玻璃液的熔制
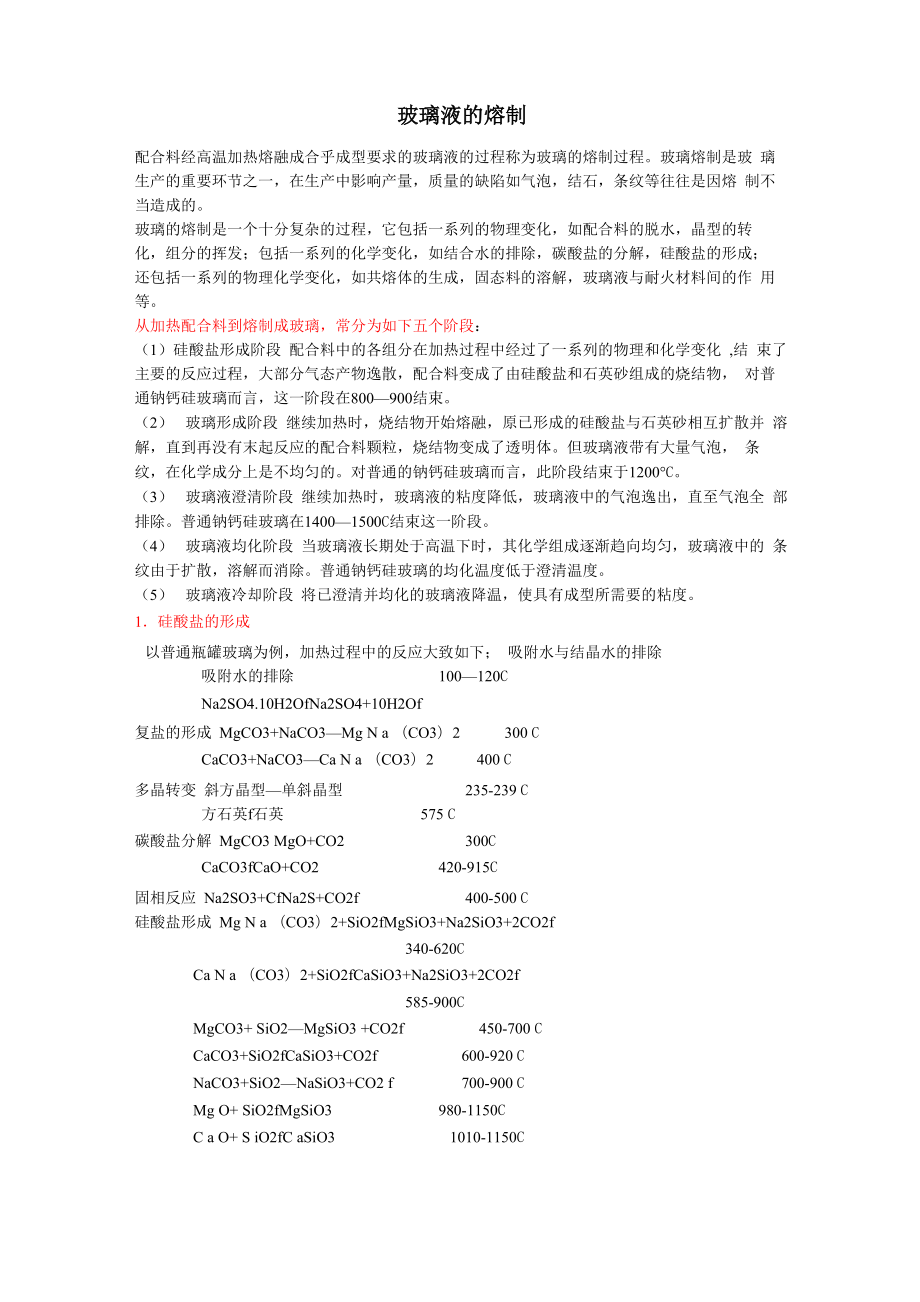


《玻璃液的熔制》由会员分享,可在线阅读,更多相关《玻璃液的熔制(7页珍藏版)》请在装配图网上搜索。
1、玻璃液的熔制配合料经高温加热熔融成合乎成型要求的玻璃液的过程称为玻璃的熔制过程。玻璃熔制是玻 璃生产的重要环节之一,在生产中影响产量,质量的缺陷如气泡,结石,条纹等往往是因熔 制不当造成的。玻璃的熔制是一个十分复杂的过程,它包括一系列的物理变化,如配合料的脱水,晶型的转 化,组分的挥发;包括一系列的化学变化,如结合水的排除,碳酸盐的分解,硅酸盐的形成; 还包括一系列的物理化学变化,如共熔体的生成,固态料的溶解,玻璃液与耐火材料间的作 用等。从加热配合料到熔制成玻璃,常分为如下五个阶段:(1)硅酸盐形成阶段 配合料中的各组分在加热过程中经过了一系列的物理和化学变化 ,结 束了主要的反应过程,大部
2、分气态产物逸散,配合料变成了由硅酸盐和石英砂组成的烧结物, 对普通钠钙硅玻璃而言,这一阶段在800900结束。(2)玻璃形成阶段 继续加热时,烧结物开始熔融,原已形成的硅酸盐与石英砂相互扩散并 溶解,直到再没有末起反应的配合料颗粒,烧结物变成了透明体。但玻璃液带有大量气泡, 条纹,在化学成分上是不均匀的。对普通的钠钙硅玻璃而言,此阶段结束于1200C。(3)玻璃液澄清阶段 继续加热时,玻璃液的粘度降低,玻璃液中的气泡逸出,直至气泡全 部排除。普通钠钙硅玻璃在14001500C结束这一阶段。(4)玻璃液均化阶段 当玻璃液长期处于高温下时,其化学组成逐渐趋向均匀,玻璃液中的 条纹由于扩散,溶解而消
3、除。普通钠钙硅玻璃的均化温度低于澄清温度。(5)玻璃液冷却阶段 将已澄清并均化的玻璃液降温,使具有成型所需要的粘度。1硅酸盐的形成以普通瓶罐玻璃为例,加热过程中的反应大致如下; 吸附水与结晶水的排除吸附水的排除100120CNa2SO4.10H2OfNa2SO4+10H2Of复盐的形成 MgCO3+NaCO3Mg N a (CO3)2300 CCaCO3+NaCO3Ca N a (CO3)2400 C多晶转变 斜方晶型单斜晶型235-239 C方石英f石英575 C碳酸盐分解 MgCO3 MgO+CO2300CCaCO3fCaO+CO2420-915C固相反应 Na2SO3+CfNa2S+CO
4、2f400-500 C硅酸盐形成 Mg N a (CO3)2+SiO2fMgSiO3+Na2SiO3+2CO2f340-620CCa N a (CO3)2+SiO2fCaSiO3+Na2SiO3+2CO2f585-900CMgCO3+ SiO2MgSiO3 +CO2f450-700 CCaCO3+SiO2fCaSiO3+CO2f600-920 CNaCO3+SiO2NaSiO3+CO2 f700-900 CMg O+ SiO2fMgSiO3980-1150CC a O+ S iO2fC aSiO31010-1150CC aSiO3+ M g S iO3fC aSiO3.MgSiO3 600-1
5、280C低共熔物形成 Na2SO3-Na2S740CNa2SO3-N a 2 C03795 CNa2SO3-Na2SiO3865CNaCO3-NaS756CNaCO3-Ca N a (CO3)2780C末起反应的NaCO3f熔融855C末起反应的NaSO3f熔融885C石英颗粒,低共熔物,硅酸盐熔融1200-1300C试验表明,配合料组成越复杂,熔融的速度就越快。如NaCO3-CaCO3-MgCO3-SiO2四组分 的配合料比NaCO3-CaCO3- SiO2三组分的配合料熔融速度快,所需温度也低。在用池窑熔制玻璃时,配合料直接加在高温区,反应在约1350C的高温下在3-5分钟内完 成,反应非
6、常迅速,基本上是在固体状态下进行的。2玻璃的形成在硅酸盐形成阶段生成的硅酸钠,硅酸钙及反应剩余的大量硅砂在继续提高温度时它们相互 溶解和扩散,由不透明的半熔烧结物转为透明的玻璃液。由于石英砂粒的溶解和扩散速度比 之各种硅酸盐的溶扩速度慢得多,所以玻璃形成阶段的速度实际上取决于石英砂粒的溶扩速 度。石英砂粒的溶扩过程分为两步,首先是砂粒表面发生溶解,而后溶解的SiO2向外扩散,两 者的速度是不同的,其中扩散速度最慢。所以石英砂粒的溶解速度决定于扩散速度。随着石英砂粒的逐渐溶解,溶融物中的SiO2含量越来越高,玻璃液的粘度也随着增加。此 时,扩散就越难进行,这导致石英砂的溶解速度减慢。由上可知,石
7、英砂粒的溶解速度不仅 与粘度和温度有关,而且与砂粒表层SiO2和熔体中SiO2的浓度差有关除 SiO2 与各种硅酸盐之间的扩散外,各硅酸盐之间也相互进行扩散,这些扩散过程有利于SiO2更好地溶解,也有利于不同区域的硅酸盐形成相对均匀的玻璃液。与硅酸盐形成过程相比,玻璃形成过程要慢得多。以平板玻璃熔制为例,从硅酸盐形成开始到玻璃形成阶段结束共需要32分钟,其中硅酸盐形成仅需3-4分钟,面玻璃形成却需要28-32 分钟。当然,硅酸盐形成和玻璃形成的两个阶段没有明显的界限,在硅酸盐形成阶段结束之 前,玻璃形成阶段即已开始。为了加速石英砂粒的溶解速度,除选用颗粒小,有棱角状的石英砂外,可适量引入助溶剂
8、, 也可适当提高熔制温度。在1150-1450C的温度区间,溶化温度提高50C,石英砂的溶解速 度就提高50%。这是因为温度提高,玻璃液粘度降低,SiO2的扩散速度加快,从而加速了 玻璃的形成。3玻璃液的澄清玻璃液中的气泡长大后上升到液面而排除的过程即澄清过程,是玻璃熔制过程中极为重要的 一环,它与制品的产量和质量有着密切的关系。对普通硅酸盐玻璃而言,澄清阶段的温度为 1400-1500C。在硅酸盐形成与玻璃形成阶段,由于配合料中部分物料的分解,部分组分的挥发,氧化物的 氧化还原反应,玻璃液与炉气及耐火材料的相互作用等原因,析出了大量气体,其中大部分 气体逸散而出,剩余气体中的大部分溶解于玻璃
9、液中,少部分以气泡的形式存在于玻璃液, 也有部分气体与玻璃液中的某组分形成化合物。因此,存在于玻璃液中的气体主要有三种形 式;即可见气泡,物理溶解的气体和化学结合的气体。因原料种类,玻璃成分,炉气性质,压力制度和熔制温度的不同,玻璃液中的气体种类和数 量也不同。常见的气体有;CO2,O2.N2,H2O,SO3,CO等,此外,还有H2,NO2,NO及惰性气 体等。玻璃液的澄清指排除可见气泡的过程。从形式上看,这是一个简单的流体力学问题,实际上 还包含一个复杂的物理化学变化。需要指出的是,玻璃液的去气与无泡是两个概念。去 气应理解为全部排除上述三种气体,这在一般生产条件下是不可能的。 排除玻璃液中
10、的气泡有两种方式同时进行。大于临界泡径的气泡由玻璃液内上升到玻璃液 面,而后破裂进入大窑空间;小于临界泡径的气泡在玻璃液表面张力的作用下溶解于玻璃液 中面消失。气泡在玻璃液中的上升速度v与玻璃液的粘度n存在下述关系;V=2/9 gr2 d-d/ng一重力加速度r一气泡半径dd玻璃液的密度和气泡中气体的密度 由上式可知,气泡上升的速度与玻璃液的粘度成反比,表明玻璃液的澄清与玻璃的组成及熔 制温度有关。与澄清有关的几个主要问题: 澄清过程中气体间的转化与平衡 在澄清过程中,玻璃液内所溶解的气体,气泡中的气体与炉气三者间的平衡关系,是由某种 气体在各相中的分压所决定的。气体总是由分压高的相进入分压低
11、的相。其间关系可用下图 表示;气体间的转化与平衡除与上述分压有关外,还与气泡中所含气体的种类有关。依据道尔顿分 压定律,当A气体进入含有B气体的气泡中时,气泡的总压将增高,气泡中B气体的分压 将减小。因而气泡将从四周玻璃液中吸收B气体,直到两相中B气体的分压相等。 气体在玻璃液中的溶解度与温度有关,玻璃液温度升高,气体在玻璃液中的溶解度减小。 澄清过程中气体与玻璃液的相互作用澄清过程中气体与玻璃液的相互作用有两种不同的状态;一类是纯物理吸附,如N2气,不 与玻璃成分发生任何反应;另一类气体如SO2,与玻璃成分间发生反应,形成化合物,随后 在一定的条件下又析出气体。O2 与玻璃液的相互作用 氧在
12、玻璃液中的溶解度首先取决于变价离子的含量,吸收的氧 使低价离子转为高价离子。例如;FeO+l/2O2Fe2O3 当玻璃液中完全没有变价氧化物时,氧在玻璃液中的溶解度是微不足道的。SO2与玻璃液的相互作用无论何种燃料,都含有硫化合物,因而炉气中均含有SO2,它能 与配合料及玻璃液相互作用形成硫酸盐,例如;XNa2O.ySiO2+ SO2Na2SO3+(X-1) Na2O.y SiO2对于含Na2O 15%, CaO12%, SiO2 73%的玻璃液,在9001200C的温度范围内,玻璃 液吸收SO2,形成硫酸盐,高于1200C时,硫酸盐开始分解,到1300C时,硫酸盐的热分 解结束。澄清过程中澄
13、清剂的作用机理 为加速澄清过程,在配合料中加入少量澄清剂,根据作用机理不同,可将澄清剂分为三类;(1) 变价氧化物类澄清剂这类澄清剂有As2O3, Sb2O3 ,CeO2,Mn2O3 等,其特点是在低温时吸收氧气,在高温时放出 氧气,其作用如下;As2O3+O2As2O5 400-1300 C 1300 CAs2O3 在玻璃熔制中作用很大,无论是高温熔制还是低温熔制,都能非常明显地加速玻璃 液中气泡的排除过程。当玻璃液中As2O3浓度在1%以下时,澄清作用随浓度增大而加快。 但浓度继续增大,对澄清无益,反而使玻璃产生乳光现象。Sb2O3的作用类似于Sn2O3,也是一种常用的澄清剂。但在不同组成
14、的玻璃液中,澄清效 果不一样。例如,在重钡冕玻璃中,Sb2O3的效果大大超过Sn2O3。而在钠钙硅酸盐玻璃 与硼硅酸盐玻璃中,两者的效果没有明显的差别。(2) 硫酸盐,硒酸盐,碲酸盐类澄清剂硫酸盐分解后产生SO2,对气泡的长大与溶解起着重要作用.Na2SO3是广泛用于制造瓶罐 玻璃, 窗玻璃和其他钠钙玻璃制品的有效澄清剂。 K2SO3,Ba2SO3,Sr2SO3, Ca2SO3, ZnSO3 ,PbSO3,Al2(SO3)3(NH4)2SO3 等所有硫酸盐与 Na2SO3 一样,在钠钙玻璃中均有很好的澄清作用。 引入配合料中的硫酸盐,其阳离子本身对澄清过程不起作用。不论引入何种硫酸盐,离子交
15、换的结果总是形成硫酸钠而产生澄清效果。与变价氧化物澄清剂As2O3,Sb2O3不同的是, 硫酸盐的澄清作用与熔化温度密切相关。低温熔制时,对澄清几乎没有影响。只有在 1400-1500 C时,硫酸盐的作用才能充分显示出来。(3) 卤化物类澄清剂 属于这类澄清剂的有氟化物,氯化物,溴化物和碘化物。工业上常用的是氟化物和氯化物。 溴化物和碘化物的澄清作用虽然更强烈,但价格昂贵而不采用。在玻璃熔体中,氟化物与SiO2反应生成SiF4而挥发,造成硅氧结构网络的断裂,使玻璃液 粘度下降,从而加速了澄清过程。4玻璃液的均化 玻璃液的均化包括化学组分均化和热均化两大部分。在玻璃形成阶段结束后,由于各种原因
16、在玻璃液中仍存在着一些与主体玻璃液化学成分不一样的局部区域。例如,化学组成不同的 透明的条状物(条纹),化学组成不同的层状玻璃液,局部熔融的粒状烧结物(疙瘩)。这种 不均质体的存在,对玻璃质量的影响极大。例如,主体玻璃与不均质体两者膨胀系数不同, 在界面必将产生结构应力,这往往是导致制品炸裂的重要原因;如两者光学常数不同,必然 使光学玻璃产生光畸变;如两者粘度不同,必然使窗玻璃产生波筋,条纹等;如两者化学组 成不同,必然使其界面的析晶倾向增大。为消除这种不均体,使整个玻璃液在化学成分上达到 一定的均匀性,这就是玻璃液的均化 过程。不同制品对玻璃化学组分的均化程度要求不同,普通钠钙硅玻璃的均化温
17、度可低于澄 清温度。玻璃液的均化过程常按如下三种方式进行;(1) 不均质体的溶解与扩散玻璃液的均化过程是一个不均质体的溶解与扩散过程。在高粘度的玻璃液中,扩散速度远 远低于溶解速度,因而,玻璃液的均化过程实际上取决于扩散速度dc/d。而扩散速度取决于 物质的扩散系数D,两相的接触面积S与两相的浓度差(C-C),dc/d =DS(C-C)由上式可知,要增加玻璃液的均化速度就必须增大扩散系数D和两相接触面积S。其中 扩散系数是温度和粘度的函数,其关系式为;D=KT/6nrn=RT/A6nrn式中 K 玻尔兹曼常数T 绝对温度r 分子半径n介质粘度,R 阿佛加德罗常数所以要提高扩散系数就必须提高熔体
18、温度 ,以降低粘度,但这受制于熔窑耐火材料的制 约。上述扩散公式是指在静止液相中的扩散。显然,不均质体在静止的高粘性玻璃液中的扩 散是极其缓慢的,熔融玻璃液的扩散系数仅为10-6-10-7 厘米/秒。例如,要消除一毫米宽的 线道所需的时间为 227 个小时。(2)玻璃液的对流 大窑和坩埚内各处玻璃液的温度是不同的,这导致玻璃液产生对流。液流断面上的速度 梯度会将玻璃液的线道拉长,不仅增加了扩散面积,而且增大了浓度梯度,从而增强了扩散 作用。可见,玻璃液的热对流有益于玻璃液的均化,但这种流动属层流而不是湍流,因而对 玻璃液的均化作用有限。热对流所产生的均化作用还有其不利的一面。这是因为热对流也增
19、强了对耐火材料的侵 蚀,这会在玻璃液中产生新的不均质体。尤其是在某些对耐火材料侵蚀大的光学玻璃中,这 种影响尤为显著。(2)因气泡上升而引起的均化当气泡由玻璃液深处向表面上浮时,气泡上浮带动附近的玻璃液流动,形成一定程度的翻滚, 在断面上产生的速度梯度导致不均质体的拉长;同时,不均质体受上浮气泡上升力的作用拉 长而成线状。这将加快玻璃液的均化过程。在玻璃液的均化过程中,除粘度外,玻璃液的表面张力对均化也有一定的影响。当玻璃 液的表面张力小于不均质体的表面张力时,不均质体的表面积趋于减小,不利于均化。为加速玻璃的均化,常采用如下方法;(1)适当提高玻璃液温度,以降低玻璃液的粘度。(2)机械搅拌
20、用坩埚窑熔制光学玻璃或特种玻璃时,常用搅拌器加速玻璃均化。(3)沸腾法 在高温时,将湿木块,萝卜或土豆等到压入玻璃液底层,使产生大量气泡,引 起剧烈搅动,从而加速玻璃均化。(3)鼓泡法 对池窑底部的玻璃液进行鼓泡,以加快均化过程。5玻璃液的冷却 均化好的玻璃液不能马上用以成型,这是因为不同成型方法要求不同的玻璃粘度。成型方法 确定后,它所需要的粘度对不同组成的玻璃来说所对应的温度也不一样。均化好的玻璃液的 粘度比成形需要的粘度小。为了达到成型所需要的粘度,就必须降温。这就是熔制玻璃过程 中冷却阶段的目的。对一般的钠钙硅玻璃,通常要降温到1000C左右才能进行成型。 在冷却阶段,影响产品产量和质
21、量的两个因素是玻璃液的热均匀程度和是否产生二次气泡。 在冷却过程中,不同部位的玻璃液间多少会有一定的温差。当这种热不均匀性超过某一范围 时,对生产会带来不利影响。生产上采用的强制冷却往往不利于玻璃液的热均化过程。 在冷却阶段,玻璃液的温度,窑内的气氛及压力制度都发生了很大的变化。因而破坏了原有 的气液相之间的平衡。由于玻璃液是高粘滞的熔体,要建立新的平衡比较缓慢。因此,在冷 却过程中平衡条件虽然改变了,也不一定出现二次气泡。但必须重视有产生二次气泡的内在 因素。二次气泡又称再生泡或灰泡,其特点是直径小(一般小于 0。 1 毫米),数量多(每立方厘米 可达几千个),分布匀。对产生二次气泡的机理已
22、作了不少研究,认为不同玻璃产生二次气 泡的原因不尽相同。硫酸盐的热分解 在已澄清的玻璃液中往往残留有硫酸盐,它们可能来自配合料中的芒硝,也可能性是炉气中的SO2,O2与碱金属氧化物反应的产物(Na20+S02+l/202 NaS03). 当某种原因使已经冷却的玻璃重新加热时,将导致硫酸盐的分解而析出二次气泡。二次气泡 的生成量不仅与温度高低有关,还与升温速率有关。升温快,二次气泡多;当窑内存在还原 气氛时,也能使硫酸盐分解而产生二次气泡。溶解气体的析出 气体的溶解度一般随温度的降低而升高。因而冷却后玻璃液再次升高温 度时将放出气体而形成气泡。6影响玻璃熔制过程的因素61 原料及配合料的影响(1
23、)配合料的化学组成配合料的化学组成对玻璃熔制速度有决定性的影响。配合料内助熔剂越多,熔制就越快。两 者的关系可用熔化速度常数T表示;T=SiO2+A12O3/Na2O+K2O+0.5 B2O3+0.125PbO这个公式只适于玻璃液的形成直至砂粒消失为止的阶段。熔化速度常数越小,玻璃熔化温度 越低;熔化速度常数t6. 05. 54.84.2熔化温度1450-146014201380-14001320-1340熔化速度常数是一个经验值,只能用以粗略估计。对于含B2O3高的玻璃,就不适用。(2)原料的性质 原料的粒度对熔化影响很大,颗粒有不规则的外形,粒度小而均匀,熔化就快;配合料的气 体率应符合要
24、求。气体的含量及种类对玻璃液的澄清及均化都有影响;另外,应从多方面考 虑选用原料的合理性。对同一氧化物组分,由不同的原料引入时,会不同程度地影响配合料 的分层(如重碱与轻碱),挥发量(如硬硼石与硼酸),熔化温度(如 Al2O3 由氧化铝粉引 入时熔点为2050,由钾长石引入时熔点为1170C),必然对熔制产生不同的影响;配合料 中的碎玻璃,可以加速玻璃熔化,但其成分必须与所生产的玻璃相同,掺入量必须稳定。(3)配合料的加工 应根据不同原料的化学性质和比重,确定其颗粒大小,以避免配合料分层;配合料中加水, 可以减少粉料的飞扬,石英砂表面为水润湿后,可以溶解纯碱和芒硝,促进石英砂的溶化。 均匀分布
25、的水分,有利于热传导,水分汽化时对玻璃液起强烈的搅拌作用,增大配合料的受 热面积。如水分过大,会增大热耗,影响熔化;配合料应混合均匀,保证任一点的配合料组 成均一致,在搬运,保存过程中不分层。62 助熔剂及澄清剂的使用助熔剂对加速玻璃熔制作用十分显著。如B2O3能降低玻璃液粘度,引入1。5%的B2O3, 可使熔窑产率提高15%-20% ;如As2O3和KNO3的混合物,能使Fe O氧化成Fe2O3,提 高玻璃液的透明度,使玻璃液的热透过性增强,从而加速熔制过程;氟化物是一种强助熔剂,在澄清阶段,氟化物蒸汽和 SiF4 的放出,加速了澄清过程。氟化物与氧化铁反应,既能生成易挥发的FeF3,大大降
26、低玻璃液中的铁含量,又能生成无色络 合物Na3FeF6,提高玻璃液的透热性。63 加料方式 加入熔窑中配合料的厚度,对玻璃的熔化速度及熔窑的生产率有重要影响。 对于池窑,以往采用间歇式加料,有许多缺点。加料时形成料堆,料堆表面温度高,内部温 度低。表面易熔原料首先熔化,沿料堆往下淌,造成已熔玻璃料液的成分不均,料堆上层低 碱部分难于熔化。粘度较大而结成薄膜,气体很难通过;料堆在自重作用下大部分沉入玻璃 液中给熔化和澄清造成困难;间歇加料时玻璃溢液面经常波动,加剧了对池壁砖的侵蚀,耐 火材料颗粒混入量增大,影响了玻璃质量;此外,加料时打开投料口,吸入冷空气使窑温波 动,影响了正常的温度制度。间歇
27、加料时,严重的飞料极易堵塞格子砖通道。玻璃池窑现多采用连续薄层加料,其优点是;配合料以薄的长垅状沿熔窑均匀分布,物料既 能得到由对流和辐射方式从上方传来的热量,也能得到由玻璃液通过热传导从下方传来的热 量,由于受热快,促进了配合料的熔化;因为料层薄,避免了配合料沉入玻璃液中,又由于 玻璃表面层温度高,有利于气泡的排除,缩短了澄清时间。64 熔制温度,气氛和压力制度 熔化温度是决定玻璃熔化速度和玻璃熔制质量的主要因素。提高熔化温度有利于料粒的熔 化,玻璃液的澄清和均化,对于平板玻璃的熔制,熔制温度在1450-1550C范围内时,温度 每升高10C,熔化能力就提高5%-10%。熔化温度与玻璃形成时
28、间及熔化率的关系如下表所 示;熔化温度与玻璃形成时间关系表玻璃熔化温度C14001450玻璃形成时间 min53736熔化温度与熔化率关系表玻璃熔化温度C137014201500155016001650420910 04024147015001530160017001 6熔化率 kg/m2d 3507001050150018003000在熔窑耐火材料允许的条件下,应尽量提高熔制温度。玻璃液对窑内气氛的变化反应极为灵敏。在无特殊要求的情况下,一般以中性焰为佳,但实 际上多数采用弱还原焰。在使用芒硝做澄清剂时,要加入一定数量的煤粉,用以进行还原反 应,为防止煤粉在投料口过早燃烧,应将熔化部产前半部
29、调整为还原性火焰。在澄清部,煤粉必须烧尽,所以澄清部应保持中性或弱氧化性气氛。澄清部采用氧化气氛利于氧化亚铁的 氧化与玻璃液的澄清。对铅玻璃的熔制,必须采用氧化气氛,否则,铅玻璃及其原料会被还 原出金属铅。窑内压力应保持在微正压或零压,以防止冷空气进入。窑内正压又不能太大,否则会影响玻 璃液的澄清,并造成烟气喷出,致使窑温下降。65 高压和真空熔制在熔制石英玻璃时,常采用高压和真空熔制技术来消除玻璃液中的气泡,高压可使小气 泡溶解于玻璃液中,抽真空可以使可见气泡迅速膨胀而排除。66 辅助电熔 在用燃料加热的熔窑中,将电流通入玻璃液中作为辅助热源,可在不增加熔窑容量的前提下 增加产量,这种新的熔制方式称为辅助电熔。加热部设在加料口,熔化部及作业部下方,可 使料层下的玻璃液温度提高40-70C,可大大提高熔化率。67 机械搅拌与鼓泡在窑池内进行机械搅拌或鼓泡是提高玻璃液澄清速度和均化速度的有效措施。
- 温馨提示:
1: 本站所有资源如无特殊说明,都需要本地电脑安装OFFICE2007和PDF阅读器。图纸软件为CAD,CAXA,PROE,UG,SolidWorks等.压缩文件请下载最新的WinRAR软件解压。
2: 本站的文档不包含任何第三方提供的附件图纸等,如果需要附件,请联系上传者。文件的所有权益归上传用户所有。
3.本站RAR压缩包中若带图纸,网页内容里面会有图纸预览,若没有图纸预览就没有图纸。
4. 未经权益所有人同意不得将文件中的内容挪作商业或盈利用途。
5. 装配图网仅提供信息存储空间,仅对用户上传内容的表现方式做保护处理,对用户上传分享的文档内容本身不做任何修改或编辑,并不能对任何下载内容负责。
6. 下载文件中如有侵权或不适当内容,请与我们联系,我们立即纠正。
7. 本站不保证下载资源的准确性、安全性和完整性, 同时也不承担用户因使用这些下载资源对自己和他人造成任何形式的伤害或损失。