多工位飞锤钻孔专用机床设计毕业设计(论文)
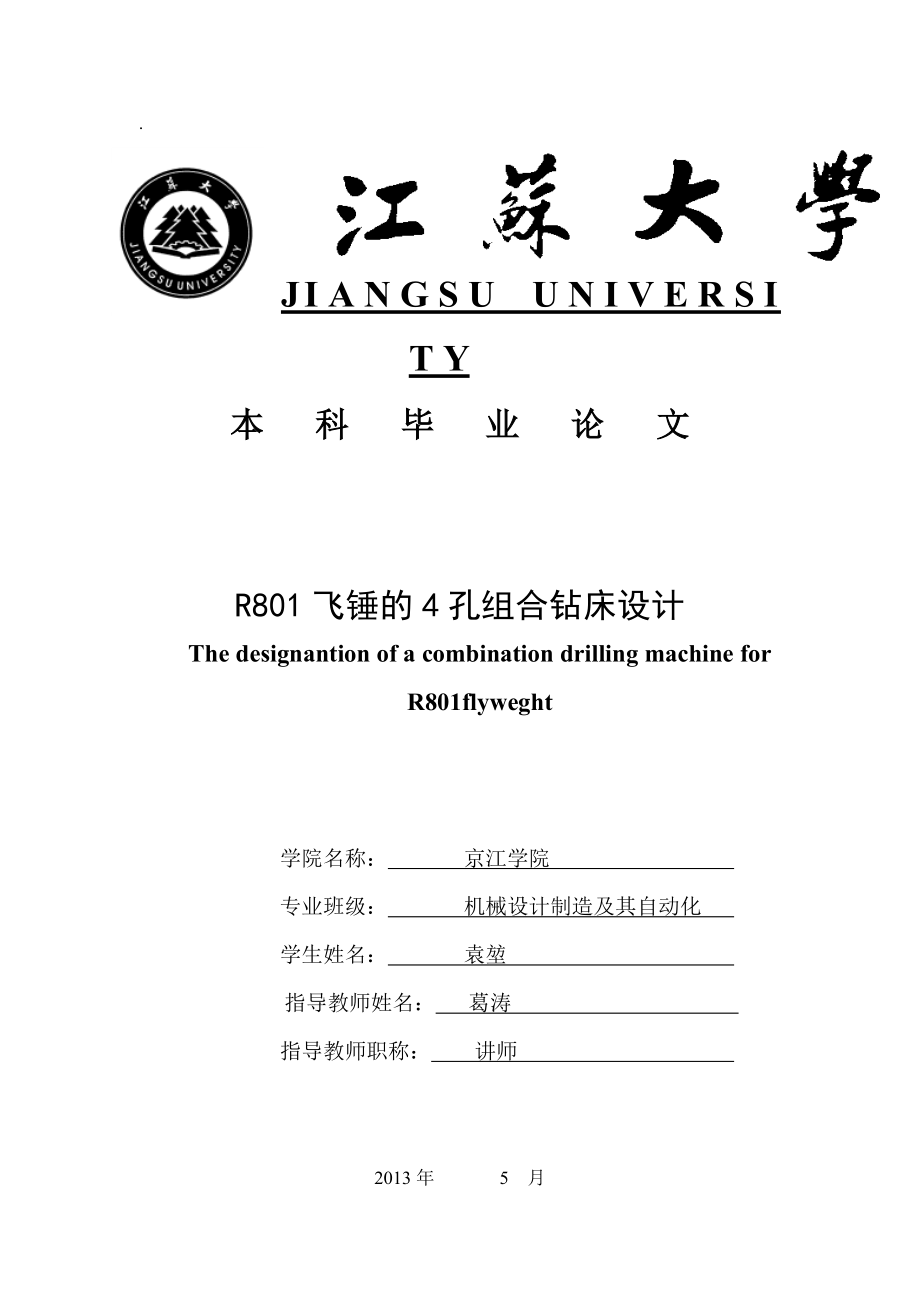


《多工位飞锤钻孔专用机床设计毕业设计(论文)》由会员分享,可在线阅读,更多相关《多工位飞锤钻孔专用机床设计毕业设计(论文)(40页珍藏版)》请在装配图网上搜索。
1、.J I A N G S U U N I V E R S I T Y本 科 毕 业 论 文R801飞锤的4孔组合钻床设计The designantion of a combination drilling machine for R801flyweght学院名称: 京江学院 专业班级: 机械设计制造及其自动化 学生姓名: 袁堃 指导教师姓名: 葛涛 指导教师职称: 讲师 2013年 5 月飞锤4孔组合钻床设计的意义专业班级:机械0902 学生姓名:袁堃指导老师:葛涛 职称:讲师摘要 本文首先通过分析比较,确定了4孔单工位组合钻床的配置型式及结构的最佳方案,遵循机械设计中标准化、通用化、系列化原
2、则, 给出机床的总体设计,绘制出代表机床总体设计的被加工零件工序图、加工示意图、机床联系尺寸图和生产率计算卡。对本机床的关键部分:主轴箱和夹具的结构进行了创新设计。由于在本台组合钻床上髓同时加工4个孔,孔多、间距小,采用常规方法排箱无法实现4孔的工序集中的加工方案。本钻床的主轴箱传动系统通过采用变位齿轮和滚针轴承等结构方面的创新设计,将常规方法下不能完成的排箱成为可能。本台组合钻床夹紧机构,采用了快速螺旋夹紧机构。减少了装卸零件所用时间,提高了生产效率。本文从企业实际需求出发。在全面分析被加工零件的结构特点、尺寸精度、被加工孔相互之间位置精度、表面粗糙度和技术要求的基础上,指出采用现有设备不仅
3、工人劳动强度大,生产率低,而且零件加工精度难以保证。根据实际需要,研制出了4孔单工位组合钻床。按上述设计方案制造出的4孔单工位组合钻床与原方案加工工件的实验结相比较,有以下几个突出的优点:1 提高了加工精度在普通钻床上加工,由于是采用多工步,各孔的位置精度不易保证,废品率一般在2:采用4孔组合钻床,因为在设计的每一个环节,都严格控制设计零件的精度,且是多刀同时加工,所加工出的零件位置精度均在要求范围内,废品率为0。通过实际运行结果证明:该4孔单工位组合钻床确实达到了“体积小,重量轻,结构简单,使用方便,效率高,质量好”的要求。既大大减轻了工人的劳动强度,又给厂家带来了可观的经济效益。2. 提高
4、了生产率在本台组合钻床上加工该零件,由于是8把刀具同时加工,缩短了辅助时间,加工循环时间仅为27min,而在原普通钻床上加工此工件,加工循环时间平均需要15分钟,生产率提高了46倍。关键词: 组合钻床 主轴箱 夹具设计 传动设计The meaning of the designation of a combination drilling machine for R801flyweghtABSTRACT In view of the actual conditions of enterprises and on the basis of overall analyzing workpiece
5、structure features,accuracy of size,surface roughness,accuracy of distance between drilled holes and other technical requirements,this article points out that the existing equipments used to manufacture workpieces may result in lower productivity,greater intensity of labor and worse working accuracy
6、Therefore,it is necessary to develop a new type of 4 hole single working position combination drilling machineThrough analysis and comparison,the article has determined the best project of the structure and the disposition of the 4 holes combination drilling machineAccording to the principle of stan
7、dardization,generalization and serialization in machine design,the article offers the master design of the drilling machine,the process drawing of workpiece,the working diagram,the connection dimensional drawing of the drilling machine and the calculating card of productivityIn some key parts of the
8、 drilling machine,there are certain new designs on the structure of the spindle box and the fixtureWith 4 hole drilled simultaneously on the drilling machine,in addition to dispersive arrangement of hole position,the 4 holes drilling program cannot be completed in conventional wayIn the transmission
9、 system of 4 hole drilling machine are used some new structural designs such as pin bearings and position-changeable gears,so that the arrangement of hole position,which cannot be finished in conventional way,can be accomplishedThe combination drilling machine is applied a fast spiral pinch machiner
10、y whose features are not only shortens the time consumed in loading and unloading workpiece but also enhances productivityAfter the experimental result of the new type of 4 hole combination drilling machine is compared with the one of the original working program,there are followingprominent advanta
11、ges:1Improving working accuracyThereject rate of workpiece cut on the general-purpose drilling machine usually reaches to 2 because of its multistep working procedure,so it is difficult to secure the spacing accuracy of every holeYet the 4 hole combination drilling machine may reach to 0This is beca
12、use the working accuracy of workpiece is strictly controlled at each design point and the spacing accuracy of workpiece cut by multitool is limited within thedesired scopeThe result checked through actual operation proves that the 4 hole combination drilling machine really meets the requirement of“s
13、mall in volume,light in weight,simple in structure,convenient in use,high in efficiency and excellent in quality”This type of drilling machine reduces the labor strength largely and brings enterprises huge economic benefits,either2Enhancing productivityIf the workpiece is cut with 4 drills on the co
14、mbination drilling machine,the auxiliary time would be shortened and the working cycle time would be limited within 27minOn the other hand,if the workpiece is cut on the general-purpose drilling machine,its working cycle time would take 15min on an average,the productivity would increase by 46 times
15、Key Words:Combination drilling machine Design of transmission systemSpindle box Design of fixture目录第一章 绪论111 论文背景及研究意义112 组合机床发展概况1121组合机床的由来1122组合机床技术装备现状与发展趋势113 本文研究的主要内容2第二章 4孔钻床总体设计321 4孔单工位组合钻床工艺方案的制定322 4孔组合钻床配置型式及结构方案的确定323 主要参数的计算4231确定切削用量,计算各主轴转速4232 确定切削力F、切削转矩M、切削功率P524 组合机床总体设计5241被加工零
16、件工序图6242加工示意图的设计6243机床联系尺寸图的绘制11244生产率计算卡14第三章 主轴箱设计1631绘制主轴箱设计原始依据图1632主轴结构形式的选择及动力计算203. 3传动系统的设计和计算2034多轴箱的坐标计算2435主轴箱通用轴类零件选择2636主轴及通用传动轴结构形式的选择方案2737通用齿轮及其他通用件及传动轴轴承型号的选用29第四章 夹具设计3141机床夹具的概述3142定位支承系统设计31421定位支承系统的设计原则31422定位支承元件及其布置3243导向装置设计33431导向装置的作用33432固定式导套的设计33433固定钻模板结构设计35 44夹紧机构设计3
17、5441夹紧方案的确定35第四章 结束语37致谢38参考文献39第一章 绪论11论文背景及研究意义目前, 我国中、小型企业的产品质量和生产效率都需要有一个新的提高。但是N-r手段却远远不能满足要求。有远见的企业家根据国情、厂情,都认为只有走技术改造的道路,按照实际情况对现有设备的技术状态进行改造,通过强化自身,以求自我发展,才是一条捷径。许多中小型企业都结合自己的实际,设计、改装适合自身特点的机床以提高工作效率,降低设备占用率和人力占用率,降低工人劳动强度。衡量对机床进行技术改造是否合理,唯一的标准是看能否满足企业的实际需要。满足企业的实际需要,既包含着通过改造以提高机床的使用性能和精度,以满
18、足生产的需要,也包含着技术上的先进性与企业投入的可能性相一致。一般来说,企业加工能力的提高有三条途径。其一是增加企业设备的拥有量;其二是对老设备进行更新;其三是进行技术改造。其中,技术改造具有投资最少、见效最快、容易实现等特点。飞锤侧面上,需加工的孔数量有多个,且为了生产效率一次要转四个孔,还要保证同轴度,间距小,排列又分散。采用普通方法排箱无法完成对4孔同时加工。采用变位齿轮和滚针轴承等创新性的结构设计,把常规状况下不能完成的钻孔成为可能,使需在多工序完成的钻削加工在同一工步完成。飞锤大的使用量较大,一般机械中多处会用到飞锤,应用这台组合钻床不仅能提高生产效率和加工精度,降低设备占用率,减轻
19、工人劳动强度,而且还会为厂家带来可观的经济效益。12组合机床及发展概况121组合机床的由来组合机床是按系列化标准化设计的通用部件和按被加工零件的形状及工艺要求设计的专用部件组成的专用机床。组合机床是随着生产的发展,由万能机床和专用机床发展来的。它既有专用机床效率高结构简单的特点,又有万能机床能够重新调整,以适应新工件加工的特点。为此,将机床上带动刀具对工件进行切削运动的部分以及床身、立柱、工作台等设计制造成通用的独立部件,称为“通用部件”。根据工件加工的需要,用这些通用部件配以部分专用部件就可组成机床,这就是组合机床。当加工对象改变了,用这些通用部件,只将部分专用部件改造,又可以组成加工新工件
20、的机床。组合机床是按工序集中原则设计的,即在一台机床上可以同时完成许多同种工序或多种不同工序的加工。122组合机床技术装备现状与发展趋势组合机床及其自动线是集机电于体的综合自动化程度较高的制造技术和成套工艺装备。它的特征是高效、高质、经济实用,因而被广泛应用于工程机械、交通、能源、军工、轻工、家电等行业。我国传统的组合机床及组合机床自动线主要采用机、电、气、液压控制,它的加工对象主要是生产批量比较大的大中型箱体类和轴类零件(近年研制的组合机床加工连杆、板件等也占一定份额),完成钻孔、扩孔、铰孔,加工各种螺纹、镗孔、车端面和凸台,在孔内镗各种形状槽,以及铣削平面和成形面等。组合机床的分类繁多,有
21、大型组合机床和小型组合机床,有单面、双面、三面、卧式、立式、倾斜式、复合式,还有多工位回转台式组合机床等;随着技术的不断进步,一种新型的组合机床_柔性组合机床越来越受到人们的青睬,它应用多位主轴箱、可换主轴箱、编码随行夹具和刀具的自动更换,配以可编程序控制器(P L C)、数字控N(N C)等,能任意改变工作循环控制和驱动系统,并能灵活适应多品种加工的可调可变的组合机床。另外,近年来组合机床加工中心、数控组合机床、机床辅机(清洗机、装配机、综合测量数控组合机床、试验机、输送线)等在组合机床行业中所占份额也越来越大。由于组合机床及其自动线是一种技术综合性很高的高技术专用产品,是根据用户特殊要求而
22、设计的,它涉及到加工工艺、刀具、测最、控制、诊断监控、清沈、装配和试漏等技术。我国组合机床及组合机床自动线总体技术水平比发达国家要相对落后。国内所需的一些高水平组合机床及自动线几乎都从国外进口。工艺装备的大量进口势必导致投资规模的扩大,并使产品生产成本提高。因此,市场要求我们不断开发新技术、新工艺,研制新产品,由过去的“刚性”机床结构,向“柔性”化方向发展,满足用户需求,真正成为刚柔兼备的自动化装各。随着市场竞争的加剧和对产品需求的提高,高精度、高生产率、柔性化、多品种、短周期、数控组台机床及其自动线正在冲击着传统的组合机床行业企业,因此组合机床装备的发展思路必须是以提高组合机床加工精度、组合
23、机床柔性、组合机床工作可靠性和组合机床技术的成套性为主攻方向。一方面,加强数控技术的应用,提高组合机床产品数控化率;另一方面,进一步发展新型部件,尤其是多坐标部件,使其模块化、柔性化,适应可调可变、多品种加工的市场需求。从2002年年底第21届日本国际机床博览会上获悉,在来自世界lO多个国家和地区的500多家机床制造商和团体展示的最先进机床设备中,超高速和超高精度加工技术装备与复合、多功能、多轴化控制设备等深受欢迎。据专家分析,机床装备的高速和超高速加工技术的关键是提高机床的圭轴转速和进给速度。该届博览会上展出的加工中心,主轴转速10000200002 rm in。最高进给速度可达2060mm
24、in;复合、多功能、多轴化控制装备的前景办被看好。在零部件一体化程度不断提高、数量减少的同时,加工的形状却日益复杂。多轴化控制的机床装备适合加工形状复杂的工件。另外,产品周期的缩短也要求加工机床能够随时调整和适应新的变化,满足各种各样产品的加工需求。然而更关键的是现代通信技术在机床装备中的应用,信息通信技术的引进使得现代机床的自动化程度进一步提高,操作者可以通过网络或手机对机床的程序进行远程修改,对运转状况进行监控并积累有关数据,通过网络对远程的设备进行维修和检查、提供售后服务等。在这些方面我国组合机床装备还有相当大的差距,因此我国组合机床技术装备高速度、高精度、柔性化、模块化、可调可变、任意
25、加工性以及通信技术的应用将是今后的发展方向。13本文研究的主要内容零件飞锤见附图l所示,有4个孔待加工,原来采用的加工方案是在普通钻床上逐孔加工,工人频繁忙于装夹工件、启动机床、进刀、退刀、停车及卸工件等,不仅工人劳动强度大,而且生产率也低,不利于保证产品加工精度。在对这4孔进行精度、相互之间位置要求以及零件的装配要求分析的基础上, 重新制定出合理的机械加工工艺方案,将4个孔安排在一道工序上完成。由于在本台组合钻床上需同时加工4个孔,不仅孔多、间距小,而且要保证孔的相对位置精度,采用常规方案排箱无法实现4孔的工序集中。因此本钻床的主轴箱传动系统通过采用变位齿轮和滚针轴承,将常规情况下不能完成的
26、排箱得以实现,从而使需在多工序完成的钻削加工在同一工步完成。底座、滑台、动力头等通用部件的合理选用:齿轮箱排箱结构紧凑:夹具部分定位合理可靠;工件装夹方便灵活;刀具更换简便;机械化程度高;减轻工人的劳动强度是本文研究的主要内容。第二章 组合钻床总体设计21组合钻床工艺方案的制定制定组合钻床工艺方案是设计组合钻床最重要的内容之一。工艺方案制定的正确与否,将决定机床能否达到“重量轻、体积小、结构简单、使用方便、效率高、质量好”的要求。为了该机床方案制定的合理、先进,在方案设计时,密切联系实际,总结实践经验,全面了解被加工零件的加工情况和影响方案制定的各种因素。主要考虑以下因素:(1)工艺过程和加工
27、精度的要求被加工零件有4孔待加工,且相互之间位置精度要求为O.04mm。将4孔集中在一个工位上可确保相互之间的位置精度,对大量生产及顺利装配创造了条件。被加工零件的表面粗糙度和位置精度要求均满足。故选用组合钻床满足被加工零件的要求。(2)加工零件的特点被加工件材料为ZG40Cr。工件刚度足够。由于被加工件为飞锤,成品要与其他零件装配。钻孔时,从装配结合面钻起,这样能够更好地保证孔的位置精度。因为钻孔过程中,中心线可能偏斜,在钻头进口处的位置精度比出口处的好,有利于两个零件的装配。(3)定位基准及加压部位的选择被加工件装配结合面为设计平面,选用设计基准为主定位基准,这样减少了累积误差,使加工精度
28、得到有利保证,同时,此平面最大,用它定位能使切削力均落在定位平面之内。选用16mm的己加工外圆表面和斜底座实现工件完全定位。通过分析被加工件的特点,在已经选择好工艺基面的同时,决定夹紧力作用点在16mm外圆附近处。因为多轴钻孔时产生很大的切削力,为使工件在加工过程中不产生位移和振动,必须将工件牢固夹住,并且有足够的加压刚度,这样可使加压合力落在定位平面之内,且接近定位平面的中心,使工件加压后定位稳定。 (4)孔间中心距的影响在确定组合机床完成工艺时,由于主轴箱的主轴结构和设置导向的需要,以及保证必须的加工精度和工作可靠性的要求,组合机床钻孔时,对于通用的主轴箱,其主轴最小中心距为24mm,这时
29、主轴能钻由l0mm以下的孔。图中空间距离为32mm, 大于24mm。(5)工件的生产方式由于被加工件属于大批量生产。将加工4孔工序集中于一台钻床,可提高组合机床的利用率。22 4孔组合钻床配置型式及结构方案的确定根据上述工艺方案确定机床的型式和总体布局。在选择机床配鬻型式时,既考虑到实现工艺方案,保证加工精度、技术要求及生产率:又考虑到机床操作、维护、修理、排屑的方便性,还注意到被加工零件的生产批量。影响组合钻床配置型式和结构方案的主要因素有:(1)加工精度在选择组合钻床的结构方案时,首先毖须注意到能否保证稳定的加工精度。通常根据经验数据进行机床配置型式的选择。固定式夹具组合钻床能达到的钻孔位
30、置精度最高,采用固定导套一般能达O20mm,当严格要求主轴与导向的同轴度,减少钻头与导套间的间隙导向装置靠近工件时,可达到O15mm。(2)机床生产率根据工件的生产类型,完全可以采用单工位固定夹具的机床型式。(3)被加工件的尺寸、形状、加工部位的特征根据被加工零件的特点,适于采用卧式机床,再考虑到采用卧式机床可使定位基面与设计基面重合,而且排除切屑容易。 (4)操作的方便性合理确定装料高度以使操作方便。在现阶段,设计组合机床时,装料高度可视6具体情况在8501060mm之间选取,由于被加工件较小,装料高度可稍高些。(5)夹具形式对机床方案的影响从工件形状看,似乎可采用立式机床加工,但是考虑到对
31、面孔之间的位置精度,立式钻床无法保证,因而采用卧式加工方案。(6)使用厂的技术能力和工作环境为使钻床在温度过高时工作性能稳定,而且由于被加工件不需多次进给,故选用机械通用部件配置钻床。23主要参数的计算231确定切削用量,计算各主轴转速组合机床能否达到预定要求与正确的选择切削用量有很大关系。切削用量选用适当,能使机床以最少的停车时间,最高的生产效率,最长的刀具寿命和最好的加工质量进行生产。目前,组合机床切削用量的选则。因是多轴加工不宜采用最大的切削速度和进给量。主要是参照实际生产中采用切削用量的情况,并根据多年来积累起来的一些经验数据进行。组合机床切削用量的选则另外一个特点,就是动力头工作时每
32、分钟的进给量只有一种,这样所有刀具每分钟的进给量是相同的。这个进给量是适合所有刀具的平均值。但同一动力头每个刀具的转速可以不一样,以便选择合理的刀具的进给量。为使所有刀具的性能得到充分发挥,钻孔时采用较高的速度和较小的每转进给量:在现有生产率要求下没必要把切削用量定的太高,以免增加刀具损耗,也可减少所需的切削功率。综合被加工件的加工精度、加工材料、工作条件、刀具耐用度等因素,初选动力滑台的进给速度为60mmmin,初定切削速度1 5mmin由计算公式:n= (21) 式中:n一为各主轴转速,单位rmin v为主轴切削速度, 单位mmin,f为每转进给量,单位mmrd为各钻头直径,单位mm。表2
33、-1各主轴转速和每转进给量各主轴转速n(rmin)各主轴刀具进给量f(mmr)备注8mm孔596.80.107初选切削速度15 mmin初选进给速度60 mmmin6mm孔795.70.08232确定切削力F、切削转矩M、切削功率P根据选择的切削用量,确定切削力,作为选择动力部件及夹具设计的依据:确定切削转矩,用以确定主轴及其他传动件(齿轮、传动轴等)的尺寸:确定切削功率,用以选择动力箱电机功率。高速钢钻头在灰铸铁上钻孔的计算公式为:F= (22)M= (23)P= (23)T= (23)式中: F轴向切削力(N)D钻头直径(mm)f每转进给量(mmr)P切削功率(kw)M切削转矩(N.mm)
34、HB零件的布氏硬度 本零件材料为ZG40Gr,取HB247270v切削速度(mmin)T刀具耐用度(min)表2-2各主轴切削力、切削扭矩、切削功率计算值钻头直径d(mm)轴向切削力F(N)切削转矩M(Nm)切削功率P(kw)刀具耐用度(min),1359.83398.60.2081851019.91967.50.161335由上表,总切削力为: =9518.8N,总切削功率为: =1.476KW,总切削扭距= 21464.4Nm24组合机床总体设计组合机床总体设计就是针对被加工零件,在选定的结构方案基础上,进行方案图纸设计,这些图纸包括:被加工零件工序图,加工示意图,机床联系尺寸图。生产率计
35、算卡。241被加工零件工序图根据被加工零件的机械加工工艺过程卡如表2-3所示,制定出被加工零件工序图。此图是根据选定的工艺方案,表示在本台机床上完成的工序内容、加工部位的尺寸精度、技术要求、定位基准、夹紧部位、以及被加工零件的材料、硬度和本机床加工前毛坯情况。是机床设计的主要依据,也是调整机床、检验精度的重要技术文件。表2-3被咖工零件加工工艺过程卡机械加工工艺过程产品型号R801零件图号003产品名称飞锤零件名称飞锤共一页第一页材料牌号ZG40Gr毛坯种类铸件毛坯可制件数1备注序号工序工序内容设备工艺装备01铸造铸造毛坯件02清砂时效处理清砂时效处理03铣端面铣侧端面X6036铣床夹具04铣
36、端面铣底端面X6036铣床夹具05钻孔钻侧端面四个通孔组合钻床专用夹具06绞孔绞侧端面四个通孔组合钻床专用夹具07检验检验零件是否合格242加工示意图的设计零件的加工方案要通过加工示意图反映出来。加工示意图表示被加工零件在机床上的加工过程,刀具、辋具的布置状况以及工件、夹具、刀具等机床各部件间的相对位置关系、机床的工作行程及工作循环等。因此,加工示意图是组合机床设计的主要图纸之一,它是刀具、辅具、夹具、主轴箱、电气装置设计及通用部件选择的主要原始资料,也是整台组合机床布局和性能的原始要求,同时还是调整机床、刀具及试车的依据。其内容包括以下几方面:(1)刀具的选择根据被加工工件4个孔的大小,选用
37、5种规格的刀具如下表所示。表2-4 刀具名称,标准尺寸及数量刀具名称钻头直径钻刀悬伸长度数量备注刀具总长刀具悬伸长莫氏锥柄麻花钻1号6138574GBT 1438.1-1996莫氏锥柄麻花钻1号8156754GBT 1438.1-1996(2)导向结构的选择导向类型的确定根据刀具导向线速度V=15mmin,小于20 mmin,故采用固定式导向,刀具在导套内既转动又移动,这种导向方法精度好。导向数量的确定报据工件形状、刀具刚度及工作情况采用单导向。导向参数的确定导套长度由经验公式 =(24)d,小直径时取大值,大直径时取小值。具体尺寸及配合见下表图2-1 固定导向装置的尺寸及配合表2-5导向装置
38、的尺寸及配合参数d(F7)D(k6)Lm配合螺钉GBT8045.5-1999数量181512205.5M64221812227M64(3)导向到工件端面距离以不妨碍排屑为原则,选为10mm。以四个垫块保证间距,实现主定位。(4)确定主轴直径及各主轴外伸长度主轴直径:d= B (26)式中: d轴的直径(mm)M主轴承受的转矩(Nmm)B系数,当材料的剪切弹性模量G=81Nmm时,非刚性主轴取7.3,传动轴为6.2。为使轴的强度足够,主轴材料均采用合金钢。表2-6主轴参数轴号材料主轴直径主轴外伸尺寸备注L1440Gr20115刚性主轴5840Gr1585(5)接杆的选择;主轴箱各主轴的外伸长度为
39、一定值,而且刀具长度也为一定值。因此,为保证主轴籍上各刀具能同时到达加工极限位置,就需要在主轴与刀具之闻设置一中间可调环节刀具接杆。由于接杆上的尺寸D与主轴外伸长度上的内孔配合,可根据尺寸及刀具为莫氏l号。选用接杆T0635-01。由于各主轴均d=20mm,故均用3号接杆、A型、长度范围215500mm(6)确定加工示意图的联系尺寸最重要的尺寸是主辅箱端丽到工件端面之间的距离。如图2-2所示。图2-2加工示意图的联系尺寸计算图该尺寸为:L=+-B-(+) (27) 式中各符号意义:主轴外伸长度钻刀悬伸长度接杆伸出长度(可调)加工孔深刀具的切出值B螺母及垫圈厚度经计算调整后选择接杆标记如表27所
40、示。表27与主轴刀具配合的接杆号刀具直径接杆号1-245 T0635-011-223 T0635-01(7)动力头工作循环及其行程的确定此台组合钻床根据被加工件为浅孔,循环过程包括:快速引进、工作进给和快速退回。如图2-3所示图2-3工作循环图工作进给长度的确定工进长度L,等于被加工孔深与刀具的切入长度与切出长度之和。如图2-4所示。图2-4工作进给长度即:=+ (2-8)按被加工件孔深最大值(长20mm)来选取,一般取为510mm,取d+(38),据此,工进长度定为35mm。快速引进长度的确定快速引进是动力头把刀具送到工作进给的位置,其长度按具体情况定为=25mm。快速退回长度其为工进与快进
41、之和。即:=+ (29)因为是固定式夹具钻孔的机床,动力头快退的行程,只要把所有刀具都退到导套内,不影响工件的装卸即可。根据以上分析计算确定的数据,绘制的加工示意图如图2-4所示。图2-4刀具加工示意图243机床联系尺寸图的绘制机床联系尺寸图是用来表示机床的配置型式、机床各部件之间相对位置关系和运动关系的总体布局图。它是进行主轴箱、夹具等专用部件设计的重要依据。(1)选用动力部件主要指选择型号、规格合适的滑台和动力箱。滑台的选用滑台渭台选用主要取决于驱动方式、所需进给力、进给速度、最大行程长度和加工精度等因素。A驱动方式的确定根据具体的加工要求、使用条件选用机械滑台。B确定轴向进给力由表2-2
42、知总切削力为: =9518.8N,由于滑台工作时,除了克服各主轴的轴向力外,还要克服滑台移动时产生的摩擦阻力,因而所选滑台的最大进给力应大于。C滑台进给速度的确定椐被加工件的实际要求,考虑刀具的耐用度,选滑台的进给速度为60mmmin。D确定滑台行程滑台行程除保证足够的工作行程外,还应留有前备量和后备量。前各量的作用是使动力部件有一定的向前移动的余地,以弥补机床的制造误差以及刀具磨损后能向前调整。前备量取为75mm。后备量的作用是使动力部件有一定的向后移动的余地,以方便装卸刀具,取为260mm工作行程为60mm,故滑台的总行程长度为400mm。E精度的选择根据加工要求,选用普通精度级。结合以上
43、因素,选用1HY32-IA液压滑台。其主要性能指标:台面宽320mm,长630mm,行程长400mm,滑台及滑座总高为280mm。允许最大进给力12500N,工作进给速度范围20650mmmin,快速移动速度10mmin,机械滑台支承总长940mm。滑台确定后,与之配套的支承部件选为ICC321-I侧底座。总长1180mm,高560mm。总宽520mm。滑台与侧底座之间用调整垫,这样可以保证最低主轴中心与最低被加工孔在垂直方向上等高。同时二进给及压力及电器装置取1HY32-F51,导轨防护装置取1HY32-F81,分级进给装置取1HY32-F91,立柱取1CL32,立柱侧底座取1CD321.动
44、力箱的选用动力箱主要依据主轴箱所需的电动机功率来选用。根据公式: = (210)式中:为切削用总功率,由表22计算得1.476kw。为多轴箱传动效率,加工黑色金属时0.80.9;有色金属时0.70.8,本系统加工铸刚,取0.8。所以=1.845kw动力箱的电动机功率应大于计算功率,并结合主轴要求的转速大小选择。因此,选用电动机型号为的I型动力箱,转速1430rmin,输出轴转速715rmin,动力箱与主轴箱结合面尺寸:长400mm,宽320mrn,高320mm,动力箱输出轴至箱底面高度为125mm。(2)确定装料高度H装料高度H指工件安装基面至机床底面的距离。一般在8501060mm之间选取。
45、具体尺寸取决于最低主轴中心至主轴箱底面的高度,滑台与侧底座之间的调整垫,滑台高度,侧底座高度。即H=+十 (2-11)式中:1HY32-I液压滑台=280mm,ICC321-I侧底座高度=560mm。为求,需先确定主轴箱轮廓尺寸。确定主轴箱轮廓尺寸 标准通用多轴箱厚度是一定的,卧式325mm。因此,确定多轴箱,主要是确定多轴箱的宽度B和高度H及最低主轴高度B=b+2 H=h+ 式中 b工件在宽度方向相距最远的两孔的距离 b=100mm最边缘主轴中心至箱体壁距离 70100mm 取=100mmh工件在高度方向相距最远的两孔距离 h=32mm最低轴高度通常推荐:取=100mmB100+2100=3
46、00mm H=h+h1+b1=32+100+100=232mm查组合机床设计简明手册,并综合其与动力箱的配套规格选取多轴箱体规格尺寸400320故最低主轴中心至主轴箱底面的高度可取100mm所以H=+=100+5+280+560=945mm作联系尺寸图如下:图2-5机床联系尺寸简图244生产率计算卡生产率计算卡是反映所设计机床的工作循环过程、动作时间、切削用量、生产率、负荷率等韵技术文件。通过生产率计算卡,可以分析所拟订的方案能否满足用户对生产率的要求。1.机床的理想生产率按下式计算:=29.8(件/h)2.机床实际生产率QQ=(件/h)公式中: 生产一个零件所需时间(min) =+= 0.6
47、+1.11=1.71min故Q=35(件/h)3.机床负荷率=0.85机床生产率计算卡被加工零件图号毛坯种类铸件名称R801飞锤毛坯重量材料ZG40Gr硬度HB245270工序名称钻飞锤上四个通孔工序号序号工布名称被加工零件数加工直径(mm)加工长度(mm)工作行程(mm)切削速度(m/min)每分钟转速(r/min)每转进给量(mm/r)每分钟进给量(mm/min)工时(min)机动时间辅助时间共计1装入工件20.52工件定位夹紧150.0113动力部件快进1200.064动力部件工进通孔6015896.80.107600.0960795.70.08605死档铁停留0.0176动力部件快退2
48、000.017松开工件200.0028卸下工件0.5备注本机床装卸工件时间为1min单间工时061.11,71机床实际生产率Q35(件/h)机床的理想生产率29.8(件/h)机床负荷率0.85根据机床使用经验,最适宜的机床负荷率为075090,由生产率计算卡可见计算出的机床实际生产率能够满足理想生产率要求,故方案制定的合理可行。第三章 主轴箱设计主轴箱是组合机床的重要组成部件,它是选用通用零件,按专用要求进行设计的。在本组合钻床设计过程中,是工作量最大的部件。由于在本机床上需同时加工16个孔,不仅孔多、间距小,而且孔的排列分散,采用常规方法排箱无法实现对16孔的工序集中。因此本钻床的主轴箱传动
49、系统在对被加工零件进行了深入分析计算的基础上,通过采用变位齿轮和滚针轴承,对主轴箱的结构进行了创新设计。不但将常规状况下不能完成的排箱得以实现,而且所设计的主轴箱结构紧凑,实现了需在多工序完成的钻削加工,现用同一工步完成的设计构思。为实现本机床“体积小,重量轻,结构简单,使用方便,效率高,质量好”的设计目标奠定了基础。31绘制主轴箱设计原始依据图依据第二章组合钻床总体设计绘制主轴箱设计原始依据图。其内容包括主轴箱设计的原始要求和已知条件。(1)主轴箱轮廓尺寸400320mm(2)工件轮廓尺寸及各孔位置尺寸。(3)工件与主轴箱相对位置尺寸根据这些数据,同时由总体设计,编制出表3-1。并绘出主轴箱
50、设计原始依据图3-1。表3-1各主轴外伸尺寸及切削用量轴号主轴外伸尺寸切削用量L工序转速切削速度切削用量1-2115钻通孔596.8150.1073-4115钻通孔795.7150.08图31主轴箱设计原始依据图详细尺寸如下32 主轴结构形式的选择及动力计算本组合机床主要用于钻孔,因此采用滚锥轴承主轴。1. 齿轮模数m可按下式估算:m=(3032) (3-1) 式中:m估算齿轮模数 P齿轮所传递率(kw) Z对啮合齿中的小齿轮齿数 N小齿轮的转速(r/min)除了驱动轴齿轮以及与驱动轴啮合的齿轮模数m=3,其余齿轮模数均取m=2。2.多轴箱的动力计算多轴箱的动力计算包括所需的功率和进给力两项=
51、+ (3-2)所以=2.103kw有前面2.3.2可得 =9518.8N3.3传动系统的设计和计算1.根据原始依据图(图31),画出驱动轴、主轴坐标位置。2.确定传动轴位置及齿轮齿数图32 齿轮的最小壁厚1)最小齿数的确定为保证齿轮齿根强度,应使齿根到孔壁或键槽的厚度a2m,驱动轴的直径为d=30mm,有机械零件设计手册知,如图210所示齿轮t=37mm,当m1=2时。驱动轴上最小齿轮齿数为: 2(t/m1+2+1.25)d0/m1 (3-3) =2(37/2+2+1.25)30/2 =28.5所以驱动轴齿数要大于等于29。为减小传动轴的种类,所有传动轴的直径初选20mm.3.(1)已知各主轴
52、及驱动轴的转速=597r /min=796r /min驱动轴 =715 r /min(2)各主轴总传动比=(3)设计传动轴由于主轴分布呈直线状,虽然主轴相对集中,但是与驱动轴距离太近,无法直接传动,只能靠传动轴间接传递,而且所需要的转速大小不一样,因此选择使用一根中间轴带动两根主轴实现,由于主轴数比较少,且轴对称。所以可考虑传动轴对称布置。考虑轴3,4的转速较高,因此齿轮基圆相对较小,考虑齿轮不发生根切,选取参数=17,m=2,=17。 主轴1,3上的齿轮与同一传动轴齿轮啮合,因此齿轮齿数与转速成反比,从而,选取=22,由于m均为2,所以=22。 与之啮合的齿轮选取z=30,利用几何作图法可确
53、定齿轮对应传动轴的位置,选取传动轴公称直径为。设此轴为轴5,轴对称的传动轴为轴6。那么驱动轴0轴与传动轴5轴,6轴的传动比如下:=1.59由式3-3可得驱动轴最小齿数为29,m=2,因此驱动轴上齿轮半径290轴与5轴,6轴均相距太近无法直接传动,必须添加中间传动轴7,由于对称关系,传动轴轴心同样位于对称轴上。分配传动比为=1.26取=20,则=25.3,取整=26,=1.3量得7轴与5轴,6轴的距离L=56.3且 =1.223因此求的 =26=26 =31所以 =31传动系统如下图图3-3多轴箱传动系统图验算如下:=715 r /min=715 r /min4修正各主轴转速n,切削速度v,每转
54、进给量S表3-2主轴转速n,切削速度v,每转进给量S修正表轴号转速(r /min)切削速度(m/min)每转进给量(mm /r)1-262915.80.0953-481415.30.07434多轴箱的坐标计算在拟定主轴箱传动系统时,传动轴位置已作了初步确定。为了保证齿轮副的正常啮合和加工主轴箱上传动轴支承孔的孔距精度,需要精确计算各传动轴的坐标足寸。1.加工基准坐标架的选择及确定各主轴坐标 (1)原则:坐标轴原点一般选取在定位销上,或者坐标轴横轴选取在箱底。 (2)基于原则之上,选取定位销为坐标轴原点,定位销竖直向上的方向为y轴,定位销水平方向为x轴。 (3)坐标轴和原点确定之后可以得出四根主轴的位置坐标,如下图:图3-4 主轴尺寸坐标图从上图
- 温馨提示:
1: 本站所有资源如无特殊说明,都需要本地电脑安装OFFICE2007和PDF阅读器。图纸软件为CAD,CAXA,PROE,UG,SolidWorks等.压缩文件请下载最新的WinRAR软件解压。
2: 本站的文档不包含任何第三方提供的附件图纸等,如果需要附件,请联系上传者。文件的所有权益归上传用户所有。
3.本站RAR压缩包中若带图纸,网页内容里面会有图纸预览,若没有图纸预览就没有图纸。
4. 未经权益所有人同意不得将文件中的内容挪作商业或盈利用途。
5. 装配图网仅提供信息存储空间,仅对用户上传内容的表现方式做保护处理,对用户上传分享的文档内容本身不做任何修改或编辑,并不能对任何下载内容负责。
6. 下载文件中如有侵权或不适当内容,请与我们联系,我们立即纠正。
7. 本站不保证下载资源的准确性、安全性和完整性, 同时也不承担用户因使用这些下载资源对自己和他人造成任何形式的伤害或损失。
最新文档
- 幼儿园绘本故事当我睡不着的时候课件
- 人教版小学五年级品德与社会上册《五十六个民族五十六朵花》ppt课件
- 人教版小学一年级音乐下册红眼睛绿眼睛ppt课件
- 人教版小学数学四年级上册《数学广角》ppt课件
- 幼儿园优质课件小猫的生日
- 幼儿园科学活动区创设与材料投放课件
- 人教版小学四年级音乐小螺号ppt课件
- 幼儿园科学教育的方法和途径课件
- 开盘前广告策略案课件
- 人教版小学一年级品德与生活《校园铃声》ppt课件
- 人教版小学五年级音乐吹起羌笛跳锅庄ppt课件
- 人教版小学四年级英语下册unit3_weather第三课ppt课件
- 人教版小学一年级上册数学第二单元上下前后ppt课件
- 人教版小学五年级美术第17课电脑动画ppt课件
- 幼儿园优质课件-幼儿园中班“我们都是好朋友”课件