某机械厂2018年度生产计划的编制
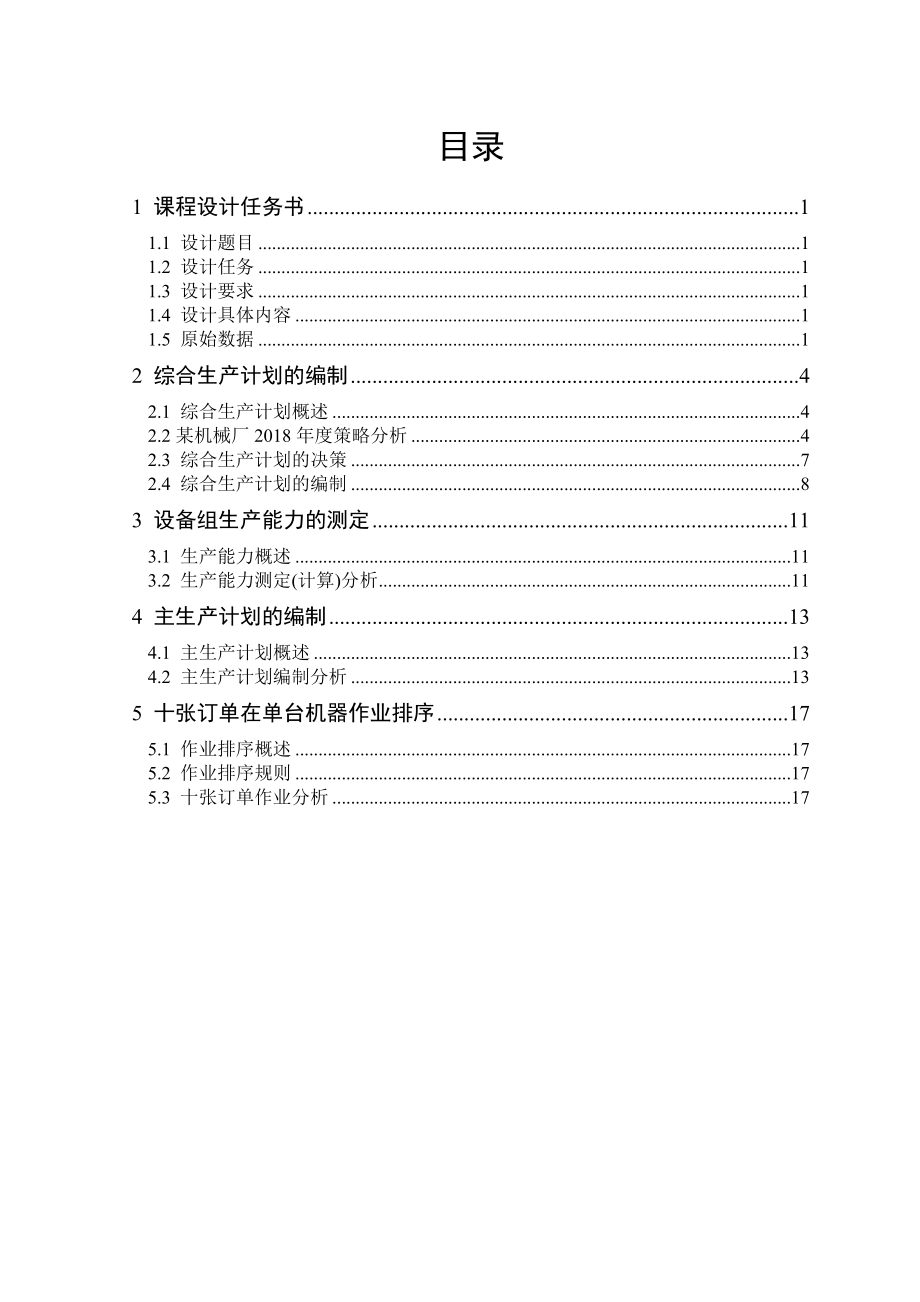


《某机械厂2018年度生产计划的编制》由会员分享,可在线阅读,更多相关《某机械厂2018年度生产计划的编制(22页珍藏版)》请在装配图网上搜索。
1、生产计划与控制课程设计目录1 课程设计任务书11.1 设计题目11.2 设计任务11.3 设计要求11.4 设计具体内容11.5 原始数据12 综合生产计划的编制42.1 综合生产计划概述42.2某机械厂2018年度策略分析42.3 综合生产计划的决策72.4 综合生产计划的编制83 设备组生产能力的测定113.1 生产能力概述113.2 生产能力测定(计算)分析114 主生产计划的编制134.1 主生产计划概述134.2 主生产计划编制分析135 十张订单在单台机器作业排序175.1 作业排序概述175.2 作业排序规则175.3 十张订单作业分析17211 课程设计任务书1.1 设计题目某
2、机械厂2018年度生产计划及生产作业计划的编制1.2 设计任务1、编制主流产品的综合生产计划与主生产计划(全年);2、编制机加工车间甲、乙、丙三种主要产品(零件)的生产作业排序。1.3 设计要求根据所提供的材料,按设计任务要求进行分析、计算和设计,并在2周内独立完成1份完整的课程设计报告。1.4 设计具体内容1、 编制综合生产计划,运用三种策略进行分析比较,选择最优方案;2、 计算设备组的生产能力;3、 编制主生产计划;4、 计算1-12月每周的现有库存;5、 十张订单在单台机器作业顺序的安排。1.5 原始数据1、该公司主要产品主流型机械的有关资料: 该产品2018年度各月出产计划见表1。 该
3、产品的投入批量为600,期初库存为400,设备组车床数15台。2、机加工车间主要产品甲、乙、丙、丁四种零件的有关资料: 四种零件结构、工业和劳动量构成差别较大,月产量分别为200,300,400和100件。 四种零件在主要工序的加工时间见表2。 每月工作天数见表1,每月份后面括号内为实际工作天数。3、其他相关数据 有关于成本的数据见表3。 关于订货量的预测,见表4。 十张订单情况见表5。表1 主流型产品2018年度各月出产计划月份(天)1(22)2(18)3(23)4(23)5(20)6(22)7(22)8(21)9(21)10(20)11(23)12(23)产品预测出产量方案89409608
4、408809009208408609608008201000表2 主要零件在车削工序上的加工时间零件名称月产量台时定额(台时/件)甲20010乙30025丙40040丁10015表3 相关数据成本类型成本值招聘成本200元/人解聘成本300元/人库存成本2元/件 月缺货成本5元/件 月材料成本100元/件分包成本20元/件单位产品加工时间5小时/件正常人工成本4元/小时加班人工成本6元/小时 表4 十二个月的订货量一月二月三月1周2周3周4周1周2周3周4周1周2周3周4周100100150200100300150100120100200150四月五月六月1周2周3周4周1周2周3周4周1周2
5、周3周4周120110130180110180150100130120160100七月八月九月1周2周3周4周1周2周3周4周1周2周3周4周130120150150120250150180160150160250续表十月十一月十二月1周2周3周4周1周2周3周4周1周2周3周4周120160150300150260100100150120200120表5 十张订单加工情况订单交货期(天)加工时间(天)剩余制造提前期作业数A15215B12333C10422D9551E72.544F63.566G111.577H54.599I192.2108J163.28102 综合生产计划的编制2.1 综合
6、生产计划概述1、综合生产计划的概念综合生产计划也称生产大纲、年度生产计划或年度生产大纲。综合生产计划是企业根据市场预测和企业所拥有的生产资源,对企业计划期内生产的产品、产量以及为保证生产所需的劳动力水平、库存等措施的决策性描述。正常的制定总和生产计划指标,既可以满足社会和用户需求,又能充分发挥企业的人力、物力和财力,还可以在提高劳动生产率和降低成本的基础上增加利润。2、综合生产计划编制步骤 确定计划期生产产品的市场需求; 分析外部约束条件和企业内部的生产条件; 拟定生产指标方案,方案优化; 综合平衡,编制计划草案; 审核批准综合生产计划。2.2某机械厂2018年度策略分析1、综合生产计划编制策
7、略3种策略的特点:追逐策略:通过调整员工的数量来达到满足生产要求,以适应变化的生产需求。平准策略:保持工人数量不变,将超出能力之外的工作外包出去,以满足最小需求预测。外包策略:通过改变库存量、订单积压和减少销售来消化缺货与剩余产品,保持稳定的劳动力数量和产品的生产量。2、三种编制方案的分析 Pi=DFi+SIi-BIi (2-1)式中:Pi每月实际需求量; DFi每月需求预测量; BIi每月初期需求量;SIi每月安全库存量;每月的期末库存公式为: Ei=Bi+Pi-DFi (2-2)式中:Ei每月月末库存量;Pi每月实际需求量;BIi每月初期需求量; DFi每月需求预测量;通过上述公式得出表6
8、:表6每月的实际需求量与库存量表月 份123456789101112期初库存量400235240210220225230210215240200205需求预测量9409608408809009208408609608008201000安全库存量235240210220225230210215240200205250实际需求量7559658108909059258208659857608251045期末库存量235240210220225230210215240200205250策略一:追逐策略,即满足需求量变化,以改变工人数调节生产能力,假设每班次工作8h。安全库存量=需求预测量25%每人月工
9、时=月工作天数8h 满足需求所需时间=实际需求量5小时/件所需人数=满足需求所需生产时间/每人月工时招聘成本=新招收的人员200元/人解聘成本=解聘人员300元/人自制材料成本=实际需求量100元/每件库存总成本=期末库存量2元/件正常人工总成本=满足需求所需时间4元/小时通过上述公式得出表7:表7 追逐策略成本分析表月 份123456789101112实际需求量7559658108909059258208659857608251045满足需求所需时间387548254050445045254625410043254925380041255225每月工作天数221823232022222121
10、202323每人每月工时176144184184160176176168168160184184所需人数2335 23252927242630242329招聘人数0120202024006招聘成本02400040004000400800001200续表月 份123456789101112解聘人数0012000300610解聘成本0036000009000018003000材料成本7550096500810008900090500925008200086500985007600082500104500库存成本470480420440450460420430480400410500正常人工成本15
11、5001930016200178001810018500164001730019700152001650020900总成本1283960由表7得出,招聘成本为5600元,解聘成本为6600元,自制材料成本为1055000元,正常人工成本为211400元,总成本为1283960元。策略二:平准策略,保持工人人数不变,变动库存,既不加班也不外包。固定工人人数。人数=5h总预测量/258天8h=5h10500(总预测量)/258天8h=26人可用生产时间=总人数工作天数工作时间安全库存量=需求预测值25%月末库存量=实际生产量-需求预测量多余库存成本=多余库存量2元/件自制材料成本=实际需求量100
12、元/件正常人工总成本=可用生产时间4元/小时通过上述公式得到表8:表8 平准策略成本分析表月 份123456789101112月初库存量400375164281358290285360374287319456月工作天数221823232022222121202323可用生产时间457637444784478441604576457643684368416047844784实际生产量915749957957832915915874874832957957需求预测量9409608408809009208408609608008201000月末库存量3751642813582902853603742
13、87319456413缺货成本000000000000安全库存量235240210220225230210215240200205250多余库存量140071138655515015947119251163自制材料成本915007490095700957008320091500915008740087400832009570095700多余库存成本280014227613011030031894238502326正常人工成本183041497619136191361664018304183041747217472166401913619136总成本1194797由表8得出,多余库存成本为271
14、6元,自制材料成本为1073400元,正常人工成本为214656元,总成本为1194797元。 策略三:外包策略。保持工人人数不变,将超出能力之外的工作外包出去,以满足最小需求预测。人数=5h最小预测量12个月/258天8h=5h800件(最小预测量) 12个月/258天8h=23人可用生产时间=总人数工作时间工作天数实际生产量=可用生产时间/单位产品加工时间外包件数=需求预测值-实际生产量外包总成本=外包件数20元/件自制材料成本=实际需求量100元/件正常人工总成本=可用生产时间4元/小时通过上市公式得出表9:表9 外包策略分析表月 份123456789101112需求预测量9409608
15、408809009208408609608008201000月工作天数221823232022222121202323可用生产时间404833124232423236804048404838643864368042324232实际生产量810662846846736810810773773736846846外包件数00001201103087187640128外包成本00002400220060017403740128002560库存量270060000000260库存成本5400120000000520自制材料成本810006620084600846007360081000810007730
16、077300736008460084600正常人工成本161921324816928169281472016192161921545615456147201692816928总成本1154988由表9得出,外包成本为14520元,库存成本为1180元,自制材料成本为864800元,正常人工成本为189888元,总成本为1154988元。2.3 综合生产计划的决策将三种策略种花费的各种成本进行汇总,并对各成本进行比较得到表10:表10 三种策略的比较分析表成本项追逐策略平准策略外包策略正常人工成本211400214656189888招聘成本560000解聘成本660000外包成本0016520库
17、存成本53602716604材料成本10550001073400949400缺货成本000总成本1283960119479711549882.4 综合生产计划的编制1、综合生产计划的编制综合生产计划计划的编制方法:线性规划法、运输表法、动态分析法、模拟仿真法、试算法等。运输表法是应用普遍的生产计划优化方法。假定产量、成本等有关变量之间的关系是现行的,假定一个简单的生产系统有三种生产方式:正常班次生产、加班生产和外包生产,产品可在计划期储存,不允许缺货。2、运输表法步骤运输表法的基本假设是:每一单位计划期内正常生产能力以及外包均有一定限制;每一单位计划期的预测需求是已知的;全部成本都与产量呈线性
18、关系。在这些假设之下图表法可算出整个计划中每一个单位最优生产计划。检查方案是否可行原则: 未使用的能力不能为负数; 每一行的生产任务总额(包括未使用的能力)应等于该行的总生产能力; 每一列生产任务总额等于该列需求。通过对外包策略的分析得出表11:表11 外包策略成本运输表月份生产方式需求/件生产能力总件总成本123456789101112一期初库存400(20)27006000000026正常生产810(20)270(22)108022140外包生产二正常生产662(20)66213240外包生产28(20)28560三正常生产846(20)6(22)85217052外包生产四正常生产846(
19、20)84616920外包生产28(20)28560续表月份生产方式需求/件生产能力总件总成本123456789101112五正常生产736(20)73614720外包生产164(20)1643280六正常生产810(20)81016200外包生产110(20)1102200七正常生产810(20)81016200外包生产30(20)30600八正常生产773(20)77315460外包生产87(20)871740九正常生产773(20)77315460外包生产187(20)1873740十正常生产736(20)73614720外包生产64(20)641280十一正常生产846(20)26(2
20、2)87217492外包生产十二正常生产846(20)84616920外包生产128(20)1282560需求9409608408809009208408609608008201000通过对运输成本分析表进行分析计算,编制总和生产计划表,得到表12:表12 综合生产计划表月份123456789101112总计需求量940960840880900920840860960800820100010720续表月份123456789101112总计计划量941960843884905926847868969810831101210796正班生产108066285284673681081077377373
21、68728469796外包生产0280281641103087187640128826库存量23524021022022523021021524020020525026803 设备组生产能力的测定3.1 生产能力概述1. 生产能力概述生产能力是指企业的固定资产,在一定时期内和一定得技术组织条件下,经过综合生产平衡后所能生产的一定种类产品最大的量。工业企业的生产能力是指直接参与产品生产的固定资产的生产能力,在确定生产能力时,不考虑劳动力不足或物资供应中断等不正常的现象。 企业的生产性固定资产; 生产能力是在企业可能达到的技术组织条件下确定的,不考虑劳动力不足和物质供应中断等不正常现象; 以实物指
22、标为计量单位; 一般以最大产品数量来表示,有时也以加工的原材料的最大数量表示。2. 生产能力的种类 设计能力 是指工业企业基本建设时,设计任务书与设计文件中所规定的生产能力。它是企业新建、改建和扩建后应该达到的最大年产量。 计划能力 是指企业在年度内依据现有的生产技术组织条件,能够达到的生产能力。它是以现有生产条件,并考虑到在年度内能够实现的各种技术的、组织的措施的效果来确定的。 实际能力 是指企业固定资产、协作关系、和生产技术组织条件下所能达到的生产能力。3.2 生产能力测定(计算)分析1. 测定生产能力的程序 确定企业的专业方向和生产大纲; 做好测定生产能力的准备工作; 计算(计算设备组、
23、工段和车间的生产能力); 进行全厂生产能力的综合平衡。2. 生产能力的计量单位 具体产品:单品种的企业以其产量来核定生产能力。 代表产品:多品种生产企业中,在结构、工艺和劳动量相近的产品中选择有代表性的产品的时间定额或者产量定额来计算生产能力。 假定产品:产品品种较多时,结构、工艺差别较大时,采用假定产品来核定。3.设备组生产能力的计算 在单一品种生产情况下,采用设备组的生产能力来核定生产能力。 在多品种生产,且加工对象在工艺、结构上相似时,采用代表产品核定生产能力。 在多品种,结构、工艺差别较大时,采用假定产品计算产品的生产能力。由于加工甲、乙、丙,丁四种产品的结构和工艺相差较大,故代表产品
24、不能代表全部产品,所以采用假定产品计算单位进行设备组生产能力的计算。已知设备组有15台车床,每台车床全年有效工作时间为8258=2064h,通过假定生产产品方法计算得出表13:单位假定产品台时定额=单位产品台时定额各产品占产量总数的比重;假定产品表示的生产能力=2588(1设备维修率)15/单位假定产品台时定额;设备维修率为10%。表13 生产能力分析表产品名称计划产量单位产品台时定额各产品占产量的比重单位假定产品台时定额假定产品标识的生产能力具体产品的生产能力=甲2001020%2206乙3002530%7.5310丙4004040%16413丁1001510%1.5103总计1000901
25、27103210324 主生产计划的编制4.1 主生产计划概述主生产计划是在综合生产计划的基础上确定各种产品的生产数量和时间进度,是综合生产计划的具体化的指标,是进一步编制生产作业计划的依据。主生产计划是以综合生产计划、市场需求预测和客户订单等作为输入,安排计划周期中的生产数量和生产时间,将生产计划转换成产品计划,是一个详细的进度计划。4.2 主生产计划编制分析1、主生产计划计算主生产计划制定步骤: 计算现有库存量。 确定主生产计划的生产量和生产时间。 主生产计划和生产时间应保证现有库存为非负,要及时为补充库存而启用主生产计划生产。为了使生产计划满足需求量而得出表14:表14 主生产计划表月份
26、项目一月二月三月周次123412341234需求预测235235235235240240240240210210210210订货量100100150200100300150100120100200150毛需求235235235235240300240240210210210210现有库存量(400)16553029560420120480240304202100主生产计划量600600600600月份项目四月五月六月周次123412341234需求预测220220220220225225225225230230230230订货量120110130180110180150100130120160
27、100毛需求220220220220225225225225230230230230现有库存量(400)3801605403209547024520390160530300主生产计划量600600600600600续表月份项目七月八月九月周次123412341234需求预测210210210210215215215215240240240240订货量130120150150120250150180160150160250毛需求210210210210215215215215240240240240现有库存量(400)90480270604452301540016052028040主生产计划量6
28、00600600600月份项目十月十一月十二月周次123412341234需求预测210210210210215215215215240240240240订货量130120150150120250150180160150160250毛需求210210210210215215215215240240240240现有库存量(400)90480270604452301540016052028040主生产计划量6006006006002、计算现有库存量现有库存量指每周的需求被满足之后剩余的可利用的库存量,其计算公式为: It=It-1+Pt-maxDt,MOt (4-1)式中:Itt周末的现有库存 I
29、t-1t-1周末的现有库存 Pt t周的主生产计划量 Dt t周预测需求 MOtt周准备发货的订货量通过上述公式并进行分析计算得到表15: 表15 现有库存表月份项目一月二月三月周次123412341234期初库存4001655302956042012048024030420210需求预测量235235235235240240240240210210210210订货量100100150200100300150100120100200150主生产计划量06000060006000060000现有库存16553029560420120480240304202100续表月份项目四月五月六月周次123
30、412341234期初库存03801605403209547024520390160530需求预测量220220220220225225225225230230230230订货量120110130180110180150100130120160100主生产计划量6000600006000060006000现有库存3801605403209547024520390160530300月份项目七月八月九月周次123412341234期初库存300904802706044523015400160520280需求预测量210210210210215215215215240240240240订货量1301
31、20150150120250150180160150160250主生产计划量06000060000600060000现有库存90480270604452301540016052028040月份项目十月十一月十二月周次123412341234期初库存404402202032011545525045395145495需求预测量200200200200205205205205250250250250订货量120160150300150260100100150120200120主生产计划量6000060006000060006000现有库存4402202032011545525045395145495
32、2453、计算待分配库存待分配库存计算分两种情况:一是第一期的待分配库存量等于期初现有库存量加本期的主生产计划量减去直至主生产计划量到达前各期的全部订货量;二是以后各期只有主生产计划量时才存在待分配库存量,计算方法时该期的主生产计划量减去从该期至下一主生产计划量到期前各期全部订货量。如表16所示:表16 待分配库存表月份项目一月二月三月周次123412341234期初库存4001655302956042012048024030420210需求预测量235235235235240240240240210210210210订货量10010015020010030015010012010020015
33、0主生产计划量06000060006000060000待分配库存3001500020002300015000续表月份项目四月五月六月周次123412341234期初库存03801605403209547024520390160530需求预测量220220220220225225225225230230230230订货量120110130180110180150100130120160100主生产计划量6000600006000060006000待分配库存3700180001700035002100月份项目七月八月九月周次123412341234期初库存300904802706044523015
34、400160520280需求预测量210210210210215215215215240240240240订货量130120150150120250150180160150160250主生产计划量06000060000600060000待分配库存018000800026004000月份项目十月十一月十二月周次123412341234期初库存404402202032011545525045395145495需求预测量200200200200205205205205250250250250订货量120160150300150260100100150120200120主生产计划量6000060006
35、000060006000待分配库存17000150140000330028005 十张订单在单台机器作业排序5.1 作业排序概述作业排序是指在多品种生产任务中,决定生产任务进入生产的顺序,以解决对关键设备或关键工作重心环节需求的矛盾。尽可能满足各种约束条件下做出最佳排序方案。5.2 作业排序规则作业排序九种规则: FCFS(先到优先):按订单到达的先后顺序进行加工; SPT(最短工时时间优先):优先选择最短加工时间的任务; EDD(交货期优先):最早交货期最早加工; SST(最松弛时间):松弛时间是指距交货期前所剩余时间所得差值,优先权给剩余时间最短的任务; MWKR(余下加工时间最长优先):
36、优先选择余下加工时间最长的任务; SCR(关键比最小优先):优先选择关键比最小的任务; LWKR(余下加工时间最短优先):优先选择余下时间最短的任务; MOPNK(余下工序最多优先):优先选择余下工序最多的任务; RNDOM(随机挑选):随机挑选任务。5.3 十张订单作业分析延迟大于0代表有延迟,小于0代表无延迟,总延迟时间为所有延迟的工位延迟时间之和。平均流程时间=总流程时间/工位数平均延迟时间=总延迟时间/工位数根据以上公式并按照9种不同规则得到以下各排序表1725。表17 FCFS(先到优先)规则排序表订单加工时间交货期开始时间结束时间延迟误期A21502-130B31225-70C41
37、059-10D5991455续表订单加工时间交货期开始时间结束时间延迟误期E2.571416.59.59.5F3.5616.5201414G1.5112021.510.510.5H4.5521.5262121I2.2192628.29.29.2J3.21628.231.415.415.4根据表17可知,流程时间为结束时间总和为173.6天,平均延迟时间为173.6/10=17.36天;其中仅有A、B、C订单无延迟,其他订单均有延迟,总延迟时间为84.6天,平均延迟时间为84.6/10=8.46天。表18 SPT(最短加工时间优先)规则排序表订单加工时间交货期开始时间结束时间延迟误期G1.511
38、01.5-9.50A2151.53.5-11.50I2.2193.55.7-13.30E2.575.78.21.21.2B3128.211.2-0.80J3.21611.214.4-1.60F3.5614.417.911.911.9C41017.921.911.911.9H4.5521.926.421.421.4D5926.431.422.422.4根据表18可知,流程时间为结束时间总和为142.1天,平均流程时间为142.1/10=14.21天;其中仅有A、B、G、I、J订单无延迟,其他订单均有延迟,总延迟时间为68.8天,平均延迟时间为68.8/10=6.88天。表19 EDD(交货期优先
39、)规则排序表订单加工时间交货期开始时间结束时间延迟误期H4.5504.5-0.50F3.564.5822E2.57810.53.53.5D5910.515.53.53.5C41015.519.59.59.5G1.51119.5211010B31221241212A21524261111J3.2162629.213.213.2I2.21929.231.412.412.4根据表19可知,流程时间为结束时间总和为189.6天,平均流程时间为189.6/10=18.96天;其中仅有A订单无延迟,其他订单均有延迟,总延迟时间为80.1天,平均延迟时间为80.1/10=8.01天。表20 SST(最松弛时
40、间)规则排序表订单加工时间交货期松弛时间开始时间结束时间延迟误期H4.550.504.5-0.50F3.562.54.5822D59481344E4.574.51315.58.58.5C410615.519.59.59.5B312919.522.510.510.5G1.5119.522.5241313J3.21612.82427.211.211.2A2151327.229.214.214.2I2.21916.829.231.412.412.4根据20表可知,流程时间为结束时间总和为194.8天,平均流程时间为194.8/10=19.48天;其中仅有H订单无延迟,其他订单均有延迟,总延迟时间为8
41、5.3天,平均延迟时间为85.3/10=8.53天。表21 MWKR(余下加工时间最长优先)规则排序表订单加工时间交货期剩余制造提前期关键比开始时间结束时间延期误期I2.2191012.2-16.80IH4.5592.36.71.71.7HJ3.21686.89.9-6.10JG1.51171011.4-0.40.4GF3.56611.514.98.98.9FD5951519.910.910.9DE2.5742022.415.415.4EB312322.525.413.413.4BC410225.529.419.419.4CA215129.531.416.416.4A根据表21可知,流程时间为
42、结束时间总和为173.6天,平均流程时间为173.6/10=17.36天;其中仅有订单H、J无延迟,其他订单均有延迟,总延迟时间为86.5天,平均延迟时间为86.5/10=8.65天。表22 SCR(关键比最小优先)规则排序表订单加工时间交货期剩余制造提前期关键比开始时间结束时间延期误期H4.5590.104.5-0.50F3.5660.44.5822D5950.881344E2.5741.11315.58.58.5G1.51171.415.51766J3.21681.61720.24.24.2I2.219101.720.222.43.43.4B3123322.425.413.413.4C41
43、02325.429.419.419.4A21511329.431.416.416.4根据表22可知,流程时间为结束时间总和为187.8天,平均流程时间为187.8/10=18.78天;其中仅有订单H无延迟,其他订单均有延迟,总延迟时间为78.3天,平均延迟时间为78.3/10=7.83天。表23 LWKE(余下加工时间最短优先)规则排序表订单加工时间交货期剩余制造提前期开始时间结束时间延期误期A215112-130C41022.16-40B31236.19-30E2.5749.111.54.54.5D59511.616.57.57.5F3.56616.6201414G1.511720.121.510.510.5J3.2
- 温馨提示:
1: 本站所有资源如无特殊说明,都需要本地电脑安装OFFICE2007和PDF阅读器。图纸软件为CAD,CAXA,PROE,UG,SolidWorks等.压缩文件请下载最新的WinRAR软件解压。
2: 本站的文档不包含任何第三方提供的附件图纸等,如果需要附件,请联系上传者。文件的所有权益归上传用户所有。
3.本站RAR压缩包中若带图纸,网页内容里面会有图纸预览,若没有图纸预览就没有图纸。
4. 未经权益所有人同意不得将文件中的内容挪作商业或盈利用途。
5. 装配图网仅提供信息存储空间,仅对用户上传内容的表现方式做保护处理,对用户上传分享的文档内容本身不做任何修改或编辑,并不能对任何下载内容负责。
6. 下载文件中如有侵权或不适当内容,请与我们联系,我们立即纠正。
7. 本站不保证下载资源的准确性、安全性和完整性, 同时也不承担用户因使用这些下载资源对自己和他人造成任何形式的伤害或损失。