“偏心套”的加工工艺
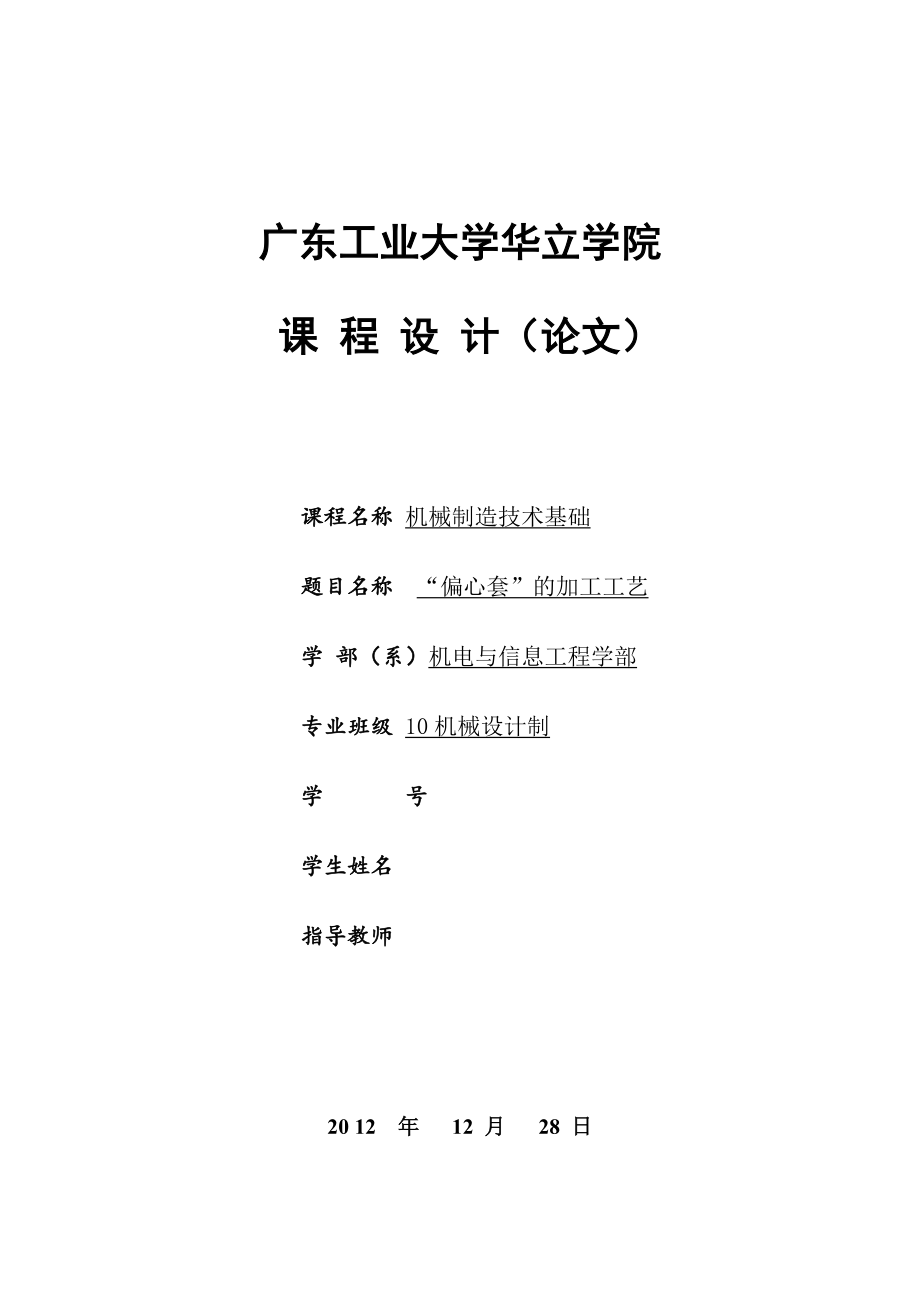


《“偏心套”的加工工艺》由会员分享,可在线阅读,更多相关《“偏心套”的加工工艺(13页珍藏版)》请在装配图网上搜索。
1、 广东工业大学华立学院 课 程 设 计(论文) 课程名称 机械制造技术基础 题目名称 “偏心套”的加工工艺 学 部(系)机电与信息工程学部 专业班级 10机械设计制 学 号 学生姓名 指导教师 20 12 年 12 月 28 日 课程设计说明书 题目:“偏心套”的加工工艺 序言 机械工业是一种基本工业形式,对于我们国家来说,他关系到国计民生的方方面面。近年来机械工业领域向着高精度,高质量,高效率,低成本方发展,数字换,自动化水平日益提高,同时由于机械行业的发展,其他各工业部门也向着高深度迈进,机械工业的
2、发展日趋重要。 机械制造过程及检测,检验中,都要用到大量的夹具。为了到到提高劳动效率,提高加工精度,减少废品,扩大机床的工艺范围,改善操作的劳动条件,如何设计好夹具成了机械制造的一项重要任务。 机床夹具是夹具中的一种,将其固定到机床上,可以可以使被加工工件对刀具与机床保持正确的相对位置,并克服切削力的影响,使加工顺利进行,机床夹具分为通用夹具和专用夹具两种。 一、 零件的分析 (一) 零件的作用 (二) 零件的工艺分析 偏心套是一偏心回转体零件,有两组组加工表面,这两组分别是Φ120外圆 ,,包括:两个Φmm外圆及端面, Φ100的外圆面,尺寸为Φmm的内圆柱面。
3、 这两组加工表面是位置度和自身的平面度和圆柱度都有很高的精度要求 ,可以先加工它的一端外圆,再借助专用夹具以这个外圆为定位基准加工另一端面,然后再加工其它加工表面. ㈠ 零件的工艺分析 1.1零件的功用﹑结构及特点 ⑴ 该零件以其内孔和轴配合,并通过键进行连接。偏心套主要其支撑和导向的作用,在工作中承受一定的载荷,因此要求其有一定的强度和耐磨性。 ⑵ 该零件硬度较高,采用GCr15轴承刚材料,在进行热处理时,在淬火和回火之间,增加一冰冷处理,这样可以更好地保证工件尺寸的稳定性,减小变形。 ⑶ 为了保证工件偏心的精度,可以采用以下加工方法: 当加工精度高,加
4、工数量大时一般采用专用工装夹具装夹工件进行加工。因该工件的两处偏心完全一样,因此,在加工时可以用同一种方法,分别两次装夹即可。 ⑷ 在加工偏心工件时,由于旋转离心作用,会影响零件的圆度,圆柱度等公差,会造成零件壁厚不均匀等,因此,在加工时,除注意保证夹具体平衡外,还应注意合理选择切削用量及有效的冷却润滑。 ⑸ 当零件上键槽精度要求不高或零星加工时,可以采用插削方法加工键槽。若键槽精度要求较高,零件数量又多时,应采用拉削的方法加工键槽。 ⑹ 偏心距误差的检查方法。首先将偏心套装在1:3000小锥度心轴上。心轴两端备有高精度的中心孔,将心轴装夹在偏摆仪两顶尖之间,将百分表触头顶在
5、φ120外圆上,转动心轴,百分表最大与最小读数之差,即为偏心距。 ⑺φ120偏心圆中心线对中心孔的轴线平行度误差检查法。同样将偏心套装在1:3000小锥度心轴上,然后将小锥度心轴放在标准V型块上,先用百分表找出偏心套外圆最高点,然后在相距30mm处,测出两最高点值,其两点误差为两轴线平行度值。 ⑻圆柱度的检测方法。将偏心套装在1:3000的小锥度心轴上,再将心轴装夹在偏摆仪两顶尖之间,将百分表触头顶在φ120mm外圆上,转动心轴,测三个横截面,其百分表最大读数与最小读数之差,即为圆柱度误差。 1.2主要加工表面及其要求 ⑴ 内孔 孔径为Φ60的孔是轴的安装孔,表面粗糙度为
6、Ra=0.8um。倒角为C1,公差等级为IT7~8,孔中心线与两外圆的偏心距均为8±0.05mm。圆柱度要求为0.01mm。 ⑵ 外圆表面尺寸为Φ120mm,公差等级为IT7~8,外圆表面素线以孔为基准,平行度要求为0.01mm,外圆表面圆柱度要求为0.01mm,粗糙度为Ra=0.8um,个外圆表面长度为40mm。 ⑶ 端面 偏心套端面长度为90mm,中间侧壁到端面距离为40mm,外端面粗糙度Ra=6.3um,中间侧壁粗糙度Ra=1.6um。 ⑷ 磨削槽 槽宽由图中给定的尺寸求得为10mm,深为2mm倒圆角R3,由圆中的尺寸要求和其功用可知其不是重要的配合面. ⑸
7、键槽 键槽深度由图中尺寸可得为4.5mm。 为保证整体零件的耐磨性和热处理的硬度达到58~64HRC。要求淬火后回火,未注粗糙度为Ra=6.3um。 ㈡ 毛坯的选择 2.1 确定毛坯的类型,制造方法和尺寸度及其公差 ①该零件的材料为 GCr15,设计要求生产类型为成批生产,形状简单,该零件因其一般只用于轻载,冲击小或无冲击的场合。为提高生产效率,选用金属模 砂型机器铸造。 ②选择零件的一端面作为分型面铸造出带孔的圆棒料。 ③由零件图技术要求知该零件精度要求较高,毛坯为精密的铸件,铸件尺寸公差 为 CT9 加工余量等级按 CT9-MA-H/G 级。各表面单边余量
8、3.0mm。 2.2 确定毛坯技术要求 ①铸件不应有裂纹、砂眼、和局部缩松、气孔及夹渣等缺陷,铸件表面应清除毛 刺同、结瘤和粘砂等。 ②球化退火处理硬度为 207~229HBW,以降低硬度,改善切削加工性,并为淬火作 好组织上的准备,材料为 GCr15。 ③未注倒角 0.5 45 ,其余粗糙度 Ra=6.3um。 ④外表面斜度为 30’,内表面起模斜度为 1 2.2 确定毛坯简图。 确定毛坯尺寸公差与机械加工余量 下料 棒料φ120mm×165mm 锻造 锻造尺寸φ155mm×φ45mm×104mm ㈢ 基准的选择 由零件图中的技术要求可知该零件的尺寸较多是以内
9、孔中心线为设计基准,且图中外圆表面 尺寸精度要求较内孔高,外圆表面素线平行度以内孔轴线为基准,根据粗精基准选择原则和基准重合统一原则,确定各表面的基准如下表所示: 序号 加工部位 基准选择 1 孔及其端面 偏心套外圆轮廓及端面(粗基准) 2 外圆轮廓 内孔中心线 3 磨削槽和倒角 内孔中心线 4 键糟 内孔中心线 ㈣ 拟定机械加工路线 ⑴确定各表面的加工方法 根据各加工表面的加工精度和表面粗糙度要求,选定如下加工方法: 孔的端面加工为车削; 孔的加工为车削—磨削; 外圆加工为车削—磨削;磨削槽的加工为
10、车削。侧壁加工为车削;键槽加工为拉削。 具体加工方法如下: ①偏心套端面:未标注公差要求,表面粗糙度为Ra=6.3um,查表知需进行粗车—精车。 ②侧壁未标准公差要求,表面粗糙度为Ra=1.6um,查表知需进行粗车—半精车—精车。 ③ 孔:表面表面粗糙度Ra=0.8um;查表得公差等级为IT7~8,查表知需进行粗车—半精车—精车。 ④外圆表面公差等级为IT7~8,粗糙度Ra=0.8um,查表知需进行粗车—半精车—精车。 ⑤磨削槽列尺寸要求和公差要求,不是重要表面,只需粗车即可。 ⑥键槽宽度要求为20。 ⑵拟定加工路线 加工方案如下: 工序号
11、 内容 设备 10 粗车端面、外圆 卧式车床 20 粗车内孔 卧式车床 30 淬火、回火 40 半精车端面、精车侧壁 卧式车床 50 车磨削槽 卧式车床 60 磨内孔 外圆磨床 70 磨外圆 80 内孔倒角 内孔磨床 90 插削键槽 拉床 90 清洗,去毛刺 100 检验 ⑶ 工艺分析 此工艺按工艺集中原则组织工序,许多工序可在同一机床上完成,减少了工件的装夹次数,易于保证加工面的质量,需要的车床少,减少了工件在工序间的运输,减少辅助时间和准备时间。 ㈤ 确定机械加工余量、工序尺寸及公差 加工余
12、量可采用查表修正确定。确定工序尺寸一般方法是:由加工表面的最后工序往前推算,最后工序的工序尺寸按零件图样的要求标注,当无其它基准交换时,同一基准面多次加工的工序尺寸只与工序(工步)的加工余量有关,当基准不重合时工序尺寸用工艺尺寸链计算,中间工序尺寸按“向、入体“原则标注,但毛坯和孔心距尺寸公差带一般取双向对称布置、中间工序尺寸的公差可从相应的加工经济精度表中查得。 偏心套零件第一道工序各工步开基准交换,其余挌表面均基准重合、统一原则,故只需查得各加工余量,便可确定工序尺寸。 根据上述资料和加工工艺,查各种表面加工余量表分别确定各加工表面的加工余量、工序尺寸及公差如下表: 工序号 工序内
13、容 单边余量 工序尺寸 Ra 10 ① 粗车端面 2.0 12.5 ② 粗车内孔 2.5 12.5 20 粗车外圆 2.1 12.5 40 ① 精车端面 0.5 90 6.3 ② 精车侧壁 0.5 40 1.6 50 车磨削槽 2 60 ①内内孔 0.5 0.8 70 ②磨外圆 0.5 0.8 80 内孔倒角 1 C1 90 插削键槽 4.5 ㈥ 机床的选择及工艺装备 ⑴ 机床的选择 ①工序10、20、40、50、80 由于有些工序包
14、括多个工步,该零件形状较规则,为减少装卸刀具次数和时间,保证工件质量,选用CA6140型卧式车床比较合适。 ②工序60、70 磨内孔和外圆:根据工件的尺寸选用M2110内圆磨床和M1432外圆磨床。 ③工序90 插削键槽根据尺寸和技术要求选用L6100拉床。 ⑵刀具选择 该零件特形表面,成批生产,一般采用通用或标准刀具,卧式车床上粗车端面用P10端面车刀,磨内孔和外圆选用白刚玉平形砂轮。 ⑶ 选择夹具 该零件加工工序10采用三爪卡盘,其余工序需用专用偏心夹具。 ⑷ 量具的选择 该零件属批量生产,一般采用通用量具。 ① 外圆和内孔加工量具 外圆表面 公差值T=0.23mm
15、,查表得计量器具不确定度允许值为 =.00018,查表得,所选用的计量器具达不到GB 3177—1997规定的 。则重新计算安全裕度A’, A’= =0.002 由于偏心套最大实体尺寸:120.043mm 其最小实体尺寸:120.0250mm 则基验收极限尺寸: 由分析得应选用150~200mm外径千分尺和150~200mm内径千分尺较合理。 ② 端面和键槽加工量具 选用0~200mm/0.02mm游标卡尺,由于大批量生产最后加工验收时为节约时间,提高效率应选用极限量规,孔量规选用锥柄圆柱塞规。 机床设备和工艺装备选择 工序号 工序内容 机床设备和工艺装备 10 ①
16、 粗车端面 CA6140 卧式车床、p10 端面车刀、0~ 200mm/0.02mm 游标卡尺 ② 粗车内孔 标准 p10 内孔车刀、三爪卡盘、150~ 200mm 内径千分尺 20 粗车外圆 CA6140 卧式车床、p10 端面车刀、150~200mm 外径千分尺、专用偏心夹具 40 ①半精车端面 CA6140 卧式车床、p10 端面车刀、0~ 200mm/0.02mm 游标卡尺、专用偏心夹具 ②精车侧壁 50 磨削槽 CA6140 卧式车床、p10 车槽车刀、游 标卡尺、专用偏心夹具 60 ①磨内孔 M2120 内孔磨床,白刚玉平形砂轮、 塞规,专用夹具
17、 70 ②磨外圆 M1331 外圆磨床,白刚玉平形砂轮, 150~200mm 外径千分尺、专用偏心夹具 80 内孔倒角 CA6140 卧式车床、p10 倒角车刀、 专用偏心夹具 90 拉削键槽 L6110 拉床,标准键槽拉刀,专用偏心夹具,0~200mm/0.02mm 游标卡尺 ⑸ 偏心套机械加工工艺过程卡 工序号 工序名称 工序内容 工艺装备 1 下料 棒料φ120mm×165mm 锯床 2 锻造 锻造尺寸φ155mm×φ45mm×104mm 3 热处理 正火 4 粗车 夹毛坯外圆,粗车内孔至尺寸φ55±0.05mm,粗车端面,见
18、平即可。车外圆至φ145mm,长45mm。 CA6140 5 粗车 调头装夹,粗车外圆至φ145mm,与上工序接刀,车端面,保证总长度95mm。在距端面46mm外车Φ100 0-0.05mm至φ102mm,槽宽6mm使槽靠外的端面距离外端面为43mm CA6140 6 精车 掉头,三抓自定心卡盘夹工件外圆,找正,车内孔至尺寸φ59 0-0.05mm,精车另一端面,保证总长92mm,并作标记,精车φ100+0.50mm圆及两内侧端面,使槽宽为8mm,保证槽靠外的端面距离外端面42mm。 CA6140 7 钳 划键槽线 8 插 以有标记的端面及外圆定位,接线找正,
19、插键槽,保证尺寸20±0.02mm及64.5+0.250mm至尺寸64+0.150mm B5020 9 钳 修锉键槽毛刺 10 精车 以φ59 0-0.05mm内孔及键槽定位,用专用偏心夹具装夹工件,车偏心φ120+0.043+0.02mm至φ121.5mm长42mm CA6140 专用工装 11 精车 以φ59 0-0.05mm内孔及键槽定位,用专用偏心夹具装夹工件,车另一端φ120+0.043+0.02mm至φ121.5mm长42-0.5-0.3mm CA6140 专用工装 12 热处理 淬火58~64HRC 13 热处理 冰冷处理 1
20、4 热处理 回火 15 磨 用专用偏心工装装夹工件φ121.5mm外圆处,按Φ59 0-0.05mm内孔找正,磨内孔至图样尺寸φ60+00.043mm M2110A 专用工装 16 钳 修锉键槽中氧化皮 17 磨 以φ60+00.043mm内孔、键槽及另一定位装夹工件。磨φ120+0.043+0.02mm至图样尺寸,并靠磨此端外端面,保证偏心盘的厚度40mm为41mm,并保证总长度91mm M1432A 专用工装 18 磨 掉头,以φ60+00.043mm内孔、键槽及另一定位装夹工件。磨另一端φ120+0.043+0.02mm至图样尺寸,并靠磨右端面
21、,保证总长90mm M1432A 专用工装 19 磨 以φ60+00.043mm内孔、键槽及另一端面定位装夹工件。靠磨φ100 0-0.05mm至图样尺寸,并靠磨两侧面保证尺寸40mm M1432A 专用工装 20 检验 按图样要求检查各尺寸和精度 21 入库 入库 ㈦ 确定切削用量及基本工时 粗车端面和内孔 ⑴ 粗车偏心套端面 步骤如下是: ①确定背吃刀量 :端面单边总余量3mm,一次走刀加工 ap=2.0mm。 ②确定进给量f:根据表查得f=0.6~0.9mm/r;根据机床的横向进给量,取f=0.8mm/r。 ③确定切削速度:V=(1-m×T
22、m×apxv×fyv)×Kv Kv=KMv ×Ktv×Kkrv×Ksv×KTv×KKv 其中Ktv=1.0.Kkrv=0.81,KSV=0.8,KTv=1.0,KKv=1.24, KMv=0.637/σb=0.637/0.735=0.87 根据 表查得 Cv=235,xv=0.15,yv=0.35,m=0.20,刀具寿命选T=60min, 故 v=72.2m/min ④确定机床主轴转速n: ns=1000v/πdw=1000×72.2/(3.14×45)=5.38r/s(323r/min) 根据表查得相近较小的机床转速为n=160r/min,所以实际切削速度V=nW×dw×π/
23、1000 =370×96×3.14/1000=111.53r/min(1.86r/s) ⑥辅助时间 :查表得,装夹工件时间为0.8min,启动机床为0.02min ⑤计算基本时间 :端面车刀选用主偏角 背吃刀量 查表得 取 批量生产,启动切削液的时间为0.05min,共计T =1.37min。 ⑵粗车 内孔 ①确定背吃到量 :总加工余量为3.0mm,一次走刀加工,ap =2.5mm。 ②确定进给量f:根据表5-102查得f=0.6~0.9mm/r;根据机床的纵向进给量,取f=0.81mm/r。 ③确定切削速度 :V=(1-m×Tm×apxv×fyv)×Kv Kv=KMv ×Ktv
24、×Kkrv×Ksv×KTv×KKv 其中Ktv=1.0,Kkrv=0.81,KSV=0.8,KTv=1.0,KKv=1.24, KMv=0.637/σb=0.637/0.735=0.87 根据表查得Cv =235,m=0.20, xv=0.15,yv=0.45,刀具寿命T=60min, 故v =55.98m/min ④确定机床主轴转速n:ns=1000v/πdw =1000×1.623/(3.14×45)=5.38r/s(323r/min) 根据表查得相近较小的机床转速为n=320r/min,所以实际切削速度 V=nW×dw×π/1000 =370×96×3.14/1000=111
25、.53r/min=54.26m/min ⑤计算基本时间 :切削加工长度L=91mm,内孔车刀选用主偏角Kr =75 , 背吃刀量 ap ==2.5mm,查表得 ,取 =3mm, =(3~5)mm, =(3~5)mm =0.39min ⑥辅助时间 :查表得,换刀时间为0.5min,切削液的开启时间为0.05min,测量尺寸时间为0.5min,共计 =1.05min。 ⑶ 精车端面 ①确定背吃刀量 ,端面单边剩余余量为1mm,二次走刀加工, ap =1.0mm。 ②确定进给量f:根据表查得f=0.6~0.9mm,查表5-5得f=0.61mm/r。 ③确定切削速度 : V=(1-m
26、×Tm×apxv×fyv)×Kv 式中Cv=242,xv=0.15,yv=0.35,m=0.20 Kv=KMv ×Ktv×Kkrv×Ksv×KTv×KKv 其中Ktv=1.0,Kkrv=0.81,KSV=0.8,KTv=1.0,KKv=1.24,KMv=0.637/σb KKv=0.637/0.735=0.87 所以v =77.47m/min ④机床主轴转速n:ns=1000v/πdw =1000×1.623/(3.14×45)=5.38r/s(323r/min) 根据表查得相近较小的机床转速为n=250r/min,所以实际切削速度 V=nW×dw×π/1000 =370×96×
27、3.14/1000=111.53r/min(1.86r/s)=71.44m/min. ⑤计算基本时间 :切削长度L=91/2=45.5mm,端面车刀选用 Kr=90 ,背吃刀量 ap =1mm,查表取 =3mm; =(3~5)mm;批量生产 =(45.5+3+4+0)mm=52.5mm ⑥辅助时间 :查表得,开启和关闭切削液时间为0.05min,换刀时间为0.5min,取量具并测量尺寸时间为0.5min,共计时间 =1.05min. ⑷ 精车侧壁 ①确定背吃刀量 :侧壁加工余量为0.5mm,一次走刀加工完成, ap =0.5mm. ② 确定进给量f:根据表查得f=0.6~0.9m
28、m/r,取f=0.5mm. ③确定切削速度V=(1-m×Tm×apxv×fyv)×Kv,式中Cv=242,xv=0.15,yv=0.35,m=0.20, KKv=KMv ×Ktv×Kkrv×Ksv×KTv×KKv 其中Ktv=1.0,Kkrv=0.81,KSV=0.8,KTv=1.0,KKv=1.0,KMv=0.637/σb Kv=0.637/0.735=0.87(表21-1) 刀具寿命选T=60min ∴v=(242/601-0.2×36000.2×0.750.15×0.520.35)×0.87×1.0×0.81 ×0.8×1.0×1.24=1.623m/s ④确定机床主轴转速n:ns=1000v/πdw =1000×1.623/(3.14×45)=5.38r/s(323r/min) 根据表查得相近较小的机床转速为n=250r/min,所以实际切削速度 V=nW×dw×π/1000 =370×96×3.14/1000=111.53r/min(1.86r/s) =94.985 m/min ⑤计算基本时间 :端面车刀选用主偏角 ,背吃量 =0.5mm,查表得 取 =3mm, =(3~5)mm ⑥辅助时间 :查表得,调节切削液的时间为0.05min,取量具并测量 尺寸时间为0.5min,共计 =1.0min.
- 温馨提示:
1: 本站所有资源如无特殊说明,都需要本地电脑安装OFFICE2007和PDF阅读器。图纸软件为CAD,CAXA,PROE,UG,SolidWorks等.压缩文件请下载最新的WinRAR软件解压。
2: 本站的文档不包含任何第三方提供的附件图纸等,如果需要附件,请联系上传者。文件的所有权益归上传用户所有。
3.本站RAR压缩包中若带图纸,网页内容里面会有图纸预览,若没有图纸预览就没有图纸。
4. 未经权益所有人同意不得将文件中的内容挪作商业或盈利用途。
5. 装配图网仅提供信息存储空间,仅对用户上传内容的表现方式做保护处理,对用户上传分享的文档内容本身不做任何修改或编辑,并不能对任何下载内容负责。
6. 下载文件中如有侵权或不适当内容,请与我们联系,我们立即纠正。
7. 本站不保证下载资源的准确性、安全性和完整性, 同时也不承担用户因使用这些下载资源对自己和他人造成任何形式的伤害或损失。