摩擦学原理第8章润滑设计
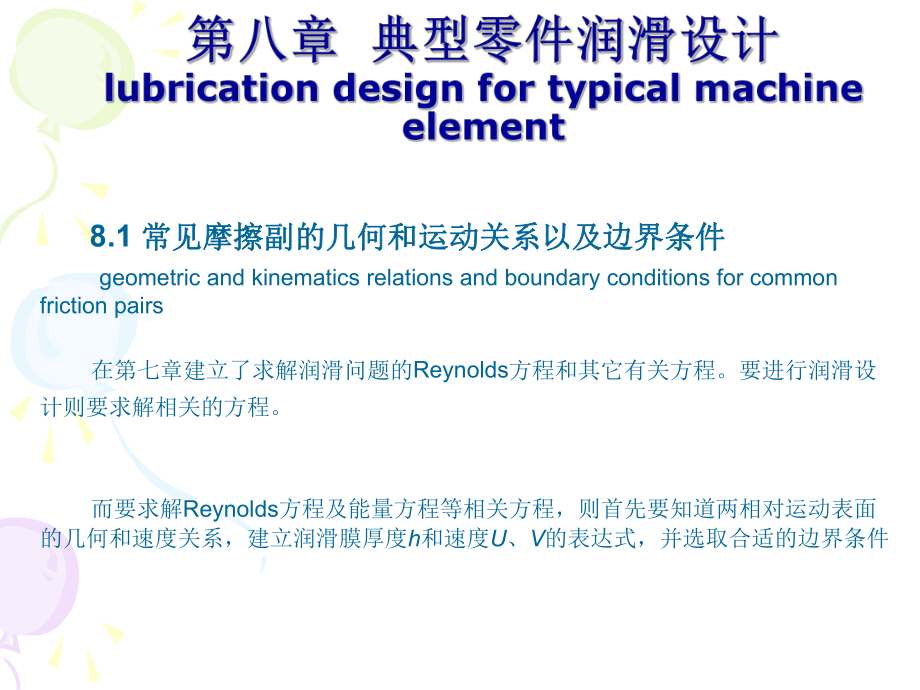


《摩擦学原理第8章润滑设计》由会员分享,可在线阅读,更多相关《摩擦学原理第8章润滑设计(130页珍藏版)》请在装配图网上搜索。
1、 8.1 常见摩擦副的几何和运动关系以及边界条件常见摩擦副的几何和运动关系以及边界条件 geometric and kinematics relations and boundary conditions for common friction pairs 在第七章建立了求解润滑问题的Reynolds方程和其它有关方程。要进行润滑设计则要求解相关的方程。而要求解Reynolds方程及能量方程等相关方程,则首先要知道两相对运动表面的几何和速度关系,建立润滑膜厚度h和速度U、V的表达式,并选取合适的边界条件 8.1.1润滑膜厚度表达式润滑膜厚度表达式 expression of film thic
2、kness 1圆轴承圆轴承 circular bearing 任意两圆弧表面间的膜厚表达式。图8.1为某一工作状态下的圆轴承,轴承半径为R,轴颈半径为r,半径间隙为C=R-r,e为偏心距,h为任一点处的膜厚。图8.1圆轴承几何关系示意图在图8.1的OO M中222()-2()cosRerhe rh(8.1)将式(8.1)两端分别减去22cose并整理可得:222(-sin)-coshRere(8.2)采用级数展开,则有:角起始线为轴承中心O和轴颈轴心O的连线,顺转动 方向度量,见图8.1。因此,当=0和=180时,润滑膜为最厚和最薄,分别为:2244224111()sin()sin.-r+ec
3、os22 411+ecosin()sin.28eehRRReeCeseRR(8.3)在流体润滑情况下有 eR,的定义见第七章,因此略去式(8.3)的高阶小量,有:coshCe(8.4)式中,minhCe(8.5)图中O1、O2分别为瓦1、2的瓦弧中心,O为轴承几何中心,O为轴颈轴心,e为轴承偏心距,为轴承偏位角,e1、e2分别为瓦1、瓦2的偏心距,e为予置偏心距。根据式(8.4)及椭圆轴承的几何关系可得瓦1和瓦2膜厚为:111222coscos hCehCe(8.6)(a)(b)图8.2 椭圆轴承几何关系示意图 其中 1222112222()2cos()-2cos eeeeeeeeee(8.7
4、)各瓦最小润滑膜厚度1 m in12 m in2hCehCe(8.8)2椭圆轴承椭圆轴承 ellipse bearing 这里阐述椭圆轴承的椭圆是工程意义上的椭圆,而不是数学里定义的椭圆,它是由圆心不重合的两段圆弧组成,见图8.2。轴承的最小润滑膜厚度取两瓦最小润滑膜厚度中较小的。半径间隙最小值,通常也称顶隙,为 mCCe,见图8.3。图8.3椭圆轴承示意图 定义椭圆度为 eC,顶隙比 minmCRmaxCR,侧隙比,三者的关系为minmaxmax111mmmCCCCeCCCC (8.9)椭圆度是椭圆轴承的一个重要参数。它是非椭圆轴承的一个特征量,它表示该轴承予负荷的大小,为此,在多油叶轴承中
5、常称此值为预负荷系数。对于油叶形轴承 maxmin一般采用23。当轴颈中心与轴承几何中心重合时,椭圆轴承的半径间隙最大值,通常也称侧隙,为 max()CC CRr(a)(b)图8.4 多油叶、多油楔轴承几何关系示意图 采用与椭圆轴承相同的方法,根据式(8.4)及三油叶轴承(瓦弧包角为120度)的几何关系为:112233coscoscoshCehCehCe(8.10)1min12min23min3-hC ehC ehC e(8.12)三油叶轴承的轴承最小润滑膜厚度应取三瓦中的最小者 3多油叶和多油楔轴承多油叶和多油楔轴承(multi wedge bearing)以以三油叶、三油楔轴承为例,见图8
6、.4。三油楔轴承内表面由圆柱和油楔两部分组成,对于圆柱部分,仍采用式(8.4)。对于油楔部分(若油楔弧半径与轴径半径之差均为 )C1112223331 cos2 cos3 coshCehCehCe油楔油楔油楔(8.14)轴承最小润滑膜厚位于轴承的圆柱部分,因此有:minhCe(8.15)三油叶轴承的预负荷系数,为:maxmaxminmin11112121CC (8.13)4齿轮与凸轮齿轮与凸轮 gear and cam 对于齿轮与凸轮润滑的问题,通常可以用半径分别与接触点的曲率半径相等的两个圆柱体的接触来近似表示,见图8.5a。并进一步通过数学变换转化为一个当量圆柱与一个平面的接触,见图8.5
7、b。因此齿轮、凸轮润滑时的油膜厚度为:RxhxRRxRRhh2)()(20222222110(8.16)式中,R称为当量曲率半径(equivalent radius of curvature)。若R1和R1分别是两轮的半径,对外啮合与内啮合两种情况,当量曲率半径R 为:1212R RRRR(8.17)h0hxR2R1h0hxR(a)(b)图8.5齿轮、凸轮润滑时的油膜厚度5可倾瓦轴承可倾瓦轴承 (tilting bearing)图8.6可倾瓦轴承的几何关系示意图 由图8.6所示的几何关系可导出可倾瓦轴承第i块轴瓦上的润滑膜厚度表达式:-(-)cos(-)cos(-)sin(-)iiiiiiih
8、 C C Cer (8.18)定义可倾瓦轴承的预负荷系数:1CC(8.19)可倾瓦轴承各瓦的最小润滑膜厚:miniihCe(8.20)可倾瓦轴承最小润滑膜厚应取各瓦中最小润滑膜厚的较小值。对可倾瓦轴承其最小润滑膜所在位置一般是在最大承载瓦上。6可倾瓦推力轴承可倾瓦推力轴承 (tilting thrust bearing)图8.7可倾瓦推力轴承结构示意图可倾瓦推力轴承润滑膜厚度可倾瓦推力轴承润滑膜厚度为:sin()ppphhr r(8.21)设最小膜厚位于()mmr,,则minsin()pp mpmhhr r(8.22)将式(8.22)代入式(8.21),可得min sin()sin()ppmp
9、mhhr rr(8.23)以圆柱轴承为例,见图8.8,设轴颈以速度转动,同时转轴轴心以 的速度和的 速度沿轴承中心O和 转轴轴心连线的方向及其垂直的方向运动。则轴颈的上某一点M相对于轴瓦上对应点 的相对速度的切向分量U和径向分量V,为8.1.2 运动速度表达式运动速度表达式 moving velocity expression 1固定瓦轴承固定瓦轴承 fixed pad bearing OMsincossin()cos()Urereeecossin=cos()sin()Veeee(8.24)(8.25)图8.8 固定瓦轴承速度示意图2可倾瓦轴承可倾瓦轴承 (tilting bearing)在可
10、倾瓦轴承中,不仅轴颈运动,而且轴瓦还绕其本身的支点运动(摆动)。因此,可倾瓦轴承的运动关系较固定瓦复杂些。我们可将瓦块M点的摆动速度沿切向、径向分解与式(8.24)、(8.25)合成并略去高阶小量,得 sin()cos()1 cos()cos()sin()sin()iiiiiiiiiiUreerVeer (8.26)ii式中,为第i块瓦的摆动角速度,为第i块瓦的支点角。图8.9可倾瓦轴承的运动示意图3动载轴承动载轴承 (dynamic bearing)图 8.10径向动载轴承()sin()cosbjUree在轴颈表面任一点M,相对于轴承内表面M点的切向和法向速度(8.27)s()sinsinb
11、Vecoee(8.28)8.1.3边界条件边界条件(boundary condition)求解润滑理论问题,建立Reynolds方程和能量方程等控制方程是其中的重要一步,但如果没有采用合适的边界条件,其结果也是大相径庭。这里所说道边界条件是指润滑流体边界的已知条件。通常有下面几种情况。1流体与固体壁面的边界条件流体与固体壁面的边界条件 fluid-solid wall boundary condition 2不同流体边界面上的边界条件不同流体边界面上的边界条件 different fluid boundary condition 3流体润滑膜上游和下游的边界条件流体润滑膜上游和下游的边界条件
12、inlet and outlet boundary conditions of fluid film 1流体与固体壁面的边界条件流体与固体壁面的边界条件 fluid-solid wall boundary condition(1)速度边界条件 speed boundary condition 当固体壁面不可渗透时,粘性流体质点将依附于固体壁面上而无滑移。若设流体速度为u,壁面速度为U,则有:对于运动固体壁面:uU对静止固体壁面:0u (8.29)(8.30)对于非粘性流体则可以有滑移,此时nnuU(8.31)(2)温度边界条件 temperature boundary condition 可认
13、为为固体壁面处润滑流体的温度与固体壁面的温度相等、热流量相等,即:TT流壁()()TTkknn 流壁Tn为法向热流梯度,通常定义从固体壁面向流体传导的热量为正。3)压力的边界条件 press boundary condition 固体壁面作用在流体上的压力与该处流体作用于固体壁面上的压力相等,即:pp流壁2不同流体边界面上的边界条件不同流体边界面上的边界条件 different fluid boundary condition 通常可认为两种润滑流体在分界面的速度、温度和压力是连续的,即uu1流2流pp1流2流2TT1流流3流体润滑膜上游和下游的边界条件流体润滑膜上游和下游的边界条件 up a
14、nd down boundary conditions of fluid film 流体润滑膜上游或下游边界条件一般是指该处流体润滑膜的压力和温度。其中上游边界处的流体膜温度,通常可以取由外界供给润滑剂和经下游边界返回上游处润滑流体的混合温度。压力边界条件中气体润滑由于气体的可膨胀性,气体润滑膜可以保持连续而无破裂,液体润滑中由于液体通常认为是不可压缩的,因此液体润滑时润滑膜下游常有破裂发生,变得较为复杂。(1)油膜形成和破裂的原因与现象 油膜破裂的原因关于油膜破裂原因,一般有两种解释。一种观点认为油里本来溶解有一部分气体,当压力降至大气一种观点认为油里本来溶解有一部分气体,当压力降至大气压以
15、下,溶解度也随之降低,于是一些气体逃逸出来形成了气穴压以下,溶解度也随之降低,于是一些气体逃逸出来形成了气穴。另一种观点认为压力降至油的液态和气态能够共存的“饱和压力时”,一部分油发生相变,成为油的“蒸汽”,因而形成气穴。但在通常的轴承运转温度下,润滑油的饱和压力比大气压低很多,而实验结果表明油膜破裂现象却在压力稍小于大气压时就发生了。因此一般认为前一种解释较为合理。所以,在流体润滑设计中通常采用环境大气压代表油膜破裂时的压力。油膜的形成与破裂现象Cole和Hughes最早用玻璃做的轴承套直接观察了径向轴承内油膜的流动状态,56年、57年相继发表了观察结果。(i)在油膜增大的区域里(即发散区域
16、里)油膜破裂成细条状,沿轴承宽度方向各处开始破裂的位置基本上是一致的。改变供油压力对于油膜破裂的位置没有什么影响。从油孔供给的油与转动的轴颈带回的破裂油膜汇合而逐渐铺开,直到覆盖轴承的全部宽度形成喇叭状的过渡区。(ii)供油压力对于油膜上游边界的形状影响很大。(iii)在油孔处添设一个轴向油槽并不能有效地加速油膜的铺开。(iv)用周向油槽供油,仍然会出现油膜破裂和油膜形成的典型现象。(v)如果将轴承沉浸在油池里,上诉现象依然发生,这说明气体来自油膜内部,不是由于低压而从轴承两端部吸入。(vi)在旋转载荷下油膜的形状与静载荷下的状态大致是一样的。油膜形成与破裂对轴承性能的影响1、对轴承的承载能力
17、、摩擦功耗和泄油量等静特性的分析表明,油膜形成与破裂对承载能力影响不大,这是 因为它们都发生在压力较小的部位。2、油膜形成与破裂对摩擦功耗如不计油膜破裂部分的摩擦功耗(即只计入油膜完整区的摩擦功耗)则影响较大。3、油膜形成与破裂对于泄油量影响大。=0.2,n=1500r/min,p=0.05Mpa,f=30Hz 时的油膜形成过程=0.2,n=1500r/min,p=0.05Mpa,F1=6N,F2=6N 时的油膜形成过程=0.2,n=1500r/min,p=0.05MPa F1=6N,F2=6N时的油膜形成过程=0.2,n=1500r/min,p=0.05Mpa 时的油膜形成过程 以激振力影响
18、为例见图以激振力影响为例见图 =0.2,n=1500r/min,p=0.05Mpa,f=20Hz,F1=6N,F2=6N小偏心率、小激振力下油膜破裂过程小偏心率、小激振力下油膜破裂过程=0.2,n=1500r/min,p=0.05Mpa,f=20Hz,F1=12N,F2=12N小偏心率、较大激振力下油膜破裂过程小偏心率、较大激振力下油膜破裂过程=0.5,n=1500r/min,p=0.05Mpa,=0.5,n=1500r/min,p=0.05Mpa,f=20Hz,Ff=20Hz,F1 1=6N,F=6N,F2 2=6N=6N中等偏心率、小激振力下油膜破裂过程中等偏心率、小激振力下油膜破裂过程=
19、0.5,n=1500r/min,p=0.05Mpa,f=20Hz,F1=12N,F2=12N中等偏心率、较大激振力下油膜破裂过程中等偏心率、较大激振力下油膜破裂过程流体润滑膜的上下游边界条件流体润滑膜的上下游边界条件Gmbel边界条件边界条件Gmbel边界条件认为润滑膜在收敛区域形成连续油膜压力,在发散区油膜破裂,无油膜压力。即 在=0,时,p=pa(8.40)在0,p=p()(8.41)它也被称为半Sommerfeld边条,Gmbel边界条件较接近实际情况,又便于数学处理,因此在理论计算中常用。(2)油膜形成与破裂的边界条件)油膜形成与破裂的边界条件 实际应用的油膜边界条件可概括为三类,连续
20、型边界条件,气穴边界条件和分离边界条件。Sommerfeld边界条件边界条件 (Sommerfeld boundary condition)Sommerfeld边界条件认为油膜是连续的,油膜压力分布是一个连续周期函数,即满足 p()=p(+2)(8.38)在 hmax处,即=0处,p=pa(pa周围环境压力)(8.39)采用此边界条件,在收敛区形成正压力,在发散区形成负压力,且正负对称,见图。Sommerfeld边界条件最为简单,但是实际上液体不可能形成较大的负压,因此,这种边条除在偏心距e很小时有一定的实际意义外,其他情况均与实际情况相差较大。(Gmbel boundary conditio
21、n)Reynolds边界条件边界条件 Reynolds boundary conditionReynolds边界条件可表述为:在油膜完整区和油膜破裂区的交界线上压力的法向梯度为0,压力的值等于pa,即:在=0时 p=pa 在=2时,p=pa,0pFloberg边界条件边界条件 Floberg boundary conditionFloberg(1961,1974年),从流量连续观点得出另一种边界条件。它实际上是Reynolds边界条件的推广,它给出了油膜破裂后的边界条件。1-1、2-2分别表示没有外界润滑剂流入情况下,油膜破裂区的开始和结束的边界,其中qx、qz分别表示油膜完整区单位宽度上x和
22、z方向的流量,qc表示油膜破裂区上单位宽度上的流量由于径向轴承只在x方向上有速度U,因此有 图8.18 Floberg边界条件312zhpqz 在边界1-1处应满足流量连续条件:1111xzcqzqxqz 即 331111111122122hUhhUhppzxzxz 经简化,可得1110ppzxxz 须满足 110ppxz在边界2-2 12322226hhppxUhxzz 分离边界条件分离边界条件 departure boundary condition1957年Hopkins提出,假设当间隙增大到某一程度时,油膜与静止表面分离,分离流线以外就形成气穴或涡旋。按照粘性流体边界层理论,分离点处速
23、度在表面法线方向的梯度为零,由此可推导出相应的压力边界条件。图8.19 分离流线根据润滑剂速度表达式1()(1)2xpyvy hyUxh 两端对y求导 2xy hdvhpUdyxh如油膜在2xx处与静止表面分离,则22202xhpUxh即22220 xpUxh上游油膜形成边界上游油膜形成边界 前面所涉及的上游润滑膜形成边界,只是简单地认为在进油孔和轴向油槽处就形成了完整的润滑膜,而实际上上游润滑膜边界通常成喇叭口状,见图8.20。1974年Etsion和Pinkus提出有轴向油槽的滑动轴承油膜上游边界的确定方法。图8.20 上游润滑膜边界成喇叭口状在任一轴向截面处的油膜厚度为:(1cos)hC
24、 假定油槽宽度为B0,开设在0=0处,从油槽流出的油在1处覆盖了轴承的全部宽度,油膜形成的边界用b()/2表示,又假设在整个轴承宽度上润滑剂下游油膜均在2处开始破裂成条状流,见图8.20。则通过0zb/2区域内的流量连续方程为020/2/2/2000bbBq dzq dzq dz假定油槽宽度为B0,开设在0=0处,从油槽流出的油在1处覆盖了轴承的全部宽度,油膜形成的边界用b()/2表示,又假设在整个轴承宽度上润滑剂下游油膜均在2处开始破裂成条状流,见图8.20。则通过0zb/2区域内的流量连续方程为020/2/2/2000bbBq dzq dzq dz(8.63)(8.62)(8.61)2Uh
25、q式中,左端表示在01内任意处的x方向流量,右端的第一项表示从破裂油膜处循环流回来的润滑剂,第二项表示从油槽中流出来的润滑剂。为了简化分析,故采用无限窄轴承假设,即将视轴承为无限窄的,此时圆周方向的压力梯度所造成影响可略去不计,故周向流量为(8.63)代入式(8.62)并整理可得002222Bbbhhh或002hbBhh周向采用Gmbel边界条件,020,,故有0(1)hC2(1)hC代入式(8.65)可得上游油膜形成的边界0(1)(1 cos)Bb(8.65)(8.68)在=1处b=B,所以01(1)(1cos)BB由式(8.69)可得到1和B0/B的关系,即101(1)cos1BB10(1
26、cos)2/11BB由式(8.71)可见,如 02/1BB就会呈现图8.20所示的喇叭形状的上游油膜形成边界。如 02/1BB,则有1=0,故在=0处油膜就覆盖了轴承的全部宽度,此时再增加油槽的宽度也不会对油膜形成边界有什么影响。有限长轴承的情况下,式(8.62)仍可适用,此时周向流量为2122hpUhqR 根据下游油膜破裂边界条件033/2/20020000()21226bBBhbhpphhdzhdzURUR 这时我们就得不到式(8.68)那样简单的表达式。但仍可以用迭代法将b和轴承内的油膜压力分布同时解出。(8.71)(8.70)的偏导数都一样,其方程不变。因此上述边界条件变为压力边条应用
27、示例压力边条应用示例对于径向滑动轴承,其常用Reynolds边条为 z方向:2Bz 时 app 方向:0时 app2app0p 时 在工程计算中常取压力为表压,如环境压力为大气压,则表压力 appp,Reynolds方程对p和对pz方向:2Bz 时 0p 方向:00p 20p 0p时 时 由于Reynolds方程是一个二阶偏微分方程,它在通常情况下没有解析解。为了揭示流体润滑的基本规律,通常可将二维流体润滑问题简化成为一维的问题,如假设轴承在z方向上无限宽,因而不存在z方向上的流动,即 8.2 滑块与止推轴承滑块与止推轴承 slider and thrust Bearing 0pz。此时,Re
28、ynolds方程化为一维方程,这就是所谓的“无限宽轴承理论”。8.2.1斜面推力轴承斜面推力轴承 bevel thrust bearing 对于无限宽斜面轴承,在为常数时,其Reynolds方程为:图8.22斜面推力轴承简图3()6ddpdhhUdxdxdx 处p取得最大值,则积分常数C为:润滑膜厚度为:2(1)h ahaxxL将式(8.84)对x积分后可得到:3(6)/dpUhhcdx 设在膜厚0h06CUh 即036hhdpUdxh 利用边界条件 12|0hhpp,并将上式再次对x积分,可得压力分布 123212()()6()hax axhUpahh x12hhxaa1.最大压力处润滑膜厚
29、度:122120221hhahhhha2.最大压力值:2max3(1)2(1)Uapa a a222111212222222(|)6ln2(1)/(1)(1)hxxxhxhphWpdxxpxdpULaaaULxdphah 3.单位宽度上轴承承载能力:式中p称为承载能力系数 5.压力中心所在位置2222)1(2ln)1()ln21(2*2*2121aaaaaaLxdxdxdpxBpxdxBWxxxxx4.摩擦阻力:22222(1)ln3(1)3(1)ln6(1)trWhaaaULBFLaaahr称为摩擦阻力系数 式中可得到承载力的极大值,这时a的值为2.2。2222)1()1/()1(2ln6)
30、(21212121aaaahUBLdxdxdpxBdxdxdpxxpBpdxBWxxxxxxxx0dWda 2220.1602UBLWh021.37hh最大压力处润滑膜厚度 摩擦力24.7thWFL由于令8.2.2曲面轴承曲面轴承 curved surface bearing 如设轴承表面为曲面。其膜厚 nhmx。这时轴承的承载能力可用与上述斜面轴承12223221132226(31)(1)(1)12(1)(1)(21)()(32)nnnnnUBLnaaaWnhanan 当n=2时,曲面为抛物面。当轴承的承载能力取极大值时有a=2.3,这时轴承的承载能力为:2220.163UBLWh当润滑膜厚
31、度按指数曲线 xhe变化时,轴承的承载能力:22323231()()61UBaaa LWaha由于 lnLa,于是有 232232()31()61nnaa l aUBaWah l aa对应于a=2.3,W取极大值:2220.165UBLWh同样的方法求得:8.2.3阶梯轴承阶梯轴承 step bearing 由Reynolds方程(8.84)可知,在等温条件下,即为常数时,如h=常数,则Reynolds方程右端项为0,这时轴承中无流体动压产生。然而如果两平行表面其中一个有一阶梯,则轴承将产生流体动压力,见图8.24。图8.24阶梯推力轴承简图这种阶梯轴承是由Rayleigh于1918年主持设计
32、的,所以被称为Rayleigh阶梯轴承。Rayleigh曾用变分法探讨在一维流动时何种油膜形状具有最大的承载能力,发现上述阶梯形状为最优。对Reynolds方程(8.84)积分两次,所得压力分布为:0136hhpUxCh对区域 1L0pp0p10C,如图所示坐标,当x=0时,p=0;x=L1时,为在阶梯处的公共压力。根据边界条件可得,有 1001316hhpULh同样,对区域 把坐标换到另一个端部,则有 2L0202326hhpULh为在阶梯处的公共压力,则 0p0210213321hhhhLLhh221 21 22 10331 122()hh LhL hhLhL h在区域 1L2221 22
33、 123311 22 1()61h LhL hUpxhLhL h在区域 2L2211 22 123321 22 1()61h LhL hUpxhLhL h在宽度B上的轴承承载能力:121002123300126()6()LLU hhU hhWWWBxdxBxdxhh1212331 22 13()UBL L L hhLhL h22232223(1)()()UBL L aLLWhL aLL12LLL12hah33222222332222()(2)()(1)3(1)0()L aLLLLL LLaWUBL aLhL aLL对上式微分并令 2WLWa为零,可分别解得使W取得最大值的 2La2222222
34、222)(2LLLLLLLLa)1(232aLL0)()1()(32122212222222LLaLaLaLLaLnLLUBLLaW由132212aaLL将式(8.121)代入式(8.124)后得到:2(1)(481)0aaa10a8666.12311a1333.02312aa1为最佳值 542.2)32(221aaLL对应于最佳参数的阶梯轴承的特性为 2max21220.20520.42624.092UBLWnxLnfL110310,6cChhpUh102320,6cChhpUh331122212212UhhUhhdpdpdxdx1233126 U hhpxChh12133126cU hhp
35、Bhh116pK UxC226pKUxCPinkus 书书p.60 Eq.(3-59),Fig.3-16:对于B1段,p=0 for x=0;p=pc for x=B1。于是有对于B2段,这里h0是一个积分常数,对于两段,h0要取不同的值,因此不能以相同的值出现在公式(3-59)中,所以这个解有点问题。在B1段,流量是守恒的。因为膜厚不变,dp/dx为常数。应当有(3)即 考虑左边界条件,C=0。于是(问题在于3式中左端和右端是分段连续函数,左端适用于B1段,右端适用于B2段)所以(3)积分后也是分段表达,即:(B1段)(B2段)式中K1,K2由h1,h3确定。然后根据压力边界条件和阶梯处压力
36、相等的准则,确定C1,C2.结果就和Pinkus的一致。1031hhh0232hhh101022123312,hhhhKKhh3231216hhhhUdxdp13231216BhhhhUpc0C我这里面感到困惑的是两个问题。先讲第一个问题:你的推导与我这里面感到困惑的是两个问题。先讲第一个问题:你的推导与Pinkus的其实一样,因为你的的其实一样,因为你的K1就相就相当于他的当于他的,K2就相当于他的就相当于他的。我以为。我以为K1,K2不能由不能由h1,h2完全确定,因为完全确定,因为h0是未知的。如果你认为是未知的。如果你认为K1K2,那么有什么理由认为,那么有什么理由认为h0是相同的呢?
37、如果认为它们不相等,将它们区别为是相同的呢?如果认为它们不相等,将它们区别为h01和和h02,于是有,于是有。C1,C2可以由两段端部压力为可以由两段端部压力为0的边条求出,都等于的边条求出,都等于0。因为。因为h01h02所以由一个阶梯处压力相当的条所以由一个阶梯处压力相当的条件不能够确定两个未知常数件不能够确定两个未知常数h01和和h02。所以我觉得。所以我觉得Pinkus的(的(3-59)式有问题。他的()式有问题。他的(3-59)式中隐含)式中隐含了了h01=h02。再讲第二个问题,关于再讲第二个问题,关于(3)式我可能没有讲清楚,那不是在两段中的流量相等,我考虑的是在式我可能没有讲清
38、楚,那不是在两段中的流量相等,我考虑的是在B1段段中,流量当然也要守恒。因为中,流量当然也要守恒。因为dp/dx处处相等,处处相等,h1 处处相等,本来没有问题。但是到了出口处,高度处处相等,本来没有问题。但是到了出口处,高度突然变成了突然变成了h2,这时发生了什么情况?你在下面的解释是加了一个,这时发生了什么情况?你在下面的解释是加了一个qz。但是我发现另外一种可能,所。但是我发现另外一种可能,所以向你请教:以向你请教:(3)式对不对(注意左右的式对不对(注意左右的dp/dx是一个值)?如果对,那么就是说在是一个值)?如果对,那么就是说在和和(考虑左边界条件(考虑左边界条件)的情况下流量守恒
39、是可能的。注意,这个结果与)的情况下流量守恒是可能的。注意,这个结果与Pinkus的结果不一样。的结果不一样。如果根据流量是守恒的原则。两边的流量为如果根据流量是守恒的原则。两边的流量为左端左端3300112212212212PPUhhUhhBB右端右端 (4)01031100232266PhhUBhPhhUBh压力的导数压力的导数3310021122331266212212hhhhUhhUhhUUhh331002112233122222hhhhhhhhhh将(将(5)式代人()式代人(4)式,有)式,有即即即有即有左端左端h0=h0右端右端 1()2xphzvz hzUxh 速度分布速度分布
40、3212hUhdpQdx流量流量8.2.4平面组合轴承平面组合轴承 (compound flat surface bearing)由平面和斜面联合组成的轴承称为组合轴承,也是工程中常见的,见图8.25。图8.25平面组合阶梯推力轴承对区域 对区域 其油膜厚度函数为:1L2L121hhhxxL2hh 2220.1602UBLWh2220.163UBLWh2220.1602UBLWh2220.1602UBLWh2220.163UBLWh2220.2502UBLWh2220.165UBLWh8.2.5可倾瓦推力轴承可倾瓦推力轴承 (tilting thrust bearing)图8.26可倾瓦轴承的
41、示意图8.3 径向滑动轴承径向滑动轴承 journal bearing 8.3.1 全圆柱轴承全圆柱轴承 (whole circle bearing)图8.28 全圆柱轴承当密度为常数时,Reynolds方程则变成33()()612hphphhUxxzzxt如果仅考虑定常工况,则稳态的Reynolds方程为33()()6hphphUxxzzx(8.142)3312121212()()()()6()6()()()(h)+6612hphphhUUVVxxyyxyUUVVhhxyt1.列出雷诺方程与边界条件2.无量纲化间隙函数间隙函数H H的表达式的表达式cos1HdxdhUdxdphdxd6)(3
42、ddHddPHdd3)(3无量纲单位无量纲单位2202,CrPpcHhrx,无量纲方程无量纲方程 30302HdhHdPm积分并代入边界条件积分并代入边界条件=0,p=03.求解(无限长假设条件)cos11cos12Sommerfeld 变换考虑间隙函数cos1H)cos1()cos1(30302dhdPm0)cos1(iidI)2sin42sin2()1(1)cos1(22025233dI)sin()1(1)cos1(023222dI25222232)1(2sin42sin23)1(sin3mHp1Sommerfeld边界条件采用Sommerfeld边界条件求得的压力分布在油膜扩散区内存在负
43、压力,因而与实际情况差别较大。222)1(2mH22)cos1)(2()cos2(sin3p2Gmbel边界条件根据Gmbel条件,只有在油膜收缩区才能建立起油膜压力;而在油膜扩散区则压力为0。对于360圆柱轴承时有:0|0,|0pp 图8.29 Gmbel边界条件示意图0压力分布表达式 222 3/2223 2(2)sinsin2 3 sin(2cos)2(2)(1)(2)(1cos)p2时 p0 无量纲油膜合力:22222 1/212(2)(1)6(2)(1)xyFF无量纲摩擦阻力:220sin2tddFHHH阻力系数:23222(4254)146(1)1(1)f212yxFtgF偏位角:
44、处和压力最大点 判断,只有当油膜终止边 3Reynolds边界条件Reynolds边界条件认为:在油膜起始边=0处,p=0。在油膜终止边 2处,p=0,0p图8.30 Reynolds边界条件示意图根据(8.147)的Reynolds方程积分后的无量纲形式 2313mHdpdHH处油膜厚度相等,即 2mHH时。才能同时满足 20mpp因此 2mHH、的位置必对称于 minH。于是有,2322 3333()mpIH IIH I将边界条件 2|0p代入式(8.171),可得 222 32()()0IH I即:222222(sincos)2(cossin)0由上式可以确定 22(8.171)2m则
45、222 3/223(2)4 sinsincossin(1)2(1cos)p 轴承承载能力系数:12222222222(1 cos)34(sincos)(1)1(1cos)偏位角:2222222 1(sincos)tan(1 cos)无量纲摩擦阻力:222220sin2tddFHHH阻力系数:22212422222222(sincos)sin2(1 cos)34(sincos)(1)f上述无限宽轴承解没有考虑润滑油轴向流动,但由于实际轴承总是有限宽的,因而真实轴承中总是有轴向流动存在以及由此产生的端泄效应。这种端泄影响使实际轴承的承载能力系数 比无限宽轴承的 小 实验表明,在上述三种边界条件得到
46、的解析解中,以Reynolds条件得出的解最接近真实轴承的情况;按Sommerfeld条件得出的解与实际出入最大。图8.31给出了这三种条件下的轴心轨迹图。图8.31圆轴承的轴心轨迹图 油膜合力 偏位角 222020sincosyxyxFFFrdplFrdplF2/0/tanyxFF 摩擦阻力 摩擦系数 21222202020)1()2(612)2(thyxtFdhrphlrddydvlrdlF321/2fFFft 动特性系数yyFxxFyyyFxxxFFFyyFxxFyyyFxxxFFFoyoyoyoyyyoxoxoxoxxx)()()()(000000yFDxFDyFDxFDyFKxFKy
47、FKxFKyyyyyxxxyxxxyyyyyxxxyxxx,8.3.2浮环轴承 floating ring bearing 图8.32浮环轴承的示意图浮环轴承如图8.32所示,浮环轴承在轴承与轴颈之间有一圆环,该环可以自由浮动,并将轴承间隙分为内外两层。在润滑膜动力粘度不变的情况下,对于浮环轴承内层油膜,即轴颈表面和浮环内表面形成的油膜,其Reynolds方程为:33()()6()rpphhhUUxxzzx对于浮环外表面和轴承内表面形成的外层油膜,相应地有,33()()6rpphhhUxxzzx求解式(8.179)和(8.180)可得到相应的内、外层油膜压力分布。(8.179)(8.180)8
48、.3.3部分圆弧瓦轴承工程中还常见部分圆弧瓦轴承,部分圆弧瓦轴承的瓦张角一般180。在部分圆弧瓦轴承的性能分析中,最常用的是Reynolds边界条件。但是不论是采用那种假设和边界条件,由于轴承的载荷角和瓦张角这两个新的独立参数的出现,使其解的形式都变得非常繁琐。由于部分瓦在空间所处的位置不同,对油膜起始边与终止边边界条件的处理亦不同。(1)如图8.33a所示,如油膜起始边落在收敛区里,即,00a,如设无量纲进油压力为 inp则相应当边界条件为:在油膜起始边 a时,inpp;在油膜破裂边 2时,0pp在油膜破裂区 2b0p 时,(2)如图8.33b所示,0a0b即油膜起始边从扩散区即开始,一种简
49、捷的处理方法是:油膜从 0开始建立压力 0时,0p;结构边界条件 b时 ,inpp而在扩散区 0a内则把压力p简单地处理为0。(3)如果圆弧瓦全部落在油膜收缩区内,亦即 0aminb,此时无油膜破裂区,全部边界条件为结构所限制(图8.33c)。a时,inppb时,inpp(4)当部分轴承全部位于扩散区内时(图8.33d),全部压力分布为0。边界条件确定后。压力分布的求解可仿照前面几节所述的方法进行。以上关于润滑膜起始及终止边界条件的处理原则对以后各章一般也都是适用的。图8.33部分圆弧瓦轴承示意图无限窄径向滑动轴承1BD时,则有 2222zpxp。因此可以略去x方向的压力项后,动力粘度为常量时
50、,相应的Reynolds方程则变成:2()6pdhhUzzdx 采用无限窄轴承假设,可以得到解析解,并且还可以计算侧泄量,这是无限宽轴承解所不具备的特点,而且当 1B,其计算结果具有一定的准确度。在普通圆柱轴承情况下,对式(8.195)积分两次得到(8.195)212226czczdxdhhUp由于压力 p对称于 0z,故 1c0。轴承两端的边界条件:2Bz时,0p可解得 2c则轴承的油膜压力分布为 22234U dhHpzhdx(8.197)无限窄轴承假设和无限宽轴承假设正相反,无限窄轴承假设认为轴承很窄时,即由上式可见当 0dxdh时,0p,这意味着油膜压力的周向边界条件只能定在 maxh
51、minh处 0p。式(8.197)代入油膜厚度h的表达式,则轴承的无量纲油膜压力分布为:2233sin(1)2(1cos)Bpd 如果周向边界采用Gmbel边界条件时,轴承承载能力系数为:222222(1)16(1)Bd偏位角:阻力系数:无量纲侧泄量:21tan422111f222BQBdQRd8.4挤压膜轴承挤压膜轴承 squeezing bearing 如果载荷沿膜厚方向交替变化,支承面之间的润滑剂就会受到挤压作用。当载荷交替变化的速度适当时,支承面间的润滑剂来不及全部都挤出而形成挤压膜润滑。这种挤压膜能承受很大的载荷。8.4.1平面挤压膜轴承 (squeezing flat bearin
52、g)对于无限宽平面挤压膜轴承,即两块无限宽矩形板在载荷W作用下相互靠近,间隙中充满粘性润滑剂在两板之间形成挤压润滑。见图8.22a,图8.34平面挤压膜轴承示意图在为常数时,其Reynolds方程为:3()12ddpdhhdxdxdt上式对x积分后,得3112dpdhxdxh dt23312122dhdh xpxdxChdthdt取边界条件为:当 2Lx 时,0p,解得 28LC 润滑膜压力分布为:223164Ldhpxh dt最大压力发生在中央截面上,为:2max332dh Lpdt h 润滑膜压力分布对于有限长矩形板的挤压润滑,其承载能力公式,可采用以下修正dtdhhBLW33式中,为端泄
53、系数,其值取决于B/L比值。有限长矩形板膜厚由h1减小到h2所经历的时间t为2122333112121hhWLBdhhWLBthh式中,L为轴承长度,“-”号表示当两表面接近,即dh/dt小于0时,压力为正。反之压力为负。3/222222233/222116644LLLLLLLLdhdhLdhWpdxxdxxh dth dthdt 单位宽度上的承载能力为:8.4.2圆盘挤压 squeezing disk 为了分析半径为a的圆盘挤压润滑,将Reynolds方程转换为极坐标形式,即thrphrrprhr1233由于对称性,有 0p,且h与r无关,故Reynolds方程简化为:dtdhhrdrdpr
54、hdrd3312上式积分后,代入边界条件:00rdrdp0arp则得油膜压力分布dtdhharp322)(3承载能力为dtdhhaprdrWa340232从而求出膜厚由h1降到h2所需的时间212241143hhWat对于椭圆盘挤压,若a和b表示椭圆的长半轴和短半轴,可以求得承载力公式为dtdhbabahW2233338.4.3径向挤压膜轴承 squeezing journal bearing 径向挤压膜轴承如图8.35所示,径向轴承在载荷W作用下形成挤压润滑时,轴心移动速度为dtdcdtde图8.35径向轴承的挤压而膜厚变化率依各点位置而不同,即dtdcdtdhcos对于无限宽轴承,0yp,
55、且x=R,则方程变为 dtdcRddpddcos12cos1223将上式积分,并代入Sommerfeld边界条件 当=0时,p=0;当=时,0ddp压力分布为dtdcRp222211cos1116由于压力分布对称于=,所以挤压膜承载能力为dtdcRdpRLW2/32023112cos2(8.221)式(8.221)和(8.222)是对于普通圆轴承采用 Sommerfeld边界条件得出的。如果对于圆轴承采用Gmbel边界条件,或者对于180包角部分圆弧轴承的挤压膜润滑,压力分布的边界条件应为:=/2时,p=0。此时,按照无限宽轴承理论可得dtdarctgcRLW2/12/322231112112
56、2/1112/32112/1222/32222311111124arctgarctgWcLRt采用同样的分析方法,可得半球面轴承的挤压膜润滑问题的结果,即dtdcRW2111)1ln(162224)1ln(1)1ln(1322222112121211224WcRt求得偏心率由1增加到2所经历的时间t为 2/12112/1222231112WcLRt(8.222)8.5 动载轴承(dynamic load bearing)前面所讨论的是载荷大小和方向都不变化的稳定载荷轴承,在给定的工况参数下,径向轴承的轴心或者推力轴承的推力盘就处于一个确定的位置并保持不变。所以这类轴承所包含的参数与时间无关。实
57、际上许多轴承所承受的载荷大小、方向或者旋转速度等参数是随时间而变化的,这种轴承统称为非稳定载荷轴承或动载荷轴承。如图8.36所示,动载荷轴承的轴心或推力盘的位置将依照一定的轨迹而运动,如果工况参数是周期性函数,则轴心运动轨迹是一条复杂的封闭曲线。动载轴承和承受稳定载荷的轴承不同,动载轴承不存在所谓“静平衡位置”,由于载荷的不断变化,其轴心位置随时间变化形成动态轴心轨迹动态轴心轨迹;由于外载荷或轴颈中心位置的改变使油膜力不能按线性化处理,而表现出明显的非线性特征;此外,由于时间的引入,动态轴心轨迹亦将和运动初始条件相关,在轴承载荷或角速度呈周期性变化时轴心的运动最终将也形成某一封闭轨迹。可开进油
58、槽的区域最小油膜厚度处易发生气蚀的区域图8.37动载轴承轴心轨迹根据轴心运动轨迹可以推算出动载荷作用下轴承最小油膜厚度的大小以及所发生的区域,包括运动中的轴颈在最小油膜区域内所持续的时间。这些都和判断动载轴承是否能正常工作或产生擦伤、磨损有关。动载轴承另一种常见的损坏形式气蚀气蚀,也与轴心轨迹有密切联系。当轴颈中心迅速地向轴承中心运动时,由于油膜收敛区迅速扩大而导致润滑油来不及充填这个扩大了的空间,从而在轴承内表面形成局部气穴,进而由于溶解在润滑油中的气体析出形成气泡;当轴颈中心再次迅速靠近轴承内表面时,由于轴颈和轴承间的挤压作用使得气泡破裂,所产生的爆破压力造成轴承内表面合金的破坏,即形成气
59、蚀。影响动载轴承轴心轨迹的因素因素包括:轴承所能承受的最大比压;轴颈、轴承的旋转角速度;外载荷的旋转角速度等;典型的动载荷轴承如内燃机的曲轴、连杆、活塞销等轴承,它们所受载荷载荷的大小和方向均为大小和方向均为周期性变化周期性变化。具有不平衡质量的转子的支持轴承承受着大小基本不变的旋转载荷。而稳定载荷轴承在启动、停车过程中以及受到振动冲击作用时,都属于动载荷轴承。如果油膜压力过大且频繁地作用在轴承内表面某些固定部位时,轴承内表面合金层因反复承受交变应力也会产生疲劳裂纹与剥落。因此,动态轴心轨迹是动载轴承研究中的重点。图8.36动载轴承的运动 动载荷轴承就其工作原理可分为两类。第一类第一类是轴颈不
60、绕自身的中心转动即无相对滑相对滑动动,而轴颈中心在载荷作用下沿一定的轨迹运动。此时,轴颈和轴承表面主要是沿油膜厚度方向运动,油膜压力由挤压效应产生。另一类另一类动载荷轴承是同时存在轴颈绕自身中同时存在轴颈绕自身中心转动和轴颈中心的运动心转动和轴颈中心的运动。因此,油膜压力包括两种来源:轴颈转动产生的动压效应和轴心运动产生的挤压效应。应用于液体润滑计算的Reynolds方程的普遍形式是分析动载荷轴承的基本方程,可以写成033126VxhUyphyxphx 式中,V0=wh-w0。方程(8.227)的右端第一项表示动压效应,第二项代表挤压效应。将Reynolds方程应用于稳定载荷轴承时,可以忽略挤
61、压效应的作用,即令wh-w=0由于油膜中压力分布与轴心位移之间的复杂关系,在分析动载荷轴承的承载量时,不能简单地将动压效应和挤压效应所产生的承载力叠加。因此,动载荷轴承的润滑计算相当复杂,只有极简单的情况才能得到解析解。动载荷轴承计算的另一特点是分析过程与稳定载荷轴承恰恰相反。在分析稳定载荷轴承时,可根据给定的几何条件直接求解Reynolds方程得到压力分布,进而确定轴承载荷的大小和方向。而在动载荷轴承计算中,已知载荷大小和方向随时间的变化情况,要求确定轴心几何位置和运动轨迹,所以是逆解Reynolds方程。由式(8.227)计算动载荷轴承的轴心轨迹在数学上属于初值问题。根据给定的轴心初始位置
62、,通常采用步进方法逐点确定轴心运动轨迹。(8.227)图8.36给出动载荷径向轴承的运动关系。轴颈除去围绕自身中心以角速度旋转之外,在动载荷W作用下轴心还按照一定的轨迹运动。如果选取=0为参考坐标轴,将轴心的运动分解到沿连心线方向和垂直连心线方向,则轴心运动的速度分量分别为:dtdcdtde)(。这里,为载荷位置角,为偏位角。这样,轴颈表面上各点相对于轴承表面存在切向速度和法向速度。设轴颈表面上坐标角为的任意点M的切向速度为U和法向速度为V0,则 sin)(coscos)(sin0dtdcdtdcVdtdcdtdcRU将U和V0的表达式代入方程(8.227),略去高阶小量,并考虑到c/R2和e
63、/R1,则节圆半径为1121iairiar 轮齿在K点啮合时,根据渐开线齿轮的性质,两个当量圆柱的中心分别在N1和N2点。它们的中心距为N1N2=(r1+r2)sin,其中为啮合角,对于标准齿轮,=0=20。两个当量圆柱的半径分别为SrRSrR022011sinsin 则线接触弹流润滑时当量曲率半径R为02102012121sin)()sin)(sin(rrSrSrRRRRR 两表面相对于接触点K的速度为)sin(30)sin(3002220111SrnuSrnu 所以,两个当量圆柱的平均速度为)1(2sin30)(2102221iSrnuuU 以上S为接触点至节点的距离接触点至节点的距离。渐
64、开线齿轮的啮合线与两个基圆的公切线相重合,而接触线的长度主要决定于模数或者径节。一对轮齿实际的接触范围可以用S值的变化范围来表示。设h1和h2分别为两齿轮的齿顶高,则S值的变化范围将是从020222222sincos)(rrhr010221211sincos)(rrhr(8.301)(8.300)Dowson和Higginson将式(8.300)和式(8.301)代入第七章线接触弹流润滑公式,计算出齿轮在啮合循环中油膜厚度的变化情况如图8.53所示。I:Dp=5,B.S.S.规范;II:Dp=10,B.S.S.规范;III:Dp=5,标准齿;IV:Dp=5,标准齿图8.53齿轮啮合循环中的膜厚
65、变化 图8.53表明:在等温条件下,当小齿轮齿顶与大齿轮齿根相接触时油膜最厚,而当大齿轮齿顶与小齿轮齿根接触时的油膜厚度最薄,节点啮合时的油膜厚度居中。节点啮合的油膜厚度对于齿轮润滑而言具有一定的代表性,这是由于节点啮合时齿面为纯滚动,计算方法简单,用等温弹流计算可以得到较高的精度。所以在齿轴传动的所以在齿轴传动的润滑设计中,通常以节点啮合时的润滑设计中,通常以节点啮合时的油膜厚度为依据油膜厚度为依据。1974年Akin分析了各种渐开线齿轮的润滑问题,提出了节点啮合的油膜厚度计算公式。8.9.1当量曲率半径当量曲率半径R equivalent radius of curvature 根据几何模
66、拟关系,两轮齿接触时的当量曲率半径为2121RRRRR 式中,R1、R2为两轮齿在节点处渐开线的曲率半径,“+”号为外啮合、“-”号为内啮合。由齿轮啮合原理推得各种渐开线齿轮节点啮合的当量曲率半径如下直齿圆柱齿轮 斜齿圆柱齿轮 直齿圆锥齿轮 弧齿圆锥齿轮 2)1(siniiaRn22)1(cossiniiaRn1sin2iiLRnm1cossin22iiLRmnm以上各式中,n为法面啮合角:为节圆螺旋角;Lm为圆锥齿轮齿宽中点处的节锥长;m为弧齿圆锥齿轮齿宽中点处的节圆螺旋角 8.9.2表面平均速度表面平均速度U surface average velocity 根据在法面上相对于节点的表面速度求得平均速度为 直齿圆柱齿轮 斜齿圆柱齿轮 直齿圆锥齿轮 弧齿圆锥齿轮 nianUsin1301cossin1301nianUnmiLnUsin301mnmiLnUcossin301n1为小齿轮每分钟转数。8.9.3单位接触宽度上的载荷单位接触宽度上的载荷W/L如果以Ft表示节点啮合时的圆周力;b为轮齿宽度;b为基圆螺旋角;则各种齿轮在单位接触宽度上的载荷分别为直齿圆柱和直齿圆锥齿轮 斜齿圆柱齿
- 温馨提示:
1: 本站所有资源如无特殊说明,都需要本地电脑安装OFFICE2007和PDF阅读器。图纸软件为CAD,CAXA,PROE,UG,SolidWorks等.压缩文件请下载最新的WinRAR软件解压。
2: 本站的文档不包含任何第三方提供的附件图纸等,如果需要附件,请联系上传者。文件的所有权益归上传用户所有。
3.本站RAR压缩包中若带图纸,网页内容里面会有图纸预览,若没有图纸预览就没有图纸。
4. 未经权益所有人同意不得将文件中的内容挪作商业或盈利用途。
5. 装配图网仅提供信息存储空间,仅对用户上传内容的表现方式做保护处理,对用户上传分享的文档内容本身不做任何修改或编辑,并不能对任何下载内容负责。
6. 下载文件中如有侵权或不适当内容,请与我们联系,我们立即纠正。
7. 本站不保证下载资源的准确性、安全性和完整性, 同时也不承担用户因使用这些下载资源对自己和他人造成任何形式的伤害或损失。