条件的确定,而确定反应的最佳工艺条件,
4、 需先从事反应热力学和动力学的研究。13氨合成反应与反应热氢气和氮气合成氨是放热,体积缩小的可逆反应,反应式如下:+=NH3AH?298= kj molT其反应热不仅与温度有关,还与压力和组成有关。氨合成反应的热效应表见教材(P143)13氨合成反应的平衡常数应用化学平衡移动原理可知,低温、高压操作有利于氨的生成。但是温度和压力对合成 氨的平衡产生影响的程度,需通过反应的化学平衡研究确定。其平衡常数为:式中,p,pi分别为总压和各组分平衡分压;yi平衡组分的摩尔分数。高压下化学平衡常数Kp值不仅与温度有关,而且与压力和气体组成有关,用逸度表 示:式中:f,Y分别为各平衡组分的逸度和逸度系数.1
5、3影响平衡时氨浓度的因素若总压为P的混合气体中含有N2,H2, NH3和惰性气体的的摩尔分数分别为yN2,yH2,yNH3和yi其关系为yN2+yH2+yNH3+yi=l.令原始氢氮比R= yH2/ yN2,则各组分的平衡分 压为所以所以整理的此式可分析影响平衡氨含量的诸因素:a.压力和温度的影响:温度越低,压力越高,平衡常数Kp越大,平衡氨含量越高。b氢氮比的影响当温度、压力及惰性组分含量一定时,使yNH3为最大的条件为若不考虑R对Kp的影响,解得R=3时,yNH3为最大值;高压下,气体偏离理想状态, Kp将随R而变,所以具有最大yNH3时的R略小于3,约在之间。c.惰性气体的影响惰性组分的
6、存在,降低了氢、氮气的有效分压,会使平衡氨含量降低。133 氨合成动力学13 氨合成催化剂以铁为主的催化剂(铁系催化剂)有催化活性高、寿命长、活性温度范围大、价廉易得等 特点,广泛地被国内外合成氨厂家采用。催化剂的活性成分是金属铁,而不是铁氧化物。使用前用氢氮混合气对催化剂还原,使 铁氧化物还原为具有较高活性的a型纯铁。还原反应方程式为:FeO Fe203+4H2=3Fe+4H20A12O3 在催化剂中能起到保持原结构骨架作用,从而防止活性铁的微晶长大,增加了催化剂 的表面积,提高了活性。Ca0 起助熔剂作用。K20 的加入可促使催化剂的金属电子逸出功降低。MgO除具有与A1203相同作用外,
7、其主要作用是抗硫化物中毒的能力,从而延长催化剂的使 用寿命。少量 CO、CO2、H2O 等含氧杂质的存在将使铁被氧化,而失去活性。但当氧化性物质清 除后,活性仍可恢复,故称之为暂时中毒。硫、磷、砷等杂质引起的中毒是不可恢复的,称 作永久性中毒。13 氨合成反应动力学过程氨合成为气固相催化反应,它的宏观动力学过程包括以下几个步骤。a.混合气体向催化剂表面扩散(外,内扩散过程);b氢,氮气在催化剂表面被吸附,吸附的氮和氢发生反应,生成的氨从催化剂表面解吸(表 面反应过程);c.氨从催化剂表面向气体主流体扩散(内,外扩散过程)氮、氢气在催化剂表面反应过程的机理,可表示为:N2(g)+Ca te2N(
8、Ca te)H2(g)+Ca te2H(Ca te)N(Ca te) + H(Ca te)NH(Ca te)NH(Ca te) + H(Ca te)NH2(Ca te)NH2(Ca te) + H(Ca te)NH3(Ca te)NH3(Ca te)NH3(g) + (Ca te)实验结果证明,N2活性吸附是最慢的一步,即为表面反应过程的控制步骤。对整个气固相催化反应过程,是表面反应控制还是扩散控制,取决于实际操作条件。低温时可能是动力学控制,高温时可能是内扩散控制; 大颗粒的催化剂内扩散路径长,小颗粒的路径短,所以在同样温度下大颗粒可能是内扩散控制,小颗粒可能是化学动力学控制。当内扩散控制时
9、,动力学方程为rNH3=kP式中rNH3为反应速率,k为扩散系数,p为反应物的总压。当化学动力学控制时,在接近平衡时:式中 rNH3-氨合成反应的净速率:k1,k2-正、逆反应速率常数;pN2, pH2, pNH3-N2,H2, NH3 的分压.a 为常数,与催化剂性质及反应条件有关,由实验测定。通常OVaVl,对以铁为主的氨合成催化剂a=,故反应达到平衡时,r=O,则整理得上式关联了 k1,k2及Kp间的关系。134 氨的合成与分离13 氨合成工艺条件的优化合成工艺参数的选择除了考虑平衡氨含量外,还要综合考虑反应速度、催化剂特性及系 统的生产能力、原料和能量消耗等。1、压力提高压力利于提高氨
10、的平衡浓度,也利于总反应速率的增加。高压法动力消耗大, 对设备材料和加工制造要求高。生产上选择压力的依据是能耗及包括能耗、原料费、设备投资、技术投资在内的综合费 用。经分析,总能耗在1530MPa间相差不大,数值较小;就综合费而言,压力从lOMPa 提高到30MPa时,下降40%左右30MPa左右是氨合成的适宜压力。从节省能源的观点出发,合成氨的压强应为1520 M Pa 的压力。2、温度温度过高,会使催化剂过早失活。塔内温度应维持在催化剂的活性温度范围(4005 20C)内。氨的合成反应存在一个使反应速度最大的温度,即最适宜反应温度,它除与催化剂活性 有关外,还取决于反应气体组成和压力。最适
11、宜反应温度与平衡反应温度之间存在确定的关 系。随着反应的进行,温度逐渐升高,当接近最适宜温度后,再采取冷却措施。3、空间速度空间速度指单位时间内通过单位体积催化剂的气体量(标准状态下的体积)。单 位h-1,简称空速。空速越大,反应时间越短,转化率越小,出塔气中氨含量降低。增大空速,催化剂床层 中平衡氨浓度与混合气体中实际氨含量的差值增大,即推动力增大,反应速率增加;同时, 增大空速混合气体处理量提高、生产能力增大。采用中压法合成氨,空间速度为 20 00030 000 h-1 较适宜。4、氢氮比动力学指出,氮的活性吸附是控制阶段,适当增加原料气中氮含量利于提高反应 速率。为达到高的出口氨浓度、
12、生产稳定的目的,循环气氢氮比略低于3(取,新鲜原料气 中的氢氮比取 3:1。5、惰性气体含量惰性气体在新鲜原料气中一般很低,只是在循环过程中逐渐积累增多,使 平衡氨含量下降、反应速度降低。生产中采取放掉一部分循环气的办法。放掉的气体称为驰 放气。另行处理以回收氨和其它有用的气体。理论上是惰性气体越少越好,但实际上这是不 现实的。要确定一个合理的惰性气体含量范围,还需大量计算,综合各种操作因素作图比较 分析得出。以增产为主要目标,惰气含量,约为10%14%,若以降低原料成本为主,约为 16%6、催化剂的粒径催化剂的粒径也必须优化,优化过程涉及的因素很多且难以定量描述,所 以优化条件只能通过实验来
13、确定。在反应初期粒径小,反应后期粒径大。13 氨的分离除了在需要氨水的地方,要用水吸收法来得到一些浓氨水外,一般都用冷凝法来分离氨。 冷却分离过程是一个能耗较大的过程,较高温度时可用水冷,冷至较低温度一般用氨冷。就 是用液氨作冷源,经过较复杂的冷冻流程将工艺气中的氨冷凝分离出来。分离氨之后的气体 含有少量氨,同时还含有H2,要送循环系统再入合成塔循环反应。为了维持系统浓度稳定, 惰性气体浓度不至累积过高,只有少量气体被引出作进一步处理。现在一般都要将里面所含 H2 分离出来循环利用,不再是简单地用作燃料。液氨冷冻系统的传热温差一般都较小,所以流程复杂。这是热力学上功的损失因素所决 定了的。进合
14、成氨塔气体中的氨由循环气带入,其数量决定于氨分离的条件。温度越低,分离效 果越好。合理的氨含量应由增产与能耗之间的经济效益来定。在 30 MPa 左右,进口氨含量 控制在; 15 MPa时为3%。13 合成塔合成塔必须保证原料气在最佳条件下进行反应。氨合成是在高温、高压下进行,氢、氮对碳钢有明显的腐蚀作用。将塔设计成外筒和内 件两部分。外筒一般做成圆筒形,可用普通低合金钢或优质碳钢制造,气体的进出口设在塔 的上、下两端顶盖上。外筒只承受高压而不承受高温。塔内件由热交换器、分气盒和催化剂筐三部分构成。热交换器供进入气体与反应后气体 换热;分气盒起分气和集气作用;催化剂筐内放置催化剂、冷却管、电热
15、器和测温仪器。冷 却管的作用迅速移去反应热。按从催化剂床层移热的方式不同,合成塔分连续换热式、多段间接换热式和多段冷激式 三种。1、多段冷激式冷激式氨合成塔有轴向冷激和径向冷激之分。大型氨厂多用立式轴向四段冷 激式氨合塔(凯洛格型)。2、连续换热式并流双套管式氨合成塔如图13 合成分离循环流程目前工业上使用的氨合成流程很多。中小合成氨厂广泛采用两级分氨流程。下图为常见 的合成流程。135 原料气的生产与净化13 生产原料气的原料合成氨的生产需要高纯氢气和氮气。氮气用最丰富而廉价的空气来制取。氢气的主要来源有:气态烃类转化、固体燃料气化和重质烃类转化。其中以天然气为原 料的气态烃类转化过程经济效
16、益最高。其在高温下与水蒸汽的作用,制取粗原料气,都可用 下式:CnHm+nH2O(g)=nCO+(n+m/2)H2或 C+H2O=CO+H2原料气的生产步骤:一、造气燃料与空气、水反应生成N2, H2, CO二、变换CO与水反应生成H2,实现氢氮比R=313 以煤焦为原料的造气过程及其优化把煤或焦炭中的可燃物质转变为H2、CO和CO2,这一过程叫做固体燃料气化,简称造 气。气化所得的气体统称煤气,进行气化的设备叫煤气发生炉。采用间歇法造气时,空气和蒸汽交替通入煤气发生炉。通入空气的过程称为吹风,制得 的煤气叫空气煤气;通入水蒸气的过程称为制气,制得的煤气叫水煤气;空气煤气与水煤气 的混合物称为
17、半水煤气。固体燃料气化法的化学计量方程式为:吹风 2C+O2+= 2CO+ kj mol-1制气 5C+5H2O(g)= 5CO+5H2 kj mol-1总反应 7CO2 N25H2O(g)=7CO N25H2kJmolT工业上采用间歇操作送风发热法,即交替进行吹风和制气。为充分利用热量和安全,生产过程如图所示。a.空气吹风空气从造气炉底部吹入,送风发热,提高炉温,吹风后的气体去废热锅炉回收 热量后放空;b.上吹制气蒸汽和空气从炉底吹入制半水煤气,半水煤气通过废热锅炉回收热量,除尘、 洗涤后送入气柜。C.下吹制气上吹制气后,炉底温度下降,炉顶温度尚高,使蒸汽和空气从炉顶吹入与碳反 应,生成半水
18、煤气从炉底导出,经除尘、洗涤, 送入气柜;d. 二次上吹下吹后,炉底充满水煤气,此时吹入空气升高炉温,可能引起爆炸。再从炉底 吹入蒸汽将炉底煤气排净,为吹风作准备。二次上吹虽可制气,但炉温低,气质差,二次上 吹时间尽可能短;e. 空气吹净空气从炉底吹入,将残存的半水煤气吹出并送入气柜,同时制得的吹风气(空气 煤气)与 b,C,d 阶段制得的半水煤气在气柜中混合。缺点:气化设备简单、便于控制,能耗大,约有一半原料被当作燃料烧掉,生产能力低, 产生三废(煤渣、含氰废水、含硫废气等)较多。13 以轻质烃为原料的造气过程及其优化轻质烃原料主要是天然气、油田气、炼厂气、轻油等,其中应用最多的是天然气,其
19、主 要成分是 CH4以轻质烃为原料生产原料气。有操作连续,工程投资省,能量消耗低等优点。1. 化学反应及转化率CH4 + H20=3H2 + CO 可逆、吸热,升高温度,提高转化率2. 副反应及催化剂中毒CH4=C+2H22CO=C+CO2CO+H2=C+H2OCH4+2H2O=CO2+4H2原料气中少量的硫会使镍催化剂中毒,因此要采取措施降低硫的含量。所以转化反应前 必须脱硫。3. 反应压力综合考虑能量消耗和经济效益,实际生产的操作压力为 Mpa,4.反应器一段转化炉是烃类蒸汽转化的关键设备之一。采用外热法使原料气和催化剂在耐热合金 管内发生造气反应。二段转化炉燃烧之前,转化气与空气必须充分
20、混合,以避免局部过热而损坏炉体。因而 通入的空气先要经一空气分布器。整个炉体为一立式圆筒,壳体材质是碳钢,内衬耐火材料, 炉内装有催化剂。5.生产工艺流程以轻质烃为原料生产原料气。有操作连续,工程投资省,能量消耗低等优点。烃类蒸汽转化法应用最多的是加压两段催化转化法,该法的生产流程如图上所示.配入%氢的天然气,在压力下被烟道气预热到380C左右,在脱硫器中经脱硫后,使其 总硫含量小于Ug/go在下配入倍体积的中压水蒸气,进一步加热到500C左右,进装有a -A12O3为载体的镍催 化剂的反应管内。气体在反应管内于650800C温度下发生转化反应:CH4 + H20=3H2 + COAH0 =C
21、H4 + 2H20=4H2 + C02AH0 =90%的CH4发生转化.转化后的气体进入二段转化炉,出来的气体组成为%, %,H257%, %,%,气体温度约1000C左右,压力为。经余热利用,温度降到场70C.优点:获得的粗原料气与半水煤气相比,含氢量高,含C0量低,杂质气体亦较少,后 处理负担轻。13 变换1.化学反应与平衡转化率用煤或烃生产出的气体都含有相当量的C0,如固体燃料制得的半水煤气含28%31%, 气体烃蒸汽转化法含15%18%,重油气化法含46%左右。C0对氨合成催化剂有毒害,必 须除去。变换利用水蒸气把C0变换为H2和易清除的C02,同时又制得了所需的原料气H2。 其反应为
22、:C0 + H20(g)= C02 + H2AH0= -41 kj molT温度、反应物组成及催化剂性能都是影响平衡转化率的因素。2.工艺条件的优化1)催化剂低温变换催化剂一般用铜催化剂。其主要成份为:, %少量Cr203。活性成份为单 质铜,活性温度范围为180 250C,使用前要用氢气还原。中温变换催化剂一般用铁铬催化剂,其主要成份为:Fe20380-90%;Cr2037-ll%;少量K20,Mg0,及A1203,起活性的成份是Fe304活性温度范围为350450C,使用前也 要用氢气还原。(2)原料气的组成为了提高CO的转化率,采用水蒸气过量的方法实现。(3)反应温度变换反应是可逆放热反
23、应,存在反应最佳温度。从热力学上看,温度上升,平衡常数下 降,转化率降低;但从动力学因素看,温度升高,反应速度增加。使变换率最大的温度为最 佳温度,从热力学和动力学关系求极值可得出。反应初期,转化率低,最佳温度高,采用中 温变换,反应后期,转化率高,最佳温度低,采用低温变换。(4)反应压力压力对平衡没有影响,但增大压力可加快反应速度,减少催化剂用量和反应设备体积, 并可降低能耗。中型厂用加压变换,小型厂MPa加压变换。加压变换的缺点是设备腐 蚀严重。3. 生产工艺流程(中变低变串联的流程)中变催化剂的铁铬或铁镁催化剂反应温度高,反应速度大,有较强的耐硫性,价廉而寿 命长。低温的铜系催化剂则正相
24、反。为了取长补短,工业上采用中变低变串联的流程,如图所示。压力对平衡无影响。变换是在常压下进行的. 增大压力可加快反应速度,减少催化剂用 量和反应设备体积,并可降低能耗。中型厂用加压变换,小型厂 MPa 加压变换。加压变换的缺点是设备腐蚀严重。13 原料气的净化脱硫,脱碳,变换, 气体的精制1.脱硫主要是H2S,其次是CS2,C0S,RSH等有机硫。其含量取决于原料的含硫量及加工方 法.以煤为原料,原料气中H2S含量一般为23gm-3,有的高达2030gm-3。H2S 对设备和管道有腐蚀作用,使变换及合成系统的催化剂中毒,还使铜洗系统的低价铜生 成硫化亚铜沉淀,增加铜耗。工业脱硫方法很多,分为
25、干法和湿法两种。前者是用固体脱硫剂(如氧化锌、活性炭、 分子筛等)将气体中的硫化物除掉;后者用碱性物质或氧化剂的水溶液即脱硫剂(如氨水法、 碳酸盐法、乙醇胺法、蒽醌二磺酸钠法及砷碱法等)吸收气体中的硫化物。干法脱硫优点是既能脱无机硫,又能脱有机硫,可把硫脱至极微量。缺点是脱硫剂不能 再生,故只能周期性操作,不适于脱除大量硫化物。湿法采用液体脱硫,便于再生并能回收硫,易于构成连续脱硫循环系统,可用较小的设 备脱大量硫化物。缺点是对有机硫脱除能力差,净化度不如干法高。目前通用的是湿法中的改良ADA法,也称之为ADA-钒酸盐法(或改良ADA法)。反应原理:(1)脱硫吸收塔中的反应:Na2C03+H2
26、SNaHS+NaHC032NaHS+4NaV03+H20Na2V409+4Na0H+2SNa2V409+2ADA(氧化态)+2Na0H+H204NaV03+2ADA(还原态)(2)再生塔中反应:2ADA (还原态)+02-2ADA(氧化态)+H202.脱碳变换气中含有大量的C02(15% 35%),对原料气的精制及氨合成不利。脱除C02的方法很多,工业上常用的是溶液吸收法,分为物理吸收和化学吸收两种。物理吸收是利用 C02 能溶于水和有机溶剂的特点。常用的有加压水洗、低温甲醇洗涤等。 如在3MPa、-30 -70C下,甲醇洗涤气体后气体中的C02可以从33%降到10ugg- 1,脱碳十分彻底。
27、化学吸收是用氨水、有机胺或碳酸钾的碱性溶液为吸收剂,利用C02能与溶液中的碱性 物质进行化学反应而将其吸收。大中型厂多采用改良热碱法,此法以K2C03水溶液为吸收液, 并添加少量活化剂如氨基乙酸或乙二醇胺,缓蚀剂如V205等。吸收解吸反应如下:K2C03 + C02 + H20 = 2KHC03当吸收液中添加氨基乙酸,吸收压强23MPa、温度85100C时,气体中的C02可 从2028%降至 ;解吸压强为1030kPa,温度105110C,用热碱脱除C02时, 也脱除了微量的 H2S。3气体的精制气体的精制就是将少量的CO、C02进一步脱除,常用的有铜洗法和甲烷化 法。甲烷化法是把CO、CO2
28、转化为对氨合成无害的CH4,主要反应是CO + 3H2 = CH4 + H2OCO2 + 4H2=CH4 + 2H2O甲烷化法镍为主的催化剂作用下,在280380C及压强 3MPa下进行甲烷化反应。 此法将气体中碳化物总量降低到10ug g-l。136 氨生产全流程制造原料气按原料的不同有各种流程,原料气的净化过程依据原料及其制造方法的差异 也有不同的选择,其流程有若干种。下面介绍几种典型的合成氨全流程。以煤为原料合成氨的全流程如图所示。选用了改良蒽琨二磺酸法脱硫、氨基乙酸法脱C O2、加压变换等新技术。如下图所示。以天然气等气态烃为原料二段转化法流程如图。特点是把脱硫放在转化之前。有益于转
29、化和变换催化剂,避免转化后把温度降到常温下脱硫,节省和利用了大量的热能。如下图所 示。137 合成氨生产的发展趋势13生产规模大型化化工发展趋势的两大特点是:大型化与综合化。大型厂的优点,除节省人力外,节能和 综合利用能量好。各工序是一个有机整体,工序间缺少独立性,局部变化会影响整体状态的 稳定性。生产规模增大,投资亦增多,但比投资却下降,即大规模生产是有利的。13降低能耗合成氨厂能耗很大,氨成本中能源费用依据原料的不同占一半左右。因此降低能耗一直 是合成氨技术改造的一个重要方面。节能降耗的方法有:扩大生产规模、选择与原料相适应的净化方法、采用新工艺及余热 的回收利用、从弛放气中回收氢等。13
30、原料多样化用什么原料,主要取决于来源与价格。采用什么样的流程,应根据不同的原料,对各工序拟使用的生产方法进行技术经济分析 和综合评价比较,以求操作可行和经济合理。天然气制氨的投资最少、能耗最小、成本也较低。究竟选择哪一种原料不能仅从经济上考虑,还要从可能性及社会条件等方面考虑。13氨的深加工目前已很少有以氨作为单一产品的合成氨工厂,而大多数是将氨深加工以生产尿素、碳 酸氢铵等化学肥料,以增加经济效益。138 尿素的合成13合成反应的物理化学基础尿素的合成分以下两步进行:1、甲铵的生成2NH3(l)+C02(g)=NH4C00NH2(l)+mol2、甲铵脱水生成尿素NH4COONH2(l)=CO
31、(NH2)2(l)+H2O(l)mol13 原则流程原则流程如下图所示:13 工艺条件的优化1、原料配比生产上用过量的氨的办法来提高 CO2 的转化率。过量氨的作用:工业上氨过量50-150%。a、促进二氧化碳转化,减小腐蚀;b、与水生成氨水,使水排除在反应之外,从而使反应加快。c、可抑制尿素缩合,甲铵水解 等副反应从而使转化率提高;d、控制自热平衡,维持最适宜反应温度。2、反应温度由上图可知:当Tf,X平f .在1 9 0 2 0 0 1时,又T每升10,V反增加一倍.综合考虑上述因素,反应温度常用1 8 5- 2 0 0C,即略高于Xmax。3、压力从反应式知,压力增加对反应有利!Pf有利
32、a)T、V定,x尿随压力增加而剧增。b)高温下,甲铵易分解为C02、NH3 进入气相,使x平下降,故:P操P甲铵平衡。不利当P增至一定程度,x平趋于定值。若P剧增,x平不增加或很少。但:a)因动力消耗增加,故成本增加;b)高压下,甲铵对设备腐蚀加剧。综合考虑以上因素,反应温度为180C时,压力应在14MPa以上;当反应温度为200C 时,压力应在24MPa以上。一般地说,实际操作压力应比理论分解压力大2-3MPa。13尿素合成塔尿素合成塔应具备以下条件:1、反应物在合成塔内最好是平推流,这样可以保持最大的反应推动力,获得较快的反应速 率;2、由于反应物为气体和液体,必须保证气液接触良好;3、必
33、须耐压、耐热、耐腐蚀。13分离和回收利用从反应器溢流而出的反应物除含尿素外,还含有未分解的氨基甲酸铵、水、和未反应的 氨和二氧化碳。因此应对其进行分离和回收利用。比较广泛的是能耗较少的二氧化碳气提 法。13尿素生产流程化工-合成氨工艺 化学工程工艺合成氨第十三章 合成氨工艺 ? 主要内容: 主要内容:1、氨合成概述2、氨合成的热力学基础、3、氨合成动力学4、原料气的生产与净化、5、氨生产全流程6、合成氨生产发展趋势、7、尿素的合成、 13-1 概述 13 一、合成氨的重要性 生产氮肥、硝酸盐、 纤维、染料等。 生产氮肥、硝酸盐、胺、纤 维、染料等。二、原料路线 直接原料: 直接原料:氢和氮 以
34、下方法获得粗原料气:氢气、氮气、一 氧化碳、以下方法获得粗原料气:氢气、氮气、一氧化碳、二氧化碳C + H 20 = C O +H 2Cn H m+nH 2O = nCO + n) H 2 2C +O2 + N2 = 2CO+ N 2 Cn H m+ (n + O2 + (n + N 2 = nCO + 2O + (n + N 2 ? 粗原料气变换: 粗原料气变换: CO + H 2O = CO2 + H 2 变换气以氢气、氮气、二氧化碳为主, 变换气以氢气、氮气、二氧 化碳为主,其中氢分子 与氮分子之比为:3:1 与氮分子之比为: 除杂净化得到合乎要 求的氢氮混合气。 除杂净化得到合乎要求的
35、氢氮混合气。三、氨合成原则流程和各化学 反应过程相互关系氨合成这一步最困难,工艺条件要求也最严格, 氨合成这一步最困难, 工艺条件要求也最严格,是主 要化学反应过程,应首先进行优化。 要化学反应过程,应 首先进行优化。13-2 氨合成的热力学基础 13一、氨合成反应与反应热 N 2 +2 = NH 3 二、反应平衡常数f NH3 Y NH3 pNH3 K f =?= KY ? K p f N2 ? fH2 YN2 ? Y H 2 p N2 ? pH2f :逸度;Y :逸度系数K f :与压力无关仅与温度有关。三、影响平衡时氨浓 度的因素 y pKp = (1+R) 2(1 ? y ? yi )
36、 2 p: 总压力;R: y H2 y N2 y、y :NH 、惰性气体的摩尔分数i 3 1、氢氮比R: R=3(此 时最大、氢氮比:此时y最大此时最大)2、温度:温度越低,Kp越大。低温催化剂为发展方向。 越大。、温度:温度越低, 越 大 低温催化剂为发展方向。3、压力:压力越大,平衡浓度越大。、压力:压力越大,平衡浓度越大。4、惰性气体含量:有较大的影响。 、惰性气体含量:有较大的影响。13-3 氨合成动 力学 13一、催化剂 铁催化剂: 铁催化剂: Fe 2 O3 5468%、FeO2936%、Al2 O3 2 4% K 2 %、% 在加热条件下原料气将铁还原: (Fe2 O3 ,FeO
37、) +H 2 = Fe+ H 2 0 A10型催化剂:活化能约170KJ/mol,起燃温度 型催化剂:活化能约 型催化剂, 起燃温度370 耐热温度510度,活性最高时的温度 度左右, 度,耐热温度度 活性最 高时的温度450度左右,粒 度左右 径13mm.二、反应动力学1:气体向催化剂表面(内、 外)扩散2:气体在催化剂表面发生活性吸附N 2 (气)一2 N (吸附)H 2 (气) 一 2 H (吸附)3:吸附的氮、氢发生反应生成氨N (吸附)+ H (吸附)一 N H (吸附)NH (吸附)+ H (吸附)一NH 2 (吸附)NH 2 (吸附)+ H (吸 附)一NH 3 (吸附)4:生成
38、的氨从催化剂表面解吸NH 3 (吸附)一NH 3(气) 5:解吸的氨从催化剂表面向气流主体扩散反应控制阶段取决于反应条件(温度、催化剂颗粒的大小) 温度一定:大颗粒为内扩散控制,小颗粒为化学动力学控制。 颗 粒一定:低温为化学动力学控制,高温为内扩散控制。 扩散控制时:y NH3 = kp化 学动力学控制:远离平衡时:r = kpN2 pH 2 k :扩散系数;p: 总压力接近平衡时:r = kl pN 2 k1、k2:正逆反应速度常数; H2 pNH3 ? k2 pNH3 H2不同粒度催化剂、压力30MP a 空速30000h 30MPa、30000h不同粒度催化剂、压力30MPa、空速30
39、000h-1时,不同 温 度下的反应结果: 温度下的反应结果: 低温时: 低温时: 化学动力学控 制,氨含 量不受 颗粒大小影响; 颗粒大小影响; 高温时: 高温时:内扩散 控制, 控制, 小颗粒催 化剂效果较好。 化剂效果较好。13-3 氨的合成与分离 13一、工艺条件的优化1、温度:400510度(可逆放热反应,最快反度 可逆放热反应, 、温度: 应速率时 的反应温度随转化率的提高而降低) 应速率时的反应温度随转化率的提高而降低) 2、压 力:加压有利于提高转化率。、压力:加压有利于提高转化率。20世纪:1015MPa;近 年:34MPa世纪:近年:世纪3、空间速度: 、空间速度: 气固相
40、催化反应空间速度越大,反应时间越短, 气固相 催化反应空间速度越大,反应时间越短, 生产强度越大。 生产强度越大。 4、氢氮比: 氮的活性吸附为合成反应的控制阶段, 、氢氮比:氮的活性吸附为合成反应的控制阶 段, 氮的含量对反应速率影响较大,略低于3可加快反应 氮的含量对反应速率影响较大, 略低于 可加快反应 速率。速率。实践:实践:32MPa、450度、催化剂粒度、度 催 化剂粒度空速24000(1/h)、R=出口氨浓度最大 空速、出口氨浓度最大 采取的方法: 新鲜原料气比为3 , 采取的方法:新鲜原料气比为 ,混合后的循环气在合 成塔入口的 比约为。 成塔入口的比约为。5、进塔气中的惰性气
41、体含量:一般、进塔气中的惰性气体含量:一般W2%6、催化剂颗粒:反应初期:温度 、催化剂颗粒:反应初期:温度440470度粒径 度粒 径 ;反应后期:温度 反应后期: 反应后期 温度420440度粒径 度粒径 816mm二、氨的分离 方法: 方法:降低温度使氨液化通过气液分离器使液氨与 其他气体分离。 其他气体分离。log y =+? p T y : 未液化的气体中氨的含量 四段冷激轴向合成塔 ? 原料气一主进气口一沿环 原料气一主进气口一 隙至顶部一 换热器管间预 隙至顶部一换热器管间预 热420度,与冷激气混合度 温度降为410度一 第一段度 温度降为 催化剂床层,温度由 催化剂床层,温度由410 上升到496度再与 冷激气度再与冷激气上升到混合降至430度,此时度混合降至NH3%为%二段、 为 一二段、 三段、四段一中心管一 三段、四段一中心管一换 热器管内一 热器管内 一出塔 (130200度)度 ? 径向塔:气体的走向是径向,每段催化剂的厚度只 径向塔: 气体的走向是径向, 有塔径
- 温馨提示:
1: 本站所有资源如无特殊说明,都需要本地电脑安装OFFICE2007和PDF阅读器。图纸软件为CAD,CAXA,PROE,UG,SolidWorks等.压缩文件请下载最新的WinRAR软件解压。
2: 本站的文档不包含任何第三方提供的附件图纸等,如果需要附件,请联系上传者。文件的所有权益归上传用户所有。
3.本站RAR压缩包中若带图纸,网页内容里面会有图纸预览,若没有图纸预览就没有图纸。
4. 未经权益所有人同意不得将文件中的内容挪作商业或盈利用途。
5. 装配图网仅提供信息存储空间,仅对用户上传内容的表现方式做保护处理,对用户上传分享的文档内容本身不做任何修改或编辑,并不能对任何下载内容负责。
6. 下载文件中如有侵权或不适当内容,请与我们联系,我们立即纠正。
7. 本站不保证下载资源的准确性、安全性和完整性, 同时也不承担用户因使用这些下载资源对自己和他人造成任何形式的伤害或损失。