芳构化催化剂应用
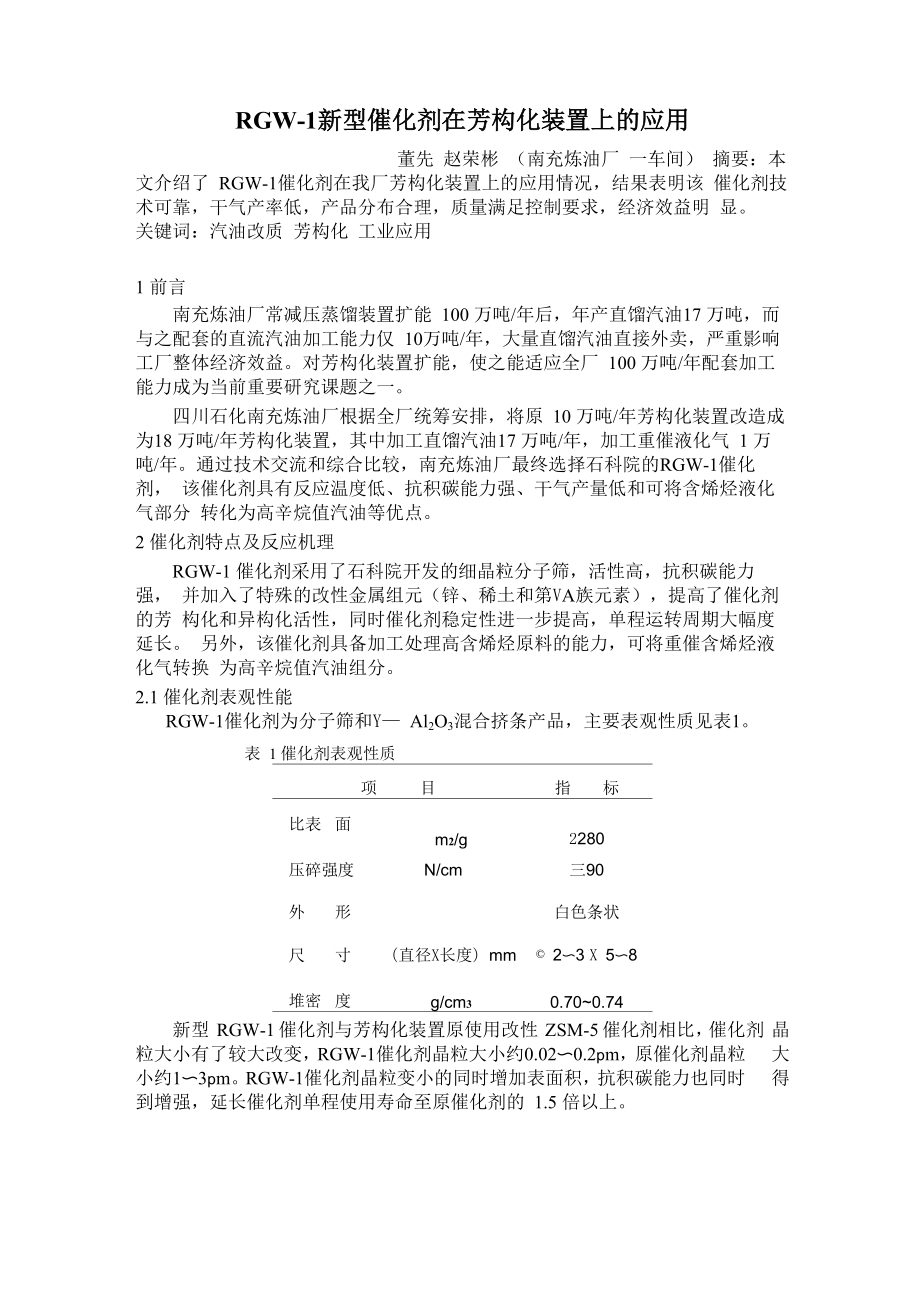


《芳构化催化剂应用》由会员分享,可在线阅读,更多相关《芳构化催化剂应用(9页珍藏版)》请在装配图网上搜索。
1、RGW-1新型催化剂在芳构化装置上的应用董先 赵荣彬 (南充炼油厂 一车间) 摘要:本文介绍了 RGW-1催化剂在我厂芳构化装置上的应用情况,结果表明该 催化剂技术可靠,干气产率低,产品分布合理,质量满足控制要求,经济效益明 显。关键词:汽油改质 芳构化 工业应用1 前言南充炼油厂常减压蒸馏装置扩能 100 万吨/年后,年产直馏汽油17 万吨,而 与之配套的直流汽油加工能力仅 10万吨/年,大量直馏汽油直接外卖,严重影响 工厂整体经济效益。对芳构化装置扩能,使之能适应全厂 100 万吨/年配套加工 能力成为当前重要研究课题之一。四川石化南充炼油厂根据全厂统筹安排,将原 10 万吨/年芳构化装置
2、改造成 为18 万吨/年芳构化装置,其中加工直馏汽油17 万吨/年,加工重催液化气 1 万 吨/年。通过技术交流和综合比较,南充炼油厂最终选择石科院的RGW-1催化剂, 该催化剂具有反应温度低、抗积碳能力强、干气产量低和可将含烯烃液化气部分 转化为高辛烷值汽油等优点。2 催化剂特点及反应机理RGW-1 催化剂采用了石科院开发的细晶粒分子筛,活性高,抗积碳能力强, 并加入了特殊的改性金属组元(锌、稀土和第VA族元素),提高了催化剂的芳 构化和异构化活性,同时催化剂稳定性进一步提高,单程运转周期大幅度延长。 另外,该催化剂具备加工处理高含烯烃原料的能力,可将重催含烯烃液化气转换 为高辛烷值汽油组分
3、。2.1 催化剂表观性能RGW-1催化剂为分子筛和Y Al2O3混合挤条产品,主要表观性质见表1。表 1 催化剂表观性质项目指标比表面m2/g2280压碎强度N/cm三90外形白色条状尺寸(直径X长度)mm 23 X 58堆密度g/cm30.700.74新型 RGW-1 催化剂与芳构化装置原使用改性 ZSM-5 催化剂相比,催化剂 晶粒大小有了较大改变,RGW-1催化剂晶粒大小约0.020.2pm,原催化剂晶粒 大小约13pm。RGW-1催化剂晶粒变小的同时增加表面积,抗积碳能力也同时 得到增强,延长催化剂单程使用寿命至原催化剂的 1.5 倍以上。RGW-1催化剂,晶粒大小约0.020.2gm
4、原催化剂,晶粒大小约13pm图1 RGW-1与ZSM-5催化剂微观结构对比图2.2反应特性RGW-1催化剂为酸性催化剂,具有强L酸和强B酸中心,反应过程可按照 正碳离子学说解释。主要存在反应过程:2.2.1直馏汽油中的烷烃发生芳构化反应生成芳烃。正构烷烃转换为芳烃过程较为复杂,主要过程包括形成正碳离子、裂解形成 烯烃、形成二聚物、环化和脱氢等五步。反应步骤如下:(1) 形成正碳离子。正构烷烃形成正碳离子主要途径包括正构烷烃在B 酸中心得到H+,然后失去H2;正构烷烃在L酸中心失去H-;正构烷烃与已 形成的正碳离子结合形成新的正碳离子,反应同(1-3)。另外,正碳离子最易 由烯烃在B酸中心获得H
5、+而形成。(2) 裂解形成烯烃。正碳离子形成后不稳定,分子易重排为仲正碳离子, 反应同(1-2),若正碳离子较大则可能在B位置上断裂形成烯烃和新的正碳离子, 直至不能再断裂的C3/C4正碳离子,这步反应是生成液化气的主要来源。(3) 形成二聚物。烯烃形成后在催化剂作用下聚合生成分子量较大的烯烃。(4) 环化。较大分子的烯烃自动环化生成环烷烃。(5) 脱氢。环烷烃在RGW-1催化剂作用下失去3H2,形成芳烃。该步反应 同(2-1)石脑油环烷烃脱氢生成芳烃,是强吸热过程,且会产生大量氢气。通过对以上反应过程分析可以发现:(1) 引入重催液化气(烯烃摩尔含量65% )后,将有利于形成正碳离子, 引发
6、反应,有利于后续反应的完成而生成高辛烷值汽油;(2) 从干气中氢气产量的多少和反应器温降可以很容易的判断脱氢生成芳 烃这一反应过程进行的深度。若干气组成中氢气所占比例上升且干气流量也增 加,这说明脱氢生成的芳烃较多,稳定汽油辛烷值较高;反之,干气产量低,干 气组成中氢气所占比例低则说明脱氢生成的芳烃较少,稳定汽油辛烷值较低;(3) 芳构化反应前后分子数目有较大变化,较低的压力有利于芳构化反应 的进行,且反应过程包含强吸热的脱氢过程,较高的温度有利于生成芳烃。故在反应末期稳定汽油辛烷值将较反应初期有一定的提高。一般认为,以上芳构化反应在高温阶段较易发生,即在当反应温度360C以 上时芳构化反应明
7、显增加。该反应阶段得到的反应产物具有较高的辛烷值。 2.2.2直馏汽油中的烷烃发生异构化反应生成异构烃直馏汽油进入反应器后,不仅发生芳构化反应,还发生异构化反应生成高辛 烷值的异构烷烃。正构烷烃吸附于催化剂的酸性中心上,强L酸中心夺取负氢离子而形成正 碳离子,正碳离子的B位的C-C链易断裂,并使断裂的基团接在正碳离子位置 上。以正戊烷异构化为例,反应过程如下:1正构烷烃与L酸结合,形成正碳离子。L酸(1-1)2正碳离子异构。L战CHrC_H-CH2-CH9-Cfl-. “c+h2CHa(1-2)3异构正碳离子夺取正构烷烃H,生成异构烷烃和新正碳离子。CEd-C4-CH2-CH:? -I CHC
8、HCHCE.CH-;(1-3)CLir-c:L-c:i:.-2:irj | CTi7 ncr: r:ri-.?H3:H 一通过以上异构化反应过程可以发现:(1) 异构化反应主要发生在较低温度阶段,属于若吸热反应,且温度越低 越有利于异构化反应平衡向生成高辛烷值汽油组分移动。由于C5/C6直链烷烃 异构化生成的高辛烷值异构化产物沸点较直链烷烃低,故反应初期反应温度较低 的情况下,稳定汽油中含有较多的异构化组分,这个从图2稳定汽油10%馏出点 变化可以很明显的看出。当从反应初期的10%馏出点45 C上升到反应末期的10% 馏出点60C,以基本接近常减压装置直馏汽油10%馏出点,故在反应末期异构 化
9、反应基本上不发生。(2) 第1步正构烷烃与L酸结合,形成正碳离子反应速度较慢,是反应 过程的控制步骤。但正碳离子除可以从正构烷烃通过脱氢得到外,其实更容易的 方式是烯烃在B酸中心获得H+而形成,这是非常容易的,所以在反应初期引入 含烯烃液化气进入反应后,将明显提高稳定汽油辛烷值12个单位,弥补由于芳 构化反应不足造成的辛烷值低问题。(3) 异构化反应前后没有分子数目的改变,故压力变化对异构化反应影响 不大。C,度温出馄点彳70o o6 5o o4 3o o2 11/AZ00/AZ517AZ2Z.AZ00,60517602L7A4图2稳定汽油10%馏出点温度变化图2.2.3低碳烯烃(C2= C5
10、=)发生芳构化反应生成芳烃; 低碳烯烃经过形成正碳离子、齐聚、环化、脱氢等步骤后最终反应成芳烃, 另外有部分形成异构烷烃。2.2.4直馏汽油中的环烷烃通过脱氢生成芳烃。-3IL +205,8 kj/mol此反应发生在催化剂一般金属活性中心,为强吸热反应过程。六元环脱氢是 体积增大的吸热反应,降低压力或提高温度对平衡移动有利,且六元环上有烷基 存在,其脱氢活性更要增加。以甲基环己烷脱氢反应为例,研究法辛烷值提高约 45个单位,发热量为205.8kj/mol。(2-1)2.2.5积碳反应原料中(直馏汽油、重催液化气)深度脱氢,生成双烯或多稀等积碳物 前生,这些物质在金属中心或L酸中心进一步聚合生成
11、积碳。一般认为五元 环深度脱氢生成的环戊二烯最易聚合生成积碳。催化剂形成积碳会覆盖催化 剂活性中心,影响催化剂活性,这是催化剂活性降低的主要原因。2.2.6干气的来源芳构化干气的主要成分为氢气、甲烷、乙烷和少量C3及以上组分。通 过对反应过程分析可知,氢气主要由环烷烃脱氢产生。而甲烷、乙烷在主反 应中不产生,其主要来源认为是由烃类热裂解产生,则当反应生成大量的甲 烷、乙烷时可认为反应温度过高,可考虑对反应器进行再生,否则将造成总 液收的降低,影响经济效益。3工艺流程及主要参数为了实现装置生产的连续进行,反应系统采用四台反应器两两串联后并 联使用,待催化剂活性降低后切除一列反应器再生,再生完毕投
12、入生产,然 后再生另一列反应器。反应器再生时仅保留一列反应器降量生产。反应产物 经过换热进入稳定系统,稳定系统采用经典的三塔流程,干气在吸收塔内被 粗汽油、稳定汽油吸收后出装置,富吸收油进入解吸塔解吸出C2以下轻组分进入吸收塔再吸收,解吸塔底脱乙烷油进入稳定塔分馏为液化气和稳定汽 油出装置。主要参数见表24。表 2 原料性质项目参数直馏汽油性质:流程,C初馏点3510%6550%11690%156终馏点k、Kjzq 八、167密度, kg/m3716液化气性质:C3=/C30, mol%42/9C4=/C4o, mol%26/20表3芳构化装置操作条件项目参数温度,C反应温度28o46o分液罐
13、温度4o吸收塔顶温度2o解吸塔顶温度2o解吸塔底温度74稳定塔顶温度6o稳定塔底温度172压力, Mpa反应器压力o.44分液罐压力o.15吸收塔顶压力1.o稳定塔压力1.15空速, h-1反应质量空速0.5表4芳构化装置物料平衡表加工量项目质量分数Kg/hX 104t/a原料液化气5.612501.0石脑油94.42112517.0合计100.02250018.00产品干气1.22700.216液化气28.664375.148汽油70.21579512.636合计100.02250018.0004 装置运行情况芳构化装置自 2010年 1月 21 日开工以来首先以直馏汽油为原料,加工量控 制
14、在22t/h,反应初始温度为300C。加工直馏汽油提温过程分为两阶段,第一阶 段反应温度300350C之间,反应提温速率为5C/d,稳定汽油研究法辛烷值 8184;第二阶段为反应温度350380C之间,反应提温速率为23C/d,稳 定汽油研究法辛烷值8284。 2月10日引入重催液化气作为原料加工,液化气 加工量1t/h,引入液化气后由于反应床程升温,故适当降低反应温度7C。引入 重催液化气后反应提温速率为2C/d,稳定汽油研究法辛烷值8385。采用RGW-1催化剂后,干气产量明显降低,总液收由装置改造前的94.5% 提高到98%以上,稳定汽油收率76%(以直馏汽油计算),干气产量很少。且引
15、入重催液化气后反应提温速率没有明显增加仍然可以达到辛烷值控制要求。目前 装置能耗约39kg标油/t原料。从装置扩能改造投产到目前已安全平稳运行近30 天,产品分布理想,质量全部合格,未发生安全环保类事故。5 目前存在的问题探讨5.1 催化剂再生RGW-1 催化剂出色的抗积碳能力和较高的活性保证了单程长时间反应周 期,同时也给再生带来了挑战。由于RGW-1催化剂晶粒大小约0.020.2 m,若 再生氮气中氧含量过高,氧气与催化剂积碳燃烧剧烈放出巨大热量,当热量不被 循环烟气迅速带走则可能导致催化剂表面温度过高,引起催化剂微观结构破坏, 使其活性降低。目前芳构化装置新氮压机正在购置当中,现有氮压机
16、循环量不足,故障率 高,再加上系统氮气压力较低导致的再生系统压力不高,使问题进一步凸显。新 催化剂的第一次再生将面临巨大的挑战。所以, 1)新催化剂再生需要提前做好 准备,提前切除再生,为再生提供足够的时间保证; 2)再生过程以不超温为前 提,宁可延长再生时间也要保证再生按要求进行,杜绝反应器床程超温。 3)再 生时启用两台氮压机,保证烟气循环量。5.2 加工重催液化气通过分析RGW-1催化剂主要反应过程可知,引入含重催液化气有利于促进 烷烃生成正碳离子而引发反应,最终提高烷烃转换率,提高稳定汽油辛烷值。同 时可以将液化气转换为稳定汽油,具有较高的经济效益。 2月10日引入重催液 化气,重催液
17、化气加工量为1t/h,反应提温速率与仅加工直馏汽油提温速率一致, 催化剂没有明显的活性下降表现。表明引入重催液化气有利于芳构化反应的进 行,同时也是具有可行性。借鉴同类装置生产经验,可适当增加重催液化气加工 量至4t/h,以提高经济效益。5.3 装置加工方案调整 目前装置主要存在三种加工方案:(1)满负荷加工直馏汽油;(2)满负荷加工直馏汽油和重催液化气;(3)单列反应器正常生产,另一列再生。 主要异同点对比见表 5。表 5 装置加工方案对比项目满负荷 加工直馏汽油满负荷加工直馏汽油和重催液化气单列反应器 正常生产加工量直馏汽油:21125kg/h直馏汽油: 21125kg/h 重催液化气:
18、1250 kg/h满负荷加工量的 5060%产品分布4.703.67稳定汽油:液化气稳定汽油辛烷值,82848385RON通过表5可以看出,一列反应器再生,另一列反应器正常生产时装置加工量 较低,现预计单列再生时间240 小时。届时装置处于低负荷运行,导致机泵、冷 却器、加热炉等偏离最佳运行负荷区域,效率下降,造成单位加工综合能耗增加。 故,若不能有效缩短再生时间,即缩短方案三生产时间,则可考虑对原料泵等主 要机泵采用变频技术,以便降低能耗。采用RGW-1催化剂后,干气产量明显降低,稳定汽油与液化气收率比也有 一定变化,这些改变为重新调整稳定系统操作创造,降低稳定能耗提供可能。即, 干气产量的
19、降低就减少了稳定汽油作为循环吸收剂量,也就降低解吸塔底和稳定 塔底热负荷。另外液化气收率的降低和解吸、稳定塔 CTST 塔板的采用提高塔板 效率,为节能操作提高保障。5.4 解吸塔使用 2.5Mpa 蒸汽凝结水提供解吸换热器热源 在芳构化扩能技改中将稳定塔底再沸器设计为 2.5Mpa 蒸汽提供热源,被加热介质稳定塔底油温度控制在173C,故2.5Mpa蒸汽凝结水温度必定大于173C。 目前,2.5Mpa蒸汽凝结水温度为183C左右,凝结水量34t/h。而解吸塔底温度 控制在74C,使用1.0Mpa蒸汽加热,蒸汽用量约0.7t/h,热负荷约为460kw。 若将2.5Mpa蒸汽凝结水若继续换热到现
20、1.0Mpa凝结水状态则可放热2300kw, 放热量和热品味都满足解析塔底需要。目前已设置好利用 2.5Mpa 蒸汽凝结水给解吸塔底加热流程,见图 3,流程 结构合理,控制方式可行。在压力匹配方面, 2.5Mpa 蒸汽凝结水经过疏水阀后 温度为183C,压力最高为1.0Mpa (该温度下饱和压力),与解吸塔底再沸器压 力等级完全匹配。通过对2.5Mpa蒸汽凝结水利用流程和控制方式、压力匹配、热量匹配等方 面分析,认为完全可以利用2.5Mpa蒸汽凝结水给解吸塔底再沸器加热。投用后 每年将减少 1.0Mpa 蒸汽用量 4800 吨,加工综合能耗降低 2.4kg 标油/吨,占装 置总能耗的 6%。图
21、 3 2.5Mpa 蒸汽凝结水利用流程6 结论南充炼油厂芳构化装置采用石科院RGW-1催化剂,对装置扩能技改后运行 结果表明,扩能技改后装置加工能力达到18万吨/年,RGW-1催化剂的应用有 效的降低能耗,减少干气产率,产品分布合理,产品质量合格。在参炼重催液化 气后增加稳定汽油收率,经济效益明显。参考文献:1 芳烃工学,赵仁殿,化学工业出版社, 2001 年2 高辛烷值汽油组分生产技术,高步良,中国石化出版社, 2006 年3 芳构化装置扩能改造技术方案探讨,杨强龙、赵荣彬,南充炼化 20101 期4 直馏汽油非临氢改质技术的工业应用,姚日远等,石油炼制与化工, 2004 年 第8期5 正丁烷异构化的研究进展,王智艳,上海化工, 2010年第8期
- 温馨提示:
1: 本站所有资源如无特殊说明,都需要本地电脑安装OFFICE2007和PDF阅读器。图纸软件为CAD,CAXA,PROE,UG,SolidWorks等.压缩文件请下载最新的WinRAR软件解压。
2: 本站的文档不包含任何第三方提供的附件图纸等,如果需要附件,请联系上传者。文件的所有权益归上传用户所有。
3.本站RAR压缩包中若带图纸,网页内容里面会有图纸预览,若没有图纸预览就没有图纸。
4. 未经权益所有人同意不得将文件中的内容挪作商业或盈利用途。
5. 装配图网仅提供信息存储空间,仅对用户上传内容的表现方式做保护处理,对用户上传分享的文档内容本身不做任何修改或编辑,并不能对任何下载内容负责。
6. 下载文件中如有侵权或不适当内容,请与我们联系,我们立即纠正。
7. 本站不保证下载资源的准确性、安全性和完整性, 同时也不承担用户因使用这些下载资源对自己和他人造成任何形式的伤害或损失。