连杆说明书初稿
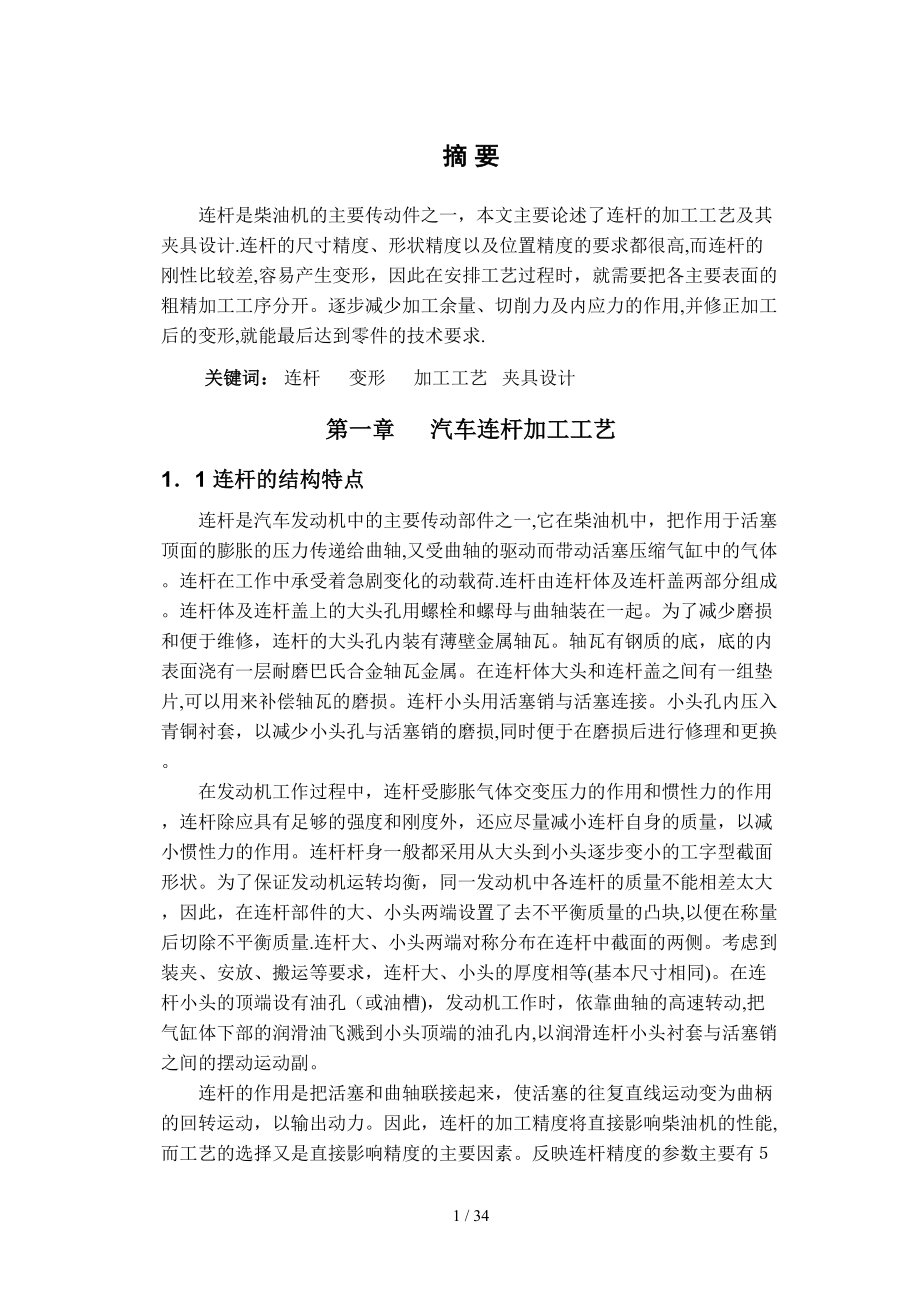


《连杆说明书初稿》由会员分享,可在线阅读,更多相关《连杆说明书初稿(34页珍藏版)》请在装配图网上搜索。
1、摘 要连杆是柴油机的主要传动件之一,本文主要论述了连杆的加工工艺及其夹具设计.连杆的尺寸精度、形状精度以及位置精度的要求都很高,而连杆的刚性比较差,容易产生变形,因此在安排工艺过程时,就需要把各主要表面的粗精加工工序分开。逐步减少加工余量、切削力及内应力的作用,并修正加工后的变形,就能最后达到零件的技术要求.关键词: 连杆 变形 加工工艺 夹具设计第一章 汽车连杆加工工艺11 连杆的结构特点连杆是汽车发动机中的主要传动部件之一,它在柴油机中,把作用于活塞顶面的膨胀的压力传递给曲轴,又受曲轴的驱动而带动活塞压缩气缸中的气体。连杆在工作中承受着急剧变化的动载荷.连杆由连杆体及连杆盖两部分组成。连杆
2、体及连杆盖上的大头孔用螺栓和螺母与曲轴装在一起。为了减少磨损和便于维修,连杆的大头孔内装有薄壁金属轴瓦。轴瓦有钢质的底,底的内表面浇有一层耐磨巴氏合金轴瓦金属。在连杆体大头和连杆盖之间有一组垫片,可以用来补偿轴瓦的磨损。连杆小头用活塞销与活塞连接。小头孔内压入青铜衬套,以减少小头孔与活塞销的磨损,同时便于在磨损后进行修理和更换。在发动机工作过程中,连杆受膨胀气体交变压力的作用和惯性力的作用,连杆除应具有足够的强度和刚度外,还应尽量减小连杆自身的质量,以减小惯性力的作用。连杆杆身一般都采用从大头到小头逐步变小的工字型截面形状。为了保证发动机运转均衡,同一发动机中各连杆的质量不能相差太大,因此,在
3、连杆部件的大、小头两端设置了去不平衡质量的凸块,以便在称量后切除不平衡质量.连杆大、小头两端对称分布在连杆中截面的两侧。考虑到装夹、安放、搬运等要求,连杆大、小头的厚度相等(基本尺寸相同)。在连杆小头的顶端设有油孔(或油槽),发动机工作时,依靠曲轴的高速转动,把气缸体下部的润滑油飞溅到小头顶端的油孔内,以润滑连杆小头衬套与活塞销之间的摆动运动副。连杆的作用是把活塞和曲轴联接起来,使活塞的往复直线运动变为曲柄的回转运动,以输出动力。因此,连杆的加工精度将直接影响柴油机的性能,而工艺的选择又是直接影响精度的主要因素。反映连杆精度的参数主要有个:(1)连杆大端中心面和小端中心面相对连杆杆身中心面的对
4、称度;(2)连杆大、小头孔中心距尺寸精度;()连杆大、小头孔平行度;(4)连杆大、小头孔尺寸精度、形状精度;()连杆大头螺栓孔与接合面的垂直度。1。2 连杆的主要技术要求连杆上需进行机械加工的主要表面为:大、小头孔及其两端面,连杆体与连杆盖的结合面及连杆螺栓定位孔等。连杆总成的主要技术要求(图1-1)如下。连杆总成图(11)121大、小头孔的尺寸精度、形状精度为了使大头孔与轴瓦及曲轴、小头孔与活塞销能密切配合,减少冲击的不良影响和便于传热.大头孔公差等级为T,表面粗糙度Ra应不大于0.4m;大头孔的圆柱度公差为。012 m,小头孔公差等级为I8,表面粗糙度a应不大于3.m。小头压衬套的底孔的圆
5、柱度公差为。05 mm,素线平行度公差为0.4/100 mm。.2。2 大、小头孔轴心线在两个互相垂直方向的平行度两孔轴心线在连杆轴线方向的平行度误差会使活塞在汽缸中倾斜,从而造成汽缸壁磨损不均匀,同时使曲轴的连杆轴颈产生边缘磨损,所以两孔轴心线在连杆轴线方向的平行度公差较小;而两孔轴心线在垂直于连杆轴线方向的平行度误差对不均匀磨损影响较小,因而其公差值较大。两孔轴心线在连杆的轴线方向的平行度在00 mm长度上公差为00 ;在垂直与连杆轴心线方向的平行度在100mm长度上公差为0。06 mm。1.2.3大、小头孔中心距大小头孔的中心距影响到汽缸的压缩比,即影响到发动机的效率,所以规定了比较高的
6、要求:19005 m。.2。4连杆大头孔两端面对大头孔中心线的垂直度连杆大头孔两端面对大头孔中心线的垂直度,影响到轴瓦的安装和磨损,甚至引起烧伤;所以对它也提出了一定的要求:规定其垂直度公差等级应不低于I9(大头孔两端面对大头孔的轴心线的垂直度在100 mm长度上公差为08 mm)。2.5 大、小头孔两端面的技术要求连杆大、小头孔两端面间距离的基本尺寸相同,但从技术要求是不同的,大头两端面的尺寸公差等级为T9,表面粗糙度Ra不大于0.m, 小头两端面的尺寸公差等级为IT12,表面粗糙度Ra不大于。3m。这是因为连杆大头两端面与曲轴连杆轴颈两轴肩端面间有配合要求,而连杆小头两端面与活塞销孔座内档
7、之间没有配合要求。连杆大头端面间距离尺寸的公差带正好落在连杆小头端面间距离尺寸的公差带中,这给连杆的加工带来许多方便。1。2.6螺栓孔的技术要求在前面已经说过,连杆在工作过程中受到急剧的动载荷的作用。这一动载荷又传递到连杆体和连杆盖的两个螺栓及螺母上。因此除了对螺栓及螺母要提出高的技术要求外,对于安装这两个动力螺栓孔及端面也提出了一定的要求。规定:螺栓孔按T8级公差等级和表面粗糙度Ra应不大于6.3m加工;两螺栓孔在大头孔剖分面的对称度公差为0.25 m。1.2.7 有关结合面的技术要求在连杆受动载荷时,接合面的歪斜使连杆盖及连杆体沿着剖分面产生相对错位,影响到曲轴的连杆轴颈和轴瓦结合不良,从
8、而产生不均匀磨损。结合面的平行度将影响到连杆体、连杆盖和垫片贴合的紧密程度,因而也影响到螺栓的受力情况和曲轴、轴瓦的磨损。对于本连杆,要求结合面的平面度的公差为0。05 m.1。3 连杆的毛坯选择连杆在工作中承受多向交变载荷的作用,要求具有很高的强度。因此,连杆材料一般采用高强度碳钢和合金钢;如45钢、55钢、0Cr、40CMn等。这里选用5钢.近年来也有采用球墨铸铁的,粉末冶金零件的尺寸精度高,材料损耗少,成本低.随着粉末冶金锻造工艺的出现和应用,使粉末冶金件的密度和强度大为提高.因此,采用粉末冶金的办法制造连杆也是一个很有发展前途的制造方法。连杆毛坯制造方法的选择,主要根据生产类型、材料的
9、工艺性(可塑性,可锻性)及零件对材料的组织性能要求,零件的形状及其外形尺寸,毛坯车间现有生产条件及采用先进的毛坯制造方法的可能性来确定毛坯的制造方法。根据生产纲领生产纲领=20万件/年,属于大批量生产。连杆选用模锻制造毛坯。连杆模锻形式有两种,一种是体和盖分开锻造,另一种是将体和盖锻成-体.这里采用整体锻造。整体锻造的毛坯,需要在以后的机械加工过程中将其切开,为保证切开后粗镗孔余量的均匀,最好将整体连杆大头孔锻成椭圆形.相对于分体锻造而言,整体锻造存在所需锻造设备动力大和金属纤维被切断等问题,但由于整体锻造的连杆毛坯具有材料损耗少、锻造工时少、模具少等优点,故用得越来越多,成为连杆毛坯的一种主
10、要形式。总之,毛坯的种类和制造方法的选择应使零件总的生产成本降低,性能提高。连杆必须经过外观缺陷、内部探伤、毛坯尺寸及质量等的全面检查,方能进入机械加工生产线.1.4连杆的机械加工工艺过程分析1。41 工艺过程的安排在连杆加工中有两个主要因素影响加工精度:(1)连杆本身的刚度比较低,在外力(切削力、夹紧力)的作用下容易变形。(2)连杆是模锻件,孔的加工余量大,切削时将产生较大的残余内应力,并引起内应力重新分布。因此,在安排工艺进程时,就要把各主要表面的粗、精加工工序分开,即把粗加工安排在前,半精加工安排在中间,精加工安排在后面。这是由于粗加工工序的切削余量大,因此切削力、夹紧力必然大,加工后容
11、易产生变形。粗、精加工分开后,粗加工产生的变形可以在半精加工中修正;半精加工中产生的变形可以在精加工中修正。这样逐步减少加工余量,切削力及内应力的作用,逐步修正加工后的变形,就能最后达到零件的技术条件。各主要表面的工序安排如下:(1)两端面:粗铣、精铣、粗磨、精磨(2)小头孔:钻孔、扩孔、铰孔、精镗、压入衬套后再精镗(3)大头孔:扩孔、粗镗、半精镗、精镗、金刚镗、珩磨一些次要表面的加工,则视需要和可能安排在工艺过程的中间或后面。.4。2 定位基准的选择在连杆机械加工工艺过程中,大部分工序选用连杆的一个指定的端面和小头孔作为主要基面,并用大头处指定一侧的外表面作为另一基面。这是由于:端面的面积大
12、,定位比较稳定,用小头孔定位可直接控制大、小头孔的中心距。这样就使各工序中的定位基准统一起来,减少了定位误差。具体的办法是,如图(15)所示:在安装工件时,注意将成套编号标记的一面不图(5)连杆的定位方向与夹具的定位元件接触(在设计夹具时亦作相应的考虑)。在精镗小头孔(及精镗小头衬套孔)时,也用小头孔(及衬套孔)作为基面,这时将定位销做成活动的称“假销”.当连杆用小头孔(及衬套孔)定位夹紧后,再从小头孔中抽出假销进行加工.为了不断改善基面的精度,基面的加工与主要表面的加工要适当配合:即在粗加工大、小头孔前,粗磨端面,在精镗大、小头孔前,精磨端面。由于用小头孔和大头孔外侧面作基面,所以这些表面的
13、加工安排得比较早。在小头孔作为定位基面前的加工工序是钻孔、扩孔和铰孔,这些工序对于铰后的孔与端面的垂直度不易保证,有时会影响到后续工序的加工精度。在第一道工序中,工件的各个表面都是毛坯表面,定位和夹紧的条件都较差,而加工余量和切削力都较大,如果再遇上工件本身的刚性差,则对加工精度会有很大影响。因此,第一道工序的定位和夹紧方法的选择,对于整个工艺过程的加工精度常有深远的影响。连杆的加工就是如此,在连杆加工工艺路线中,在精加工主要表面开始前,先粗铣两个端面,其中粗磨端面又是以毛坯端面定位.因此,粗铣就是关键工序.在粗铣中工件如何定位呢?一个方法是以毛坯端面定位,在侧面和端部夹紧,粗铣一个端面后,翻
14、身以铣好的面定位,铣另一个毛坯面。但是由于毛坯面不平整,连杆的刚性差,定位夹紧时工件可能变形,粗铣后,端面似乎平整了,一放松,工件又恢复变形,影响后续工序的定位精度。另一方面是以连杆的大头外形及连杆身的对称面定位。这种定位方法使工件在夹紧时的变形较小,同时可以铣工件的端面,使一部分切削力互相抵消,易于得到平面度较好的平面。同时,由于是以对称面定位,毛坯在加工后的外形偏差也比较小。.4。 确定合理的夹紧方法既然连杆是一个刚性比较差的工件,就应该十分注意夹紧力的大小,作用力的方向及着力点的选择,避免因受夹紧力的作用而产生变形,以影响加工精度.在加工连杆的夹具中,可以看出设计人员注意了夹紧力的作用方
15、向和着力点的选择。在粗铣两端面的夹具中,夹紧力的方向与端面平行,在夹紧力的作用方向上,大头端部与小头端部的刚性高,变形小,既使有一些变形,亦产生在平行于端面的方向上,很少或不会影响端面的平面度.夹紧力通过工件直接作用在定位元件上,可避免工件产生弯曲或扭转变形。在加工大小头孔工序中,主要夹紧力垂直作用于大头端面上,并由定位元件承受,以保证所加工孔的圆度.在精镗大小头孔时,只以大平面(基面)定位,并且只夹紧大头这一端。小头一端以假销定位后,用螺钉在另一侧面夹紧。小头一端不在端面上定位夹紧,避免可能产生的变形。1。.4连杆两端面的加工采用粗铣、精铣、粗磨、精磨四道工序,并将精磨工序安排在精加工大、小
16、头孔之前,以便改善基面的平面度,提高孔的加工精度。粗磨在转盘磨床上,使用砂瓦拼成的砂轮端面磨削。这种方法的生产率较高。精磨在M7130型平面磨床上用砂轮的周边磨削,这种办法的生产率低一些,但精度较高.1。45连杆大、小头孔的加工连杆大、小头孔的加工是连杆机械加工的重要工序,它的加工精度对连杆质量有较大的影响。小头孔是定位基面,在用作定位基面之前,它经过了钻、扩、铰三道工序。钻时以小头孔外形定位,这样可以保证加工后的孔与外圆的同轴度误差较小。小头孔在钻、扩、铰后,在金刚镗床上与大头孔同时精镗,达到IT6级公差等级,然后压入衬套,再以衬套内孔定位精镗大头孔.由于衬套的内孔与外圆存在同轴度误差,这种
17、定位方法有可能使精镗后的衬套孔与大头孔的中心距超差.大头孔经过扩、粗镗、半精镗、精镗、金刚镗和珩磨达到IT6级公差等级。表面粗糙度a 为.m,大头孔的加工方法是在铣开工序后,将连杆与连杆体组合在一起,然后进行精镗大头孔的工序。这样,在铣开以后可能产生的变形,可以在最后精镗工序中得到修正,以保证孔的形状精度。14.6 连杆螺栓孔的加工连杆的螺栓孔经过钻、扩、铰工序。加工时以大头端面、小头孔及大头一侧面定位。为了使两螺栓孔在两个互相垂直方向平行度保持在公差范围内,在扩和铰两个工步中用上下双导向套导向。从而达到所需要的技术要求。粗铣螺栓孔端面采用工件翻身的方法,这样铣夹具没有活动部分,能保证承受较大
18、的铣削力.精铣时,为了保证螺栓孔的两个端面与连杆大头端面垂直,使用两工位夹具。连杆在夹具的工位上铣完一个螺栓孔的两端面后,夹具上的定位板带着工件旋转100 ,铣另一个螺栓孔的两端面。这样,螺栓孔两端面与大头孔端面的垂直度就由夹具保证。1.4. 连杆体与连杆盖的铣开工序剖分面(亦称结合面)的尺寸精度和位置精度由夹具本身的制造精度及对刀精度来保证。为了保证铣开后的剖分面的平面度不超过规定的公差00mm ,并且剖分面与大头孔端面保证一定的垂直度,除夹具本身要保证精度外,锯片的安装精度的影响也很大。如果锯片的端面圆跳动不超过0。02 m,则铣开的剖分面能达到图纸的要求,否则可能超差.但剖分面本身的平面
19、度、粗糙度对连杆盖、连杆体装配后的结合强度有较大的影响。因此,在剖分面铣开以后再经过磨削加工。14。8大头侧面的加工以基面及小头孔定位,它用一个圆销(小头孔).装夹工件铣两侧面至尺寸,保证对称(此对称平面为工艺用基准面)。.5连杆加工工艺设计应考虑的问题1.。1工序安排连杆加工工序安排应注意两个影响精度的因素:(1)连杆的刚度比较低,在外力作用下容易变形;(2)连杆是模锻件,孔的加工余量大,切削时会产生较大的残余内应力。因此在连杆加工工艺中,各主要表面的粗精加工工序一定要分开。.5.2 定位基准精基准:以杆身对称面定位,便于保证对称度的要求,而且采用双面铣,可使部分切削力抵消.统一精基准:以大
20、小头端面,小头孔、大头孔一侧面定位。因为端面的面积大,定位稳定可靠;用小头孔定位可直接控制大小头孔的中心距。53 夹具使用应具备适应“一面一孔一凸台”的统一精基准.而大小头定位销是一次装夹中镗出,故须考虑“自为基准”情况,这时小头定位销应做成活动的,当连杆定位装夹后,再抽出定位销进行加工。保证螺栓孔与螺栓端面的垂直度。为此,精铣端面时,夹具可考虑重复定位情况,如采用夹具限制7个自由度(其是长圆柱销限制4个,长菱形销限制个)。长销定位目的就在于保证垂直度。但由于重复定位装御有困难,因此要求夹具制造精度较高,且采取一定措施,一方面长圆柱销削去一边,另一方面设计顶出工件的装置。1. 切削用量的选择原
21、则正确地选择切削用量,对提高切削效率,保证必要的刀具耐用度和经济性,保证加工质量,具有重要的作用.6。1 粗加工时切削用量的选择原则粗加工时加工精度与表面粗糙度要求不高,毛坯余量较大。因此,选择粗加工的切削用量时,要尽可能保证较高的单位时间金属切削量(金属切除率)和必要的刀具耐用度,以提高生产效率和降低加工成本。金属切除率可以用下式计算: V。f.a.000式中:Zw单位时间内的金属切除量(3/s)V切削速度(m/s)f 进给量(m/r)ap切削深度(mm)提高切削速度、增大进给量和切削深度,都能提高金属切除率。但是,在这三个因素中,影响刀具耐用度最大的是切削速度,其次是进给量,影响最小的是切
22、削深度。所以粗加工切削用量的选择原则是:首先考虑选择一个尽可能大的吃刀深度ap,其次选择一个较大的进给量度f,最后确定一个合适的切削速度V。选用较大的ap和以后,刀具耐用度t 显然也会下降,但要比对t的影响小得多,只要稍微降低一下V便可以使t回升到规定的合理数值,因此,能使V、的乘积较大,从而保证较高的金属切除率。此外,增大ap可使走刀次数减少,增大f又有利于断屑。因此,根据以上原则选择粗加工切削用量对提高生产效率,减少刀具消耗,降低加工成本是比较有利的.1)切削深度的选择:粗加工时切削深度应根据工件的加工余量和由机床、夹具、刀具和工件组成的工艺系统的刚性来确定。在保留半精加工、精加工必要余量
23、的前提下,应当尽量将粗加工余量一次切除.只有当总加工余量太大,一次切不完时,才考虑分几次走刀。)进给量的选择:粗加工时限制进给量提高的因素主要是切削力。因此,进给量应根据工艺系统的刚性和强度来确定。选择进给量时应考虑到机床进给机构的强度、刀杆尺寸、刀片厚度、工件的直径和长度等。在工艺系统的刚性和强度好的情况下,可选用大一些的进给量;在刚性和强度较差的情况下,应适当减小进给量.3)切削速度的选择:粗加工时,切削速度主要受刀具耐用度和机床功率的限制。切削深度、进给量和切削速度三者决定了切削功率,在确定切削速度时必须考虑到机床的许用功率。如超过了机床的许用功率,则应适当降低切削速度。2精加工时切削用
24、量的选择原则精加工时加工精度和表面质量要求较高,加工余量要小且均匀。因此,选择精加工的切削用量时应先考虑如何保证加工质量,并在此基础上尽量提高生产效率.1)切削深度的选择:精加工时的切削深度应根据粗加工留下的余量确定。通常希望精加工余量不要留得太大,否则,当吃刀深度较大时,切削力增加较显著,影响加工质量。)进给量的选择:精加工时限制进给量提高的主要因素是表面粗糙度。进给量增大时,虽有利于断屑,但残留面积高度增大,切削力上升,表面质量下降。3)切削速度的选择:切削速度提高时,切削变形减小,切削力有所下降,而且不会产生积屑瘤和鳞刺。一般选用切削性能高的刀具材料和合理的几何参数,尽可能提高切削速度.
25、只有当切削速度受到工艺条件限制而不能提高时,才选用低速,以避开积屑瘤产生的范围。由此可见,精加工时选用较小的吃刀深度a和进给量,并在保证合理刀具耐用度的前提下,选取尽可能高的切削速度V,以保证加工精度和表面质量,同时满足生产率的要求。1.7 连杆的机械加工工艺过程由上述的分析可知,连杆的尺寸精度、形状精度以及位置精度的要求都很高,但是连杆的刚性比较差,容易产生变形,这就给连杆的机械加工带来了很多困难,必须充分的重视.连杆机械加工工艺过程如下表(1)所示: 表(11)工序工序名称工序内容工艺装备1铣铣连杆大、小头两平面,每面留磨量05mX2K2粗磨以一大平面定位,磨另一大平面,保证中心线对称,无
26、标记面称基面。(下同)M5钻与基面定位,钻、扩、铰小头孔Z3004铣以基面及大、小头孔定位,装夹工件铣尺寸mm两侧面,保证对称(此平面为工艺用基准面)X62W组合机床或专用工装扩以基面定位,以小头孔定位,扩大头孔为60mZ30806铣以基面及大、小头孔定位,装夹工件,切开工件,编号杆身及上盖分别打标记。X62组合机床或专用工装锯片铣刀厚2mm7铣以基面和一侧面定位装夹工件,铣连杆体和盖结合面,保直径方向测量深度为25mm2组合夹具或专用工装磨以基面和一侧面定位装夹工件,磨连杆体和盖的结合面M7309铣以基面及结合面定位装夹工件,铣连杆体和盖mmmm斜槽X6组合夹具或专用工装10锪以基面、结合面
27、和一侧面定位,装夹工件,锪两螺栓座面mm,R11m,保证尺寸mmX2W11钻钻20mm螺栓孔Z0012扩先扩2-12mm螺栓孔,再扩2m深19mm螺栓孔并倒角3013铰铰12。2mm螺栓孔Z30504钳用专用螺钉,将连杆体和连杆盖装成连杆组件,其扭力矩为112N.m1镗粗镗大头孔T6 86倒角大头孔两端倒角X62磨精磨大小头两端面,保证大端面厚度为mmM7138镗以基面、一侧面定位,半精镗大头孔,精镗小头孔至图纸尺寸,中心距为mm可调双轴镗19镗精镗大头孔至尺寸T211520称重称量不平衡质量弹簧称21钳按规定值去重量22钻钻连杆体小头油孔。5mm,10mmZ30253压铜套双面气动压床24挤
28、压铜套孔压床2倒角小头孔两端倒角Z3052镗半精镗、精镗小头铜套孔T2117珩磨珩磨大头孔珩磨机床8检检查各部尺寸及精度2探伤无损探伤及检验硬度3入库连杆的主要加工表面为大、小头孔和两端面,较重要的加工表面为连杆体和盖的结合面及连杆螺栓孔定位面,次要加工表面为轴瓦锁口槽、油孔、大头两侧面及体和盖上的螺栓座面等。连杆的机械加工路线是围绕着主要表面的加工来安排的。连杆的加工路线按连杆的分合可分为三个阶段:第一阶段为连杆体和盖切开之前的加工;第二阶段为连杆体和盖切开后的加工;第三阶段为连杆体和盖合装后的加工。第一阶段的加工主要是为其后续加工准备精基准(端面、小头孔和大头外侧面);第二阶段主要是加工除
29、精基准以外的其它表面,包括大头孔的粗加工,为合装做准备的螺栓孔和结合面的粗加工,以及轴瓦锁口槽的加工等;第三阶段则主要是最终保证连杆各项技术要求的加工,包括连杆合装后大头孔的半精加工和端面的精加工及大、小头孔的精加工.如果按连杆合装前后来分,合装之前的工艺路线属主要表面的粗加工阶段,合装之后的工艺路线则为主要表面的半精加工、精加工阶段。1.8 确定各工序的加工余量、计算工序尺寸及公差1.8. 确定加工余量 用查表法确定机械加工余量:(根据机械加工工艺手册第一卷 表3.-2 表3.226 表.22)()、平面加工的工序余量(mm) 单面加工方法单面余量经济精度工序尺寸表面粗糙度毛坯4312。5粗
30、铣15T12()40()15精铣0。6T10()3.8().粗磨0.IT8()38.2()1. 精磨0。17()8()0.8 则连杆两端面总的加工余量为:A总= =(A粗铣+A精铣+A粗磨+A精磨)2=(1。+0.6+030。1)mm(2)、连杆铸造出来的总的厚度为H=38+=mm。82 确定工序尺寸及其公差(根据机械制造技术基础课程设计指导教程 表2 表234)1)、大头孔各工序尺寸及其公差(铸造出来的大头孔为5 m)工序名称工序基本余量工序经济精度工序尺寸最小极限尺寸表面粗糙度珩磨.0865565.5。4精镗。465465。408半精镗1561.6二次粗镗26446.3一次粗镗262215
31、扩孔56052)、小头孔各工序尺寸及其公差(根据机械制造技术基础课程设计指导教程表29表2-30)工序名称工序基本余量工序经济精度工序尺寸最小极限尺寸表面粗糙度精镗0。2.6铰0.296.4扩92.5钻钻至12.1.9 计算工艺尺寸链1.。1 连杆盖的卡瓦槽的计算增环为: ; 减环为: ;封闭环为:1)、极限尺寸为: 0.204。5 =25 m=29-。1 = 24。7mm)、的上、下偏差为:=2(0。05)0。25(m)0.20.1=0。0(m)3)、的公差为:= 0.25(。30)= 55 m4)、的基本尺寸为:=30= 2m5)、的最终工序尺寸为:= mm1.9。 连杆体的卡瓦槽的计算增
32、环为: ; 减环为: ;封闭环为:)、极限尺寸为: = 13。30-4.5 8。35mm=295.=7。8 mm)、的上、下偏差为:=0.30-(-0。5)= 0。5m 0。10010= 。20 m)、的公差为: =0。35(020)=0。54)、的基本尺寸为:=135 = 8 mm5)、的最终工序尺寸为:=m.0 工时定额的计算1。10.1铣连杆大小头平面选用X52K机床根据机械制造工艺设计手册表2.481选取数据铣刀直径D 100m 切削速度Vf 2。7 m切削宽度= m 铣刀齿数Z = 6 切削深度p = 3 m则主轴转速 = 100v/D = 75in根据表3。131 按机床选取n 5
33、0 mi则实际切削速度V = D/(1000) = 。67m/s 铣削工时为:按表2.10 L= L1 =+1。5 5 mm L = mm基本时间jm z= (3+5+3)(5000.16)= 。 mn按表2。546 辅助时间ta 0.。5 = 0.18 min 1。02 粗磨大小头平面选用M735磨床根据机械制造工艺设计手册表2470选取数据砂轮直径D =0 mm 磨削速度V 033 /s切削深度a = 0.3 m r0= 0.033 mm/ Z = 8则主轴转速n = 10/D = 1588r/mi根据表3。18 按机床选取n 10rmi则实际磨削速度V = Dn/(00060) =.20
34、 m/s磨削工时为:按表2.5-11基本时间tj =zkfr0z =(0.31)(100。0338) = 01 min按表3140 辅助时间a = 021 min1.10。3 加工小头孔(1) 钻小头孔 选用钻床Z3080 根据机械制造工艺设计手册表.438(1)选取数据钻头直径D= 0 切削速度 = 9 mm切削深度ap 10 mm 进给量f = 。1m/r则主轴转速n 1000v/ = 94r/min根据表130 按机床选取000 r/mn则实际钻削速度 n/(10060) 10 m钻削工时为:按表。57L = m L1 = 1.mm 2 =2.5mm基本时间j = Ln (1015。5)
35、/(0.11000) = 0 in按表。41 辅助时间ta = .5 in按表2。42 其他时间t = 0。mn(2) 扩小头孔 选用钻床300根据机械制造工艺设计手册表。4-53选取数据扩刀直径 30 mm 切削速度 =.32 m/s切削深度ap =15 m 进给量 = 0。8mm则主轴转速n =100v/ 203 r/min根据表3130 按机床选取n 25 r/m则实际切削速度V =D/(10060)=039 m/s 扩削工时为:按表2.57L =10 mm L = m基本时间/n=(1+3)/(。825)=007min按表。-1 辅助时间t025in() 铰小头孔 选用钻床Z380根据
36、机械制造工艺设计手册表2。481选取数据铰刀直径D = 30 mm 切削速度V=0.22 ms切削深度ap =.10 mm 进给量f 08m/r则主轴转速n 000v/ 140rin根据表3.1- 按机床选取n =200 r/in则实际切削速度VDn(10060) = 032 m/s 铰削工时为: 按表2.57L=1m L1 0 L2= m基本时间tj = L/fn= (10+3)(000) = 009in按表2. 辅助时间ta= 0.25 min.10铣大头两侧面 选用铣床62W根据机械制造工艺设计手册表2.477(88)选取数据铣刀直径D=20 m 切削速度V= .64m/s铣刀齿数Z =
37、 切削深度p = 4mm af =。10r则主轴转速n = 1000v = 61 rmin根据表。174 按机床选取=750 r/min则实际切削速度V= Dn/(10006) 0。7 m/s 铣削工时为:按表2。10L=40 mm L1=+15=8。5m L2=.5 mm基本时间j =L/fz = (4+8.5+.5)(7500。103)=03 mi按表 辅助时间a0.40。45= 0。18 min1.10。5、扩大头孔选用钻床床Z30 刀具:扩孔钻根据机械制造工艺设计手册表2。45选取数据扩孔钻直径D60 mm 切削速度V = 1。29 m/s进给量f = 0。50 m/r 切削深度p=3
38、.0 m 走刀次数I= 1则主轴转速=000/=41 r/min根据表314 按机床选取n0rmn则实际切削速度VDn/(0060)=1.5 /s 扩削工时为: 按表2。57L= 4 mm L = 3 L2 =3 m 基本时间: 10。6铣开连杆体和盖 选用铣床X62W根据机械制造工艺设计手册表2。49(90)选取数据铣刀直径 =3 mm 切削速度V= 0.3 /s切削宽度ae 3 mm 铣刀齿数Z 4 切削深度a =2 mm af = 0。15 mm/r 0 m 则主轴转速n = 100v/D= 103 r/n根据表。174 按机床选取=750r/in则实际切削速度V n/(10006) =
39、2.47 m/s铣削工时为: 按表2。510 L= 17 mm L1 = - +2 = 6mm L2 = 2 m基本时间= Li = (17+2)(148) = 。7 min按表2546 辅助时间ta=0.04=0。18 min1。10.7 加工连杆体(1) 粗铣连杆体结合面 选用铣床X62W根据机械制造工艺设计手册表24(84)选取数据铣刀直径 = mm 切削速度V 0。35 m/s 切削宽度ae = 05 mm铣刀齿数Z 8 切削深度a=2 mm af = 0。1m/则主轴转速n= 1000v/D= 8 /in根据表3。1-74 按机床选取n = 0 r/mi则实际切削速度V= Dn/(1
40、0060) =294 m 铣削工时为: 按表。50L=8 m L1 = +1。= 75 mm L = .5 mm基本时间tj = /f = (8+7。5+2.)/(.9608) = 0。03 min按表2。5-4 辅助时间ta040。4=0。18mi(2) 精铣连杆体结合面 选用铣床X6W根据机械制造工艺设计手册表2.484选取数据铣刀直径 75 mm 切削速度V 04 /s铣刀齿数Z = 8 切削深度p = 2 mma=0。7 mr 切削宽度a=0 m则主轴转速n= 1000v/D 107 rmi根据表3。174 按机床选取n = 750 /mi则实际切削速度 = n/(10000)=2.9
41、4 m/s 铣削工时为:按表25-0 = 38 mm 1 = 7.5mm L2 = 2。5 mm基本时间tj = L/fmz =(3+7.2。)/(.966) = . min按表- 辅助时间t =04. = 0.8 min(3) 粗锪连杆两螺栓底面 选用钻床Z32根据机械制造工艺设计手册表-67选取数据锪刀直径 = 28 mm 切削速度V 0。2 m/s锪刀齿数 = 6 切削深度p = 3 m 进给量 =.1mr则主轴转速n = 100v/D 50. /mn根据表1- 按机床选取n =0 r/min则实际切削速度V= D/(0000)= 2。94m/ 锪削工时为: 按表。5-7 28 mm 1
42、 1。5 mm 基本时间= L/n (28+1。5)/(0。1508) 004 min(4)铣轴瓦锁口槽 选用铣床X62根据机械制造工艺设计手册表2。49选取数据铣刀直径D= 63 mm 切削速度 03m/s铣刀齿数Z = 2 切削深度ap = 2 mm 切削宽度e = 0。 m f = 002 mr 则主轴转速 1000v/ = 4 /min根据表.17 按机床选取=100 /min则实际切削速度V = D(00060)。33 m/s 铣削工时为: 按表。5 L=5 mm L1=0.5631。 3 m L =1.5 mm基本时间tj=Lfz=(5+33+1.5)(1024)=002 mi按表
43、2。5-6 辅助时间a。0.5=1 m(5) 精铣螺栓座面 选用铣床X62W根据机械制造工艺设计手册表2.90选取数据铣刀直径D=3 mm 切削速度= 0.47 m/s铣刀齿数Z = 切削深度a = 2 mm 切削宽度a = 5 af=0.015 mm/r 则主轴转速n =1000/ 2 r/n根据表3.131 按机床选取n= 10 r/in则实际切削速度V Dn/(1000)= 0.49 m/s 铣削工时为: 按表25-10 L= 8mm L = 1.5 = 19 mm L2 3m基本时间tj=L/fmz = (2+19+3)/(1024) = 0。02 mi按表2546 辅助时间t = .
44、4。4 = 0。1 min(7) 精磨结合面 选用磨床730根据机械制造工艺设计手册表2。4-10选取数据砂轮直径D=0 mm 切削速度 =00 /s 切削深度p0. mm 进给量r0 = 06 mm/r则主轴转速n = 1000v/ = 7r/mi根据表3148 按机床选取 = 10 /mn则实际切削速度V = Dn/(100060) =。20m/s 磨削工时为: 按表。511 基本时间j= =02min (=0.1 1 z)1。10。8 铣、磨连杆盖结合面(1) 粗铣连杆上盖结合面 选用铣床X62W根据机械制造工艺设计手册表2。74(84)选取数据铣刀直径D = 7mm 切削速度V= 。3
45、5 m/s切削宽度ae mm 铣刀齿数Z = af = .12 mr 则主轴转速 1000v/D = 89 /mi根据表3。174 按机床选取n 00 r/min则实际切削速度V D(060)= 039/s 铣削工时为:按表50 L =38 m L1 = +1。5= 1 m L = 25 mm基本时间tj = L/fz=(8+16+25)/(1008) = 007 min按表25-46 辅助时间ta=0。0。4=0.18 min(2) 精铣连杆上盖结合面 选用铣床62根据机械制造工艺设计手册表2.4-84选取数据铣刀直径D 75m 切削速度V= .42 /s切削宽度ae = m 铣刀齿数Z=
46、8 进给量 07 mm/r 则主轴转速n =10v/D = 107 /min根据表3.74 按机床选取n 10 r/in则实际切削速度V Dn(10060) = 03 s铣削工时为: 按表210L 38 L 15 = 7。5 mm L2 2.5 m基本时间tj = L/fmz (38+7。5+25)(1108)=. mi按表256 辅助时间ta=。4。01mi(3) 粗铣螺母座面 选用铣床X62根据机械制造工艺设计手册表2.48选取数据铣刀直径 63 m 切削速度V = 03 /s铣刀齿数Z 24 切削宽度ae = 5 m af =0.1m/r 则主轴转速n 1000v/= 03/min根据表
47、.14 按机床选取n =10 /mi则实际切削速度V = Dn(10060) =.3 ms 铣削工时为:按表2。5-10 L = 28mm L1= 15 75 mm L2 = 2.5 m基本时间tj= /fmz (+7。+2。)/(0024) = 0.0min按表2。5-4 辅助时间t=00.45=0。1 min(4) 铣轴瓦锁口槽 选用铣床62W根据机械制造工艺设计手册表。0选取数据铣刀直径D = 3 m 切削速度V = 。31 m/铣刀齿数Z = 24 切削深度ap =2 mm 切削宽度e = 。 mm af = 0.2 mm/r 则主轴转速n 1000v/D = 94r/m根据表.17按
48、机床选取n 0r/i则实际切削速度V = n/(100) 0.33/s 铣削工时为: 按表2.510 L = 5 m L1 = .531.5= 3 m L = 1。5mm 基本时间tj =L/fmz = (5+31。5)(02) 00min按表2546 辅助时间 0。40。45= 0。8 min() 精磨结合面 选用磨床M30根据机械制造工艺设计手册表2。17选取数据砂轮直径D 40 m 切削速度V = 0。330 s 切削深度ap。 mm 进给量fr0 =.06 m/则主轴转速n =100/D 157 r/min根据表3。14 按机床选取= 0 r/mn则实际切削速度V= n(1060) =
49、0。m/s磨削工时为: 按表251 基本时间 = =002 n (=0 k=1 z=)1。9 铣、钻、镗(连杆总成体)(1) 精铣连杆盖上两螺母座面 选用铣床62W根据机械制造工艺设计手册表240选取数据铣刀直径D = 63mm 切削速度V = 。4m/s切削宽度ae = mm 铣刀齿数Z = 4切削深度ap = 2 mm af = 0。015m/r 则主轴转速n = 1000v = 42 /mi根据表17 按机床选取 = 1 rmin则实际切削速度V =n/(10060) =49 m 铣削工时为: 按表2。5-10L = 8mm L1 = +1。5 =. mm L2 = 2。5 mm基本时间tj/mz
- 温馨提示:
1: 本站所有资源如无特殊说明,都需要本地电脑安装OFFICE2007和PDF阅读器。图纸软件为CAD,CAXA,PROE,UG,SolidWorks等.压缩文件请下载最新的WinRAR软件解压。
2: 本站的文档不包含任何第三方提供的附件图纸等,如果需要附件,请联系上传者。文件的所有权益归上传用户所有。
3.本站RAR压缩包中若带图纸,网页内容里面会有图纸预览,若没有图纸预览就没有图纸。
4. 未经权益所有人同意不得将文件中的内容挪作商业或盈利用途。
5. 装配图网仅提供信息存储空间,仅对用户上传内容的表现方式做保护处理,对用户上传分享的文档内容本身不做任何修改或编辑,并不能对任何下载内容负责。
6. 下载文件中如有侵权或不适当内容,请与我们联系,我们立即纠正。
7. 本站不保证下载资源的准确性、安全性和完整性, 同时也不承担用户因使用这些下载资源对自己和他人造成任何形式的伤害或损失。