甲醇生产培训材料
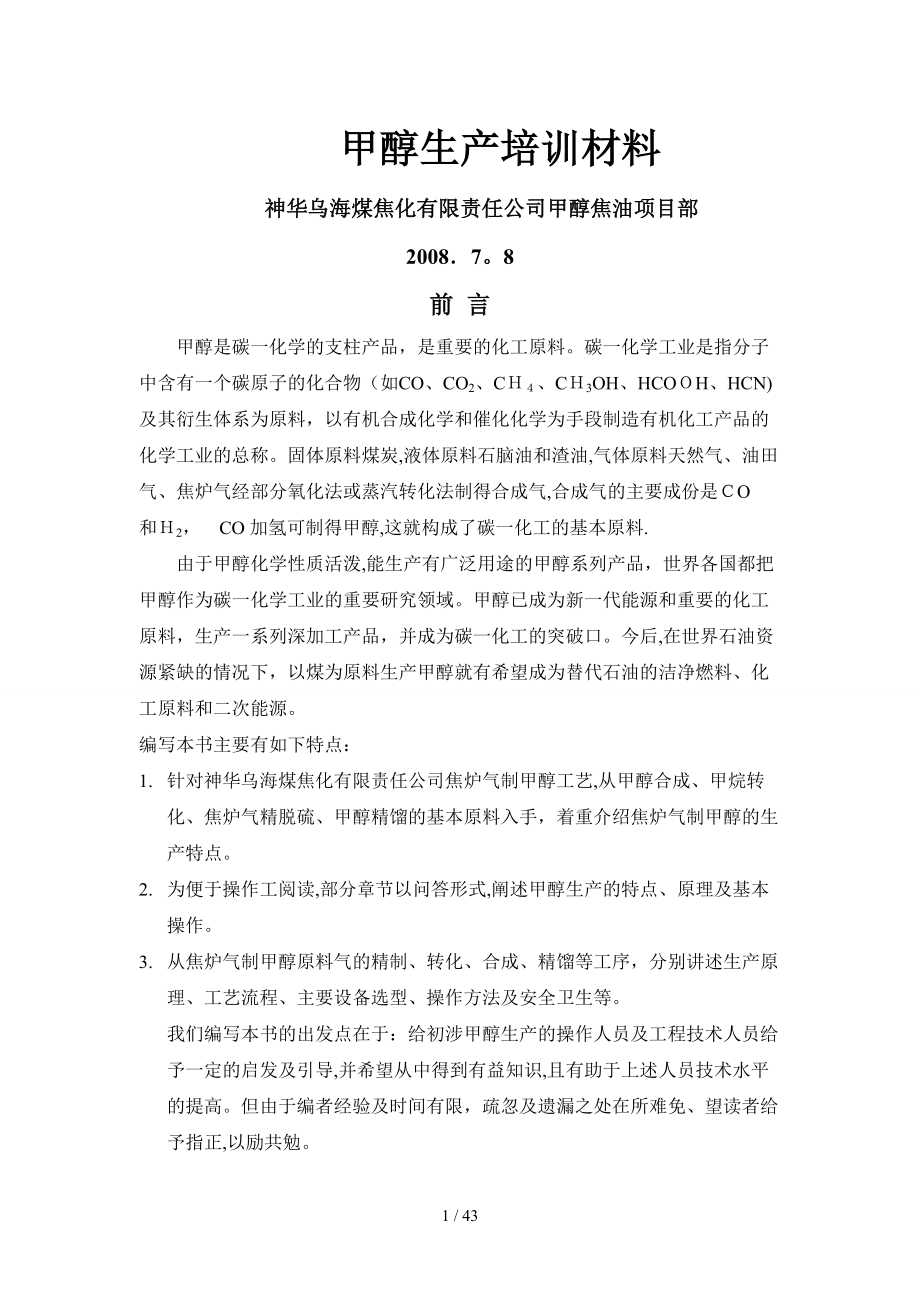


《甲醇生产培训材料》由会员分享,可在线阅读,更多相关《甲醇生产培训材料(43页珍藏版)》请在装配图网上搜索。
1、甲醇生产培训材料神华乌海煤焦化有限责任公司甲醇焦油项目部20087。8前 言甲醇是碳一化学的支柱产品,是重要的化工原料。碳一化学工业是指分子中含有一个碳原子的化合物(如CO、CO2、C、C3OH、HCOH、HCN)及其衍生体系为原料,以有机合成化学和催化化学为手段制造有机化工产品的化学工业的总称。固体原料煤炭,液体原料石脑油和渣油,气体原料天然气、油田气、焦炉气经部分氧化法或蒸汽转化法制得合成气,合成气的主要成份是O和2,CO 加氢可制得甲醇,这就构成了碳一化工的基本原料.由于甲醇化学性质活泼,能生产有广泛用途的甲醇系列产品,世界各国都把甲醇作为碳一化学工业的重要研究领域。甲醇已成为新一代能源
2、和重要的化工原料,生产一系列深加工产品,并成为碳一化工的突破口。今后,在世界石油资源紧缺的情况下,以煤为原料生产甲醇就有希望成为替代石油的洁净燃料、化工原料和二次能源。编写本书主要有如下特点:1. 针对神华乌海煤焦化有限责任公司焦炉气制甲醇工艺,从甲醇合成、甲烷转化、焦炉气精脱硫、甲醇精馏的基本原料入手,着重介绍焦炉气制甲醇的生产特点。2. 为便于操作工阅读,部分章节以问答形式,阐述甲醇生产的特点、原理及基本操作。3. 从焦炉气制甲醇原料气的精制、转化、合成、精馏等工序,分别讲述生产原理、工艺流程、主要设备选型、操作方法及安全卫生等。我们编写本书的出发点在于:给初涉甲醇生产的操作人员及工程技术
3、人员给予一定的启发及引导,并希望从中得到有益知识,且有助于上述人员技术水平的提高。但由于编者经验及时间有限,疏忽及遗漏之处在所难免、望读者给予指正,以励共勉。 甲醇焦油项目部2087-8目 录第1章 概况第2章 焦炉气合成甲醇第3章 甲醇生产基础知识第4章 甲醇生产操作注意事项第章 概况甲醇是极为重要的有机化工原料和洁净液体燃料,是碳一化工的基础产品.甲醇化工是化学工业的一个重要分子。固体原料煤炭、液体原料石脑油和渣油、气体原料天然气和油田气或煤层气等经部分氧化法或蒸汽转化法制得合成气。合成气的主要成分是一氧化碳和氢气.一氧化碳加氢可制得甲醇,这就构成了碳一化工的基本原料。由于甲醇的生产工艺简
4、单,反应条件温和,技术容易突破,甲醇及其衍生物有着广泛的用途,世界各国都把甲醇作为碳一化工的重要研究领域。现在甲醇已成为新一代能源的重要起始原料,生产一系列深度加工产品,并成为碳一化工的突破口。在世界能源紧缺以及清洁能源、环保需求的情况下,以煤为原料生产甲醇,甲醇就有希望成为替代石油的清洁燃料、化工原料与二次能源。甲醇的性质:1、 物理性质甲醇是最简单的饱和醇,分子式H3,相对分子量3204,常压沸点67,常温常压下是无色透明、略带乙醇香味的挥发性液体.甲醇与水互溶,在汽油中有较大溶解度。甲醇剧毒,易燃烧,其蒸气与空气的混合物在一定范围内会发生爆炸,爆炸极限为66.5(体积分数)。甲醇的主要物
5、理性质见表-1。甲醇的饱和蒸气压、密度见表-2。甲醇与水无限互溶,甲醇水溶液的密度随着温度的升高而降低,也随着甲醇的浓度增加而降低,甲醇水溶液的沸点随着甲醇浓度增加而降低。甲醇可与许多有机化合物按任意比例混合,并与其中00多种有机化合物形成共沸混合物.见表(1)许多共沸物的沸点与甲醇的沸点相近,在精馏粗甲醇时,可以蒸馏出以下混合物来。分子式 CH3分子量 32。04沸 点 64.57闪 点 (开口容器)、2(闭口容器)自燃点 73(空气中)461(氧气中)临界温度 24临界压力 7954105Pa蒸汽压 1.28971Pa比 重 0.7913(d4)密 度 081gl(0)比 热 470253
6、3 J(205)粘 度 0.5945厘泊(2)导热系数 2.09103J/cms表面张力 22515N/cm蒸发潜热 35。95 kJ(64.7)折射率 1。32(20)熔融热 3。69 kJ/mo燃烧热 2.0 k/o(25液体)生成热 23798 /ml(25液体)爆炸极限 36。5体积(空气中)化学性质在甲醇的分子结构中含有一个甲基与一个羟基,因为它含有羟基,所以具有醇类的典型反应;又因它含有甲基,所以又能进行甲基化反应。甲醇可以与一系列物质反应,所以甲醇在工业上有着十分广泛的应用。 甲醇氧化,生成甲醛、甲酸。甲醇在空气中可被氧化为甲醛,然后被氧化为甲酸。CH3OH + 1/O2 HCO
7、 H0 (1-1)HCO + 1/2O2HCOOH (12)甲醇在60070通过浮石银催化剂或其他固体催化剂,如铜、五氧化二钒等,可直接氧化为甲醛。 甲醇氨化,生成甲胺,将甲醇与氨以一定比例混合,在020、5.02.0MPa压力下,以活性氧化铝为催化剂进行反应,可以得到一甲胺、二甲胺及三甲胺的混合物,再经精馏,可以得到一、二或三甲胺产品。CH3OH+ NH H3H + H2O (1)2CH3O + N3(CH3)2NH + HO (14) 3CH3OH + N (C)3N+ 32O (1) 甲醇羰基化,生成醋酸,甲醇与一氧化碳在温度25、压力5070MP下,通过碘化钴催化剂,或者在温度180、
8、压力3-4Pa下,通过铑的羰基化合物催化剂(以碘甲烷为催化剂),合成醋酸。CHOH + C C3CO (16) 甲醇酯化,生成各种脂类化合物 甲醇与甲酸反应生成甲酸甲酯CH3OH +HCOH COOC +H2O (1-7) 甲醇与硫酸作用生成硫酸氢甲酯、硫酸二甲酯H3O H2SO4 CH3HSO4 +H2O (18)2CH3O + H2SO4 (H3)2S4 2 H2O (1) 甲醇与硝酸作用生成硝酸甲酯CH3O +N3 H3NO3 + H2O (1-1) 甲醇氯化,生成氯甲烷,甲醇与氯气、氢气混合,以氯化锌为催化剂可生成一、二、三氯甲烷,直至四氯化碳.CH3OH+ CI2 + C3 + 3C
9、I + HC+ H2O (111)CHI + I2 CH2+ HCI (112)C2I CI2 CH3+ HC (1-1)CHCI I2 CCI4+ C (14) 甲醇与氢氧化钠反应,生成甲醇钠,甲醇与氢氧化钠在8500下反应脱水可生成甲醇钠。CH3OH+ NaHH3a + 2O (115)甲醇的脱水,在高温下,在ZSM5型分子筛或0.5.m的金属硅铝催化剂下,甲醇可脱水生成二甲醚。 2CH3OH(CH3)2 + 2 (116) 甲醇与苯反应,生成甲苯。在。5MPa、30-8下,甲醇与苯在催化剂存在下生成甲苯。CHOHC666CH3+H2O (11) 与光气反应,生成碳酸二甲酯,光气先于甲醇反
10、应生成氯甲酸甲酯.甲酸甲酯进一步与甲醇反应生成碳酸二甲酯。(0)甲醇与二硫化碳反应,生成二甲基亚砜,甲醇与二硫化碳以AI23作催化剂先合成二甲基硫醚,再与硝酸氧化生成二甲基亚砜.4CH3O +CS22(CH) +O2 +H (18)3(C)2S + 2HNO3 3(H3)2S O (119)甲醇的裂解,甲醇在加温加压下,可在催化剂上分解为CO和H2。C3OH C + 22 (120)3甲醇用途:甲醇是重要的化工原料,甲醇主要用于生产甲醛,其消耗量约占总量的3040%;其次作为甲基化剂,生产甲胺、甲烷氯化物、丙烯酸甲酯、甲基丙烯酸甲酯、对苯二甲酸二甲酯等;甲醇羰基化可生成醋酸、醋酐、甲酸甲酯、碳
11、酸二甲酯等.其中,甲醇低压羰基化生成醋酸,近年来发展很快.随着碳一化工的发展,由甲醇出发合成乙二甲醇、乙醛、乙醇等工艺正在日益得到重视。甲醇作为重要的原料在敌百虫、甲基对硫磷、多菌灵等农药生产中,在医药、染料、塑料、合成纤维等工业中有着重要的地位。甲醇还可经生物发酵生成甲醇蛋白,用作饲料添加剂。甲醇不仅是重要的化工原料,而且还是性能优良的能源和车用燃料.它可直接用作汽车燃料,也可与汽油掺和使用,它可直接用于发电站或柴油机的燃料,或经ZSM分子筛催化剂转化为汽油,它可与异丁烯反应生成甲基叔丁基醚,用作汽油添加剂。第二章 焦炉气制甲醇 早期甲醇由木材或木质素干馏制得,今天在工业上已经被淘汰。自从1
12、923年德国BAF公司首次用一氧化碳和氢在高温高压下用锌铬催化剂实现了甲醇合成工业化之后,甲醇的工业化合成便得以迅速发展。当前,合成法甲醇生产几乎成为目前世界上生产甲醇的唯一方法。合成甲醇所需的有效化学成份为O、O2和H2。从理论上讲,凡同时含有该三种成份的气体均可用于甲醇合成,通过转化的方法能生成这三种组份的物质均可用作甲醇生产的原料。焦炉煤气主要含O、CO2、H2、4等组份,原料焦炉煤气组成为:组份 CO O H2 CH4 N2 2 Cmn %v 6.0 7 58 26 . 0。8 25 00H2S:2040gN3有机硫:50mg/m3(主要有OS、S2、H4S等)焦油+尘:50g/NmN
13、H3:50 m/Nm3萘:400 mg/NBTX:2000mgNm3H:300 mg/Nm3由于焦炉气中氢含量高、甲烷含量高、CO和O2含量低,用这样的气体经净化后虽然可以直接用于甲醇合成,但原料和动力消耗将非常高。为了充分利用焦炉煤气生产甲醇,降低原料和动力消耗,焦炉煤气必须进行再转化生产出合成甲醇较理想的合成气,再进行甲醇合成。另外,进甲醇合成之前,必须将气体中的硫、焦油、萘等有毒成份清除干净,以避免甲醇催化剂中毒失活。一、焦炉气制甲醇工艺系统技术1甲醇合成技术1) 高压法(1.6294MPa)采用锌铬催化剂,反应温度为3600,压力196294MPa但是,由于原料及动力消耗大,反应温度和
14、压力高,生成粗甲醇中有机杂质含量高,而且投资大,成本高,当今其已属于被淘汰的方法.2) 低压法(。MP8。0MPa)低压法基于高活性的铜系催化剂,反应温度低(2270),在较低的压力下可获得较高的甲醇收率,而且选择性好,减少了副反应,改善了甲醇质量,降低了原料的消耗。3) 中压法(98MPa120Ma)中压法仍采用与低压法相同的铜系催化剂,反应温度也与低压法相同,但由于提高了合成压力,相应的动力消耗略有增加.目前,世界上新建或扩建的甲醇装置几乎都采用低压法或中压法,其中尤以低压法为最多.工艺技术方案的比较和选择焦炉气除萘、除焦油从焦化装置送来的焦炉气中还含有大量萘、焦油、粉尘等易凝或易结晶的物
15、质,在常温常压下,这些物质也许还不会凝结或结晶,但经加压后,由于其分压得以上升,造成部分这样的物质的以凝结为液滴或固体颗粒,如果不将这些物质尽量除去,将对后续工序造成危害甚至危及整个装置的安全。焦炉气和合成气的脱硫甲醇生产中使用的甲醇合成催化剂易受硫化物毒害而失去活性,必须将焦炉煤气中的硫化物除净.甲醇原料气中的硫可以各种形态的含硫化合物存在,如硫化氢(2)、硫氧化碳(CS)、二硫化碳(CS2)、硫醇(RSH)、硫醚(RSR)、环状硫化物(如噻吩C4H4S)等。湿法脱硫技术主要用于硫化氢的脱除,而且只能用于初级脱硫,脱硫后的气体中硫化氢含量一般只能达到0g/3。要达到甲醇合成的精度,还必须串以
16、固体精脱硫系统。1)湿法粗脱硫:湿法脱硫可分为物理吸收法、化学吸收法与直接氧化法三类.其中,最重要的是湿式氧化法脱硫技术。目前运用较为广泛且性能较好的脱硫方法有PDS法、改良法,栲胶法、茶灰法、M法、改良对苯二酚法、C法。)干法精脱硫主要有物理吸附法和化学吸附法.(1)吸附法 氧化铁法b。 氧化锌法c. 活性炭法(2)转化吸收法a. 锰矿法。 复合型脱硫剂 钴钼+氧化锌d。 铁钼锰矿法e. 铁钼+氧化锌鉴于焦化的湿法脱硫已将焦炉气中的2脱到4mg/N3以下,本项目拟采取如下脱硫措施:第一步:为减少高温固体脱硫剂消耗,在常温常压下用常温氧化铁脱硫剂将焦炉气中H2脱到1g/Nm3以下。第二步:焦炉
17、气加压进转化炉前,在35040温度下,用铁钼催化加氢转化有机硫+ZnO脱硫剂将焦炉气中总硫脱到mg/N3以下,达到二段转化催化剂可以承受的含量.第三步:纯氧转化后,焦炉气中剩余有机硫几乎全部转化为2,用常温ZO吸收,使合成气中总硫0.1pp。焦炉气压缩机采用电机驱动的活塞式焦炉气压缩机。转化气(即新鲜合成气)和甲醇合成循环气的气量均较大,而且气体很干净,采用离心式压缩机。焦炉气转化由于焦炉气中含氢量高、甲烷含量高、O和CO2含量低,其组成类似于天然气经一段蒸汽转化后、进二段转化前的一段转化气。用这样的气体直接合成甲醇是非常不经济的,必须进行深度转化.本装置采用纯氧转化的方案。甲醇合成甲醇合成气
18、(主要成分是、O和O2)在催化剂的作用下,反应生成甲醇,其反应式如下:CO2H2 H3O9073kJmlC+3H CH3OHH2O+8。2J/ml反应是放热而且可逆的。采用气固相绝热等温混合型甲醇合成反应器,合成催化剂采用四川天一科技股份有限公司研制生产的XNC98型铜基甲醇合成催化剂。该反应器可有效地利用甲醇合成反应热所副产的中压蒸汽,温度控制简单灵活,触媒生产强度大。甲醇精馏:采用三塔精馏流程.甲醇产品贮罐:采用平底立式圆筒状内浮顶贮罐。氮氧站空分系统由一套使用填料塔和前段净化流程(分子筛+活性氧化铝)的制氧装置组成,采用分子筛吸附预净化、增压透平膨胀机、填料上塔低温精馏制氧工艺。整套系统
19、包括:空气过滤系统、空气压缩系统、空气预冷系统、分子筛纯化系统、分馏塔系统、氧气压缩系统、氮气压缩系统、液体贮存及汽化系统、仪控系统、电控系统等。空气压缩机和氧气压缩机采用蒸汽透平驱动的离心式压缩机,氮气压缩机则采用电机驱动的活塞式压缩机。二 、工艺流程说明 本装置工艺过程分为焦油脱萘系统、焦炉气气柜系统、干法粗脱硫系统、焦炉气压缩系统、焦炉气精脱硫系统、纯氧转化系统、转化气精脱硫系统、合成气压缩系统、甲醇合成系统及甲醇精馏系统.工艺系统流程图如下:联合压缩机甲醇合成甲醇精馏精甲醇产品罐焦炉气精甲醇产品装车台氮气焦炉气气柜焦炉气压缩焦炉气精脱硫综合加热炉空分及氮氧压纯氧转化干法粗脱硫热回收冷却
20、分离转化气精脱硫氧气中压蒸汽甲醇弛放气循环气烟气放空焦炭过滤工艺说明如下:1) 焦炉气气柜系统从焦化装置送来的焦炉气经管道进入焦炉气预处理系统,出来后进入焦炉气压缩机进口.由于焦化装置送来的焦炉气压力仅几百毫米水柱,且供气过程有可能出现波动,为保证甲醇装置供气稳定,在焦化装置与甲醇装置之间的焦炉气管线上设气柜缓冲。当供气量大于甲醇装置用气量时,气柜活塞上升,贮气量增大;当供气量小于甲醇装置用气量时,气柜活塞下降.气柜活塞设有高限和低限的报警和联缩,当达到报警位置时,报警系统会向主控人员发出声光报警,提醒操作人员及时处理;如果操作人员在报警后未及时处理,活塞继续运动到联锁位置时,联缩系统会自动从
21、系统中泄放部分焦炉气到火炬系统燃烧处理或使焦炉气压缩机减量或停车。焦炉气压缩本装置的任务是将由气柜来的压力为200mmH2O的焦炉气压缩至2.3Ma(g),温度约4送至粗脱硫工段,其气量为75000Nm3h.生产流程简述自气柜来的温度为40,压力为200 mmHO(表)的焦炉气由总管送至本工段,然后进入一级气缸,一级压缩后压力为.3003MPa(绝)温度17的气体经一级排气缓冲器(F/2ABC)缓冲稳压后进入一级冷却器(C601/AC)冷却,气体冷却至40后进入一级分离器(F62107ABC),分离掉水分后经二级吸气缓冲器(F6210AB)进入二级气缸,二级压缩至0.103Pa(绝)后经二级排
22、气缓冲器(F214ABC)缓冲稳压后进入二级冷却器(C623BC),气体冷却至40进入二级分离器(628ABC),分离掉水分后经三级吸气缓冲器(F615AC)进入三级气缸,三级压缩至 Ma(表)、4的气体经三级出口缓冲器(F61ABC)缓冲稳压后由总管送往粗脱硫工段。精脱硫 本装置的任务是将焦炉气中所含的各种形态的硫脱除,以满足转化装置的转化触媒、甲醇合成装置的合成触媒对硫的要求。装置每小时处理气量750Nm。气体中含硫化氢0mg/Nm3,有机硫0g/N。由于焦炉气中的硫形态比较复杂,本装置采用加氢转化、脱除的干法脱硫流程将总硫脱至小于01pm. 本装置包括铁钼加氢转化、中温脱硫把关,以及触媒
23、的升温还原系统。本装置采用的工艺流程具有如下特点:流程短、操作简单、净化度高。采用氧化锌中温脱硫,避免了化工工艺中忌讳的冷热病,降低了消耗。.精脱硫流程焦炉气压缩机来的压力2.MPa,温度40 OC的焦炉气含无机硫20/N3,有机硫50Nm,先经过除油器(T003A,B)粗脱硫槽(12A,B)滤去油雾和脱除无机硫后送至转化装置利用余热提温到约35OC。升温后的气体经铁钼小加氢转化器(R0301A,B)进入铁钼大加氢转化器(R0302 ),气体中的有机硫在此转化为无机硫,另外,气体中的氧也在此与氢反应生成水,不饱和烃加氢成为饱和烃。加氢转化后的气体 进入中温精脱硫槽(301 /B),脱去绝大部分
24、的无机硫送往转化装置 ,出转化降温至4OC的转化气进常温氧化锌脱硫槽使气体中的总硫达到0.1ppm以下,出氧化锌脱硫槽的气体压力约为1.6a,温度约为40OC送往联合压缩机装置。甲烷转化本装置的任务是将原料气中的甲烷转化成合成甲醇的有效气体C0和2。 装置包括焦炉气和蒸汽预热、焦炉气转化以及转化气热回收装置.生产流程简述来自压缩的焦炉气,压力23P,温度40O,甲烷含量约26.经焦炉气加热炉(F04014)加热至约350后,送往精脱硫工段脱除有机硫和无机硫。脱硫后的焦炉气,压力约。a,温度约5OC返回转化工段。为甲烷转化反应的需要,同时为防止焦炉气在高温下析碳,在焦炉气中加入2.7P的饱和蒸汽
25、,蒸汽流量根据焦炉气的流量来调节.加入蒸汽后的焦炉气经蒸焦加热炉( 0011)加热至 60OC进入转化炉(F042)上部.加热炉用燃料气作为热源。来自空分工段的氧气,温度25,压力约。5MPa,加入蒸汽后进入蒸氧加热炉加热至0 OC后,进入转化炉上部,氧气流量根据转化炉出口温度和焦炉气流量来调节。焦炉气和氧气分别进入转化炉上部后立即进行氧化反应放出热量,并很快进入催化床层,进行以下反应:2H2O2O+1154al ()2CH4+O=2CO+4H217.0kca (2)H4+H2O=CO2493kcal ()CH4+CO2=O+2H21cl (4)OHCO2H+9。8kcal (5)反应最终按(
26、5)式达到平衡,转化气由转化炉底部引出,温度 90985,压力约.7MPa,甲烷含量约0.进入废热锅炉(0401)回收热量副产蒸汽,转化气温度降为30,然后经中压锅炉给水加热器(E42)、脱盐水预热器(E40),温度降为18。进入加压塔再沸器、常压塔再沸器,温度降至125后,经脱盐水预热器(E0403)进一步回收反应热后,转化气温度降至约0,经水冷器冷却至0.经气液分离器(V046)分离工艺冷凝液后,经氧化锌脱硫槽(0A,B)脱除气体中残余的硫,为甲醇合成做最后的把关。出氧化锌脱硫槽的转化气温度40,压力约。6p经过滤器后送往合成气压缩工段。 气液分离器出口的工艺冷凝液去循环水系统。来自锅炉房
27、的锅炉给水,温度约5,压力约49Pa,在锅炉给水预热器用转化气加热至185后,一部分送往甲醇合成,一部分经废热锅炉的汽包 进入废热锅炉,生产39MPa中压蒸汽。废热锅炉所生产的蒸汽除供给本工段用汽外,富裕蒸汽送往蒸汽管网。来自甲醇合成工段的驰放气和闪蒸气,经综合加热炉燃烧,为焦炉气和蒸汽、氧气、锅炉水等提供热量。合成气压缩本装置为30万吨年甲醇合成装置的合成气压缩机组,处理新鲜气量1200 Nm3/,循环气量48000N3/,合成气出口压力为7。Ma(A)。除部分接管外,整个装置由压缩机厂成套供应。合成气压缩机为离心式二合一机组,由汽轮机驱动,汽轮机为冷凝式。生产流程简述来自转化工段的新鲜气,
28、温度4,压力1.6Ma(),进入合成气压缩机一段压缩至7。4MPa(A),进入循环段与来自甲醇合成的循环气混合,压缩至。9MPa(A).压缩机出口合成气送至甲醇合成.来自过热蒸汽管网的过热蒸汽,温度45,压力33P(A),经主汽阀、调节阀进入汽轮机,汽轮机排汽温度49,压力.12a(A),进入空冷器,经冷却冷凝后,冷凝液用冷凝液泵打入除氧站。甲醇合成本装置生产规模按30吨/年甲醇设计,实际生产能力为30万吨/年,年操作时间8000小时。整个装置由甲醇合成、余热回收、粗甲醇分离等几部分组成。分离粗甲醇后的循环气送至合成气压缩,补充新鲜气并加压后,返回甲醇合成塔循环利用。生产流程简述 来自合成气压
29、缩的合成气,经气气换热器(E0601)预热到25,进入甲醇合成塔(601),在催化剂的作用下进行甲醇合成反应 CO2H=CH3OH+QC2+3H2=CH3OH+HOQ及副反应 4CO+H=C4H9OHO 8CO+7H2=CH18+8H2O等 甲醇合成塔为管壳式反应器,管内填装触媒,反应管外为沸腾热水,利用反应热副产蒸汽。合成塔出口气进气气换热器(00)与合成塔入口气换热,把入口气加热到活性温度以上,同时合成塔出口气温度降至110,经空冷器(E0602)、水冷器(0603)冷却到4后,进入甲醇分离器(V61)进行气液分离。出甲醇分离器气体大部分作为循环气去合成气压缩机增压并补充新鲜气,一小部分作
30、为弛放气,压力约。4MP(),经调节阀减压至0。40MPa(),与闪蒸槽(V0602)出来的贮罐气混合后.Pa(g),送往转化装置作燃料气。 甲醇分离器底部出来的粗甲醇减压至0.4Ma(g)后送入闪蒸槽(V00),粗甲醇中的溶解气绝大部分被释放出来,该气体与弛放气混合后用作燃料气。粗甲醇送往甲醇精馏。 甲醇合成塔壳侧出来的汽液混合物经上升管进入汽包(V03)进行汽液分离,分离下的水返回合成塔,蒸汽则进入蒸汽管网。 为了保证锅炉水质量,从汽包定期排放锅炉污水,同时向汽包内加入少量磷酸盐溶液以改善锅炉水的水质。主要设备的选定说明甲醇合成塔 一台管壳式反应器 反应管442X7 共4829根触媒装填量
31、 48.703塔径 0m 粗甲醇的精馏精馏原理:利用液体混合物中各组份具有不同的沸点,在一定温度下各组分所具有的不同蒸汽压,在精馏塔各块塔板上形成浓度梯度,使下降液体与上升蒸汽两者间发生热交换和质量交换,液体部分汽化,汽体部分冷凝,使其沸点不同的物质得到分离,如此反复多次,以达到分离液体混合物的目的。工艺流程:粗甲醇经计量,加碱中和、预热后进入预蒸馏塔,从预塔塔顶除去比甲醇沸点低的低沸点物及溶解的气体,如甲酸甲酯、二甲醚、一氧化碳、二氧化碳等。从预塔底出来的预后甲醇(基本不含低沸点杂质)用泵送入加压精馏塔精制,从加压精馏塔顶出来的甲醇蒸汽作为常压精馏塔再沸器热源,除达到冷凝加压精馏塔顶甲醇蒸汽
32、的目的外,同时为常压精馏塔提供热量。冷凝的甲醇蒸汽除抽出部分经冷却后作为产品精甲醇送到精甲醇计量槽外,其余部分作为加压塔回流液经加压塔回流泵全部回到加压精馏塔顶部。加压塔得到的精甲醇产品约为本装置总产量的一半.从加压塔底部出来的釜液全部送到常压精馏塔中部作为常压精馏塔进料,塔顶甲醇蒸汽经冷凝冷却后,除部分作为精甲醇产品送到精甲醇计量槽外,其余部分作为常压塔回流液经常压塔回流泵全部回到常压塔顶部。加压塔得到的精甲醇产品约为本装置总产量的一半.甲醇合成过程中由于副反应的发生而生成微量乙醇、异丙醇、丁醇、高级烷烃类等杂质,这些杂质部分与水和甲醇形成共沸物而不易与甲醇完全分离,从而影响产品精甲醇质量。
33、为了控制这些杂质可能对产品精甲醇质量造成的影响,从常压精馏塔中下部杂质富集区的几块塔板上抽出部分杂醇油经冷却后装桶出售,这样就可以有效控制杂质蒸发进入上部塔板甲醇蒸汽中的量,从而达到使精甲醇产品满足要求的目的。从常压精馏塔塔底部排出比甲醇沸点高的高沸物(如水、乙醇等),经废水泵送到纯氧转化系统汽提塔处理.预塔和加压精馏塔再沸器热源采用本装置转化气低位废热,根据精馏塔灵敏板温度控制通过再沸器的转化气量(其余转化气走旁路),转化气的冷凝水先用作预塔进料粗甲醇预热的热源,然后送到纯氧转化系统汽提处理。常压精馏塔再沸器的热源为加压塔顶出来的甲醇蒸汽.10)精甲醇罐区装置任务:贮存和装车精甲醇来自甲醇精
34、馏系统的合格产品精甲醇,经管道分别(或同时)送入精甲醇贮罐。当甲醇罐车到场装车时,精甲醇贮罐的甲醇产品由精甲醇输送泵送装车台,经计量后由装车鹤管装车,或者由管道送去界外火车装车.来自氮气总管的氮气通过自力式调节阀减压后分去各甲醇罐保护甲醇,分别从各呼吸阀放空.氮氧站本装置任务:制出合格的氧气(纯度为:9999%)和氮气(纯度为:9。9%)工艺流程空气过滤和压缩:空气首先进入空气吸入过滤器,在空气吸入过滤器中除去灰尘和其它颗粒杂质,然后进入主空压机,经过多级压缩后进入空冷塔,压缩机级间的热量被中间冷却器中的冷却水带走。空气的冷却和纯化:空气在进入分子筛吸附器前在空冷塔中冷却,以尽可能降低空气温度
35、减少空气中水含量从而降低吸附器的工作负荷,并对空气进行洗涤.进入空冷塔上部的冷冻水来自水冷塔,它利用干燥的出塔污氮进行冷却,然后进入空冷塔上部.分子筛纯化系统:由两台分子筛吸附器组成,吸附空气中的水份、二氧化碳和一些碳氢化合物,两台分子筛吸附器一台工作,另一台再生。空气的精馏:出吸附器的空气分为两股,一股直接进入主换热器冷却后进入下塔,另一股为膨胀空气,首先经过膨胀机增压端的压缩及后冷却器的冷却,再进入主换热器被冷却,经膨胀机膨胀后进入上塔中部。下塔的上升气体通过与回流液体接触含氮量不断增加。所需的回流液氮来自下塔顶部的冷凝蒸发器,在冷凝蒸发器中液氧蒸发,氮气冷凝。下塔从上到下产生以下产品:纯
36、氮气、纯液氮、38O2的富氧液空。在下塔底部获得含氧为38的富氧液空,顶部获得纯度为9。9%的纯氮气。下塔底部抽出的富氧液空经过冷器过冷后进入上塔,而下塔顶部的氮气则进入冷凝蒸发器中。进入冷凝蒸发器的氮气被液氧冷却成为液氮,其中一部分液氮回下塔作为下塔的回流液体,另一部分液氮经过冷器过冷后进入上塔参加精馏,还有部分液氮作为液体产品送出。在上塔中产生:底部产生液氧和氧气、上部产生污氮气、顶部产生纯氮气。各种物流进入上塔,经过上塔的进一步分离,可在上塔顶部获得纯度为9.9%的氮气,中上部抽出污氮气,底部获得纯度为96的液氧和氧气。氮气、污氮气经过冷器、主换热器复热后出冷箱;复热后的氮气一部分作为产
37、品气送出,另一部分氮气则送水冷却塔回收冷量。复热后的污氮气为成两部分,一部分作为分子筛吸附器的再生用气,另一部分也送入水冷却塔回收冷量。底部抽出的产品氧气去主换热器被复热至常温后送出冷箱.产品的分布:液氧回路(液氧从主冷底部排出,进入液氧贮槽、气氧回路(气氧以0.0MP(G)压力从冷箱输出去氧气透平压缩机);气氮回路(上塔低压气氮直接从冷箱输出,一部分作为产品气去氮压机,另一部分送入水冷塔对水进行冷却);液氮回路(液氮从液氮量筒排出,进入液氮贮槽);污氮回路(一股污氮用于分子筛吸附器的再生,另一股送到水冷塔对水进行冷却,还有一小部分进入冷箱,对冷箱充气);仪表及解冻用的干燥空气(空分设备仪表(
38、处于正常工作状态)及解冻用的干燥空气从分子筛吸附器的出口抽出后送至仪表空气网络);液体排放(从冷箱排出的所有低温液体汇集后送至喷射蒸发器蒸发后排入大气);排气(各系统的排气先送至各消声器再排入大气)。第三章 甲醇生产基础知识干法脱硫基础知识1、铁钼触媒及镍钼触媒对有机硫及烯烃的加氢转化反应RSH H2 RH+2S+QRSR+22RH+H2S+Q44S+42 CH0+H2S+QCS4H2 CH4H2S+C +H2 CO+HSQC2H4+2 C2H6+生产中铁钼触煤在进行上述反应的同时还存在下列反应:CO+3H2CH4+H2O+(甲烷化反应)H2+O 2H2O(燃烧反应)CH4 C+CH(析碳反应
39、)2C+CO生产中铁钼的转化反应及副反应均为放热反应,在操作中应控制好触媒层温度变化情况,及时调整进铁钼转化器焦炉气预热温度.、氧化锰对H2S的吸收反应nO+HSMnS+H2OMS不再有吸收能力,因此锰矿硫饱和后要进行更换或再生。3、氧化锌对H的吸收反应 氧化锌除对有吸收作用外,还对有机硫有吸收作用,其可与硫化物反应生成十分稳定的ZnS。ZnOH2S ZS+H2+QZnOCOS nSCO2QnO+C2H5SZS+2H4HO+Q2 ZnO+CS2 2 ZS+C2+Q二、甲烷转化基础知识1、甲烷转化的化学反应甲烷部分氧化制合成气的总反应式如下:CH412O=CO+2+3。5kJ/ol但实际反应过程
40、非常复杂,而且伴有一些副反应发生,包括氧化反应、重整反应、水煤气变换反应以及积炭和消炭反应等。 氧化反应 4 2O=C2+22O+80J/mCH4 + 3/O2=C+2O +519kJ/molC4 + 12O2=CO2+H2561k/molC4 + 3/2 O2+H2+19JmolH + /2O2=H2O+41.molC4+ O=CO+ 2 +27mol 重整反应 CH H2C+H2206k/mlCH4+ CO2=2CO+2H22J/mol 水煤气变换反应 CO+ H2O=C2+2+412kJ/m 积炭和消炭反应H4C+H-74。9 kJ/ol2COCO+C 72。4 kJ/oC+O= CO
41、+H-131。3kmol、甲烷部分氧化制合成气反应的平衡常数甲烷部分氧化制合成气反应的平衡常数可用下面公式表示:k=( CO 2) /(p CH4p O212)式中kp-甲烷部分氧化制合成气反应的平衡常数p CH 、p CO、2、 p O2分别表示甲烷、一氧化碳、氢气、氧气的平衡分压。对甲烷部分氧化制合成气反应CH4+ 1/2=CO+22用公式计算结果的平衡常数见下表反应温度()平衡常数(Kp)反应温度()平衡常数(Kp)60070080902.691101。0296112。0411400110004201400103.010111.95741111。201。081111由表可知,反应平衡常数
42、随着温度的升高而有所降低。3、甲烷部分氧化制合成气的反应机理甲烷部分氧化制合成气的反应机理比较复杂,至今存在争议。目前,研究人员对负载型金属催化剂上的甲烷部分氧化制合成气的反应机理主要有两种观点:即间接氧化机理(也称燃烧-重整机理)和直接氧化机理.间接氧化机理认为,甲烷先与氧气燃烧生成水和二氧化碳,在燃烧过程中氧气完全消耗,剩余的甲烷再与水和二氧化碳进行重整反应生成氢气和一氧化碳。直接氧化机理认为,甲烷直接在催化剂上分解生成氢气和表面碳物种,表面碳物种再与表面氧反应生成一氧化碳。3CH4 +2H2O+ CO24CH4+ 2O2 完全 氧化直接转化 混合重整4CO +8H2甲烷部分氧化制合成气的
43、反应机理示意(1)间接氧化机理 Prtr等首先提出了在i催化剂上甲烷部分氧化反应是按间接氧化机理进行的,即先燃烧后重整的反应机理。他们的研究工作开始于1946年,以一种耐火材料负载10Ni作为催化剂,在。1P,2900下进行反应.他们在实验中观察到在n(CH4):n(O)2:1的条件下,在入口处催化剂床层温度远高于炉温,表明有放热反应发生;随后催化剂床层温度下降,表明存在一个吸热反应。据此他们认为最初的放热反应是由于在催化剂床层上一部分甲烷与化学计量的氧发生完全燃烧反应,随后的吸热反应是未反应的甲烷与H2O或 CO发生重整反应。Vermire等讨论了甲烷部分氧化过程微型反应器中镍催化剂床层的“
44、热点”问题.在固定炉温下测定催化剂床层温度梯度发现,接近催化剂入口处发生放热反应,床层后半部发生吸热反应。“热点”较反应前温度升高大约100.当炉温约为80时H4和CO选择性与空速无关,60时随空速降低而升高.他们认为这符合燃烧重整机理。(2)直接氧化机理直接氧化机理首先由Schmid等人提出。他们用t、Rh催化剂研究甲烷部分氧化,以高转化率转化成了2和CO,并且甲烷转化率和合成气选择性随空速增加而增加。他们认为,由于实验条件下甲烷、水蒸汽重整反应进行得很慢,在这样短的接触时间内,可以基本排除重整反应发生的可能,因此,他们提出甲烷部分氧化应遵循如下的直接氧化机理4(g)CHxd(x)HadHd
45、2 H2(g)O2(g)2 Oada+OaCOaCO(g)可存在的副反应:xad+ OadH(x1)d+HadHad+ OadHadOHd+ HadH2O()COd OadCO2(g)可以看出,甲烷首先在催化剂表面上活化裂解为碳物种x(x=0-3)和氢,随后表面碳物种和反应生成CO,CO可能被深度氧化为C2。吸附态的原子可能互相结合生成H或与结合生成OH物种,而OH与另外吸附的H原子结合生成H2O。根据以上反应机理,可以较好地解释原料气预热可使合成气选择性增加的原因。高的进气温度将使催化剂表面温度升高,甲烷的裂解反应加快,同时使得H原子结合和H2的脱附速度加快。此外,温度升高使原子的覆盖度降低
46、,副反应速度减慢,因此原料预热可使合成气选择性增加。Bhattay等在负载型Pd催化剂上发现,当温度升高达到773以上时,C的生成量大幅度降低。他们认为甲烷首先与催化剂表面作用生成CH吸附物种,并可能进一步脱氢生成的Cx(x=0)吸附物种与表面Oad反应生成CO;同时H3吸附物种也可能脱离催化剂表面形成C3自由基,在气相中被氧化生成CO2.温度高于923时,生成的C可能与表面吸附物种Cx(x=)反应生成C和2。该机理能合理解释温度高于13K时反应仅生成CO的现象。4、催化剂积炭研究甲烷部分氧化反应过程中可能的积炭反应包括: 2CO=CO2C +172.4k/m C4=C+H274。9kJ/ol
47、CO+ H2= 2O33。47 /mol它们都是可逆反应,从热力学分析可知,如果增加温度或减少体系压力,甲烷裂解反应式产生积炭的可能性增大;O歧化反应式和反应式产生积炭的可能性减少。如果降低温度或增大体系压力,则结果正好相反.温度对积炭反应的影响非常大,要避免催化剂积炭必须选择适当的温度,避免热力学积炭区。在部分氧化制合成气体系中, O2与H4摩尔比对积炭温度存在某种曲线关系,在生产实际操作中,可根据不同温度条件选择适宜的原料配比,或根据不同的原料配比,选择适宜的反应温度,以尽量减少催化剂积炭。arge等人对甲烷部分氧化制合成气反应中金属催化剂上,在不同温度下对纯CH4和纯O在镍催化剂上积炭速
48、率进行研究,发现在113K的温度下,O歧化速率比甲烷解离反应速率分别慢0倍和5倍,这表明甲烷催化裂解是生成积炭的主要途径。他们还认为积炭的起因与生成合成气的机理无关 ,通过采用合适的催化剂可以从动力学上避免积炭。Lunsfol等利用XP方法对催化剂积炭进行了研究,发现催化剂的积炭受原料气配比的影响.在70时,当(C4):(O2)时,催化剂产生大量积炭;当n(CH4): (O)1.75时,催化剂活性偏低,但无积炭生成;当(4): n(O2)=1.78时,催化剂表面的积炭达到单层稳态分布,几乎看不出催化剂活性下降;在8连续进行5小时,催化剂仍很稳定。载体对催化剂的抗积炭性能有很大的影响。其中M g
49、 O为载体时催化剂的抗积炭性能最好。还原态镍催化剂表面由C歧化产生的积炭量的顺序是N /gO Ni /CaNi / SiO。、催化剂近年来甲烷部分氧化制合成气催化剂的研制工作十分活跃,据文献报道催化剂的活性组分主要集中在Pt、R、R、Co、i、r等第属金属.一般将这些催化剂分为三类:第一类是以Ni、Co为主的负载型催化剂,所用载体主要为Al2O3、TiO2、O、ZrO2、Y型分子筛等。第二类是L、Pt、Pd、u、h等负载型贵金属催化剂,所用载体主要为Al、MgO 、iO 和独石等。第三类是金属催化剂,主要包括钙钛矿型氧化物和a2O3-Zr、Y2O3ZrO2.Ni基负载型催化剂具有较高的催化活性
50、,且成本低,强度高,易于制备而极具应用价值。但在高温反应条件下,活性组分N易流失和烧结,且催化剂易积炭失活,稳定性较差。目前研究者主要通过在催化剂中添加助剂和选择不同的催化剂载体等方法来提高催化剂的活性、抗积炭性能和稳定性。实际生产中,为保证催化剂有较长的使用寿命和尽量减少副反应,应在确保甲醇产量的前提下,根据催化剂的性能,尽可能在较低温度下操作,(在催化剂使用初期,反应温度宜维持较低的数值,随着使用时间增长,逐步提高反应温度)。另外,甲醇合成反应温度越高,则副反应增多,生成的粗甲醇中有机杂质等组分的含量也增多,给后期粗甲醇的精馏加工带来困难。三、 甲醇合成的基础知识1、合成甲醇的化学反应主反
51、应:C+2H2H3H+0。5J/molCO3CHO+H2+59.6 J/mol(1) 副反应:2CO4H2C3OCH3H2O+200. /l3CH4H2O115.6 mol4CO+8H2C4H9OH +H2O+49.2kJ/mlCO+2CH2O42 kJ/olnCO2n2(2)nnH+Q kJo2、温度对甲醇合成反应的影响甲醇的合成反应是一个可逆放热反应。从化学平衡考虑,随着温度的提高,甲醇平衡常数数值将为降低。但从反应速度的观点来看,提高反应温度,反应速度加快。因而,存在一个最佳温度范围。对不同的催化剂,使用温度范围是不同的。307型合成甲醇催化剂的操作温度:1300 ,而最佳温度:2126
52、0 。实际生产中,为保证催化剂有较长的使用寿命和尽量减少副反应,应在确保甲醇产量的前提下,根据催化剂的性能,尽可能在较低温度下操作,(在催化剂使用初期,反应温度宜维持较低的数值,随着使用时间增长,逐步提高反应温度).另外,甲醇合成反应温度越高,则副反应增多,生成的粗甲醇中有机杂质等组分的含量也增多,给后期粗甲醇的精馏加工带来困难。3、压力对甲醇合成反应的影响甲醇的合成反应是一个体积收缩的反应,增加压力,反应向生成甲醇的方向移动;从动力学考虑,增加压力,提高了反应物分压,加快了反应的进行;另外,提高压力也对抑制副反应,提高甲醇质量有利。所以,提高压力对反应是有利的.但是,压力也不宜过高,否则,不
53、仅增加动力消耗,而且对设备和材料的要求也相应提高。307型合成甲醇催化剂的操作压力:35 MP。4、空速对甲醇合成反应的影响气体与催化剂接触时间的长短,通常以空速来表示,即单位时间内,每单位体积催化剂所通过的气体量。其单位是m3(标)/(m3催化剂h),简写为1。空速是调节甲醇合成塔温度及产醇量的重要手段。在甲醇生产中,气体一次通过合成塔仅能得到6%的甲醇,新鲜气的甲醇合成率不高,因此,新鲜气必须循环使用。在一定条件下,空速增加,气体与催化剂接触时间减少,出塔气体中甲醇含量降低。但由于空速的增加,单位时间内通过催化剂的气体量增加,所以甲醇实际产量是增加的。当空速增大到一定范围时,甲醇产量的增加
54、就不明显了。同时由于空速的增加,消耗的能量也随之加大,气体带走的热量也增加。当气体带走的热量大于反应热时,床层温度会难于维持.甲醇合成的空速受到系统压力、气量、气体组成和催化剂性能等诸多因素影响。C30型合成甲醇催化剂的操作空速:4002000 1.5、碳氢比的控制对甲醇合成反应的影响甲醇由一氧化碳、二氧化碳与氢反应生成,反应式如下:O+HCHOHCO2+H=CH3+H2O 从反应式可以看出,氢与一氧化碳合成甲醇的物质的量比为,与二氧化碳合成甲醇的物质的量比为3,当一氧化碳与二氧化碳都有时,对原料气中碳氢比(或M值)有以下两种表达方式:f =(2CO2)/(+ CO2)=。02。15或 M=
55、2 /(C1.5 CO2)=2。02。05不同原料采用不同工艺所制得的原料气组成往往偏离上述值或M值。生产中合理的碳氢比应比化学计量比略高些,按化学计量比值,f值或M值约为2,实际控制得略高于2,即通常保持略高的氢含量。过量的氢对减少羰基铁的生成与高级醇的生成及延长催化剂寿命起着有益的作用。6、 惰性气体含量对甲醇合成反应的影响甲醇系统的惰性气体是指氮、氩气及其他不凝性的有机化合物.系统中惰性气含量高,相应地降低了CO、CO2、H的有效分压,对合成甲醇反应不利,动力消耗也增加。惰性气体来源于原料气及合成甲醇过程的副反应。对于甲醇生产厂家,循环气中惰性气含量会不断累积,需要经常排放一部分气体来维
56、持惰性气的一定含量。一般控制原则:在催化剂使用初期活性较好,或者是合成塔的负荷较轻、操作压力较低时,可将循环气中惰性气含量控制在0-2%;反之,控制在15%左右。控制循环气中惰性气含量的主要方法是排放粗甲醇分离器后气体.排放气量的计算公式如下:V放空(新鲜新鲜)放空式中V放空放空气体的体积,m3(标)/ h; V新鲜新鲜气体的体积,m3(标) h; I新鲜放空气体中惰性气含量,%; 放空新鲜气体中惰性气含量,%;7、 二氧化碳含量对甲醇合成反应的影响二氧化碳也能参加合成甲醇的反应,对于铜系催化剂,二氧化碳的作用比较复杂,既有动力学方面的作用,还可能具有化学助剂的作用,归纳起来,其有利的方面为:含有一定量的C2可促进甲醇产率的提高;提高催化剂的选择性,可降低醚类等副反应的发生; 可更有利于调节温度,防
- 温馨提示:
1: 本站所有资源如无特殊说明,都需要本地电脑安装OFFICE2007和PDF阅读器。图纸软件为CAD,CAXA,PROE,UG,SolidWorks等.压缩文件请下载最新的WinRAR软件解压。
2: 本站的文档不包含任何第三方提供的附件图纸等,如果需要附件,请联系上传者。文件的所有权益归上传用户所有。
3.本站RAR压缩包中若带图纸,网页内容里面会有图纸预览,若没有图纸预览就没有图纸。
4. 未经权益所有人同意不得将文件中的内容挪作商业或盈利用途。
5. 装配图网仅提供信息存储空间,仅对用户上传内容的表现方式做保护处理,对用户上传分享的文档内容本身不做任何修改或编辑,并不能对任何下载内容负责。
6. 下载文件中如有侵权或不适当内容,请与我们联系,我们立即纠正。
7. 本站不保证下载资源的准确性、安全性和完整性, 同时也不承担用户因使用这些下载资源对自己和他人造成任何形式的伤害或损失。