机械类文献综述
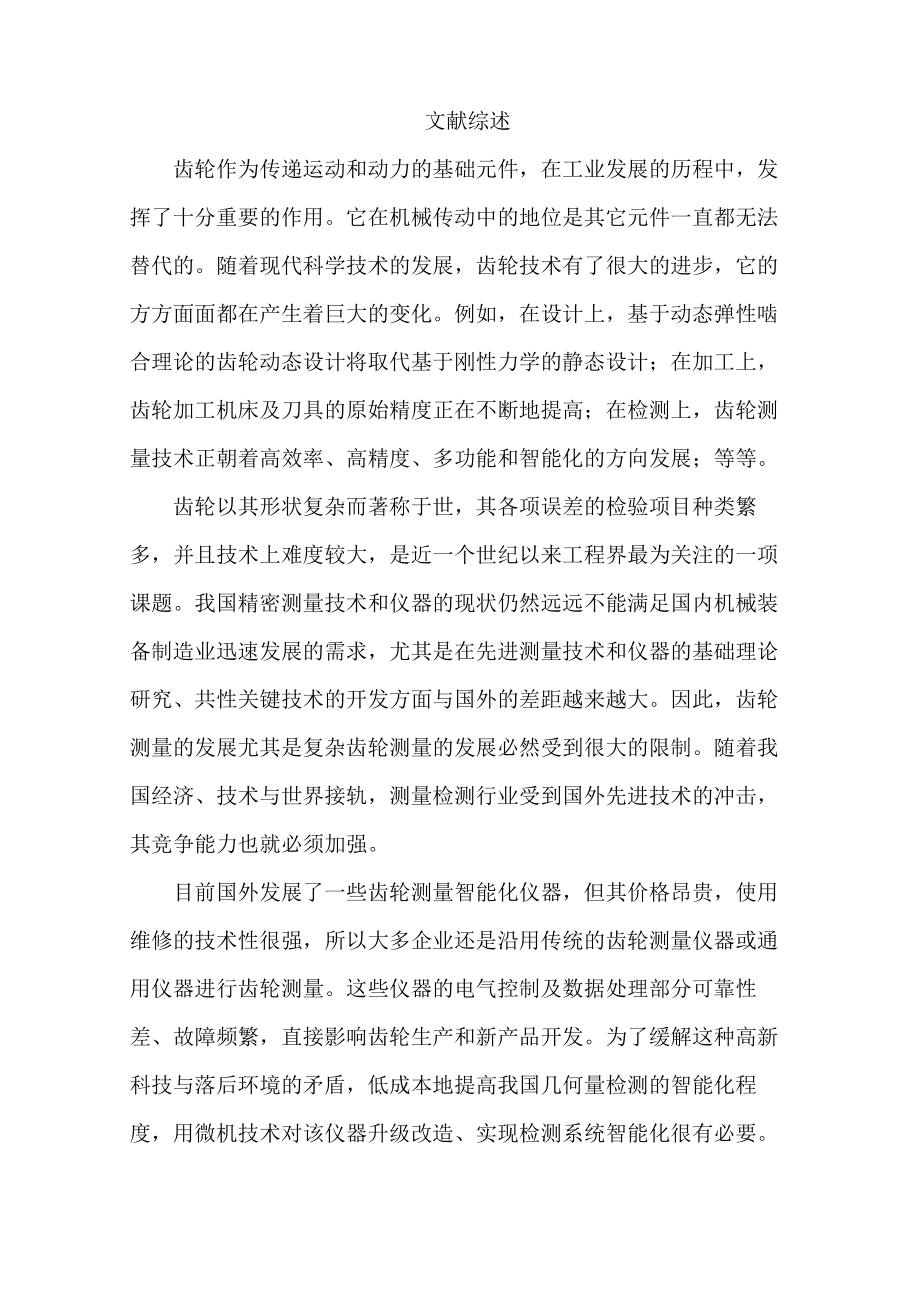


《机械类文献综述》由会员分享,可在线阅读,更多相关《机械类文献综述(27页珍藏版)》请在装配图网上搜索。
1、文献综述齿轮作为传递运动和动力的基础元件,在工业发展的历程中,发 挥了十分重要的作用。它在机械传动中的地位是其它元件一直都无法 替代的。随着现代科学技术的发展,齿轮技术有了很大的进步,它的 方方面面都在产生着巨大的变化。例如,在设计上,基于动态弹性啮 合理论的齿轮动态设计将取代基于刚性力学的静态设计;在加工上, 齿轮加工机床及刀具的原始精度正在不断地提高;在检测上,齿轮测 量技术正朝着高效率、高精度、多功能和智能化的方向发展;等等。齿轮以其形状复杂而著称于世,其各项误差的检验项目种类繁 多,并且技术上难度较大,是近一个世纪以来工程界最为关注的一项 课题。我国精密测量技术和仪器的现状仍然远远不能
2、满足国内机械装 备制造业迅速发展的需求,尤其是在先进测量技术和仪器的基础理论 研究、共性关键技术的开发方面与国外的差距越来越大。因此,齿轮 测量的发展尤其是复杂齿轮测量的发展必然受到很大的限制。随着我 国经济、技术与世界接轨,测量检测行业受到国外先进技术的冲击, 其竞争能力也就必须加强。目前国外发展了一些齿轮测量智能化仪器,但其价格昂贵,使用 维修的技术性很强,所以大多企业还是沿用传统的齿轮测量仪器或通 用仪器进行齿轮测量。这些仪器的电气控制及数据处理部分可靠性 差、故障频繁,直接影响齿轮生产和新产品开发。为了缓解这种高新 科技与落后环境的矛盾,低成本地提高我国几何量检测的智能化程 度,用微机
3、技术对该仪器升级改造、实现检测系统智能化很有必要。研究真正反映齿轮三维几何空间形状和制造误差组成因素的齿 轮整体检测方法在我国具有积极的现实意义,特别是研究用检测简 便、精确、迅速的测量方法改造现有测量机更为突出。20 世纪 80 年代以前,齿轮测量原理主要以比较测量为主,其实 质是相对测量。具体方式有两种:一是将被测齿轮与一个标准齿轮进 行实物比较,从而得到各项误差;二是展成测量法,就是将仪器的运 动机构形成的标准特征线与被测齿轮的实际特征线作比较,确定相应 误差。而精确的展成运动是借助一些精密机构来实现的,不同的特征 线需要不同的展成机构。比较测量的主要缺点是:测量精度依赖于标 准件或展成
4、机构的精度,机械结构复杂,柔性差,同一个齿轮需要多 台仪器测量。对于齿廓误差测量而言,展成式测量技术仅限于渐开线 齿廓误差测量上。对于非渐开线齿轮的端面齿廓测量,采用展成法测 量是十分困难得,因为展成机构太复杂并且缺乏通用性。多年来,国内外诸多学者在大型齿轮测量领域进行了广泛的研 究,丰富了大型齿轮测量方面的理论和方法。在检测仪器方面,各国 均开发了由计算机控制的齿轮量仪,其机构大量应用新技术和新元 件,如计算机数控技术运用于控制、驱动、数据处理等;光栅、同步 感应器、容栅、磁栅、电感测微技术、电容测微技术、激光测量技术 等用于位移测量,不断提高齿轮测量精度。总的发展趋势为:1)测量 软件功能
5、的增强和扩展,由于大齿轮的结构复杂大、重量重等原因, 这就要促使其必须实现自动化的要求,即机电一体化的趋势。用计算 机进行控制,用软件进行复杂的数据处理,也就大大提高了效率。2) 实现自动控制系统,由于很多机械加工场地存在一定的危险性,为了 达到安全生产的目的,实现远程控制是大势所趋的事情。在远程控制 室工作进行实时监控在机测量的同时还可以整理数据报告,检验和打 印报告单,既节约时间又节约人力资源。对于测量数据的处理与利用, 在早期的齿轮测量中。人工读指示表(如千分表等)获取齿轮误差,得 到的是误差幅值,仅仅能用来评判被检项目合格与否。电动记录器的 出现,靠人工读曲线,使工艺误差分析成为可能。
6、而计算机的采用, 使自动处理测量结果、分析工艺误差并将分析结果反馈到加工系统进 而修正加工参数成为现实9。目前,在齿轮测量数据处理方面,通 常采用的方法为最小区域法和最 d-乘法。理论上讨论最多的是最 小区域法,实际中广泛使用的是最小二乘法,同时数字滤波技术也得 到一定应用。如今的常用渐开线圆柱齿轮测量仪器有几十种。它们的 测量方法都已经为人们所熟知。按照齿轮测量的原理不同,可以大致 把它们分为两大类。类是比较法测量,或者称为相对测量法测量。 例如。齿形测量仪通过用机械范成或电子范成的渐开线与被测齿轮的 实际曲线比较并获得误差。这种测量方法现在用途极为广泛。另一类 是绝对测量法。例如,测量齿形
7、时,把实际的齿形曲线与数学理论曲 线相比较并获得误差。2 齿轮精度设计概述口 渐开线圆柱齿轮精度设计涉及面广,现简述如下。(1)公差组与精度等级 对齿轮传动一般有四个方向的要求 传动准确,即传动比变化尽量小; 传动平稳,即振动与噪声尽可能小.避免产生动 载荷与撞击; 工作点面接触好,即载荷分布要均匀,避免动载荷大时齿面应力集中,引起早期点蚀、折断而降低使用寿命 齿轮副侧隙要合适。按上述分析,齿轮精度标准按误第特性对传动性能的 主要影响划分为三个公差组表1 齿轮精度标准划分公差组公差与极限偏差陕差特性对传动性能的主要影响賂 ,弘F, F此以齿轮一转为周期的误差传递运动的准确性1Fi Ff、片、凡
8、*片,耳在齿轮一周内多次周期重复出现的误并传动平稳性、振动、噪声19F” Ft, %肉向课差载荷分布的均匀性关丁齿厚极限偏差和公法线平均长度偏差两个项H,由于它们属于侧隙配台系统,所以不包括在上述三个公差组内。齿轮精度设计就是要 确定两个公差组的精度等级,同时还要根据实际情况确定三个公差组 内帽膻评定指标。圆柱齿轮加工误差分析何淑菊, 邱淑英(哈尔滨工程大学 机电工程学院, 黑龙江 哈尔滨 150001) 从加工误差来看,影响齿向方向接触精度的主要因素是齿向误 差, 影响齿距累积误差的主要因素是齿轮的几何偏心, 就齿轮坯基 准面误差对齿向误差及齿距累积误差所产生的影响进行分析, 并找 出齿轮坯
9、基准面跳动值的一种确定方法, 并对加工齿轮改进方法进 行探讨。1 齿轮坯的基准面误差对齿向误差的影响准面是指加工齿轮时的定位面, 齿轮坯基准端面对齿轮轴心线 的垂直误差, 会使被 加工齿轮产生齿向误差或轴向齿距误差同理, 当安装齿轮坯的夹具 之端面 (基准面)出现跳动时也会出现类似上述结果齿向误差不仅 取决于上述两个方面, 也受其他诸多因素的影响:(1) 齿轮安装误差; 齿轮端面不平 (端面跳动) ; 夹具定位面 不平 (支承端面跳动)(2) 机床刀架几何误差: 横向倾斜, 纵向 倾斜2 基准面误差对齿距累积误差的影响 齿轮的齿距累积误差是分度圆上任意两个同侧齿面的实际弧长与公 称弧长之差最大
10、值的绝对值, 而影响齿 距累计误差的主要因素是齿轮的几何偏心。,齿距累积误差是齿轮的 几何偏心的 2倍.在实际加工中,引起工件偏心 的齿轮几何偏心的 原因有:1)由夹具心轴的径向跳动所引起的齿轮几何偏心 e12)由齿坯基准孔与夹具轴间的装配间隙引起的齿轮几何偏心 e23)由夹具支承端面与心轴轴线不垂直即夹具支承面跳动造成的齿轮 几何偏心 e34)由齿坯端面跳动引起的齿轮几何偏心 e45)机床工作台及锥孔等误差造成的几何偏心 e56)齿轮心轴在夹紧下变形而引起的齿坯几何偏心 e6上述各种造成工件偏心的总和, 在向量方向未知情况下可近似的按概率法合成为减小上述某些因素可以通过对机床安装定位夹具或补
11、偿误差所引起 几何偏心来消除, 但齿坯的端面径向跳动误差所引起的几何偏心是 不易消除的 因为工件在制造时必然存在一定的误差, 而且工件在夹 具上安装的角相位是随机性, 因此可按下式近似确定en k * b * 方/d式中:b为工件齿部厚度;d为定位面最大直径;Ab为工件端面 在定位最大直径上的跳动值; k 为系数 (根据机床、 夹具及调正的精度选择, 一般为 13)3,齿轮基准面跳动数值的确定方法齿轮的基准面是齿部加工的定位基准, 它的精度将直接影响齿 轮的齿向、 齿轮累积误差和接触精度, 此项精度值一般可在标准中 查得 对于某些要求偏严、 加工难度较大的齿轮, 为保证达到齿向 误差和齿距累积
12、误差的要求,应选择端面跳动精度要求较高的数值 而后把端面跳动数值做下列比较才能确定 (如图 )端面跳动对齿向误差和齿距累积误差的比较10)要求:式中:B为齿宽;Ab为轴孔配合间隙;Ad为端面跳动值选定的端跳值只有符合上述公式要求才是有效的, 反之会因 Ad 的干涉, 使定位面不能接触而失效 由上式作相应变换, d M B 广,即表明夹具心轴与齿轮孔的配合间隙也要符合上式, 才能使齿轮坯 的定位基准面与夹具定位面很好的接触当采用重叠装夹时, 端面跳动对齿轮精度影响为: 下层工件只受本 身下面端跳动的影响, 而上层工件除受本身下端跳动影响外还受下 层工件上下两面端跳动的影响; 工件两端面是车削而成
13、, 所以其跳 动方向不固定, 且重叠工件的装夹亦是随机的, 因此, 三个端跳 相互独立, 但其综合影响亦可采用概率合成, 即2 +寸+匂1若工件两端面跳动特性无差异,则二 V e6 二二岂二 ,J 二 丁3 E如果下层工件之端跳正好满足精度要求,(即工艺能力系数, 有 超 差),则上层工件的工艺能力相对下降7倍,其超差量将增加如 果多个工件重叠装夹,芒引起工件歪斜,有时便会使各工件接触面出现间隙或定位轴弯曲 为了保证精度, 当采用重叠装夹加工时, 应将公差适当缩小, 取原计算公差的 0.60.8 倍即可, 并且控制 端跳的加工误差1)加工齿轮时, 为了减少齿向误差, 齿坯基准面误差, 即端面
14、跳动公差应为齿向公差的一半2)齿轮基准端面跳动值应符合式 (10 ) 要求3)为了提高加工齿轮精度, 应保证齿轮毛坯端面与轴孔的垂直度、 轴孔的精度以及夹具的精度要求,即保证夹具零件 (工件心轴、 垫 圈、 螺母以及夹具底座等) 的制造精度及夹具的精度要求; 保证 刀具刀杆、 刀垫、 螺母的制造精度; 刀杆直 径按 级精度制造; 刀杆各配合粗糙度 应在以上用线性化方法研究直齿圆柱齿轮的动态性能胡舸 王建宏 陈国冲(1.重庆大学化学化工学院重庆 400030;2重庆大学机械工程学院重庆 400030)该文献是首先建立了一对啮台齿轮的有限元模型,然后将用非线 性方程表示的模型线性化,通过结合应用有
15、限元理论和接触力学理 论,得到齿轮的动态传输误差(比二)和接触力以及动态响应的关系。 此方法在齿轮动态研究领域显示出了较强的优越性。由于将非线性问 题转化成线性问题,避开了冗长的迭代过程,加速了求解过程。再者, 在接触及其附近区域使用接触力学理论,仅用数日较少的单元就可得 到精度足够的解。我国对直齿圆柱齿轮动态性能的研究已经很长时间了。刚开始 时,质量一弹簧模型得到了广泛应用并得出了很多有用的结论。但是 在这些研究中,系统的激励被假定为方波或类似的波形,但事实上并 非如此。直齿圆柱齿轮的动态性能是一种很复杂的现象,在本质上是 非线性的参数振动。如果不考虑制造误差,直齿圆柱齿轮的激励主要 来自于
16、接触刚度的变化和传动中同时啮合齿对数的变化。G. L-OsTIGuY 和 I. CONSTANINEScu应用有限元法 研究了一个单齿的自然频率、模态和由模态分析得到的啮合过程中的 瞬态响应。R. B. BHA等发现有限元方法在研究轮系的动态时十分有 用,因为关联的因素可以很容易地在质量矩阵和刚度矩阵中得到体 现。他们使用具有两个质量、两个弹簧和两个阻尼器的模型作为研究 对象,其中一组代表啮合的轮齿,另外一组代表齿轮的其他部分的影 响。AM ucHE等”提出了一种对理想齿面使用雅可比矩阵作动态约束 的自动算法来计算轮齿的变形。很明显,按照传统的思维,为了在轮齿上的接触区域得到精度足 够的解,有
17、限元的数目必须相当多才行,而局部细化又不适用于接触 区域在两个物体表面移动的情形,但有限元可以以相当的精度计算出 距接触区域一定距离的点的变形。另一方面,当接触物体远大于接触 区域时,弹性半平面法可以比较准确地给出接触区域内两点的相对位 移。因此,可以综台使用有限元法和半平面法来计算出直齿圆1 有限元分析1. 1 齿轮的有限元模型齿轮的有限元模型如图1 所示,轮齿的有限元模型如图2 所示。 轮齿受力后表面情况较复杂,因此轮齿表面用八节点的单元来表示, 而在其余地方,情况相对来说比较简单,用常用的四节点单元来表示。 齿轮主要用来传递力矩,就齿轮总体而言,非线性变形主要集中在轮 齿上,离轮齿越远的
18、地方,也就是说离齿轮中心越近的地方,齿轮的变形和受力情况相对越简单,因此有限元单元的数目也就相应地减少。ffl 1齿轮的有眼元模型12 数学模型直齿圆柱齿轮的动力学模型如图3 所示,可以用以下方程来表示。抓用+北+ &屯=码 f=l,2(1)式中旳齿轮上各节点的位移m禹-质量矩阵和刚度矩阵G阻尼矩阵Fi力矢量在许多有限元分析中,阻尼矩阵。是用质量矩阵III和刚度矩阵岛的线性组合来表示,也就是 Ray1ei 曲阻尼模型 - 7jm.十 Zki式中n和入是线性系数。在这里,为了表示方便,可以将主动轮和从动轮的式(1)表示组合起来写成齿轮对的有限元表示mx 十 ci + Ax = F13 非线性方程
19、的线性化应用 Newmark 方法对式(3)离散化,可写成以下形式灵kx-F图2轮齿上单元的分布,齿表面为八节点 单元,其余邮分为四节点单元图3啮合齿轮对的力学模型flM.kxF式中*等效刚度矩阵Z = Jt 十一 mc如0加山-离散的微小时间段P,y -定臾Newmark方法的参数F等效力矢量F = BFc-RFc 互相臥合的齿轮的接触力矢量B个已知的、非方阵的矩阵,用来将接触力分配给附近的节点,矩阵B决于单元的边界几何以及有限元的插值模式R动态项(6)一褊耳% 為式中 勺一齿轮上承受力矩卩的节点的位移 斗一一齿轮上其余节点的位移爲与齿轮上承受力矩T的节点相对应 的动态项Rx 一与齿轮上其余
20、节点相对应的动态项 y 一齿轮传输的力矩5 将力矩尸分配到边界节点的矢量 从式卩)分别求得卜=-严+二”(7)k =A;(B + jB)眞 + 町(Rx -區显)式中 k=k-%xk rt.-r*W faiV aR-kRkST+k%齿轮对的节点位移可表乐为 x=|x4=?z+*GJ -kBFCR15 相对于接触点的参照点位移对于相互啮合轮齿上的一对接触点,尽管在轮齿的表面是八节点 的单元,但由于轮齿啮合的复杂性,不能直接由节点位移根据位移模 式来计算接触点的位移。但是位于接触点正下方,距其一定距离的参 照点的位移可以用有限元法相当准确地计算出来。而接触点和参照点 之间的相对位移可由弹性半平面法
21、来计算。下面首先用有限元法计算齿轮上参照点的位移式中,u和v,分别表示参照点在z轴和y轴的位移。G是已知的, 由有限元位移模式和参照点的坐标决定的矩阵,用来从有限元节点位 移计算出参照点位移。下标r表示是参照点,下标x和y表示x坐标 和 y 坐标。16 接触点和参照点之间的相对位移一对相互啮合的齿轮,轮齿在接触点的外形轮廓应为渐开线,但 由于接触区域相当小,因此,可以近似地认为接触区域的轮廓外形为 圆弧,其半径可由齿轮的渐开线方程得到。17 接触点的位移齿轮轮齿表面上接触点的位移是由参照点的位移加上接触点和 参照点之间的相对位移。如图4所示,f和f分别表示一对啮合齿轮的轮齿表面曲线。西表示 轮
22、齿上的两个可能接触点在未变形之前的初始距离。全局坐标系为x, y,位于接触点的局部坐标系为x7, y。局部坐标系的y轴方向为 接触点的法线方向。 d 为主动轮和从动轮上接触点到参照点之间的距 离。由式(9)得到的参照点位移为全局坐标系x, y下的位移,利用旋 转矩阵将其转换成局部坐标系z。y下的位移。一对共轭齿轮,如 果不考虑齿轮的弹性变形,接触点的轨迹应为齿轮的啮合线。但实际 上齿轮承载以后,齿轮的弹性变形使得实际接触点不再是啮合线上 的点。对于接触分析而言,由于轮齿受力后实际接触点应在理论接触 点附近。因此,将轮齿表面上理论接触点附近的区域离散化,在齿面 的法线方向计算出一系列的可能接触点
23、, 并计算这些可能接触点对 在受力前的距离,然后将可能接触点对的距离与动态项相加,距离最 近的可能接触点对作为实际接触点。从该文献我们了解到使用有限元和接触力学研究一对参数相同 的齿轮对的动态性能。接触力是通过在接触齿对的半分析法的有限元 公式得到。所使用的方法具有以下显著特点。(1) 需要作任何假设,它克服了有限元法在静态分析、响应计算等应 用中的一些限制。(2) 由于在接触点不是靠增加单元数目来提高精度,因此所使用的有 限元数目大为减少,相应地减少了计算时间。(3) 晟后联立求解的方程都是线性方程,求解过程耍远比直接求解非 线性方程简单,因为目前非线性方程的求解一般都是采用迭代法。(4)
24、本方法特别适用于离散动态模型中啮合建模比较困难的多体多接 触系统。在三坐标测量机上精确测量渐开线圆柱齿轮的齿形误差黄富贵 张认成华侨大学针对传统齿针对传统齿形误差测量方法的测量误差来源多、 测 头与工件装调整误差大等缺点, 提出一种在三坐标测量机上利用扫 描法实现渐开线圆柱轮齿形误差测量的新方法。该测量方法具有测量 采集点精度高、 齿形轮廓曲线拟合误差小、 测量过程与误差处理过 程人工干预少、 测量精度高等特点。齿形误差是反映齿轮工作平稳性精度的重要指标之一, 齿形误 差的精确测量与评定可以有效地判定第 公差组的性能指标, 同时, 通过对齿形误差测量结果的分析, 可以找到误差的产生原因,为齿
25、轮加工机床参数的调整、 刀具的修磨等提供科学依据。因此, 齿轮 齿形误差的精确测量一直以来都是齿轮 测量技术人员的一个研究热点。目前, 渐开线圆柱齿轮齿形误差的 测量方法主 要有标准设计齿形比较法、 标准渐开线轨迹法和坐标测量法等三大 类。标准设计齿形比较法是将被测实际齿形与标准设计齿形曲线进行 比较而得到齿形误差的方法。该方法的主要问题在于: 被测齿轮端 面与齿轮定位孔的孔心线垂直度误差、 成像误差等将直接影响测量 结果的准确性。因此,该方法只适于盘类齿轮齿形误差的测量, 而 且测量精度低, 一般只能对/级以下精度的齿轮进行测量。标准渐开 线轨迹法是将被测齿形与仪器复现的标准理论渐开线轨迹进
26、行比较, 求出齿形误差, 并通过在直尺基圆盘式、 圆盘杠杆式等机械展 成仪或电子展成仪上实现。该方法的主要问题在于: 仪器的基准误 差被测齿轮的安装误差以及基圆盘的直径尺寸误差等对测量结果影 响较大。坐标测量法是将被测齿形上若干点的实际坐标与理论坐标进 行比较的一种测量方法。采用这种方法测量必须解决两个问题: 实 际坐标的获取; 理论坐标的计算。该方法的主要问题是计算繁琐特 别是测点要求多、 测点布置有特殊要求时,数据处理工作量大。针 对目前齿形误差测量与数据处理的缺点,本文提出了一种在三坐标测 量机上利用扫描法实现测量点数据采集、利用三次样条函数实现齿形 工作曲线拟合、利用展成法实现齿形误差
27、评定的渐开线圆柱齿轮齿形 误差测量的新方法。该测量方法测量点数据采集与齿形误差评定简 便,测量效率高,测量精度高。1,其原理如下GB10095-88渐开线圆柱齿轮精度中齿形误差的定义为:在端 截面上,齿形工作部分内(齿顶倒棱部分除外)包容实际齿形且距离 为最小的两条设计齿形间的法向距离。设计齿形可以是修正的渐开线 (包括理论渐开线、凸齿形和修缘齿形等)图 1 齿形误差测量简图。 根据渐开线圆柱齿轮齿形展成法的形成原理,理论齿形上各点的展开 角增量厶与应的展开长度增量应满足以下关系式式中 r 为齿轮的基圆半径,可由被测齿轮参数求得。若被测齿轮为渐开线圆柱直齿轮rb二m*cosa/2;若被测齿轮为
28、渐开线圆柱斜齿轮, 则rb=m*Z*cosat/2,rb单位为mmog为展开长度增量,为角 度增量。2,其测量方法是要实现对被测齿轮齿形误差的评定,首先应得 到被测齿轮的实际齿形轮廓曲线。该曲线可以采取如下方法获得:先 对实际齿轮齿形轮廓上有限点的坐标数据进行精确采集,然后采用三 次样条函数将实际齿形轮廓上有限点拟合成连续曲线。三次样条函数 的主要优点是其光滑程度较高,保证了插值函数一阶、二阶导数的连 续性。因此,实际齿形曲线用三次样条函数拟合在理论上可行,而且 符合齿轮的 设计要求。三次样条函数的拟合精度主要决定于采集点 的多少与分布形式。实际测量中,采集点应主要分布在齿轮正常工作 齿面上,
29、靠近齿顶或齿顶修缘部分尽量不采点;过渡渐开线与正常工 作齿面交界处以下部分不采点;靠近齿轮分度圆附近采集点应分布较 密,靠近齿顶和齿根部采集点应分布较疏,采集点的数量也不要太多。 测量实践表明:对于模数为22 的齿轮,齿面上的采集点数一般控 制在 *%点以下,这样可以得到较高的拟合精度。图1齿形误差测量简图从该文献我们了解到在Status FX 777型三坐标测量机上利用扫 描法实现渐开线圆柱齿轮齿形误差的测量方法,可克服传统齿形误差 测量方法的测量误差来源多、测头与工件安装调整误差大的缺点。同 时,该测量方法除测量数据采集、实际齿形轮廓曲线的三次样条函数 拟合需要人工干预外,数据处理与齿形误
30、差的评定全部依靠计算机完 成,测量误差与评定误差小,测量简便实用。理论分析与比较测量实 验结果表明:该测量方法的测量精度高,适合于盘类渐开线圆柱直齿 轮和斜齿轮齿形误差的精确测量。计算机辅助渐开线圆柱齿轮精度设计李亚非,王 诚(长沙理工大学 汽车与机械工程学院,湖南 长沙 410114)介绍了笔者开发的一种用Visual C+语言编写的齿轮精度CAD 软件,该软件操作简单,采用了新国标,能快速正确地确定齿轮的精 度等级、 检验项目及公差值,并可生成齿轮零件图,实例证明软件 正确可行。齿轮精度的高低,直接影响到齿轮传动的工作性能和使用寿命。 因此,各国先后多次制订和修订了广泛应用于汽车、飞机、机
31、床、工 程机械、 农业机械、 仪器仪表等机械产品中的圆柱齿轮精度标准。 但整个齿轮精度设计过程十分繁琐,要查取多张表格,用到的计算公 式多而复杂,设计工作量大,花费时间多,且易出错。对此,人们想 到了计算机辅助设计的方法,基于 GB/T100951988 渐开线圆柱 齿轮精度 的 CAD 系统,大多采用 VB 语言编程及三个公差组来控 制齿轮公差。本文介绍一种采用Visual C+语言自主开发的基于2008 年新国标的设计软件,摒弃三个公差检验组的分类,根据齿轮工作环 境选择推荐的检验组,用该软件可以轻松完成齿轮精度设计工作。1 软件的界面设计Visual C+是种面向对象的程序设计语言,提供
32、可视化编程工具应用程序向导AppWizard和类向导ClassWizard,用它可以方便的设 计出良好的图形用户界面。图 1 为本软件的界面(含一个实例的运 行结果) 。它用一个界面集成了两大功能:设计参数的输入,设计 结果的显示及输出。 运行时,用户只需对有关控件进行简单的操作 (如在文本框中输入已知参数值,或用鼠标点击按钮等)就能完成相 应的任务。2 软件的工作流程设计免 jtt严 itKKrtrS 诫 if 4JV Tifi9&- - 2ooe:砂用请EErtJLSfM 嗣Fl-b旳 |a d M7-0. I r r J社 iiTia& :c r匚血1殆电卩昉IT:;:常吐己融磁I图1软
33、件界面图ZE涓定車个囱轮栓脸项日打印数捱图2软件沛程图输入己幻掘丰潇定齿坯精陀硝定齿轮制特麦主a!akx文件常定精度箋级根据最新的国家标准以及参考文献第 10 章第 5 节介绍的圆柱齿轮 精度设计方法和步骤,圆柱齿轮精度设计的主要内容有:(1)齿轮精度等级的确定;(2)单个齿轮精度评定指标的确定;(3)齿轮副精度评定指标的确定;(4)齿坯精度的确定。该软件的工作流程见图 2。 其流程图的设计要点简介如下:2.1 输入已知参数在 “输入已知参数” 框架内,包含有 10 个文本框,2 个下拉列表 框,下拉列表框中列出了机床、 轻型汽车、 重型汽车、 汽轮机减 速器、 一般减速器、 起重机、 农业机
34、械等不同用途的齿轮,输入 齿轮的齿数、 模数、 转速、 应用范围等已知数据。 确定精度等级2.3 确定单个齿轮检验项目GB/T 100951988 将单个齿轮的各项公差分为三个公差计算机先根 据齿轮应用范围,使用要求,工作条件查表确定精度等级大致范围, 再根据计算得出的小齿轮圆周速度查表确定其精度等级组,并将同一 公差组内的各项指标分为若干个检验组。然后根据生产批量、 使用 要求、 测量设备条件等选择一个检验组来检查齿轮的精度。但 2008 年的国家标准没有给出公差组和检验组,并指出:在检验中,测量全 部轮齿要素的偏差既不经济也没必要。该软件按齿轮工作性能要求推 荐了若干个检验组,将齿轮使用范
35、围分为机床、轻型汽车、 重型汽 车等 12 大项数十小项。表 1 为机床齿轮的分类及推荐检验项目举 例。检验项目还可以根据生产实际情况作适当调整。当有条件检验 和 时,可以不必检验 和 。测量 简单、 方便,所以常用。 如果 能检验 和 ,则不必检验 。检验项目确定后即可根据国家标准 中给出的计算公式自动求出各偏差允许值。2.4 确定齿轮副精度 齿轮副的评定指标主要有:齿轮副的中心距偏差 ,齿轮副的轴线平 行度偏差 和 ,齿轮副的侧隙 等。侧隙通常由齿厚偏差 或公法线平 均长度偏差 来控制。测量公法线长度比测量齿厚方便、 精确,因此 生产中常用测量公法线长度的方法来控制齿轮副侧隙。2.5 确定
36、齿坯精度齿坯是指在轮齿加工前供制造齿轮用的工件。齿坯精度包括内孔、 顶圆、 端面等定位基准面和安装基准面的尺寸 偏差和形位误差以及表面粗糙度要求。具体数据有表可查。2.6 数据打印 为了方便计算数据的保存及打印,软件生成一个 TXT 文本,保存输 入参数、 国标规定的精度项目和侧隙指标计算值等2.7 生成工程图利用新的开发工具 ARX (Au toCAD Run time eXt ension)对 At oCAD 进 行二次开发,ARX程序本质上是Windows DLL程序,与AutoCAD共 享 地址 空间, 以消 息驱 动的 方式直 接调 用 AutoCAD 的 核心 函 数,Au to
37、CAD通过调用入口函数来调用该文献采用 51 单片机及其外部扩展电路对 209T 制动梁端 轴焊接预热温度进行检测和显示,控制了 209T 制动梁端轴的焊接 在设定的预热温度下进行。应用表明,该预热温度检测系统达 到了改善焊接接头的塑性、防止冷裂纹和减少焊后残余应力 的目的,提高了 209T 制动梁更换端轴的质量,保证了客车运 行中制动梁端轴工作的可靠性。计算机辅助圆柱齿轮精度设计系统的研究 牛贵峰 姚辉前 邱亚玲(南石油学院机电工程学院 四川成都 610500) 齿轮精度设计牵涉的因素较多 标准中对渐开线圆柱齿轮精度 共规定了 个指标 使得精度设计繁杂 麻烦 本文介绍用 语言编写的 软件来完
38、成齿轮精度设计工作 人机对话采用交互式窗口 使得设计 方便 迅速经实际运行表明该系统在齿轮精度设计上有效准确1 ,齿轮精度设计概述渐开线圆柱齿轮精度设计涉及面广 现 简述如下公差组与精度等级对齿轮传动一般有四个方面的要求传动 准确 即传动比变化尽量小传动平稳 即振动与噪声尽可能小 避免产 生动载荷与撞击工作点面接触好 即载荷分布要均匀 避免动载荷大 时齿面应力集中 引起早期点蚀 折断而降低使用寿命齿轮副侧隙要 合适按上述分析 齿轮精度标准按误差特性对传动性能的主要影响划 分为三个公差组 详见表表I 齿轮精度标准划分公差组公差与极限偏差溟差特性对传动性能的主要影响F/, F” 质,FC, F F
39、*以齿轮一转为周期的谋差传递运动的准潇性11F/, F-,号,F=臨,FjB在齿轮一周内寒次周期重复出现的谋差传动平稳性、振动、噪声塊.Flr质齿向溟差载荷分布的均匀性关于齿厚极限偏差和公法线平均长度偏差两个项目由于它们属 于侧隙配合系统 所以不包括在上述三个公差组内齿轮精度设计就是 要确定三个公差组的精度等级 同时还要根据实际情况确定三个公差 组内相应评定指标选择齿轮精度等级必须根据其用途 工作条件等要 求来确定 如考虑齿轮使用的场合 工作速度 对振动噪声的要求以及 使用寿命等方面的要求 同时还应考虑在不同用途不同工作条件时 对齿轮的要求侧重点不同 因此各公差组应选用不同的精度等级 精 度等
40、级的选择一般有两种方法一为计算法 一为类比法 计算法相应 复杂 类比法必须有丰富的资料 目前已总结许多资料可供设计时参 考 本文是在类比法基础上辅以适当的计算来确定齿轮的精度等级齿 轮副的侧隙为保证齿轮传动正常工作 在齿轮非工作点面间应有合理 的侧隙以贮存润滑油和补偿齿轮在工作时的变形 对于齿轮副的侧隙 精度标准规定采用基中心距制 即通过改变齿厚以得到不同的侧隙 为此规定了种齿厚极限偏差及代号 侧隙的设计就是要确定齿厚上下偏差及其代号 齿厚上 下偏差的确定可用计算法 类比法和试验法考虑到类比法资料不全 试验法成本较高 故本文采用计算法 虽然公式中考虑的因素尚不全 面 但也是目前设计中比较可靠的
41、方法2 ,基于以上分析 我们给出齿轮精度设计的流程框图如如下图 所示由于 Visual Basic 语言是一种面向对象编程的模块化语言与传 统的面向过程的语言不同 它通过鼠标单击界面上的控件就可以使该 控件所代表的事件发生 即完成相应的任务 所以执行程序时 也可以 不完全按照框图所示的顺序 如在该软件中 确 定 好 齿 厚 上下偏 差后 又感觉齿轮精度等级确定得不妥 只要再单击 确定齿轮精度钮 就可重新确定齿轮精度等级。是否改轮?星示大、小齿轮鏑加井H用 子程序宦IMWa那齿思站舉大齿轮糖果定氐i*匪野 Bvii Em按斛齿轮 计鼻參数计*其特点主要是整个齿轮精度设计系统始终采取了友好的人机 界面用户只要按计算机提示键入相应的内容 程序就会自动运行并输 出结果 实践证明 本算法能够快速成功地解决渐开线圆柱齿轮的精 度设计问题 程序采用Visual Basic编程语言可方便与其它高级语言 兼容 在机械设计中具有一定的实用性.看了这么多的文献论文,对自己所要做的设计也有了一些初步的 理解,相信自己在老师和学长的帮助下,会顺利的完成这次课程设计!
- 温馨提示:
1: 本站所有资源如无特殊说明,都需要本地电脑安装OFFICE2007和PDF阅读器。图纸软件为CAD,CAXA,PROE,UG,SolidWorks等.压缩文件请下载最新的WinRAR软件解压。
2: 本站的文档不包含任何第三方提供的附件图纸等,如果需要附件,请联系上传者。文件的所有权益归上传用户所有。
3.本站RAR压缩包中若带图纸,网页内容里面会有图纸预览,若没有图纸预览就没有图纸。
4. 未经权益所有人同意不得将文件中的内容挪作商业或盈利用途。
5. 装配图网仅提供信息存储空间,仅对用户上传内容的表现方式做保护处理,对用户上传分享的文档内容本身不做任何修改或编辑,并不能对任何下载内容负责。
6. 下载文件中如有侵权或不适当内容,请与我们联系,我们立即纠正。
7. 本站不保证下载资源的准确性、安全性和完整性, 同时也不承担用户因使用这些下载资源对自己和他人造成任何形式的伤害或损失。