提高三坐标测量机测量螺纹孔位置度精度的方法
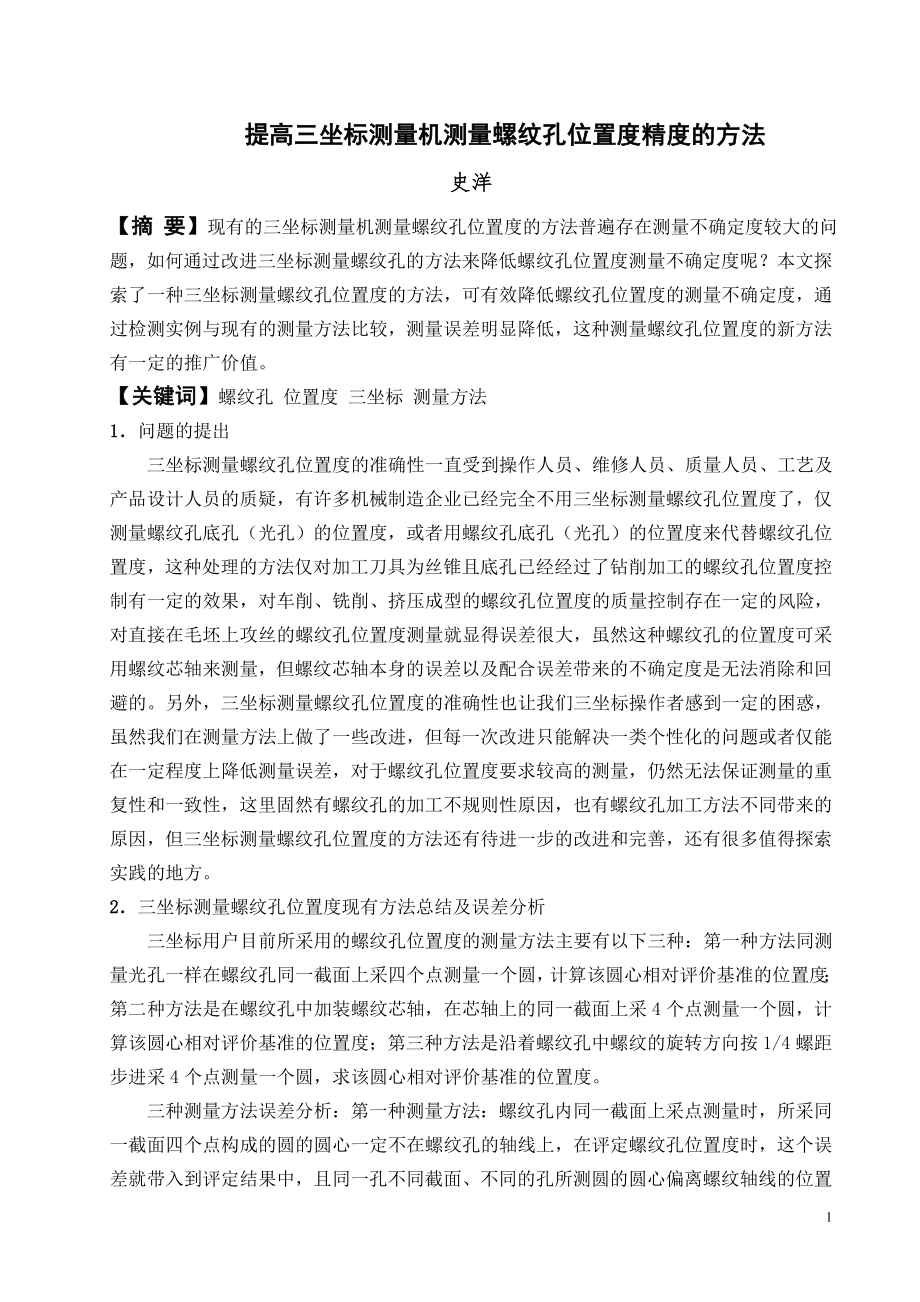


《提高三坐标测量机测量螺纹孔位置度精度的方法》由会员分享,可在线阅读,更多相关《提高三坐标测量机测量螺纹孔位置度精度的方法(4页珍藏版)》请在装配图网上搜索。
1、提高三坐标测量机测量螺纹孔位置度精度的方法史洋【摘 要】现有的三坐标测量机测量螺纹孔位置度的方法普遍存在测量不确定度较大的问题,如何通过改进三坐标测量螺纹孔的方法来降低螺纹孔位置度测量不确定度呢?本文探索了一种三坐标测量螺纹孔位置度的方法,可有效降低螺纹孔位置度的测量不确定度,通过检测实例与现有的测量方法比较,测量误差明显降低,这种测量螺纹孔位置度的新方法有一定的推广价值。【关键词】螺纹孔 位置度 三坐标 测量方法1问题的提出 三坐标测量螺纹孔位置度的准确性一直受到操作人员、维修人员、质量人员、工艺及产品设计人员的质疑,有许多机械制造企业已经完全不用三坐标测量螺纹孔位置度了,仅测量螺纹孔底孔(
2、光孔)的位置度,或者用螺纹孔底孔(光孔)的位置度来代替螺纹孔位置度,这种处理的方法仅对加工刀具为丝锥且底孔已经经过了钻削加工的螺纹孔位置度控制有一定的效果,对车削、铣削、挤压成型的螺纹孔位置度的质量控制存在一定的风险,对直接在毛坯上攻丝的螺纹孔位置度测量就显得误差很大,虽然这种螺纹孔的位置度可采用螺纹芯轴来测量,但螺纹芯轴本身的误差以及配合误差带来的不确定度是无法消除和回避的。另外,三坐标测量螺纹孔位置度的准确性也让我们三坐标操作者感到一定的困惑,虽然我们在测量方法上做了一些改进,但每一次改进只能解决一类个性化的问题或者仅能在一定程度上降低测量误差,对于螺纹孔位置度要求较高的测量,仍然无法保证
3、测量的重复性和一致性,这里固然有螺纹孔的加工不规则性原因,也有螺纹孔加工方法不同带来的原因,但三坐标测量螺纹孔位置度的方法还有待进一步的改进和完善,还有很多值得探索实践的地方。2三坐标测量螺纹孔位置度现有方法总结及误差分析 三坐标用户目前所采用的螺纹孔位置度的测量方法主要有以下三种:第一种方法同测量光孔一样在螺纹孔同一截面上采四个点测量一个圆,计算该圆心相对评价基准的位置度;第二种方法是在螺纹孔中加装螺纹芯轴,在芯轴上的同一截面上采4个点测量一个圆,计算该圆心相对评价基准的位置度;第三种方法是沿着螺纹孔中螺纹的旋转方向按1/4螺距步进采4个点测量一个圆,求该圆心相对评价基准的位置度。三种测量方
4、法误差分析:第一种测量方法:螺纹孔内同一截面上采点测量时,所采同一截面四个点构成的圆的圆心一定不在螺纹孔的轴线上,在评定螺纹孔位置度时,这个误差就带入到评定结果中,且同一孔不同截面、不同的孔所测圆的圆心偏离螺纹轴线的位置有较大的差异,这就是造成螺纹孔位置度测量重复性差、散差大等测不准的主要原因。第二种测量方法是因为螺纹芯轴将螺纹孔轴线延长了,且螺纹配合误差的存在,螺纹芯轴本身的误差都是造成螺纹孔位置度测不准的原因。第三种方法是沿螺纹孔螺纹旋向方向步进采点,虽然保证了所采点构建圆的圆心理论上在螺纹孔轴线上,评定位置度结果较前两种测量方法误差较小,但由于采集的四个点不在同一截面上,轴线稍有倾斜就会
5、带来较大的采点误差存在,这些误差都将带入到螺纹孔位置度的评价结果中。以上三种螺纹孔位置度的三坐标测量方法广泛应用于汽车、发动机等机械加工制造行业。如果产品要求的螺纹孔位置度公差较大,如位置度公差大于0.2或者位置尺寸公差大于0.1,三种测量方法的测量结果也可以近似的反映出螺纹孔位置的加工质量,尤其当螺纹孔直径在M6左右及以下,螺距小于等于1时,测量误差还是可以接受的。尤其是第三种测量方法测量误差相对其它两种测量方法误差还是比较小的,而且也适合测量螺纹孔直径较大或者螺距较大的孔的位置度。但当螺纹孔位置度公差要求小于0.2,或者位置尺寸公差的要求小于0.1时,以上三种测量方法就显得测量误差较大,尤
6、其不适合做设备能力值和工序能力值的测量。3螺纹孔位置度新的测量方法的探索 准确测量螺纹孔位置度的关键就是在构建螺纹孔轴线时要保证采点误差最小,以便能确保采点构建的轴线与螺纹孔加工的轴线重合,其次要保证评定螺纹孔位置度时,评定点要固定在同一截面上。我们一直在探索和尝试一些新的测量方法来降低螺纹孔位置度的测量评价误差,保证测量结果的准确性。下面是我们最新应用的一种测量螺纹孔位置度的方法,测量误差明显小于沿着螺纹孔中螺纹的旋转方向按1/4螺距步进采四个点测量一个圆,评价该圆圆心相对基准的位置度的测量方法。3.1 新的螺纹孔位置度的测量方法的测量原理简述新的螺纹孔位置度的测量方法测量原理为直接触测螺纹
7、孔内两个相距螺距整数倍的圆柱,用2个圆柱的质心点构建螺纹孔轴线。每个圆柱面采8个点,分两层,每层四个点,两层的间距为1/2螺距。用这种方法构建的螺纹孔轴线误差明显较第三种方法(沿着螺纹孔螺纹的旋转方向按1/4螺距步进采4个点测量一个圆)小,同时我们计算出这个螺纹孔轴线与攻丝孔端面的交点,求交点相对评价基准的位置度,这样就保证了评定螺纹孔位置度时,评定点固定在同一截面上。3.2新的螺纹孔位置度的测量方法的测量与评定程序 新的螺纹孔位置度的测量方法的具体测量和构建评定过程如下: 如图1,测量螺纹孔端面的PL1面,把PL1面作为第一方向并找正,建立零件坐标系A1:在零件坐标系A1下,测量螺纹孔,测量
8、方向始终沿着PL1面的法线正方向;在每个螺纹孔中测量2个圆柱面,一个靠近螺纹孔进口端,一个靠近螺纹孔出口端,两个圆柱面的间距为螺距的整数倍;每个圆柱面采8个点,分两层,每层4个点,两层的间距为1/2螺距。4螺纹孔位置度新的测量方法的应用实践 为了验证新的螺纹孔位置度的测量方法是否可靠,我们将这种测量方法应用在某零件螺纹孔的位置度的检测上。我们进行了两种测量方法的对比测量实验,根据两种测量方法原理编辑了两个三坐标测量程序,分别将同一个零件测量五次,每次测量重新装夹零件。其中4个螺纹孔的位置度的测量结果如表1、表2,其5次测量结果的分布图如图2、图3。表1:按方法3的测量方法:1个零件4个孔5次测
9、量结果统计表 单位:mm方法3:按1/4螺距步进采4点构建一个圆,求该圆心的位置度孔号114孔115孔116孔117孔位置度公差10.00560.01110.01770.01090.0220.00650.00960.01590.00580.0230.00670.00960.01270.00690.0240.00690.01080.01060.00190.0250.00640.00850.01490.00480.02表2:按新的测量方法1个零件4个孔5次测量结果统计表 单位:mm新的测量方法:采2个圆柱,求2个圆柱质心的连线与螺纹孔端面的交点的位置度孔号114孔115孔116孔117孔位置度公差
10、10.01190.01160.01020.01380.0220.01020.01350.01110.01520.0230.00960.01220.01030.01560.0240.00990.01250.01060.01670.0250.00980.01190.010.01550.02分布图如下: 图2:按方法3的测量方法1个零件4个孔5次测量结果分布图图3:按新的测量方法1个零件4个孔5次测量结果分布图通过图2、图3的对比,我们可以发现下列规律: 按新的测量方法测量的同一个孔的位置度,5次测量结果散差明显小于方法3的测量结果; 按新的测量方法测量同一个零件4个孔的位置度,测量结果的发散区间明
11、显小于方法3的测量结果。5结论 新的螺纹孔位置度的三坐标测量方法保证了螺纹孔轴线构建的准确性,保证了螺纹孔位置度的评定点始终在同一截面的固定性,该测量方法保证了螺纹孔位置度的测量总误差小于0.02,。同一个零件的同一个螺纹孔,位置度的测量重复性好;连续加工的不同零件,相同编号的螺纹孔位置度测量一致性好;同一把刀具加工的不同螺纹孔,位置度测量结果分散性小。因此,新的螺纹孔位置度的测量方法测量结果可靠、误差较小。这种测量方法还可应用于螺纹孔位置尺寸、螺纹孔轴线的垂直度、平行度、倾斜度等螺纹孔所有位置公差的测量,也可推广应用于具有螺纹轴类零件等外螺纹轴线的垂直度、平行度、倾斜度等螺纹零件的位置公差的测量。参考资料: 1 三坐标测量机 1999年8月 张国雄 2 机械设计手册 2008年4月 成大先 3 形位公差与检测技术 2009年1月 陈山弟4
- 温馨提示:
1: 本站所有资源如无特殊说明,都需要本地电脑安装OFFICE2007和PDF阅读器。图纸软件为CAD,CAXA,PROE,UG,SolidWorks等.压缩文件请下载最新的WinRAR软件解压。
2: 本站的文档不包含任何第三方提供的附件图纸等,如果需要附件,请联系上传者。文件的所有权益归上传用户所有。
3.本站RAR压缩包中若带图纸,网页内容里面会有图纸预览,若没有图纸预览就没有图纸。
4. 未经权益所有人同意不得将文件中的内容挪作商业或盈利用途。
5. 装配图网仅提供信息存储空间,仅对用户上传内容的表现方式做保护处理,对用户上传分享的文档内容本身不做任何修改或编辑,并不能对任何下载内容负责。
6. 下载文件中如有侵权或不适当内容,请与我们联系,我们立即纠正。
7. 本站不保证下载资源的准确性、安全性和完整性, 同时也不承担用户因使用这些下载资源对自己和他人造成任何形式的伤害或损失。