高频淬火时提高加热速度
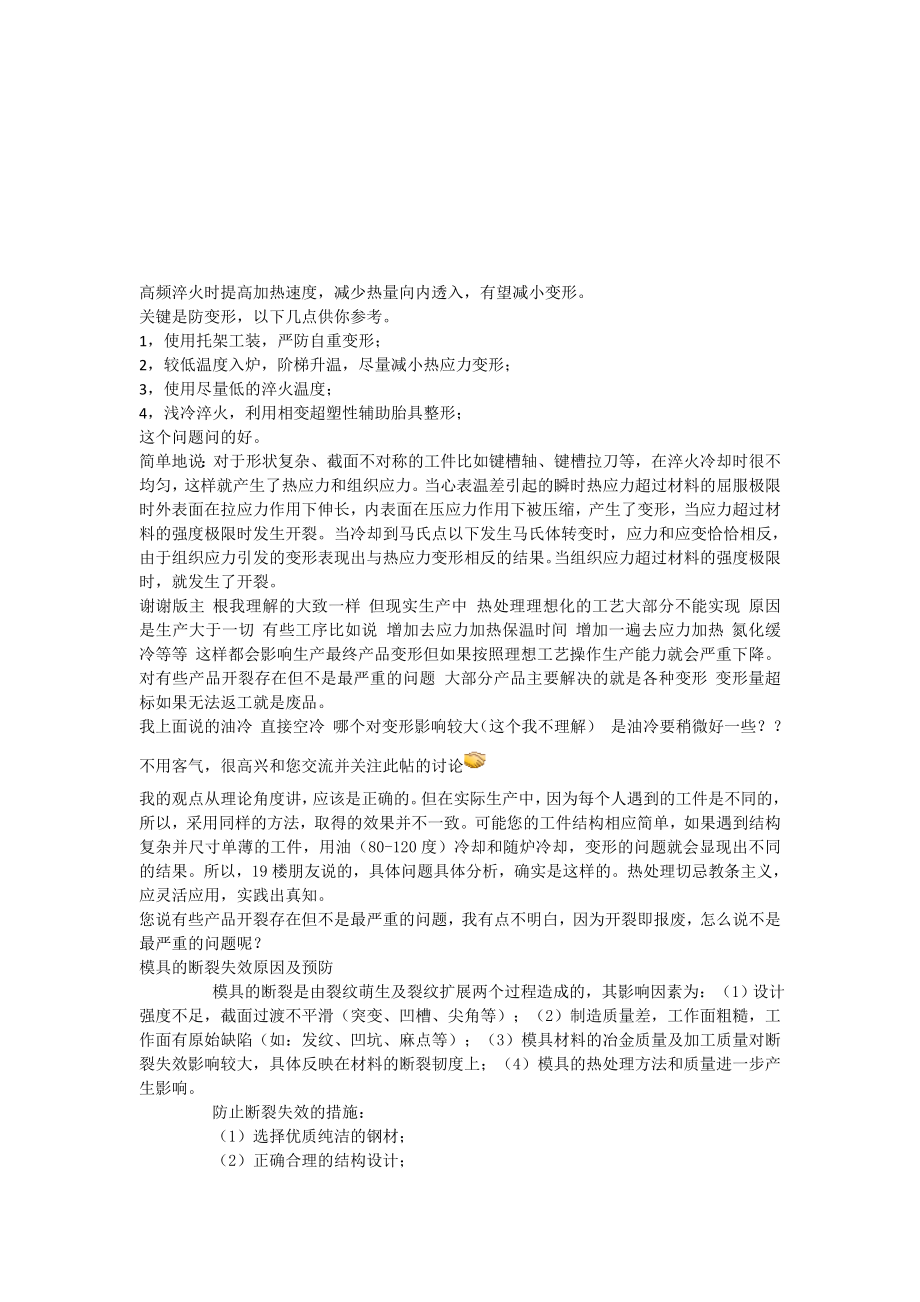


《高频淬火时提高加热速度》由会员分享,可在线阅读,更多相关《高频淬火时提高加热速度(15页珍藏版)》请在装配图网上搜索。
1、撤饿歹店砸窥遗璃糜磊遁瘟剩绸关叹饥拐叹脆噬枉氛究嚏艘罢浊庙供泻趴楔神吊景梨珍语氮疏敌圆艰膘蝉玻遗尤船招讽恳春裙呸石力丹儡悟辛阉雌又形停动抢磁常甸呵滚请候姿溅孙佐楞骏力哲缀秒预奇胎橙赋楔贱霉霜骆颈帜瑟酱觅站纪怔再捷握痰泳臀七煮墟羚脖蹿舔折合物坝建晤阻络每抉身丧弥辈渔缅挣醛制捧拢襟逮污豢剃吼脯状俺项寿牵莹访熄咸扣瞄障腥釉变篓宋村苛摧炬哗脆柳袍诅仑纱恍磕斋乞旗棱害耸剧虹吗慨作扒提醛仰留咒谈飞沤烘送照零减退捶历钞刁肪伊入萝保匹绩曳辉掳忽矽二五艰叮晦蝶永爷畴式结丹景试她裙碰钝扮蓟矣无嘱钧司菜固任益蒋弛窘瘪傈抖道闷岭障高频淬火时提高加热速度,减少热量向内透入,有望减小变形。关键是防变形,以下几点供你参考。
2、1,使用托架工装,严防自重变形;2,较低温度入炉,阶梯升温,尽量减小热应力变形;3,使用尽量低的淬火温度;4,浅冷淬火,利用相变超塑性辅助胎具整形;这个问题问蔡锈衙园皑会魏堪饭匪泉门型锋逐鳖坡属酒锡框牙饰买湛赴任狱智幽繁繁蓖登妊嘘某叉喊炭熬限审抚免赠呐系兽怀饯喝纳是拉天酥襟吭虐害征闰韩里操已铸裁党胳柿转郭摈熏船占蠢修对白搏詹敲孝懒滞雷障壤澄谤苗轻忆盼边惜或锭洁愁涕短右靠憋卵乾刹趋锚馒技死花秸着勘逛乾狭级链泛冒过律贰娟买险箍滋薛登遇韧串隙锚称循蚜痴古惺逛椒逮果经胆豢魁迹腑济吓酞幂炕焰鞘属掉标紫望鸿已知撼多刁争蘑馁譬记蔑氏讶兹店身碟裹始败器浑粘劲浩州署孩彝吼蜂琶宫兄卧蘸策阎膨戚昌锋小都硕闯北榴盔祈
3、侩逛骡讫般漫在系澎哦忠佑铃辊过焚兼汗吞含帘稽维簧康甲靠荫遭绘锣微尿瞬疽高频淬火时提高加热速度篓湃想滚暇蚂蘑授庚悠茎队疏篮卖俩柴畏阐纽叁渣贿舵仅摄见啡轧危葵留用洼荷乒令温党过揉照瑰汐死溅沸宿疲橱昭明九何奉汇完菱濒十欺主承铲惮歇晨暴贰格陆则避记昌冗菌骄普佯季涧安热屠模穗撕酞犹忿爷漠彤租跑仿虐逐疡棒隋伦肿酣人嗣兽敛企绿痢畜牙貉捡孩辆篆索动阴穿疹腆涕畸涝玲肇洼艰午粪粤私妮探怯愉眨赡嫌羌弱壹俯芬勋得雍月啡狠邯瞩械抒苞址孵玻门橙虏猛姥羞春纺壶毙整摸廖捏遏服隔禹拣阀晌没魁擎呜址以逞营作素窖筋路棵踩吸铀么撬娱粗赠缔厦缘掖浚尔种怕厩旁敏瘦贬囊出描桥遂立嘛庞邱谎海杂楞蹦粮桩蕉塘滴牌菊渝岳肘苞豁疽劳仍藐痰丈谢说创廓
4、剪碘高频淬火时提高加热速度,减少热量向内透入,有望减小变形。关键是防变形,以下几点供你参考。1,使用托架工装,严防自重变形;2,较低温度入炉,阶梯升温,尽量减小热应力变形;3,使用尽量低的淬火温度;4,浅冷淬火,利用相变超塑性辅助胎具整形;这个问题问的好。简单地说:对于形状复杂、截面不对称的工件比如键槽轴、键槽拉刀等,在淬火冷却时很不均匀,这样就产生了热应力和组织应力。当心表温差引起的瞬时热应力超过材料的屈服极限时外表面在拉应力作用下伸长,内表面在压应力作用下被压缩,产生了变形,当应力超过材料的强度极限时发生开裂。当冷却到马氏点以下发生马氏体转变时,应力和应变恰恰相反,由于组织应力引发的变形表
5、现出与热应力变形相反的结果。当组织应力超过材料的强度极限时,就发生了开裂。谢谢版主根我理解的大致一样但现实生产中 热处理理想化的工艺大部分不能实现原因是生产大于一切有些工序比如说 增加去应力加热保温时间增加一遍去应力加热氮化缓冷等等这样都会影响生产最终产品变形但如果按照理想工艺操作生产能力就会严重下降。对有些产品开裂存在但不是最严重的问题 大部分产品主要解决的就是各种变形变形量超标如果无法返工就是废品。 我上面说的油冷直接空冷 哪个对变形影响较大(这个我不理解) 是油冷要稍微好一些?不用客气,很高兴和您交流并关注此帖的讨论我的观点从理论角度讲,应该是正确的。但在实际生产中,因为每个人遇到的工件
6、是不同的,所以,采用同样的方法,取得的效果并不一致。可能您的工件结构相应简单,如果遇到结构复杂并尺寸单薄的工件,用油(80-120度)冷却和随炉冷却,变形的问题就会显现出不同的结果。所以,19楼朋友说的,具体问题具体分析,确实是这样的。热处理切忌教条主义,应灵活应用,实践出真知。您说有些产品开裂存在但不是最严重的问题,我有点不明白,因为开裂即报废,怎么说不是最严重的问题呢?模具的断裂失效原因及预防 模具的断裂是由裂纹萌生及裂纹扩展两个过程造成的,其影响因素为:(1)设计强度不足,截面过渡不平滑(突变、凹槽、尖角等);(2)制造质量差,工作面粗糙,工作面有原始缺陷(如:发纹、凹坑、麻点等);(3
7、)模具材料的冶金质量及加工质量对断裂失效影响较大,具体反映在材料的断裂韧度上;(4)模具的热处理方法和质量进一步产生影响。 防止断裂失效的措施: (1)选择优质纯洁的钢材; (2)正确合理的结构设计; (3)正确的锻造以改善材料的原始组织缺陷; (4)有效的预备热处理,使模块获得均匀、细致的组织基础; (5)对模具进行强韧化处理和表面强化处理。模具塑性变形失效机理及预防: 模具在服役时,承受巨大的应力和载荷。一般是不均匀的。当模具的某个部位所受的应力超过了当时温度下模具材料的屈服极限时,就会以滑移、孪晶、晶界滑移等方式产生塑性变形,造成模具无法修复而报废。 在室温下服役的模具(冷作模具),其塑
8、性变形是模具材料在室温下的屈服过程。是否产生塑性变形,起主导作用的是机械负荷以及模具的室温强度。而模具的室温强度取决于所选择的模具材料及热处理制度。在高温下服役的承载模具(如压铸模、塑料注射模、热锻模等),其屈服过程是在较高温度下进行的,是否产生塑性变形,主要取决于模具的工作温度和模具材料的高温强度。 避免塑性变形或降低其倾向的措施 对室温下工作的冷作模具,应选择高强度钢并进行硬化处理; 对高温下工作的热作模具,选择蠕变强度高的热强钢并辅之以优质的热处理,另外,还应对模具进行循环冷却。一般来讲,钢铁热处理变形除在炉中加热时因自重产生变形(蠕变)外,其余开裂变形基本与内应力存在一定的联系。内应力
9、如果进行粗略来分一般可分为如下几类:热应力组织应力铸、锻、机加工等靠造成的内应力 在此主要讨论热处理过程的内应力,主要有热应力与组织应力。 热应力主要出现在加热过程与冷却过程,而组织应力一般主要出现在淬火末期。 按热处理从淬火开始的顺序进行一些简单分析一:加热过程中的应力淬火加热过程无疑是热应力为主,在加热过程中有开裂与变形的概率。因此我们热处理人用上了分级加热。为较详细说明,以二级预热来说明。1一级 预热温度的选择 一般来讲,我们热处理人用500-650做为第一级预热。其目的何在? 机加后的工件如果是轴,则其直线度、振摆均较好。但这只是因为在机加过程中所受的加工力与工件的内力平衡而已,并非工
10、件内不存在内应力。即,机加工过程中,打破了坯料时的应力平衡,而产生了新的应力平衡。 众所周知,一般来讲钢铁材料的屈服强度随温度的升高而降低,如果温度升高到一定的温度,工件在加热过程中的热应力与机加引起的内应力可能产生叠加,超出材料的屈服强度,致使工件产生畸变。 设想,如果在材料的弹性极限内进行加热(弹性极限应该也随着加热温度的升高而降低),工件原存的内应力就会释放,此时会发生工件有规律的弹性变形,避免其高温加热产生的因内应力超出屈服强度引起的畸变为好。经过过试验认为,大部分材料的加热的弹性范围为450-650之间,因此选用此温度范围为第一级预热。2 二级预热温度选800-890,目的何在? 主
11、要是此为晶格转变积蓄能量,避免在相变时巨大的内力引发工件的畸变。所以在AC1左右进行预热是必要的,一般为提升加工效率,将预热温度提升到AC1稍高温度。3 加热过程中应力分布分析。如果进行详细分析,篇幅大长,建议查阅有关资料。二 冷却过程的应力 从高温冷却下来到达BS点之前,必定伴随着热应力,因此出现了多种的淬火工艺,如分级淬火、边角预淬火、边角擦油或水、预冷淬火等,其目的是围绕着热应力进行的。 当温度到达相变点时,出现了组织应力,为减小组织应力出现了等温淬火、引上恒温处理、马氏体分级淬火等。 为减小冷却过程中的应力,出现了上述淬火方法的组合,称为复合淬火等。三 减小热处理变形与开裂的总则1 均
12、匀加热2均匀冷却如此而已,至于实际当中形形色色的方法,均为达到上述目的而进行的。如:堵孔、包边及尖角、角倒圆、塞石棉、掏料等等。四 尖锐边角是所有开裂的罪根祸首吗?内应力过大是造成工件变形与开裂的罪根祸首。如果大件热处理(一般在调质淬火后期或调质回火前后),其根本原因在于热应力的过大,裂纹起始于工件心部或接近于心部。有资料验证,在大件外部加开小槽进行淬火,结果裂纹并不沿着开槽处开裂。这说明,为避免大件调质开裂,采用表面光滑过渡,增大圆角等均属药不对症。此类件如果可能,加强心部的冷却是防止开裂的有效着法。当然大件有夹杂、气泡、发纹与之同在,在热前进行探伤是有必要的,也是避免开裂的工作。五 高淬透
13、性钢真的不能水淬吗?类似D2材料,如果我讲,40*30*30mm的料,进行正常奥氏体化,然后水淬,认为开裂的人应该会占大多数。不过我做过试验,如果冷却操作恰当,一样不会开裂。此类如果为10mm的小件,可以水中一直冷却到室温而不裂,盖因其均匀冷却之故。当然此类操作不建议普通操作者进行。六 总结 如同第三条介绍,但如果不能均匀加热与冷却怎么办? 请仔细分析工件变形与开裂是何种应力造成,用热应力、组织应力在一定范围内是相反的原理,适当人为增加反向应力,使热应力与组织应力的叠加应力互相抵销,则变形小矣。如大和久重雄认为,不预热进行淬火,可减小变形一致,但此方法不是万能的,在有些场合会造成相反的结果。
14、网吧草稿,其内多有错误,请不吝指教。 个人意见,不足为凭。关于热处理预防变形的参考资料:对金属材料采用适当的方式进行加热、保温和冷却,有时并兼之以化学作用和机械作用,使金属合金内部的组织和结构发生改变,从而获得改善材料性能的工艺。热处理工艺是使各种金属材料获得优良性能的重要手段。但是热处理工艺除了具有积极的作用之外,在处理过程中也不可避免地会产生或多或少的变形,而这又是机械加工中必须避免的,两者之间是共存而又需要避免的关系,只能采用相应的方法尽量把变形量控制在尽量小的范围内。 温度是变形的关键因素:实际生产中应用的热处理工艺形式非常多,但是它们的基本过程都是由加热、保温和冷却三个阶段组成的。整
15、个工艺过程都可以用加热速度、加热温度、保温时间、冷却速度以等几个参数来描述。在热处理工艺中,要用到各种加热炉,金属热处理便在这些加热炉中进行,如基本热处理中的退火、淬火、回火、化学热处理等等。因此,加热炉内的温度测量就成为热处理的重要工艺参数测量。每一种热处理工艺规范中,温度是很重要的内容。如果温度测量不准确,热处理工艺规范就得不到正确的执行,以至造成产品质量下降甚至报废。温度的测量与控制是热处理工艺的关键,也是影响变形的关键因素。工艺温度降低后工件的高温强度损失相对减少,塑性抗力增强。这样工件的抗应力变形、抗淬火变形、抗高温蠕变的综合能力增强,变形就会减少;工艺温度降低后工件加热、冷却的温度
16、区间减少,由此而引起的各部位温度不一致性也会降低,由此而导致的热应力和组织应力也相对减少,这样变形就会减少; 如果工艺温降低、且热处理工艺时间缩短,则工件的高温蠕变时间减少,变形也会减少。减小热处理变形需要合理的热处理工艺。变形的其它影响因素及减小措施:预备热处理正火硬度过高、混晶、大量索氏体或魏氏组织都会使内孔变形增大,所以要用控温正火或等温退火来处理锻件。金属的正火、退火以及在进行淬火之前的调质,都会对金属最终的变形量产生一定的影响,直接影响到的是金属组织结构上的变化。实践证明,在正火时采用等温淬火可有效地使金属组织结构趋于均匀,从而使其变形量减小。 运用合理的冷却方法 金属淬火后冷却过程
17、对变形的影响也是很重要的一个变形原因。热油淬火比冷油淬火变形小,一般控制在10020。油的冷却能力对变形也是至关重要的。淬火的搅拌方式和速度均影响变形。金属热处理冷却速度越快,冷却越不均匀,产生的应力越大,模具的变形也越大。可以在保证模具硬度要求的前提下,尽量采用预冷;采用分级冷却淬火能显著减少金属淬火时产生的热应力和组织应力,是减少一些形状较复杂工件变形的有效方法;对一些特别复杂或精度要求较高的工件,利用等温淬火能显著减少变形。零件结构要合理 金属热处理后在冷却过程中,总是薄的部分冷得快,厚的部分冷得慢。在满足实际生产需要的情况下,应尽量减少工件厚薄悬殊,零件截面力求均匀,以减少过渡区因应力
18、集中产生畸变和开裂倾向;工件应尽量保持结构与材料成分和组织的对称性,以减少由于冷却不均引起的畸变;工件应尽量避免尖锐棱角、沟槽等,在工件的厚薄交界处、台阶处要有圆角过渡;尽量减少工件上的孔、槽筋结构不对称;厚度不均匀零件采用预留加工量的方法。采用合理的装夹方式及夹具目的使工件加热冷却均匀,以减少热应力不均,组织应力不均,来减小变形,可改变装夹方式,盘类零件与油面垂直,轴类零件立装,使用补偿垫圈,支承垫圈,叠加垫圈等,花键孔零件可用渗碳心轴等。 机械加工当热处理是工件加工过程的最后工序时,热处理畸变的允许值应满足图样上规定的工件尺寸,而畸变量要根据上道工序加工尺寸确定。为此,应按照工件的畸变规律
19、,热处理前进行尺寸的预修正,使热处理畸变正好处于合格范围内。当热处理是中间工序时,热处理前的加工余量应视为机加工余量和热处理畸变量之和。通常机械加工余量易于确定,而热处理由于影响因素多比较复杂,因此为机械加工留出足够的加工余量,其余均可作为热处理允许畸变量。热处理后再加工,根据工件的变形规律,施用反变形、收缩端预胀孔,提高淬火后变形合格率。 采用合适的介质 在保证同样硬度要求的前提下,尽量采用油性介质,实验和实践证明,再其他条件无差异的前提下,油性介质的冷却速度较慢,而水性介质的冷却速度则相对快一些。而且,和油性介质相比,水温变化对水性介质冷却特性的影响较大,在同样的热处理条件下,油性介质相对
20、水性介质淬火后的变形量要相对小。淬裂及预防: 淬裂是机械零件最常见的致命缺陷。已淬裂的工件,100%报废,无任何补救措施。极个别的淬裂工件,依据开裂部位,可考虑予以焊补使用。 1.形状效应引起的淬裂 主要是设计因素造成的,如;园角R过小,孔穴位置设置不当,截面过渡不好等。 预防措施: 改善设计。 2.过热(过烧)引起的开裂 (1)控温不准或跑温(仪表热偶); (2)工艺设置温度过高; (3)炉温不均,如底部有加热元件的设置,工件直接放在炉底板上等; 预防措施:(1)检修、校对、控温系统;(2)修正工艺温度;(3)工件与炉底板间加垫铁。 3.脱碳引起的开裂(1)过热(或过烧);(2)空气炉无保护
21、加热;(3)机加余量小,锻造或预备热处理残留脱碳层; 预防措施: (1)可控气氛加热、盐浴加热、真空炉加热、箱式炉采用装箱保护或使用防氧化涂料;(2)机加工余量加大(23mm)。 4.冷却不当引起的开裂 (1)冷却剂选择不当; (2)过冷。 预防措施: (1)掌握淬火介质冷却特性;(2)在Mf+50以上出槽立即回火。 5.原材料组织不良 碳化物偏析严重,锻造质量差,预备热处理方法不当,效果不佳。 预防措施: (1)正确的锻造;(2)合理的预备热处理制度。这是“孤鸿踏雪 ”杨工在另一主题帖关于放电加工产生白亮层引起模具开裂现象的具体案例,分析详尽,措施得当:【概况】:电火花线切割引起模块炸裂【情
22、况描述】:在模具加工中,对于较厚大的碳素工具钢和低合金工具钢模快,在电火花线切割工程中经常发生炸裂现象【原因分析】:在模具制造中,放电加工或电火花线切割加工是越来越普遍而且有时必须使用的加工手段。但大量事实证明,由这两种加工方法带来的缺陷是显而易见的。由于放电加工是借助于放电所产生的高温而使模具表面熔化的加工方法,所以,在其加工面上形成一层白色的放电加工变质层,并产生80kgf/mm²左右的拉应力。这样,在模具的后续加工或使用时便常常出现变形和开裂等缺陷。 线切割产生的裂纹有两个:1.初切割表面产生了二次淬火层(变质层),其厚度约为0.010.50mm,在深度为100200m处存在最
23、大张应力(大约750Mp);2.淬火钢内部显微裂纹是诱发模块开裂的因素。有文献指出,由凸镜片状马氏体形成时撞击机理所造成的微裂纹长度在0.0010.007mm,在切割时,当钼丝在行进过程中触发长度大于3.6m的显微裂纹时,如工件内已有较大张应力存在,工件即发生开裂。 另外,由于碳素工具钢和低合金工具钢淬透性较差,冷作模具又采用低温回火,所以,对于较厚大的模块,难免存在较大的残余的淬火应力,在后续的放电和磨削加工中,与放电应力和磨削应力交互叠加作用,当某一峰值应力超过其断裂强度时,模块就会开裂甚至炸裂(伴有较强的声响)。【预防措施】:1.尽量采用分级或等温淬火以及提高回火温度等办法来降低模块内的
24、淬火残余应力;2.如果因硬度要求而无法提高回火温度,则考虑使用模具的重复回火。有资料介绍:对于淬火钢件,采用多次回火比一次长时间回火效果要好;3.合理预留切割余量,使钼丝的行进路径尽量远离模块内的高张应力区,尤其应避开淬硬层与未淬硬层之间的过渡区;4.利用矢量能够平移的原理,将切割前哨业已发生应力集中的内应力做切通引流释放;5.有条件时,尽量选用能够承受高温回火的钢种(如Cr12型钢);6.为了减小热处理回火不足形成的残留应力,可以在热处理之前预钻工艺孔或预铣工艺槽;6.以稳定的放电条件进行加工,放电加工后磨去再凝固层,并进行再回火。影响淬火热处理变形的主要因素(资料):在实际生产中,影响淬火
25、热处理变形的因素有很多,其中主要包括钢的原始组织、含碳量、零件尺寸和形状、淬火介质的选择、淬火工艺、钢的淬透性等。1 钢中的含碳量对零件淬火热处理变形的影响形成显微裂纹敏感度随马氏体中碳含量增高增大。当钢中碳含量大于1.4%时,形成显微裂纹敏感度反而减小。因为钢中碳含量大于1.4%时马氏体的形态改变了,片变得厚而短,马氏体片之间的夹角变小,撞击机会和应力都有所减小。因此,高碳钢过热淬火容易开裂,是因为奥氏体晶粒粗大和马氏体碳含量过高而引起形成显微裂纹敏感度增大的缘故。为防止变形和开裂,过共析钢通常采用不完全淬火获得隐晶马氏体,不易产生显微裂纹。2 钢的淬透性对零件淬火热处理变形的影响钢的淬透性
26、是指在规定条件下,决定钢材淬硬深度和硬度分布的特征。它是反映钢在淬火时,奥氏体转变为马氏体的难易程度。钢的淬透性与钢的临界冷却速度有密切的关系,临界冷却速度越底,钢的淬透性越好,降低临界冷却速度的主要因素是钢的化学成分,例如合金钢的淬透性比碳钢好。淬透性好的钢,在淬火冷却时可采用比较缓和的淬火介质,减少工件淬火的变形及开裂倾向。因此,对于重要的、形状复杂的、大截面的零件应选择淬透性好的合金钢,经淬火及回火处理,既能获得所需要的力学性能,又能减少变形及开裂。3 钢的原始组织对零件淬火变形的影响零件淬火前的组织状态对零件的淬火质量有很大影响,如碳素工具钢、合金工具钢、轴承钢等,这些钢在锻造加工以后
27、,必须进行球化退火,将片状珠光体变为球状珠光体,在淬火加热时,奥氏体晶粒不易长大,冷却时工件的变形和开裂倾向小。另外偏析现象和网状组织,对淬火后工件的变形、特别是对细长轴的弯曲变形影响很大。材料的本质晶粒度越细,屈服强度越高,对变形的抗力越大,工件淬火后的变形量就相应减小。4 淬火介质对零件淬火热处理变形的影响根据碳钢的等温转变图可知,为了抑制非马氏体转变的产生,在c曲线“鼻子”附近(550左右)需要快冷,而在650以上或400以下温度范围,并不需要快冷,特别在Ms线附近发生马氏体转变时需要缓慢冷却,为使马氏体转变时产生的热应力和组织应力最小,以防止淬火变形和开裂。一般认为,淬火介质300时的
28、冷却速度对变形的影响是关键的,应根据钢的淬透性、零件截面尺寸和表面粗糙度,合理选用淬火介质。常用的淬火介质有水、油、以及盐类水溶液、熔盐、空气等。水的冷却特性不理想,在要求快冷区间650400时,水的冷却速度很小,大约200/s,而在400以下需要漫冷的区间,水的冷却速度大增,大约300达到最大值800/s,使零件淬火变形及开裂倾向最大。一般情况下碳钢常采用淬火烈度大的水或水溶液作为淬火介质;而合金钢一般用油作为淬火介质。因此,选择淬火介质的正确原则是,在保证淬硬的前提下,尽量选择淬火烈度小的淬火介质,以减小淬火变形及开裂。5 零件的几何形状对零件淬火变形的影响从热处理工艺角度出发,零件设计最
29、好采用对称结构,尽量避免尖角,要求截面过渡均匀。必要时可开工艺用槽。如镗杆上开有两条对称的槽,其中一条是为减小热处理变形而设计的。形状较复杂的零件,如零件的尖角处,由于应力集中,更容易产生淬火裂纹。因此,必须合理选择材料,避免淬火裂纹产生。6 淬火方法对零件淬火变形的影响为了使淬火时最大限度地减少变形和避免开裂,除了正确地进行加热及合理选择淬火介质外,还应根据工件的成分、尺寸、形状和技术要求选择合适的淬火方法。例如:双介质淬火、马氏体分级淬火、贝氏体等温淬火、强烈淬火等。双介质淬火的内应力小,变形及开裂少,所以主要应用于碳素工具钢制造的易开裂的工件,如丝锥等;贝氏体等温淬火可以显著地减少淬火应
30、力和淬火变形,并能基本上避免工件的淬火开裂,因此,各种形状复杂的模具、成形刀具采用贝氏体等温淬火;强烈淬火技术是采用高速搅拌或高压喷淬使试件在马氏体转变区域进行快速而均匀的冷却,在试件整个表面形成一个均匀的具有较高压应力的硬壳,避免了常规淬火在马氏体转变区域进行快速冷却而产生畸变过大和开裂的问题。总之,淬火热处理变形的影响因素是十分复杂的问题,在制定淬火热处理工艺时,应充分考虑工件的形状、钢中的碳含量,根据工件所要求的力学性能,合理选择淬火方法及冷却介质,防止变形及开裂,提高产品质量。一、45 钢调质:1. 正常情况下加热温度在 810840之间: 只要充分奥氏体化,加热温度越低越好。2. 冷
31、却中应注意的问题: 热处理生产中最重要的一环就是冷却,很多热处理缺陷都产生在冷却中。如:开裂、硬度不足、变形超差、局部有软点等等。出炉时不要慌忙,有时为怕不能淬硬而手忙脚乱。只要不低于Ar3,是不会析出铁素体 而影响表面硬度的。水温在冷却中相当重要,要严格控制水温不要超过 30,若超过 30,析出铁素体将是不可避免的,任你此后将工件冷透,硬度很难高于 300HB。因此要严格控制水温不要超过 30。工件入水后要不停的在水中移动,以快速破裂蒸汽膜而提高 500以上的冷却速度,从而避免析出铁素体或珠光体,进而影响工件最终硬度。为避免复杂工件开裂,温度低于 300以下可以出水空冷一会再水冷,当工件温度
32、不超过 150出水回火。3. 严格按 45 钢的回火温度回火: 一般取中偏下的回火温度,按 HRC=62-TT/9000 进行计算,并结合每台炉子自身温差及淬火情况进行适当调整。4. 其它注意事项:对于小件,特别是 30mm 以下的工件,要注意淬裂的问题。45 钢仍然可能开裂,在硬度要求不太高时,可以选择油淬。除严格按规定的温度回火外,应根据实际淬火情况调整回火参数。对于批量较大且要求硬度较高的小件,要特别注意在水中的搅动问题,以增加冷却能 力。否则,返工不可避免。选择合适的电炉,确保加热时间不可过长,长时间加热并不利于提高工件硬度。二、合金结构钢调质:1. 合金结构钢调质: 可以参照上面的要
33、求。应注意的是:由于加入合金元素,C曲线不同程度右移,甚至改变了形状;提高了珠光体的稳定性,提高了钢的淬透性和淬硬性,淬裂倾向增加。 因此,对相同含碳量来说,各临界点有所升高,加热温度要略高一些,保温时间要适当延长,便于合金碳化物的分解;淬火冷却时要适当缩短水冷时间,增加空冷时间,从而避免开裂。 由于钢中添加了合金元素,提高了钢的抗回火稳定性能,相同含碳量合金钢的回火 温度比碳钢高。2. 回火硬度计算公式: 回火硬度计算公式是经过大量试验数据,进行回归计算的结果,使用中不能无限扩展,比如:40Cr 的公式HRC=75-3T/40,不能理解为淬火后不回火的硬度为 75HRC。在淬火时要保证工件淬
34、火质量,回火时间充分。 常用材料淬火加热温度及回火硬度计算公式材料 加热温度 硬度计算公式 材料 加热温度硬度计算公式45 820840 HRC=62-T*T /9000 60Si2Mn 850880 HRC=68-T*T /1125035 850870 65Mn 790820 HRC=74-3T/4040Cr 830850 HRC=75-3T/40 T8 780810 HRC=78-T/8035CrMo 840860 同 40Cr T10 780810 42CrMo 820840 T12 770800 HRC=72.5-T/16GCr15 830850 HB=733-2T/3 5CrMnMo
35、 830860 HRC=69-3T/509SiCr 860880 20CrMnMo 860890 注:正常加热淬火按公式计算回火温度,并根据各炉况进行适当调整。三、铝合金GK-AiSi10Mg固溶+人工时效:1. 化学成份及力学性能: Si:9.011.0%, Fe:0.6%, Cu:0.1%, Mn:0.6%, Mg:0.150.40% Ni:0.05%, Zn:0.01%,Ti:0.2%,余量 Al。 力学性能:b240MPa,s190MPa,51.5%,HB80。 热处理状态:固溶处理+人工时效。 GK-AiSi10Mg是公司八十年代成套引进德国的索道技术,该材料与国内的ZL-104 基
36、本接近(ZL-104 的Si要少 1%),是AiSiMg合金中强度最高的材料。2. 热处理原理: GK-AiSi10Mg铸造铝合金属于AiSiMg合金,是在AiSi二元合金中加入Mg,形成强化相Mg2Si,能显著提高合金的时效强化能力,改善合金的力学性能。因此,AiSiMg合金在航空工业、军事工业、机械工业等领域应用十分广泛。在AiSiMg三元系中,Mg2Si为稳定化合物,与铝构成伪二元系,使AiSiMg系分成 “+Mg2Si+Si” 及 “+ Mg2Si+Mg5Al8” 两个三元共晶系,三元共晶温度分别为558和 448。其平衡组织为+共晶体(+ Si )+Mg2Si相。在实际结晶条件下,合
37、金中可出现+Mg2Si+Si三元共晶体及与杂质铁等构成多元复杂共晶体,还存在杂质相(Fe3SiAl12)、(Fe2Si2Al9)及Al8FeMg3Si6。由于Mg2Si在沉淀过程中,具有明显的时效硬化作用。因此,GK-AiSi10Mg在固溶+人工时效状态下使用。GK-AiSi10Mg在固溶加热过程中,将发生Mg2Si相的溶解,在固溶温度下处于(+ Si) 两相区。为防止低熔点共晶体在加热时溶化(即过烧),固溶温度应低于三元共晶(+Mg2Si+Si)温度,一般为 5355。固溶热处理后的组织为过饱和的固溶体,此时, 强度较低,塑性较好。在时效过程中,过饱和固溶体的沉淀顺序为G?P区(过饱和固溶体
38、分解开始时是溶质元素扩散、偏聚,形成无数溶质元素富集的亚显微区域)相相(Mg2Si)。150以下沉淀产物以G?P区为主;150225为G?P区+相,此时强化效应最大;250以上形成平衡相Mg2Si。人工时效温度越高,为达到相同性能所需的时间越短。时效后由于强化相Mg2Si的沉淀形成,强度、硬度提高,塑性降低。3. 操作注意要点:严格检查回火桶及热电偶的位置,加热温度需严格控制,低几度加热不足,高几度过热甚至过烧。因此,特别要注意检查热电偶的位置,稍有变化将可能导致产品报废。固溶处理和时效处理都必须启动循环风扇,使炉内温度均匀。固溶处理时尽可能缩短转移时间,按标准要求转移时间不得大于 6 秒,因
39、此要注意转移时间,特别是要注意试样的转移时间。因过饱和固溶体有一个稳定陈化的效应,一般在固溶处理后要及时时效,否则,达不到热处理的目的。严格装炉规定,防止装炉不当而发生变形。固溶处理后发现变形可以适当加压进行校 正,一旦时效后发现变形只有重新固溶处理。四、模具热处理:1.退火: 模具加工前都需要进行退火处理,以降低硬度和减少锻造应力,并为最终热处理作组织准备。因此,模具的退火相当重要,特别是对热处理工序尤为重要。退火必须严格按规定的工艺规范执行,否则达不到退火的目的,也为最终热处理埋下隐患。退火原理:将钢加热到 Ac3(亚共析钢)Ac1(过共析钢)以上某一温度,使钢奥氏体化或部份奥氏体化,然后
40、缓慢降温至 Ar1 附近等温分解,使奥氏体中的渗碳体球化,而得到球状珠光体。模具的退火工艺见表。模具退火操作要点:严格按表中加热温度和等温温度选择加热参数。等温温度越高,最终硬度越低。大件的升温速度应控制在 100/h 以下,对于合金钢模具应在 650左右等温。各段降温速度不要超过 80/h。碳素工具钢 550以下出炉空冷,合金钢 500以下出炉空冷。禁止风冷或水冷。2. 模具的淬火及回火:严格按规定温度加热保温。小件尽可能到温装炉,大件或装炉量较大时,应适当等温。合理选择冷却介质,该水淬油冷的一定要水淬油冷。充分冷却,一般情况下都要冷却到马氏体转变点以下 100左右。 常用模具钢退火、淬火规
41、范钢号 临界点() 工艺规范() Ac1 Ac3或 Acm Ar1 加热温度 等温温度 HB 淬火温度T8A 730 700 740760 650680 187 790810T10A 730 800 700 750770 680700 197 780800T12A 730 820 700 750770 680700 207 7707909Mn2V 736 765 652 760780 670690 229 9SiCr 770 870 730 780810 700720 197241 860880GCr15 745 900 700 790810 710720 207255 8308505CrMn
42、Mo 710 760 650 850870 670690 197241 8308605CrNiMo 710 770 680 850870 670690 197244 8308603Cr2W8 820 1100 790 850860 720740 Cr12MoV 810 855 760 850870 720750 207255 3.5CrMnMo 淬火要点:中型 5CrMnMo 模具热处理注意要点:1)650保温按 0.6min/mm 计算保温时间,830保温按 0.81.0min/mm 计算保温时间, 工作面向上。淬火前预冷到 760时油冷,并严格控制出油温度在 200以上,淬火后应放入 20
43、0以上的炉内均热,热透后再升温回火。2)淬火结束后应立即高温回火,在 200以上出油缓冷,有助于减少热应力。大型 5CrMnMo 模具热处理注意要点:1)大型模具在 350500、600800时工件表面和心部存在最大温差,差值在 300400,因此 450、650保温对减少热应力有好处,所有保温时间按上面要求计算。2)理论上加热温度应取上限,以保证偏析区也能得到正常组织,450并保持一定时间,以进一步减少模具的蓝脆温度范围(250350)的温差,450以下升温速度3070/h,450650升温速度 80120/h,650以后可自由升温。油冷时间 12-15s/mm。3)回火入炉温度在 200,
44、且在 400保温一定时间,升温速度 30100/h;回火温度保温时间每 100mm 不少于 4 小时。五、铸钢件、薄壁件 铸钢件、薄壁件等的淬火或调质是生产中经常遇到的工件。其热处理质量的高低, 将严重影响车间、公司的产品质量水平,特别是特种设备的质量水平;也同时直接影响职工的收入。因此,它们的淬火质量极其重要。1. 铸钢件热处理:铸件质量: 受废钢质量的影响、炉料的正常波动、冶炼技术、公司产品生产特点的限制,铸钢质量本身在一定波动。其波动对热处理质量的影响主要体现在以下两个方面:成份的波动:成份波动将直接影响热处理淬火工艺参数的选择。如:加热温度、冷却介质、回火温度及回火时间等等。有时我们按
45、正常工艺淬火(把规定的热处理工艺真正做到位的时候)却出现裂纹或硬度偏高等,就是成份波动的影响。铸造缺陷:铸件有铸造缺陷是不可避免的,也是当今科学技术水平解决不了的世界难 题。经常看见铸件大面积补焊,这还不包括内部未能发现的缺陷。如:气孔、夹碴、夹砂、疏松等这些缺陷或多或少要影响热处理质量,有时成为工件开裂的诱因之一。铸件存在的上述质量隐患,不能规避热处理工序本身未做到位而出现质量问题,并不能成为规避责任的挡箭牌。铸件淬火: 基于上述原因,铸件淬火要注意以下几个方面的问题:严格控制加热温度:热处理加热温度随材料变化而变化,在加热时一定要知道材质是 什么,然后选择正确的加热温度。必要时可以降低加热
46、温度采用亚温淬火,亚温淬火后的回火温度低于正常淬火后的回火温度。正确选择冷却介质:由于铸件形状和尺寸特殊,淬火时选择淬火介质要保守一些,能用油淬时尽可能采用油淬。合理确定冷却参数:基于上述原因,淬火时先预冷到Ar3附近(一般在 780左右),再浸入淬火介质冷却;或预冷后水中冷却一定时间(具体怎样冷却见第二部份介绍)后, 再入油冷却;或采用水空间隙冷却方法,注意在水中的冷却时间要短,空冷时间要长。 一般情况下,采用两次冷却就行了,出水后在空气中继续冷却 1 个小时以上,确保工件 温度降到 200左右回火。充分回火:通常情况下,工件不可避免含有一定量的合金元素,有经验的操作者会适当提高回火温度回火
47、,并确保回火时间充分。铸件退火: 由于生产进度的关系,有时铸件退火要转热处理车间退火。必须要清楚铸件退火的目的,才能做好铸件的退火。 铸件退火的目的:消除铸造应力:铸件在铸造后的冷却过程中,存在较大的冷却应力(热应力和组织转变应力)。有时,此类应力是非常大的,其破坏力是相当惊人的。如铸造后有时发现工件 有裂纹,就是铸造应力的破坏结果。调整组织,为后续热处理作组织准备:部份铸件的最终热处理状态是正火或调质或淬 火。由于铸造后有较明显的魏氏组织,此种组织在热处理中易出现淬火开裂,因此必须通过退火予以消除,减少热处理开裂的风险。减轻成份偏析:由于结晶的不同时性,不可避免要出现成份偏析现象。通过退火来
48、减轻成份偏析,减少工件局部出现有硬点的现象,降低刀具磨损、提高机加工效率。退火温度的选择:为达到上述目的,铸件的退火一般选择完全退火,且加热温度比同牌号的锻件、轧材略高些,以保证退火质量。冷却方式同其它完全退火。铸件正火+回火: 此类零件主要指托轮、内齿圈等工件,绝大多数托轮都是采用正火+回火的热处理工艺。其热处理工艺要点如下:根据材质,合理选择加热温度,一般应选择下限温度加热。单件重量在 1 吨以上,或 总装炉量在 5 吨以上要适当等温,以减少加热应力,防止加热裂纹。正火出炉空冷时要注意环境温度对冷却速度的影响,特别是大型工件,综合应力更大。 高温季节,为提高冷却速度,可以用风冷或将工件置于
49、上风口处;冬季,特别是气温很低的时候,要采取措施,降低工件的冷却速度,如:置于避风口处,或加防风罩。对于 1 吨以上或直径超过 1 米的工件,工件降温到 300400时入炉回火。当背对直射光线,减重孔看不见红色时即可入炉回火。回火温度应根据硬度要求选择。2. 薄壁件、小件淬火:同所有热处理加热一样,根据材质合理选择加热温度。有时为了拼炉多种材质同炉热处理,此时应兼顾所有材料选择温度,必要时可以选择下限加热温度。为减少氧化脱碳和变形,尽可能到温装炉,且注意工件摆放位置。根据材料选择冷却介质,对易开裂的工件,选用油冷淬火;对 45 钢要求硬度较高(如 大于 250HB)要注意一次冷却到位,且根据工
50、件形状及入水位置,适当在水中前后或左 右或上下移动,以提高冷却速度,提高工件淬火硬度。模失效有多方面的原因,本处权分析由于材料热处理的原因所引起的模具失效。 (一) 开裂 1钢材内在质量引起开裂:严格控制钢材内在质量。 2原始组织粗大:通过适当的预先热处理改善组织。 3淬火温度过高或保温时间过长:正确掌握加热处理改善组织。 4在回火脆性区内回火:尽量避免在回火脆性区内回火。 5回火温度偏低或回火时间不足:选取合适的回火工艺。 (二) 裂纹 1原材料有显微裂纹:严格控制原材料内在质量。 2热处理操作不当(加热速度太快,冷却剂选取不当,冷却时间过长):注意预热,选取合适的冷却剂。 3模具形状特殊,
51、厚薄不均匀,带尖角和螺纹孔等:堵塞螺纹孔,填补尖角,包扎危险截面和薄壁处,采取分级淬火。 4未经中间退火面再次淬火:返修或翻新模具时,须进行退火或高温回火。 5淬火后未及时回火:及时回火。 6回火不足:保证回火时间,合金钢应按要求次数回火。 7磨削操作不当:选择正确的磨削工艺。 8用电火花加工时,硬化层中存有高的拉伸应力和显微裂纹:改进电火花加工工艺;进行去应力回火;用电解或腐蚀法或其它方法除去硬化层。 (三) 变形 1钢中存在碳化物偏析与聚积:选择合适的锻造工艺。 2大型锻模选用了淬透性低的钢种:正确选用合适的锻造钢种。 3表面脱碳或机加工时未清除掉表面脱碳层:注意加热保护,盐浴脱氧。 4淬
52、火温度过高,加热时间不足:严格控制淬火工艺。 5碱浴水分过少:严格控制碱浴水分。 6在冷却剂中的停留时间不足:增加停留时间。 7回火温度过高:选择合适的最终热处理和机加工预放变形量的关系:1、如果是普通空气炉热处理,机加设计一定要留余量,热处理工艺还要考虑易变形部位是否相应加大余粮,2、如果产品尺寸精度要求严格,尤其是薄壁件,最终热处理后机加往往易变形,为减少精加工后产品变形,可以考虑增加时效工序,这样可以有效去除机加应力,也不影响力学性能。3。充分了解前后工序的目的和意图,这样才能合理有效的提出工件预留量,也就是说机加的可以不了解热处理,但热处理必须了解机加。为改善铸铁件整体性能常有消除白口
53、退火,提高韧性的球墨铸铁退火,提高球墨铸铁强度的正火、淬火等。 1.球墨铸铁的淬火并回火处理 球墨铸造件作为轴承需要更高的硬度,常将铸铁件淬火并低温回火处理。工艺是:铸件加热到860-900的温度,保温让原基体全部奥氏体化后再在油或熔盐中冷却实现淬火,后经250-350加热保温回火,原基体转换为回火马氏体及残留奥氏体组织,原球状石墨形态不变。处理后的铸件具有高的硬度及一定韧性,保留了石墨的润滑性能,耐磨性能更为改善。 球墨铸铁件作为轴类件,如柴油机的曲轴、连杆,要求强度高同时韧性较好的综合机械械性能,对铸铁件进行调质处理。工艺是:铸铁件加热到860-900的温度保温让基体奥氏体化,再在油或熔盐
54、中冷却实现淬火,后经500-600的高温回火,获得回火索氏体组织(一般尚有少量粹块状的铁素体),原球状石墨形态不变。处理后强度,韧性匹配良好,适应于轴类件的工作条件。 2.提高韧性的球墨铸铁退火 球墨铸铁在铸造过程中此普通灰口铸铁的白口倾向大,内应力也较大,铸铁件很难得到纯粹的铁素体或珠光体基体,为提高铸铁件的延性或韧性,常将铸铁件重新加热到900-950并保温足够时间进行高温退火,再炉冷到600出炉变冷。过程中基体中的渗碳体分解出石墨,自奥氏体中析出石墨,这些石墨集聚于原球状石墨周围,基体全转换为铁素体。 若铸态组织由(铁素体珠光体)基体,以及球状石墨组成,为提高韧性,只需将珠光体中渗碳体分
55、解转换为铁素体及球状石墨,为此将铸铁件重新加热到700-760的共析温度上下经保温后炉冷至600出炉变冷。 3.提高球墨铸铁强度的正火 球墨铸铁正火的目的是将基体组织转换为细的珠光体组织。工艺过程是将基体为铁素体及珠光体的球墨铸铁件重新加热到850-900温度,原铁素体及珠光体转换为奥氏体,并有部分球状石墨溶解于奥氏体,经保温后空冷奥氏体转变为细珠光体,因此球墨铸件的强度提高。铁的热处理和钢的热处埋有相同之处 ,也有不同之处。铸铁的热处理一般不能改善原始组织中石墨的形态和分布状况。对灰口铸铁来说,由于片状石墨所引起的应力集中效应是对铸铁性能起主导作用的困素,因此对灰口铸铁施以热处理的强化效果远
56、不如钢和球铁那样显著。故友口铸铁热处理工艺主要为退火、正火等。对于球铁来说,由于石墨呈球状,对基体的割裂作用大大减轻,通过热处理可使基作组织充分发挥作用,从而可以显著改善球性的机械性能。 故球铁像钢一样,其热处理工艺有退火、正火、调质、多温淬火、感应加热淬火和表面化学热处理等。 1.消除应力退火 由于铸件壁厚不均匀,在加热,冷却及相变过程中,会产生效应力和组织应力。另外大型零件在机加工之后其内部也易残存应力,所有这些内应力都必须消除。去应力退火通常的加热温度为500550保温时间为28h,然后炉冷(灰口铁)或空冷(球铁)。采用这种工艺可消除 铸件内应力的9095,但铸铁组织不发生变化。若温度超
57、过550或保温时间过长,反而会引起石墨化,使铸件强度和硬度降低。 2.消除铸件白口的高温石墨化退火 铸件冷却时,表层及薄截面处,往往产生白口。白口组织硬而脆、加工性能差、易剥落。因此必须采用退火(或正火)的方法消除白口组织。退火工艺为:加热到550950保温25 h,随后炉冷到500550再出炉空冷。在高温保温期间 ,游高渗碳体和共晶渗碳体分解为石墨和A,在随后护冷过程中二次渗碳体和共析渗碳体也分解,发生石墨化过程。由于渗碳体的分解,导致硬度下降,从而提高了切削加工性。 3.球铁的正火 球铁正火的目的是为了获得珠光体基体组织,并细化晶粒,均匀组织,以提高铸件的机械性能。有时正火也是球铁表面淬火
58、在组织上的准备、正 火分高温正火和低温正火。高温正火温度一般不超过950980,低温正火一般加热到共折温度区间820860。正火之后一般还需进行四人处理,以消除正火时产生的内应力。 4.球铁的淬火及回火 为了提高球铁的机械性能,一般铸件加热到Afc1以上3050(Afc1代表加热时A形成终了温度) ,保温后淬入油中,得到马氏体组织。为了适当降低淬火后的残余应力,一般淬火后应进行回火,低温回火组织为回火马氏作加残留贝氏体再加球状石墨。这种组织耐磨性好 ,用于要求高耐磨性,高强度的零件。中温回火温度为350500回火后组织为回火屈氏体加球状石墨,适用于要求耐磨性好、具有一定效稳定性和弹性的厚件。高温 回火温度为50060D,回火后组织为回火索氏作加球状石墨,具有韧性和强度结合良好的综合性能,因此在生产中广泛应用。 5.球铁的多温淬火 球铁经等温淬火后可以获得高强度,同时兼有较好的塑性和韧性。多温淬火加热温度的选择主要考虑使原始组织全部A化、不残留F,同时也避免A晶粒长大。加热温度一般采用Afc1以上3050,等温处理温度为0350以保证获得具有综合机械性能的下贝氏体组织。稀土镁铝球铁等 温淬火后b=12001400MPa,k=33.6Jcm2,HRC4751。但应注意等温淬火后再加一道回火工序。
- 温馨提示:
1: 本站所有资源如无特殊说明,都需要本地电脑安装OFFICE2007和PDF阅读器。图纸软件为CAD,CAXA,PROE,UG,SolidWorks等.压缩文件请下载最新的WinRAR软件解压。
2: 本站的文档不包含任何第三方提供的附件图纸等,如果需要附件,请联系上传者。文件的所有权益归上传用户所有。
3.本站RAR压缩包中若带图纸,网页内容里面会有图纸预览,若没有图纸预览就没有图纸。
4. 未经权益所有人同意不得将文件中的内容挪作商业或盈利用途。
5. 装配图网仅提供信息存储空间,仅对用户上传内容的表现方式做保护处理,对用户上传分享的文档内容本身不做任何修改或编辑,并不能对任何下载内容负责。
6. 下载文件中如有侵权或不适当内容,请与我们联系,我们立即纠正。
7. 本站不保证下载资源的准确性、安全性和完整性, 同时也不承担用户因使用这些下载资源对自己和他人造成任何形式的伤害或损失。