“数控机床装配、调试和维修”项目样题
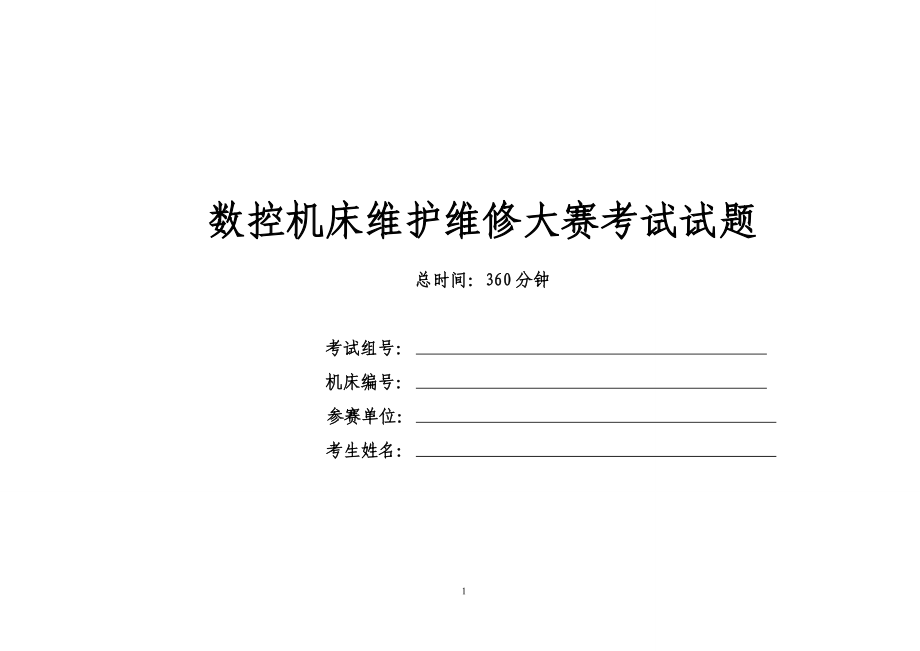


《“数控机床装配、调试和维修”项目样题》由会员分享,可在线阅读,更多相关《“数控机床装配、调试和维修”项目样题(27页珍藏版)》请在装配图网上搜索。
1、 数控机床维护维修大赛考试试题 总时间:360分钟 考试组号: 机床编号:参赛单位:考生姓名:注意事项:1、考生在考试过程中应该遵守相关的规章制度和安全守则,如有违反,则按照相关规定在考试的总成绩中扣除相应分值2、在裁判员确定机械、电气安全完成后方可进行精度检测和机械加工项,否则视为非法操作,裁判员有权取消其考试资格。3、考生必须认真填写各答题卡,考试完成后上交。4、考生在排除故障的过程中,如因为考生的原因造成机床出现新的故障,酌情扣分。但如果在考试的时间内将故障排除,不予扣分。5、考生在参数设置环节,如修改了评分范围以外的参数,如果修改后的参数对机床运行无影响,则不予扣分,如果影响到机床正常
2、运行,则酌情扣分,如果改善了机床的运行状态,则酌情加分。6、所有考试成绩必须以6小时 ( 360分钟 ) 内工作完成内容进行计算。7、由于装配、参数设置、精度检测等原因造成机床定位精度超差,根据超差数据在总成绩中扣除相应分值。(超差小于0.01mm扣3分,0.010.02mm扣5分;超过0.02mm扣8分)。8、在机床进给轴装配及调试过程中,没达到规定时间和没完成技术要求内容时裁判不发给选手溜板箱和轴承座定位销,达到规定时间没完成技术要求内容而要求发放定位销者,除扣除相应小分外,还需再在总成绩中扣除5分。得分第一题:数控机床进给轴装配及调试 (共22分) 请根据现场配备工具、Z轴部装图及本阶段
3、考核内容完成相应装配、准备工作并填写表一。本阶段考核内容(所有项选手完成后需经裁判确认可方能进行下一环节)表一:装配工艺流程卡产品型号部件名称共 2 页第 1 页序号装配内容及技术要求装配工艺及技术要求工艺装配工具完成情况备注自检记录一清洗及零件的摆放,符合金属切屑机床通用技术条件的各项规定用毛刷蘸取洗油清洗所有的零部件,要毛刷所有零部件的摆放互补碰撞,所有零部件洗后达到物见本色求洗后达到物见本色,摆放时要求所有洗油零部件互补碰撞棉布二拆卸机床尾座放在软基面上将尾座放在胶皮垫上人工操作尾座无损伤三以Z轴电机座为基准,安装及调整Z轴溜板箱、轴承支架,要求Z轴电机座、溜板箱、轴承支架三者的同轴度上
4、、侧母线均0.01/全长,其轴承孔或丝杆螺母孔与机床床身导轨平行度上、侧母线全长允差均为0.01/200mm。将变径套及检棒组合后分别放在丝杠螺母孔和电机座轴承孔中,和轴承支架孔中。将百分表和杠杆百分表吸固在放在导轨上的桥尺上,将两表的顶尖分别顶在检棒的上、侧母线上。检验并调整轴承支架、Z轴溜板箱、Z轴电机座的位置,使三者同轴,达到精度后规定所有定位销。百分表上母线误差为_经裁判确认后,发给选手溜板箱和轴承座的定位销,以便选手进行后面的安装调试工作杠杆百分表侧母线误差为_变径套检棒桥尺四安装Z轴电机座、轴承支架的轴承组件,安装Z轴溜板箱的滚珠丝杠副组件,对Z轴滚珠丝杠副及其整套传动部件予以固定
5、将丝杠螺母副组件穿入溜板箱孔中并紧固,穿入丝杠法兰盘,将Z轴电机座轴承组件安装到丝杠左端面,将轴承支架的轴承组件安装到轴承支架中,紧固法兰盘,并安装到正确位置。用圆螺母紧固转动,直至Z轴电机座轴承组件完全进入Z轴电机座轴孔中。油壶安装后整套传动部件运转正常锤子铝套钩型扳手产品型号部件名称共 2 页第 2 页序号装配内容及技术要求装配工艺及技术要求工艺装配工具完成情况备注自检记录裁判确认记录五按图纸正确的固定及预紧滚珠丝杠副后,复检滚珠丝杠副在轴承座、电机座、丝杠螺母座端上、侧母线径向跳动将百分表和杠杆百分表吸固在放在导轨上的桥尺上,将两表的顶尖分别顶在丝杠的上、侧母线上。检验丝杠三点的误差内六
6、扳手上母线误差为_百分表侧母线误差为_杠杆百分表桥尺六Z轴滚珠丝杠副安装后其与电机连接端的径跳和轴窜检侧及调整,径跳允差0.012mm,轴窜允差0.008mm将百分表、杠杆百分表分别固定在适当位置,将两表的顶尖分别顶在联轴器的侧母线和丝杠右端面中心孔中的5钢珠上,转动丝杠检验丝杠的径跳和轴窜,并调整。百分表联轴器径跳误差为_杠杆百分表轴窜误差为_5钢珠七安装Z轴伺服电机、滚珠丝杠副防护板按照装配图中的位置安装Z轴伺服电机、滚珠丝杠副防护板。安装时不要碰撞Z轴伺服电机。加长内六扳手安装及紧固后Z轴伺服电机、滚珠丝杠副防护板无松动现象,且位置正确内六扳手八机床防护门、尾座等其它零件的安装按照装配图
7、中的位置安装机床防护门、尾座等其它零件内六扳手安装及紧固后机床防护门、尾座等其它零件无松动现象,且位置正确在加工工件前必须安装机床防护门油石棉布九机床精度检测与补偿利用步距规的等步距的特点,用千分表侧定位精度,并在计算后通过在Z轴参数中进行补偿。步距规补偿后定位误差为_千分表十装入机床主轴卡盘按照装配图中的位置安装主轴卡盘内六扳手安装及紧固后主轴卡盘运转正常 裁判签字Z轴装配示意图得分第二题: 数控机床电气连接(共7分)请考生结合数控机床电气原理图,将机床接线端子排XT1,XT2尚未连接的电缆按照要求连接完毕,连接时端子排从右端第一条电缆开始编号为XT1-1,XT2-1依次填写表二,如果因为端
8、子排或其他原因造成电缆与端子不对应,需在备注中说明 。全部连接正确得7分,连接错误1条扣1分,扣完为止。如果出现连接不牢靠,连接过于凌乱酌情扣分。 表二:电气连接记录表所在位置电缆端号电缆名称或作用得分备注XT1-1U01 主轴电机风扇电源XT1-2XT1-3XT1-4XT1-5XT1-6XT1-7XT1-8XT1-12XT1-14XT2-1XT2-2XT2-3XT2-4XT2-5XT2-6XT2-7XT2-8XT2-9XT2-10XT2-11XT2-12XT2-13XT2-14XT2-15XT2-16XT2-17XT2-18XT2-19XT2-20XT2-21XT2-22XT2-23XT2-
9、24XT2-25XT2-28XT2-29XT2-30XT2-31得分第三题:数控机床参数设置、调试、故障维修(共43分)1、 上电前的检查,此检查在系统上电运行之前必须进行,经裁判检查无误后方可以通电运行。(5分)表三:上电检查记录表序号检查事项是否正常解决方法备注1各电源的相电阻及对地电阻。若中间经过空开.交流接触器.保险等器件,应手动令这些器件导通测量。2电源变压器的进出线顺序,务必检查。如:伺服变压器,主轴变压器,220V控制变压器, 110V控制变压器等。3开关电源,24V正负是否正确。之间是否有短路现象。4各继电器线圈控制电源正负是否正确,连接是否牢靠。5伺服电机电源线相序是否正确,
10、各电机电源及反馈端子是否连接正确牢靠。6检查各回路导线、电缆的规格是否符合设计要求。7各伺服电机电源线与码盘线是否一一对应。连接是否牢靠。8检查所有24V继电器线圈接线是否正确。9各轴限位开关是否动作灵活、可靠。目测开关安装位置是否正确。10Z轴是否安装完成。11机械是否有干涉,尾座是否已经归位。裁判没有签字确认前擅自通电者扣5分 裁判确认: 得分2、请考生根据提供的机床相关技术指标及技术要求设置相关的参数机床技术指标及要求: 表四:机床相关部件技术指标: 项目名称数值单位项目名称数值单位主轴电机的额定功率5.5KWX轴伺服电机极对数3无主轴电机的最高转速4500r/minX轴伺服电机编码器线
11、数2500主轴电机的极对数2无X轴电机与丝杆传动比1:1主轴电机的基本频率50HzX轴丝杠螺距4mm主轴电机的额定电压380VX轴电机额定及最高转速1200/2000r/min主轴额定电流 11.6AZ 轴伺服电机极对数3主轴电额定转速1460r/minZ轴伺服电机编码器线数2500主轴电机与主轴传动比3:2无Z轴电机与丝杆传动比1:1主轴档位1无Z轴丝杠螺距6mm主轴编码器每转脉冲数1024无Z轴电机额定及最高转速1200/2000r/min表五:机床技术指标要求序号项目名称要求单位备注X轴Z轴1主轴速度范围1202100r/min2主轴手动初始转速300r/min3机床坐标显示(公制/英制
12、)公制4是否采用断电保护否5外置存储设置类型U盘6是否显示pmc轴否7上电系统是否提示回零否8脉冲输出方式单脉冲单脉冲9正负软极限设置根据机床实际情况进行设置微米正确设置10回参考点方向正向正向11参考点位置及偏差00微米12回参考点快移速度X轴2500Z轴3000mm/min13回参考点定位速度200200mm/min14单向定位偏移值10001000微米15最高快移速度30005000mm/min16最高加工速度15003000mm/min17快移加减速时间常数64ms64ms18快移加减速捷度时间常数3232ms19加工加减速时间常数6464ms20加工加减速捷度时间常数3232ms21
13、定位允差2020微米22最大跟踪误差1200012000微米得分3、数控系统、变频器、伺服参数的调整与修改。(共13分)1)根据系统的连接手册、变频器说明书和伺服说明书以及技术指标进行参数设置,置参数时详细填写表六,以备裁判对照考生填写的答题表进行分数的给定。所有参数的总分为13分,全部设置正确得13分,设置错误或漏设1个扣1分,扣完13分为止,参数设置应能符合技术要求及保证机床正常运行。 表六: 参数调整表参数类别序号参数名称调整前数值调整后的数值单位系统参数1主轴编码器每转脉冲数2公制/英制编程3是否采用断电保护机床位置4英制默认显示小数点后位数5外置存储设置类型6是否显示系统时间7是否显
14、示pmc轴8主轴编码器方向 PMC用户参数P0上电系统是否提示回零P1主轴总档位数P2主轴手动初始速度P3主轴是否支持抱闸P4主轴速度完成最大时间P5DA对应主轴最高理论转速P7刀架工位数P30一档理论低速P31一档理论高速P38一档实测低速P39一档实测高速P46一档传动比分子P47一档传动比分母参数类别序号参数名称X轴Z轴单位调整前数值调整后的数值调整前数值调整后的数值轴参数1外部脉冲当量分子微米2外部脉冲当量分母无3正软极限位置微米4负软极限位置微米5回参考点方向无6参考点位置微米7参考点开关偏差微米8回参考点快移速度毫米/分9回参考点定位速度毫米/分10单向定位偏移值毫米11最高快移速
15、度毫米/分12最高加工速度毫米/分13快移加减速时间常数毫秒14快移加减速捷度时间常数毫秒15加工加减速时间常数毫秒16加工加减速捷度时间常数毫秒17定位允差微米伺服参数1是否带反馈无2最大跟踪误差微米3电机每转脉冲数个4步进电机拍数无5反馈电子齿轮比分子无6反馈电子齿轮比分母无7参考点零位脉冲输入使能无8是否是步进电机无变频器参数调整表:序号参数编号参数名称调整后前参数调整后的参数12345伺服驱动参数调整表:序号参数编号参数名称调整前的参数调整后的参数12345得分4、阅读plc程序,填写表七:(共5分) 表七 :序号要求答案1系统复位开始后,经过多长时间如果复位未完成系统会提示复位失败2
16、换刀所允许最大时间为多少3简单描述循环启动实现的条件得分5、机床功能检查及调试(共20分)考生可以根据所列选项进行试车,保证机床各项功能的正确性,各动作能够正常实现。如在调试过程中出现故障,考生应进行排除并做详细记录填入故障排除记录栏,经裁判签字确认以后方可进行下一步。 表八:上电过程记录表类别检查事项技术指标检验标准是否正常故障原因分析故障排除记录备注电源机床总电源将所有空气开关保险全部拉下。并将数控系统电源线拆下。合上总电源开关,测量单项,三相电压是否正常,符合系统要求。根据电气图纸,逐步合上空开或保险,检查各电源电压是否正常。按从强到弱,从前到后的顺序经行。数控系统电源测量世纪星电源插头
17、24V电压是否正常,对应脚号的极性是否正确,然后断开电源,将电源插头插入。系统启动急停急停回路各电源没有问题,打开急停,系统是否能够复位并显示正常,拍下急停以后,系统处在急停状态。 裁判签字:1)手动方式下功能检查。检测如下功能时首先将机床的工作状态切换到手动方式下,按照表逐项进行检查,如果有问题请进行调试和维修并记录在故障排除记录栏 表九:手动方式下功能检查记录表类别检查事项技术指标检验标准是否正常故障原因分析故障排除记录备注手动进给+X方向按下机床X轴正向点动按键,机床向正方向移动-X方向按下机床X轴负向点动按键,机床向负方向移动+Z方向按下机床Z轴正向点动按键,机床向正方向移动-Z方向按
18、下机床Z轴负向点动按键,机床向负方向移动倍率修调在机床移动过程中,增减机床进给倍率,机床移动速度按比例变化 手动快速进给+X方向同时按下机床X轴正向点动和快速进给按键,机床向X正方向快速移动-X方向同时按下机床X轴负向点动和快速进给按键,机床向X负方向快速移动+Z方向同时按下机床Z轴正向点动和快速进给按键,机床向Z正方向快速移动-Z方向同时按下机床Z轴负向点动和快速进给按键,机床向Z负方向快速移动倍率修调在机床移动过程中,增减机床进给倍率,机床移动速度按比例变化机床硬限位保护+X方向超程手动将机床移动到X轴正向超程的位置,机床应急停并提示X轴正向超程如限位开关无效禁止运行机床-X方向超程手动将
19、机床移动到X轴负向超程的位置,机床应急停并提示X轴负向超程+Z方向超程手动将机床移动到Z轴正向超程的位置,机床应急停并提示Z轴正向超程-Z方向超程手动将机床移动到Z轴负向超程的位置,机床应急停并提示Z轴负向超程超程解除机床超程后,按下超程解除按键,系统能够复位,手动移动机床解除超程主轴主轴正转按下主轴正转按键,主轴正转主轴停止按下主轴停止按键,主轴停止旋转主轴反转按下主轴反转按键,主轴反转主轴点动按下主轴点动按键,主轴正转,手摇(手摇方式)+X方向手摇方式下按下X轴正向点动按键选择X轴,倍率开关选10,顺时针摇动手轮,机床X轴向正方向移动-X方向手摇方式下按下X轴正向点动按键选择X轴,倍率开关
20、选10,逆时针摇动手轮,机床X轴向负方向移动+Z方向手摇方式下按下Z轴正向点动按键选择Z轴,倍率开关选10,顺时针摇动手轮,机床Z轴向正方向移动-Z方向手摇方式下按下Z轴正向点动按键选择Z轴,倍率开关选10,顺时针摇动手轮,机床轴向负方向移动手摇倍率分别选择不同的倍率1、10、100摇动手轮一格,机床相应移动0.001、0.01 、0.1MM回参考点X轴回参考点工作方式切换到回零方式,按下x轴正向点动按键,机床回零,连续回零5次,并记录回零后机床坐标值。Z 轴回参考点工作方式切换到回零方式,按下z轴正向点动按键,机床回零,连续回零5次,并记录回零后机床坐标值。手动选刀1号刀选择1号刀位,按下刀
21、位转换,机床开始换刀。并最终停在1号刀位2号刀选择2号刀位,按下刀位转换,机床开始换刀。并最终停在2号刀位3号刀选择3号刀位,按下刀位转换,机床开始换刀。并最终停在3号刀位4号刀选择4号刀位,按下刀位转换,机床开始换刀。并最终停在4号刀位机床软限位保护+X方向手动移动机床X轴正方向,应当在硬限位5-10MM处提示X正软限位到。需要裁判确认-X方向手动移动机床X轴负方向,应当在硬限位5-10MM处提示X负软限位到。+Z方向手动移动机床Z轴正方向,应当在硬限位5-10MM处提示Z正软限位到。-Z方向手动移动机床Z轴负方向,应当在硬限位5-10MM处提示Z负软限位到。冷却手动开停按下冷却开停开关,冷
22、却开,灯亮。再按下冷却关,灯灭掉。2)MDI或自动方式: 表十:MDI或自动方式功能检查记录表序号检查事项检验方法是否正常故障原因分析故障排除记录备注主轴在MDI方式下M03 (S设为500)输入M03 S500后,主轴正转此项对速度无要求M04 (S设为500)输入M04 S500后,主轴反转M05 输入M05后,主轴停止旋转需裁判确认S指令分别在主轴正转和反转方式下输入S150/S1000/S2100,观察实际转速与指令转速是否相符。相差应在2%主轴修调给定主轴一速度,然后增减主轴倍率,主轴速度应该按相应比例变化刀架在MDI方式下1号刀输入T01后,按循环启动,刀架旋转开始换刀,换刀成功后
23、停在1号刀位2号刀输入T02后,按循环启动刀架旋转开始换刀,换刀成功后停在2号刀位3号刀输入T03后,按循环启动刀架旋转开始换刀,换刀成功后停在3号刀位4号刀输入T04后,按循环启动刀架旋转开始换刀,换刀成功后停在4号刀位冷却M08输入M08,按下循环启动后,冷却开M09输入M09,按下循环启动后,冷却关。机床运行速度G01 F在G01方式下,指定一段行程,并给定一速度,机床应该按照指定速度移动G00在G00方式下,指定一段行程,机床应该按照设定速度移动机床运行距离在G01方式下,指定0.1-1MM行程,并给定一较低速度,利用百分表检测机床实际移动距离与指令距离是否一致27得分第四题:位置精度
24、的检测与补偿(共16分)1、根据位置精度测量作业指导书,对机床的Z轴进行步距规测试,步距规目标位置示意图如下。机床回零参考点为起点P1P4P11050目标位置P5P3步距规结构示意图测试后,将测量与计算出的相关数据填入下面的表格,并根据计算出的数据填写补偿参数表并将计算过程记录下来:表十一:机床位置精度测试记录表测量记录机床型号机床编号测试轴补偿状态环境温度湿度测试者测试日期序号123456目标位置Pi /mm趋近方向位置偏差Xij(m)j=1234 5数据处理结果单向平均位置偏差m标准不确定度Si/m2Si/m-2Si/m+2Si/m单向重复定位偏差Ri-4Si/m反向差值Bi/m双向重复定
25、位精度Ri/m双向平均位置偏差/m标准JB/T8324.1-1996方向单 向单 向双 向定位精度A/mm重复定位精度R/mm平均反向差值/mm2、补偿参数的设置表十二:位置精度检测与补偿参数表反向间隙(微米)螺补类型(0-无,1-单向,Z-双向,3,4-扩展)补偿点数参考点偏差号补偿间隙偏差值(微米)0偏差值(微米)1偏差值(微米)2偏差值(微米)3偏差值(微米)4偏差值(微米)5偏差值(微米)6偏差值(微米)7偏差值(微米)8偏差值(微米)9偏差值(微米)103、请将以上表格输入到数控系统的相关参数,然后测量出补偿后的数据填入下面表格,并根据测量数据计算出相关的误差值。表十三:机床位置精度
26、测试记录表: 测量记录机床型号机床编号测试轴补偿状态环境温度湿度测试者测试日期序号123456目标位置Pi /mm趋近方向位置偏差Xij(m)j=1234 5数据处理结果单向平均位置偏差/m标准不确定度Si/m2Si/m-2Si/m+2Si/m单向重复定位偏差Ri-4Si/m反向差值Bi/m双向重复定位精度Ri/m双向平均位置偏差/m标准JB/T8324.1-1996方向单 向单 向双 向定位精度A/mm重复定位精度R/mm平均反向差值/mm本环节需要裁判签字确认,否则不得分。 裁判签字确认:数控机床位置精度计算方法及评定标准目标位置Pi :运动部件编程要达到的位置。下标i表示沿轴线选择的目标
27、位置中的特定位置。实际位置Pij(i=0m,j=1n):运动部件第j次向第i个目标位置趋近时的实际测得的到达位置。位置偏差Xij :运动部件到达的实际位置减去目标位置之差,Xij =Pij Pi。单向趋近:运动部件以相同的方向沿轴线(指直线运动)或绕轴线(指旋转运动)趋近某目标位置的一系列测量。符号表示从正向趋近所得参数,符号表示从负向趋近所得参数,如Xij或Xij。某一位置的单向平均位置偏差或 : 运动部件由n次单向趋近某一位置Pi所得的位置偏差的算术平均值。 = 或 = 某一位置的双向平均位置偏差 :运动部件从二个方向趋近某一位置Pi所得的单向平均位置偏差和 的算术平均值。= (+)/2某
28、一位置的反向差值Bi :运动部件从二个方向趋近某一位置时两单向平均位置偏差之差。 Bi=轴线反向差值B和轴线平均反向差值:运动部件沿轴线或绕轴线的各目标位置的反向差值的绝对值Bi中的最大值即为轴线反向差值B。沿轴线或绕轴线的各目标位置的反向差值的Bi的算术平均值即为轴线平均反向差值B=max. Bi =在某一位置的单向定位标准不确定度的估算值Si或Si:通过对某一位置Pi的n次单向趋近所获得的位置偏差标准不确定度的估算值。即Si= 和 Si=在某一位置的单向重复定位精度Ri或Ri及双向重复定位精度Ri Ri=4 Si 和 Ri=4 SiRi =max.2 Si+ 2 Si+Bi; Ri;Ri轴
29、线双向重复定位精度R: 则有 R=max.Ri轴线双向定位精度A: 由双向定位系统偏差和双向定位标准不确定度估算值的2倍的组合来确定的范围。 即 A= max (i+2 Si;i+2 Si)min (i-2 Si;i-2Si)请考生根据所提供的公式,将相关精度的计算过程记录下来:得分第五题:机床工件的加工测试(共7分)请根据所提供的图纸和给定刀具加工出正确的工件注意事项:在进行加工之前,一定要保证卡盘安装正确牢固,防护安装到位,否则不允许进行加工操作。 实操试题a bLhse2020125202545工具、刀具及工件毛坯(参考)1、外圆端面车刀:(株洲钻石)说明:方柄(2020125)、刀尖角
30、35、主偏角95参考刀具型号:MVJNR2020K16 参考刀片型号:VNMG160408-DFa hbLs202020125252、外螺纹车刀:(株洲钻石)说明 :方柄(2020125)、牙形角60、螺距2mm。参考刀具型号:SWR2020K16参考刀片型号:RT16.01W-2GM3、毛坯:38102,毛坯要求车外圆、端面;端面要求平整。4、评分标准:该考评任务共7分。工件合格满分7分。一、工件(配分:7分)序号检测精度允差(mm)实测(mm)配分评分标准(扣完为止)得分1圆弧R150.11每超差0.1扣0.5分2直径尺寸36-0.11每超差0.05扣0.5分333-0.11每超差0.05扣0.5分428-0.11每超差0.05扣0.2分5长度尺寸1000.10.5每超差0.1扣0.2分6740.10.5每超差0.1扣0.2分7螺纹尺寸M3222外径、表面粗糙度、长度不合格各扣0.5
- 温馨提示:
1: 本站所有资源如无特殊说明,都需要本地电脑安装OFFICE2007和PDF阅读器。图纸软件为CAD,CAXA,PROE,UG,SolidWorks等.压缩文件请下载最新的WinRAR软件解压。
2: 本站的文档不包含任何第三方提供的附件图纸等,如果需要附件,请联系上传者。文件的所有权益归上传用户所有。
3.本站RAR压缩包中若带图纸,网页内容里面会有图纸预览,若没有图纸预览就没有图纸。
4. 未经权益所有人同意不得将文件中的内容挪作商业或盈利用途。
5. 装配图网仅提供信息存储空间,仅对用户上传内容的表现方式做保护处理,对用户上传分享的文档内容本身不做任何修改或编辑,并不能对任何下载内容负责。
6. 下载文件中如有侵权或不适当内容,请与我们联系,我们立即纠正。
7. 本站不保证下载资源的准确性、安全性和完整性, 同时也不承担用户因使用这些下载资源对自己和他人造成任何形式的伤害或损失。