Joint welding wire
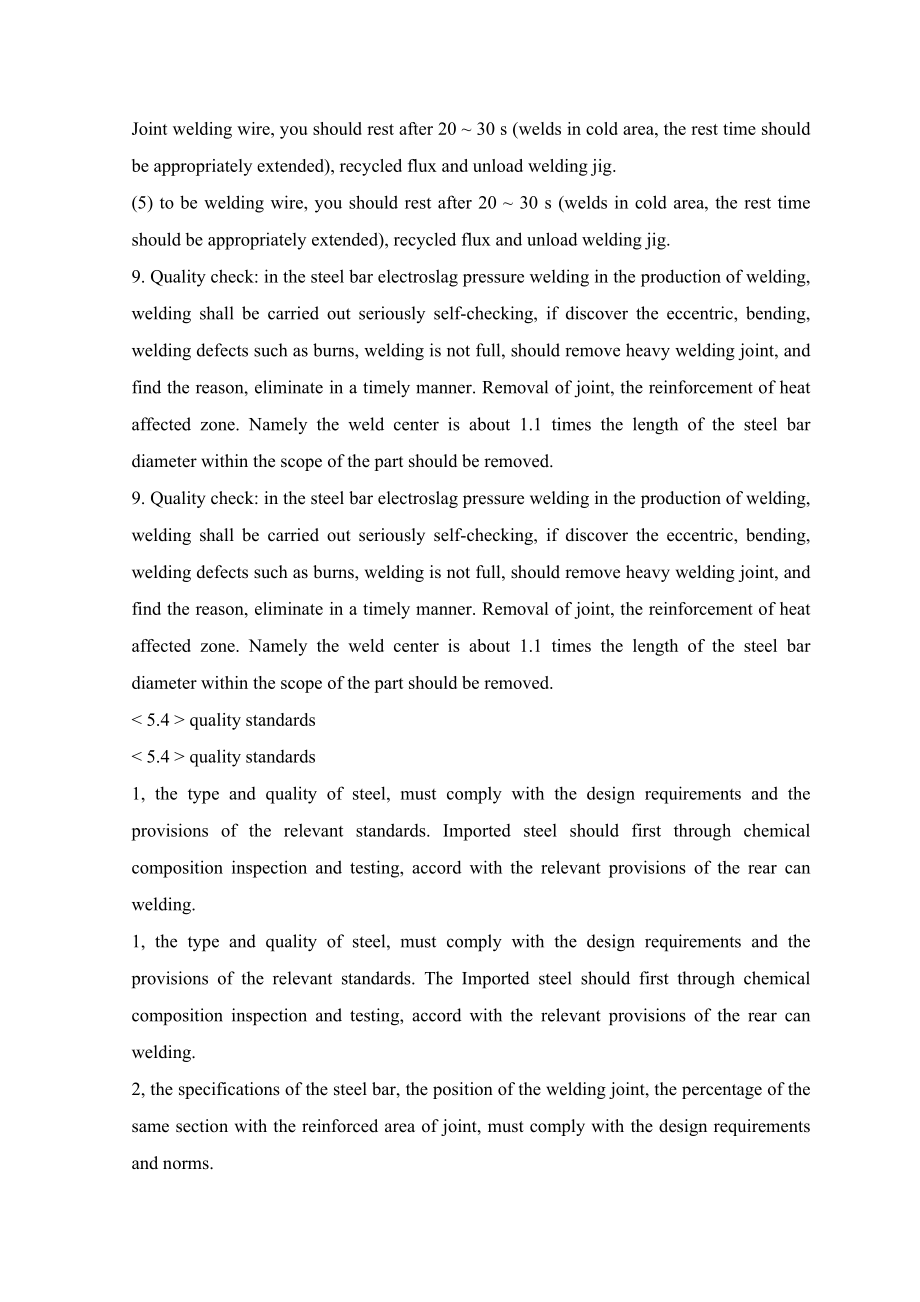


《Joint welding wire》由会员分享,可在线阅读,更多相关《Joint welding wire(5页珍藏版)》请在装配图网上搜索。
1、Joint welding wire, you should rest after 20 30 s (welds in cold area, the rest time should be appropriately extended), recycled flux and unload welding jig. (5) to be welding wire, you should rest after 20 30 s (welds in cold area, the rest time should be appropriately extended), recycled flux and
2、unload welding jig. 9. Quality check: in the steel bar electroslag pressure welding in the production of welding, welding shall be carried out seriously self-checking, if discover the eccentric, bending, welding defects such as burns, welding is not full, should remove heavy welding joint, and find
3、the reason, eliminate in a timely manner. Removal of joint, the reinforcement of heat affected zone. Namely the weld center is about 1.1 times the length of the steel bar diameter within the scope of the part should be removed. 9. Quality check: in the steel bar electroslag pressure welding in the p
4、roduction of welding, welding shall be carried out seriously self-checking, if discover the eccentric, bending, welding defects such as burns, welding is not full, should remove heavy welding joint, and find the reason, eliminate in a timely manner. Removal of joint, the reinforcement of heat affect
5、ed zone. Namely the weld center is about 1.1 times the length of the steel bar diameter within the scope of the part should be removed. quality standards quality standards 1, the type and quality of steel, must comply with the design requirements and the provisions of the relevant standards. Importe
6、d steel should first through chemical composition inspection and testing, accord with the relevant provisions of the rear can welding. 1, the type and quality of steel, must comply with the design requirements and the provisions of the relevant standards. The Imported steel should first through chem
7、ical composition inspection and testing, accord with the relevant provisions of the rear can welding. 2, the specifications of the steel bar, the position of the welding joint, the percentage of the same section with the reinforced area of joint, must comply with the design requirements and norms. 2
8、, the specifications of the steel bar, the position of the welding to be, the percentage of the same section with the reinforced area of be, must comply with the design requirements and norms. 3, electroslag pressure welding head of mechanical performance testing must be qualified. From each batch o
9、f joint mechanical properties test, taking three random joint in tensile test. 3, electroslag pressure welding head of mechanical performance testing must be qualified, the From each batch of be mechanical properties test, taking three random be in tensile test. A. in general structure, level with 3
10、00 steel joint as A batch. A. in the general structure, level with 300 steel to be as A batch. B. in the cast-in-place reinforced concrete multilayer structure, with each floor or construction section of the level of steel joint as a group, are still less than 300 joint as a batch. B. in the cast -
11、in - place reinforced concrete multilayer structure, with each floor or construction section of the level of steel to be as a group, are still less than 300 to be as a batch. 4, steel bar electroslag pressure welding head individually appearance inspection, the results shall meet the following requi
12、rements: 4, steel bar electroslag pressure welding head individually appearance inspection, the results shall meet the following requirements: 1) welding package is relatively uniform, highlights the minimum steel surface 4 mm higher. 1) welding package is relatively uniform, highlights the minimum
13、steel surface 4 mm who. 2) electrode in contact with the steel bar, no obvious burn defect. 2) electrode in contact with the steel bar, no obvious burn defect. 3) the bending Angle of joint is not greater than 4 . 3) the bending Angle of be is not greater than 4 . 4) of the joint axis deviation shou
14、ld be no more than 0.1 times the bar diameter, at the same time is not more than 2 mm. 4) of the be axis deviation should be no more than 0.1 times the bar diameter, at the same time is not more than 2 mm. 5) inspection unqualified should remove heavy welding joint, or to take remedial measures. 5)
15、inspection unqualified should remove heavy welding to be, or to take remedial measures. the finished product protection the finished product protection Joint weld than, should rest after 20 30 s to short of the fixture, bending to avoid joint. To be weld than, should rest after 20 30 s to short of t
16、he fixture, bending the to get to be. should be paid attention to the quality problem should be paid attention to the quality problem 1. The steel bar electroslag pressure welding production, should pay attention to any link of the whole welding process. Joint parts should be clean; Reinforced insta
17、llation should be solidarity; Fixture fastening, fight, arc process, strive to reliable; Arc process, delay fully; Electroslag process, short and stable, extrusion process, the appropriate pressure. Steel bar electroslag pressure welding head welding defects and the prevention measures 1. The steel
18、bar electroslag pressure welding production, should pay attention to any link of The whole welding process, to be with parts should be clean; Reinforced the installation should be, solidarity; Fixture fastening, fight, the arc process, strive to reliable; The Arc process, delay fully; Electroslag pr
19、ocess, short and stable, extrusion process, the appropriate pressure, Steel bar Electroslag pressure welding head welding defects and the prevention measures The items are welding defect prevention measures The items are welding defect prevention measures 1 the axis offset 1. Straightening steel end
20、s 1 the axis offset 1. Straightening steel ends 2. Correct installation jig and reinforced 2. The Correct installation jig and reinforced 3. Avoid excessive extrusion 3. Get excessive extrusion 4. Repair or replace the fixture in a timely manner 4. Repair or replace the fixtures in a timely manner 2
21、 bend 1. Straightening steel ends 2 bend 1. Straightening steel ends 2. Pay attention to the bar on the installation and support 2. Pay attention to the bar on the installation and support 3. Avoid excessive discharge after welding fixture 3. Get excessive discharge after welding fixture 4. Repair o
22、r replace the fixture 4. Repair or replace the fixture 3 welding thin and big package 1. Reduce spinning speed 3 welding thin and big package 1. Reduce spinning speed 2. Decrease the welding current 2. Decrease the welding current 3. Reduce the welding time 3. Reduce the welding time 4 bit edge 1. D
23、ecrease the welding current 4 bit edge 1. Decrease the welding current 2. The welding time 2. The welding time 3. Pay attention to the starting point of the jaw, to ensure that the steel bar under freely 3. Pay attention to the starting point of the jaw, to ensure that the steel bar under freely 5 n
24、ot weld 1. Increase the welding current 5 not weld 1. Happens the welding current 2. Avoid welding time is too short 2. Get welding time is too short 3. The inspection jig, ensure reinforcement under freely 3. The inspection jig, ensure reinforcement under freely 6 1. The welding package unevenness
25、of reinforced end demand is flat and level June 1. The welding package unevenness of reinforced end demand is flat and level 2. The loading flux uniform as far as possible 2. The loading flux uniform as far as possible 3. To extend the time of welding, appropriate increase the fusion quality 3. To e
26、xtend the time of welding, appropriate happens the fusion quality 7 hole 1. According to the specified requirements for flux 7 hole 1. According to the specified requirements for flux 2. Remove steel welding parts of the rust 2. Remove steel welding parts of the rust 3. Ensure the embedment depth by welding in flux 3. Ensure the embedment the depth by welding in flux 1. 8 burns reinforced conductive parts remove all rust
- 温馨提示:
1: 本站所有资源如无特殊说明,都需要本地电脑安装OFFICE2007和PDF阅读器。图纸软件为CAD,CAXA,PROE,UG,SolidWorks等.压缩文件请下载最新的WinRAR软件解压。
2: 本站的文档不包含任何第三方提供的附件图纸等,如果需要附件,请联系上传者。文件的所有权益归上传用户所有。
3.本站RAR压缩包中若带图纸,网页内容里面会有图纸预览,若没有图纸预览就没有图纸。
4. 未经权益所有人同意不得将文件中的内容挪作商业或盈利用途。
5. 装配图网仅提供信息存储空间,仅对用户上传内容的表现方式做保护处理,对用户上传分享的文档内容本身不做任何修改或编辑,并不能对任何下载内容负责。
6. 下载文件中如有侵权或不适当内容,请与我们联系,我们立即纠正。
7. 本站不保证下载资源的准确性、安全性和完整性, 同时也不承担用户因使用这些下载资源对自己和他人造成任何形式的伤害或损失。