压铸铝合金平板件工艺设计毕业论文
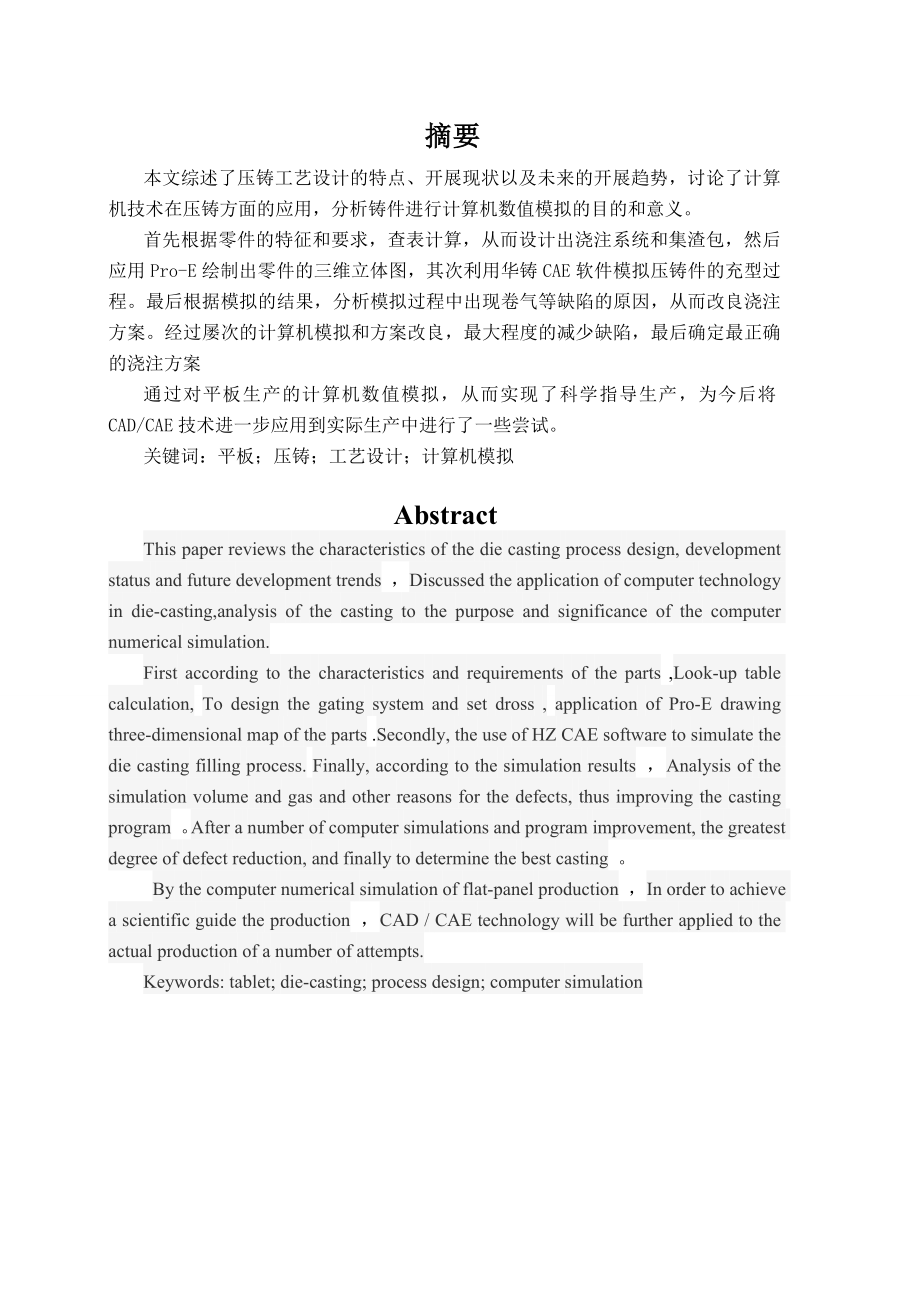


《压铸铝合金平板件工艺设计毕业论文》由会员分享,可在线阅读,更多相关《压铸铝合金平板件工艺设计毕业论文(35页珍藏版)》请在装配图网上搜索。
1、摘要本文综述了压铸工艺设计的特点、开展现状以及未来的开展趋势,讨论了计算机技术在压铸方面的应用,分析铸件进行计算机数值模拟的目的和意义。首先根据零件的特征和要求,查表计算,从而设计出浇注系统和集渣包,然后应用Pro-E绘制出零件的三维立体图,其次利用华铸CAE软件模拟压铸件的充型过程。最后根据模拟的结果,分析模拟过程中出现卷气等缺陷的原因,从而改良浇注方案。经过屡次的计算机模拟和方案改良,最大程度的减少缺陷,最后确定最正确的浇注方案通过对平板生产的计算机数值模拟,从而实现了科学指导生产,为今后将CAD/CAE技术进一步应用到实际生产中进行了一些尝试。关键词:平板;压铸;工艺设计;计算机模拟 A
2、bstractThis paper reviews the characteristics of the die casting process design, development status and future development trends ,Discussed the application of computer technology in die-casting,analysis of the casting to the purpose and significance of the computer numerical simulation.First accord
3、ing to the characteristics and requirements of the parts ,Look-up table calculation, To design the gating system and set dross , application of Pro-E drawing three-dimensional map of the parts .Secondly, the use of HZ CAE software to simulate the die casting filling process. Finally, according to th
4、e simulation results ,Analysis of the simulation volume and gas and other reasons for the defects, thus improving the casting program 。After a number of computer simulations and program improvement, the greatest degree of defect reduction, and finally to determine the best casting 。 By the computer
5、numerical simulation of flat-panel production ,In order to achieve a scientific guide the production ,CAD / CAE technology will be further applied to the actual production of a number of attempts. Keywords: tablet; die-casting; process design; computer simulation 摘要1第一章 绪论31.1 压铸的根本概念31.2我国铝合金压铸的开展历
6、史、现状34566777第二章 压铸铝合金平板件工艺设计82.1 铸件立体图8910102.3.2 铸孔1010 分型面的类型1011111213151719第三章:计算机数值模拟223.1计算机辅助设计(CAD)技术及常用CAD软件223.2 Pro/E的功能简介22 3.3 Pro/E三维建模过程23233.5 第一套方案数值模拟分析253.5.1 几何模型的建立2626第四章 浇注方案的优化29:29304.3 方案评估32第五章 结论33致 谢34参考文献35第一章 绪论1.1 压铸的根本概念压铸是将熔融状态或半熔融状态的合金浇压铸机的压室,在高压力的作用下,以极高的速度充填在压铸模的
7、型腔内,并在高压下使熔融合金冷却凝因而成形的高效益、高效率的精密铸造方法。高压力和高速度是压铸时熔融合金填充成形的两大特点,也是压铸与其它铸造成形方法最根本的区别所在。压铸时常用压射比压在几兆至几十兆帕的范围内,甚至高达500Mpa;充填速度在120 m/s范围内;充填时间很短与铸件大小、壁厚有关,一般为,最短的仅有千分之几秒。此外,压铸模应具有很高的尺寸精度和很小的外表粗糙度值。由于具有以上所述特点,使得压铸件的结构、质量、性能、压铸工艺以及生产过程都具有自己的特点。1.2我国铝合金压铸的开展历史、现状近几十年来,由于铝的冶炼方法与工艺的不断改良,尤其是铝材料根底问题的突破,铝工业开展速度惊
8、人,铝合金在交通运输、航空航天。轻工建材、通讯、电子等部门获得广泛的应用。世界各国越来越重视对铝合金材料成型技术特别是压铸技术的研究开发和推广应用。汽车工业是铝合金材料的主导消费市场,同时汽车技术的开展更是促进了铝合金成型技术的研究。我国的压铸工业在近半个世纪中,从无到有,开展成为一个新兴产业。汽车、摩托车工业始终是压铸工业最大的市场,我国压铸工业受国内汽车、摩托车工业的跃升和拉动而进入一个新的开展时期。压铸件产量从1990年的14.9万吨到1997年的31.2万吨,7年间翻了一番;从1997年的31.2万吨到2002年的62.4万吨,5年间又翻了一番;2003年为70.8万吨,2004年为8
9、0万吨,年增长保持在20以上。压铸件主要是铝合金件,2002年用于汽车、摩托车行业的铝合金压铸件到达41.5万吨,占当年全国压铸件产量的三分之二。我国应该明确铝合金压力铸造技术研究方向,加大投入力度,尽快形成自主产权的先进共性技术,以及其它铸造工艺,普遍形成产业规模,扭转我国铸造工艺落后、能源和资源消耗高、技术含量低、铸件附加值不高、国际竞争力不强的状况。由于整个压铸过程都是在压铸机上完成,因此,随着对压铸件的质量、产量和扩大应用的需求,开始对压铸设备提出新的更高的要求,传统压铸机已经不能满足这些要求,因此,新型压铸机以及新工艺、新技术应运而生。例如,为了消除压铸件内部的气孔、缩孔、缩松,改善
10、铸件的质量,出现了双冲头或称精、速、密压铸;为了压铸带有镶嵌件的铸件及实现真空压铸,出现了水平分型的全立式压铸机;为了提高压射速度和实现瞬时增加压射力以便对熔融合金进行有效地增压,以提高铸件的致密度,而开展了三级压射系统的压铸机。又如,在压铸生产过程中,除装备自动浇注、自动取件及自动润滑机构外,还安装成套测试仪器,对压铸过程中各工艺参数进行检测和控制。它们是压射力、压射速度的显示监控装置和合型力自动控制装置以及电子计算机的应用等。以下介绍的便是压铸行业中出现的新工艺技术。(1)真空压铸真空压铸是利用辅助设备将压铸型腔内的空气抽除且形成真空状态,并在真空状态下将金属液压铸成形的方法。其真空度通常
11、在380600毫米汞柱的范围内,可以通过机械泵获得。而对于薄壁与复杂的铸件,真空度应该更高。由于型腔抽气技术的圆满解决,真空压铸在20世纪50年代曾盛行一时,但后来应用不多。目前,真空压铸只用于生产要求耐压、机械强度高或要求热处理的高质量零件,其今后的开展趋向是解决厚壁铸件和消除热节部位的缩孔,从而更有效地应用于可热处理和可焊接的零件。 真空压铸的特点是:显著减少了铸件中的气孔,增大了铸件的致密度,提高了铸件的力学性能,并使其可以进行热处理。消除了气孔造成的外表缺陷,改善了铸件的外表质量。可减小浇注系统和排气系统尺寸。由于现代压铸机可以在几分之一秒内抽成需要的真空度,并且随着铸型中反压力的减小
12、,增大了铸件的结晶速度,缩短了铸件在铸型中的停留时间。因此,采用真空压铸法可提高生产率10%20%.采用真空压铸时,镁合金减少了形成裂纹的可能性裂纹时镁合金压铸时很难克服的缺陷之一,经常发生在型腔通气困难的部位,提高了它的力学性能,特别是可塑性。2充氧压铸 国外在分析铝合金压铸件的气泡时发现,其中气体体积分数的90%为氮气,而空气中的氮气体积分数应为80%,氧气的体积分数为20%。这说明气泡中局部氧气与铝液发生了氧化反响。因此出现了充氧压铸的新工艺。 充氧压铸是消除铝合金压铸件气孔,提高铸件质量的一个有效途径。所谓充氧压铸是在铝液充填型腔,用氧气充填压室和型腔,以置换其中的空气和其他气体,当铝
13、金属液充填时,一方面通过排气槽排出氧气,另一方面喷散的铝液与没有排除的氧气发生化学反响而产生三氧化二铝质点,分散在压铸件内部,从而消除不加氧时铸件内部形成的气孔。这种三氧化二铝质点颗粒细小,约在1m以下,其重量占铸件总重量的0.1%0.2%,不影响力学性能,并可使铸件进行热处理。3精速密压铸精速密压铸是一种精确地、快速的和密实的压铸方法,又称套筒双冲头压铸法。国外在20世纪60年代中期开始在压铸生产中应用这一方法。精密速压铸法在很大程度上消除了气孔和缩松这两种压铸件的根本缺陷,从而提高了压铸件的使用性能,扩大了压铸件的应用范围。 4半固态压铸半固态压铸是当金属液在凝固时,进行强烈的搅拌,并在一
14、定的冷却速率下获得50%左右甚至更高的固体组分浆料,并将这种浆料进行压铸的方法。压铸机 压铸机就是在压力作用下把熔融金属液压射到模具中冷却成型,开模后得到固体金属铸件的一系列工业铸造机械,最初用于压铸铅字。随着科学技术和工业生产的进步,尤其是随着汽车、摩托车以及家用电器等工业的开展,又从节能、节省原材料诸方面出发,压铸技术已获得极其迅速的开展。1.4.1 压铸机的分类压铸机分热压室压铸机和冷压室压铸机两大类。冷压室压铸机按其压室结构和布置方式又分卧式、立式两种形式。热压室压铸机与冷压室压铸机的合模机构是一样的,其区别在于压射、浇注机构不同。热压室压铸机的压室与熔炉紧密地连成一个整体,而冷压室压
15、铸机的压室与熔炉是分开的。 有以下根本分类:热室压铸机 、 冷室压铸机 、常规热室压铸机 、卧式热室压铸机、 立式冷室压铸机 、卧式冷室压铸机 、全立式冷室压铸机 1.4.2 压铸机的组成1合模机构:驱动压铸模进行合拢和开启的动作。当模具合拢后,具有足够的能力将模具锁紧,确保在压射填充的过程中模具分型面不会胀开。锁紧模具的力即称为锁模力又称合型力,单位为千牛,是表征压铸机大小的首要参数。 (2) 压射机构:按规定的速度推送压室内的金属液,并有足够的能量使之流经模具内的浇道和内浇口,进而填充入模具型腔,随后保持一定的压力传递给正在凝固的金属液,直至形成压铸件为止。在压射动作全部完成后,压射冲头返
16、回复位。 (3) 液压系统:为压铸机的运行提供足够的动力和能量。 4电气控制系统:控制压铸机各机构的执行动作按预定程序运行。 5零部件及机座:所有零部件经过组合和装配,构成压铸机整体,并固定在机座上。6其他装置先进的压铸机还带有参数检测、故障报警、压铸过程监控、计算机辅助的生产信息的存储、调用、打印及其管理系统等。 7辅助装置:根据自动化程度配备浇料、喷涂、取件等装置。铝合金与其它金属材料相比具有以下特点: (1)密度小: 铝合金的密度接近2.7克/立方厘米,约为铜的1/3。 (2)强度高: 铝合金的强度高。经过一定程度的冷加工可强化基体强度,局部牌号的铝合金还可以通过热处理进行强化处理。 (
17、3)导电导热性好: 铝的导电导热性能仅次于银、铜和金。 (4)耐蚀性好: 铝的外表易自然生产一层致密牢固的AL2O3保护膜,能很好的保护基体不受腐蚀。通过人工阳极氧化和着色,可获得良好铸造性能的铸造铝合金或加工塑性好的变形铝合金。 (5)易加工: 添加一定的合金元素后,可获得良好铸造性能的铸造铝合金或加工塑性好的变形铝合金。高压力和高速度是压铸中熔融合金充型过程的两个主要特点。压铸中常见的压射比压在几兆帕至几十兆帕范围内,有的甚至高达几百兆帕。其充型速度一般在0.5-120m/s范围内,它的充型时间很短,一般为0.01-0.2s,最短的仅为千分之几秒。因此,利用这种方法生产的零件尤其独特的优点
18、。可以得到m。因此,个别压铸件不需要经过机械加工或仅是个别部位加工即可使用。压铸的主要优点:(1)铸件的强度和外表粗糙度较高。由于压铸模的激冷作用,又在压力下结晶,因此压铸件外表层晶粒极细,组织致密,所以外表层的硬度和强度都比拟高。(2)生产率高。压力铸造的生产周期短,一次操作的循环时间约为5s-3min,这种方法适应于大批量生产。虽然压铸生产的优势很突出,但是它也有一些明显的缺点:(1)压铸件表层常存在气孔。这是由于液态合金的充型速度太快,性强中的气体很难完全排除,常以气孔形式存留在铸件中。因此一般压铸件不能进行热处理,也不适宜在高温条件下工作。这是由于加热温度高时,气孔内的气体膨胀,导致压
19、铸件外表鼓包,影响质量与外观。(2)压铸的合金类别和牌号有限制。目前只适用于锌、铝、镁等合金的压铸。对于某一种合金类别,由于压铸时的激冷产生剧烈收缩,因此也仅限与几种牌号的压铸。(3)压铸的生产准备费用高。由于压铸机本钱高,压铸模加工周期长、本钱高,因此压铸工艺仅适用于大批量生产。压力铸造CAE主要包括计算机辅助铸造过程模拟、工艺设计、盈利分析及缺陷预测等内容,其中铸造过程模拟是根底和核心。目前,铸造过程模拟研究主要集中在以下4个方面(1) 充型凝固模拟。其开展趋势是辅助设计浇注系统。(2) 缩孔缩松预测。这方面铸钢件的研究已比拟成熟。(3) 凝固过程应力模拟。主要针对铸件剩余应力和剩余变形进
20、行模拟,而液固共存时应力场数值模拟是应力模拟的核心,也是整个铸造过程模拟的难点,主要借助有限元分析技术。国内外不少数值模拟软件已经具有应力分析的功能。(4) 凝固过程微观组织模拟。微观组织模拟是一个复杂的过程,比凝固和充型过程模拟具有更大的困难。近年来各种微观组织模拟方法纷纷出现,已成为材料科学的研究热点之一。目前主要的模拟方法有确定性模拟、随机性模拟、相场模拟、介观尺度模拟方法等。现在使用的铸造过程模拟软件主要有芬兰的Cast CAE 4.0,美国的PAM-Cast Optic Cast and Flow Cast,德国的Magma soft 等,各有特点,各有侧重,但根本都可以完成充型模拟
21、、凝固分析、剩余应力和变形分析,有的也能对铸件缺陷和性能预测等内容进行分析,对铸件的显微组织分析。以上软件只要边界条件准确,分析精度根本能够到达要求。目前,国内有关低压铸造CAE技术的研究越来越多,关于其他压力铸造的却非常少。国内铝合金压铸CAE技术的研究还不成熟,在这方面的应用还比拟少,尤其是在填充、凝固方面涉及的较少,还需要做大量的工作。采用CAE模拟技术,可以缩短产品试制周期、降低本钱、提高材料利用率以及提高产品质量的稳定性。本文以铝合金压铸件进行压铸过程的数值模拟,通过计算机数值模拟展示铝合金液态充型的全过程,分析缺陷,改善不合理的工艺设计方案并优化主要的工艺参数,为类似铸件的进一步研
22、究和生产提供一些借鉴和参考。 本文开展铝合金平板压铸工艺设计以及充型过程的计算机模拟研究,通过模拟研究优化压铸工艺方案和主要的工艺参数,使得铸件减少卷气,浇缺乏或缩孔等缺陷,到达提高质量的目的,主要研究以下几个方面:介绍国内铝合金压铸行业的概况,铝合金铸件的成型方法以及CAE技术在压铸成型中的应用;平板件压铸工艺的选择和确定,主要有分型面的选择、浇注系统的设计、集渣包的设计以及其他工艺参数确实定等;利用软件对不同的压铸工艺方案进行充型模拟,并根据模拟结果分析充型过程对铸件的质量影响;优化方案,调整压铸工艺方案和主要的工艺参数。第二章 压铸铝合金平板件工艺设计2.1 铸件立体图所用零件为铝合金平
23、板,材料为铸ZL104铸造精度为CT7,铸件的平均壁厚为8mm,其立体图如图2-1. 2-1铸件立体图铝合金平板图的具体结构尺寸如图2-2 2-2零件图要从压铸工艺性的观点来审视分析产品零件的合金材料、形状结构、尺寸精度及其他特点。对那些不适合压铸的因素要予以排除使其合理化。只有在必要时才采用特殊的模具结构和特殊的工艺措施。诸如形成内侧凹的活动镶件、配用真空压铸系统等。对零件图进行工艺分析,一般要注意的问题列述如下:1合金种类及要求的技术性能;2尺寸精度及形位精度;3壁厚、壁的连接、肋和圆角;4分型、出模方向与出模斜度;5抽芯部位、有无型芯交叉和内侧凹;6推出方向、推杆位置;7小孔、深孔、螺纹
24、和齿的压铸;8铸入镶嵌件的装夹定位及金属的包覆;9图案、文字、符号和凸纹;10基准面和机械加工的部位;11外表外观;12特殊质量要求。 GB64l486?铸件尺寸公差?中规定了压力铸造生产的各种铸造金属及合金铸件的尺寸公差。此项国家标准等效采用IS08062l984?铸件尺寸公差制?。铸件尺寸公差的代号为CT。由于设计的零件是铝合金压铸件,应选取CT5CT7。查文献1表25可知:再根据此次设计零件的成产要求,所以公差等级选择CT7。2.3.2 铸孔 由于在实际生产中机械加工比拟麻烦,而且此零件对孔的要求并不是很高,为了节省时间,所以铸件的所有孔均采用铸造的方法。2.4 压铸机的选择*本课题设计
25、的压铸件在分型面的投影面积为?cm压铸件的重量为?kg,铝合金一般件的推荐压射比压为3050MPa,这里我们取40MPa,有参考文献?压铸模设计手册?第50页图3-5查出,选择压铸机的主要原那么是要考虑锁模力和压室的容量,我们这里采用常用的卧式冷室压铸机,其型号选用J1113G合理确实定分型面,不但能够简化压铸型的结构,还能保证铸件的质量。压铸模的分型面是指压铸模的定模和动模结合的外表。而模具上垂直于锁模力方向的结合面,即为根本分型面。 分型面的类型各种常见的分型面类型如图3-1所示。1选在铸件最大轮廓尺寸处,以便脱模。2尽可能地使压铸件在开模后留在动模局部3有利于浇注系统、溢流排气系统的布置
26、4保证压铸件的尺寸精度和外表质量5简化模具结构、便于模具加工6防止压铸机承受临界载荷7防止使用定模抽芯机构8应考虑压铸合金的性能对具体的铸件,在选择分型面的时候,要全面满足这些原那么是很难的,有时会发生矛盾,因此常常是满足最重要原那么的情况下,再适当考虑其他问题,分清主次,选择适宜的方案由于本文所述的平板件,底面是一个大的平面,从模具的成形性和可加工性,以及平板件结构考虑,选择底面大平面作为分型面,如图2-2,这样分型那么模具加工简单,出模也很方便。如此的分型面设计,有利于浇注系统和溢流系统的布置,浇口和溢流槽去除方便,铸件成型后外形美观,没有多余的留痕。综合考虑到这些因素和条件,平板件的分型
27、面就确定了。 2-2分型面浇注系统是金属液在压力作用下充填型腔的通道,浇注系统的设计直接影响着金属液在模型中的流动状态以及进入型腔的位置和方向,合理的浇注系统和集渣包是获得合格铸件的重要因素。只有浇注系统确定后才能确定压铸模的总体结构。设计浇注系统需考虑的因素:压铸件结构特点技术要求合金种类及其特性压铸机类型及特点压铸模浇注系统组成直浇道、横浇道、内浇口、余料我的第一种方案5个内浇口,内浇道与横浇道一体。如图2-3 2-3 带浇注系统的零件图 内浇口的设计主要是确定内浇口的位置、形状和尺寸。由于铸件的形状复杂多样,涉及的因素很多,设计时难以完全满足应遵循的原那么,内浇口的截面积目前尚无切实可行
28、的精确计算方法,因此进行内浇口设计时,经验是很重要的因素。一、内浇口位置选择依据:(1)保证金属液先充填型腔深处难以排气部位,防止过早封住分型面,使排气顺畅;(2)防止金属液正面冲击型芯和型腔;(3)少用分浇口,减少金属液汇流;(4)使流程尽量短,流向改变少;(5)考虑内浇口的去除。二、内浇口作用及设计内容:内浇口作用:根据压铸件的结构、形状、大小,将金属液以最正确流动状态引入型腔,以获得优质压铸件。设计内容:确定内浇道位置、形状和尺寸。三、内浇口设计的原那么:(1)有利于压力传递,一般设在压铸件厚壁处,有利于型腔排气。(2)薄壁复杂压铸件用较薄的内浇口,以保证较高的充填速度;一般结构压铸件,
29、用较厚内浇口,使金属液流动平稳。(3)金属液进入型腔后不能正面冲击型芯,以减少动能损耗,防止型芯冲蚀。(4)应使金属液充填型腔时的流程尽可能短,以减少金属液的热量损失:(5)内浇道的数量以单道为主,以防止多道金属液进入型腔后从几路集合,相互冲击,产生涡流、裹气和氧化夹渣等缺陷。(6)压铸件上精度、外表粗糙度要求较高且不加工的部位,不宜设置内浇道。(7)内浇道的设置应便于切除和清理四、内浇口截面积Ag计算达伏克对内浇道截面积和压铸件质量之间的关系提出的经验公式: 式中 Ag内浇口面积 V-压铸件的体积 由此可以得到平板件五、平均壁厚b的计算查?压铸模设计手册?第96页b= 式中:,为各个部位的壁
30、厚。 ,为对应部位壁厚的面积。经计算,压铸件的平均壁厚约为b=8mm。六、内浇口尺寸设计1、 内浇口厚度尺寸h计算 hg 0.5*相连的压铸件壁厚。 (2)h过小,浇口处合金液凝固过快,铸件内部组织疏松;h 过大,铸件轮廓不清,内浇口切除困难。由于已经计算出平均壁厚b,我们通过查表2-4,并综合要注意的要点,确定内浇口厚度尺寸h=4mm 表2-4 内浇口厚度的经验数据 单位:mm合金 压铸件壁厚3-66复杂简单复杂简单复杂简单与铸件壁厚之比/%锌合金20-40铝合金40-60镁合金40-60铜合金40-602、内浇口宽度B的计算由公式Ag=h*B得到 B=Ag/h=380/4=95mm3、内浇
31、口长度L2L3mm 综合考虑L=3mm七、单个內浇口的尺寸第一种方案内浇口的具体尺寸为:B=20mm L=3mm h=4mm横浇道是指从直浇道未端到内浇道口之间的通道。本次设计零件的横浇道选用梯形横浇道。一、横浇道的设计要点:(1)横浇道的截面积应从直浇道起到内浇口止,逐渐缩小,如在横浇道中出现截面积扩大的现象,金属液流过这里时那么会出现负压,由此必然会吸收分型面上的空气,增加金属液流动过程中的涡流。(2)横浇道应具有一定的厚度和长度,假设横浇道过薄,那么热量损失大;假设过厚时冷却速度缓慢,影响生产率,增大金属消耗。保持一定长度的目的,主要对金属液起到稳流和导向的作用。(3)横浇道截面积在任何
32、情况下都不应小于内浇口截面积。m。二、横浇道的形式及尺寸 (1)横浇道截面积的计算由?压铸模设计手册?第115页表4-28可知 Ar=(3-4)Ag 取Ar=3Ag式中 Ar横浇道的截面积,mm; Ag内浇口截面积,mm;由此可得每个横浇道的面积为2横浇道的尺寸计算 根据公式 式中 D-横交道深度或直径mm W-横浇道宽度mm Ar-横浇道截面积 ,-系数由?压铸模设计手册?表4-29可查的那么 取D=26mm. 取W=20mm.由此可以算出每个横浇道的具体尺寸位: D=26mm,W=20mm,L=20mm三、 横浇道与内浇口的连接方式把内浇道,横浇道设置在同一模面上,内浇道,横浇道都设置在动
33、模上,端面联接方式如图2-5所示。其剖面图如图2-6所示2-5横浇道与内浇口连接方式 2-6横浇道与内浇口剖面图卧式冷室压铸机直浇道一般由压铸机上的压室和压铸模上的浇口套组成,在直浇道上的这一段称为余料。一、直浇道设计要点:1)根据所需压射比压和压室充满度选定压室和浇口套的内径。2)浇口套的长度一般应小于压铸机压射冲头的跟踪距离,便于余料从压室中脱出。3)横浇道人口应开设在压室上部内径二分之二以上部位,防止金属液在重力作用下进人横浇道,提前开始凝固。4)分流器上形成余料的凹腔其深度等于横浇道的深度,直径与浇口套相等,沿圆周的脱模斜度约5。5)有时将压室和浇口套制成一体,形成整体式压室。内孔精度
34、好,压射时阻力小,但小,但加工较复杂,通用性差。6)采用深导人式直浇道,可以提高压室的充满度,减小深型腔压铸模的体积,当使用整体式压室时,有利于采用标准压室或现有的压室。m 二、直浇道尺寸确实定 根据以上要点可以确定最正确尺寸为: D=60mm,H=30mm在模型设计中必须将溢流槽和浇注系统作为一个整体来考虑。溢流槽的采用和设置是提高压铸件质量,消除局部紊流带来的缺陷的重要措施之一,有时还可以弥补由于浇注系统设计不合理而带来的铸造缺陷。其作用与效果主要决定于设置的部位,容量大小以及本身的结构形式等。溢流槽的总容积不少于压铸件体积的20%,小型铸件比值应更大。本设计选择的是梯形溢流槽,如图2-7
35、所示 2-7梯形溢流槽一、溢流槽的作用存储带有杂质和冷污的金属,也起到过渡排气的作用;容纳充填中形成的涡流和冷隔的金属液体;作为铸件存放、运输及加工时支撑、吊挂、装夹或定位的附加局部;对于分别处于动、定模型腔内的铸件,在包紧力接近相等时,为了防止铸件包紧在定模内,在动模上布置溢流槽,增大对型芯的包紧力,使铸件在开模时随动模带出;作为铸件出模时推杆推出的位置,防止铸件变形或在铸件外表留有推杆痕迹;转移缩松、缩孔、涡流裹气和冷隔部位。二、溢流槽的布置要点(1)对于金属液最先冲击的部位和内浇口两侧;(2)型芯反面金属集合处;(3)金属液最后填充的部位;(4)铸件局部厚壁处;(5)主横浇道的端部;(6
36、)大平面上容易产生缺陷集中的部位;其他排气条件不良的部位都应该布置溢流槽。三、溢流槽尺寸设计根据推荐的梯形溢流槽尺寸数据可以查出符合本零件的每个溢流槽尺寸为A=35mm,a=6mm,H=14mm,c=2mm,b=10mm,B=35mm,A 溢流槽长度B 溢流槽宽度a溢流口长度b溢流口宽度c溢流口厚度如图2-8为溢流槽的截面 2-8溢流槽截面示意图 本文采用梯形溢流槽进行设计,溢流槽布置在分型面上。为使溢流槽能充分发挥作用到达其应有的效果,不致消耗过多的金属,增加投影面积,影响铸件尺寸精度,降低充填型腔的有效压力,甚至影响和打乱充填形态或引起其他反作用,应在布置溢流槽时慎重考虑。一般在模具设计时
37、,事先在准备布置集渣包处保存一定的余地。试压验证后,观察铸件上金属液的流痕和缺陷产生的形态,最后确定合理的布局和容量。因此在第一种方案中先不设置溢流槽,待确定后在更加准确的设置。图2-7为优化后的溢流槽布置方案方案 2-7溢流槽在分型面上第三章:计算机数值模拟3.1计算机辅助设计(CAD)技术及常用CAD软件计算机辅助设计(CAD:Computer Aided Design)技术是以计算机、外围设备及其系统软件为根底,包括二维绘图设计、三维几何造型设计、有限元分析(FEA)及优化设计、数控加工编程(NCP)、仿真模拟及产品数据管理等内容。随着Internet/Intranet网络和并行、高性能
38、计算及事务处理的普及,异地、协同、虚拟设计及实时仿真也得到广泛应用。常用CAD软件:1. 国外软件: AutoCAD、Cimatron、Solidedge、UG、I-DEAS、Solidworks、Pro/ENGINEER。 2. 国内软件: CAXA电子图板和CAXA制造工程师、 开目CAD、GS-CAD98、金银花系统、高华CAD。3.2 Pro/E的功能简介本文采用的三维建模软件为Pro-EPro/EPro/Engineer操作软件是美国参数技术公司Parametric Technology Corporation,简称PTC的重要产品。在目前的三维造型软件领域中占有着重要地位,并作为当
39、今世界机械CAD/CAE/CAM领域的新标准而得到业界的认可和推广,是现今最成功的CAD/CAM软件之一。 Pro/E第一个提出了参数化设计的概念,并且采用了单一数据库来解决牲的相关性问题。另外,它采用模块化方式,用户可以根据自身的需要进行选择,而不必安装所有模块。Pro/E的基于特征方式,能够将设计至生产全过程集成到一起,实现并行工程设计。它不但可以应用于工作站,而且也可以应用到单机上。Pro/E采用了模块方式,可以分别进行草图绘制、零件制作、装配设计、钣金设计、加工处理等,保证用户可以按照自己的需要进行选择使用。1 参数化设计和特征功能 Pro/Engineer是采用参数化设计的、基于特征
40、的实体模型化系统,工程设计人员采用具有智能特性的基于特征的功能去生成模型,如腔、壳、倒角及圆角,您可以随意勾画草图,轻易改变模型。这一功能特性给工程设计者提供了在设计上从未有过的简易和灵活。2 单一数据库 Pro/Engineer是建立在统一基层上的数据库上,不象一些传统的CAD/CAM系统建立在多个数据库上。所谓单一数据库,就是工程中的资料全部来自一个库,使得每一个独立用户在为一件产品造型而工作,不管他是哪一个部门的。换言之,在整个设计过程的任何一处发生改动,亦可以前后反响在整个设计过程的相关环节上。例如,一旦工程详图有改变,NC数控工具路径也会自动更新;组装工程图如有任何变动,也完全同样反
41、响在整个三维模型上。这种独特的数据结构与工程设计的完整的结合,使得一件产品的设计结合起来。这一优点,使得设计更优化,成品质量更高,产品能更好地推向市场,价格也更廉价。3.3 Pro/E三维建模过程1绘制零件整体框架,拉伸出一个平板模型;2草绘零件平面,拉伸出各个槽;3整体平板绘制完毕,挖出平面上的大小孔;4草绘反面的根本图形,拉伸出零件的各个特征;5完成各个部位倒角;6零件图绘制完成;7绘制零件的浇注系统;8绘制零件的排溢系统;9绘制浇注系统排溢系统倒角;10完成三维建模。 HZCAE/ Inter CAST中国铸造领域最著名的模拟分析系统,是分析和优化铸件铸造工艺的重要工具,它以铸件充型过程
42、、凝固过程数值模拟技术为核心对铸件进行铸造工艺分析。 目前“HZCAE集成化软件系统在国内市场占有率达80%左右,首钢、鞍钢、一汽集团、东风汽车公司、浙江大学、航天三院等220多家工矿企业、科研院校使用该系统,几年来为企业带来直接经济效益两亿多元。德国西门子公司指定该系统是中国出口到该公司铸件的首选模拟软件;丰田汽车公司日本总部采用该系统对近10个关键铸件的工艺进行模拟分析优化;新家坡马来西亚天鹅金工已购置该系统,HZCAE是目前唯一走出国门的铸造模拟分析系统。铸造材质:铸钢、球铁、灰铁、铸铝、铸铜、铸镁、铸锌等各种各类铸造合金 铸造方式:砂型、金属型、熔模、低压、压力、倾斜铸造、钢锭模铸造等
43、 分析内容:冷却凝固过程、流动充型过程、充型换热耦合过程 缺陷预测:夹渣、卷气、冷隔、浇缺乏、缩孔、缩松 一、前置处理:HZCAE的前置处理是模拟过程的准备工作,它实现了CAD模型的导入,利用STL预览检查三维造型是否正确,有限差分网格的划分。另外,还可以通过HZCAE提供的CAD功能对实体造型进行简单修改。 三维造型平台用户可任选,绝大局部三维造型系统包括CATIA、PRO/E、UG、SOLIDEDGE、SOLIDWORKS、I-DEAS、AutoCAD、MDT、Inventor、CAXA、金银花等均能与本系统顺利接口。 自动网格剖分、速度快、稳定性好、容错能力强,一般中等复杂程度铸件,剖分
44、千万个网格几分钟内完成; 异位网格计算功能,即流动基于一套网格,凝固基于另一套网格,同时不影响计算精度 全自动非均匀网格剖分,智能化识别壁厚,薄壁处网格变细,厚大部位自动采用粗大网格,大大提高分析效率 全自动序列剖分,按给定规那么,全自动生成一系列网格尺寸不同的剖分结果,满足客户的各种需要 高性能的容错与网格修补功能自动修补三位CAD数据交换引起的错误,智能化修正线接触网格二、 计算分析:合金属性参数,铸件、铸型、砂芯等材料的物性参数,各种材质间的界面导热系数,用于铸件的充型过程、凝固过程以及流动与传热的耦合计算。 能够进行低压铸造、压铸、金属型铸造的多周期、多阶段全过程的分析; 可以对包括水
45、、油、气等不同冷却介质的各种复杂冷却工艺进行优化分析; 能够模拟多个不同规格的浇包同时浇注的的复杂浇注过程; 能够模拟补浇工艺、点冒口过程;应用了重力补缩技术,可以直接准确模拟缩孔缩松的形成过程,实现了缩孔缩松的位置、形状和大小的定量的模拟;在微机上实现实用的流场分析、流动与温度耦合计算,单元数可达数百万个。流动场、耦合场分析技术在国内首屈一指;三、后置处理:(1)后处理采用最新可视化技术、多媒体技术,丰富、直观、生动,任意实时缩放、任意实时旋转、任意实时剖切。可自动生成X射线透视图、凝固色温图、温度梯度图、铸件结构图、铸型系统装配图、流动向量图、填充体积图、压强分布图、充型温度分布图等。颜色
46、随意调整、画面直接打印;(2)分析结果三维动画自动合成,动画演示直观准确,透彻明了。动态过程完整细腻;后处理中实时动态显示技术、动画显示技术到达国际同类软件的先进水平;(3)数值鼠标技术,HZCAE特有。在各种函数三维分布图形画面上,伴随鼠标移动,在鼠标光标的延伸空间,以数字方式即时刷新显示鼠标所指单元相应的几何、物理函数值,或区域极值,或区域统计值,包括:1、鼠标所指单元的温度、压力、速度、凝固时间、Niyama函数、缩松孔隙率等函数值;2、鼠标所指点所在的每个液相连通区域,每个缩孔连通孔腔,每个缩松连续区域等的体积,以及相关函数值在相应区域的极值等;3、鼠标所指点的尺寸坐标、单元坐标位置、
47、单元尺寸大小,也包括STL图形上任意点的三维尺寸坐标位置。自动生成任意点温度曲线,鼠标直接点取、方便灵活;铸件铸型CT剖片,各种方向,任意剖片,直接明了;孤立区全自动搜索,自动统计,最终缺陷预测3.5 第一套方案数值模拟分析 由于第一种方案设计并不知道金属液的具体流向,因此溢流槽的设计变得有点盲目性,为了节省模拟时间第一次模拟先不设置溢流槽,在模拟完成后,分析模拟结果,看在哪些部位容易出现缺陷和确定最后凝固的部位,最后再设置溢流槽,这样不仅可以节省模拟时间,也使得溢流槽的设置更加准确。具体立体图如图3-1 3-1第一套方案图3.5.1 几何模型的建立 首先将铸件、浇注系统、溢流槽等三维数字模型
48、输出成STL文件,分别导入到华铸CAE软件的前处理模块进行网格划分。然后设定铸件的材质、初始值条件、热传导条件、浇口尺寸等工艺参数。在压铸过程中,压铸工艺参数有压力、充填速度、金属液充填特性和合金的温度等,这些参数影响到金属液填充和最终铸件质量。在应用华铸CAE进行分析时,首先设定这些参数模拟生产情况下的铝合金液压铸充填、凝固过程。方案一:压力模拟结果如图3-2 a c d e 图 3-2根据以上充型压力模拟变化可以看出,充型过程中横浇道的充型压力较大,特别是中间部位,压铸零件整体充型压力较低,趋向一致,充型也较为平稳,起始充型压力比拟大,到后面,充型趋于平稳,压力也逐渐变小。速度模拟结果图:
49、 c e 图3-3根据以上充型速度模拟图可以看出来,整体充型速度一致,开始时,浇注系统内的液体充型速度较快,渐渐的,充型速度趋于平稳一致,在一些拐弯处和零件的较大的平面处,充型速度较其他位置要快。由速度充型过程分析,由图3-8可以看出在内浇口之间容易出现集气的缺陷,根据图3-9分析得到在零件的右侧由于其他部位已经充满,留有一局部最后充型,这样会形成集气,卷气等缺陷;图3-10到图3-13充型过程相对稳定;由图3-12可以确定最后充型的过程。 第四章 浇注方案的优化:1、 在内浇口设计上,我们应遵循尽可能少的原那么,由于内浇口过多,会导致较多的金属液支流,在不同方向上的金属液相碰撞时会引起卷气、
50、缩孔、缩松等缺陷;2、 内浇口相距较近时会引起两个内浇口之间的地方出现集气的缺陷,这种缺陷由于不能再内浇口之间布置溢流槽,所以并不能消除此缺陷;3、 由于最后凝固的地方肯定会出现集气的缺陷,所以我们应该在最后凝固的地方设计溢流槽,是缺陷集中在溢流槽内。 根据以上分析我又重新设计浇注系统以及溢流槽,方案2采用两个内浇口,内浇口与直浇道的连接方法与方案一一致,在主横浇道末端都设有一个圆形的小槽,防止金属液流速过快冲击浇注系统,引起卷气等缺陷,方案如图4-1所示 图4-1压力模拟结果如图4-2: a b c 充型s时的速度场分布 d e f 图4-2速度模拟结果如图4-3: a b c d e f
51、图4-3从图4-8可知,金属液从浇注系统流出向两侧填充;图4-9显示,金属液继续向两侧逐渐充型;由图4-10金属液充型图可知,在零件的左侧可能有少量的地方会出现集气现象;由图4-11显示,金属液开始充填零件的上部位,充型过程显示良好;由图4-12显示,金属液在零件的左上部为已经开始填充溢流槽,由此可以把左侧充型的缺陷都集中在溢流槽内,这正是设计最初的目的,结果符合要求。由图4-12显示零件的由上部位也开始填充溢流槽,其他部位已经充型完毕,这样说明,最后填充的部位是溢流槽,符合设计目的,缺陷将集中在溢流槽内,其他部位将无明显缺陷。4.3 方案评估相比拟5个内浇口的方案与优化后的方案:优化后采用2
52、个内浇口,这样防止了在内浇口之间存在集气的缺陷,同时也防止了由于内浇口过多,使得金属液流向复杂,难以控制最后充型的地方,对于设置溢流槽存在较大困难,同样也防止了由于流向不同的金属液相互冲击造成的卷气等缺陷。虽然优化后的方案在一些地方也有可能出现集气的缺陷。但相比拟而言,优化后的方案出现的缺陷已经大大降低,所以采用优化后的方案作为最终方案进行压铸。第五章 结论本文针对铸钢件铸造工艺问题,用计算机模拟的方式对压铸铝合金平板方案工艺参数进行了科学的优化设计。利用Pro/E和华铸CAE对铝合金平板充型的整个过程进行了数值模拟及模拟结果分析研究,探索出了较为理想的工艺。而且改良了铝合金。平板件原生产工艺
53、,实现了消除压铸缺陷,提高产品质量的目标。利用CAD/CAE仿真技术的优势,在不消耗实际生产所需的人力、物力、财力和时间的前提下,对计算机应用技术如何指导铸造生产进行了较为全面探索,并获得了以下研究成果:(1)在设置内浇口时,要尽可能少,内浇口之间的距离不能太小,内浇口要尽可能设置在分型面上;(2)横浇道的截面积从直浇道起至内浇口应逐渐减小,一般出口处截面比进口处小10-30%;(3)溢流槽要设置在最后充型的部位,使缺陷集中在溢流槽内。 总之,将计算机CAD/CAE技术应用在铸造工业中,可以快速、准确、低本钱地研究压铸产全过程,采用这项技术对于彻底改变压铸艺方案制订中的盲目性、确保铸件质量、提
54、高铸造生产率乃至推动铸造技术进步具有举足轻重的作用。 致 谢本科就要毕业了,四年匆匆,一眨眼之间就过去了,犹如白驹过隙一般。经过几个月的查资料、整理材料,工艺设计、写说明书,今天终于可以顺利完成设计。想了很久,要写下这一段谢辞,表示可以进行毕业辩论了,自己想想求学期间的点点滴滴涌上心头,时光匆匆飞逝,四年的努力与付出,随着毕业设计的完成,终于让学生的大学生活,得以画上完美的句号。设计得以完成,首先要谢谢李萍老师,因为设计是在老师的悉心指导下完成的。老师渊博的专业知识,严谨的治学态度,精益求精的工作作风,诲人不倦的高尚师德,严以律己、宽以待人的崇高风范,朴实无华、平易近人的人格魅力对我影响深远。我也要感谢研究生师兄的无私帮助,每每遇到困难,他都会不厌其烦的进行指导,是我在设计过程中学到了许多知识。本设计从选题到完成,每一步都是在李老师和研究生的指导下完成的,倾注了他们大量的心血。在此,谨向李老师表示崇高的敬意和衷心的感谢。另外,要感谢在大学期间所有传授我知识的各位老师,一起努力的同学,谢谢给我的帮助和支持。
- 温馨提示:
1: 本站所有资源如无特殊说明,都需要本地电脑安装OFFICE2007和PDF阅读器。图纸软件为CAD,CAXA,PROE,UG,SolidWorks等.压缩文件请下载最新的WinRAR软件解压。
2: 本站的文档不包含任何第三方提供的附件图纸等,如果需要附件,请联系上传者。文件的所有权益归上传用户所有。
3.本站RAR压缩包中若带图纸,网页内容里面会有图纸预览,若没有图纸预览就没有图纸。
4. 未经权益所有人同意不得将文件中的内容挪作商业或盈利用途。
5. 装配图网仅提供信息存储空间,仅对用户上传内容的表现方式做保护处理,对用户上传分享的文档内容本身不做任何修改或编辑,并不能对任何下载内容负责。
6. 下载文件中如有侵权或不适当内容,请与我们联系,我们立即纠正。
7. 本站不保证下载资源的准确性、安全性和完整性, 同时也不承担用户因使用这些下载资源对自己和他人造成任何形式的伤害或损失。