1.2微合金元素在控制轧制中的作用ppt课件
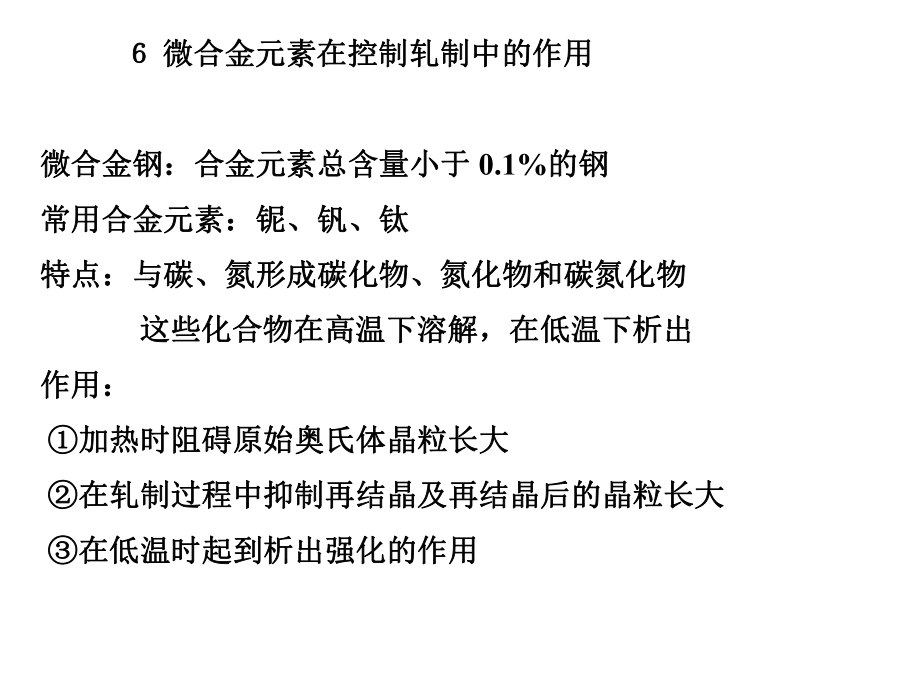


《1.2微合金元素在控制轧制中的作用ppt课件》由会员分享,可在线阅读,更多相关《1.2微合金元素在控制轧制中的作用ppt课件(34页珍藏版)》请在装配图网上搜索。
1、 微合金元素在控制轧制中的作用微合金元素在控制轧制中的作用微合金钢:合金元素总含量小于微合金钢:合金元素总含量小于 0.1%的钢的钢常用合金元素:铌、钒、钛常用合金元素:铌、钒、钛特点:与碳、氮形成碳化物、氮化物和碳氮化物特点:与碳、氮形成碳化物、氮化物和碳氮化物 这些化合物在高温下溶解,在低温下析出这些化合物在高温下溶解,在低温下析出作用:作用:加热时阻碍原始奥氏体晶粒长大加热时阻碍原始奥氏体晶粒长大 在轧制过程中抑制再结晶及再结晶后的晶粒长大在轧制过程中抑制再结晶及再结晶后的晶粒长大 在低温时起到析出强化的作用在低温时起到析出强化的作用 钢的成分钢的成分 常规轧制常规轧制 控制轧制控制轧制
2、%s N/mm2 FATT s N/mm2 FATT0.14C+1.3Mn 313.9 +10 372.7 -100.14C+0.034Nb 392.4 +50 441.3 -500.14C+0.08V 421.8 +40 451.1 -250.14C+0.004Nb 490.3 -70 +0.06V 微量合金元素需要控轧工艺微量合金元素需要控轧工艺 控轧工艺也需要微量合金元素控轧工艺也需要微量合金元素6.1 微合金元素在热轧中的溶解和析出微合金元素在热轧中的溶解和析出6.1.1 轧前加热过程中的溶解轧前加热过程中的溶解1铌在奥氏体中的溶解铌在奥氏体中的溶解 C%、T加加 铌的溶解度增加铌的溶
3、解度增加 6 锰促进铌向奥氏体中固溶锰促进铌向奥氏体中固溶2钒在奥氏体中的溶解钒在奥氏体中的溶解 T加加、Mn%钒的溶解度增加钒的溶解度增加 每增加每增加 1%锰可使钒增加锰可使钒增加 30%溶解量溶解量 研究表明,钒的碳化物在研究表明,钒的碳化物在 900时就全部固溶于奥氏体中时就全部固溶于奥氏体中 了,其溶解度要比了,其溶解度要比 Nb(CN)大得多。大得多。3钛在奥氏体中的溶解钛在奥氏体中的溶解 与铌类似与铌类似66.1.2 控制轧制过程中微量元素碳氮化合物的析出控制轧制过程中微量元素碳氮化合物的析出以以 Nb(CN)为例研究析出状态为例研究析出状态1各阶段中各阶段中Nb(CN)的析出状
4、态的析出状态出炉前的出炉前的Nb(CN)质点状态质点状态 含铌钢加热到含铌钢加热到 1200均热均热 2 小时,小时,90%以上的铌固以上的铌固溶到奥氏体中,没固溶的溶到奥氏体中,没固溶的Nb(CN)质点粗大,大约在质点粗大,大约在 1000 左右,对轧后奥氏体晶粒的再结晶不起作用。左右,对轧后奥氏体晶粒的再结晶不起作用。将钢加热到将钢加热到 1260,保温,保温 30 min,Nb(CN)全部溶解全部溶解出炉后冷却到轧制前出炉后冷却到轧制前Nb(CN)的析出状态的析出状态 未变形的奥氏体中未变形的奥氏体中Nb(CN)析出很慢,析出极少,与析出很慢,析出极少,与出炉前相差无几。即使析出,出炉前
5、相差无几。即使析出,Nb(CN)质点也很大,质点也很大,可达可达1000300 ,其大小与析出温度有关。,其大小与析出温度有关。变形奥氏体中变形奥氏体中Nb(CN)的析出状态的析出状态变形中析出变形中析出动态析出过程动态析出过程 变形速度很低时才能变形速度很低时才能 发生发生变形后析出变形后析出静态析出过程静态析出过程变形使钢中铌的析出大大加快变形使钢中铌的析出大大加快变形量越大、变形后停留时间越长变形量越大、变形后停留时间越长析出量越多析出量越多 Nb(CN)析出需要孕育期,变形量越大、固溶体过饱和程度析出需要孕育期,变形量越大、固溶体过饱和程度越高,轧后到弥散相开始析出的停留时间越短,并且
6、析出速度越高,轧后到弥散相开始析出的停留时间越短,并且析出速度越高。越高。高温轧制时,由于发生动态再结晶,变形产生的位错和畸变高温轧制时,由于发生动态再结晶,变形产生的位错和畸变能消失,碳氮化物没有显著析出,析出速度不大。能消失,碳氮化物没有显著析出,析出速度不大。低温轧制时,奥氏体不发生再结晶,晶内缺陷增多,形变诱低温轧制时,奥氏体不发生再结晶,晶内缺陷增多,形变诱导析出,大大促进了碳氮化物的析出,析出速度增加。导析出,大大促进了碳氮化物的析出,析出速度增加。Nb(CN)质点的析出部位及大小与变形温度有关:质点的析出部位及大小与变形温度有关:高温轧制后再结晶区轧制),高温轧制后再结晶区轧制)
7、,Nb(CN)质点沿奥氏体质点沿奥氏体晶界析出,而在晶内析出量很少,颗粒直径在晶界析出,而在晶内析出量很少,颗粒直径在200 左右。左右。低温轧制后未再结晶区轧制),低温轧制后未再结晶区轧制),Nb(CN)质点在晶界质点在晶界上也在晶内和亚晶界上析出,颗粒细小,直径上也在晶内和亚晶界上析出,颗粒细小,直径50100 控制轧制就是应用这种微细的控制轧制就是应用这种微细的Nb(CN)质点固定亚晶界,质点固定亚晶界,阻止奥氏体晶粒再结晶,达到细化晶粒的目的。阻止奥氏体晶粒再结晶,达到细化晶粒的目的。在奥氏体向铁素体转变过程中和在铁素体内在奥氏体向铁素体转变过程中和在铁素体内Nb(CN)的析出状态的析
8、出状态当当AF相变发生后,微量元素达到高度过饱和,产生相变发生后,微量元素达到高度过饱和,产生快速析出。快速析出。析出地点:析出地点:AF转变的相界面转变的相界面 呈细小点状成排排呈细小点状成排排 列称为相间沉淀列称为相间沉淀 6冷却速度大,析出温度低,相间沉淀排间距小,析出质冷却速度大,析出温度低,相间沉淀排间距小,析出质点小。析出时间长,质点长大。点小。析出时间长,质点长大。16如铌钢如铌钢 830析出,经析出,经 5 min后,质点为后,质点为300 800析出,经析出,经 1 小时后,质点为小时后,质点为50 100 720析出,质点只有析出,质点只有40 80相变后剩余在铁素体中的固
9、溶铌将在铁素体中继续析出。相变后剩余在铁素体中的固溶铌将在铁素体中继续析出。研究表明,碳氮化物在钢中的沉淀方式有:研究表明,碳氮化物在钢中的沉淀方式有:有规则分布有规则分布 列状相间沉淀列状相间沉淀无规则分布无规则分布 位错线上沉淀和基体沉淀位错线上沉淀和基体沉淀两者共存在于各个铁素体晶粒中,后者是主要的和多见的,列两者共存在于各个铁素体晶粒中,后者是主要的和多见的,列状组织相当稀少。状组织相当稀少。Nb(CN)析出特点析出特点析出时机析出时机 析出物特点析出物特点 质点大小质点大小加热后加热后 是固溶于奥氏体后的剩余化合物是固溶于奥氏体后的剩余化合物 1000轧制前轧制前 析出数量极少,析出
10、部位在晶界析出数量极少,析出部位在晶界 3001000在奥氏体在奥氏体 有孕育期形变诱导析出,动态析有孕育期形变诱导析出,动态析区变形时区变形时 出,析出数量少,析出部位在位出,析出数量少,析出部位在位 5070 错密度高处错密度高处在变形后的在变形后的 变形诱导析出的继续,析出量大,变形诱导析出的继续,析出量大,200(再结晶再结晶)停留时间里停留时间里 主要析出在晶界、亚晶界、变形主要析出在晶界、亚晶界、变形 50100(未再未再 (直到相变前直到相变前)带、位错处带、位错处 结晶区变形结晶区变形)AF相变中相变中 在在A/F相界上或相界上或F相内成无规则沉淀相内成无规则沉淀 50100F
11、相区相区 位错上,位错上,F相内相内 502影响影响 Nb(CN)析出的因素析出的因素变形量和析出时间的影响变形量和析出时间的影响 变形量增加、析出时间加长变形量增加、析出时间加长 析出量增加析出量增加 6 在大变形量条件时,开始随时间增长而增加,但很快达到饱和在大变形量条件时,开始随时间增长而增加,但很快达到饱和变形温度的影响变形温度的影响 析出量相等,未再结晶区轧制所需时间比再结晶区轧制短析出量相等,未再结晶区轧制所需时间比再结晶区轧制短 在同一条件下,析出量一定时,在高温等温时间短,而低温所在同一条件下,析出量一定时,在高温等温时间短,而低温所 需等温时间长。需等温时间长。化学成分的影响
12、化学成分的影响 钢的成分不同,析出量不同钢的成分不同,析出量不同 16.2 微合金元素在控制轧制和控制冷却中的作用微合金元素在控制轧制和控制冷却中的作用微合金元素的作用主要是细化铁素体晶粒及析出微合金元素的作用主要是细化铁素体晶粒及析出强化强化6.2.1 加热时阻止奥氏体晶粒长大加热时阻止奥氏体晶粒长大 加入铌、钒、钛等元素可以阻止奥氏体晶粒加入铌、钒、钛等元素可以阻止奥氏体晶粒长大,长大,提高钢的粗化温度。提高钢的粗化温度。微量合金元素形成高度弥散的碳氮化合物小微量合金元素形成高度弥散的碳氮化合物小颗粒,颗粒,对奥氏体晶界起固定作用,阻止奥氏体晶界迁移,对奥氏体晶界起固定作用,阻止奥氏体晶界
13、迁移,阻止阻止奥氏体晶粒长大。奥氏体晶粒长大。6.2.2 抑制奥氏体再结晶抑制奥氏体再结晶1对动态再结晶临界变形量对动态再结晶临界变形量(P)的影响的影响 在普碳钢中加入铌、钒后,使在普碳钢中加入铌、钒后,使P,显著阻滞形变,显著阻滞形变奥氏体的动态再结晶奥氏体的动态再结晶 1动态再结晶的开始时间动态再结晶的开始时间 Q235钢钢 60秒秒 0.18 Nb钢钢 110秒秒 0.35 Nb-V钢钢 160秒秒 0.482对再结晶数量的影响对再结晶数量的影响随铌析出量增加,奥氏体再结晶数量降低。随铌析出量增加,奥氏体再结晶数量降低。1 13对再结晶速度的影响对再结晶速度的影响 加入铌后,再结晶速度
14、加入铌后,再结晶速度,再结晶开始时间,再结晶开始时间和完成时间都比不含铌钢推迟。和完成时间都比不含铌钢推迟。1 温度在温度在1000以上时,铌量增加对再结晶速度的以上时,铌量增加对再结晶速度的影响不显著。影响不显著。4对静态再结晶临界变形量的影响对静态再结晶临界变形量的影响 加入铌,临界变形量增加加入铌,临界变形量增加 6 6含铌量不同对再结晶临界变形量的影响也不同含铌量不同对再结晶临界变形量的影响也不同5对再结晶晶粒大小的影响对再结晶晶粒大小的影响 在同样条件下轧制温度和变形量相同),含铌钢的再结晶在同样条件下轧制温度和变形量相同),含铌钢的再结晶晶粒小于不含铌钢的再结晶晶粒。晶粒小于不含铌
15、钢的再结晶晶粒。铌在奥氏体中以三种形式存在:铌在奥氏体中以三种形式存在:加热时尚未溶到奥氏体中的加热时尚未溶到奥氏体中的Nb(CN)固溶到奥氏体中的铌固溶到奥氏体中的铌加热时溶解、轧制过程中重新析出的加热时溶解、轧制过程中重新析出的Nb(CN)一般认为,第种一般认为,第种Nb(CN)颗粒较大,不能抑制再结晶颗粒较大,不能抑制再结晶 的发生的发生T1000 再结晶先于铌的析出,再结晶达再结晶先于铌的析出,再结晶达50%后后 铌才开始析出。铌阻止再结晶的原因是铌才开始析出。铌阻止再结晶的原因是 由于固溶于奥氏体中的铌与位错的相互由于固溶于奥氏体中的铌与位错的相互 作用阻止晶界的迁移。作用阻止晶界的
16、迁移。T900 Nb(CN)在再结晶之前析出,在再结在再结晶之前析出,在再结 晶过程中继续析出。晶过程中继续析出。铌阻止再结晶的作用机理有不同的看法。铌阻止再结晶的作用机理有不同的看法。其一,有人认为是固溶于奥氏体中的铌的作用其一,有人认为是固溶于奥氏体中的铌的作用其二,有人认为是析出细小的其二,有人认为是析出细小的Nb(CN)质点阻止再结质点阻止再结 晶的进行晶的进行 也有人认为两者都起作用也有人认为两者都起作用6.2.3 细化铁素体晶粒细化铁素体晶粒 微量合金元素的加入,阻止奥氏体晶粒长大,又能阻止奥氏微量合金元素的加入,阻止奥氏体晶粒长大,又能阻止奥氏体再结晶的发生,因而细化了铁素体晶粒
17、。体再结晶的发生,因而细化了铁素体晶粒。实验表明,铌的细化铁素体晶粒效果最为明显,钛次之,钒最差。实验表明,铌的细化铁素体晶粒效果最为明显,钛次之,钒最差。加入量达一定值后,铁素体加入量达一定值后,铁素体晶粒基本不变。晶粒基本不变。铌量的饱和值为铌量的饱和值为0.04%,钛量为钛量为0.08%,钒量为钒量为0.10%。6.2.4 影响钢的强韧性能影响钢的强韧性能晶粒细小晶粒细小强韧性好强韧性好沉淀强化沉淀强化强度提高强度提高 韧性降低韧性降低铌:在控制轧制中,铌产生显著的晶粒细化和中等的铌:在控制轧制中,铌产生显著的晶粒细化和中等的 沉淀强化沉淀强化钛:沉淀强化作用大,晶粒细化中等。钛钢抗脆性
18、能钛:沉淀强化作用大,晶粒细化中等。钛钢抗脆性能 力较低。力较低。对于厚规格的常化板,钛和镍结合最有利。对于厚规格的常化板,钛和镍结合最有利。钒:产生中等程度的沉淀强化和比较弱的晶粒细化。钒:产生中等程度的沉淀强化和比较弱的晶粒细化。61.Nb、V、Ti 等元素在控轧中的作用如何?等元素在控轧中的作用如何?2。铌、钒、钛在钢中的溶解度和哪些参数有关?。铌、钒、钛在钢中的溶解度和哪些参数有关?3。微合金元素从加热、轧制到相变后的各个阶段中其。微合金元素从加热、轧制到相变后的各个阶段中其 析出物的特点、质点大小如何?析出物的特点、质点大小如何?4。用图示意说明钢中铌、钒、钛含量对材料强韧性的。用图示意说明钢中铌、钒、钛含量对材料强韧性的 影响?影响?5。为什么说微合金化钢只有采用控制轧制工艺才能获。为什么说微合金化钢只有采用控制轧制工艺才能获 得良好的力学性能?又为什么说采用控制轧制工艺得良好的力学性能?又为什么说采用控制轧制工艺 的钢在多数情况下需要加入微量合金元素?的钢在多数情况下需要加入微量合金元素?
- 温馨提示:
1: 本站所有资源如无特殊说明,都需要本地电脑安装OFFICE2007和PDF阅读器。图纸软件为CAD,CAXA,PROE,UG,SolidWorks等.压缩文件请下载最新的WinRAR软件解压。
2: 本站的文档不包含任何第三方提供的附件图纸等,如果需要附件,请联系上传者。文件的所有权益归上传用户所有。
3.本站RAR压缩包中若带图纸,网页内容里面会有图纸预览,若没有图纸预览就没有图纸。
4. 未经权益所有人同意不得将文件中的内容挪作商业或盈利用途。
5. 装配图网仅提供信息存储空间,仅对用户上传内容的表现方式做保护处理,对用户上传分享的文档内容本身不做任何修改或编辑,并不能对任何下载内容负责。
6. 下载文件中如有侵权或不适当内容,请与我们联系,我们立即纠正。
7. 本站不保证下载资源的准确性、安全性和完整性, 同时也不承担用户因使用这些下载资源对自己和他人造成任何形式的伤害或损失。