ERP实验报告(最终版)
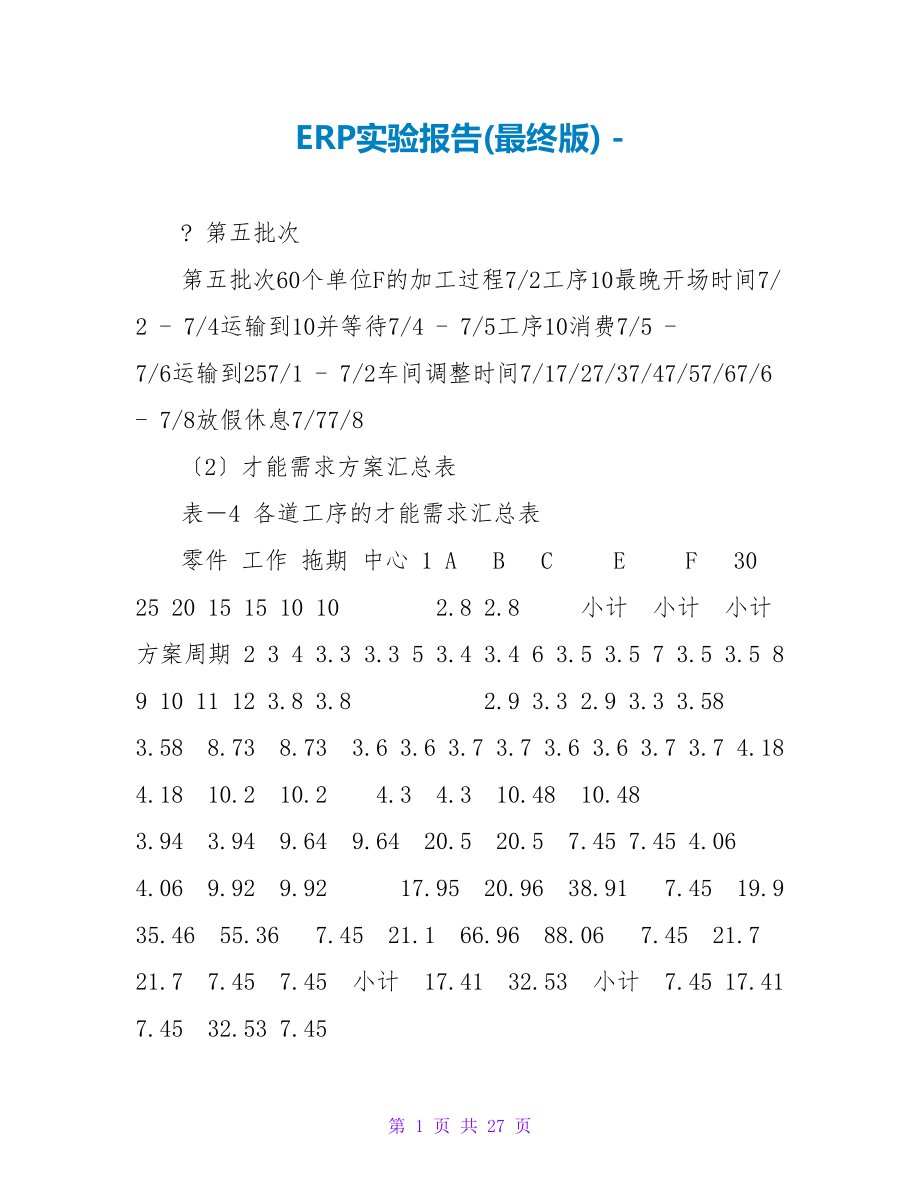


《ERP实验报告(最终版)》由会员分享,可在线阅读,更多相关《ERP实验报告(最终版)(27页珍藏版)》请在装配图网上搜索。
1、ERP实验报告(最终版) - ? 第五批次 第五批次60个单位F的加工过程7/2工序10最晚开场时间7/2 - 7/4运输到10并等待7/4 - 7/5工序10消费7/5 - 7/6运输到257/1 - 7/2车间调整时间7/17/27/37/47/57/67/6 - 7/8放假休息7/77/8 2才能需求方案汇总表 表4 各道工序的才能需求汇总表 零件 工作 拖期 中心 1 A B C E F 30 25 20 15 15 10 10 2.8 2.8 小计 小计 小计 方案周期 2 3 4 3.3 3.3 5 3.4 3.4 6 3.5 3.5 7 3.5 3.5 8 9 10 11 12
2、3.8 3.8 2.9 3.3 2.9 3.3 3.58 3.58 8.73 8.73 3.6 3.6 3.7 3.7 3.6 3.6 3.7 3.7 4.18 4.18 10.2 10.2 4.3 4.3 10.48 10.48 3.94 3.94 9.64 9.64 20.5 20.5 7.45 7.45 4.06 4.06 9.92 9.92 17.95 20.96 38.91 7.45 19.9 35.46 55.36 7.45 21.1 66.96 88.06 7.45 21.7 21.7 7.45 7.45 小计 17.41 32.53 小计 7.45 17.41 7.45 32.
3、53 7.45 编制才能需求方案表时,数据主要是利用下面的方式:将主消费方案中的方案产量与单位产品的才能资总量相乘,求得每个产品系列在各方案周期的总才能需求;将每个产品系列所需要的才能加总,求得对应方案的总才能;分析p 个关键工作中心的才能情况,并提出平衡的建议。 5 编制才能负荷图 1 工作中心30 4.003.00才能需求2.001.000.00123456789112周期 图 1 工作中心30的才能负荷图 2 工作中心25 5.004.00才能需求3.002.001.000.00123456789112周期 图 2 工作中心25的才能负荷图 3 工作中心20 12.0010.008.00
4、才能需求6.004.002.000.00123456789112周期 图 3 工作中心20的才能负荷图 4工作中心15 100.0080.00才能需求60.0040.0020.000.00123456789112周期 图 4 工作中心15的才能负荷图 5工作中心10 40.0030.00才能需求20.0010.000.00123456789112周期 图 5 工作中心10的才能负荷图 关于才能/负荷的调整,首先可以调整才能例如:调整劳动力、变更工艺道路、转包后增加设备、进步设备的利用率。其次可以调整负荷例如:并行作业、分批消费、调整订单等。 6、请选择某个批次的产品制定对应的车间作业方案PAC
5、,要求对该批次产品的消费过程所涉及的各个关键工作中心制定“派工单” 工程 F 工序号 10 关键工作中心 10 数量 60 最早开工时间 5月6号 最晚开工时间 5月7号 最晚完工时间 5月10号 7 心得体会与经历总结 在做实验过程中涉及的理论东西不多,没有大段的概念,主要的是要求我们对平时所学知识点的应用,更加注重理论的重要性。主要涉及的章节有ERP与预测、ERP的消费方案大纲、ERP主消费方案的编制、ERP物料需求方案的编制和ERP才能需求方案的编制,其中涉及的内容主要有预测方法、主消费方案的编制方法和步骤、在不同时区的毛需求量确实定、关于粗才能方案的编制、物料需求几环的计算步骤、MRP
6、编制的方法、用倒序排产发计算工序的开工日期和完工日期、绘制才能负荷图等 首先根据上一年度产品A的实际需求数据利用挪动平均法,得到本年度各个周期产品T,A的预测量。根据预测的数据得到公式 Y12?T?27.22?0.5556然后编制MPS,再制定各个物料的物料需求方案。根据已经计算好的MRP编制每道工序的才能需求方案,再计算每个工作中心的可用才能,计算每个工作中心对各个负荷的加工天数,用倒排序法计算每道工序的开工日期和完工日期,用visio软件画出每道工序的开工和完工时间及中间过程。然后编制各道工序的才能需求汇总表,画出才能负荷图,最后选择某个批次的产品制定对应的车间作业方案。 在整个实验中自己
7、还是学到了很多东西,因为在选这门课程的时候问过学长,他们说这门课程是很有用的,所以相对于别的专选听的算是认真的。并且我们只看到了它的表象,感觉和我们会计一点也不挂钩,没啥用,我觉得其实不然这上面好多东西都和我们专业相关,只是我们没能透过现象看到其本质。我觉得这门课程对于我们以后工作上是有用的,也许如今这些知识点都学得是一知半解的,但是要将那些需要自己记住和理解的都应该记住,这样在我们以后出去工作后也能做铺垫,为自己刘一个比拟好的根底,那样学起来也不会那么吃力,也许还会有事半功倍的效果。在实验过程中没有能完全将老师讲的知识点完完全全的理解和吃透,并且还存在着一些问题,通过自己做这份实验报告,对于
8、有些知识比以前就理解的深入多了例如物料需求方案的编制,老师把数据给出来了,然后自己就一个一个的对着算,然后将这些数据全部自己算了一遍。在这过程中我觉得最大的收获是学会了两个软件一个是visio,一个是SPSS软件,我觉得他们好有用,能帮我们减轻很多的负担,还能帮我们节约大量时间,也有利于我们进展分析p 。在整个报告中需要用倒序排产法计算工序的开工日期和完工日期这个环节有些不是自己画的,在开场的时候不懂怎么推出时间,然后问了一下同学自己探索了好长时间才弄懂,就画只画了零件A和零件B的其余的是抄的同学的,自己感觉会画了,然后就偷懒了。还有一些知识点没弄懂得,也是在网上找的。 在整个过程中仍然存在着
9、很大的缺乏,这些需要自己去改正,对于自己的整体评价是虽然做的不是那么尽善尽美,但是我觉得自己态度是很端正的,那些东西我愿意去学,愿意花时间去弄懂,虽然没能把这门课学的很好,至少我为它付出了,也许没有专业课的时间多。关于这门课唯一觉得比拟认同自己的也就只有态度了,态度也只能说是比拟好,对自己的期望分值是81分。 评分: 企业资方案ERP实验报告 20222022 专 业: 学 号: 姓 名: 年 级: 指导老师: 长江大学管理学院实验中心 实验一 企业资方案与才能需求方案 实验背景资料 1、某产品A的物料清单如图1所示,LT表示物料提早期,括号中的数表示物料的用量因子。其中,零件D为外购品,其它
10、零件B、C、E、F为需要企业安排消费。 产品ALT0B1LT1C2LT2E2LT2F1LT1D2LT1 图1 产品A的物料清单 2、产品A的需求数据、零件的库存信息、工艺道路,以及工作中心工时定额信息和工序间隔时间分别见以下各表。 表-1 方案展望期内产品A的需求 产品A 周期 实际订单量 需求时区 1 24 2 25 3 20 方案时区 4 25 5 18 6 20 7 0 8 预测时区 9 10 11 12 10 0 0 8 0 表-2 产品A上一年度的实际需求数据 周期 实际需求量 1 20 2 21 3 21 4 22 5 24 6 24 7 25 8 9 10 11 12 26 25
11、 26 27 27 表-3 产品A各加工工序的时间间隔 工作中心 30 25 20 15 10 库房 工序间隔时间 等待时间 2 1 1 1 1 运输时间 1 1 1 1 1 1 表-4 产品A的工艺道路及工时定额 工程 A B C E F 工序号 10 10 10 20 10 20 10 关键工单件加工消费准备作中心 30 25 15 20 10 15 10 时间 0.1 0.06 0.15 0.07 0.12 0.25 0.11 时间 0.4 0.28 1.6 1.1 0.85 0.96 0.85 平均批量 单件准备时间 单件总时间 20 40 80 80 100 100 80 0.02
12、0.07 0.02 0.0138 0.0085 0.0096 0.0106 0.12 0.067 0.17 0.0838 0.1285 0.2596 0.1206 3、产品A的批量规那么是净需求量法;零件B、C的批量规那么均是:2周期净需求量,零件E的批量规那么是:3周净需求,零件F的批量规那么是:固定批量60。 表-5 各零部件的批量规那么 项方案收到量 目 1 2 3 A E F B 38 现有库存 已分配量 提早期 固定批量 4 5 6 7 8 14 140 22 33 1 2 1 2 2周 3周 60 2周 80 C 72 4、各个工作中心的工时定额数据。企业每周工作5天,每天工作8小
13、时,每个工作中心只有一个操作工,所有的工作中心利用率和效率均为95%。 假设第2周接收到的80件零件E的第一道工10已经完成,其第二道工序20还需要在第一周占用工作中心15的才能。 试根据以上数据编制消费物料的需求方案、才能需求方案,并分析p 其才能负荷情况,以及外购物料D的采购方案。 实验过程 1、预测展望期内的产品A的需求 根据上一年度产品A的实际需求数据利用挪动平均法预测方法,得到本年度各个周期产品A的预测量如表-1所示。 表-1 挪动平均法预测 周期 上一年度实际需求 三个月的一次挪动平均 三个月的二次挪动平均 1 2 3 4 5 6 7 8 9 10 11 12 20 21 21 2
14、2 24 24 25 26 25 26 27 27 20.67 21.33 22.33 23.33 24.33 25 25.33 25.67 26 26.67 21.44 22.33 23.33 24.22 24.89 25.33 25.67 26.11 根据上表中的数据,得到的预测公式为: Y12?T?27.22?0.5556T 1 根据上式,可以预测该年度各个月份的需求量如表-2所示: 表-2 方案展望期内产品A的预测需求 产品A 周期 预测需求 需求时区 1 28 2 28 3 29 方案时区 4 29 5 30 6 31 7 31 8 预测时区 9 10 11 12 33 33 34
15、32 32 2、编制产品A的主消费方案MPS 1)根据消费规划和方案清单确定对每个主消费方案对象的消费预测。2)根据消费预测、已收到的客户订单、配件预测以及该最终工程作为非独立需求项的需求数量,计算总需求。3)根据总需求量和事先确定好的订货策略和批量、平安库存量和期初库存量,计算各时区的主消费方案量和预计可用量。4)用粗才能方案评价主消费方案备选方案的可行性,模拟选优,给出主消费方案报告。 在需求时区内:客户需求取代了预测值,毛需求量为客户的订单需求;在方案时区时:需求将预测需求和实际需求加以合并,通常取两者中较大者;在预测时区内:毛需求量为预测值 方案周期 1 2 表3 产品A的主消费方案
16、3 4 5 6 7 8 9 10 11 12 实际需求 预测需求 主消费方案 20 28 24 21 28 25 21 29 29 22 29 29 24 30 30 24 31 31 25 31 31 26 25 32 32 32 32 26 33 33 27 33 33 27 34 34 3、制定各个物料的物料需求方案表-4 表4 各零部件的物料需求方案 工程 毛需求量 库存 方案周期 1 2 3 55 7 110 80 138 55 33 60 110 0 110 110 3 29 26 55 58 51 109 122 60 0 122 4 0 0 61 58 0 0 122 12 1
17、38 61 26 34 60 122 0 122 122 5 31 30 61 60 62 60 122 126 26 60 0 126 6 0 0 63 62 0 0 126 0 264 63 23 37 60 126 0 126 126 7 31 32 31 63 62 64 62 126 130 0 23 60 0 130 8 0 0 65 64 0 0 130 130 264 65 18 42 60 130 0 130 130 9 33 32 65 64 66 64 130 134 18 60 0 134 10 0 0 67 66 0 0 134 0 0 67 11 49 60 134
18、 0 134 134 11 34 33 67 66 68 66 134 0 11 0 12 34 0 0 68 0 0 0 11 0 24 25 29 29 30 31 32 32 33 33 方案接收量 38 B 14 28 净需求量 方案入库 方案下达 毛需求量 C LT=2 库存 48 50 58 方案接收量 72 33 57 109 60 0 110 净需求量 方案入库 方案下达 毛需求量 方案接收量 E LT=2 库存 净需求量 方案入库 方案下达 毛需求量 方案接收量 F LT=1 库存 净需求量 方案入库 方案下达 毛需求量 方案接收量 D LT=1 库存 0 净需求量 方案入库
19、 采购下达 140 140 110 110 126 126 134 134 22 22 27 27 制定方法:首先根据A产品的物料清单和主消费方案得出B、C的需求量,并根据A物料清单中的比例来确定彼此之间的关系,而E、D、F的需求量是由B决定的,产品A的批量规那么是净需求量法;零件B、C的批量规那么均是:2周期净需求量,零件E的批量规那么是:3周净需求,零件F的批量规那么是:固定批量60。净需求量=本期需求量-上期末可用库存量-本期方案接收量+平安库存,方案下达量由批量规那么决定,当毛需求大于期初库存时,净需求=毛需求-期初库存,综上计算得到各零部件需求方案。 4 编制每道工序的才能需求方案
20、1计算每道工序在每个工作中心上的负荷 1工作中心30 从工艺道路可以看出,工作中心30只与物料A有关,根据12批次的A物料可以算出各周期内工作中心30的才能需求如下: 24 25 29 29 30 31 31 32 32 33 33 34 第一批次24个单位的A需要的才能为:24*0.1+0.4=2.8小时 第二批次25个单位的A需要的才能为:25*0.1+0.4=2.9小时 第三批次29个单位的A需要的才能为:29*0.1+0.4=3.3小时 第四批次29个单位的A需要的才能为:29*0.1+0.4=3.3小时 第五批次30个单位的A需要的才能为:30*0.1+0.4=3.4小时 第六批次3
21、1个单位的A需要的才能为:31*0.1+0.4=3.5小时 第七批次31个单位的A需要的才能为:31*0.1+0.4=3.5小时 第八批次32个单位的A需要的才能为:32*0.1+0.4=3.6小时 第九批次32个单位的A需要的才能为:32*0.1+0.4=3.6小时 第十批次33个单位的A需要的才能为: 33*0.1+0.4=3.7小时 第十一批次33个单位的A需要的才能为:33*0.1+0.4=3.7小时 第十二批次34个单位的A需要的才能为:34*0.1+0.4=3.8小时 2工作中心25 从工艺道路可以看出,工作中心25只与物料B有关,根据5批次的物料B可以算出各周期内工作中心25的才
22、能需求如下: 55 61 63 65 67 第一批次55个单位的B需要的才能为:55*0.06+0.28=3.58小时 第二批次61个单位的B需要的才能为:61*0.06+0.28=3.94小时 第三批次63个单位的B需要的才能为:63*0.06+0.28=4.06小时 第四批次65个单位的B需要的才能为:65*0.06+0.28=4.18小时 第五批次67个单位的B需要的才能为:67*0.06+0.28=4.3小时 3工作中心20 从工艺道路可以看出,工作中心20只与物料C有关,根据5批次的C物料可以算出各周期内工作中心20的才能需求如下: 109 122 126 130 134 第一批次1
23、09个单位的C需要的才能为:109*0.07+1.1=8.73小时 第二批次122个单位的C需要的才能为:122*0.07+1.1=9.64小时 第三批次126个单位的C需要的才能为:126*0.07+1.18=9.92小时 第四批次130个单位的C需要的才能为:130*0.07+1.1=10.2小时 第五批次134个单位的C需要的才能为:134*0.07+1.1=10.48小时 4工作中心15 工作中心15从工艺道路可以看出,工作中心15与物料C与E有关,5批次的C与2个批次E 根据5批次的C物料可以算出各周期内工作中心15的才能需求如下: 109 122 126 130 134 第一批次1
24、09个单位的C需要的才能为:109*0.15+1.6=17.95小时 第二批次122个单位的C需要的才能为:122*0.15+1.6=19.9小时 第三批次126个单位的C需要的才能为:126*0.15+1.6=20.5小时 第四批次130个单位的C需要的才能为:130*0.15+1.6=21.1小时 第五批次134个单位的C需要的才能为:134*0.15+1.6=21.7小时 根据2批次的E物料可以算出各周期内工作中心15的才能需求如下: 138 264 第一批次138个单位的E需要的才能为:138*0.25+0.96=35.46小时 第二批次264个单位的E需要的才能为:264*0.25+
25、0.96=66.96小时 第二周接收80个单位的E需要的才能为:80*0.25+0.96=20.96小时 5工作中心10 工作中心10从工艺道路可以看出,工作中心10与物料E与F有关 根据2批次的C物料可以算出各周期内工作中心15的才能需求如下: 138 264 第一批次138个单位的E需要的才能为:138*0.12+0.85=17.41小时 第二批次264个单位的E需要的才能为:264*0.12+0.85=32.53小时 根据5批次的C物料可以算出各周期内工作中心15的才能需求如下: 60 60 60 60 60 第一批次60个单位的F需要的才能为:60*0.11+0.85=7.45小时 第
26、二批次60个单位的F需要的才能为:60*0.11+0.85=7.45小时 第三批次60个单位的F需要的才能为:60*0.11+0.85=7.45小时 第四批次60个单位的F需要的才能为:60*0.11+0.85=7.45小时 第五批次60个单位的F需要的才能为:60*0.11+0.85=7.45小时 2、计算每个工作中心的可用才能 力1?8?0.95?0.957.22小时/天 各个工作中心的可用能3、计算每个工作中心对各个负荷的加工天数必要时取整 1工作中心30 第一批次24个单位的A需要的才能为:24*0.1+0.4=2.8小时1天 第二批次25个单位的A需要的才能为:25*0.1+0.4=
27、2.9小时1天 第三批次29个单位的A需要的才能为:29*0.1+0.4=3.3小时1天 第四批次29个单位的A需要的才能为:29*0.1+0.4=3.3小时1天 第五批次30个单位的A需要的才能为:30*0.1+0.4=3.4小时1天 第六批次31个单位的A需要的才能为:31*0.1+0.4=3.5小时1天 第七批次31个单位的A需要的才能为:31*0.1+0.4=3.5小时1天 第八批次32个单位的A需要的才能为:32*0.1+0.4=3.6小时1天 第九批次32个单位的A需要的才能为:32*0.1+0.4=3.6小时1天 第十批次33个单位的A需要的才能为: 33*0.1+0.4=3.7
28、小时1天 第十一批次33个单位的A需要的才能为:33*0.1+0.4=3.7小时1天 第十二批次34个单位的A需要的才能为:34*0.1+0.4=3.8小时1天 2工作中心25 第一批次55个单位的B需要的才能为:55*0.06+0.28=3.58小时1天 第二批次61个单位的B需要的才能为:61*0.06+0.28=3.94小时1天 第三批次63个单位的B需要的才能为:63*0.06+0.28=4.06小时1天 第四批次65个单位的B需要的才能为:65*0.06+0.28=4.18小时1天 第五批次67个单位的B需要的才能为:67*0.06+0.28=4.3小时1天 3工作中心20 第一批次
29、109个单位的C需要的才能为:109*0.07+1.1=8.73小时1天 第二批次122个单位的C需要的才能为:122*0.07+1.1=9.64小时1天 第三批次126个单位的C需要的才能为:126*0.07+1.18=9.92小时1天 第四批次130个单位的C需要的才能为:130*0.07+1.1=10.2小时1天 第五批次134个单位的C需要的才能为:134*0.07+1.1=10.48小时1天 4工作中心15 第一批次109个单位的C需要的才能为:109*0.15+1.6=17.95小时2天 第二批次122个单位的C需要的才能为:122*0.15+1.6=19.9小时2天 第三批次12
30、6个单位的C需要的才能为:126*0.15+1.6=20.5小时3天 第四批次130个单位的C需要的才能为:130*0.15+1.6=21.1小时3天 第五批次134个单位的C需要的才能为:134*0.15+1.6=21.7小时3天 第一批次138个单位的E需要的才能为:138*0.25+0.96=35.46小时5天 第二批次264个单位的E需要的才能为:264*0.25+0.96=66.96小时9天 第二周接收80个单位的E需要的才能为:80*0.25+0.96=20.96小时3天 5工作中心10 第一批次138个单位的E需要的才能为:138*0.12+0.85=17.41小时2天 第二批次
31、264个单位的E需要的才能为:264*0.12+0.85=32.53小时9天 第一批次60个单位的F需要的才能为:60*0.11+0.85=7.45小时1天 第二批次60个单位的F需要的才能为:60*0.11+0.85=7.45小时1天 第三批次60个单位的F需要的才能为:60*0.11+0.85=7.45小时1天 第四批次60个单位的F需要的才能为:60*0.11+0.85=7.45小时1天 第五批次60个单位的F需要的才能为:60*0.11+0.85=7.45小时1天 4、用倒排序法计算每道工序的开工日期和完工日期 1每种零件各批次所对应的工序开完工时间 1零件A ? 第一批次24(图名、
32、不能超过页边距、倒退的日期超过MRP的日期 第一批24单位A的加工过程5-6工序30最晚开场时间5-6 - 5-9运输并等待5-9工序10开场5-9 - 5-10工序30消费5-10 - 5-11运输到库房5-65-75-85-95-105-115-11 - 5-13放假休息5-125-13 ? 第二批次25 第二批25单位A的加工过程5-13工序30最晚开场时间5-13 - 5-16运输并等待5-16 - 5-17工序30消费5-17 - 5-18运输到库房5-135-135-135-135-135-135-18 - 5-20放假休息5-135-13 ? 第三批次29 第三批29单位A的加工
33、过程5-20工序30最晚开场时间5-20 - 5-23运输并等待5-23 - 5-24工序30消费5-24 - 5-25运输到库房5-205-215-225-235-245-255-25 - 5-27放假休息5-265-27 ? 第四批次29 第四批次29个单位A的加工过程5/27工序30最晚开场时间5/27 - 5/30运输并等待5/30 - 5/31工序30消费5/31 - 6/1运输到库房5/275/285/295/305/316/16/1 - 6/3放假休息6/26/3 ? 第五批次30 第五批次30个单位A的加工过程6/3工序30最晚开场时间6/3 - 6/6运输并等待6/6 - 6
34、/7工序30消费6/7 - 6/8运输到库房6/36/46/56/66/76/86/8 - 6/10放假休息6/96/10 ? 第六批次31 第六批次31个单位A的加工过程6/10工序30最晚开场时间6/10 - 6/13运输并等待6/13 - 6/14工序30消费6/14 - 6/15运输到库房6/106/116/126/136/146/156/15 - 6/17放假休息6/166/17 ? 第七批次31 第七批次31个单位A的加工过程6/17工序30最晚开场时间6/17 - 6/20运输并等待6/20 - 6/21工序30消费6/21 - 6/22运输到库房6/176/186/196/20
35、6/216/226/22 - 6/24放假休息6/236/24 ? 第八批次32 第八批次32个单位A的加工过程6/24工序30最晚开场时间6/24 - 6/27运输并等待6/27 - 6/28工序30消费6/28 - 6/29运输到库房6/246/256/266/276/286/296/29 - 7/1放假休息6/307/1 ? 第九批次32 第九批次32个单位A的加工过程7/1工序30最晚开场时间7/1 - 7/4运输并等待7/4 - 7/5工序30消费7/5 - 7/6运输到库房7/17/27/37/47/57/67/6 - 7/8放假休息7/77/8 ? 第十批次33 第十批次33个单
36、位A的加工过程7/8工序30最晚开场时间7/8 - 7/11运输并等待7/11 - 7/12工序30消费7/12 - 7/13运输到库房7/87/97/107/117/127/137/13 - 7/15放假休息7/147/15 ? 第十一批次33 第十一批次33个单位A的加工过程7/15工序30最晚开场时间7/15 - 7/18运输并等待7/18 - 7/19工序30消费7/19 - 7/20运输到库房7/157/167/177/187/197/207/20 - 7/22放假休息7/217/22 ? 第十二批次32 第十二批次32个单位A的加工过程7/22工序30最晚开场时间7/22 - 7/
37、25运输并等待7/25 - 7/26工序30消费7/26 - 7/27运输到库房7/227/237/247/257/267/277/27 - 7/29放假休息7/287/29 2零件B ? 第一批次55 第一批次55个单位B的加工过程5/13MRP开场时间5/14工序25最晚开场时间5/14 - 5/16运输到25并等待5/16 - 5/17工序25消费5/17 - 5/18运输到305/13 - 5/14车间调整时间5/135/145/155/165/175/185/18 - 5/20放假休息5/195/20 ? 第二批次61 第二批次61个单位B的加工过程5/28工序25最晚开场时间5/2
38、8 - 5/30运输到25并等待5/30 - 5/31工序25消费5/31 - 6/1运输到305/27 - 5/28车间调整时间5/275/285/295/305/316/16/1 - 6/3放假休息6/26/3 ? 第三批次63 第三批次63个单位B的加工过程6/11工序25最晚开场时间6/11 - 6/13运输到25并等待6/13 - 6/14工序25消费6/14 - 6/15运输到306/10 - 6/11车间调整时间6/106/116/126/136/146/156/15 - 6/17放假休息6/166/17 ? 第三批次65 第五批次65个单位B的加工过程6/25工序25最晚开场时
39、间6/25 - 6/27运输到25并等待6/27 - 6/28工序25消费6/28 - 6/29运输到306/24 - 6/25车间调整时间6/246/256/266/276/286/296/29 - 7/1放假休息6/307/1 ? 第五批次67 第五批次67个单位B的加工过程7/9工序25最晚开场时间7/9 - 7/11运输到25并等待7/11 - 7/12工序25消费7/12 - 7/13运输到307/8 - 7/9车间调整时间7/87/97/107/117/127/137/13 - 7/15放假休息7/147/15 3零件C ? 第一批次109 第一批次109个单位的C加工过程5-6M
40、RP的开场时间5-8工序15开场最晚开场时间5-8 - 5-10运输并等待5-6 - 5-8消费调整时间5-75-85-10 - 5-14工序15消费5-11 - 5-13放假休息5-125-14工序20开场5-17 - 5-185-14 - 5-165-16 - 5-17运输到运输到20并等待工序20消费工作中心305-18 - 5-20放假休息5-195-65-95-105-115-135-145-155-165-175-185-20 ? 第二批次122 第二批次122个单位的C加工过程5-20MRP的开场时间5-22工序15开场时间 5-22 - 5-24运输并等待5-24 - 5-28
41、工序15消费5-28工序20进展消费5-30 - 5-315-31 - 6-15-28 - 5-30在工作运输到运输到20并等待中心20消费工作中心305-205-20 - 5-22消费调整时间5-215-225-235-245-255-25 - 5-27放假休息5-265-275-285-295-305-316-16-1 - 6-3放假休息6-26-3 ? 第三批次126 第三批次126个单位C的加工过程6-4工序15最晚开场时间6-4 - 6-6运输到15并等待6-11工序20开场6-6 - 6-11工序15消费6-11 - 6-13运输并等待6-13 - 6-146-14 - 6-15工
42、序20 消费运输到306-3 - 6-4车间调整时间6-46-36-56-66-76-86-8 - 6-10放假休息6-96-106-116-126-136-146-156-15 - 6-17放假休息6-166-17 ? 第四批次130 第四批次130个单位C的加工过程6-18里程碑说明6-18 - 6-20运输到15并等待6-20 - 6-25工序15消费6-25工序20开场6-25 - 6-27运输并等待6-27 - 6-28工序20消费6-28 - 6-29运输到306-17 - 6-18间隔说明6-186-176-196-206-216-226-22 - 6-24放假休息6-236-2
43、46-256-266-276-286-296-29 - 7-1放假休息6-307-1 ? 第五批次134 7-2工序15最晚开场时间第五批次134个单位C的加工过程7-9工序20开场7-9 - 7-11运输并等待7-11 - 7-12工序20消费7-12 - 7-13运输到307-2 - 7-4运输到15并等待7-4 - 7-9工序15消费7-1 - 7-2车间调整时间7-27-17-37-47-57-67-6 - 7-8放假休息7-77-87-97-107-117-127-137-13 - 7-15放假休息7-147-15 4零件E ? 第二周接收的80个单位的E 5/6MRP开场时间第二周
44、接收到的80个单位E的加工过程5/6工序15最晚开场时间5/6 - 5/8运输到15并等待5/8 - 5/11工序15消费5/65/75/85/95/105/115/11 - 5/13放假休息5/125/13第一批次138 第一批次138个单位E的加工过程5/9工序10最晚开场时间5/9 - 5/11运输到10并等待5/15工序15消费5/13 - 5/155/15 - 5/17工序10消费运输到15并等待5/6MRP开场时间5/17 - 5/24工序15消费5/24 - 5/25运输到255/25 - 5/27放假休息5/255/265/275/65/6 - 5/9车间调整时间5/75/85
45、/95/105/11 - 5/13放假休息5/115/125/135/145/155/165/175/18 - 5/20放假休息5/185/195/205/215/225/235/24 ? 第二批次264 第二批次264个单位E的加工过程5/28工序10最晚开场时间5/28 - 5/30运输到10并等待6/6工序15开场5/30 - 6/6工序10消费6/6 - 6/8运输到15并等待6/10 - 6/21工序15消费6/21 - 6/22运输到255/27 - 5/286/1 - 6/3车间调整放假休息5/285/295/305/316/16/26/35/276/46/56/66/76/8
46、- 6/106/15 - 6/176/22 - 6/24放假休息放假休息放假休息6/86/96/106/116/126/136/146/156/166/176/186/196/206/216/226/236/24 5零件F ? 第一批次60 第一批次60个单位F的加工过程5/6MRP开场时间5/7工序10最晚开工时间5/7 - 5/9运输到10并等待5/9 - 5/10工序10消费5/10 - 5/11运输到255/6 - 5/7车间调整时间5/65/75/85/95/105/115/11 - 5/13放假休息5/125/13 ? 第二批次60 第二批次60个单位F的加工过程5/215/21
47、- 5/23工序10最晚开场时间运输到工作中心10并等待5/23 - 5/24工序10消费5/24 - 5/25运输到工作中心255/20 - 5/21消费开场时间5/205/215/225/235/245/255/25 - 5/27放假休息5/265/27 ? 第三批次 第三批次60个单位F的加工过程6/4工序10最晚开场时间6/4 - 6/6运输到10并等待6/6 - 6/7工序10消费6/7 - 6/8运输到256/3 - 6/4车间调整时间6/36/46/56/66/76/86/8 - 6/10放假休息6/96/10 ? 第四批次 第四批次60个单位F的加工过程6/18工序10最晚开场时间6/18 - 6/20运输到10并等待6/20 - 6/21工序10消费6/21 - 6/22运输到256/17 - 6/18车间调整时间6/176/186/196/206/216/226/22 - 6/24放假休息6/236/24 第 27 页 共 27 页
- 温馨提示:
1: 本站所有资源如无特殊说明,都需要本地电脑安装OFFICE2007和PDF阅读器。图纸软件为CAD,CAXA,PROE,UG,SolidWorks等.压缩文件请下载最新的WinRAR软件解压。
2: 本站的文档不包含任何第三方提供的附件图纸等,如果需要附件,请联系上传者。文件的所有权益归上传用户所有。
3.本站RAR压缩包中若带图纸,网页内容里面会有图纸预览,若没有图纸预览就没有图纸。
4. 未经权益所有人同意不得将文件中的内容挪作商业或盈利用途。
5. 装配图网仅提供信息存储空间,仅对用户上传内容的表现方式做保护处理,对用户上传分享的文档内容本身不做任何修改或编辑,并不能对任何下载内容负责。
6. 下载文件中如有侵权或不适当内容,请与我们联系,我们立即纠正。
7. 本站不保证下载资源的准确性、安全性和完整性, 同时也不承担用户因使用这些下载资源对自己和他人造成任何形式的伤害或损失。