机械制造工艺学输出轴机械加工工艺规程制订课程设计
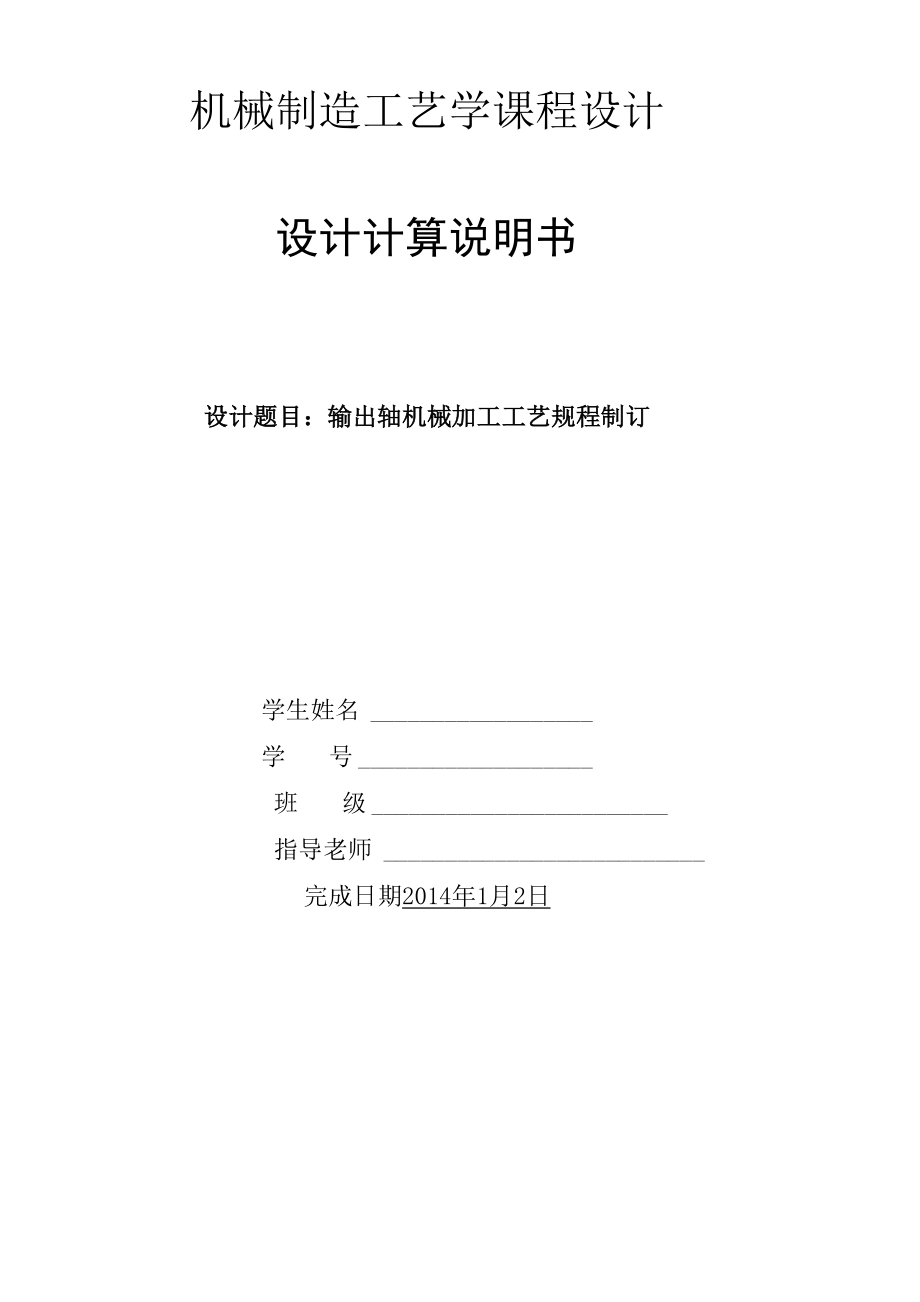


《机械制造工艺学输出轴机械加工工艺规程制订课程设计》由会员分享,可在线阅读,更多相关《机械制造工艺学输出轴机械加工工艺规程制订课程设计(33页珍藏版)》请在装配图网上搜索。
1、机械制造工艺学课程设计设计计算说明书设计题目:输出轴机械加工工艺规程制订学生姓名学号班级指导老师完成日期2014年1月2日目录第一节序言1 第二节零件分析一、零件的功用分析2二、零件的工艺分析2第三节 机械加工工艺规程制订一、确定生产类型3二、确定毛坯制造形式31、毛坯种类的选择42、毛坯制造方法的选择4三、选择定位基准1、精基准的选择42 、粗基准的选择 5四、选择加工方法1、典型面的加工形式52、机械加工顺序的安排6五、制定工艺路线1、工序的划分62、工艺路线的确定7六、确定加工余量、粗糙度及毛坯尺寸1、各工序加工余量和表面粗糙度的确定82、确定毛坯的尺寸8七、工序设计1、加工设备及工艺装
2、备选择92、工序尺寸及其公差的确定10八、确定切削用量和基本时间1 、切削用量和基本时间的参数 1 22、各工序的切削余量和时间定额的具体计算13第四节 专用机床夹具的设计一、明确设计要求、收集设计资料-27二、确定定位方案、选择定位元件-27三、确定工件夹紧方案,设计夹紧机构-28四、确定夹具总体结构和尺寸29五、夹具精度分析30六、夹具使用说明30参考文献第一节 序言机械制造工艺学课程设计是在我们学完了机械制造工艺学基础课、部分专业 程并完成了生产实习及之后进行的。这是我们进行毕业设计之前对所学各课程的 一次深入的综合性的链接,也是一次理论联系实际训练。它要求学生综合地运用 所学过的专业知
3、识,针对一个具体的工程实际零件进行机械加工工艺规程制订及 专用机床夹具设计,使学生初步具备制订机械加工工艺规程及设计专用机床夹具 的能力,为随后的毕业设计进行一次综合训练和准备,也为以后所从事的机械工 程工作打下基础。就我个人而言,我希望能通过这次课程设计对自己未来将从事 的工作进行一次适应性训练,从锻炼自己分析问题、解决问题的能力,为今后参 加祖国的现代化建设打下一个良好的基础。我也相信通过课程设计能将零碎的知 识点都联系起来,系统而全面的做好设计。本次课程设计是机械制造工艺学这门课程的一个阶段总结,是对课堂中学习 的基本理论中学到的实践知识的一个实际应用过程。由于知识和经验所限,设计 会有
4、许多不足之处,所以恳请老师给予指导。本次设计的目的在于:(1)熟练运用机械制造工艺学课程中的基本理论,正确地解决零件在加工 过程中的定位、夹紧以及工艺路线的安排,工序尺寸的确定等问题,制订出保证 该零件质量的机械加工工艺规程。(2)针对机械加工工艺规程中的某一道工序,选择合适的定位、夹紧、向 等原件,组成合理的定位、夹紧、导向方案,设计出适合该工序的专用机床夹具, 进一步提高结构和机构的设计能力。(3)培养综合分析和解决本专业的一般工程问题的独立能力,拓宽和深化 所学知识。(4)培养树立正确的设计思想、设计思维,掌握工程设计的一般程序、规 范和方法的能力。(5)培养正确地使用技术知识、国家标准
5、、有关手册、图册等工具书,进 行设计计算、数据处理、编写技术文件等方面的工作能力。(6)培养自己进行调查研究、面向实际、面向生产,向工人和工程技术人 员学习的基本工作态度、工作作风和工作方法。(7)熟悉轴类零件加工工艺过程和掌握夹具设计的方法步骤,为以后从事 相关的技术性工作打下坚实的基础。(8)通过对输出轴零件的机械加工工艺设计,使我们在机械制造工艺规程 设计,工艺方案论证,机械加工余量计算,工艺尺寸的确定,编写技术文件及查 阅技术文献等各个方面得到一次综合性训练。初步具备设计一个中等复杂程度零 件工艺规程的能力。(9)能根据被加工零件的技术要求,运用夹具设计的基本原理和方法,拟 定夹具设计
6、方案,完成夹具机构设计,初步具备设计出高效、省力、经济合理并 能保证加工质量的专用夹具的能力。(10)通过零件图、装配图的绘制,使我们进一步熟练绘图软件的使用。 熟悉和掌握我国相关的制图标准和要求。机械制造技术基础课程设计所选定的题目为输出轴零件的加工工艺及夹具 设计,结合机械制造技术基础及大学四年专业相关课程,完成了对输出轴从零件 毛坯到零件成品的加工过程分析和工艺安排。包括零件各工作表面的加工选择, 机床、刀具、定位、夹紧;并对其中某些关键加工工序做了夹具设计,由于知识 和经验所限,设计会有许多不足之处,所以恳请老师给予指导。第二节 零件分析一、零件的功用分析本设计所设计的零件是机床变速器
7、输出轴,其主要作用:一是传递转矩,使 车床主轴获得转动的动力,二是工作过程中经常承受载荷,三是支撑传动零部件。 84的孔与变速器配合起定心作用,通过10- 24的通孔将动力传至该轴, 再由 59处通过键将动力输出。该轴在工作中需要承受一定的冲击载荷和较大 的扭矩。因此,该轴应具有足够的耐磨性和抗扭强度。设计中一定要注意表面热 处理。因为它是动力输出的关键零件之一,它的加工质量对机床的安全性和稳定 性都有很大的影响。二、零件的工艺分析从图示零件分析,该输出轴结构简单,属于阶梯轴类零件。主要由有59、 64、69、79、180的外圆柱面、54、84、108的内圆柱表面和10 个24的孔和一个16的
8、键槽组成。为了保证输出轴旋转是的速度,表面粗糙度 有较高的要求,外圆的粗糙度要求都为Ra12.5um,内圆的粗糙度为Ra2.5um,轴 的小端面的粗糙度为Ra25um,大端面为Ra3.2um。形位精度也比较高,为了外圆 和外面零件的配合后受力均匀,59,64的外圆的径向跳动量小于0. 04mm, 84的跳动量小于0.04mm, 24孔的轴线的跳动量小于0.05mm,为了保证键槽 和键的配合,键槽对59外圆的对称度为0.08mm。由于输出轴在工作中要承受 较大的冲击载荷和扭矩,为了增强耐磨性和抗扭强度,要对输出轴进行调质处理, 硬度为200230HBW,保持均匀。通过分析该零件,其布局合理,方便
9、加工,我 们通过径向夹紧可保证其加工要求,整个图面清晰,尺寸完整合理,能够完整表 达物体的形状和大小,符合要求第三节 机械加工工艺规程制订一、确定生产类型零件的生产类型是指企业(或车间、工段、班组、工作地等)生产专业化程 度的分类,一般可分为大量生产、成批生产和单件生产三种类型,在实际生产中 一般分为单件小批生产、中批生产、大批大量生产。不同的生产类型有着完全不 同的工艺特征,它对工艺规程的制订具有决定性的影响。零件的生产类型是按零 件的年生产纲领和产品特征来确定的。生产纲领是指企业在计划期内应当生产的 产品产量和进度计划。年生产纲领是包括备品和废品在内的某产品年产量。零件 的生产纲领N可按下
10、式计算:N = Qn (1 + a % + 卩 %)式中:N零件的生产纲领,单位为件/年Q产品的年产量(台/年)n每台产品中该零件的数量(件/台)嚥-备品率,一般取2%-4%*%-废品率,一般取0.3%-0.7%根据上式就可以计算求得出零件的年生产纲领,再通过查表,就能确定该零 件的生产类型。假设输出轴Q=10000件,备品率为3%,机械加工废品率为0.5%,则该零件 的年生产纲领为N=Qn (1+:+陀)=10000X1X(1 + 3%+0.5%)件/年=10351 件/年 可见,输出轴的年产量是10351件。根据机械制造工艺学课程设计指导书 表5-8,零件质量为6kg左右,可知该零件为轻型
11、零件,本设计零件变速器输出 轴的生产类型为轻型大批量生产,其毛坯制造、加工设备及工艺装备的选择应呈 现大批生产的工艺特点,如利用专用设备配以通用工艺设备等,其工艺特点见表 5-9。二、确定毛坯制造形式毛坯的选择和拟定毛坯图是制定工艺规程的最初阶段工作之一,也是一个比 较重要的阶段,毛坯的形状和特征(硬度,精度,金相组织等)对机械加工的难 易,工序数量的多少有直接影响,因此,合理选择毛坯在生产占相当重要的位置, 同样毛坯的加工余量的确定也是一个非常重要的问题。毛坯种类的选择决定与零件的实际作用,材料、形状、生产性质以及在生产 中获得可能性,毛坯的制造方法主要有以下几种:1、型材 2、锻造 3、铸
12、造 4、 焊接 5、其他毛坯。根据零件的材料,推荐用型材或锻件,但从经济方面着想, 如用型材中的棒料,加工余量太大,这样不仅浪费材料,而且还增加机床,刀具 及能源等消耗,而锻件具有较高的抗拉抗弯和抗扭强度,冲击韧性常用于大载荷 或冲击载荷下的工作零件。1、毛坯种类的选择根据零件的形状、材料分析,材料为 45号钢轴类零件,适合型材或锻件, 但从经济方面着想,如用型材棒料加工余量太大,这样浪费材料,也增加机床、 刀具等的损耗;而且从零件的用途分析,输出轴将传递较大的扭矩,性能要求高, 而锻件具有较高的抗拉抗弯和抗扭强度,冲击韧性大,故综合考虑选用锻件。2、毛坯制造方法的选择毛坯的选择和拟定毛坯图是
13、制定工艺规程的最初阶段工作之一,也是一个比 较重要的阶段,毛坯的形状和特征(硬度,精度,金相组织等)对机械加工的难 易,工序数量的多少有直接影响,因此,合理选择毛坯在生产占相当重要的位置, 同样毛坯的加工余量的确定也是一个非常重要的问题。 毛坯种类的选择决定与零件的实际作用,材料、形状、生产性质以及在生产中获 得可能性,毛坯的制造方法主要有以下几种:1、型材 2、锻造3、铸造4、焊接5、其他毛坯。根据零件的材料,推荐用型材或锻件,但从经济方面着想,如用 型材中的棒料,加工余量太大,这样不仅浪费材料,而且还增加机床,刀具及能 源等消耗,而锻件具有较高的抗拉抗弯和抗扭强度,冲击韧性常用于大载荷或冲
14、 击载荷下的工作零件。三、选择定位基准1、精基准的选择选择精基准的出发点是保证加工精度,特别是加工表面的相互位置精度,以 及安装的方便可靠。其选择的原则要遵从基准重合,基准统一,自为基准,互为 基准等原则。加工输出轴时,主要体现的是基准统一和自为为基准原则。在轴类零件加工中,为保证各主要表面的相互位置精度,选择定位基准时, 应尽可能使其与装配基准重合并使各工序的基准统一,而且还要考虑在一次安装中尽可能加工出较多的面。轴类零件加工时,精基准的选择通常有两种: 首先方案是采用顶尖孔作为 定位基准。这样,可以实现基准统一,能在一次安装中加工出各段外圆表面及其 端面,可以很好的保证各外圆表面的同轴度以
15、及外圆与端面的垂直度,加工效率 高并且所用夹具结构简单。所以对于实心轴(锻件或棒料毛坯) ,在粗加工之 前,应先打顶尖,以后的工序都用顶尖孔定位。对于空心轴,由于中心的孔钻出 后,顶尖孔消失,可采用下面的方法:(1) 在中心通孔的直径较小时,可直接在孔口倒出宽度不大于 2mm 的 6锥 面,用倒角锥面代替中心孔。(2) 在不宜采用倒角锥面作为定位基准时,可采用带有中心孔的锥堵或带锥 堵的拉杆心轴。锥堵与工件的配合面应根据工件的的形状做成相应的锥形,如果 轴的一端是圆柱孔,则锥堵的锥度取 1:500。通常情况下,锥堵装好后不应拆 卸或更换,如必须拆卸,重装后必须按重要外圆进行找正和修磨中心孔。如
16、果轴 的长径比较大,而刚性差,通常还需要增加中间支承来提高系统的刚性,常用的 辅助支承是中心架或跟刀架。 精基准选择的另一方案是采用支承轴径定位因为 支承轴径既是装配基准,也是各个表面相互位置的设计基准,这样定位符合基准 重合的原则,不会产生基准不重合误差,容易保证关键表面间的位置精度。根据上述定位基准的选择原则,分析本零件,选取顶尖孔作为定位精基准。 当零件外圆加工完毕以后,可以以外圆为精基准加工内孔,由于前面的工序使用 中心孔精加工出来的输出轴外圆同轴度非常高,并且表面粗糙度等各项性能指标 都很高,故使用加工后的外圆作为精基准而加工出来的孔和外圆的同轴度也非常 高。本零件选择两中心孔和 7
17、9作为精基准,选择59和 180作为粗基准来 加工两中心孔。2、粗基准的选择。对于一般的轴类零件而言,以外圆作为粗基准是完全合理的。本零件就是先 以大端为基准加工小端端面和中心孔,然后夹大端,顶小端粗车各外圆。然后以 外圆为基准粗加工各孔。这样可以保证各重要加工表面加工余量充足,而且使重 要加工表面的加工余量尽量均匀。四、选择加工方法1、典型面的加工形式 粗加工阶段:其任务是切除毛坯上大部分余量,使毛坯在形状和尺寸上接近 零件成品,因此,主要目标是提高生产率,去除内孔,端面以及外圆表面的大部 分余量,并为后续工序提供精基准,如加工59、64、69、79、180外 圆柱表面。半精加工阶段:其任务
18、是使主要表面达到一定的精加工余量,为主要表面的 精加工做好准备,如59、64、69、79外圆柱面,84内孔、10X024 法兰孔等。精加工阶段:其任务就是保证各主要表面达到规定的尺寸精度,并可完成一 些次要表面的加工。如精度和表面粗糙度要求,主要目标是全面保证加工质量, 如各轴颈外圆精磨。热处理工序的安排:热处理的目的是提高材料力学性能,消除残余应力和改 善金属的加工性能。热处理主要分:预备热处理,最终热处理和内应力处理等。 本零件输出轴材料为45钢,加工前进行正火预备热处理是在毛坯锻造之后消除 零件的内应力。粗加工之后,为消除因加工变形残余内应力,同时降低材料的硬 度,获得零件材料较高的综合
19、力学性能,采用调质处理。表4-1 输出轴各加工表面方案需加工表面尺寸精度等级表面粗糙度Ra/um加工方案59外圆IT712.5um粗车一半精车一精车64外圆IT 612.5um粗车一半精车一精车69外圆IT 612.5um粗车一半精车一精车79外圆IT 612.5um粗车一半精车一精车180外圆12.5um粗车54内孔12.5um粗车84内孔IT 73.2um粗车一半精车一精车108内孑L3.2um粗车 24通孔IT 73.2um钻一扩一铰8通孔12.5um钻键槽底表面IT 96.3um粗铣一精铣键槽两侧表面IT 93.2 um粗铣一精铣轴小端面IT725 um轴大端面IT73.2um2、机械
20、加工顺序的安排(1)机械加工顺序 遵循“先基准后其他”原则,首先加工精基准,即在前面加工阶段先 加工输出轴的左、右端面,59和180外圆表面,钻中心孔。 遵循“先粗后精”原则,先安排粗加工工序,后安排精加工工序。 遵循“先主后次”原则,如先加工外圆表面,再加工键槽。 遵循“先面后孔”原则,先加工79外圆表面,做为定位基准再加工 其余各孔。(2)热处理工序 毛坯锻造成型后,应当对毛坯进行正火处理以去除内应力,然后再进行机械加工。在粗加工之后、精加工之前,安排调质处理,调质硬度为HBW200,获得 良好的综合机械性能。(3)辅助工序 在对本零件的所有加工工序完成之后,安排去毛刺、清洗、终检工序。五
21、、制定工艺路线1、工序的划分(1)工序集中 工序集中就是将零件的加工集中在少数几道工序中完成,每道工序加工内容 多,工艺路线短。其主要特点是:可以采用高效机床和工艺装备,生产率高; 减少了设备数量以及操作工人人数和占地面积,节省人力、物力; 减少了工件安装次数,利于保证表面间的位置精度; 采用的工装设备结构复杂,调整维修较困难,生产准备工作量大。(2)工序分散 工序分散就是将零件的加工分散到很多道工序内完成,每道工序加工的内容 少,工艺路线很长。其主要特点是设备和工艺装备比较简单,便于调整,容易适应产品的变换,对工人的技术 要求较低;可以采用最合理的切削用量,减少机动时间; 所需设备和工艺装备
22、的数目多,操作工人多,占地面积大。 工序集中或分散的程度,主要取决于生产规模。一般情况下,单件小批生产 时,采用工序集中,在一台普通机床上加工出尽量多的表面;批量生产时,采用 工序分散。终上以及结合图纸要求,采用工序分散。2、工艺路线的确定(1)工艺方案一:(仅锻出54孔毛坯)1、备料2、精锻3、粗车小头端面4、粗车各台阶面5、掉头粗车大头端面6、半精车小头端面及各台阶面7、铣键槽8、掉头钻扩铰10X24法兰孔9、粗镗台阶孔10、半精镗84孔11、半精车大头端面12、打大头端面中心孔13、钻2X8油孔14、精车四个台阶面15、精铣大小头端面(2)工艺方案二:(锻出各阶梯孔毛坯)05、锻造毛坯
23、;10、正火;15、粗车、半精车180大端面、59小端面;20、粗车、半精车外圆柱面、倒角;25、钻、扩、铰 10*24 通孔、倒角;30、精车大小两端面;35、粗镗、半精镗、精镗:1血、84、内孔;40、钻中心孔;45、钻2*8斜孔;50、精车外圆柱面;55、铣键槽;60、去毛刺;65、终检;比较方案一方案二,主要区别在于孔加工顺序的安排,是否在外圆加工完后 再加工。分析零件可知,该轴上外圆表面精度较高,而孔除84和10-24外, 其他各孔精度都较低,若在外圆加工完后再以外圆表面定位夹紧来加工孔,可能 会损坏已加工表面。故应尽可能按排在外圆表面加工完之前加工。综上分析,采 用加工方案二。六、
24、确定加工余量、粗糙度及毛坯尺寸1、各工序加工余量和表面粗糙度的确定(1)该轴材料为45钢,屈服强度二 p2 p3精加工时,应根据粗加工留下的余量确定背吃刀量,使精加工余量小而均匀。(2) 进给量 f 的选择粗加工时对表面粗糙度要求不高,在工艺系统刚度和强度好的情况下,可以 选用大一些的进给量;精加工时,应主要考虑工件表面粗糙度要求,在一般表面 粗糙度数值越小,进给量也要相应减小。(3) 切削速度 v 的选择切削速度主要应根据工件和刀具的材料来确定。粗加工时, 主要受刀具寿 命和机床功率的限制。如超出了机床许用功率,则应适当降低切削速度;精加工 时,a和f用得都较小,在保证合理刀具寿命的情况下,
25、切削速度应选取的尽可 p 能高,以保证加工精度和表面质量,同时满足生产率的要求。切削用量选定后, 应根据已选定的机床,将进给量f和切削速度v修定成机床所具有的进给量f 和转速n,并计算出实际的切削速度v。工序卡上填写的切削用量应是修定后的 进给量f、转速n及实际切削速度v。转速n (r/min)的计算公式如下:n-十xlOOO,式中d刀具(或工件)直径(nm); v切削速度(m/min )(4)时间定额的选择时间定额T包括:基本时间Tm、辅助时间Ta、布置工作地时间Ts、休息与 T生理需要时间Tr、准备与终结时间Te。单件和成批生产的单件时间定T - T + T - T + T + T + T
26、 + TT p n m a s r n大批量生产的单件时间定T =T +T +T +TT m a s r2、各工序的切削余量和时间定额的具体计算(1)工序15粗车 外圆059端面切削用量及基本时间的确定计算切削用量切削深度:a = 2.5mm,一次切除。p进给量:根据机械制造工艺学课程设计指导书表5-42,选用f=0.6mm/r 计算切削速度:按机械制造工艺学课程设计指导书表 5-43,切削速度的计 算公式为v = -XX 1 (m/min)c t 0 .2 a 0 .15 f 0 . 35(寿命选 T=60min),式中c = 403。v当切削条件变换时要加上修正系数 k。查机械制造工艺学课
27、程设计指导书v表 5-32, K“ = 1.15 , K = 0.8 , k = 1,K = 1, K = 0.97 。MVSVkvkrvBV所以,V =Cvk =x 1.15 x 0.8 x 1 x 1 x 0.97 =165-3(m/mc t 0.2 a 0.15 f 0.45 V 60 0.22.50.150.6 0.35pin)确定机床主轴转速:1000 V 二 100 x 165 .3 =877.4(r/min)n =Cs兀d兀x 60w按机床选取n =900r / min 。所以实际切削速度兀dn = xx 60 x 900 =169.56(m/min)1000 1000计算切削工
28、时:t l + l + l 式中,1 = =30, l = 3, I = 0,所以 t =匸212nf2l + l + l = 30 + 3=0.06 (min)t =|2nf900 x 0.6(2)工序20车4)180外圆及端面,粗车各内孔、倒角,切削用量及基本时间的确定计算切削用量(a) 车 180端面切削深度:a = 2.5mm,一次切除。 p进给量:根据机械制造工艺学课程设计指导书表5-42,选用f=0.94mm/r。计算切削速度:按机械制造工艺学课程设计指导书表 5-43,切削速度的计算公式为(寿命选 T=60min)Cvt 0.2 a 0.15 f 0.45(m/min),式中 c
29、 = 393。v当切削条件变换时要加上修正系数Kv。查机械制造工艺学课程设计指导书表5-32, K =1.15, K =0.8, K =1, K =1, K = 0.97。 MVSVkvkrvBV所以,V = CTK =393x 1.15 x 0.8 x 1 x 1 x 0.97=1386C t0.2 a0.15 f 0.45 V60 0.22.50.15 0.94 0.45p(m/min)确定机床主轴转速:1000 V = 1000 x 138 .6 =243.9(r/min) n =ls x dx x 181w按机床选取n =250r/min。所以实际切削速度V =兀dn =兀 x 181
30、 x 250 =142.1 (m/min)1000 1000计算切削工时1 + i + i,式中 l = 90.5 , l = 3 , l = 0,所以 t l + l + l = 90 .5 + 3 =0.40 nfnf250 x 0.94(min)(b) 车180外圆面切削深度:a = 2.5mm,一次切除。p进给量:根据机械制造工艺学课程设计指导书表5-42,选用f=0.94mm/r。 计算切削速度:按机械制造工艺学课程设计指导书表 5-43,切削速度的计(m/min),式中。c = 313v算公式为(寿命选T=60min), v =c”Ct 0.2 a 0 .15 f 0.45p当切削
31、条件变换时要加上修正系数Kv。查机械制造工艺学课程设计指导书表5-32,KM=115,K = 0.8,SVk =1, K = 0.81, K = 0.97。 kvkrvBV所以,cvt 0 .2 a 0 .15 f 0 .45p313x 1.15 x 0.8 x 1 x 0.81 x 0.9760 0.22.50.15 0.94 0.45=89.4(m/min)确定机床主轴转速按机床选取n =160r/min。1000 v = 1000 x 89 .4 =157.3 (r/min)C兀dw 所以实际切削速度兀 x 181兀dnV1000=兀 x 181 x 160 =90. 9(m/min)1
32、000检验机床功率:主切削力Fc按金属切削原理所示公式计算得:F =9.81 CZFza pxFz f yFzv nFzk Fz式中:C =270,C FzxFz=1.0y =0.75,Fzn =-0.15FzkmFb=( b ) n0 . 6370 . 6= 0-956kkrF=0.89k yaF=0.9k = 1九FF z =981 x 270 x 2.5 x0.940.75 x90.9-0.15 x 0.956 x 0.89 x 0.9 x 1 =2461 (N)切削时消耗功率pc为F vc c6 x 10 42461 x 90.96 x 10 4=3.72(kW )由机械制造工艺学课程
33、设计指导书表5-13可知,CA6140主电动机功率 为7.5kW,故机床功率足够。检验机床进给系统强度:,径向切削力 F按金属切削原理所示公式计算 :F =9.81c axFyf yFyv nFy k Fy yFypFy已知主切削力FZ = 2734-5Ny式中:c =199; x =0.9; y =0.6; n =-0.3FyFyFyFyk = ( & b )n =)1.35 = 0.922mF 0 .637 f 0 .637kkrF二 0-50k = 0.7yaF仁二 1.25Af所以:F = 9.81 x 199 x 2.50.9 x 0.94 0.6 x 90.9-0.3 x 0.92
34、2 x 0.50 x 0.7 x 1.25 = 447 .4( N) z而轴向切削力F =9.81 c a xFx f yFxv nFx kxFx pFx式中: c =294; x =1.0; y =0.5; n =-0.4FxFxFxFxk = ( & b )n = (-016 ) = 0.941mF0 .637 f0 .637k = 1.17krFk = 0.7yaFF 二 9.81 x 294 x 2.5 x 0.94 0.5 x 90.9 -0.4 x 0.941 x 1.17 x 0.7 x 0.85 二 754xk = 0.85(N)AF取机床导轨与床鞍之间的摩擦系数口=0.1则切
35、削力在纵向进给方向对进给 机构的作用力为F = F + u(F + F ) = 754 + 0.1 x (2461 + 447 .4) = 1044 .8(N)x y z而机床纵向进给机构可承受的最大纵向力为3530N,故机床进给系统可正常 工作。切削工时:nf式中 / = 30,l = 3,l = 0,所以12t = I + 匚 + 12 =30 + 3=0.22 (min)t 12nf 160 x 0.94(c) 粗车108内孔切削深度:a 2.6mm,一次切除。p进给量:根据机械制造工艺学课程设计指导书表 5-42,选用 f=0.2mm/min。计算切削速度:按机械制造工艺学课程设计指导
36、书表5-43,切削速度的计算公式为cvt 0 .2 a 0 .15 f 0 .2(m/min),式中 c 393。v寿命选 T=60min)V C当切削条件变换时要加上修正系数。查机械制造工艺学课程设计指导书表 5-438,K MV所以,1 . 15K 0.8SVK 1, kvK 0.9 ktK 0.81 K 0 .97 krvBV393t 0 .2 a 0.15 f 0 .2p60 0.22.60.15 0.20.2x1.15 x0.8x1x0.9x0.81x0.97 =135.6(m/min)确定机床主轴转速n1000 二1000 x 135 .6 =437(r/min)兀 x98.8按机
37、床选取n =400r/min。所以实际切削速度V 1000兀dn =兀 x 98 .8 x 400 =124.1 (m/min)1000计算切削工时t -亠丄式中1 = 10,l1 = 3,l2 = 0,所以Tnfl + l + l =10 丄 3=0.16 (min)t =T 210nf400 X 0 .2(d) 粗车84内孔切削深度: a = T.25mm ,一次切除。p进给量:根据机械制造工艺学课程设计指导书表5-42,选用 f=0.2mm/r。 计算切削速度:按机械制造工艺学课程设计指导书表 5-43,切削速度 的计算公式为寿命选 T=60min)V Cc(m/min),式中 c =
38、393vvt 0 . 2 a 0 . T5 f 0 . 2p当切削条件变换时要加上修正系数Kv。查机械制造工艺学课程设计指导书表 5-32,KMV=T.T5,所以KSV= 0.8 Kkv= TK = 0 .9 ktK = 0.8T K = 0.97BVkrvm/min)vt 0 .2 a 0.T5 f 0 .2K=V393X 1.15 X 0.8 X1X 0.9 X 0.81 x 0.97 =150.4600.21.250.150.20.2确定机床主轴转速:n=1000 V = 1000 x 150 .4 =618.1 (r/min)C按机床选取n =560r/min。所以实际切削速度V T0
39、00兀 dn =兀 x 75 x 560 =136.3(m/min)T000计算切削工时t =亠土厶式中1 = 13 l = 3 I = 0,所以Tnft = 1 + - + 12 二一=0.14 (min)nf(e)粗车54内孔560 X 0 .2切削深度:a = 2mm, 一次切除。 p进给量:根据机械制造工艺学课程设计指导书表5-42,选用f=0.2mm/r。 计算切削速度:按机械制造工艺学课程设计指导书表5-43切削速度 的计算公式为寿命选 T=60min) VCc(m/min),式中 c = 393。vvt 0.2 a 0 .15 f 0.2当切削条件变换时要加上修正系数S。查机械制
40、造工艺学课程设计指导书表 5-32,KMV = 1.15 KSV= -8 所以,SVK = 1,kvK 二 0.9, K 二 0.81, K 二 0.97 。 ktkrvBVcTK =393 x 1.15 x 0.8 x 1 x 0.9 x 0.81 x 0.97 =140,2(m/min)t0.2 a0.15 f 0.2 V 60 0.220.15 0.20.2p确定机床主轴转速:1000 VC兀d二 1000 x 140 .2 =970.7(r/min)n x 46w按机床选取n =560r/min。所以实际切削速度- ndn = n x 46 x 900 =130(m/min) V =1
41、000 1000计算切削工时l + l. + l,式中 l = 17, l = 3, l = 0,所以 t =匸12nfl + l + l = 17 + 3=0.11 (min)t = 12-nf900 x 0 .23)工序 25 粗车小端外圆表面切削用量及基本时间的确定计算切削用量(a)车180左端面切削深度: a =1.25mm ,一次切除。a = 1 . 25 mm p进给量:根据机械制造工艺学课程设计指导书表5-42,选用f=0.94mm/r。 计算切削速度:按机械制造工艺学课程设计指导书表5-43,切削速度 的计算公式为寿命选 T=60min) VC393c(m/min),式中vct
42、 0 .2 a 0.15 f 0 .45vp当切削条件变换时要加上修正系数Kv。查机械制造工艺学课程设计指 导书表 5-32,K = 1.15 , MVK SV = 0.8Kkv= 1K =1, K = 0.97。 krvBV所以,cvt 0.2 a 0.15 f 0.45p=393KV 60 0.21 .25 0.15 0.94 0.45x 1.15 x 0.8 x 1x 1x 0.97=127.9(m/min)确定机床主轴转速:1000 V = 1000 x 127 .9 =231.4(r/min)ns=n d Cn x 176w按机床选取n =250r/min。所以实际切削速度V =兀d
43、n =兀 x 176 x 250 =138.16(m/min) 1000 1000计算切削工时1 + 1 + 1,式中 1 = 30,l = 3,l = 0,所以 t =1-12nf1 + 1 + 1 =30 + 3=0.14(min)t =12nf250 x 0.94(b)粗车各外圆切削深度:a = 1.25 mm , 一次切除。 p进给量:根据机械制造工艺学课程设计指导书表5-42,选用f=0.6mm/r。 计算切削速度:按机械制造工艺学课程设计指导书表5-43,切削速度 的计算公式为(寿命选T=60min)C式中 c = 327 。vc(m/min),vt 0.2 a 0 .15 f 0
44、.35pK = 1.15 , KMVSV=0.8, K kv当切削条件变换时要加上修正系数S。查机械制造工艺学课程设计指 导书表5-32,1 , K = 0 , K = 0.97 。krvBV所以,v =v Kc t 0 .2 a 0 .15 f 0 .35 Vpm/min)39360 0.21.25 0.15 0.60.35x 1. 15 x 0.8 x 1 x 0.81 x 0.97=120.5ns51000V=Cndw11000V=Cndw21000V=Cndw31000V=Cndw41000Vns1ns2ns3ns4C兀dw5确定机床主轴转速: =1000 x 120 .5 =639.
45、6(r/min)n x 60二 1000 x 120 .5 =590.4(r/min)n x 65=1000 x 120 .5 =548.2(r/min)n x 70二 1000 x 120 .5 =479.7(r/min)n x 80=1000 x 120 .5 =319.8(r/min)n x 120按机床选取n =500r/min。所以实际切削速度兀d n =兀 x 60 x 500 =94.2(m/min)V =1 1 1000 1000 兀d n = n x 650 x 500 =102.5(m/min)V =22 1000 1000- nd n = n x 70 x 500 =10
46、9.9(m/min)V =3-3 10001000V = nd 4n = n x 80 x 500 =l25.6(m/min)410001000- nd n = n x 120 x 500 =188.4(m/min)V =5-510001000检验机床功率:主切削力f按金属切削原理表5-13所示公式计算cF =9.81 C a xFz f yFzv nFzkzFz pFz式中: C =270;x =1.0;y =0.75;n =-0.15FzFzFzFzkmF =命)叮=(廿75 = 0-956k krF=0.89所以: F = 9.81 x 270 x1.25x0.6 0.75 x 188 .4 -0.15 x 0.956 x0.89x0.9x1= 787 .7(N) z切削时消耗功率P为cF Vc c6 x 10 4787 .7 x 1206 x 10 4=1.58(kw)由机械制造工艺学课程设计指导书表5-14可
- 温馨提示:
1: 本站所有资源如无特殊说明,都需要本地电脑安装OFFICE2007和PDF阅读器。图纸软件为CAD,CAXA,PROE,UG,SolidWorks等.压缩文件请下载最新的WinRAR软件解压。
2: 本站的文档不包含任何第三方提供的附件图纸等,如果需要附件,请联系上传者。文件的所有权益归上传用户所有。
3.本站RAR压缩包中若带图纸,网页内容里面会有图纸预览,若没有图纸预览就没有图纸。
4. 未经权益所有人同意不得将文件中的内容挪作商业或盈利用途。
5. 装配图网仅提供信息存储空间,仅对用户上传内容的表现方式做保护处理,对用户上传分享的文档内容本身不做任何修改或编辑,并不能对任何下载内容负责。
6. 下载文件中如有侵权或不适当内容,请与我们联系,我们立即纠正。
7. 本站不保证下载资源的准确性、安全性和完整性, 同时也不承担用户因使用这些下载资源对自己和他人造成任何形式的伤害或损失。
最新文档
- 部编人教版语文三年级下册第八单元 方帽子店 ppt课件
- 微生物灭菌问题培训课件
- 廊坊房地产市场整合课件
- 廖小菲XXXX财务报告—利润表-课件
- 廊坊售后11月目标完成报告课件
- 部编人教版四年级语文上册《口语交际 我们与环境》优质ppt课件
- 延伸存取列表课件
- 部编人教版语文三年级下册第六单元 习作:身边那些有特点的人 ppt课件
- 廉颇蔺相如列传重点语句翻译上课-课件
- 廉颇蔺相如列传课件
- 廉颇蔺相如列传公开课优质课-课件
- 微生物活菌计数方法教学课件
- 部编人教版三年级数学下册第4课时 简单的路线图课件
- 廉洁行医秉公奉廉医疗卫生行业廉洁自律培训模板课件
- 部编人教版六年级道德与法制上册第8课《我们受特殊保护》 ppt课件完整版