底座加工工艺及加工孔夹具设计课程设计说明书
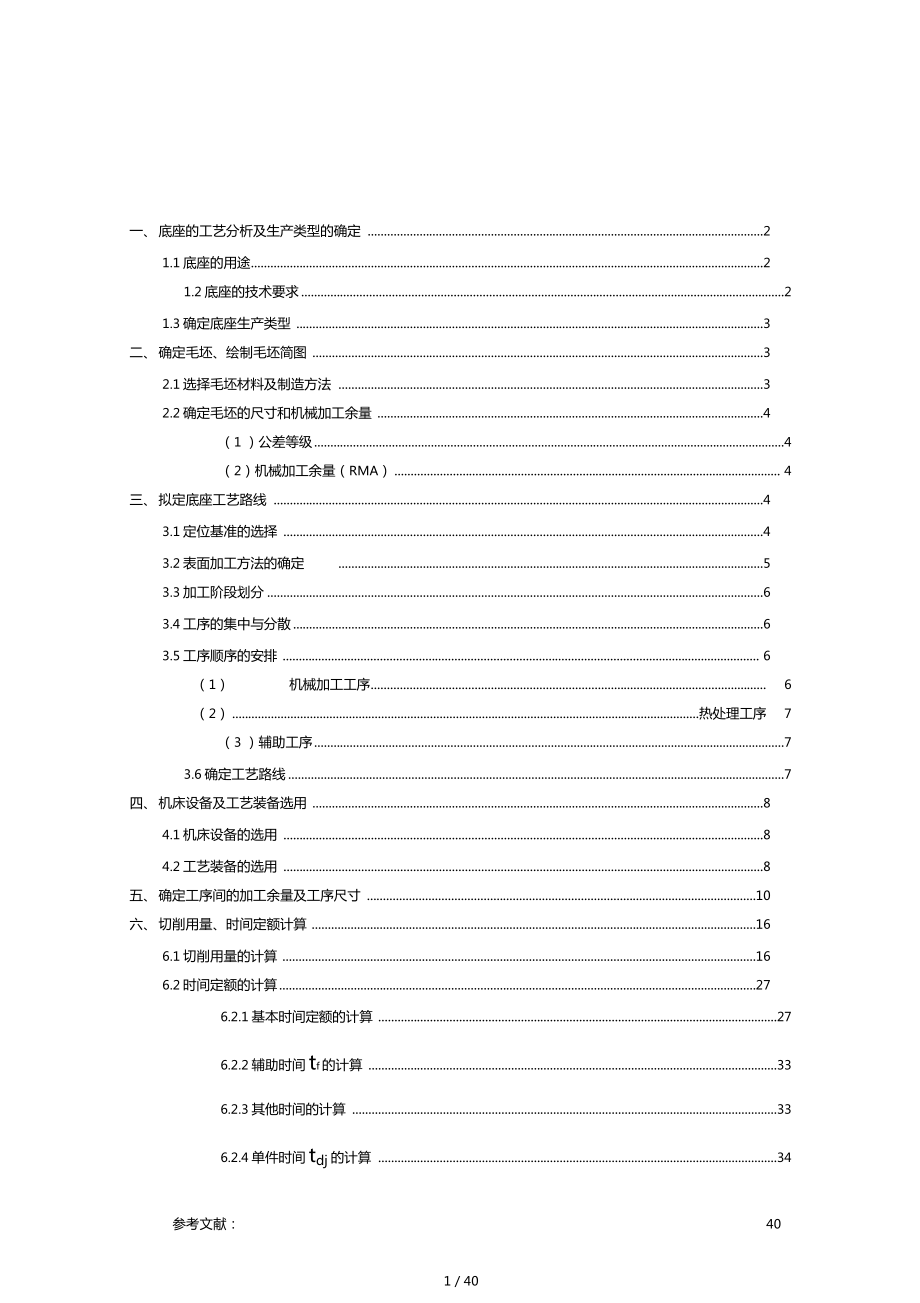


《底座加工工艺及加工孔夹具设计课程设计说明书》由会员分享,可在线阅读,更多相关《底座加工工艺及加工孔夹具设计课程设计说明书(41页珍藏版)》请在装配图网上搜索。
1、一、底座的工艺分析及生产类型的确定 21.1底座的用途21.2底座的技术要求21.3确定底座生产类型 3二、确定毛坯、绘制毛坯简图 32.1选择毛坯材料及制造方法 32.2确定毛坯的尺寸和机械加工余量 4(1 )公差等级4(2)机械加工余量(RMA) 4三、拟定底座工艺路线 43.1定位基准的选择 43.2表面加工方法的确定53.3加工阶段划分63.4工序的集中与分散63.5工序顺序的安排 6(1)机械加工工序6(2)热处理工序7(3 )辅助工序73.6确定工艺路线7四、机床设备及工艺装备选用 84.1机床设备的选用 84.2工艺装备的选用 8五、确定工序间的加工余量及工序尺寸 10六、切削用
2、量、时间定额计算 166.1切削用量的计算 166.2时间定额的计算276.2.1基本时间定额的计算 276.2.2辅助时间tf的计算 336.2.3其他时间的计算 336.2.4单件时间tdj的计算 34七、夹具设计357.1夹具的作用357.2夹具类型选用 357.3确定定位方案 357.4定位误差的计算 357.4确定导向装置377.5确定夹紧机构 377.6其他装置的确定38八、设计体会394、底座的工艺分析及生产类型的确定1.1底座的用途底座如图1.1所示,是用于支撑和连接若干部件的基础零件图1.1底座三维图1.2底座的技术要求表1-2底座零件技术要求表加工表面尺寸/mm表面粗糙度R
3、a/m底座前后端面856.3* 32孔内表面 3212.5底座左右端面10812.5底座上端面 443.23xM8孔上表面683.2* 20孔 203.21.3确定底座生产类型由于底座生产纲领为10000件/年,即N=10000件/年。用PRO/E绘图软件测出该底座体积V=673510m2,已知灰铸铁HT200的密度二=7.2g/cm,则此底座零件质量 m=x V =7.2g/cm x 673.510cm2 =4849.272g=4.849kg。由查【卩表1-3知,底座属轻型零件;由表1-4 知,该底座的生产类型为大批生产。二、确定毛坯、绘制毛坯简图2.1选择毛坯材料及制造方法本课题中选择铸件
4、毛坯,材料为灰铸铁HT200灰铸铁是碳钢的基体加片状石墨,有良好的铸造性能、减震性、耐磨性和切削性,较 低的缺口敏感性。由于是大批生产,故选用砂型机器造型。此方法生产率高、铸件 精度高、表面质量与机械性能均好2.2确定毛坯的尺寸和机械加工余量(1)公差等级根据该零件的生产类型及毛坯材料由【2】表2-28 (摘自GB/T6414-1999)确定该零件毛坯铸件的公差等级 CT=1Q(2)机械加工余量(RMA)由【3】表1-6确定该铸件的机械加工余量等级为 G级,由于砂型 铸造孔的加工余量需降低一级,故孔的机械加工余量等级为F级。由【3】表1-7知,零件左右端面基本尺寸为108mm则机械加工余 量为
5、4mm双侧加工;上下端面基本尺寸为 171mm则机械加工余量 为5mm单侧加工;3X M8孔上表面基本尺寸为6mm则机械加工余 量为3.5mm单侧加工;前后端面基本尺寸为85mm则机械加工余量 为2.5mm双侧加工; 32孔基本尺寸为32mm则机械加工余量为 3mm双侧加工。由以上数据绘出底座毛坯图,见附图(1)底座毛坯图。三、拟定底座工艺路线3.1定位基准的选择定位基准有粗基准和精基准之分, 通常先确定精基准,然后在确定粗基准。精基准的选择:考虑到要保证零件的加工精度和装配准确方便,选择 32孔和前端面作为精基准,符合“便于装夹”原则。零件上很多表面都可以采用作为基准进行加工, 即遵循了 “
6、基准统一”的原则。 该底座的设计基准是 32孔的中心轴线,实现了设计基准和工艺基准 的重合,选择前端面作为精基准也同样实现了“基准重合”的原则。 选择前端面作为精基准,夹紧可作用在后端面上,夹紧稳定可靠。粗基准的选择:作为粗基准的表面应该平整,没有飞边、毛刺或 其他表面缺陷。选择 70外圆面和后端面作为粗基准。采用70外圆面定位加工 32内孔,可保证 32孔壁均匀;采用后端面作为粗 基准加工前端面可以为后续工序准备好精基准。3.2表面加工方法的确定表3-2底座零件各表面加工方案加工表面尺寸/mm表面粗糙度 Ra/ m加工方案备注底座前后端面856.3粗铣表1-8* 32孔内表面 3212.5钻
7、表1-7底座左右端面10812.5粗铣表1-8底座上端面 443.2粗铣-半精铣表1-83X M8孔上表面683.2粗铣-半精铣表1-8*20孔 203.2钻-扩-铰表1-73.3加工阶段划分该底座加工质量要求不高,可将加工阶段划分为以下两个阶段:粗加工阶段:高效的切除各加工表面上的大部分余量,并加工出精基准。半精加工阶段:消除粗加工后留下的误差,使其达到一定的精度。3.4工序的集中与分散选用工序集中原则安排底座的加工工序。该底座的生产类型为大批生产,可以采用通用机床配以专用夹具,以提高生产率;而且运用 工序集中原则使工件的装夹次数少, 不但可以缩短辅助时间,而且由 于在一次装夹中加工了许多表
8、面,有利于保证各加工表面的之间的相 对位置精度要求。3.5工序顺序的安排(1)机械加工工序1)遵循“先基准后其他”原则,首先加工精基准一一 ?32孔和前端 面。2)遵循“先粗后精”原则,先安排粗加工工序,后安排精加工工序。3)遵循“先主后次”原则,先加工主要表面一一?32H11孔和前端面, 后加工次要表面一一上端面等。4) 遵循“先面后孔”原则,先加工底座前端面,再加工?32H11孔。(2) 热处理工序机械加工完成后安排退火工序,消除内应力。(3) 辅助工序精加工后安排检验工序,切削加工后安排去毛刺、清洗工序3.6确定工艺路线零件的加工路线就是把加工工件所需的各种工序科学合理的按 照先后顺序排
9、列起来。在综合考虑上述工序顺序安排原则的基础上, 表3-6列出了底座的工艺路线。表3-6底座工艺路线工序号工序名称1粗铣前后端面2去除车后毛刺3扩* 32孔4钻4X M8-6HJ 12 孔; 16基孔,并攻制螺纹5粗铣左右端面6粗铣、半精铣上端面7粗铣、半精铣3xM8孔上表面8钻、扩、较 20孔9去除交孔毛刺10钻3X M8基孔,并攻制螺纹11钻4X M8-6H基孔,并攻制螺纹12钻4X M8-6H深12孔深16基孔,并攻制螺纹13钻 2X M12-6HJ 14 孔 J 20 (两端)14去毛刺15清洗16终检四、机床设备及工艺装备选用4.1机床设备的选用由于此底座生产类型为大批生产,宜选用通
10、用设备。工序1、5、6、7均为铣削工序,由 表4-14可选用X51型立式铣床;工序2、 13均是去除切削后毛刺,可使用钳工台;工序3为扩?30孔,工序4、10、11、12、13均为先钻基孔后攻丝,由【表4-5可选用Z3040型摇臂钻床;工序8为钻、扩、较=20孔,工序多可选用四面组合钻床。4.2工艺装备的选用由于此底座生产类型为大批生产,宜选用专用夹具。工序1、5、6、7均为铣削工序,由【表3-23 (摘自JB/T7954-1999 )可选用镶齿套式面铣刀铣削,采用游标卡尺检验;工序 2、13均是去除切削后 毛刺,可选用平锂;工序 3为扩 30孑L,由【表3-9 (摘自GB/T1142-198
11、4)选用套式扩孔钻;工序 4、10、11、12、13均为先钻基孔后攻丝,由111表3-4 (摘自GB/T 1438.2-1996 )选用莫氏锥柄麻 花钻,根据生产批量由111表3-38 (摘自GB/T 3464.1-1994 )选用细 柄机用丝锥,选用卡尺和塞规检验;工序 8为钻、扩、铰20孑L,选 用钻头复合铰刀,选用卡尺和塞规检验;工序 9是去除交孔毛刺,可 使用刮刀。底座工艺路线及设备、工装的选用如表4-2所示工序号工序名称机床设备刀具量具1粗铣前后端面X51型立式铣床镶齿套式面铣刀游标卡尺2去除车后毛刺钳工台平锂3扩* 32孔摇臂钻床套式扩孔钻卡尺、塞规4钻 4X M8-6HJ 12孔
12、J 16基孔,并攻 制螺纹摇臂钻床莫氏锥柄麻花钻、细柄机用丝锥卡尺、塞规5粗铣左右端面X51型立式铣床镶齿套式面铣刀游标卡尺6粗铣、半精铣上端面X51型立式铣床镶齿套式面铣刀游标卡尺7粗铣、半精铣3X M8孔上表面X51型立式铣床镶齿套式面铣刀游标卡尺8钻、扩、铰个20孔四面组合钻钻头复合铰卡尺、塞规床刀9去除交孔毛刺刮刀10钻3X M8基孔,并攻制螺纹摇臂钻床莫氏锥柄麻花钻、细柄机用丝锥卡尺、塞规11钻4X M8-6H基孔,并攻制螺纹摇臂钻床莫氏锥柄麻花钻、细柄机用丝锥卡尺、塞规12钻 4X M8-6H深 12孔深16基孔,并攻 制螺纹摇臂钻床莫氏锥柄麻花钻、细柄机用丝锥卡尺、塞规13钻 2
13、X M12-6HJ 14孔J 20(两端)并攻制螺纹摇臂钻床莫氏锥柄麻花钻、细柄机用丝锥卡尺、塞规14去毛刺钳工台平锂15清洗清洗机16终检卡尺、塞规五、确定工序间的加工余量及工序尺寸1、工序1粗铣前后端面工序1的加工过程为:1)以左端面A定位粗铣右端面B,余量为乙,保证工序尺寸P ;2)以右端面定位粗铣左端面,余量为 乙,保证工序尺寸F2,达 到零件设计尺寸D的要求,故F2=85mm根据加工方案,可画出尺寸链如图5-1所示。求解各工序尺寸的 过程如下:F2D(a)A面F11Z2F2(b)图5-1第一道工序工艺尺寸链图1)从图 5-1(a)知,F2=85mm2) 从图5-1 (b)知,P =
14、F2+Z2,其中乙为粗铣余量,由于A面加工余量是经粗铣一次性切除好,故A面加工余量各等于A面毛坯余量,即 Z2 =2.5mm,故 F2= (85+2.5) mm=87.5m。双边余量相等,即Z1 = Z2 =2.5mm2、工序3扩 32孔由于工序3中 32孔是一次扩孔保证,而且扩孔可以达到工序3 所要求的精度,故工序3后保证尺寸P3为所要求的设计尺寸,即P=32mm.3、工序4钻4X M8-6HJ 12孔J 16基孔,并攻制螺纹(工序10、 11、12、13 同工序 4)工序4中用d=7mm勺钻头打螺纹基孔,基孔的尺寸直接由钻头保 证,再由M8号细柄机用丝锥攻丝,尺寸由丝锥保证。4、工序5粗铣
15、左右端面 工序5的加工过程为:1)以左端面C定位粗铣右端面D,余量为乙,保证工序尺寸P ;2)以右端面定位粗铣左端面,余量为 Z2,保证工序尺寸巳,达到零 件设计尺寸D的要求,故巳=108mm根据加工方案,可找出全部尺寸链如图5-2所示。求解各工序尺 寸的过程如下:巳D(a)PZ2F2(b)图5-2第五道工序工艺尺寸链图1) 从图 5-2 (a)知,F2=108mryi2) 从图5-2 (b)知,F二巳+Z2,其中乙为粗铣余量,由于C面 加工余量是经粗铣一次性切除好,故C面加工余量各等于C面毛坯余 量,即乙=4mm故F2 = ( 108+4) mm=112mm双边余量相等,即Z1 = Z2 =
16、4mm5、工序6粗铣、半精铣上端面工序6的加工过程为:1) 以下底面定位,粗铣上端面,余量为 乙,保证尺寸F ;2) 以下底面定位半精铣上端面,余量为 乙,保证尺寸F2,F等 于上、下端面设计尺寸 D,即F2=D=171m。根据加工方案,可画出尺寸链如图5-3所示。求解各工序尺寸的过程 如下:查【表2-36知,半精铣余量 乙=1mm由工序尺寸链图可知R = F2+Z2二(171+1) mm=172mm由毛坯图可知此处总余量 Z=5mi, 故粗铣加工余量乙二(5-1 ) mm=4mm21Z2理rP11P2图5-3第六道工序工艺尺寸链图6、工序7粗铣、半精铣3X M8孔上表面工序7的加工过程为:1
17、)以上端面定位,粗铣孔上表面,余量为 乙,保证尺寸R ;2)以上端面定位,半精铣孔上表面,余量为乙,保证尺寸F2 ,巳 等于上端面距孔表面的设计尺寸,即 F2 =6mm根据加工方案,可画出尺寸链如图5-4所示。求解各工序尺寸的 过程如下:查111表2-36知,半精铣余量乙=1mm由工序工艺尺寸链图可知 粗铣保证尺寸P1=F2-Z2= (6-1 ) mm=5mm由毛坯图可知此处加工总余 量 Z=3.5mm 故粗铣余量乙二(3.5-1 ) mm=2.5mmP1FP2Z2 ,1r1r图5-4第七道工序工艺尺寸链图7、工序8钻、扩、铰?20孔工序8加工过称为:1)钻孔保证尺寸R ;2)扩孔保证尺寸P2
18、 ;3)铰孔保证尺寸P3,P3等于孔设计尺寸,即P3=20mm根据加工方案,可画出尺寸链如图5-5所示。求解各工序尺寸的 过程如下:查【1】表2-28知,钻孔至d=18mm即P=18mm钻孔余量Z1=18mrn 扩孔至d=19.8mm 即卩P2 =19.8mm扩孔余量 乙=1.8mm铰孔至d=20mm 即 P3=20mrn 铰孔余量 Z3=0.2mmJAPr巳PZ21LF1fZ3,IF1L3333图5-5第八道工序工艺尺寸链图8、工序13钻2X M12-6HJ 14孔J 20 (两端)并攻制螺纹工序13中用d=11mm勺钻头打螺纹基孔,基孔的尺寸直接由钻头 保证,再由M12号细柄机用丝锥攻丝,
19、尺寸由丝锥保证。六、切削用量、时间定额计算6.1切削用量的计算1、工序1粗铣前后端面该工序分两个工步:工步1是以A面定位粗铣B面;工步2是以 右端面定位,粗铣左端面。1)背吃刀量的确定工步1的背吃刀量ap1取为乙,由前面计算得乙=4mm故ap1=4mm 而工步2的背吃刀量ap2取为乙,则如前所已知 乙=4mm故ap2=4mm2)进给量的确定由表5-7,按机床功率4.5KW工件刚度中等条件选取,该工序的每齿进给量fz取为0.2mm/z。3)铣削速度的确定由111表5-9,按镶齿铣刀、d/z=80/10的条件选取,铣削速度v 暂取为40m/min。由公式(5-1 ) n=1000 v / (刀d)
20、可求得该工序 铣刀转速,n=1000x 40m/min/ (刀 x 80mim =159.2mm 参照表【11 4-15 所列X51型立式铣床的主轴转速,取转速 n=160r/min。再将此转速 代入公式(5-1),可求出该工序的实际铣削速度为:v =n d/1000=160r/min x 刀 x 80mm/1000=40.2m/min 且工序的每转进给量 f = fz x Z=0.2 x 10=2mm/r2、工序3扩?32孔1)背吃刀量的确定取 ap=6mm2)进给量的确定由【11表5-23,根据钻孔直径选取,该工序的每转进给量f取为0.8mm/r。3)扩孔速度的确定由111表5-24,按扩
21、孔钻直径及铸件材料选取,铣削速度v暂取为87.5m/min。由【公式(5-1 ) n=1000 v / (刀d)可求得该工序铣 刀转速,n=1000x 487.5m/min/ (刀 x 32mrh =870mm 参照【11 表 4-6 所列摇臂钻床Z3040的主轴转速取n=800r/min。再将此转速代入公 式(5-1 ),可求出该工序的实际铣削速度v= n 刀 d/1000=800r/min x 刀 x 32mm/1000=25.6m/min3、工序4钻4x M8-6HJ 12孔J 16基孔,并攻制螺纹(1) 工步1钻4x M8-6HJ 12孔J 16基孔1)背吃刀量的确定背吃刀量ap1 =
22、Z=7mm2)进给量的确定由【表5-22 ,根据铸件材料及加工孔径选取,该工序的每转进给量 f 取为 0.15mm/r。3)钻削速度的确定由】表5-22,根据铸件材料及加工孔径选取,该工序的钻削速【1】度V暂取20m/min。由 公式(5-1) n=1000 v / (刀d)可求得该 工序钻头转速,n=1000x 20m/min/ (刀 x 7mr)i =909.5r/mm,参照 表4-6所列摇臂钻床Z3040的主轴转速取n二800r/min。再将此转速 代入公式(5-1),可求出该工序的实际铣削速度v= n ji d/1000=800r/min x 刀 x 7mm/1000=17.59m/m
23、ir。(2)工步2攻制螺纹1)背吃刀量的确定背吃刀量 ap1=Z-Z= (8-7) mm=1mm2)进给量的确定由于攻螺纹的进给量就是被加工螺纹的螺距,故该工序的每转进给量f取为1mm/r。3)攻螺纹速度的确定由】表5-37,根据铸件材料选取,该工序的钻削速度v暂取5m/min。由【11公式(5-1 ) n=1000 v / ( j d)可求得该工位主轴转 速,n=1000x 5m/min/ ( j x 8mm =198.9r/mm,参照【11表 4-6 所列 摇臂钻床Z3040的主轴转速取 n二200r/min。再将此转速代入公式(5-1),可求出该工序的实际铣削速度v= n j d/100
24、0=200r/min x j x 8mm/1000=5.03m/mir。4)切削速度和进给量的校验刀具的每分钟进给量fm、刀具转速n和进给量f之间的关系为fm= nf,因此可分别求出钻孔和攻螺纹的每分钟进给量,即钻孔:fm=800r/min x 0.15mm/r=120mm/min攻螺纹fm =200r/min x 1mm/r=200mm/min由于两者不相等,因此需对上述切削用量进行修改。因为攻螺纹时,f =200mm/min/800r/min=0.25mm/r,所以本工序对钻孔的进给量进行修改。令f =0.25mm/r,则钻孔的每分钟进给量fm =800r/min x 0.25mm/r=2
25、00mm/min等于攻螺纹的每分钟进给量,这与组合机床切削用量的选择原则相符 合。综上所述,各工位的背吃刀量和切削速度按前述保持不变,而只需将钻孔的进给量改为f =0.25mm/r。4、工序5粗铣左右端面该工序分两个工步:工步1是以C面定位粗铣D面;工步2是以 右端面定位,粗铣左端面。1)背吃刀量的确定工步1的背吃刀量取为乙,由前面计算得 乙=4mm故ap!=4mm 而工步2的背吃刀量ap2取为乙,则如前所已知 乙=4mm故ap2=4mm2)进给量的确定由】表5-11,按工件材料和背吃刀量及铣刀直径条件选取,该 工序的每齿进给量fz取为0.18mm/z。3)铣削速度的确定由】表5-13 ,按高
26、速钢立铣刀、d/z=50/6的条件选取,铣削速 度v暂取为38m/min。由】公式(5-1 ) n=1000 v / (刀d)可求得 该工序铣刀转速,n=1000x 38m/min/ (刀x 50mr)i =241.9mm 参照表 】4-15所列X51型立式铣床的主轴转速,取转速 n=255r/min。再将 此转速代入公式(5-1),可求出该工序的实际铣削速度为:v =n d/1000=255r/min x 刀 x 50mm/1000=40.1m/min且工序的每转进给量 f = fz x Z=0.18 x 6=1.08mm/r。5、工序6粗铣、半精铣上端面该工序分两个工步:工步1是粗铣上端面
27、;工步2是半精铣上端 面。(1) 工序1粗铣上端面1)背吃刀量的确定工步1的背吃刀量取为由前面计算得 乙=4mm故ap!=4mm2)进给量的确定由表5-7 ,按机床功率4.5KVV工件刚度中等条件选取,该工 序的每齿进给量fz取为0.2mm/z。3)铣削速度的确定由111表5-9,按高速钢套式面铣刀、d/z=80/10的条件选取,铣 削速度v暂取为38.3m/min。由111公式(5-1) n=1000 v / (刀d) 可求得该工序铣刀转速,n=1000x 38.3m/mi n/ (刀x 80mm = 152.4mm 参照表【4-15所列X51型立式铣床的主轴转速,取转速n=160r/min
28、。 再将此转速代入公式(5-1),可求出该工序的实际铣削速度为:v =n d/1000=160r/min x 刀 x 80mm/1000=40.2m/min 且工序的每转进给量 f = fz x Z=0.2 x 10=2mm/r(2)工步2半精铣上端面1)背吃刀量的确定工步2的背吃刀量ap2取为Z2,由前面计算得Z2=Z-乙二(5-4) mm=1mm故 ap2=1mm2)进给量的确定由表5-7,按机床功率4.5KVV工件刚度中等条件选取,该工 序的每齿进给量fz取为0.2mm/z。3)铣削速度的确定由】表5-9,按高速钢套式面铣刀、d/z=80/10的条件选取,铣 削速度v暂取为40m/min
29、。由【公式(5-1 ) n=1000 v / (刀d)可 求得该工序铣刀转速,n=1000x 40m/min/ (刀x 80mr) =159mm参照 表【4-15所列X51型立式铣床的主轴转速, 取转速n=160r/min。再 将此转速代入公式(5-1),可求出该工序的实际铣削速度为:v =n d/1000=160r/min x 刀 x 80mm/1000=40.2m/min 且工序的每转进给量f = fz x Z=0.2 x 10=2mm/r6、工序7粗铣、半精铣3x M8孔上表面(1) 工序1粗铣3x M8孔上表面1)背吃刀量的确定工步1的背吃刀量ap!取为乙,由前面计算得 乙=2.5mm
30、故ap1=2.5mm2)进给量的确定由表5-7,按机床功率4.5KW工件刚度中等条件选取,该 工序的每齿进给量fz取为0.2mm/z。3)铣削速度的确定由】表5-9,按高速钢套式面铣刀、d/z=80/10的条件选取,铣 削速度v暂取为38.3m/min。由】公式(5-1) n=1000 v / (刀d) 可求得该工序铣刀转速,n=1000x 38.3m/mi n/ (刀 x 80mr)i = 152.4mm 参照表】4-15所列X51型立式铣床的主轴转速,取转速n=160r/min。 再将此转速代入公式(5-1),可求出该工序的实际铣削速度为:v =n d/1000=160r/min x 刀
31、x 80mm/1000=40.2m/min 且工序的每转 进给量 f = fz x Z=0.2 x 10=2mm/。(2)工步2半精铣上端面1)背吃刀量的确定工步2的背吃刀量ap2取为Z2 ,由前面计算得乙二Z-乙二(3.5-2.5 ) mm=1mm故 ap2=1mm2)进给量的确定由表5-7 ,按机床功率4.5KVV工件刚度中等条件选取,该工 序的每齿进给量fz取为0.2mm/z。3)铣削速度的确定由】表5-9 ,按高速钢套式面铣刀、d/z=80/10的条件选取,铣 削速度v暂取为40m/min。由公式(5-1 ) n=1000 v / (刀d)可 求得该工序铣刀转速,n=1000x 40m
32、/min/ (刀x 80mm =159mm参照 表【4-15所列X51型立式铣床的主轴转速, 取转速n=160r/min。再将此转速代入公式(5-1),可求出该工序的实际铣削速度为:v =n d/1000=160r/min X 刀 x 80mm/1000=40.2m/min 且工序的每转 进给量 f = fz x Z=0.2 x 10=2mm/r7、工序8钻、扩、铰?20孔(1)钻孔工步1)背吃刀量的确定取 ap = Z1=18mim2)进给量的确定由111表5-22,根据铸件材料及加工孔径选取,该工序的每转进给量f取为0.3mm/r。3 )钻削速度的确定由111表5-22,根据铸件材料及加工
33、孔径选取,该工序的钻削速度v暂取20m/min。由公式(5-1) n=1000 v / (刀d)可求得该 工序钻头转速,n=1000X 20m/min/ (刀 x 18mm =353.7r/mm,参照【11 表4-6所列摇臂钻床Z3040的主轴转速取n二315r/min。再将此转速 代入公式(5-1),可求出该工序的实际铣削速度v= n ji d/1000=315r/min x 刀 x 18mm/1000=17.8m/min(2)扩孔工步1)背吃刀量的确定取 ap = Z2 =1.8mm2)进给量的确定由】表5-22,根据钻孔直径及零件材料选取,该工序的每转进 给量f取为0.6mm/r。3)扩
34、孔速度的确定由】表5-24,按扩孔钻直径及铸件材料选取,铣削速度v暂取【1】一为99.6m/min。由 公式(5-1 ) n=1000 v / (刀d)可求得该工序铣 刀转速,n=1000x 99.6m/min/ (刀 x 19.8mm) =1601.2mm 参照 表 4-6所列摇臂钻床Z3040的主轴转速取n=1600r/min。再将此转速代 入公式(5-1 ),可求出该工序的实际铣削速度v= n ji d/1000=1600r/min x x 19.8mm/1000=99.5m/min。(3)铰孔工步1)背吃刀量的确定取 ap = Z3=0.2mm2)进给量的确定由【1】表5-31,根据钻
35、孔直径及零件材料选取,该工序的每转进给量f取为1mm/r。3)铰孔速度的确定由】表5-31,根据钻孔直径及零件材料选取,该工序的切削速度v暂取为4m/min。由【11公式(5-1) n=1000 v / ( j d)可求得该 工序铣刀转速,n=1000x 4m/min/ ( j x 20mr)i =63.7mm 参照【11 表4-6所列摇臂钻床Z3040的主轴转速取n=50r/min。再将此转速代入 公式(5-1 ),可求出该工序的实际铣削速度v= n j d/1000=50r/min x j x 20mm/1000=3.1m/min8工序13钻2X M12-6HJ 14孔J 20 (两端)基
36、孔并攻制螺纹(1) 工步1钻2X M12-6HJ 14孔J 20 (两端)基孔1)背吃刀量的确定背吃刀量ap1 =Z=11mm2)进给量的确定由111表5-22,根据铸件材料及加工孔径选取,该工序的每转进给量f取为0.15mm/r。3)钻削速度的确定由111表5-22,根据铸件材料及加工孔径选取,该工序的钻削速度v暂取20m/min。由【公式(5-1) n=1000 v / (刀d)可求得该 工序钻头转速,n=1000x 20m/mi n/ (刀 x 11mr)i =578.7r/mm,参照【11表4-6所列摇臂钻床Z3040的主轴转速取n二630r/min。再将此转速代入公式(5-1),可求
37、出该工序的实际铣削速度v= n ji d/1000=630r/min x x 11mm/1000=21.78m/min(2)工步2攻制螺纹1)背吃刀量的确定背吃刀量 ap2 =Z-Z1= (12-11) mm=1mm2)进给量的确定由于攻螺纹的进给量就是被加工螺纹的螺距,故该工序的每转进给量f取为1mm/r。3)攻螺纹速度的确定由111表5-37,根据铸件材料选取,该工序的钻削速度v暂取 5m/min。由【11公式(5-1 ) n=1000 v / (刀d)可求得该工位主轴转 速,n=1000x 5m/min/ ( ji x 12mm =132.6r/mm,参照【11 表 4-6 所列 摇臂钻
38、床Z3040的主轴转速取 n=160r/min。再将此转速代入公式(5-1),可求出该工序的实际铣削速度v= n j d/1000=160r/min x j x 12mm/1000=6.03m/min(3)切削速度和进给量的校验刀具的每分钟进给量fm、刀具转速n和进给量f之间的关系为fm= nf,因此可分别求出钻孔和攻螺纹的每分钟进给量,即钻孔fm=630r/min x 0.15mm/r=94.5mm/min攻螺纹fm =160r/min x 1mm/r=160mm/min由于两者不相等,因此需对上述切削用量进行修改。因为攻螺纹时,f =160mm/mi n/630r/mi n=0.25mm/
39、r所以本工序对钻孔的进给量进行修改。令f =0.25mm/r,则钻孔的每分钟进给量fm=630r/min x 0.25mm/r=157.5mm/min 160mm/min等于攻螺纹的每分钟进给量,这与组合机床切削用量的选择原则相符 合。综上所述,各工位的背吃刀量和切削速度按前述保持不变,而只需将钻孔的进给量改为f =0.25mm/r。6.2时间定额的计算 6.2.1基本时间定额的计算1、工序1粗铣前后端面1) 粗铣前端面据】表5-43中面铣刀铣平面(对称铣削、主偏角k r= 90 o)的l + l + l基本时间计算公式tj1 2可求出该工序的基本时间。由式中jfMzi=148mm J = 1
40、3mm 取 i2=1mryili=0.5 (d- .d2 a。2) + (1 3) =0.5 X(80- ,802 702 ) +仁21.6mmfMz= f x n= fz x Zx n=0.2mm/r x 10z/r x 16r/min=32mm/min。I + I + I将上述结果代入公式tj12,则该本工步的基本时间tj=jfMzj(148mm+21.6mm+1mi/320mm/min=0.53min=31.8s。2) 粗铣后端面据】表5-43中面铣刀铣平面(对称铣削、主偏角k r= 90 o)的I + I + I基本时间计算公式tj 12可求出该工序的基本时间。由式中fMz丨=70mr
41、p I2 = 1 3mn,取2=1mmI1=0.5 (d- ,d2 ae2) + (1 3) =0.5 x(80- ,80_702 ) +1二21.6mmfMz= f x n= fz x Zx n=0.2mm/r x 10z/r x 160r/min=320mm/min。I + I + I将上述结果代入公式tj12,则该本工步的基本时间tj=jfMzJ(70mm+21.6mm+1mi/320mm/min=0.29min=17.4s。综上所述,该工序总的基本时间tj=31.8s+17.4s=49.2s。2、工序3扩?32孔根据表5-41扩孔的基本时间计算公式tj L 匕 上j fn fn可求出该
42、工序的基本时间。其中盲孔12=0;h = D 2 cot +(1 口 2)=(32-23)mm/2cot60 o +1mm=3.6mm 由 前可知 f =0.8mm/r, n =800r/min , l =63mm 贝U tj = ( 63+3.6+0) mm/ (0.8 mm/rx 800 r/min ) =0.1min=6s。3、工序4钻4X M8-6HJ 12孔J 16基孔,并攻制螺纹(工序10、12、13同工序4)1) 钻 4X M8-6HJ 12 孔; 16 基孔根据11】表5-41 ,钻孔的基本时间计算公式tj二丄L_U 可求出j fn fn该工序的基本时间。其中,D厂廿h = c
43、otkr +(1L 2 )=7mm/2cot30o+1mm=7.06m; |2 =1 4,取 2l2=1mm 由前面可知 f =0.25mm/r, n=800r/min , l =16mm 则tj=( 16+7.06+1) mm/0.25 mm/rx 800 r/min )=0.1203min=7.218s。2) 攻 4X M8-6HJ 12 孔 J 16 螺纹根据【1】表5-46 ,用丝锥攻螺纹的基本时间计算公式 .=心匸岂+匕上也j可求出该工序的基本时间。式中h=(1LI 3)P ,取 fnfn。丿h=1mml2 二 2L3 P,取i2=2mm由前面可知 f =mm/r, n = n =2
44、00 r/min ; 则 tj i12 1 2 p 2 =0.15min=9s。.1 200综上所述,工序4总的基本时间tj= (7.218+9 ) s=16.218s。4、工序5粗铣左右端面根据表5-43中面铣刀铣平面(对称铣削、主偏角k r= 90 o) 的基本时间计算公式tj11 12可求出该工序的基本时间。由于该工Mz序包括两个工步,即两个工件同时加工,故式中 I=2X 86mm=192mmJ=13mm 取 I2=1mrph =0.5 d - d2 ae213 =0.5 X ( 50- 502 322 ) +1=6.8mm;fMz = f n = fMz X ZX n =0.18mm/
45、r X 6z/r X 255r/min=275.4mm/min。将上述结果代入公式tj二丄上,则该本工序的基本时间tj =fMz(192mm+6.8mm+1)i/275.4mm/min=0.73min=43.8s 。5、工序6粗铣、半精铣上端面1)粗铣上端面根据表5-43中面铣刀铣平面(对称铣削、主偏角k r= 90 o) 的基本时间计算公式tjl2可求出该工序的基本时间。式中f MzI =44mrp l2=1 3mm 取 l2 = 1mrph =0.5 d - d2 ae213 =0.5 X ( 80-, 802 552 ) +1二 12mm;fMz =f n = fz X ZX n =0.
46、2mm/r X 10z/r X 160r/min=320mm/min。将上述结果代入公式tj二丄上,则该本工序的基本时间tj =fMz(44mm+12mm+1)mm20mm/min=0.18min=10.8s。2)半精铣上端面半精铣的I、h、I2、fz、z、n均与精铣时相同,故半精铣的基本时间tj =10.8s。综上所述,工序4总的基本时间tj= (10.8+10.8 ) s=21.6s。6、工序7粗铣、半精铣3X M8孔上表面1) 粗铣上端面根据表5-43中面铣刀铣平面(对称铣削、主偏角k r= 90 o)的基本时间计算公式tjb l2可求出该工序的基本时间。式中jfMzl =68mrp J
47、=1 3mm 取 l2 = 1mrph =0.5 d - _d2 ae21口3 =0.5 X ( 80- .802 682 ) +1=19.93mm;fMz =f n = fz X ZX n =0.2mm/r X 10z/r X 160r/min=320mm/min。将上述结果代入公式tj二丄上,则该本工序的基本时间tj = fMz(68mm+19.93mm+1)i/320mm/min=0.28min=16.8s。2) 半精铣上端面半精铣的l、h、l2、fz、Z、n均与精铣时相同,故半精铣的基本时间tj =10.8s。综上所述,工序4总的基本时间tj二(16.8+16.8 ) s=33.6s。
48、7、工序8钻、扩、铰?20孔1)钻孔工序根据11】表5-41 ,钻孔的基本时间计算公式tj二丄H可求出j fn fn该工序的基本时间。其中,Dcotkr 1=18mm/2cot30b+1mm=16.6m; 钻盲孔时取 l2=0mm 由前面可知 f =0.25mm/r, n =800r/min , l=16mqn则 tj = (38+16.6+0) mm/(0.3 mm/r x 315r/min ) =0.58min=34.8s。2)扩孔工序根据表5-41扩孔的基本时间计算公式.二丄 匕可求出j fn fn该工序的基本时间。盲孔12=0;h = D 2 cotkr +(1 口 2)=(19.8-
49、18)mm/2cot60 o+1mm=1.52mm由前可知f =0.6mm/r, n =50r/min , I =38mm 贝U tj = / 38+1.52+0) mm/ 0.6mm/r x 50 r/min ) =1.32min=79.2s。1)铰孔工步根据表5-41扩孔的基本时间计算公式.二丄二匕可求出j fn fn该工序的基本时间。盲孔J=0;h =冷4cotkr +(1口 2)=(20-19.8)mm/2cot60 o+1mm=1.06mm由前可知f =1mm/r, n =50r/min , l =38mm 则 tj = / 38+1.06+0) mm/(1mm/rx 50r/min
50、 ) =1.32min=46.872s综上所述,工序8总的基本时间tj=34.8+79.2+46.872=160.872s&工序11钻4X M8-6H基孔,并攻制螺纹1)钻4X M8-6H基孔根据表5-41 ,钻孔的基本时间计算公式tj二丄l一“可求出j fn fn该工序的基本时间。其中,D厂h = cotkr + (1 L 2 )=7mm/2cot30D+1mm=7.06n;T盲孔 l2=0mm 由前面可知 f =0.25mm/r, n=800r/min , I =7mm 则tj = (7+7.06+0) mm/(0.25 mm/r x 800 r/min ) =0.0703min=4.21
51、8s2)攻4x M8-6H螺纹根据【1】表5-46 ,用丝锥攻螺纹的基本时间计算公式 tj匕士也+匸士也i可求出该工序的基本时间。式中Ii=(1L|3)P,取 fn fn0 丿h=1mm 盲孔取 i2=0mm 由前面可知 f=1mm/r, n = n=200 r/min ;贝卩7+1+0匕=区 2 =0.08 min = 4.8sj 十200丿综上所述,工序4总的基本时间tj= /4.218+4.8 ) s=9.018s。9、工序13钻2X M12-6HJ 14孔J 20 (两端)基孔并攻制螺纹1) 钻2XM12-6HJ 14孔J 20 (两端)基孔根据11】表5-41 ,钻孔的基本时间计算公
52、式.二丄二匕可求出j fn fn该工序的基本时间。其中,h =Dcotkr 1=11mm/2cot30b+1mm=10.5m;2取 i2=1mm 由前面可知 f =0.25mm/r, n =630r/min , I =20mm 则 tj =/ 20+10.5+1) mm/ (0.25 mm/r x 630r/min ) =0.2min=12s。2) 攻2xM12-6Hj 14孔J 20 (两端)螺纹根据【1】表5-46 ,用丝锥攻螺纹的基本时间计算公式tj +11勺2 +1 S % i可求出该工序的基本时间。 式中l1=(1U3)P ,取、_ fn fn。丿h=1mm l2=(23)P,取 i
53、2=2mm 由前面可知 f =0.25mm/r, n = n。=160r/min ;则 tj =卩4 勺 *2、2 =0.2125min=12.75s。j I 1160 丿综上所述,工序4总的基本时间tj= /12+12.75) s=24.75s。6.2.2辅助时间tf的计算辅助时间tf与基本时间tj之间的关系为tf = (0.150.2 ) tj,本 例tf=0.15tj,则各工序的辅助时间分别为:工序1的辅助时间:tf =0.2 X49.2s=9.84s工序3的辅助时间:tf =0.2 X6s=1.2s工序 4 的辅助时间:tf =0.2 Xl6.218s=3.236s工序5的辅助时间:t
54、f =0.2 X43.8s=8.76s工序6的辅助时间:tf =0.2 X21.6s=4.32s工序7的辅助时间:tf =0.2 X 33.6s=6.72s工序 8 的辅助时间:tf =0.2 Xl60.872s=32.1744s工序 11 的辅助时间:tf =0.2 X 9.018s=1.8036s工序 13 的辅助时间:tf =0.2 X 24.75s=4.95s6.2.3其他时间的计算除了作业时间(基本时间与辅助时间之和)以外每道工序的单件 时间还包括布置工作地时间、 休息与生理时间和准备与终结时间。由于该零件的生产类型为大批生产,分摊到每个工件上的准备与终结时 间甚微,可忽略不计;布置
55、工作地时间tb是作业时间的2%7%,休 息与生理时间tx是作业时间的2%4%,取为3%,则各工序的其他 时间tb tx可按关系式(3% +3%)X tj tf计算,它们分别为:工序 1 的其他时间:tb tx =6%X( 49.2+9.84 ) s=3.5424s工序 3 的其他时间:tb tx =6%X( 6+1.2) s=0.432s工序 4 的其他时间:tb tx =6%X( 3.236+16.218 ) s=19.514s 工序 5 的其他时间:tb tx =6%X( 43.8+8.76 ) s=3.1536s 工序 6 的其他时间:tb tx =6%X( 21.6+4.321 ) s
56、=1.56s 工序 7 的其他时间:tb - tx =6%X( 33.6+6.72 ) s=2.4192s 工序 8 的其他时间:tb tx =6%X (160.872+32.1744 )s=11.58s 工序 11 的其他时间:tb tx =6%x( 9.018+1.8036 ) s=0.65s 工序 13 的其他时间:tb tx =6%X( 24.75+4.95 ) s=1.782s6.2.4单件时间tdj的计算工序1的单件时间:tdj=49.2s+9.84s+3.5424s=62.5824s工序3的单件时间:tdj =6s+1.2s+0.432s=7.632s工序4的单件时间:tdj=3
57、.236s+16.218s+19.514s=38.968s工序5的单件时间:tdj =43.8s+8.76s+3.1536s=55.7136s工序6的单件时间:tdj =21.6s+4.32s+1.56s=27.48s工序7的单件时间:tdj =33.6s+6.72s+2.4192s=42.7392s工序8的单件时间:tdj =160.872s+32.1744s+11.58s=204.6264s工序11的单件时间:tdj= (9.018+1.8036+0.65 ) s=9.018s工序13的单件时间:tdj =24.75s+4.95s+1.782s=31.482s将上述零件工艺规程设计的结果填
58、入工艺文件七、夹具设计7.1夹具的作用夹具的主要功用是实现工件的正确定位和夹紧,使工件加工时相 对于机床、刀具由正确的位置,以保证工件的加工质量和生产率的要 求。7.2夹具类型选用此零件的生产类型为大批量生产,故采用专用夹具。7.3确定定位方案根据工序简图规定的定位基准,选用一面两销定位方案。长定 位销与工件定位孔配合,限制四个自由度;定位销轴肩小环面与工 件定位端面接触,限制一个自由度;支承钉与工件头部方块接触限 制一个自由度,实现工件正确定位。定位孔与定位销的配合尺寸取 为 32H7/f6 (在夹具上标出定位销配合尺寸* 32f7 )。由11】表8-7 , 定位销选用 A32f7 X 34
59、 JB/T 8014.2-1999 ;由【表8-2,由于圆头 支承钉容易保证与工件的定位,基面间的点接触相对稳定,故选用 B12X 6mm JB/T8029.2-1999。7.4定位误差的计算定位误差:D包括基准位移误差:W和基准不重合度误差:B,即由于工件定位基准和工序基准都是32孔中心轴线,因此不存在基准不重合误差,即基准不重合误差b 二 0mm已知孔销配合最大间隙=Dmax dmin由】表8-8知,可换定位销d的上下偏差分别为Omm-O.O11mm;41 / 40惦HZ孔的极限偏差为孔的最大直径销孔配合选用h6 ,由【4】表E-4可知,15H7+0.018mm、0mm,则孔 的公差 g =0.018mm,Dmax =(15 0.18)mm =1518mm;由【4】表E-5可知,15h6销的极限偏差为0mm -0.011mm,则销 的公差=0.011mm,销的最小直径dmin = (15-0.011)mm = 14.989mm。所以孔销配合最大间隙二 Dmax - dmin = 15.018 -14.989 = 0.029mm故间隙引起的工件定位误差1-2g=0.09mm即,基准位移误差w = 0.029mm综上,夹具定位误差D 二 B w = 0 0.029 二 0.029mm7.4确定导向装置此零件生产类型为大批量生产,为维修
- 温馨提示:
1: 本站所有资源如无特殊说明,都需要本地电脑安装OFFICE2007和PDF阅读器。图纸软件为CAD,CAXA,PROE,UG,SolidWorks等.压缩文件请下载最新的WinRAR软件解压。
2: 本站的文档不包含任何第三方提供的附件图纸等,如果需要附件,请联系上传者。文件的所有权益归上传用户所有。
3.本站RAR压缩包中若带图纸,网页内容里面会有图纸预览,若没有图纸预览就没有图纸。
4. 未经权益所有人同意不得将文件中的内容挪作商业或盈利用途。
5. 装配图网仅提供信息存储空间,仅对用户上传内容的表现方式做保护处理,对用户上传分享的文档内容本身不做任何修改或编辑,并不能对任何下载内容负责。
6. 下载文件中如有侵权或不适当内容,请与我们联系,我们立即纠正。
7. 本站不保证下载资源的准确性、安全性和完整性, 同时也不承担用户因使用这些下载资源对自己和他人造成任何形式的伤害或损失。
最新文档
- 高中物理-第3章-专题-弹力摩擦力综合问题及物体的受力分析ppt课件-新人教版必修1
- 高中英语外研版选修六ppt课件:Module+2+Section+Ⅰ+Introduction+&+Reading+—+Pre-reading
- 高中英语外研版必修三ppt课件:Module+4+Section+Ⅴ+Writing—+环保类作文
- 高中英语必修4-Unit-2-Working-the-landppt课件
- 《高等石油地质》复习资料--课件
- 高中英语人教选修6ppt课件:Unit-3-Section-Ⅱ
- 高中信息技术基础《初识冒泡排序》优质课教学ppt课件
- 高中议论文语段训练修改ppt课件
- 高中英语必修五人教版ppt课件:Unit-3-Period-Three
- 党课ppt课件信仰的力量精编版
- 蔬果变变变课件
- 中央空调系统构成和设备配置课件
- 促进身心健康课件-人教课标版
- 传出神经系统药理---课件
- 一年级数学10的分与合课件