液相加氢技术进展
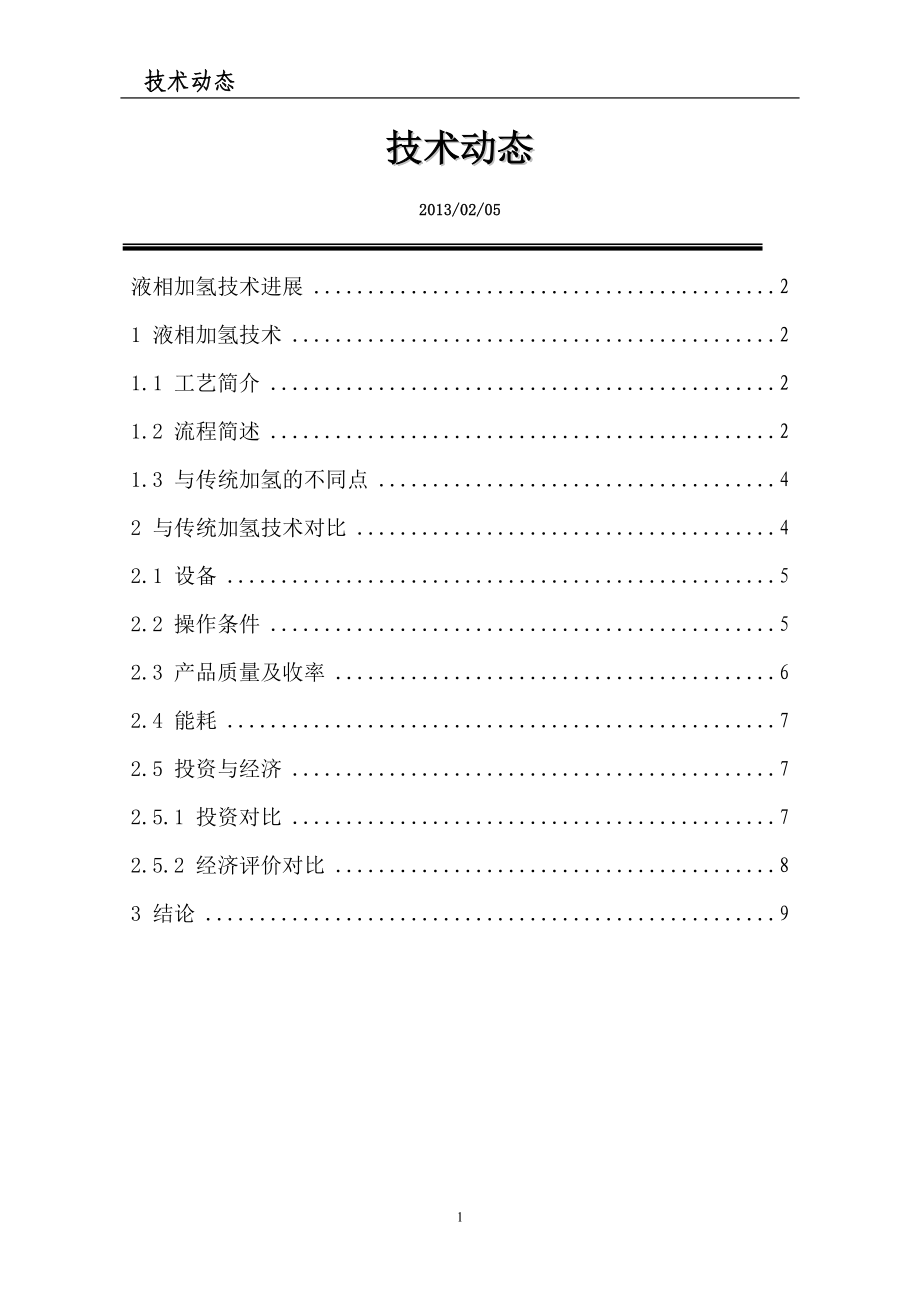


《液相加氢技术进展》由会员分享,可在线阅读,更多相关《液相加氢技术进展(9页珍藏版)》请在装配图网上搜索。
1、 技术动态 技术动态2013/02/05液相加氢技术进展21 液相加氢技术21.1 工艺简介21.2 流程简述21.3 与传统加氢的不同点42 与传统加氢技术对比42.1 设备52.2 操作条件52.3 产品质量及收率62.4 能耗72.5 投资与经济72.5.1 投资对比72.5.2 经济评价对比83 结论9液相加氢技术进展 在现代炼油行业,加氢处理装置往往由于操作条件较为苛刻,所以装置投资很大。为此,为生产满足环保要求的清洁的石油产品,世界各国炼油技术人员开发了很多加氢技术,以降低装置的投资和能耗。其中液相加氢技术是近几年发展起来的一种成熟的突破性加氢技术。1 液相加氢技术1.1 工艺简介
2、 在加氢技术中,反应是以液相进行的。传统加氢技术大量的富氢气循环气与进料一起进入反应器,以确保反应所要求的氢气被转换成液相。液相加氢工艺技术反应部分不设置氢气循环系统,依靠液相产品循环以溶解足量的氢气,满足加氢反应的需要。由于取消了氢气循环系统,节省了循环压缩机系统、高分系统及其相应设备,可以大大节约投资和能耗。同时由于液相加氢工艺技术可以消除催化剂的润湿因子影响,而且循环油的比热容大,从而提高催化剂的利用效率,大大降低反应器的温升,降低裂化等副反应。1.2 流程简述原料油自装置外来,通过原料油过滤器进行过滤,然后与精制柴油换热,进入滤后原料油缓冲罐,再经反应进料泵升压后,在流量控制下,与少量
3、补充氢混合作为混合进料(图1)。混合进料经过与一部分反应产物换热后,进入反应进料加热炉加热至所需温度,加热后的进料再与一定量的反应循环产物及一定量的补充新氢混合后进入加氢精制反应器第一催化剂床层,在催化剂作用下进行脱硫、脱氮、烯烃饱和、芳烃饱和等反应,加入到第一催化剂床层进料中的氢气量由进料液体的饱和限度决定,加入足够的氢气,直到第一催化剂床层有少量的尾气排出,这样可以确保氢气被完全饱和。该反应器设置4个催化剂床层,床层间均需注入新氢,使原料油含氢量再饱和。来自加氢精制反应器的反应产物,一部分经反应产物循环泵升压后在流量控制下与加热后的新鲜进料混合,通过饱和液体循环物料为反应提供所需的氢气,该
4、部分循环反应产物同时还用于吸收反应器放出的热量。另一部分经反应产物-原料油换热器换热后,经流量控制阀控制进入热低压分离器进行气液分离,液相送至汽提塔;气相经热低分气-低分油换热器与低分油换热,再经热低分气空冷器冷却后,进入冷低压分离器,在冷低压分离器中进行气、油、水三相分离。冷低压分离器含硫污水与尾气分离器中分离出的含硫污水混合后出装置;低分气与尾气分离器顶气体一同送出装置;油相经热低分气-低分油换热器与低分油换热后进入汽提塔。为了防止反应流出物中的铵盐在低温部位析出,通过反应产物注水泵将除氧水注至热低分空冷器上游侧以溶解反应产生的铵盐。反应器所有催化剂床层的排气在尾气冷却器中冷却,然后进入尾
5、气分离器中进行气、油、水三相分离,其中,分离出的尾气与冷低压分离器顶低分气混合后出装置,含硫污水与冷低压分离器分离出的含硫污水混合后出装置,冷凝烃被送回至精制柴油-原料油换热器前的进料中。为了防止反应尾气中的的铵盐在低温部位析出,通过反应产物注水泵将除氧水注至尾气空冷器上游侧以溶解反应产生的铵盐。装置外来的重整氢经新氢压缩机经二级升压分别注入至每层催化剂床层及与升压后的混合原料处。1.3 与传统加氢的不同点 从上面的论述可知,液相加氢技术较传统的加氢技术在流程上可省去整个循环氢系统及循环氢脱硫系统,取而代之的是反应器底部的循环泵,同时由于此技术正常生产时石脑油产品量很低,因此后续分馏部分只设置
6、一座汽提塔,省掉了传统加氢技术中的分馏塔、分馏塔底重沸炉、塔顶空冷器、水冷器、回流罐等设备。2 与传统加氢技术对比 以某炼厂200万ta柴油加氢精制装置为例,对传统加氢精制技术和液相加氢精制技术在设备选择、主要操作条件、产品质量及收率、能耗和投资等5个方面进行对比。2.1 设备对传统加氢精制技术和液相加氢精制技术在设备选择的主要区别见主要设备对比表1。表1 主要设备对比表序号设 备传统加氢技术液相加氢技术1热高分有无2冷高分有无3循环氢脱硫塔有无4循环氢压缩机入口分液罐有无5分馏塔有无6分馏塔底重沸炉有无7尾气分离器无有8尾气空冷器无有9高压空冷器有无10循环氢压缩机有无11反应器循环泵无有1
7、2贫胺液泵有无13分馏塔底重沸炉泵有无14反应器重量/t450400通过以上对比可知,液相加氢技术较传统加氢技术节省了高压容器、循环氢系统、循环氢脱硫系统、高压空冷和分馏系统等设备;同时增加了反应器循环泵和部分低压空冷。另外,由于液相加氢反应器结构与传统加氢有较大区别,反应器床层较多,各床层间有气液分离空间,因此液相加氢反应器重量要比传统的大。2.2 操作条件 对传统加氢精制技术和液相加氢精制技术在主要操作条件上的区别见对比表2。表 2 主要操作条件对比表序号主要操作条件传统加氢技术液相加氢技术1反应器入口总压/MPa(g)8.08.02反应器入口温度/312/341320/3803平均反应温
8、度/341/370363/3954空速/h-11.61.65氢油比(体积)350/6循环比(体积)/1.75/1.07化学耗氢(N)/(m3.m-3进料)66.3/68.270.5/64.88反应器数量119床层数量2410操作周期/a33由表2可见,液相加氢技术较传统加氢技术反应压力相同,平均反应温度稍高,化学耗氢基本相同,两种加氢技术的主催化剂体积空速相同,催化剂用量没有区别。2.3 产品质量及收率对传统加氢精制技术和液相加氢精制技术在产品质量及收率上的区别见对比表3。表 3 产品质量及收率对比表序号项 目传统加氢技术液相加氢技术加氢精制产品石脑油精制柴油石脑油精制柴油1产量/(kg.h-
9、1)235725797621232595542收率,%0.9098.500.8199.103密度(kg.m-1)720745840828.04流程/-1351801583785(硫)/(g.g-1)2050406(氮)/(g.g-1)-67十六烷值45-8十六烷指数-489闪点/555510(多环芳烃),%11- 由表3可见,液相加氢技术较传统加氢技术在产品质量方面均满足要求,在精制柴油产品收率上液相加氢技术高于传统加氢技术。2.4 能耗 对传统加氢精制技术和液相加氢精制技术在能耗上的区别见对比表4。表 4 能耗对比表序号公用工程消耗传统加氢技术液相加氢技术备注(1)104KJ.t-11耗电/
10、(kW.h.h-1)450039082.512燃料气/(kg.h-1)200034428.053蒸汽(3.5MPa)/(t.h-1)25035.174蒸汽(1.0MPa)/(t.h-1)-284.4-39.36节能/(104kJ.t-1)26.37 注:(1)液相加氢技术较传统加氢技术能耗节省。从以上两表可见,在影响装置能耗的主要4项消耗上液相加氢技术较传统加氢技术节省26.37104kJt原料。因此液相加氢技术在能耗方面具有较大优势,主要体现在电和燃料的用量上。这是因为液相加氢技术流程较为简单,取消了传统加氢技术当中的循环氢回路,进而可省去循环氢压缩机等用电设备的消耗,同时后续的分馏系统中只
11、设置汽提塔,减少了重沸炉设备,大大地减少了燃料气的用量。因此液相加氢技术在能耗方面较传统加氢技术有非常大的优势。2.5 投资与经济2.5.1 投资对比对传统加氢精制技术和液相加氢精制技术在投资上的区别见对比表5。表5 投资对比表序号投 资传统加氢技术液相加氢技术差值装置工程投资/万元3864535188-3466一静设备-37071反应器/万元260029253252反应器内件3909505603重沸炉14620-14624循环氢脱硫塔3700-3705分馏塔800-806热高分8500-8507冷高分2430-2438循环氢压缩机入口分液罐1630-1639循环氢脱硫塔入口分液罐1630-1
12、6310高压空冷器2200-22011高压换热器22821241-1041二机械设备-6571循环氢压缩机20000-20002反应产物循环泵0165016503贫胺液泵2400-2404分馏塔底重沸炉670-67三安装工程费59706625655四自控工程费36854008323五专利技术许可费350420038502.5.2 经济评价对比对传统加氢精制技术和液相加氢精制技术在经济评价上的区别见对比表6。表 6 经济评价对比表序号经济评价指标传统加氢技术液相加氢技术1生产成本/(元/原料.t-1)223.2184.82内部收益率(税后),%10.0420.21 总体来说,液相加氢精制技术比传
13、统加氢精制技术工程投资低,但液相加氢精制技术专利技术许可费较高,从而抵消了液相加氢精制技术的投资优势。 液相加氢技术在生产成本方面优势比较明显,在投资方面液相加氢技术与传统加氢技术基本相当,但由于液相加氢技术生产成本很低,所以装置投资回收更快。3 结论 经过对传统加氢精制技术和液相加氢精制技术在设备选择、主要操作条件、产品质量及收率、能耗和投资等五个方面进行对比得出以下结论: (1)液相加氢技术较国内传统加氢技术投资基本相当。 (2)液相加氢技术较国内传统加氢技术在能耗方面有较大优势,大大降低了生产成本。 (3)在精制柴油产品收率上液相加氢技术高于传统加氢技术。 (4)液相加氢技术由于取消了循环氢回路,高压设备大大减少,减少了占地面积和设备投资,同时也降低了设备维护成本和装置的运行安全风险。9
- 温馨提示:
1: 本站所有资源如无特殊说明,都需要本地电脑安装OFFICE2007和PDF阅读器。图纸软件为CAD,CAXA,PROE,UG,SolidWorks等.压缩文件请下载最新的WinRAR软件解压。
2: 本站的文档不包含任何第三方提供的附件图纸等,如果需要附件,请联系上传者。文件的所有权益归上传用户所有。
3.本站RAR压缩包中若带图纸,网页内容里面会有图纸预览,若没有图纸预览就没有图纸。
4. 未经权益所有人同意不得将文件中的内容挪作商业或盈利用途。
5. 装配图网仅提供信息存储空间,仅对用户上传内容的表现方式做保护处理,对用户上传分享的文档内容本身不做任何修改或编辑,并不能对任何下载内容负责。
6. 下载文件中如有侵权或不适当内容,请与我们联系,我们立即纠正。
7. 本站不保证下载资源的准确性、安全性和完整性, 同时也不承担用户因使用这些下载资源对自己和他人造成任何形式的伤害或损失。