互换性的概念
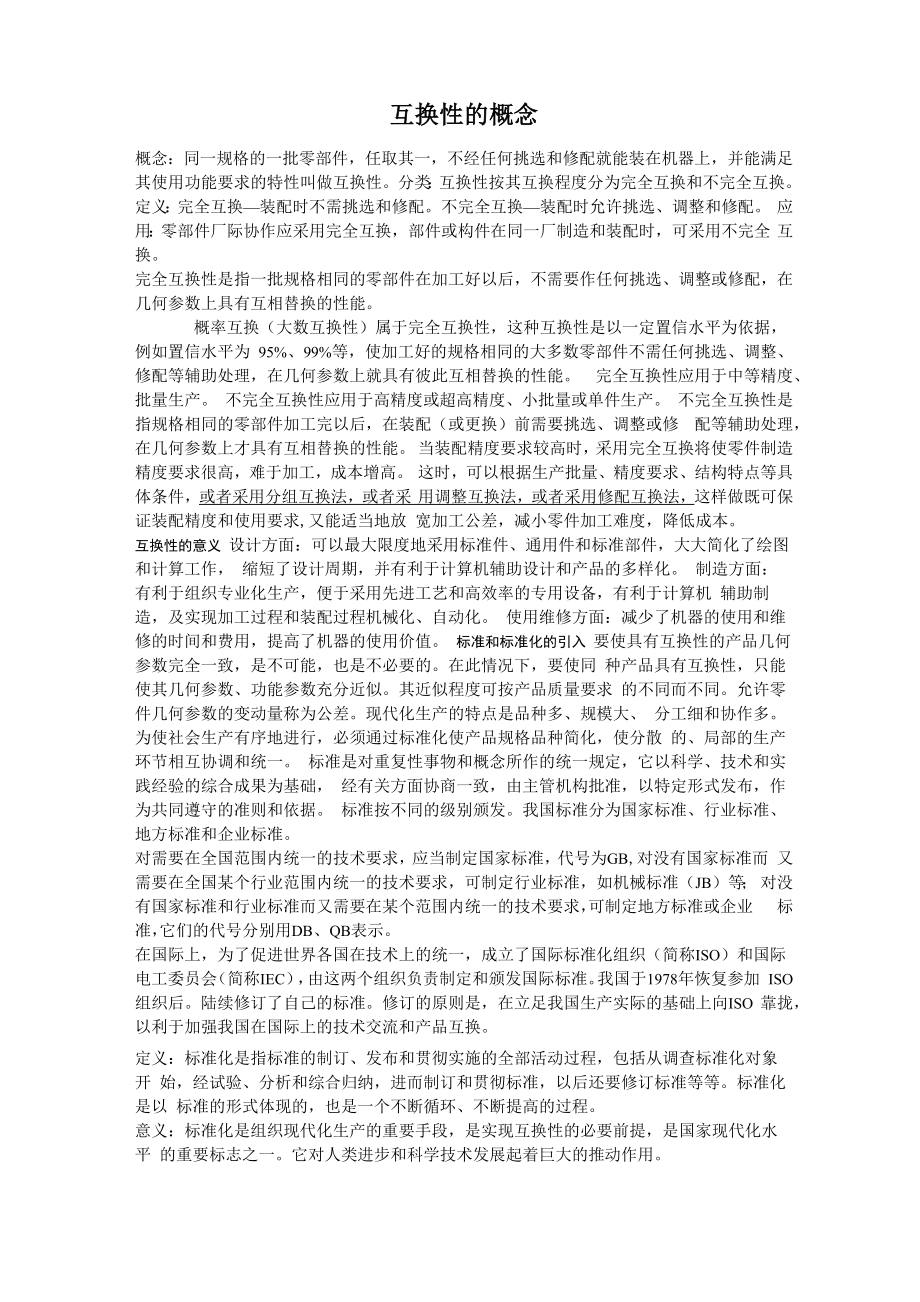


《互换性的概念》由会员分享,可在线阅读,更多相关《互换性的概念(18页珍藏版)》请在装配图网上搜索。
1、互换性的概念概念:同一规格的一批零部件,任取其一,不经任何挑选和修配就能装在机器上,并能满足 其使用功能要求的特性叫做互换性。 分类:互换性按其互换程度分为完全互换和不完全互换。 定义:完全互换装配时不需挑选和修配。不完全互换装配时允许挑选、调整和修配。 应用:零部件厂际协作应采用完全互换,部件或构件在同一厂制造和装配时,可采用不完全 互换。完全互换性是指一批规格相同的零部件在加工好以后,不需要作任何挑选、调整或修配,在 几何参数上具有互相替换的性能。概率互换(大数互换性)属于完全互换性,这种互换性是以一定置信水平为依据, 例如置信水平为 95%、99%等,使加工好的规格相同的大多数零部件不需
2、任何挑选、调整、 修配等辅助处理,在几何参数上就具有彼此互相替换的性能。 完全互换性应用于中等精度、批量生产。 不完全互换性应用于高精度或超高精度、小批量或单件生产。 不完全互换性是指规格相同的零部件加工完以后,在装配(或更换)前需要挑选、调整或修 配等辅助处理,在几何参数上才具有互相替换的性能。 当装配精度要求较高时,采用完全互换将使零件制造精度要求很高,难于加工,成本增高。 这时,可以根据生产批量、精度要求、结构特点等具体条件,或者采用分组互换法,或者采 用调整互换法,或者采用修配互换法,这样做既可保证装配精度和使用要求,又能适当地放 宽加工公差,减小零件加工难度,降低成本。互换性的意义
3、设计方面:可以最大限度地采用标准件、通用件和标准部件,大大简化了绘图和计算工作, 缩短了设计周期,并有利于计算机辅助设计和产品的多样化。 制造方面:有利于组织专业化生产,便于采用先进工艺和高效率的专用设备,有利于计算机 辅助制造,及实现加工过程和装配过程机械化、自动化。 使用维修方面:减少了机器的使用和维修的时间和费用,提高了机器的使用价值。 标准和标准化的引入 要使具有互换性的产品几何参数完全一致,是不可能,也是不必要的。在此情况下,要使同 种产品具有互换性,只能使其几何参数、功能参数充分近似。其近似程度可按产品质量要求 的不同而不同。允许零件几何参数的变动量称为公差。现代化生产的特点是品种
4、多、规模大、 分工细和协作多。为使社会生产有序地进行,必须通过标准化使产品规格品种简化,使分散 的、局部的生产环节相互协调和统一。 标准是对重复性事物和概念所作的统一规定,它以科学、技术和实践经验的综合成果为基础, 经有关方面协商一致,由主管机构批准,以特定形式发布,作为共同遵守的准则和依据。 标准按不同的级别颁发。我国标准分为国家标准、行业标准、地方标准和企业标准。对需要在全国范围内统一的技术要求,应当制定国家标准,代号为GB,对没有国家标准而 又需要在全国某个行业范围内统一的技术要求,可制定行业标准,如机械标准(JB)等; 对没有国家标准和行业标准而又需要在某个范围内统一的技术要求,可制定
5、地方标准或企业 标准,它们的代号分别用DB、QB表示。在国际上,为了促进世界各国在技术上的统一,成立了国际标准化组织(简称ISO)和国际 电工委员会(简称IEC),由这两个组织负责制定和颁发国际标准。我国于1978年恢复参加 ISO组织后。陆续修订了自己的标准。修订的原则是,在立足我国生产实际的基础上向ISO 靠拢,以利于加强我国在国际上的技术交流和产品互换。定义:标准化是指标准的制订、发布和贯彻实施的全部活动过程,包括从调查标准化对象开 始,经试验、分析和综合归纳,进而制订和贯彻标准,以后还要修订标准等等。标准化是以 标准的形式体现的,也是一个不断循环、不断提高的过程。意义:标准化是组织现代
6、化生产的重要手段,是实现互换性的必要前提,是国家现代化水平 的重要标志之一。它对人类进步和科学技术发展起着巨大的推动作用。优先数和优先数系GB3212005 中规定以十进制等比数列为优先数系,并规定了五个系列,它们分别用系列 符号R5、RIO、R20、R40和R80表示,其中前四个系列作为基本系列,R80为补充系 列,仅用于分级很细的特殊场合。优先数系的五个系列中任一个项值均为优先数。按公比计算得到的优先数的理论值,除 1O 的整数幂外,都是无理数,工程技术上不能直接应用。实际应用的都是经过圆整后的近似值。 根据圆整的精确程度,可分为:(1 )计算值:取五位有效数字,供精确计算用。 (2)常用
7、值:即经常使用的通常所称的优先数,取三位有效数字。 完工后的零件是否满足公差要求,要通过检测加以判断。检测包含检验与测量。 检验是确定零件的几何参数是否在规定的极限范围内,并作出合格性判断,而不必得出被测 量的具体数值; 测量是将被测量与作为计量单位的标准量进行比较,以确定被测量的具体数值的过程。 意义:检测不仅用来评定产品质量,而且用于分析产生不合格品的原因,及时调整生产,监 督工艺过程,预防废品产生。检测是机械制造的“眼睛”。产品质量的提高,除设计和加工精 度的提高外,往往更有赖于检测精度的提高。所以,合理地确定公差与正确进行检测,是保 证产品质量、实现互换性生产的两个必不可少的条件和手段
8、。机械精度设计概述 一般来说,在机械产品的设计过程中,需要进行以下三方面的分析计算: (1)运动分析与计算。根据机器或机构应实现的运动,由运动学原理,确定机器或机构的 合理的传动系统,选择合适的机构或元件,以保证实现预定的动作,满足机器或机构的运动 方面的要求。(2)强度的分析与计算。根据强度、刚度等方面的要求,决定各个零件的合理的基本尺寸, 进行合理的结构设计,使其在工作时能承受规定的负荷,达到强度和刚度方面的要求。(3)几何精度的分析与计算。零件基本尺寸确定后,还需要进行精度计算,以决定产品各 个部件的装配精度以及零件的几何参数和公差。精度设计原则 互换性原则:机械零件几何参数的互换性是指
9、同种零件在几何参数方面能够彼此互相替换的 性能。经济性原则:工艺性 、合理的精度要求、合理选材、合理的调整环节、提高寿命。 匹配性原则:根据机器或位置中各部分各环节对机械精度影响程度的不同,对各部分各环节 提出不同的精度要求和恰当的精度分配,做到恰到好处,这就是精度匹配原则。 最优化原则:探求并确定各组成零、部件精度处于最佳协调时的集合体。例如探求并确定先 进工艺,优质材料等。第一章公差与极限偏差的比较两者区别: 从数值上看:极限偏差是代数值,正、负或零值是有意义的;而公差是允许尺寸的变动范围, 是没有正负号的绝对值,也不能为零(零值意味着加工误差不存在,是不可能的)。实际计 算时由于最大极限
10、尺寸大于最小极限尺寸,故可省略绝对值符号。从作用上看:极限偏差用于控制实际偏差,是判断完工零件是否合格的根据,而公差则控制 一批零件实际尺寸的差异程度。从工艺上看:对某一具体零件,公差大小反映加工的难易程度,即加工精度的高低,它是制 定加工工艺的主要依据,而极限偏差则是调整机床决定切削工具与工件相对位置的依据。 两者联系:公差是上、下偏差之代数差的绝对值,所以确定了两极限偏差也就确定了公差。 加工误差与公差的关系工件在加工过程中,由于工艺系统误差的影响,使加工后的零件的几何参数与与理想值不相 符合,其差别称为加工误差。其中包括:尺寸误差:实际尺寸与理想尺寸之差。几何形状误差:宏观几何形状误差(
11、形状误差,由工艺系统误差所造成)、微观几何形状误 差(表面粗糙度,刀具在工件上留下的波峰和波长)、表面波度误差(加工过程中振动引起 的)。位置误差:各要素之间实际相对位置与理想位置的差值。加工误差是不可避免的,其误差值在一定范围内变化是允许的,加工后的零件的误差只要不 超过零件的公差,零件是合格的。所以,公差是设计给定的,用于限制加工误差的;误差则 是加工过程中产生的。标准公差的特点IT6可读作:标准公差6级或简称6级公差。同一基本尺寸的孔与轴,其标准公差数值大小应随公差等级的高低而不同。公差等级I,公差值(,见表1-8。同一公差等级的孔与轴,随着基本尺寸大小的不同应规定不同的标准公差值。公差
12、是加工误差的允许值,同一等级的公差具有相同的加工难易程度。 总之,标准公差的数值,一与公差等级有关,二为基本尺寸的函数。各种基本偏差形成配合的特点间隙配合有AH (ah)共十一种,其特点是利用间隙贮存润滑油及补偿温度变形、安装 误差、弹性变形等所引起的误差。生产中应用广泛,不仅用于运动配合,加紧固件后也可用 于传递力矩。不同基本偏差代号与基准孔(或基准轴)分别形成不同间隙的配合。主要依据 变形、误差需要补偿间隙的大小、相对运动速度、是否要求定心或拆卸来选定。过渡配合有JSN (jsn)四种基本偏差,其主要特点是定心精度高且可拆卸。也可加键、 销紧固件后用于传递力矩,主要根据机构受力情况、定心精
13、度和要求装拆次数来考虑基本偏 差的选择。定心要求高、受冲击负荷、不常拆卸的,可选较紧的基本偏差,如N (n),反之 应选较松的配合,如:K (k)或JS (js)。过盈配合有PZC (pzc) 13种基本偏差,其特点是由于有过盈,装配后孔的尺寸被胀大 而轴的尺寸被压小,产生弹性变形,在结合面上产生一定的正压力和摩擦力,用以传递力矩 和紧固零件。选择过盈配合时,如不加键、销等紧固件,则最小过盈应能保证传递所需的力 矩。第二早形位公差的标注以公差框格的形式标注(两格或多格)/0 0.05A怪養特征符号公差佰基唯指引线(从表3-1中选)(以mm为单位)(由基准字母表示)(指向被测要素) 公差值如果公
14、差带为圆形或圆柱形,公差值前加注0,如果是球形,加注S0O 基准单一基准用大写表示;公共基准由横线隔开的两个大写字母表示;如果是多基准, 则按基准的优先次序从左到右分别置于各格。 指引线 用细实线表示。从框格的左端或右端垂直引出,指向被测要素。,-OJ0.JA! A 1Bc6 M0Q1s * o.tAB*0.1/0.06甘重要提示: 指引线指向被测要素时,要注意区分轮廓要素和中心要素。 基准符号用带小圆的大写字母以细实线与粗的短实线相连,基准要素也要注意区分轮廓要 素和中心要素。r1J0、-J一也r.LOOO.O15CO0.005丄601C0.02A举例(标注改错)标注的解释.I-o O.QO
15、IZ 0.015B解釋代号含义70鬥&外園林dtf殛度舍差为QOgnn .70险)外慟忌舫寸基准轴钱E的卷向跳动公差为0, Olanm右瑞而对左端面的平行度公差为0 Olnm遂冷带彤状虫同一正截面上,半径差为0,004nuo的两同心圆间的区域左垂宜于基准轴筒的三一测量平 面内,半轻菱为Q”013】叫圆心在 基准轴线R上的两同心圆间的区域距离兔公差.01rinT平行基推 平面的两平行平面间的区域3,0?0C.O21-II0,32A1_I17T图a为给定方向上素线的直线度,其公差带为宽度等于公差值0.02mm的两平行平 面间的区域。图b为轴线在任意方向的直线度,其公差带为直径等于公差值0.02mm
16、的圆柱体内 的区域。图c为给定方向上被测素线对基准素线的平行度,其公差带为宽度等于公差值 0.02mm且平行于基准A的两平行平面间的区域。形位误差及其评定形状误差一般是对单一要素而言的,仅考虑被测要素本身的形状的误差。形状误差评定时, 理想要素的位置应符合最小条件。斤谓最小条件是指被测实际要素对其理想要素的最大变动 量为最小。对于轮廓要素(线面轮廓度除外)符合最小条件的理想要素是指处于实体之外与被测要素相 接触,使被测要素对它的最大变量最小。如图所示,评定形状误差时,形状误差值的大小可用最小包容区域(简称最小区域)的宽度或直径表示。 所谓最小区域,是指包容被测实际要素时,具有最小宽度或直径的包
17、容区。最小包容区域评定形状误差值的方法,称为最小区域法,最小区域法则是符合最小条件的评 定形状误差的基本方法。按最小区域法评定的形状误差值而且是唯一的,因而评定结果具有 权威性。理想要素的位置应符合最小条件。最小条件分为两种情况:轮廓要素 理想要素位于零件实体之外与实际要素接触,并使被测要素对理想要素的最 大变动量为最小中心要素 理想要素应穿过实际中心要素,并使实际中心要素对理想最大变动量为最小 位置误差是对关联要素而言的,关联要素相对于基准有方位要求。因此,位置误差评定时, 被测要素的理想要素的方位与基准有关。定向误差:是被测实际要素对一具有确定方向的理想要素的变动量,该理想要素的方向由基
18、准确定。意义:定向误差值用定向最小包容区域(简称定向最小区域)的宽度或直径表示。定向最小 区域是指按理想要素的方向包容被测实际要素时,具有最小宽度或直径的包容区域。理想要 素首先要与基准平面保持所要求的方向,然再按此方向来包容实际要素,所形成的最小包容 区域,即定向最小区域。定位误差:是被测实际要素对一具有确定位置的理想要素的变动量,该理想要素的位置由基 准和理论正确尺寸来确定。意义:定位误差值用定位最小包容区域(简称定位最小区域)的宽度或直径表示。定位最小 区域是指以理想要素定位来包容被测实际要素时,具有最小宽度或直径的包容区域。如图所 示为点的位置度误差。由基准和理论正确尺寸(图中带框尺寸
19、)确定理想点的位置,以该点 为圆心作一圆包容被测点,此圆内部区域即为定位最小包容区域。定向和定位的相同点和不同点: 相同点:都是将被测实际要素与其理想要素进行比较。 不同点:它们的区别在于确定理想要素方位的条件各有不同。确定定向误差时,理想要素首先受到相对于基准的方向的约束,然后使实际要素对 它的最大变动量为最小,这种最大变动量最小已“定向”的前提,显然与形状误差中涉及的最 小条件有所区别,称为定向最小条件。至于定位误差,则理想要素置于相对于基准某一确定位置上,其定位条件可称为定 位最小条件。公差原则的定义 定义:处理尺寸公差和形位公差关系的规定。有关定义、符号局部实际尺寸(Da、da):实际
20、要素的任意正截面上,两对应点间的距离。局部实际尺寸和单一要素的体外作用尺寸 图例0 0.012050.005520.0关联要素的体外作用尺寸 是局部实际尺寸与位置误差综合的结果。是指结合面全长上,与实际孔内接(或与实际轴外 接)的最大(或最小)的理想轴(或孔)的尺寸。而该理想轴(或孔)必须与基准要素保持 图样上给定的功能关系。关联体外作用尺寸图例图例最大实体状态(MMC):实际要素在给定长度上具有最大实体时的状态。最大实体尺寸(MMS):实际要素在最大实体状态下的极限尺寸。(轴的最大极限尺寸dmax,孔的最小极限尺寸Dmin)边界:由设计给定的具有理想形状的极限包容面。 最大实体边界:尺寸为最
21、大实体尺寸的边界。(最大实体实效状态)MMVC:图样上给定的被测要素的最大实体尺寸(MMS)和该要素 轴线、中心平面的定向或定位形位公差所形成的综合极限状态。最大实体实效尺寸)MMVS:最大实体实效状态下的边界尺寸。MMVS=MMSt 形位其中:对外表面取“+”;对内表面取“-” 最大实体实效边界:尺寸为最大实体实效尺寸的边界。最大实体实效尺寸(单一要素)MM = D hn 一 =&口一。一m me最大实体实效尺寸(关联要素)- elH1S + O. OS= I 5.0独立原则定义:图样上给定的每一个尺寸和形状、位置要求均是独立的,应分别满足要求 标注:不需加注任何符号。应用:应用较多,在有配
22、合要求或虽无配合要求,但有功能要求的几何要素都可采用。适用 于尺寸精度与形位精度精度要求相差较大,需分别满足要求,或两者无联系,保证运动精度 密封性,未注公差等场合。 测量:应用独立原则时,形位误差的数值一般用通用量具测量。 包容要求 定义:实际要素应遵守最大实体边界,其局部实际尺寸不得超过最小实体尺寸。标注:在单一要素尺寸极限偏差或公差带代号之后加注符号“O ”, 应用:适用于单一要素。主要用于需要严格保证配合性质的场合。 边界:最大实体边界。测量:可采用光滑极限量规(专用量具)。包容要求标注 包容要求应用举例 如图所示,圆柱表面遵守包容要求。圆柱表面必须在最大实体边界内。该边界的尺寸为最大
23、实体尺寸020mm, 其局部实际尺寸在0 19.97mm020mm内。直线度/mm定义:控制被测要素的实际轮廓处于其最大实体实效边界之内的一种公差要求。当其实际尺 寸偏离最大实体尺寸时,允许其形位误差值超出其给出的公差值,即形位误差值能得到补偿。 标注:应用于被测要素时,在被测要素形位公差框格中的公差值后标注符号“ M ”;应用于 基准要素时,应在形位公差框格内的基准字母代号后标注符号“ M ”。最大实体要求的应用(被测要素)应用:适用于中心要素。主要用于只要求可装配性的零件,能充分利用图样上给出的公差 提高零件的合格率。边界:最大实体要求应用于被测要素,被测要素遵守最大实体实效边界。最大实体
24、实效尺寸:MMVS=MMS土tt被测要素的形位公差,“+”号用于轴,“-”号用于孔。 最大实体要求应用举例如图所示,该轴应满足下列要求: 实际尺寸在019.7mm020mm之内; 实际轮廓不超出最大实体实效边界,即其体外作用尺寸不大于最大实体实效尺寸 dMMVS=dMMS+t=20+0.1=20.1mm 当该轴处于最小实体状态时,其轴线直线度误差允许达到最大值,即等于图样给出的直线度公差值(00.1mm)与轴的尺寸公差(0.3mm)之和0 0.4mm。V00.1 MA*如图所示,被测轴应满足下列要求: 实际尺寸在011.95mm012mm之内;实际轮廓不得超出关联最大实体实效边界,即关联体外作
25、用尺寸不大于关联最大实 体实效尺寸 dMMVS=dMMS+t=12+0.04=12.04mm当被测轴处在最小实体状态时,其轴线对A基准轴线的同轴度误差允许达到最大值,即等于图样给出的同轴度公差( 0 0.04 )与轴的尺寸公差(0.05)之和( 0 0.09 )。图例采用公差原则边界及边界尺寸mm给定的形 位公差mm可能允许的最大形 位误差值mma独立原则无0.0080.008b包容要求最大实体边界200.021c最大实体要求最大实体实效边界39.90.10.2 最大实体要求的两种特殊应用当给出的形位公差值为零时,则为零形位公差。此时,被测要素的最大实体实效边界等于最 大实体边界,最大实体实效
26、尺寸等于最大实体尺寸。当形位误差小于给出的形位公差,又允许其实际尺寸超出最大实体尺寸时,可将可逆要求应 用于最大实体要求。从而实现尺寸公差与形位公差相互转换的可逆要求。此时,在形位公差框格中最大实体要求的形位公差值后加注“ R ”。 零形位公差举例如图所示孔的轴线对 A 的垂直度公差,采用最大实体要求的零形位公差。该孔应满足下列 要求:实际尺寸在0 49.92mm0 50.13mm内; 实际轮廓不超出关联最大实体边界,即其关联体外作用尺寸不小于最大实体尺寸D=49.92mm。当该孔处在最大实体状态时,其轴应与基准 A 垂直;当该孔尺寸偏离最大实体尺寸时,垂 直度公差可获得补偿。当孔处于最小实体
27、尺寸时,垂直度公差可获得最大补偿值0.21mm。公差原则的选择0 0 QA0 50 +0.13应根据被测要素的功能要求,充分发挥公差的职能和采取该公差原则的可行性、经济性。 独立原则用于尺寸精度与形位精度精度要求相差较大,需分别满足要求,或两者无联系,保 证运动精度、密封性,未注公差等场合。包容要求主要用于需要严格保证配合性质的场合。 最大实体要求用于中心要素,一般用于相配件要求为可装配性(无配合性质要求)的场合 形位公差值的选择 总的原则:在满足零件功能的前提下,选取最经济的公差值。根据零件的功能要求,考虑加工的经济性和零件的结构、刚性,按表中数系确定要素的公差 值。并考虑以下因素:同一要素
28、给出的形状公差应小于位置公差值;圆柱形零件的形状公差 值(轴线的直线度除外)应小于其尺寸公差值;平行度公差值应小于其相应的距离公差值 对于以下情况,考虑到加工的难易程度,在满足零件功能的要求下,适当降低12级选用: 孔相对于轴;细长比较大的轴和孔;距离较大的轴和孔;宽度较大(大于1/2长度)的零件 表面;线对线和线对面的相对于面对面的平行度、垂直度公差。 举例 30K7和 50M7采用包容原则。底面F的平面度公差为0.02mm; 30K7孔和50M7孔的内端面对它们的公共轴线的圆跳 动公差为 0.04 mm。30K7孔和50M7孔对它们的公共轴线的同轴度公差为0.03mm。6- 11H10对5
29、0M7孔的轴线和F面的位置度公差为0.05mm,被测要素的位置度公差应用 第四章 表面粗糙度及检测 在机械零件切削的过程中,刀具或砂轮遗留的刀痕、切屑分离时的塑性变形和机床振动等因 素,会使零件的表面形成微小的峰谷。这些微小峰谷的高低程度和间距状况就叫做表面粗糙 度,也称为微观不平度,它是一种微观几何形状误差。最大实体要求。*CC ll0 .04A-B_350M7_5-1 UU表面粗糙度对零件性能的影响 影响零件的耐磨性。影响配合性质的稳定性。 影响零件的疲劳强度。 影响零件的抗腐蚀性。影响零件的密封性。 对零件的外观等也有着不同程度的影响。表面粗糙度的基本术语取样长度1(新标准用lr):是用
30、于判别被评定轮廓的不规则特征的X轴方向上的长度,是评 定表面粗糙度所规定的一段基准线长度。应与表面粗糙度的大小相适应 (见书 P111 表 4-1。)。规定取样长度是为了限制和减弱表面波纹度对表面粗糙测量结果的影响,一般在一 个取样长度内应包含5个以上的波峰和波谷。评定长度ln (新标准用ln):是用于判别被评定轮廓的X轴方向上的长度,在测量或评定时 所必需的一段长度,可包含一个或几个取样长度。一般情况下,取1n= 51。表面不均匀的表 面,宜选用较长的评定长度。表面粗糙度(评定参数)的选择评定参数的选择:如无特殊要求,一般仅选用高度参数。推荐优先选用Ra值,因为Ra能 充分反映零件表面轮廓的
31、特征。在常用值范围内(Ra为0.0256.3um),优先选用Ra 以下情况下例外:当表面过于粗糙(Ra6.3um)或过于光滑(RaV 0.025 um )时,可选用Rz,因为此 范围便于选择用于测量Rz的仪器测量。当测量面积很小时,如顶尖、刀具的刃部、仪表的小元件的表面,可选用Ry值。 表面粗糙度(参数值)的选择 表面粗糙度参数值的选择原则:在满足零件表面功能要求的前提下,尽量选取较大的参数值。 一般原则:同一零件上,工作表面比非工作表面粗糙度值小;摩擦表面比非摩擦表面要小 受循环载荷的表面要小;配合要求高、联接要求可靠、受重载的表面粗糙度值都应小;同一 精度,小尺寸比大尺寸、轴比孔的表面粗糙
32、度值要小。在零件图上的标注:A、尺寸公差B、形状公差C、位置公差D、表面粗糙度0.015 A530.006a210.0圆柱齿轮传动公差及检测 运动精度:是指传递运动的准确性。为了保证齿轮传动的运动精度,应限制齿轮一转中最大 转角误差Ai工。 运动平稳性精度:要求齿轮运转平稳,没有冲击、振动和噪声。要限制一齿距角范围内转角 误差的最大值i R。 接触精度:要求齿轮在接触过程中,载荷分布要均匀,接触良好,以免引起应力集中,造成 局部磨损,影响齿轮的使用寿命。 齿侧间隙:在齿轮传动过程中,非接触面一定要有合理的间隙。一方面为了贮存润滑油,一 方面为了补偿齿轮的制造和变形误差。上述 4 项要求,对于不
33、同用途、不同工作条件的齿轮其侧重点也应有所不同。如:对于分度机构,仪器仪表中读数机构的齿轮,齿轮一转中的转角误差不超过12, 甚至是几秒,此时,传递运动准确性是主要的; 对于高速、大功率传动装置中用的齿轮,如汽轮机减速器上的齿轮,圆周速度高,传递功率 大,其运动精度、工作平稳性精度及接触精度要求都很高,特别是瞬时传动比的变化要求小, 以减少振动和噪声; 对于轧钢机、起重机、运输机、透平机等低速重载机械,传递动力大,但圆周速度不高,故 齿轮接触精度要求较高,齿侧间隙也应足够大,而对其运动精度则要求不高。 渐开线圆柱齿轮的制造误差影响上述4 项要求的误差因素,主要包括齿轮的加工误差和齿轮副的安装误
34、差。为了便于分析齿轮的各种制造误差对齿轮传动质量的影响,按误差相对于齿轮的方向特征, 可分为径向误差、切向误差和轴向误差;齿轮为圆周分度零件,其误差具有周期性,按误差在齿轮一转中是否多次出现,即在齿轮一 转中出现的周期或频率,可分为以齿轮一转为周期的长周期误差,或低频误差,它主要影响 传递运动的准确性;以齿轮一齿为周期短周期误差,或高频误差,它主要影响工作平稳性。 圆柱齿轮传动精度的评定指标 根据齿轮精度要求,把齿轮的误差分成影响运动准确性误差、影响运动平稳性误差、影响载 荷分布均匀性误差和影响侧隙的误差。并相应提出精度评定指标。运动精度的评定指标 切向综合误差(AF i) 齿距累积误差(AF
35、p)及K个齿距累积误差(AFpk) 齿圈径向跳动(AFr) 径向综合误差(AFi) 公法线长度变动(厶Fw)平稳性的评定指标 一齿切向综合误差(Af i) 一齿径向综合误差(Afi) 基节偏差(Afpb) 齿形误差(Aff) 齿距偏差 (Afpt ) 接触精度的评定指标 齿轮工作时,两齿面接触良好,才能保证齿面上载荷分布均匀。在齿高方向上,齿 形误差会影响两齿面的接触;在齿宽方向上,齿向误差会影响两齿面的接触。 齿向误差( FB):侧隙的评定指标为使齿轮啮合时有一定的侧隙,应将箱体中心距加大或将轮齿减薄。考虑到箱体加 工与齿轮加工的特点,宜采用减薄齿厚的方法获得齿侧间隙(即基中心距制)。齿厚
36、减薄量是通过调整刀具与毛坯的径向位置而获得的,其误差将影响侧隙的大小。此 外,几何偏心和运动偏心也会引起齿厚不均匀,使齿轮工作时的侧隙也不均匀。为控制齿厚减薄量,以获得必要的侧隙,可以采用下列评定指标:齿厚偏差(AES), 公法线平均长度偏差(EWm)齿轮副精度的评定指标齿轮副切向综合误差 Fic:装配好的齿轮副,在啮合转动足够多的转数内,一个 齿轮相对于另一个齿轮的实际转角与公称转角之差的最大幅值。齿轮副的一齿切向综合误差 fic:装配好的齿轮副,在啮合转动足够多的转数内, 一个齿轮相对于另一个齿轮的一个齿距的实际转角与公称转角之差的最大幅值。 齿轮副的接触斑点 :安装好的齿轮副,在轻微制动
37、下运转后,齿面上分布的接触擦 亮痕迹 齿轮副的侧隙 :齿轮副的侧隙分圆周侧隙和法向侧隙。 齿轮精度等级的确定齿轮及齿轮副共规定有12个精度等级,用1, 2, , 12表示。其中1级精度最高, 12级 精度最低。齿轮和齿轮副的误差项目都规定了相应的公差或极限偏差,并将单个齿轮的公差项目分为 I、II、III公差组。齿轮的精度等级应根据齿轮的用途、使用要求、传递功率及圆周速度及其它技术要求而定, 同时考虑切齿工艺及经济性。齿轮3个公差组的精度等级应分别规定,可采用同级,也可以 不同级,但同一公差组中的项目必须同级。一般齿轮传动多按齿轮圆周线速度确定第II公差组的精度等级。当对传递运动准确性没有特
38、别要求时,第I公差组的精度常比第II公差组低一个等级,当所传递的功率不特别大时, 第III公差组一般采用和第II公差组相同的精度等级。标注示例 例: 7 6 6 G M GB10095 1988表示齿轮第I、II、III公差组的精度分别为7级、6级、6级,齿厚上、下偏差代号 分别为G、M。 如果三个公差组的精度等级相同,则只需标注的一个数字: 例:7 FLGB 100951988表示齿轮第I、II、III公差组的精度同为7级,齿厚上、下偏差代号分别为F、L。 例:4 (-0.330、-0.495 ) GB 100951988表示齿轮第I、II、III公差组的精度同为4级,齿厚上、下偏差值分别为-0 .330mm、 -0.495mm。 齿轮装配图上应标注齿轮副精度等级和齿轮副的极限侧隙: 例:副 7 6 6 (+0.223、+0.388) t GB10095-1988 表示齿轮副切向综合误差精度为7级,切向一齿综合误差精度为6级,接触斑点精 度为6级,齿轮副最小、最大圆周侧隙分别为+0.223mm、+0.388mm。
- 温馨提示:
1: 本站所有资源如无特殊说明,都需要本地电脑安装OFFICE2007和PDF阅读器。图纸软件为CAD,CAXA,PROE,UG,SolidWorks等.压缩文件请下载最新的WinRAR软件解压。
2: 本站的文档不包含任何第三方提供的附件图纸等,如果需要附件,请联系上传者。文件的所有权益归上传用户所有。
3.本站RAR压缩包中若带图纸,网页内容里面会有图纸预览,若没有图纸预览就没有图纸。
4. 未经权益所有人同意不得将文件中的内容挪作商业或盈利用途。
5. 装配图网仅提供信息存储空间,仅对用户上传内容的表现方式做保护处理,对用户上传分享的文档内容本身不做任何修改或编辑,并不能对任何下载内容负责。
6. 下载文件中如有侵权或不适当内容,请与我们联系,我们立即纠正。
7. 本站不保证下载资源的准确性、安全性和完整性, 同时也不承担用户因使用这些下载资源对自己和他人造成任何形式的伤害或损失。