AnIntroductiontoSixSigma(ppt 32)
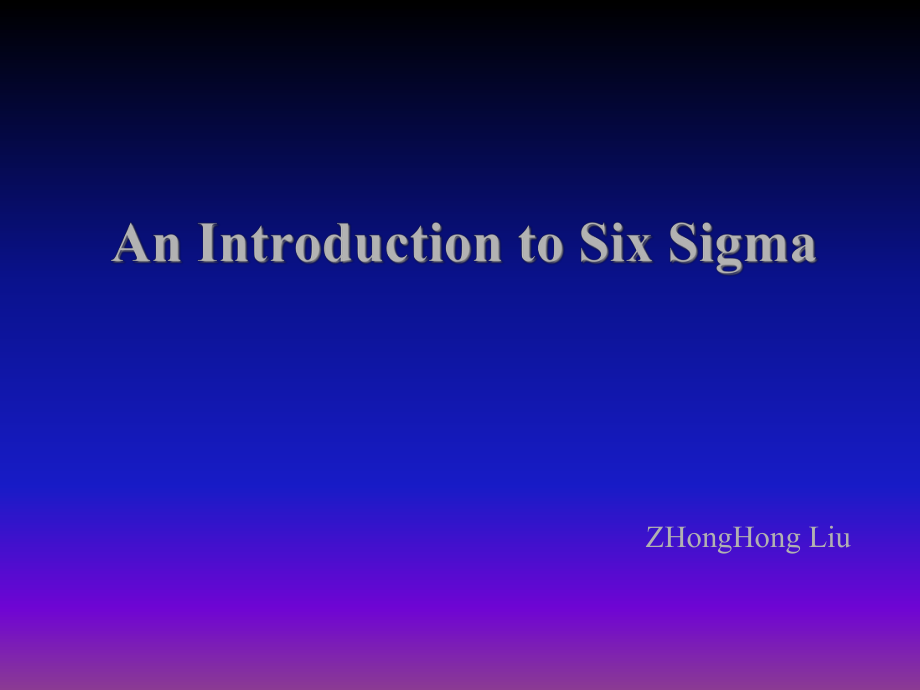


《AnIntroductiontoSixSigma(ppt 32)》由会员分享,可在线阅读,更多相关《AnIntroductiontoSixSigma(ppt 32)(32页珍藏版)》请在装配图网上搜索。
1、ZHongHong Liu To learn the systematic approach to Six Sigma problem solving M before A before I before C To understand some M.A.I.C.tool kit To understand how you will be affected by Six Sigma methodology Define Measure,Analyze,Improve and Control Define KPIV and KPOV Explain how process outputs are
2、 a function of the inputs Explain the value of measurement“Nothing New”Most of the tools have been around for decadesNeglected due to difficulty and disciplineBUTWorldwide competitionMakes neglect dangerousComputing resourcesMakes application possible99%Good is Not Good Enough 5,000 incorrect surgic
3、al procedures each week 20,000 lost articles of mail each hour No electricity for almost 7 hours each month Unsafe drinking water for almost 15 minutes each dayWhere Does Industry Stand?7Sigma Scale of Measure1,000,000100,00010,0001,000100101PPMRestaurant BillsDoctor Prescription WritingPayroll Proc
4、essingOrder Write-up Journal VouchersWire TransfersAirline Baggage HandlingPurchased Material Lot Reject RateDomestic Airline Flight Fatality Rate (0.43 PPM)Best-in-ClassAverage Company 3 4 56 2 1IRS-Tax Advice(phone-in)(140,000 PPM)lVisionlPhilosophy lVehicle for:Customer focus Breakthrough improve
5、ment Continuous improvement People involvement lAggressive goal lMetric(standard of measurement)lMethodSix Sigma VisionThe Vision of Six Sigma is to delight customers by delivering world-class quality products through the achievement of Six Sigma levels of performance in everything we do.Six Sigma P
6、hilosophyThe Philosophy of Six Sigma is to apply a structured,systematic approach to achieve breakthrough improvement across all areas of our business.Whats the Strategy?Know whats important to the Customer(CTQs)Reduce defects Center around target Reduce VariationSix Sigma GoalReduce Defect RateImpr
7、ove Product YieldImprove Customer SatisfactionIncrease Product ProfitWhat problem we should focus on?High Defect Rate Low Product Yield Long Cycle time High Downtime High Maintenance Cost Bottleneck Step Poor Process CapabilityUnsatisfactoryBreakthrough StrategySEAGATE CONFIDENTIALFilenameAuthorDate
8、Revision#Slide#Deploy Overview.pptMarch 27,2000113Six Sigma-Six Sigma Enables Breakthrough LevelImprovement!12345 The problem with continuous improvements as the only goal,Organization sees improvement BUT loses the game.Time in YearsStandard Approaches Current Tools Kaizen Lean Manufacturing Re-eng
9、ineering Typical TQMImprovementBreakthrough Strategy-Trained&DedicatedIndividuals-Analytical Expertise-70%Improvement perProjectSix SigmaTimeReject RateSpecial VariationHistorical Level(0)Optimum Level(1)Natural Variation under 0 Natural Variation under 1(30)(31)2308,537366,80746,210523363.4 PPMProc
10、essCapabilityDefects per Million Opp.Six Sigma-Aggressive Goal3 Sigma 6 Sigma5 Sigma4 Sigma 93.32%99.379%99.9767%99.99966%HistoricalCurrentIntermediateLong-RunSigmaLong-Term YieldStandardSix Sigma-Performance Target Average Deviation from Mean1 TUSLp(d)p(d)12345699.99966%Good(6 Sigma)20,000 lost art
11、icles of mail per hourUnsafe drinking water for almost 15 minutes each day5,000 incorrect surgical operations per weekTwo short or long landings at most major airports each day200,000 wrong drug prescriptions each yearNo electricity for almost seven hours each monthSeven articles lost per hourOne un
12、safe minute every seven months1.7 incorrect operations per weekOne short or long landing every five years68 wrong prescriptions per yearOne hour without electricity every 34 years99%Good(3.8 Sigma)Six Sigma-Practical MeaningCustomer Focus:A Model For SuccessTechnologyCapabilityOrganizationPeopleProc
13、essest Management is responsible to help drive the total employee population to a higher level of problem solving proficiencyt Identifies their best candidates for Black Belt appointmentt Demonstrates high enthusiasm to keep Six Sigma moving forwardt Provides the lead at getting Green Belts(includin
14、g themselves)identified and through trainingt Asks the right questions to all employees to assure the discipline of Six Sigma and its tool kit are properly and fully exploitedt Drives the broad use of Six Sigma methods and tools,including FMEA,DOE,SPC,etct Owns day to day&career management of the Bl
15、ack Belt,including appropriate placement when Black Belts assignment concludesSix Sigma System-ManagementSix Sigma Basic PrincipleThe Improvement Strategy(MAIC)Focus_Vital Few xiYYYYYx1,x2,.xnx1,x2,.xnVital Few xiVital Few xiVital Few xiVital Few xi Phase_MeasureAnalyzeImproveControl6786786786786786
16、78678678Select Product or Process Key Characteristic(s);e.g.,Customer YDefine Performance Standards For YValidate Measurement System for YEstablish Process Capability of Creating YDefine Improvement Objectives For YIdentify Variation Sources In YScreen Potential Causes For Change In Y&Identify Vital
17、 Few xiDiscover Variable Relationships Between Vital Few xiEstablish Operating Tolerances On Vital Few xiValidate Measurement System For xiDetermine Ability To Control Vital Few xiImplement Process Control System On Vital Few xiSIX SIGMA METHODS GENERATE DATA-BASED DECISIONS*What To Do With the Vita
18、l Few.ProcessKPIVKPIVKPIVKPOVCTQVital Few“Correct”(In-Spec)Defect-Free!KPIV Control Control Control -InputsNote:Statistically proven relationships between Inputs and OutputsManage the INPUTS and good OUTPUTS will followManufacturing Variation Causes A Hidden FactoryIncreased Cost -Lost CapacityThe p
19、rocess map reveals this hidden factoryYield After Inspection or TestEach defect must be detected,repaired and placed back in the process.Each defect costs time and money.Hidden FactoryNOTOKOK Wasted Time Wasted Money Wasted Resources Wasted Floor spaceDefects and the Hidden FactoryRolled Throughput
20、YieldHidden FactoryNOTOKYield After Inspection or Test=OKProcessABCRolled Yield81%73%Final TestD66%Using“final test(or first time)yield”ignores the hidden factory.Final test performance is a function of inspection&test not actual defect data.Rolled Throughput Yield(RTY)includes the hidden factory,re
21、work as well as scrap.It looks at output with zero defects.Rolled-Throughput YieldClassical First-Time YieldIf we are so good at X,why do we constantly test and inspect Y?nYnDependentnOutputnEffectnSymptomnMonitornX1.XNnIndependentnInput-ProcessnCausenProblemnControl To get results,should we focus o
22、ur behavior on the Y or X?Focus on X rather than Y,as done historicallyThe Focus of Six SigmaKPIVKPOV*Narrow the Scope of Input Variables-ID Leveraged KPIVsOptimized Process30-5010-154-8Key Process InputVariables(KPIVs)8-10KPIVsCritical KPIVs3-6Key Leverage KPIVsInputs VariablesProcess MapMulti-Vari
23、 Studies,CorrelationsScreening DOEsDOEs,RSMC&E Matrix and FMEAGage R&R,CapabilityT-Test,ANOM,ANOVAQuality SystemsSPC,Control PlansMeasureAnalyzeImproveControlData Driven Analysis1.We only use experience,not data2.We collect data,but just look at the numbers3.We group the data so as to form charts an
24、d graphs4.We use census data with descriptive statistics5.We use sample data with descriptive statistics6.We use sample data with inferential statisticsLevels of Analysis:What level are you at?The Foundation of the Six Sigma ToolsGoal Data is used to classify,describe,improve,control*Six Sigma Terms
25、 and Definitions1.Customerany One who receives a product,service or information from an operation or process.The term is frequently used to describe External customers-those who purchase the manufactured products or services which are the basis for the existence of the business.However,Internal cust
26、omers,also important,are internal GEL persons who receive the intermediate or internal products or services from internal Suppliers.2.CTQCritical to Quality Characteristic-a characteristic of a product,service or information which is important to the customer.CTQs must be measurable in either a cont
27、inuous scale manner(I.e.3.00mg,etc.)or descriptive manner(correct/incorrect,etc.)3.OpportunityAn event which generates an output(product,service or information).4.UnitA discrete item(lamp,invoice,etc.)which possesses one or more CTQ(Note:Units must be considered with regard with the specific CTQ(s)o
28、f concern by a customer and/or for a specific process)5.DefectAn output of an opportunity which does not meet a defined specification;ORA failure to meet an imposed requirement on a single quality characteristic or a single instance of non-conformance to the specification6.DPUDefects per Unit-the nu
29、mber of defects counted,divided by the number of products or characteristics(units)produced.7.DPMODefects per Million Opportunities-the number of defects counted,divided by the actual number of opportunities to generate that defect,multiplied by one million.8.COPQCost of Poor Quality-the cost incurr
30、ed from generating a defectORCost which would be avoided if,rather than a Defect,the Opportunity yielded a success.9.KPIVKey Process INPUT Variable-an independent material or element,with descriptive characteristic(s),which is either an object(going into)or a parameter of a process(step)and which ha
31、s a significant(Key)effect on the output of the process10.KPOVKey Process OUTPUT Variable-a dependent material or element,with descriptive characteristic(s),which is the result of a process(step)which either is,or significantly affects the customers CTQ.11.Rolled Throughput YieldThe likelihood that
32、any given unit of product,service or information will contain Zero Defects.12.CapabilityThe best that a process,which is in control,can perform under current conditions.12.EntitlementThe Best,Potential performance of a process based on process design14.DFSSDesign for Six Sigma(often referred to as Design for Manufacturability)
- 温馨提示:
1: 本站所有资源如无特殊说明,都需要本地电脑安装OFFICE2007和PDF阅读器。图纸软件为CAD,CAXA,PROE,UG,SolidWorks等.压缩文件请下载最新的WinRAR软件解压。
2: 本站的文档不包含任何第三方提供的附件图纸等,如果需要附件,请联系上传者。文件的所有权益归上传用户所有。
3.本站RAR压缩包中若带图纸,网页内容里面会有图纸预览,若没有图纸预览就没有图纸。
4. 未经权益所有人同意不得将文件中的内容挪作商业或盈利用途。
5. 装配图网仅提供信息存储空间,仅对用户上传内容的表现方式做保护处理,对用户上传分享的文档内容本身不做任何修改或编辑,并不能对任何下载内容负责。
6. 下载文件中如有侵权或不适当内容,请与我们联系,我们立即纠正。
7. 本站不保证下载资源的准确性、安全性和完整性, 同时也不承担用户因使用这些下载资源对自己和他人造成任何形式的伤害或损失。