精益管理在工厂的活学活用
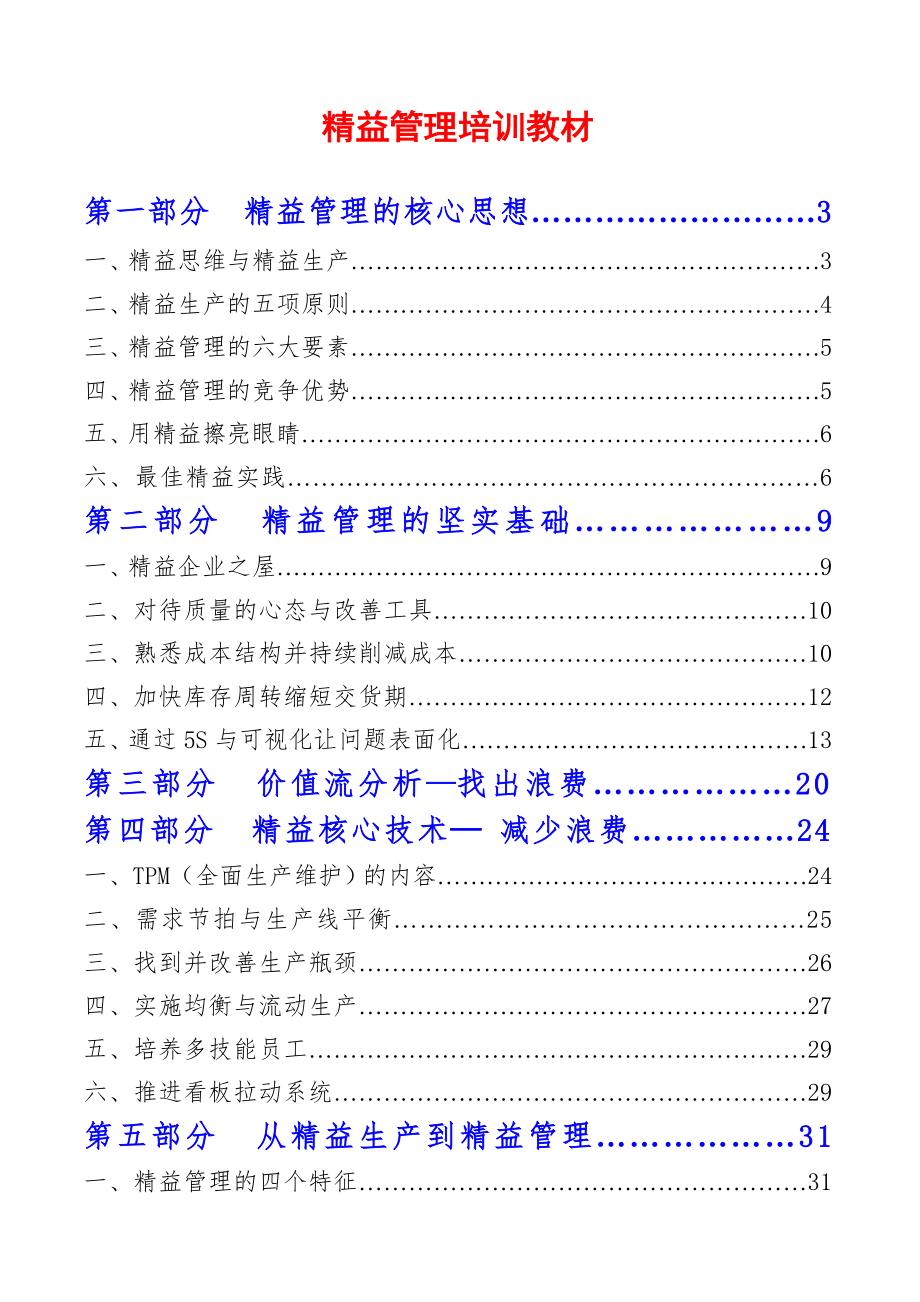


《精益管理在工厂的活学活用》由会员分享,可在线阅读,更多相关《精益管理在工厂的活学活用(48页珍藏版)》请在装配图网上搜索。
1、精益管理培训教材第一部分 精益管理的核心思想3一、精益思维与精益生产3二、精益生产的五项原则4三、精益管理的六大要素5四、精益管理的竞争优势5五、用精益擦亮眼睛6六、最佳精益实践6第二部分 精益管理的坚实基础9一、精益企业之屋9二、对待质量的心态与改善工具10三、熟悉成本结构并持续削减成本10四、加快库存周转缩短交货期12五、通过5S与可视化让问题表面化13第三部分 价值流分析找出浪费20第四部分 精益核心技术 减少浪费24一、TPM(全面生产维护)的内容24二、需求节拍与生产线平衡25三、找到并改善生产瓶颈26四、实施均衡与流动生产27五、培养多技能员工29六、推进看板拉动系统29第五部分
2、从精益生产到精益管理31一、精益管理的四个特征31二、进行精益产品的开发32三、创建精益的供应链34四、精益的人力资源:合适的人在合适的位置上36五、精益的行政管理:厉行节约36六、支持全方位的变化36第六部分 精益成功的关键人的因素38一、团队建设/员工参与:塑造精益型员工38二、精益型中基层干部的培养40三、有多少个表现差距42四、精益管理的持续改善42附录46一、精益生产的产生与推广46二、精益化管理、精细化管理、精确化管理47第一部分 精益管理的核心思想一、精益思维与精益生产1、什么是精益管理?精益管理源于精益生产。精益生产(LPLean Production)是美国麻省理工学院教授詹
3、姆斯P沃麦克等专家通过“国际汽车计划(IMVP)”对全世界17个国家90多个汽车制造厂的调查和对比分析,认为日本丰田汽车公司的生产方式是最适用于现代制造企业的一种生产组织管理方式。 精益管理由最初的在生产系统的管理实践成功,已经逐步延伸到企业的各项管理业务,也由最初的具体业务管理方法,上升为战略管理理念。它能够通过提高顾客满意度、降低成本、提高质量、加快流程速度和改善资本投入,使股东价值实现最大化。制造系统演化史(1)福特首创的装配线是大规模低品种生产方式的代表,工人被当成工作的机器。(2)丰田系统是建立在准时化观念上的拉动式生产模式,以应付小订单多品种的挑战。精益思维和精益生产系统(3)起源
4、于20世纪50年代丰田汽车公司,而在80年代中期被欧美企业纷纷采用。随着微利时代的来临,精益生产模式成为企业竞争的有力武器2、精益管理的内涵、意义精益管理要求企业的各项活动都必须运用“精益思维” (Lean inking)。“精益思维”的核心就是以最小资源投入,包括人力、设备、资金、材料、时间和空间, 创造出尽可能多的价值,为顾客提供新产品和及时的服务。 精益管理的目标可以概括为:企业在为顾客提供满意的产品与服务的同时,把浪费降到最低程度。精益管理就是管理要: (1)“精”少投入、少消耗资源、少花时间,尤其是要减少不可再生资源的投入和耗费,高质量。 (2)“益”多产出经济效益,实现企业升级的目
5、标。更加,精益求精。 精益企业的概念始创于丰田公司(Toyota)大野耐一(Taiichi Ohno)实行的即时生产(Just-in-Time,简称JIT)概念,其核心是在企业的生产环节及其它运营活动中彻底消灭浪费现象。 在过去,精益思想往往被理解为简单的消除浪费,表现为许多企业在生产中提倡节约、提高效率、取消库存(JIT)、减少员工、流程再造等。但是,这仅仅是要求“正确地做事”,是一种片面的、危险的视角。而现在的精益思想,不仅要关注消除浪费,同时还以创造价值为目标“做正确的事”。归纳起来,精益思想就是在创造价值的目标下不断地消除浪费。 企业在全球化的背景下正面临着日益激烈的竞争形势,对企业进
6、行精益改革已成为一个发展趋势。 价值LeanManufacturing精益生产 Manufacturing精益生产Value站在客户的立场上Value Stream 从接单到发货过程的一切活动Flow象开发的河流一样通畅流动BTR-按需求生产Perfect没有任何事物是完美的不断改进降低成本, 改善质量, 缩短生产周期PerfectDemand PullFlowValue Stream流动需求拉动二、精益生产的五项原则完美价值流精益生产关键特性:(1)着眼于速度和过程简化(2)在生产过程中“拉动”材料。(3)根据客户的需求平衡操作。(4)除非受订单的限制,否则最小批量生产。(5)延伸至供应商。
7、P-D-Q-C-S-MCost 成本Quality 质量三、精益管理的六大要素Safety、Morale安全、士气Delivery 交货Production 生产 将精益管理落到实处:时段目标的完成PDQCSM工作开始前1、2、3、1、2、3、1、2、3、1、2、3、1、2、3、1、2、3、工作中1、2、3、1、2、3、1、2、3、1、2、3、1、2、3、1、2、3、工作结束前1、2、3、1、2、3、1、2、3、1、2、3、1、2、3、1、2、3、四、精益企业的竞争优势 对于制造型企业而言,在以下方面已经有无数的实践证明是取得成效的:库存大幅降低,生产周期减短,质量稳定提高,各种资源(能源、空
8、间、材料、人力)等的使用效率提高,各种浪费减少、生产成本下降,企业利润增加。同时,员工士气、企业文化、领导力、生产技术都在实施中得到提升,最终增强了企业的竞争力。 对于服务型企业而言,提升企业内部流程效率,做到对顾客需求的快速反应,可以缩短缩短从顾客需求产生到实现的过程时间,大大提高了顾客满意度,从而稳定和不断扩展市场占有率。 在三到五年的时间里 生产时间减少 90% 库存减少 90% 生产效率提高 60% 到达客户手中的缺陷减少 50% 废品率降低 50% 与工作有关的伤害降低 50% 否则,要检查一下你在哪里做错了!五、用精益擦亮我们的眼睛理念的挑战当我们使用传统观念思考的时候,即使问题摆
9、在你面前,你也看不见。六、最佳精益实践1、丰田式生产管理:不降低成本就无法提高利润(1)成本中心型 以计算或实际的成本为中心,加上预先设定好的利润而得出售价,其公式为:售价 = 成本+利润,在供应销量时,以售价为中心,当市场售价降低时利润随之减少,其公式为:利润 = 售价 成本,缺乏改善意识的企业属于此类型,市场好时有较高的利润,市场差时大幅度下降。(3)利润中心型 在供应销量时,以利润为中心,当市场售价降低时,成本也必须下降以获得的利润 (目标利润 ) 不会减少,其公式为:成本 = 售价 利润,减少浪费-降低成本的主要手段 不增加价值的活动(如:生产过程改变零件尺寸、形状或功能,非价格) 是
10、浪费;尽管是增加价值的活动,但所用资源超过了绝对最少的界限,也是浪费。丰田式生产管理目的就是取消那些不增加产品价值的工作,即降低成本。 2、丰田式生产管理哲理的理论框架丰田式生产管理哲理的理论框架包含“一个目标”、“两大支柱”和“一大基础”。 (1)“一个目标”是低成本、高效率、高质量地进行生产,最大限度地使顾客满意。 (2)“两大支柱”是准时化与人员自主化。 (3)“一大基础”是指改善(Improvement)。改善是丰田式生产管理的基础。这里的改善是指这样的含义: 从局部到整体永远存在着改进与提高的余地。在工作、操作方法、质量、生产结构和管理方式上要不断地改进与提高。 消除一切浪费。丰田式
11、生产管理哲理认为不能提高附加价值的一切工作(包括生产过剩、库存、等待、搬运、加工中的某些活动,多余的动作,不良品的返工等)都浪费。这些浪费必须经过全员努力不断消除。 连续改善 (Continuous Improvement)是当今国际上流行的管理思想。它是指以消除浪费和改进提高的思想为依托,对生产与管理中的问题,采用由易到难的原则,不断地改善、巩固,改善、提高的方法,经过不懈的努力,以求长期的积累,获得显著效果。 3、丰田式生产管理的关键原则丰田式生产管理的关键原则归纳如下: (1)建立看板体系(Kanban system)。 (2)强调实时存货(Just In Time)。 (3)标准作业彻
12、底化。 (4)排除浪费、不平及模糊等。 (5)重复问五次为什么,然后想如何做(How),以严谨的态度打造完美的制造任务。 (6)生产平衡化。 (7)充分运用“活人和活空间”。 (8)养成自动化习惯。 (9)弹性改变生产方式。 4、丰田式生产管理的四大规则蕴涵在丰田式生产管理之中的隐性知识(Tacit Knowledge)可以用四条基本规则来概括。这些规则指导着每一产品和服务所涉及的每一项作业、每一处衔接和每一条流程路线的设计,实施和改进这四条规则如下: 规则一:所有工作的内容、次序、时间和结果都必须明确规定。 规则二:每一种客户-供应商关系都必须是直接的,发送要求和得到回应的方式必须明确无误,
13、非“是”即“否”。 规则三:每一种产品和服务的流转路线都必须简单而直接。 规则四:所有的改进都必须在老师的指导下,按照科学的方法,在尽可能低的组织层面上进行。 这四条规则要求,企业的各种作业、衔接和流程路线必须能够进行自我检测,以自动发出问题警示。正是由于不断地对问题做出响应,看似僵化的体系才得以保持柔性,能够灵活适应不断变化的环境。 5、丰田式生产管理:工人如何学习规划如果说丰田式生产管理的规则是隐性的,那么它们又是怎样传播的呢?丰田的管理者并不具体告诉工人和主管们如何工作,而是采用一种教与学的方法,让工人们通过解决问题来领悟这些规则。例如,在教第一条规则时,主管会来到工作现场,向正在工作的
14、工人提出一系列问题: 你是怎样做这项工作的? 你怎样判断自己做的方式是正确的? 你如何知道自己的工作成果没有瑕疵? 如果遇到问题,你会怎样处理? 这一持续发问的过程,使得员工对自己的具体工作领悟得越来越深刻。在经历了多次类似的提问之后,这名员工就逐渐学会了如何按照规则一来设计各种作业。 所有的规则都是通过苏格拉底式的反复提问和解决问题来传授的。虽然这是一种非常有效的教学方法,但是员工获得的知识却是隐性的,所以,只有当管理者有能力并且愿意用这种提问方式来督促工人在实践中学习时,丰田生产方才能够被成功地复制和移植。 第二部分 精益管理的坚实基础一、精益企业之屋观念转变,消除浪费,价值流管理,团队精
15、神设备总有效性自动化及防错作业快速转换流动生产设备布局多技能员工小批量生产缩短生产周期均衡混流生产看板拉动准时化生产库存降低消除浪费降低成本全面质量管理全面生产维护精益企业 TPM:全面生产维护TVM:全面可视化管理精益思想:(1)由顾客确定产品价值结构 。利用工业社会的规模优势和信息社会的信息低成本优势,来满足顾客个性化的需求。精益管理的出发点是产品价值结构,价值结构只能由最终顾客来确定,而价值结构也只有由具有特定价格、能在特定时间内满足顾客需求的特定产品(商品或服务,而经常是既是商品又是服务的产品)来表达时才有意义。 (2)变“成批移动”为“单件流动”。(3)生产由顾客拉动 。采用拉动式系
16、统可以真正实现按需生产。拉动式生产就是从市场需求出发,由市场需求信息决定产品组装,再由产品组装拉动零部件加工。整个过程相当于从后(后工序)向前(前工序)拉动,故这种方式被称为拉动式(Pul1)方法。(4)消除产业价值链的muda(日文的muda,是浪费的意思,延伸为:任何没有附加价值的作业)。 二、对待质量的心态与改善工具质量:不仅仅是“结果面”的质量 “结果面”的质量:客户对产品和服务的满意度 “过程面”的质量:从订单到发货一切过程的工作心态和质量对待缺陷,三不政策 DONT ACCEPT 不接受! DONT MAKE 不制造! DONT DELIVER 不传递!质量方法的三步曲 源头防范开
17、发与设计 质量功能展开QFD 失效模式分析FMEA 并行工程CE 过程控制生产与制造 持续改善PDCA 三、熟悉成本结构并持续削减成本1、精益生产与成本的关系质量间接员工精益的通俗定义灵巧的双手投资直接员工间接员工质量产品生命周期成本LEAN全自动Cost管理创造价值所说的浪费,指多余的“花費”。排除浪费(无用功,空闲)不是责人,而是攻事(事实)关键是对现场的看法思路认识(设计)的方法变动费固定费其他水电费直接劳务费材料费能拉开差距制造方法不同、固定费的使用方法不同,成本大不相同。很难拉开差距TPS对成本的认识(从降低到改善) 管理技术对整体最优化的追求成本成本降低成本改善产生C/F的发动机组
18、织机制构建(调味品)各企业间难有大的差别。过程周期时间缩短流动化暗知明知管理成本生命线(眼看不到的竞争力的源泉)現金主義(掩盖問題本質)产品的制造方法工作的推进方法管理的运转方法人的使用方法物的传送方法 易被模仿难被模仿20世纪后半期,世界汽车工业进入一个市场需求多样化的新阶段,而对质量的要求也越来越高,这就给制造业提出了这样一个新课题:只有有效地组织多品种、小批量生产,避免生产过剩所引起的设备、人员、库存、资金等一系列资源浪费,以保持企业竞争能力。在这种历史背景下,从丰田相佐诘开始,经丰田喜一郎及大野耐一等人的共同努力,综合了单件生产和批量生产的特点和优点,创造了一种多品种、小批量混合生产条
19、件下高质量、低消耗的生产方式。 追根溯源,从理论渊源上看,它是美国企业管理理论与日本本土企业实践”嫁接”的产物。2O世纪50年代初,朝鲜战争爆发,美军为了解决后勤军需问题,就近在日本下订单,采购军需品。但从朝鲜前线反馈回来的信息表明,从日本采购的电话机质量不稳定,问题较多。麦克阿瑟将军到日本去视察,发现日本企业完全是手工作坊式的装配,没有明确的分工和作业流程,更别提流水作业了。于是,麦克阿瑟将军请美国国防部的军需官,为日本企业起草了MTP (中级管理技术)和JIS(基层督导员相当于主任或班组长)两套培训教材,借助这两套教材,日本企业开始了从模仿外国产品到学习外国管理的转型过程,把美式管理中的技
20、术层面同日本文化结合起来,从而诞生了TPS。 2、产品成本的构成分摊费用 20 30 % 直接人工 5 15% 材料成本 50 70% 四 、加快库存周转缩短交货期1、什么是库存?现 金原辅料 存 货现 金使存货量最小使存货损失最小使存货转化为现金的时间最短 产 品在制品WIP2、加快库存周转的两个方向:库存周转=销售成本(原材料+在制品+成品)库存余额X 12方向一:加大分子 方向二:减小分母3、制造系统中的时间企业的生产流程包括:订单处理、物料计划、采购下单供应商备料、运输、来料检验、存储、搬运、加工、检验和返工、过程等待、成品库存、发运、货款回收等环节订单处理采购下单供应商备料运输来料检
21、验原料存储搬运和等待加工检验及返工成品存储成品发运货款回收制造周期交付周期5S:素养(系统化)2S:整顿3S:清扫4S:清洁(标准化)1S:整理更高质量更低成本提高安全性降低废品率提高产品多样性提高交付可靠性五、通过5S与可视化让问题表面化1、现场5S管理整理 整顿 清扫 清洁 素养 +安全 +节约 +学习2、 5S精髓回顾项目内容/定义理论/原则方法/工具目的1S整理要/不要区分:功能/使用价值、使用频率处理:1、报销、2、回收、3、降级、4、变更用途 5、放入指定地点、6、其它抽屉/樱桃彻底/高标准先示范后推广、激励、排名红单/排空间2S整顿要放好三定(定点、定量、定容)/三易(易找、易取
22、、易放)目视/可视化时间3S清扫扫三扫:1)扫黑:表面2)扫漏:内在 3)扫怪:目标与现状的差异、问题清扫分工表(区域、岗位、责任人、工具、方法、频率)美化环境4S清洁以上3S反复做标准化制度/程序/标准化巩固5S素养身美要我做-我要做,执行-主动参与、长期教育/培训人品3、做5S就是做可视化标准化作业(1)可视化让问题表面化可视化原则:视觉化(彩色管理) 透明化(把隐藏的地方显露出来) 界限化(上下线.界线标示出来)目的:要管理的地方和物品上做标示,让任何人容易认出,方便使用,容易判断及遵守(2)可视化8大专业手法 管理看板 色标管理 地址系统 操作图表卡 快速反应信号 形迹管理与防呆 油漆
23、工程 定点定向拍摄4、(1)现场管理看板小虎队现场管理Jan. Apr. Jul. Dec.生产率Goal合理化建议GoalGoal员工信息中心Jan. Apr. Jul. Dec.Jan. Apr. Jul. Dec.Jan. Apr. Jul. Dec.多种技能Jan. Apr. Jul. Dec.我们的口号:零缺陷!Goal质量缺陷率(2)色标管理合格品或安全区待审查区固定位置的物品废品、返工区有害物品或防撞标识红蓝白黄灰一般区域(3)地址系统P54P54-AO54P55O55A23457891006908070203040506010DBA02020DBA02010DBA02040DB
24、A02060DBA0205023457891006908070203040506010DBA02030DBA02070DBA02080DBA02100DBA02090DBA01010DBA01020DBA01030DBA01040DBA01050DBA01060DBA01070DBA01080DBA01100DBA01090SWENFA-OP54/55-L01FA-OP54/55-L02(4)操作图表卡全面质量管理操作校验校核基线安装光学器件压紧螺钉(5) 快速反应信号 - Andon 板好处: 提供下列视觉和听觉帮助: - 目前生产状态 - 库存情况 - 设备状态 - 质量状态 - 需求援助
25、状态 - 按节拍生产状态支持小组的快速反应 提高运行能力Andon 板(6) 形迹管理与防呆Everything has its place and everything in its place每件物品有指定的位置!定位的时候将物品轮廓画出来,更加直观,一目了然TOOLS锤子扳手螺丝刀121081210812108(7)油漆工程(8)定点定向拍摄后前 供应商 顾客信息控制工序C工序A工序B第三部分 价值流分析找出浪费关键:前后一致理解流程看到价值憧憬未来状态1、什么是价值流一个产品的主要流程所需要经过的所有行动(包括增加价值的行动和不增加价值的行动):1) 从原材料到成品2) 从概念到正式发
26、布的产品设计流程3) 从订单到付款流程2、为什么要图析价值流n 建立超越单个工艺过程层次而看到宏观生产流程的能力n 帮助发现浪费源n 展示了信息流与物流之间的联系n 广泛沟通的工具n 确定优先次序n 结合精益的概念与技术避免“只挑容易的” 来改进 n 形成实施计划的基础n 描绘为了影响这些定量的数据,应该做些什么3、价值流图析步骤Product family产品族工作计划及实施Current status当前状态图Future status未来状态图 将注意力集中在单个的产品族上 了解工艺工程当前是如何运作的 设计一个精益价值流 制订“未来状态”的实施计划4、从增值比看改善的空间 增值比率增值
27、时间(Value added time)制造周期(Manufacturing cycle time)X 100%=增值时间:站在客户立场看制造过程中的增值动作和时间如:改变形状、改变性能、组装、包装等5、六大损失、七大浪费精益管理的目标可以概括为:企业在为顾客提供满意的产品与服务的同时,把浪费降到最低程度。企业生产活动中的浪费现象很多,主要可概括为:六大损失、七大浪费。努力消除浪费现象是精益管理的最重要的内容。 (1)生产中的能力损失:停机损失 换型损失(从合格到合格) 故障损失 其它损失 质量损失 速度损失(定额速度 、标准速度、 实际速度)YESNO设备计划运行吗?NO设备有能力运转吗?N
28、O设备在运行吗?IN GOOD PRODUCTION计划停机时间换型时间故障维修时间其他损失(待料,早退) YES YES设备设置好了吗? YESNO设备在生产合格产品吗?质量损失 YESNO设备在全速运行吗?速度损失 YESNO(2)七种浪费过量生产: 实际上不需要的加工和程序;库存 因无需求造成的积压和多余的库存多余搬运 不必要的物品移动;返工/检验 提供有缺陷的产品或不满意的服务。过程不当 提供顾客并不需要的服务和产品。多余动作:人员在工作中不必要的动作等待 因生产活动的上游不能按时交货或提供服务而等候; 其中:库存为七大浪费之首。交货问题质量问题效率问题维修问题库存水平1)库存掩盖所有
29、问题交货问题质量问题效率问题维修问题库存水平2)通过降库存暴露问题3)通过降库存暴露问题交货问题质量问题效率问题维修问题第四部分 精益核心技术减少并消除浪费一、TPM(全面生产维护)的内容5S(整理、整顿、清扫、清洁、素养) 零灾害、零不良、零故障零损失自主保养计划保养产品、设备开发管理个别改善教育训练品质保养间接部门效率化安全与卫生企业经营效率化1、 设备三件事:1)预防性维护 MTBF(平均故障间隔时间) 2)快速修复-生产 MTTR(平均故障修复时间) 3)快速换型-切换 换型时间百分比 2、 零缺陷法则 隐藏的异常现象Hidden abnormalities暴露隐藏的异常现象,在它们发
30、生之前预防品质和功能的缺陷Expose hidden abnormalities and prevent quality and functional failures before they happen FAILURES缺陷磨损、松动、泄漏、污垢、灰尘腐蚀、变形、原物料的粘连、表面缺陷破裂、过热、颤动、噪音、及其它异常现象。Wear, play, slackness, leakage, dust, dirt, corrosion, deformation, adherence of raw materials, surface damage, cracking, overheating,
31、vibration, noise, and other abnormalities缺陷只是露在水面上的冰山一角A failure is the tip of the iceberg!3、 零故障的五种对策:为减少设备故障,实现零故障目标,制造与保养部门的任务健全基本条件遵守使用条件复元劣化部分提升技术水准改善设计上的弱点清扫、加油、加锁紧设定正确的电压、电流、油压外观异常点检连络有计划的修理定期点检提高精度、可靠度“零”错误的修理技术保养部门的任务技术支持活动使用部门的任务自主保养活动信息交换“零”操作错误的技能二、需求节拍与生产线平衡(需求)节拍与生产线速度 .节拍时间确定了每一工位必须完成
32、工作的速率(操作周期时间)节拍时间是流动线的节奏或拍子可用工作时间1、(需求)节拍与生产线速度 客户需求数量Takt节拍时间=2、设计一个好的节拍时间 Takt Time (seconds)30 120 改善余地小 很难应付变动 紧张 太长的工作步骤,难以标准化 操作岗位轮换不容易 注意力分散合适区域节拍时间复杂度三、找到并改善生产瓶颈1、 消除系统瓶颈和变差T/T 消灭七大浪费 消除六大损失 员工培训 全员参与 标准化操作消除简化合并工具箱2、如何提高瓶颈产出 五步法n 步骤一 找出系统的瓶颈n 步骤二决定如何挖尽瓶颈的潜能(不停运转)n 步骤三其它的一切配合上述决定n 步骤四 把瓶颈松绑(
33、绕过、替代、外包)n 步骤五 假如步骤四打破了原有的瓶颈,那么就回到步骤一四、实施均衡与流动生产1、实现流动生产的四个前提涂刷机加焊接冲压我们的流动线是U型布局,可随时满足顾客的要求 我们的员工是多技能的,因为实施单件流,WIP不断降低因为实行快速换型,我们可以每天生产所有的型号因为作业标准化,我们可以生产出质量最好的产品2、 “U”型布局和连续流 Job/Function Based Layout Flow Based Layout U-Shape Layout工厂布局类型。按功能布局(集中、利用率高)。按流程布局(搬运多、周期长、能力损失大)。U型布局(优化布局)。U型的变种(E,X,Y,
34、etc.) Why?U-shape Advantages:可结合Job与Flow布局的优势“U”型布局和连续流123 45610987 Flexible Line Capacity One - Piece Flow Communication Save Space具有柔性生产能力有利于单件流便于员工沟通节约场地Why?U-shape必备条件1、人流在内、物流在外。2、人员站立操作。657891043213、快速换型好处:减少停机时间,增加生产计划的灵活性,减少浪费,减少库存成本,提高运行能力。快速换型八步法现场观察并写下换型步骤记录时间和各种浪费区分内部及外部活动 分析所有换型动作把可能的内部
35、动作转为外部优化内外部操作试验并改进新设想STEP 1STEP 2STEP 3STEP 4STEP 5STEP 6STEP 7建立和实施新的操作标准 STEP 84、 标准化:是改进的基础n 为什么要标准化? - 代表最好的、最容易的和最安全的方法 - 提供了一种衡量绩效的手段 - 表现出因果之间的联系五、培养多技能员工好处:对于员工:-知道自己技能水平-了解需要学习的技能-产生学习新技能的欲望-明白可以向谁学习请教对于领导:-知道现场管理者培养下属的结果-可以监督员工的技能培养-体现规范化的现场管理水平对于管理者:-知道下属技能水平-便于应急安排工位-激发下属学习新技能欲望-便于对下属技能考
36、核六、推进看板拉动系统1、拉动系统及供应链我们只在需要的时候发运需要的物料拉动系统配料地址0017-0010-002R2、JIT 物料运动的目标在正确的时间以正确的方式按正确的路线把正确的物料送到正确的地点,每次都刚好及时。3、拉动系统:物流和信息流Material 物料Pull Card 拉动卡Key 要点:PlantsupermarketComponentsAssembly物流信息流4、拉动系统:看板如何工作当操作根据节拍时间平衡后,在工艺流程中使用“方型”看板来作为工作与拉动零件的信号操作 #1操作 #2操作 #3K物流方向K= 满看板K= 空看板拉动工作信号不工作开始工作工序看板系统5
37、、看板拉动的六大规则 规则一:后一道工序要到前一道工序去取货。 规则二:前一道工序只生产后一道工序要领取的数量。 规则三:没有看板时不运送、不制造。 规则四:看板一定要挂在作业的相关实物上。 规则五:必须生产百分之百的合格品。 规则六:逐步减少看板的数量。第五部分 从精益生产到精益管理 精 态度 准 习惯 细 技能 严 文化KASH一、 精益管理的四个特征精态度态度您最宝贵的财富精益求精,追求最好准习惯准确准时 效率与效果矩阵 PDCA管理循环 时间管理矩阵细技能SOP(标准作业细化)n 工作 n 重现性n 人的动作n 设备及生产线n 最少的问题n 品质n 均匀 严文化按章执法,无缝考核。怎样
38、增强员工执行能力: “当变化由我们完成时,它是令人激动的,而当它发生到我们身上时,就是危险的。”l 没有人会拒绝改变,但所有人都拒绝被改变。l 员工不会做你希望的,只会做你检查的。二、如何进行精益的产品研发精益的产品研发:u QFD质量功能展开u MEA失效模式分析u CE并行工程1、QFD质量功能展开质量功能展开图(Quality Function Deployment, QFD):是一种有组织, 有步骤的工具,用来辩别客户的需要,并且把该种需要准确的转化成产品的可测量的具体技术指标,以及进一步转化成生产控制的要求。 产品的研制产品的制造转化转化客户的需要 通过制作质量功能展开图,认真地倾听
39、客户的心声。质量功能展开图建造质量屋WhatImportance(1) 列出客户的需要(3) 列出主要输入“ ys”Big Y(2) 对客户需要的重要性排序(4) 输入与客户要求之间的关系QFD排序: 1 至 5关系: 1, 3, 92、FMEA失效模式分析失败模式及效果分析( Failure Mode & Effect Analysis),辩别产品或流程潜在的会发生缺陷的地方,作好计划以防止这些缺陷发生FMEA 工作原理失败的模式产品的功能后果+ 严重程度Severity (1-10)原因+ 发生的频率Occurrence (1-10)控制措施+ 易觉察性Detectability (1-1
40、0)RPN持续改善风险排序 (RPN)RPN=S x O x D = 1 to 1000Titanic Example (泰坦尼克的例子)产品TitanicApril 15,1912泰坦尼克号。1912年4月15Transportpeople acorssOcean运载旅客穿越大西洋Sinking沉船Loss of Life (10)丧命No futurebusiness (5)将来没生意Loss of Property (8)蚀财Traveling toofast ( 8)航速太快Not postinga lookout (6)未设置了望塔Not heedingwarning of iceb
41、ergs (9)未留意冰山警告Over-Confidencein unsinkability( 9)对不会沉没的过分自信Speedmeter (2)航速表1084160240720900功能失败模式后果/严重程度模式原因/发生频率控制/易察觉性RPNContinuousImprovement持续改善3、CE并行工程 1986年,美国国防工程系统首次提出了“并行工程”的概念,初衷是为了改进国防武器和军用产品的生产,缩短生产周期,降低成本。由于该方法的有效性,不久,各国的企业界和学术界都纷纷研究它,并行工程方法也从军用品生产领域扩展到民用品生产领域。1986年美国国防分析研究所在其R-338研究报
42、告中提出的定义: “并行工程是对产品及其相关过程(包括制造过程和支持过程)进行并行的一体化设计的一种系统化的工作模式。这种工作模式力图使开发者们从一开始就考虑到产品全生命周期(从概念形成到产品报废) 中的所有因素,包括质量、成本、进度和用户需求”。 简要地来讲,并行工程即concurrent engineering,简称CE,是集成地、并行地设计产品及其零部件和相关各种过程(包括制造过程和相关过程)的一种系统方法。换句话说,就是融合公司的一切资源,在设计新产品时,就前瞻性地考虑和设计与产品的全生命周期有关的过程。在设计阶段就预见到产品的制造、装配、质量检测、可靠性、成本等各种因素。三 创建精益
43、的供应链1、全流程的精益供应链新产品开发营销与销售采购生产制造 物流配送产品研究与开发并行工程供应商早期参加分销系统与销售管理零售商伙伴关系订单处理流程“精益化”零部件供应系统供应商能力培育JIT式供应生产制造系统拉动式生产(JIT)零库存、零缺陷JIT配送系统降低库存物流“精益化” 精益管理是一个动态的、以顾客为导向的过程,通过这一过程,使企业内各个部门、全体员工都能够在创造价值的目标下不断地消除浪费。精益管理的思想概括2、供应链图析客户的客户现在要货!缓冲客户3 天制造商缓冲7 天供应商缓冲7 天供应商的供应商缓冲5 天 周MRP13 周 交付周期4 周 “执行”时间9 周缓冲预测变动3、
44、精益供应链图析客户的客户现在要货!缓冲客户1 天制造商缓冲3 天供应商缓冲1 周供应商的供应商缓冲1周半3 周拉动信号13 天 交付周期品种增加四、精益的人力资源:知人善任如何把合适的人放到合适的位置上五、精益的行政管理:厉行节约n 出差旅行 n复印机及办公设备n 应酬费 维护合同n 报销单 订阅报刊杂志n 办公面积 电话n 办公家具 会议成本n 办公用品 养成良好工作习惯n 不提倡打印 开会可以用投影,讨论可以用电邮 体验无纸办公n 可能的话,多使用便条n 砍掉多余的报表,停止不必要的文件流动 大多数的报告与复印件都是在浪费时间与金钱,明确限定公 司各个层面所需的报表与提交时间。n 发电邮时
45、,尽量少用CC 责任明确,减少彼此打扰n 提高会议效率 尽可能在一间屋子里,以尽量少的人做出决定。 开短会,尽量控制在30分钟以内。 开会只用来作出决定。六、支持全方位的变化n 生产部门 把支持功能从中央分散,建立产品团队 用团队解决问题并施行改进 整顿工作场地 消灭浪费,实施流动n 计划调度部门 依靠“拉式”系统 监控更少的工作中心 通过目视控制系统来管理支持全方位的变化n 维修管理部门 设备可用性与可靠性成为焦点 单元/流动线施行预防性维护并监控停工时间 快速换型生产与灵活性成为焦点 单元/流动线工具与换型管理n 质量部门 用失效模式分析设置监控/检验点 在可能的地方进行差错预防 支持单元
46、/流动线团队处理改进事宜n 采购部门 供应与需求“拉动”速率相连接 采购的准则:交货期 质量 价格 供应商需要培训与技术支援n 市场营销部门 准确及时的需求信息反馈 小批量观念,而不是累积大订单对生产的冲击 避免紧急订单 促销策略与营运部门一同制订n 产品开发部门 以可制造性设计/可装配性设计为重点 标准化产品 一次性合格生产设计 减少设计与成形产品的周期时间支持全方位的变化n 工艺部门 标准化工艺 习惯生产线节拍时间的考虑,远离传统的“工位效率” 差错预防工艺 将焦点从提高单个工序效率变更到消除约束(瓶颈,生产能 力,可靠性与柔性)上n 会计部门 事先成本法:倒冲劳动力与材料消耗/成本 从跟
47、踪工厂宏观绩效过渡到跟踪产品族绩效 从被动汇报到主动监控 支持小批量生产n 人力资源部门 实行培训计划 支持问题解决团队/建议制度 企业文化和绩效考评系统第六部分 精益成功的关键:人的因素一、团队建设/员工参与:塑造精益型员工我们小组的努力达到了目标团队建设/员工参与自然工作小组教育和培训健康和安全沟通建议及表彰Business ObjectivesScrapJan. Apr. Jul. Dec.UptimeGoalOn Time DeliveryGoalGoal员工信息中心Jan. Apr. Jul. Dec.Jan. Apr. Jul. Dec.从事工作的人员最了解其本职工作在工作地点的所
48、有层次上都需要作出决策受某一改革影响的人需要参与实施这个改革,(1)自然工作小组-NWG 激发主人翁精神 T Together 一起 通过消除浪费和关注客户 E Everybody 每人达到不断完善的目的 A Achieve 达到 培养多技能员工 M More 更多 提高效率(2)考核体系 考核班组,而不是个人 建立指标体系 指标得分决定班组奖金 定期奖励最佳班组小虎队现场管理Jan. Apr. Jul. Dec.生产率Goal合理化建议GoalGoal员工信息中心Jan. Apr. Jul. Dec.Jan. Apr. Jul. Dec.质量缺陷率Jan. Apr. Jul. Dec.多种技能Jan. Apr. Jul. Dec.我们的口号:零缺陷!Goal(3)宝洁经理人的九句真言1、回顾
- 温馨提示:
1: 本站所有资源如无特殊说明,都需要本地电脑安装OFFICE2007和PDF阅读器。图纸软件为CAD,CAXA,PROE,UG,SolidWorks等.压缩文件请下载最新的WinRAR软件解压。
2: 本站的文档不包含任何第三方提供的附件图纸等,如果需要附件,请联系上传者。文件的所有权益归上传用户所有。
3.本站RAR压缩包中若带图纸,网页内容里面会有图纸预览,若没有图纸预览就没有图纸。
4. 未经权益所有人同意不得将文件中的内容挪作商业或盈利用途。
5. 装配图网仅提供信息存储空间,仅对用户上传内容的表现方式做保护处理,对用户上传分享的文档内容本身不做任何修改或编辑,并不能对任何下载内容负责。
6. 下载文件中如有侵权或不适当内容,请与我们联系,我们立即纠正。
7. 本站不保证下载资源的准确性、安全性和完整性, 同时也不承担用户因使用这些下载资源对自己和他人造成任何形式的伤害或损失。