年产200吨硫酸链霉素工业盐发酵车间的工艺课程设计
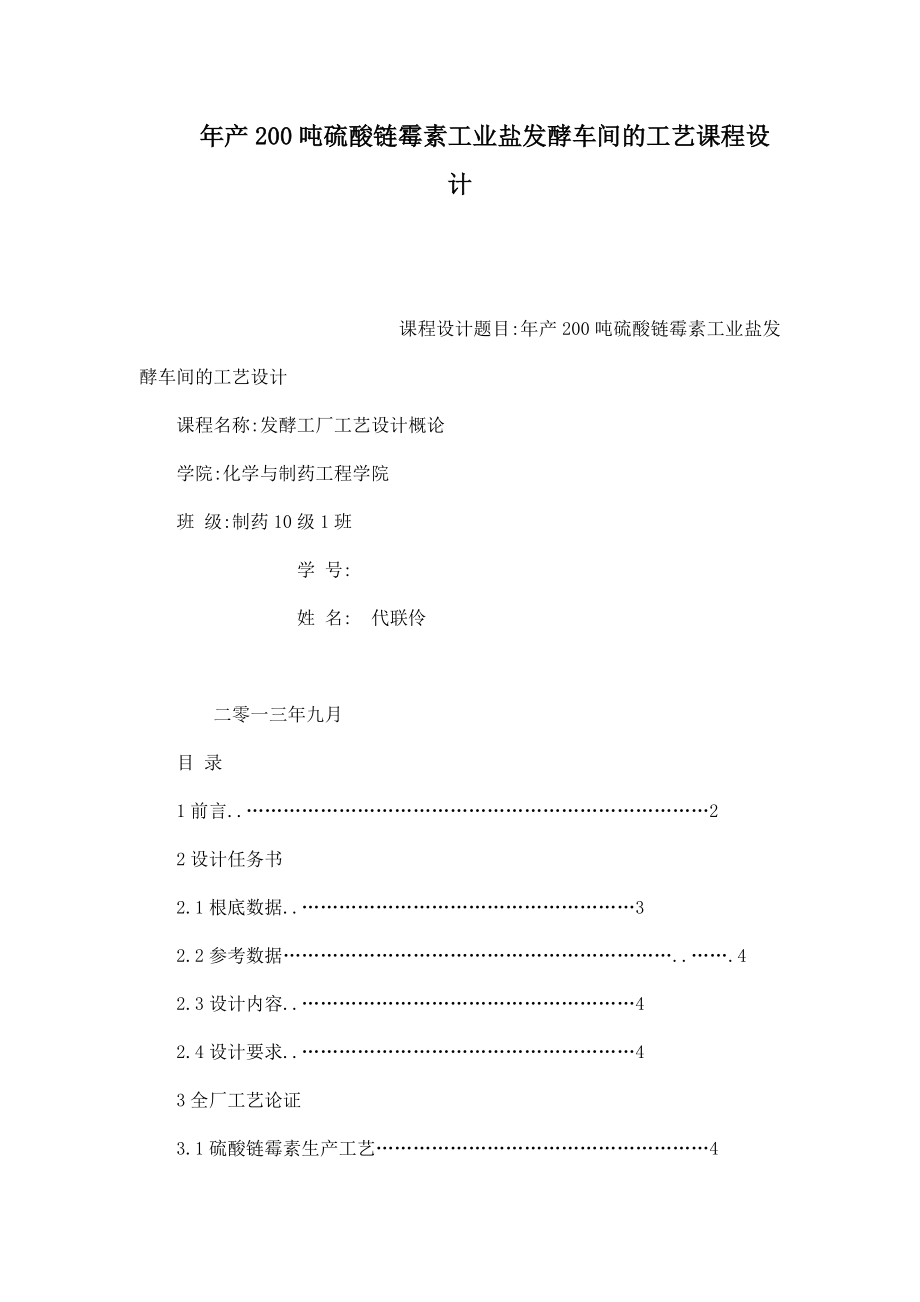


《年产200吨硫酸链霉素工业盐发酵车间的工艺课程设计》由会员分享,可在线阅读,更多相关《年产200吨硫酸链霉素工业盐发酵车间的工艺课程设计(28页珍藏版)》请在装配图网上搜索。
1、年产200吨硫酸链霉素工业盐发酵车间的工艺课程设计 课程设计题目:年产200吨硫酸链霉素工业盐发酵车间的工艺设计课程名称:发酵工厂工艺设计概论学院:化学与制药工程学院班 级:制药10级1班 学 号: 姓 名: 代联伶 二零一三年九月目 录1前言.22设计任务书2.1根底数据.32.2参考数据.42.3设计内容.42.4设计要求.43全厂工艺论证3.1硫酸链霉素生产工艺43.1.1硫酸链霉素生产工艺概述.43.1.2筛选生产菌种.53.1.3无菌空气的制备.53.2发酵工艺.53.2.1斜面孢子培养.53.2.2摇瓶种子培养.53.2.3种子罐扩大培养.53.2.4发酵罐培养.53.3溶氧的影响
2、及控制.63.4温度.63.5 PH值.63.6泡沫与消沫.63.7提取工艺.74工艺计算4.1物料衡算.94.2热量衡算.104.3耗水量的计算.115发酵车间设备的选型计算5.1发酵罐的选型.135.2生产能力、数量和容积确实定.135.2.1发酵罐容积确实定.135.2.2生产能力的计算.135.2.3发酵罐个数.135.2.4主要尺寸的计算.135.2.5搅拌器的设计.135.2.6搅拌轴功率的计算.145.3设备结构的工艺设计.165.3.1空气分布器.165.3.2挡板.166冷却管的布置6.1冷却面积的计算.166.1.1冷却管组数和管径.176.1.2冷却管总长度L计算.186
3、.1.3每组管长L0和管组高度186.1.4每组管子圈数.187、PH测定198、消泡199、观察窗口.1910、液面高度显示管安装.1911、封头连接方式.1912、密封方式.1913、对本设计的评述.1914、参考文献.201、前言 硫酸链霉素的主要成分是链霉素,链霉素(streptomycin)是一种氨基葡萄糖型抗生素,分子式C21H39N7O12。于1943年由美国 S.A.瓦克斯曼从链霉菌中析离得到,是继青霉素后第二个生产并用于临床的抗生素。它的抗结核杆菌的特效作用,开创了结核病治疗的新纪元。 硫酸链霉素化学结构式 链霉素是一种从灰链霉菌的培养液中提取的抗菌素。属于氨基糖甙碱性化合物
4、,它与结核杆菌菌体核糖核酸蛋白体蛋白质结合,起到了干扰结核杆菌蛋白质合成的作用,从而杀灭或者抑制结核杆菌生长的作用。链霉素属窄谱抗生素,主要对革兰氏阴性杆菌如大肠杆菌、产气杆菌、肺炎杆菌、痢疾杆菌、变形杆菌、布鲁氏菌、鼠疫杆菌等有抗菌作用。特别对结核杆菌作用较强,在低浓度时有抑菌作用,在高浓度时有杀菌作用。但对大多数革兰氏阳性菌不如青霉素,对真菌、立克次氏体、病毒等无效。 由于硫酸链霉素肌肉注射的疼痛反响比较小,适宜临床使用,只要应用对象选择得当,剂量又比较适宜,大局部病人可以长期注射(一般2个月左右)。所以,应用数十年来它仍是抗结核治疗中的主要用药。 其生产过程分为两大步骤:菌种发酵,将冷干
5、管或沙土管保存的链霉菌孢子接种到斜面培养基上,于27下培养7天。待斜面长满孢子后,制成悬浮液接入装有培养基的摇瓶中,于27下培养4548小时待菌丝生长旺盛后,取假设干个摇瓶,合并其中的培养液将其接种于种子罐内已灭菌的培养基中,通入无菌空气搅拌,在罐温27下培养6263小时,然后接入发酵罐内已灭菌的培养基中,通入无菌空气,搅拌培养,在罐温为27下,发酵约78天。提取精制,发酵液经酸化、过滤,除去菌丝及固体物,然后中和,通过弱酸型阳离子交换树脂进行离子交换,再用稀硫酸洗脱,收集高浓度洗脱液链霉素硫酸盐溶液。洗脱液再经磺酸型离子交换树脂脱盐,此时溶液呈酸性,用阴离子树脂中和后,再经活性炭脱色得到精制
6、液。精制液经薄膜浓缩成浓缩液,再经喷雾枯燥得到无菌粉状产品,或者将浓缩液直接做成水针剂。12、设计任务书2.1根底数据生产规模:200吨/年产品规格:成品效价为800单位/mg生产天数:300天/年接种量:15%倒罐率:1%发酵周期:8天每天放罐:3罐发酵装料系数:70%发酵液收率:95%提炼总收率:75%平均发酵水平:22000单位/ml种子培养基配比g/L:牛肉膏 6%,葡萄糖 4%,KH2PO4 1%,MgSO4 1%生产培养基配比g/L:葡萄糖4%,黄豆饼粉0.8%,玉米浆1.5%,(NH4)2SO4 0.5%,豆油0.2%,KH2PO4 0.01%,CaCO3 0.04%2.2参考数
7、据罐体的高径比H/D:13搅拌桨直径与罐体直径之比Di/D: 1/31/2挡板宽度与罐体直径之比Wb/D :1/81/12(4块挡板)最下层搅拌桨高度与罐体直径之比:0.81.0相邻两层搅拌桨距离与搅拌桨直径之比:12.5发酵条件:转数350r/min ,温度28,pH7.2(400L发酵罐)冷却水进出口温度分别为25、30黏度:38cP培养基比热容: C.0374.18X+4.181-X【X:固形物的质量百分比】2.3设计内容根据以上设计任务,查阅有关资料、文献,搜集必要的技术资料,工艺参数与数据,进行生产方法的选择,工艺流程与工艺条件确实定与论证。工艺计算:全厂的物料衡算;发酵车间的热量衡
8、算(即蒸汽耗量的计算);水用量的计算;发酵车间耗冷量计算。发酵车间设备的选型计算:包括设备的容量、数量、主要的外形尺寸。对发酵设备进行详细化工计算与设计。2.4 设计要求根据以上设计内容,书写设计说明书完成图纸(1号图纸):带控制点工艺流程图(初步设计阶段),发酵设备总装图(剖面和俯视图)或车间平面布置图。3、全厂工艺论证13.1硫酸链霉素生产工艺3.1.1硫酸链霉素生产工艺概述硫酸链霉素的整个生产过程可分为以下4个工艺阶段:筛选生产菌种无菌空气的制备和发酵工艺链霉素的提取硫酸链霉素的加工制备由这四个工艺阶段硫酸链霉素生产厂家一般将其生产分为以下四个生产车间:生产菌种筛选和准备车间发酵车间提取
9、车间精制车间 除以上四个车间外,为保障生产过程中对培养基和无菌水等的需要,还设置了其它部门。3.1.2筛选生产菌种 出发菌株多采用灰色链霉菌。灰色链霉菌的孢子梗直而短,不呈螺旋形,孢子数量很多,孢子乃断裂而成,呈椭圆形,气生菌丝和孢子均呈白色,单菌落生长饱满,呈梅花型或馒头型,直径为 34mm,基质菌丝透明,在斜面背后产生淡色色素。3.1.3无菌空气的制备 在抗生素的工业发酵中,生产菌大多是好痒菌,要求连续通入大量无菌空气,故无菌空气的质量标准是至关重要的。目前工业发酵企业一般采用二级过滤除菌:总过滤器粗过滤除菌和进罐前分过滤器过滤除菌。这样可很大程度上降低杂菌污染情况。3.2发酵工艺 链霉素
10、发酵生产工艺与其它抗生素相似,采用漂浮培养法,在通气搅拌条件下,菌种在一定组成的培养基内,经过23级的种子扩大培养,最后进行发酵生产。其过程一般包括:斜面孢子培养、摇瓶种子培养、种子罐培养和发酵培养等。3.2.1斜面孢子培养 将砂土管(或冷冻管)菌种接种到斜面培养基,经培养后即得原始斜面。原 始斜面质量要求一般为:菌落分布均匀,密度适中,颜色洁白,但菌落饱满。再从原始斜面的饱满单菌落接种至斜面上,长成后即得生产斜面,斜面上的菌落应为白色饱满的梅花形和馒头形,反面为淡棕色色素,排除各种杂型菌落。经两次传代,可到达纯化的目的,排出变异的菌株。其质量还应通过摇瓶实验来进行控制。合格的孢子面存在低温冷
11、库(04)内备用。3.2.2摇瓶种子培养 生产斜面的菌落接种到摇瓶种子培养中,经过培养基即得摇瓶种子。链霉素发酵经常使用摇瓶种子来接种种子罐。种子质量以菌丝阶段、发酵单位、菌丝粘度或浓度、糖氮代谢、种子液色泽和无菌检查为指标。摇瓶种子可以直接接种子罐,也可以再扩大培养,用培养所得的子瓶来接种。摇瓶培养的培养基成分为黄豆饼粉、葡萄糖、硫酸铵、碳酸钙等。黄豆饼粉的质量和葡萄糖的用量对种子质量都有影响。3.2.3种子罐扩大培养 种子罐培养是用来扩大种子量的。种子罐培养可为23级,根据发酵罐体大小和接种量来确定。第一级种子罐一般采用摇瓶种子接种,23级种子罐那么是逐级转移,接种量一般都为10%左右。种
12、子质量对后期发酵的影响甚大,种子必须符合各项质量要求(糖氮代谢、菌丝粘度和浓度、菌丝阶段、效价和无菌要求),方能转罐。因此在培养过程中,必须严格控制好罐温、通气搅拌和泡沫,以保证菌丝生长良好,得到符合要求的种子。3.2.4发酵罐培养 发酵罐培养是链霉素生物合成的最后一步,也是最关键的一步,链霉素的发酵培养基主要由葡萄糖、黄豆饼粉、硫酸铵、玉米浆、磷酸盐和碳酸钙等组成。各成分元素的差异都会影响发酵生产的进行。 1 碳源 链霉素产生菌?灰色链霉菌可以利用葡萄糖、果糖、半乳糖、木糖、D一甘露醇、麦芽糖、乳糖和淀粉。2 氮源 目前都采用复合氮源。有机氮源如黄豆粉等,无机氮源如硫酸铵等铵盐,3 磷源 营
13、养物质除碳、氮源外,磷源亦是很主要的因素之一,由于营养物供能及合成菌丝蛋白,整个代谢过程很多需有磷酸盐的参与,同时物质代谢所产生的能量,一局部被利用于高能磷酸化合物主要是ATP的生成。3.3溶氧的影响及控制 链霉素产生菌?灰色链霉菌是一种高度需氧菌。它在整个代谢过程中以葡萄糖作为主要碳源,只有以氧做为最终电子受体时方能获得大量能量,来满足菌体生长、繁殖和合成链霉素。据文献记载19,空气中氧在培养液中的饱和浓度1 a tm, 25大约只有 0.2 毫克分子O2升/小时,而链霉素发酵液中菌体的摄氧率在 1050 毫克分子O2升/小时。因此向发酵液中迅速地补充溶解氧是链霉素发酵中的重要问题11。对溶
14、氧水平有较大影响的因素主要有:a、菌体代谢是否旺盛。b、培养液的粘度:过高的粘度会影响氧的传递,即影响氧由气相溶解于液相之中。c、补料:补糖后糖代谢加快。d、罐压:在培养前期,一般罐压每升高或降低 0.lkg/cm2 溶氧浓度就升高或降低 4%左右;在培养中、后期,罐压每升高或降低 0.lkg/cm2 溶氧浓度就升高或降低 3%左右。但罐压超过一定限度对菌体的生长、代谢就要产生不良影响。e、空气流量:体积氧传递系数中,Vs为空气在罐中的直线速率,它与空气流量是等效的。应尽量增大Vs,但其超过一定限度后溶氧浓度不再上升,反而会造成泡沫上升,发酵中间产物未及被利用即被带出而造成不良后果,甚至使搅拌
15、器周围充满气泡从而使搅拌失去作用,造成溶氧下降。f、搅拌:不同的搅拌桨形式以及速度,对溶氧也会产生很大的影响。机械搅拌能损坏菌丝体,对发酵液过滤不利。采用空气搅拌器那么克服了这一缺点,提高了罐的利用率。采用大直径小浆叶的搅拌器,在适当增加转速下,能得较高的吸氧率。另外将涡轮式改为多棒式搅拌器,可降低功率消耗近一半。3.4温度 灰色链霉菌对温度敏感。据报道,z-38 菌株对温度高度敏感:25时,发酵单位为1180毫克/升/118小时;27时为2041毫克/升/118小时;29时为2194 毫克/升/104 小时,而31时那么为414 毫克/升/72 小时。故认为链霉素生产适宜培养温度为28.5左
16、右。有些人认为不一定在 2431的范围,应随菌株不同而适宜温度有所改变。3.5 pH 值 pH值直接影响到发酵过程中各种酶活动,影响菌体对基质代谢的速度,甚 至改变菌体的代谢途径及细胞结构。菌体的发育生长和抗生素的合成有不同的适宜pH值。发酵过程中pH值必须予以控制,才能符合菌体生长和抗生素合成的需要。适合链霉菌菌丝生长的 pH 约为6.57.0,适合于链霉素合成的 pH 约为 6.87.3,pH低于 6.0 或高于7.5,对链霉素的生物合成不利。pH对链霉素发酵 影响很大,故很多国家为了准确控制 pH 值,使用 pH 自动控制装置。这样,可 提高发酵单位,又可以减少培养基中碳酸钙的用量,在发
17、酵液预处理时,还可减少中和用的酸量12。3.6泡沫与消沫 链霉素发酵过程产生大量泡沫,尤其在发酵前期,由于菌丝生长处于对数生长期,代谢旺盛,在通气和连续搅拌条件下产生大量泡沫,如不及时进行消沫控 制,就产生逃液等现象,发酵不易正常进行。故一般都需加一定量之消沫剂进行 消沫。消沫剂分油脂类、脂肪酸类、脂肪酸酷类、醇类、醚类、胺类、酞胺类、金属碱类、硅酮类等,抗菌素生产中可应用硅酮、聚氧乙烯和聚氧丙烯的共聚物,其中硅酮对微生物影响小,是一种较好的消沫剂。国内已成功地使用了聚氧乙烯甘油醚和聚氧丙烯甘油醚作为消沫剂。13。3.7 提取工艺 经34级发酵生物合成链霉素。发酵液用水稀释,草酸酸化至pH3.
18、0左右,加热至7580,通过离心别离或板框过滤,除去大量不溶性菌丝体、酸性蛋白、钙镁离子、培养基残渣等杂质,冷却至15以下,再用NaOH中和得到符合离子交换工艺要求的澄清链霉素原液。这一过程在生产上称为发酵液的预处理。原液中的链霉素在水溶液中离解成三价阳离子,应用钠型弱酸性阳离子交换树脂110树脂或大孔D-152树脂进行吸附,洗脱后成为链霉素洗脱液,在这一步提取过程中使水溶液中的链霉素得到富集,含量由不到1%浓缩到20%。同时,通过离子交换树脂的选择作用,除去绝大局部的无机离子、色素、蛋白质及可见的固形物等。 链霉素提取液经大孔伯胺基吸附树脂D303树脂通过Schiff反响除去双氢链霉糖、链霉
19、胍、链霉胺等不含醛基的链霉素同系物,再经强酸性阳离子交换树脂125树脂和弱碱性阴离子交换树脂703树脂组成的混合床脱盐中和得到提纯液。 提纯液先经药用活性炭脱色处理,吸附色素和细菌内毒素,经减压蒸发,在45以下浓缩,链霉素含量由10%左右浓缩到45%。最后为了进一步提高成品色级和保证细菌内毒素及热原合格,参加一定量的药用活性炭脱色处理得到符合质量要求的成品浓缩液。成品浓缩液经过石棉板除菌过滤,喷雾枯燥得到白色或类白色的无菌粉末,分装出厂。 4、工艺计算4.1物料衡算3 首先计算生产1000kg成品链霉素所需耗用的原辅材料及其他物料量:发酵液量:V1100080022000(1-1%)95%75
20、%51.55m3种子液量接种量为15%:V2V115%7.7325m3牛肉膏耗用量:种子液用量:V26%7.73251036%463.95kg 葡萄糖耗用量:种子液用量:V24%7.73251034%309.3kg发酵液用量:V14%51.551034%2062kg葡萄糖总共耗用量:309.3+20622371.3kgKH2PO4耗用量:种子液用量:V21%7.73251031%77.325kg发酵液用量:V10.01%51.551030.01%5.155kgMgSO4耗用量:种子液用量:V21%7.73251031%77.325kg黄豆饼粉耗用量:发酵液用量:V10.8%51.551030.
21、8%412.4kg玉米浆耗用量发酵液用量:V11.5%51.551031.5%773.25kg9.(NH4)2SO4耗用量:发酵液用量:V10.5%51.551030.5%257.75kg10.豆油耗用量:发酵液用量:V10.2%51.551030.2%103.1kg11.CaCO3耗用量:发酵液用量:V10.04%51.551030.04%20.62kg200吨/年,链霉素厂发酵车间的生物料衡算物料名称生产1000kg链霉素产品的物料量200t/a,链霉素生产的物料量每日物料量发酵液量m351.551031034.37种子液量m37.7321546.45.15牛肉膏耗用量kg463.9592
22、7901237.2葡萄糖耗用量kg2371.34742601580.87KH2PO4耗用量kg82.481649654.99MgSO4耗用量kg77.3251546551.55黄豆饼粉耗用量kg412.482480274.93玉米浆耗用量kg773.25154650515.5(NH4)2SO4耗用量kg257.7551550171.8豆油耗用量kg103.12062068.7CaCO3耗用量kg20.62412413.754.2热量衡算3 对于单发酵罐,利用直接蒸汽混合加热,蒸汽消耗量为: 式中:D?蒸汽消耗量,kg G?被加热料液量,kg c?料液的比热,kJ/kg? t2?加热结束时料液的
23、温度, t1?加热开始时料液的温度, i?蒸汽的热焓,kJ/kg ?加热过程中由于热损失而增加的蒸汽消耗量,可取5%-10% 又料液的比热: c0.374.18x+4.18(1-x) x?固形物的质量百分比根据地理位置及气候条件,取一年中的最低室温10作为料液的初始温度t1,取10%,忽略种子液的加热被加热料液量:G34370+1374.67+3.44+274.93+515.5+171.83+68.73+13.7536792.85kg固形物的质量百分比: x2365.78/55184.2756.43%料液的比热: c0.374.186.43%+4.181-6.43%4.0kJ/kg? 故直接蒸
24、汽混合加热,蒸汽的消耗量: D1Gct2-t1?1+i-t2?c36792.854.0121-101+10%/503.67-1214.0 8.23105kg 4.2.2发酵罐空罐灭菌时的蒸汽消耗量估算:4 D5VFs 式中: VF?发酵罐全容积,m3 s?发酵罐灭菌时,罐压下蒸汽的密度,kg/m3 灭菌时的温度为121,在该温度下水蒸汽的密度s943.1kg/m3 发酵罐全容积VF 34.3770%49.1m3 故 D25VFs549.1105kg 4.2.3发酵罐实罐灭菌保温时的蒸汽消耗量估算4 一般来讲,保温时间内的蒸汽消耗量可按发酵罐实罐灭菌直接蒸汽加热升温时的蒸汽消耗量的30%50%来
25、估算。 故 D350%D14.12105kg 总蒸汽的耗用量为:DD1+D2+D314.67105kg200t/a链霉素车间总热量衡算表名称规格(MPa)每吨产品消耗(kg)每天消耗(kg)年消耗量(kg)蒸汽0.3(表压)14.671059.781052.931084.3耗水量的计算4种子液用水量:5.15m3发酵液用水量:34.37m3发酵冷却水用量:只考虑全年平均负荷WQc2*tk-tH式中:W?冷却水消耗量,kg/h Q?物料的热效应,kJ/h c2?冷却水的比热kJ/kg*,通常水的比热为4.183kJ/kg* tk?冷却水的出口温度 tH?冷却水的进口温度在计算冷却水耗量时,其冷却
26、水的进出口温差ttk-tH取5冷冻水或冷盐水 其中发酵罐发酵过程中的热效应计算:F*VL 式中:Q?发酵罐的热效应,kJ/hQF?单位体积发酵液所产生的热量,又称发发酵热,kJ/m3*h,对于链霉素发酵,其值为18800kJ/m3*h VL?发酵罐内发酵液体积,m3 其中发酵罐内发酵液体积见发酵罐公称容积计算:VL60*70%42m3那么WQc2*tk-tHQF*VLc2*tk-tH 18800*424.183*5 37752.8kg/h5发酵车间设备的选型计算工艺设备选型与设备选材的原那么7 满足?药品生产质量管理标准?(2021年修订)中有关设备选型的要求。 根据该厂生产特点,结合企业生产
27、经验,以保证产品质量为前提,充分利用公司现有符合GMP要求的设备。5.1发酵罐5 根据发酵物的发酵特性,选用机械涡轮搅拌通风发罐通用罐,选用此种发酵罐的原因主要是:历史悠久,资料齐全,在比较放大方面积累了较丰富的成功经验,成功率高。5.2生产能力、数量和容积确实定5 5.2.1发酵罐容积确实定 公称容积的计算 V0200*1000*800(22000*300*3*99%*95%*70%)70% 17.5m3,取20m3 那么选用公称容积20m3的发酵罐。 5.2.2生产能力的计算 平均每罐产品生产量: 20*70%*99%*95%*70%*22000/800253.46kg 5.2.3发酵罐个
28、数 N发酵周期每天放罐数8*3+125个 5.2.4主要尺寸的计算 公称容积:20m3 发酵罐的H/D值取2 20m3通用式发酵罐的主要尺寸来确定.得到罐内径m2.3封头容积m31.76圆柱高m4.6圆柱局部容积m319.1封头高m0.615不计上封头的容积m320.86罐体总高m5.83全容积m322.65.2.5搅拌器设计 从消耗功率来看:平叶弯叶箭叶 从发酵液中气含率来看:平叶弯叶箭叶 从轴向混和效果来看:箭叶弯叶平叶 从上述条件综合考虑,再考查国内外的主要选型情况。本次设计选用六弯叶涡轮式搅拌器。常用六弯叶涡轮式搅拌器的尺寸比例为h:b:d1:d4:5:13:20,r0.5d1,38由
29、前得出d2.3m,可推出h0.46m,b0.575m,d11.495m,r0.7475m,38。 采用3层搅拌器,最下层搅拌桨与罐体直径之比取0.8,那么最下层搅拌桨高度为1.84m,根据静液面高,选取相邻两层搅拌桨距离与搅拌桨直径之比为1,那么相邻两层搅拌桨距离为2m。搅拌器尺寸hm0.46底距(m)1.84bm0.575搅拌桨个数(个)3dm2.3相邻搅拌桨距离(m)2rm0.748d1m1.495 5.2.6搅拌轴功率的计算 搅拌转速以小罐为比较放大,其转数为N1350r/min,搅拌叶径D10.25m,按比较放大公式: N2N1D1/D22/33500.19/12/3116r/min
30、参考设计数据与工厂实际,为保证发酵罐的溶氧系数,取N2110r/min。发酵液体被搅动后流体的雷诺数可用下式计算: (110/60)121088.5/(3810-3) 5.25104104 视为湍流状态 此状态下,单一搅拌器的轴功率: P NpN3D5 4.8110/603151088.5 31kw 上两式中:Np?功率系数,在圆盘弯叶涡轮式湍流情况下取值4.8 N?搅拌转数,r/s D?搅拌器直径,m ?液体密度kg/m3,热量衡算中己算出,1088.5kg/m3 ?醪液黏度,N?s/m2 在计算搅拌轴功率时,因HL/D,D/D值不符合标准尺寸范围,根据实际情进行校正,校正式为:P校PD/D
31、?HL/DD/D*HL/D* 31*0.53.8351/331/2 42.93kw式中:D/D*和HL/D*为标准尺寸范围值,而D/D和HL/D为实际值HL?液面静高,其值为圆柱局部液高3.22m+底封头高0.615m,共高3.835m D?搅拌器直径,1m 总轴功率可由下式计算: PmP校1+0.6?(m-1) 本设计为3层搅拌器,那么总轴功率: PmP校1+0.6(3-1) 2.2P校 2.242.93 94.44kw 根据轴功率Pm可得出所需电动机输出功率: P电Pm+PT/ Pm1+10%+2%/ 94.441.12/0.95 111.34kw式中:PT?轴封摩擦损失之功率,kw,分为
32、填料合轴封摩擦损失功率取10%Pm,端面轴封摩擦损失的功率取2%Pm ?传动机构效率,皮带传动为0.95主要轴功率电机转速(r/s)2总轴功率kw94.44单一轴功率kw31电机输出功率kw111.34校正轴功率kw42.93 5.3设备结构的工艺设计5 设备结构的工艺设计,是将设备的主要辅助装置的工艺要求交代清楚,以供制造加工和采购时取得资料数据。本设计的主要辅助设备包括:5.3.1空气分布器6 对于好气发酵罐,分布器主要有两种形式,即多孔(管)式和单管式,本设计的发酵流程通气量大,所以采用单管通风。由于其进风速高,又有涡轮板阻挡,叶轮打碎、溶氧是没有问题的。通气管贴着罐壁到发酵罐底部,在搅
33、拌器正下方开口向下。5.3.2挡板6 挡板的作用是加强搅拌强度。本设计中虽有竖式冷却蛇管,但为了消除液面漩涡,更好的提高搅拌功率,采用4块挡板,挡板的宽度W取罐径的1/10,为0. 23m。挡板与罐壁之间应留有一定的间隙,防止培养液中的固体成分堆积在挡板背侧,其大小为0.1W,0.023m。6.冷却管布置56.1冷却面积的计算 发酵罐采用内部列管式蛇管换热。蛇管进水温度为25,出水温度为30,醪液温度不超过36。 冷却面积使用牛顿传热定律公式计算,即: 式中:F?冷却面积,m2 Q总?发酵罐的热效应,kJ/h K?竖式列管换热器传热系数,选用4.18500kJ/m3?h? tm?对数平均温差,
34、 其中平均温差 36-25-36-30?11/6 8.2 故冷却面积: 18800424.188008.2 28.80m2 又圆筒外外表积为:A0 因为外淋罐壁冷却效果相当于50%的列管冷却面积,相当于列管面积为42.150%21m2 由冷却水用量衡算处得冷却水体积流量为W11.2410-3m3/s,冷却方式采用内置竖直蛇管.取冷却水在竖直蛇管中流速v1m/s,那么根据流体力学方程式,冷却管总截面积: S总W/v11.2410-3 m2 那么进水总管直径d总S总/0.7851/20.12m6.1.1冷却管组数和管径 设管径d0.组数为n.由前得到的S总n?0.785d02 根据发罐的尺寸,选择
35、6组竖直蛇管.那么管径 d0S总/n?0.7851/2 11.2410-3/60.7851/2 0.049m查金属材料表选取?453.5无缝管,d内38mmd0,满足要求,取d平均40mm。现取竖直蛇管圈端部U型弯管曲径为0.25m那么直管距离为0.5m,两端弯管总长度为l0: 那么 l0D3.146.1.2冷却管总长度L计算由上知冷却管总面积F8.21m2,现取无缝钢管?453.5,每米长冷却面积F03.140.0410.1256m2 冷却管占有体积V0.7850.0526.1.3每组管长L0和管组高度 L0L/n65.4/610.9m 另需接管2.4m24弯处接管0.1m,那么实际管长L实
36、L+2.467.8m。 可排竖直蛇管的高度,设为静液面高度,下部可伸入封头0.25m。设发酵罐内附件占有体积0.2m3,那么发酵液总占有体积: 筒体局部液深为: 又两端弯管总长l01.57m,两端弯管总高为0.5m 一圈管长:l2h+l026.1.4每组管子圈数 n0L0/l10.9/13.171圈 现取管间距为:2.5D外2.5冷却管与冷却面积冷却面积(m2)28.8冷却管总长(m)67.8冷却管型号?453.5冷却管高度(m)10.9冷却组数(组)6冷却管圈数(圈)1每组管长(m)11.3管间距(m)0.1127、 pH测定6 电极测量,在装料液面中间部位开两个电极插入孔。8、消泡6因化学
37、消泡容易造成染菌,因而选用罐外消泡器,本设计设备选用离心式消泡器。9、观察窗口6 装料液面部位装置观察窗。10、液面高度显示管安装6 外置有机玻璃管。11、封头连接方式5 上封头直接焊接于筒身上,但在顶上开有人孔,以便进行检修。12、密封方式5 主要是指搅拌轴的密封问题,搅拌抽伸入罐内的方式主要有三种:从顶部伸入,从底部伸入和斜入法,斜入不是本设计的考虑范围。而对于顶部伸入和底部伸入法,小罐适合顶部伸入法,而大罐那么采用从底部伸入,此法有很多优点,如转动噪声小,重心低,可以减少罐壁厚度,轴的长度缩短后,可使稳定性提高,罐底的空间可以充分安装机械消沫等自动控制部件。本设计由于发酵罐较大,故采用底
38、部伸入法。但采用底部伸入法后,对轴封的要求就更为严格,因此本设计采用双端面机械轴封,并用无菌油类或水进行冷却和润滑。 13、对本设计的评价 本次设计,我的设计题目是年产200吨硫酸链霉素工业盐发酵车间工艺设计,刚看到这个题目是,我感觉一片茫然,不知该从何处下手。后来经过老师的指导,自己也查阅了相关书籍和资料,终于找到了些眉目。 设计时主要借助的途径就是网络,通过在网上找的设计模板,再参加自己的设计思想和数据,经过两周的工作,终于大致完成了本次设计任务。 上学期期末,我们也进行了化工原理的课程设计,那次设计老师每天都会在教室对我们进行指导,我们也从零开始,一步一步地完成了那次设计任务,虽然时间紧
39、迫,过程辛苦,但是看着自己最后设计出来的成果,还是感到由衷的开心,也学习和收获了很多。但是这次设计,我觉得老师的指导相对有些少,有些根本的数据也没有提供,所以导致我们在设计时很迷茫。对应模板时,很多数据都不知道是从何而来的,让设计之初就陷入了瓶颈。 尽管面对这么多问题,但是这次设计也是有所收获的,我通过在中国知网查阅资料,了解了硫酸链霉素的各种相关知识,也知道了发酵车间的设计内容。 物料恒算和热量衡算的局部是我们学过的制药工程的内容,通过这次设计过程,我又回忆了所学的知识,得以更加了解和熟悉了知识。为以后更灵活方便地运用这些知识打下了根底。 我选画的图形是发酵罐设备图,参考了?化工原理课程设计
40、?和?制药工程设备?两本书,在画图中,通过查资料和数据我对计算的数据又进行了适当的调整,使我对本次设计过程有了更全面的认识,看着根据自己的数据画出的图后,我感到有一种成就感,虽然设计过程参照了模板,但是整个画图过程,却是我自己的劳动成果。同时对模板也有了一个全新的理解和认识。 通过这次课程设计,我学到了根据相应数据设计药厂生产所需的材料的计算。让原来看起来很高深的东西变得根底和简单,我相信在今后的设计或工作中,我能总结本次设计经验,完成以后的设计任务。总的来说,本次设计收获颇丰。当然,由于知识水平有限,我的设计中肯定存在很多自己没有发现的问题和错误,恳请老师斧正,我也必将虚心接受老师的意见和批评,谢谢老师,老师辛苦了!14、参考文献1.袁亚萍.周永翔等.链霉素生产工艺实验论文.西南大学药学院J20062.王志祥.?制药工程学?.化学工业出版社.2021年3.吴思方.?发酵工厂工艺设计概论?.中国轻工业出版社.1900年4.张濂 ?化学反响工程原理?.华东理工大学出版社.2007年5.周国庆、张红兵.?化工工艺设计手册?.化学工业出版社.1996年6.胡洪波、彭华松.?生物工程产品工艺学?.高等教育出版社.2006年7.易学文、谢万如?制药工程课程设计?.2021年
- 温馨提示:
1: 本站所有资源如无特殊说明,都需要本地电脑安装OFFICE2007和PDF阅读器。图纸软件为CAD,CAXA,PROE,UG,SolidWorks等.压缩文件请下载最新的WinRAR软件解压。
2: 本站的文档不包含任何第三方提供的附件图纸等,如果需要附件,请联系上传者。文件的所有权益归上传用户所有。
3.本站RAR压缩包中若带图纸,网页内容里面会有图纸预览,若没有图纸预览就没有图纸。
4. 未经权益所有人同意不得将文件中的内容挪作商业或盈利用途。
5. 装配图网仅提供信息存储空间,仅对用户上传内容的表现方式做保护处理,对用户上传分享的文档内容本身不做任何修改或编辑,并不能对任何下载内容负责。
6. 下载文件中如有侵权或不适当内容,请与我们联系,我们立即纠正。
7. 本站不保证下载资源的准确性、安全性和完整性, 同时也不承担用户因使用这些下载资源对自己和他人造成任何形式的伤害或损失。