等离子制造技术与增材制造装备
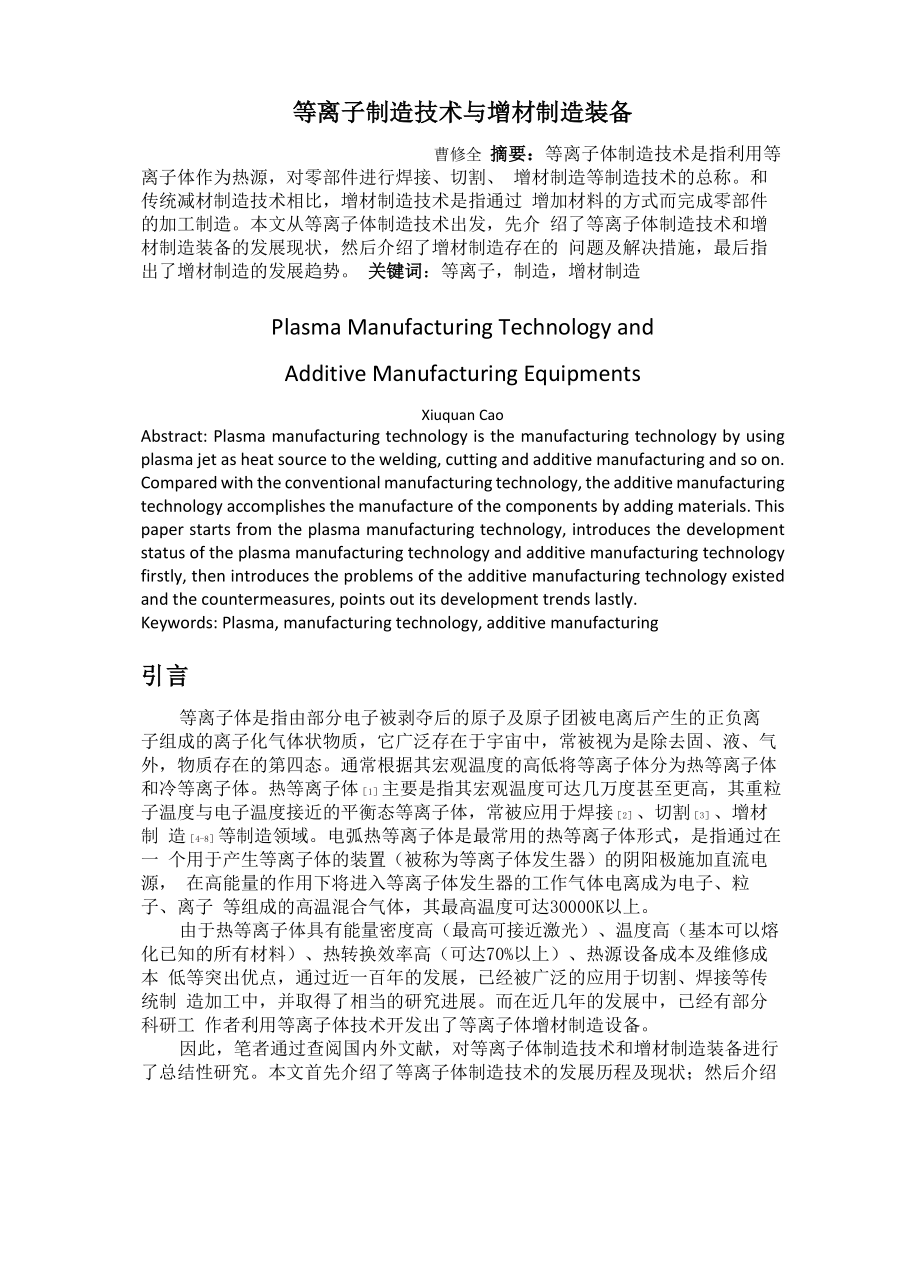


《等离子制造技术与增材制造装备》由会员分享,可在线阅读,更多相关《等离子制造技术与增材制造装备(16页珍藏版)》请在装配图网上搜索。
1、等离子制造技术与增材制造装备曹修全 摘要:等离子体制造技术是指利用等离子体作为热源,对零部件进行焊接、切割、 增材制造等制造技术的总称。和传统减材制造技术相比,增材制造技术是指通过 增加材料的方式而完成零部件的加工制造。本文从等离子体制造技术出发,先介 绍了等离子体制造技术和增材制造装备的发展现状,然后介绍了增材制造存在的 问题及解决措施,最后指出了增材制造的发展趋势。 关键词:等离子,制造,增材制造Plasma Manufacturing Technology andAdditive Manufacturing EquipmentsXiuquan CaoAbstract: Plasma ma
2、nufacturing technology is the manufacturing technology by using plasma jet as heat source to the welding, cutting and additive manufacturing and so on. Compared with the conventional manufacturing technology, the additive manufacturing technology accomplishes the manufacture of the components by add
3、ing materials. This paper starts from the plasma manufacturing technology, introduces the development status of the plasma manufacturing technology and additive manufacturing technology firstly, then introduces the problems of the additive manufacturing technology existed and the countermeasures, po
4、ints out its development trends lastly.Keywords: Plasma, manufacturing technology, additive manufacturing引言等离子体是指由部分电子被剥夺后的原子及原子团被电离后产生的正负离 子组成的离子化气体状物质,它广泛存在于宇宙中,常被视为是除去固、液、气 外,物质存在的第四态。通常根据其宏观温度的高低将等离子体分为热等离子体 和冷等离子体。热等离子体1主要是指其宏观温度可达几万度甚至更高,其重粒 子温度与电子温度接近的平衡态等离子体,常被应用于焊接2、切割3、增材制 造4-8等制造领域。电弧热等离子
5、体是最常用的热等离子体形式,是指通过在一 个用于产生等离子体的装置(被称为等离子体发生器)的阴阳极施加直流电源, 在高能量的作用下将进入等离子体发生器的工作气体电离成为电子、粒子、离子 等组成的高温混合气体,其最高温度可达30000K以上。由于热等离子体具有能量密度高(最高可接近激光)、温度高(基本可以熔 化已知的所有材料)、热转换效率高(可达70%以上)、热源设备成本及维修成本 低等突出优点,通过近一百年的发展,已经被广泛的应用于切割、焊接等传统制 造加工中,并取得了相当的研究进展。而在近几年的发展中,已经有部分科研工 作者利用等离子体技术开发出了等离子体增材制造设备。因此,笔者通过查阅国内
6、外文献,对等离子体制造技术和增材制造装备进行 了总结性研究。本文首先介绍了等离子体制造技术的发展历程及现状;然后介绍了增材制造装备的发展历程及现状;接着介绍了增材制造技术存在的问题并提出 了相应的解决方案;最后笔者提出了自己的见解,指出了增材制造技术的发展趋 势。等离子体制造技术19世纪30年代英国的M.法拉第以及其后的J.J.汤姆孙、J.S.E.汤森德等人相 继研究气体放电现象,这实际上是等离子体实验研究的起步时期。 1879 年英国 的W.克鲁克斯采用“物质第四态”这个名词来描述气体放电管中的电离气体。 1928年美国的I.朗缪尔首先引入等离子体这个名词,等离子体物理学才正式问世。 从此开
7、启了等离子体技术研究的新纪元,等离子体技术得到了快速发展。随着等离子体技术的不断发展,其被广泛的应用于各个领域,如加工制造 9-11、纳米材料制备12, 13、垃圾处理14-17等众多领域。等离子体制造属于等离子 体技术的诸多早期应用之一,是指利用经机械压缩、自磁压缩、热压缩后形成的 等离子体的高温、高能量密度等特性,对零部件进行加工制造,如焊接、切割、 增材制造等。 1954 年,美国 Union Carbide 公司的 Robert Gage 发现,经过压缩 的电弧能量更加集中,电弧温度和射流速度大幅度提高,这种具有高温长弧柱特 性的拘束态电弧很快被用于切割有色金属,随后进一步的实验研究证
8、实这种压缩 电弧也可用于焊接,从此开启了等离子体制造技术的新纪元。等离子体制造技术 的出现极大的促进了制造业的发展,解决了许多困扰业界的难点。等离子体焊接制造技术等离子体焊接制造18-21是指利用等离子体技术,通过焊接的方法加工制造成 形零部件,如压力容器的焊接成形、发动机缸体的焊接成形等,其原理如图 1 所示。当前主流的等离子体焊接技术主要可以分为穿孔性等离子体焊接、等离子 体-MIG复合焊接和激光-等离子体符合焊接。弾缝等离子豪图 1 等离子体焊接原理图1)穿孔性等离子体焊接。 穿孔型等离子弧焊接22又称为穿透等离子弧焊接、小孔焊接。利用等离子弧 熔透工件,并在等离子流力作用下,形成穿透工
9、件的小孔,熔池围绕小孔分布。 随着等离子弧的不断移动,新的熔融金属在小孔前端不断形成,并沿熔池壁向后 流动,而小孔也随电弧移动,因此这些金属便填充小孔原先的位置,冷凝后便形 成焊缝,焊缝断面呈“倒喇叭”状。该方法可实现单面焊双面成形,常用于厚板 的打底焊。由于穿孔等离子弧焊接的工艺参数可调“窗口”小,因此工艺研究较 少,国内外研究者的主要精力集中在对等离子弧、熔池的热场或流场和小孔成型 过程的数值模拟与分析。国外在数值模拟上起步较早,如加州大学伯克利分校的 Y.F. Hsu 等人23在 1988 年便通过对穿孔等离子弧焊接的传热与流体流动进行了数值计算,并建立 起二维准稳态有限元数值模型;19
10、93年,R. G. Keanini等人【24针对穿孔等离子 弧焊接的热场和流场,首次提出三维准稳态有限元模型;1999年,H.G. Fan等人 【25建立了等离子弧焊接的热传导和流体流动二维瞬态模型。而在国内, 2002 年,哈尔滨工业大学的吴林、董红刚等人【26针对固定穿孔 等离子弧焊接率先建立了等离子弧二维稳态热传导模型,对熔池的电流密度和温 度分布模拟,并通过迭代法,计算出焊缝溶深和熔宽,其结果与实验结论一致。 2006 年,山东大学武传松等人【27在分析了等离子弧对熔池的“挖掘”作用和厚 度方向等离子弧热流分布后,提出三维瞬态小孔等离子弧焊接热场的有限元模型 模拟的熔池形状和演变规律与
11、实验结果接近,在接近稳态时的端面形状和达到稳 态时间也与实测结果一致。2)等离子体-MIG复合焊接等离子-MIG复合焊接【21 是将等离子气体保护钨极电弧焊和气体保护熔化极 电弧焊结合起来的一种复合热源焊接工艺。与传统 MIG 焊接工艺相比,其最大 优势在于:焊接速度提高两倍;热输入少、HAZ窄、焊接变形与飞溅小;等离子 的小孔效应明显,熔深增加。在国外,1972年,荷兰PHILIPS公司研究中心的W.G. Essers和A.C. Liefkens 等人28首次提出了 PlasmaMIG焊接方法,并在20世纪80年代开发出设备, 且在德国工厂中得到应用。1995 年由乌克兰巴顿焊接研究所的工程
12、人员在以色 列组建了 PlasmaLaser Technologies(PLT公司),开发出商品化的 Super一MIGD 等 离子旁轴复合热源焊接系列产品 【29。在 Plasma-MIG 焊接工艺方面,日本的 T. Ogawa等人通过确定合理的工艺参数提高了铜-铁异种接头性能30】; 1992年, 德国 R. Draugelates 等人成功将 PlasmaMIG 焊用于铝合金水下焊接【31;还有诸 如巴西等国的诸多科研工作者也在此方面做了较多的研究32, 33。而在国内,哈尔滨工业大学的吴林等人建立了双电源同轴复合焊接系统,实 现了对铝合金的焊接【34。沈阳工业大学的李德元等人通过设计等
13、离子-MIG同轴 复合的枪体和 PLC 主控单元,成功地将等离子电源和 MIG 电源结合,并对枪体 流场和温度场模拟、熔池形状和温度场形态模拟、起弧过程、熔滴过渡、组织成 分进行了深入研究 【35。哈尔滨焊接研究所的周大中、孙军等人提出了单电源 PlasmaMIG 焊接方法,研究了一种使用一个陡降特性的焊接电源同时为两个电 弧供电的单电源PlasmaMIG焊方法,并研究了该方法的电流分配与调节特性、 电压与电位关系、熔滴过渡与电弧形态等电弧特性,其实验结果表明,这种法简 单易行,有利于实际生产应用【36。3)激光-等离子体复合焊接 激光-等离子体复合焊接是指利用同样具有高能量密度的激光和等离子
14、体复合,组成一个优势互补的焊接系统,达到特殊应用场合的焊接需要。在国外,英国Conventry大学从1992年至今一直使用400W的CO2激光器与 50A的等离子体复合,焊接0.60.8mm厚的不锈钢、钛和铝合金等材料,结果 表明,与单独激光焊相比,复合焊接速度提高了 11.5倍,且能够熔透高反射 的铝合金材料【37】;乌克兰KrivtsunIgor模拟了激光-等离子复合焊接熔滴过渡过程、 焊接熔池动力学、熔池温度分布、熔池形貌和穿孔过程,其结果与实际相符【38。在国内,北京航空制造工程研究院的陈俐研究了 YAG激光-等离子复合焊接 时的热源光谱特征39。清华大学的都东、李志宁等人对激光-等离
15、子复合焊接的 传热和流动特性进行了研究40。等离子体切割制造技术等离子切割制造技术 3, 18, 41-43是利用高温等离子电弧的热量使工件切口处 的金属局部熔化(和蒸发),并借高速等离子的动量排除熔融金属以形成切口, 从而制造出所需工件的一种制造方法,其原理如图 2 所示。通常,等离子体切割 制造技术可以分为:注水空气等离子切割制造技术,反极性空气等离子切割制造 技术,水下等离子切割制造技术等三类。G6图 2 等离子体切割原理:1-电极;2- 工作气体;3- 辅助气体;4-保护罩;5- 冷却型喷嘴;6-工件;7-等离子体弧;8-对中环。1)注水空气等离子切割制造技术。注水等离子切割具有以下优
16、点:1)新型注水等离子割炬使得部分蒸发的水 蒸汽形成等离子体,增加了等离子弧的最高温度,进而增加了等离子体的穿透能 力;2)减少切割金属边缘氮化层,可避免焊接时气孔、裂纹等缺陷的产生;3) 增加切割边缘的垂直度,减小切口表面粗糙度,提高焊接接头的强度;4)与氧 乙炔切割相比,切割端面热影响区减小 2/3,显微硬度降低1/2;5)切割构件的 边缘变形量减小可直接用于焊接。目前仅有乌克兰巴顿所开发了系列 PLAZER Cut 等离子切割装备。2)反极性空气等离子切割制造技术。反极性空气等离子切割与普通等离子切割相比,具有以下突出优势:1)小 孔吸收热量的能力增加1. 5倍,焊接效率提高20%40%
17、; 2)切割厚度增加2 3倍,极限厚度可达200mm; 3)切口宽度降低10%15%。目前,乌克兰巴顿 所对此作了研究,提高了电极使用寿命。3)水下等离子切割制造技术。水下等离子切割具有如下优点:1)可以有效降低等离子弧切割时的弧光、 噪声和烟尘的污染; 2)降低工件切割温度,从而减小变形。从切割枪中不仅喷 出等离子气,而且在等离子弧周围喷出高速水流,有助于等离子弧的进一步压缩。 乌克兰巴顿所开发的水下等离子切割设备,可在海水下 27mm 处切割 25mm 厚 的钢或有色金属,若将工件置于空气中切割,切割厚度可达80mm。德国梅塞尔、 美国LTEC、武汉金嘉数控等公司也开发出了相应产品。等离子
18、体增材制造技术 等离子体增材制造技术5-7是指利用等离子体的高温、高能量密度特性,将 金属或非金属材料熔化,通过一层一层的叠加材料而形成零件的制造技术。与传 统的减材制造技术相比,它具有以下突出优点:容易实现三维数字化制造,尤其 适合难加工材料、复杂结构零件的研制生产;原材料利用率高,符合绿色制造理 念;增材制造后的性能及质量优越,有时可以实现结构减重;无需借助刀具和模 具就可以直接制造出产品,响应速度快。由于等离子体增材制造技术发展较晚, 国内外几乎同时开始研究,因此差距不大。同时,由于等离子体增材制造技术还 处于发展初期,仅有如向永华、徐滨士等少数科研工作者对此作了研究。增材制造装备增材制
19、造(Additive Manufacturing, AM)技术(俗称3D打印),是近年来 迅速发展起来的高端数字化制造技术44-50。它是采用材料逐渐累加的方法制造实 体零件的技术,相对于传统的材料去除切削加工技术,是一种“自下而上”的 制造方法,其工作示意图如图3所示。图 3 增材制造示意图增材制造装备就是增材制造技术发展的载体,是增材制造技术的硬件支撑, 是在利用增材制造技术进行零部件的制造过程中所使用的设备的总称。因此,增 材制造装备的产生必然伴随着新的增材制造技术的发展,而新的增材制造技术又 促进人们探索新的增材制造装备,二者相互依存。下面将结合增材制造技术的发 展(主要文献:44-5
20、0)对增材制造装备的发展进行概略性介绍。增材制造技术是20世纪80年代后期发展起来的一项新兴前沿技术,被认为 是制造技术领域的一次重大突破。增材制造技术在发展初期主要应用于模具加工 以及用于组装和功能测试的样件加工等。近十年来,由于不断取得突破,增材制 造技术逐渐被应用于实际产品的加工。金属零部件最终产品的增材制造技术发展 尤其迅速,在结构复杂、材料昂贵的产品生产,以及小批量定制生产方面,成本、 效率和质量优势突出。因此,增材制造技术在国防领域得到了各国政府的高度重 视,并通过政府资助、企业 RD 资金等方式投入了大量的研发经费。2006年,美国国防部下一代制造技术计划(NGMTI)重点投资增
21、材制造技术, 波音、洛马、通用动力、雷神等军工企业参与研究,大力推动钛合金等高价值材 料零部件增材制造技术的发展和应用。2010 年,欧盟第六个框架计划开展了” 大型航空航天组件快速生产”(Aapolac)项目,旨在提高金属沉积成形工艺的可行 性,重点关注钛以及镍和钢的沉积技术。 2012 年,美国国防高级研究计划局 (DARPA)的资助成立了“创新金属加工.直接数字化沉积(CIMP. 3D)”研究中心, 旨在研发先进的增材制造技术,支持 DARPA 开放制造计划,并作为制造演示工 厂,推进和部署增材制造技术在美国国防领域关键金属系统研制生产中的应用。英国政府自 2011 年开始持续增大对增材
22、制造技术的研发经费。英国工程与 物理科学研究委员会中设有增材制造研究中心,参与机构包括拉夫堡大学、伯明 翰大学、英国国家物理实验室、波音公司以及德国 EOS 公司等 15 家知名大学、 研究机构及企业。除了英美外,其它一些发达国家也积极采取措施,以推动增材制造技术的发 展。德国建立了直接制造研究中心,主要研究和推动增材制造技术在航空航天领 域中结构轻量化方面的应用;法国增材制造协会致力于增材制造技术标准的研究 在政府资助下,西班牙启动了一项发展增材制造的专项,研究内容包括增材制造 共性技术、材料、技术交流及商业模式等四方面内容;澳大利亚政府于 2012 年 2 月宣布支持一项航空航天领域革命性
23、的项目“微型发动机增材制造技术”,该 项目使用增材制造技术制造航空航天领域微型发动机零部件,有力促进该技术在 航空航天等领域的应用。因此,增材制造技术以其独特的优势得到了全球范围内广泛关注,不仅得到 了英美等发达国家的高度重视,投入巨资进行研究,而且欧洲的EADS、罗尔-罗 伊斯等为代表的大型航空航天军工企业,也采用“产、学、研”的方式进行增材 制造技术的研究应用工作。正是在各国政府的高度重视和科研工作者的不懈努力 下,增材制造技术已经取得了突破性的进展。当然,增材制造装备随着增材制造 技术的发展也取得了长足的发展。现有增材制造技术根据其使用的增材制造装备 所使用的热源的不同,主要有激光增材制
24、造技术,电子束增材制造技术和等离子 体增材制造技术。激光增材制造技术激光增材制造技术是指利用激光作为材料熔化热源,研制增材制造装备,利 用该装备进行零配件的增材制造加工。通常可以分为激光直接熔化沉积( LMD) 增材制造技术和激光选区熔化(SLM)增材制造技术。1)激光直接熔化沉积(LMD)增材制造技术。LMD 技术是采用同步输送的金属原料方法,按照 CAD 分层生成的图形文件 逐层沉积出三维金属零件实体的工艺过程,其工作示意图如图 4 所示。 LMD 的 主要特点是同轴送粉、光斑直径大、激光功率大(数千瓦级)、粉末完全熔化、 成形效率高,成形精度13mm。适用一般用于形状相对复杂的大型金属构
25、件 毛坯的制备,零件在使用前需进行加工,加工余量较大。图 4 激光直接熔化沉积( LMD )增材制造示意图在美国能源部研究计划支持下,Sandia及Los Alomos国家实验室率先发展 出称为 LENS 及 LMD 的技术,研究了不锈钢、镍基合金、钛合金、难熔金属等 材料的组织及性能,并采用该项技术制造标准 -3(SM3 )导弹三维导向和姿态 控制系统中的铼零件,可降低 50% 的制造成本和制造周期,显示出该技术在高 性能金属零件直接成形方面的优势。由于该技术在大型钛合金结构件直接成形方面的突出优势及其在飞机等装 备研究生产中的广阔应用前景,高性能钛合金结构件的激光快速成形研究一直是 该领域
26、的研究重点。美国加利福尼亚先进结构研究院设计了一种 MX3D 机器人 用于大型结构件制造,可实现大坡度结构件的制造。AirBus公司的A300机型和 A350XWB 机型已经开始使用 3D 打印的零件,有些支架类零件可以减重 30%55 %,节省大量地原材料。激光直接熔化沉积(LMD)增材制造技术主要有以下特点:(1)无需模具;(2)适于难加工金属材料制备;(3)精度较高,可实现复 杂零件近净成形;(4)内部组织细小均匀,力学性能优异;(5)可制备梯度材料; (6)可实现损伤零件的快速修复;(7)加工柔性高,能够实现多品种、变批量 零件制造的快速转换。2)激光选区熔化(SLM )增材制造技术。
27、激光选区熔化制造技术是将零部件CAD模型分层切片,采用预铺粉的方式, 扫描振镜带动激光束在计算机控制下沿图形轨迹扫描选定区域的合金粉末层,使 其熔化并沉积出与切片厚度一致、形状为零件某个横截面的金属薄层,直到制造 出与构件 CAD 模型一致的金属零件,工作过程示意图如图 5 所示。图 5 激光选区熔化( SLM )增材制造示意图2003 年底德国推出了世界上第一台 SLM 设备。近年来,德国 EOS 、 Concept Laser、SLM Solutions、英国Renishaw等技术公司在激光选区熔化增材 制造技术与设备方面取得了长足的进步SLM设备采用的激光器几乎都采用高光 束质量维护性好
28、、光电转化效率高的光纤激光器。 为了进一步提高激光选区熔 化增材制造技术的沉积效率, 2012 年 11 月,德国 SLM-Solutions 公司采用两台 激光器/ 两台扫描振镜组成激光选区熔化增材制造成形系统,设备成形尺寸范围 为500mmX280mmX325mm,两台激光扫描装置可以单独工作,也可以同时工作, 能满足大型复杂构件的应用需求。在应用方面,美国 GE 公司在各大型企业中率先成立金属材料激光熔化增材 制造研发团队,并于 2012 年收购了 Morris 和 RQM 两家专业从事 SLM 制造技 术的公司。GE公司将在LEAP喷气发动机中采用SLM制造燃油喷嘴。每台发动 机预计1
29、9个燃油喷嘴。GE公司在未来三年内预计每年生产25000个燃油喷嘴, 共计约 10 万个燃油喷嘴。美国 NASA 马歇尔航天飞行中心的科学家和工程师们于 2012 年采用激光选区熔化成形技术制造了复杂结构金属零部件样件,用于“太空发射系统”重型 运载火箭。NASA认为这项技术可以极大地降低制造零件所需的时间,在一些情 况下甚至将制造时间从数月降低至数周,提高了经济可承受性。由于不再需要把 零部件焊接到一起,其结构强度得到提高,变得更加可靠,使整体火箭更加安全。 NASA 目前暂定在 2017 年第一次“太空发射系统”飞行试验中使用由激光选区 熔化技术制造的零部件。 2013 年 8 月, NA
30、SA 对 SLM 制造的 J-2X 发动机喷注 器样件进行了热试车,结果表明 SLM 制造的零件可完全满足发动机零件的设计 使用要求。 美国加利福尼亚大学圣迭戈分校太空发展探索团队用 3D 打印方法 制造火箭发动机推力室组件。相对于传统制造方法, 3D 打印技术为火箭发动 机提供一种全新的制造方法。SLM 制造激光功率一般在数百瓦级,主要由以下特点:(1)精度高(最高可 达 0.05mm )、质量好,加工余量很小或无加工余量,除精密的配合面之外,制 造的产品一般经喷砂或抛光等后续简单处理就可直接使用 ,;(2)适合中、小型 复杂结构件(尤其是复杂薄壁型腔结构件)的高精度整体快速制造。电子束增材
31、制造技术 电子束增材制造技术是指利用电子束的高温高能量密度而开发出的增材制 造设备,将材料熔化而通过增加材料的方法制造成形零部件的制造技术。通常可 以分为电子束熔丝(EBFF )增材制造技术和选区电子束熔化(EBM)增材制造 技术。1)电子束熔丝(EBFF )增材制造技术。 电子束熔丝增材制造技术又称为电子束自由成形制造技术( Electron Beam电孑車沉施金匾Freeform Fabrication, EBFF),是在真空环境中,高能量密度的电子束轰击金属表 面形成熔池,金属丝材通过送丝装置送入熔池并熔化,同时熔池按照预先规划的 路径运动,金属材料逐层凝固堆积,形成致密的冶金结合,直至
32、制造出金属零件 或毛坯,其原理见图 6。熔积賂护方向图6电子束熔丝增材制造技术原理图 由于欧美等发达国家科研实力相对较好,美国 Sciaky 公司已经成功开发了 电子束熔丝增材制造设备。电子束熔丝增材制造的功率可达几十千瓦级,制造精 度约24mm,对提高复杂结构大型工件的生产效率具有重要意义。电子束熔丝增材制造具有以下优点:(1)沉积效率高。电子束可以很容易实现数十 kW 大功率输出,可以在较 高功率下达到很高的沉积速率(15kg/h),对于大型金属结构的成形,电子束熔 丝增材制造速度优势十分明显。(2)真空环境有利于零件的保护。电子束熔丝增材制造在10-3Pa真空坏境 中进行,能有效避免空气
33、中有害杂质(氧、氮、氢等)在高温状态下下混入金属 零件,非常适合钛、铝等活性金属的加工。(3)内部质量好。电子束是“体”热源,熔池相对较深,能够消除层间未 熔合现象;同时,利用电子束扫描对熔池进行旋转搅拌,可以明显减少气孔等缺 陷。电子束熔丝沉积成形的钛合金零件,其超声波探伤内部质量可以达到 AA 级。(4)可实现多功能加工。2)选区电子束熔化(EBM )增材制造技术。选区电子束熔化(EBM)增材制造技术是指电子束在偏转线圈驱动下按预先 规划的路径扫描,熔化预先铺放的金属粉末;完成一个层面的扫描后,工作舱下 降一层高度,铺粉器重新铺放一层粉末,如此反复进行,层层堆积,直到制造出 需要的金属零件
34、,整个加工过程均处于 10-2Pa 以上的真空环境中,能有效避免 空气中有害杂质的影响,其原理图如图 7 所示。图7选区电子束熔化(EBM)增材制造原理图选区电子束熔化(EBM)增材制造技术源于20世纪90年代初期的瑞典, 瑞典 Chalmers 工业大学与 Arcam 公司合作开发了选区电子束熔化( Electron Beam Melting,EBM)增材制造技术,并以CAD-to-Metal申请了专利。2003年, Arcam公司独立开发了 EBM设备,目前以制造EBM设备为主,产品已成系列, 兼顾成形技术开发。美国、日本、英国、德国、意大利等许多研究机构、工厂、 大学从该公司购置了 EB
35、M 设备,在航空、航天、医疗、汽车、艺术造型等不同 领域开展研究,其中,生物医学植入物方面的研究较为成熟。近年来,在航空航 天领域的应用也迅速兴起,美国波音公司、Synergeering group公司、CalRAM公 司、意大利 Avio 公司等针对火箭发动机喷管、承力支座、起落架零件、发动机 叶片等开展了大量研究,有的已批量应用,材料主要铜合金、 Ti6Al4V、 TiAl 合 金等。由于材料对电子束能量的吸收率高且稳定,因此,电子束选区熔化技术可 以加工一些特殊合金材料。选区电子束熔化增材制造精度在 0.3mm 左右,电子 束最大扫描速度可达7km/s,还可以实现多电子束同时扫描成形制造
36、。选区电子束熔化增材制造技术主要有以下特点:( 1)真空工作环境,能避免空气中杂质混入材料。(2)电子束扫描控制依靠电磁场,无机械运动,可靠性高,控制灵活,反 应速度快。(3)成形速度快,可达60cm3/h,是激光选区熔化的数倍。(4)可利用电子束扫描、束流参数实时调节控制零件表面温度,减少缺陷与变形。(5) 良好的控温性能使其能够加工 TiAl 等金属间化合物材料。(6)尺寸精度可达土0.1mm,表面粗糙度约在R a1550之间,基本近净成 形。( 7)真空环境下成形,无需消耗保护气体,仅消耗电能及不多的阴极材料, 且未熔化的金属粉末可循环使用,因此可降低生产成本。( 8)可加工钛合金、铜合
37、金、钴基合金、镍基合金、钢等材料。 等离子体增材制造技术 等离子体增材制造技术是指利用等离子体作为加热热源而开发的增材制造 装备而通过增加材料的方法而成形零部件的制造方法。由于等离子体增材制造技 术相比于激光增材制造技术和电子束增材制造技术发展较晚,国内外研究工作相 对较少,但由于等离子体热源的突出优势,已经得到了广大科研工作者的关注, 并已经取得了一定的科研成果。等离子体增材制造技术通常可分为等离子体熔积 成形增材制造技术和等离子体选区熔化增材制造技术。1)等离子体熔积成形增材制造技术。等离子熔积成形增材制造技术是基于快速成形层积原理,采用焊接方法中高 度压缩、集束性好的等离子束熔化同步供给
38、的金属粉末,在基板上逐层堆积形成 金属原型或零件的技术,其实质是计算机控制下的三维等离子粉末堆焊成形,其 原理示意图如图 8 所示。图8等离子体熔积成形增材制造原理图华中科技大学张海鸥等人5, 7早在 2002 年就开始了对等离子体熔积成形增 材制造技术的研究。该课题组自主研发了等离子体熔积成形增材制造设备,并基 于该设备进行了等离子体熔积成形增材制造工艺研究,确定了转弧电流、熔积速 度和送粉量之间的相互关系。大连理工大学徐文骥等人也在同年研究了等离子体 熔积成形增材制造在模具中的应用。等离子体熔积成形增材制造技术主要有以下特点:( 1)设备成本低,运行维 护简单;( 2)对工作环境要求较低,
39、可适应于一般的工厂环境;( 3)易于实现自 动化。2)等离子体选区熔化增材制造技术。等离子体选区熔化增材制造技术加工原理与激光选区熔化增材制造技术和 电子束选区熔化增材制造技术加工原理基本相似:首先由三维实体造型软件(CAD) 设计出零件的三维数字化模型;然后将零件的 CAD 三维模型沿 z 向离散成系列 二维层面,即对数字模型进行切片分层icing),获得分层文件,得到各层截面 的切片二维轮廓,并对二维轮廓进行填充,进行路径规划;接着将分层数据传输 给成形机,利用等离子弧熔化合金粉末,焊枪和送粉系统根据单层的成形数据和 材料需要,在计算机系统控制、步进电机驱动X、y、z轴三维运动下,对成形路
40、 径精确定位,按当前层层面几何形状进行扫描熔覆。每完成一层熔覆后,焊枪上 升一个位距,如此逐层熔覆最终实现金属零件的直接精密成形。装甲兵工程学院装备再制造技术重点实验室向永华、徐滨士等人 6在 2010 年提出了基于微束等离子熔覆工艺的直接金属成形方法,设计并开发基于等离子 熔覆的金属零件直接制造软、硬件系统,并采用该系统进行中空零件成形实验。 实验结果表明,并采用微束等离子熔覆直接制造系统可以得到成形良好、组织细 密的金属零件。南京航空航天大学张禹等人在 2013 年基于机器人堆焊增材制造 进行研究,探索解决弧坑塌陷的工艺措施,并提出一整套制备表面光洁零件的堆 焊成形工艺,最终制得了低碳钢与
41、铝合金堆焊成形制品。结果表明:通过降低热 输入量,在机器人指令中加入填弧坑动作以及使焊接路径适当重叠可以很好的解 决弧坑塌陷问题;堆焊成形的零件可以用电解加工的方法作为后处理工艺,得到 表面光洁的零件。等离子体选区熔化增材制造技术具有和等离子体熔积成形增材制造技术相 同的优点,在此不再赘述。综上所述,增材制造技术是有别于传统减材制造技术的一种新型制造技术, 它的出现解决了许多传统制造技术难点,尤其是在复杂零件的加工制造方面。而 增材制造装备是增材制造技术发展的载体,是支撑其发展的硬件措施。增材制造存在的问题及解决措施增材制造技术虽然得到了全球的高度重视,并取得了一定的科研唱过,但仍 然是处于成
42、长过程的技术,还不够成熟,目前主要用于个性化的单件生产。增材 制造技术仍然存在以下问题:1)增材制造技术与塑料注射机等成熟的大批量成形技术相比,生产成本过 高。与传统切削加工技术相比,产品的尺寸精度和表面质量相距较大。增材制造 技术目前只能算一丝曙光,真正达到大规模应用产生效益,还需要很长的时间发 展和积累。2)目前的金属增材制造技术都不能直接形成符合要求的零件表面,它都必 须经过表面的机械加工,去除表面多余的、不连续的和不光滑的金属,才能作为 最终使用的零件。3)材料的可选择范围可能是最大的障碍,目前可以用于增材制造技术的材 料不超过 100 种,而在工业中应用的材料可能已经超过 10000
43、 种,且增材制造技 术材料的物理性能尚有待于提高。4)增材制造技术直接成形的金属零件在制作过程中因为反复经受局部接近 熔点温度受热,内部热应力状态复杂,成形体中容易夹杂空穴,未完全熔融的粉 末和胚体缺陷等,应力处理和控制还不能满足要求,严重影响了成形件的强度。5)三维设计技术的普及关系到增材制造技术能否进入家庭。市场正在呼唤 孩子们能够操作和喜爱的软件,打印物品要成为新一代计算机游戏,引起孩子的 兴趣,发挥儿童的创造性,才能有无限光明的未来。为了解决上述问题,现有增材制造技术必须从以下几方面加以改善:1)研究新型增材制造装备。重点开发低成本的增材制造装备,降低增材制 造成本。同时,提高新型增材
44、制造装备的加工精度,使得采用增材制造技术制造 的零部件在不经其它加工工序的情况下能达到使用要求。2)加快增材制造用材料的研究。由于当前适用于增材制造用的材料种类有 限,极大的限制了增材制造技术的发展,因此必须加快增材制造用材料的研究, 寻找新的适合增材制造的材料。3)加工增材制造过程的工艺及仿真研究。重点研究增材制造工艺过程,并 利用计算机仿真技术模拟增材制造过程,分析零部件制造过程中的热、力等影响 零部件成形质量的因素,提高增材制造零部件性能。增材制造发展趋势在各国政府的高度重视和科研工作者的不懈努力下,增材制造技术主要朝着 以下方向发展:1. 向近无缺陷、高精度、新材料成形方向发展。由于现
45、有增材制造技术还 存在着各种缺陷,如制造精度较低、材料种类受限等,这必将促使科研工作者加 大该方面的研究,制造出向近无缺陷、高精度的多材料零部件。2. 向多领域应用发展。增材制造技术当前主要集中于航空领域,应用领域较 小。而增材制造技术优势突出,比较向其他领域延伸。如今,增材制造技术已经 延伸到了生物医药领域,用于打印人造骨骼等。3. 向多种热源复合增材制造方向发展。当前主要的增材制造设备基本都是基 于某一单一热源研制而成,而每一种单一热源都存在其局限性。利用多种热源复 合,可形成优势互补,形成更为完善的增材制造装备,促进增材制造技术的进一 步发展。4. 增材制造装备将会进一步商业化。从国外的
46、发展情况来看,对于每一项增 材制造技术,都有一家或数家成熟的商业装备制造商,形成了系列化的增材制造 装备。同时,国外的装备制造商除了硬件装备制造外,还进行了大量典型材料成 形工艺与材料性能的研究,掌握典型材料成形工艺核心技术,形成较为完备的工 艺参数数据库。面对应用需求的日益扩大,增材制造装备研制将会进一步商业化。参考文献1 Fauchais P, Vardelle A. Thermal Plasma J. IEEE Transactions on Plasma Science. 1997, 25(6): 1223-1258.2 Wu C. Welding Thermal Processes
47、and Weld Pool Behaviors M. China Machine Press, 2007: 22-23.3 陈小平.等离子割炬的设计D.安徽理工大学,2006.4 徐文骥,金洙吉,邓琦林,等基于等离子熔射成形技术的快速模具制造J.制造技术与机 机床. 2002(3): 23-24.5 黄永军,张海鸥,王桂兰,等金属模具的等离子熔积直接成形及精整加工J.航空制造技 术. 2004(8): 93-95.6 向永华,徐滨士,吕耀辉,等微束等离子粉末熔覆金属零件直接快速成形研究J.中国表 面工程. 2009, 22(4): 44-48.7 徐继彭,张海鸥,王桂兰,等金属粉末等离子熔积成
48、形的初步工艺试验研究J.电加工与 模具. 2005(2): 39-42.8 H Z, J X, G. W. Fundamental study on plasma deposition manufacturingJ. surface & Coatings Technology. 2003, 171: 112-118.9 Zhukov M F, Zasypkin I M. Thermal Plasma Torches design: characteristics, application M. Cambridge International Science Publishing, 2007:
49、22-52.10 平毅斌,屈金山 . 等离子纵缝焊机在不锈钢容器制造工艺中的应用 J. 新技术新工艺 . 2002(10): 29-30.11 邓德伟,陈蕊,张洪潮.等离子堆焊技术的现状及发展趋势J.机械工程学报.2013, 49(7): 106-112.12 Lin H, Liao S, Hung S. The dc thermal plasma synthesis of ZnO nanoparticles for visible-light photocatalystJ. Journal of Photochemistry and Photobiology A-Chemistry. 200
50、5, 174(1): 82-86.13 Sun W, Hu R, Liu H, et al. Embedding nano-silicon in graphene nanosheets by plasma assisted milling for high capacity anode materials in lithium ion batteriesJ. Journal of Power Sources. 2014, 268: 610-619.14 高飞.二路进气热等离子喷枪用于垃圾焚烧飞灰处置的研究D.浙江大学,2010.15 X T, Q W, L Y. Diagnositic of
51、novel atmospheric plasma source and its application to vitrication of waste incinerator fly ashJ. 2008, 22(5): 3057-3064.16 Park Y J, Heo J. Corrosion behavior of glass and glass-ceramics made of municipas solid waste incinerator fly ashJ. waste management. 2004, 24(8): 825-830.17 Liu B, Kikuchi M,
52、Li H P. Dual torch plasna arc furnace for medical waste treament J. plasma science and technology. 2007, 9(6): 709-712.18 韩善果,杨永强,闫德俊.先进等离子焊接与切割技术研究现状J.电焊机.2013, 43(10): 6-9.19 胡志坤.高速电弧焊工艺的研究现状J.电焊机.2008, 38: 32-35.20 Olsson R, Stemver M. High speed welding give a competitive edgeJ. Welding Review I
53、nternational. 1995, 14(8): 128-131.21 Bengtsson P. High productivity MIG/MAG welding processes J. Welding and metal fabrication. 1992, 60(6): 226-228.22 董春林,吴林,邵亦陈 . 穿孔等离子弧焊发展历史与现状 J. 中国机械工程. 2000, 11(5): 577-581.23 Hsu Y, Rubinsky B. Two-dimensional heat transfer study on the key hole palsma arc pr
54、ocess J. Heat mass Transfer. 1988, 31(7): 1409-1421.24 Russell G, Keanini, Boris R. Three dimensional simulation of the palsma arc welding processJ. heat And Mass Transfer. 1993, 36(13): 3283-3298.25 Fan H, Kovacevic R. key hole formation and collapse in plasma arc welding J. Appl.Phys. 1999, 32(22)
55、: 2902-2909.26 董红刚,高洪明,吴林 . 固定电弧等离子弧焊接的热传导的数值计算 J. 焊接学报. 2002, 23(4): 24-30.27 武传松,王怀刚,张明贤 . 小孔等离子弧焊接热场瞬时演变过程的数值分析 J. 金属学报. 2006, 4(23): 311-316.28 Esser W G, Liefkens A C. Plasma-MIG welding developped by PhilipsJ. machinery and production engineering. 1972, 1(11): 632-633.29 Asai S, Ogawa T, Ishiz
56、aki Y. aplication of plasma MIG hybrid welding to dissimilar joints between copper and steelJ. Welding in the world. 2012, 56: 37-42.30 Draugelates R, Bouaifl B, Bartzsch J. Investigations on underwater welding by the plasma MIG methodJ. Pro Second Int Offshore Polar Eng Conf. 1992: 199-207.31 Onoko
57、hei, Liu Z, Era T. Development of a plasma MIG welding system for aluminiumJ. Welding International. 2009, 23(11): 805-809.32 Ton H. Physical properties of the plasma-MIG welding arcJ. Journal of Physics. 1975(8): 922-933.33 De O M A, Dutra J C. electrical model for the plasma-MIG hybird welding pro
58、cessesJ. Welding and Cutting. 2007, 6(6): 324-328.34 白岩,高洪明,吴林.基于LabView的熔化极等离子弧焊接电信号分析J.焊接学报.2006, 27(8): 59-62.35 张义顺.等离子一MIG焊接方法及其双弧复合特性的研究D. 2006.36 周大中,孙军.单电源等离子一MIG焊方法J.焊接学报.1990,11(3): 149-154.37 Johnson T A, Ittin J B, Bacon M C. LaserPlasma Technique Welds Sheet MetalJ. Instrial Laser Revie
59、w. 1995(11): 21-24.38 Semak V V, Steele R J, Fuerschbach P W. role of beam absorption in plasma during laser weldingJ. Applied Physics. 2000, 33(10): 1179-1185.39 陈俐,段爱琴.YAG激光等离子弧复合焊接热源光谱特征分析J.电加工与模具.2007(6): 19-21.40 李志宁,都东,常保华. 激光等离子弧复合焊接熔池流动和传热的数值分析 J. 焊接学报. 2007, 28(7): 37-40.41 陈苗荪.中国等离子弧切割机的现状
60、及其分析J.切割论坛.2006(9): 23-25.42 杨素媛,潘文方.国内等离子切割的现状及发展趋势J.第十四次全国焊接学术会议.2010: 24-27.43 Ott Dirk.现代等离子切割技术及其智能化J.电焊机.2013, 43(5): 20-24.44 吴洁.3D打印技术及其应用现状J.黑龙江科技信息.2013(26): 174.45 铭刘,张坤,樊振中.3D打印技术在航空制造领域的应用进展J.装备制造技术.2013(12): 232-235.46 祁萌,李晓红,胡晓睿,等增材制造技术在国外国防领域的发展现状与趋势J.国防制造 技术. 2013(5): 12-16.47 陈济轮,杨洁,于海静. 国外高能束增材制造技术应用现状与最新发展 J. 航天制造技术.2014(4): 1-4.48 陈济轮,董鹏,张昆,等. 金属材料增材制造技术在航天领域的应用前景分析 J. 电加工与 模具. 2014(1): 66-69.49 黄秋实,李良琦,高彬彬.国外金属零部件增材制造技术发展概述J.国防制造技术.2012(5): 26-29.50 邓龙辉,刘小静.浅析3D打印技术及其在中国的发展J.通讯世界.2014(7): 125-126.
- 温馨提示:
1: 本站所有资源如无特殊说明,都需要本地电脑安装OFFICE2007和PDF阅读器。图纸软件为CAD,CAXA,PROE,UG,SolidWorks等.压缩文件请下载最新的WinRAR软件解压。
2: 本站的文档不包含任何第三方提供的附件图纸等,如果需要附件,请联系上传者。文件的所有权益归上传用户所有。
3.本站RAR压缩包中若带图纸,网页内容里面会有图纸预览,若没有图纸预览就没有图纸。
4. 未经权益所有人同意不得将文件中的内容挪作商业或盈利用途。
5. 装配图网仅提供信息存储空间,仅对用户上传内容的表现方式做保护处理,对用户上传分享的文档内容本身不做任何修改或编辑,并不能对任何下载内容负责。
6. 下载文件中如有侵权或不适当内容,请与我们联系,我们立即纠正。
7. 本站不保证下载资源的准确性、安全性和完整性, 同时也不承担用户因使用这些下载资源对自己和他人造成任何形式的伤害或损失。
最新文档
- 幼儿园绘本故事当我睡不着的时候课件
- 人教版小学五年级品德与社会上册《五十六个民族五十六朵花》ppt课件
- 人教版小学一年级音乐下册红眼睛绿眼睛ppt课件
- 人教版小学数学四年级上册《数学广角》ppt课件
- 幼儿园优质课件小猫的生日
- 幼儿园科学活动区创设与材料投放课件
- 人教版小学四年级音乐小螺号ppt课件
- 幼儿园科学教育的方法和途径课件
- 开盘前广告策略案课件
- 人教版小学一年级品德与生活《校园铃声》ppt课件
- 人教版小学五年级音乐吹起羌笛跳锅庄ppt课件
- 人教版小学四年级英语下册unit3_weather第三课ppt课件
- 人教版小学一年级上册数学第二单元上下前后ppt课件
- 人教版小学五年级美术第17课电脑动画ppt课件
- 幼儿园优质课件-幼儿园中班“我们都是好朋友”课件