风电叶片通用维修作业指导书(共155页)
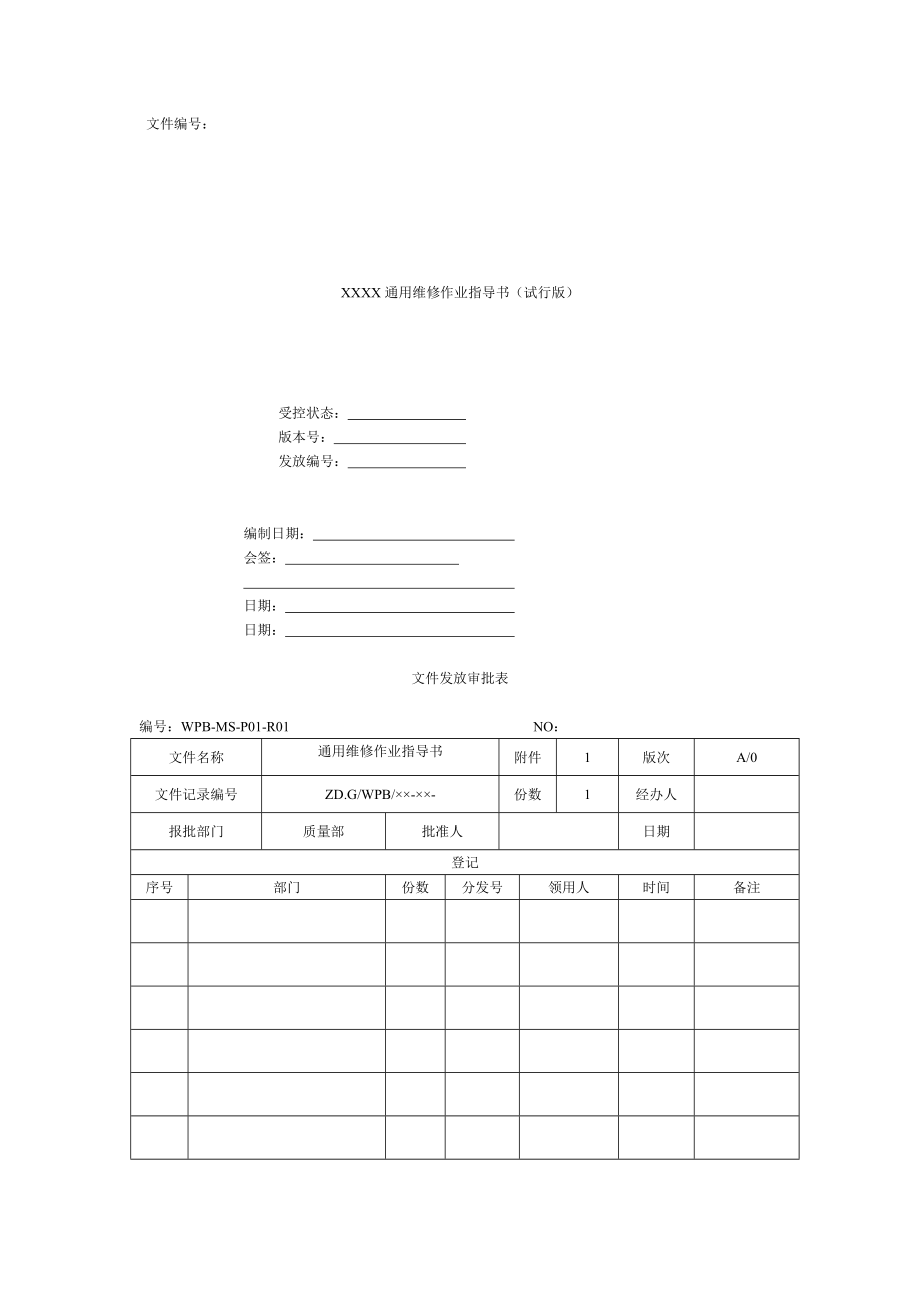


《风电叶片通用维修作业指导书(共155页)》由会员分享,可在线阅读,更多相关《风电叶片通用维修作业指导书(共155页)(155页珍藏版)》请在装配图网上搜索。
1、 文件编号:XXXX通用维修作业指导书(试行版) 受控状态: 版本号: 发放编号: 编制日期: 会签: 日期: 日期: 文件发放审批表编号:WPB-MS-P01-R01 NO:文件名称通用维修作业指导书附件1版次A/0文件记录编号ZD.G/WPB/-份数1经办人报批部门质量部批准人日期登记序号部门份数分发号领用人时间备注第一章 第一章 概述1.1适用范围XXXX风电叶片股份有限公司(以下简称“XXXX”)下辖八家制造分厂,不同工厂之间由于叶片制造水平、质量控制手段及地域环境差异等因素,导致生产的叶片质量参差不齐,维修方案呈现多样化,同时早期相关的质量受控文件维修大纲存在一定内容的缺陷,为统一公
2、司内部及售后叶片维修方案,规范叶片不合格品维修操作,特制定本维修作业指导书。本作业指导书适用于XXXX股份有限公司厂内及厂外叶片质量缺陷的维修作业指导。1.2 内容介绍通用维修作业指导书分为两部分,第一部分为通用维修工艺及典型缺陷维修方案,主要为真空灌注工艺维、手糊袋压工艺、手糊工艺、芯材(轻木、PVC)缺陷维修方案、蒙皮开天窗维修方案、粘接胶缺胶维修方案、皱褶维修方案、 预埋叶型叶根空腔维修方案、 避雷线接入量不足维修方案。第二部分为针对叶片通用接收标准的质量缺陷分别制定单独的维修方案,主要为腹板质量缺陷、主梁质量缺陷、蒙皮及粘接质量缺陷、叶片外观及零部件质量缺陷、避雷线连接质量缺陷五个章节
3、。1.3 相关说明通用维修作业指导书用来指导通用相关缺陷的维修方案,各子公司在对相关质量缺陷实施维修方案过程中需要灵活运用,不同叶片叶型、缺陷位置、操作现场环境等多种因素都会影响具体维修方案的出具及实施,需要各子公司工艺装备部及市场服务部具备技术能力的技术人员出具详细的实施维修方案,如存在困难,市场服务部及各子公司质量部可提交相关资料上报OA流程到总部质量部,由总部质量部组织相关人员进行评审后出具维修方案,详细流程见下发文件NCR处置管理办法。1.4附则1、 任何与技术文件相关而在本指导书中未涵盖的质量缺陷(如:重量、重心、扭角、预弯、Tg等)的维修方案,需要提交XXXX总部质量部NCR评审小
4、组进行维修方案评审。2、 叶片产品脱模后在厂内及出厂运输吊装过程中产生不可抗拒外力、人为等原因导致的叶片损伤质量问题,按接收标准中的相关内容进行判定,根据相应的接收标准对应的维修作业指导书进行维修方案的编制,如存在未涵盖的质量缺陷及缺陷对应的维修作业指导书,提交XXXX总部质量部NCR评审小组进行缺陷和维修方案的评审。3、任何缺陷的维修方案编制,在本指导书中无法明确参照的,需要提交XXXX总部质量部NCR评审小组进行缺陷维修方案的评审。4、备注说明中相关内容为需根据实际情况确认,在本指导书中仅给出简要的维修思路,供参考。各子公司可根据缺陷发生具体位置、严重程度等情况,编制详细的维修方案,并提交
5、XXXX总部质量部NCR评审小组进行缺陷和维修方案的评审。5、XXXX总部质量部NCR评审小组根据实际情况,负责对本维修作业指导书定期进行内容补充及修订。第二章 通用维修方案 本章的内容主要为通用维修工艺及典型缺陷维修方案,主要为真空灌注工艺、手糊袋压工艺、手糊工艺、蒙皮开天窗维修方案、挂机叶片腹板缺胶维修方案及避雷线接入量不足维修方案。(一)通用缺陷维修方案2 .1通用维修要求对于缺陷维修,要遵从以下三要素:1) 维修方案可操作性强,实施工艺有效可靠;2) 维修完成后,维修不应使原来结构产生重量及力矩偏差超出公差范围和外观改变;3) 维修完成后,叶片在使用要求寿命期限内可正常运行。2.1.1
6、缺陷维修的一般要求2.1.1.1 环境条件工厂内:在缺陷维修过程中,要求现场操作环境温度应大于16,环境湿度小于80%。维修作业选取在车间内等有条件的地方,场地要求清洁、干燥、通风良好。工厂外:在缺陷维修过程中,要求环境温度应大于16,环境湿度小于80%。若环境温度不满足要求条件,需具备与要求相接近的条件进行维修:如温度较低搭建密闭的小空间内加热达到要求;如环境温度较高时,需考虑树脂及粘接胶的适用期;禁止在雨雪天气(湿度大)、大风天气(风速8m/s)或其他较恶劣的气象条件下进行。2.1.2 主要原材料维修使用原材料跟叶片生产过程中的原材料需一致,使用的原材料要保证表面干净卫生,无油渍、灰尘、异
7、物等污染。2.1.3 操作人员要求(1)参与缺陷维修的人员,必须经培训后持证上岗,现场操作时要求相关人员需佩戴防毒口罩、橡胶手套和其他劳保用品。(2)负责缺陷维修的人员(岗位主操人)必须进行相关的工艺培训,并且考核合格后方可上岗。(3)负责缺陷维修的人员(岗位主操人)具有实际操作技能,尤其是对产品结构、材料性能、含胶量控制、增强材料的裁剪和铺放、产品厚度均匀性及影响产品质量的各种因素都要有比较全面的了解。(4)负责缺陷维修的人员(岗位主操人)要严格按照修复方案进行修复。(5)检验人员负责维修过程的记录、监控及维修质量的验证。2.1.4 缺陷打磨2.1.4.1准备打磨缺陷,便于对缺陷做进一步检查
8、。在打磨缺陷前应当制定详细的检查方案,防止检查过程造成缺陷的进一步扩大。打磨缺陷前,清理缺陷区域卫生,保持清洁、干燥。2.1.4.2 打磨错层要求对缺陷区域进行打磨时,如没有特殊说明,均按照表1要求打磨错层,且打磨区域过渡平缓,无明显凹凸。实际每层打磨的轴向长度和弦向宽度计算方法为:缺陷所处区域的织物单层厚度打磨比例。如UD1200在轴向打磨长度为:0.8mm(单层灌注厚度)100(打磨比例1:100)为80mm,弦向打磨宽度为0.8mm(单层灌注厚度)5(打磨比例1:5)为4mm。单层织物灌注和手糊厚度详见表2所示。表1 缺陷区域错层打磨要求原纤维织物类型叶片轴向方向叶片弦向方向主梁单向织物
9、(0)1:1001:5后缘梁单向织物(0)1:100双轴织物(45)1:501:50三轴织物(0/45)四轴织物(0/90/45)在打磨过程中将不合格底部打磨成规则形状(矩形或正方形)以便于玻纤布的铺设,图1所示的是UD损伤打磨示意图。表2 纤维织物单层厚度织物类型织物规格灌注单层厚度/mm手糊单层厚度/mm单轴织物UD1200及带毡0.84双轴织物Biax8080.60.8三轴织物Tri750及带毡0.6Tri973及带毡0.7Tri1215及带毡0.8四轴织物4AX20001.2备注:由于单层织物厚度受所处位置层数、纤维供应商(编制方式及纤维直径)和当地气压等因素影响,存在浮动情况。因此以
10、上表2中各织物单层厚度数据可以根据实际各分子公司积累数据适当微调。图1 UD损伤打磨示意图如果缺陷区域靠近产品边缘,如蒙皮切割边、主梁边、腹板翻边、粘接角翻边等区域,则错层打磨到边缘为止。若缺陷区域涵盖产品铺层起止位置,如叶根铺层起点、主梁起止位置、后缘梁起止位置等,则打磨到相应铺层的最远端,打磨错层将不按照表1所示,而是按照sop标准操作规程要求的各个铺层的具体位置为止。如果缺陷区域层数过多时,按照表1的打磨错层要求计算,已经超出实际产品的长度和宽度,则需按照以下打磨错层要求进行,详见表3所示:表3 缺陷区域错层打磨要求原纤维织物类型叶片长度方向叶片弦向方向主梁单向织物(0)1:1001:2
11、后缘梁单向织物(0)1:100双轴织物(45)1:201:20三轴织物(0/45)四轴织物(0/90/45)维修铺层公差,按以下公差执行:叶片长度方向20mm;叶片弦长方向20mm。2.1.4.3 清洁要求必须保证待修面表面为粗糙面,且洁净无粉尘、无异物。铺层前使用脱脂纱布蘸取丙酮或其他适用的清洗剂对待修区域表面进行擦拭,并待其完全挥发后方可进行下一步操作。2.1.5 方案的编制确认缺陷可维修后,按照打磨错层要求对缺陷区域进行打磨,根据缺陷打磨后状况,编写详细的维修方案,维修方案至少包括但不限于以下内容:(制定维修方案模板)(1)维修方案明确描述维修区域的详细尺寸;(2)所需要的主要原材料的规
12、格型号、尺寸和数量,如玻璃纤维织物规格、树脂或粘接胶牌号及配比等;(3)维修思路:维修简易流程及关键步骤等。(4)固化工艺。若过程中必须要发生方案变更时,任何的变更必须事前得到工艺装备部的认可,并如实记录变更内容。维修结果由质量管理部门最终签字确认合格后方可转序。2.1.6 固化要求 维修层应满足固化要求,维修完成后需对有Tg值要求的区域进行加热后固化,直到达到叶片设计所要求的Tg值,如下表4所示。对于厂外维修,若Tg测试不具备条件的情况下,可以采用测试硬度的方法来间接判断固化情况,其中,对于维修区域随机选择至少5个测试点,使用邵氏硬度仪测试,邵氏硬度70HD判断为合格固化。表4 Tg测试要求
13、测试项目测试方法检验标准玻璃钢材料DSCTg70粘接胶DSCTg65维修区域表面邵氏硬度仪邵氏硬度70HD2.1.7 资料记录(1)所有维修的资料应及时存档,便于追溯。(2)B1级及以上维修,每步骤完工后需要确认合格后方可进行下个步骤,必须拍照保留证据。(3)厂外维修的任何一个不合格品至少应包含勘察报告、维修报告和质量确认记录。(4)顾客或业主有要求时,经质量部对维修质量进行审核后开具维修合格证。2.2 真空灌注工艺维修方案真空灌注工艺适用于维修面积较大、层数较多、对产品外观有较大影响、关键部件出现的缺陷和影响合模粘接界面的区域等的结构维修或补偿维修。详细要求如下: 面积较大和层数较多的判断标
14、准,原则上以质量检验接收标准中B1级及以上等级中相关规定的要求。 影响产品外观,主要指对产品的外形的平整度、翼型有较大影响,若采用其他工艺无法恢复原形的情况。 关键部件,通常指的是主梁、后缘梁以及叶根2m以内区域。 影响合模粘接区域,主要指的是蒙皮主梁上、后缘粘接区。原则上,若待修缺陷满足以上其中一条要求,即可选择此工艺维修方案。2.2.1工具/设备/灌注辅材 主要用工具/设备:圆盘角磨机、毛刷、剪刀、盒尺、真空泵、吸尘设备、红外测温枪、真空表。 主要用灌注辅材:钢丝螺旋管、吸胶毡、导流网、PVC角/管、乘胶桶、PPR管、三通/阀门、脱模布、多孔膜、真空膜。2.2.2维修流程 图2 真空灌注工
15、艺维修流程2.2.3主要流程工序2.2.3.1打磨铺层(选其一)打磨掉n层,铺放n+1层相应规格玻纤织物,第n+1层与第n层的纤维织物种类相同,纤维织物面积根据不合格区域面积和错层要求制定,纤维织物放置顺序由大到小或由小到大按照错层铺设,最后一层须覆盖整个打磨面50mm,维修铺层示意图如图3和图4所示。图3 铺层示意图(由大到小顺序)图4 铺层示意图(由小到大顺序)2.2.3.2流道铺设按维修方案中具体的辅材及流道布置指导说明铺设真空胶带、脱模布、多孔膜、吸胶毡导流网,包覆至少双层真空膜。在辅材铺放时,有以下几个原则可参考:(1) 真空胶带铺设尽量远离最外侧纤维布层100mm以上。(2)多孔膜
16、原则上只铺放在有导流网铺放的区域下面,且终端超出导流网20-30mm,多孔膜搭接宽度20mm。(3)吸胶毡作为导气通道,尽量铺设在流道对立面,不与布层接触,连接到抽气口上。布层与吸胶毡通道通过吸胶毡搭条连接,吸胶毡搭条间距约在0.5-1m,且分布均匀。(4)导流网铺设,距离铺层四周约为10020mm,若为后缘梁维修时,由于宽度所限,在弦长方向距离布层终点适当缩小间距,但最小间距需30mm。(5)流道布置,在轴向方向,距离铺层起点和终点100mm,注胶口居中放置。在弦长方向原则上若需要维修区域宽度800mm,则选择从单边灌注,对立边抽气;若维修区域宽度800mm,则选择居中铺放流道,在弦长方向,
17、两边同时布置抽气通道。详见示意图4和5。(6)脱模布覆盖整个维修区域,若为了不影响邻近区域的表面干净卫生,尽量在有胶液达到的区域,均覆盖上脱模布。(7)布置真空抽气系统,抽气口原则上要均匀布置,且数量不少于2个,间距以1.5-3m为宜。可根据维修区域长度适当增加抽气口。若维修发生在距离模具边缘位置,也可以选择使用模具真空系统抽气。抽气口根据流道布置原则,单边灌注时选择对立边布置,中间灌注时,选择两边均匀布置抽气口。抽气管道连接到真空泵上,为减少抽气管道进胶返到真空泵内,几个抽气管道可以使用三通连接起来,形成单根抽气管道连接到真空泵上,详见示意图5和6。图5 单边灌注抽气系统布置图6 中间灌注抽
18、气系统布置2.2.3.3真空检验及灌注至少布置双层真空膜,抽二包一,若一二真空均无法保住真空的情况下,确认由于粘接界面的特殊情况,可采取包覆第三真空膜,增大包真空面积。将真空度抽至40mbar以下(北京康庄地区换算为-0.092MPa),以保压15分钟真空降值50mbar(0.005MPa)为合格。使用相同灌注树脂基体,树脂与固化剂配比合格,灌注至整个维修区域织物被环氧树脂完全浸润。关闭注胶管,保持真空泵一直处于抽气状态。常用树脂型号及配比详见下表5所示。表5 典型灌注树脂体系配比表厂家树脂牌号固化剂牌号质量比(树脂:固化剂)上纬SW2511-1A SW2511-1BS100:302迈图RIM
19、135RIMH137100:302RIM035CRIMH037100:282巴斯夫ER5400EC5440100:281ER5300EC5310100:202亨斯迈LY1564XB3486100:342东汽DQ200EDQ204H100:3222.2.3.4 固化灌注树脂固化条件为70以上,保温5小时;并记录固化曲线(或填写固化记录),作为维修记录的一部分。固化过程温度控制策略:(1) 全自动时间-温度记录仪,如热电偶仪等设备;(2) 要求固化过程中温度能实时显示或检测到如测温枪温度显示仪等设备;(3)固化开始时加热器设置温度不高于55,并且固化前期每隔15min记录一次维修区域表面温度,待树
20、脂放热峰结束后调整加热器设置温度至要求值,每隔30min记录一次维修区域表面温度,直至固化结束。为了保证修补区域的固化质量,需要测试树脂的Tg,要求见表6。对于厂内叶片维修区域有Tg值值要求的,若检验不合格,此叶片不得出厂;对于出厂叶片维修时,需要对维修区域取样测量Tg值,确保满足固化要求。 若条件不允许,可使用硬度仪检测固化后表面硬度。对于维修区域随机选择至少5个测试点,使用邵氏硬度仪测试,邵氏硬度70HD判断为合格固化。表6 Tg测试要求项目测试方法检验标准玻璃钢材料DSCTg70维修区域表面邵氏硬度仪邵氏硬度70HD2. 3 手糊真空袋压工艺不合格区域必须进行补偿维修时、对外形尺寸要求较
21、高、符合质量检验接受标准中B级中相关规定的要求时,原则上采用手糊真空袋压工艺。2.3.1工具/设备/辅材(1)主要用工具/设备:圆盘角磨机、毛刷、剪刀、刮板、羊毛辊/猪鬃辊、盒尺、真空泵、吸尘设备、红外测温枪、真空表、乘胶桶。(2)主要用真空袋压辅材:钢丝螺旋管、螺旋管、吸胶毡、PPR管、三通/阀门、脱模布、多孔膜、真空膜。2.3.2维修流程图7 手糊真空袋压维修工艺维修流程2.3.3主要流程工序2. 3.3.1 打磨铺层打磨掉n层,手糊铺放n+1层相应规格玻纤织物,第n+1层与第n层的纤维织物种类相同,纤维织物面积根据不合格区域面积和错层要求制定,由大到小或由小到大按照错层铺设,最后一层须覆
22、盖整个打磨面50mm,维修铺层示意图如图3和图4。2.3.3.2 手糊树脂混合1) 手糊树脂及粘接剂混合配比以使用手糊树脂迈图MGS LR135和固化剂MGS LH135为例,其质量配比为:100:352;联美手糊树脂(HPE355:/HPC355Z)配比比例同迈图要求。室温(25)下可操作时间为0.5-1小时,当胶温40,禁止使用。若采用其他供应商手糊材料,以相应的手糊树脂体系技术说明书为准。环氧树脂与胺类固化剂的配比必须严格遵守质量比要求,固化剂的过量或者不足均会导致环氧树脂体系的固化不完全,从而无法保证维修产品质量。2 )手糊树脂混合要求使用干净毛刷或搅拌棒,充分搅拌至目测颜色均匀一致,
23、搅拌时间不少于3min。3)手糊树脂混合原则1)防止胶液中混入气泡;2)配胶量采用少量多次的原则,每次配胶量要保证在树脂凝胶前用完。2.3.3.3 玻璃纤维织物糊制1)推荐使用手糊工具羊毛辊,用来浸渍树脂;猪鬃辊用于驱赶气泡;螺旋辊,硬塑料制成,用于压实铺层和排除气泡。2)首先使树脂浸润纤维束的整个表面,然后使纤维束内部的空气完全被树脂所取代。在铺第1、2层时,树脂含量要适当增多,保证第1、2层纤维织物完全浸透树脂并紧密贴合,同时有利于排出气泡。3)过程中使用成型工具将每一层纤维织物刷平、压紧,使之紧密贴合,并注意排除气泡,使纤维织物充分浸渍,不得将两层或两层以上的纤维织物同时铺放。如此重复上
24、述操作,直到达到所需的厚度为止。2.3.3.4 真空袋压手糊完毕后在玻纤布上贴一层脱模布,并在维修区域四周提前贴好密封胶带用真空膜密封维修区域,布置好抽真空辅材及抽真空系统,保持真空度低于-0.080MPa以下,且真空泵一直处于抽气状态,直至固化完成。在辅材铺放时,有以下几个原则可参考:(1)真空胶带铺设尽量远离最外侧纤维布层100mm以上。(2)吸胶毡作为导气通道,围绕铺设在维修区域一周,不与布层接触,连接到抽气口上。布层与吸胶毡通道通过吸胶毡搭条连接,吸胶毡搭条间距约在0.5-1m,且分布均匀。(3)脱模布覆盖整个维修区域,若为了不影响邻近区域的表面干净卫生,尽量在有胶液达到的区域,均覆盖
25、上脱模布。(4)为保证维修区域手糊含胶量,尽量不要铺设导流网,可选择在脱模布上铺设一层废旧真空膜,然后在废旧真空膜上放一条“Z”字形吸胶毡导气,如图8所示。(5)布置真空抽气系统,抽气口原则上要均匀布置,且数量不少于2个。可根据维修长度适当增加抽气口。若维修发生在距离模具边缘位置,也可以选择使用模具真空系统抽气。抽气管道连接到真空泵上,为减少抽气管道进胶返到真空泵内,几个抽气管道可以使用三通连接起来,形成单根抽气管道连接到真空泵上,详见示意图8。图8 中间灌注抽气系统布置2.3.3.5 固化 手糊树脂固化条件为60以上,保温3小时。固化过程温度控制策略:(1)全自动时间-温度记录仪,如热电偶仪
26、等设备;(2)要求固化过程中温度能实时显示或检测到如测温枪温度显示仪等设备;(3)固化开始时加热器设置温度不高于55,并且固化前期每隔15min记录一次维修区域表面温度,待树脂放热峰结束后调整加热器设置温度至要求值,每隔30min记录一次维修区域表面温度,直至固化结束。为了保证修补区域的固化质量,需要测试树脂的Tg,取样检测,要求玻璃钢Tg60。对于厂内叶片维修区域有Tg值值要求的,若检验不合格,此叶片不得出厂。对于出厂叶片维修时,需要对维修区域取样测量Tg值,确保满足固化要求。 若条件不允许,可使用硬度仪检测固化后表面硬度。对于维修区域随机选择至少5个测试点,使用邵氏硬度仪测试,邵氏硬度70
27、HD判断为合格固化。2.4 手糊工艺维修方案符合质量检验接受标准中C1级中相关规定的要求、无特殊要求、不影响产品结构、外形尺寸要求不高的、原成型方法采用手糊成型的及真空灌注和手糊真空袋压要求之外或由于特殊条件限制无法实施前两者成型工艺的等,原则上采用手糊工艺。2.4.1工具/设备/辅材(1)主要用工具/设备:圆盘角磨机、毛刷、剪刀、刮板、羊毛辊/猪鬃辊、盒尺、吸尘设备、红外测温枪、胶盆。(2)主要用辅材:脱模布。2.4.2维修流程图9 手糊维修工艺维修流程2.4.3主要流程工序2.4.3.1打磨铺层打磨掉n层,手糊铺放n+1层相应规格玻纤布,第n+1层与第n层的纤维布种类相同,纤维布面积根据不
28、合格区域面积和错层要求制定,由大到小按照错层铺设,最后一层须覆盖整个打磨面50mm,维修铺层示意图如图2。2.4.3.2 手糊树脂混合(1)手糊树脂及粘接剂混合配比以使用手糊树脂迈图MGS LR135和固化剂MGS LH135为例,其配比为:100:352(质量比);联美手糊树脂(HPE355:/HPC355Z)配比比例同迈图要求。室温(25)下可操作时间为0.5-1小时,当胶温40,禁止使用。若采用其他供应商手糊材料,以相应的手糊树脂体系技术说明书为准。树脂与固化剂的混合必须严格遵守,固化剂的过量或者不足均会导致环氧树脂体系的固化不完全,影响维修区域产品质量。(2)手糊树脂混合要求使用干净毛
29、刷或搅拌棒,充分搅拌至目测颜色均匀一致,搅拌时间不少于3min。(3)手糊树脂混合原则1)防止胶液中混入气泡;2)配胶量采用少量多次的原则,每次配胶量要保证在树脂凝胶前用完。2.4.3.3 玻璃纤维织物糊制(1)推荐使用手糊工具:羊毛辊,用来浸渍树脂;猪鬃辊用于驱赶气泡;螺旋辊,硬塑料制成,用于压实铺层和排除气泡。(2)首先使树脂浸润纤维束的整个表面,然后使纤维束内部的空气完全被树脂所取代。在铺第1、2层时,树脂含量要适当增多,保证第1、2层纤维织物完全浸透树脂并紧密贴合,同时有利于排出气泡。(3)过程中使用成型工具将每一层纤维织物刷平、压紧,使之紧密贴合,并注意排除气泡,使纤维织物充分浸渍,
30、不得将两层或两层以上的纤维织物同时铺放。如此重复上述操作,直到达到所需的厚度为止。2.4.3.4 特殊工艺要求(1)由于织物纤维方向不同,其强度也有不同。所用玻璃纤维织物的铺层方向即铺层方式应按工艺要求进行,糊制前先用刷子或毛辊将整个打磨区域薄薄涂一层树脂胶液,而后再进行铺设。(2)同一铺层纤维尽可能连续,忌随意切断或拼接。若应设计或工艺要求,选择切断时搭接宽度50-70mm。同时,每层搭接位置应尽可能错开。(3)糊制厚度在8mm以下时可一次成型,而当糊制厚度大于8mm时,应分多次成型,否则会因固化散热不良导致产品发焦、变色,影响性能。(4)若手糊的几何尺寸比较复杂或较长时,某些地方增强材料铺
31、放不平整,气泡不易排除时,可用剪刀将该处剪开,并使之贴平,应当注意每层剪开的部位应错开,以免造成强度损失。(5)手糊完毕后在玻纤布上贴一层脱模布,手糊玻璃钢的含胶量为45%-55%。2.4.3.4 手糊固化要求手糊树脂固化条件为60,保温3小时;并记录固化曲线(或填写固化记录),作为维修记录的一部分。固化过程温度控制策略:a、全自动时间-温度记录仪,如热电偶仪等设备;b、要求固化过程中温度能实时显示或检测到如测温枪温度显示仪等设备;c、固化开始时加热器设置温度不高于55,并且固化前期每隔15min记录一次维修区域表面温度,待树脂放热峰结束后调整加热器设置温度至要求值,每隔30min记录一次维修
32、区域表面温度,直至固化结束。对于有Tg值要求的维修,固化完成后,取样检测,要求玻璃钢Tg60。对于厂内叶片维修区域Tg值不合格,此叶片不得出厂。对于出厂叶片维修时,需要对维修区域取样测量Tg值,确保满足固化要求。若条件不允许,可使用硬度仪检测固化后表面硬度。对于维修区域随机选择至少5个测试点,使用邵氏硬度仪测试,邵氏硬度70HD判断为合格固化。2.4.4 手糊检验手糊完成后,布层平顺、贴实紧密,空腔、毛刺、气泡缺陷按照相关检验标准判定。纤维织物浸润完全,无浸渍不良、发白干纱等缺陷。(二) 典型缺陷维修方案2.5 蒙皮开窗维修方案2.5.1适用范围1、腹板粘接缺陷此维修方案仅适用于指导叶片长度方
33、向从叶尖至叶根1/3长度区域内腹板胶层空腔、扛胶、粘接宽度不足、胶层超厚等各种形式的腹板粘接缺陷维修。2、避雷缺陷此维修方案针对避雷接闪(铝叶尖、叶尖接闪器、无法从内部维修的叶中接闪器)电阻值不合格的缺陷维修(未导通或接触不良)。3、损伤缺陷此维修方案适用于指导蒙皮凹陷、粘接后腹板鼓包、叶尖位置蒙皮损伤的缺陷维修。2.5.2 维修流程1、腹板粘接缺陷维修流程缺陷区域附近前缘/后缘蒙皮打磨剖开缺陷区域粘接面、前缘/后缘粘接区、缺胶区域腹板外侧打磨糙面并清理卫生缺陷区域填胶腹板外侧手糊补强 糊制玻璃钢板内衬前缘粘接角/后缘修复前缘/后缘剖开区蒙皮修复加热固化维修结果确认。2、避雷缺陷维修流程缺陷区
34、域所处迎风面蒙皮打磨剖开检修避雷接闪系统电阻测试剖开区域内/外侧打磨糙面并清理卫生糊制玻璃钢板内衬剖开区蒙皮修复加热固化维修结果确认。3、损伤缺陷维修流程缺陷区域打磨剖开缺陷区域内/外侧打磨糙面并清理卫生糊制玻璃钢板内衬剖开区缺陷修复加热固化维修结果确认。2.5.3 维修工序1、腹板粘接缺陷维修工序(1)缺陷区域附近前缘/后缘蒙皮打磨剖开(以PS面腹板前缘缺胶为例)将缺陷区域前缘侧打磨剖开,剖开区域为迎风面主梁前缘梁边向前缘侧;剖开长度为缺陷起点和终点两侧各缩进150-200mm;剖开宽度为前缘梁边向前缘侧预留20-30mm后向前缘打磨100mm;剖开区域上限需小于100mm宽,视可操作适当减
35、小剖开宽度,若剖至合模缝则打磨至合模缝为止,打磨切开示意图如下图9所示。图9 切口示意图(2)清理胶渣若为哑铃形缺胶(即为在腹板粘接区宽度上,中间区域有胶,两端缺胶)或腹板内侧开放式缺胶或封闭性缺胶,需要将缺胶区域的粘接胶清理干净。具体操作方法为,使用封钢刀片将已有的粘接胶凿掉,过程中可以用小锤轻轻敲击(若操作空间能够满足角磨机使用,则使用小角磨机将胶层打磨开)。当在中间某一区域打开整个宽度上的粘接胶后,可以采取将刀片从内测向外敲击粘接胶,以防粘接胶落入到腹板内侧,无法清理。使用此方法完成所有缺胶处粘接胶清理。若为腹板外侧缺胶,则直接转入下道工序。(3)打磨粗糙面及倒角粘接胶清理后,使用砂纸对
36、缺陷区域粘接面及对应位置腹板外侧、剖口内蒙皮四周3-50mm区域进行整体糙面处理,处理时要保证无胶渣、无光滑面;同时在剖开轴向和弦向两端按照1:50比例,打磨倒角。(4)清理卫生将打磨区域粉尘清理干净,并使用脱脂纱布蘸取稀料或丙酮处理打磨面待其挥发后完成清理。(5)腹板缺胶区域补胶使用刮板将称量好比例的粘接胶树脂和快固化剂混合均匀,判定颜色一致为合格,涂抹在整个腹板缺胶区域的翻边上,并使用夹压装置在维修段进行加压。(6)收胶在加压后,对挤出腹板外侧的粘接胶及时收胶,完成后使用4层双轴纤维对腹板外侧进行手糊补强处理,补强时布层错茬10mm,由小到大,迎风面主梁上粘接宽度不小于30mm。(7)腹板
37、粘接胶固化对此段粘接胶使用热风机或电加热毯进行加热,确保粘接胶固化后,方可撤除加压装置。加热温度为70以上,保温5小时为固化完成。取样测量粘接胶TG合格后方可进行下步操作。(8)前缘内衬固定前缘使用预制随形内衬做垫板,内衬四周与打开区域四周保证有20mm的粘接宽度,在其上四周刮胶与打开区域四周内部粘接,使用细铁丝或纤维纱线打孔并穿孔拉紧固定,保证内衬与蒙皮紧密粘接,待至少半个小时以上,粘接胶固化完成,方可进行下步操作。(9)蒙皮及粘接角手糊/真空灌注修复以下为手糊修复方案:参考下方示意图10。其中1号为预制内衬层(2层双轴纤维);2号及3号为手糊粘接角和手糊蒙皮;2、3、手糊粘接角和蒙皮1、预
38、制内衬层图10 开口区域修铺层复示意图在内衬上手糊5层808g/双轴织物和3层1215 g/三轴织物(其中第3层为补强布),在轴向和弦向两端分别与打磨倒角搭接,搭接宽度50mm,按原布层顺序铺放纤维。详细的手糊袋压工艺方案,参考2.3。以下为真空灌注修复方案:刷手糊树脂:在预制玻璃钢板上刷一层手糊树脂,覆盖一层脱模布,直至固化以后将脱模布撕除。铺层灌注固化:按照原布层顺序铺放n+1层布,依次铺放粘角-内蒙皮-外蒙皮布层,第n+1层与第n层玻纤布类型相同,按照由小到大或由大到小顺序进行错层铺放,最后一层需覆盖整个打磨面50mm。在布层上方依次脱模布、多孔膜、导流网,布置流道和真空系统。详细的真空
39、灌注工艺维修方案参考2.2。若涉及到芯材区域,需在铺层的原始位置填补同规格芯材。整个维修过程不可伤及主梁。2、避雷缺陷维修工序(1)开窗将缺陷区域对应的内外蒙皮和芯材切开/在迎风面距离避雷点叶根位置100mm处切开,S=300150mm,切割过程不可伤及主梁。(2)避雷系统检修检查避雷系统各个组件连接是否存在异常,并维修异常情况,如拧紧螺栓或者重新更换线鼻子连接,或者清理避雷螺栓孔和避雷线及线鼻子连接处胶渣,消除无接触或接触不良。(3)电阻测试连接完毕以后,对该点位置电阻及整个避雷系统电阻进行测试,合格后则进行下一步。(4)糊制内衬玻璃钢板在同型号其他叶片的相同位置手糊二层808g/m2双轴布
40、,四周比开窗区域宽出50mm,要求布层上下都铺放脱模布,固化以后,在距离左右两端80mm的中心线处打2个孔,用纤维纱串联起来。(5)倒角打磨在开窗四周外蒙皮按照打磨原则长度和弦长方向倒角1:50的比例打磨,清理干净;在开窗四周内蒙皮50mm区域内使用砂纸打磨粗糙,并清理干净表面卫生。(6)粘接预制玻璃钢板在天窗四周50mm的内蒙皮刮一层快速粘接胶,将预制玻璃钢板塞进蒙皮内侧,确保预制玻璃钢板的四周都与内蒙皮接触不少于30mm,拉紧纤维纱,使预制玻璃钢板与内蒙皮紧贴,直至粘接胶完全固化。(7)刷手糊树脂在预制玻璃钢板上刷一层手糊树脂,覆盖一层脱模布,直至固化以后将脱模布撕除。(8)铺层灌注固化按
41、照原布层顺序铺放n+1层布,依次铺放内蒙皮-填补同规格芯材-外蒙皮布层,第n+1层与第n层玻纤布类型相同,按照由小到大或由大到小顺序进行错层铺放,最后一层需覆盖整个打磨面50mm。在布层上方依次脱模布、多孔膜、导流网,布置流道和真空系统,见附图所示:将真空度抽至40mbar以下(康庄地区换算为-0.092Mpa),以保压15分钟真空降值40mbar(0.004MPa)为合格。灌注系统图见附图所示:70固化5小时,固化完成后,要求玻璃钢Tg70。详细的真空灌注工艺维修方案参考2.2。3、损伤缺陷维修工序(1)开窗将缺陷区域对应的内外蒙皮和芯材切开。(2)糊制内衬玻璃钢板在同型号其他叶片的相同位置
42、手糊二层808g/m2双轴布,四周比开窗区域宽出50mm,要求布层上下都铺放脱模布,固化以后,在距离左右两端80mm的中心线处打2个孔,用纤维纱串联起来。(3)倒角打磨在开窗四周外蒙皮按照打磨原则长度和弦长方向倒角1:50的比例打磨,清理干净;在开窗四周内蒙皮50mm区域内使用砂纸打磨粗糙,并清理干净表面卫生。(4)粘接预制玻璃钢板在天窗四周50mm的内蒙皮刮一层快速粘接胶,将预制玻璃钢板塞进蒙皮内侧,确保预制玻璃钢板的四周都与内蒙皮接触不少于30mm,拉紧纤维纱,使预制玻璃钢板与内蒙皮紧贴,直至粘接胶完全固化。(5)刷手糊树脂在预制玻璃钢板上刷一层手糊树脂,覆盖一层脱模布,直至固化以后将脱模
43、布撕除。(6)铺层灌注固化按照原布层顺序铺放n+1层布,依次铺放内蒙皮-填补同规格芯材-外蒙皮布层,第n+1层与第n层玻纤布类型相同,按照由小到大或由大到小顺序进行错层铺放,最后一层需覆盖整个打磨面50mm。在布层上方依次脱模布、多孔膜、导流网,布置流道和真空系统,见附图所示:将真空度抽至40mbar以下(康庄地区换算为-0.092Mpa),以保压15分钟真空降值40mbar(0.004MPa)为合格。灌注系统图见附图所示,70固化5小时,固化完成后,要求玻璃钢Tg70。详细的真空灌注工艺维修方案参考2.2。2.5.4备注说明(1)腹板扛胶的维修,在扛胶区域开窗后,具体的维修方案同粘接过程中的
44、扛胶维修方案。(2)此蒙皮开窗维修方案也可适用于指导其他缺陷的维修,如前后缘重大粘接缺陷等。(3)原则上,使用此方案,均使用真空灌注维修方案进行蒙皮修复,若厂外维修满足不了,需经过评审后方可采用手糊维修方案进行蒙皮修复。(4)维修时需检验人员全程跟踪,并对修复过程中蒙皮剖口、糙面处理、界面卫生、修复关键尺寸、真空检验、固化温度及时间、TG值等进行确认及数据记录(图片记录)。2.6 挂机叶片后缘UD贯穿性褶皱维修方案2.6.1适用范围此方案针对挂机叶片发现的后缘UD贯穿性褶皱缺陷的维修。2.6.2 维修流程褶皱区域打磨平整及其他区域打磨粗糙表面清理卫生纤维织物准备手糊补强 抽真空袋压加热固化硬度
45、测试维修结果确认。2. 6.3 备注说明(1)褶皱打磨及其他区域打磨粗糙使用角磨机将缺陷区域的玻璃钢褶皱进行打磨,打磨后要求玻璃钢表面平顺过渡。同时,将褶皱缺陷区域周围的玻璃钢表面打磨粗糙,后缘UD的打磨的边界尺寸满足UD布层在长度方向按照1:100的比例计算,弦长方向打磨按照1:2的比例计算,若褶皱跨过后缘UD整个铺层宽度,则弦长方向错层按照原sop文件要求执行。UD上蒙皮铺层按照(2)打磨表面清理使用蘸有丙酮或其他可替代的清洗剂溶液的脱脂纱布对打磨的表面进行清理,除去表面粉尘及杂质。(3)纤维织物准备根据褶皱所在区域的铺层结构,准备包括此区域的后缘UD铺层(m层)和UD上蒙皮铺层(n层),
46、玻纤织物同原区域所在的玻纤织物规格。(4)手糊浸润对准备好的纤维织物进行手糊浸润,按照从小到大顺序进行铺设,铺设过程中每层纤维布以褶皱线为中心,向叶尖和叶根方向居中铺设。糊制过程中控制好树脂用量及及时赶除布层中气泡。(5)抽真空袋压及加热固化在布层上方依次铺放脱模布、吸胶毡、废旧真空膜等辅材,布置真空抽气系统,抽真空。使用加热毯或其他加热设备对手糊区域进行加热固化,详细要求请参考2.3手糊袋压维修工艺方案。(6)固化度使用巴士硬度计进行测量,巴士硬度50Hba为合格,测量方法为不同区域选择测试至少3个点以上。2.7 厂外及挂机叶片腹板缺胶的胶层过厚维修方案2.7.1 适用范围主要针对厂外及挂机
47、叶片腹板缺胶的胶层过厚出具的维修方案。2.7.2 维修流程维修方案主要为两种缺陷的维修方案,如下:(1)腹板粘接翻边胶层过厚维修方案:针对厂外及挂机叶片腹板粘接翻边胶层过厚的缺胶维修方案,腹板翻边与主梁的粘接胶层超过15mm及以上厚度,同时存在间断性缺胶。(2)腹板粘接芯材PVC胶层过厚维修方案:针对厂外及挂机叶片腹板粘接芯材PVC胶层过厚的缺胶维修方案,腹板粘接芯材PNV与主梁的粘接胶层超过15mm及以上厚度,同时存在间断性缺胶。维修流程:1、 腹板粘接翻边胶层过厚:打磨玻璃钢垫板制备放置玻璃钢垫板翻边手糊补强加热固化。2、 腹板粘接芯材PVC胶层:粘接胶清理芯材PVC板制备放置芯材PVC板
48、腹板外侧手糊补强加热固化。2.7.3 维修工序1、 腹板粘接翻边胶层过厚(1)打磨:将缺胶位置的翻边及粘接胶打磨去掉,按照打磨要求打磨倒角,清理干净。(2)玻璃钢垫板制备:根据胶层厚度制备一定厚度的玻璃钢垫板,玻璃钢垫板厚度小于胶层厚度12mm,制备工艺为手糊环氧玻璃钢工艺。(3)放置玻璃钢垫板:将制备好的玻璃钢垫板放置到打磨好的胶层位置中,其余空腔位置用粘接胶填实。(4)翻边手糊补强:根据产品翻边厚度层数进行手糊补强,最后在外侧再补强两层手糊织物。(5)加热固化:采用加热设备(热风枪、石英灯)对维修产品区域进行加热固化,60固化3小时,固化后测试产品硬度满足要求。2、 腹板粘接芯材PVC胶层
49、过厚(1)粘接胶清理:将芯材PVC缺胶位置的粘接胶清理干净,注意将粉尘清理及包覆好;(2)芯材PVC板制备:根据胶层厚度制备一定厚度的芯材PVC板,芯材PVC板厚度小于胶层厚度12mm,制备工艺为芯材PVC外侧包覆两层纤维织物;(3)放置芯材PVC板:将制备好的芯材PVC板放置到清理好的胶层位置中,其余空腔位置用粘接胶填实;(4)腹板外侧手糊补强:在腹板外侧进行手糊补强3层织物,3层织物的长度与缺胶位置一致,宽度为100mm、120mm、140mm,铺设时做好织物的错层,铺层是从里到外宽度分别为100mm、120mm、140mm;(5)加热固化:采用加热设备(热风枪、石英灯)对维修产品区域进行
50、加热固化,60固化3小时,固化后测试产品硬度满足要求。2.7.4 备注说明 上述的维修方案只针对在腹板粘接缺陷位置人员可以到达的修复情况,如叶片已挂机,同时腹板粘接缺陷位置人员无法到达的质量问题情况,需要将上报总部质量部NCR小组进行组织评审,根据评审结果做出叶片更换或记录在案的处理方案。第三章 腹板质量缺陷的维修方案3.1 腹板芯材间隙、台阶的维修方案3.1.1 适用范围此维修方案针对腹板PVC板材间隙、缺失或台阶缺陷的维修。3.1.2 维修流程序号缺陷类型不可接受情况描述等级维修方案1芯材间隙、缺失、台阶1、3mm芯材间隙5mm;2、芯材间隙、缺失(宽度)5mm且长度1000mm。C1手糊
51、补强2层纤维织物(织物类型与腹板织物材料一致)维修。1、芯材间隙、缺失(宽度)5mm且长度1000mm。2、芯材台阶:台阶5mm。B21、芯材间隙、缺失(宽度)5mm且长度1000mm:打磨填补芯材手糊袋压。2、芯材台阶(台阶5mm):打磨平整手糊n+1层纤维织物。1、C1级维修流程缺陷区域表面打磨粗糙缺陷区域手糊补强固化。2、B2级维修流程(1)芯材间隙、缺失(宽度)5mm且长度1000mm缺陷区域打磨及富树脂层清理缺陷区域芯材填补芯材上方玻璃钢n+1层手糊抽真空袋压维修加热固化。(2)芯材台阶:台阶5mm缺陷区域台阶打磨及富树脂层清理芯材上方玻璃钢n+1层手糊加热固化。3.1.3 维修工序
52、1、C1级的维修工序 (1)打磨清理将缺陷区域的外表面打磨粗糙,长度方向和弦长方向分别超出缺陷区域50-80mm,如下图11,打磨完成后,须保证待修面表面为粗糙面,且洁净无粉尘、无异物。图11 打磨示意图(2)手糊补强在打磨的缺陷区域手糊铺放2层与缺陷区域所用相同规格的纤维布,轴向弦向5cm每层错层。详细手糊作业要求可参见2.4手糊工艺维修。(3)固化使用加热毯或其他加热方式对维修区域进行加热,手糊树脂固化条件为60,保温3小时;对于有Tg值要求的维修,固化完成后,取样检测,要求玻璃钢Tg60。2、 B2级的维修工序(芯材间隙、缺失(宽度)5mm且长度1000mm)(1)打磨清理将缺陷区域芯材
53、上方的玻璃钢层(n层)打磨,按照布层的打磨要求,在长度方向和弦长方向分别按照1:50的比例打磨,局部过窄区域可按照1:20比例进行打磨。打磨完成后,须保证待修面表面为粗糙面,且洁净无粉尘、无异物。(2)富树脂层清理将间隙或缺失芯材所在区域的富树脂层打磨清理干净,若间隙或缺失芯材所在区域为空腔,则需要将空腔区域表面打磨粗糙。(3)缺陷区域芯材填补准备与间隙或缺失所处的相同规格的芯材(材质、厚度、宽度)填补到间隙或缺失区域,填补后芯材间隙2mm。(4)缺陷区芯材上方玻璃钢层修复在芯材上方按照原布层顺序铺放n+1层布,第n+1层与第n层玻纤布类型相同, 按照由小到大或由大到小顺序进行错层铺放,最后一
54、层在宽度和弦长方向分别超出已铺放布层外侧各50mm。(5)手糊袋压维修手糊完毕后采取袋压,详细要求请参考2.3手糊袋压维修工艺方案。(6)加热固化 使用加热毯或其他加热方式对维修区域进行加热,保证维修区域完全固化,固化条件为60,保温3小时;对于有Tg值要求的维修,固化完成后,取样检测,要求玻璃钢Tg60。3、 B2级的维修工序(芯材台阶:台阶5mm)(1)打磨清理将缺陷区台阶打磨平整,在长度方向和弦长方向分别按照1:50的比例打磨,局部过窄区域可按照1:20比例进行打磨。打磨完成后,须保证待修面表面为粗糙面,且洁净无粉尘、无异物。(2)台阶边缘富树脂层清理将台阶区域的富树脂层打磨清理干净,若
55、台阶为腹板蒙皮表面台阶,则直接将富树脂打磨干净即可,若为腹板翻边处台阶,则将富树脂打磨干净后,需要填补相应高度芯材。(3)缺陷区域芯材填补在台阶打磨干净后,准备与间隙或缺失所处的相同规格的芯材(材质、厚度、宽度)填补到间隙或缺失区域,填补后芯材间隙2mm。(4)缺陷区上方玻璃钢层修复在维修后台阶上方按照原布层顺序铺放n+1层布,第n+1层与第n层玻纤布类型相同, 按照由小到大或由大到小顺序进行错层铺放,最后一层在宽度和弦长方向分别超出已铺放布层外侧各50mm。(5)手糊袋压维修手糊完毕后采取袋压,详细要求请参考2.3手糊袋压维修工艺方案。(6)加热固化 使用加热毯或其他加热方式对维修区域进行加
56、热,保证维修区域完全固化,固化条件为60,保温3小时;对于有Tg值要求的维修,固化完成后,取样检测,要求玻璃钢Tg60。3.2 腹板损伤的维修方案3.2.1 适用范围此维修方案针对腹板因遭受撞击、剐蹭等外力所形成的硬性损伤缺陷的维修。3.2.2 维修流程序号缺陷类型不可接受情况描述等级维修方案1腹板损伤损伤区域300*300mm,伤及玻璃钢纤维结构且未伤及芯材本体结构。C11、损伤区域300*300mm,伤及玻璃钢纤维结构且未伤及芯材本体结构打磨损伤玻璃钢并手糊n+1层玻纤补强维修工艺。2损伤区域300*300mm或伤及芯材本体结构。B21、损伤区域300*300mm未伤及芯材本体:打磨损伤玻
57、璃钢,手糊袋压维修工艺。2、伤及芯材本体:打磨损伤玻璃钢,修补芯材再手糊袋压维修工艺。维修流程:1、C1级维修流程缺陷区域表面打磨缺陷区域手糊补强固化。2、B2级维修流程(1)损伤区域300*300mm,伤及玻璃钢纤维结构且未伤及芯材本体结构损伤区域打磨及清理缺陷区玻璃钢层修复加热固化。(2)伤及芯材本体。损伤区域打磨及清理缺陷区域芯材填补缺陷区芯材上方玻璃钢层手糊袋压加热固化。3.2.3 维修工序1、C1级维修工序(1)打磨清理将缺陷区域打磨,长度方向和弦长方向分别超出缺陷区域50-80mm。打磨完成后,须保证待修面表面为粗糙面,且洁净无粉尘、无异物。(2)手糊补强在打磨的缺陷区域手糊铺放n
58、+1层与缺陷区域所用相同规格的纤维布,铺设要求按照从大到小或者从小到大的顺序,按照轴向1:50比例错层(局部过窄区域1:20)进行手糊铺设,最后一层在宽度和弦长方向分别超出已铺放布层外侧各50mm,详细手糊作业要求可参见2.4手糊工艺维修。(3)固化使用加热毯或其他加热方式对维修区域进行加热,保证维修区域完全固化,手糊树脂固化条件为60,保温3小时;对于有Tg值要求的维修,固化完成后,取样检测,要求玻璃钢Tg60。固化要求参见2.4.3.4手糊固化工艺要求。2、 B2级维修工序(损伤区域300*300mm,伤及玻璃钢纤维结构且未伤及芯材本体结构)(1)打磨清理将缺陷区域的玻璃钢层(n层)打磨,
59、按照布层的打磨要求,在长度方向和弦长方向分别按照1:50的比例打磨(局部维修区域过窄可按照1:20比例打磨),清理干净打磨粉尘,须保证待修面表面为粗糙面,且洁净无粉尘、无异物。(2)缺陷区芯材上方玻璃钢层修复在芯材上方按照原布层顺序铺放n+1层布,第n+1层与第n层玻纤布类型相同, 按照由小到大或由大到小顺序进行错层铺放,最后一层在宽度和弦长方向分别超出已铺放布层外侧各50mm,。(3)手糊袋压维修手糊详细要求请参考2.3手糊袋压维修工艺方案。(4)加热固化使用加热毯或其他加热方式对维修区域进行加热,保证维修区域完全固化。手糊树脂固化条件为60,保温3小时;对于有Tg值要求的维修,固化完成后,取样检测,要求玻璃钢Tg60。3、 B2级维修工序(伤及芯材本体)(1)打磨清理将缺陷区域芯材上方的玻璃钢层(n层)打磨,按照布层的打磨要求,在长度方向和弦长方向分别按照1:50的比例打磨(局部维修区域过窄可按照1:20比例打磨),清理干净打磨粉尘,须保证待修面表面为粗糙面,且洁净无粉尘、无异物。(2)损伤芯材清理将损伤区域芯材,用工器具掏出或者将损伤区域打磨平整。打磨完成后,须保证待修面表面为粗糙面,且洁净无粉尘、无异物。(3)缺陷区域芯材填补准备与间隙或缺失所处的相同规格的芯材(材质、厚度、宽度)填补到间隙或缺失区域,填补后芯材间隙2mm。(
- 温馨提示:
1: 本站所有资源如无特殊说明,都需要本地电脑安装OFFICE2007和PDF阅读器。图纸软件为CAD,CAXA,PROE,UG,SolidWorks等.压缩文件请下载最新的WinRAR软件解压。
2: 本站的文档不包含任何第三方提供的附件图纸等,如果需要附件,请联系上传者。文件的所有权益归上传用户所有。
3.本站RAR压缩包中若带图纸,网页内容里面会有图纸预览,若没有图纸预览就没有图纸。
4. 未经权益所有人同意不得将文件中的内容挪作商业或盈利用途。
5. 装配图网仅提供信息存储空间,仅对用户上传内容的表现方式做保护处理,对用户上传分享的文档内容本身不做任何修改或编辑,并不能对任何下载内容负责。
6. 下载文件中如有侵权或不适当内容,请与我们联系,我们立即纠正。
7. 本站不保证下载资源的准确性、安全性和完整性, 同时也不承担用户因使用这些下载资源对自己和他人造成任何形式的伤害或损失。