毕业设计论文空压机机械系统设计(全套图纸
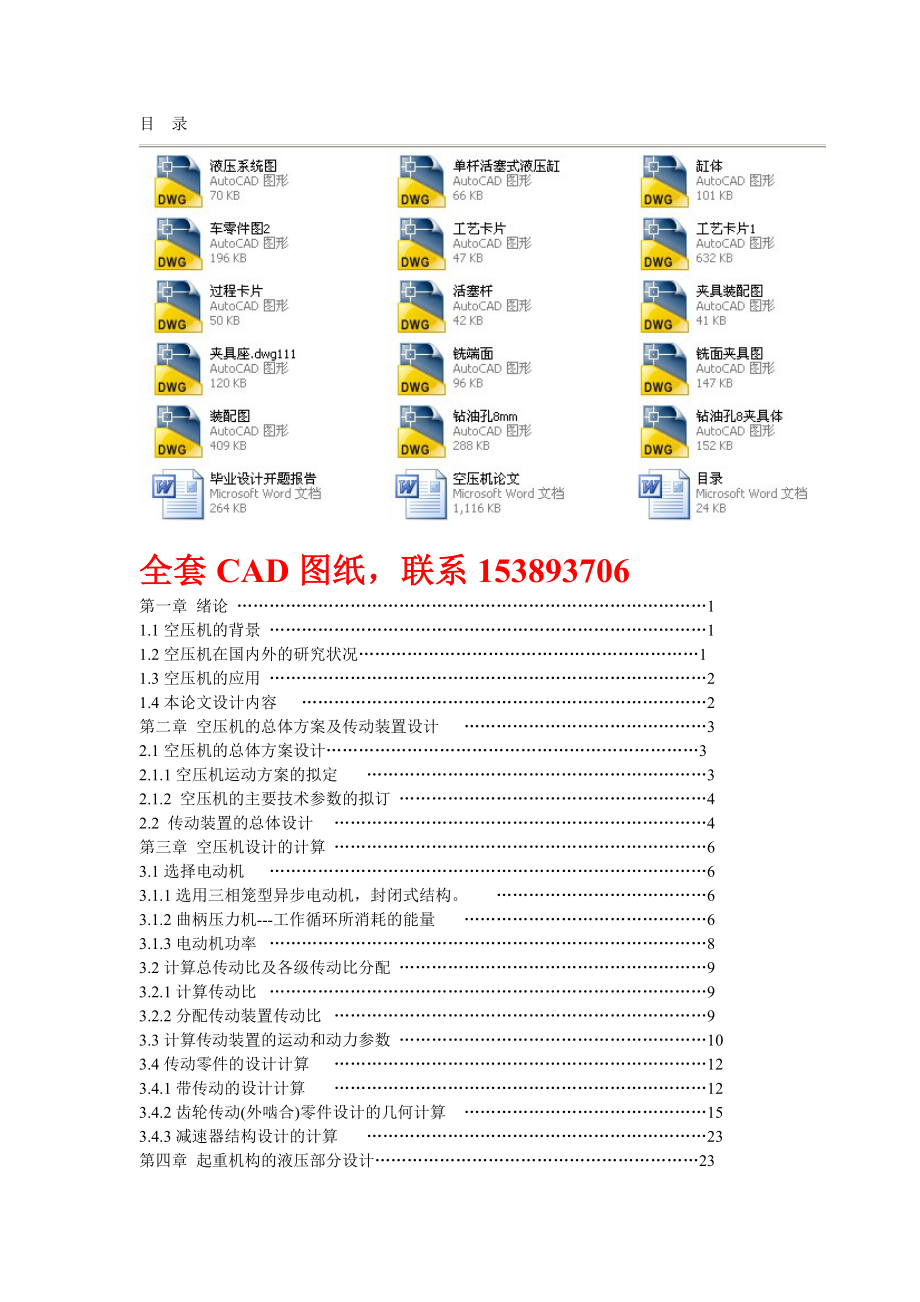


《毕业设计论文空压机机械系统设计(全套图纸》由会员分享,可在线阅读,更多相关《毕业设计论文空压机机械系统设计(全套图纸(36页珍藏版)》请在装配图网上搜索。
1、目 录全套CAD图纸,联系153893706第一章 绪论11.1空压机的背景11.2空压机在国内外的研究状况11.3空压机的应用21.4本论文设计内容2第二章 空压机的总体方案及传动装置设计32.1空压机的总体方案设计32.1.1空压机运动方案的拟定32.1.2 空压机的主要技术参数的拟订42.2 传动装置的总体设计4第三章 空压机设计的计算63.1选择电动机63.1.1选用三相笼型异步电动机,封闭式结构。63.1.2曲柄压力机-工作循环所消耗的能量63.1.3电动机功率83.2计算总传动比及各级传动比分配93.2.1计算传动比93.2.2分配传动装置传动比93.3计算传动装置的运动和动力参数
2、103.4传动零件的设计计算123.4.1带传动的设计计算123.4.2齿轮传动(外啮合)零件设计的几何计算153.4.3减速器结构设计的计算23第四章 起重机构的液压部分设计234.1 伸缩机构液压缸设计 254.1.1 确定液压缸类型和安装方式 254.1.2 确定伸缩液压缸的主要性能参数和主要尺寸 254.2 起升机构液压马达设计计算 26第五章 空压机的确定275.1 空压机的主要技术参数 275.1.1 主要技术参数 275.1.2 各种泵的比较 295.2 空压机的确定 305.3 油箱的选择 30结论32致谢33参考文献34第一章 绪论1.1空压机的背景随着我国制造业的发展,空压
3、机床的发展越来越成为机械制造行业的中流砥柱,通用型高性能压力机,广泛适用于航空、汽车、农机、电机、电器、仪器仪表、医疗器械、家电、五金等行业。锻压机械是指在锻压加工中用于成形和分离的机械设备,1842年,英国工程师史密斯创制第一台蒸汽锤,开始了蒸汽动力锻压机械的时代。1795年,英国的布拉默发明水压机,但直到19世纪中叶,由于大锻件的需要才应用于锻造。随着电动机的发明,十九世纪末出现了以电为动力的机械压力机和空气锤,并获得迅速发展。二十世纪初,锻压机械改变了从19世纪开始的向重型和大型方向发展的趋势,转而向高速、高效、自动、精密、专用、多品种生产等方向发展。于是出现了每分种行程2000次的空压
4、机。所谓空压机一般是指每分钟的行程次数为普通压力机的510倍的压力机。空压机是带有自动送料装置,可完成板料高效率、精密加工的机械压力机,具有自动、高速、精密三个基本要素。自60年代以来,空压机已有较大的发展,其每分钟行程次数已从几百次发展到3千次左右,其吨位已从十吨发展到上百吨。目前空压机主要用在电子、仪器仪表、轻工、汽车等行业中进行特大批量的冲压生产。近年来,随着模具技术和冲压技术的发展,空压机的应用范围在不断地扩大,数量在不断地增加。预计不久的将来,空压机在冲压用压力机中的比例将会愈来愈大。1.2空压机在国内外的研究状况近十多年来,随着对发展先进制造技术的重要性获得前所未有的共识,冲压成形
5、技术无论在深度和广度上都取得了前所未有的进展,其特征是与高新技术结合,在方法和体系上开始发生很大变化。计算机技术、信息技术、现代测控技术等冲压领域的渗透与交叉融合,推动了先进冲压成形技术的形成和发展。冷冲压生产的机械化和自动化,为了满足大量生产的需要,冲压设备已由单工位低速压力机发 展到多工位空压机。一般中小型冷冲件,既可在多工位压力机上生产,也可以在空压机上采用多工位级进模加工,是冷冲压生产达到高度自动化。在汽车、航空航天、电子和家用电器领域,需要大量的金属板壳零件,特别是汽车行业要求生产规模化、车型个性化和覆盖件大型一体化。进入21 世纪,我国汽车制造业飞速发展,面对这一形势,我国的板材加
6、工工艺及相应的冲压设备都有了长足的进步。1.3空压机的应用随着电子工业的发展,小型电子零件的需求日趋高涨,促进了高精度、高效率的空压机的发展。目前日本已成为空压机技术的领军,在100kN压力、8mm冲程下,滑块速度可达4000次/min。我国金丰、江苏扬锻、高将精机、江苏扬力、徐锻和西安通力等公司都有空压机产品。2004年已开发出了速度达1200次/min的SH系列SH25开式高速精密压力机。其他还有VH开式、JF75G闭式系列空压机。这些压力机广泛应用于电子和微电子行业,全面提高了行业技术装备水平,替代了大量的进口机床。1.4本论文设计内容为了提高生产效率,压力机在不断向高速发展。目前,国内
7、自行设计,生产的空压机较少,主要还是以进口设备为主。因此,急需要设计一重空压机,满足生产需要。第二章 空压机的总体方案及传动装置设计2.1空压机的总体方案设计2.1.1空压机运动方案的拟定随着我国制造业的发展。空压机的发展越来越成为机械制造行业的中流砥柱,本文旨在设计冲压效率高,机器的结构简单,成本低,工作可靠,自动化程度高,机械震动小的空压机。该空压机的工作机构采用曲柄滑块机构,由曲柄,连杆,滑块等零件。传动系统为齿轮传动。由于开式压力机操纵简单,本论文所设计的压力机的冲压力为:100。故本文采用开式。压力机运动方案如下图: 2.1.2 空压机的主要技术参数的拟订空压机的主要技术参数是反映一
8、台压力机的工艺能力,所能加工零件的尺寸范围,以及有关生产率等指标。拟订分别如下:1 公称压力 1000 2 滑块行程 303 冲头工作频率 1000次/4 工作台板尺寸 前后 500 左右 8005 滑块底面尺寸 前后 300 左右 4006 立柱间的距离 4502.2 传动装置的总体设计由于本文设计的空压机承载能力和速度大,故采用圆柱齿轮传动和带传动。按照工作要求和条件。 3种传动方案如下图所示:其中 a为带传动和直齿轮传动; b为直齿轮传动; c直齿轮传动和斜齿轮传动.本文选a)传动方案。第三章 空压机设计的计算3.1选择电动机3.1.1选用三相笼型异步电动机,封闭式结构。 电动机功率计算
9、:其中:-平均功率(千瓦) A -工作循环所需的总能量(焦) t - 工作循环时间(秒) k一般为1.2-1.6 ,本文中取1.6式中 n 为压力机滑块行程次数 为压力机行程利用系数,采用自动化送料为1,本文中取0.63.1.2曲柄压力机-工作循环所消耗的能量压力机一工作循环所消耗的能量A为 A= 式中:-工件变形功(属有效能量) -拉延垫工作功,即进行拉延工艺时压边所需的功(属有效能量) -工作行程时由于曲柄滑块机构的摩擦所消耗的能量 -工作行程时由于压力机受力系统的弹性变形所消耗的能量 -压力机空程向下和空程向上时所消耗的能量 -单行程时滑块停顿飞轮空转所消耗的能量 -单次行程时滑块时离合
10、器接合所消耗的能量下面对这些能量分别计算:1)工件变形功=0.315(焦)式中 -为压力机公称压力(牛) -为板料厚度(米)对于快速压力机(毫米)故=63000(焦)、2)拉延垫工作功式中 -为压力机公称压力(牛) -为压力机滑块行程长度(米)故=833.3(焦)3)工作行程时由于曲柄滑块机构的摩擦所消耗的能量式中 -摩擦当量力臂(米) -公称压力(牛) -公称压力角(度)故 =2088(焦)4)工作行程时由于压力机受力系统的弹性变形所消耗的能量为:式中 -压力机公称压力(牛) -压力机总的垂直变形(米) -压力机垂直刚度 故=1250(焦)5)压力机空程向下和空程向上时所消耗的能量根据曲柄压
11、力机空程损耗功及飞轮空转损耗功率表知=100(焦)0.16(千瓦)6)滑块停顿飞轮空转时所消耗的能量(千米)式中 -压力机单次行程时的循环周期(秒) -曲轴回转一周所需时间(秒) -压力机行程次数及行程利用系数。故 =11400(焦)7)单行程时,离合器接合所消耗的能量(焦)综上所述:总功 A= 63000+833.3+2088+1250+100+11400+ 故A=102089焦3.1.3电动机功率选用电动机型号为 同步转速1000r/min ,6极,满载转速970r/min 3.2计算总传动比及各级传动比分配3.2.1计算传动比因为压力机行程 s=30mm求主轴转速冲头工作频率P=1000
12、次/min 滑块行程S=30mm故滑块与连杆线速度V=1m/s主轴转速故总传动比式中 -电动机满载转速(r/min)3.2.2分配传动装置传动比分配传动比应考虑以下原则:1.各级传动的传动比应在合理范围内,不超出允许的最大值,以符合个中传动形式的工作特点,并使结构比较紧凑。2.应注意使各级传动件尺寸协调,结构匀称合理。3.尽量使传动装置外廓尺寸紧凑或重量较小。4.尽量使各级大齿轮浸油深度合理(低速级大齿轮浸油稍深,高速级大齿轮能浸到油。)在卧式减速器设计中,希望各级齿轮直径相近,以避免为了各级齿轮都能浸到油,而使某级大齿轮浸油过深造成搅油损失增加。5.要考虑传动零件之间不会干涉碰撞。由式=式中
13、 -带传动的传动比-减速器的传动比为使V带传动外廓尺寸不致过大,初步取=3,则减速器传动比为:因此带传动的传动比为3,减速器的传动比为4.85。3.3计算传动装置的运动和动力参数1)各轴转速I轴 II轴 2)各轴输入功率I轴 II轴 III轴的输出功率则分别为输入功率乘轴承效率0.98。3)各轴输入转矩电动机输出转矩 III轴输入转矩I轴 II轴 III轴的输出转矩则分别为各轴的输入转矩乘轴承效率0.98。运动和动力参数计算结果整理于下表:轴名功率Pkw转矩T转速nr/min传动比效率输入输出输入输出电动机轴27.2226897030.96I轴26.1325.61771.8756.43234.
14、850.95II轴24.8424.343558348766.673.4传动零件的设计计算3.4.1带传动的设计计算带传动是两个或多个带轮之间用带作为挠性拉曳零件的传动,工作时借助零件之间的摩擦(或啮合)来传递运动或动力。根据带的截面形状不同,可分为平带传动、V带传动、同步带传动、多楔带传动等。带传动是具有中间挠性件的一种传动,其优点有:1)能缓和载荷冲击;2)运行平稳,无噪声;3)制造和安装不像啮合传动那样严格;4)过载时将引起带在带轮上打滑,因而可防止其他零件的损坏;5)可增加带长以适应中心距较大的工作条件(可达15m)。由于本设计中要求转速高,为保证稳定传动皮带不打滑,选用V带传动,计算如
15、下:(1)定V带型号和带轮直径1)工作情况系数由机械设计第4版(P188)表11.5得, 2)计算功率3)选带型号由机械设计第4版(P188)查看图11.15选C型。4)小带轮直径由机械设计第4版(P189)表11.6取=400mm5)大带轮直径 (设=0.01)6)大带轮转速 (2)计算带长初取中心距=650mm带长由机械设计第4版(P179)图11.4得基准长度(3)求中心距和包角1)中心距 2)小轮包角(4)求带根数带速由机械设计第4版(P191-192)表11.8查得;由机械设计第4版(P191-192)表11.8查得;由机械设计第4版(P194-195)表11.12查得;由机械设计第
16、4版(P193)表11.10查得故带根数取根(5)求轴上载荷张紧力 (由机械设计第4版(P179-180)表11.4查得带质量)轴上载荷 3.4.2齿轮传动(外啮合)零件设计的几何计算和其他机械传动比较,齿轮传动的主要优点是:工作可靠,使用寿命长;瞬时传动比为常数;传动效率高;结构紧凑;功率和速度适用范围很广等。缺点是:齿轮制造需要专用机床和设备,成本较高;精度低时,振动和噪声较大;不宜用于轴间距离大的传动等。齿轮传动应满足下列两项基本要求:1)传动平稳要求瞬时传动比不变,尽量减小冲击、振动和噪声;2)承载能力高要求在尺寸小、重量轻的前提下,齿轮的强度高、耐磨性好,在预定的使用期限内不出现断齿
17、等失效现象。在齿轮设计和生产中,有关齿廓曲线、齿轮强度、制造精度、加工方法以及热处理工艺等,基本上都是围绕这两个基本要求进行的。预期使用寿命10年,每年300个工作日。在使用期限内,工作时间占20%。载荷无变化,动力机为电动机,工作有中等振动,传动不逆转,齿轮对称布置。传动尺寸无严格限制,小批量生产,齿面允许少量点蚀,无严重过载。因传动尺寸无严格限制,批量较小,故小齿轮用,调质处理,硬度241HB286HB,平均取为260HB,大齿轮用45钢,调质处理,硬度229HB286HB,平均取240HB。齿轮传动计算如下:一齿面接触疲劳强度计算1初步计算1)转矩 式中 P-电动机功率 -小齿轮转速2)
18、齿宽系数 由机械设计第4版(P218)表12.13,取=1.03)接触疲劳极限 由机械设计第4版(P223)图12.17c得, 4)初步计算的许用接触应力 5)值由机械设计第4版(P227)表12.16,取=856)初步计算的小齿轮直径 取=130mm式中 u-减速器传动比-小齿轮转矩7)初步齿宽b b=2校核计算1)圆周速度 2)精度等级由机械设计第4版(P207)表12。6,选8级精度。3)齿数z和模数m初取齿数;由机械设计第4版(P206)表12.3,取m=3,则 4)使用系数由机械设计第4版(P215)表12.9,=1.55)动载系数由机械设计第4版(P216)图12.9,=1.16)
19、齿间载荷分配系数 由此得 7)齿向载荷分布系数由机械设计第4版(P218)表12.118)载荷系数K 9)弹性系数由机械设计第4版(P221)表12.12,=189.810)节点区域系数由机械设计第4版(P222)图12.16,取=2.511)接触最小安全系数 由机械设计第4版(P225)表12.14,取=1.0512)总工作时间 13)应力循环次数 由机械设计第4版(P226)表12.15,估计 原估计应力循环次数正确。 14)接触寿命系数 由机械设计第4版(P224)图12.18,取 15)许用接触应力 16)验算 计算结果表明,接触疲劳强度较为合适,齿轮尺寸无需调整。3确定传动主要尺寸1
20、)实际分度圆直径d因模数取标准值时,齿数已重新确定,但并未圆整,故分度圆直径不会改变,即2)中心距a 3)齿宽b 取 二齿根弯曲疲劳强度验算1)重合度系数 2)齿间载荷分配系数 由机械设计第4版(P217)表12.10,3)齿向载荷分布系数 由机械设计第4版(P225)图12.14,4)载荷系数K 5)齿形系数 由机械设计第4版(P229)图12.21得, 6)应力修正系数 由机械设计第4版(P230)图12.22得,7)弯曲疲劳极限 由机械设计第4版(P231)图12.23c得,8)弯曲最小安全系数 由机械设计第4版(P225)表12.14得,=1.259)应力循环次数 由机械设计第4版(P
21、226)表12.15,估计 原估计应力循环次数正确 10)弯曲寿命系数 由机械设计第4版(P232)图12.24得, 11)尺寸系数由机械设计第4版(P232)图12.25得,=1.012)许用弯曲应力13)验算 传动无严重过载,故不作静强度校核。另偏心齿轮的计算如下:1)转矩 式中 P-电动机功率 -齿轮转速2)齿宽系数 由机械设计第4版(P218)表12.13,取=0.83)接触疲劳极限 由机械设计第4版(P223)图12.17c得,4)初步计算的许用接触应力 5)值由机械设计第4版(P227)表12.16,取=956)齿轮直径 取=430mm式中 u-减速器传动比-齿轮转矩7)齿宽b b
22、=8)圆周速度 9)精度等级由机械设计第4版(P207)表12。6,选9级精度。10)齿数z和模数m初取齿数;由机械设计第4版(P206)表12.3,取m=10,则3.4.3减速器结构设计的计算1减速器各部位及附属零件的名称和作用(1)窥视孔和窥视孔盖在减速器上部可以看到传动零件啮合处要开窥视孔,以便检查齿面接触斑点和齿侧间隙,了解啮合情况。润滑油也由此注入机体内。(2)放右螺塞减速器底部设有放油孔,用于排出污油,注油前用螺塞堵住。(3)油标油标用来检查油面高度,以保证有正常的油量。油标有各种结构类型,有的已定为国家标准件。(4)通气器减速器运转时,由于摩擦发热,使机体内温度升高,气压增大,导
23、致润滑油从缝隙向外渗漏。所以多在机盖顶部或窥视孔盖上安装通气器,使机体内热涨气体自由逸出,达到机体内外其他相等,提高机体有缝隙处的密封性能。(5)启盖螺钉机盖于机座接合面上常涂有水玻璃或密封胶,联结后接合较紧,不易分开。为便于取下机盖,在机盖凸缘上常装有一至二个启盖螺钉,在启盖时,可先拧动此螺钉顶起机盖。(6)定位销为了保证轴承座孔的安装精度,在机盖和机座用螺栓联后,镗孔之前装上两个定位销,销孔位置尽量远些。如机体结构是对称的(如蜗杆传动机体),销孔位置不应对称布置。(7)调整垫片调整垫片由多片很薄的软金属制成,用以调整轴承间隙。有的垫片还要起调整传动零件(如涡轮、圆锥齿轮等)轴向位置的作用。
24、(8)环首螺钉、吊环和吊钩在机盖上装有环首螺钉或铸出吊环或吊钩,用以搬运或拆卸机盖。在机座上铸出吊钩,用以搬运机座或整个减速器。(9)密封装置在伸出轴与端盖之间有间隙,必须安装密封件,以防止漏油和污物进入机体内。密封件多为标准件,其密封效果相差很大,应根据具体情况选用。2计算铸铁减速器机体结构尺寸1)机座壁厚一级 =0.025a+1=8mm2)机盖壁厚一级 =0.02a+1= 8mm3)机座凸缘厚度bb=1.5=15.75mm4)机盖凸缘厚度=1.5=12.90mm5)机座底凸缘厚度=2.5=26.25mm6)地脚螺钉直径=0.036a+12=25.68mm7)地脚螺钉数目nn=6()8)轴承
25、旁联接螺栓直径=0.75=19.26mm9)机盖与机座联接螺栓直径=0.5=12.84mm10)联接螺栓的间距=150200取=150mm11)轴承盖端螺钉直径=0.4=10.27mm12)窥视孔盖螺钉直径=0.3=7.70mm13)定位销直径=0.7=8.99mm14)至外机壁距离=26mm(见机械设计课程设计指导书P27表4)15)至凸缘边缘距离=24mm(见机械设计课程设计指导书P27表4)16)轴承旁凸台半径=24mm17)凸台高度根据低速级轴承座外径确定,以便于扳手操作为准。18)外机壁至轴承座端面距离=+8=58mm19)大齿轮顶圆(涡轮外圆)与内机壁距离1.2=12.60mm20
26、)齿轮端面与内机壁距离=10.5mm21)机盖、机座肋厚、0.85=7.31mm0.85=8.93mm22)轴承端盖外径=轴承孔直径+523)轴承端盖凸缘厚度=10.27mm24)轴承旁联接螺栓距离尽量靠近,以和互不干涉为准,一般取第4章 起重机构的液压部分设计 起重机构部分主要由起升机构和伸缩机构两部分组成。其中伸缩机构主要是控制伸缩臂。高空作业车下臂兼做起重基本臂,伸缩臂在基本臂里面,由伸缩油缸控制,不工作时,回缩至基本臂内部,进行起重作业时,伸缩臂进行伸缩。起升机构则主要是用于实现重物的提升和下降。以下具体进行起重机构液压部分的设计:4.1 伸缩机构液压缸设计上臂油缸具体设计如下: 设液
27、压缸单活塞杆双向运动时的负载力相同,不记执行件质量。液压系统工作压力为P=16MPa。4.1.1 确定液压缸类型和安装方式根据主机的运动要求,按机械设计手册4表23.639,选择液压缸类型为单杆活塞式双作用液压缸。此类液压缸特点为活塞双向运动产生推、拉力。活塞在行程终了时不减速14。 将缸体固定,活塞杆运动,按机械设计手册4表23.640 液压缸的安装方式,选择合适的安装方式。考虑机构的结构要求,上臂起升、下降时液压缸的活塞杆进行伸缩实现运动需求。查机械设计手册4表23.6-40 液压缸的安装 (P23-176)选择法兰型安装方式4。4.1.2确定伸缩液压缸的主要性能参数和主要尺寸根据主机的动
28、力分析和运动分析,确定液压缸的主要性能参数和主要尺寸:1) 液压缸内径D的计算 根据载荷力的大小和选定的系统压力来计算液压缸内径D 计算公式: =3.57 (4.1)式中 -液压缸内径(m); -液压缸推力(kM); -选定的工作压力(MPa)。计算如下:下臂处于水平位置时,液压缸对伸缩臂的推力最大,即如下图所示时推力最大。 ( 图4.1.1) 其中:-伸缩臂自重,由计算为3.8510。 -液压缸对伸缩臂的推力。 (4.2)查表23.4-1 摩擦系数,取0.1 。 表23.4-1 摩擦系数导轨类型导轨材料运动状态摩擦系数滑动导轨铸铁对铸铁起动时低速()高速(0.150.200.10.120.0
29、50.08滚动导轨铸铁对滚柱(珠)淬火钢导轨对滚柱0.0050.020.0030.006静压导轨铸铁0.005(表八)将0.1 ,代入式(4.2),得: 将代入式(4.1),得: 按机械设计手册4表23.6-33(P23-173)给出的缸筒内径尺寸系列圆整成标准值。即取2)活塞杆直径的计算 根据速度比的要求来计算活塞杆直径 (4.3)式中 -活塞杆直径(); -液压缸直径(); -速度比。此处,取液压缸的往复运动速度比为1.46,由机械设计手册4表23.6-57(P23-191)4查得: (4.4)将代入式(4.4) 得: 查机械设计手册4表23.6-34 液压缸活塞杆外径尺寸系列4(摘自GB
30、/T2348-1993)取液压缸活塞杆外径尺寸如下: 3)液压缸行程的确定 伸缩臂总长为2.8,查机械设计手册4表23.6-35 液压缸活塞行程第一系列()4,由以上条件取S值如下: 。4)流量的计算由原始数据得,伸缩臂全伸时间 30,且由上面计算可知液压缸活塞杆的行程为1250,则,液压缸活塞杆运动的最小速度。查机械设计手册4表23.44知:,取最大为0.12。即,液压缸活塞杆运动的最大速度为: 则液压缸流量 4.2 起升机构液压马达设计计算 起升液压马达驱动起升减速机旋转,带动滚筒将钢丝绳收进或放出,实现重物的提升和下降14。4.2.1 转矩的计算 起重机构的最大起重重量是1300,以下计
31、算重物对滚筒中心的转矩18。 (4.2.1)其中,F是起重机构的最大起重量。 由高空作业车主要性能参数可知单绳起升速度为0-40。取最大速度为40,计算转矩。即重物起升速度为: ;已知滚筒直径为: ;力F对滚筒中心点取矩: (4.5)其中:F起重机最大起重量; -滚筒半径。将,代入(式4.2.1)。计算得: 考虑成本问题选取齿轮减速机较大传动比为50,则此处液压马达所必须具备的输出转矩为。查机械设计手册4表23.622 QJM系列定量液压马达的技术参数, 表23.622QJM系列定量液压马达的技术参数型号排量/压力/转速范围最大输出转矩/重量额定最大1QJM52-2.01QJM52-2.51Q
32、JM52-3.21QJM52-4.01QJM52-5.01QJM52-6.31QJM61-81QJM61-101QJM61-161QJM61-202.02.53.24.05.06.381016202020201010102020101031.531.531.516161631.531.516161320132012501200116011251631501321-25882010783142108918112701421036297441153531642183180180180180180180500500500500(表九)选定液压马达型号为: 1QJM6120第5章 空压机的确定5.1
33、空压机的主要技术参数 空压机是将原动机(如电动机和内燃机等)的机械功率转换为液体压力能(液压能)的元件。通常分为齿轮泵、叶片泵、柱塞泵、螺杆泵。5.1.1 主要技术参数主要技术参数如下15:(1)泵的排量() 泵每转一周,所能排除的液体体积。(2)泵的理论流量() 在额定转速时、用计算方法得到的单位时间内泵能排出的最大流量。(3)泵的额定流量() 在正常工作条件下,保证泵长时间运转所能输出的最大流量。(4)泵的额定压力() 在正常工作条件下,能保证泵长时间运转的最高压力。(5)泵的最高压力() 允许泵在短时间内超过额定压力运转时的最高压力。(6)泵的额定转速 在额定压力下,能保证长时间正常运转
34、的最高转速。(7)泵的最高转速( 在额定压力下,允许泵在短时间内超过额定转速时的最高转速。(8)泵的容积效率(%) 泵的实际输出流量和理论流量的比值。(9)泵的总效率(%) 泵输出的液压功率与输入的机械效率的比值。(10)泵的驱动功率() 在正常工作条件下能驱动空压机的机械效率。5.1.2 各种泵的比较齿轮泵叶片泵轴向柱塞泵径向柱塞泵外啮合 式内啮合式单作用 式双作用式斜盘式斜轴式配流式阀式通轴式非通轴式隔块式摆线式定 量定量变量定量定 量 变 量 定量变 量定量结 构最简较简简较简较简复杂复杂最复杂最复杂较复杂尺 寸 重 量小小小较小较小大大最大最大较大寿 命短短短较短较短较长较长长长较短价
35、格最廉较廉廉较廉较廉昂贵昂贵最昂贵最昂贵较昂贵流量脉动最大小小较小最小小小小小大抗污染能力强强强较弱较弱弱弱弱弱较弱耐冲击能力较弱较强较弱较弱弱弱最 强最 强 (表十)5.2 空压机的确定 泵的基本参数是压力、流量、转速、效率。一般应根据系统的实际工况来选择,为了提高系统的可靠性,延长泵的使用寿命,一般车辆用液压系统工作压力可选择为泵额定压力的50%-60%。选择泵的第二个重要因素是泵的流量或排量,泵的流量与工况有关,选择泵的流量需大于液压系统工作时的最大流量。泵的效率值是泵的质量好坏的体现,另外,泵的最高压力和最高转速不宜同时使用,以延长使用寿命13。根据液压缸的动作可知,3个液压缸同时动作
36、且速度都为,且液压马达也动作时,系统所需流量最大而自动控制时系统所需流量最小,二者差距较大7。此处选择空压机时我们考虑只执行一项动作时,空压机所必须提供的功率,流量。这有利于减小流量的波动,化简系统的复杂程度。(1)空压机的最大工作压力空压机最大工作压力,由下式确定: (5.1)式中 -空压机最大工作压力,; -液压缸的最大工作压力,。其中。 -管路损失。取。则。 (2)空压机的流量空压机的流量: (5.2)式中 -空压机的流量,; -系统泄漏系数,取; -同时动作液压缸最大总流量,。其中: 液压缸最大流量为36.2。 回转机构液压马达排量为3.140,转速为10-100。 起重机构液压马达排
37、量为10,转速为1-25。因为系统中有溢流阀等,取溢流量等总和3。代入式(5.1)得: 即: 。 选型:CBG 2080/2063 型号为CBG 2080/2063的空压机外形尺寸如下所示16: (5.2.1)5.3 油箱的选择油箱在液压系统中除了储油外,还起着散热、分离油液中的气泡、沉淀杂质等作用。油箱中安装有很多辅件,如冷却器、加热器、空气过滤器及液位计等7。查机械设计手册4表23.9-1 油箱容量4: 表23.9-1 油箱容量JB/T79381999(L)46.3102540631001602503154005006308001000125016002000315040005000630
38、0(表十一) 油箱容量与系统的流量有关,一般容量可取最大流量的35倍。取油箱容量为800L。结论通过几个月的努力,基本实现了预期的设计目标,通过对所选择的零件的校核计算,得出如下结论:(1):空压机冲头上下往复运动是靠偏心齿轮完成的。(2):在本论文中的所有的计算值都是理论值,可能在实际中会存在一些其他的问题。(3):由于时间的仓促,对于该空压机设计所涉及到的其他机构,如送料机构、减震机构等,没有进行设计。通过对所选课题的全面研究及所给参数的分析确定空压机的整体方案,并进行主轴组件的设计计算和主轴箱的整体结构安排,最终完成空压机的设计从而全面培养了综合运用所学的基础理论,分析解决实际问题的能力
39、;为以后更好的走向工作岗位打下坚实的基础。致谢首先,感谢悕向儒老师的悉心教导,悕老师知识渊博,教学严谨,在百忙之中抽空认真负责地指导我,使我在选题和撰写过程中克服很多困难,同时让我在做毕业设计的阶段里学到了好多以前没接触的知识。其次,感谢马雄锋和刘国藩同学在这几个月中对我的帮助。最后,再次衷心的感谢悕老师及所有关心和帮助过我的同学们,毕业在即,祝愿他们身体健康,工作顺利。参考文献1 . 赵升吨,张学来,高长宇,杨辉.空压机的现状及发展趋势J.锻压装备及制造技术,2005,39(1):17-24.2 . 邱宣怀.机械设计(第四版),19973 . 姚艳 ,空压机弹性动力学研究及仿真 导师:郗向儒
40、 西安理工大学 2007年硕士论文4 . 张策.机械动力学M.北京:高等教育出版社,20005 . 孙桓,陈作模.机械原理(第六版)M.北京:高等教育出版社,2001:6 . 徐以光,空压机的发展过程 CMET.锻压装备与制造技术 1985年 第05期7 . 200吨高速自动压力机 CMET.锻压装备与制造技术 1974年 第Z1期8 . 郭涪泽,高速精密压力机概述 CMET.锻压装备与制造技术 1988年 第06期9 . 李建平,王恩福,符起贤,董秋武,麦志辉.空压机振动分析与控制J.机电工程技术,2006,35(6):56-58. 10 .吴宗泽,机械设计,北京:高等教育出版社,2001 11 .孔凌嘉,张春林主编,机械基础综合课程设计,北京理工大学出版社, 2004,ISBN 7-5640-0093-7 12.肖景荣 姜奎安 ,冲压工艺学,机械工业出版社,199913.卢秉恒,机械制造技术基础,机械工业出版社,2005.514.冯辛安,机械制造装备设计,机械工业出版社,2005.1215.杨黎明,黄凯,等.机械零件设计手册.北京:国防工业出版社.1984.16.Peter Van Zant著.赵树武,朱践知,于世恩译.芯片制造M. 北京:电子工业出版社,2004.
- 温馨提示:
1: 本站所有资源如无特殊说明,都需要本地电脑安装OFFICE2007和PDF阅读器。图纸软件为CAD,CAXA,PROE,UG,SolidWorks等.压缩文件请下载最新的WinRAR软件解压。
2: 本站的文档不包含任何第三方提供的附件图纸等,如果需要附件,请联系上传者。文件的所有权益归上传用户所有。
3.本站RAR压缩包中若带图纸,网页内容里面会有图纸预览,若没有图纸预览就没有图纸。
4. 未经权益所有人同意不得将文件中的内容挪作商业或盈利用途。
5. 装配图网仅提供信息存储空间,仅对用户上传内容的表现方式做保护处理,对用户上传分享的文档内容本身不做任何修改或编辑,并不能对任何下载内容负责。
6. 下载文件中如有侵权或不适当内容,请与我们联系,我们立即纠正。
7. 本站不保证下载资源的准确性、安全性和完整性, 同时也不承担用户因使用这些下载资源对自己和他人造成任何形式的伤害或损失。
最新文档
- 人教版小学二年级语文下册第18课《雷雨》ppt课件
- 人教版小学一年级数学下册《练习十五》ppt课件
- 人教版五年级数学下册第二单元整理与复习ppt课件
- 人教版三年级数学下册综合ppt课件
- 人教版五年级下册数学第四单元复习ppt课件
- 人教版小学三年级下-两位数乘两位数ppt课件
- 人教版三年级下册英语ppt课件
- 人教版小学四年级数学上册《角的分类》ppt课件
- 人教版四年级数学下册《乘法交换律和结合律》ppt课件
- 人教版数学二年级下册《轴对称图形》PPT课件
- 人教版四年级下册数学期中考前复习ppt课件
- 人教版三年级数学下册《位置与方向》PPT课件
- 人教版四年级数学下册《三角形的特性》PPT课件
- 人教版七年级下册英语ppt课件
- 人教版五年级下册《约分的练习课》练习十六ppt课件