年产10000吨电锌厂焙烧车间初步设计课程设计
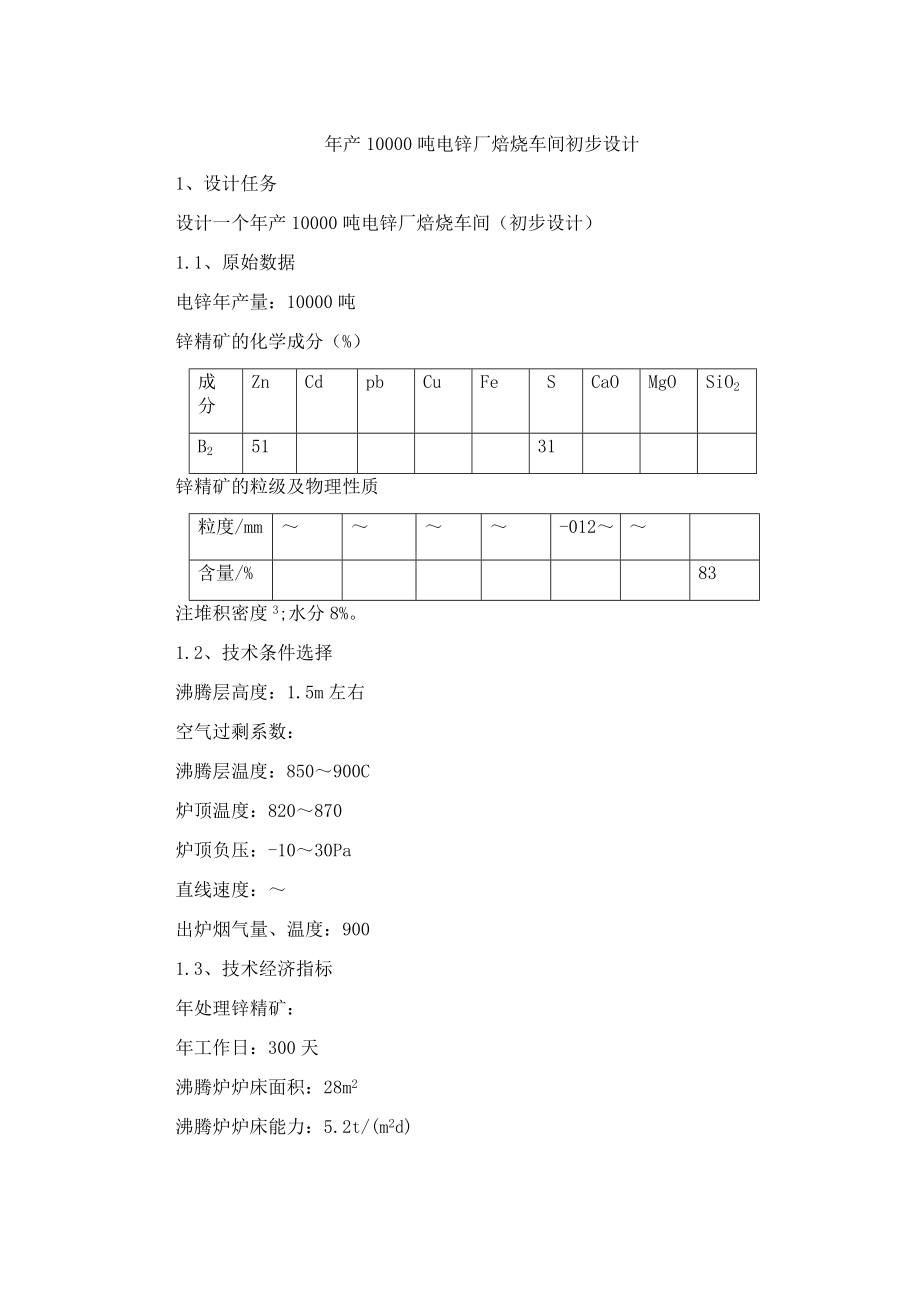


《年产10000吨电锌厂焙烧车间初步设计课程设计》由会员分享,可在线阅读,更多相关《年产10000吨电锌厂焙烧车间初步设计课程设计(44页珍藏版)》请在装配图网上搜索。
1、年产10000吨电锌厂焙烧车间初步设计1、设计任务设计一个年产10000吨电锌厂焙烧车间(初步设计)1.1、原始数据电锌年产量:10000吨锌精矿的化学成分(%)成分ZnCdpbCuFe SCaOMgOSiO2B25131锌精矿的粒级及物理性质粒度/mm-012含量/%83注堆积密度3;水分8%。1.2、技术条件选择沸腾层高度:1.5m左右空气过剩系数:沸腾层温度:850900C炉顶温度:820870炉顶负压:-1030Pa直线速度:出炉烟气量、温度:9001.3、技术经济指标年处理锌精矿:年工作日:300天沸腾炉炉床面积:28m2沸腾炉炉床能力:5.2t/(m2d)焙烧矿产出率(包括烟尘和焙
2、砂):88%(占锌精矿的)烟尘含锌量:54.89%焙砂含锌量:56.91%焙烧料含锌量:48%脱硫率:93.6%焙烧锌直收率:52%冶炼总回收率:95%出炉烟尘含量:35%(占焙烧矿的)出炉烟气SO2量:9365%(体积百分数)烟尘含Ss量:1.73%焙砂含Ss量:0.4%烟尘含Sso42-量:2.14%焙砂含Sso42-量:1.10%炉 型 煤低位 热值 / c a/ kg 燃烧 温度 灰渣含 碳量 % 煤耗 kg/t 投资 / 万元 层燃式手烧炉 5000 600 18 40 8 喷燃式煤粉炉 6000 900 12 30 12 普通沸腾炉 4500 700 8 28 16 节煤型沸腾炉
3、3000 1100 4 18 16 2、原始资料、锌矿的分布及品位 截至2002年,全世界查明锌储量为20000万吨,储量基础为45000万吨,现有储量和储量基础的静态保证年限为23年和51年。锌储量和储量基础占锌资源量的和。中国锌的储量和储量基础均居世界首位,已成为世界最大的铅锌资源国家。根据统计资料,在我国铅锌储量中铅锌平均品位只有 4.66%,而根据目前铅锌价格水平和成本水平,只有铅锌(1:2.5)合计地质品位在78以上的地质储量才是能经济利用的储量,目前我国能经济利用的铅锌合计储量只有万吨,仅占总储量的 42.6%。锌在自然界多以硫化物的状态存在,主要矿物是闪锌矿(ZnS),但这种硫化
4、矿的形成过程中有FeS固溶体,成为铁闪锌矿(nZnSmFeS).含铁高的闪锌矿会使提取冶炼过程复杂化。流化床的地表部位还常有一部打分被氧化的氧化矿,如菱锌矿(ZnCO3)、硅锌矿(Zn2SiO4)、导极矿(H2Zn2SiO5)等。 我国铅锌储量较多的省(区)主要是云南、广东、甘肃、四川、广西、内蒙古、湖南和青海等八省(区),其铅锌储量占全国总储量的80.7%。大中型锌矿187处,探明资源总量7961万吨,储量1950万吨,其中大型锌矿区44处,探明资源总量5352万吨,储量 1553万吨,分别占全国的 58.1%和76.6%。 目前已探明的储量主要集中在云南、广东、内蒙古、江西、湖南和甘肃等六
5、省。各大区储量见下表: 中国铅锌资源各大区分布比例(%)表中国中南西南西北华北华东东北100%14%2.2、精矿的组成成分铅锌矿的开采分露天开采和地下开采两种。由于金属品位不高,铅锌共生,并含有大量的脉石和其他杂质金属,矿石需先经过选矿。通过采用浮选法优先选出锌精矿,副产铅精矿和硫精矿。我国某些大型企业铅锌矿产出的锌精矿成分实例如下表。硫化锌精矿是生产锌的主要原料,成分一般为:锌45%46%,铁5%15%,硫的含量变化不大,为30%33%。可见,锌精矿的主要组分为Zn,Fe和S,三者占总重的90%左右。硫化锌精矿是生产锌的主要原料,成分一般为:Zn4560%,Fe515%,S3033%,浮选精
6、矿粒度较细,90%为0.07mm,堆密度1.72.0g/cm3。 锌精矿化学成分等级含锌量(%)杂质不大于(%)CuPbFeAsSiO21552503454402.0锌精矿成分实例(%)表精矿来源ZnPbSFeCuCdAsSbSiO2Ag(g/t)湖南某矿山80黑龙江某矿山85广东某矿山1180甘肃某矿山33硫化锌精矿的粒度细小,95%以上小于40um,堆密度为1.72g/cm3.在选用精矿氧化焙烧脱硫设备时,应当充分利用精矿粒度小、表面积大、活性高、硫化物本身也是一种“燃料”的特点,使硫化锌能迅速氧化成氧化锌,又能充分利用精矿的自身的能量。、锌精矿的物理及化学性质锌精矿一般是由铅锌矿或含锌矿
7、石经破碎、球磨、泡沫浮选等工艺而生产出的达到国家标准的含锌量较高的矿石。精矿在空气的氧化开始是在颗粒的表面进行的。当精矿粒度较小时,会有更多的气固接触,单位面积内反应的硫化锌就会增加。但随着反应的进行,粒子表面形成一层坚硬的氧化锌壳,于是气流中的氧化分子穿过氧化锌层才能到达反应界面,增加了氧气的扩散阻力,从而减慢了硫化锌例子中心部分的氧化程度,所以粒度较小的精矿有利于扩散过程,保证硫化锌氧化得更完全。矿物物相组成:其物相包括:ZnS、CdS、PbS、CCuFeS2、FeS2、Fe7S8、CaCO3、MgCO3、SiO2其他等。2.4、锌的用途(1). 钢材的镀锌方面,起防腐作用。 (2). 优
8、良的合金,如做装饰品的铜锌合金(黄铜),Cu-Sn-Zn形成的青铜,作为耐磨合金的Cu-Sn-Pb-Zn合金。 (3). 锌可以制造用于航天仪表上的Ag-Zn电池。 (4). 利用Zn熔点低的特点,还可浇铸精密铸件。 (5). 锌在冶金工业中作为还原剂,化学工业中作为制造颜料用的原材料。 2.5、结构设计的注意点(1)、为便于操作,炉篦深度不宜超过2mm;沿炉篦宽度设一个炉门。(2)、炉膛高度以易于操作为原则。(3)、炉膛长宽比宜选用3:1。(4)、炉膛应成断面放大式,与垂直面成22。(5)、炉膛内最边壁的风帽与炉内壁距离为20-30mm。(6)、筑砌内、外层耐火砖、红砖时砖缝要错开,且之间要
9、有搭接砖。(7)、外层砖筑砌完后,外圈要用钢架拉起来,以增加其钢性、整体牢固性。(8)、当用煤量大于180kg/h时,加煤应采用机械加煤、出渣。(9)、合理、合适的挡火墙高度有利于控制进入烘干机的热气体温度,避免烧坏烘干机筒体前端。(10)、穿过沸腾炉的喂料管,要外敷耐热混凝土或选用耐高温的耐热不锈钢,并做好之间的密封。(11)、沸腾炉出气口附近要装设测温热电偶,以利于控制出气烟气温度。3.、锌沸腾炉焙烧工艺流程3.1、火法炼锌工艺流程 火法炼锌工艺流程图火法炼锌的基本原理就是将氧化锌在高温下用碳质还原,并利用锌沸点低的特点,使锌以蒸气挥发,然后冷凝为液体锌。以竖缺罐炼锌为例,其原则工艺流程如
10、上图。 3.2、湿法炼锌工艺流程 湿法炼锌主要有焙烧、浸出(见浸取)、浸出液净化和电积等工序。锌精矿焙烧后用电解废液进行中性浸出,使大部分氧化锌溶解,得到的矿浆分离出上清液和底流矿浆。上清液净化后电积产出金属锌,熔铸成锭。底流矿浆进行酸性浸出以溶解残余的氧化锌,酸性浸出液返回到中性浸出;含锌约20的酸性浸出渣,须进一步处理,传统方法采用回转窑挥发,回收其中的锌、铅和湿法炼锌工艺流程部分稀散金属焙烧使精矿中的硫化锌转变为可溶于稀硫酸的氧化锌,即酸溶锌。湿法炼锌是第一次世界大战期间开始应用的。其本质是用稀硫酸(即废电解液)浸出焙烧矿中的锌,锌进入溶液后再以电解法从溶液中沉积出来。湿法炼锌可直接得到
11、很纯的锌,不象火法蒸馏炼锌还需精炼。除此之外,操作所需劳动力较少,劳动条件也较好,只是电能消耗大。3.3、沸腾炉焙烧工艺流程 高温氧化流态化焙烧工艺流程图备料工序送来的混合锌精矿送入炉前仓,再由仓下调速胶带给料机、定量给料机,计量后由分配圆盘分别加到两台抛料机上,将混合精矿抛入焙烧炉内。焙烧炉产出的焙砂经两台流态化冷却器和高效圆筒冷却机进一步冷却至150左右。冷却后的焙砂经埋刮板运输机送到球磨机室进行球磨,磨细后的焙烧矿与烟尘混合用汽化喷射泵送制液车间浸出制液。沸腾焙烧炉产出的烟气经余热锅炉回收烟气余热后,经两段旋涡收尘器、电收尘器收尘后由排烟机送制酸系统。火法炼锌和湿法炼锌的第一步冶金过程就
12、是焙烧。其中火法炼锌厂的焙烧是纯粹的氧化焙烧,湿法炼锌厂进行的也是氧化焙烧,但焙烧时要保留少量的硫酸盐,以补偿浸出和电解过程中损失的硫酸。同时希望尽可能少生成铁酸锌。1300K 当焙烧温度一定时,焙烧过程中锌的存在形态取决于pSO2和pO2。如图中A点和B点。 当气相组成不变,改变焙烧温度时,也可改变焙烧产物中锌存在的形态。如图中红线所示,当温度升高时,ZnO区域扩大,ZnSO4稳定区缩小。在实际的锌精矿焙烧过程中,就是通过控制焙烧温度和气相组成来控制焙烧产物中锌的存在形态。生产中通过控制供风量(空气过剩系数)来调节气相组成。 火法炼锌的焙烧温度一般控制在1273K以上,有的达到1340137
13、0K。空气过剩系数为。湿法炼锌的焙烧温度一般控制在11431193K,有的达到1293K。空气过剩系数为。3.4、沸腾炉焙烧原理3.4.1、锌精矿焙烧反应一般规律 流态化焙烧的理论基础是固体流态化,当气体通过固体料层的速度不同时,可将料层变化分为三种状态:即固定床、膨胀床及流态化床。锌精矿沸腾焙烧就是利用具有一定气流速度的空气自上而下通过炉内矿层,使固体颗粒被吹动,相互分离而呈悬浮状态,达到固体颗粒(锌精矿)与气体氧化剂(空气)的充分接触,以利化学反应的进行。主要化学反应为: 2ZnS3O22ZnO2SO2.(1) ZnS2O2ZnSO4 (2) ZnOSO2+1/2O2ZnSO4(3) 3Z
14、nSO4ZnS=4ZnO4SO2(4) 最新的理论认为硫酸锌的生成实际上要经历一个生成碱式硫酸锌的过程: 3ZnS+11/2O2=ZnO2ZnSO4+SO2(5) ZnO2ZnSO4+SO2+1/2O2=2ZnSO4(6)3.4.2、锌精矿焙烧动力学过程及机理 金属硫化物的氧化反应是一个气、固相的多相反应过程,过程很复杂。反应分成以下几步骤: (1)氧分子经扩散到达硫化物表面; (2)氧分子在硫化物表面被吸收,并分解成为活性氧原子; (3)氧原子向硫化物晶格中扩散,与金属离子和硫阴离子结合生成金属氧化物和吸附态的SO2; (4)SO2分子从固体表面解吸扩散到气相中。、传热原理 流态化床的热传递
15、可分为三种形式,即固体与气体间、流态化床内各部分之间、流态化床与管壁之间的热传递。传热方式主要是对流。由于流态化床内固体与气体之间接触多,有效传热面积大,故总的传热效率比固定床大。 由于流态化床内固体颗粒快速循环以及气流使床层激烈搅动,因而流态化床内各部分的温度几乎一致,就是在大量放热反应的焙烧过程中,床层内积分的温度仍能保持均匀一致,这对焙烧过程是非常有利的条件。在生产实践中可以控制床层内温度差在10K波动。3.5、硫酸化焙烧 当进行硫酸化焙烧时,进行下列反应: ZnSO4 = ZnO + SO3 ZnO2ZnSO4 = 3ZnO + 2SO3 SO2 + 1/2O2 = SO3 在实际焙烧
16、过程中, pT在范围内,此时与温度关系如图所示。总压曲线pT与ZnSO4和ZnOZnSO4的分解曲线相交于A、B和A、B。当温度低于A、A点所对应的温度时,ZnSO4稳定存在,当温度高于B、B点所对应的温度时,ZnO稳定存在,当温度介于两者之间时, ZnOZnSO4稳定存在。因此控制一定的压力和温度,可使ZnS氧化成所需要的产物。硫化物的焙烧氧化过程是从表面向内部进行的,反应前期生成的氧化物层必然会对氧分子的向内扩散和SO2分子的向外扩散起阻碍作用,使反应速度下降,固体颗粒越大,扩散所需的时间越长,也就是完成反应的时间越长,如果在生产条件下不能满足这个时间的要求,氧化过程就不能进行彻底,造成焙
17、烧产物含硫上升,质量下降。所以硫化矿的粒度是焙烧质量的一个重要条件。当处于低温焙烧时, SO2通过氧化物层扩散,还会与氧气和氧化物进行反应,使得硫酸盐大量增加。在工业上采用提高O2浓度的方法来强化焙烧过程。除此之外,温度对扩散过程有决定性的影响,较高的温度能加速气体的扩散,在工业上将控制焙烧温度作为控制焙烧反应速度的重要手段。决定硫化锌精矿氧化焙烧速度的控制环节:(1) 氧通过颗粒周围的气膜向其表面扩散(外扩散);(2) 氧通过颗粒表面的氧化物层向反应界面扩散(内扩散);(3) 在反应界面上进行化学反应;(4) 反应的产物SO2向着与氧相反方向的扩散。反应速度是由以上四个环节中最慢的环节来决定
18、。硫化锌矿氧化生成的氧化锌层比较疏松,对氧和SO2的扩散阻力不大,因此决定反应速度的环节是气膜中氧的扩散和界面反应。在830以下,界面反应的阻力占主要地位,880以上,气膜传质的阻力占绝对优势。颗粒粒度的减小有利于界面反应,也有利于扩散过程,但不能过小,否则增加烟尘率。 焙烧过程中只要减少Fe2O3的生成,就可以较少铁酸锌的生成。从图中可以看到,当焙烧温度一定时,lgpO2时,Fe2O3分解为Fe3O4,这样可以减少产物中铁酸锌的生成。提高焙烧温度可使Fe3O4的稳定区域扩大,也减少铁酸锌的生成。因此,焙烧过程中一定要维持低氧分压和适当提高焙烧温度。锌精矿流态化酸化焙烧流程图3.6、焙烧的目的
19、和要求1)锌精矿焙烧的目的 将精矿中的ZnS尽量氧化成ZnO,同时让铅、镉、砷等杂质氧化变成易挥发的化合物从精矿中分离。使精矿中硫氧化成SO2,产出足够浓度的SO2烟气供制酸。2)锌精矿焙烧的要求尽时能完全地氧化金属硫化物,并在焙烧矿中得到氧化物及少量硫酸盐;使砷和锑氧化,并以挥发物状态从精矿中除去;在焙烧时尽可能少地得到铁酸锌,因为铁酸锌不溶于稀硫酸溶液;得到细小粒子状的焙烧矿以利于后序工作浸出的进行。3.7、锌冶炼时的综合回收: 硫:在沸腾焙烧烟气中回收. 铅:在氧化锌浸出渣中回收. 金,银:在浸出渣中用浮选法回收为精矿. 镉:在铜镉渣中予以回收. 铜:在铜镉渣中予以回收. 铟,镓,锗:在
20、铟锗渣中回收. 钴:在净液时以钴渣形式回收. 铊:在除氟氯过程中(多膛炉或回转窑)的烟尘中回收3.8、锌精矿焙烧操作控制、影响因素及生产故障处理 锌精矿的氧化过程是复杂的多相反应过程,与许多因素有关,为保证焙烧炉的的正常操作,应加强对主要影响因素的控制。.1、开炉正常开炉是指焙烧炉从常温开始升温到达正常条件的全操作过程,开炉所用时间4872h,临时停炉后的开炉是指从当前状态开始达到正常工艺操作条件的全操作过程。3.8.2 正常操作条件的控制与调整1)物料的物理化学性质。物料颗粒愈小,比表面积愈大,就愈有利于焙烧,但颗粒也不宜太细,如颗粒过细,在生产中会形成过多的烟尘量,影响焙烧的正常运行工况2
21、)沸腾层温度 流化层的温度主要是通过调整加料量、鼓风量以及二者之间的比例来控制的。在正常操作下流态化层的温度都是比较稳定的,有时由于精矿含硫品位、加料量和鼓风量的波动会使温度发生变化。随着温度的升高,氧化过程的总速度加快。但是温度太高,会发生烧结现象不利于焙烧。沸腾炉正常运行工况下,沸腾层温度控制在850 950。在正常操作中,沸腾层温度分布均匀,各点温差不超过10,而且温度变化趋势也很一致,当温差变化大或温度趋势发生背离时,应考虑到炉内出现局部不沸腾等故障。3)烟气温度 烟气温度只作为操作参考而不作为控制对象。烟气温度测点设于炉顶或烟气出口,一般情况下,烟气温度和沸腾层温度有一个相对固定的温
22、差。当精矿含水少或粒度过细时,会进入上部空间燃烧,使烟气温度上升,此时,烟尘量增大,烟气系统的热负荷也上升,烟尘品质下降。4)鼓风量与过剩空气系数 一定的鼓风量即要维持焙烧炉的沸腾状态,又要为焙烧提供一定的过剩空气系数。鼓风量决定于加料量,应通过冶金计算来确定。实际鼓风量应高于理论鼓风量,两者的比值称为空气系数。空气系数一般为1.051.20,空气系数太大会使烟气量增大使SO2浓度降低,设备负荷增大。反之会使焙砂质量下降,甚至造成工艺事故,因此鼓风量的调整应与加料量调整同步进行。根据经验计算1吨精矿鼓风需求量为15001800Nm3/t。5)风箱压力 风箱压力不作为控制对象,只是炉况的参考。它
23、是沸腾层和炉床阻力的情况的反映。在正常生产中,风箱压力会很缓慢地上升,这是由于炉内会出现风帽堵塞,大颗粒沉积和烧结物的原因。在鼓风量变化后,风箱压力也会发生微小变化,过一段时间后回复到原来的值,这是因为沸腾层的密度变化需要一段时间才能稳定。当箱压力出现突然变化,则说明炉内发生了异常情况。6)加料量 加料量是一个重要的控制参数,它决定了沸腾层温度和鼓风量,以及烟气温度,加料量的任何变化都会引起主要操作参数的控制指标的变化。对一定金属锌产量,加料量的大小决定于精矿中Zn品位, Zn品位低时,加料量相对较大,高时加料量相对较小,所对对加料量的调整除根据炉况外,还应根据精矿中Zn的品位进行。应将焙砂和
24、烟尘残硫作为加料量调整的重要参考。在鼓风量与加料量匹配且温度正常时,如果残硫高于控制上限,则应考虑减少加料量以使精矿在炉内有足够的停留时间充分氧化。7)炉顶压力 炉顶压力测点位于烟道口,其控制范围在+30-30Pa之间,对炉顶压力控制原则是使烟气能顺利进入烟气系统,并尽量保持较高的SO2浓度,烟道不产生烟气泄漏。通过调节排烟机导叶开度来控制这个压力。生产故障处理1)低风量操作 焙烧炉有时因各种原因需降低加料量操作鼓风量降至额定鼓风量75%以下称之为低风量操作。低风量操作时,最低鼓风量不能低于额定鼓风量的50%,并将操作温度控制在870920,每隔23h将鼓风量升至额定鼓风量的90100%鼓风1
25、3 min再降下来。低风量操作时,可以暂停排料13h,这个时间也可以根据风箱压力上升的情况决定。在生产中不宜长时间处于低风量的操作,它会使大颗粒沉积速度增加,并易发生局部烧结。2)停电故障 停电故障,指无事先准备的突然停电,此时最重要的是做好炉内保温。立即关闭焙烧炉的加料口,做好再次开炉前的各项准备工作,来电后,首先启动热力系统,然后按短期停炉后的开炉方法进行操作,如果炉内有烧结现象,可用压缩空气翻吹烧结部位,直到沸腾正常,风箱压力处于合理范围。3)炉内烧结 炉内发生烧结时,风箱压力会在短时间内明显变化。各温度点温差增大,溢流焙砂量减少。当出现上述征兆时,首先应停止加料以防烧结进一步恶化,待炉
26、温降到880后停止鼓风,用钢钎等工具找出烧结部位,用压缩空气翻吹烧结部位,并反复用大风量翻动沸腾层,风箱压力恢复到正常范围即可开炉加料。4)炉底沉积 由焙砂中的大颗粒物料引起。大多数焙烧炉在操作一段时间后都会出现这个现象,物征是风箱压力不断上升。定期增大鼓风量可以部分排出这些大颗粒沉积物。但无论采取哪种方法都不可能消除炉底沉积,因此当风箱压力上涨到一定程度时,就应停炉对炉床进行彻底清理。减缓炉底沉积的最重要的手段是严格控制精矿粒度,尤其是防止硬块,石块金属杂物等进入炉内。另外应根据精矿的成份控制炉温。例如精矿含铅上升时,应适当降低焙烧温度以减缓颗粒“生长”的速度。5)炉壁结块下塌 炉壁结块下塌
27、一般发生在短期停炉后的开炉初期,炉壁上的结块因热胀冷缩的原因与壁面结全松动而滑塌,如果下塌面积小可以不作处理继续操作,如果下塌面积大而导致风箱压力发生变化,则应按烧结故障方法处理。3.9、沸腾焙烧炉及主要附属设备的结构、性能(1)、沸腾焙烧炉(以109m2沸腾炉为例)1) 沸腾焙烧炉炉壳由钢板焊接而成,内补粘土砖,局部易受腐蚀的部分使用高铝砖。炉壳外面覆盖保温材料以确保钢板不受大气腐蚀。2) 风箱 风箱处于炉子下部,呈倒锥形,主要作用是使入炉的空气沿炉底均匀分布,要求有足够的容积。 空气分布板采用直通式。3)炉床 炉床位于焙烧炉底部,风箱上部,由分布板、风帽、炉底捣打料等组成。炉床的面积决定于
28、焙烧炉的生产能力,它的主要使用之一是使进入风箱的空气沿焙烧断面均匀分布,使炉内物料沸腾。109m2沸腾焙烧炉在炉底下部是分布板由钢板钻孔制成,风帽焊接在分布板的孔眼上,根据炉型的不同,风帽的排布方式采用正方型棋盘式排布。 炉床耐火混凝土采用矾土水泥,厚200240mm,与风帽上端面平。4) 风帽109m2沸腾焙烧风帽采用直孔式风帽,和一般的风帽相比,直孔式独孔风帽有以下优越性:a 出口气流流速大,可达40m/s,不易堵塞,在运转一年后其堵塞率不超过30%。b 风帽基本上不会出现烧损,适合高温焙烧要求,寿命长,运行成本低。C 风帽容易清理。5) 炉体 109m2沸腾焙烧炉采用扩大型,经扩大后上部
29、空间断面积为209m2,气体流带从下部直线段从0.55m/s降低到0.27m/s。焙烧总高为17m,炉底到烟气出口高度13.4m,炉壁用粘土砖砌筑,在炉壳和粘土砖之间砌一层保温砖。在下部沸腾层区域有冷却装置安装孔和人孔,在距炉底1.8m处设有开炉燃烧孔。排料口下缘炉底940mm。排料口用异形砖砌筑以留出安装溢流高度调节板的槽,使沸腾层高度可以在940mm到1060mm之间。与溢流口相对的是两个加料口,其中心距炉底1800mm,在满足加料的条件下,加料口应尽量小,以减少漏风量。在直段还设有电偶孔,喷水孔,在底部炉墙上还设有底流排放孔和排放装置。(2)沸腾层冷却装置 沸腾层的冷却装置采用冷却盘管,
30、主要作用是导出沸腾层的热量以使焙烧温度保持在要求的范围。冷却装置一般与余热锅炉共用一套热力系统,压力为4.4Mpa,盘管受热面积为40.2m2。这种冷却盘管具有寿命长,工作压力高,设备紧凑等优点。主要缺点是管束悬空,固定困难,最下排管受焙砂冲刷腐蚀严重,使用寿命为二年。(3) 焙砂冷却设备 从溢流口和锅炉排出的物料需冷却后才能进行输送和细磨。溢流焙砂由流态化冷却器和圆筒冷却器冷却。流态化冷却器冷却效率高,结构简单,体积小,能耗低,故障小。焙砂入口温度1000,经流态化冷却器后降至500 ,与锅炉烟尘混合后再进入冷却圆筒进一步冷却。冷却圆筒是一个五腔室的筒型旋转体,在腔室之间是冷却水。焙砂从头部
31、进入腔室之后在螺旋叶片的拔动下向尾部运行,通过腔壁与水发生热交换。圆筒冷却器处理量为18t/h,焙砂入口温度500 ,出口温度可降至143 ,冷却水循环量210t/h,温差25 。(4) 焙砂输送设备 焙砂短距输送采用刮板运输机,刮板运输机具有耐高温、密封性好、结构简单、维护简便、维护简便、能源消耗少等优点。长距离输送采用气动输送,采用气动输送设备的优越性在于基本不受现场配置的约束,设备紧凑,占地面积少。主要缺点是管道发生堵塞时处理困难,动力消耗大,对收尘装置的要求高,粉尘飞扬量大造成金属损失和环境污染。4、锌精矿沸腾焙烧冶金计算4.1、锌精矿物相组成计算 锌精矿平均化学成分为(%):ZnCd
32、PbCuFeSCaOMgOSiO25131 根据精矿的物相分析,计算精矿中各元素呈下列化合物的形态:Zn、Cd、Pb、Cu、Fe呈硫化物:ZnS、CdS、PbS、CuFeS2、Fe7S8和FeS2;脉石中的Ca、Mg、Si分别呈CaCO3、MgCO3、SiO2形态存在。以100公斤锌精矿(干量)进行计算。4.1.1. ZnS量: 公斤 其中Zn: 公斤 S: 公斤 4.1.2. CdS量: 公斤其中Cd: 公斤 S: 公斤 4.1.3. PbS量: 公斤其中Pb: Pb=1.8 公斤 S: S=0.28 公斤 4.1.4. CuFeS2 量 : 公斤4.1.5.Fe7S8和FeS2量 CuFe
33、S2中的Fe为0.27公斤,余下的铁量为:除去ZnS、CdS、PbS和CuFeS2含S,余下S量为:此S分布于Fe7S8和FeS2之间。 设:FeS2中Fe为X公斤,S为Y公斤,可列如下方程式:FeS2: Fe7S8: 解方程式得:X=0.36 Y即FeS2中:Fe =3.92 公斤 S =4.51 公斤 FeS2=0.77 公斤 Fe7S8中: Fe=7.93-0.36=6.57 公斤 S=5.37-0.41=4.96 公斤 Fe7S8=11.53 公斤4.1.6.CaCO3量: 公斤其中: CaO=1.4公斤 CO2 4.1.7.MgCO3量: 公斤其中: MgO= 0.5公斤 CO2=
34、计算结果如下表所示: 锌精矿物相组成(公斤)组成ZnCdPbCuFeSCaOMgOCO2SiO2其他共计ZnS51CdSPbS2.08CuFeS2FeS2Fe7S8CaCO3MgCO3SiO2其他共计51100、烟尘产出率及其化学和物相组成计算 矿产出率一般为锌精矿的88%,而烟尘产出率占烧结矿的4550%,取50%,则烟尘量为:88x0050=44公斤。 根据生产实践,镉60%进入烟尘,锌48%进入烟尘。其他组分在烟尘中的分配率假定为50%。 各组分进入烟尘的数量为: Zn=510.50=0.25公斤 SiO20.5=0.915公斤 生产实践,烟尘中残硫以硫酸盐形态SSO42-为2.14%,
35、以硫化物形态Ss为1.73%。PbO与SiO2结合成PbOSiO2,余下SiO2为游离形态,其他金属为氧化物形态存在。 各组分化合物进入烟尘中的数量如下:Ss量:000.0173=0.761公斤 SSO42-量:1004.2.1.ZnS量: 公斤其中:Zn=1.555 公斤 S=0.761 公斤4.2.2.ZnSO4量: 公斤其中:Zn=1.925 公斤 S=0.942 公斤 O=1.884 公斤4.2.3. ZnOFeO3量:烟尘中Fe先生成Fe2O3。其量为: 公斤Fe2O3有1/3与ZnO结合成ZnOFeO3,其量为:公斤ZnOFeO3量:公斤余下的FeO34.2.4 ZnO=4.2.5
36、. CdO量: 公斤4.2.6. CuO量:CuO CuO= 公斤4.2.7. PbOSiO2量: 公斤与PbO结合的SiO2量: 公斤 余留之SiO2烟尘的物相组成(公斤)组成ZnCdCuPbFeSsSso42-CaOMgOSiO2O其他共计ZnSZnSO4ZnOZnOFeO3Fe2O3CdOCuO0.376PbOSiO2CaOMgOSiO2其他共计%100、焙砂产出率及其化学和物相组成计算沸腾焙烧时,锌精矿中各组分转入焙砂的量为: MgO=0.5-0.25=0.25公斤 SiO2按生产实践,焙砂中Sso42-取1.10%,Ss取0.4%,Ss和Sso42-全部与Zn结合:PbO与SiO2结
37、合成PbOSiO2,其他金属为金属氧化物形态存在。预定焙砂重量为:88x0.55=44公斤 各组分化合物进入焙砂的数量如下:Sso42量: Sso42=44Ss量: Ss=444.3.1.ZnSO4量: ZnSO4=公斤4.3.2.ZnS量: ZnS=公斤4.3.3.ZnOFe2O3量:焙砂中Fe先生成Fe2O3,其量为: 公斤Fe2O3有40%与ZnO结合生成ZnOFe2O3,其量为公斤ZnOFe2O3量:ZnOFe2O3=公斤余下的Fe2O34.3.4 ZnO=公斤4.3.5.CdO量:CdO=公斤4.3.6.CuO、PbSiO2等的数量与烟尘相同焙砂的物相组成计算结果表组成ZnCdCuP
38、bFeSsSso42-CaOMgOSiO2O其他共计ZnSZnSO4ZnOZnOFeO3Fe2O3CdOCuOPbOSiO2CaOMgOSiO2其他共计20%100、焙烧需要的空气量及产出烟气量与组成计算假定95%的硫生成SO2,5%的硫转化成SO3,需要的O2量则为:由烟尘和焙砂中得,氧化物和硫酸盐的含氧量为:因此,100公斤锌精矿(干量)焙烧需要理论氧量为:空气中氧的重量百分比为23%,则需要理论空气量为: 公斤 为了加速反应的进行,提高设备生产能力,实际鼓风量比理论空气量要大,对于湿法炼锌的沸腾焙烧,按工厂实践,过剩空气系数可取1.25,故实际需要空气量为: 空气中各组分的重量百分比为:
39、N277%、O223%。鼓入232.89公斤空气,其中: N20.77=179.32公斤 O23 ,实际需要空气之体积为: 标米3空气中各组分的体积百分比为:N277%、O223%其中:N20.79=143.46 标米3 O20.23=37.84 标米3沸腾炉排出烟气量和组成为:.焙烧过程中产出量: SO2 SO3.CaCO3和MgCO3分解产出CO2.锌精矿及空气带水分产生的水蒸气量:进入沸腾焙烧炉的锌精矿含一定量水分,取8%,即100公斤干精矿带入水分为: 空气带入水分量计算:。换算为此条件下空气需要两为:33,带入水分量为:体积:3 烟气和组成计算结果表 组 成重 量(公斤)体 积(标米
40、3)体 积 比(%)SO2SO3CO2N2O2H2O共计、沸腾焙烧物料平衡 沸腾焙烧物料平衡表 加 入 产 出名 称公 斤 % 名 称公 斤 %干锌精矿烟尘精矿中水分焙砂干空气烟气空气中水分共计共计、热平衡计算、热收入 进入沸腾焙烧炉热量包括反应热及精矿,空气和水分带入热量登。.1.硫化锌按下式反应氧化放出之热量为Q1:ZnS+1O2= ZnO+SO2+105930千卡生成ZnO之ZnS量:(20.21+0.79+17.69+0.96)=54.92公斤 Q1= 千卡.2.硫化锌按下式反应硫酸盐化放出之热量为Q2:ZnS+2O2=ZnSO4+185050 千卡 生成ZnSO4之ZnS量: 公斤
41、Q2= 千卡.2O3按下式反应生成ZnOFe2O3放出之热量为Q3:ZnO+Fe2O3=ZnOFe2O3+27300 千卡 生成ZnOFe2O3之ZnO量:(0.79+0.96) Q3 = 千卡.2按下列反应氧化放出热量为Q4 4FeS2+11O2=2Fe2O3+8SO2+790600千卡 Q4= 千卡.5. FeS按下列反应氧化放出热量为Q5 2FeS+O2=Fe2O3+2SO2+293010千卡 Fe7S8 CuFeS2 Q5= 千卡.6. CuFeS2和Fe7S8分解得到硫燃烧放出热量为Q6 2CuFeS2=Cu2S+2FeS+S2 分解出S量:公斤 Fe7S8=7FeS+S2 分解出S
42、量:公斤 1公斤硫燃烧放出热量为2222千卡 Q6=(0.0759+0.57)2222=1435千卡.7 PbS+3/2O2=PbO+SO2+100690千卡 PbO+SiO2=PbOSiO2+2030千卡生成PbO放出热量:千卡生成=PbOSiO2生成=PbOSiO2放出热量:千卡 Q7=875.57+14.488=890千卡.8 CdS+3/2O2=CdO+SO2+98800千卡 Q8= 千卡.2S按下式反应氧化放出热量为Q9 Cu2S+2O2=2CuO+SO2+127470千卡 生成CuO之Cu2 Q9=千卡.10 进入沸腾炉焙烧的锌精矿温度为40 Q10=100400.2=800千卡
43、.11,空气温度为20 Q11200.316=1220千卡.,100公斤精矿中由水分带入热量为Q12Q12401.0=350千卡 热量总收入Q总数为: Q总数=Q1+Q2+Q3+Q4+Q5+Q6+Q7+Q8+Q9+Q10+Q11+Q12 =59730+8246+731+1270+20679+1435+890+246+520+800+1220+350=96117千卡、热支出 .烟 炉顶烟气温度900,各组分比热为(千卡/米3)SO2SO3CO2N2O2H2O比热 Q烟0.403)900=61290千卡 .尘(有炉中出来焙砂温度为850) Q尘8500.2=7540千卡 .焙 由炉中出来焙砂温度为
44、850 Q焙8500.2=7540千卡 .蒸 Q蒸= G水t水C水+G水r40575=5350千卡4.6.2.分1(1公斤CaCO3分解吸热378千卡/公斤,1公斤MgCO3分解吸收314千卡/公斤)Q分1=3782.5+3141.36=1183千卡 .2和Fe7S8分解吸收之热量为Q分2(按1公斤Fe消耗热量为222千卡计)Q分2=(0.27+6.57)222=1518千卡.散(散热损失均为热收入的5%)Q散=961170.5=4806千卡 .剩 Q剩=Q总-(Q烟+Q尘+Q焙+Q蒸+Q分1+Q分2+Q散) =96117-(61290+7815+6780+5350+1183+1518+480
45、6)=7375千卡热 收 入热 支 出项 目千卡 %项 目千卡 %焙烧反应热烟气带走热61290ZnS氧化生成ZnO59730烟尘带走热7815ZnS转化成ZnSO48246焙砂带走热6780ZnO和Fe2O3生成ZnOFe2O3731水分蒸发带走热5350FeS2氧化成Fe2O31269碳酸盐分解1183FeS氧化成Fe2O320679CuFeS2和Fe7S8分解1518分解硫燃烧1435炉壁及炉顶散热4806PbS生成PbOSiO2890剩余热7375CdS氧化成CdO246Cu2O氧化成CuO520精矿带走热800空气带走热1220水分带走热350共计96117100共计96117100
46、5、沸腾炉的计算与效果5.1、沸腾炉结构沸腾炉结构由炉床、炉膛、混合室等三部分组成,如图所示。 沸腾炉结构1. 进料口 2.排渣口 3.均风箱 4.布风板 5.炉门 6. 风帽图中,炉床部分包括均风箱、布风板、风帽、出渣口等;炉膛部分包括垂直段、扩散段、悬浮段及炉门。沸腾炉的设计,从结构上充分满足了流体力学和热力学原理。沸腾炉的燃料采用从炉门上方呈正负压分界处喂入的结构,可促使燃料和热渣均匀混合及充分燃烧。也有利于热烟气在扩散段释放并由风机抽入换热装置混合。沸腾炉的炉门设为一个,作看火、调火和检修使用,炉门需方便耐火砖活砌或出现结渣时打开清理,避免操作人员在高温下进入炉内清理结渣,即方便又安全
47、。小炉床的设计保证了节煤这一基本要素,其炉床面积比一般沸腾炉减小1/3,单位时间加煤量减小30%,因此节煤效果明显、操作方便。5.2、 沸腾炉具有以下特点(1) 燃料在沸腾炉中呈沸腾状态,燃烧层正常燃烧的温度为8501100。而风动气垫层温度较低,一般在200300,但因料层很厚,沸腾床能长时间闷火,蓄热能量大;(2) 由于鼓入高压空气,使炉内空气过量系数高,形成强氧燃烧,燃烧和燃尽条件好;(3) 沸腾层内受热面积大,传热强烈,易于燃烧。因此炉膛内单位容积热强度高,达到6.38.4105k J /m3h;(4) 用煤量少。垂直段仅以5%的煤燃烧,其余95%均为热渣,节煤效果好;(5) 炉床面积
48、小,使燃料的沸腾高度及风压、风速增加,司炉工操作更容易,对异常情况特别是结渣的早期处理更及时;(6) 设计采用较厚的保温层,可减少炉体热散失,炉温变化较小,有利于延长炉体的使用寿命;5.3、 炉床布风板有效面积F布 (m2)的计算: 布 = (1)式中:B计 计算小时耗煤量,kg/h; LO理论燃烧空气消耗量,m3 标 煤/kg;a沸 沸腾区过量空气系数,取1.15; V垂 垂直段底部冷态空气流速取0.8m/s。B计=P炉 沸腾炉的功率1500Mj-2000Mj,为了方便计算取平均值1740 Mj;QL 燃煤的低位热值11514Kj/。B计=153 kg/h理论空气需要量(L0)的计算当QL1
49、2546kJ/kg(劣质煤), L0=QL/4140+0.455m3(标)/kg =115144140m3(标)/kg布 = =0.1977计算的,布风板的有效直径圆整后为5005.4、 风帽的计算风帽的总通风面积f帽 为 单个风帽通风面积f帽 的总和。单个风帽通风面积f帽 的计算 如式2: f帽 = (2)式中:V帽 通过风帽小孔的风速,m/s;风帽的小孔风速约3045 m/s才能使沸腾段的10的煤炭处于悬浮状态,取V帽40 m/s;f帽 每个风帽小孔的通风面积,m2。f帽 = = =0.003954花板是由钢板或铸铁板制成的多孔平板,用它来固定风帽,并使之按一定方式排列,以求达到均匀布风。
50、花板的尺寸应与炉膛相应部位的内截面相适应,厚度为2035毫米(mm)左右。风帽插孔一般按等边三角形布置,孔距为风帽直径的1.31.7倍,帽沿间的最小间距不得小于20毫米(mm)。风帽有菌形(蘑菇形)、柱形、球形和伞形等形式。其中应用最广的是菌形风帽。柱形风帽是目前应用较多的一种新型的风帽。菌形风帽,风帽颈部钻有直径68毫米(mm)的小孔68个。小孔可以是水平的,也可以钻成向下倾斜15的斜孔。这种风帽的阻力小,工作性能良好,但结构稍较复杂,清渣较为困难,在帽沿处经常出现卡渣现象。此外,风帽菌头部分冷却面不够,容易出现氧化烧穿等现象。这种风帽逐渐被柱形风帽所取代。柱形风帽,由于取消了帽沿,因而尺寸更小,构造也更简单,并且还克服了菌形风帽的一些缺点,因此工作性能更为良好。采用菌形风帽,风帽颈部钻有直径68毫米(mm)的小孔68个。小孔可以是水平的,也可以钻成向下倾斜15的斜孔
- 温馨提示:
1: 本站所有资源如无特殊说明,都需要本地电脑安装OFFICE2007和PDF阅读器。图纸软件为CAD,CAXA,PROE,UG,SolidWorks等.压缩文件请下载最新的WinRAR软件解压。
2: 本站的文档不包含任何第三方提供的附件图纸等,如果需要附件,请联系上传者。文件的所有权益归上传用户所有。
3.本站RAR压缩包中若带图纸,网页内容里面会有图纸预览,若没有图纸预览就没有图纸。
4. 未经权益所有人同意不得将文件中的内容挪作商业或盈利用途。
5. 装配图网仅提供信息存储空间,仅对用户上传内容的表现方式做保护处理,对用户上传分享的文档内容本身不做任何修改或编辑,并不能对任何下载内容负责。
6. 下载文件中如有侵权或不适当内容,请与我们联系,我们立即纠正。
7. 本站不保证下载资源的准确性、安全性和完整性, 同时也不承担用户因使用这些下载资源对自己和他人造成任何形式的伤害或损失。
最新文档
- 幼儿园绘本故事当我睡不着的时候课件
- 人教版小学五年级品德与社会上册《五十六个民族五十六朵花》ppt课件
- 人教版小学一年级音乐下册红眼睛绿眼睛ppt课件
- 人教版小学数学四年级上册《数学广角》ppt课件
- 幼儿园优质课件小猫的生日
- 幼儿园科学活动区创设与材料投放课件
- 人教版小学四年级音乐小螺号ppt课件
- 幼儿园科学教育的方法和途径课件
- 开盘前广告策略案课件
- 人教版小学一年级品德与生活《校园铃声》ppt课件
- 人教版小学五年级音乐吹起羌笛跳锅庄ppt课件
- 人教版小学四年级英语下册unit3_weather第三课ppt课件
- 人教版小学一年级上册数学第二单元上下前后ppt课件
- 人教版小学五年级美术第17课电脑动画ppt课件
- 幼儿园优质课件-幼儿园中班“我们都是好朋友”课件