铸造工艺学课程设计
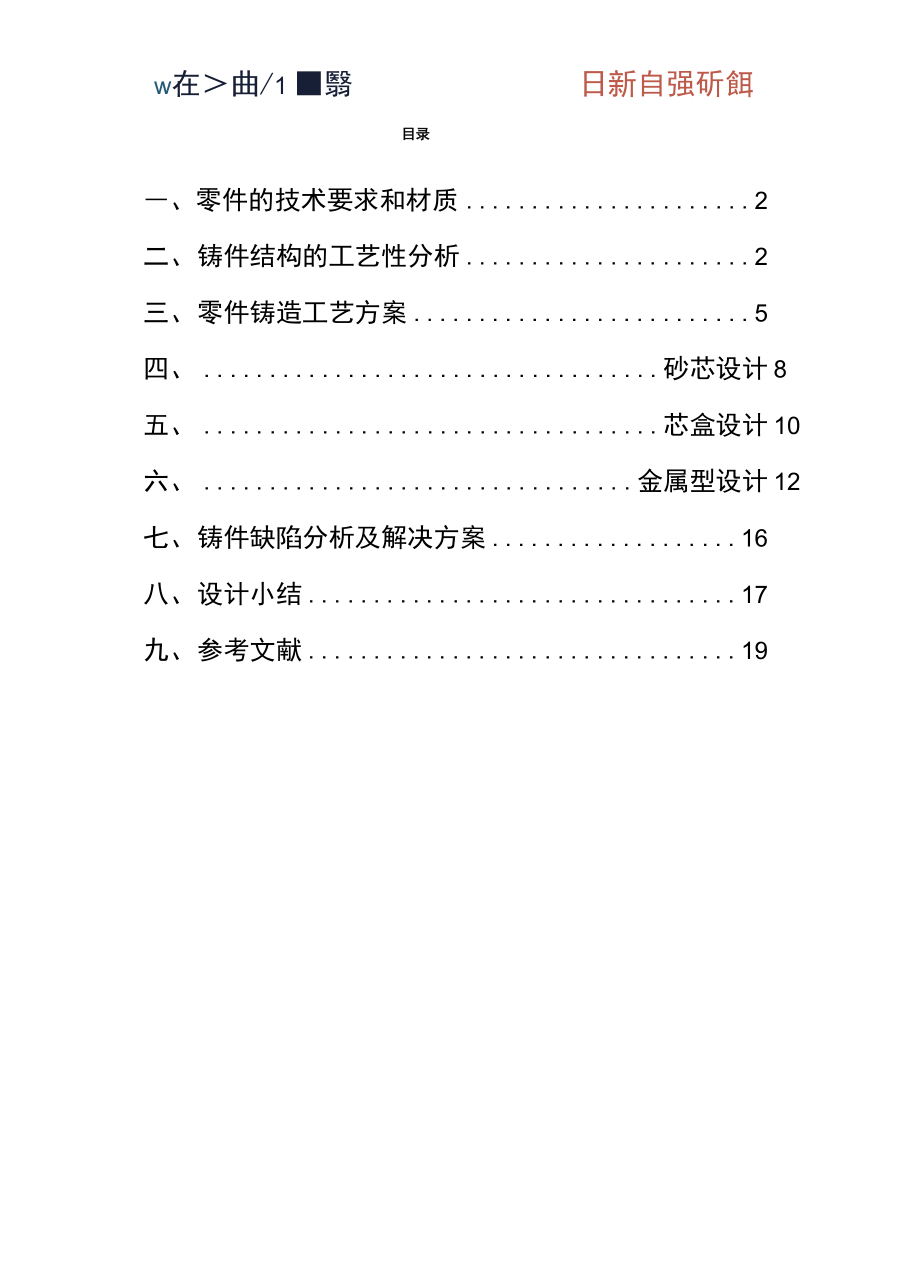


《铸造工艺学课程设计》由会员分享,可在线阅读,更多相关《铸造工艺学课程设计(20页珍藏版)》请在装配图网上搜索。
1、w在曲/1 翳日新自强斫餌目录、零件的技术要求和材质2二、铸件结构的工艺性分析2三、零件铸造工艺方案5四、砂芯设计8五、芯盒设计10六、金属型设计12七、铸件缺陷分析及解决方案16八、设计小结17九、参考文献19越為&点止學日掰自强術合设计内容、设计步骤、公式及计算备注一、零件的技术要求及材质零件名称:盖11、零件的技术要求铸件尺寸公差按GB6414 - 86 CT41.2零件的材质分析材料:ZL102铸件成型材料为ZL102,其化学成分如下:表一 ZL102化学成分SiCuMgMnAl10.0-13.0W 0.30 (杂质)W0.10W 0.5 (杂质)余量中大批量生产金属型铸造由于ZL10
2、2成分在共晶点左右,故在铝硅二元系中,铸 造性能最好强度也较高,致密度较好,但塑性较低。具有良好 的抗蚀性,耐磨性和耐热性。必须进行热处理,提高力学性能。 适用于薄壁复杂铸件及对气密性要求较高的铸件以及压铸件。二.铸件结构的工艺性分析从铸造工艺角度,结合零件结构特征对铸造生产方法进行 选择。本零件因中大批量生产,采用金属型。2.1、铸件壁厚铸件的壁厚要力求均匀,壁的后、薄不宜相差悬殊,在保证 能浇注成型的条件下尽量采用最小壁厚;尽量避免采用大的薄 壁平面,若必需采用大的薄壁平面时,则设有铸孔或加强筋。 ZL102砂型铸造中的最小壁厚为3mm。盖的零件图如图所示,壁厚基本均匀,主要壁厚3mm,最
3、 小壁厚3mm,最大壁厚21mm,为一小型铸件;铸件除满足几何 尺寸精度及材质方面的要求外,无其他特殊技术要求。2.2、壁的连接铸件的连接应圆滑过度,并应尽量避免铸件有厚大的热节点,尤其是三个以上断面集结于一点或一根线上,都是比较难于铸造的。零件如图2-1:图2-1零件图魁為于大學日新自强瓠亓合:2.3、铸件三维实体图三铸造工艺方案的设计铸造工艺方案设计的内容主要有铸造工艺方法的选择,铸 件浇注位置及分型面的选择,铸件初加工基准面的选择,铸造工 艺设计有关工艺参数的选择等。3. 1、铸造工艺方法的选择铸造工艺方法的选择应综合考虑以下因素:(1)零件的使用性能:即零件承受的载荷情况情况及其所处的
4、 工作环境(例如压力、温度、气态或液态介质的性质等)对铸件 的尺寸精度和表面光洁度的要求。(2)零件的铸造工艺性能:即零件所采用的合金材料的铸造性能 (如合金熔点、线收缩、体收缩、流动性以及形成气孔、缩孔等缺陷的倾向:见表2)和零件结构的铸造工艺性,如零件重量、 轮廓尺寸、最小壁厚、最小铸孔、铸造圆角、铸造斜度等。(3)经济的合理性:即各种铸造方法生产费用的比较和成品零件 的生产总费用综合性比较。在合理选择铸造方法时,后者的比较 起决定作用。倉為$4乞空止學日歸自强斫合3.2、浇注位置及分型面的选择3.2.1、浇注位置的选择原则:(1) 铸件上重要工作面和大平面应尽量朝下或垂直安放(2) 应保
5、证铸件有良好的液态金属导入位置,保证铸件能充满(3) 保证铸件能自下而上的顺序凝固(4) 应尽量少用或不用砂芯;3. 2.2、铸件分型面的选择原则:(1) 最好将整个铸件安置在同一半型中成型,(2) 应尽量减少分型面的数目。(3) 应尽量不用或少用砂芯,(4) 分型面应尽量选择平面。底注式左(5) 注意减轻铸件清理和机械加工量。 右开型。 该零件的浇注位置和分型面如图3-1:底注式左右开型。图3-1铸件图3. 3、机械加工初基准的选择机械加工初基准的选择应注意下列问题(1) 应尽量选择铸件非加工面为初基准:(2) 应选择加工余量最小或尺寸公差最小的表面为初基准:(3) 应选择铸件尺寸最稳定的表
6、面为加工初基准:(4) 当铸件上没有合适的初基准时,可增设工艺凸台作为辅助 基准。该零件的初基准如图3-2 :图3-2铸件图(部分)机械加工余量为1mm外表面的 起模斜度1,内表 面的起模 斜度为2芯头高12mm,斜度a=2 ,“D”式芯头.3.4、工艺参数的选择:(1)机械加工余量的选择:根据航空铸造工艺手册及铸件的最外廓尺寸可选机械加工余量为1mm;(2)工艺余量的选择:收缩率取 对于金属型铸造,为了简化模具,故把这两侧凸台上的直径1%为10mm的孔做成工艺余量。(3)铝合金收缩率取1%;(4)铸件尺寸公差按GB6414-86CT4;(5)据2表3-57可选定,外表面的起模斜度1,内表面的
7、起 模斜度为2。四、砂芯设计砂芯的功用是形成铸件的内腔、孔和铸件外型不能出砂的分. 砂型局部要求特殊性能的部分有时也用砂芯.盖采用树脂砂手工制芯4.1芯头的设计砂芯主要靠芯头固定在模底板上。对于垂直芯头为了保证, 轴线垂直、牢固地固定在砂型上,必须有足够的芯头尺寸。盖的芯头高度为12mm;垂直芯头的斜度a=2。为了定位采 用“D”式芯头.4.2、冷铁的设计O在丼學晡自强溺合-日新自强瓠行合五、芯盒装配的设计5.1芯盒材料的选择采用ZL104,自由线收缩率0.91.1%,标准:GB1173-74。5.2芯盒分盒面的设计,如图5-1旧1Lf-DLL1图5-1芯盒装配图5.3芯盒内腔尺寸的确定芯盒内
8、腔尺寸二(零件尺寸士工艺尺寸)(1+K)5.4芯盒的壁厚根据芯盒的平均轮廓尺寸(A+B) /2,及芯盒材质来决定壁芯盒壁厚7mm厚。(A+B)/2300mm,材料为ZL104,由砂型铸造工装设计 查表11-4得:壁厚5 =7mmo5.5芯盒的定位与夹紧 用铰链式卡子将其锁紧,如图5-2.5.6金属芯盒的尺寸偏差分开式芯盒分盒面之间的间隙取0.1mm。在分盒面上芯 盒内腔错位的允许偏差为0.1mm.芯盒上定位销孔距公差为 0.25mm。5.7芯盒的搬运芯盒的搬运:本芯盒体积小,所以不设置手柄和吊轴,直 接用芯盒边缘实现搬运过程.扩张式 浇注系统0图6-1浇注系统图金属型设计6.1、浇注系统及冒口
9、的设计和计算6.1.1浇注系统的设计(1)铝合金金属铸造常采用扩张式浇注系统。其形式如图6-1:(2)浇注系统最小断面积的计算:Fmin二KQ/bH式中:Q:铸件的毛重(g)K:系数(铝合金为0.0080.0108)b:铸件平均壁厚(包括加工余量在内),cmFmin=1.1cmH:铸件的高度,cmFmin:浇道最小断面积(cm?)经计算得:Q=0.23Kg,K=0.008 b=0.35cm H=4.1cm所以 Fmin=1.1cm2F 直=1.1cm21.1F内=12卅6.1.2直、内浇道断面积的确定查看参考资料得:F直:F内二1: (0.51 ),取F直:F内二1:所以 F 直=1.1cm2
10、, F 内二 1.2cm26.1.3冒口的设计与计算(1)、采用明冒口,增大补缩,起尺寸如图6-2(2)、冒口的切割余量=5mm(3)、为了便于切割,可将冒口的跟的切割余量做成缩颈图6-2冒口表示图6.2、型体、底座设计6.2.1、型腔尺寸计算型腔尺寸的计算,除了铸件公称尺寸及偏差外,还应考虑合金 从固相线冷却到室温的收缩。涂料厚度和金属型材料从室温升 至预热浇注温度的膨胀率。计算公式Ax二(Ap+ApK5)AAx式中Ax型腔尺寸,mm;Ap铸件平均尺寸,mm;K综合线收缩,;5涂料厚度,mm; Ax铸型尺寸制造公差,mm.铸件的平均尺寸按下式计算Ap二Amin+AA/2K=1%;5 =0.2
11、mm.经计算型腔尺寸如图6-3:6.2.2、金属型的壁厚金属型的壁厚是综合考虑金属型强度、刚度重量及铸件的冷却曰新自强斫合速度来确定的。壁厚太大,增加铸型重量,操作笨拙,没有必 要;壁厚过薄,铸型温度不均,易因应力而变形,缩短寿命。铸型的型芯综合考虑及结合经验数据,因铸件壁厚10mm ;铝合金铸件金属型壁厚15mm20mm.取壁厚为15mm.排气经计算型腔尺寸及壁厚如下图:6.2.3、型腔的排气 应该铸件有砂芯,所以采用铸型的型芯排气,见图6-4定位销定位锁紧机构:图6-4型腔排气图插销锁,偏心624、铸型的定位采用定位销定位锁锁6.2.5锁紧机构(1)、铰链式金属型的固定支点为插销锁。其形状
12、及尺寸如图6-5:曰新自强知行合r(2)、用偏心锁锁紧左如图6_6:图6-5插销锁右半型,图6-6偏心锁七、铸件缺陷分析与解决方案铸造工艺设计的是否合理,影响到是否能够获得合格的、 高质量的铸件。此次设计因薄壁铸件可能存在一些缺陷:为防 止卷气,因此需控制金属液的流速,保证金属液平稳充型。為必点/以學曰歸自强溺合-八、设计心得经过四个星期的努力,我终于将铸造工艺课程设计做完了。 在这次作业过程中,我遇到了许多困难,一遍又一遍的计算,一 次又一次的设计方案修改这都暴露出了前期我在这方面的知 识欠缺和经验不足.刚开始在铸造工艺设计时,我始终找不到 最佳的分型面和浇注方案,令我非常苦恼.后来在蔡老师
13、的指 导下,我找到了问题所在之处,将之解决了。因太久没有电脑绘 图,在用AUTOCAD画图时遇到了很多困难,但在同学和老师的 帮忙下,最终克服了困难。在此我要向他们表示最诚挚的谢意。 整个作业过程中,我遇到的最大,最痛苦的事是文档。一来自己 没有电脑,用起来很不方便;最可恶的是在此期间, AUT0CAD2007的免费版本有病毒,几乎把我们全班人的电脑都 感染了,以至于画不出剖面线,最后还是在一台有很强杀毒软 件的电脑上,经复制粘贴到新的图纸上才成功的画好了剖面 线,圆满地完成了这次设计。尽管这次作业的时间是漫长的,过程是曲折的,但我的收获 还是很大的。不仅仅掌握了金属型模具设计的步骤与方法;也
14、 不仅仅对铸造工艺设计这门课有了更进一步的掌握。对我来 说,收获最大的是方法和能力,那些分析和解决问题的方法与 能力。在整个过程中,我发现像我们这些学生最最缺少的是经 验,没有感性的认识,空有理论知识,有些东西很可能与实际脱為必点/以學曰歸自强溺合-节。总体来说,我觉得做这种类型的设计对我的帮助还是很大 的,它需要我们将学过的相关知识都系统地联系起来,从中暴 露出自身的不足,以待改进.有时候,一个人的力量是有限的, 合众人智慧,我们的作品会更完美.最后再次感谢蔡老师的悉心指导!為必点/以學曰歸自强溺合-九、参考资料(1) 严青松:铸造工艺学,南昌航空大学自编教材。(2) 李维谦、唐自忠主编:航空铸造手册,国营洪都机械厂 1980、 10(3) 耿鑫明编著:金属型铸件生产指南,化学工业出版社,2008.8(4) 龙文元、卢百平主编金属液态成型模具设计化学工业出版社,2010.6(5) 铸造工艺设计及铸件缺陷控制,李希晨主编,化学工业出版社,2009
- 温馨提示:
1: 本站所有资源如无特殊说明,都需要本地电脑安装OFFICE2007和PDF阅读器。图纸软件为CAD,CAXA,PROE,UG,SolidWorks等.压缩文件请下载最新的WinRAR软件解压。
2: 本站的文档不包含任何第三方提供的附件图纸等,如果需要附件,请联系上传者。文件的所有权益归上传用户所有。
3.本站RAR压缩包中若带图纸,网页内容里面会有图纸预览,若没有图纸预览就没有图纸。
4. 未经权益所有人同意不得将文件中的内容挪作商业或盈利用途。
5. 装配图网仅提供信息存储空间,仅对用户上传内容的表现方式做保护处理,对用户上传分享的文档内容本身不做任何修改或编辑,并不能对任何下载内容负责。
6. 下载文件中如有侵权或不适当内容,请与我们联系,我们立即纠正。
7. 本站不保证下载资源的准确性、安全性和完整性, 同时也不承担用户因使用这些下载资源对自己和他人造成任何形式的伤害或损失。